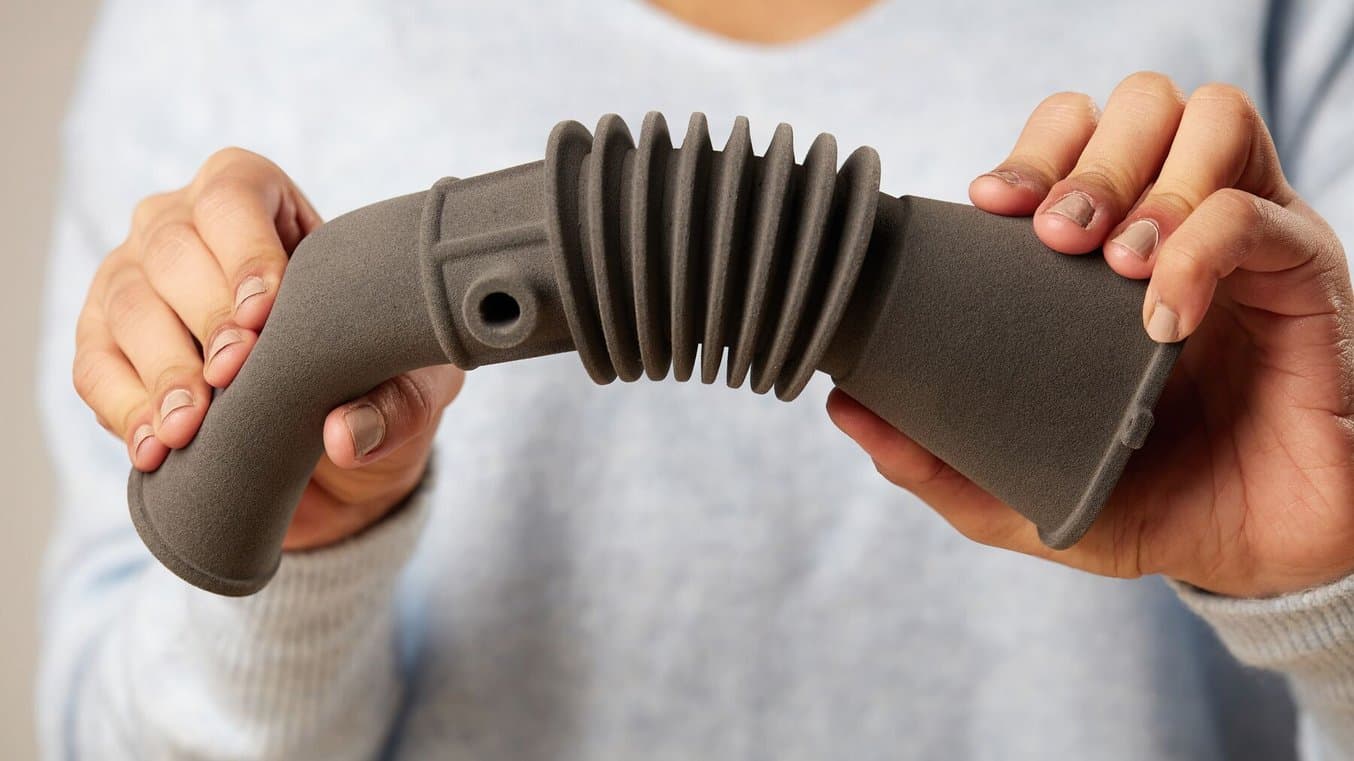
Qu'est-ce que le TPU ?
Le TPU, ou polyuréthane thermoplastique, est un type d'élastomère thermoplastique (TPE) couramment utilisé par les fabricants dans les secteurs de l'automobile, du transport, de l'aérospatiale, des articles de sport et des appareils médicaux. Le TPU combine la grande durabilité des pièces en plastique avec l'élasticité des pièces en caoutchouc, ce qui le rend idéal pour les applications où il doit être plié ou comprimé de façon répétée.
En raison de son élasticité, le TPU est souvent utilisé comme modificateur d'impact pour des produits tels que les casques, les emballages de protection, les produits anti-vibration et les joints d'étanchéité. Le TPU présente également une excellente résistance à l'abrasion et est utilisé dans les environnements à forte friction, tels que les intérieurs de voitures, les câbles électriques et les isolateurs. Le TPU résiste également aux taches d'huile, ce qui le rend parfait pour les applications où l'huile est souvent présente.
Comment les pièces en TPU sont-elles fabriquées ?
Les produits en TPU sont omniprésents dans notre vie quotidienne : il peut donc être très intéressant de les produire en masse, le plus souvent grâce au moulage par injection. De nombreux produits que nous considérons comme du caoutchouc sont en fait du TPU.
Le moulage par injection est un moyen rentable de produire des pièces en grande quantité, mais il présente des limites en termes de flexibilité géométrique ou de personnalisation. Les pièces moulées par injection sont standardisées pour être produites en centaines de milliers ou en millions d'exemplaires. Dans des secteurs comme la fabrication de dispositifs médicaux ou d'articles de sport, il existe une forte demande pour des solutions alternatives qui se prêtent mieux à la production de petites séries ou à la personnalisation.
La production de masse empêche également les petites entreprises et les startups de commercialiser rapidement leurs produits, car elles dépendent des grands sous-traitants de moulage par injection.
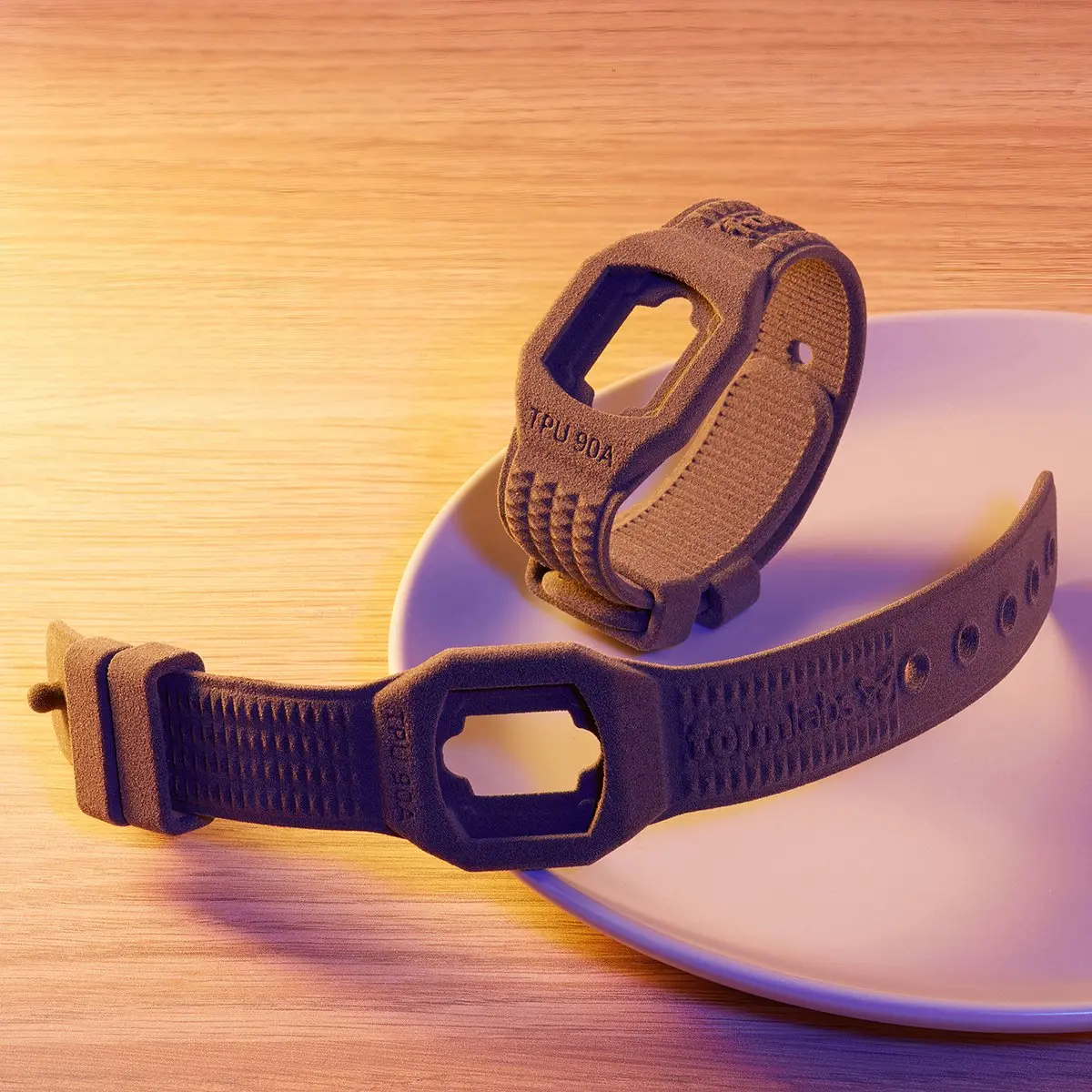
Présentation de TPU 90A Powder pour des pièces SLS flexibles, résistantes et sûres pour la peau
Regardez notre webinaire pour découvrir comment TPU 90A Powder peut vous aider à produire en interne des pièces en caoutchouc à surface douce avec les imprimantes 3D de la série Fuse.
Pourquoi imprimer en 3D des pièces en TPU ?
L'impression 3D avec des matériaux TPU et TPE offre des possibilités que ne permettent pas les flux de travail traditionnels pour obtenir des pièces d'une plus grande complexité géométrique, des conceptions personnalisées ou sur mesure, une itération et une conception plus rapides, et une production en petites séries plus rentable.
Il existe plusieurs options pour l'impression 3D de TPU, notamment les technologies de dépôt de fil fondu (FDM) et de frittage sélectif par laser (SLS). Avec les progrès de la technologie et des matériaux d'impression 3D, le nombre de fabricants qui intègrent ce flux de travail dans leur processus a augmenté de manière exponentielle.
L'impression 3D de TPU permet un cycle itératif plus court pour les applications de prototypage rapide, et ouvre des possibilités de personnalisation pour la production de pièces à usage final. Dans les secteurs où une partie du processus de développement des produits est externalisée (en général la phase de fabrication de la production de masse), l'impression 3D peut permettre un flux de travail de bout en bout amélioré et intégré verticalement.
L'impression 3D de TPU peut également aider les fabricants à répondre à la demande de produits personnalisés. Selon une étude de Deloitte, dans certaines catégories, plus de 50 % des consommateurs ont exprimé leur intérêt pour l'achat de produits ou de services personnalisés, la majorité d'entre eux étant prêts à payer davantage pour un produit ou un service personnalisé. Pour les applications dans lesquelles le TPU et le caoutchouc sont couramment utilisés, comme par exemple les casques, les orthèses et les semelles intérieures, les pièces en TPU imprimées en 3D sont parfaites pour les rembourrages de casques personnalisés en masse, les orthèses, les équipements sportifs, les lunettes, les écouteurs, ou encore les composants de préhension ergonomiques pour les produits technologiques.
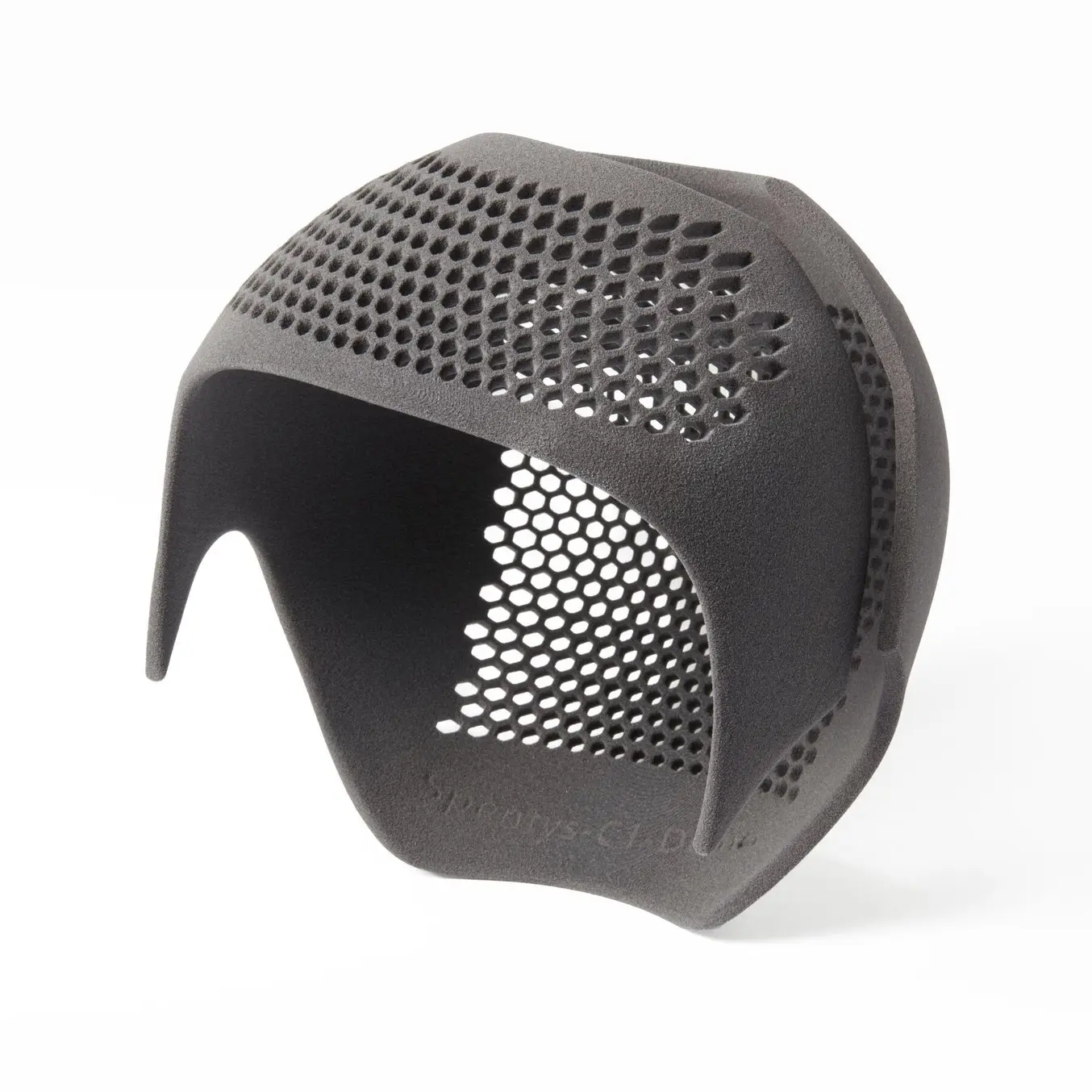
TPU 90A Powder de Formlabs permet de créer des produits sur mesure pour des applications telles que ce couvre-chef protecteur personnalisé.
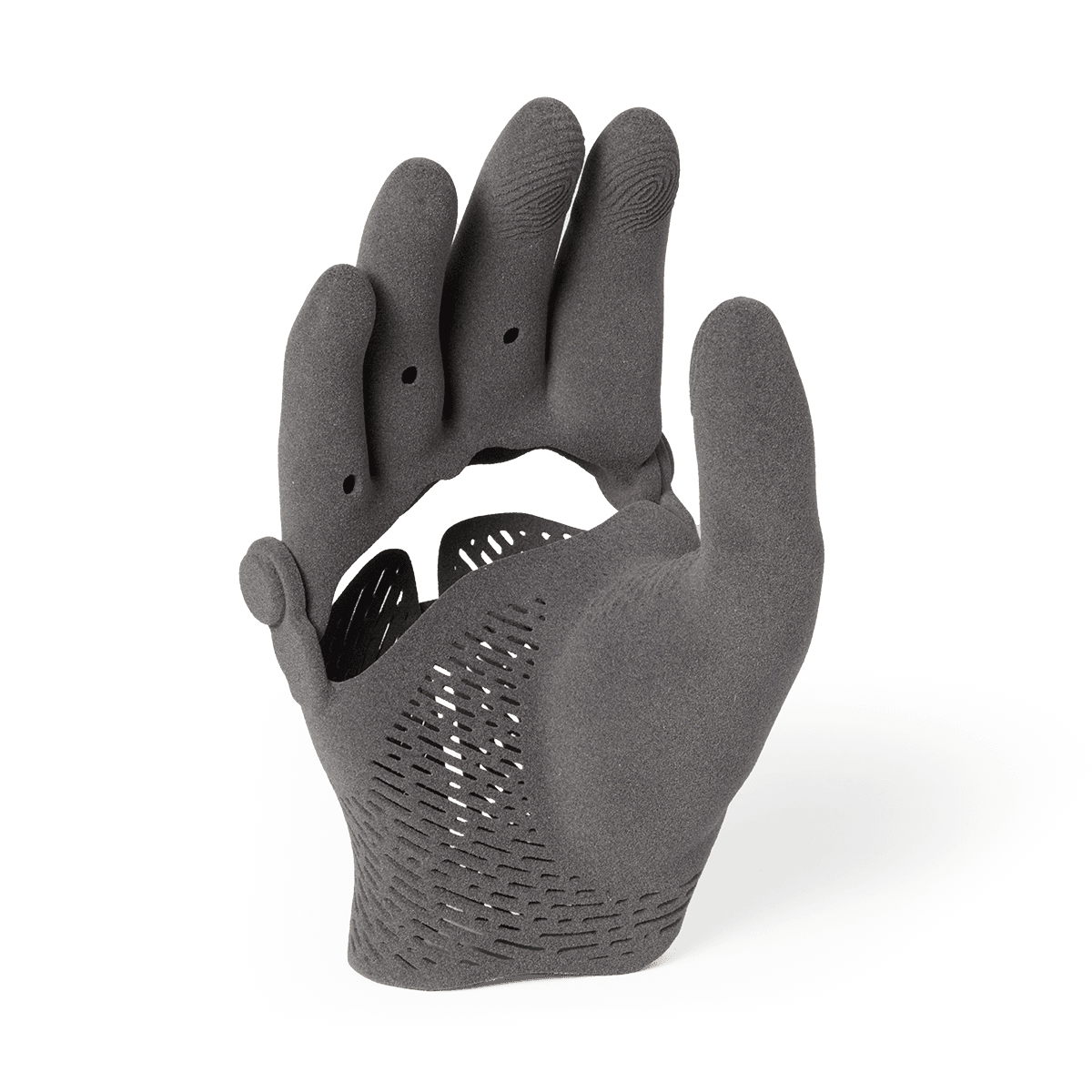
Cette prothèse de main imprimée en TPU 90A Powder est flexible, solide et durable.
Comment imprimer en 3D avec du TPU
Le TPU peut être imprimé en 3D avec des imprimantes 3D FDM ou SLS. Chaque technologie présente des avantages uniques, et avant de choisir une technologie, il est important de déterminer ce qui convient le mieux à votre propre flux de travail et aux besoins de votre entreprise.
Impression 3D FDM de TPU | Impression 3D SLS de TPU | |
---|---|---|
Résistance des matériaux fonctionnels | ★★☆☆☆ | ★★★★★ |
Résolution | ★★☆☆☆ | ★★★★☆ |
Précision | ★★★★☆ | ★★★★★ |
Finition de surface | ★★☆☆☆ | ★★★★☆ |
Volume de production | ★★☆☆☆ | ★★★★★ |
Conceptions complexes | ★★☆☆☆ | ★★★★★ |
Facilité d’utilisation | ★★★★★ | ★★★★☆ |
Avantages | Faibles coûts des matériaux et appareils Rapide et facile pour les petites pièces simples | Pièces fonctionnelles, solides et isotropes Rendement important Conceptions autoportantes Excellente liberté de conception |
Inconvénients | Les pièces sont anisotropes et ne sont ni étanches ni fonctionnellement solides. Liberté de conception limitée | Finition de surface légèrement irrégulière |
Applications | Prototypage rapide et peu coûteux Modèles simples de preuve de concept | Prototypage fonctionnel Production en petite série de pièces d'utilisation finale : joints automobiles, joints d'étanchéité, collecteurs, biens de consommation, chaussures, prothèses et orthèses. |
Impression 3D de TPU avec l'impression 3D FDM
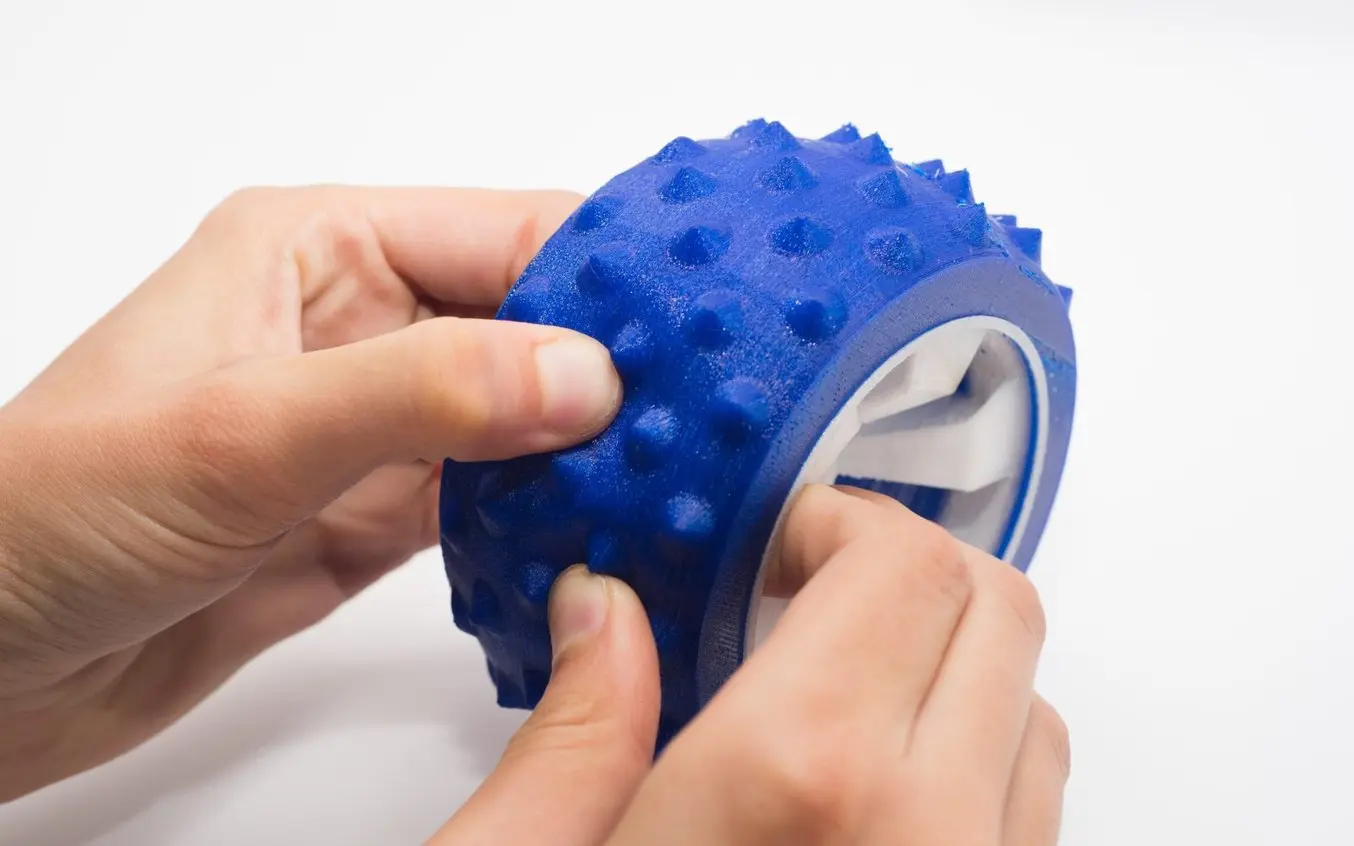
L'impression 3D de TPU sur des imprimantes FDM est une bonne option d'entrée de gamme, mais ce matériau est difficile à imprimer en 3D et présente des limites en termes de conception. (Image source: Hubs)
Pour les entreprises qui souhaitent se lancer dans l'impression 3D de TPU, une imprimante FDM bon marché est une bonne option pour un flux de travail d'entrée de gamme. Le filament de TPU pour le FDM est peu coûteux et peut être un bon moyen de tester des concepts de design et des prototypes visuels, surtout si l'objectif final est la production en série avec le moulage par injection.
Cependant, le TPU peut être un matériau difficile à imprimer en 3D sur des imprimantes FDM, car le filament souple peut facilement obstruer la buse, ce qui entraîne des problèmes techniques et un taux de réussite d'impression plus faible. L'impression 3D de TPU avec des imprimantes FDM offre également une liberté de conception limitée, des pièces moins précises sur le plan dimensionnel et des lignes de couche visibles.
Les pièces en TPU imprimées par FDM sont anisotropes, ce qui signifie que leur résistance n'est pas la même selon les différents axes ou plans de contrainte. En d'autres termes, l'application d'une force à une pièce en TPU imprimée par FDM sera différente en fonction de sa direction. Cette anisotropie constitue un véritable problème pour les pièces en TPU qui doivent souvent être étirées, comprimées et tordues même dans la phase de prototypage.
Filaments TPU pour imprimantes FDM
De nombreux fabricants d'imprimantes et de matériaux FDM proposent des filaments TPU présentant des propriétés diverses. Les filaments de TPU pour le FDM sont généralement des matériaux élastiques un peu plus durs offrant une dureté Shore de 95A, mais on peut y remédier en modifiant les paramètres d'impression ou la conception.
Impression 3D de TPU avec l'impression 3D SLS
La technologie d'impression 3D SLS est idéale pour les applications plus fonctionnelles et à plus haut rendement telles que les prototypes fonctionnels pour les tests ou la production en petites séries de produits finaux personnalisables tels que les orthèses, les rembourrages de casques et les produits portables. Les utilisateurs de l'impression 3D SLS peuvent tirer parti de la résistance et de la flexibilité exceptionnelles du TPU pour commercialiser plus rapidement leurs produits ou transformer les soins aux patients. Sa grande résistance au déchirement permet d'obtenir des pièces en élastomère solides et durables, et l'accessibilité des systèmes SLS d'atelier, comme les imprimantes de la série Fuse, permet de réduire le coût par pièce. En outre, le faible taux de renouvellement rend le système plus abordable et plus évolutif, car il permet une utilisation des poudres plus efficace et réduit les dépenses liées à l'achat de nouveaux matériaux.
Les pièces en TPU imprimées en 3D par SLS sont parfaites pour les applications où des formes complexes sont nécessaires ou utiles à la performance. Les pièces SLS ne nécessitent aucune structure de support, ce qui permet des géométries complexes avec des canaux internes, des treillis ou des structures en accordéon de type collecteur. Dans des applications telles que les casques de protection ou les semelles et orthèses de chaussures, les structures en treillis caoutchouteux offrent une résistance élevée à la compression qui renforce l'efficacité du produit.
Matériaux en TPU pour imprimantes SLS
Il existe plusieurs systèmes de frittage sélectif par laser (SLS) qui proposent une poudre de TPU. Beaucoup de ces systèmes sont de grandes machines industrielles avec des exigences complexes en matière d'infrastructure, telles que des systèmes de ventilation dédiés, une grande surface au sol ou des circuits électriques spéciaux. Depuis l'introduction de systèmes SLS abordables comme la série Fuse de Formlabs, l'impression 3D de TPU sur des systèmes à lit de poudre est à présent plus accessible.
TPU 90A Powder de Formlabs est sans danger pour la peau, ce qui ouvre de nouveaux horizons dans les domaines des appareils de technologie portable et des appareils médicaux, où les réglementations en matière de sécurité limitent l'utilisation de nombreuses pièces imprimées en 3D. Avec TPU 90A Powder, les ingénieurs et les concepteurs peuvent tout à la fois tirer parti de la liberté de conception de l'impression 3D, de la résistance élevée au déchirement et à l'allongement du caoutchouc, et du fait que les thermoplastiques moulés sont sûrs pour la peau.
Grâce aux imprimantes SLS de la série Fuse, TPU 90A Powder de Formlabs est simple à utiliser et peut facilement s'intégrer dans un flux de travail SLS existant, ou être le premier matériau SLS avec lequel vous vous lancez. Le matériau s'imprime à l'air ambiant et ne nécessite pas d'atmosphère inerte, ce qui est le cas pour d'autres matériaux SLS.
En outre, les pièces en TPU n'utilisent pas Surface Armor (la coque semi-frittée qui entoure les pièces imprimées avec des poudres plus rigides) sur les imprimantes de la série Fuse, ce qui simplifie le processus de dépoudrage avec la Fuse Sift. Bien que TPU 90A Powder n'ait pas besoin de Surface Armor, il est recommandé de sabler les pièces afin d'éliminer l'excès de poudre et d'obtenir un matériau plus propre et plus facile à travailler. Il est tout à fait possible d'utiliser TPU 90A Powder avec votre imprimante de la série Fuse actuelle, mais Formlabs vous recommande d'employer une chambre de fabrication, un tamis et une imprimante Fuse dédiés.
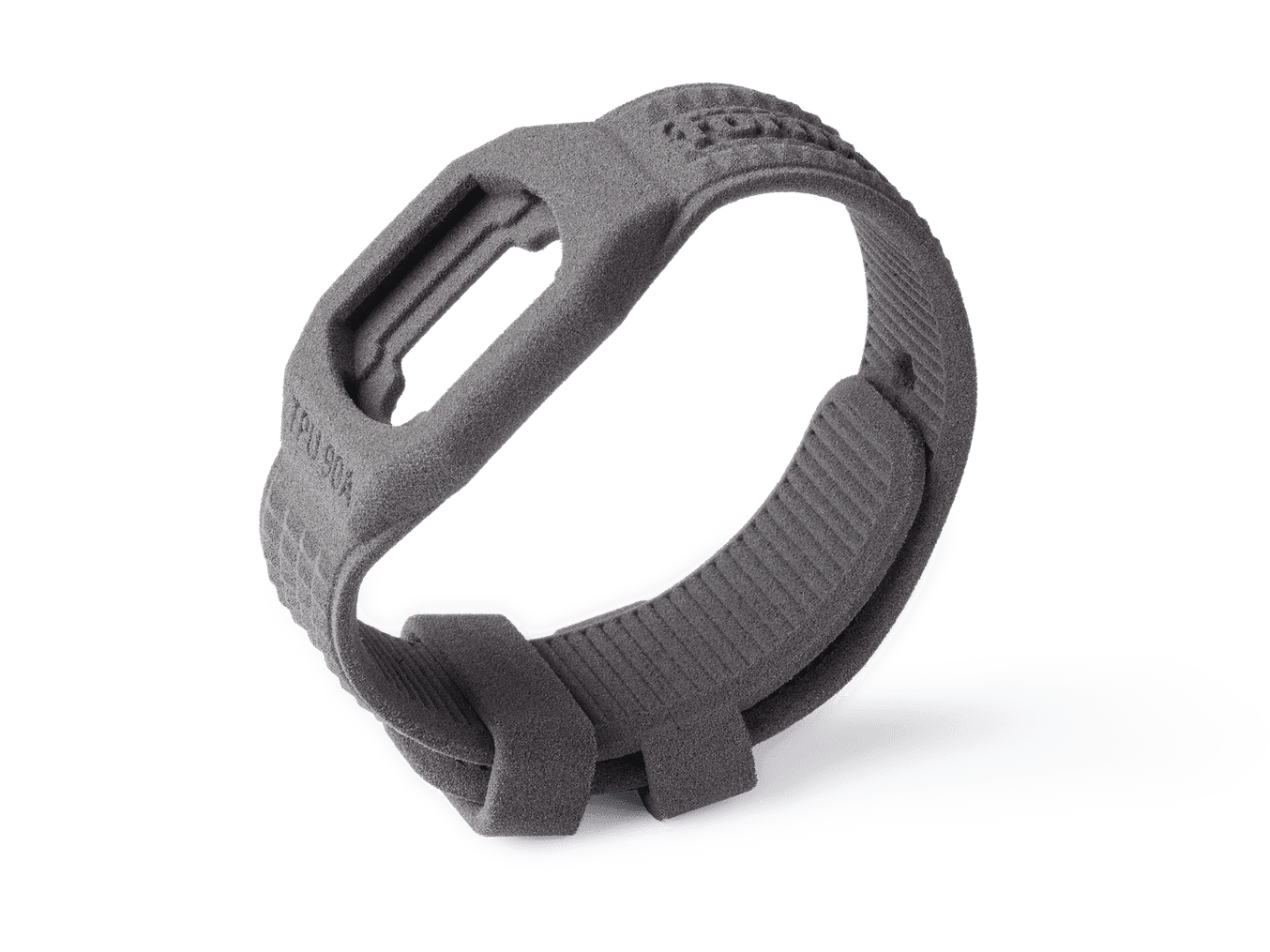
TPU 90A Powder : la poudre SLS flexible de Formlabs
Commandez un échantillon gratuit de bracelet de montre imprimé en TPU 90A Powder, notre premier matériau SLS flexible.
Applications de l'impression 3D de TPU
Il existe des flux de travail éprouvés permettant de produire en série des pièces en TPU avec des méthodes traditionnelles. Cependant, l'impression 3D de TPU offre une excellente alternative dans de nombreuses situations, notamment lorsque la vitesse ou la facilité d'utilisation est nécessaire pour le prototypage rapide, les aides à la fabrication produites à la demande et les applications de personnalisation. Qu'il s'agisse de fabriquer des prototypes rapides ou de concevoir des pièces d'utilisation finale et des biens de consommation personnalisés, l'impression 3D de TPU peut rendre les flux de travail plus rapides et plus efficaces en réalisant des pièces fidèles et précises.
Prototypage rapide
L'impression 3D avec le TPU permet aux entreprises de regrouper leurs capacités de prototypage dans leurs locaux, ce qui réduit les délais et les coûts qui accompagnent la sous-traitance à des fournisseurs de services ou des ateliers d'usinage.
Le prototypage d'un casque de sport, par exemple, nécessite de pouvoir fabriquer une coque dure ainsi que des coussinets souples à l'intérieur. Des entreprises innovantes conçoivent de nouvelles structures en treillis pour ces coussinets afin qu'ils amortissent mieux les chocs, et le TPU est un matériau idéal pour ce genre d'applications.
Expérimenter de nouvelles conceptions et formes empêche d'avoir recours à des méthodes d'outillage traditionnelles, et sous-traiter les pièces peut prendre des semaines. Le fait de pouvoir utiliser un seul flux de travail et un seul type de technologie pour la coque extérieure rigide et les coussinets intérieurs souples permet à ces innovateurs de réaliser des itérations beaucoup plus rapidement. Ces casques devront subir des tests physiques approfondis, de sorte que dix coussinets d'amortissement seront nécessaires pour une seule série de tests. Ces volumes sont trop importants pour qu'une surface d'amortissement soit minutieusement fabriquée à la main, mais trop faibles pour que le moulage traditionnel de TPU soit rentable. La solution est l'impression 3D en interne.
Avec TPU 90A Powder, les imprimantes 3D SLS de la série Fuse peuvent facilement imprimer plusieurs structures en treillis qui permettent d'apporter de légères modifications pour tester différentes conceptions. En modifiant la conception de la pièce pour par exemple épaissir la paroi, vous pouvez produire des pièces avec différents niveaux de dureté en fonction des applications et changer les dimensions après les essais.
Le flux de travail de la série Fuse donne accès à de nombreux matériaux qui offrent une large gamme de propriétés mécaniques. Vous pouvez ainsi garder le développement et la fabrication en interne et gérer la conception de nombreux composants différents à l'aide d'une seule technologie. TPU 90A Powder permet de concevoir un tout nouveau type de produit, qui peut être directement imprimé en 3D avec nos imprimantes fiables de la série Fuse.
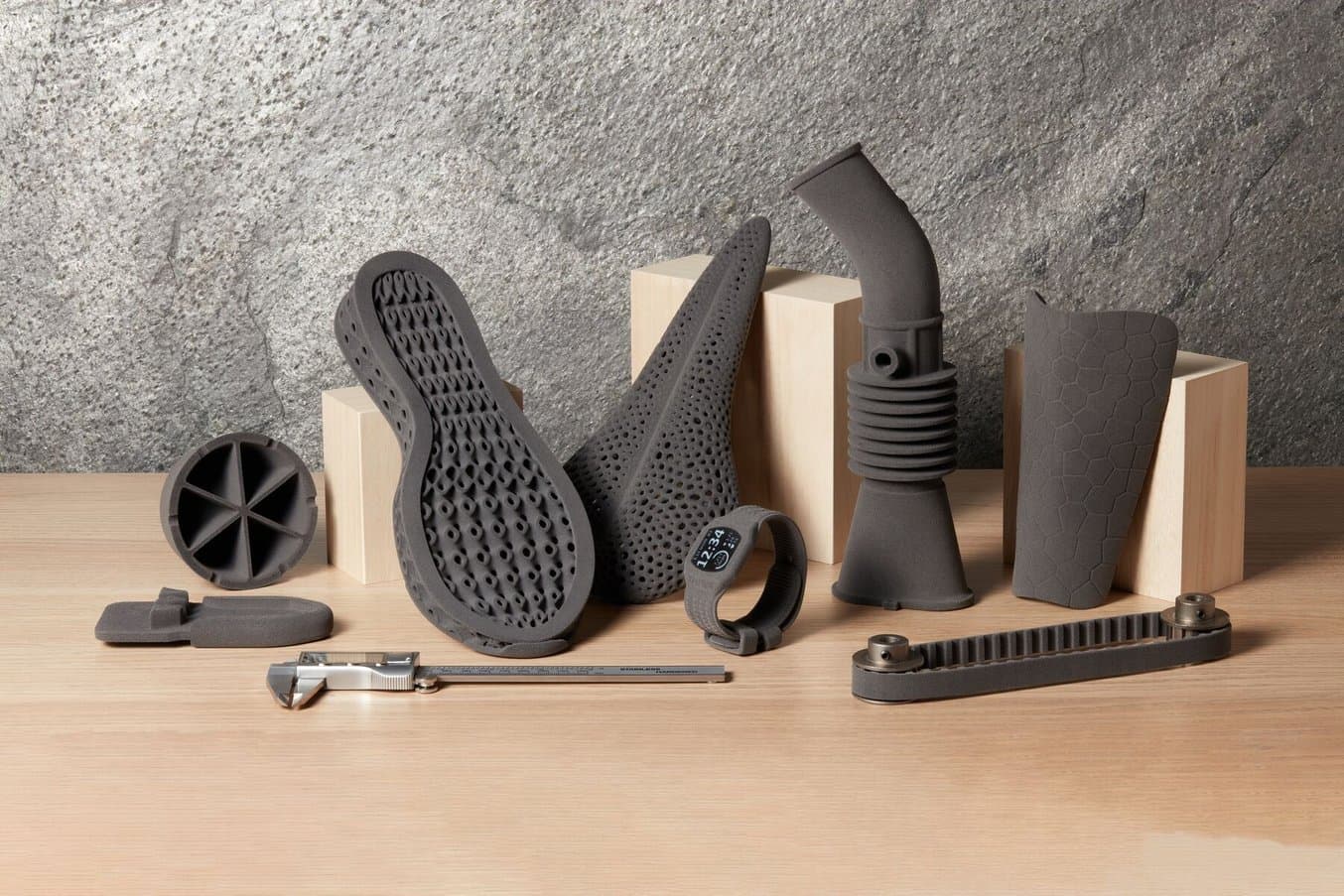
TPU 90A Powder est idéale pour le prototypage de pièces fonctionnelles nécessitant de la flexibilité, telles que des objets de technologie portable sûrs pour la peau, des équipements sportifs performants ou des semelles intérieures de chaussures.
Aides à la fabrication
Si vous ne travaillez pas dans ce secteur, les différences entre les types d'aides à la fabrication peuvent être difficiles à saisir. Mais qu'il s'agisse d'un gabarit, d'un support, d'un boîtier ou d'un autre type de pièce, l'essentiel est que ces pièces jouent un rôle pivot dans tout le processus de fabrication. TPU 90A Powder résout un problème auquel de nombreux fabricants sont confrontés : éviter que leur équipement de fabrication coûtant des millions de dollars ne subisse une usure trop importante.
Les aides à la fabrication à surface douce peuvent contribuer à prolonger la durée de vie des machines lourdes en amortissant certains impacts ou en offrant une forme de préhension parfaite. Lorsque des joints ou des sceaux se cassent après des années d'utilisation répétée, l'opérateur peut imprimer instantanément une pièce de rechange et remettre la chaîne de fabrication en service en quelques heures à peine, au lieu d'attendre des jours voire des semaines pour obtenir une nouvelle pièce.
L'impression 3D constitue une garantie pour les fabricants : elle les protège des arrêts de production dus à une pièce cassée ou à une machine défectueuse. Plus les matériaux dont ils disposent en interne sont variés, mieux ils se protègent des retards de la chaîne d'approvisionnement et des coûts élevés des réparateurs. Grâce aux pièces en caoutchouc imprimées en 3D, un tout nouveau sous-ensemble de composants d'équipement peut désormais être réparé ou remplacé à la demande. Éviter l'arrêt d'une chaîne de production ou d'un processus peut permettre d'économiser des milliers de dollars par jour.
Le TPU peut être utilisée pour des amortisseurs de vibrations dans les essais automobiles et aérospatiaux, ainsi que pour les gabarits dans les processus industriels tels que le thermoformage. Dans les usines automobiles, les grands systèmes robotiques fonctionnent sur des portiques qui doivent se plier et pivoter. Des coussins personnalisés et des boîtiers souples peuvent aider ces machines à éviter les frottements et à prolonger leur durée de vie.
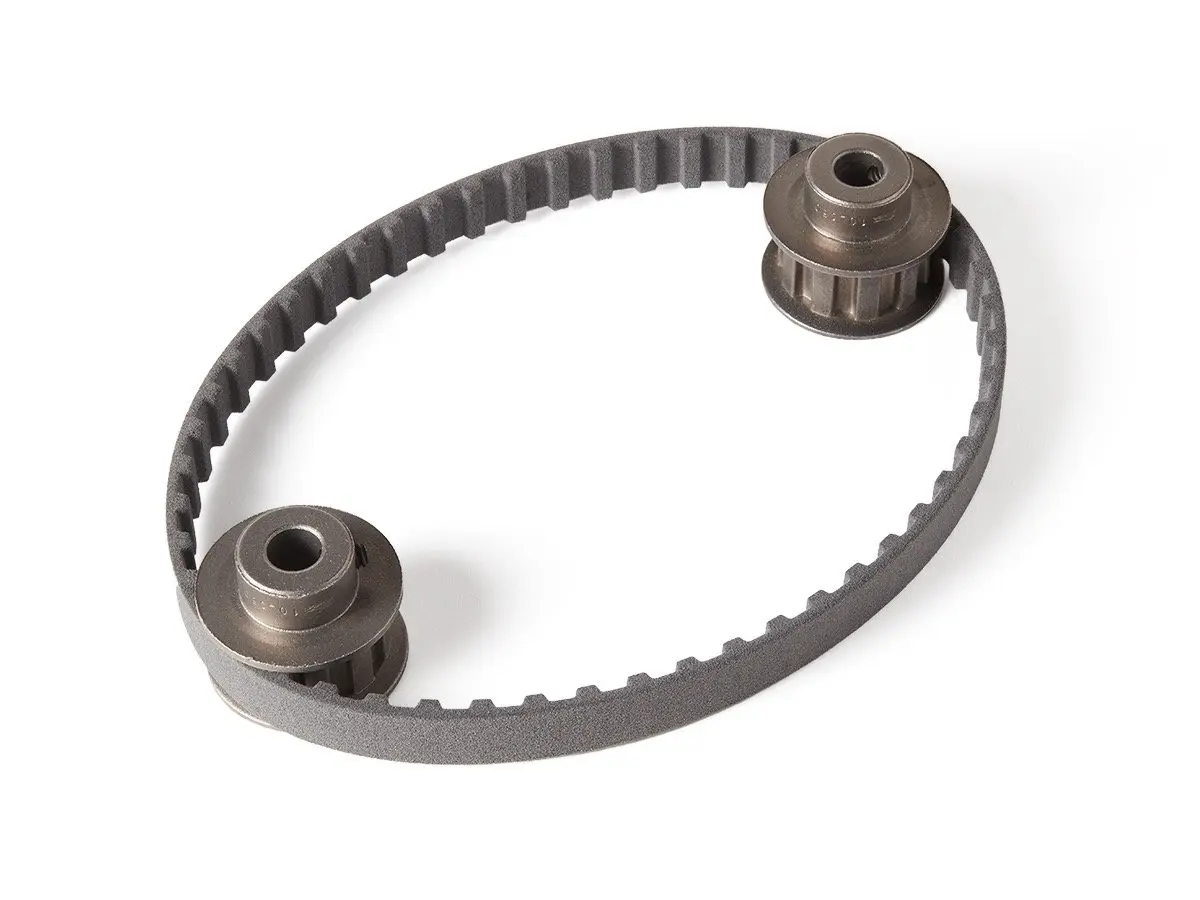
Le fait de disposer de matériaux en TPU signifie que des pièces de rechange et des aides à la fabrication flexibles peuvent être conçues et imprimées le jour même, pour que la production ne s'arrête jamais.
Petites séries d'objets de technologie portable personnalisés
Dans les secteurs du sport, de la mode et des technologies portables, il est impératif d'offrir des options de personnalisation pour les marques qui cherchent à conquérir davantage de parts de marché. Les coûts associés à l'outillage rendaient presque impossible la production de petites séries ou de pièces uniques, mais tout cela a changé avec l'arrivée des imprimantes 3D.
Cependant, la plupart des matériaux imprimés en 3D étaient trop rigides pour le marché des articles de sport ou des objets de technologie portable, ou tout du moins l'étaient avant le lancement de TPU 90A Powder. Il peut s'agir de semelles de chaussures personnalisables en fonction de l'empreinte et de la répartition du poids d'une personne, de casques de football conçus pour absorber les chocs, ou encore d'un bracelet de montre confectionné sur mesure : les possibilités sont illimitées.
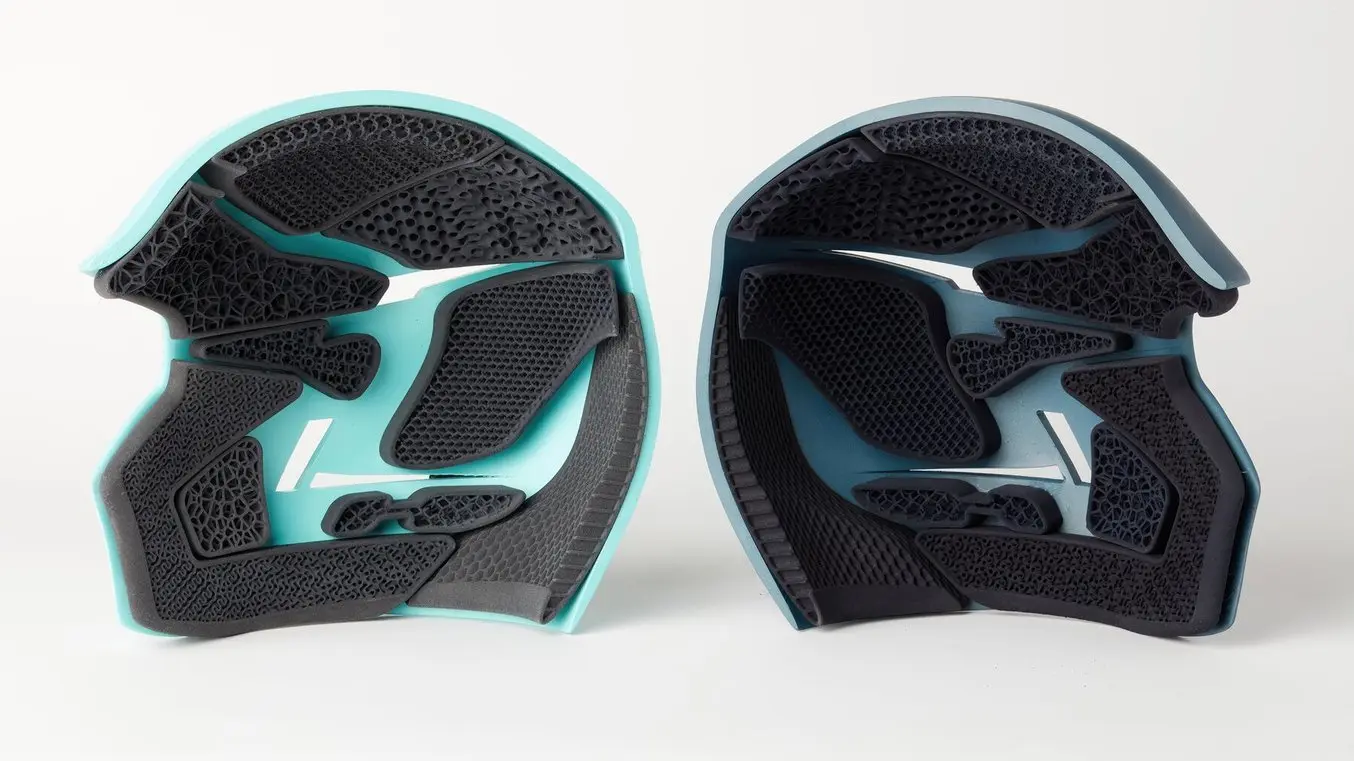
Casque de football américain avec rembourrages personnalisés imprimés en TPU sur une imprimante 3D SLS de la série Fuse.
Dispositifs médicaux
Offrant une durabilité et une résistance exceptionnelles, TPU 90A Powder est idéale pour les prothèses, les orthèses, les appareils spécifiques aux patients et les dispositifs médicaux. La possibilité d'imprimer en 3D des pièces finales souples et résistantes crée de nouvelles opportunités pour les professionnels de la santé en combinant la résistance au déchirement et l'allongement à la rupture des matériaux en caoutchouc avec la liberté de conception et la durabilité de l'impression 3D SLS.
TPU 90A Powder est un élastomère flexible, idéal pour l'impression 3D de pièces médicales telles que :
-
Composants et dispositifs médicaux d'utilisation finale, prototypes
-
Coussinets orthopédiques et manchons de prothèses
-
Objets de technologie portable, joints, amortisseurs et tubes
-
Attelles, casque de remodelage crânien
-
Semelles athlétiques et correctives
L'impression 3D dans le domaine de la santé, bien qu'en plein essor, est limitée par des exigences strictes en matière de matériau (notamment en ce qui concerne les certifications de sécurité, de résistance et de propriétés mécaniques). Le TPU imprimé en 3D ouvre de nouvelles perspectives pour différentes applications dans le domaine de la santé, et constitue un outil de plus dans l'assortiment disponible.
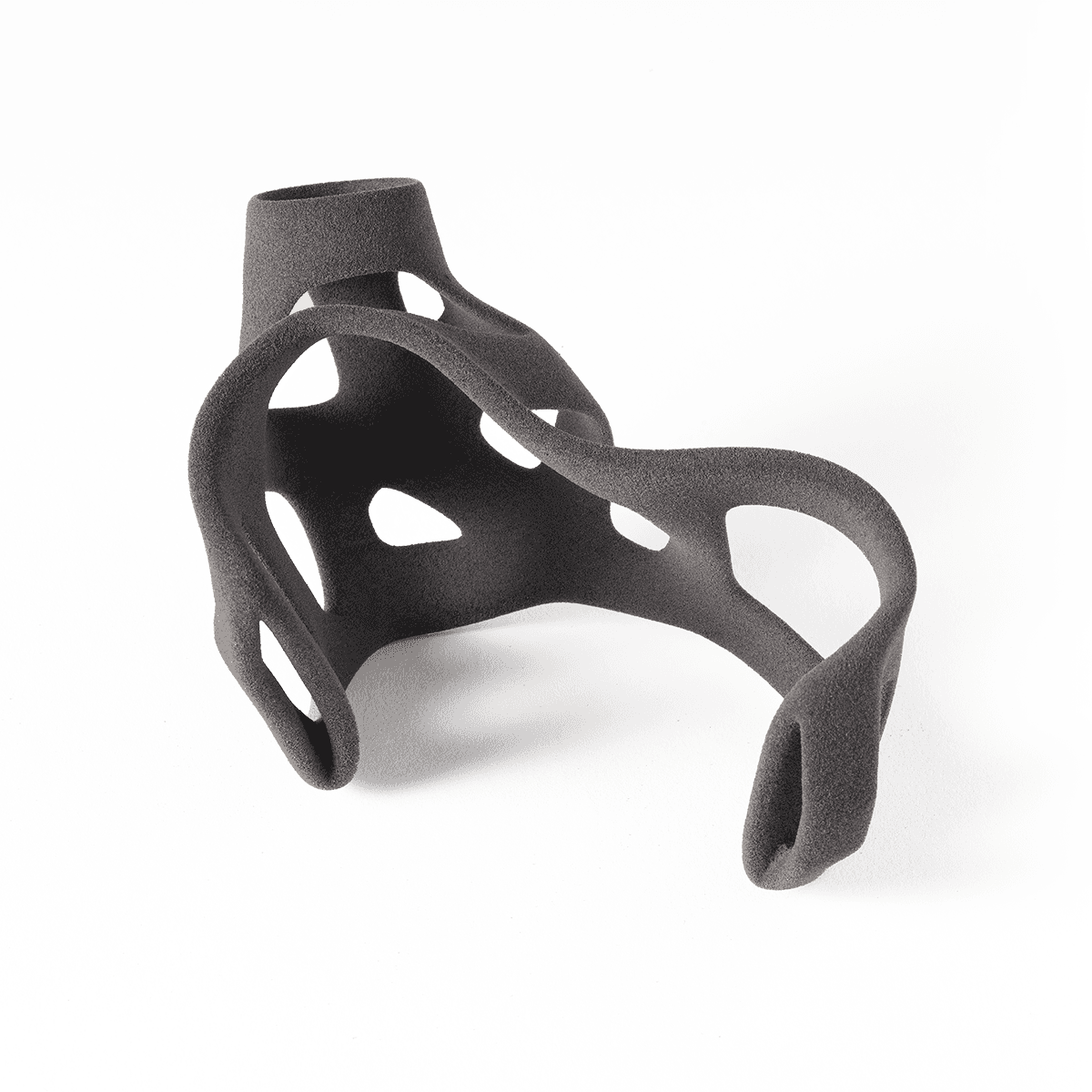
Cette attelle de pouce sur mesure offre une plus grande flexibilité et un meilleur contrôle que les attelles conventionnelles afin de soutenir le doigt et de le protéger contre d'autres blessures.
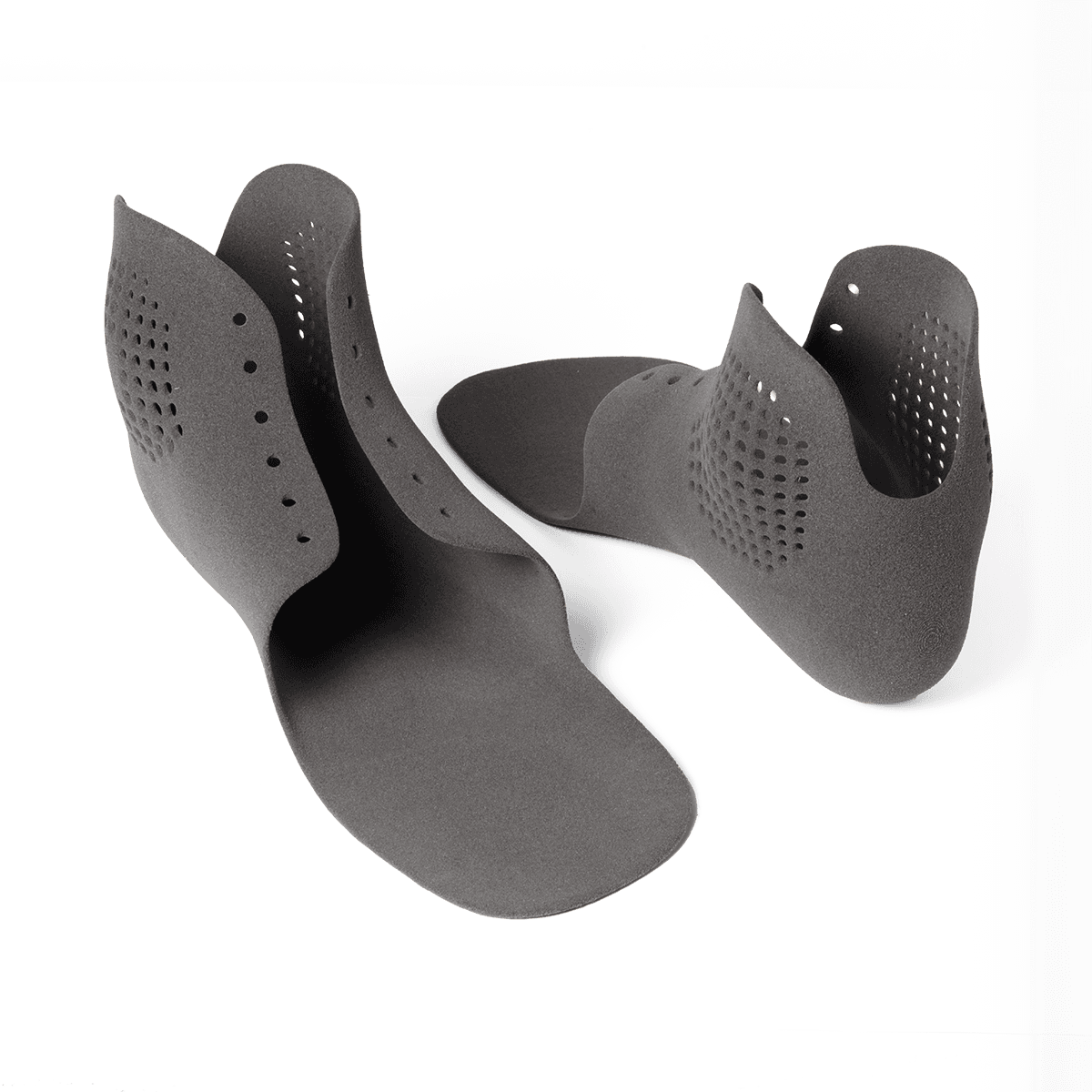
Le TPU est parfait pour une grande variété d'orthèses, par exemple les semelles orthopédiques et les semelles de sport.
Études de cas
Composants de protection pour les machines de Heidelberg, leader mondial des presses d'imprimerie
Heidelberger Druckmaschinen AG est le premier fabricant mondial de presses offset. Il est présent dans plus de 170 pays et emploie près de 10 000 personnes dans le monde. L’entreprise fabrique une vaste gamme d’équipements et de technologies d’automatisation pour l’ensemble de la chaîne d’impression, des presses à grande vitesse aux machines de découpe et de pliage.
Ils utilisent leur imprimante 3D SLS Fuse 1+ 30W pour créer des composants de machines, notamment des pièces légères pour les robots de transfert, de nouvelles pièces pour les plieuses, et des pièces de rechange pour les composants de machines qui étaient auparavant fabriqués en acier. TPU 90A Powder leur permet de créer des pièces flexibles capables de résister aux chocs et suffisamment malléables pour s'adapter aux machines rigides existantes.
Comme les pièces de rechange ou les aides à la fabrication doivent s'adapter aux systèmes robotiques existants, les pièces ont souvent des formes étranges et complexes. Elles sont spécialement conçues pour l'application concernée en fonction des charges et des forces auxquelles elles sont soumises, et doivent pouvoir résister à une usure constante. Les pièces imprimées en 3D sont souvent combinées à d'autres composants, comme des roulements métalliques ou du téflon couvrant des pièces pour réduire la friction. Certaines pièces sont moins complexes, mais nécessitent tout de même une grande exactitude ou une grande précision.
Les pièces en TPU empêchent la contamination croisée, couvrent les bords tranchants, protègent les capteurs ou préviennent l'usure. L'impression 3D SLS avec TPU 90A Powder est un processus parfait pour ce type de pièce et peut protéger des machines coûteuses contre les dommages associés à une utilisation aussi intense.
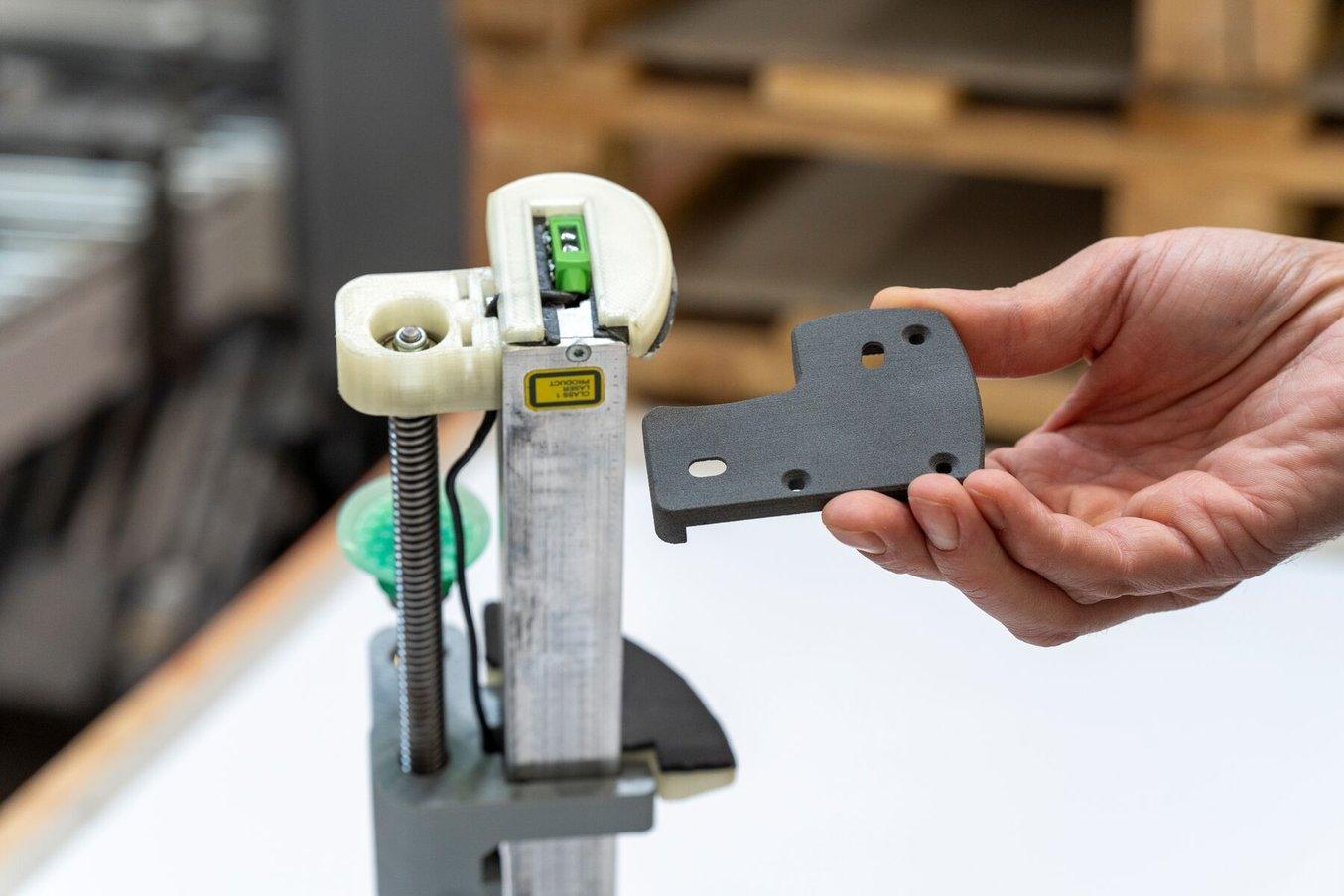
Une pièce flexible imprimée en TPU 90A Powder pour protéger les capteurs et autres outils de fin de bras.
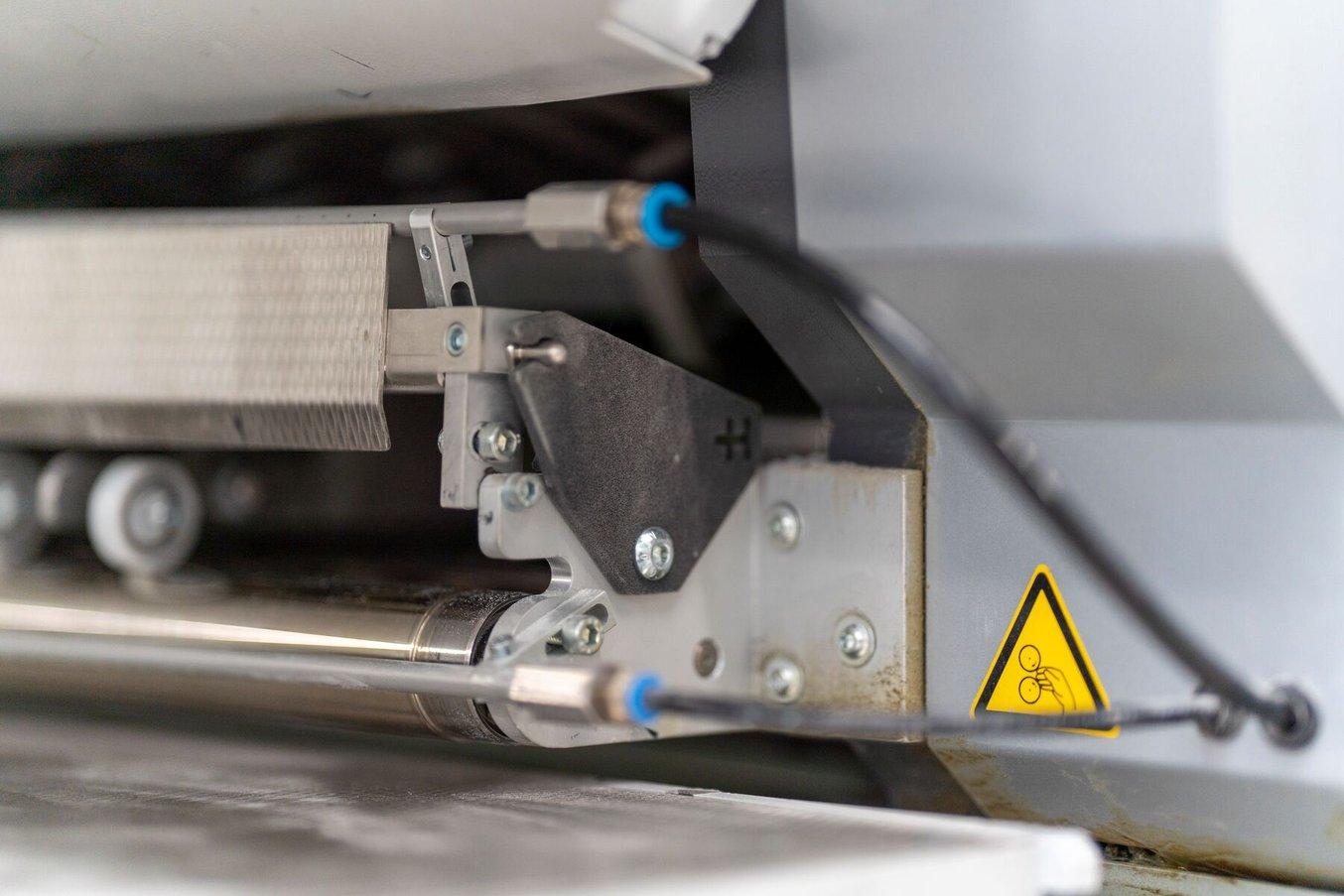
Les pièces flexibles sont idéales pour les composants encliquetables. En couvrant les bords tranchants, elles protègent également les opérateurs.
Une pièce spécifique – un guide-câble imprimé avec TPU 90A Powder – protège les câbles électriques d'une forte friction, améliorant ainsi leur longévité et minimisant les temps d'arrêt. Si l'un de ces câbles se rompt ou s'effiloche, l'ensemble de la machine est hors service jusqu'à ce qu'un câble de remplacement puisse être commandé et installé. Les composants de protection tels que ce guide-câble peuvent contribuer au bon fonctionnement d'un atelier.
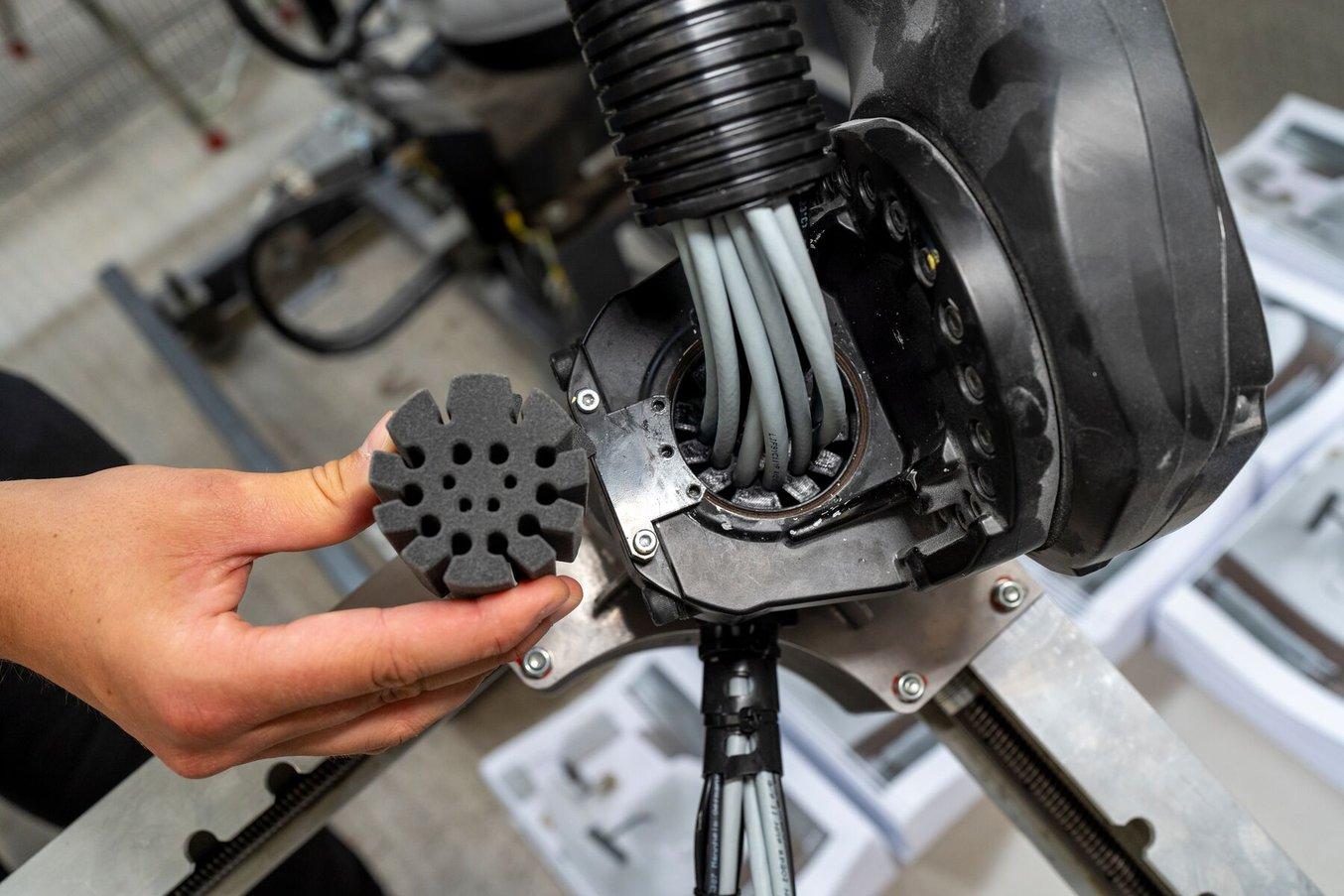
Ce guide-câble flexible produit avec une imprimante 3D SLS de la série Fuse permet une conception complexe et offre une solution durable à long terme pour protéger les câbles de l'usure.
L'accessibilité et le coût abordable de la série Fuse et de TPU 90A Powder permettent à l'entreprise de prendre le contrôle de sa propre chaîne d'approvisionnement et de ses besoins en matière de maintenance. Les pièces en TPU 90A Powder sont idéales pour protéger les machines, améliorer la longévité des composants et, en fin de compte, aider l'entreprise à réduire ses coûts et à éviter les temps d'arrêt.
Comment la Deutsche Bahn remet ses trains sur les rails grâce à des aides à la fabrication en TPU
Le service de maintenance de la Deutsche Bahn à Neumünster est chargé de la révision et de l'entretien des trains appartenant au réseau de transport public allemand, et l'impression 3D contribue à rendre ses opérations aussi efficaces que possible. Grâce à l'intégration de l'impression 3D dans son flux de travail, la Deutsche Bahn a économisé des millions d'euros et réduit les délais de remise en service des wagons.
Carsten Wolfgramm, ingénieur de fabrication et expert en fabrication additive, supervise deux imprimantes 3D SLS Fuse 1+ 30W. L'une imprime avec Nylon 12 Powder et l'autre TPU 90A Powder. « Nous utilisons les machines Formlabs parce que le rapport qualité-prix est imbattable pour nous. Elles sont fiables et toujours prêtes à l'emploi, en particulier les imprimantes SLS. Cela facilite grandement le travail lorsqu'il faut sans cesse modifier les pièces. Elles fonctionnent 24 heures sur 24, sept jours sur sept, tout au long de l'année », nous dit M. Wolfgramm.
Dans le cadre des tâches d'entretien habituelles, les techniciens retirent les porte-bagages pour les repeindre et poser un film sur les murs des wagons. Le déplacement des porte-bagages endommageait fréquemment les murs, réduisant à néant tout le travail que l'équipe de maintenance venait d'effectuer. Pour protéger les murs, l'équipe de DB a conçu et imprimé en 3D avec TPU 90A Powder des protections personnalisées pour les porte-bagages. Ces protections se glissent sur les porte-bagages et isolent leurs bords de manière à ce qu'ils ne puissent pas endommager les murs des trains fraîchement peints.
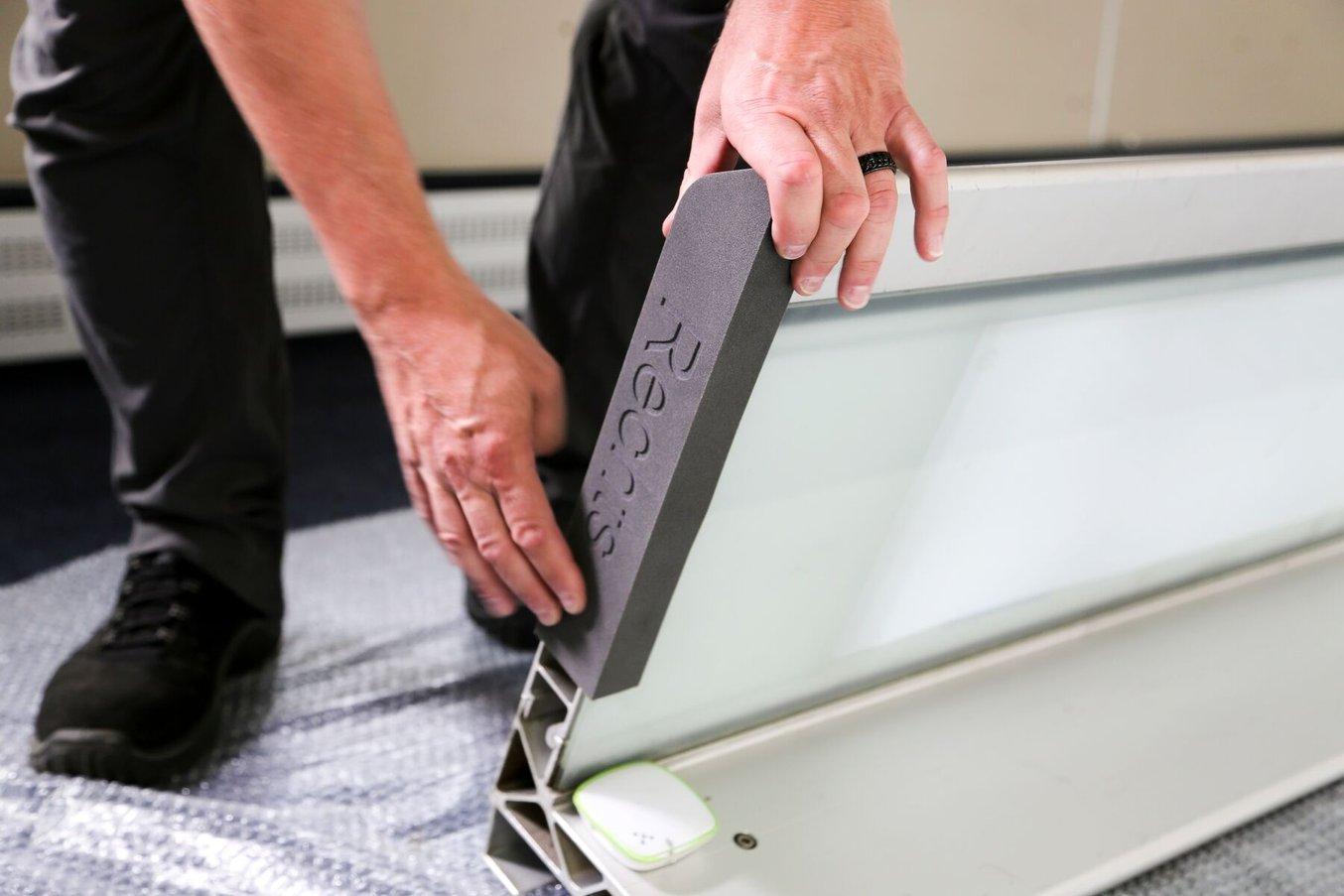
Un matériau souple, TPU 90A Powder, est utilisé par l'équipe pour protéger les porte-bagages contre les rayures et les chocs.
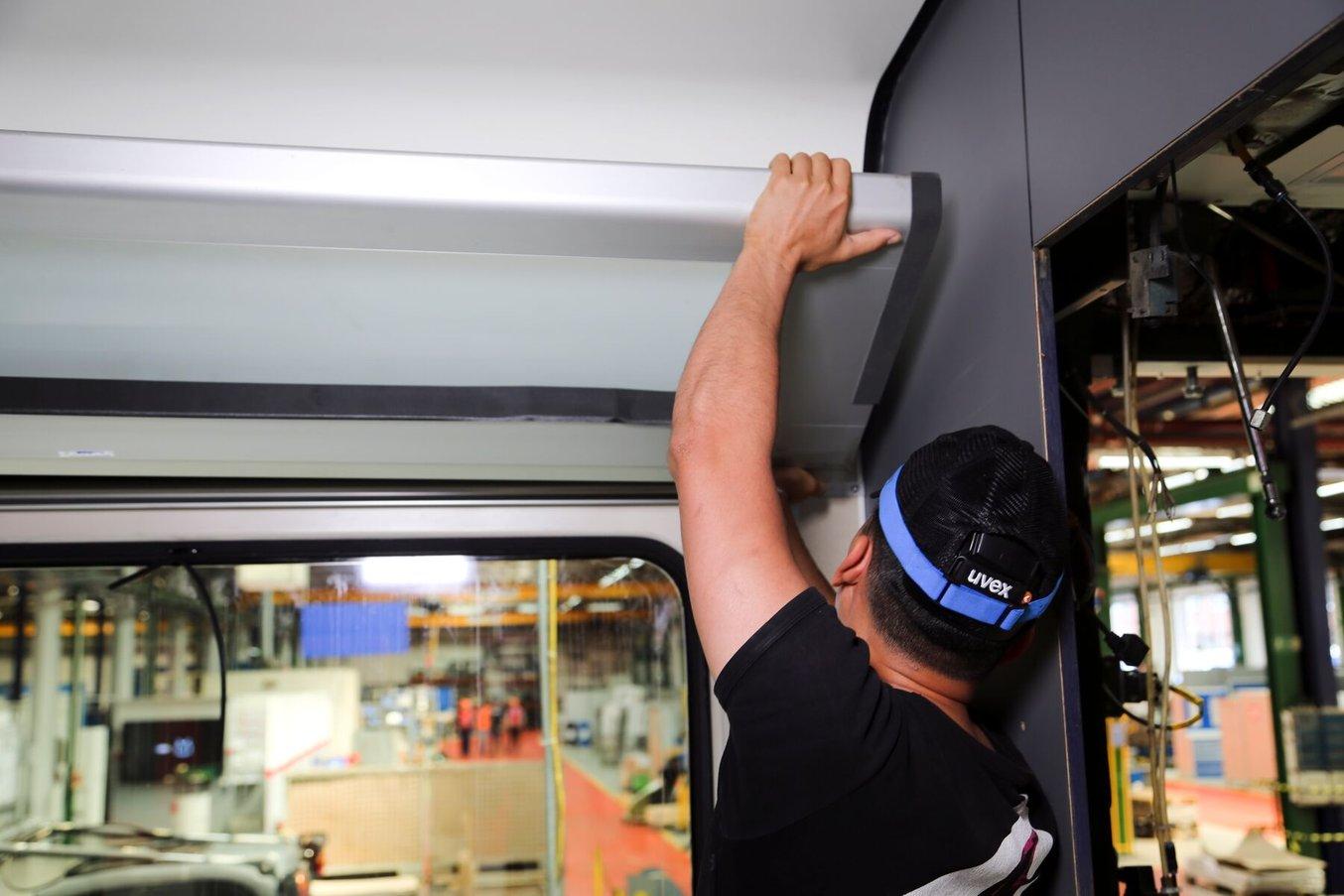
L'impression 3D SLS permet d'obtenir un design fin qui s'insère entre le porte-bagages et le mur.
« Avant que nous ne développions cette protection contre les rayures et que nous ne l'imprimions en 3D, nos collègues la masquaient toujours avec du papier bulle ou des moyens similaires pour essayer d'éviter les rayures, mais cela ne fonctionnait pas toujours. C'est la première fois que nous parvenons à éliminer complètement les rayures grâce aux nouvelles pièces en TPU. »
Carsten Wolfgramm, ingénieur de fabrication et expert en fabrication additive, Deutsche Bahn
En démontrant les économies de coûts et la réduction du temps de travail rendues possibles par l'impression 3D de pièces MRO comme celles-ci, la Deutsche Bahn offre un modèle aux grandes entreprises de transport qui souhaitent intégrer l'impression 3D dans leurs flux de travail. L'accès à la fabrication en interne de pièces flexibles et personnalisables imprimées en 3D telles que ces protections permet à la Deutsche Bahn d'améliorer l'efficacité de ses processus et de remettre les trains sur les rails plus rapidement.
Prototypage dans une entreprise américaine de jouets et de vélos électriques : Radio Flyer et TPU
Apprécié par les familles depuis plus de 100 ans, Radio Flyer est le fabricant de l'emblématique Original Little Red Wagon®, qui est entré au National Toy Hall of Fame (Panthéon national des jouets). Ils ont toujours joué un rôle central dans la culture populaire et leurs chariots, trottinettes, tricycles, karts, vélos électriques et autres produits innovants sont restés en tête de la liste de Noël de chaque enfant, au plus grand plaisir des petits comme des grands.
L'impression 3D occupe une place importante dans le processus de développement de Radio Flyer, et l'ingénieur concepteur Agostino Lobello a découvert que TPU 90A Powder permettait de réaliser des prototypes entièrement fonctionnels. « Sa finition de la surface à forte adhérence est bien meilleure que celle des autres TPE/TPU d'impression 3D avec lesquels j'ai travaillé. De ce point de vue, il ressemble davantage à notre TPE/TPU moulé par injection, ce qui est intéressant pour un prototype. Actuellement, la meilleure alternative à ce processus serait un outil prototype et l'injection de TPE ou d'autres uréthanes, ce qui est à la fois plus rentable et plus rapide », explique M. Lobello.
"Nous sommes impatients d'utiliser ce matériau pour fabriquer des bandes de roulement, des poignées, des pare-chocs, des coussins de siège et des prototypes de ressort avec un taux d'élasticité spécifique."
Agostino Lobello, ingénieur de conception
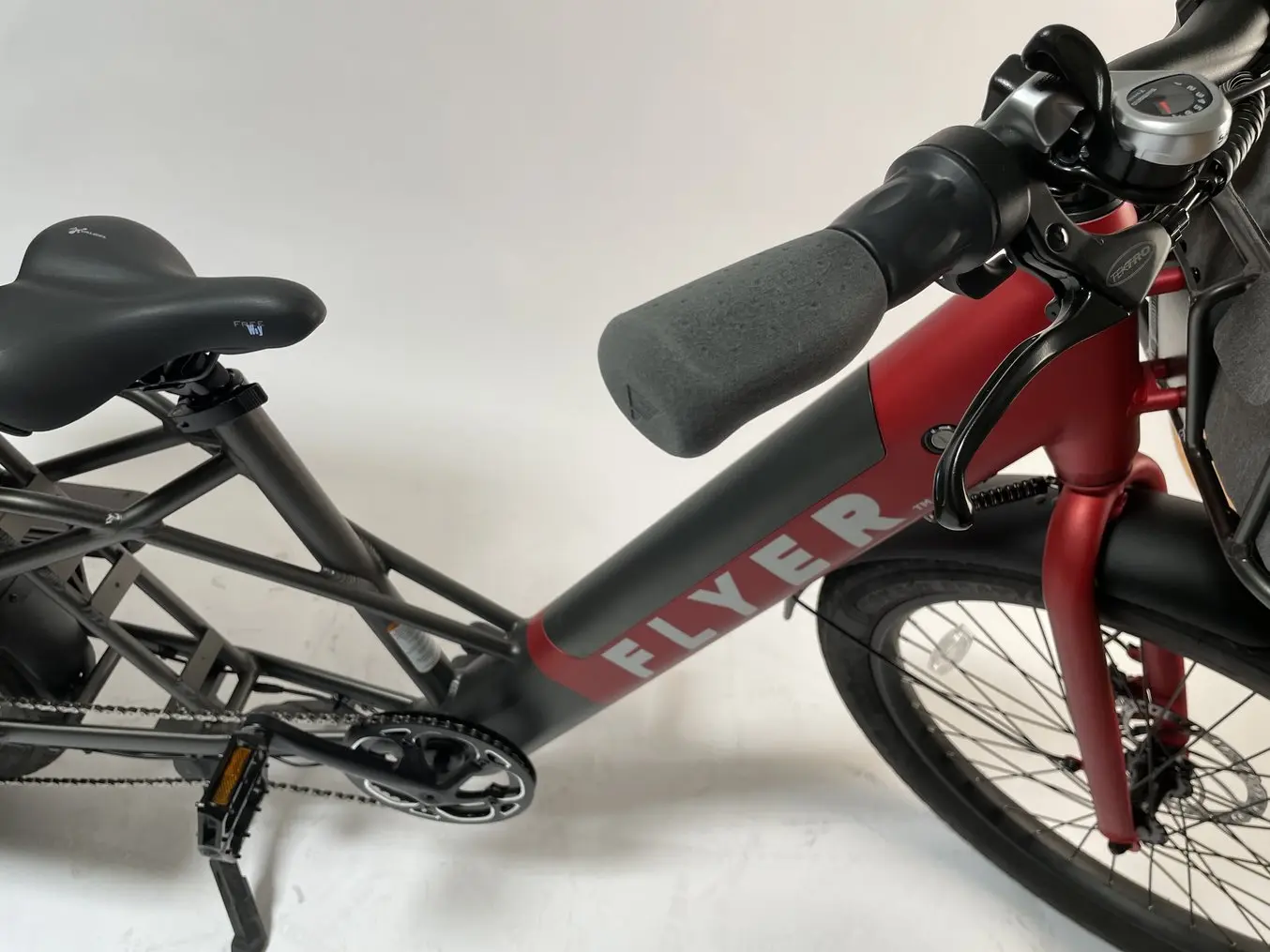
L'utilisation de TPU 90A Powder sur les imprimantes de la série Fuse permet à Radio Flyer de créer des prototypes fonctionnels de pièces telles que ce guidon à prise souple installé sur leur vélo électrique Flyer™ L885.
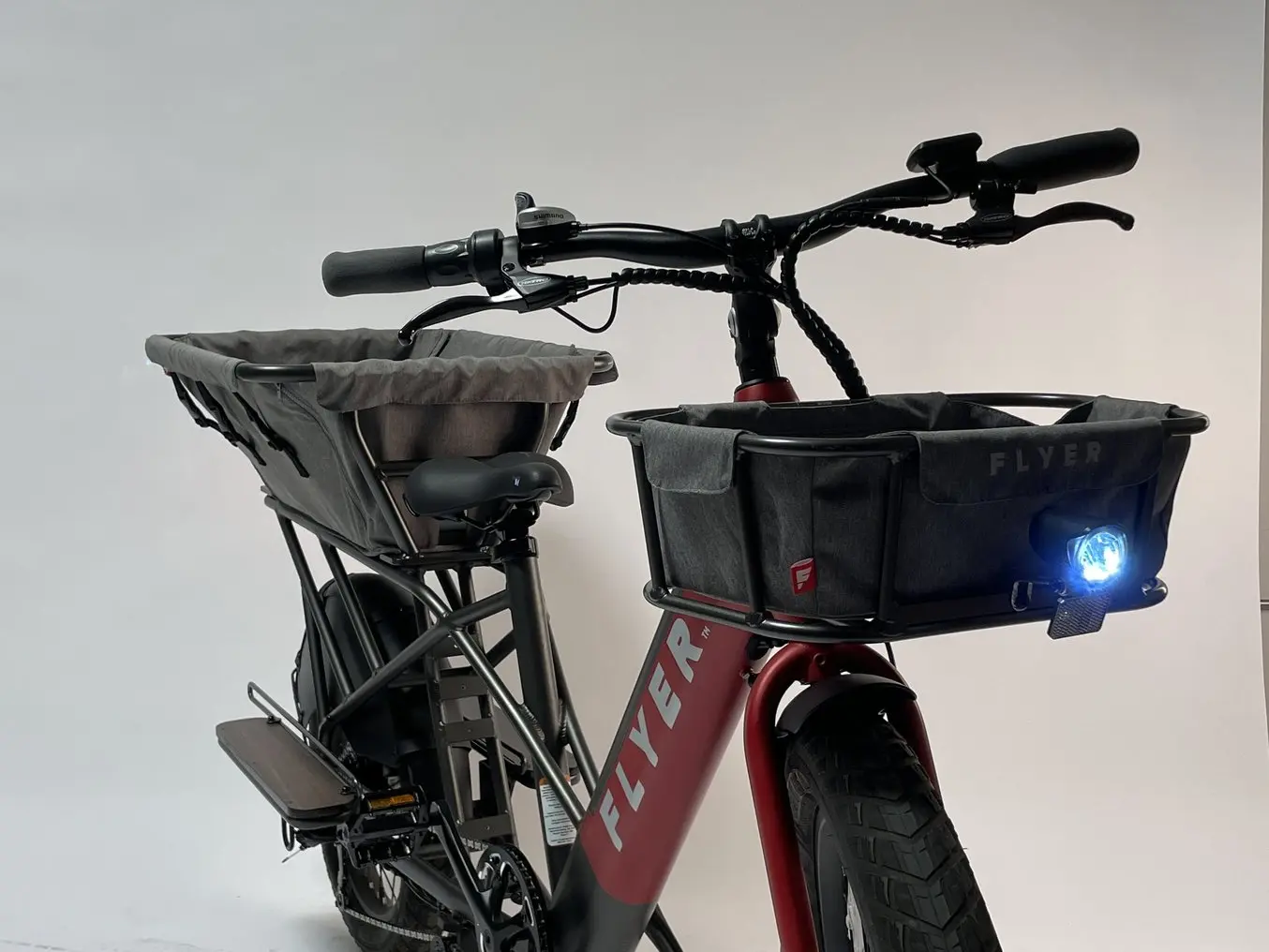
Lancez-vous dans l'impression 3D de TPU avec la série Fuse
Avec TPU 90A Powder, un flux d'impression 3D SLS accessible offre aux fabricants la possibilité d'améliorer leur processus de conception grâce à un prototypage itératif de haute qualité, ou de s'engager dans la production de pièces d'utilisation finale personnalisées.
L'écosystème SLS Fuse, qui comprend à la fois les imprimantes et la Fuse Sift, est compact, abordable et accessible. TPU 90A Powder de Formlabs permet de nouvelles applications et optimise les flux de travail grâce à la création de pièces résistantes, flexibles et isotropes qui devaient auparavant être moulées. Les solutions de fabrication en interne vous donnent plus de contrôle et de flexibilité dans votre processus de conception et de fabrication, quel que soit votre secteur ou votre application. TPU 90A Powder de Formlabs est sûre pour la peau, ce qui ouvre de nouvelles possibilités pour les secteurs de la santé et des objets de technologie portable.
Pour en savoir plus sur la production de pièces en TPU imprimées en 3D avec le flux de travail SLS de Formlabs, vous pouvez demander un échantillon gratuit en TPU 90A Powder ou contacter notre équipe commerciale pour discuter de votre application unique.