Conception de vélos : l'impression 3D transforme le processus d'innovation chez The Rider Firm
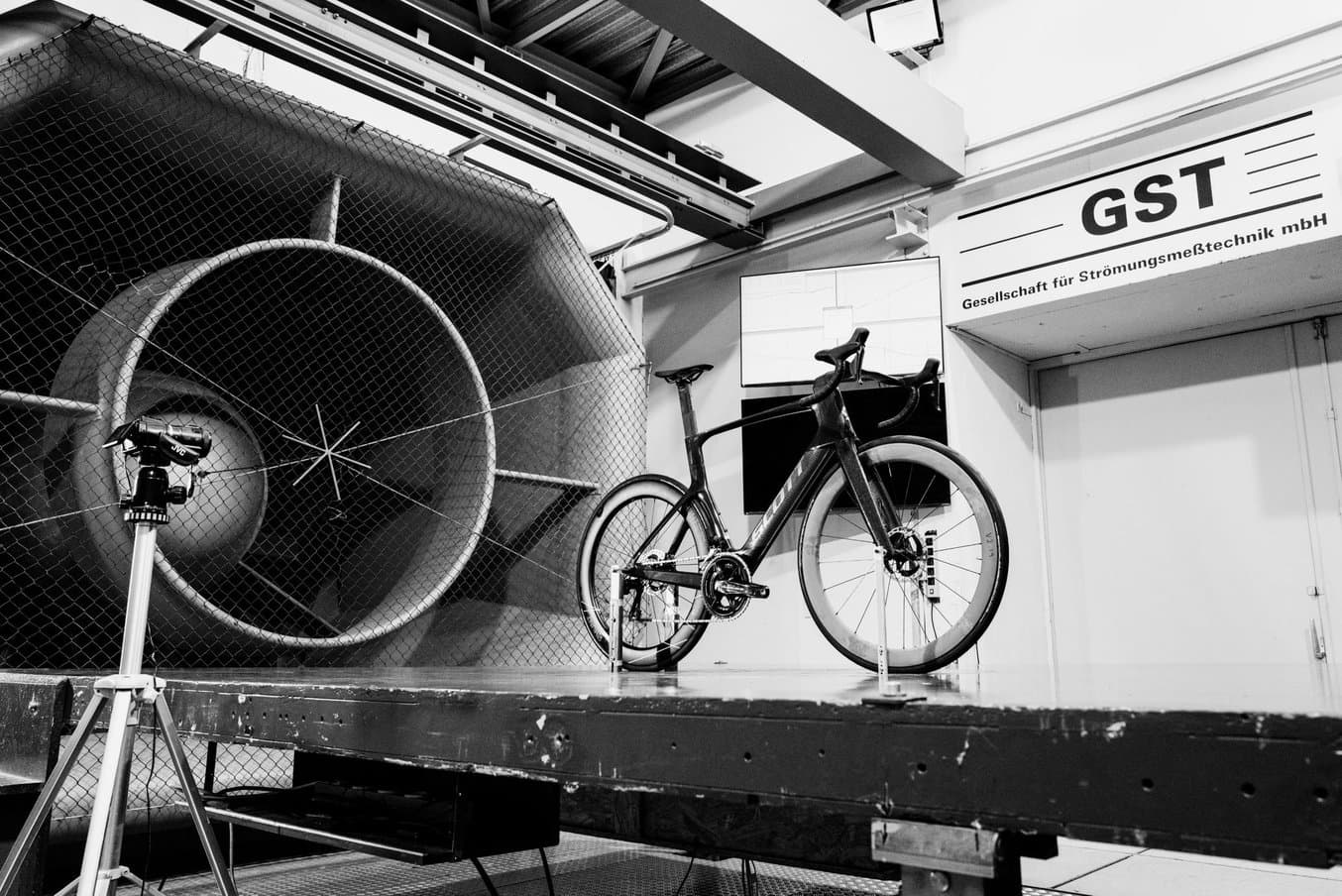
Hunt Bike Wheels teste ses profils de jantes dans la soufflerie de Friedrichshafen, dans le sud de l'Allemagne
Alors que le monde adopte de plus en plus le vélo pour se rendre au travail, explorer la nature, s'entraîner ou participer à des courses, il est primordial que les fabricants de vélos suivent l'évolution constante des tendances et des développements technologiques. The Rider Firm est la société à l'origine de l'une des plus grandes marques mondiales de roues destinées au consommateur direct, Hunt Bike Wheels, ainsi que d'autres marques de matériel, de composants et de vélos de pointe, notamment Privateer Bikes, Cairn Cycles et Dissent 133.
L'objectif étant de produire des vélos et des composants de haute performance à la portée de tous les cyclistes, le processus de développement doit être plus intelligent et plus efficace que celui des marques de vélos traditionnelles dotées de budgets plus importants. L'acquisition d'une imprimante 3D SLA grand format Form 3L a été la dernière mesure en date prise par l'entreprise pour stimuler l'innovation et redéfinir son flux de travail.
Si la plupart des opérations de fabrications se déroulent à Taïwan, The Rider Firm développe ses produits au Royaume-Uni, où les équipes s'appuient fortement sur la Form 3L, notamment pour le prototypage. Dan Hicks, ingénieur en développement chez Privateer Bikes et Patrick Brown, ingénieur en design chez Hunt Bike Wheels, nous ont donné un aperçu de leur flux de travail et de la façon dont la Form 3L aide les équipes d'ingénieurs à innover constamment et à lancer de nouveaux produits.
Hunt Bike Wheels : impression 3D de jantes prototypes fonctionnelles à l'échelle réelle pour des essais en soufflerie
Le nom Hunt Bike Wheels fait référence à la mission de l'entreprise, qui consiste à rechercher en permanence tous les petits détails qui améliorent le produit. L'équipe d'ingénieurs expérimentés travaille sans relâche pour créer des roues qui offrent des performances exceptionnelles sur différents terrains. Grâce à des recherches, des développements et des tests approfondis, ils visent à améliorer la vitesse, la stabilité et l'efficacité en optimisant l'aérodynamisme de leurs roues. Dans le cyclisme professionnel, chaque avantage compte : la différence aérodynamique entre les roues est minuscule, de l'ordre de 2 à 5 % à 45 kilomètres à l'heure, mais cette différence peut représenter les quelques secondes qui séparent la première de la dixième place.
Patrick Brown nous a expliqué le processus de développement des roues. Celui-ci commence par la conception par les ingénieurs de différents profils de jantes et par leur test à l'aide de la mécanique des fluides numérique (CFD, de l'anglais Computational Fluid Dynamics), qui est en fait une soufflerie virtualisée. L'analyse CFD permet à l'équipe d'identifier les profils de jantes les plus performants, qui seront ensuite testés en situation réelle à l'aide de prototypes imprimés en 3D.
Pour sa dernière paire de roues LIMITLESS, l'équipe a testé environ 45 profils de jantes différents par analyse CFD et a identifié ceux qui présentaient la plus faible traînée et les meilleures caractéristiques de maniabilité en cas de vent latéral. Ils ont fini par obtenir quatre roues avant et trois roues arrière qu'ils ont imprimées en 3D et testées dans le Windkanal de Friedrichshafen, dans le sud de l'Allemagne.
Grâce au grand volume d'impression de la Form 3L , les ingénieurs ont pu imprimer les roues de vélo en cinq ou six sections chacune, en fonction du nombre de trous de rayon utilisés dans les sections, et ont pu placer quatre sections de jante à la fois sur la plateforme de fabrication. Après post-polymérisation et post-traitement, les pièces imprimées ont été collées avec de la résine époxy et transformées en prototypes fonctionnels, assemblés avec des moyeux, des rayons et des pneus.
À propos de l'utilisation de Grey Pro Resin, Patrick Brown explique que les roues imprimées en 3D « sont un peu molles, mais elles peuvent supporter environ 65 % de la tension d'une paire de roues en fibre de carbone. Nous les fabriquons donc assez droites et précises ; elles sont alors assez bonnes pour la soufflerie. »
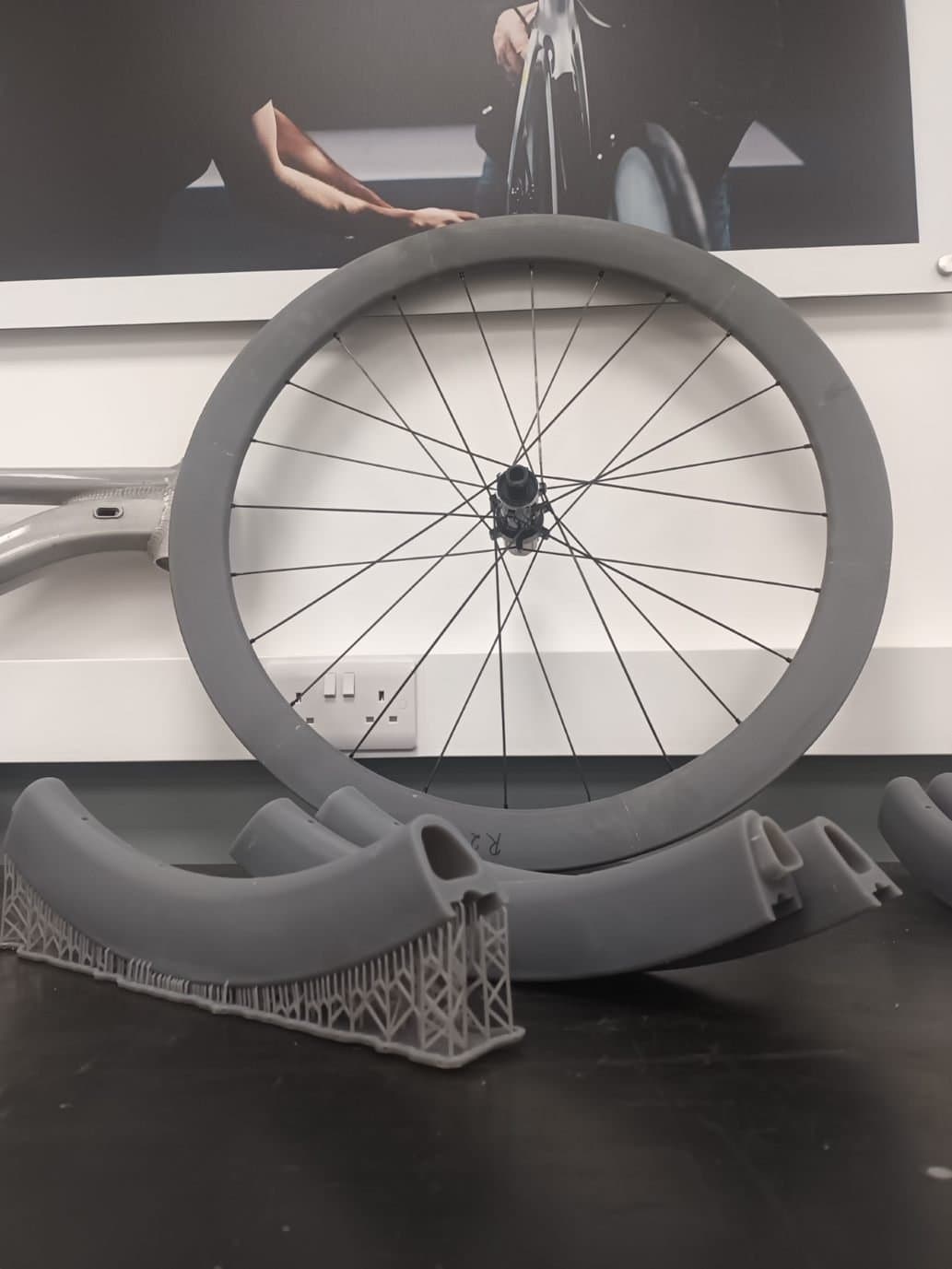
Grey Pro Resin est un matériau idéal pour le prototypage, car il peut supporter environ 65 % de la tension d'une paire de roues en fibre de carbone.
Par le passé, Hunt Bike Wheels faisait appel à un prestataire de services tiers pour imprimer en 3D les différentes sections de la roue, mais cela présentait de nombreux inconvénients. Tout d'abord, les ingénieurs devaient envoyer les profils de roues finalisés deux à trois mois à l'avance, ce qui ralentissait le processus et réduisait la marge de manœuvre. M. Brown a ajouté que pour leur dernier projet avec la Form 3L, ils avaient « obtenu les dernières impressions juste avant [leur départ] ». Cela signifie qu'ils ont pu faire des modifications jusqu'à la dernière minute. Les pièces sous-traitées n'étaient pas non plus assez solides pour gonfler le pneu à la pression requise, car certaines d'entre elles pouvaient se déchirer et devenir inaptes aux tests.
« Je peux maintenant simuler beaucoup plus longtemps et continuer à développer de nouveaux profils. Le fait d'avoir cette flexibilité en interne a été un grand avantage pour nous. »
Patrick Brown, ingénieur concepteur chez Hunt Bike Wheels
« Nous devons être en mesure de gonfler les pneus à une pression telle que le pneu prenne la bonne forme sur la roue. Il est très important pour nous que les pièces imprimées ne soient pas seulement précises d'un point de vue géométrique, mais aussi qu'elles soient suffisamment solides pour que nous obtenions le bon profil aérodynamique sur l'ensemble de la pièce. » Grey Pro Resin a répondu à ces exigences importantes avec une précision impressionnante, supportant jusqu'à 3,5 bars de pression des pneus gonflés. M. Brown a également souligné que l'excellent état de surface offert par Grey Pro Resin était un élément clé lors des essais aérodynamiques.
« [Dans la soufflerie], ils tournent sur un rouleau, la roue tourne donc à 45 kilomètres par heure ».
Patrick Brown, ingénieur concepteur chez Hunt Bike Wheels
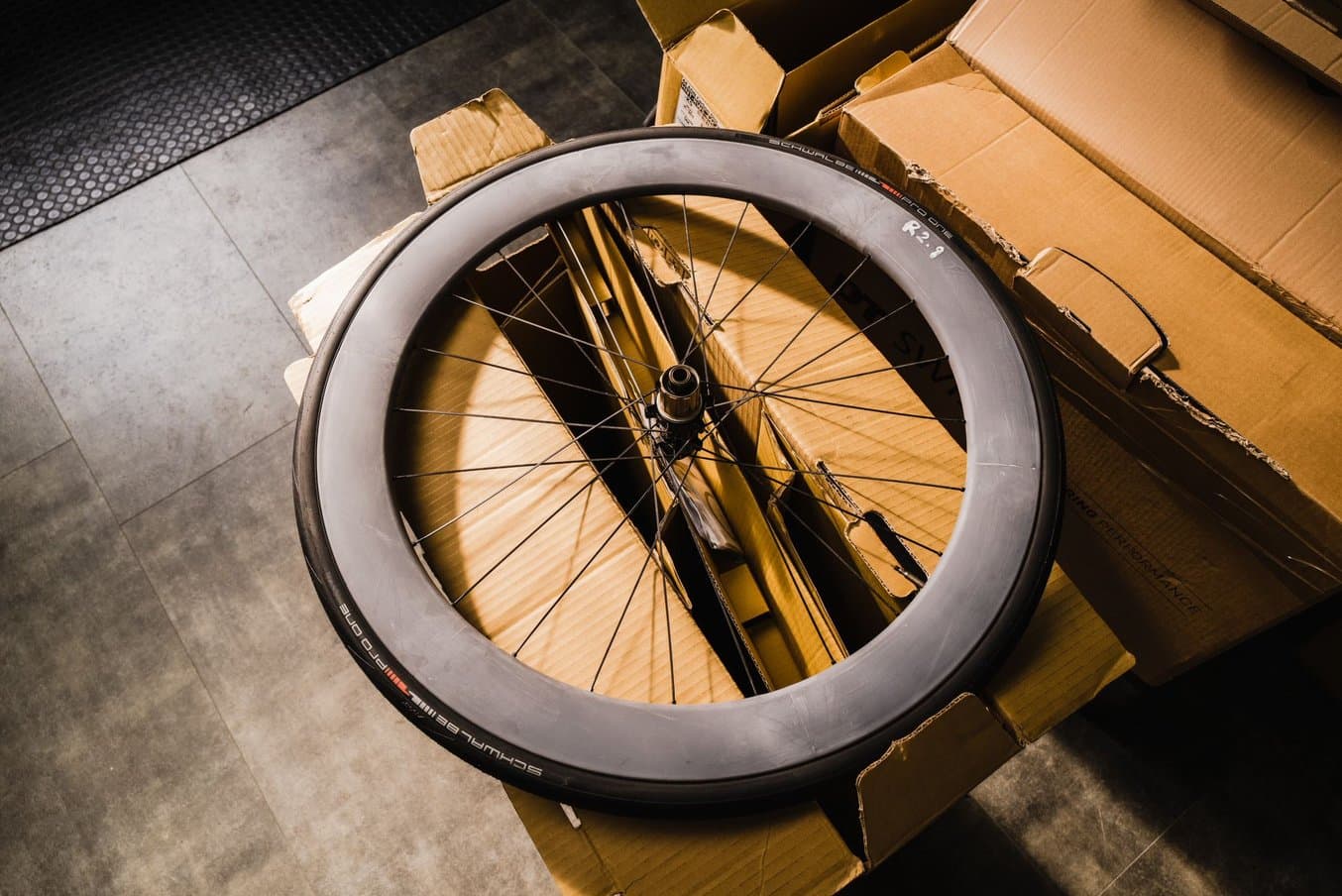
L’excellente qualité de surface de Grey Pro Resin a été déterminant pour les essais aérodynamiques.
L'impression 3D en interne permet également à l'équipe d'ingénieurs d'itérer davantage, tout en réduisant les coûts. À l'époque de la sous-traitance, Hunt Bike Wheels dépensait environ 2000 £ pour un seul prototype de jante. Grâce à la Form 3L, ces coûts ont été réduits de 90 % et s'élèvent désormais à environ 200 £.
« Cela signifie que lorsque nous allons dans la soufflerie, nous pouvons prendre un nombre beaucoup plus important de roues, ce qui nous permet de valider des études CFD plus larges. Nous évitons ainsi trois ou quatre cycles d'itération et arrivons à un produit de qualité supérieure. Chaque fois que nous sortons un produit, nous savons qu'il est en très bon état dès le départ », explique M. Hicks.
La Form 3L représente désormais un élément essentiel du modèle d'entreprise, car il permet à The Rider Firm de garder une longueur d'avance sur ses concurrents. En fait, M. Hicks affirme que « grâce à l'ingéniosité de nos prototypes et à la légèreté de nos opérations commerciales, nous vous offrons une roue qui présente les mêmes performances aérodynamiques que les grandes entreprises pour la moitié du prix ».
Privateer Bikes : repousser les limites avec des cadres de vélo complets et le prototypage rapide
Chez Privateer Bikes, l'équipe d'ingénieurs utilise la Form 3L pour toute une série d'applications de prototypage, y compris le prototypage de cadres de vélo complets et de protections de cadre.
Travaillant sur une nouvelle gamme de vélos, l'équipe d'ingénieurs de Privateer Bikes a imprimé des cadres entiers et certaines des sections les plus complexes du cadre en différentes tailles. Cela lui a permis de monter des composants dessus, par exemple de presser des roulements et des fourches à ressort dans le cadre afin de garantir la capacité de production et de vérifier les distances pour différentes tailles de cadre. « Nous pouvons vérifier les jeux, le mode d'assemblage, si les composants s'emboîtent ou si quelque chose bute lorsque les suspensions bougent ».
En outre, l'impression de l'ensemble du cadre a permis au designer graphique interne de le peindre à la bombe afin de tester des concepts avec le graphisme et de créer des autocollants pour les nouveaux vélos. Les cadres ont été imprimés en 3D avec Grey Pro Resin en plusieurs exemplaires plus petits, qui ont ensuite été assemblés et collés ensemble. Une fois que le vélo est entièrement assemblé et que les pièces sont collées, il peut résister à des charges considérables, « ce qui permet une manipulation brutale ».
« L'impression 3D est très pratique pour faire des expériences », explique M. Hicks. Il ajoute que « pour les équipes de marketing, il est bon d'avoir quelque chose de tangible, car lorsque nous parlons d'un design, nous pouvons le communiquer beaucoup mieux en ayant simplement l'accessoire et en le montrant aux gens. »
M. Hicks souligne que la Form 3L a été particulièrement utile pour le prototypage de protections de cadre personnalisées pour leurs vélos. Sur un VTT, la chaîne vient souvent buter contre la base, ce qui peut être assez bruyant et endommager le cadre. C'est pourquoi l'équipe a développé ces protections de cadre sur mesure en caoutchouc qui se collent à la base du pédalier.
Normalement, l'équipe n'aurait pas eu la possibilité de prototyper ce type de pièces. Elle aurait donc simplement envoyé la conception au fournisseur taïwanais, qui aurait fabriqué l'outillage de production et lui aurait envoyé un échantillon de la pièce finale. L'ensemble du processus prend normalement trois à quatre mois et coûte entre 3000 et 4000 $. Il aurait été difficile d'améliorer, d'itérer et d'optimiser la pièce, car toute modification de la conception aurait nécessité la fabrication d'un nouvel outillage, ce qui aurait entraîné de nouvelles dépenses.
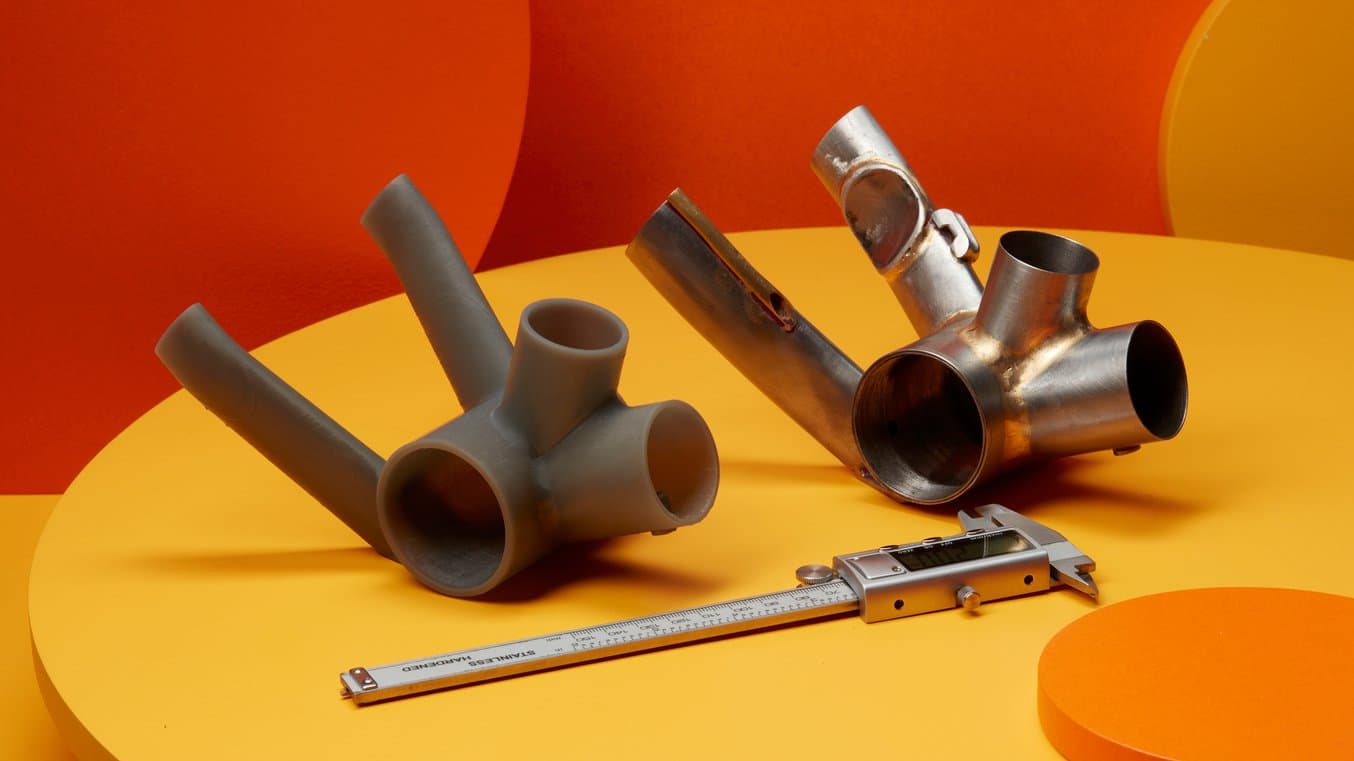
Prototypage rapide : choisir le bon procédé et les bons matériaux
Dans ce webinaire, découvrez comment vous pouvez créer des modèles conceptuels et des prototypes fonctionnels plus rapidement que jamais, ainsi qu'effectuer des révisions rapides de vos conceptions sur la base d'essais en conditions réelles.
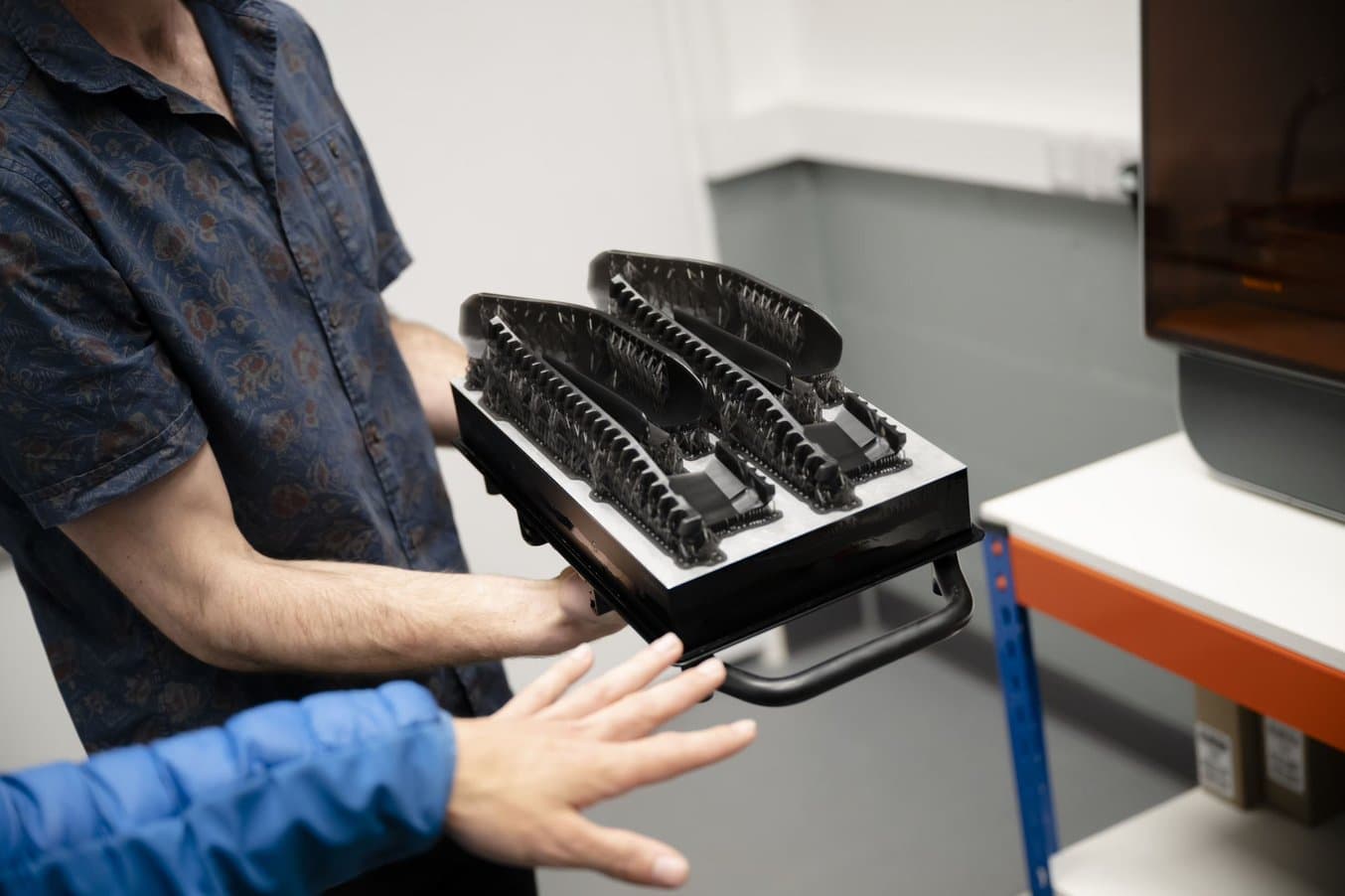
La Form 3L a été un outil formidable pour imprimer les prototypes des protections de cadre en Flexible 80A Resin.
Grâce à l'impression 3D, les ingénieurs de Privateer Bikes peuvent imprimer trois ou quatre modèles et réaliser des prototypes très rapidement. « La modification de la conception ne nous coûte rien, ce qui signifie que lorsque nous envoyons un fichier de production au fabricant, nous pouvons immédiatement lancer la production », explique M. Hicks. Il ajoute que cela leur a permis d'économiser environ six mois sur le projet et environ 4000 ou 5000 $ sur l'outillage de production.
« Lorsque nous envoyons un fichier de production au fabricant, nous pouvons immédiatement lancer la production », explique M. Hicks.
Dan Hicks, ingénieur en développement chez Privateer Bikes
Le matériau choisi pour cette application particulière était Flexible 80A Resin, qui « possède le bon niveau de dureté » et est donc idéale pour les prototypes fonctionnels testés directement sur des vélos. Ils ont testé ces protections sur les vélos pendant plusieurs mois, en vérifiant les points d'impact de la chaîne et les endroits où elle fait encore du bruit, et en procédant à des modifications en fonction de ces résultats.
« Nous pouvons mettre en œuvre de nombreux aspects de la conception pour la fabrication, car il est beaucoup plus facile de réfléchir aux lignes de séparation dans l'outil et à leur fonctionnement quand on a l'ensemble devant soi. »
Dan Hicks, ingénieur en développement chez Privateer Bikes
L'impression 3D : une réponse rapide à l'évolution des tendances
« Nous ne savons pas ce que les gens feront dans deux ans. Mais nous sommes aujourd'hui très bien placés pour réagir rapidement aux changements de tendances et pour nous lancer dans de nouveaux projets. »
Dan Hicks, ingénieur en développement chez Privateer Bikes
Dans un avenir proche, The Rider Firm envisage de développer d'autres vélos électriques et leurs composants. Ces vélos impliquent des conceptions plus complexes, M. Hicks soulignant que « plus il y a de composants à ajuster, plus la tâche est difficile » et que l'impression 3D leur permettra de prototyper toutes ces configurations.
« Tout le monde roule à vélo différemment », c'est pourquoi l'équipe de The Rider Firm est curieuse de voir ce que les gens vont faire. Avec la Form 3L dans son arsenal, l'entreprise est désormais en bonne position pour répondre rapidement à l'évolution des tendances et poursuivre ses efforts d'innovation.