Kastalon crée de nouvelles catégories de produits en polyuréthane grâce à des moules imprimés en 3D
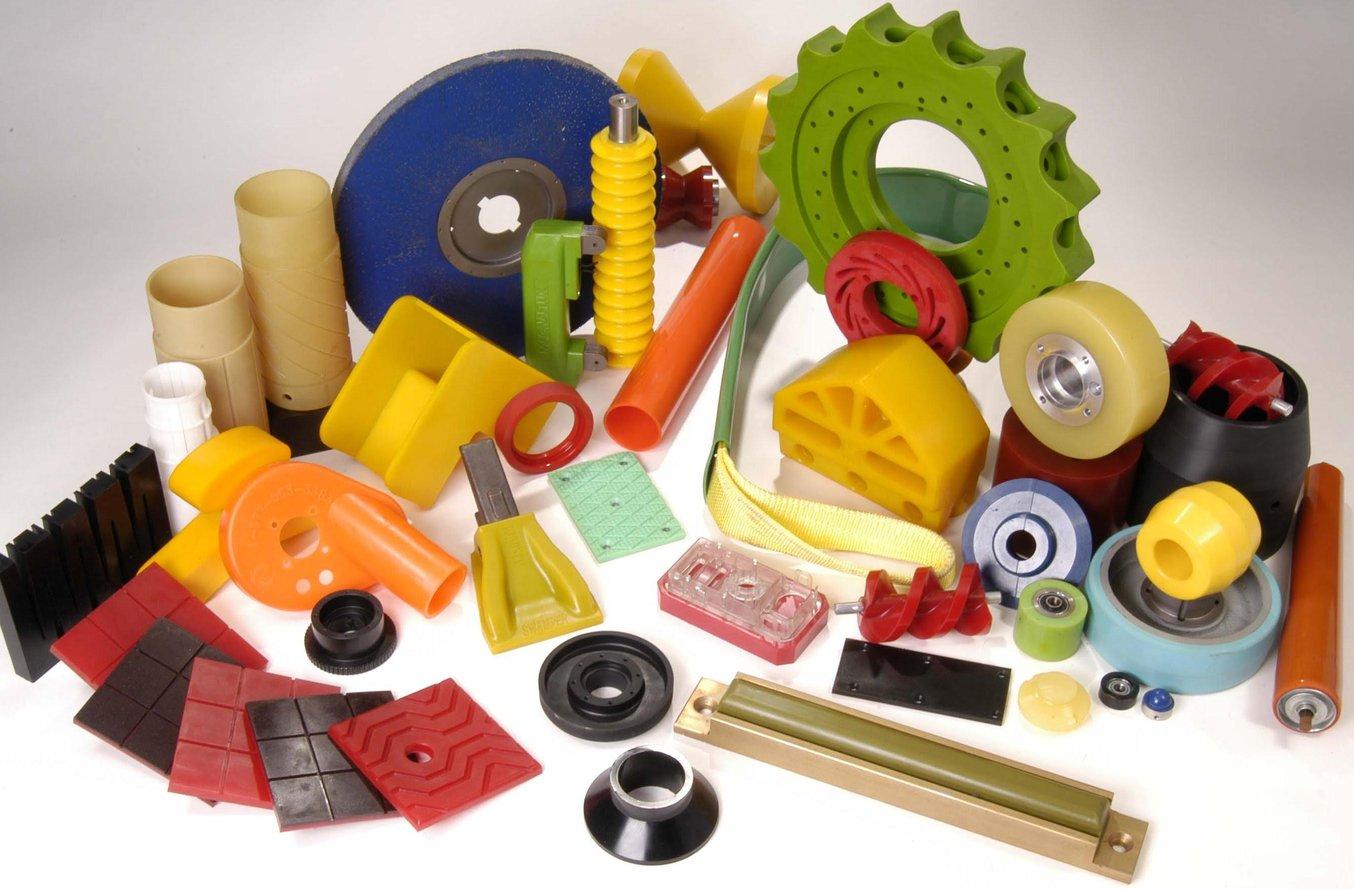
Ils sont d'une importance capitale, mais passent pourtant souvent inaperçus : les rouleaux de manutention pour les chaînes de production, les garnitures de frein pour les montagnes russes ou encore les cales qui maintiennent les avions de chasse en place... Les composants en polyuréthane sont souvent essentiels au fonctionnement d'un système complet, même s'il ne s'agit peut-être pas du premier matériau qui attire notre attention lorsque nous regardons un produit. Pour qu'ils fonctionnent correctement dans le cadre d'un assemblage plus complexe, les composants en polyuréthane doivent être conçus de manière à optimiser l'utilisation du matériau, à respecter des tolérances étroites et à supporter des charges ou des déformations prolongées.
Kastalon, un fabricant de polyuréthane basé dans l'Illinois, résout des problèmes depuis des décennies pour produire des milliers de pièces personnalisées en polyuréthane qui peuvent répondre à cette gamme variée d'exigences. L'ingénieur produit Brian Baer nous a expliqué comment la Form 3L, une imprimante 3D stéréolithographique (SLA) grand format, a ouvert de nouvelles possibilités à l'entreprise pour la fabrication d'outils de production et d'outillages, ainsi que pour la recherche et le développement de produits.
« La possibilité d'imprimer en 3D des moules entièrement neufs représente un avantage énorme pour apporter des petites modifications et des adaptations. Nous sommes également ravis de pouvoir atteindre la tolérance de +/- 0,005. Nous avons réalisé des choses qui n'étaient pas possibles auparavant, et le volume de production ne cesse de croître. »
Brian Baer, ingénieur
Combiner l'impression 3D et l'usinage traditionnel chez Kastalon
Kastalon conçoit et fabrique des centaines de moules personnalisés pour produire des centaines de milliers de pièces en polyuréthane. Jusqu'à présent, lorsque les clients demandaient des pièces finales, l'équipe de Kastalon évaluait le modèle en fonction de la faisabilité de la fabrication du moule, puis usinait un moule en aluminium ou en acier.
Auparavant, le coût et la complexité du processus d'usinage obligeaient parfois Kastalon, comme de nombreux fabricants de matières plastiques, à refuser des pièces trop compliquées à mouler ou qui n'étaient pas rentables pour les petites séries et le prototypage. Quand les moules présentaient trop de caractéristiques imbriquées, de petits canaux ou de broches, le processus de conception, de fraisage et parfois de révision complète était souvent inefficace. Il était cependant difficile de refuser des commandes. Comme M. Baer avait travaillé avec différentes technologies d'impression 3D au cours de sa formation, il s'est mis à chercher des solutions alternatives pour la fabrication de moules.
Des années auparavant, un essai avec l'impression 3D avait laissé de mauvais souvenirs à une partie de l'équipe, c'est pourquoi M. Baer a effectué des recherches en fonction de certains critères. L'équipe avait besoin d'un appareil qui respecte des tolérances de +/- 0,005 pouce, de matériaux qui résistent à des températures de coulée de 80 à 150 °C, et d'un système qui soit abordable.
« Ce n'est que lorsque j'ai trouvé Formlabs et que j'ai vu le large éventail de matériaux capables de résister à des températures élevées et offrant certaines propriétés spécifiques que j'ai compris que cette imprimante pouvait effectivement répondre à [nos] besoins. »
Brian Baer, ingénieur
La Form 3L est arrivée chez Kastalon à la fin de l'année 2022, mais quelques tests ont été nécessaires avant que tous les collaborateurs soient convaincus. Au début, les collègues étaient sceptiques quant aux matériaux et aux tolérances possibles, jusqu'à ce que M. Baer imprime quelques pièces d'essai. « J'ai imprimé une pièce pour les employés de notre atelier d'usinage, qui ont effectué un test de rugosité de surface RA. Le responsable de l'atelier a été très impressionné par le fait que la pièce correspondait aux spécifications que je lui avais données et par son aspect lisse », explique M. Baer.
Aujourd'hui, explique M. Baer, le directeur de l'atelier d'usinage est le premier à lui envoyer des pièces pour qu'il les imprime en 3D plutôt que de les usiner. « Il est l'une des premières personnes à suggérer l'impression 3D lorsqu'elle se prête à des commandes. L'atelier est submergé par des projets plus importants. Si une petite pièce peut être imprimée, il préfère que nous nous en occupions pour alléger sa charge de travail », explique M. Baer.
Nouvelles possibilités en matière de géométries, de tests et d'opérations
L'impression 3D ouvre de nouvelles possibilités pour le moulage de pièces en polyuréthane. L'équipe de développement de Kastalon peut essayer de nouvelles caractéristiques de conception et de nouvelles géométries qui ne sont pas réalisables avec des moules métalliques, ou effectuer de petites modifications de conception sans que cela ne rende obsolète un moule usiné. L'équipe peut proposer de nouvelles conceptions en toute confiance, car elle a été en mesure de procéder à des tests approfondis sans craindre que les nombreuses petites modifications ne submergent l'atelier de métallurgie.
Moule pour pince d'extraction : réalisable grâce à l'impression 3D
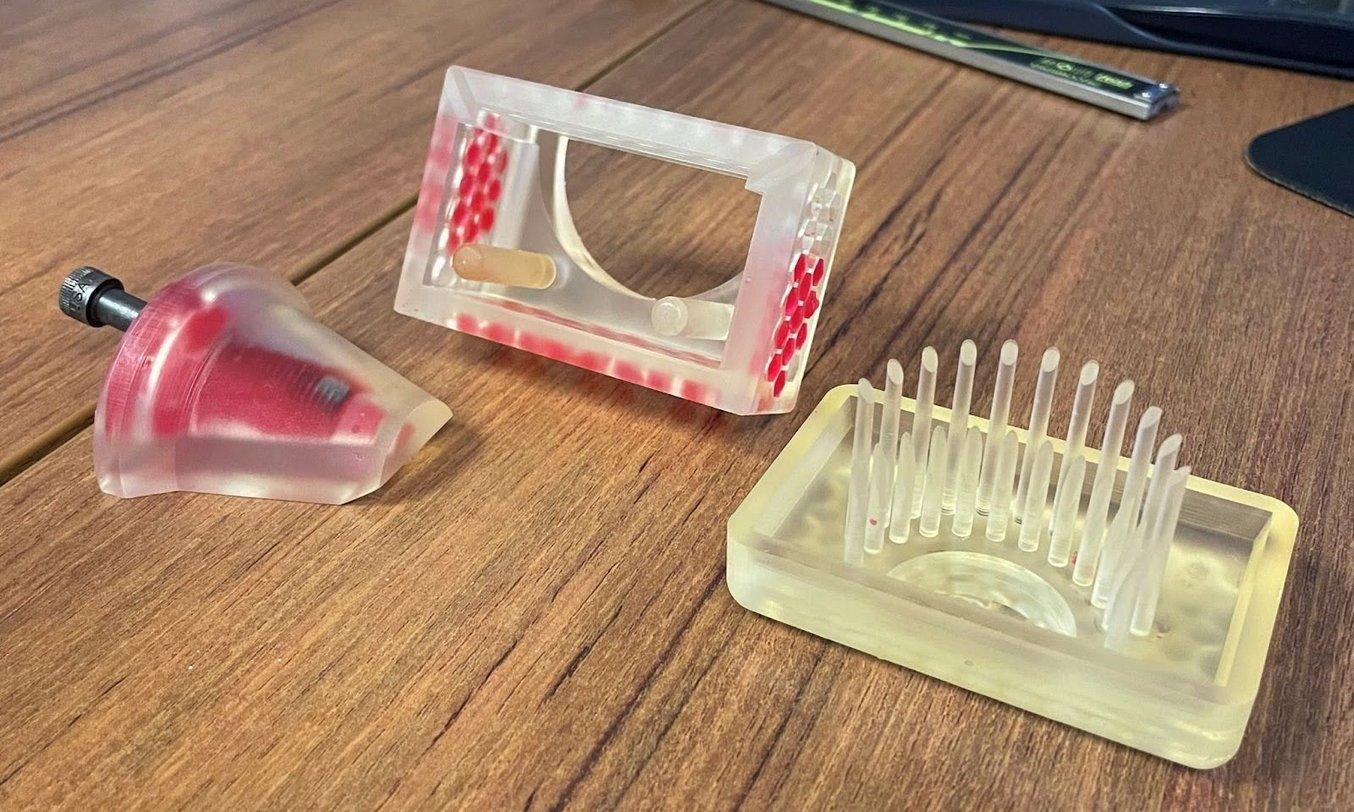
Kastalon a dû refuser la demande un client qui souhaitait une pièce avec 24 trous borgnes décalés par rapport à la surface, car le moule aurait été tout simplement trop difficile à usiner.
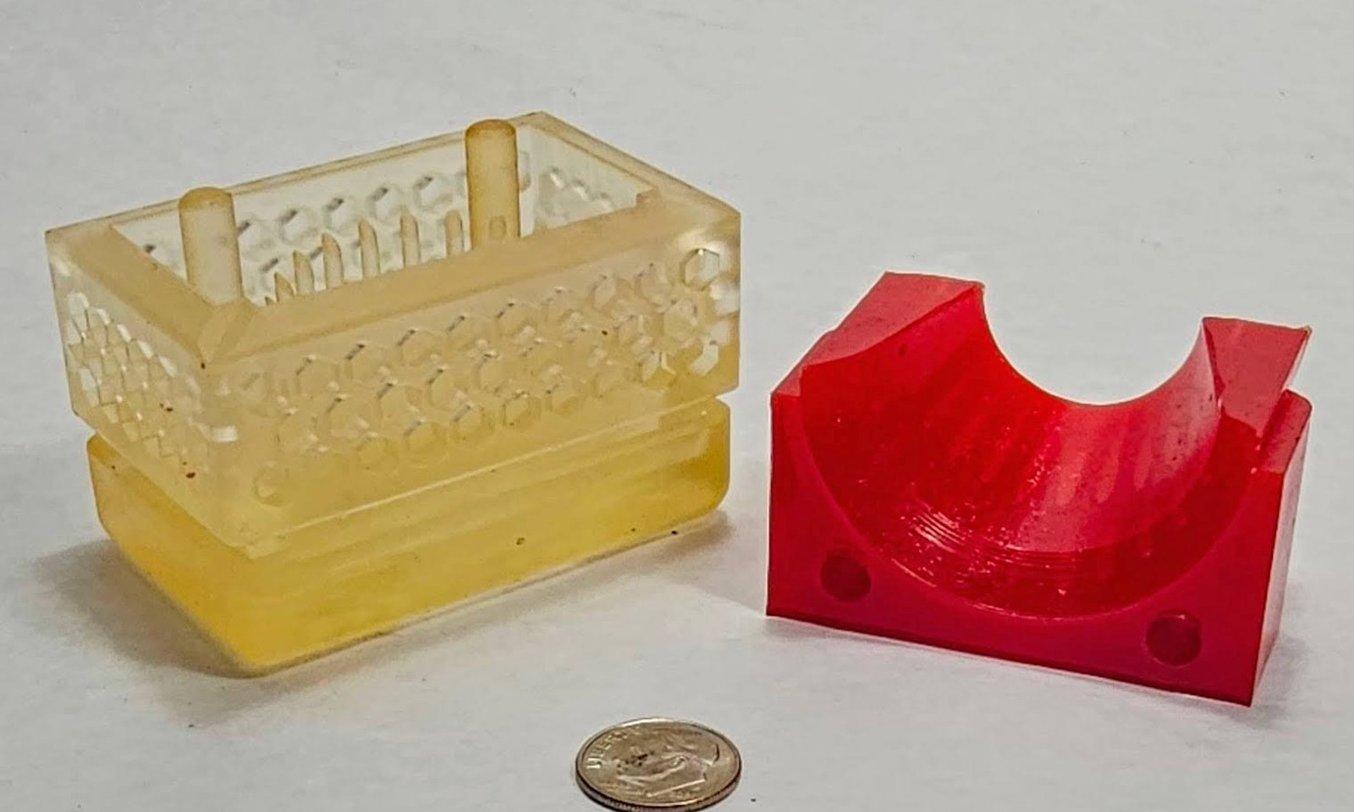
Grâce à la Form 3L et à High Temp Resin, M. Baer a pu imprimer et couler la pièce en polyuréthane finie (à droite) en moins d'une journée.
Comme elle ne disposait pas encore de la Form 3L, l'équipe de Kastalon a dû annoncer à un client qu'elle ne pouvait pas accepter la commande de la pince d'extraction. Cela aurait peut-être été possible avec de nombreux tests et de nouvelles tentatives, mais les 24 broches ne traversent pas complètement la pièce et sont espacées de seulement 0,03125 pouce.
En raison de ces distances et du fait qu'il s'agit de trous borgnes qui se terminent avec un décalage sous la surface de la pièce, cette pièce nécessiterait un usinage extrêmement difficile avec des fraises longues et très délicates. L'autre option serait de produire les broches individuellement et de les fixer ensuite de manière à ce qu'elles soient positionnées dans la bonne orientation. Cependant, comme chaque broche a un diamètre de 0,104 pouce, ce ne serait pas une tâche facile.
Après avoir évalué les différents procédés d'usinage possibles, l'équipe a dû refuser la commande. « Nous avons longuement discuté de la faisabilité de cette tâche, et notre réponse négative au client a été lourde de conséquences », explique M. Baer.
Quelques semaines plus tard, la Form 3L est arrivée, et M. Baer a conçu et imprimé le moule en une demi-journée pour démontrer l'intérêt qu'il y avait à imprimer en 3D des géométries complexes comme celle-ci. Le coût des matériaux revenait à un peu plus de 30 €, et la conception lui a pris environ deux heures. « L'impression 3D a immédiatement gagné le respect de toute l'équipe. Cela a ouvert les yeux de beaucoup de nos employés et nous a permis de leur dire : "Nous pouvons accepter plus de commandes, car nous sommes désormais capables de réaliser ce genre de choses" », explique M. Baer.
Roue anti-écrasement
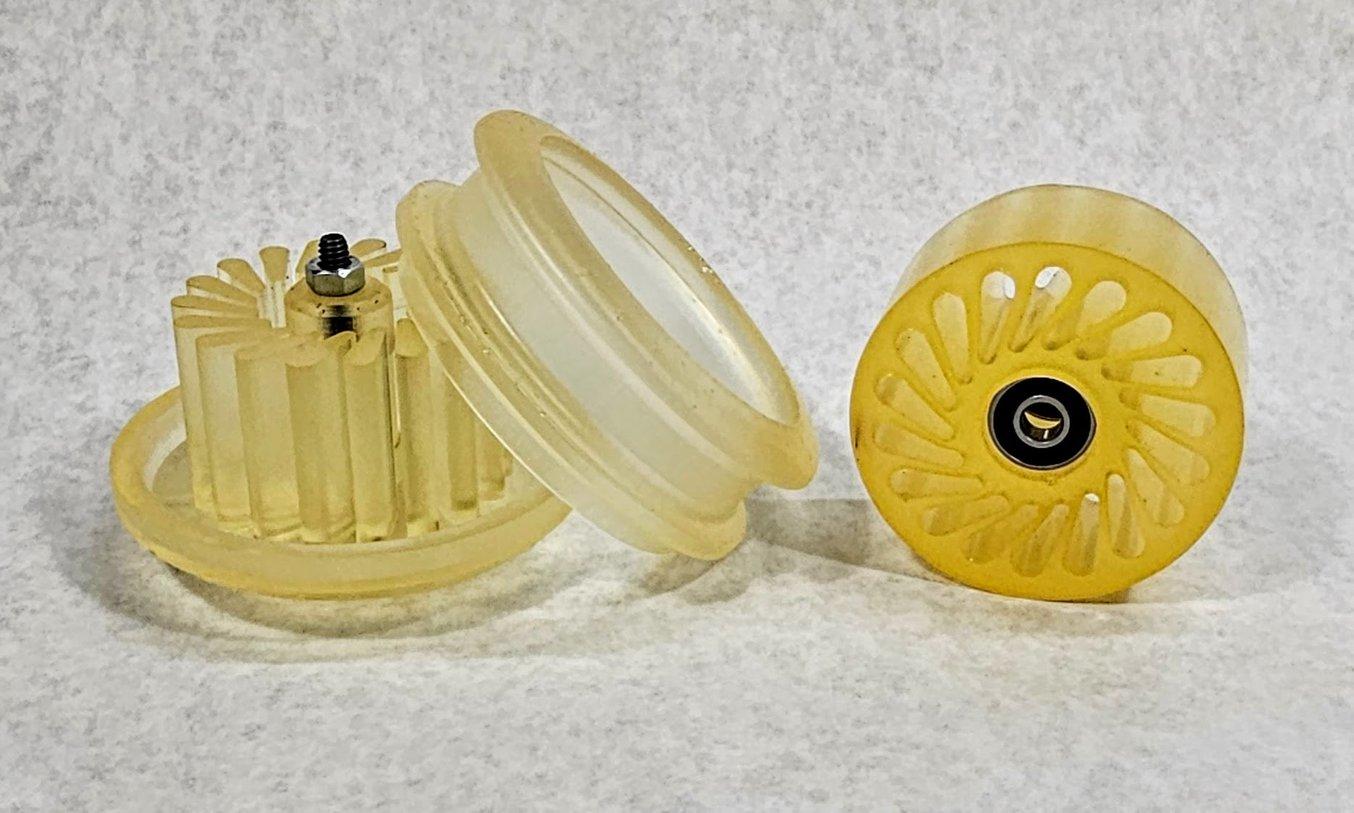
Ces moules (à gauche, en haut et en bas) et ces roues (à droite) sont conçus pour se déformer uniformément en cas de surcharge. Grâce aux ouvertures en forme de gouttes, le poids est réparti de manière uniforme afin que la roue n'écrase pas le produit.
La Form 3L entre en scène lorsque de minuscules caractéristiques rendent un moule trop difficile à usiner. Ces petites roues anti-écrasement qui servent à maintenir en place des produits déformables (par exemple des emballages en carton) sur des systèmes de convoyage sont utilisées à la place des assemblages de ressorts : au lieu qu'un ressort exerce une pression sur le carton, la roue elle-même se déforme uniformément pour maintenir le carton en place tout en douceur.
Cependant, les moules présentent un espace extrêmement réduit entre les « ailettes » qui servent à former les ouvertures en forme de gouttes dans les roues. Cela rend la fabrication du moule presque impossible.
Les roues ont une largeur de 2 pouces et l'épaisseur de la paroi entre les ailettes est de 0,125 pouce. « Il est peut-être possible de percer des trous de deux pouces de profondeur avec un espacement de 0,125 pouce, mais si vous leur envoyez un design de ce type, les usineurs exprimeront leur mécontentement », explique M. Baer.
De plus, un moule en aluminium en plusieurs parties rendrait également le processus d'assemblage plus compliqué. Il y a un compromis à faire : soit usiner le moule avec les ailettes en une seule pièce (comme sur l'image ci-dessus) et rendre le dégagement extrêmement difficile pour les machinistes, soit fabriquer toutes les ailettes individuellement et les assembler en une seule pièce, ce qui impliquerait plus de réglages et d'assemblage de petites pièces, et donc un surcroît de travail et de frustration.
L'impression 3D s'est logiquement imposée comme solution, et M. Baer a pu facilement concevoir dans Solidworks un moule en deux parties avec un roulement amovible, qui a ensuite été imprimé avec High Temp Resin et Rigid 10K Resin sur la Form 3L. Grâce aux moules en Rigid 10K Resin, l'équipe a pu couler 25 roues pour le client, pour une fraction du coût d'un moule usiné. « Nous avons fabriqué de nombreuses variétés et styles de petites roues, ce que nous ne pouvions pas faire avant la Form 3L, car ce n'était pas rentable pour nous », explique M. Baer.
Usinage | Impression 3D | |
---|---|---|
Nombre de composants | 21 | 3 |
Temps de conception | 7 h | 3 h |
Temps de préparation | 5 h | - |
Durée d'exécution | 35 h | 12 h |
Temps total | 47 h | 15 h |
Tests internes de modèles pour des ressorts de grande taille
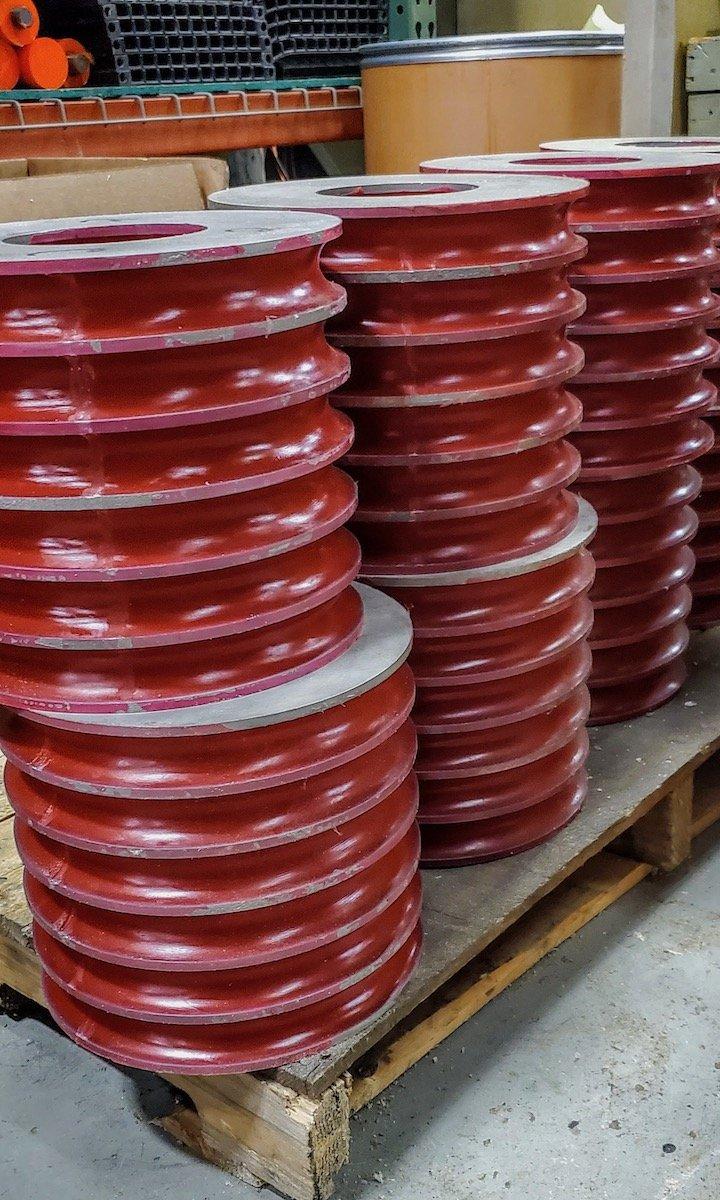
Les pièces en polyuréthane telles que ces ressorts rouges sont généralement moulées dans de grands moules en aluminium.
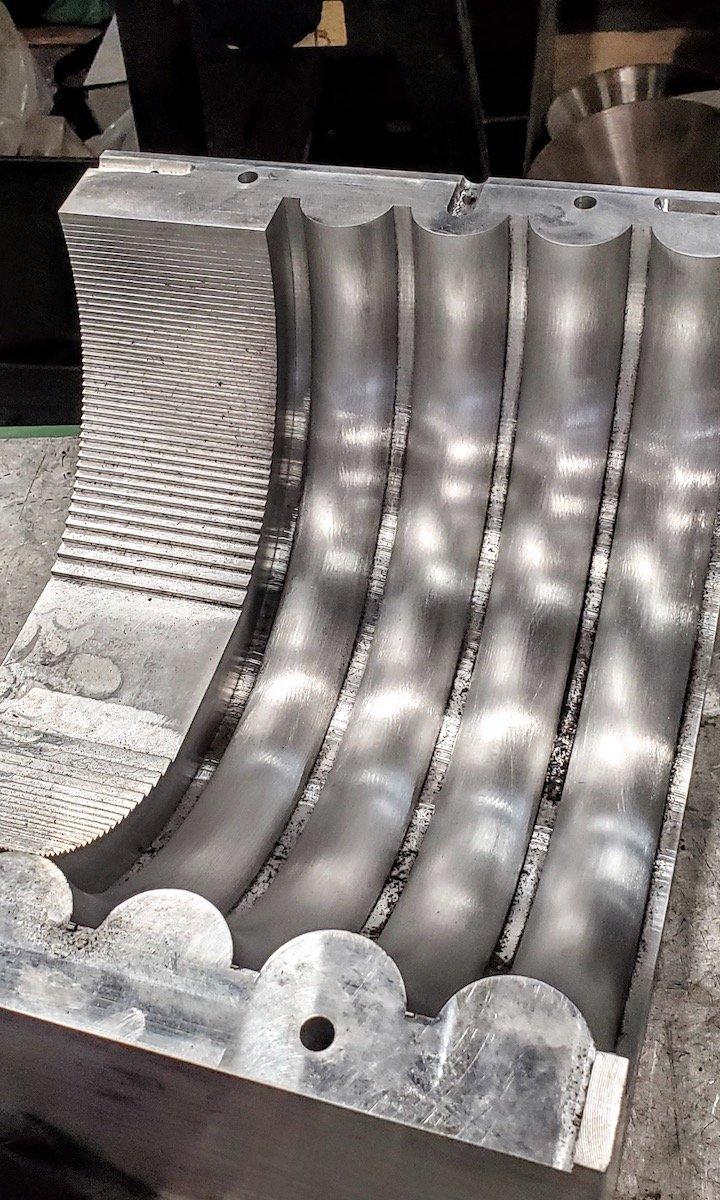
Ces moules en aluminium, ou dans certains cas en acier, sont coûteux et longs à usiner.
Le stade de baseball des Astros de Houston est équipé d'un dôme rétractable en cas de conditions météorologiques défavorables. Les ressorts fabriqués par Kastalon permettent de le maintenir tendu et opérationnel, même en cas d'ouragan.
Avant de fabriquer des moules d'une telle taille, l'équipe de Kastalon effectue des tests complets de conception et de matériaux sur des modèles réduits. En modifiant légèrement la conception et en testant des ressorts avec différentes géométries et différentes formulations de polyuréthane, le produit final a été optimisé pour pouvoir résister à des périodes prolongées de grande tension.
Cependant, malgré le changement d'échelle, chaque moule en aluminium restait coûteux, surtout s'il n'était utilisé que pour des tests internes. Désormais, la Form 3L permet à l'équipe de tester de nombreuses conceptions de ressorts différentes à un coût bien moindre sans submerger l'atelier d'usinage.
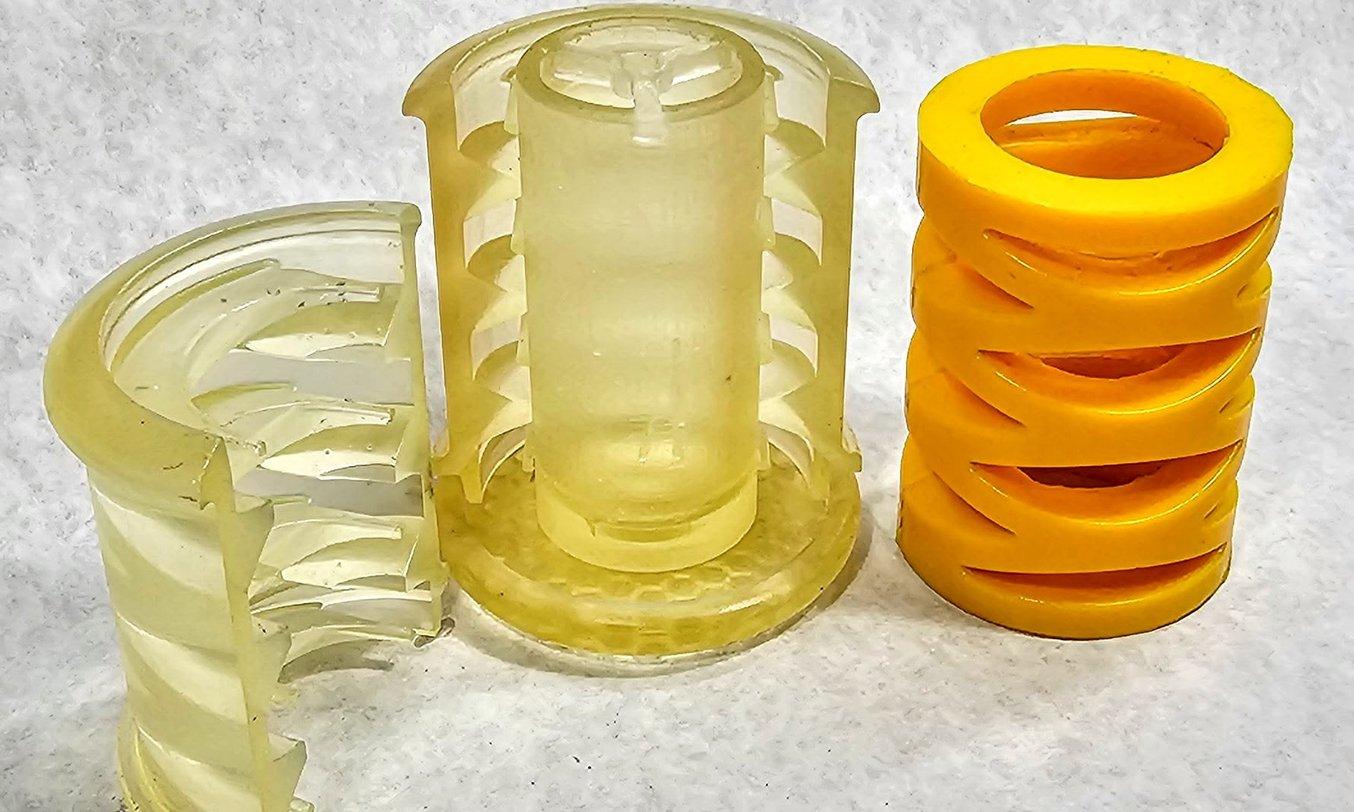
Ces moules (High Temp Resin, à gauche) et les ressorts en polyuréthane moulés (orange, à droite) sont des prototypes dont la géométrie a été conçue pour reproduire des ressorts en disques empilés.
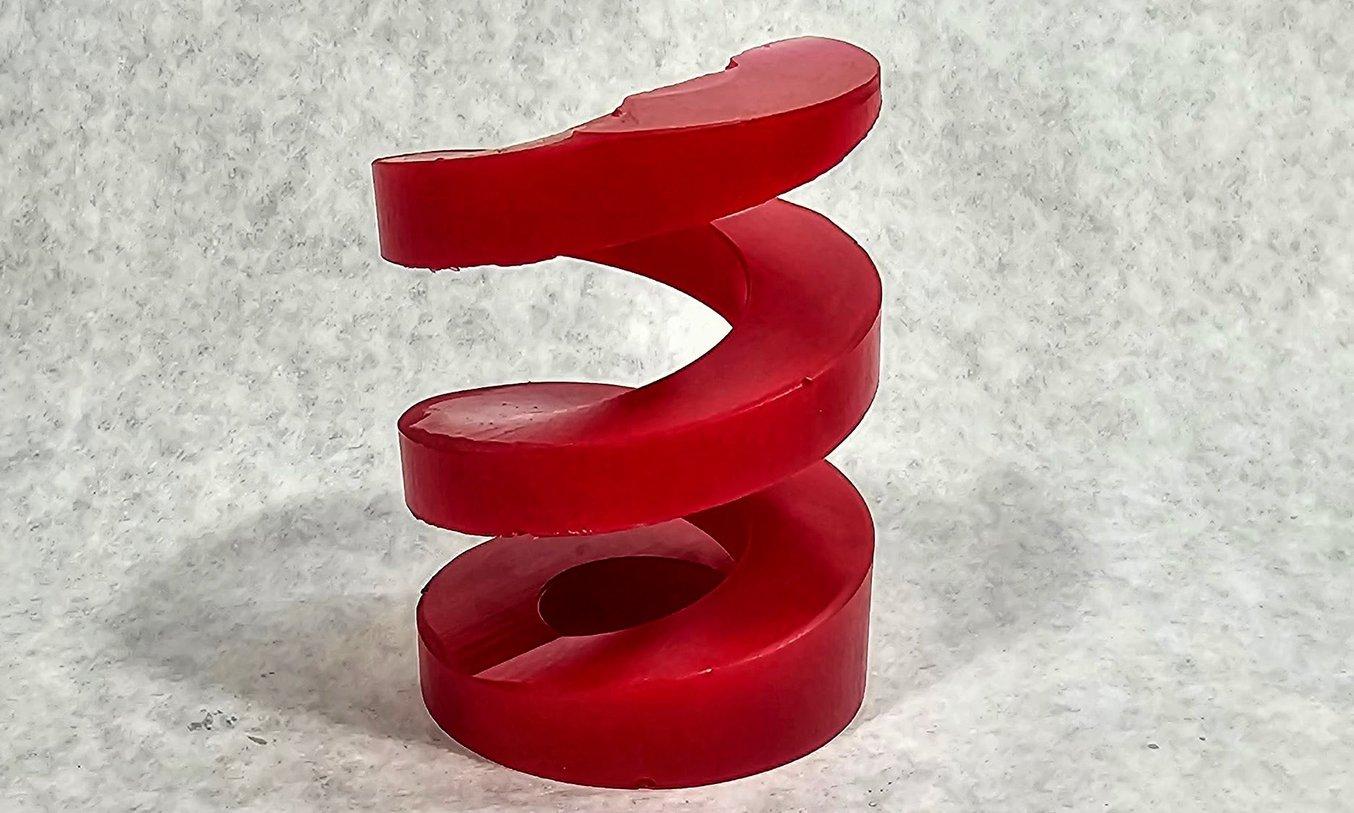
L'impression 3D permet à M. Baer et à son équipe d'expérimenter de nouvelles géométries et conceptions sans donner plus de travail à l'atelier d'usinage.
« Nous pouvons désormais imprimer et tester un grand nombre de formes et de géométries complexes qui auraient auparavant requis un budget énorme rien que pour les essais ou la recherche et le développement », explique M. Baer. En testant de nouvelles formes et géométries complexes sans que cela n'implique des coûts élevés de matériaux d'usinage et de main-d'œuvre, Kastalon peut désormais non seulement prendre plus de commandes, mais aussi fabriquer de meilleures pièces pour ses clients actuels.
Rouleaux moulés : comment éviter d'usiner du polyuréthane mou
Pour les rouleaux revêtus ou les manchons pour rouleaux, le processus traditionnel consistait à mouler un cylindre en polyuréthane et de le faire passer par une étape d'usinage supplémentaire pour réduire le diamètre extérieur à la taille et à la finition de surface souhaitées. L'étape supplémentaire de l'usinage des rainures peut être réalisée dans une variété de styles et de tailles en fonction de l'utilisation du rouleau. Dans ce cas particulier, l'usinage de longues rainures horizontales dans du polyuréthane souple s'est avéré une tâche difficile. Pour les commandes importantes, cette étape d'usinage manuel gourmande en main-d'œuvre réduisait le bénéfice de la commande et prenait des heures de travail à l'atelier d'usinage. « L'usinage du polyuréthane souple est salissant, ne donne pas toujours de bons résultats et ne permet pas toujours d'obtenir de belles finitions lors de la découpe », explique M. Baer.
L'usinage direct des rainures aurait pris environ trois heures par rouleau. Cependant, l'usinage de métal était trop coûteux et risqué, d'autant plus qu'aucun moule n'avait jamais été créé auparavant avec cette géométrie et que personne ne pouvait garantir le résultat final. Pour fabriquer un moule en métal, l'équipe aurait eu besoin d'un outil à fil ou d'une fraiseuse avec une tête partielle, deux équipements coûteux spécialisés pour certaines géométries et applications spécifiques.
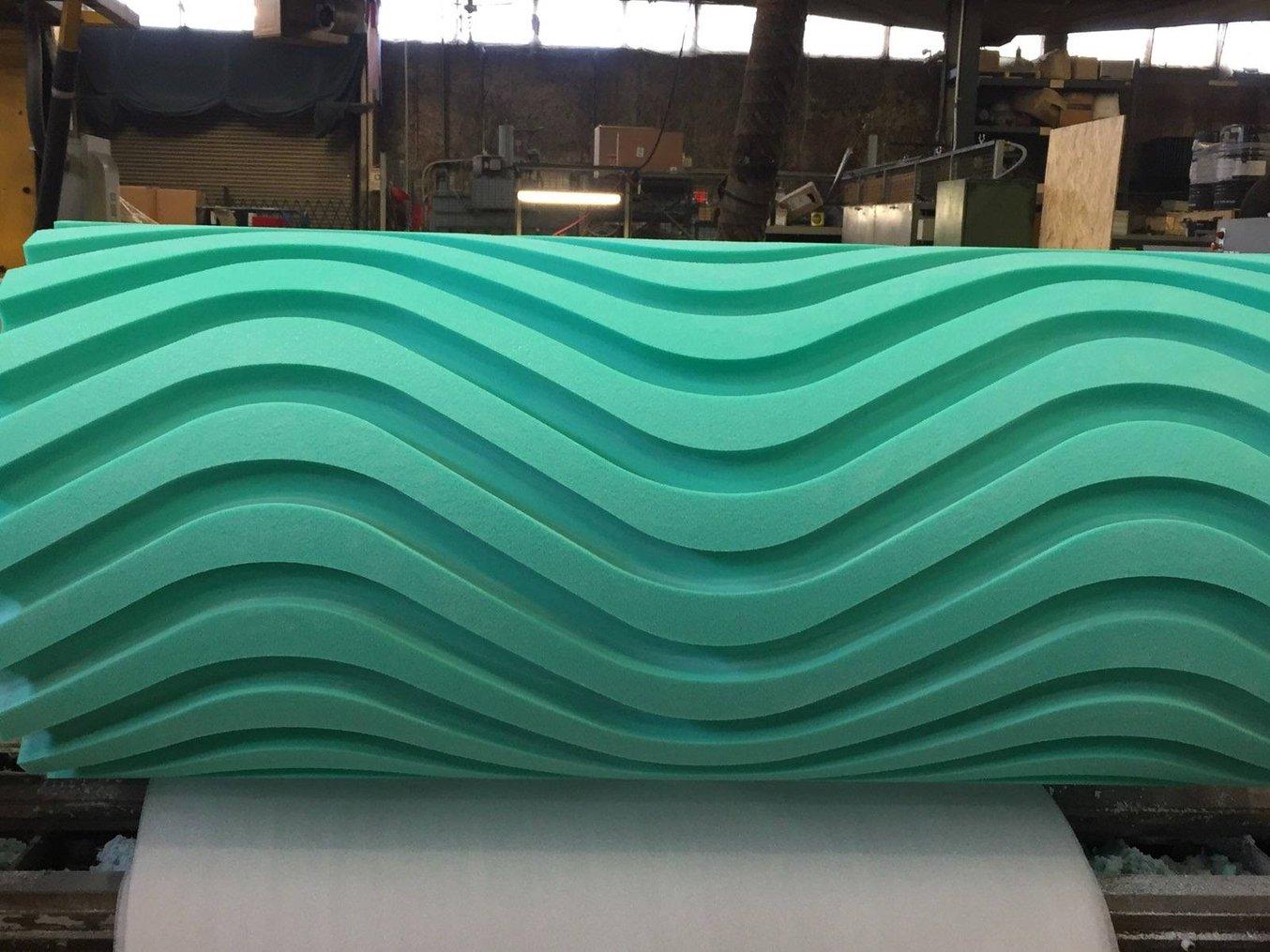
L'usinage du polyuréthane souple peut être fastidieux et prendre beaucoup de temps, en particulier pour les pièces de grande taille comme ce rouleau, qui est moulé puis usiné pour obtenir la forme finale.
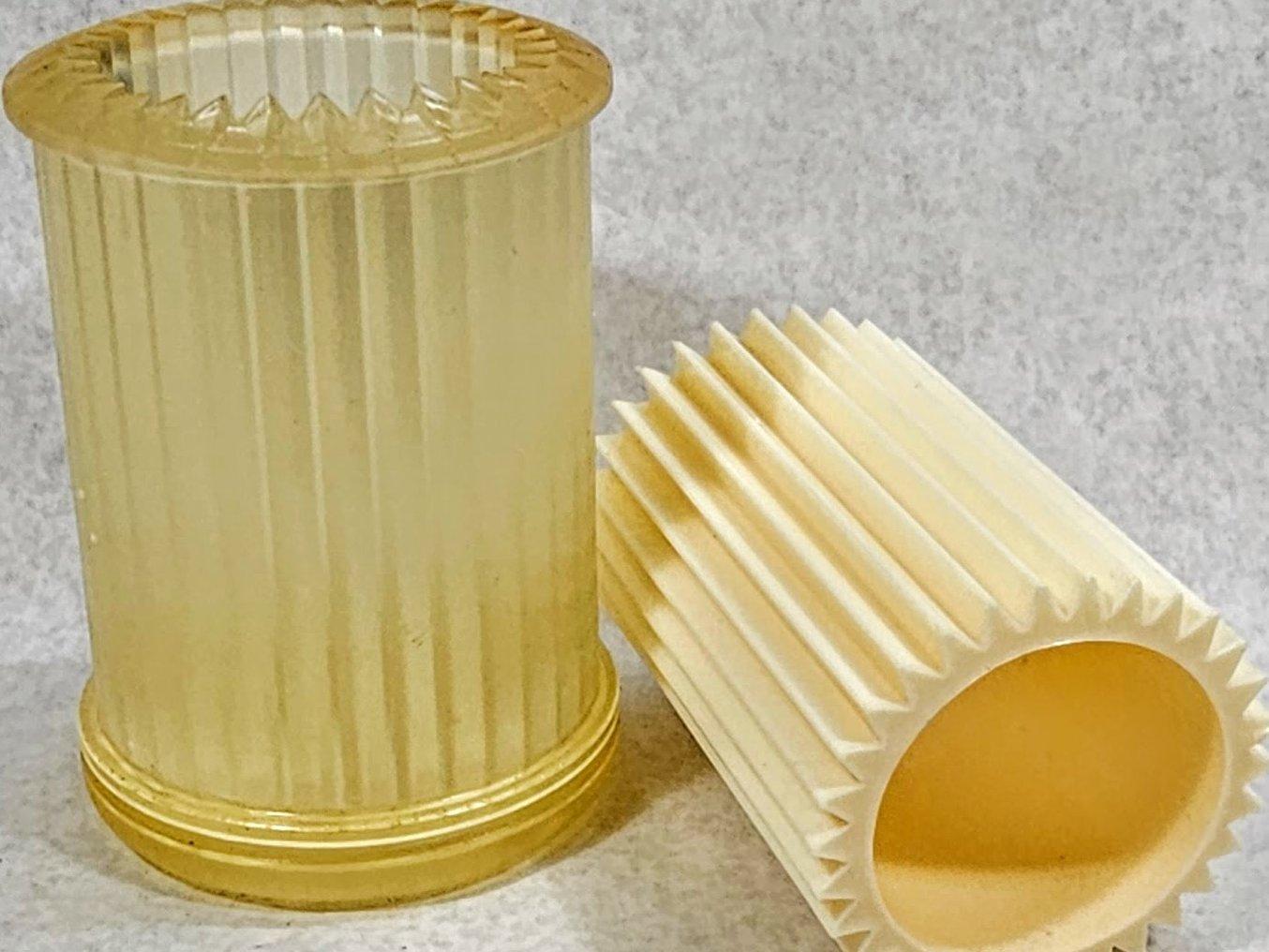
Lorsque les pièces sont petites, l'usinage des minuscules rainures peut s'avérer presque impossible. M. Baer a commencé à imprimer des moules pré-rainurés, de sorte que chaque moulage crée une pièce complète sans usinage supplémentaire.
M. Baer s'est rendu compte de la situation et a décidé d'essayer quelque chose de nouveau. Il a conçu et imprimé en 3D un moule permettant de mouler le polyuréthane dans la forme rainurée dont ils avaient besoin. L'impression directe sur la Form 3L avec High Temp Resin ou Rigid 10K Resin a offert une solution rentable qui a permis d'économiser des heures de travail manuel.
Lorsqu'il choisit un matériau, M. Baer tient compte de la résolution et de la hauteur des couches, du coût par litre, de la résistance et de la couleur/transparence. En fonction de ces facteurs, il opte généralement pour High Temp Resin ou Rigid 10K Resin. Pour les prototypes, les pièces uniques ou les petites quantités, High Temp Resin est privilégiée en raison de son faible coût et de sa transparence, car il est utile d'également voir l'intérieur de la pièce pour décider des modifications du design. Mais pour les pièces qui doivent être coulées en plus grande quantité, l'équipe s'appuie sur les propriétés mécaniques supérieures de Rigid 10K Resin. « Nous utilisons Rigid 10K Resin depuis peu, principalement parce qu'elle résiste mieux au démoulage. »
Usinage | Moule imprimé en 3D | |
---|---|---|
Pièces par année | 40 | 40 |
Préparation du moulage | 1 h | 1 h |
Travail manuel après le moulage par pièce | 3 h | 0 h |
Temps total | 160 h | 40 h |
Capacité accrue et produits améliorés
En moins d'un an, la Form 3L a complètement transformé le processus décisionnel de Kastalon. N'étant plus limitée par les contraintes traditionnelles de l'usinage, l'équipe d'ingénieurs peut désormais accepter de nouvelles commandes auxquelles elle n'aurait pas osé s'attaquer auparavant, et a optimisé des processus qui engloutissaient des milliers de dollars en temps de travail et en matériaux.
« Notre volume de production a augmenté. Nous avons gagné en confiance, et les commandes réalisées par la Form 3L n'ont cessé d'augmenter. Nous pouvons essayer de nouvelles choses et aider l'équipe de vente à répondre aux souhaits des clients, simplement pour montrer que c'est possible. »
Brian Baer, ingénieur
Les employés de l'atelier d'usinage de Kastalon se sont forgé une réputation de précision, de cohérence et d'excellence. L'ajout de moules imprimés en 3D n'a pas fait l'unanimité au début, mais les résultats parlent d'eux-mêmes. Conscient des propriétés mécaniques, des tolérances et de la liberté géométrique que permet la stéréolithographie, même le directeur de l'atelier d'usinage s'est mis à imprimer des pièces en 3D.
Pour en savoir plus sur l'outillage rapide, consultez notre page d'applications. Pour voir la Form 3L, visitez notre page produit.