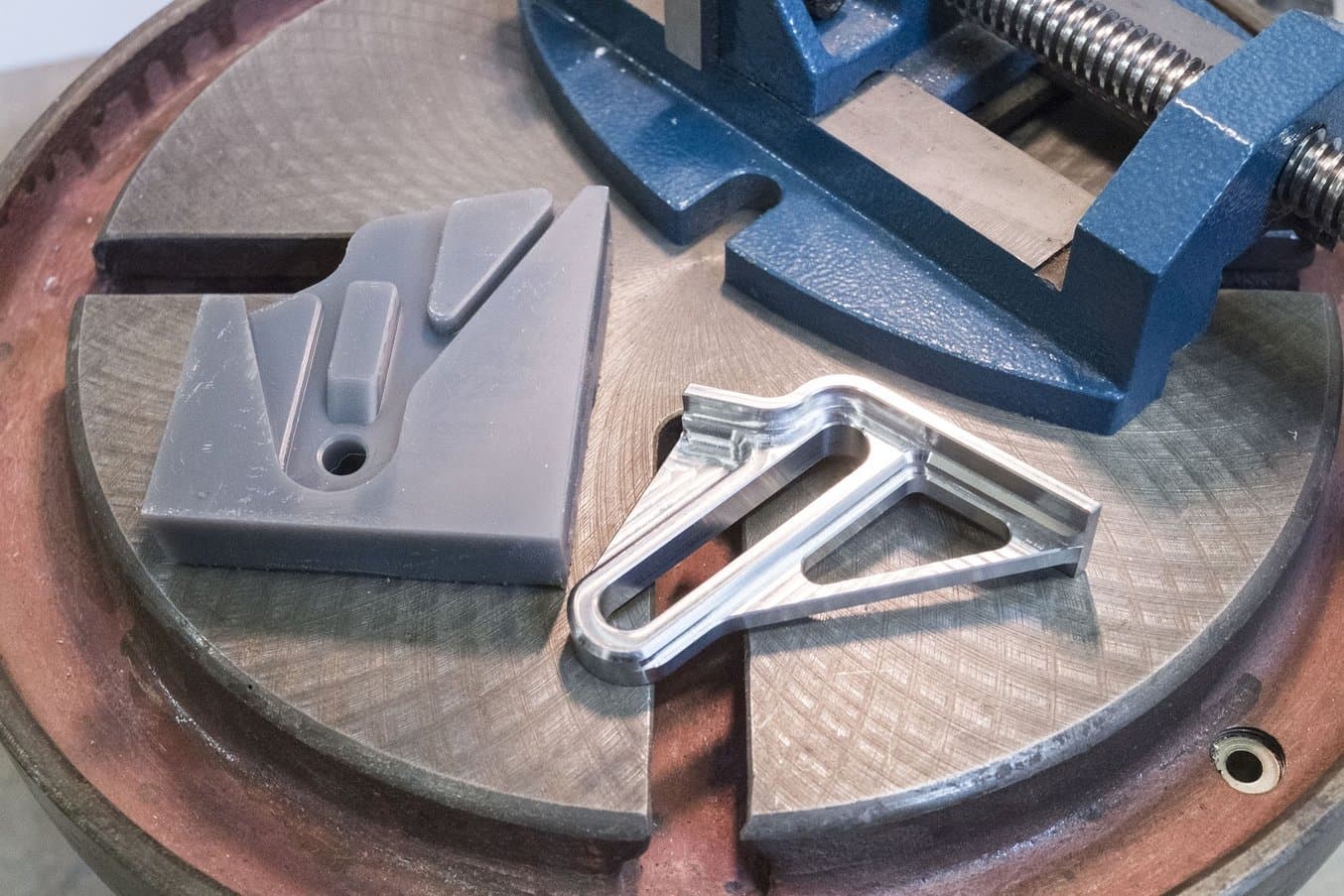
A dropout drilling fixture printed in Draft Resin
In 2019 Formlabs introduced Draft Resin with the goal of creating a material accurate enough to meet prototyping needs while enabling faster design iterations. Since we launched this material, our users wasted no time incorporating it into their product design processes.
From fast print initiation speeds to minimal support removal, wash, and cure times, Draft Resin has an optimized workflow to truly maximize efficiency.
Draft Resin is ideal for:
- Initial prototypes
- Same-day design iterations
- Live 3D printing demos
- High-throughput applications
- Quickly printing large parts
This past October, we launched a new formulation of Draft Resin that boasts a faster print time and improved surface finish. We recently followed up with Albatross Bikes Founder Will Hilgenberg, a user of the original Draft Resin, to hear what he thinks of the reformulated Draft Resin and how his team are incorporating it into their workflows to quickly create engineering samples.
Albatross Bikes Tests Draft Resin V2
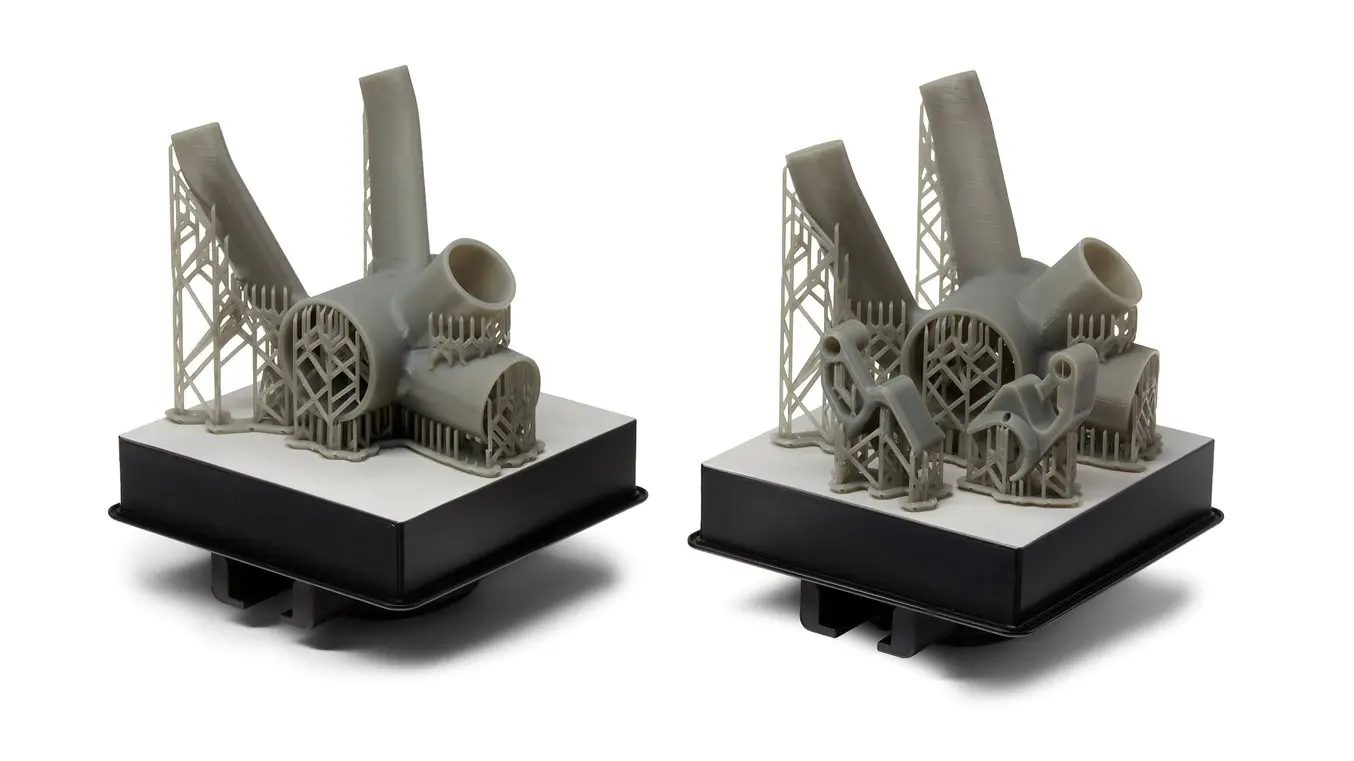
Draft Resin has been updated to improve support removal.
Although they had success with the first version of Draft Resin released last year, Albatross Bikes was looking for Draft Resin to do even more.
Their wish list was comprised of:
- More printing options other than 300 microns.
- Easier to remove supports.
- Eliminate the distinct odor that came with Draft Resin.
- A new color that better matched engineering prototypes.
Offered in a new grey color to better match most engineering prototypes, reformulated Draft Resin supports both 200 and 100 micron settings compared to Draft Resin V1, which only printed at 300 microns. Higher resolutions settings reduce the impact curves and odd edges will have on prototyped parts, which could get in the way if a user wants a high resolution looks-like final prototype. Best of all, Draft Resin V2 prints at 200 microns in a comparable speed to Draft Resin V1 at 300 microns, making this new reformulation by far the fastest printing 200 micron resin available for an SLA printer.
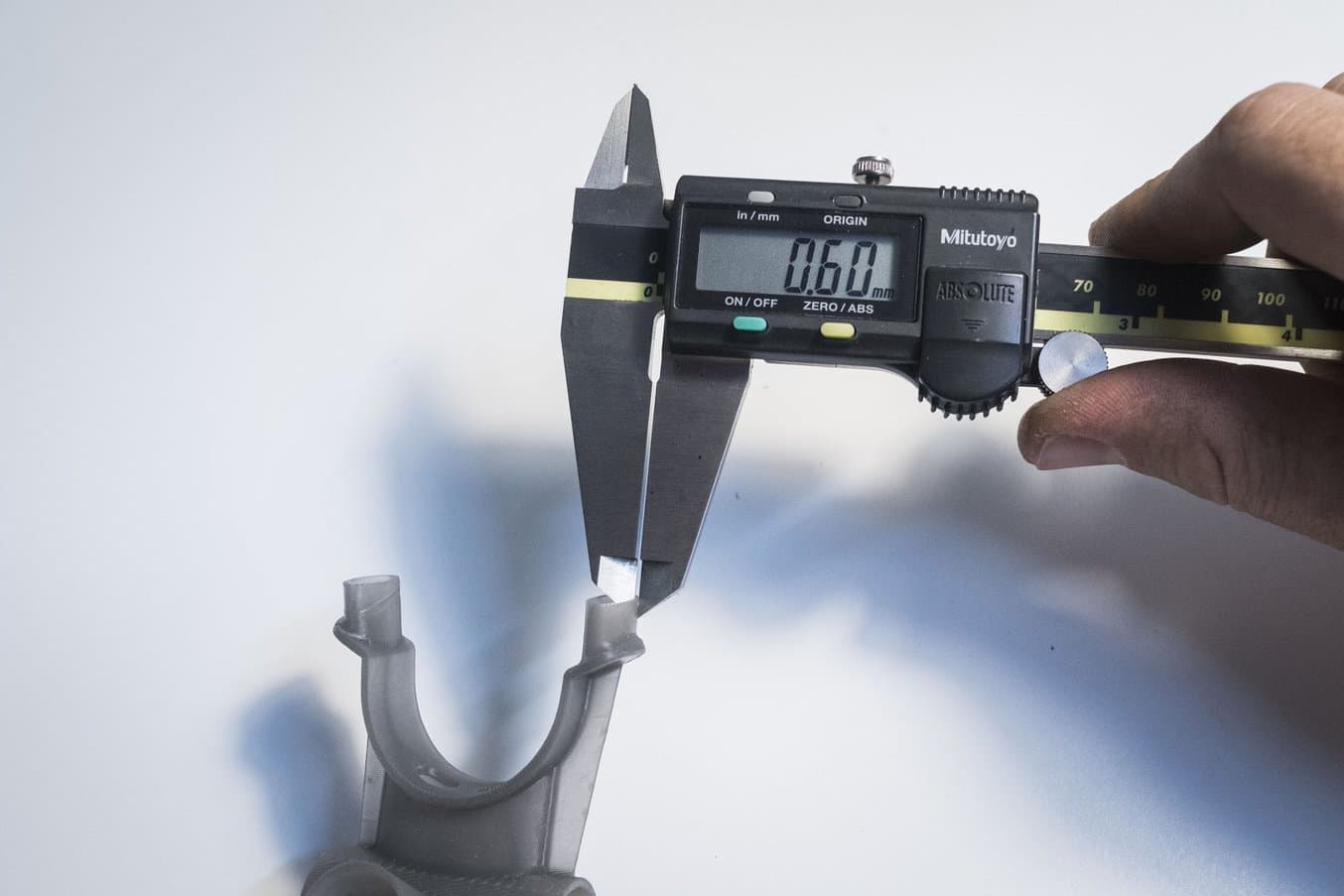
“The thinnest walls that we were able to consistently produce with Draft Resin V2 were down to 0.6 mm in thickness for some relatively well supported sections of the model. This is in contrast to Draft Resin V1 where we were only confident in being able to print down to 1 mm wall thicknesses to preserve the dimensional quality of the models we were printing.”
Will Hilgenberg
Due to its thick layer lines, 3D printed parts created by Draft Resin V1 could be difficult to remove from supports. This would require careful placement of the prints on the build platform, extra time spent in PreForm tweaking part orientation, and additional post-processing time to sand down rough touch points. With improved resolution options available on Draft Resin, Albatross Bikes were able to spend less time finicking with their files and prints, and more time printing without worrying about difficult post processing. According to Will, “We were able to scale prints down without modifying the wall thicknesses to allow for printing.”
One complaint unique to Draft Resin was that some people could detect a foul odor emanating from the uncured resin. While not a universal observation, Albatross Bikes had to move their 3D printer to another location in the office to print in Draft Resin V1. With Draft Resin V2, that odor has been completely eliminated.
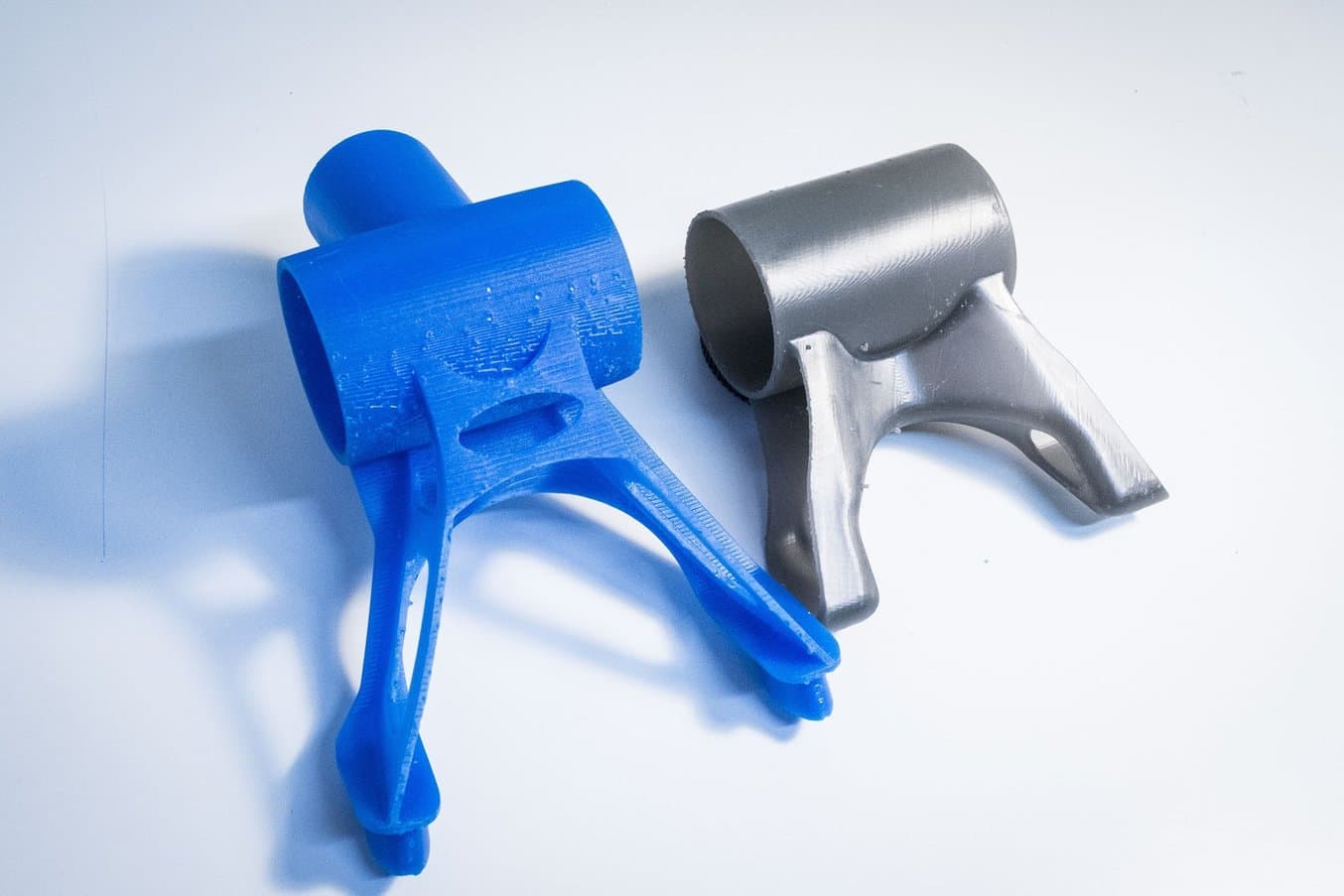
Draft V1 vs Draft V2 color difference
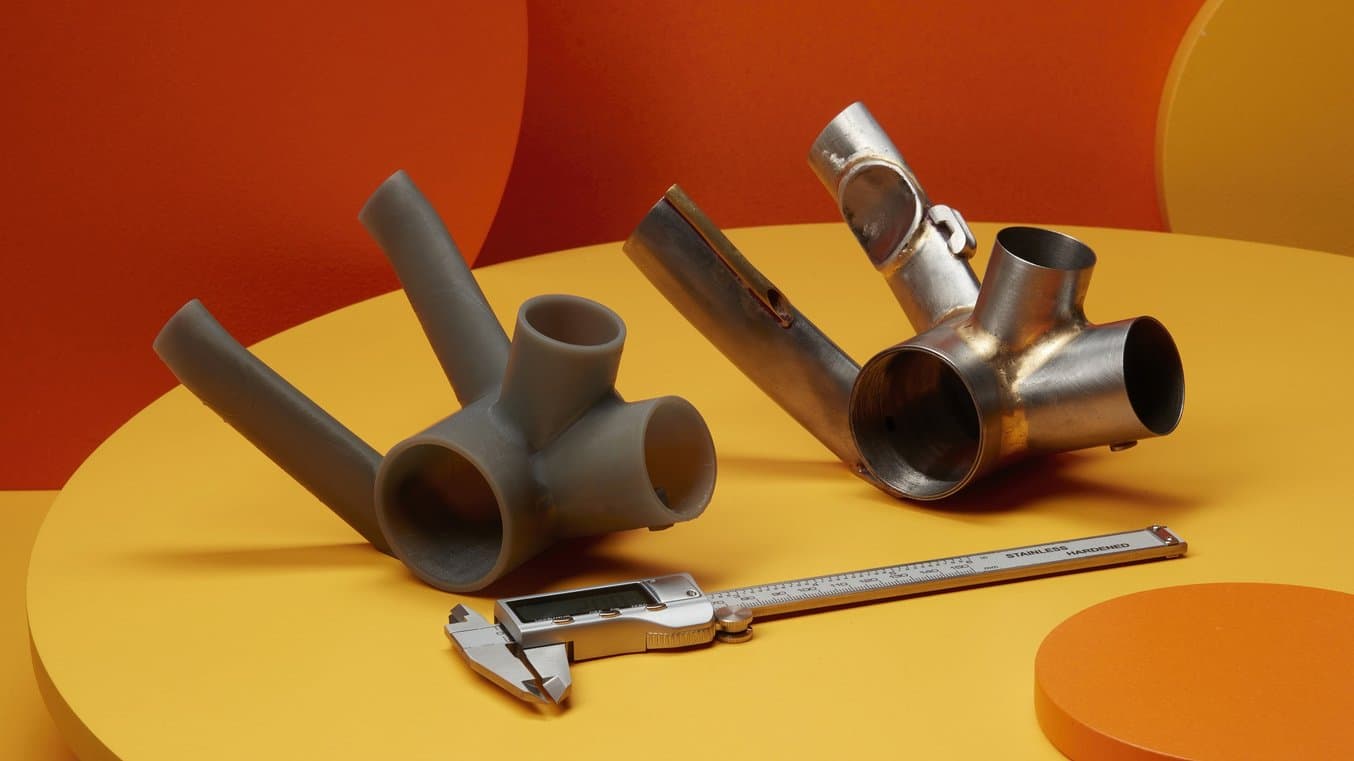
Draft Resin and its metal counterpart
Advice for Engineers Using Draft Resin
“Draft Resin is a product that has seen use at our company. It fit the niche between FDM and SLA.”
Will Hilgenberg
Today, engineers and designers often turn to fused filament modeling (FDM) machines for initial concept prototyping, and use stereolithography (SLA) machines for higher fidelity models. Now, you can use Draft Resin for early prototypes and switch to Standard or Engineering Resins for detailed, functional models - all on the same machine. With Draft Resin, SLA is the fastest technology for printing quick prototypes, up to 10x faster than similarly sized parts on an FDM printer.
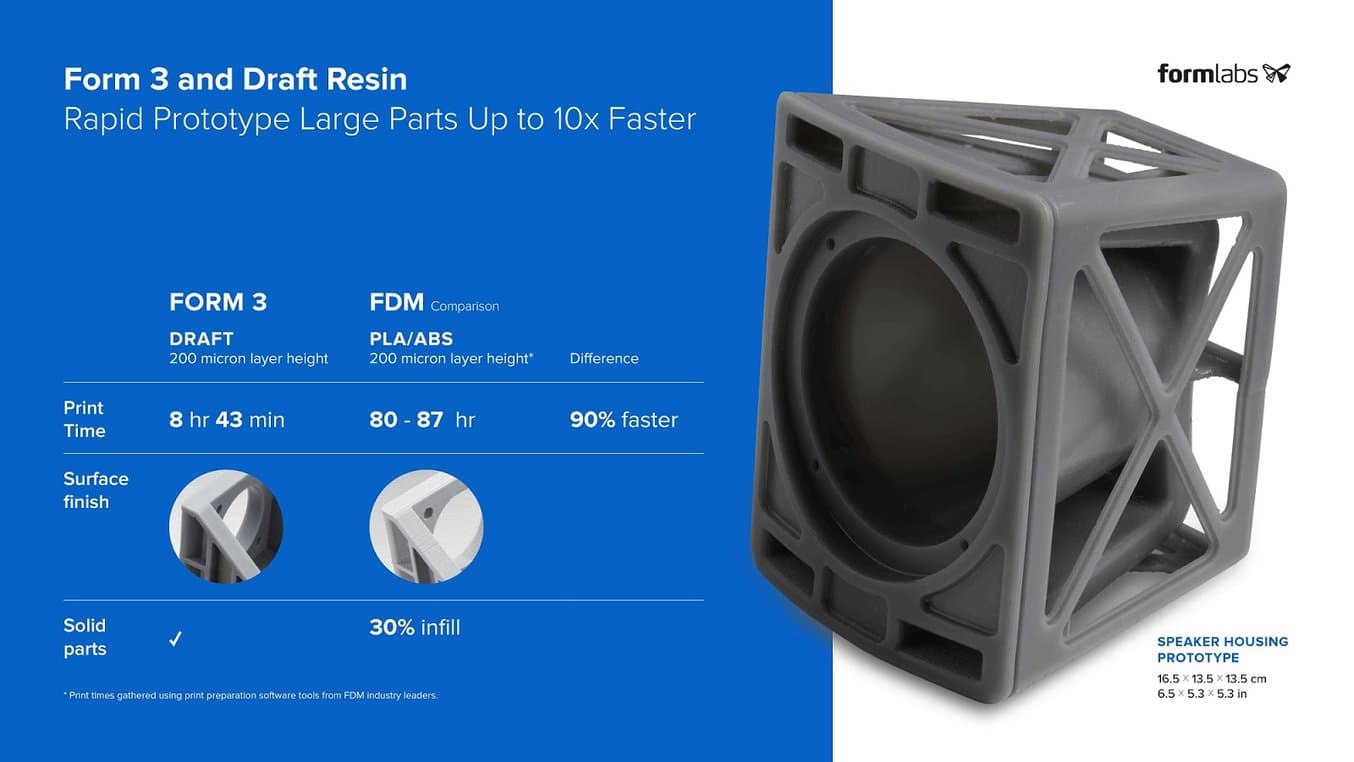
A large speaker prototype printed with Draft Resin
“This resin does an excellent job of not replacing FDM printing but rather bridging the gap between traditional FDM and SLA printing technology.”
Will Hilgenberg
If an engineer wants to create a new jig prototype, speed can vary based on the size and complexity of the part. For a standard sized jig, printing on the Form 3 or Form 2 can take approximately five hours. Draft Resin can finish the same part in 1 hour and 20 minutes, a 73% speed improvement. This means less time printing and more time to iterate on product designs to create better products.
Test Draft Resin V2 For Yourself
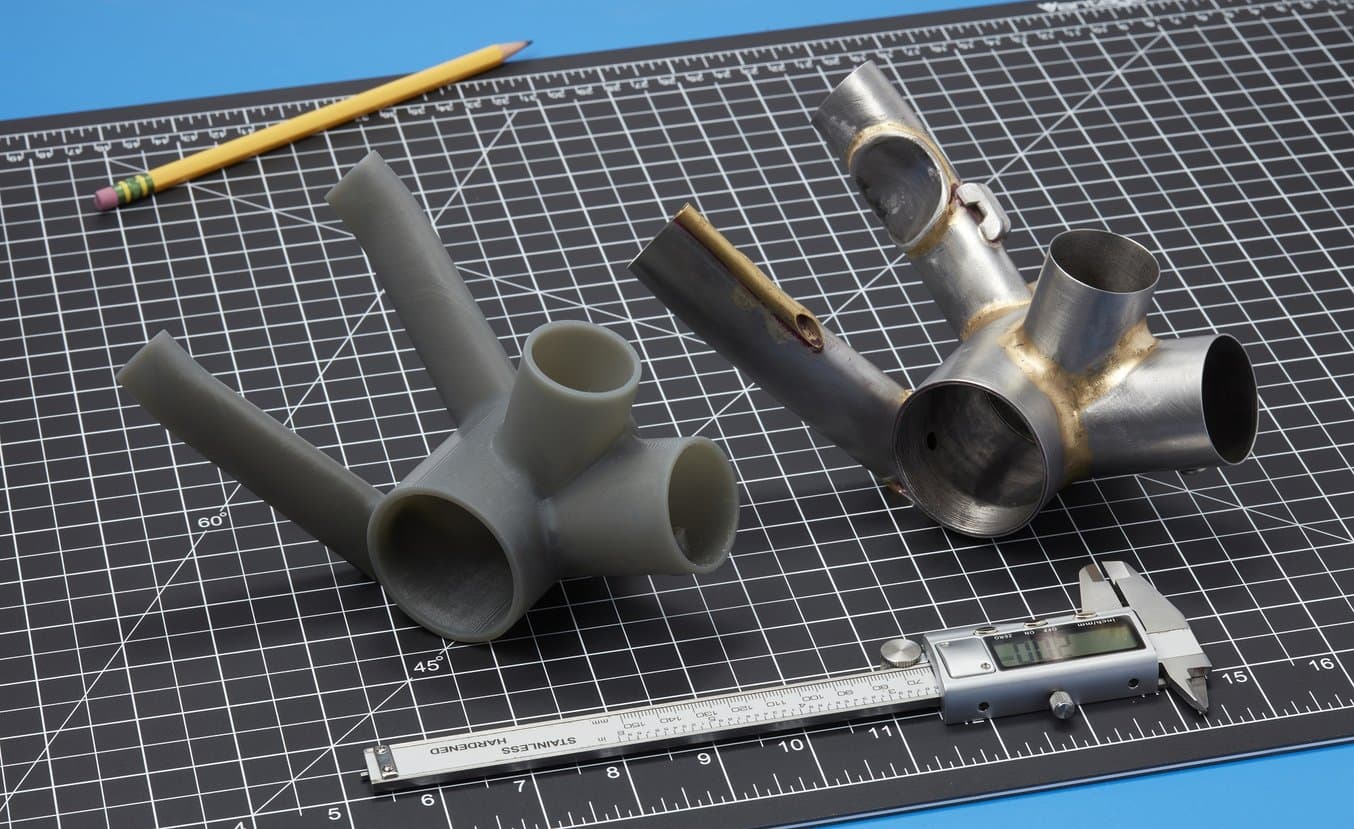
Draft Resin and its metal counterpart
To recap, our reformulated Draft Resin offers:
- Improved surface finish: the newest formulation prints at both 200 and 100 micron layers, compared to 300 microns for the previous version, while maintaining the same fast speed.
- More professional appearance: the newest formulation offers a new grey appearance for professional looking presentation models.
- Easier to use: the newest formulation takes advantage of Formlabs LFS technology to reduce support touchpoints and minimize Form Wash and Form Cure times.
These upgrades make rapid prototyping with Formlabs SLA 3D printers easier and better than ever before.
If you have any exciting use cases of Draft Resin, let us know on social media by tagging @Formlabs in your posts!