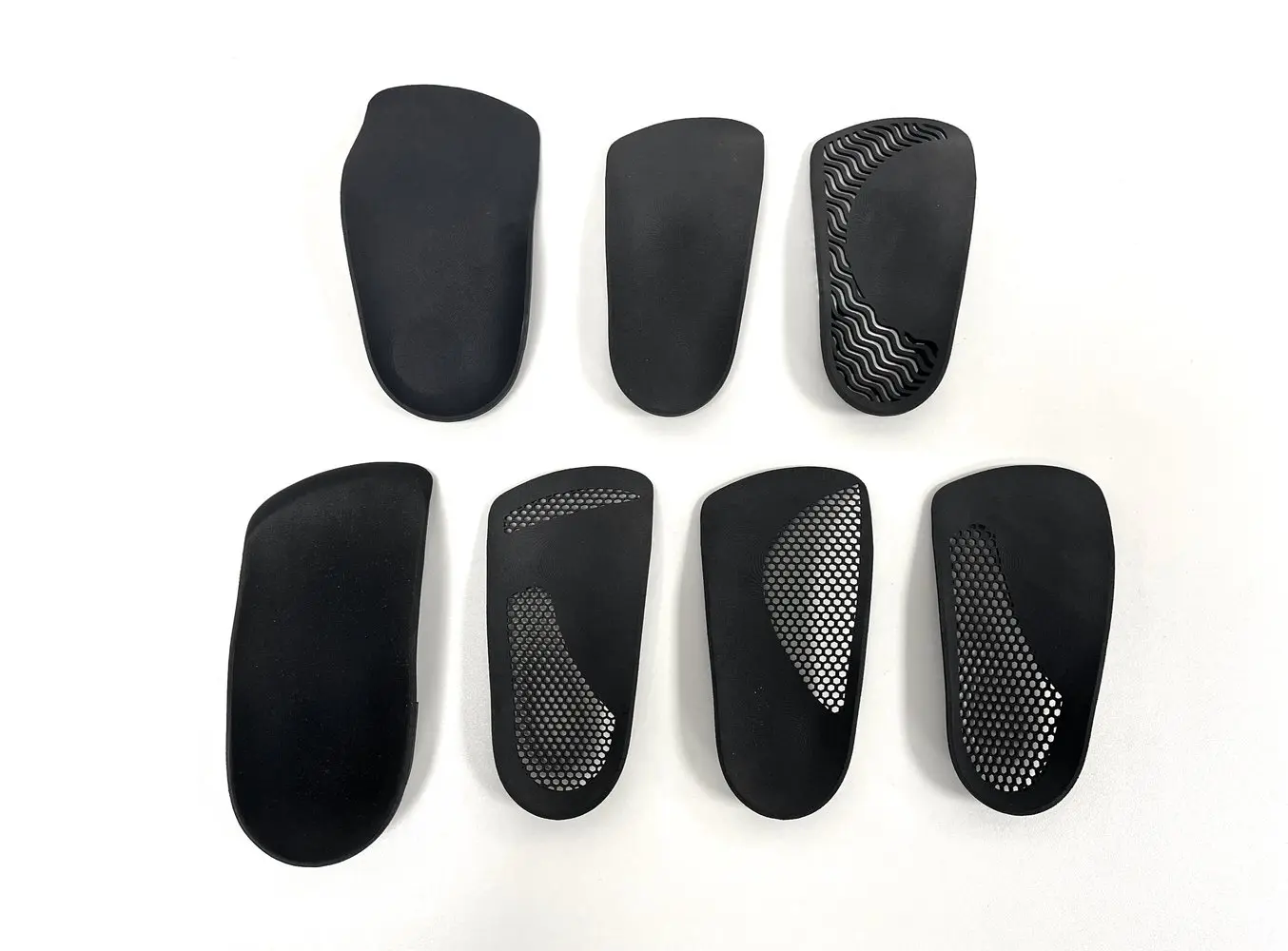
MAG Orthotics Limited à Sheffield, Royaume-Uni, propose des produits et des réparations sur mesure dans le domaine de l'orthétique et de la podologie. L'entreprise est actuellement en pleine transition vers un avenir numérique et a récemment introduit l'impression 3D afin d'économiser des ressources, du temps et des matériaux. Mais la transition vers des flux de travail numériques ne concerne pas seulement le procédé de fabrication, mais aussi les choix de tout le réseau d'orthésistes et de podologues avec lesquels MAG travaille.
Les fabricants d'orthèses travaillent dans un écosystème complexe qui se situe encore entre les anciens systèmes de fabrication et les nouveaux. En collaboration avec le distributeur Additive-X, le fournisseur de logiciels Fit360, et son réseau de podiatres et d'orthèses, MAG Orthotics essaie de pousser le marché vers des processus de travail numériques. Au sein de ce réseau complexe, MAG Orthotics a dû s'appuyer sur l'expérience de ses partenaires tout en informant les distributeurs et les professionnels de la santé des avantages des processus numériques et des produits imprimés en 3D.
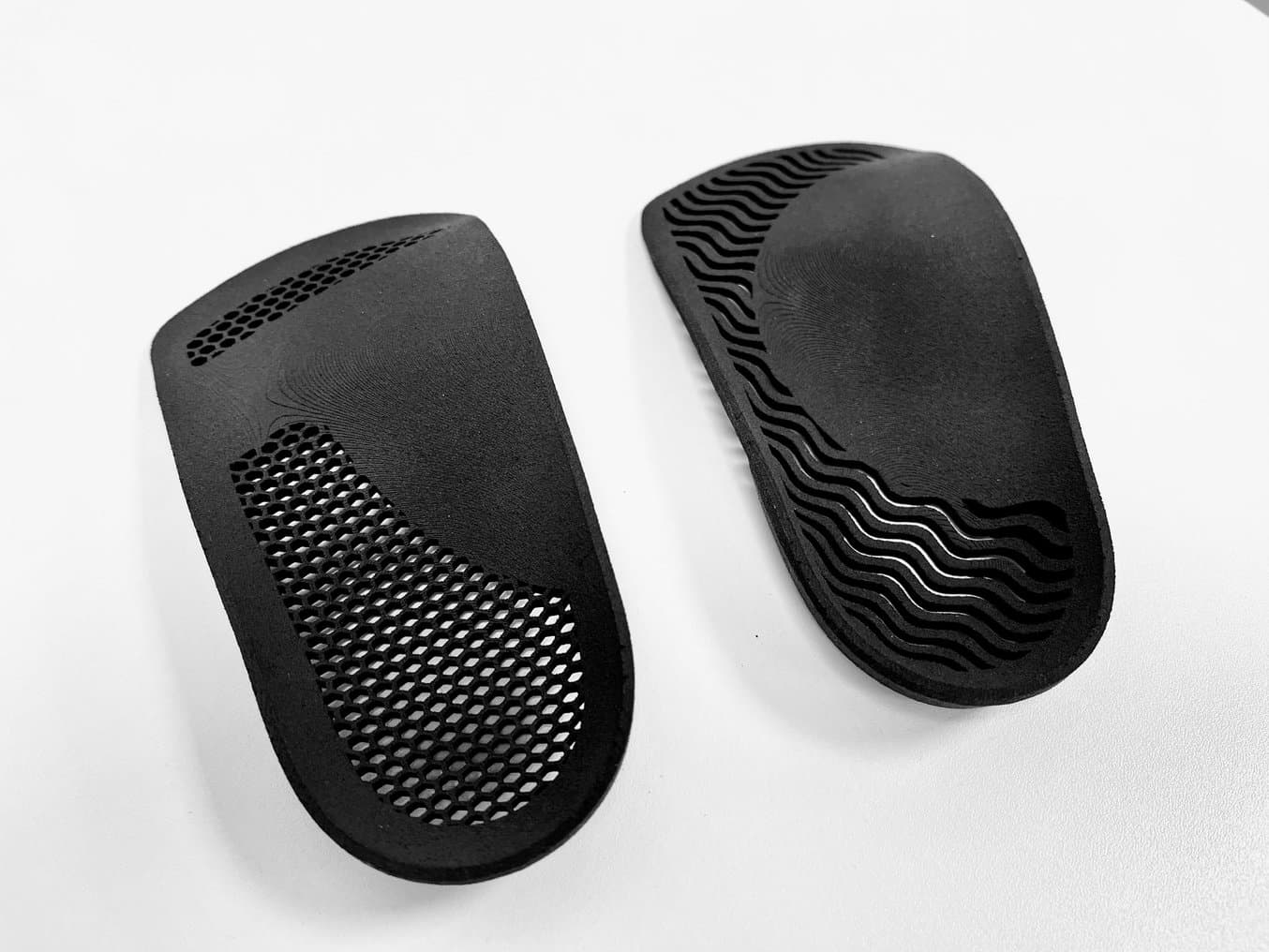
L'avenir de la fabrication de semelles orthopédiques et la production sans déchets avec MAG Orthotics : transformation des processus avec Formlabs et FIT360
Découvrez la puissance de la numérisation de la production de semelles, y compris pour la conception et l'impression. MAG Orthotics vous parlera de son parcours vers l'impression 3D et de son engagement en faveur du développement durable.
Un écosystème complexe
MAG Orthotics travaille avec des orthésistes et des podologues du National Health Service (NHS), d'hôpitaux distincts et de cliniques privées dans tout le Royaume-Uni. Lee Lingard est le spécialiste de la CAO et du développement 3D pour MAG Orthotics. Il s'occupe de toutes les impressions 3D de la société. Les podologues et les orthésistes envoient à MAG Orthotics un scan par e-mail ou une boîte d'empreinte en mousse (FIB) physique que MAG scanne ensuite. Cette prescription est ensuite envoyée à M. Lingard, qui déterminera la meilleure façon de concevoir et de fabriquer le dispositif.
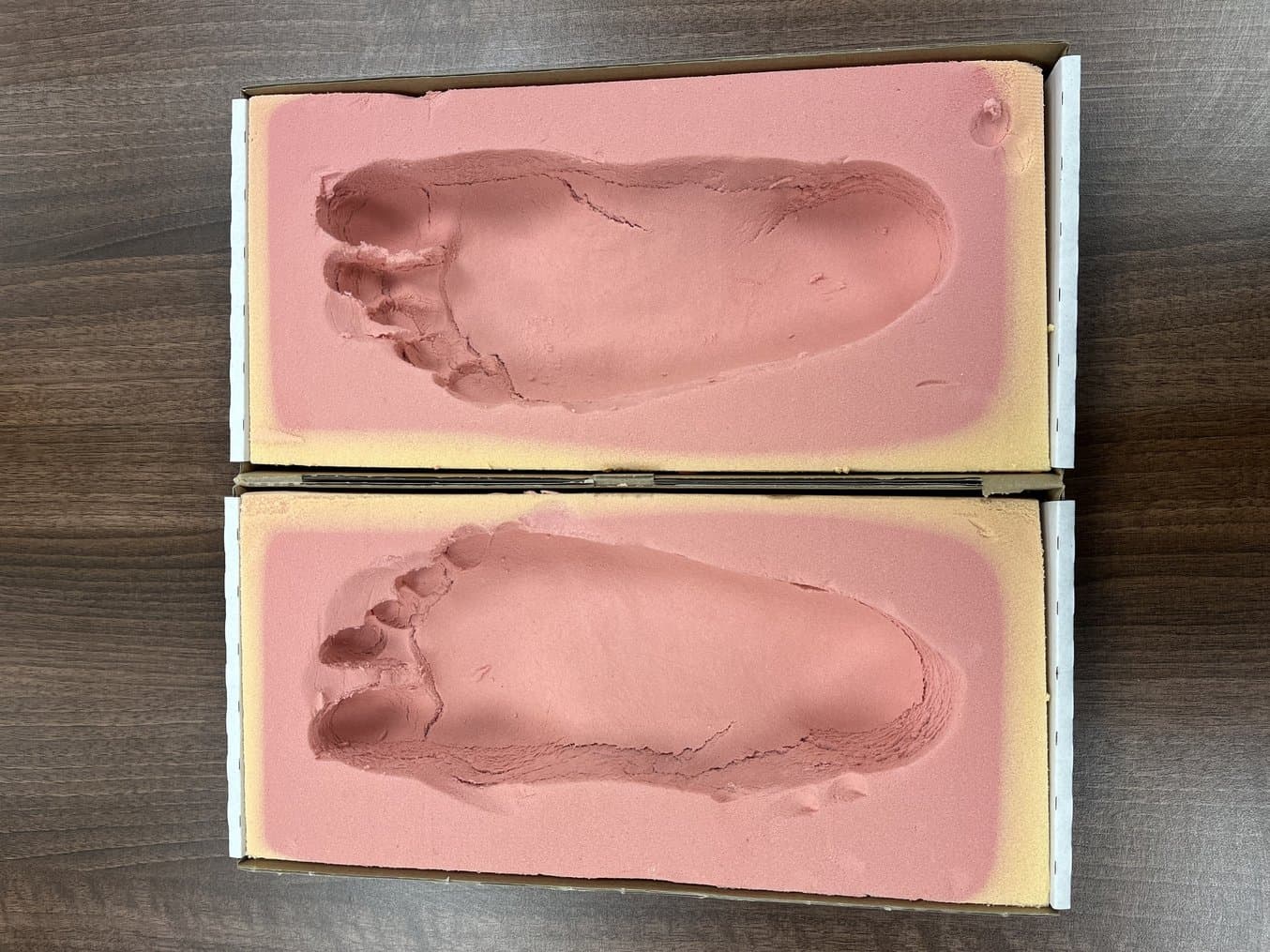
Certains techniciens orthopédistes et podologues envoient encore des empreintes physiques en mousse à MAG Orthotics.

Les empreintes en mousse doivent d'abord être scannées, ce qui prend plus de temps que dans le cas d'un processus de travail purement numérique.
La conception chez MAG Orthotics est réalisée avec Fit360, un logiciel de FAO pour la conception d'orthèses personnalisées pour le fraisage, l'usinage et l'impression 3D. Le choix de la méthode de fabrication utilisée dépend essentiellement du matériau demandé par l'orthésiste. Chez MAG Orthotics, la fabrication des dispositifs est réalisée sur des machines CNC, une imprimante FDM et deux imprimantes 3D à frittage sélectif par laser Fuse 1+ 30W.
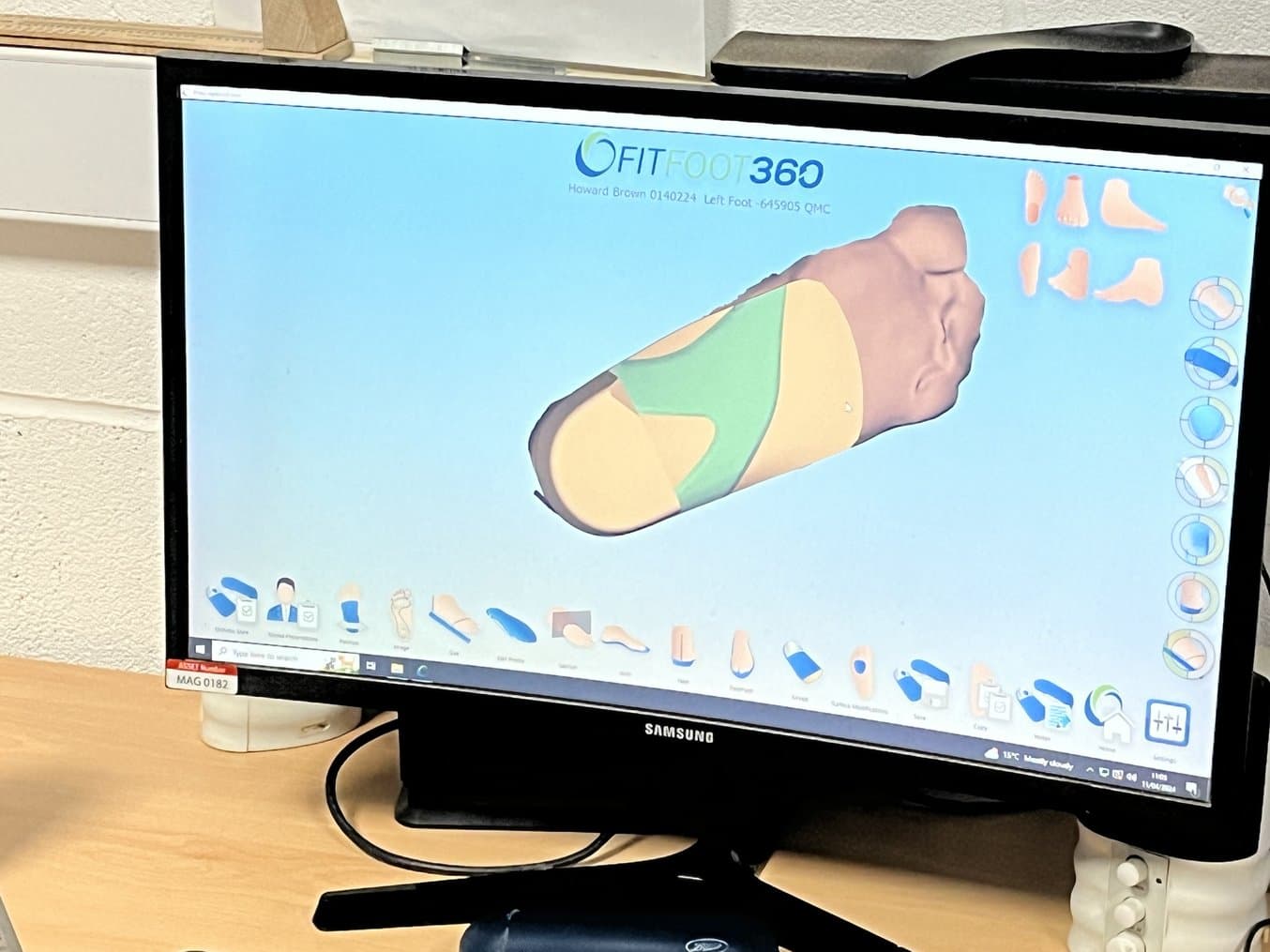
MAG Orthotics utilise le logiciel Fit360 pour concevoir ses semelles.
Chris Lawrie, propriétaire et directeur général de Fit360, déclare : « Ce qui est formidable dans notre collaboration avec MAG, c'est que le logiciel permet de choisir si le matériau doit être fraisé, imprimé à partir d'un matériau solide ou imprimé à partir d'un matériau souple avec une autre méthode. » À une époque où la production d'orthèses passe d'une technologie de fabrication à l'autre et d'un matériau à l'autre, ces options permettent à MAG de fournir l'orthèse prescrite tout en intégrant un flux de travail de conception cohérent.
S'éloigner des méthodes traditionnelles
Le passage d'un produit conventionnel fraisé à un produit imprimé en 3D est difficile, car il faut d'abord apprendre à maîtriser les nouvelles technologies et les processus de travail qui y sont associés. M. Lingard déclare : « Quand quelque chose de nouveau arrive sur le marché, j'ai très envie de l'apprendre, donc c'était passionnant pour moi. J'aime la technologie. »
Mais si M. Lingard embrasse l'avenir numérique, le secteur dans son ensemble n'a pas encore opéré sa transition. « Je fais de la conception CAO depuis 15 ans maintenant », explique M. Lingard, « mais il y a toujours des orthésistes qui demandent la méthode traditionnelle. Il y a donc là une grande lacune à combler pour nous. »
C'est la raison pour laquelle MAG utilise encore certaines méthodes de production traditionnelles. En tant que laboratoire, leur rôle est d'interpréter les prescriptions pour les mettre en forme. Pour l'instant, cela implique l'utilisation de quelques vieilles fraiseuses, tandis que la production est en train d'être convertie à des processus numériques plus respectueux de l'environnement.
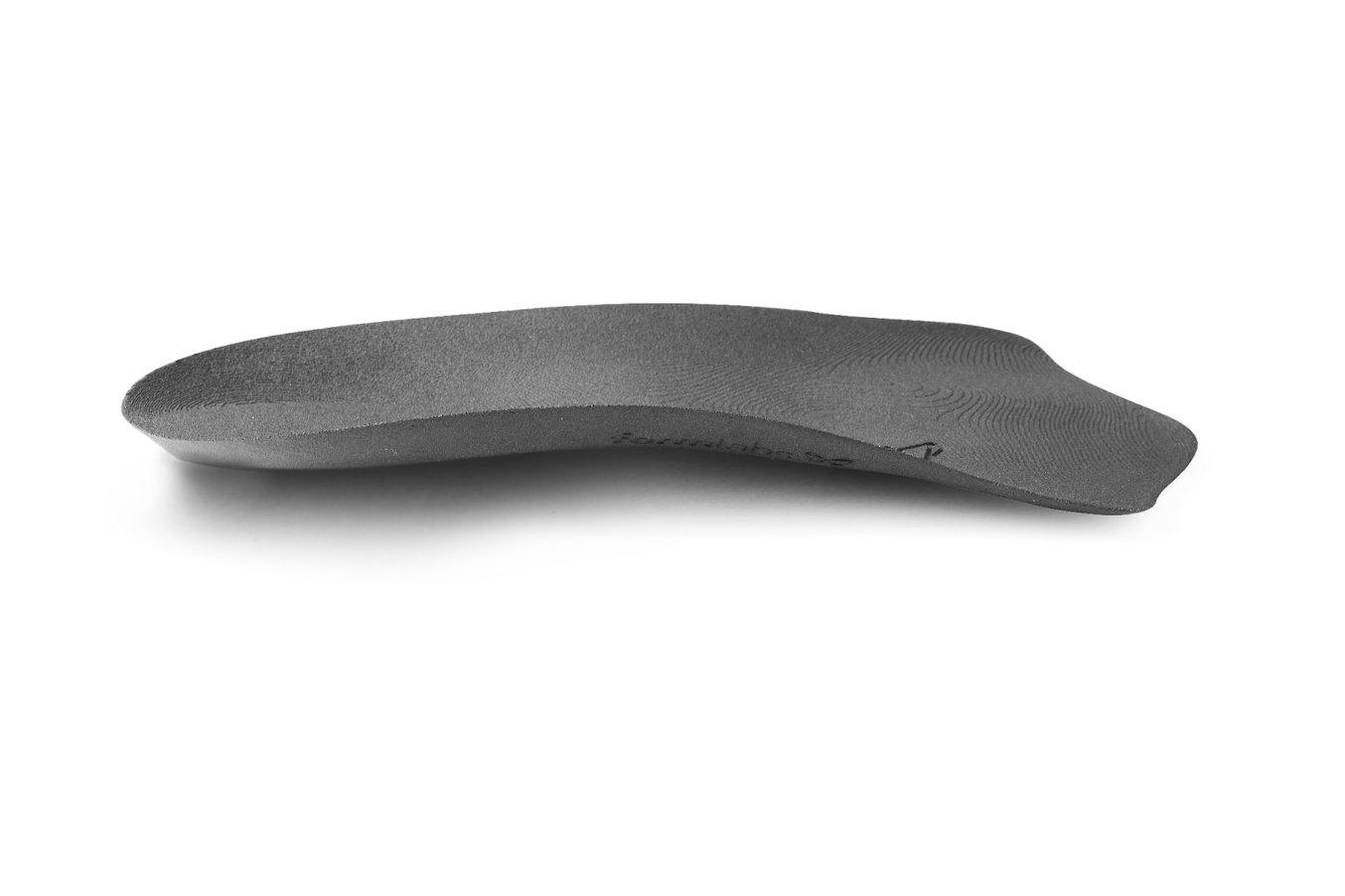
Commandez votre pièce imprimée 3D pour la coque de la semelle
Découvrez la puissance de Nylon 11 Powder et révolutionnez votre jeu de semelles intérieures. Profitez d'un retour élastique et d'une durabilité excellents, testés de manière indépendante pour dépasser les quatre millions de pas.
Se lancer dans l'impression 3D SLS
Mark Joyce, directeur de MAG Orthotics Works, considère l'impression 3D comme une étape importante pour se déplacer vers des processus plus durables. Au début, MAG a externalisé son processus d'impression 3D, juste pour voir comment cela se passait. La sous-traitance était coûteuse et ajoutait de la durée, car les orthèses devaient être expédiées à MAG Orthotics. À ce moment-là, selon M. Joyce, « nous avons pensé que nous devions nous-mêmes entrer dans le secteur. »
M. Joyce a travaillé avec Additive-X pour trouver l'imprimante qui conviendrait le mieux à ses activités. Les facteurs clés de leur évaluation étaient le coût, la longévité et la fiabilité. Après avoir recherché d'autres imprimantes SLS, M. Joyce a constaté que la plupart des autres solutions étaient trop complexes et trop chères. Il a donc opté pour la Fuse 1+ 30W, une imprimante dont les matériaux, le matériel et le prix correspondaient à ses ajustements.
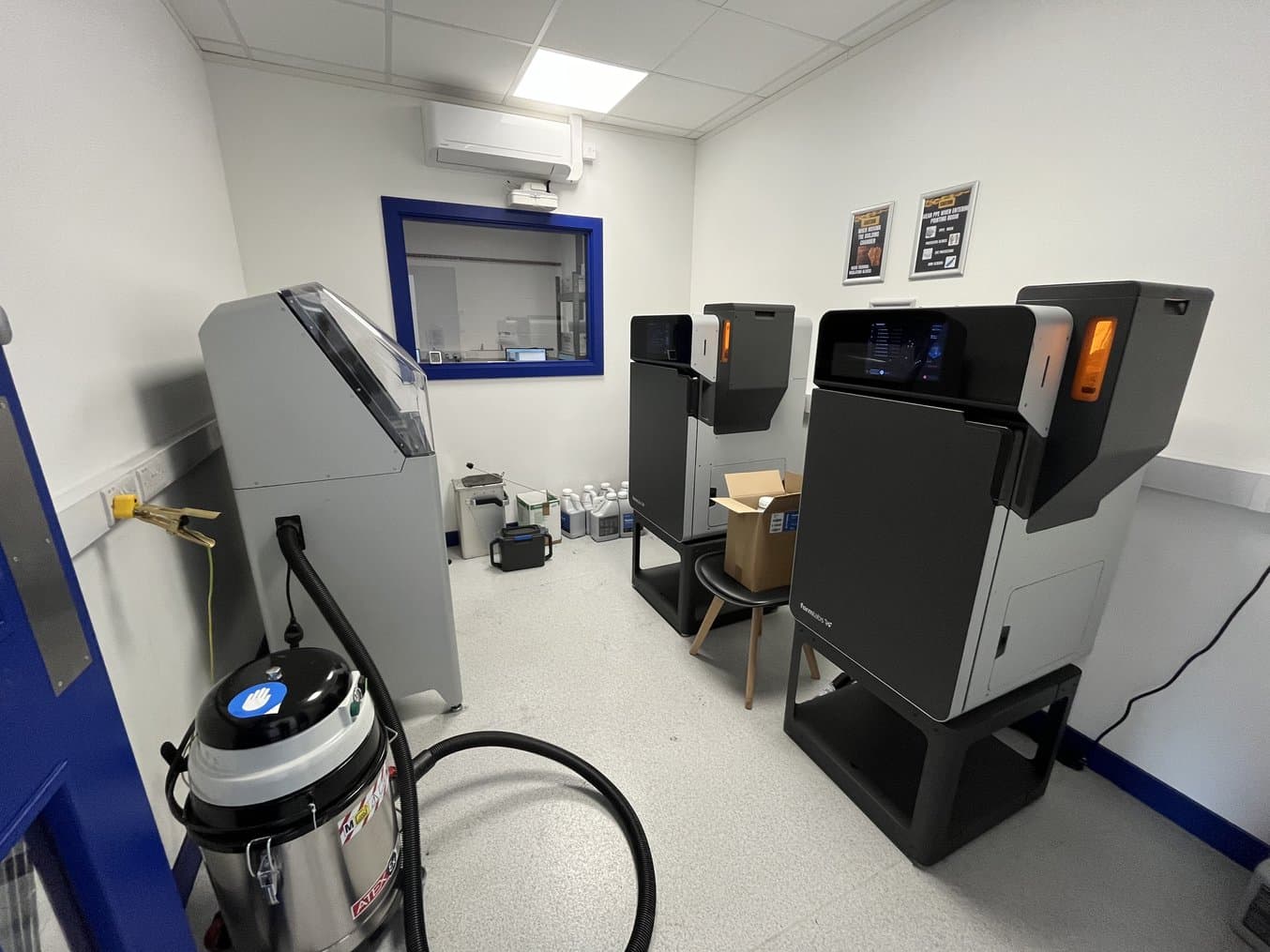
MAG Orthotics imprime en interne sur deux imprimantes 3D Fuse 1+ 30W (à droite), ce qui ajoute de la redondance à leur production.
L'équipe imprime maintenant sur la Fuse tous les jours. M. Lingard explique : « Nous utilisons encore des fraiseuses CNC, mais nous essayons d'introduire des imprimantes partout où c'est possible. » Mais l'un des principaux obstacles à l'adoption des flux de travail numériques n'est pas d'ordre interne.
« Notre plus grande bataille est celle des orthoprothésistes, car ils aiment les vieilles méthodes, il est difficile de les faire adopter ces nouvelles technologies », explique M. Lingard. Pour s'attaquer à ce problème, M. Lingard a commencé à offrir aux orthésistes une paire de semelles imprimées en 3D et EVA pour les comparer pour eux-mêmes. Une orthésiste, qui pratique la course à pied et la randonnée, a constaté qu'elle aimait les semelles imprimées en 3D après les avoir essayées pendant une semaine.
« C'est un coût pour nous, car il s'agit évidemment de temps, de délai de production, de matériaux, etc. Nous essayons de susciter l'enthousiasme des gens pour ces nouvelles technologies », explique M. Lingard. En investissant maintenant, MAG Orthotics ouvre la voie à une production plus propre et plus rapide à l'avenir.
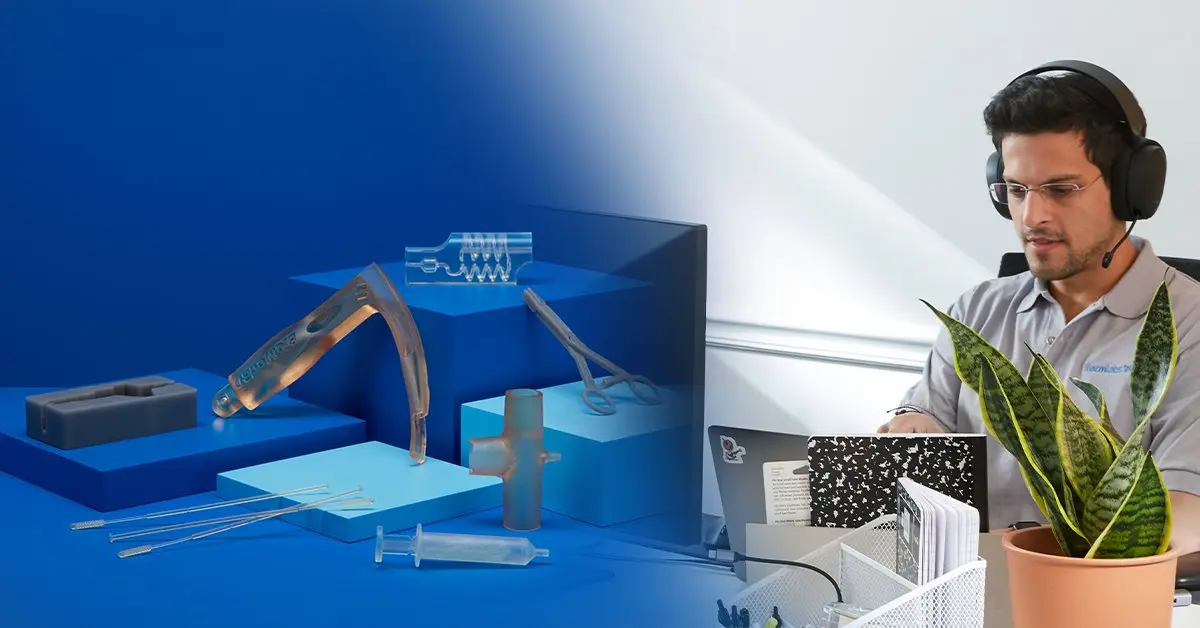
Discutez avec notre équipe commerciale médicale
Que vous deviez fabriquer des outils chirurgicaux adaptés aux patients ou un prototype de dispositif médical cardiaque, nous sommes là pour vous aider. L'équipe de Formlabs Medical est composée de spécialistes dévoués qui savent exactement comment vous soutenir et répondre aux besoins de votre entreprise.
Impression
Au Royaume-Uni, les appels d'offres tiennent compte de la politique « zéro décharge » et du bilan carbone. L'un des objectifs de MAG Orthesis dans le cadre de la transition vers des processus de travail numériques et l'impression 3D est également de réduire au minimum les déchets de fabrication.
« Avant, nous utilisions beaucoup de plâtre. Nous le modelions à la main, puis nous le recouvert d'EVA ou de polypropylène. Nous avons ensuite progressé et démarré l'utilisation de la conception CAO et des machines numériques contrôlées par ordinateur pour les usiner, mais il y avait encore beaucoup de déchets. Mais avec la poudre et le TPU, nous avons une production de déchets très, très faible, et c'est la voie écologique à suivre. »
Mark Joyce, directeur général, MAG Orthotics
En tant qu'imprimante SLS, la Fuse 1+ 30W imprime de la poudre. Contrairement à l'usinage CNC, où les matériaux qui ne font pas partie de la semelle finie sont éliminés, la poudre non frittée peut être réutilisée pour l'impression des inserts suivants.
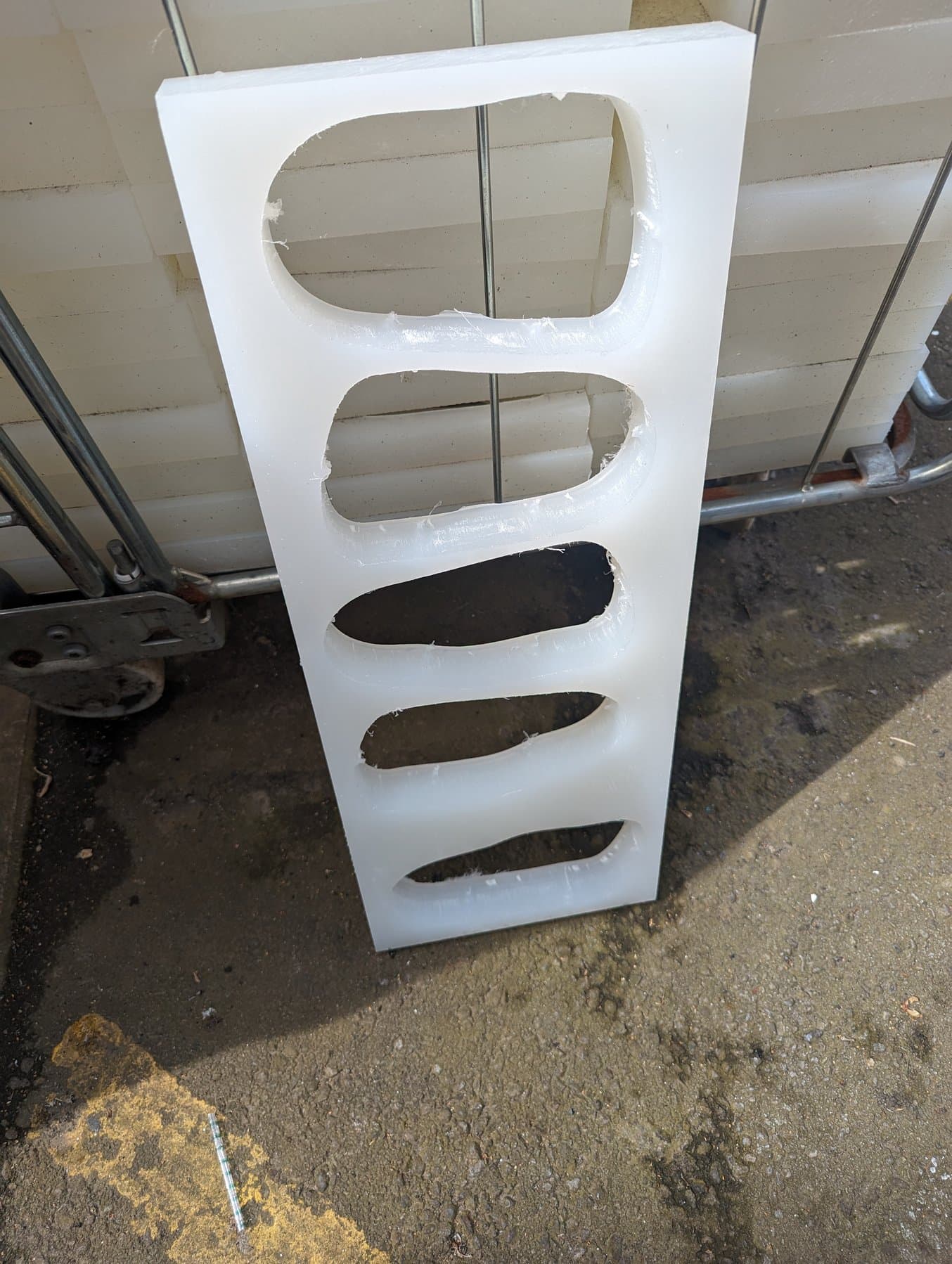
Les déchets de matériaux en polypropylène provenant de la fabrication CNC s'accumulent rapidement.
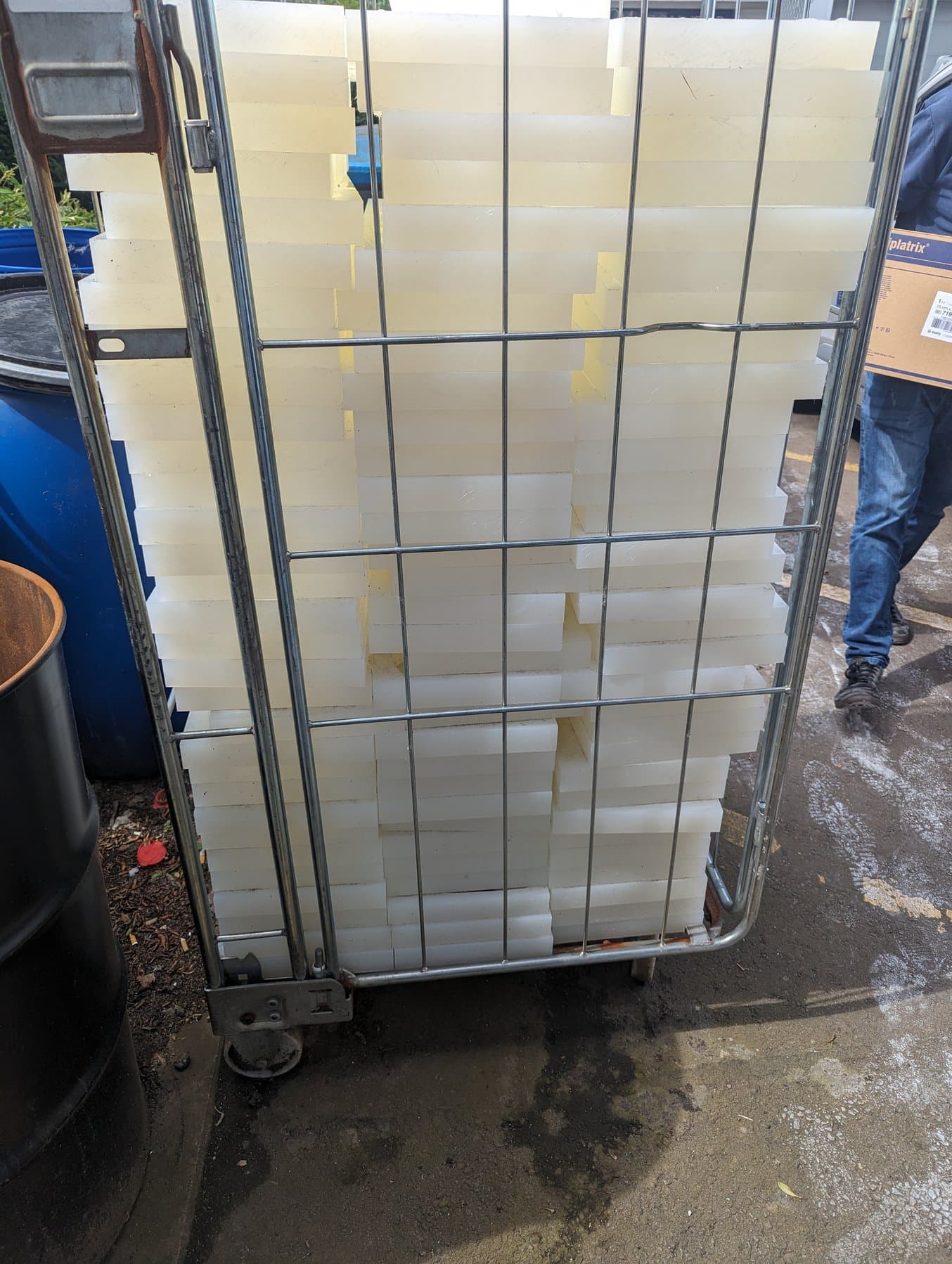
La réduction des déchets est l'une des principales raisons pour lesquelles MAG Orthotics a adopté l'impression 3D.
MAG imprime les semelles en Nylon 11 Powder, un matériau solide et très ductile approuvé pour le contact avec la peau. Nylon 11 Powder absorbe très peu d'humidité et est résistante à la lumière, à la chaleur et aux produits chimiques, ce qui en fait un matériau idéal pour la production de semelles intérieures. L'impression de Nylon 11 Powder dans une atmosphère de gaz inerte, dans ce cas de l'azote, signifie une oxydation plus faible de la poudre, ce qui conduit à un taux de renouvellement plus élevé et donc à encore moins de déchets.
En outre, en n'ayant pas à collecter les empreintes physiques auprès des fournisseurs, ils utilisent moins de carburant et soumettent les véhicules à moins d'usure, pour un processus plus respectueux de l'environnement du début à la fin.
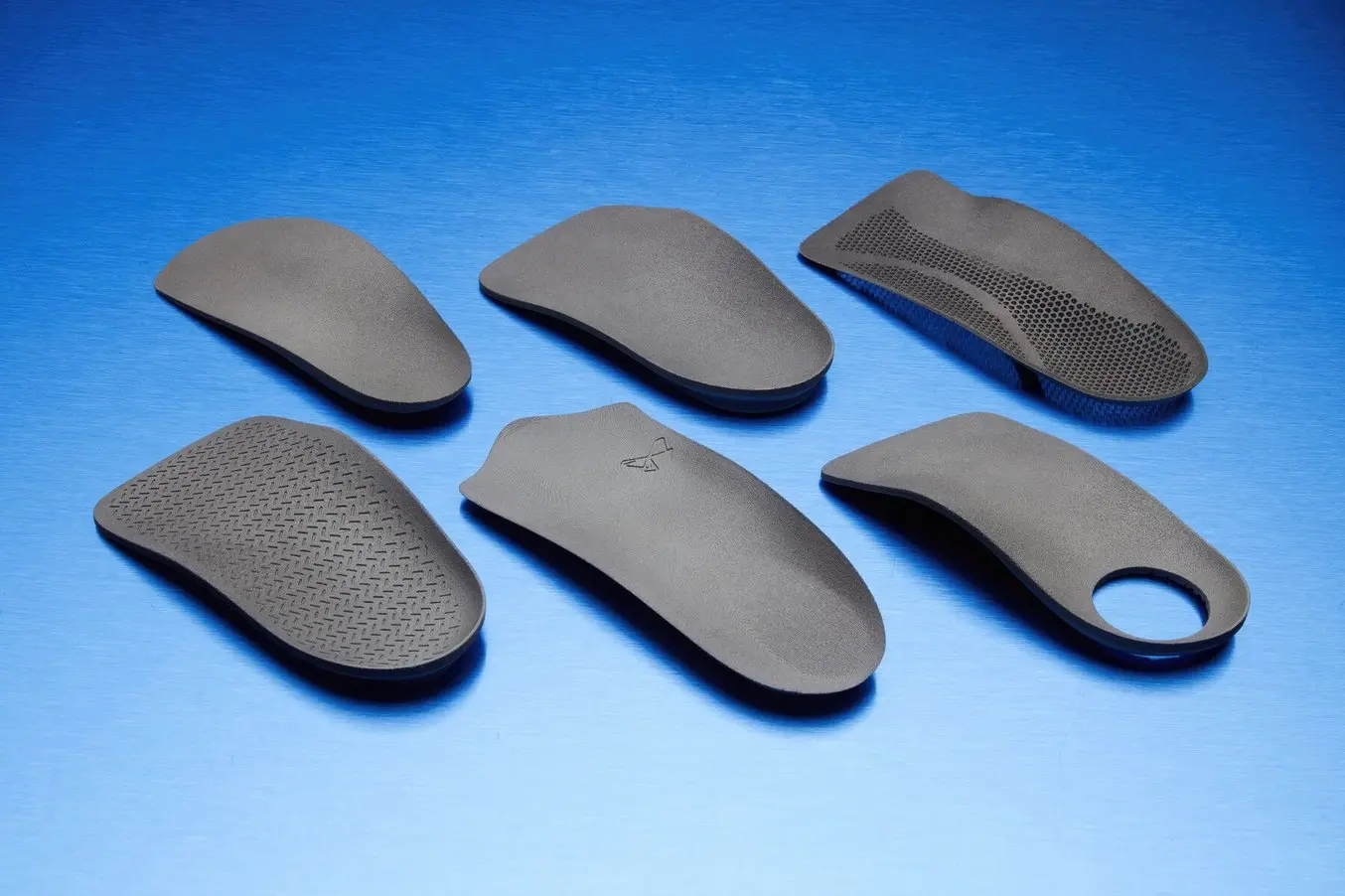
Révolutionnez votre production de semelles avec la Fuse 1+ 30W de Formlabs
Augmentez votre production de semelles tout en économisant du temps et de l'argent. Dans ce webinaire, nous expliquons pourquoi la Fuse 1+ 30W de Formlabs est la solution idéale pour commencer à passer à la fabrication numérique ou à augmenter votre production de manière abordable et efficace.
Gains de temps
Les flux de travail numériques ont un énorme potentiel pour réduire la durée de fabrication. Avec les procédés traditionnels, il fallait se rendre dans une clinique pour récupérer les empreintes. MAG s'efforce de « convaincre les entreprises et les cliniques d'investir dans un scanner portable qui leur permettra de scanner le pied », explique Joyce. « Quand un scan et une ordonnance sont envoyés par e-mail via un simple lien, on gagne immédiatement trois jours », explique Joyce.
« Avec la mousse EVA fraisée, il y a toutes les bavures et les chutes qu'il faut couper, et il faut appliquer des gabarits pour couper tout autour, puis tout lisser, tout mettre en forme : tout prend beaucoup plus de temps. C'est pourquoi nous aimons les semelles imprimées en 3D, car elles peuvent être fabriquées beaucoup plus rapidement et avec moins d'efforts. »
Lee Lingard, spécialiste du développement CAO et 3D, MAG Orthotics
Avec les flux de travail numériques, un podologue peut soumettre un scan numérique et une commande le lundi matin. Une heure plus tard, la commande est traitée et dans l'heure qui suit, Lingard peut concevoir les semelles orthopédiques. Ensuite, les semelles sont imprimées le lundi après-midi, l'impression se faisant en continu. Le lendemain, les semelles pouvaient être nettoyées et finies, pour un délai de fabrication d'un peu plus d'une journée.
En comparaison, l'utilisation d'empreintes en mousse prend environ 72 heures de plus, car il faut ajouter le temps de récupération et le traitement administratif de la commande. Même si la durée d'impression réelle peut être plus longue que le temps passé sur la machine CNC, une machine CNC nécessite une utilisation manuelle et un post-traitement important. Dès qu'une imprimante 3D est prête, l'impression proprement dite est entièrement automatique, ce qui permet aux employés de se consacrer à des tâches plus importantes ou de réaliser des impressions pendant la nuit. Les semelles provenant d'une imprimante SLS doivent être nettoyées, mais ne nécessitent guère d'autre post-traitement, ce qui signifie que le flux de travail numérique global prend moins de temps et de main-d'œuvre. Dans l'ensemble, M. Joyce affirme qu'ils minimisent le temps de fabrication des commandes en produisant des semelles avec l'impression 3D, en plus de diminuer leur empreinte carbone.
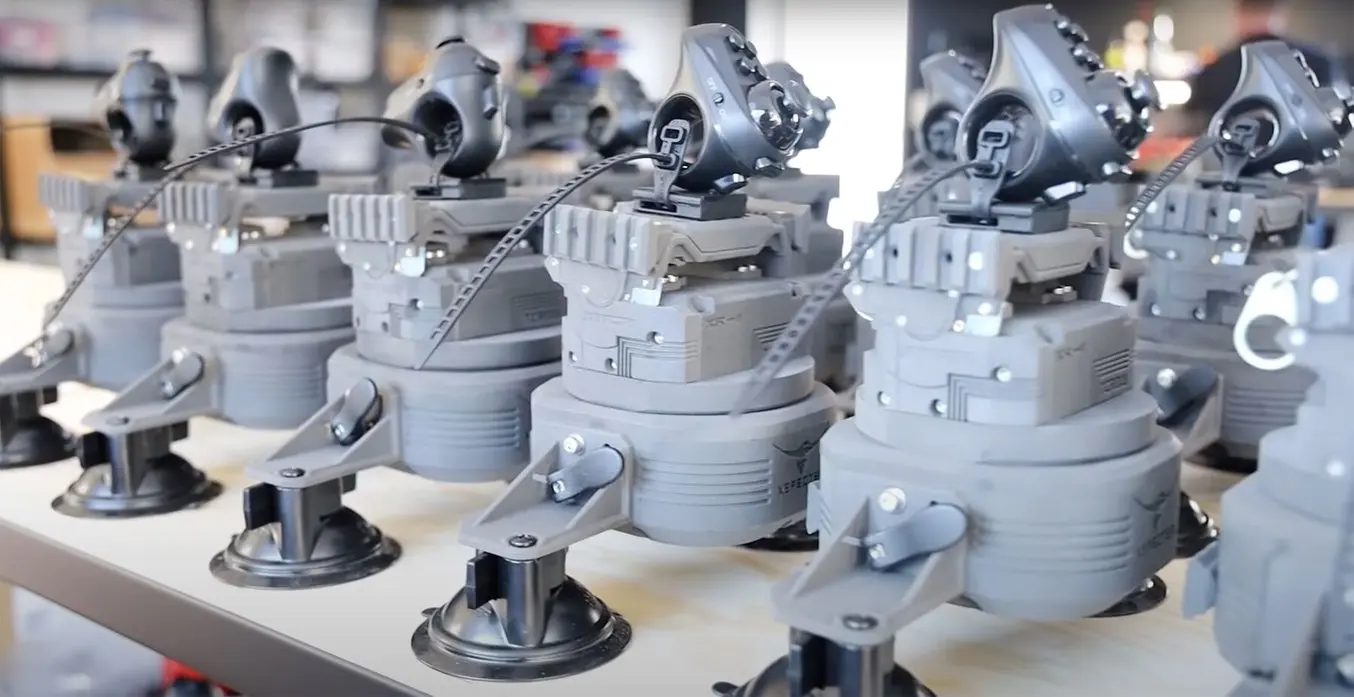
Le SLS pour la production finale
L'impression 3D pour la production finale n'est pas seulement accessible : elle est aussi plus abordable, plus agile et plus évolutive que jamais grâce à l'écosystème SLS Fuse. Explorez notre page dédiée à la production SLS pour comparer les différentes méthodes de fabrication, consulter les tarifs des poudres en vrac et découvrir comment 15 fabricants exploitent actuellement les imprimantes de la série Fuse.
En route vers l'avenir
MAG Orthotics continue de travailler avec les orthèses pour passer à des flux de travail numériques et adapte sa production de SLS. Deux imprimantes 3D Fuse 1+ 30W ajoutent une redondance pour l'impression, garantissant qu'il y aura toujours au moins une imprimante en fonctionnement. MAG Orthotics étudie également la possibilité de fournir un lissage à la vapeur, une étape de post-traitement courante effectuée sur les pièces imprimées en 3D par SLS pour améliorer la porosité et réduire la rugosité, afin d'obtenir une texture plus lisse et plus brillante.
En collaboration avec Fit360, Additive-X, Formlabs et son réseau d'orthésistes et de podiatres, l'équipe de MAG Orthotics s'efforce de passer à des processus de travail numériques et à réduire au maximum ses déchets. Les nouvelles technologies d'impression 3D telles que la Fuse 1+ 30W les y aident.
En savoir plus sur l'impression 3D de semelles orthopédiques ou discuter avec un expert en impression 3D pour trouver la solution adaptée à votre entreprise.
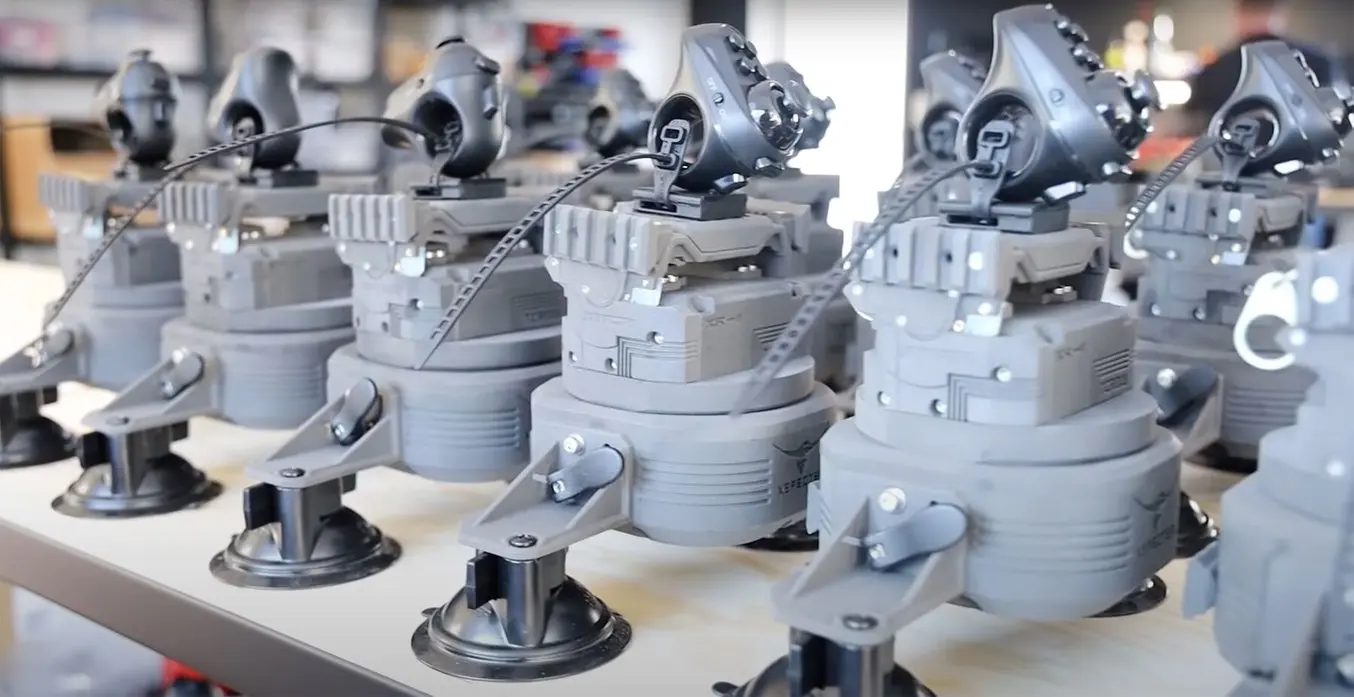
Le SLS pour la production finale
L'impression 3D pour la production finale n'est pas seulement accessible : elle est aussi plus abordable, plus agile et plus évolutive que jamais grâce à l'écosystème SLS Fuse. Explorez notre page dédiée à la production SLS pour comparer les différentes méthodes de fabrication, consulter les tarifs des poudres en vrac et découvrir comment 15 fabricants exploitent actuellement les imprimantes de la série Fuse.