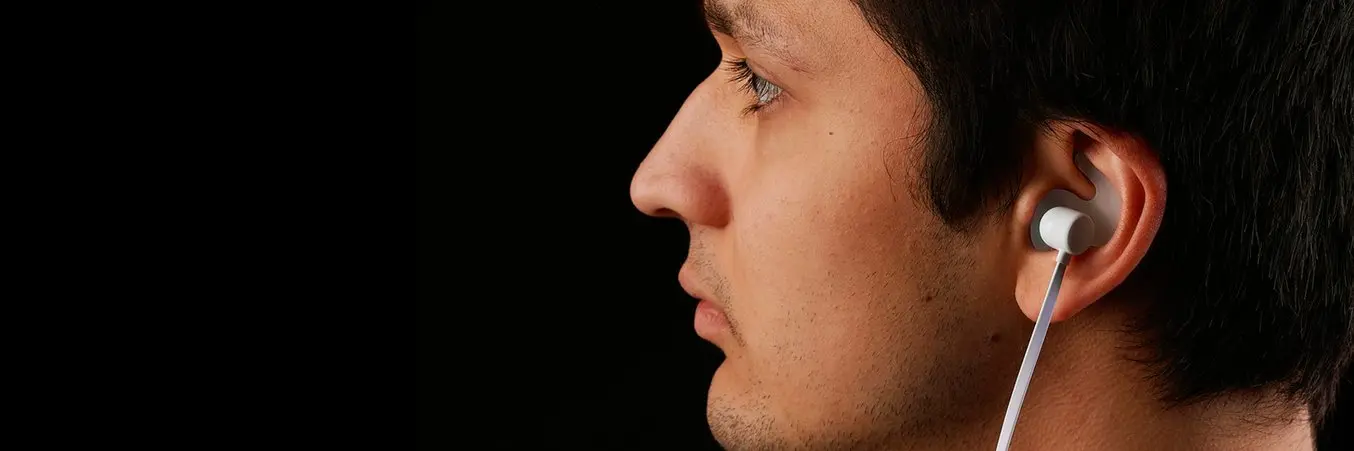
La majorité des produits fabriqués en série disponibles sur le marché actuellement pourrait nous faire croire que l'être humain existe en trois tailles seulement. Cela n'est pas le cas. Alors pourquoi les produits que nous achetons ne reflètent-ils pas cette réalité ?
Les produits sur mesure sont bien meilleurs et les consommateurs en sont conscients, mais leur fabrication est souvent bien plus coûteuse. La collecte de données auprès des clients est fastidieuse, les outils dédiés sont très onéreux et le suivi des pièces personnalisées à partir de la commande initiale, durant la production et jusqu'à l'expédition est complexe.
L'impression 3D change la donne. La baisse des coûts et les innovations dans le domaine des matériaux ont rendu l'impression 3D compatible avec la production, et promettent de faire du rêve de la personnalisation de masse une réalité.
Lors de CES 2018, Formlabs a fait la démonstration de cette réalité. Notre stand a reconstitué un processus de production complet d'écouteurs sur mesure(du scan intra-auriculaire au produit fini) pouvant être facilement répliqué dans les marchés de masse.
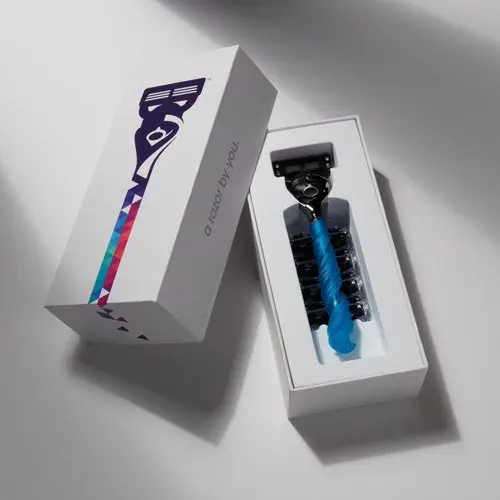
Guide de la personnalisation de masse
Ce guide donnera aux fabricants un aperçu des différentes approches de la personnalisation, des techniques les plus pertinentes et bien plus.
Une fabrication rentable de produits sur mesure
Les produits sur mesure sont meilleurs, c'est aussi simple que cela. Un écouteur réalisé sur mesure fournira une longévité, un confort, une stabilité et une réduction du bruit sans pareil sur le long terme.
Avec les avancées des technologies de scan et les imprimantes 3D de haute qualité devenues abordables, la fabrication de masse d'écouteurs sur mesure et d'autres produits du domaine de l'audiologie est désormais une option.

L'impression 3D n'est pas un remède miracle, mais elle permet de maîtriser beaucoup des défis généralement associés à la fabrication de masse de produits sur mesure :
- L'impression 3D ne nécessite aucun outil ; il est inutile de produire des milliers de pièces pour rentabiliser les coûts de moulage initiaux.
- Le niveau de complexité et d'originalité est illimité ; une imprimante 3D ne dépense pas plus de temps, d'énergie, ni de matériau pour une forme complexe que pour une forme simple. En outre, puisqu'aucun outil n'est requis, aucun coût de production supplémentaire n'est généré pour l'impression de nombreux designs.
- Avec des imprimantes 3D de bureau, il est plus facile d'augmenter le volume de production au fur et à mesure que la demande augmente.

L'observation du processus de fabrication des écouteurs sur mesure révèle un aspect important quant à l'intégration de l'impression 3D dans la fabrication ou la recherche sur la personnalisation de masse : les produits finis ne doivent pas nécessairement être imprimables en 3D. Vous pouvez toujours utiliser l'impression 3D pour créer des moules (comme dans le cas des écouteurs), des modèles pour le formage sous vide, ou des pièces à couler, et toujours fabriquer les produits finis dans un matériau éprouvé et rentable.
Procédure d'impression 3D adaptée aux environnements de marché de masse
Le scanner intra-auriculaire Phoenix de 3Shape’s et l'imprimante 3D SLA Form 2 de Formlabs s'associent pour fournir un processus intuitif et accessible qui peut être utilisé aussi bien pour la production d'une pièce unique que pour la fabrication de masse.
De la première à la dernière étape, le processus requiert un travail minimal, une empreinte énergétique réduite et il débouche sur un produit fini de haute qualité.

Le processus commence par un scan rapide et non intrusif du canal auditif du client à l'aide d'un scanner 3D. Un technicien travaille le fichier numérique pour produire un moule imprimable en 3D et l'envoie par une connexion sans fil à l'imprimante 3D. Une fois imprimées, les pièces sont rincées dans de l'alcool isopropylique et post-traitées. Un technicien coule de la silicone biocompatible dans les moules, retire les coques imprimées en 3D puis s'occupe de la finition et de l'apprêt du produit final.
Découvrez ce guide étape par étape de la production d'embouts auriculaires sur mesure en silicone avec la Form 2 et la Clear Resin de Formlabs.

Le futur de la personnalisation de masse
Les écouteurs sur mesure ne sont que le commencement. Les progrès dans les domaines de l'impression 3D et des technologies de numérisation ont permis d'ouvrir un marché auparavant réservé aux audiophiles ou aux artistes et nous sommes convaincus qu'à l'avenir, de nombreux autres secteurs pourront proposer les performances, le confort et la praticité des produits sur mesure à leurs clients.
LApprenez-en plus sur le futur de la fabrication et de la personnalisation de masse fdes experts sont intervenus lors de notre conférence Digital Factory, dont New Balance qui a annoncé un partenariat avec Formlabs afin d'incorporer l'impression 3D à sa ligne de production de chaussures à grande échelle basée au Massachusetts.
Davantage d'applications dans le domaine de l'audiologie ?
Apprenez-en plus sur lesoffres actuelles de Formlabs pour l'audiologie et le partenariat avec 3Shape, et restez informé(e) pour les prochaines innovations en 2019.
