Formlabs is happy to announce that the Fuse 1 selective laser sintering (SLS) printer has begun shipping to customers, with over 60 pre-order and reservation printers already in the field and printing.
After concluding several months of rigorous beta testing with a host of innovative companies, our totally re-designed SLS 3D printer is ready to deliver industrial grade nylon parts, right on your workbench. Delivering production ready nylon at a low cost per part, a large build chamber to accommodate various project sizes, and the ability to print 24/7, no other SLS printer offers the quality and ease of use as the Fuse 1.
Formlabs has also begun to ship the Fuse Sift, an all-in-one powder recovery station for the Fuse 1. The Fuse Sift was created to flawlessly integrate into your SLS workflow and deliver a seamless, simple post-processing setup.
SLS 3D printing has long been the domain of expensive, high-end industrial printers, often times putting them out of reach for most business and product designers. Our goal with the Fuse 1 is to deliver the industrial power of SLS into your workshop with an affordable, compact system for production-ready nylon parts.
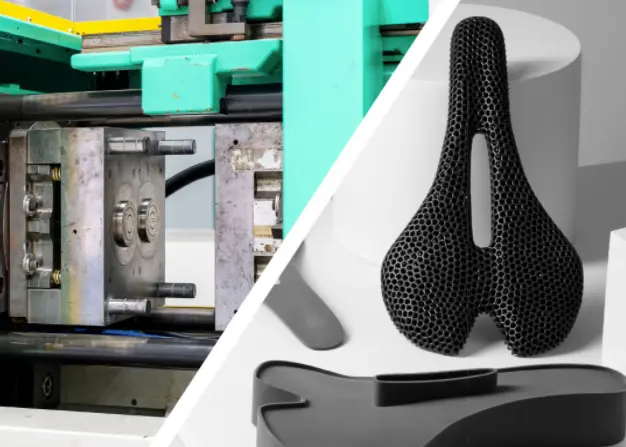
SLS 3D Printing vs. Injection Molding: When to Replace Molded Parts With 3D Printing?
This white paper showcases the cost-dynamics for real-life use cases, and presents guidelines for using SLS 3D printing, injection molding, or both.
Affordable SLS Printing On Your Workbench
The Fuse 1 offers a number of benefits typically found in industrial level SLS printers costing four times as much:
- Low material costs. With an expansive build chamber and the ability to reuse nylon powder, the Fuse 1 offers industrial quality SLS 3D printing for a low cost per part.
- High productivity and throughput. SLS printing is the fastest additive manufacturing technology for functional, durable prototypes and end-use parts. Many parts can be tightly arranged during printing to maximize the available build space. Create hundreds of parts with each print cycle and keep your machine running 24/7 with multiple build chambers.
- Design freedom. With no need for support structures, SLS 3D printing allows for the creation of intricate geometries, interlocking parts, interior channels, and other complex designs.
- Proven, end-use materials. Nylon and its composites are proven, high-quality thermoplastics with mechanical properties comparable to those created with conventional manufacturing methods like injection molding.
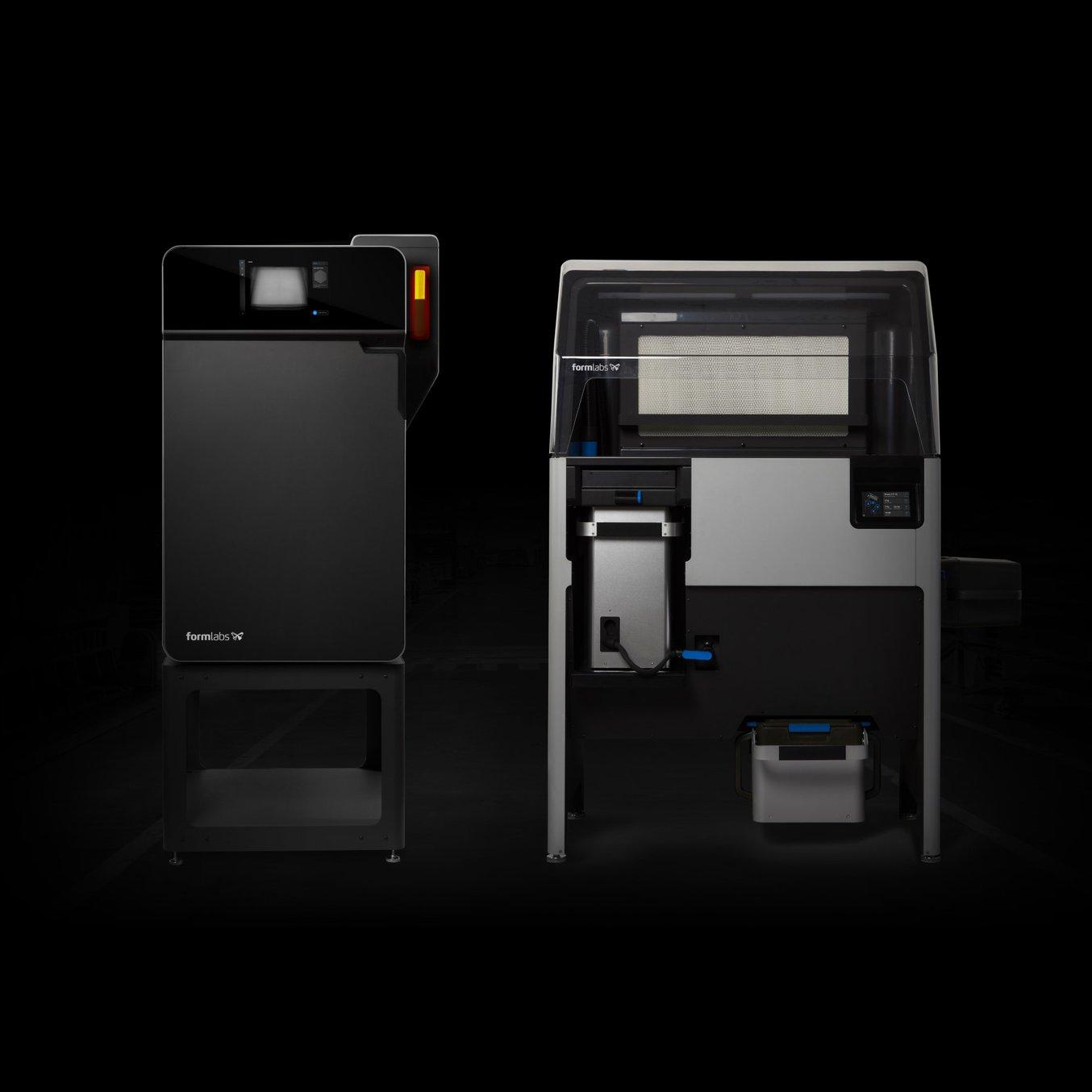
Fuse 1 & Sift Virtual Tour
Experience the Fuse 1 & Fuse Sift firsthand with an interactive walkthrough.
These benefits are exemplified by user Partial Hand Solutions. According to Partial Hand Solutions Founder Matthew Mikosz, “I’ve always wanted an SLS printer, but they are unattainable at their current price points. The Fuse 1 is perfect for small businesses like Partial Hand Solutions.” Matthew was able to create affordable end-use medical prosthetics in-house for the first time. Most importantly, Matthew feels that “using the Fuse 1 has expanded my horizons when it comes to future design work.”
A Material That Does It All
The real power of the Fuse 1 comes from its ability to print resilient, ready-to-use nylon parts. Balancing strength, flexibility, and detail, Nylon 12 Powder is a highly capable material for both functional prototyping and end-use production of complex assemblies and durable parts with high environmental stability. Our Nylon 12 Powder is specifically developed for use on the Fuse 1.
Nylon 12 Powder is ideal for:
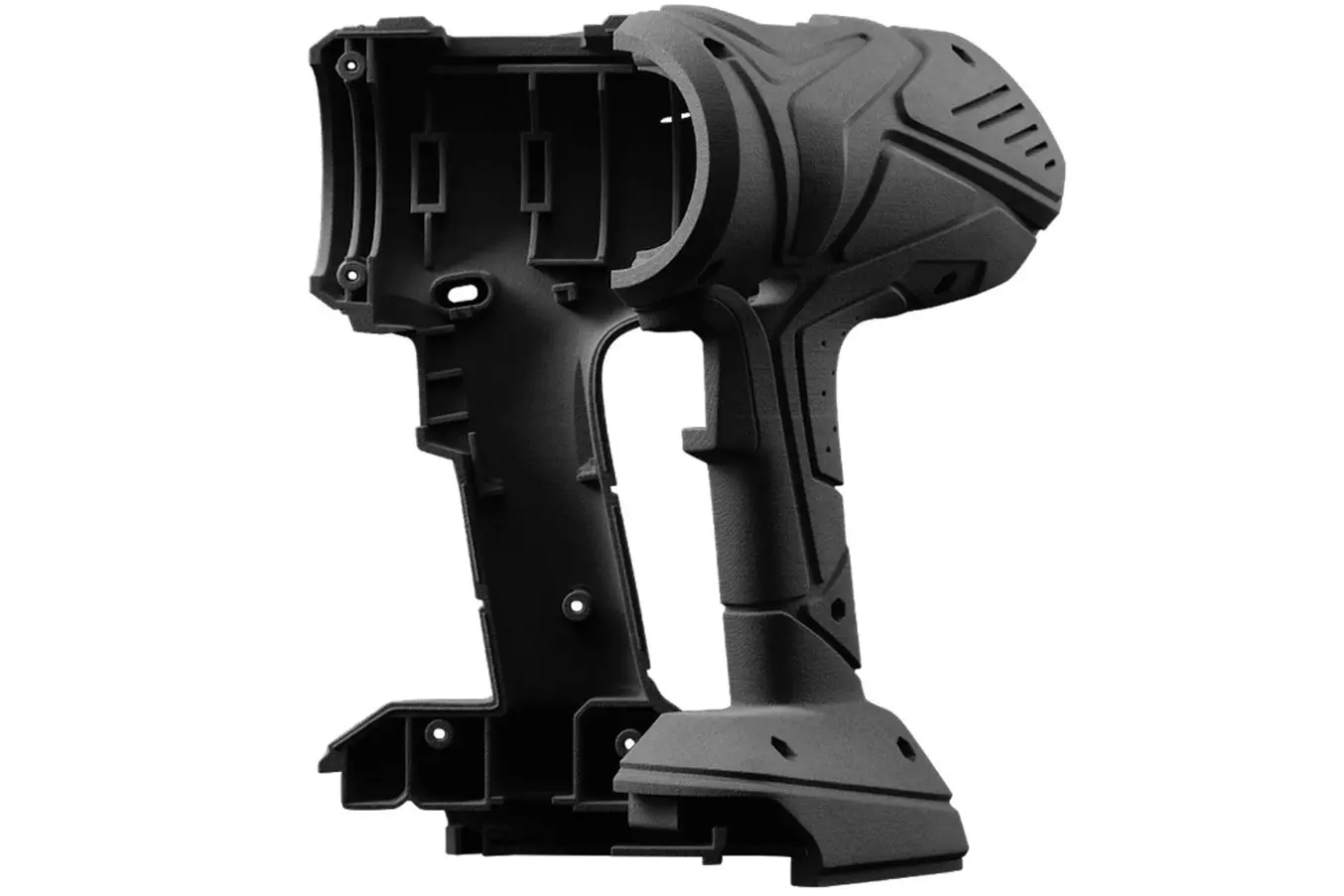
Engineering
Take control of your entire product development process, from iterating on your first concept design to manufacturing ready-to-use products:
- Rapid prototyping
- Mockups of products for in-field customer feedback
- Functional prototyping
- Rigorous functional testing of products (e.g: ductwork, brackets)
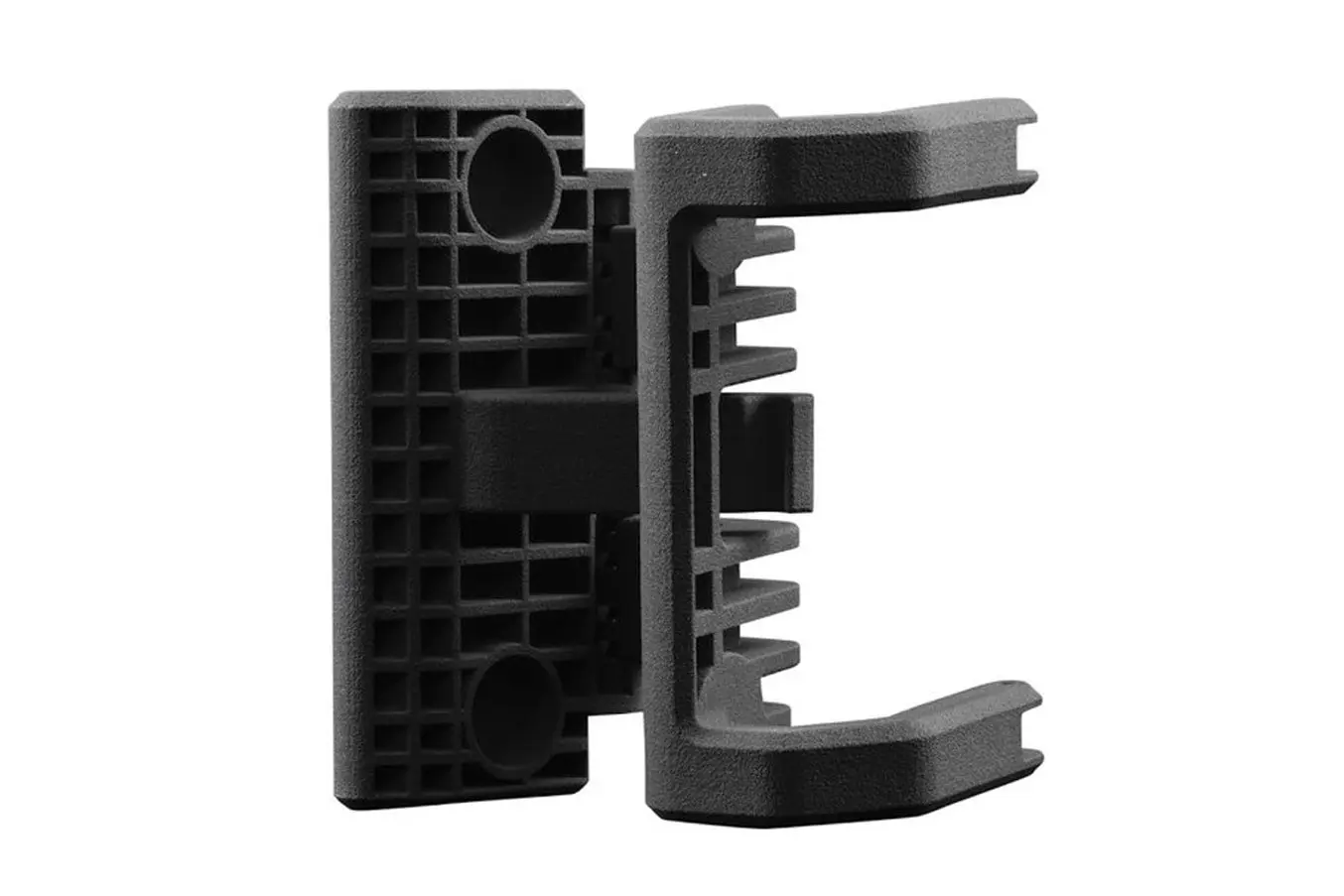
Manufacturing
Own your supply chain and respond quickly to changing demands:
- End-use production
- Small batch manufacturing
- Production of novel mass customization consumer products
- Replacement part production, supply chain robustness
- Long-lasting, durable jigs and fixtures (e.g clips and clamps) and tooling
- Custom automotive or motorcycle parts, marine equipment, military ‘resupply on demand’
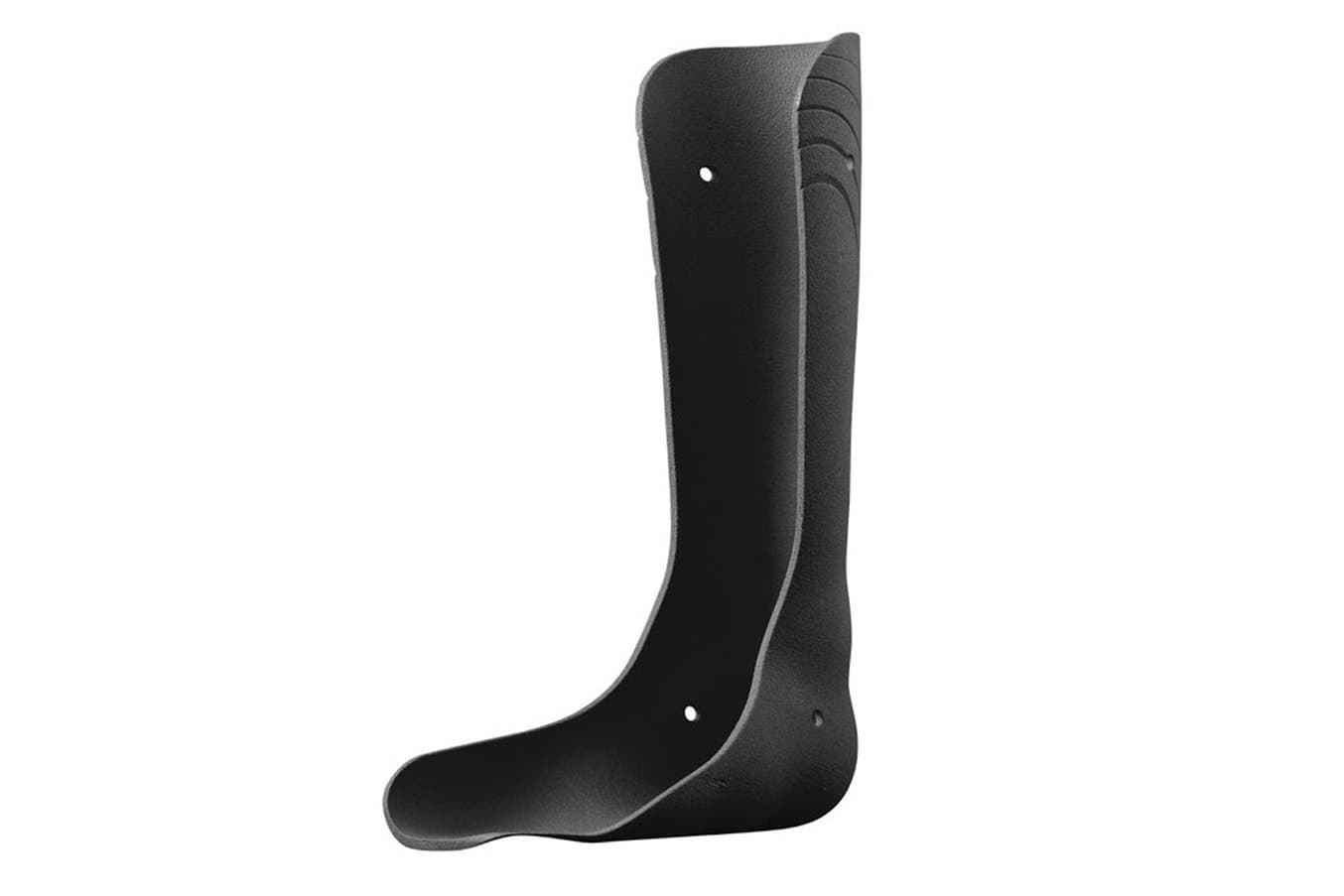
Healthcare
Manufacture ready-to-use, patient-specific medical devices in-house:
- Medical device prototyping
- Prosthetics and orthotics (i.e. limb replacements + braces)
- Surgical models + tools
- End-use parts (nylon 12 is biocompatible + compatible with sterilization)
Tessy Plastics is a contract manufacturer for custom plastic injection molded products for both the medical and consumer industries. Tessy Plastics Research and Development Engineer Brian Anderson has been using the Fuse 1 on his shop floor to find creative solutions to the array of problems that appear at their shop, from broken machines to the creation of custom fittings and tooling.
The material properties of Nylon 12 Powder were incredibly important to Brian and his team when considering deployment of the Fuse 1. “The first thing our team did was try and break the nylon parts. They’re strong!”. The team went on to create dozens of end-use parts including a custom pulley system to address a last minute customer request. “The custom pulleys printed last week are working well in production as functional parts. They have very delicate splines on the inside of the vacuum tooling that are holding up well unscrewing molded parts from the core.”
SLS Post-Processing Made Easy
“The Fuse 1 and Fuse Sift work incredibly well together and it’s exactly what I would expect from this caliber tool.”
Partial Hand Solutions Founder Matthew Mikosz
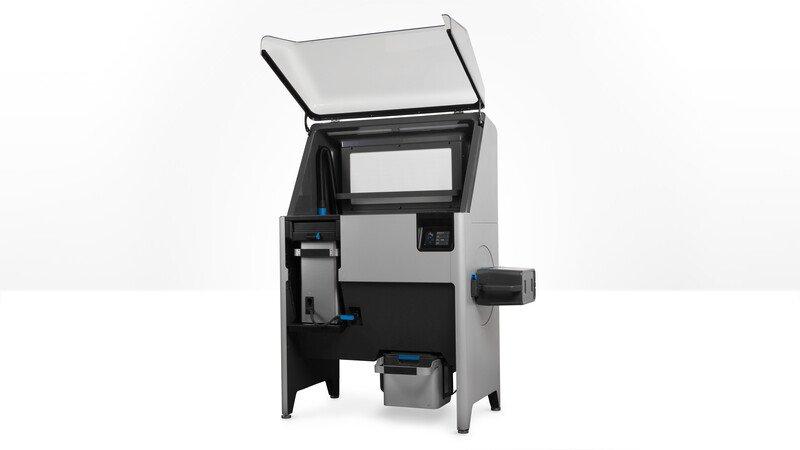
The Fuse Sift was created to invoke a word most people do not associate with SLS post-processing: intuitive. An all-in-one powder recovery station, the Fuse Sift combines part extraction, powder recovery, storage, and mixing in a single free-standing device. Highly convenient and compact, this is the most functionality you'll get in a single device on the SLS market.
In the Fuse 1 workflow, a single device, Fuse Sift, handles the extraction of parts and unsintered powder, as well as storing, dosing, and mixing of streams. The Fuse Sift will also help you recycle powder, making your workflow more efficient and reducing costs. The Fuse 1 operates with a 30% material refresh rate, meaning you can print with up to 70% recycled powder, indefinitely. Fuse Sift can dispense and mix used and new powder automatically so you can reduce waste and control your powder supply.
Get Started With the Fuse 1
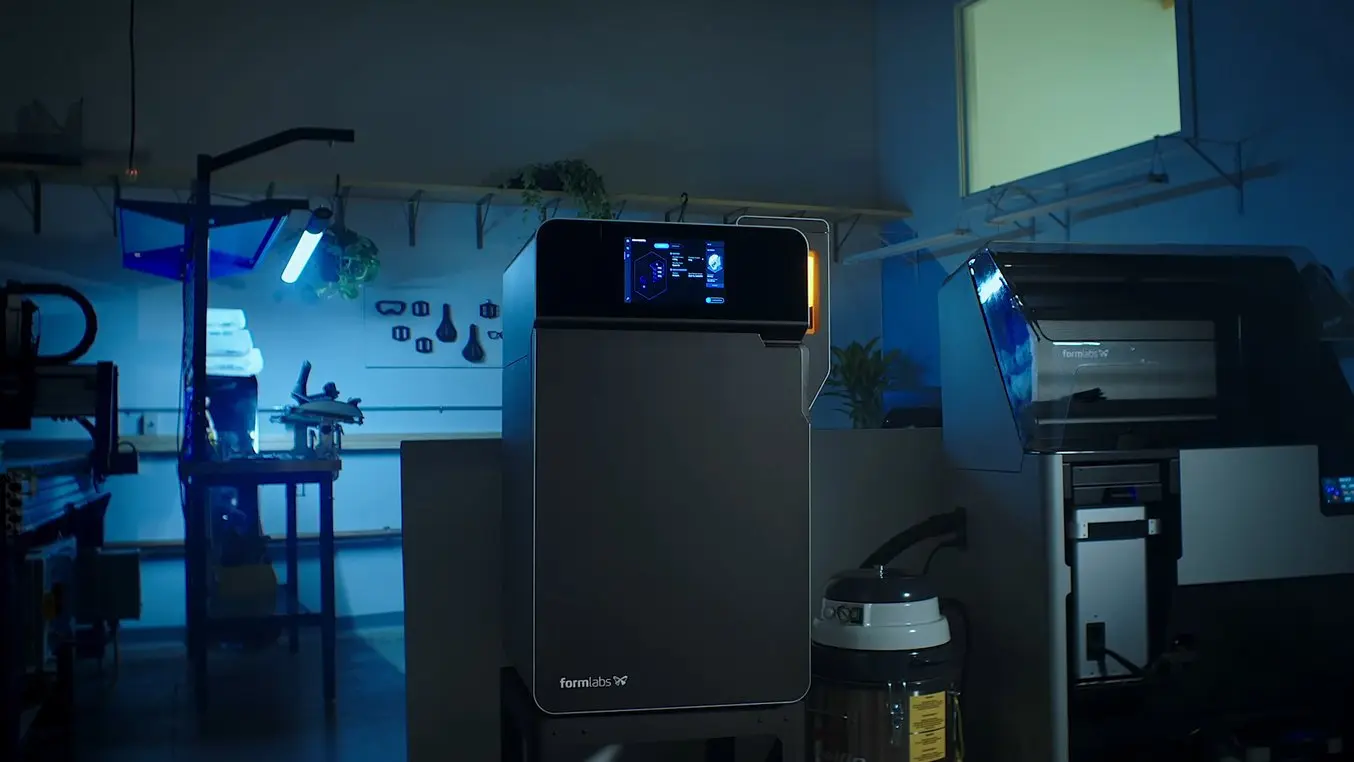
Formlabs is known for designing additive workflows that make industrial-quality 3D printing manageable for businesses of any size. The Fuse 1 and Fuse Sift empower businesses to take control of the design process, print production-ready nylon parts in-house, increase throughput, and bring industrial level SLS 3D printing to the benchtop at a truly entry-level price point. Contact a Formlabs 3D printing specialist to learn how SLS 3D printing could enhance your throughput and productivity.