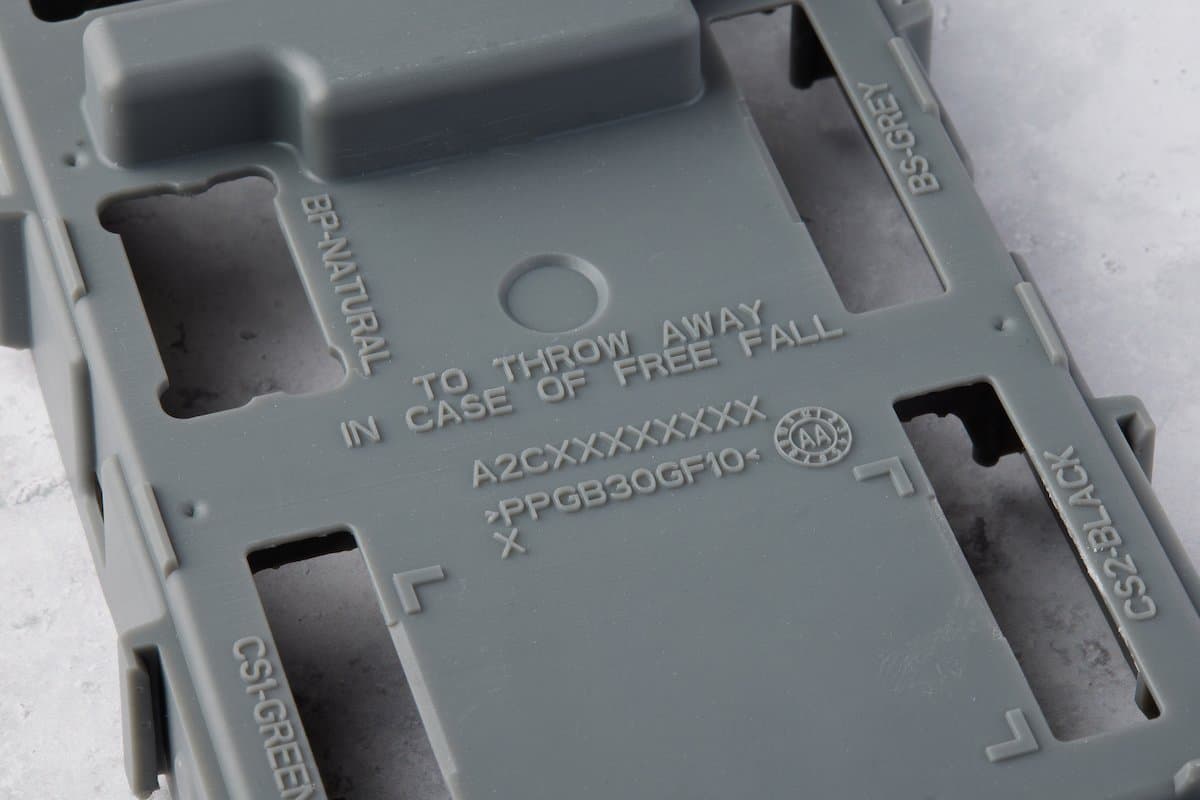
3D printing resolution is a constantly discussed but commonly misunderstood topic. The variety of 3D printing technologies and the growing number of manufacturers have complicated the matter further. The introduction of masked stereolithography (MSLA) 3D printers, which use an LCD screen to selectively mask light in order to cure only the intended regions of the exposed liquid resin, adds an additional layer to the resolution debate. MSLA 3D printers are becoming very popular for their ability to rapidly print high quality parts.
The resolution of LCD screens is typically measured by the number of pixels they have across their long axis — a metric the public is familiar with through the common use of digital screens in phones, televisions, and tablets. They combine emphasis on pixel count with emphasis on individual pixel size — saying that the smaller the pixel, the higher the resolution.
However, despite this focus on pixel count or individual pixel size, what most 3D printing users care about are the tangible outcomes of a 3D print: surface finish, dimensional accuracy, and minimum feature size. Though pixel size is one element of creating these outcomes, they are dependent on a whole host of factors like material properties, optical settings, mechanical consistency, and more.
By printing and analyzing several parts from Form 4 (desktop MSLA, 50 µm pixel size, 10” 4K screen), Form 3+ (laser-powered SLA with 85 µm spot size), Printer C (desktop MSLA, 28 µm pixel size, 9” 8K screen), and Printer D (desktop MSLA, 19 x 24 µm pixel size, 9” 12K screen) we will demonstrate that this common resolution metric does not have a direct effect on tangible printed part outcomes.
Though Form 4 has a larger individual pixel size than some competitors, the testing results demonstrate that it achieves comparable if not superior surface finish, dimensional accuracy, and minimum feature size when compared to MSLA 3D printers with smaller pixel sizes. Finding the right balance also empowered our team to optimize Form 4 for other metrics that customers really care about — faster speed, better reliability, and substantially longer component lifetime.
Output Characteristics: What Really Matters For 3D Printed Parts
Printer design, including pixel size as one input, impacts three major characteristics of printed parts. These characteristics — surface finish, minimum feature size, and dimensional accuracy — are measurable and standardized, but because they are impacted by a complex combination of processes and components, they are harder to report. A slightly larger pixel size does not matter as much as the quality, consistency, and uniformity of the light it is masking or letting through.
Each of these characteristics can be significantly affected by almost every key aspect of the system, optics, materials, and the print process and its parameters. It is not possible to relate a single system input parameter directly to a single output, except as a limit.
For example, pixel or spot size sets a lower limit on positive feature size in the horizontal plane (i.e. you cannot have a single positive feature smaller than the pixel or spot size). Typically, however, the minimum feature size ends up being far larger than this limit (often much greater than 100 µm) because of multiple factors, such as peel forces.
Description | Measurement | Key Driving Parameters | |
---|---|---|---|
Surface Finish | How smooth a surface is or appears to be | Visual/qualitative, surface profiler (Ra) measurement | Layer thickness Optical properties of resin Consistency of interlayer process |
Minimum Feature Size | The smallest feature that can be produced of a certain type. Depends highly on the type of feature. | Calipers CMM 3D scanner | Mechanical properties of resin Optical PSF |
Dimensional Accuracy | How accurately a target geometry is reproduced | Calipers CMM 3D scanner Gauge pins Other fit tests | Temperature Mechanical repeatability Optical consistency |
Resolution Inputs
Resin 3D printers have either a laser (laser-powered SLA), a digital light projector (DLP), or a light processing unit (most commonly an LCD screen) that selectively masks a light source like a bank of LEDs (MSLA).
Laser-powered SLA 3D printers typically have very high resolutions because the laser can be precisely controlled in the XY plane, and has a small spot size. However, these characteristics are just one input — the actual minimum feature size is still affected by multiple factors, and so measurements are on par with professional MSLA printers that do not use a laser. Additionally, laser-powered SLA printers often have slower print times because of the need to trace the laser spot across the entire layer.
In DLP 3D printing, XY resolution is defined by the pixel size — the smallest feature the projector can reproduce within a single layer. This depends on the resolution of the projector, the most common being full HD (1080p), and its distance from the optical window. As a result, most desktop DLP 3D printers have a fixed XY resolution, generally between 35 to 100 microns.
DLP 3D printers’ resolution diminishes as build volume grows bigger because there are no projectors available with significantly more pixels. Therefore, manufacturers have to increase the distance from the light source with the same number of pixels, leading to decreased resolution and print quality.
Pixel Size and Point Spread Function (PSF)
Surface finish, feature size, and accuracy are affected by every part of the 3D printer and its process. Single inputs like pixel size can set theoretical lower limits that aren’t seen in realistic situations. For example, while a pixel or laser spot size of 80 microns could theoretically be the limiting factor in curing a single positive feature (like the diameter of a cylindrical pin) the peel forces would pull on the part and cause it to fail, putting the minimum diameter for these pins to be at around 500 microns.
In MSLA 3D printers that use LCD screens to mask light, the actual image projected onto the resin is typically significantly larger and more diffuse than the original pixel. This effect is known as Point Spread Function (PSF): the way an original or idealized image is blurred by the projection process. So for MSLA printers, the size of the pixel does not matter as much as the power distribution and shape of the light as it hits the resin.
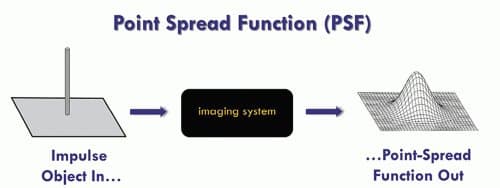
When comparing the PSF of Form 4 (with light projected through an LCD screen made up of 50 µm pixels) to Form 3+ (with light coming from a laser with an 80 µm spot size), the PSF images show that Form 4’s light is concentrated and direct, with the highest energy clustered tightly in the middle of the pixel.
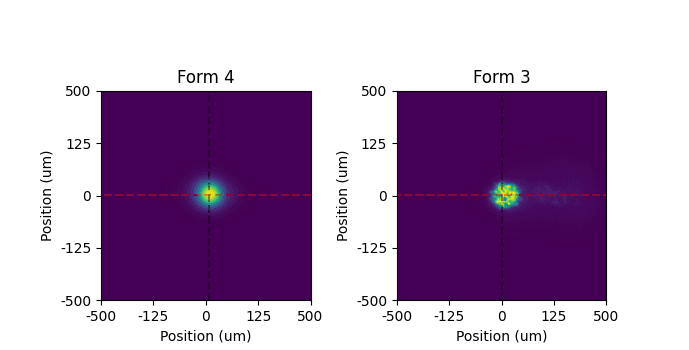
When comparing the Point Spread Function (PSF) of Form 4 with that of the Form 3 Series, it’s possible to see that both printers produce highly concentrated light clustered in the center of the pixel or laser spot — translating directly to high resolution.
Testing Results and Conclusion
Surface Finish
Surface finish is important — it impacts not only the look and feel of a part but also how that part might fit into an existing assembly or perform as a mold. Surface finish can be measured by eye — how smooth parts appear to be, as well as by using a surface profiler (Ra) measurement. Besides pixel or laser spot size, the driving inputs that affect surface finish are the Z-axis layer height, the optical properties of the resin, and the consistency of the interlayer (peel and squish) process.
The surface finish, to the naked eye, is virtually indistinguishable between them. Curved surfaces appear smooth, edges are sharp, and both positive and negative or engraved features are clearly outlined. Embossed text is detailed, easy to read, and uniformly raised against the surface.
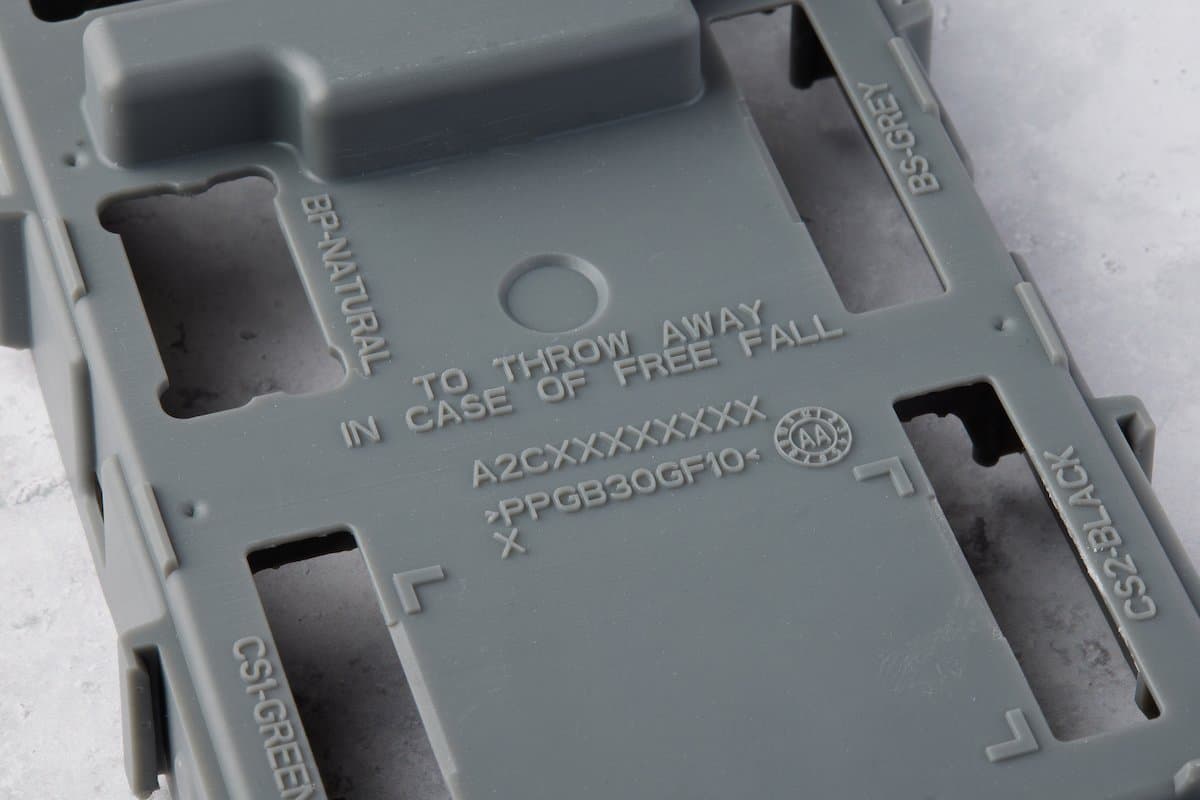
Printer A: Form 4 MSLA
- 50 µm pixel size
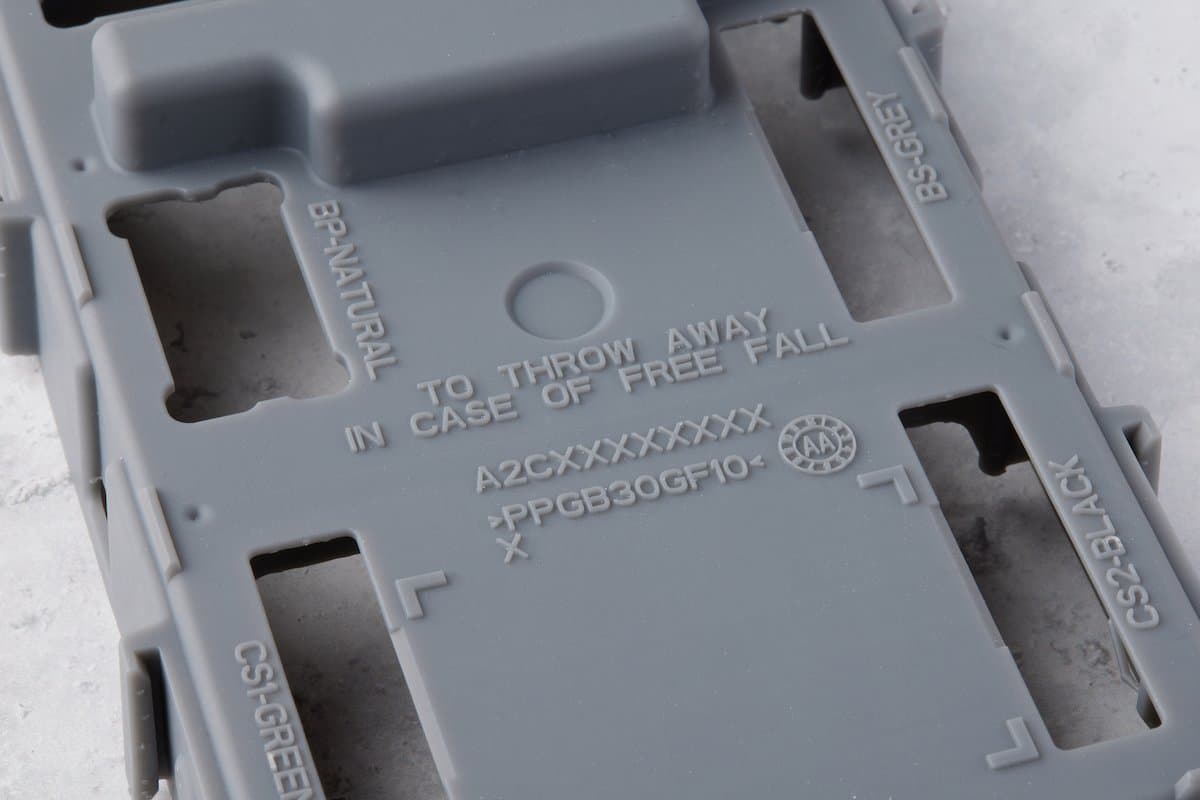
Printer B: Form 3+
- 85 µm spot size
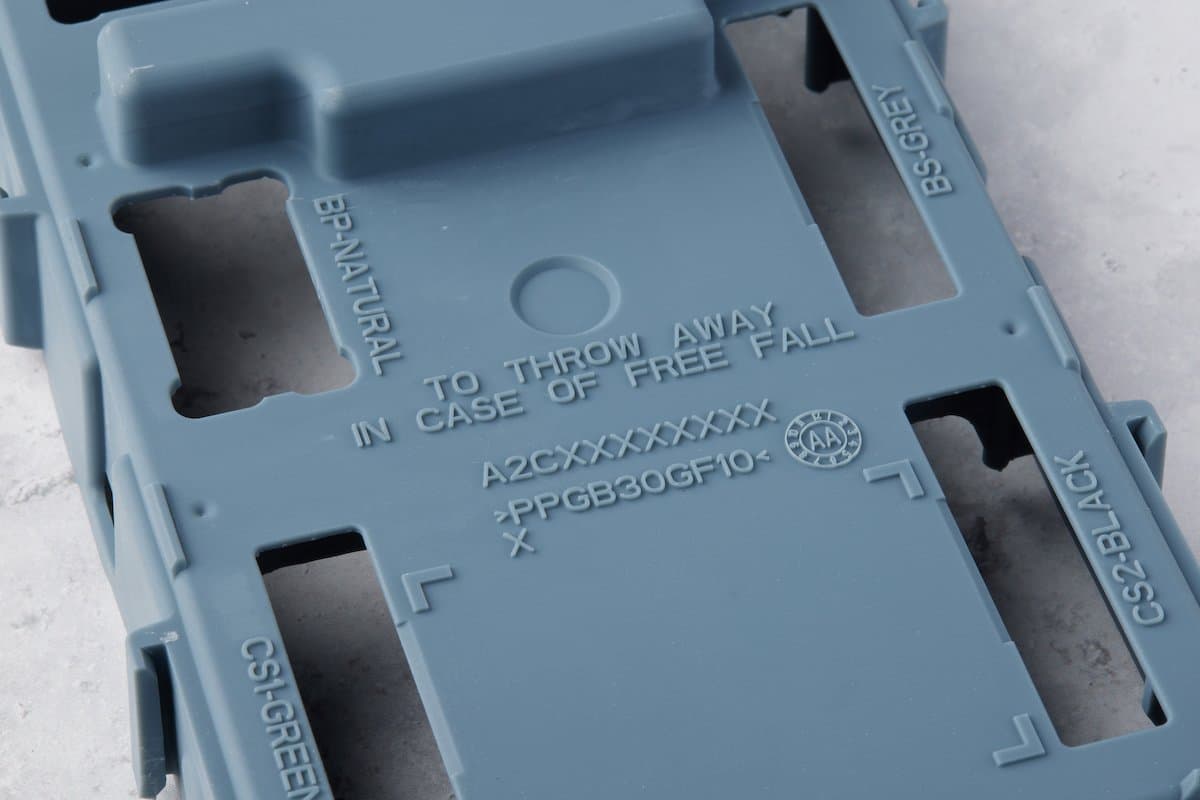
Printer C: MSLA
- 28 µm pixel size
- 9” 8K screen
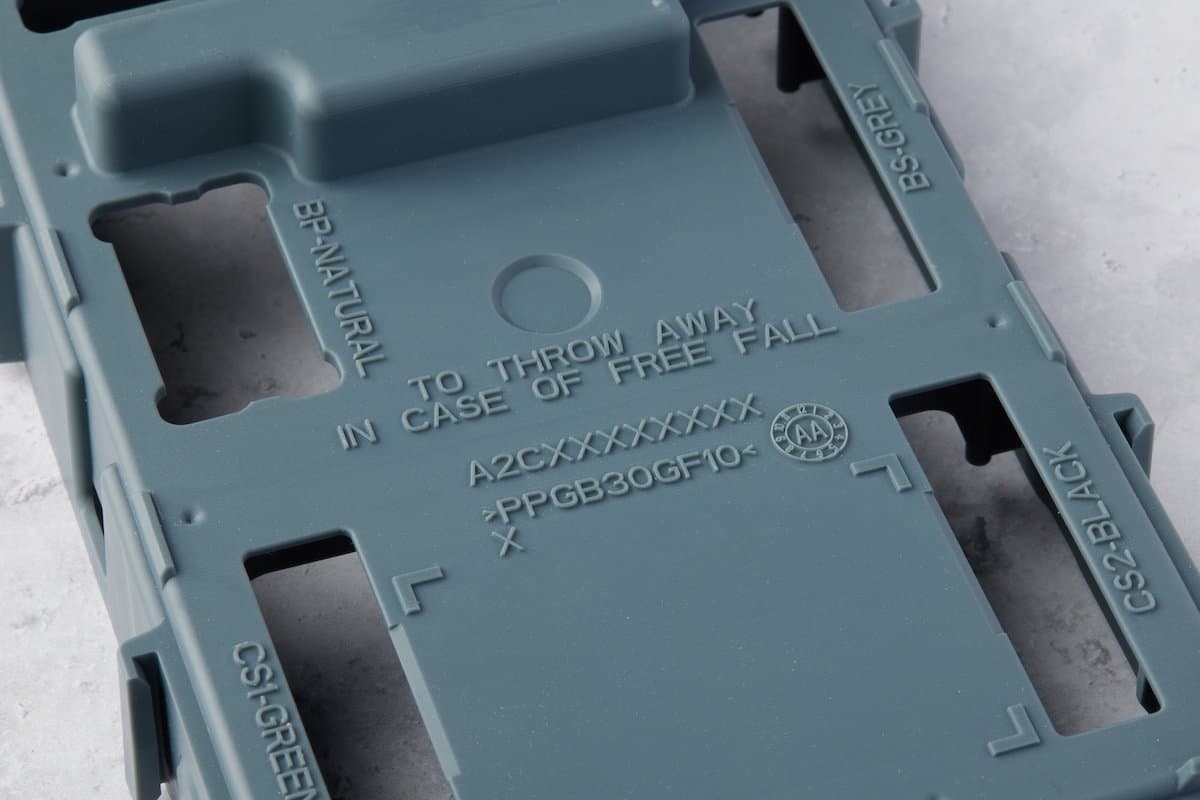
Printer D: MSLA
- 19 x 24 µm pixel size
- 9” 12K screen
Dimensional Accuracy
Dimensional accuracy, or how well the part matches the measurements of the original file, is important for repeatability and part success. If a printer cannot produce the intended geometry, the parts won’t function in their intended setting. Dimensional accuracy is very important in certain applications such as dental or orthodontic models, where a perfect reproduction of the scanned file, and thus the patient’s anatomy, is crucial for a successful procedure.
Accuracy is measured by calipers, a coordinate measuring machine (CMM), a 3D scanner, gauge pins, or other fit tests. Besides pixel or laser spot size, the driving inputs that affect dimensional accuracy are printing temperature, mechanical repeatability, and optical consistency.
As the scans demonstrate, smaller pixel or laser spot size does not translate directly to better dimensional accuracy. The dental models are almost perfectly dimensionally accurate, for the printers with the ‘larger’ single points of light: Form 4’s dental model is more accurate than the Printer C’s, even though Printer C has a smaller pixel size.
Printer A: Form 4 MSLA
- 50 µm pixel size

Key Dimensional Measurement Absolute Error from Ideal (mm): Length (0.72), Width (0.22), Raised Feature Width (0.12), Raised Feature Smallest Length (0.06)
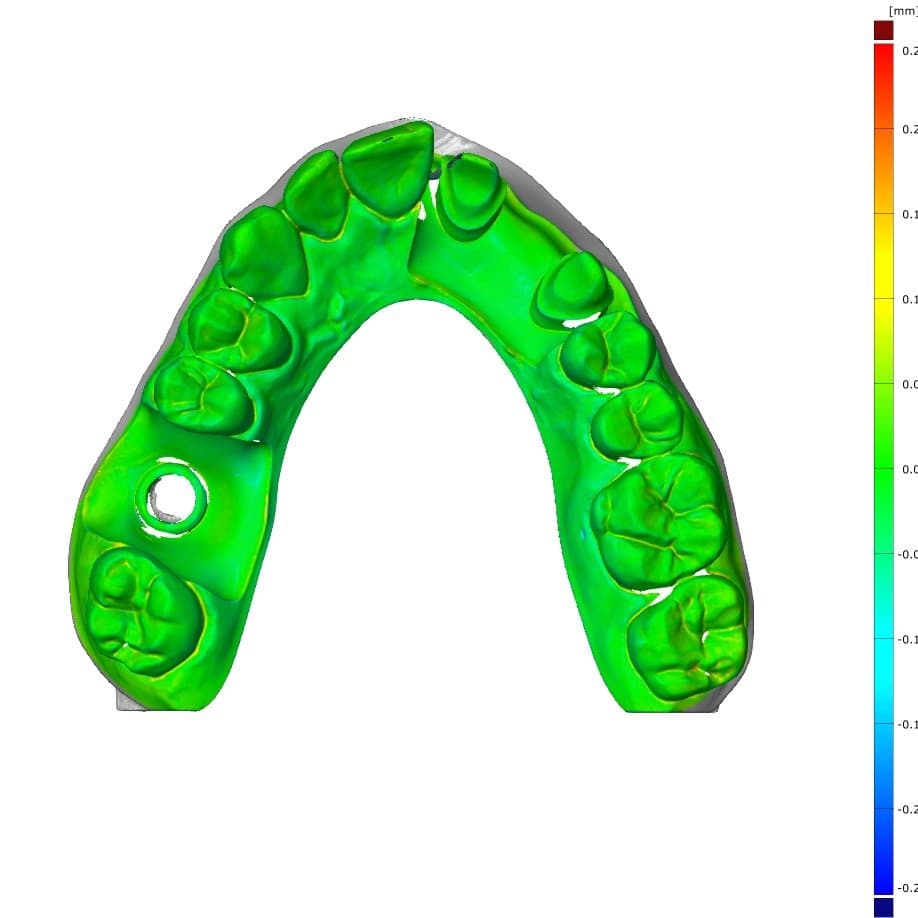
Percentage of surface within 50 μm of ideal: 95.5%
Printer B: Form 3+
- 80 µm laser spot size
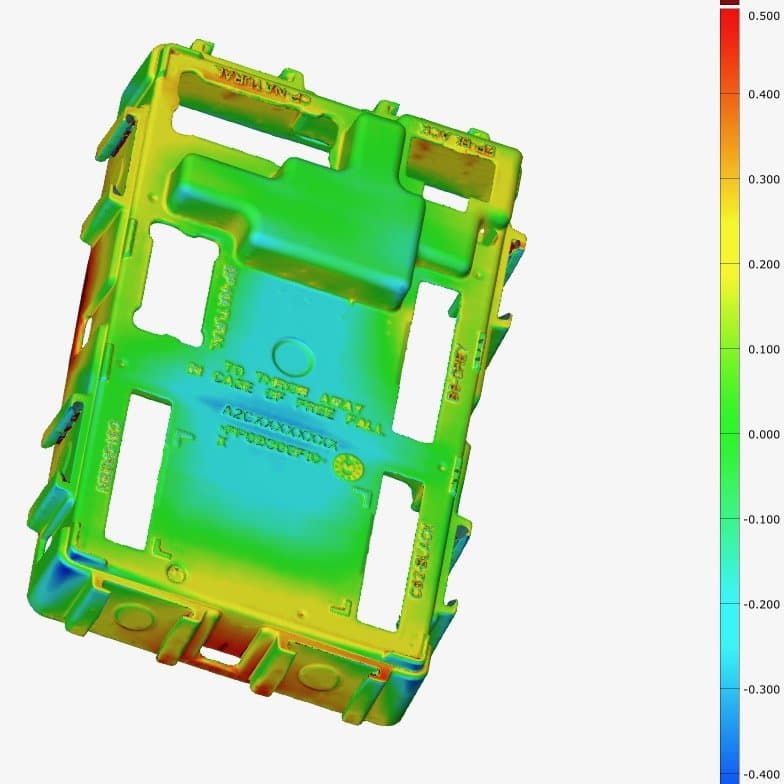
Key Dimensional Measurement Absolute Error from Ideal (mm): Length (0.44), Width (0.42), Raised Feature Width (0.16), Raised Feature Smallest Length (0.09)
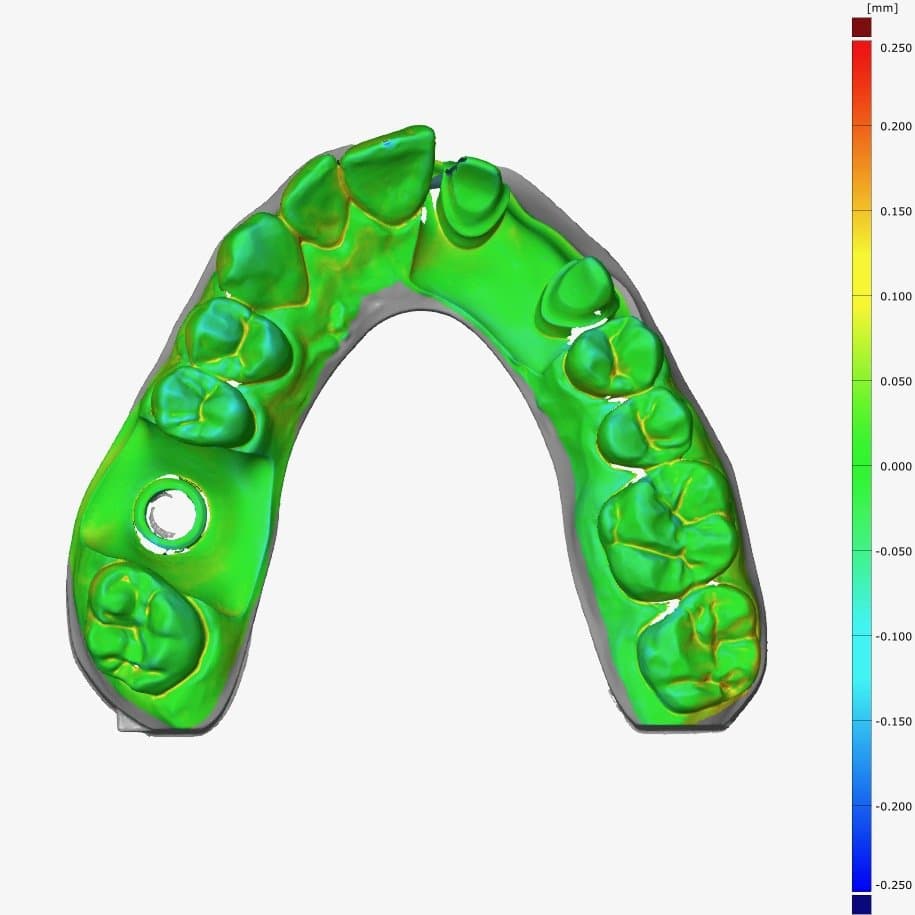
Percentage of surface within 50 µm of ideal: 82.1%
Printer C: MSLA
-
28 µm pixel size
-
9” 8K screen
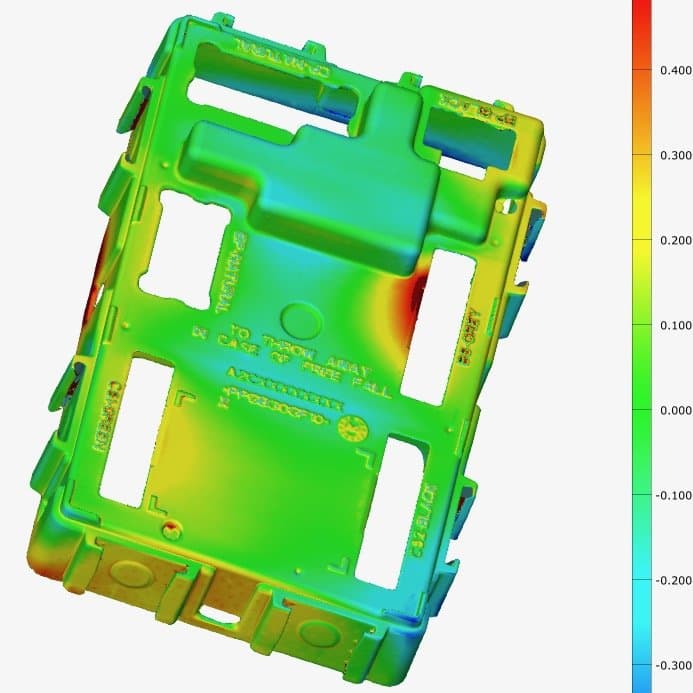
Key Dimensional Measurement Absolute Error from Ideal (mm): Length (0.38), Width (0.30), Raised Feature Width (0.07), Raised Feature Smallest Length (-0.05)
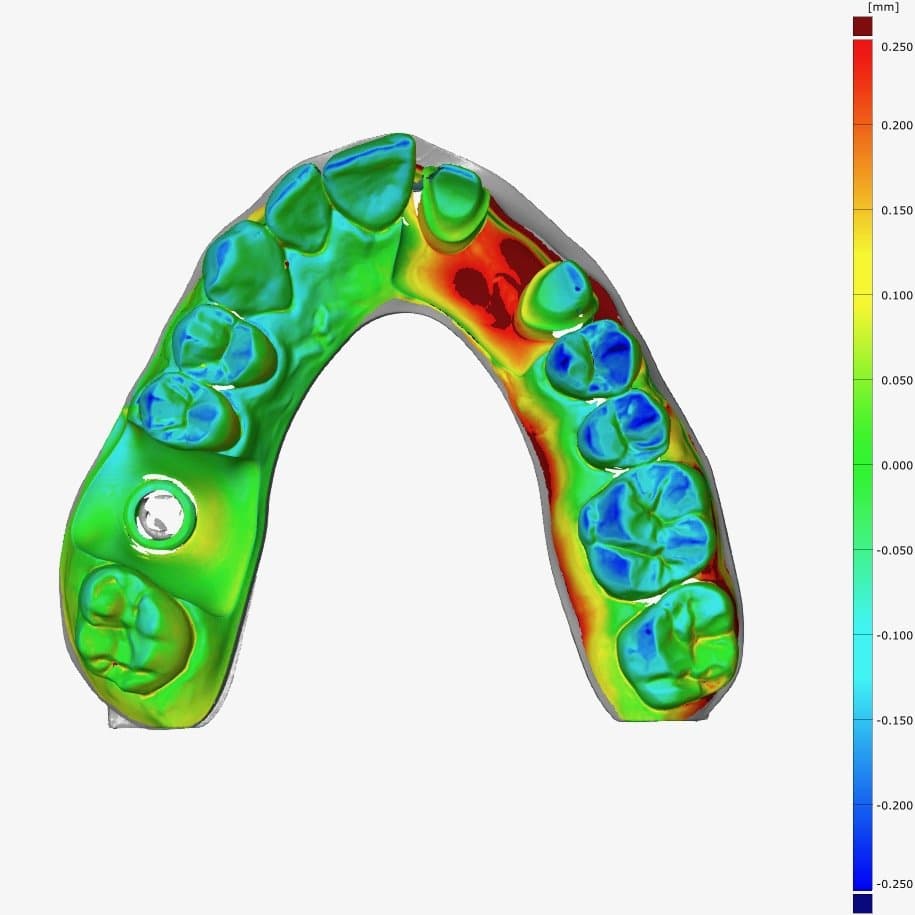
Percentage of surface within 50 µm of ideal: 53.9%
Printer D: MSLA
-
19 x 24 µm pixel size
-
9” 12K screen
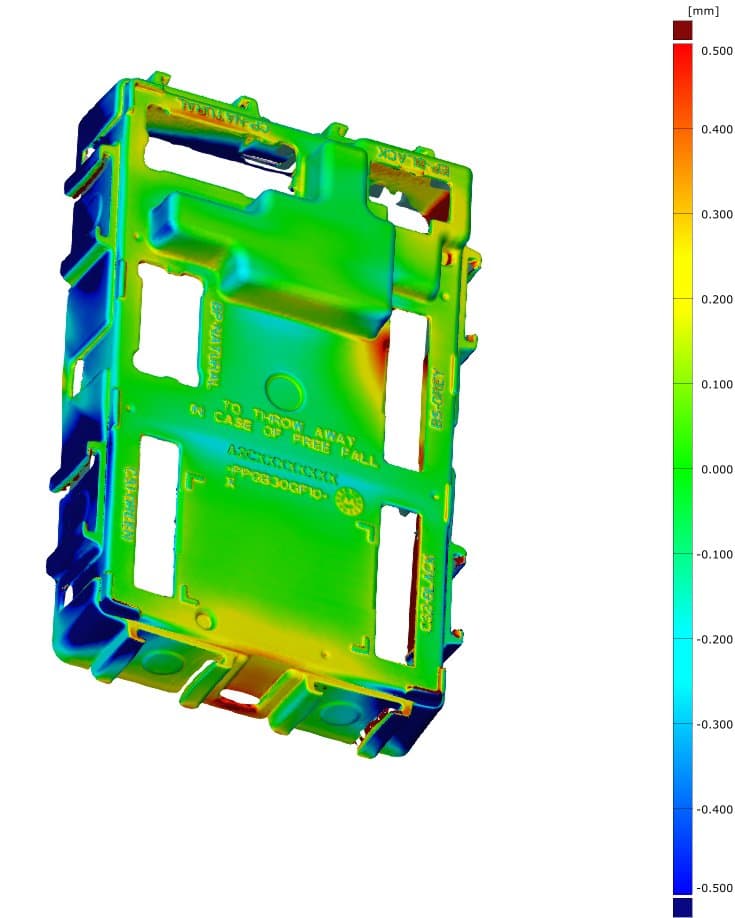
Key Dimensional Measurement Absolute Error from Ideal (mm): Length (+0.77), Width (-0.37), Raised Feature Width (-0.371), Raised Feature Smallest Length (-0.052)
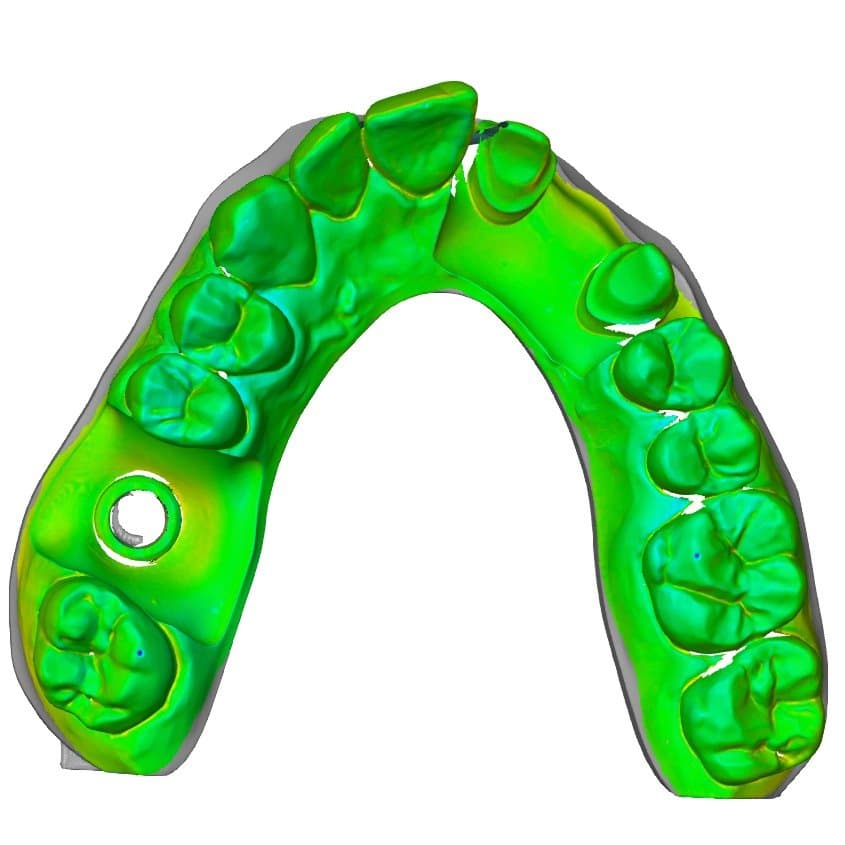
Percentage of surface within 50 µm of ideal: 87.2%
Feature Size
Feature size as a performance metric refers to minimum feature size, or the smallest size feature a 3D printer can produce. This feature size will change based on whether it’s an engraved feature, embossed, positive wire, or negative hole or channel. These features can be measured by a simple pass/fail test, or by using calipers, a CMM, or a 3D scanner.
As stated above, pixel size or laser spot size may seem like an easy metric for single positive features, but the realities of print processes mean that there are no printers capable of producing single positive features the size of a single pixel — 20 µm, 30 µm, 50 µm, or 80 µm. Instead, the factors that influence the minimum feature size are temperature, mechanical repeatability, and optical consistency.
As the photos demonstrate, Form 4 delivers some of the best minimum features. Every printer had difficulty completing the full set of negative channels, but Form 4 and Printer D delivered four out of five channels clearly, while Form 3+ and Printer C delivered only three out of five.
Unsupported walls were difficult for each printer, with varying degrees of uprightness. Each printer created a perfect unsupported wall at the thickest thickness, and Form 4 continued to create the following four walls relatively upright. Both Printer C and Printer D had unsupported walls fall completely over as they thinned. Though these printers struggled at different locations on the test model, failures did not correlate with smaller or larger pixel or laser spot size. It can be inferred that minimum feature size is a function of several factors including print process mechanisms and resin properties.
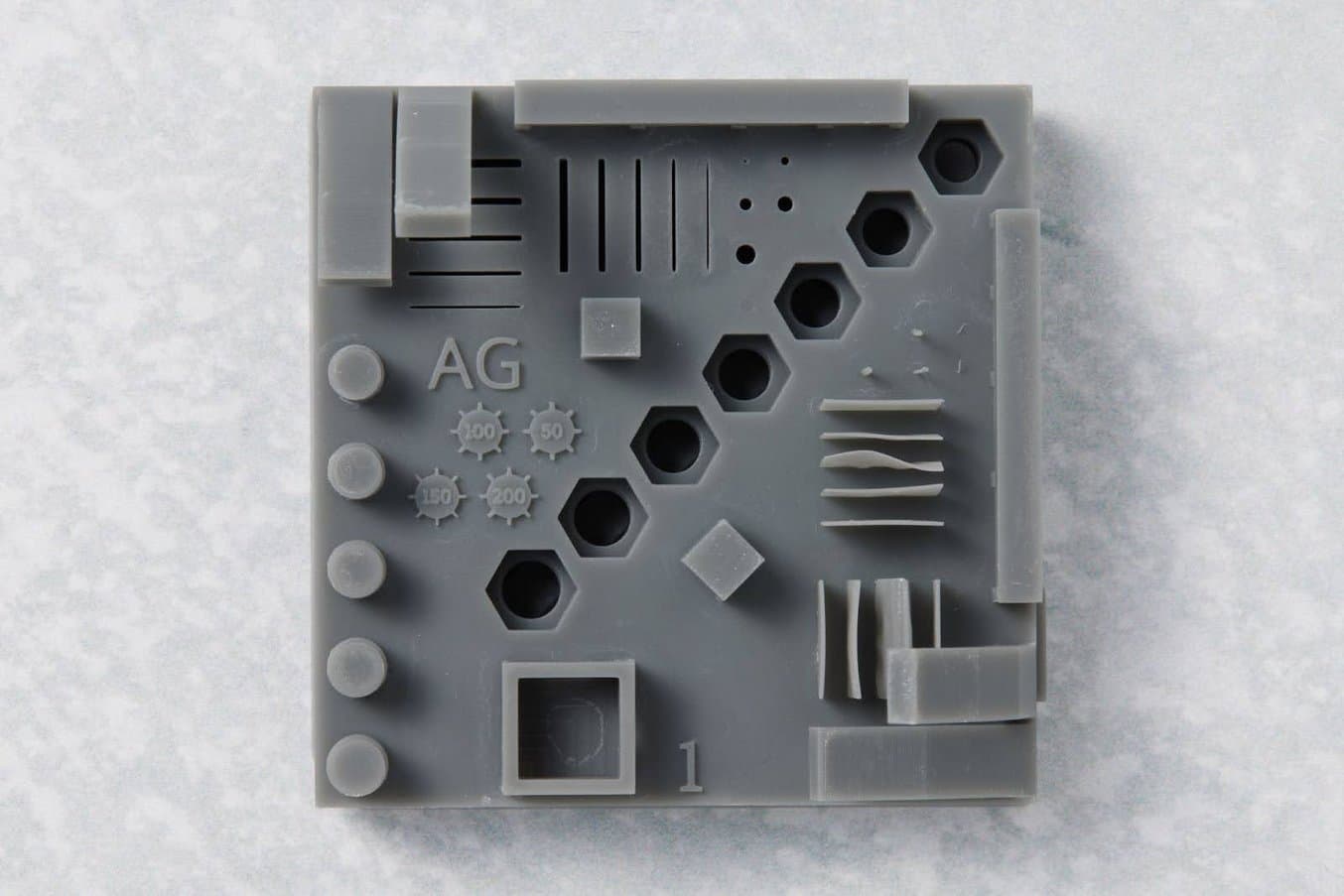
Printer A: Form 4 MSLA
- 50 µm pixel size
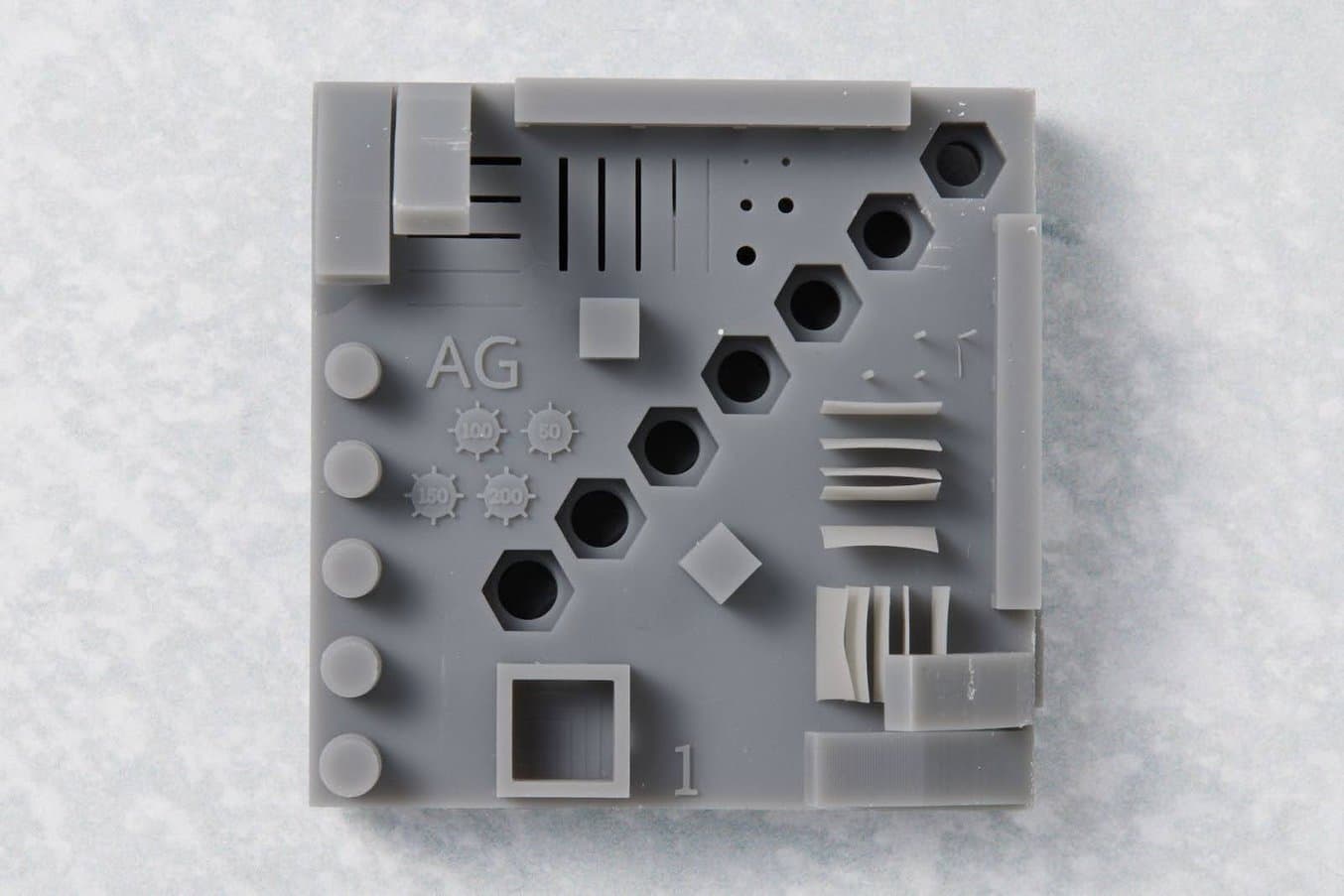
Printer B: Form 3+
- 85 µm spot size
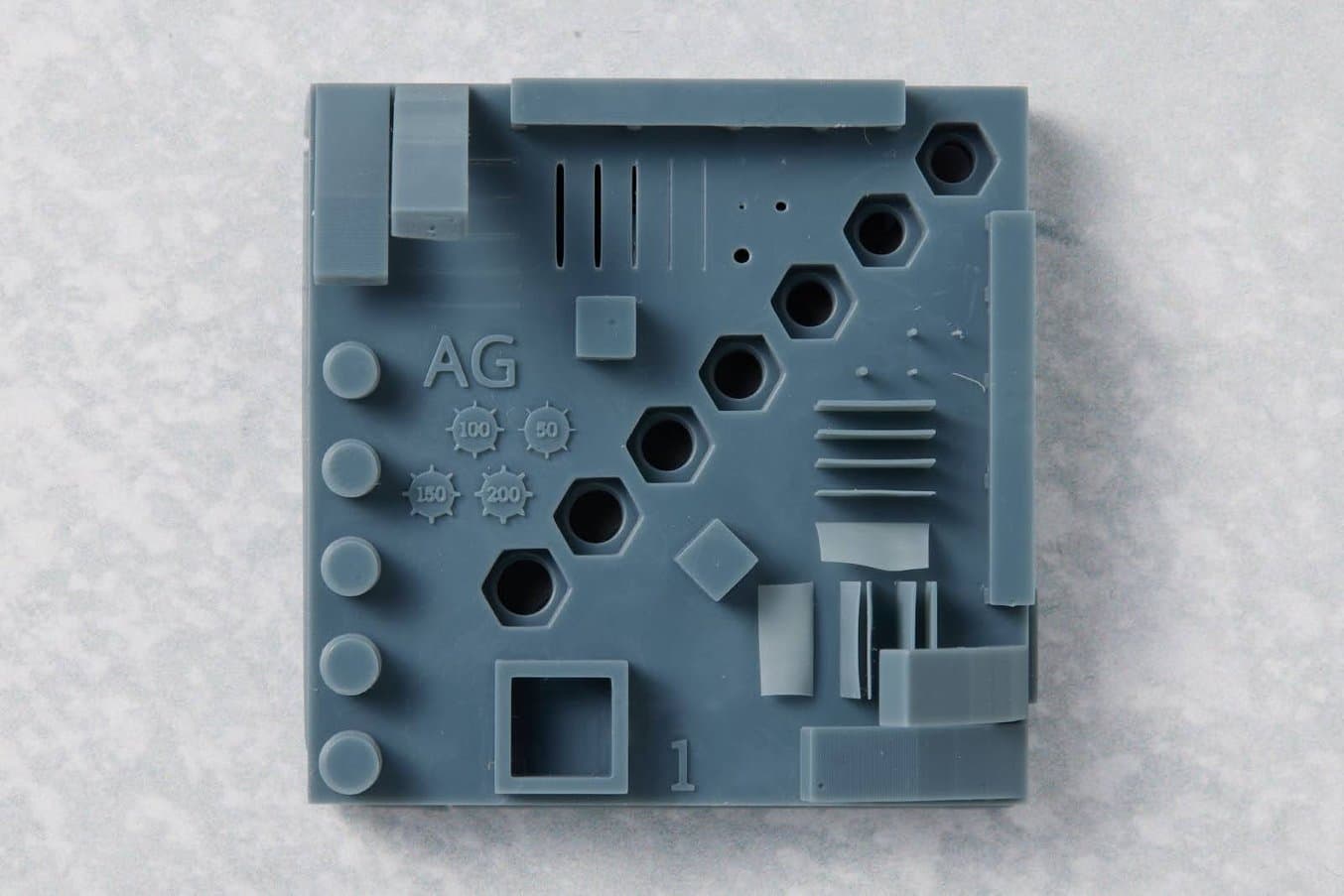
Printer C: MSLA
- 28 µm pixel size
- 9” 8K screen
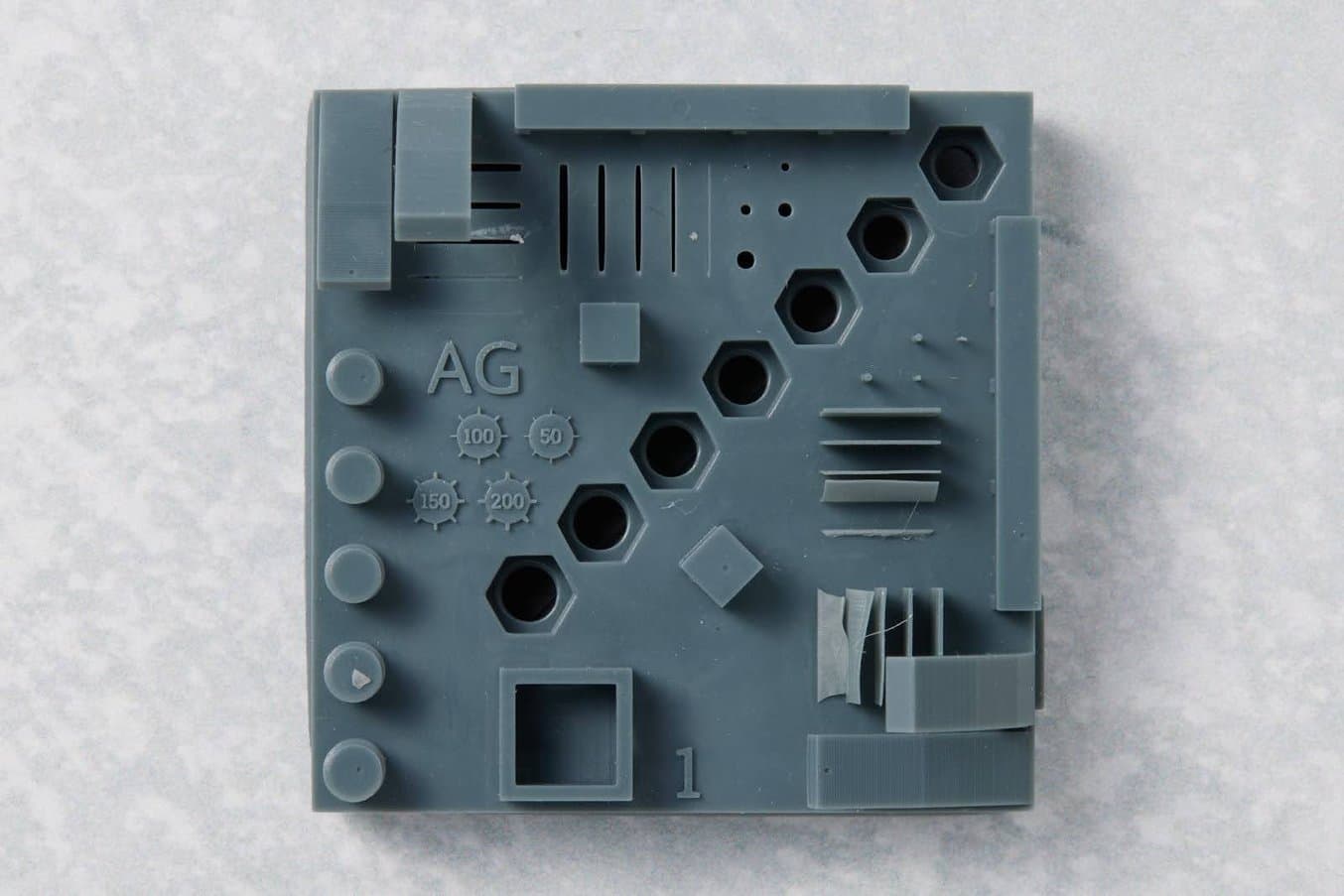
Printer D: MSLA
- 19 x 24 µm pixel size
- 9” 12K screen
Simplifying the Resolution Debate in SLA 3D Printing
Despite the ease with which manufacturers tout pixel size as the end-all, be-all of 3D printing resolution, the truth (and the real-world impact) is more complex.
Resolution is not solely dependent on the size and shape of the light as it passes through an LCD screen or is emitted from a laser or light projector. It is also dependent on the PSF of that light, print processes, mechanical consistency, and optical properties of the resin. Resolution should be looked at as an input when talking about the outcomes of surface finish, feature size, and dimensional accuracy. With that information and viewpoint, 3D printing users can evaluate which printer is the best fit for their specific needs.
Formlabs carefully evaluated the tradeoffs of pixel size, speed, reliability, and component lifetime when creating the Light Processing Unit of Form 4. Because LCD screen pixel size has no tangible impact on the three major outcomes of resolution, a larger pixel size is not a compromise — it’s an investment into power and speed.
To explore the next generation of SLA 3D printing, learn more about Form 4. Curious to see the surface finish, minimum feature size, and dimensional accuracy possible with Form 4’s LFD technology? Request a free sample part to be shipped to your office.