There are few things more tragic in life than children suffering severe trauma — but when an accident does happen, Romans Ferrari is one of the best places for recovery.
Located close to Lyon in France, Romans Ferrari is a pediatric rehabilitation center that provides care to children and adolescents who have had trauma, brain damage, brain tumors, polytrauma, and severe burns.
The center has immense experience providing treatment for severe facial burns, which includes specialized compressive masks that reduce the risk of complications and scarring. However, the traditional way to produce these masks involved an uncomfortable workflow that could induce post-traumatic stress disorder in children.
Read on to learn how Romans Ferrari developed a new digital workflow for creating custom compressive masks for treating facial burns using 3D scanning and 3D printing, thanks to a multi-team collaboration among doctors, prosthetists, and engineers.
How Severe Burns Are Treated
Romans Ferrari accepts children and adolescents from across France who get referred to them by various hospitals after the initial (life-saving, ICU) treatments. The first step is to welcome the patient as soon as possible from a medical standpoint to avoid scarring complications from forming, such as scar contractures and hypertrophic scars, which mean volume gains and the development of fibrous and thick scars.
The goal is to epidermise the wounds as soon as possible, so that there are no more open wounds that may lead to infections, complications, and fluid disbalance. Then, the actual rehabilitation starts which includes dressing the skin with compressions and rehabilitation sessions that combine physiotherapy, filiform showers, and other methods.
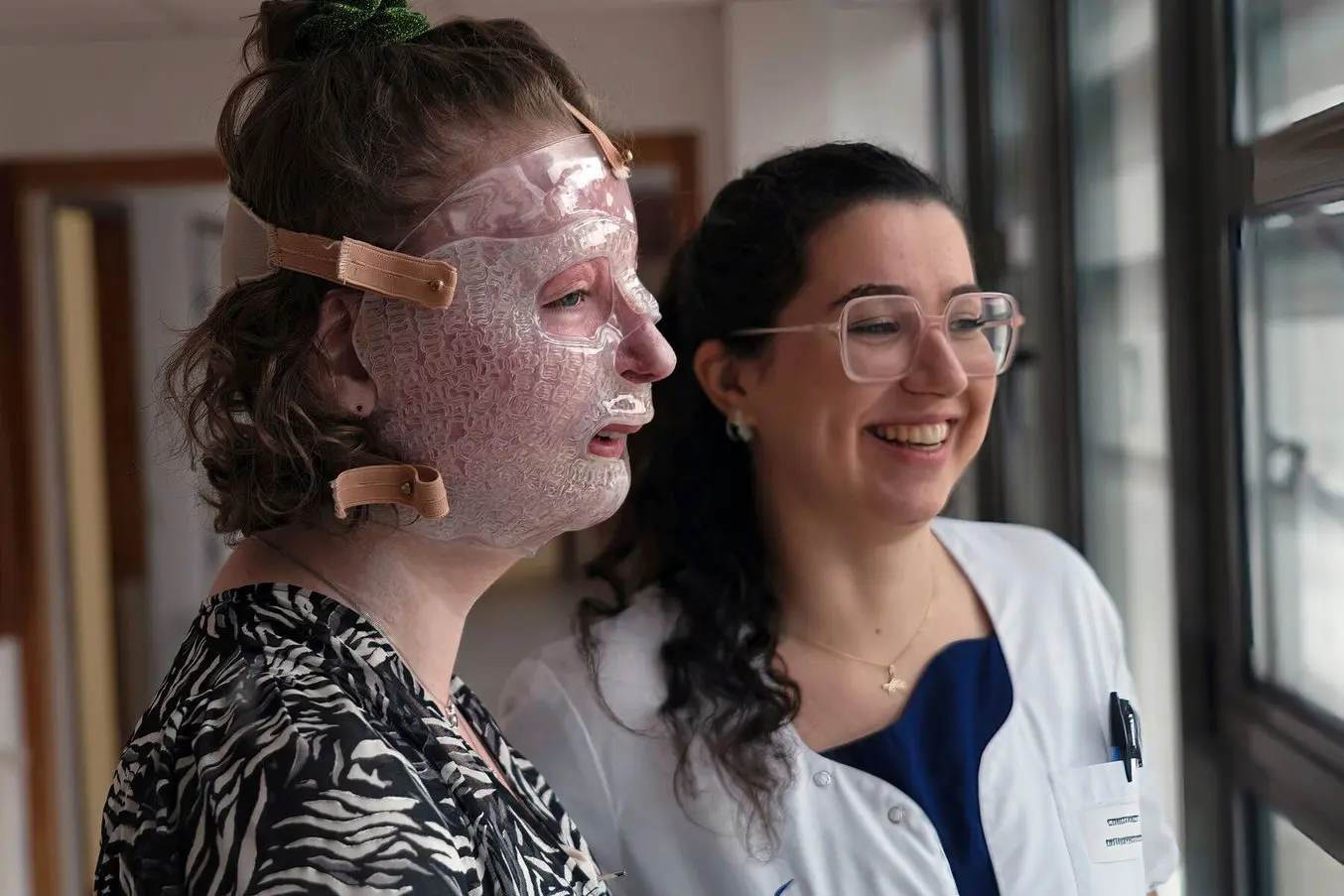
Laura Weibel, a patient at Centre Romans Ferrari, wearing a compressive face mask.
Compression devices help scars mature and heal, preventing complications, improving scar texture, making the skin more flexible, and guiding the body to develop the most comfortable and aesthetic scars possible as children grow.
Beyond the traditional compressions used by burn centers worldwide, Romans Ferrari’s team also developed custom devices that include specialized reliefs, called growth and maturation devices or DMDGs by the center, which allows for more targeted support at the scar level and a slightly finer way to work on the scar progression in terms of intra-scar adhesion and elasticity.
Previously, for facial burns, compressive masks were made from plaster casts. The orthoprosthetist created a negative with plaster strips, from which they created a positive, which they used to thermoform the final mask.
“It required the patients to be motionless for the duration of the plaster cast that lasts about half an hour, which can be difficult, especially for children, and could reactivate symptoms of post-traumatic stress disorder because the bandages are a little warm, and it is sometimes unpleasant for the patients to have the heat on their face.”
Sara Arias, Doctor for Physical and Medical Rehabilitation, Centre Romans Ferrari
Inventing a Digital Workflow for Compressive Facial Masks
“3D printing is something we've dreamed of for quite a long time. We had imagined that a 3D printer would allow us to produce a mask based on the scanned file without ever having to touch the patient. It was when Mr. Veauville arrived and had an engineering perspective that he said, ‘We have to put that in the hands of engineers.’”
Christophe Debat, General Manager, Centre Romans Ferrari
Jean-François Veauville, a board member at Romans Ferrari, formerly worked as an aeronautical construction engineer in Toulouse focused on composite materials. He gave engineering students at the research university École Centrale de Lyon a study to complete to understand whether 3D printing can be used to produce the mask directly or to improve the process of creating it.
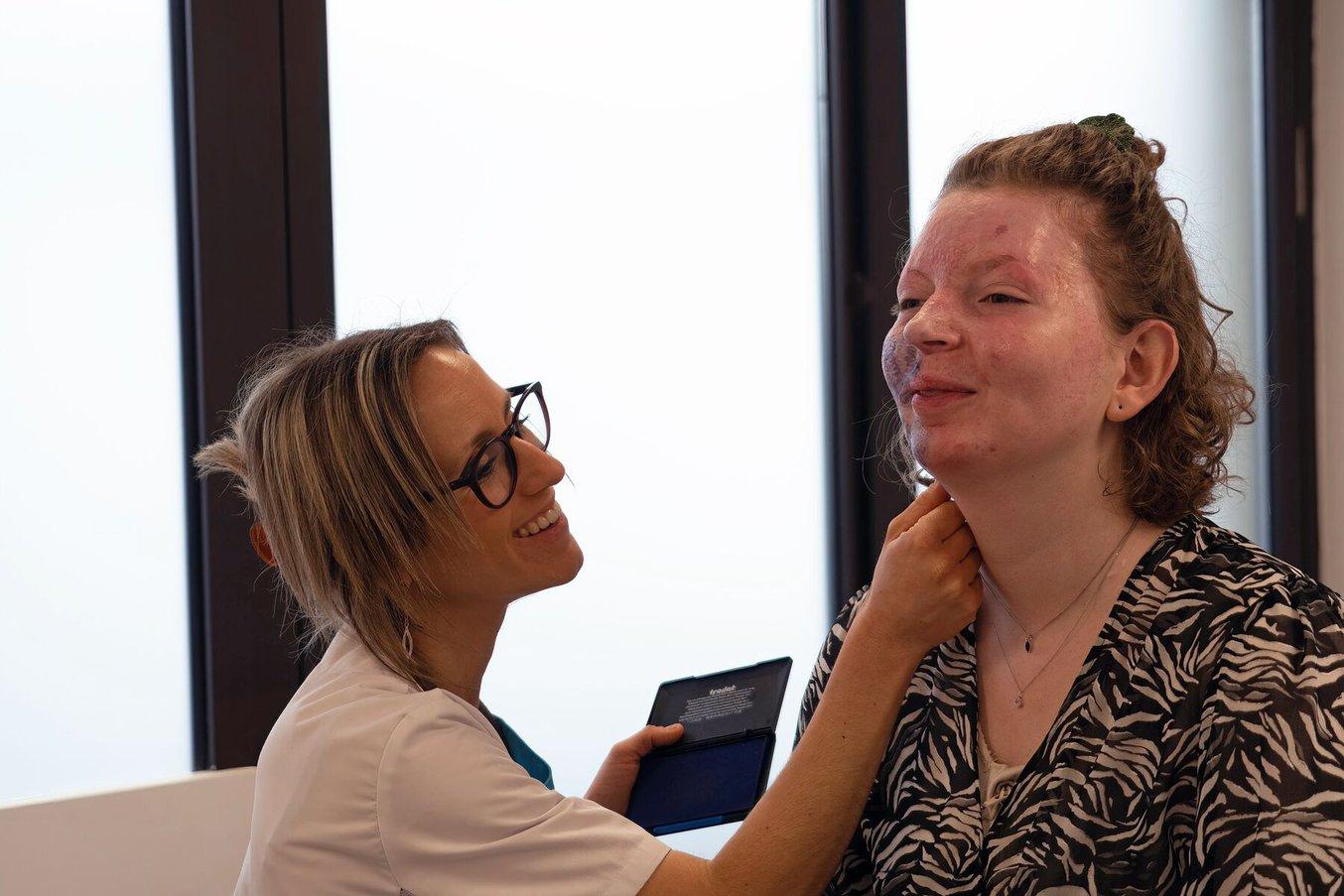
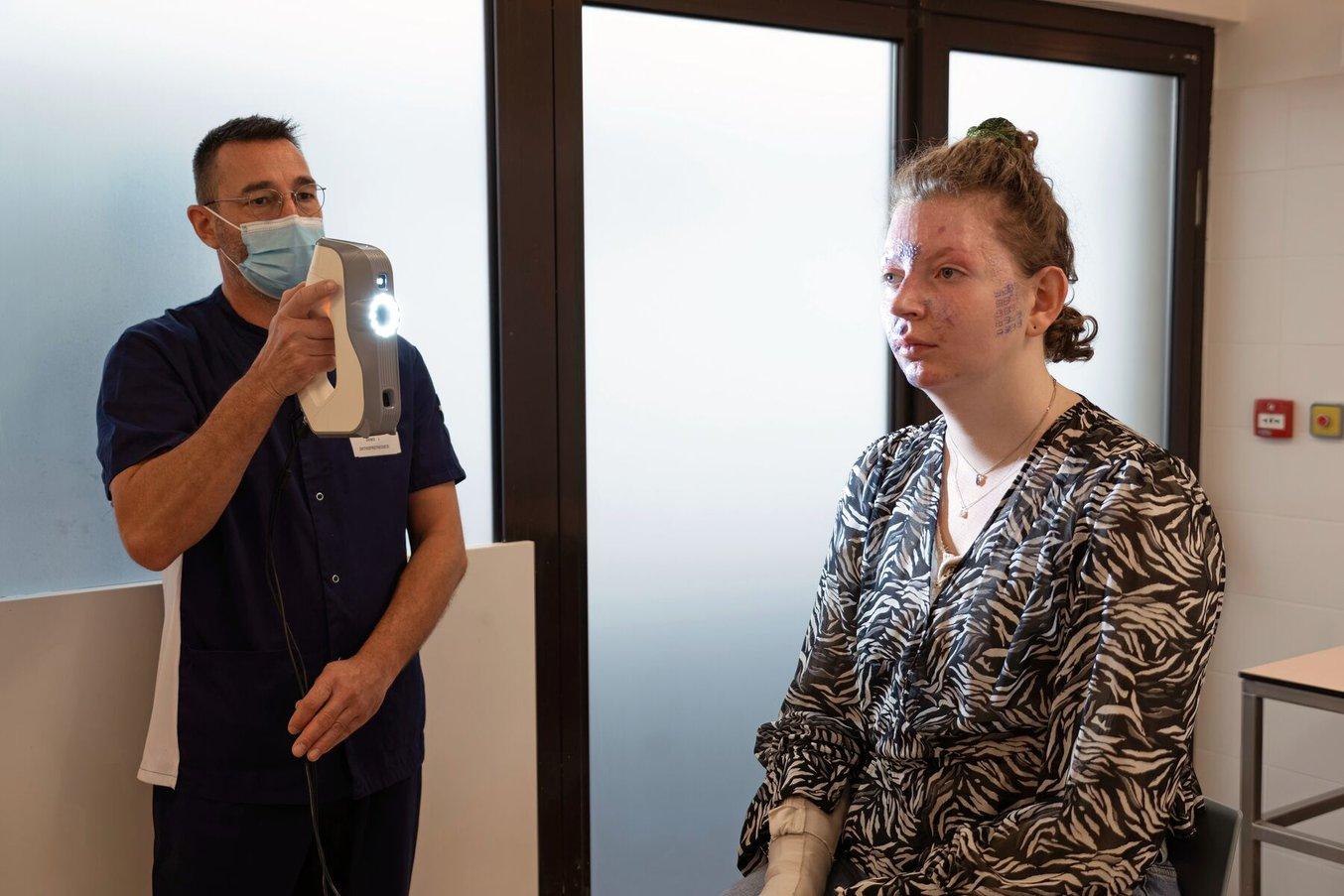
The new digital workflow starts with the doctor marking the eventual locations of the targetted reliefs and then an orthoprosthetist 3D scanning the face of the patient.
They evaluated multiple 3D printing technologies available, and worked with service providers to order test prints. After conducting a great deal of research over six months, the results indicated that 3D printing could be used to produce the positives which were previously made out of plaster.
But that was just part of the challenge, as the team had to figure out a way to digitalize the entire workflow. The student team then connected Mr. Veauville to 3DZ France, a reseller and integrator of 3D printing equipment, who collaborated with Romans Ferrari’s team to find the best solution for each step of the workflow. This included digitally replicating the current manual process with high accuracy, finding the right 3D printing solution for producing the masks, and validating the entire workflow.
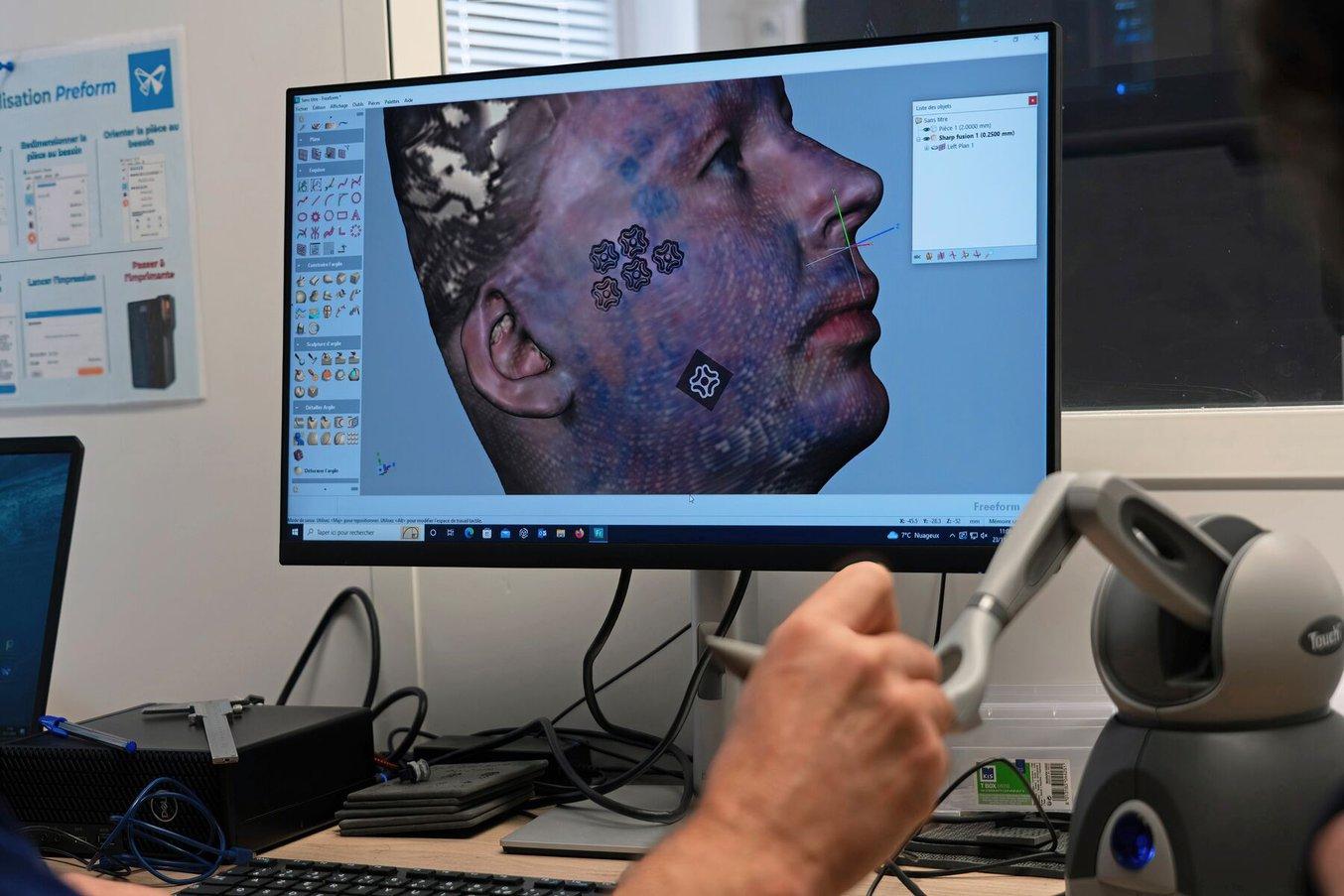
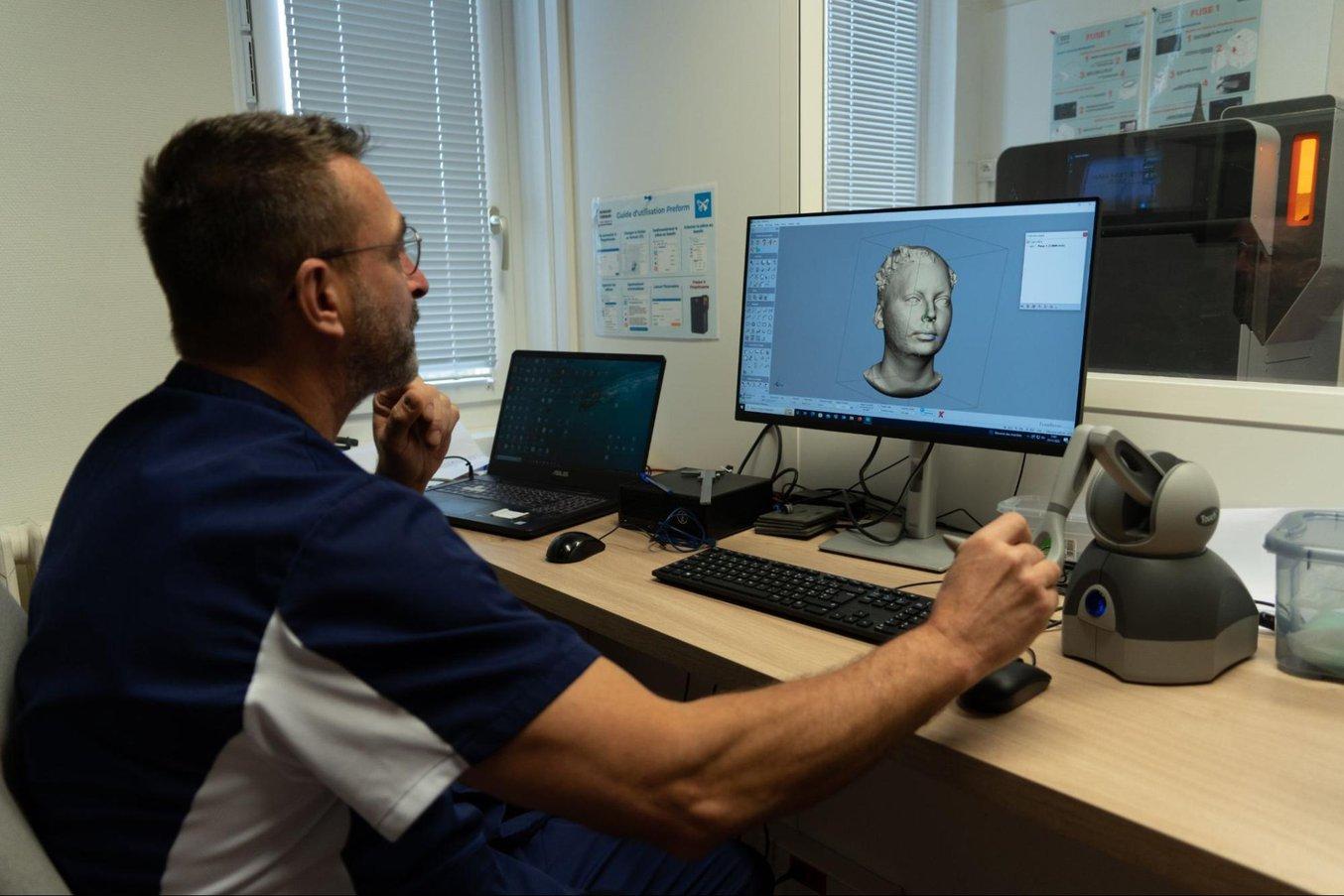
The orthoprosthetist uses a digital pen to precisely add the targeted reliefs to the design before creating a 3D printable model.
“The real difficulty was to understand what the practitioners were expressing and to transform the medical language into technical language because we have different lexicons. The first challenge was to relieve the child in the process of capturing the scanning data. Second, to have a solution that is easy to deploy and can be quickly learned at the practitioner level.”
Patrick Ferraris, CEO, 3DZ France
The new workflow involves scanning the patient’s face with a 3D scanner and using CAD software to design a mask based on the scan. Before scanning, the doctor gently marks the locations for the DMDG devices onto the face of the patient and the technician uses a digital pen to precisely add these engraved details to the design. The mask is then 3D printed on a Fuse 1 selective laser sintering (SLS) 3D printer and serves as the positive for thermoforming the final mask.
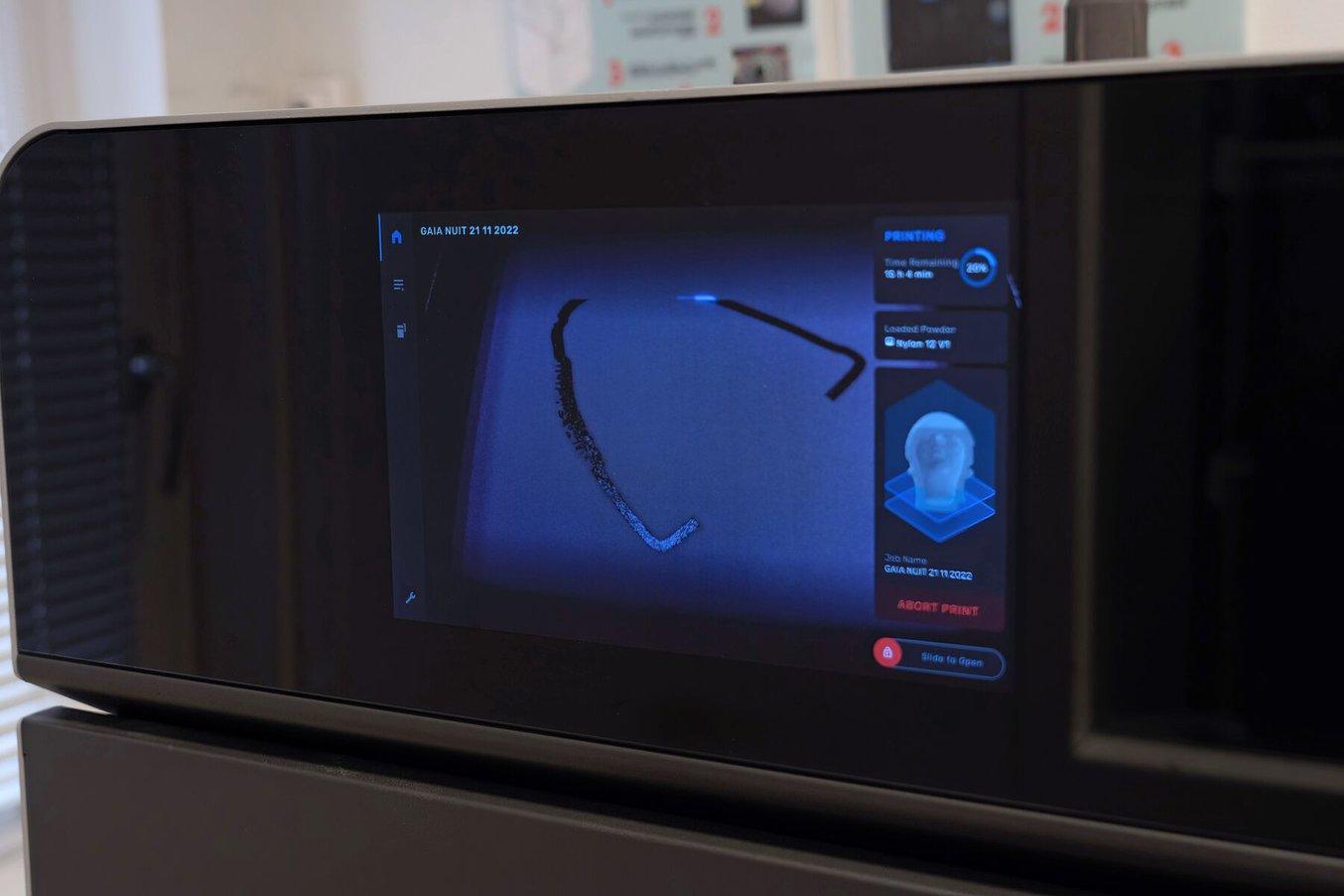
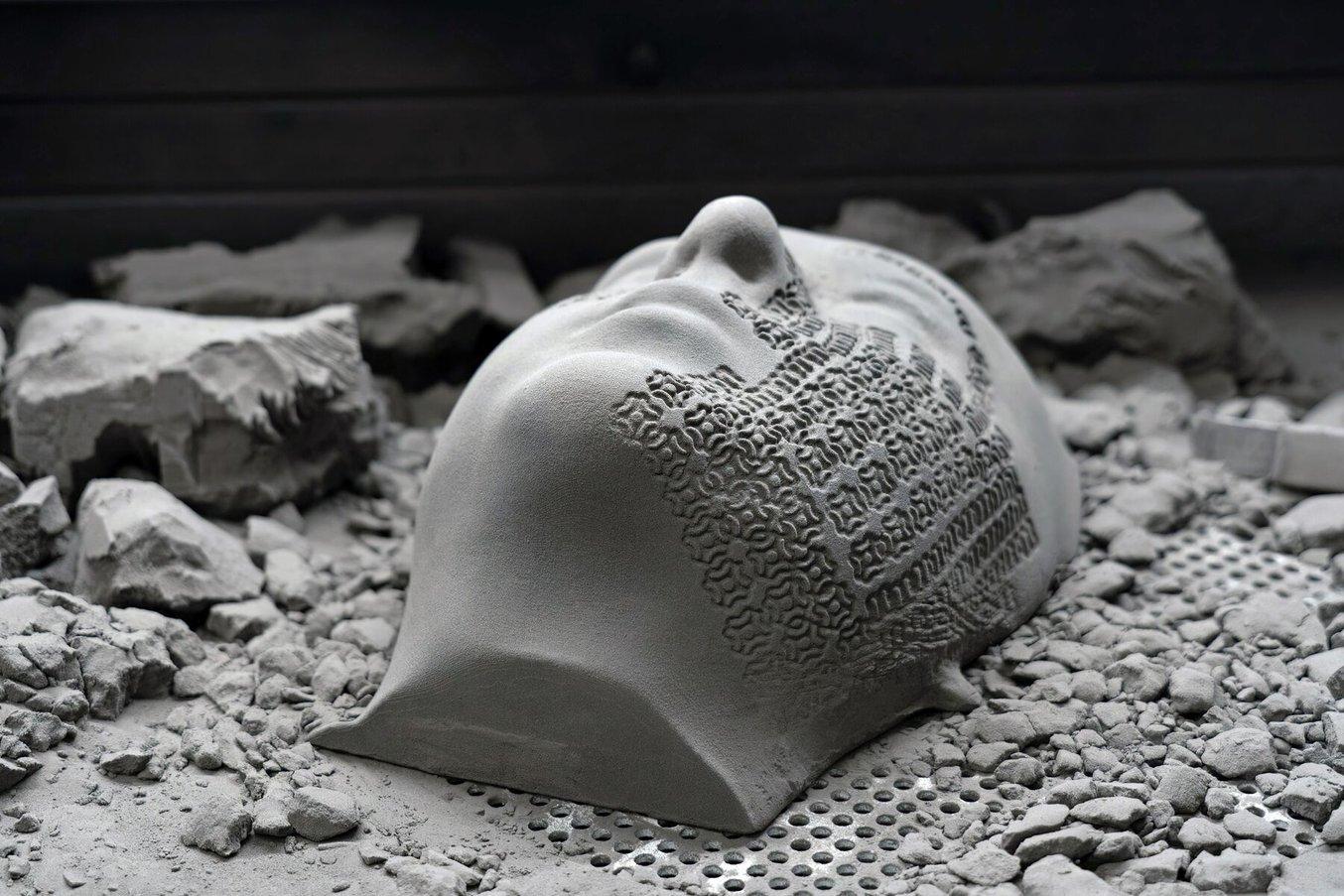
The masks are 3D printed on a Fuse Series SLS 3D printer.
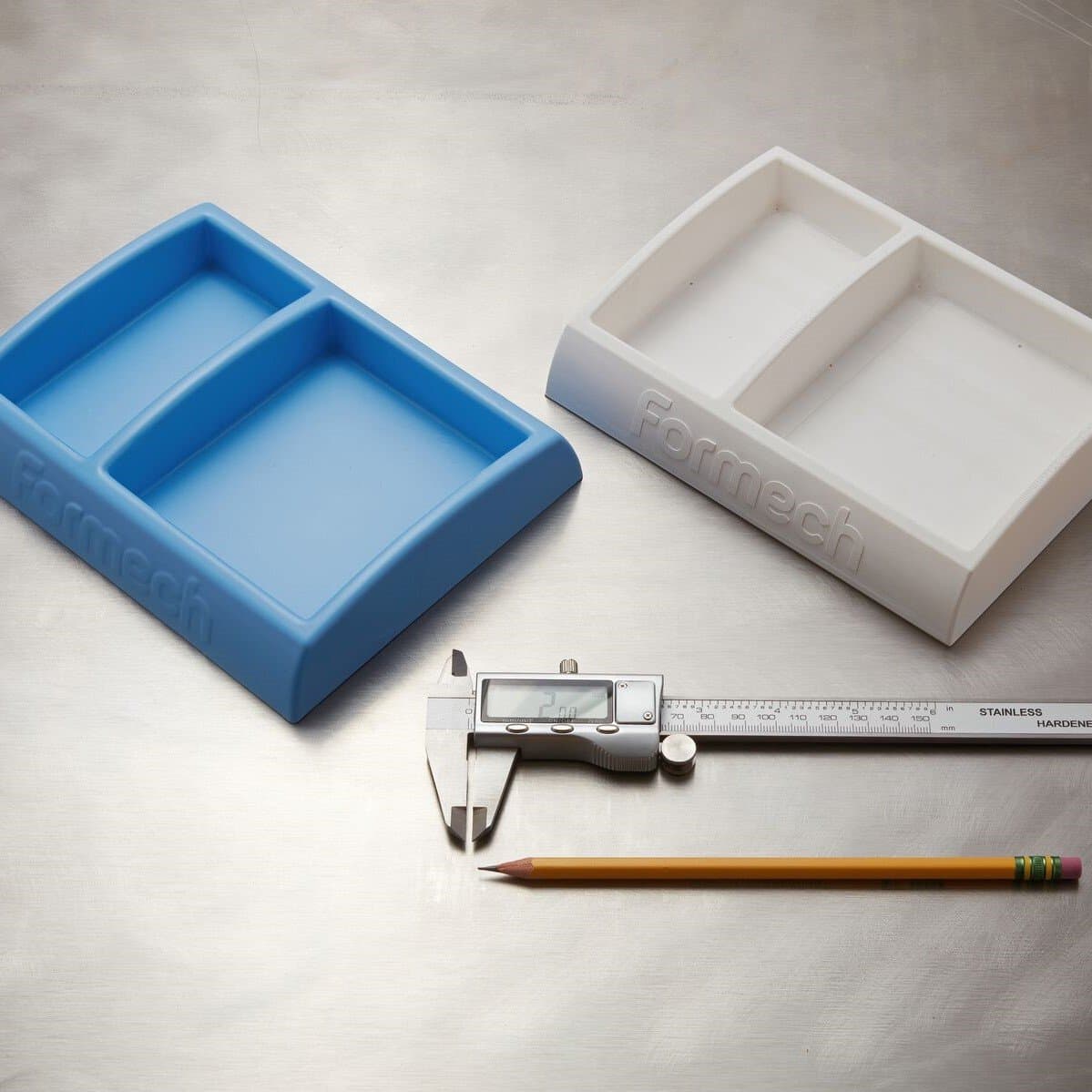
Rapid Thermoforming With 3D Printed Molds: A Practical Guide
Accelerate product development, reduce costs and lead times, and create custom or low volume products with ease by combining 3D printed rapid tooling and thermoforming.
As subcontracting the masks is expensive and can take several days, the center was looking for a solution that can be implemented directly in the center. “This type of development is not compensated by the health agency for our facility. We were able to work on this because of donations, and because the Formlabs machine which was recommended to us was affordable enough that it fit within our means,” said Mr. Veauville.
More Comfort and Better Outcomes for the Patients
“[The new workflow] is faster and also more comfortable for the patient because they don't feel the plaster strips on their face. The results of 3D printing have always been satisfactory. Where we needed to think as a team, and especially to provide training to the orthoprosthetists, was how to place the DMDG devices with sufficient precision. It is necessary to place these reliefs of different shapes in a very precise way on the scar according to the zones which need it,” said Dr. Arias.
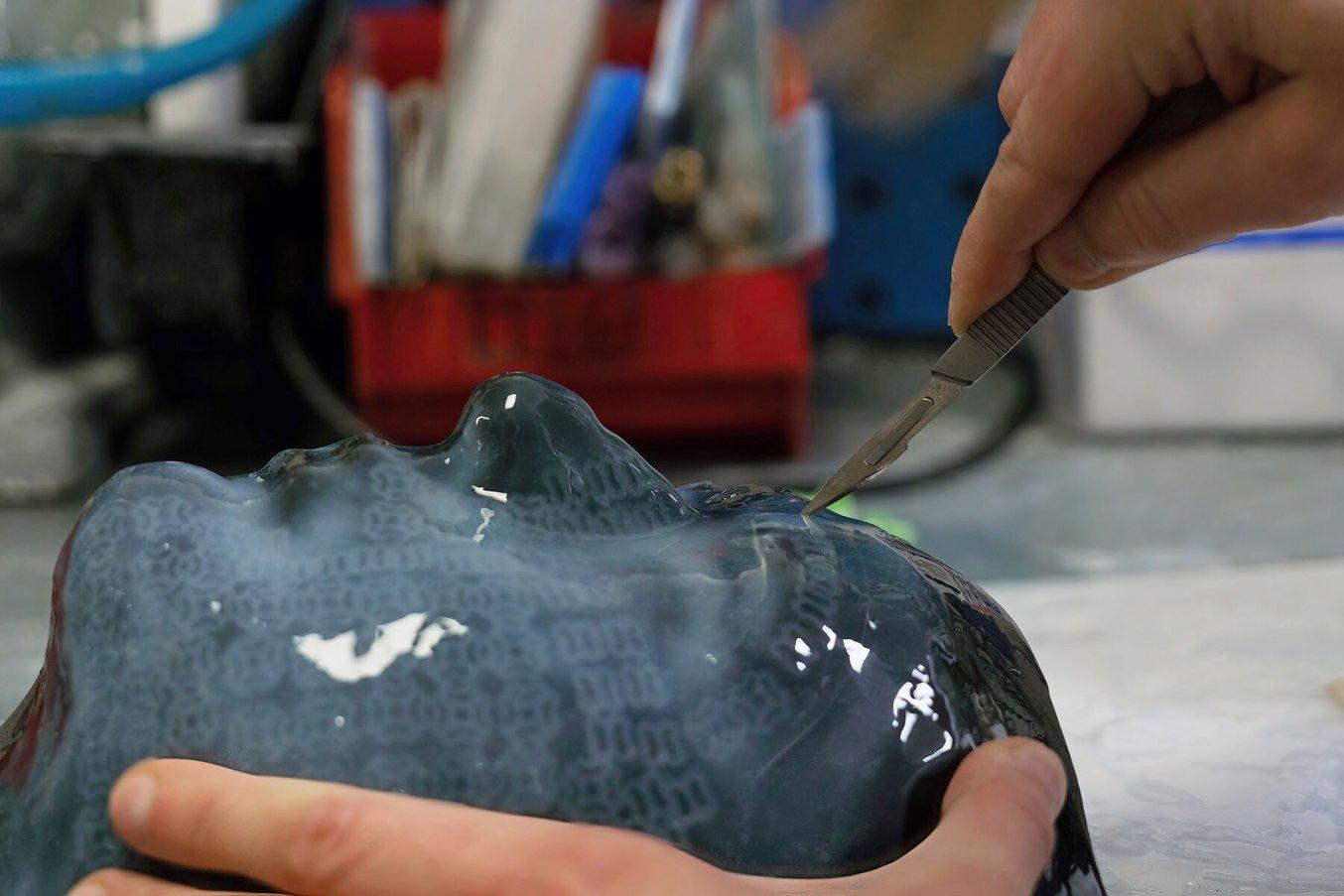
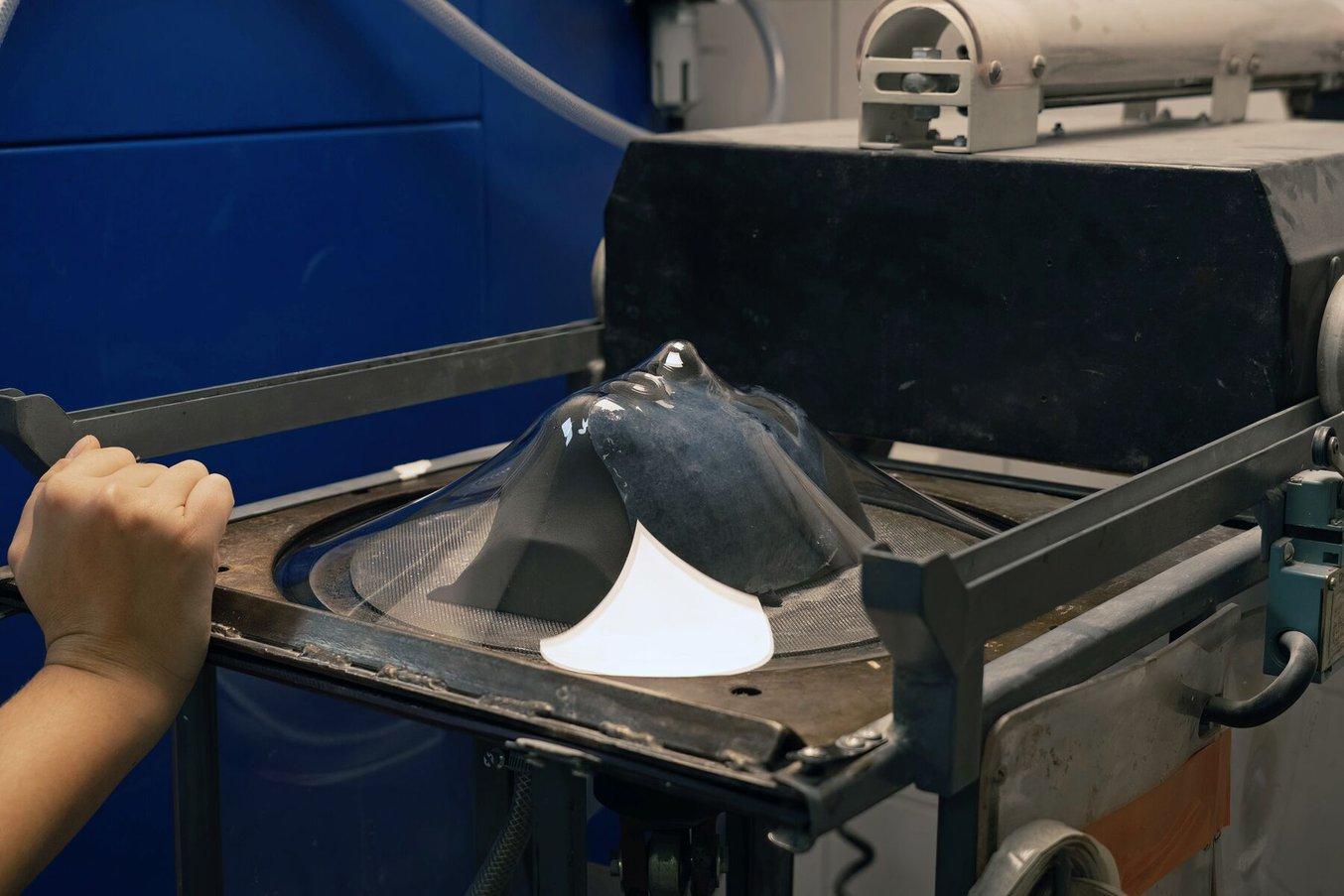
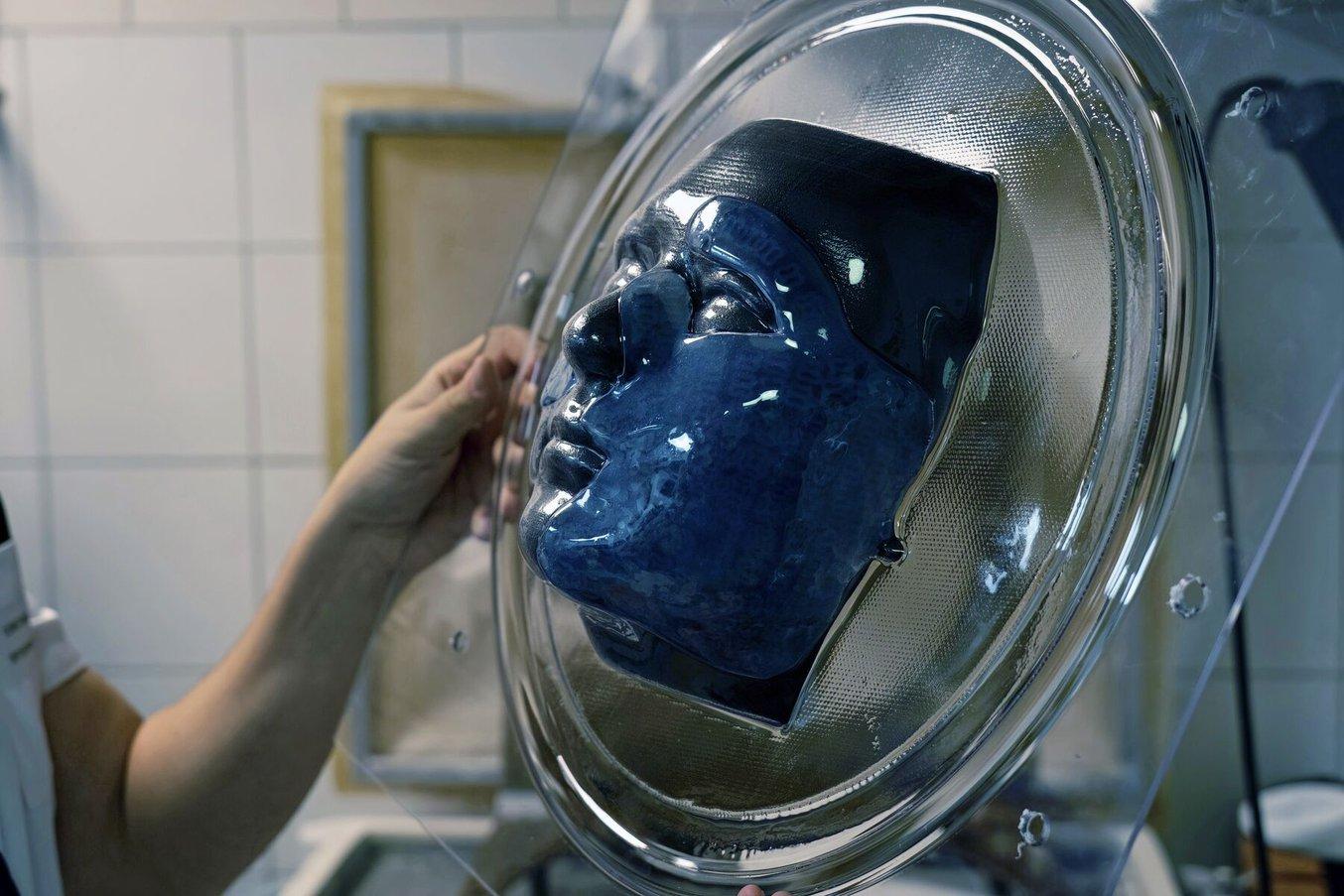
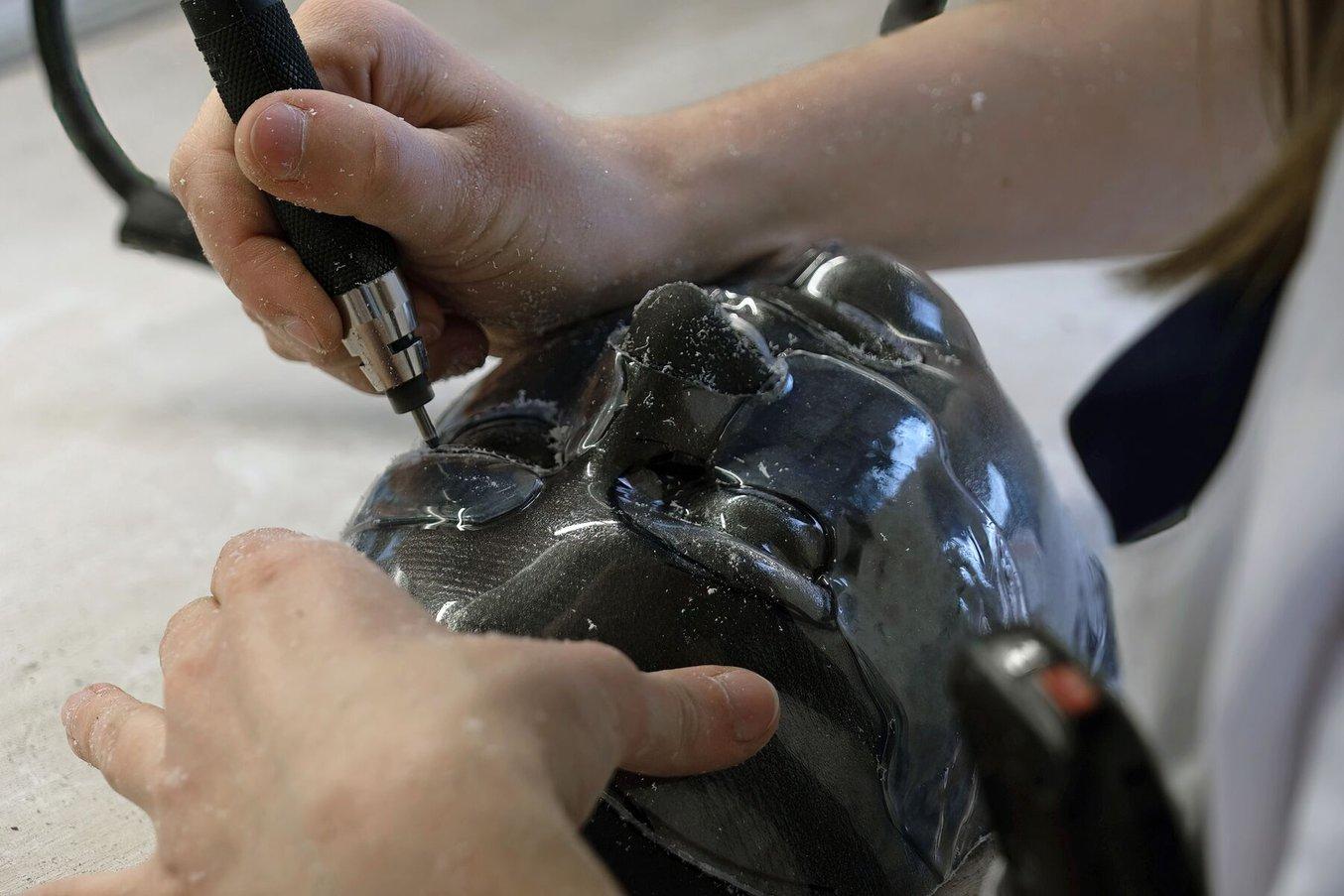
The reliefs are handcrafted on 3D printed molds out of silicone, which then serves as the positive for thermoforming the final mask out of a transparent plastic sheet.
Depending on the extent of their injuries and the rehabilitation required, patients often stay in the center for more than one year. During this time, they live on the site and continue with their studies. They also go on group outings, attend concerts, and get prepared for life outside, as initially, it can be difficult to do so without worrying about other people staring at them.
“I've been wearing it every day for over a year now. At first, it's a bit weird, it's not very pleasant, you want to take it off, and it feels a bit itchy. But after that, you get used to it and I can say that when I don't have it on, it almost pulls me, so I almost prefer to have the mask on. I feel that it has an effect on my skin, I really see the difference because a year ago my skin was not like this at all, I was redder, puffier, and much more rigid, so I feel that the mask really has positive effects.”
Laura Weibel, Patient, Centre Romans Ferrari
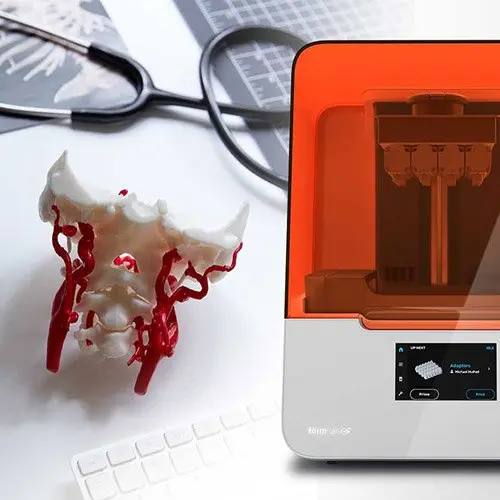
Intro to Medical 3D Printing
Join Formlabs for this introduction to learn best practices for medical 3D printing and see the latest Formlabs Medical ecosystem, including multiple new medical-grade products!
Making the Innovation Widely Known So Patients Globally Can Benefit From a Better Treatment
“Since we set up [the new workflow] barely a year ago, we have already exceeded a hundred masks. We are able to produce compressive devices that we could not produce using conventional methods. Our fitters have mastered the tool and the process, and are now producing these devices whenever they’re necessary.”
Christophe Debat, General Manager, Centre Romans Ferrari
Romans Ferrari currently treats approximately 25% of severely burned children in France and they have worked with clinics within France and in other countries such as Italy and Jordan.
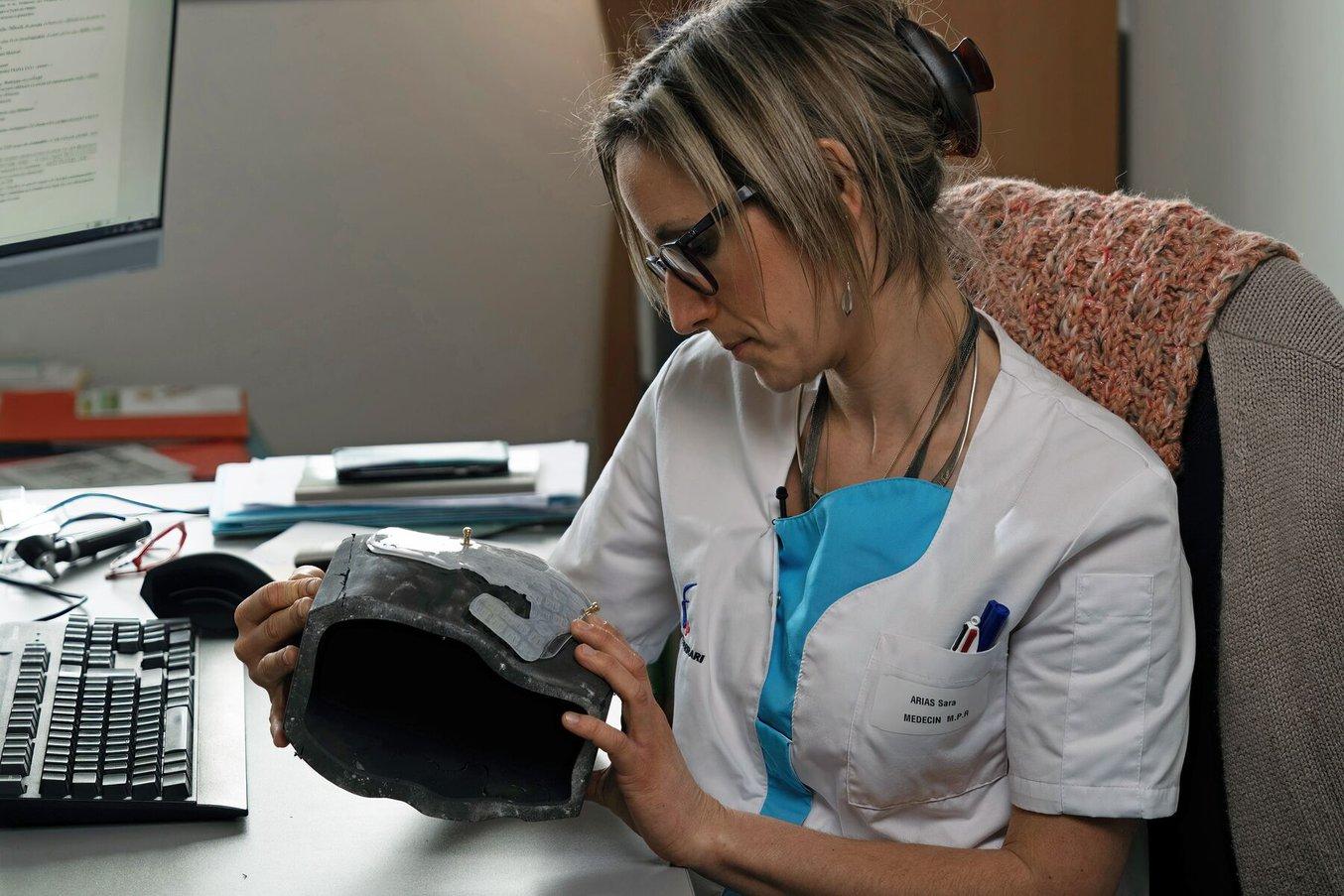
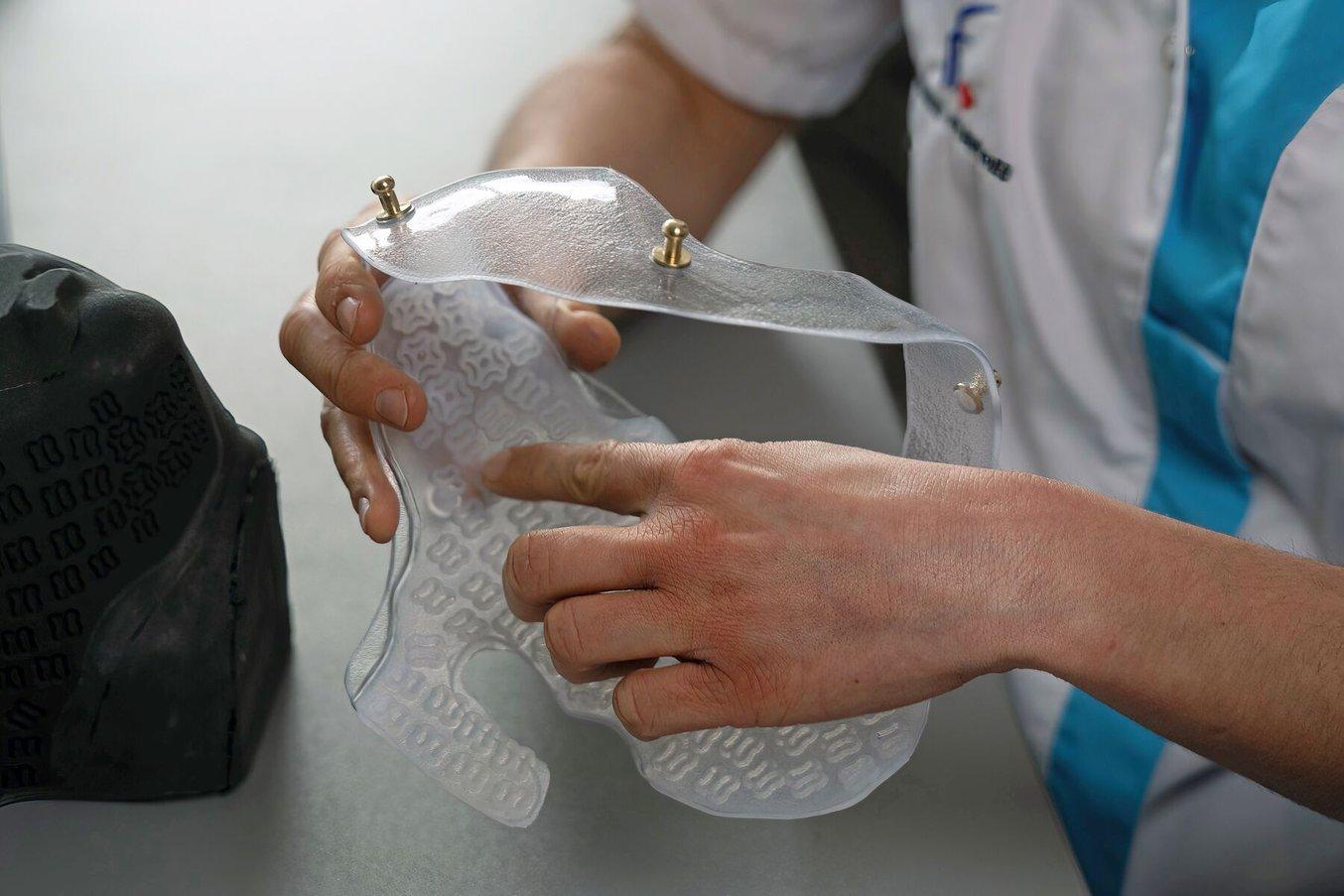
Romans Ferrari’s team has treated over 100 patients using the new digital workflow and now they’re hoping to make their innovation available for more patients.
Thanks to the use of digital technologies, it has also become possible to provide treatment for patients who live far away from Lyon. Recently, Romans Ferrari collaborated with the organization Doctors Without Borders in Jordan, where doctors scanned the face of a patient and sent the scan file to the pediatric rehabilitation center. The team was then able to manufacture compressive devices in France and ship them to Jordan.
“Due to our extensive experience, we aim to provide this technique to all patients, as the methods and tools we produce are unique and far more efficient than those available elsewhere. The idea is to be able to find partners with whom we will have the scanner, the doctor who will design the medical devices, and we manufacture them at cost, so others can also benefit from this innovation.”
Christophe Debat, General Manager, Centre Romans Ferrari