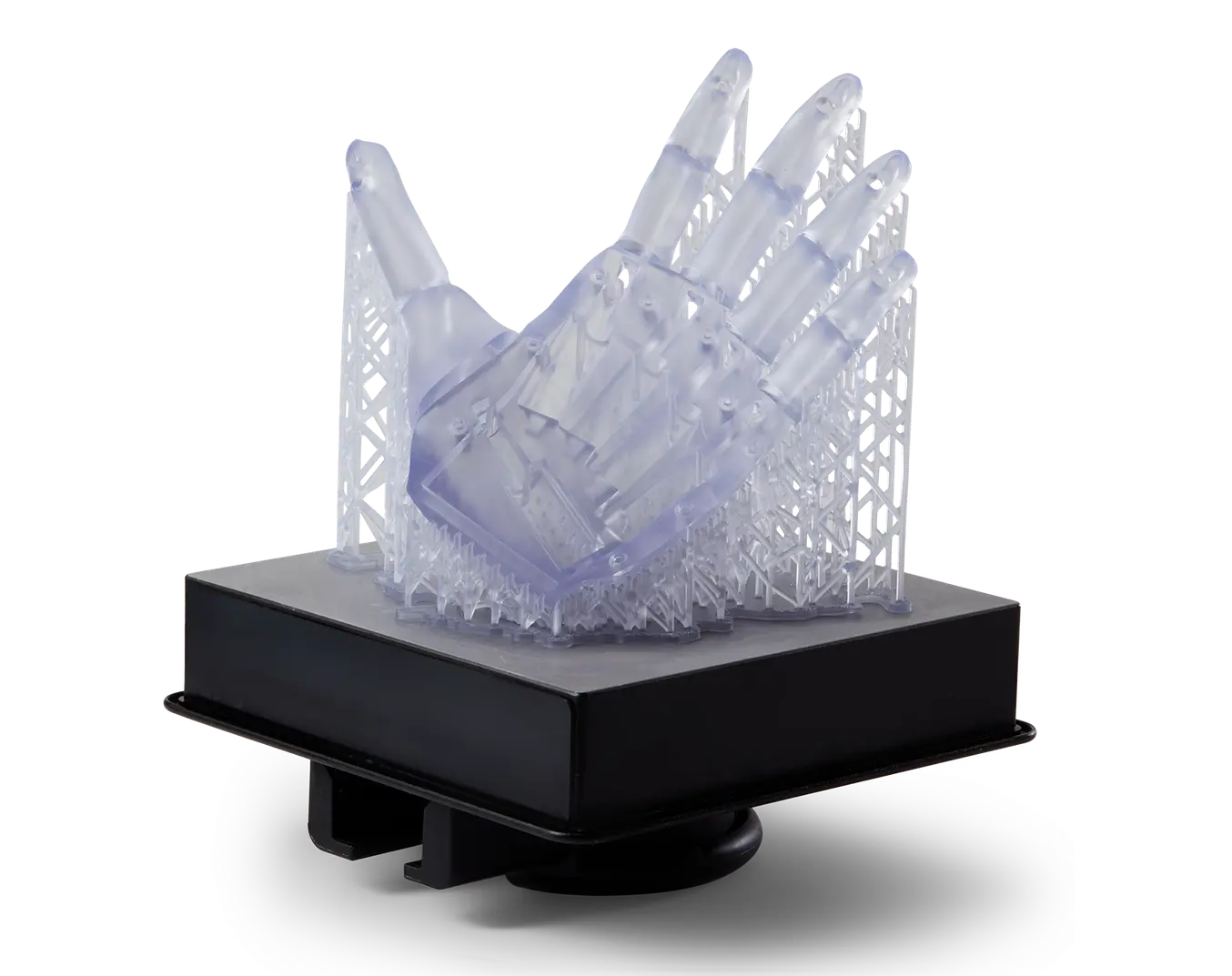
Why Choose Flexible 80A Resin?
Create silicone, urethane and rubber-like parts. Produce flexible parts in-house in a matter of hours, replacing outsourcing and molding.
Elastomeric
Leverage bendable parts that return to shape slowly.
Soft and Strong
Stretch and compress parts through repeated cycles without cracking.
Transparent
Create objects that are clear, providing visibility into the model.
Durable
Support user testing with looks and feels like prototypes that can be put to the test.
Applications
Flexible 80A Resin is ideal for hard, flexible prototypes and a great alternative to mold making.
Consider Flexible 80A Resin for:
Material Properties*
Flex 80A Resin
Ultimate Tensile Strength
Stress at 50% Elongation
Stress at 100% Elongation
Elongation
Tear Strength
Hardness Shore A
* Material properties may vary based on part geometry, print orientation, print settings, and temperature. Data was obtained from parts printed on a Form 3 with 100 µm Flexible 80A settings, washed in a Form Wash for 10 minutes, and post-cured at 60°C for 10 minutes in a Form Cure.
Post-Processing
Form Wash Settings
10 minutes + 10 minutes
Wash parts printed in Flexible 80A Resin in two cycles, preferably using fresh solvent for the second wash. When washed in TPM, Flexible 80A Resin remains waxy when printed at any layer thickness and requires post-cure. Post-curing removes the waxiness.
Form Cure Settings
10 min
60 °C
For parts printed in an engineering-focused resin (such as those in the Rigid, Tough & Durable, and Flexible & Elastic families), post-curing ensures that the parts reach their optimal mechanical properties and can function as designed. There is only one recommended post-curing time for Flexible 80A Resin.