Des inhalateurs innovants et bon marché accessibles à des millions de personnes : simplifiez vos processus R&D grâce à l'impression 3D
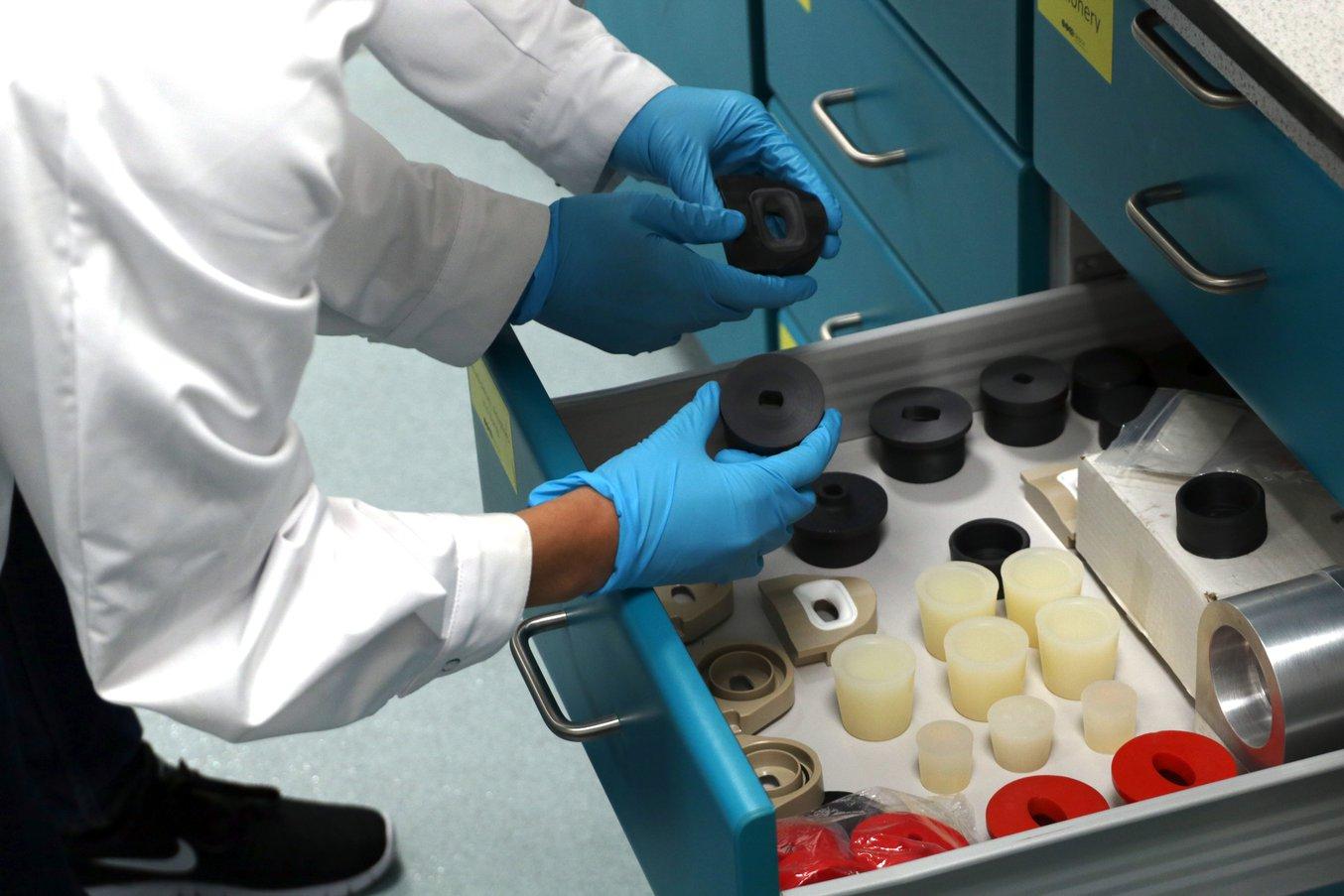
L'équipe de Coalesce Product Development crée des dizaines de prototypes pour chaque dispositif médical.
Selon l'Organisation mondiale de la santé, on estime que 262 millions de personnes dans le monde souffrent d'asthme, ce qui entraîne près d'un demi-million de décès. Pour les personnes souffrant de problèmes respiratoires tels que l'asthme ou la bronchopneumopathie chronique obstructive (BPCO), un dispositif d'inhalation est nécessaire pour faciliter la respiration. Les médicaments inhalés peuvent contrôler les symptômes de l'asthme et permettre aux personnes asthmatiques de mener une vie normale et active. Malheureusement, beaucoup ne peuvent s'offrir ou n'ont pas accès à ce genre de dispositifs, en particulier les personnes non assurées et celles des pays à faible revenu. Des études publiées dans « Annals of American Thoracic Society » et dans « Journal of Allergy and Clinical Immunology » ont estimé que les coûts annuels par personne pour le traitement de l'asthme se situaient entre 1800 et 4900 $ pour les seules prescriptions d'inhalateurs et de médicaments, ce qui comprend les coûts directs (par exemple, les médicaments et les visites chez le médecin) et les coûts indirects (par exemple, les congés non payés). Une enquête sur les coûts de la santé réalisée en 2005 a révélé que 44 % des personnes asthmatiques ont cessé de prendre leurs médicaments ou de se rendre chez le médecin pour faire des économies.
La société britannique Coalesce Product Development, spécialisée dans les dispositifs médicaux, cherche à résoudre certains de ces problèmes. L'entreprise met au point des dispositifs d'administration de médicaments innovants, notamment des inhalateurs et des injecteurs, destinés à être utilisés dans des produits d'inhalation génériques offrant une valeur nettement supérieure à celle des produits de marque, qui peuvent coûter plus de 380 $ par mois.
Les inhalateurs doivent être utilisables par toutes sortes de personnes, des adolescents aux patients âgés présentant des comorbidités. Par conséquent, la taille, la forme et l'interface utilisateur de chaque nouvel inhalateur doivent être conçues et testées avec soin. Pour y parvenir, l'équipe de Coalesce s'est tournée vers l'impression 3D en interne pour prototyper, tester et fabriquer divers dispositifs de formes et de tailles différentes. Pour tester chaque produit en cours de développement, l'entreprise développe également ses propres bancs d'essai, gabarits et montages imprimés en 3D.
Pour cet article, nous nous sommes entretenus avec Vinnay Chhabildas, designer industriel chez Coalesce, qui nous a expliqué comment l'équipe a étendu son utilisation de l'impression 3D au cours des cinq dernières années, pourquoi elle continue d'investir dans les produits Formlabs pour développer ses dispositifs médicaux, et quelles résines elle utilise en fonction des différentes applications.
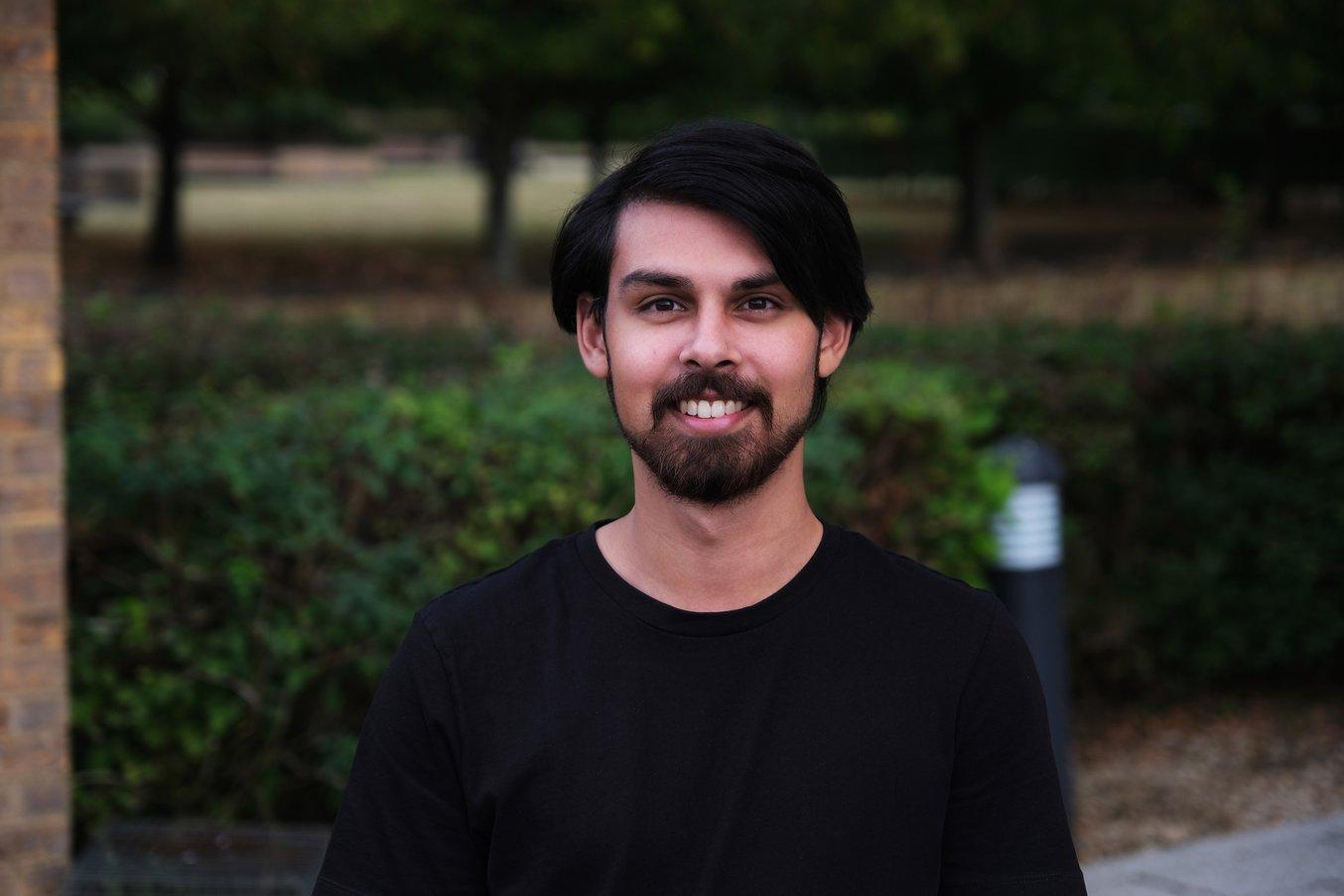
Coalesce Product Development
Vinnay Chhabildas utilise l'impression 3D pour créer des prototypes visuels, réduire la sous-traitance et produire des itérations de conception plus rapidement. Le résultat en est un dispositif d'administration de médicaments innovant.
Investir dans l'écosystème Formlabs pour fabriquer des dispositifs médicaux
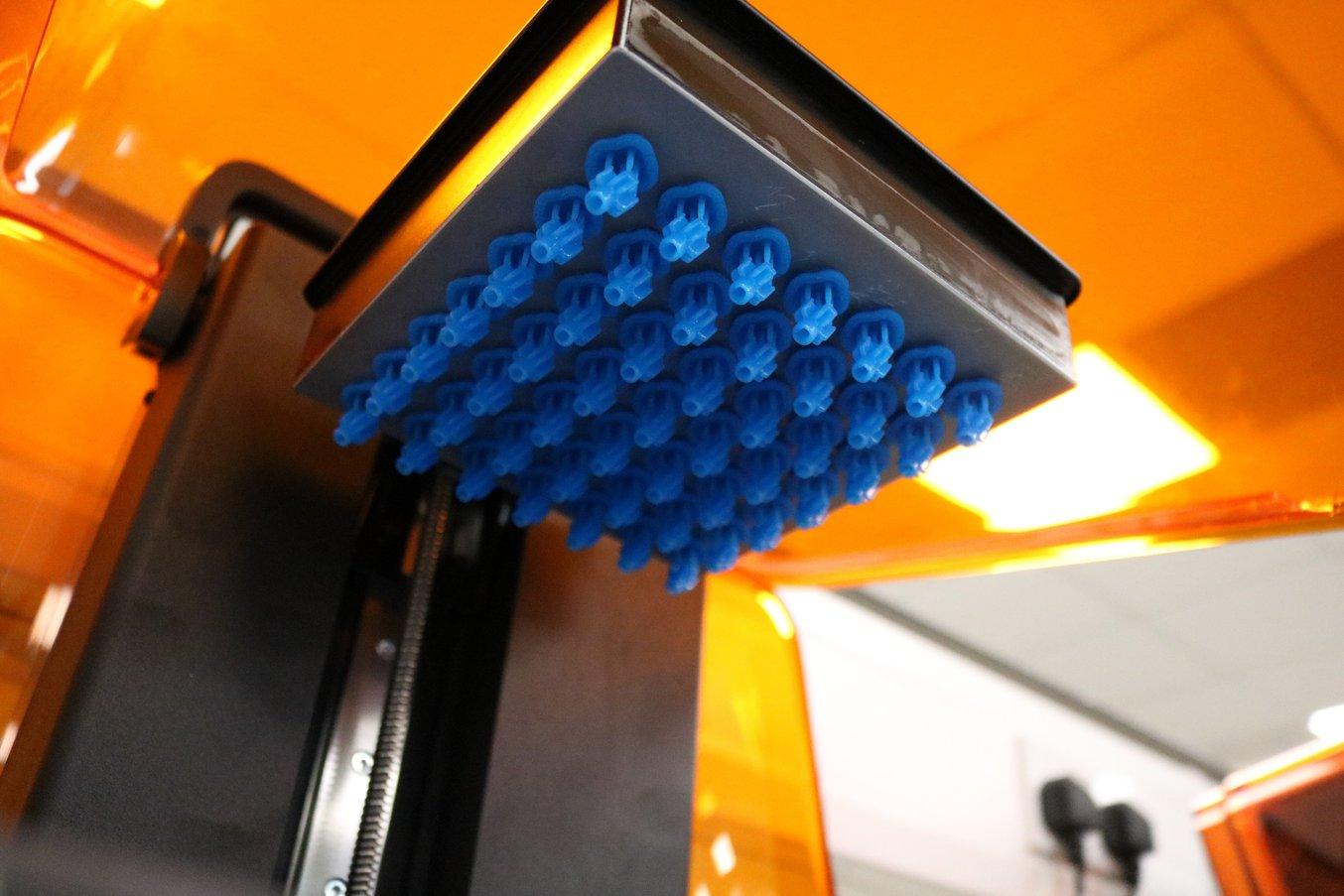
Draft Resin est utilisée pour tester les fixations avant qu'elles ne soient usinées.
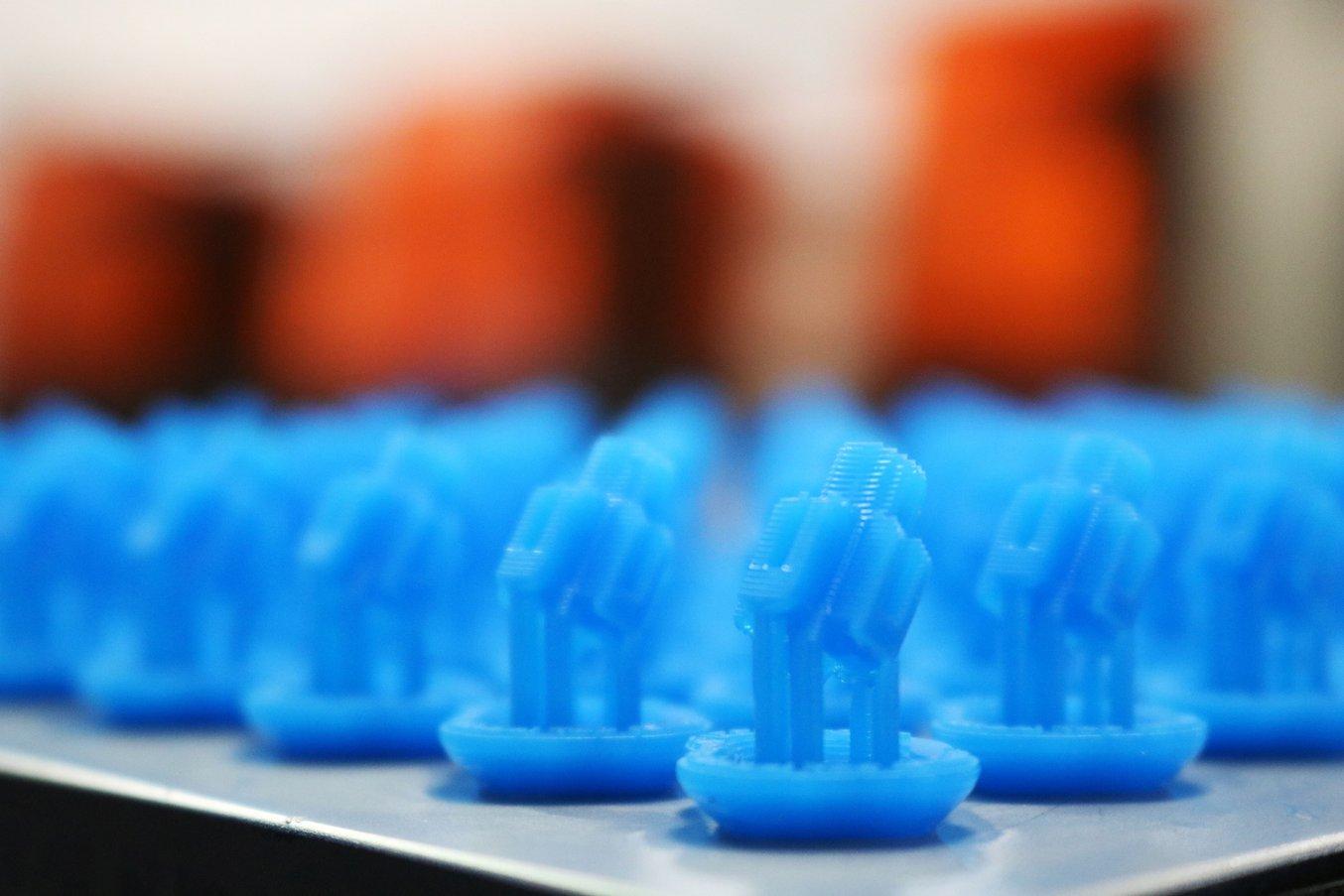
Coalesce a d'abord investi dans une imprimante 3D stéréolithographique (SLA) Form 2 lors de sa sortie en 2015. À l'époque, l'équipe dépendait encore largement de la sous-traitance pour produire ses prototypes, et devait attendre plusieurs jours pour que les pièces arrivent par la poste. L'équipe a rapidement fait l'achat de plusieurs Form 2, et a ainsi pu devenir beaucoup moins dépendante de la sous-traitance.
Coalesce a utilisé la Form 2 pour développer et prototyper la structure de plusieurs dispositifs d'inhalation et d'auto-injection. Par exemple, pour les boîtiers de son dispositif électronique de profilage de la respiration (BPD), les concepteurs ont choisi White Resin pour sa finition lisse et ses propriétés mécaniques, qui leur ont permis de percer dans le matériau et d'ajouter des inserts en laiton.
Vinnay a déclaré que « la stéréolithographie offre un bon équilibre entre le niveau de détail, la finition de surface, la durabilité, le choix des matériaux et la précision dimensionnelle. Comme nous développons des dispositifs comportant des pièces mobiles, nous avions besoin d'un moyen efficace de prototyper de petits mécanismes en interne. Nous avons suivi les progrès de la technologie d'impression 3D au cours des dernières années, et l'approche de Formlabs nous a plu. Lorsque la Form 2 est sortie, nous en avons commandé une immédiatement, suivie d'une deuxième quelques semaines plus tard. »
Dans un premier temps, les prototypes imprimés en 3D ont été utilisés pour développer la structure extérieure du BPD. Une fois la conception aboutie, les pièces imprimées ont été peintes et exposées à la conférence Drug Delivery to the Lungs (DDL), un rassemblement annuel pour les spécialistes de l'administration de médicaments par voie pulmonaire et nasale. Les prototypes de BPD étaient si réalistes qu'on pouvait les confondre avec un produit final.
Par la suite, les mêmes prototypes de dispositifs ont été utilisés dans une étude clinique sur la fonction pulmonaire. Les résultats ont montré à quel point les variations peuvent être importantes entre les différents profils d'inhalation.
Passer par des sous-traitants aurait coûté environ 20 fois plus cher que le coût brut de l'impression des pièces en interne. L'impression des boîtiers du BPD avec la Form 2 coûte 11 £, contre environ 250 £ si l'on passe par des sous-traitants. Mais selon M. Vinnay, le principal avantage est le gain de temps : il n'a fallu que huit heures pour imprimer les pièces, qui ont pu être peintes et recevoir une finition en quelques jours. Le même processus prendrait une semaine ou deux à un entrepreneur externe.
Boîtier d'inhalateur | Impression 3D en interne | Impression 3D sous-traitée |
---|---|---|
Coût | 13€ | 295€ |
Délai de production | 1 à 2 jours | 1 à 2 semaines |
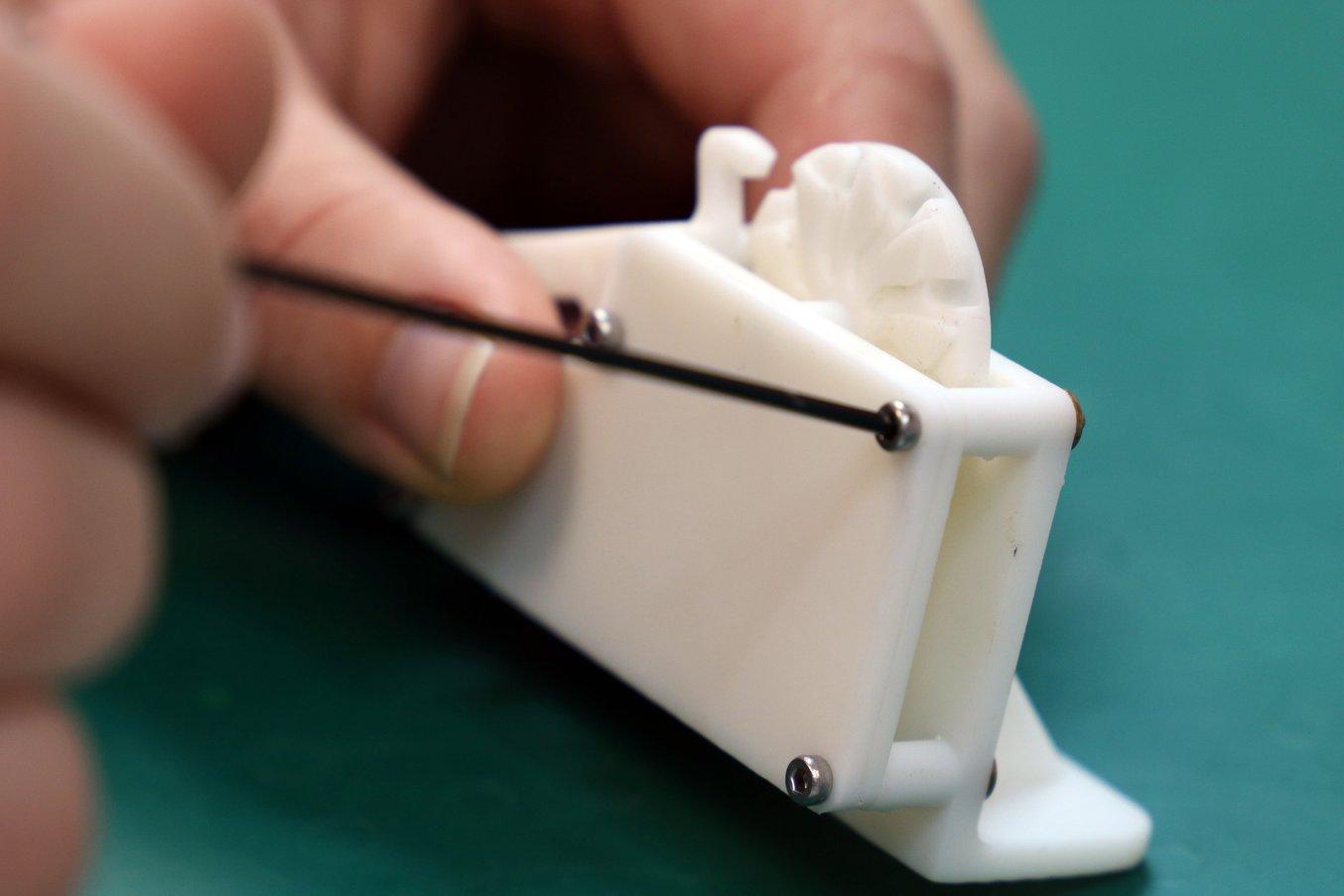
Des filets de vis peuvent être facilement insérés dans des pièces imprimées en 3D, dans le cas présent avec White Resin.
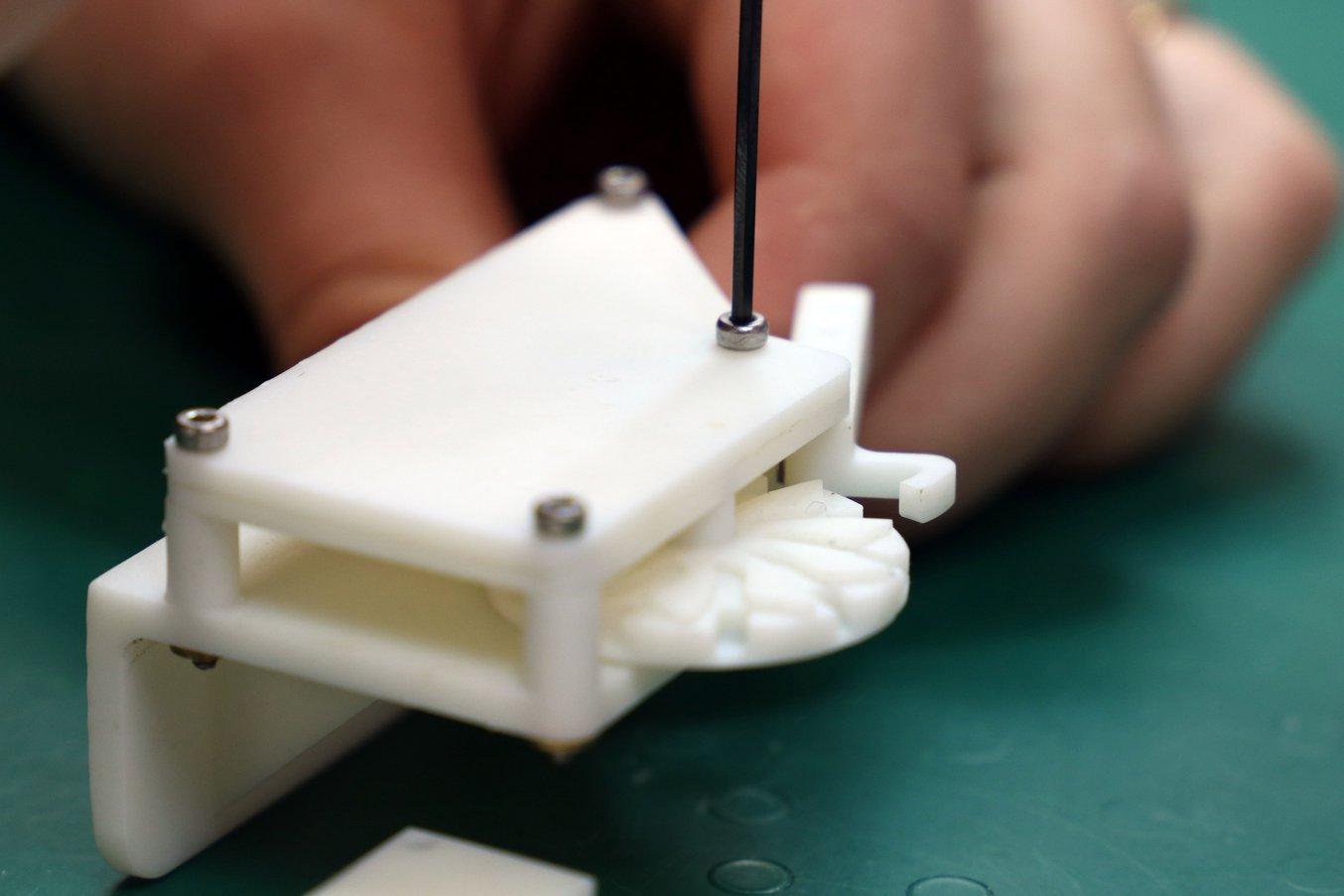
Développer l'impression 3D en interne avec la Form 3
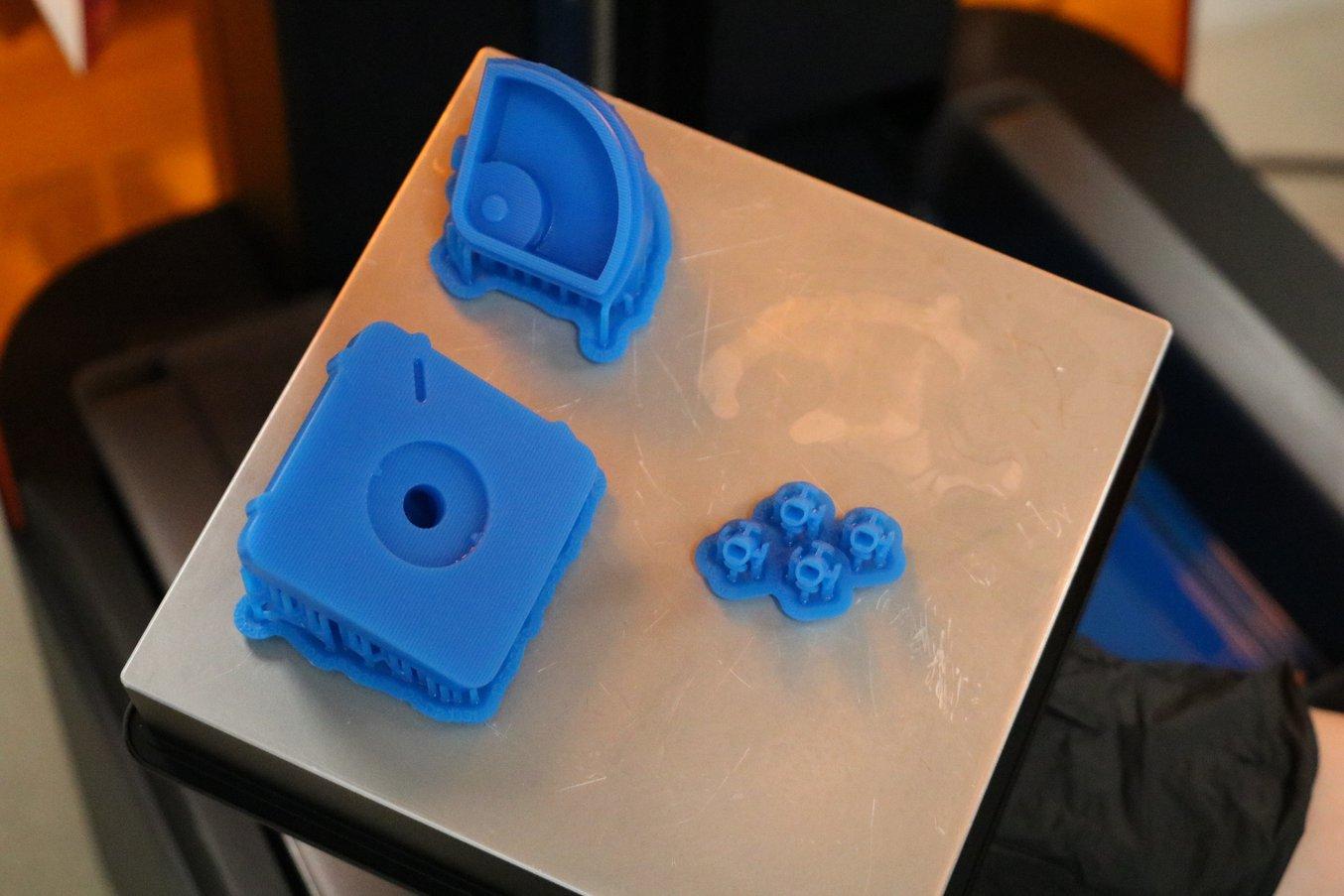
Le prototypage rapide est essentiel au succès de Coalesce.
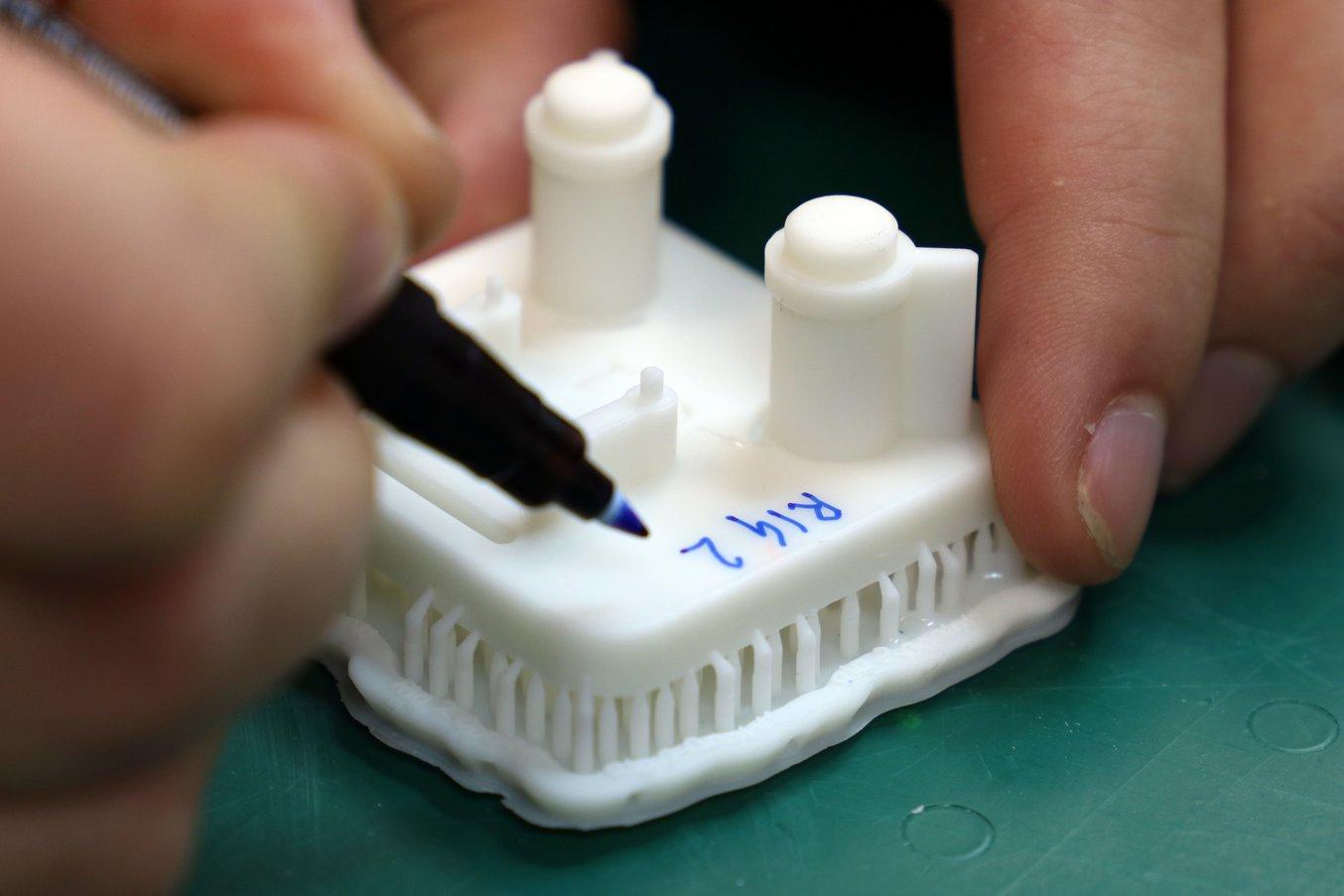
Après avoir constamment utilisé la Form 2 pendant des années et imprimé en 3D la plupart des pièces en interne, l'équipe a modernisé son parc en achetant trois Form 3.
Avec la Form 3, Coalesce a pu continuer à produire des prototypes visuels et esthétiques, mais aussi véritablement intégrer l'impression 3D dans le développement de ses dispositifs, et reproduire de minuscules détails internes. Grâce à la précision de la technologie Low Force Stereolithography (LFS) dont est équipée la Form 3, l'équipe a pu résoudre les principaux problèmes liés au développement des inhalateurs. Il faut par exemple pouvoir analyser la distribution des particules fines des médicaments en poudre sèche à l'aide de tests analytiques, afin de garantir une administration régulière et précise.
Vinnay a résumé la situation en disant que « la Form 3 nous a permis d'imprimer des détails fins et des maillages délicats, et d'optimiser le dispositif pendant la phase de conception. Nous avons la possibilité de modéliser une pièce, de la modifier quand nous le souhaitons et d'obtenir la pièce physique en quelques heures. Nous n'avons plus besoin de fournisseur tiers, et nous obtenons les pièces plus rapidement. Nos Form 3 sont absolument essentielles pour notre activité. Je ne sais pas ce que nous ferions sans elles. »
Aujourd'hui, l'équipe utilise ses trois Form 3 non-stop, cinq jours par semaine, ce qui les rend indispensables au processus de développement. L'équipe utilise l'impression 3D pour de plus en plus d'applications, et imprime désormais des outils pour aider à tester ses dispositifs. Ils impriment par exemple des embouts buccaux avec BioMed Clear Resin, un matériau biocompatible et sans danger pour la peau, et les testent sur des patients. L'impression 3D permet à l'équipe d'éviter de mouler par injection des pièces coûteuses en plastique.
Vinnay nous a expliqué que la raison pour laquelle son équipe est restée fidèle à Formlabs est « qu'il n'y a pas de meilleure alternative aux imprimantes Formlabs sur le marché. D'autres plateformes existent, mais aucune ne peut offrir la qualité d'impression, la fiabilité et la facilité d'utilisation auxquelles Formlabs nous a habitués. Notre expérience avec PreForm et de Dashboard est si positive que tout autre produit nous paraît inférieur. Depuis que nous avons commencé à utiliser la Form 2 et que nous sommes passés à la Form 3, nous n'avons pas utilisé d'autre imprimante. »
Une large gamme de matériaux d'impression 3D SLA
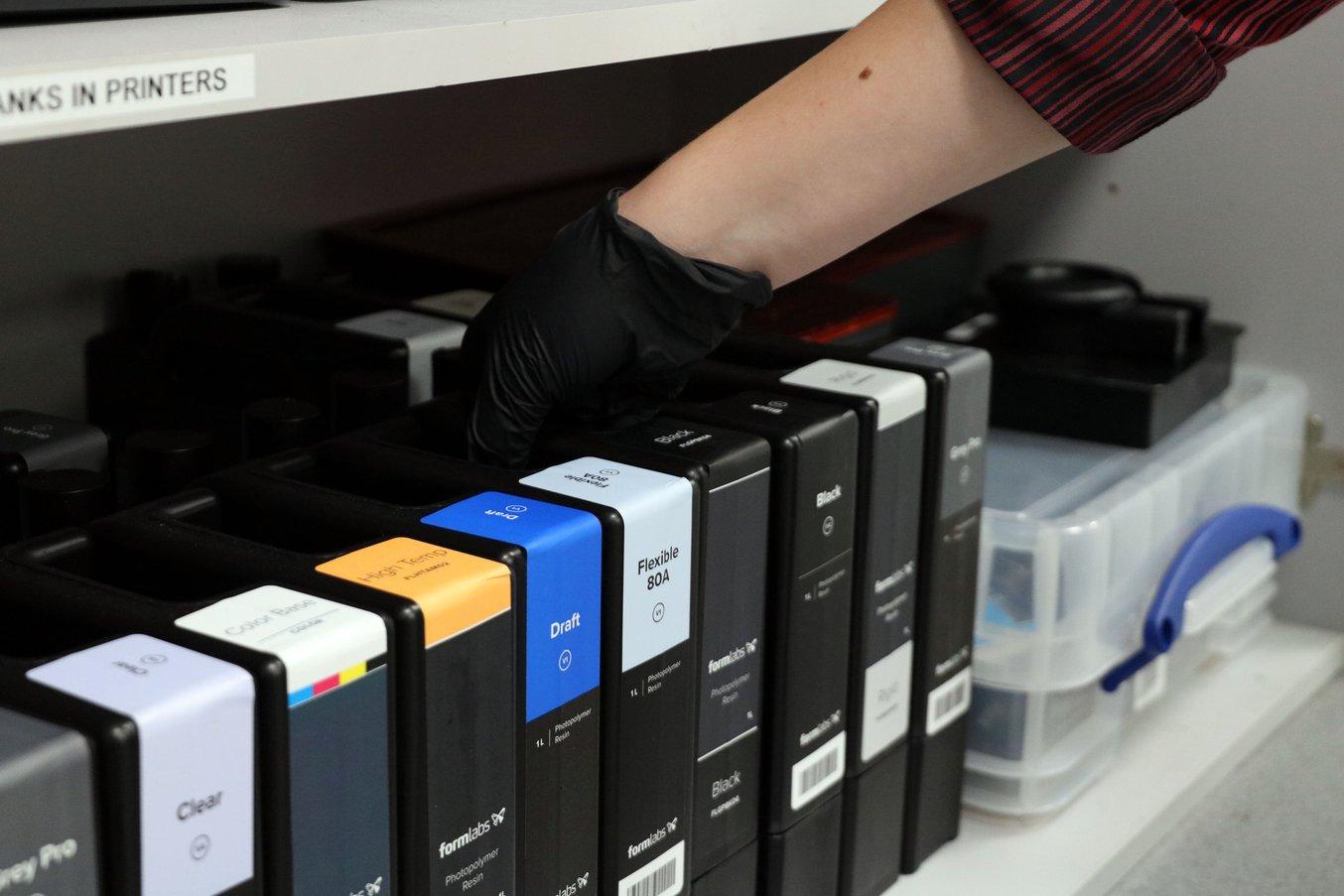
Coalesce utilise beaucoup de résines Formlabs.
L'un des principaux avantages de l'impression 3D SLA est sa vaste gamme de matériaux. Cela permet à une seule Form 3 de jouer plusieurs rôles au sein d'une organisation, car elle peut imprimer différents types de pièces en fonction de l'application.
Afin d'accélérer la fabrication de gabarits d'essai, l'équipe s'est tournée vers Draft Resin pour créer des pièces plus rapidement. Avec Draft Resin, des fixations peuvent être imprimées en une heure environ. Le temps gagné est précieux, et Vinnay nous dit que « l'équipe dispose également d'une machine CNC en interne. C'est incroyable de pouvoir imprimer en 3D et juger de l'apparence d'une pièce CNC sans même avoir à configurer la machine CNC. »
Coalesce utilise la gamme de matériaux Formlabs de la manière suivante :
Draft Resin est utilisée pour tester les fixations avant qu'elles ne soient usinées. Grâce à la vitesse d'impression du matériau, l'équipe est en mesure d'itérer rapidement différents modèles de fixations, et de modifiaer les trous de fixation et les montages à vis. En imprimant plusieurs fixations à la fois, l'équipe peut accélérer les tests de ses inhalateurs.
Hight Temp Resin est utilisée pour créer des outils fonctionnant en conjonction avec un outil de thermoscellage. Étant donné que de nombreuses pièces de l'inhalateur doivent être thermoscellées, il est essentiel d'utiliser de l'outillage personnalisé pour mieux contrôler le processus. Selon M. Vinnay, ces pièces ne sont souvent pas usinables, et l'impression 3D leur permet de créer des outils de forme parfaite.
Rigid Resin est également utilisée pour l'outillage. L'équipe estime que Rigid Resin est parfaite pour les petites caractéristiques complexes qui doivent conserver leur précision dimensionnelle, comme par exemple les petites formes maillées qui doivent résister aux forces du flux d'air.
Grey Pro Resin est utilisée de la même façon que Rigid Resin, principalement pour imprimer des fixations et de l'outillage. L'équipe de Coalesce a constaté que Grey Pro Resin résiste mieux à l'usure, et qu'elle convient donc pour imprimer des engrenages ou des pièces subissant une friction.
Les résines standard (White Resin et Black Resin) sont utilisées pour les modèles esthétiques. White Resin est parfaite pour les boîtiers extérieurs, car elle est facile à peindre. Des modèles en White Resin entièrement peints et post-traités sont utilisés comme modèles de présentation avant qu'un appareil ne soit validé pour la production finale.
BioMed Clear Resin est utilisée pour imprimer les embouts buccaux qui sont ensuite testés par de vrais patients. Coalesce fait appel à un cabinet de conseil en facteurs humains pour ses essais, et BioMed Clear Resin permet d'imprimer et de tester toutes sortes de modèles à moindre coût. Sans BioMed Clear Resin, ces pièces en plastique devraient être moulées par injection.
Elastic 50A Resin est principalement utilisée dans le laboratoire chimique de Coalesce pour créer des adaptateurs personnalisés destinés à un simulateur pulmonaire. L'adaptateur doit sceller l'embout buccal testé, ce qui n'est possible qu'avec une pièce semblable au silicone. Elastic 50A Resin peut se plier, s'étirer, se comprimer et résister à des cycles répétés sans se déchirer, ce qui la rend parfaite pour les adaptateurs.
Clear Resin est utilisée comme type de matériau de remplissage en raison de son aspect transparent. L'équipe assemble les dispositifs imprimés avec Clear Resin, polit la résine, puis observe comment les différents composants fonctionnent à l'intérieur de l'inhalateur. Cela leur permet d'examiner des détails internes qui ne seraient pas visibles en imprimant avec Black Resin ou Grey Pro Resin.
L’impression 3D pour les dispositifs médicaux
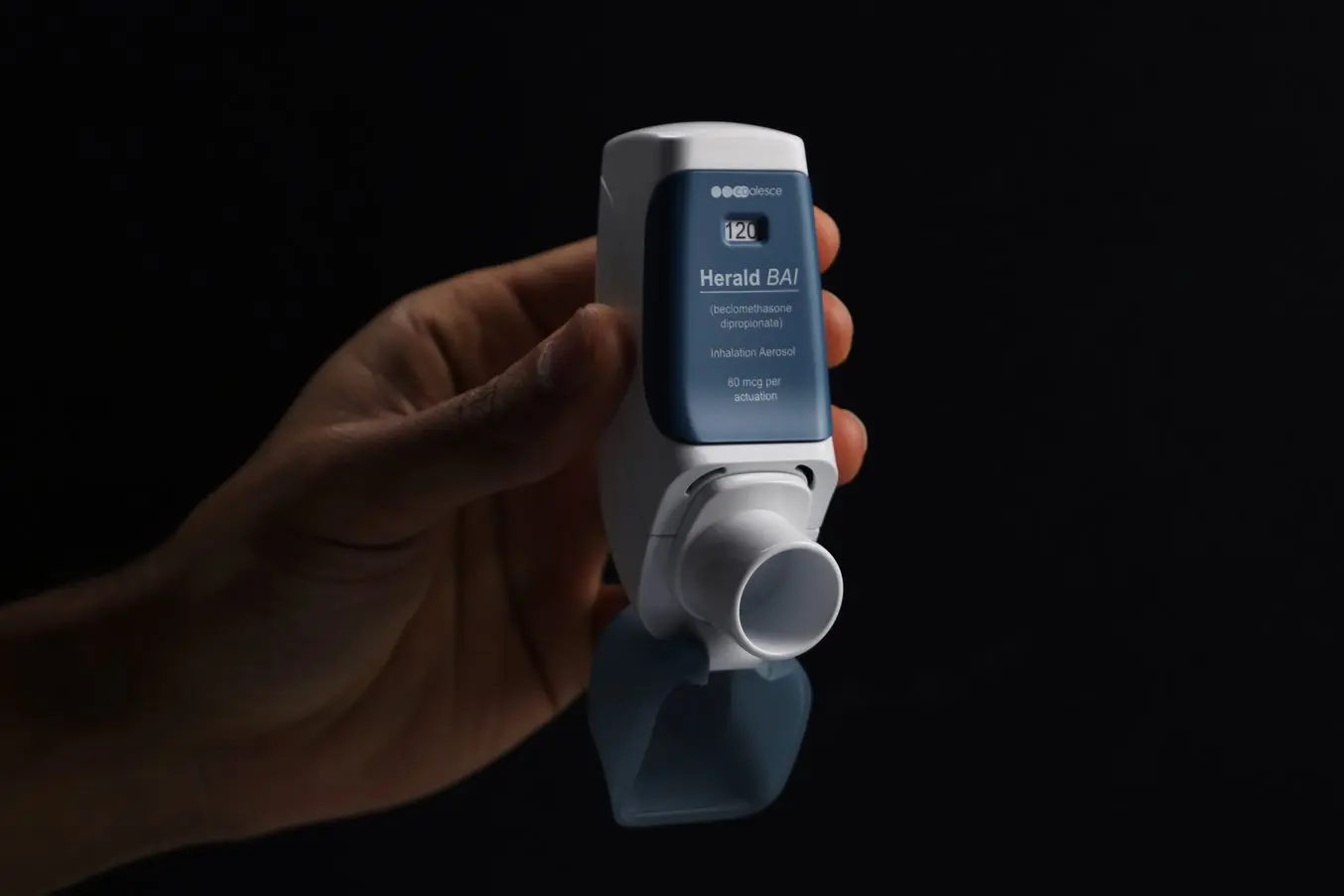
Les inhalateurs actionnés par la respiration (BAI) sont semblables aux dispositif de type « appuyer et respirer », mais ils sont plus faciles à utiliser : les patients n'ont qu'à ouvrir, inspirer et fermer.
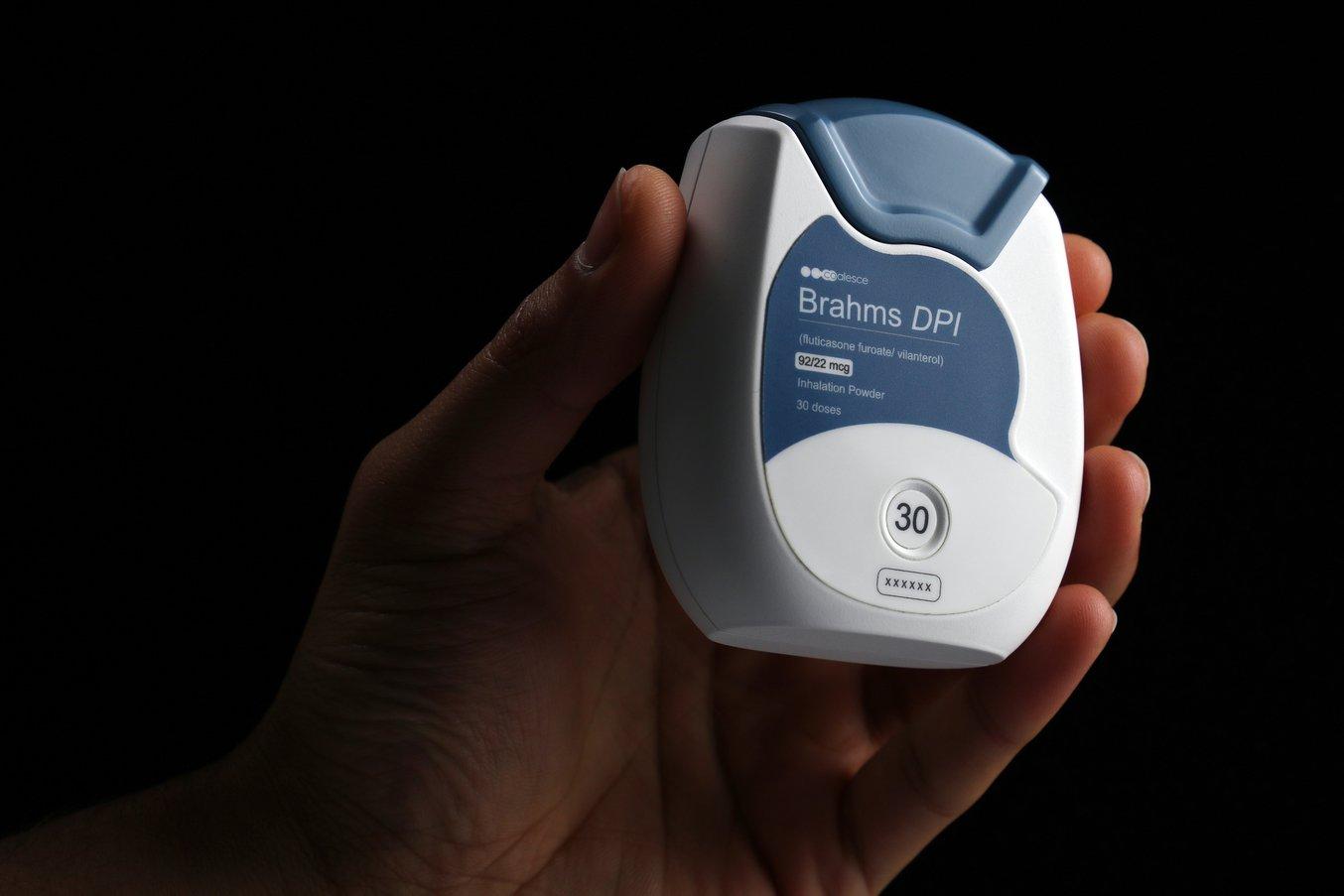
La plateforme de l'inhalateur à poudre sèche (DPI) pré-dosé permet l'utilisation de plusieurs médicaments, séparément ou en combinaison. L'interface utilisateur indique s'il faut ouvrir, inspirer ou fermer, et le compteur de doses offre une excellente lisibilité.
L'adoption de l'impression 3D en interne peut apporter un énorme avantage et des gains de temps importants aux entreprises de développement de dispositifs médicaux. Non seulement elle peut être utilisée pour créer des prototypes visuels, mais elle peut également contribuer à réduire la sous-traitance, à réaliser plus rapidement des itérations de conception, à créer de l'outillage sans recourir au moulage par injection, et plus encore.
Grâce aux imprimantes 3D de Formlabs, Coalesce Product Development a réduit de 80 à 90 % les délais de fabrication pour les boîtiers de ses dispositifs médicaux, et réduit ses coûts de 96 %. Au fil du temps, ils ont continué à investir dans les applications d'impression 3D, ce qui les place en tête du développement des produits d'inhalation. La réduction des coûts et la rapidité du développement ont permis à l'entreprise de mettre au point des dispositifs pour ses clients, mais aussi de développer sa propre technologie dont elle pourra ensuite octroyer la licence à d'autres sociétés pharmaceutiques mondiales, le tout avec des moyens financiers relativement modestes.
Enfin, Vinnay a résumé ce qu'il pense des imprimantes Formlabs en une phrase : « Les imprimantes 3D Formlabs jouent un rôle essentiel chez Coalesce. »
Contactez Formlabs pour découvrir comment l'impression 3D SLA de bureau peut simplifier les flux de travail de prototypage et de test, et commandez un échantillon gratuit pour votre application spécifique.