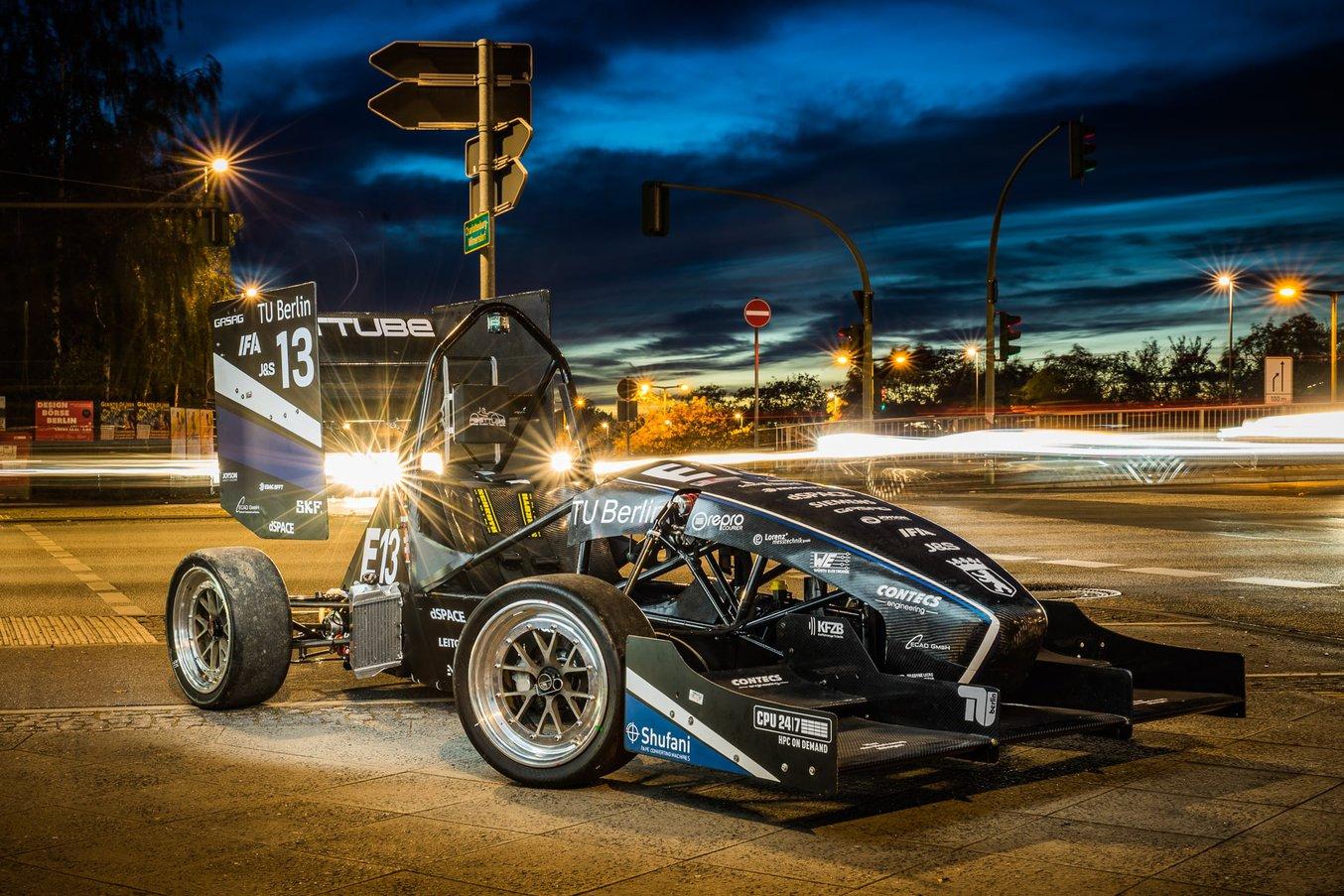
The Formula Student is a yearly engineering design competition in which student teams from around the world build and race formula-style cars. The Formula Student Team TU Berlin (FaSTTUBe) is one of the largest groups; 80 to 90 students have been developing new racing cars every year since 2005.
For the first time, this season they are building three models: combustion, electric and autonomous. From fall to summer, they have a year to design, manufacture, assemble, and test the vehicles before the races. Teams are evaluated on the business model, design concept, cost report, and racing performance in particular for power, efficiency, and endurance.
This year the team added a Form 3 SLA 3D printer to their toolset that they have used to save time, costs, and create parts that would not be possible any other way:
-
Prototypes: they print prototypes for various parts such as mountings of the anti-roll bar or stakeholders of the HV Battery.
-
Molds to manufacture carbon fiber parts: the team printed a dozen molds to fabricate carbon fiber parts that could not have been made otherwise.
-
End-use parts: about 30 final parts of the cars are directly 3D printed from button holders, shifters of the steering wheel to hose and sensor connectors of the cooling systems.
Niklas Werner, the Technical Manager and Felix Hilken, the Head of Aerodynamics and Carbon Manufacturing, introduced us to the FaSTTUBe facilities and walked us through these applications.
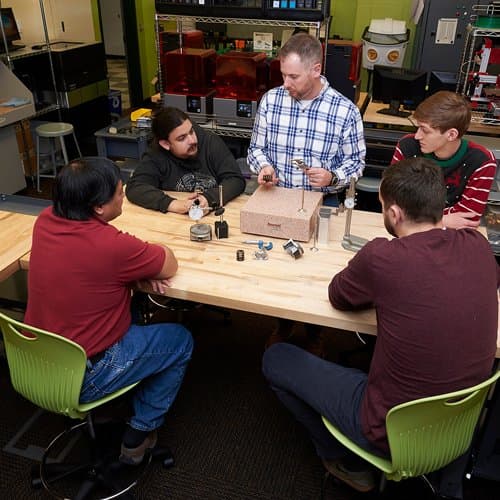
Guide to 3D Printing In Education
In this guide, we’ll discuss the benefits of 3D printing in education, from improved student collaboration to workforce development and empowered creativity.
Hand Laminating Carbon Fiber Parts on 3D Printed Molds
One of the most iconic parts of any race car is the steering wheel. Last season, the team used laser cutting to create a carbon plate and selective laser sintering (SLS) to create the grips and the body that houses the electronics.
Since reducing weights is essential in the construction of racing cars, they tried to print the grips hollow, but it would not be strong enough to bear the grip of the driver. This year they decided to fabricate the parts from carbon fiber, which is a great material to lower weight while maintaining or increasing strength.
Felix developed a workflow that employs 3D printed molds for wet lay-up lamination that is a great way to start fabricating carbon fiber parts with minimum supplies.
Watch the video to see how the carbon laminating process works.
By using carbon fiber, the team reduced the weight of the steering wheel housing from 120 g to 21 g. Felix needed a day to design and build the mold. They were able to push the design to geometries that would be extremely difficult to manufacture traditionally.
“The great thing about 3D printing is that a complex shape is as easy to do as a simple one, it requires the same amount of work and equipment. Some of the features on here can literally not be done with any other process in an economical way,” said Hilken.
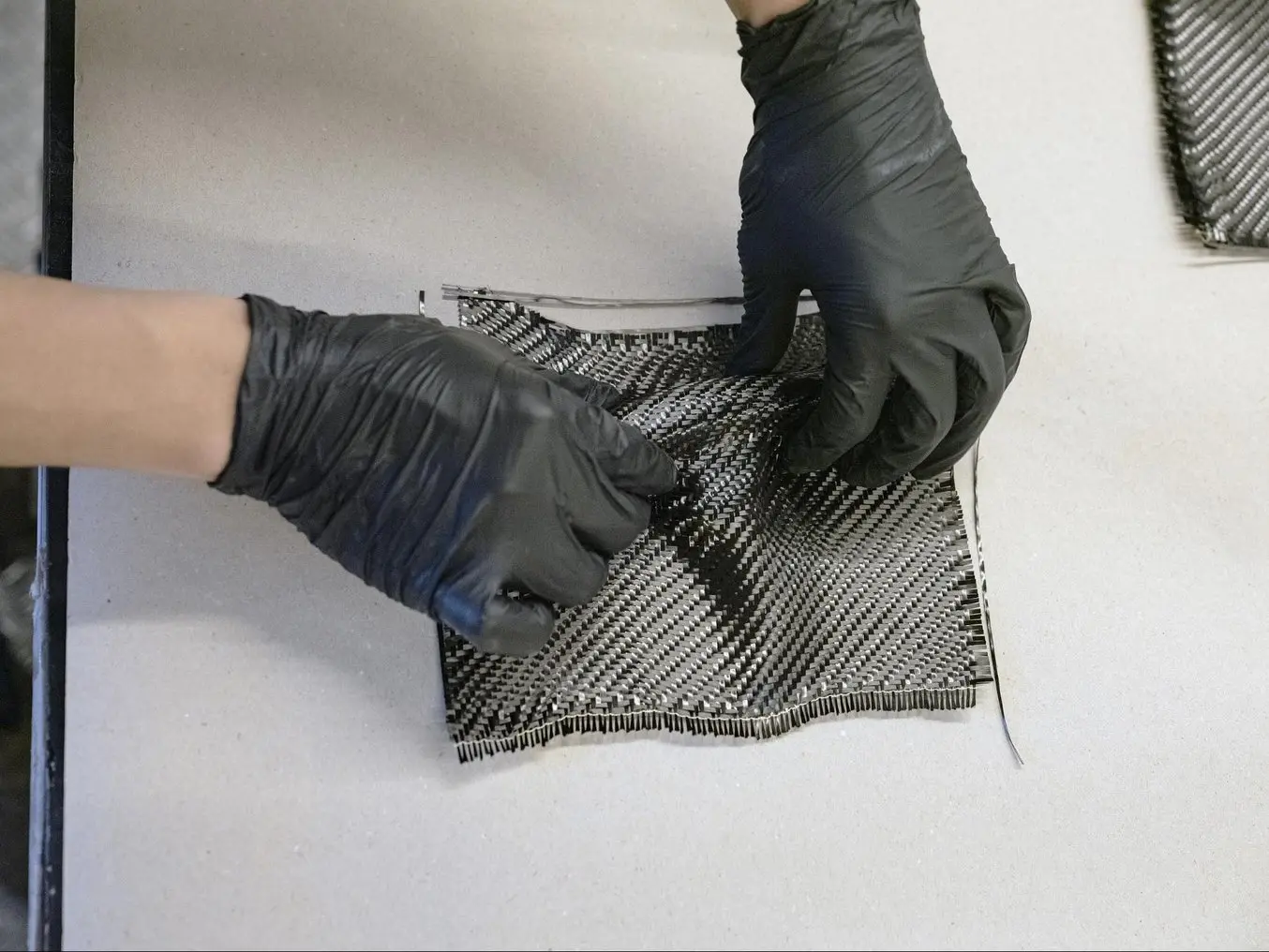
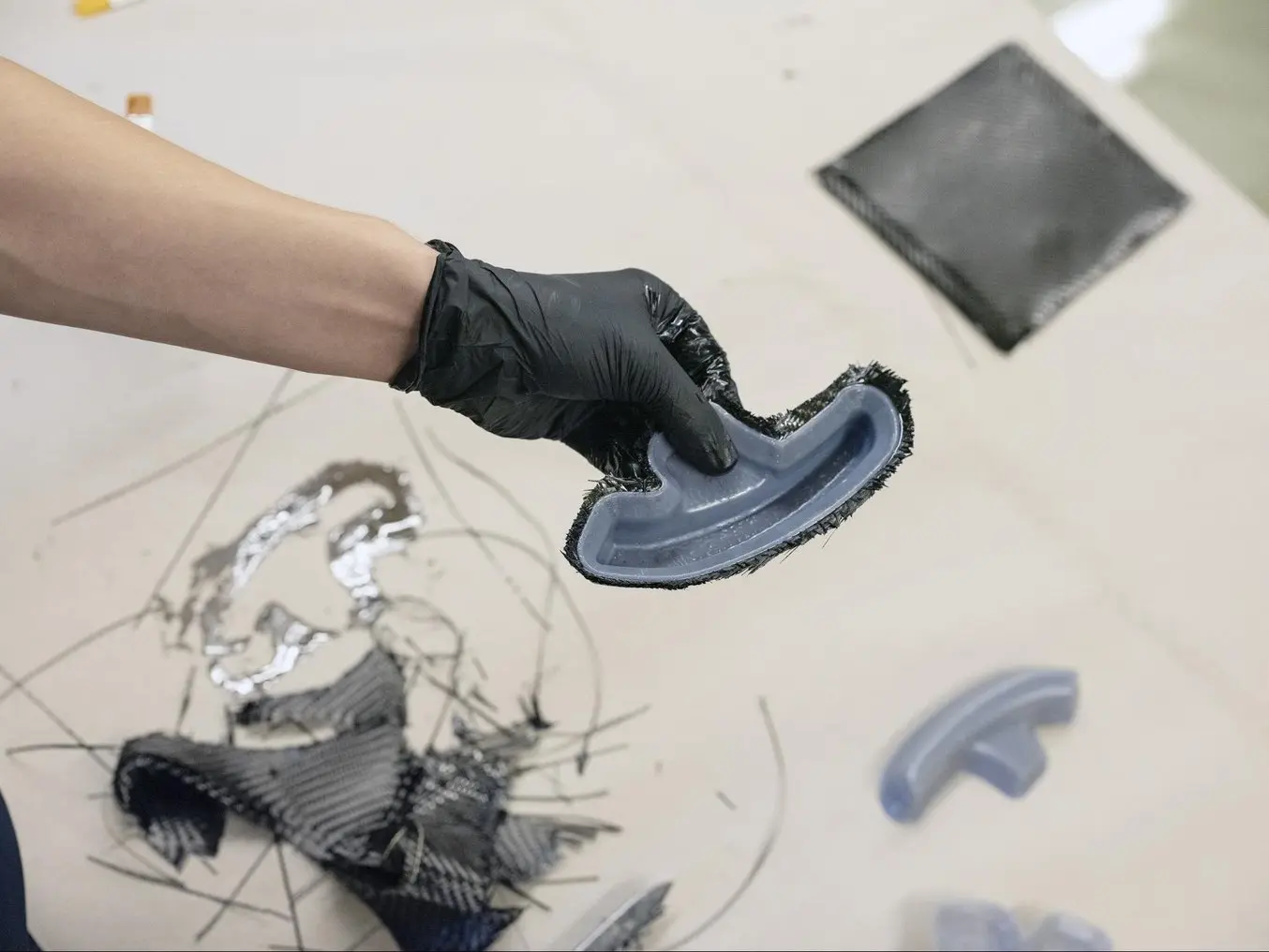
Felix laminated three layers of carbon fiber on a 3D printed mold and then used another negative mold to press the layers together.
Felix used Tough 1500 Resin because it balances elongation and modulus. Parts printed in this material can bend significantly and quickly spring back to their original shape, which facilitates the demolding of the part. With this technique, Felix estimates that one mold could be used to fabricate about ten parts. As this is a manual process, it depends on how meticulous the operator is: the mold can end up with stuck fibers or damages from the separation process.
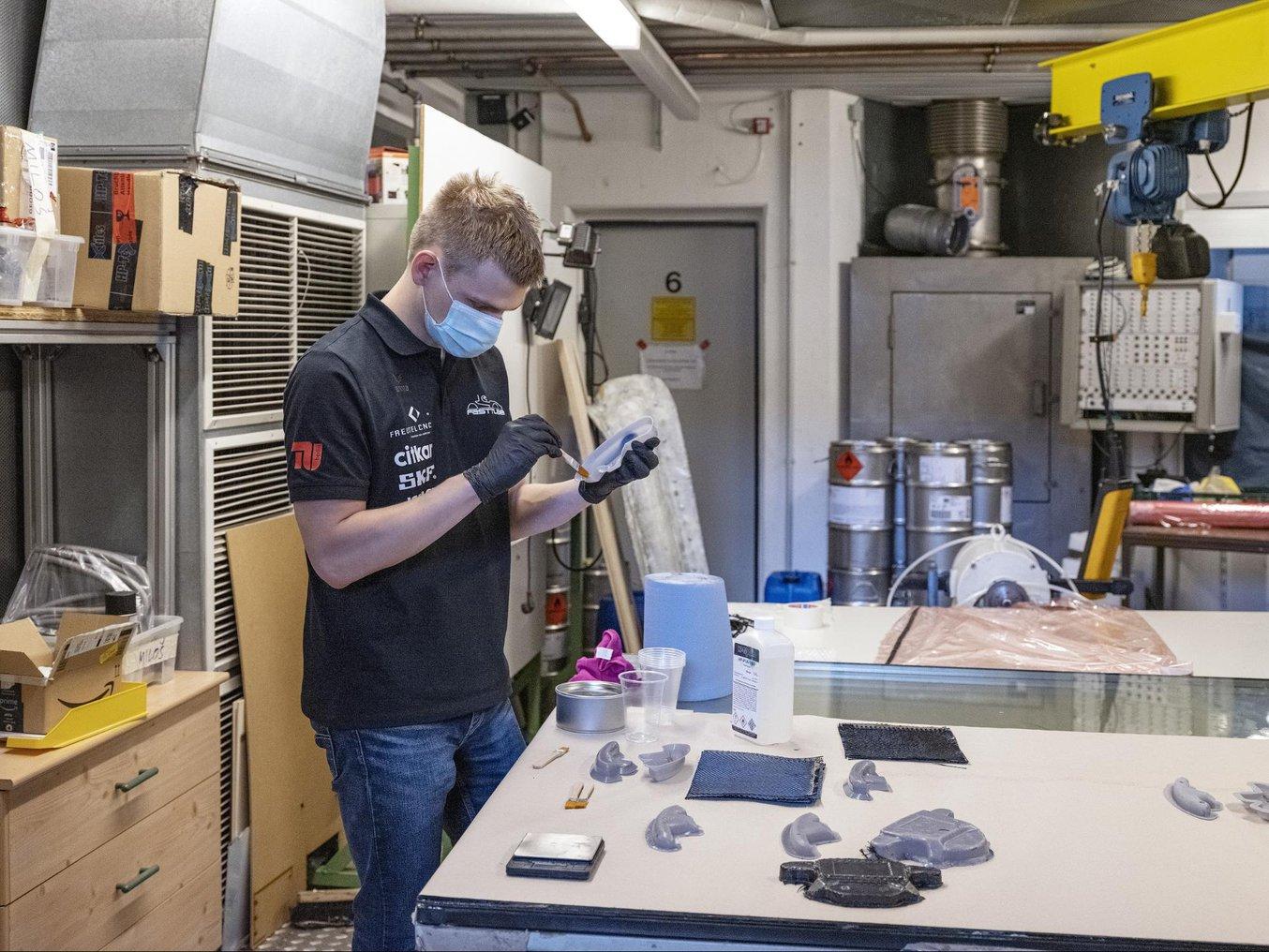
Wet lay-up lamination with 3D printed mold is a great way to start fabricating carbon fiber parts with minimum supplies.
Without 3D printing, the team would have had to outsource the CNC milling of an aluminum mold, which is expensive, has a long lead time, and requires specialized tools.
“I would have CNC machined the mold, but I would need to get specialized tools, and wait to get a slot on the machine. But I could not even do this geometry, in particular some of the small corners. I would need to use a design that doesn't have any screws in it, so the part would not be sensitive to positioning,” said Felix.
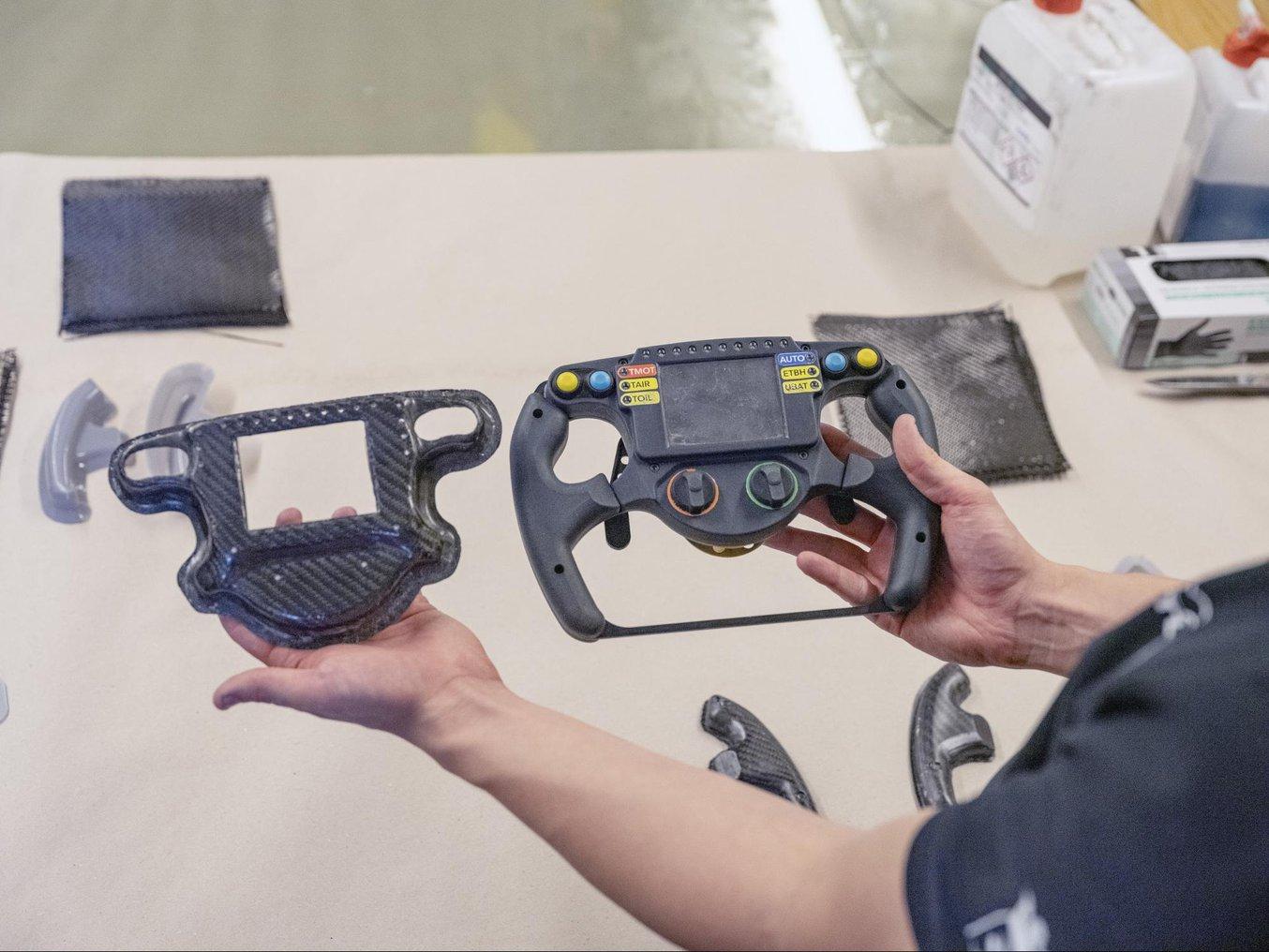
The new carbon chassis (left) next to the assembled steering wheel (right) from last year.
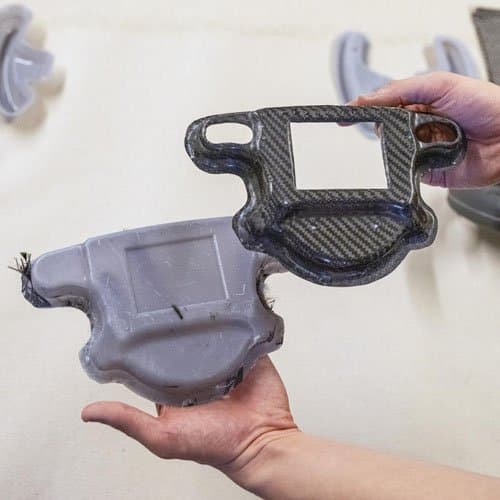
Carbon Fiber Parts Manufacturing With 3D Printed Molds
Download this white paper for composite mold design guidelines and step-by-step guides to the prepreg and hand laminating methods to create carbon fiber parts.
Costs and Lead Time Analysis
3D printing the molds for hand laminating carbon fiber parts helped the team drastically reduce costs and lead time. Here is a comparison between outsourcing the metal mold and 3D printing it in house for the steering wheel. We take labor costs and material costs into account and we assume an engineer’s billing rate of $200 an hour.
Outsourced CNC machined mold | In-house 3D printed mold | |||
---|---|---|---|---|
Equipment | Carbon fiber, resins, tools, vacuum bag | Carbon fiber, resins, tools, vacuum bag Form 3 printer, Tough 1500 Resin | ||
Mold Production time | 4-6 weeks | 2 days | ||
Labor Costs | 0 | $300 | ||
Material costs | 0 | $10 | ||
Total Mold Production Costs | $900 | $310 |
End-Use Parts From Shifter Pedals to Cable Collectors
The grips and the body are not the only parts on the steering wheels that leveraged 3D printing. In fact, besides the molded carbon parts, the carbon plate, and the electronics, all the other components of the steering wheel are 3D printed on the Form 3 as well.
The button holders, shifter pedals, mounts of the shifter pedals, and the switches were printed with Tough 2000 Resin for its toughness and durability and then spray painted for a uniform color.
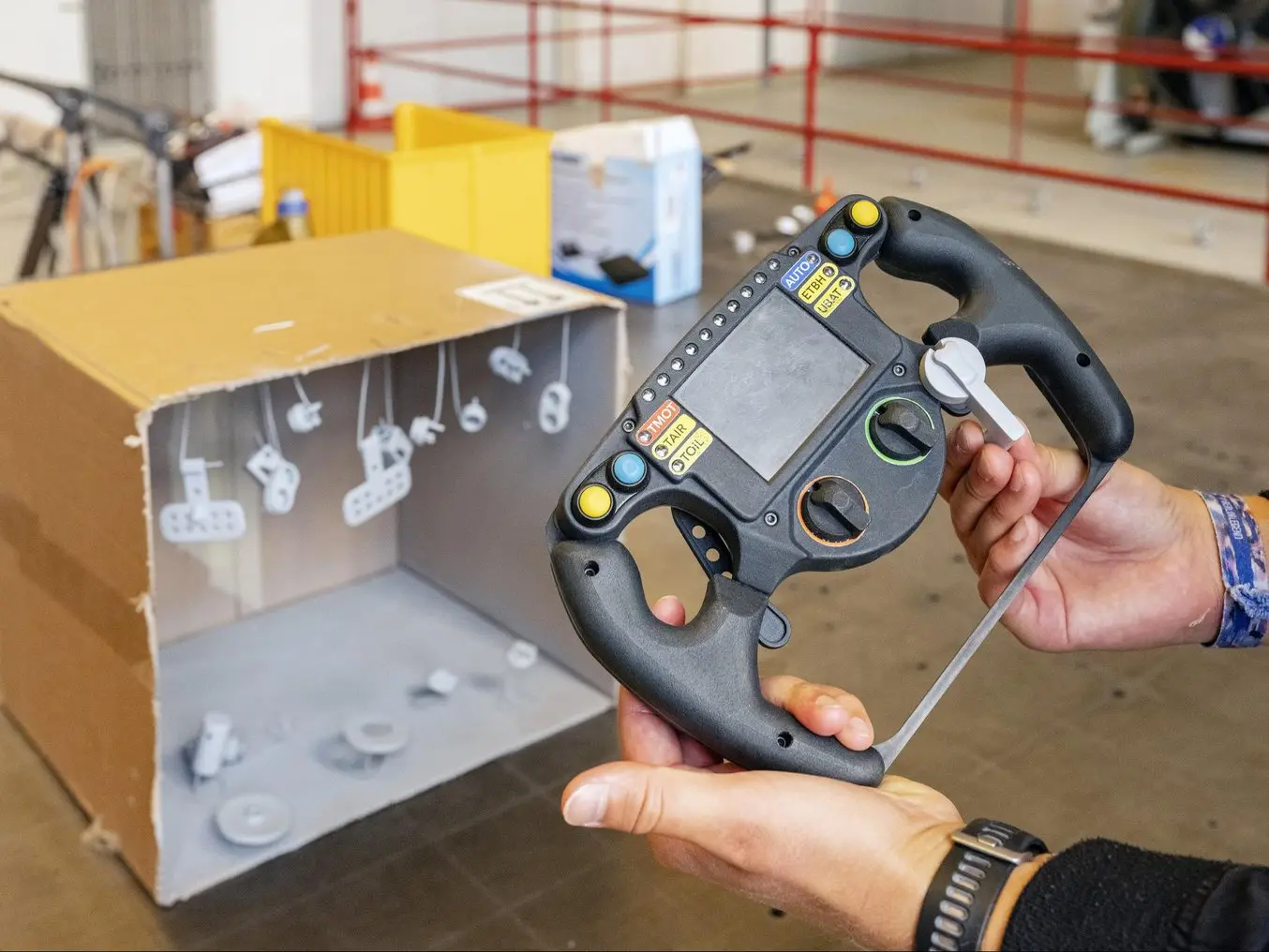
Buttons, button holders, shifter pedals, and the mounts of the shifter pedals on the new steering wheel are all directly 3D printed.
Altogether, the car has around 30 SLA printed parts currently. For example, the team also printed cable collectors to neatly organize the cables in the wire harnesses. These are made out of Durable Resin that provides the flexibility to fit around the tubes of the metal chassis.
“Those are great for assembling the wire harness because they look nice and it's important to make a great first impression for the judges when they see it,” said Niklas.
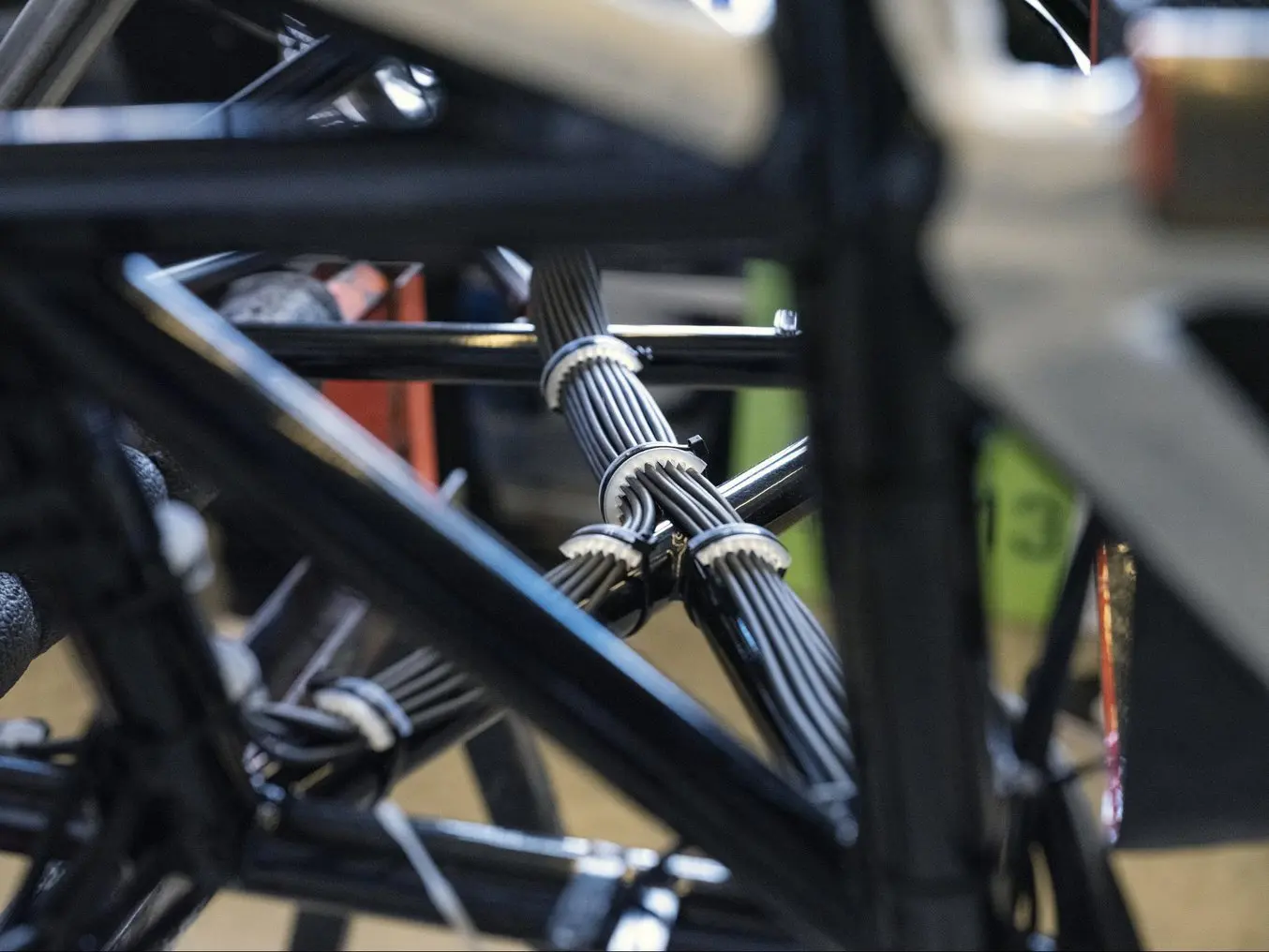
The 3D printed cable collectors help to neatly organize the cables in the wire harnesses.
There are some 3D printed holders and enclosures and the team is also planning to create other parts like the endings of the brake light and TSAL parts—lights in the electric vehicle, that show whether the system is running on high voltage.
Prototyping a Generative Designed Part Before Metal 3D Printing
It should come as no surprise that the team also used 3D printing for prototyping as well. For example, they prototyped the mount of the end valve on the front of the chassis, which is a complex part that was designed with topology optimization. The final part will be manufactured with metal 3D printing.
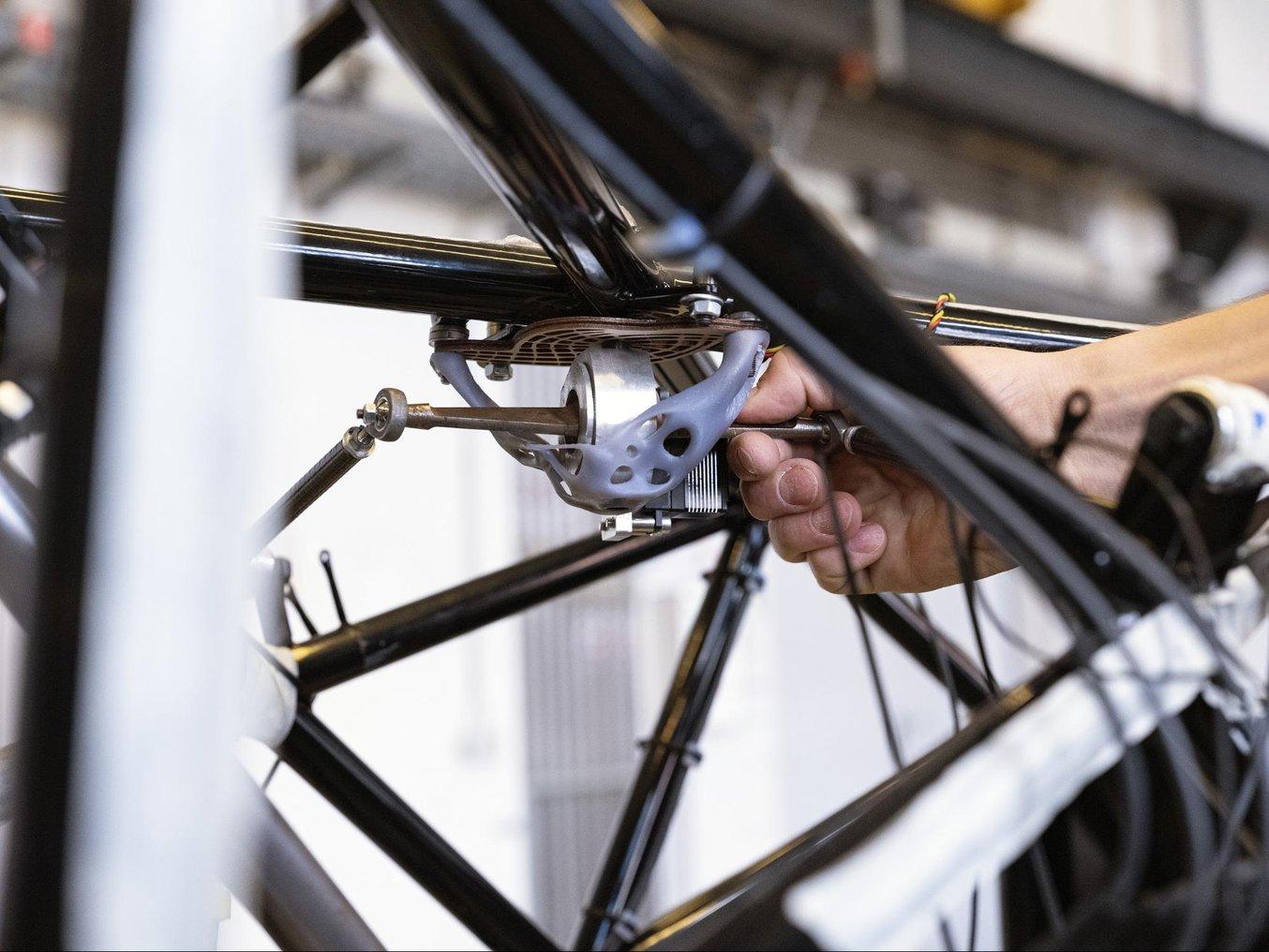
The team used 3D printing to prototype a complex topology optimized mount that will be 3D printed in aluminum.
“We printed it with Formlabs printer out of resin because it's not as expensive. We had the option to validate if it fits on the chassis or not. We saw that it does and now it's going to be made manufacturing in aluminum,” said Niklas.
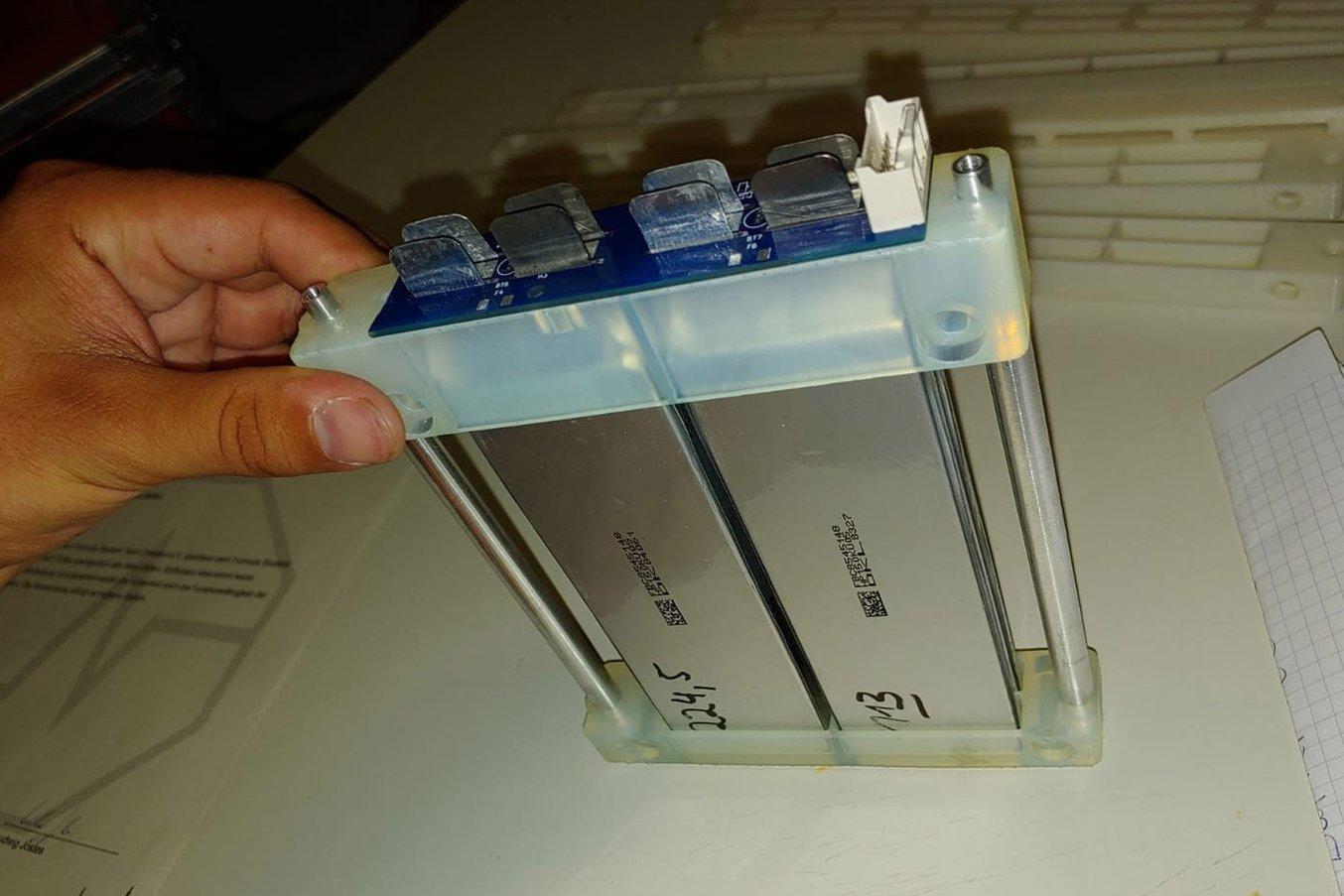
Holders for the electric race car’s battery cell were also prototyped with 3D printing.
Finalizing the Cars for the Racing Season

The team is currently still very much developing the three race cars so the range of applications where 3D printing is used will inevitably grow.
One of their most ambitious upcoming projects is creating the airflow intake out of carbon. This will be a larger part that will require 3D printing the mold in multiple parts, assembling it, and then hand laminating the part over the mold.
The three racing cars should hit the track for testing in the spring and Niklas, Felix, and the team hopes that the racing season can start once the COVID-19 restrictions are lifted.