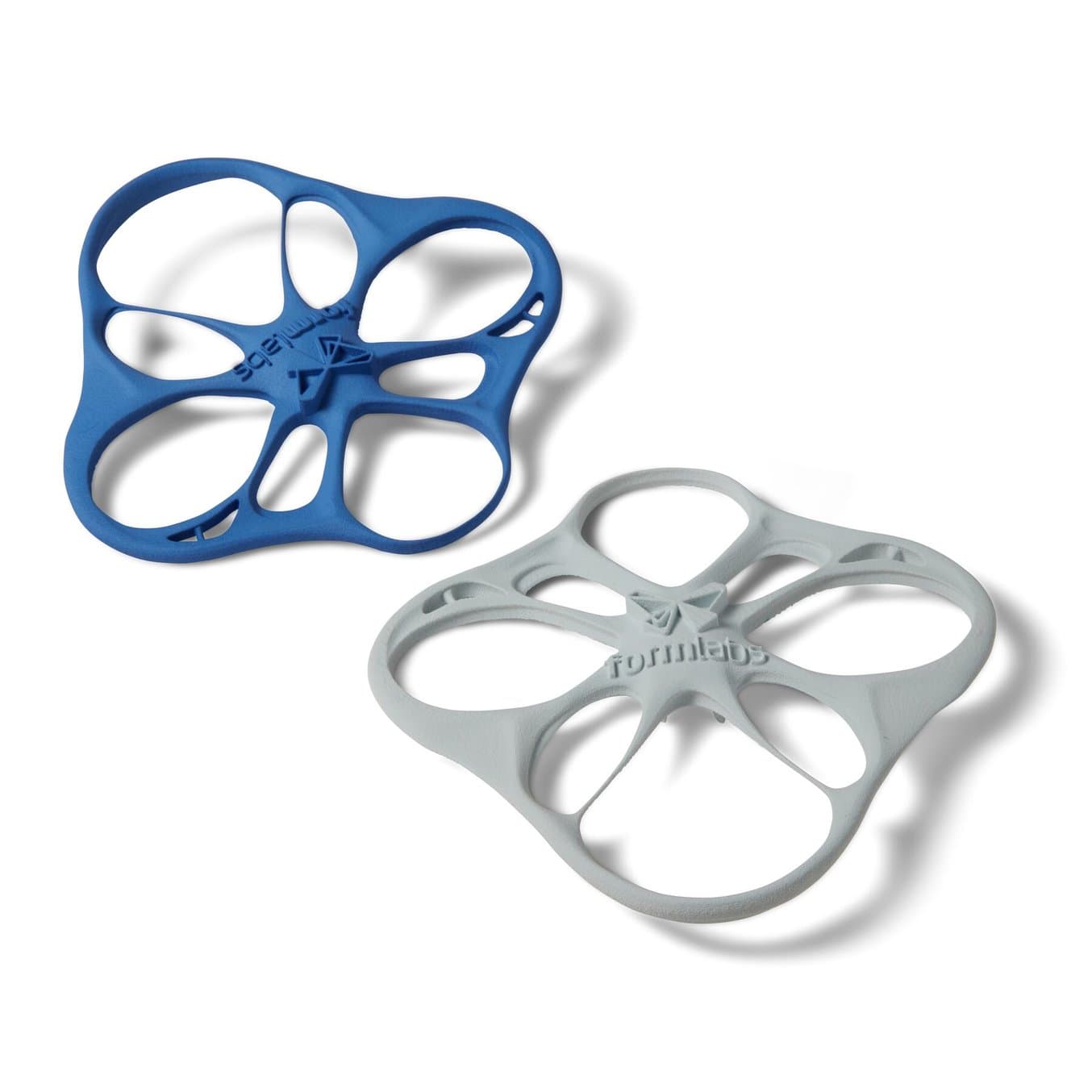
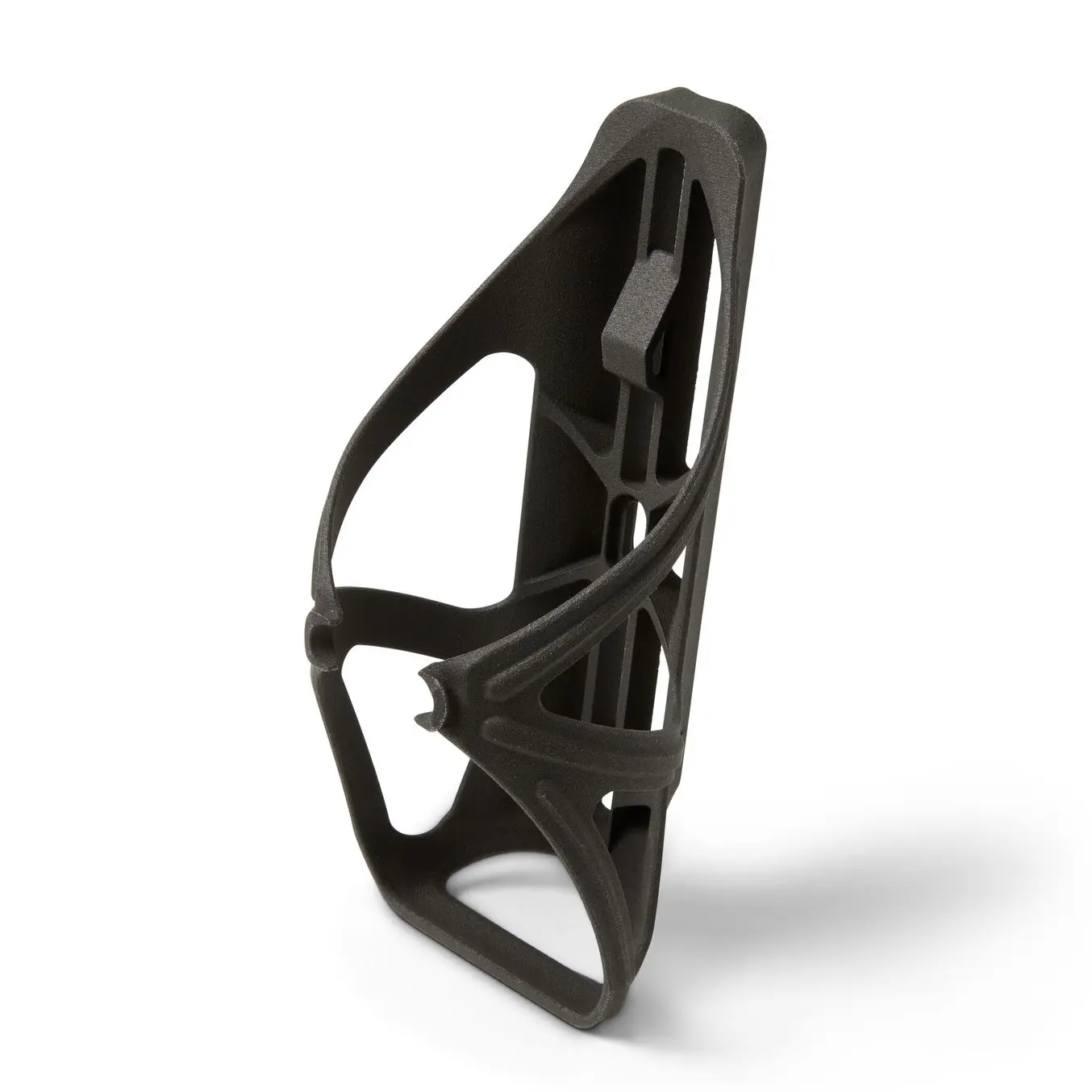
Formlabs is excited to announce an evolution of the Fuse Series SLS ecosystem: the release of two new, advanced powders and the expansion of SLS capabilities through Formlabs' open ecosystem for the Fuse 1 and Fuse 1+ 30W 3D printers.
The new Nylon 12 White Powder and Nylon 12 Tough Powder are materials that empower Fuse Series customers to expand their in-house capabilities. Nylon 12 White Powder makes advanced post-processing workflows easier than ever, for dyed, painted, and coated photo-ready parts that match your brand’s aesthetic and are ideal for medical applications where color contrast is necessary. Nylon 12 Tough Powder’s high ductility and low refresh rate make rugged, end-use parts more affordable than ever.
In addition to new Formlabs powders, we’re also opening up the SLS ecosystem — Fuse Series customers can now use third-party powders through Open Material Mode and even customize print settings through Print Settings Editor.
Nylon 12 White Powder: Familiar Properties With Expanded Possibilities
SLS 3D printing has been steadily increasing in popularity over the past few years, and there are more Fuse Series SLS 3D printers installed globally than any other powder bed fusion 3D printing technology. The ease of use, scalable footprint, and affordability of the Fuse Series make it an ideal choice for businesses looking to increase functional prototyping capabilities in-house, solve problems on the factory floor with on-demand manufacturing aids, or move to 3D printing for the serial production of end-use parts.
Nylon 12 Powder is Formlabs’ best-selling, multi-purpose SLS material — its strength and dimensional accuracy make it an excellent all-purpose material. For some applications, however, its dark grey color makes it less versatile.
For final-stage approvals in the prototyping process, many businesses need parts that match their brand and design system. Switching from one fabrication technology to another for final stage parts in order to achieve the right color can cost days of lead time or lead to small changes in print results, nullifying the work done for dimensional accuracy and consistency.
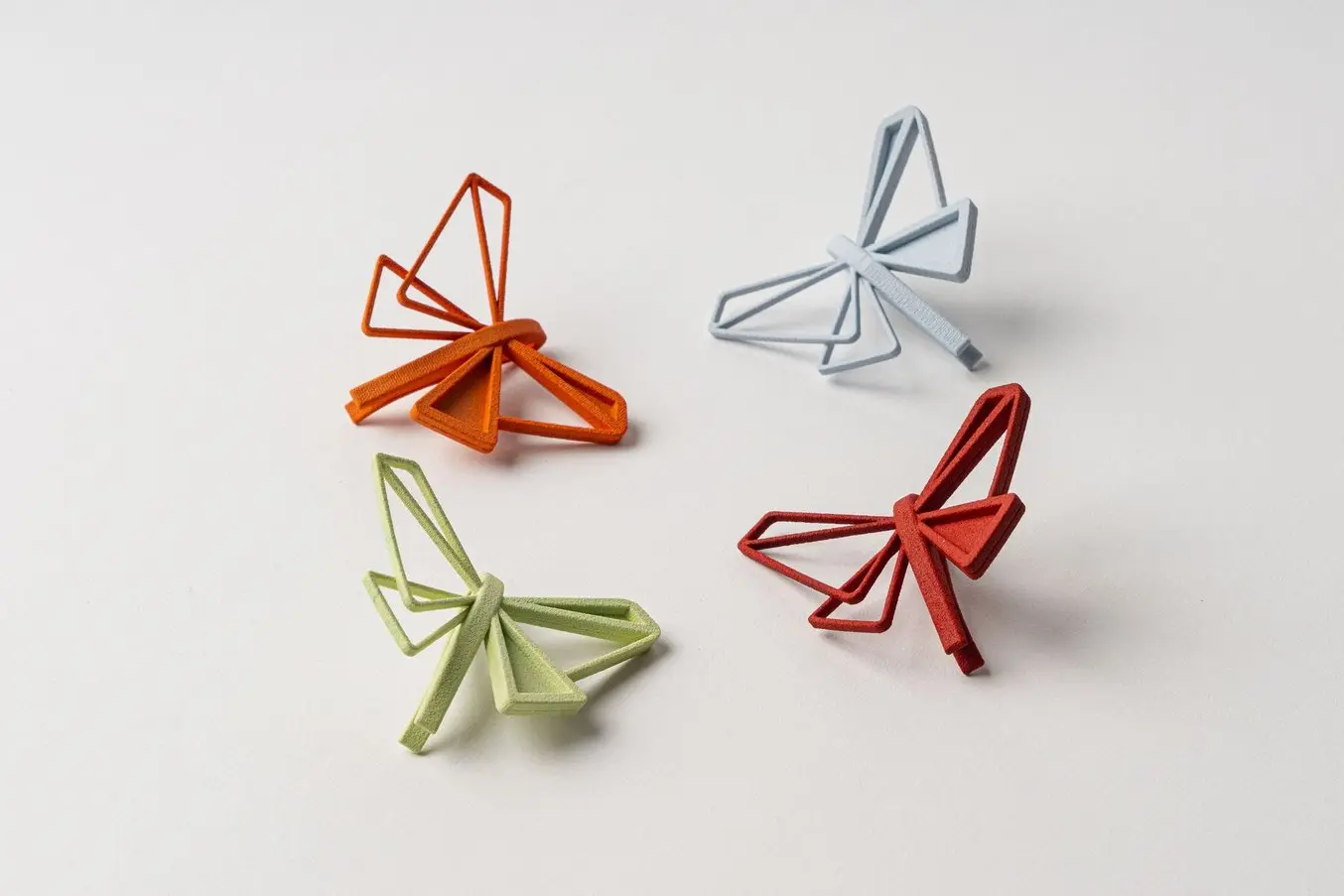
Parts printed on the Fuse Series SLS 3D printers in Nylon 12 White Powder are ideal for painting and dyeing. These four parts demonstrate the color clarity you can achieve with this material through a simple dyeing process.
With Nylon 12 White Powder, customers can leverage the same technology throughout the entire process, from original concept to final part in whichever color makes the most sense. Nylon 12 White Powder is ideal for coating, painting, and dyeing, and allows product designers to rely on consistent material properties throughout. The pure white color ensures that final stage design review products can perfectly match the end-use production runs made through injection molding.
Biocompatibility and Surgical Cutting Guides
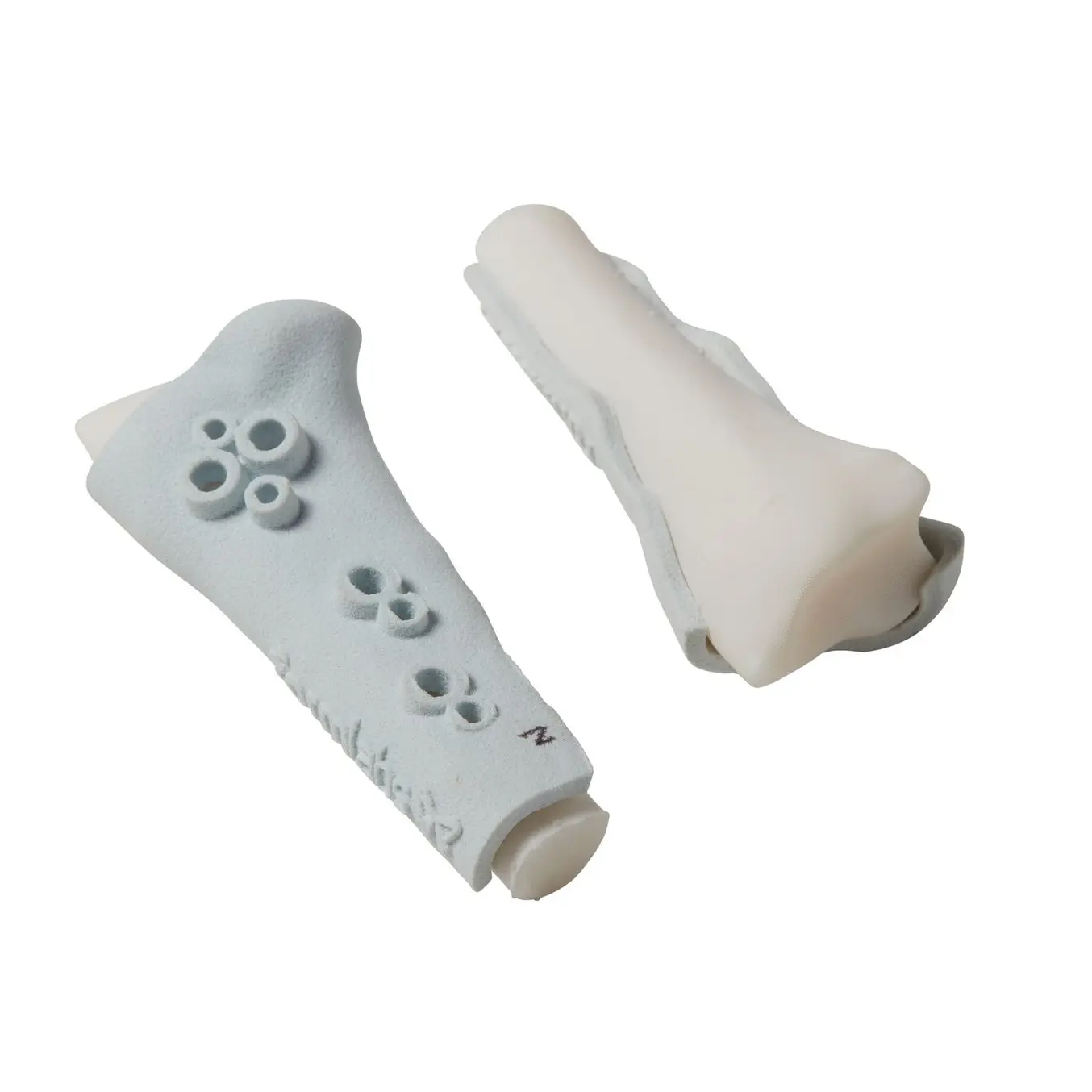
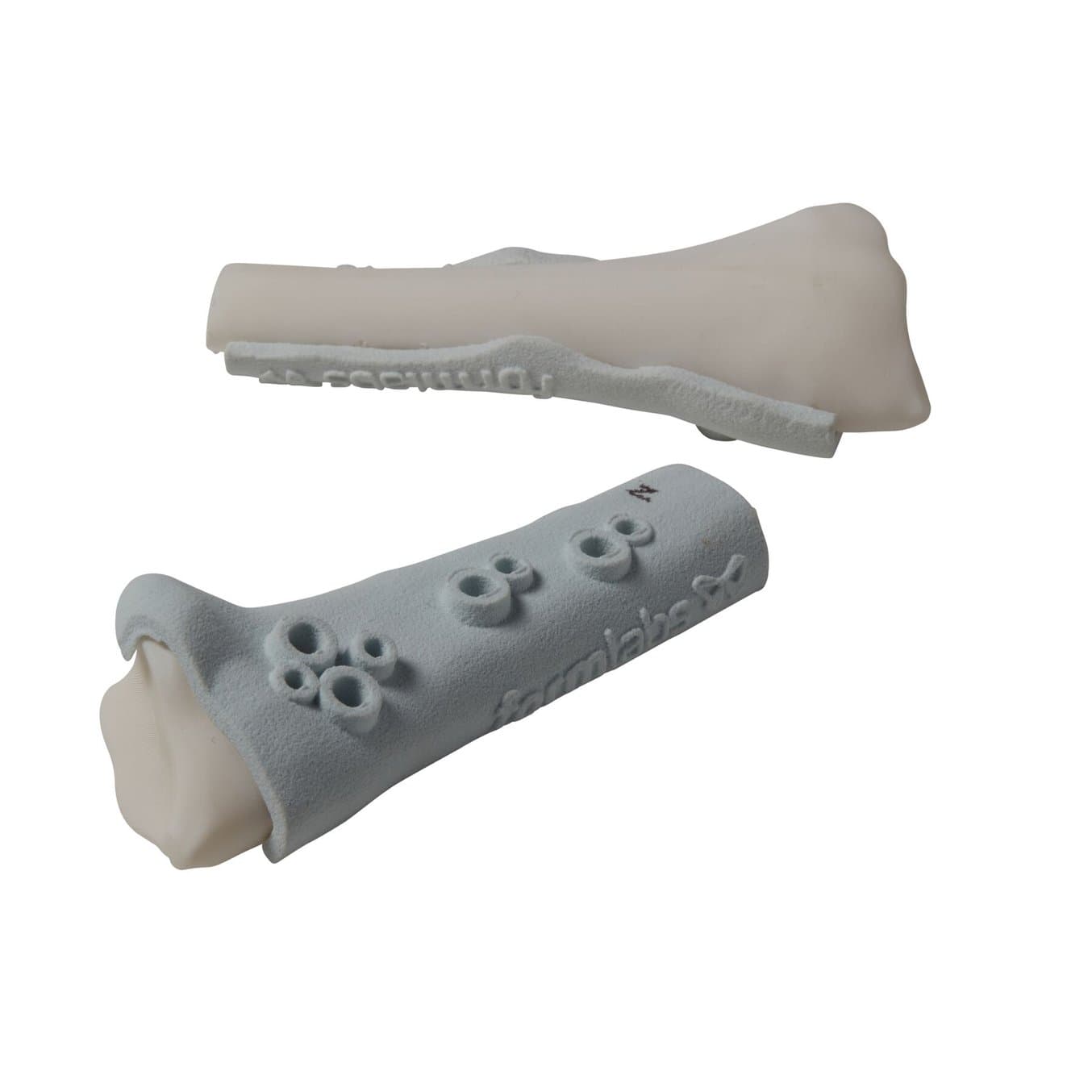
Though Formlabs’ first biocompatible materials were resins for the Form Series stereolithography (SLA) 3D printers, the Fuse Series and Nylon 12 Powder parts have been certified as biocompatible for years, and have been used by medical device manufacturers and point-of-care providers for cutting guides and more. The industry standard for surgical cutting guides is white parts, for the best contrast against human skin and the surgical area.
Nylon 12 White Powder will continue to hold the same biocompatibility standard as the dark grey Nylon 12 Powder, making it an ideal choice for cutting guide manufacturers. Those who may have been wary of bringing SLS 3D printing in-house due to the high prices of traditional machines can now scale up their operation with the Fuse Series while maintaining industry-standard color offerings and material properties.
By matching the biocompatibility standard of Nylon 12 Powder, Nylon 12 White Powder provides an affordable, accessible option for businesses to either expand their offerings into surgical cutting guides or finally bring fabrication in-house.
Biocompatibility certification is ongoing — contact our team to ensure that you have all the certifications you need at your time of purchase.
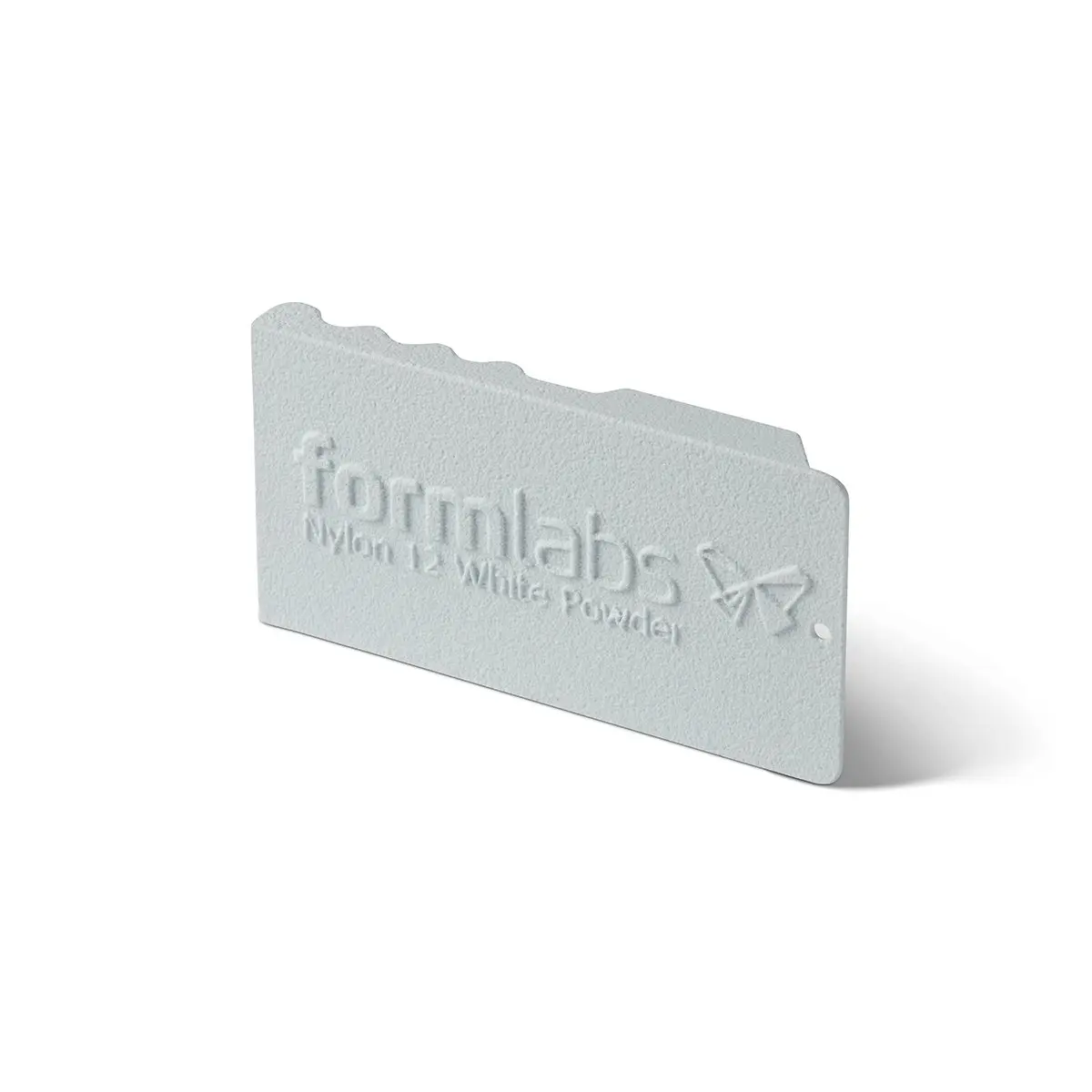
Request a Free SLS Sample Part
See and feel Formlabs quality firsthand. We’ll ship a free Nylon 12 White Powder sample part printed on the Fuse 1+ 30W to your office.
Nylon 12 Tough Powder: Improvement to Accuracy, Affordability, Ductility
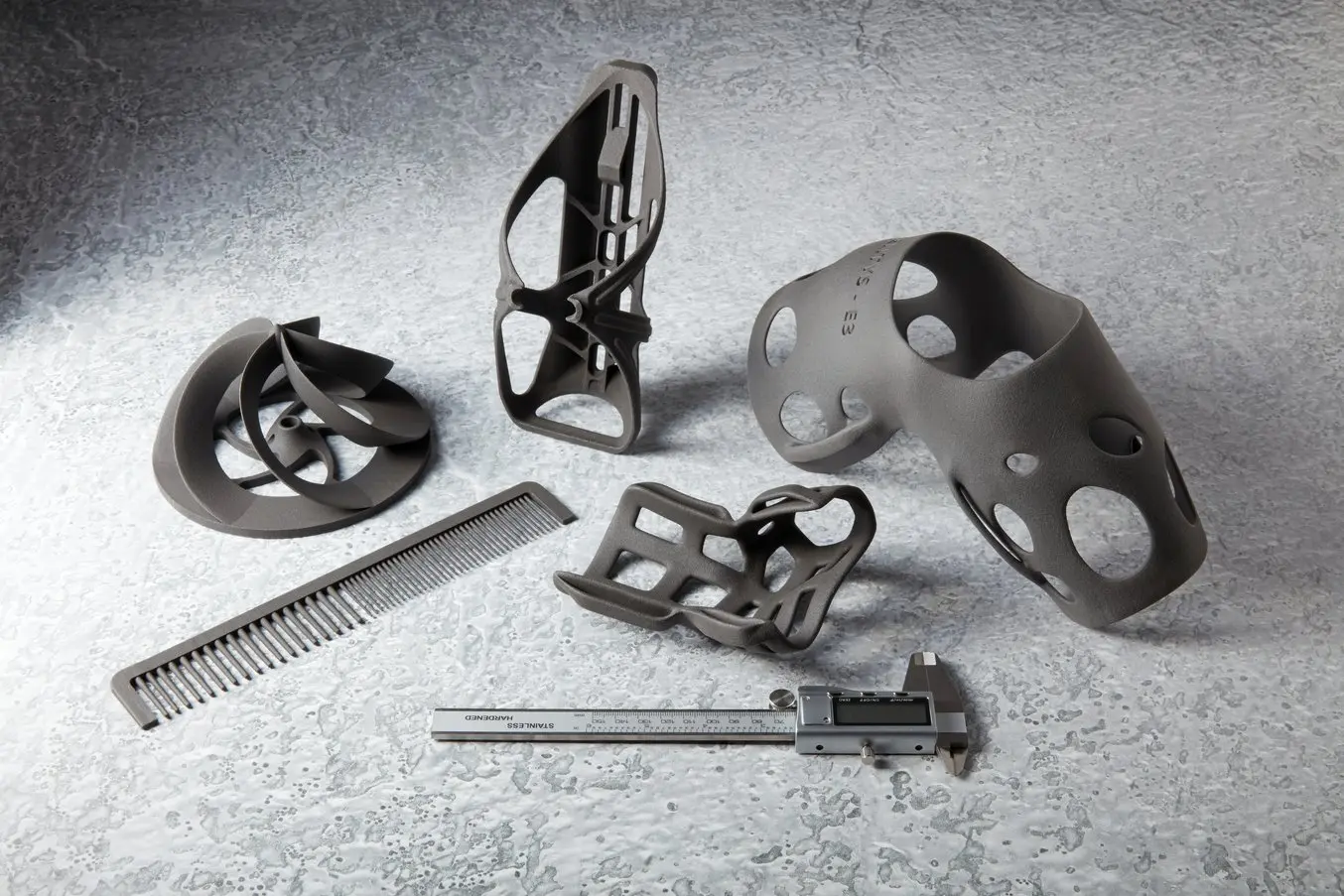
Nylon 12 Tough Powder produces parts for prototyping that have high ductility without compromising on dimensional accuracy.
Nylon 12 Powder has been a workhorse for Formlabs’ Fuse Series customers — it’s the most popular powder by a large margin. Still, we know nothing’s perfect. The high volume of Nylon 12 Powder parts our customers have shared with us has shown us that there’s always room for improvement. In the case of this popular material, dimensional accuracy and ductility could get better. Nylon 12 Tough Powder is our answer to that — with enhanced ductility it can match the mechanical performance of large-format industrial powder 3D printing materials.
At 18.8%, Nylon 12 Tough Powder has a 64% higher elongation at break (EAB) than Nylon 12 Powder in the XY axis. For many years, Fuse users have shared that long, thin parts tend to warp during the sintering process. Nylon 12 Tough Powder’s high EAB works against the factors that create warping and helps long, thin parts maintain their structural integrity.
Nylon 12 Tough Powder’s refresh rate also enables a lower cost per part. The 20% refresh rate makes it easy to use all your unsintered powder from previous prints, so no material goes to waste.
Improved Strength for Every Application
For functional prototyping of all geometries, added strength improves the functional testing process. Customers prototyping climbing equipment, ski and snowboard bindings, consumer products, and more need to rely on one material throughout the process so they can concentrate on design changes and not compensation for changing material properties.
Manufacturing aids and replacement parts on the factory floor need to hold their tolerances for integration into existing machinery and last through multiple cycles without deformation to keep operations running smoothly. Tougher, stronger materials give manufacturers confidence that their machines can keep running.
There are many customers using the current Nylon 12 Powder for end-use applications, like Brose, who prints end-use automotive components for customers like BMW and Mercedes on their three Fuse Series printers. Nylon 12 Tough Powder can help these customers expand their end-use printing with a material capable of withstanding even greater stresses and longer wear.
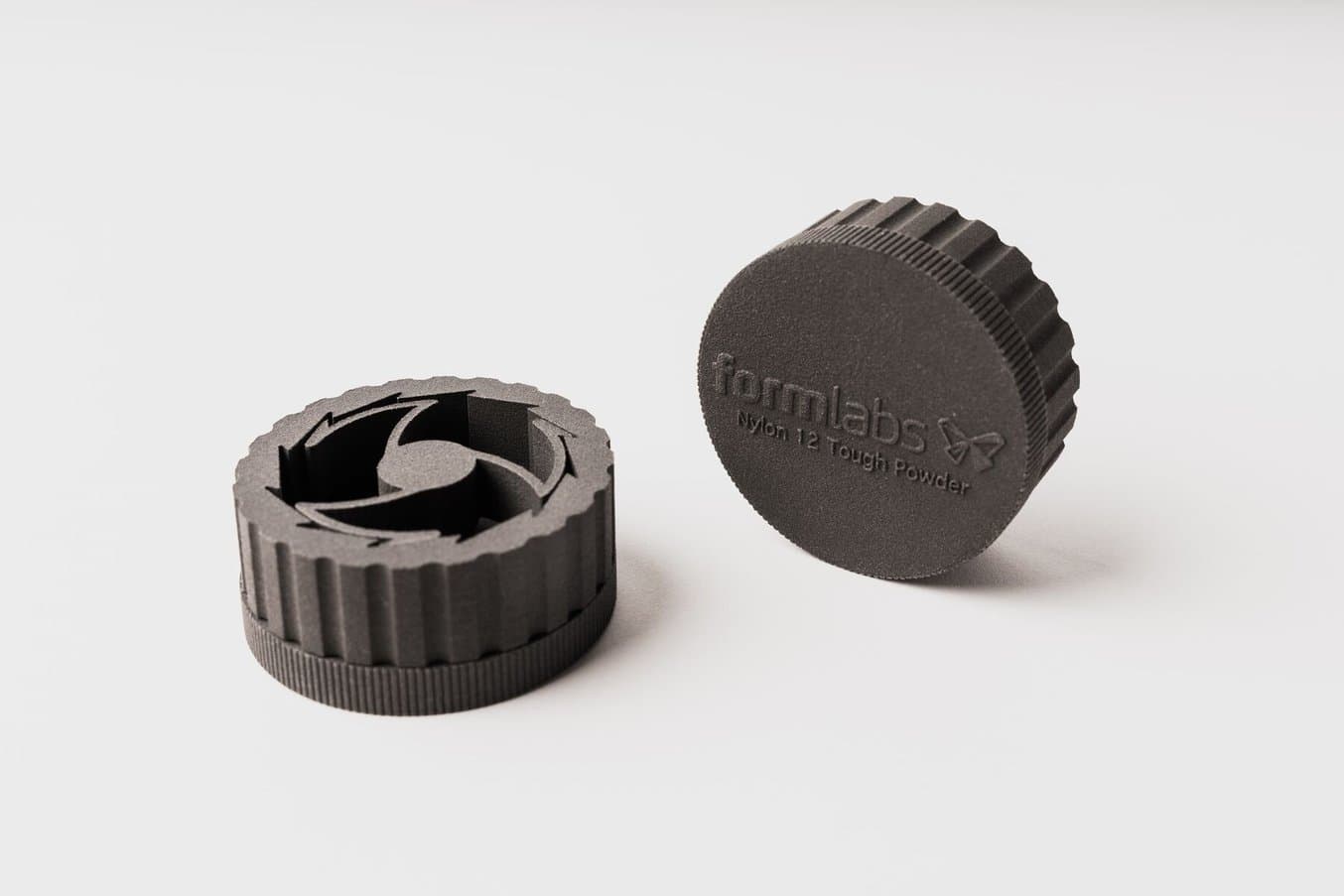
Request a Free SLS Sample Part
See and feel Formlabs quality firsthand. We’ll ship a free Nylon 12 Tough Powder sample part printed on the Fuse 1+ 30W to your office.
Open Ecosystem for the Fuse Series
Formlabs’ Fuse Series was the first truly affordable industrial-quality SLS 3D printer on the market. The powerful Fuse 1 and Fuse 1+ 30W printers allowed small business owners to bring this industrial 3D printing process in-house and allowed larger manufacturers to scale their 3D printing operations without massive overhead costs or infrastructure. Though the Fuse Series is the only truly accessible, reliable, industrial-quality powder bed fusion 3D printer available, we know there’s more that our customers can do. That’s why we’re opening up the Fuse Series and the Formlabs ecosystem.
Open Material Mode for the Fuse Series
Fuse Series customers can pay a one-time licensing fee per printer, and use any 1064 nm powder on their Fuse 1 or Fuse 1+ 30W printer.
Open Material Mode (OMM) gives businesses and innovators a chance to think outside the box (or build chamber) with the security of a proven, high-quality system. Using OMM on Fuse Series printers empowers researchers and innovators to experiment and push the boundaries within a proven system. Because they can rely on consistent parts from the printer, drawing conclusions from results can lead to faster iterative changes to their designs or materials.
For specialized research applications and unique workflows, the ability to use third-party powders opens up new possibilities for production. For workflows that had it all — ideal customer, design, material — and just needed a turnkey, affordable production system, the Fuse Series can produce hundreds of thousands of parts for a lower cost (and faster delivery timeframe) than other available methods.
SLS Print Settings Editor: Customize Your Fuse Workflow for Free
SLS 3D printing, perhaps due to its traditionally higher startup cost and footprint, is typically perceived as more complex than SLA or fused deposition modeling (FDM) 3D printing. The Fuse Series became the global standard for powder 3D printing by turning that conception on its head — it became the first industrial printer to be thought of as ‘plug and play.’ Though we spent years developing the settings that ensure consistency and ease of use, innovators and developers in the SLS industry are ready to do more.
Print Settings Editor allows these experts to start from a set of trusted parameters. From there, they can tweak and adjust parameters like exposure, layer thickness, X, Y, and Z, scaling correction factors, heaters, recoater speed, and more, to tailor their workflows.
The explosion in popularity for SLS happened quickly, and the applications of the Fuse Series are growing every day. A one-size-fits-all approach no longer makes the most sense, and for customers who are moving beyond iterative prototyping, being able to dial their own print processes can be a powerful tool. For production customers who are printing tens of thousands of the same part, changing a single parameter could mean the difference between making or missing a delivery timeline. For a researcher, being able to alter layer thickness could enable a new geometry that supercharges development. Print Settings Editor puts the control in the customers’ hands, without taking away the consistency, reliability, and ease of use that the Fuse Series is known for.
Expansion in the World of SLS
Two new powders and potentially limitless new capabilities for the Fuse Ecosystem usher in a new era of SLS printing. The Fuse Series has been the world’s best-selling SLS ecosystem since it became available. Now, that industrial power and accessibility can be combined with the creativity and innovation in our community. Trying new materials, tweaking your print process, changing what’s available to create something new — these are the ways industries get moved forward. We’re so excited to see where SLS goes next, and we’ll get there together.
To learn more about Fuse, visit our website. To see the quality of Nylon 12 White Powder or Nylon 12 Tough Powder for yourself, request a sample.