Vers des voitures imprimées en 3D : 5 façons dont l'impression 3D change la donne dans l'industrie automobile
Bien que l'achat d'une voiture imprimée en 3D auprès de votre concessionnaire ne soit pas encore pour demain, l'impression 3D joue depuis des années un rôle essentiel dans le développement des voitures. Dernièrement, nous commençons même à voir l'impression 3D gagner du terrain dans ce secteur.
L'impression 3D peut apporter une valeur ajoutée considérable aux chaines d'approvisionnement, débloquant ainsi une vaste gamme d'applications. Au fur et à mesure que cette technologie devient plus accessible, tant en termes techniques que financiers, les entreprises peuvent intégrer des procédés de fabrication additive en interne pour épauler les processus en place dans les ateliers de production. De nouveaux matériaux résilients ouvrent des perspectives pour la production d’impressions 3D fonctionnelles de haute précision pouvant remplacer les pièces finales et offrir des possibilités de personnalisation et des performances de pointe, mais ce n’est que le début.
Continuez la lecture pour découvrir cinq façons essentielles dont l'impression 3D dynamise l'innovation dans toute l'industrie automobile, de la conception à la fabrication et bien plus encore.
1. Repenser le processus de prototypage
L'utilisation la plus courante de l'impression 3D dans l'industrie automobile a toujours été le prototypage. Grâce à la grande vitesse de réalisation du prototypage possible avec l'impression 3D, le prototypage rapide est devenu virtuellement synonyme d'impression 3D, et cette technologie a révolutionné le processus de développement des produits.
Avec l'impression 3D, les concepteurs automobiles peuvent rapidement fabriquer un prototype de pièce ou d'assemblage, allant d'un simple élément d'intérieur à un tableau de bord complet, voire même à un modèle réduit d'une voiture entière. Le prototypage rapide permet aux entreprises de démontrer rapidement la faisabilité de leurs idées. Ces concepts peuvent être développés pour obtenir des prototypes présentant très fidèlement le même aspect et le même fonctionnement que les produits finis, et de faire passer une série d'étapes de validation aux produits en vue d'une production de masse. Dans l'industrie automobile, cette validation rapide est essentielle. « Arrêter une ligne de production automobile, même pour juste une heure, peut coûter une fortune » dit Andrew Edman, Responsable conception de produits, ingénierie et conception de produits chez Formlabs.
En utilisant l'impression 3D par stéréolithographie en interne, les concepteurs et ingénieurs de Ringbrothers peuvent réaliser de nombreuses versions de leurs créations rapidement et à moindre frais.
Le prototypage était un processus long et potentiellement coûteux car plusieurs versions d'un produit étaient créées avant de faire un choix définitif. Avec l'impression 3D, des prototypes convaincants peuvent être créés en une journée et à moindres frais.Les imprimantes 3D de bureau permettent aux équipes de conception et d'ingénierie d'intégrer cette technologie en interne pour accélérer le cycle de réalisation des prototypes et de réduire l'attente entre l'idée et le produit final, renforçant ainsi le flux de développement global des produits.
2. Créer des pièces personnalisées, complexes et de haute-performance
L'impression 3D est idéale pour produire des pièces personnalisées à moindre coût, donnant ainsi aux fabricants de nouvelles capacités de production qui leur permettre d'accroitre leur offre.
Pour les petites entreprises dont le sur-mesure est le cœur de métier, comme l'atelier de voitures customisées Ringbrothers, l'impression 3D a permis d'améliorer la qualité et la productivité de leurs travaux, et d'avoir l'espace nécessaire pour expérimenter et parfaire leurs designs, sans devoir s'inquiéter des frais élevés et du long temps de fabrication qui étaient jusqu'alors inévitables pour leurs travaux de personnalisation.
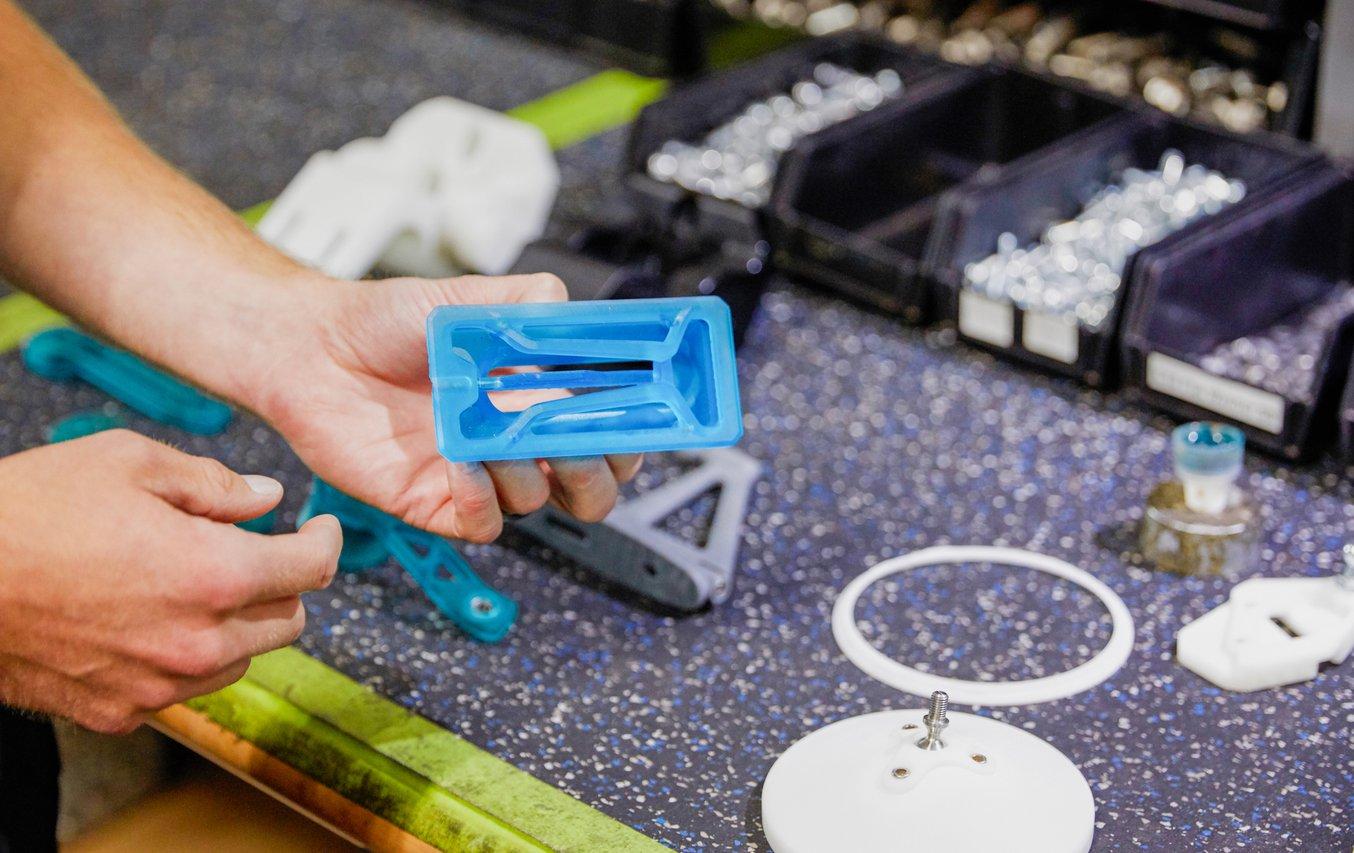
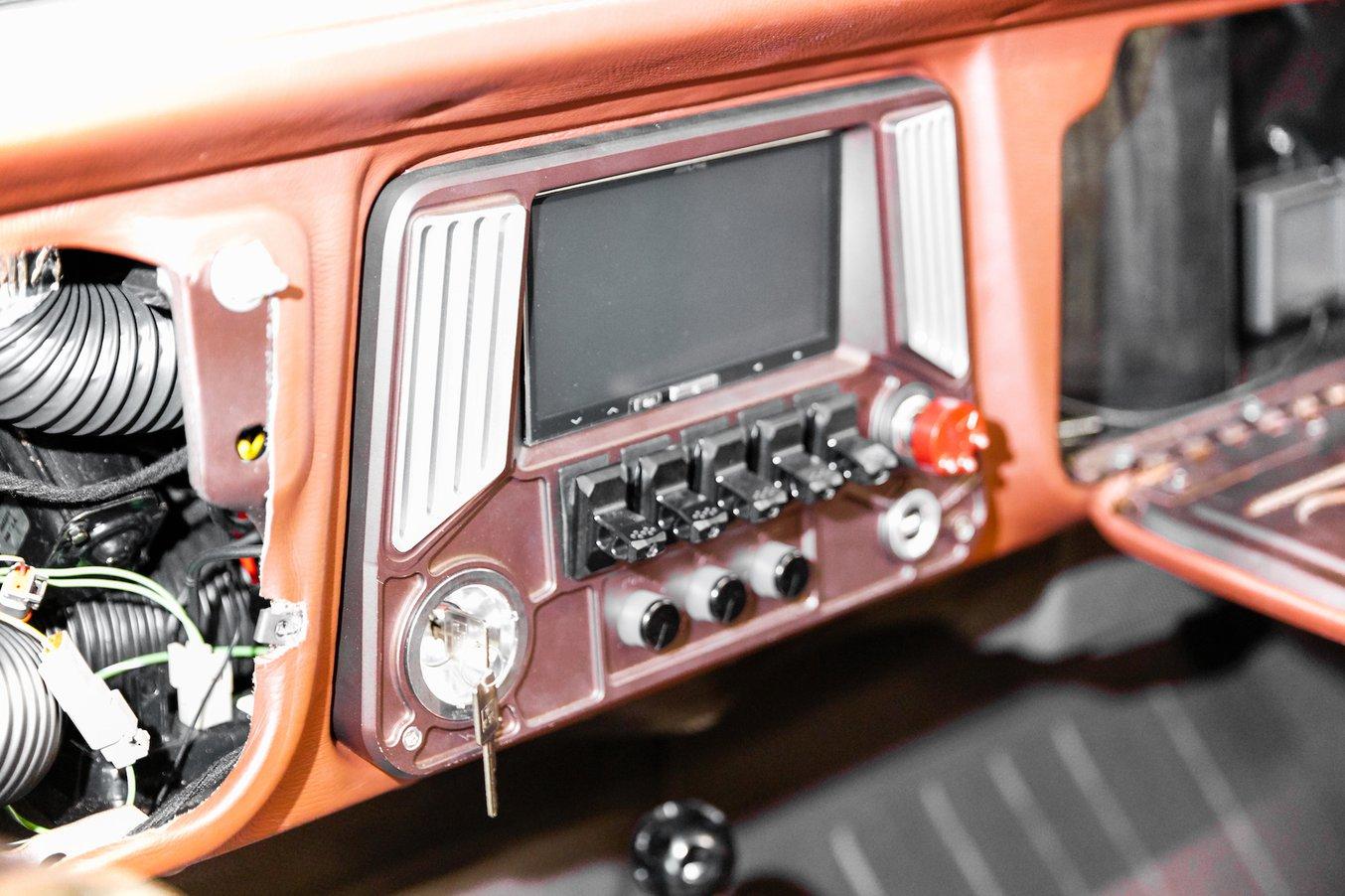
Ringbrothers utilise l'impression 3D pour créer des pièces finales personnalisées, comme cet évent.
De grandes sociétés associent également les techniques d'impression 3D aux moyens traditionnels. Volkswagen a recréé son célèbre Microbus de 1962, en remplaçant son moteur à essence avec un entrainement électrique de 120 hp (89 W) développant une couple de 234,5 Nm. Le concept car Type 20 présente également de nombreuses améliorations rendues possible par l'impression 3D, y compris des roues moulées en aluminium réalisées à partir d'un design génératif. Même les cache-moyeux sont imprimés en 3D, ils ont beau ressembler à de l'acier matricé, ils ont en fait été fabriqués sur une imprimante 3D SLA Formlabs, puis galvanisés pour avoir l'aspect et le toucher d'une pièce métallique.
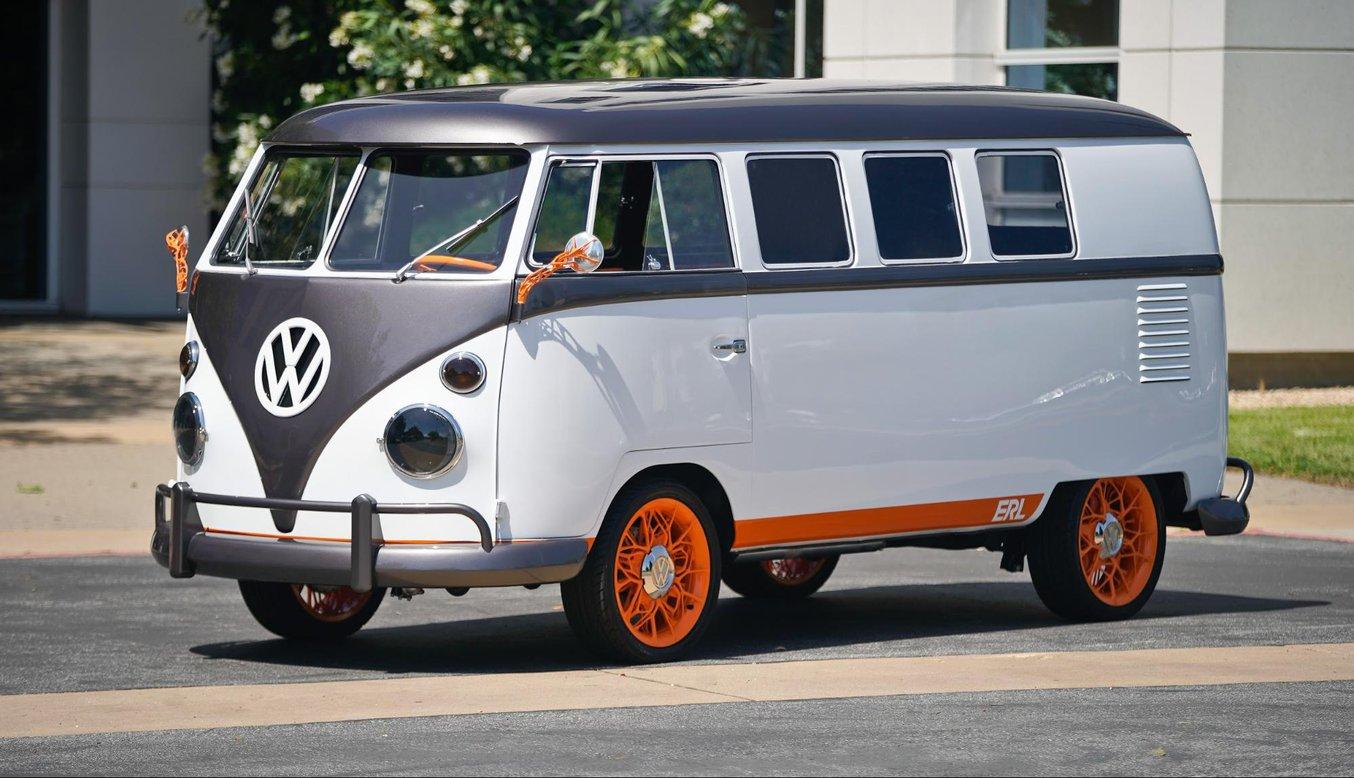
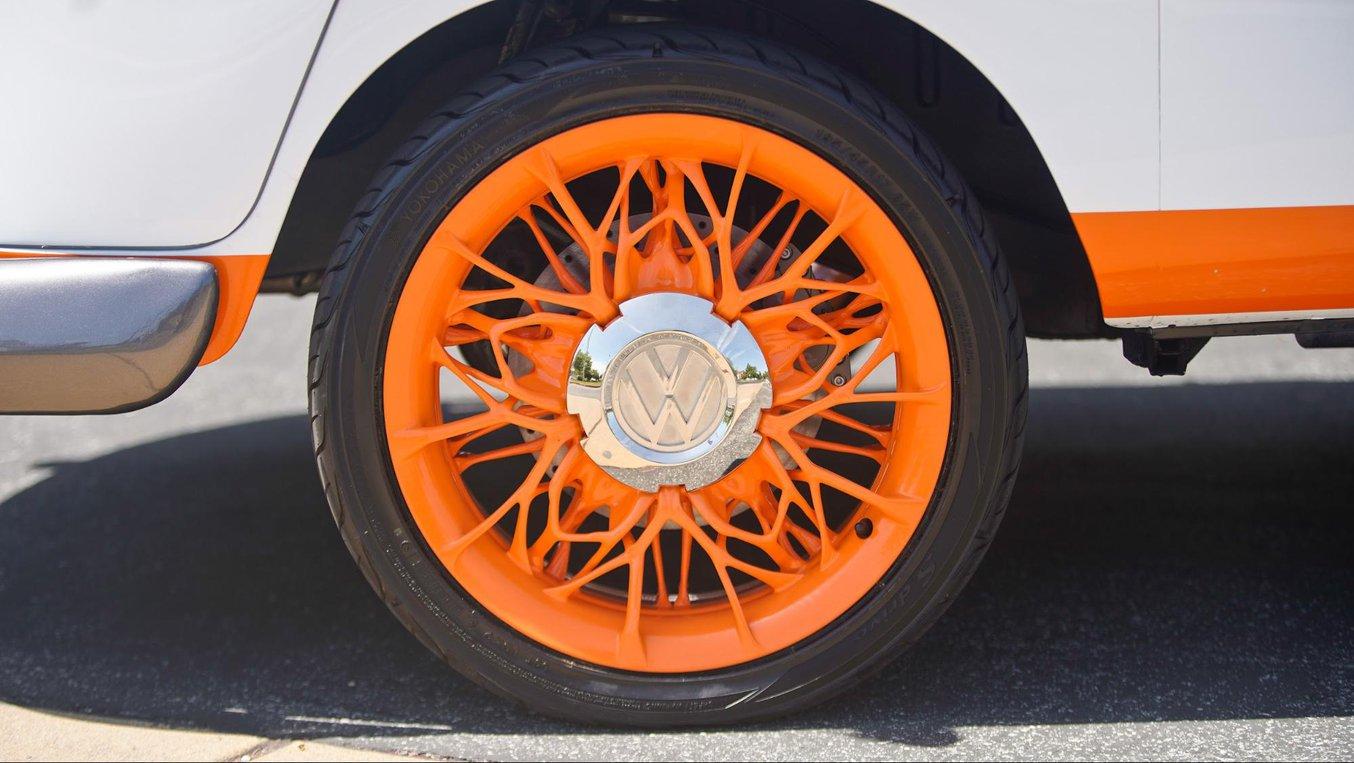
Les cache-moyeux de ce Microbus VW ont été imprimés en 3D sur une imprimante 3D SLA Formlabs puis galvanisés et polis pour prendre l'apparence de l'acier chromé. (images : VW)
La The Bentley Speed 6 en est un autre exemple. Le fabricant de voitures de luxe a utilisé une technique d'impression 3D de pointe pour créer des pièces bien plus détaillées (grilles, évents latéraux, poignées de porte, et échappements) que ce qu'il est possible de faire avec les techniques de production actuelles.
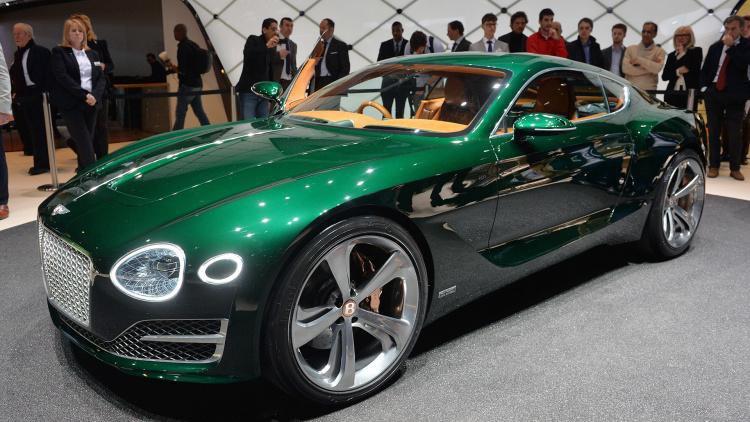
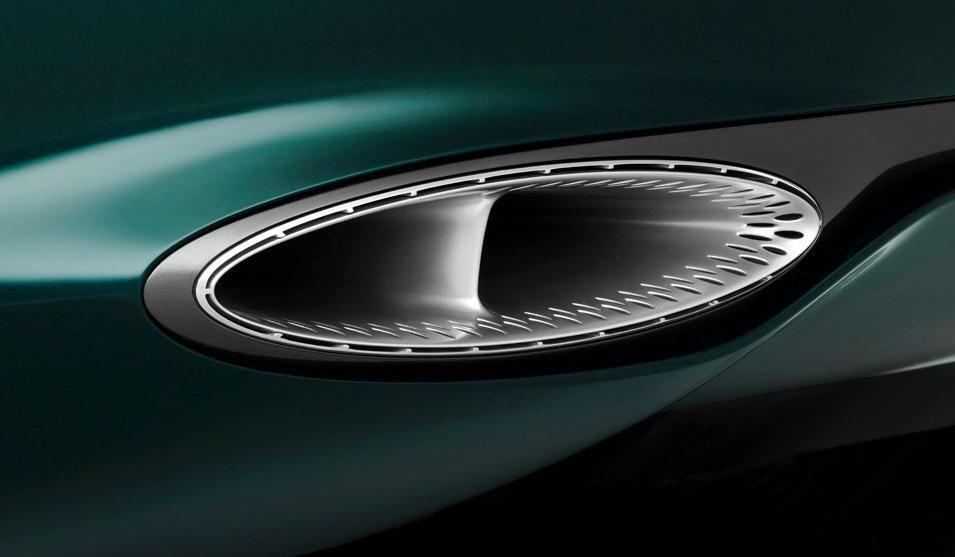
Bentley a utilisé une technique d'impression de métal pour créer ces pièces détaillées avec une précision à l'échelle du micron. (source : Bentley)
Mais l'impression 3D n'est pas réservée aux voitures de luxe, de collection, ou de présentation. Le logiciel de personnalisation Twikit a permis au fabricant de voitures britannique MINI d'offrir des services de personnalisation à tous ses clients grâce à l'impression 3D, laissant aux propriétaires des voitures le libre contrôle du design. Les clients peuvent personnaliser des composants internes ou externes de leurs véhicules dans un vaste choix de caractères, de modèles et d'images, et pré-visualiser le résultat en 3D. Un tel projet est seulement viable car les réductions des coûts permises par l'impression 3D ont mis ce type de personnalisations à la portée du grand public.
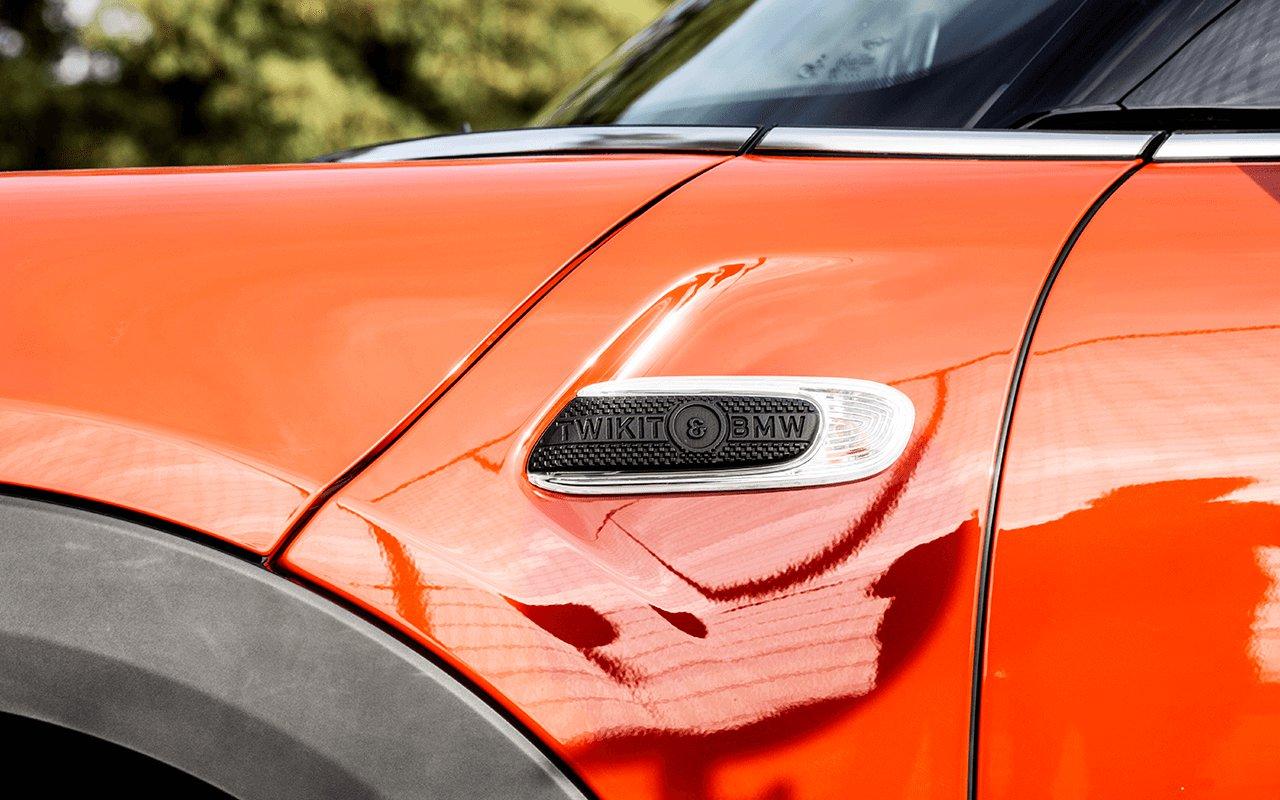
La collaboration de MINI avec Twikit donne aux propriétaires de Minis le plein contrôle sur la personnalisation des composants internes et externes de leur véhicule. (Source : Twikit)
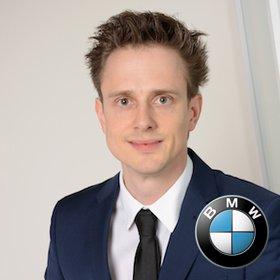
L'impression 3D en production chez BMW
Christian Gröschel, chef de projet chez BMW, décrit le processus de la société pour développer et mettre en œuvre son programme additif.
Regarder la VidéoL'impression 3D a également permis de créer des pièces qui n'auraient tout simplement pas pu être créées par d'autres moyens. L'étrier de frein monobloc à huit pistons de Bugatti en est un exemple parfait. Pour certains de ses composants, Bugatti préfère le titane en raison de ses excellentes performances, mais traiter ce métal avec les techniques conventionnelles est cher et difficile L’utilisation de l’impression 3D a non seulement permis à Bugatti de produire l'étrier à l’échelle requise, mais elle a également accru le potentiel de performance de la voiture en réduisant considérablement le poids du composant tout en le rendant considérablement plus rigide et plus résistant que l’alternative classique (aluminium).
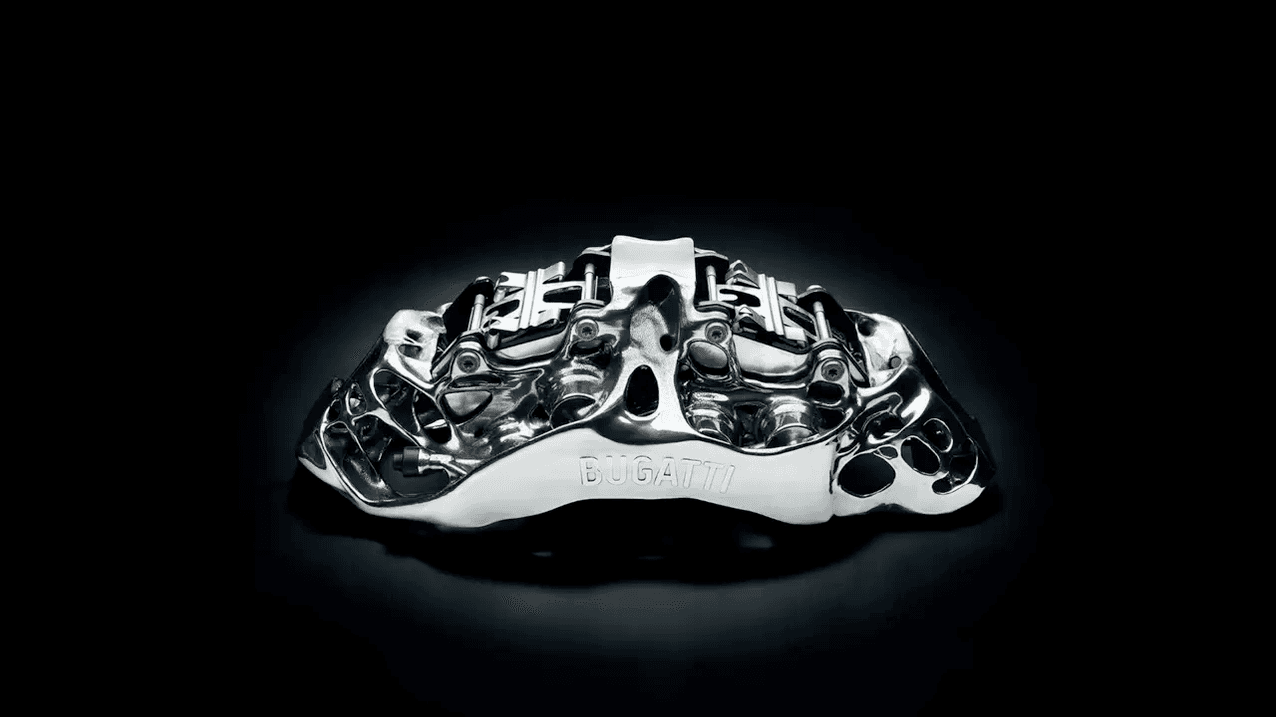
L'étrier de frein monobloc à huit pistons de Bugatti est le composant fonctionnel en titane le plus grand au monde produit en impression 3D. (source : Bugatti)
3. Fabrication d'outillage et d'aides à la production industrielle
Les ingénieurs utilisent des aides à la production industrielle pour simplifier et améliorer la fiabilité des processus de fabrication et d'assemblage, réduisant les durées de cycle et améliorant la sécurité des travailleurs. Les usines automobiles et leurs fournisseurs utilisent des milliers de gabarits et d'éléments conçus et optimisés pour leur utilisation finale. Le résultat en est une multitudes d'outils sur mesure ajoutant des coûts et de la complexité au procédé de fabrication.
Sous-traiter la production de ces pièces personnalisées auprès de prestataires de services d’usinage qui les produisent à partir d’un bloc solide en plastique ou en métal peut retarder la production de plusieurs semaines, et ces longs délais de réalisation font qu'il est également difficile de s'adapter aux changements survenus dans les ateliers.
La fabrication additive peut réduire les délais de réalisation à quelques heures et réduire considérablement les coûts par rapport à la sous-traitance de la fabrication des pièces auprès d'un fournisseur externe. Comme la complexité ne cause pas de frais supplémentaires, les pièces peuvent aussi être mieux optimisées pour leur utilisation finale. De nouveaux matériaux d'impression 3D ont également permis aux fabricants de remplacer les composants en métal par des pièces plastiques imprimées en 3D dans de nombreux cas, ou de prototyper et tester les outils avant de s'engager.
Il en résulte que la production d'aides à la fabrication en impression 3D devient l'une des applications les plus importantes de l'industrie.
Pankl Racing Systems utilise des fixations imprimées en 3D pour maintenir les pièces au tapis du convoyeur quand elles passent par plusieurs étapes d'usinage.
Par exemple, Pankl Racing Systems s'appuie sur une station d'impression 3D comprenant plusieurs imprimantes 3D SLA Formlabs pour fabriquer les outils dont ils ont besoin en production. Pour la fabrication de pièces destinées à des ensembles de boîtes de vitesses, chaque pièce produite par la société nécessite une série de gabarits, de fixations et autres outils personnalisés conçus spécifiquement pour cette pièce lorsqu’elles passent par plusieurs étapes d’usinage automatique. En utilisant l'impression 3D, les ingénieurs de Pankl ont réduit les délais de réalisation des gabarits de 90 %, les faisant passer de deux à trois semaines à moins d'une journée, ainsi que les coûts de 80-90 %, permettant une économie de 125 000 €.
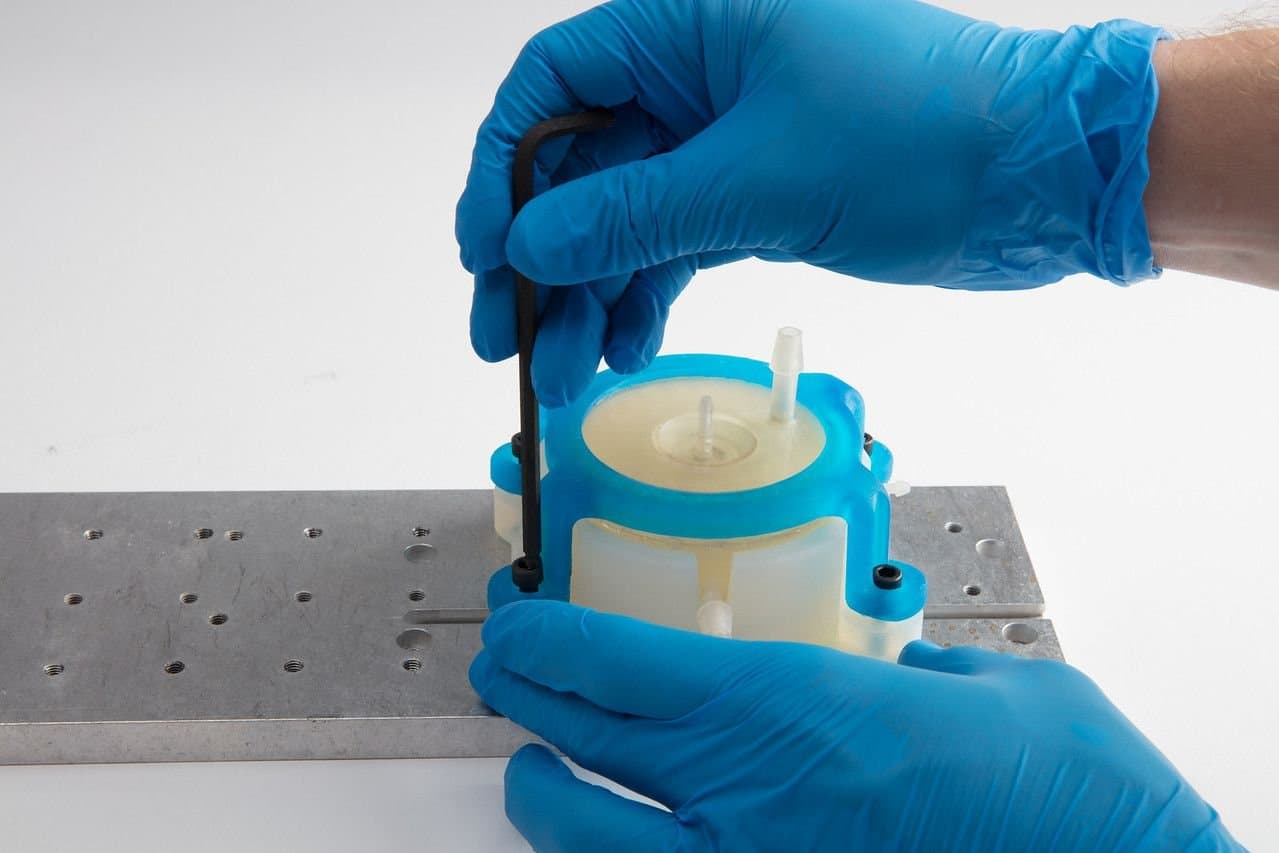
Conception de gabarits et de fixations par impression 3D
Téléchargez notre livre blanc pour apprendre comment réduire les coûts et les cycles de développement et créer des processus de travail optimisés avec les gabarits et fixations imprimés en 3D.
Télécharger le Livre blanc4. Résoudre le problème des pièces de rechange
Les pièces de rechange ont toujours représenté un défi dans l'industrie automobile. Par nature, la demande en composants de rechange est sporadique et imprévisible, leur production fait donc l'objet d'une décision financière discutable dans certains cas. Cependant, la valeur des produits est plus précaire et les réparations sont plus difficiles en l'absence de pièces de rechange disponibles. La production de pièces de rechange pour anticiper des besoins futurs demande également un investissement important en espace de stockage.
L'impression 3D est bien placée pour avoir un impact positif important sur le problème posé par les pièces de rechange dans le secteur. « Je pense que les facteurs les plus importants [dans la résolution du problème des pièces de rechange via l'impression 3D] sont l'obtention de matériaux pouvant correspondre aux performances des matériaux plus traditionnels utilisés pour les pièces de première main et à la rentabilité. Nous nous rapprochons de cela », a déclaré Edman. « Ce n’est pas tant une question de si l'impression 3D prendra en charge la production de pièces de rechange mais plutôt de quand elle le fera. »
Avec l'utilisation de CAO, les modèles de chaque pièce peuvent être conservés sous format numérique, il n'y a donc plus besoin de conserver un stock physique. Avec la prolifération des imprimantes 3D d'atelier, une pièce de rechange pourrait éventuellement être produite en magasin à la demande du client. L’accessibilité de la technologie encouragera les fournisseurs à ouvrir de nouveaux espaces dans lesquels ils pourront fournir facilement des pièces de rechange imprimées en 3D.
Même les pièces qui n'existent plus peuvent potentiellement être reconfigurées, à l'aide de la rétro-ingénierie, sur la base d'analyses numériques des pièces existantes. Des modèles anciens peuvent donc retrouver une nouvelle vie. « Les gens ont des voitures de collection qui ont plus de 50 ans. Un jour nous serons peut-être capables de fournir des pièces pour ces véhicules de manière automatique grâce à l'impression 3D. » a déclaré Edman.
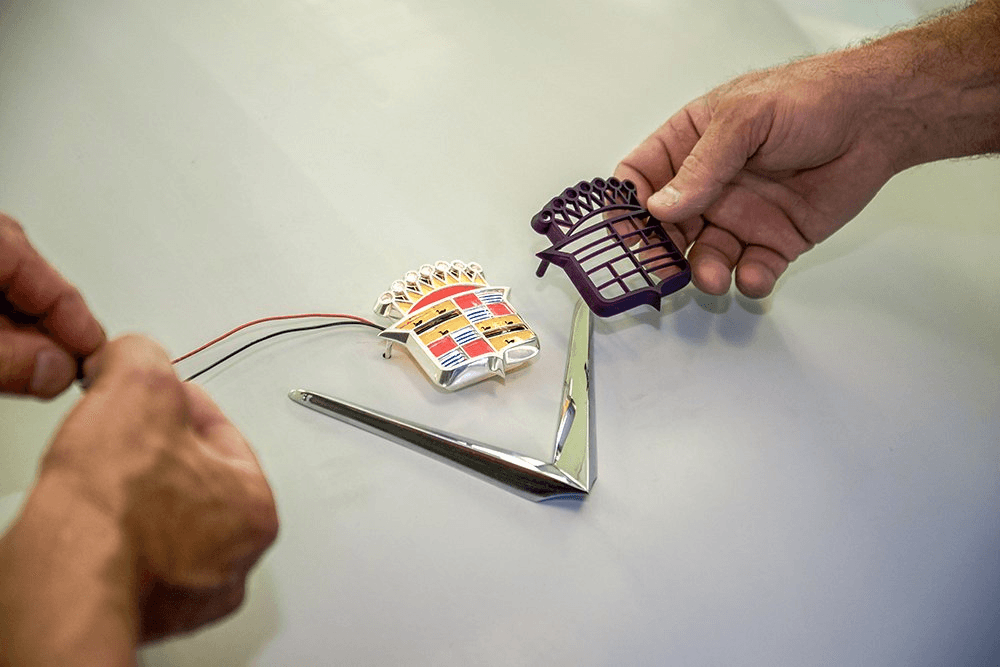
Ringbrother a reproduit l'emblème d'une Cadillac pour une voiture de collection customisée en imprimant la forme en 3D et en y moulant l'emblème en métal.
5. Faciliter la fabrication des pièces générales
Alors que l'impression 3D devient plus abordable en ce qui concerne le coût de l'équipement et des matériaux, nous assisterons à une transition progressive vers la production de pièces automobiles de série.
Les imprimantes 3D peuvent améliorer l'efficacité au stade de la fabrication des pièces générales. Comme le remarque Edman, « là où vous verrez [les techniques d'impression 3D devenir plus populaires plus tôt] seront les secteurs où il est possible d’utiliser les avantages de l’additif pour combiner des composants ensemble. Vous pourriez avoir un assemblage de 6 ou 7 pièces automobiles qui peuvent maintenant être combinées en une seule pièce imprimée. Vous économisez du temps et des coûts d’assemblage, même si chaque pièce est plus chère. » En consolidant les pièces, les méthodes d'impression 3D peuvent également aider à réduire le poids et donc à améliorer le rendement énergétique.
La diversité des matériaux disponibles pour l’impression 3D commence à répondre aux exigences mécaniques des différents composants d’un véhicule. À mesure que les méthodes additives arrivent au même prix que les méthodes traditionnelles (moulage, moulage sous pression, etc.), il sera plus logique d'un point de vue productif et financier d'intégrer davantage l'impression 3D dans la fabrication générale de pièces.
+1. Voitures imprimées en 3D
Bien qu'une voiture entièrement imprimée en 3D et prête à la commercialisation soit encore futuriste, il existe quelques projets passionnants qui indiquent la direction dans laquelle le secteur pointe :
EDAG’s Light Cocoon : Ce concept réalisé par le développeur automobile indépendant EDAG bénéficie d’une structure porteuse imprimée en 3D, inspirée de la nature et ressemblant à une branche. En dépit du fait que la structure utilise moins de matériaux qu'un châssis standard, toutes les exigences imposées aux composants structurellement pertinents sont respectées. Pour rendre le châssis résistant aux éléments, la structure est recouverte de tissu.
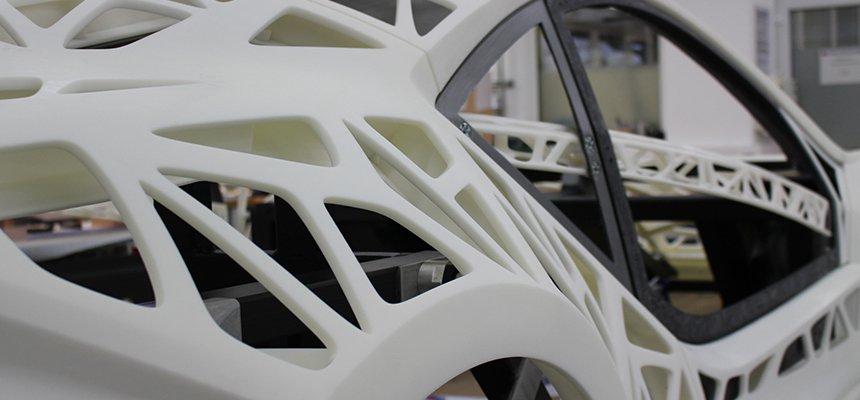
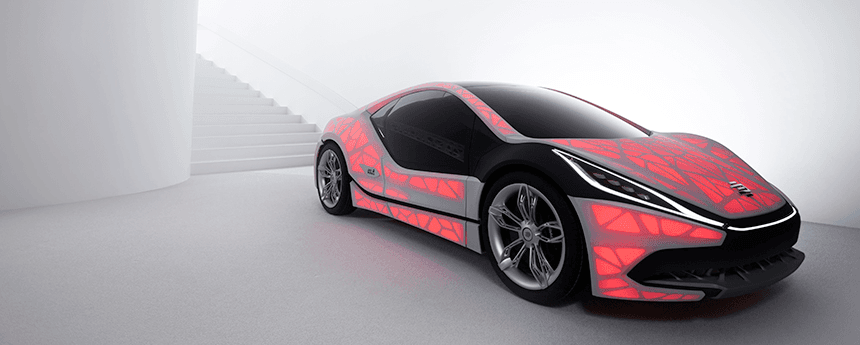
Outre la résistance aux intempéries, la couverture du Light Cocoon d’EDAG offre une liberté absolue en matière de conception et d’individualisation. (source : EDAG)
The Blade : La « première supervoiture imprimée en 3D au monde » est conçue pour être fabriquée à partir de matériaux peu chers (pour des supervoitures), tels que des tubes en fibre de carbone et des tiges en aluminium, qui sont assemblés à des pièces métalliques imprimées en 3D conçues de manière générative pour obtenir un véhicule léger aux performances élevées.
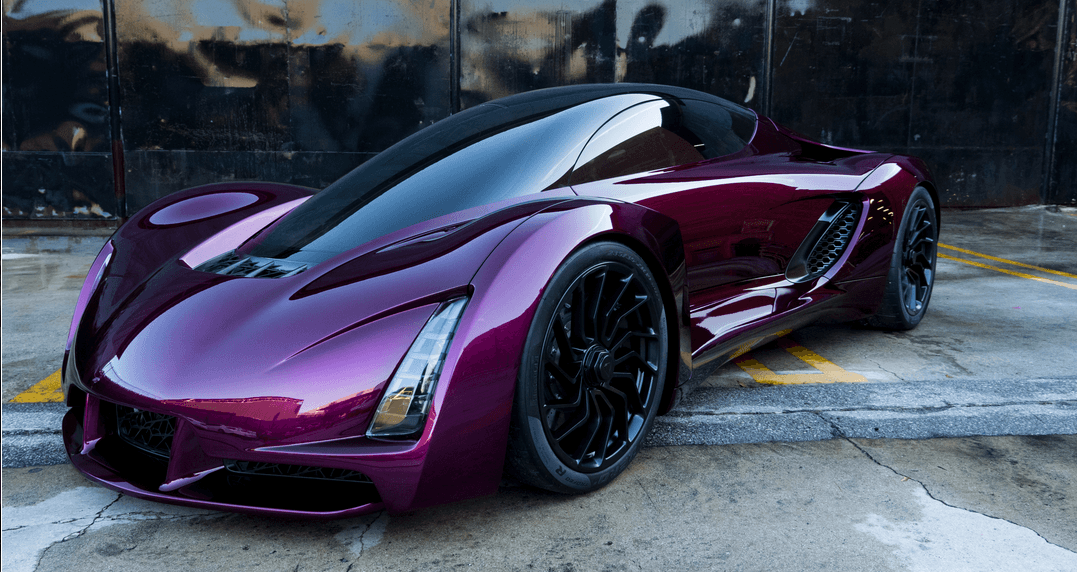
La Blade est la « première supervoiture imprimée en 3D » (source : Divergent3D)
Strati : La première voiture électrique au monde à utiliser largement l'impression 3D au cours du processus de production est fabriquée par Local Motors. La voiture est composée de 50 pièces différentes, bien moins que les quelque 30 000 pièces d’un véhicule traditionnel. Son châssis et la plupart des éléments structurels ont été imprimés en 3D en moins de 24 heures, et la société vise à réduire le temps d'impression à moins de 10 heures.
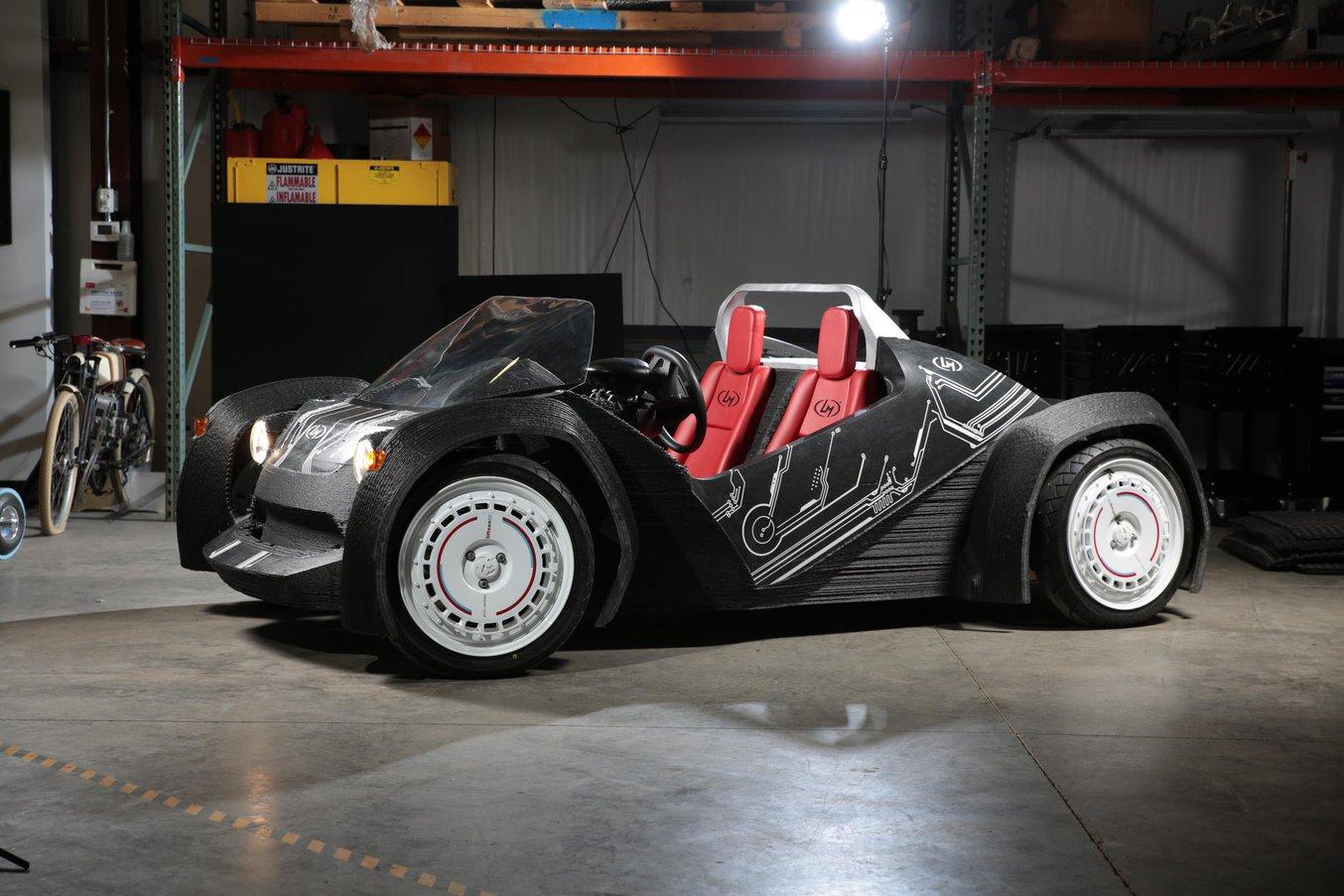
Strati consiste de 50 pièces individuelles et il a fallu moins de 24 heures pour l'imprimer en 3D.
LSEV : Développée par la société italienne XEV, la LSEV pourrait être la première voiture électrique imprimée en 3D « grand public » lorsqu'elle arrivera sur le marché plus tard cette année. Hormis le châssis, les sièges et le pare-brise, toutes les pièces visibles de la LSEV sont imprimées en 3D. Grâce à l'utilisation intensive de l'impression 3D, l'entreprise est parvenue à réduire le nombre de composants de 2 000 à seulement 57, ce qui a permis d'obtenir un design léger ne pesant que 450 kilos.
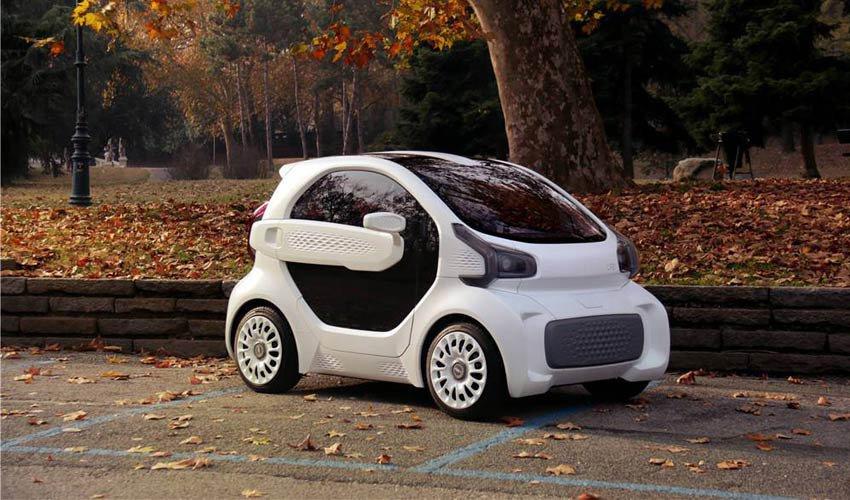
La LSEV est la première voiture électrique imprimée en 3D « grand public », elle arrivera sur le marché plus tard cette année.
Bien que ces projets, et de nombreuses autres initiatives de voitures imprimées en 3D, en soient encore au stade de la conception, le développement de l'intégration de l'impression 3D dans divers domaines de l'industrie automobile est frappant. Dans certains cas, la technique d'impression 3D repousse les limites et aide à ouvrir de nouvelles possibilités en conception et production. Dans d'autres, l'impression 3D permet de réduire les coûts et de gagner du temps.
Alors que la compréhension de la valeur de l'impression 3D continue de se répandre dans l'industrie et que la technologie et les matériaux disponibles deviennent de plus en plus polyvalents, cette tendance croissante se poursuivra.
En savoir plus sur les applications de l'impression 3D en production industrielle