Comment se lancer dans la fabrication numérique et créer un laboratoire en partant de zéro
Marco De Rossi a quitté la Colombie et est venu en Europe pour étudier la conception de produits à l'école polytechnique de Milan. À l'époque, les imprimantes 3D étaient plutôt rares, même dans les universités. Mais après avoir pu constater le potentiel de cette technologie pendant ses études, il a décidé de poursuivre un doctorat en fabrication numérique dans le secteur médical à l'université polytechnique de Valence, en Espagne.
Si l'université de Milan était bien équipée en scanners laser, en imprimantes 3D et en matériel de visualisation avancé, la nouvelle institution n'avait pas accès à des outils de fabrication numérique ; il a donc dû commencer par créer un laboratoire en partant de zéro. « J'ai dû créer un laboratoire d'impression 3D avant même d'avoir la possibilité de commencer mon doctorat », a déclaré M. De Rossi.
En partant d'un budget très limité, M. De Rossi a réussi à se lancer dans la fabrication numérique et à construire un laboratoire de trois salles doté d'une large gamme d'outils qui peut désormais s'autofinancer. Entretemps, il a pu travailler avec des chercheurs, des ingénieurs et des médecins sur de nombreux projets, notamment des modèles anatomiques, des pièces de rechange pour un appareil à rayons X, et des rétroconceptions pour l'analyse aérospatiale.
Lisez la suite pour découvrir ces applications et découvrir des conseils pratiques pour mettre en place un laboratoire, utiliser les bonnes ressources, collaborer avec la communauté locale et embaucher du personnel motivé.
Quatre conseils pour mettre en place un laboratoire de fabrication numérique
Commencer petit et acquérir de l'expérience
Créer un laboratoire à partir de rien peut sembler une tâche intimidante au premier abord, mais M. De Rossi a découvert qu'il est plus facile de diviser le processus en petites étapes avec des objectifs clairs.
« Au début, c'est très difficile, mais il faut avoir un point de départ. Je conseille de d'abord obtenir l’attribution d'une salle dédiée à l'université et d'acquérir de l'expérience en impression 3D. Avec cette expérience, essayez de décrocher des subsides. Vous ne pouvez tout simplement pas attendre d'avoir l'argent pour commencer. Il faut bien commencer quelque part, même vous n'utilisez d'abord qu'une imprimante peu coûteuse pour expérimenter, présenter vos créations et susciter l'enthousiasme des gens », a déclaré M. De Rossi.
« Ensuite, essayer de décrocher des subsides et le soutien d'autres chercheurs. Tout ce que j'avais au départ, c'était une salle et du matériel d'occasion bon marché. Notre plus grand succès a sans doute été d'obtenir des fonds. Nous avons reçu 25 000 dollars pour acheter du matériel. Mais vous ne parviendrez pas à obtenir une bourse de 25 000 dollars si vous n'avez rien à montrer », a déclaré M. De Rossi.
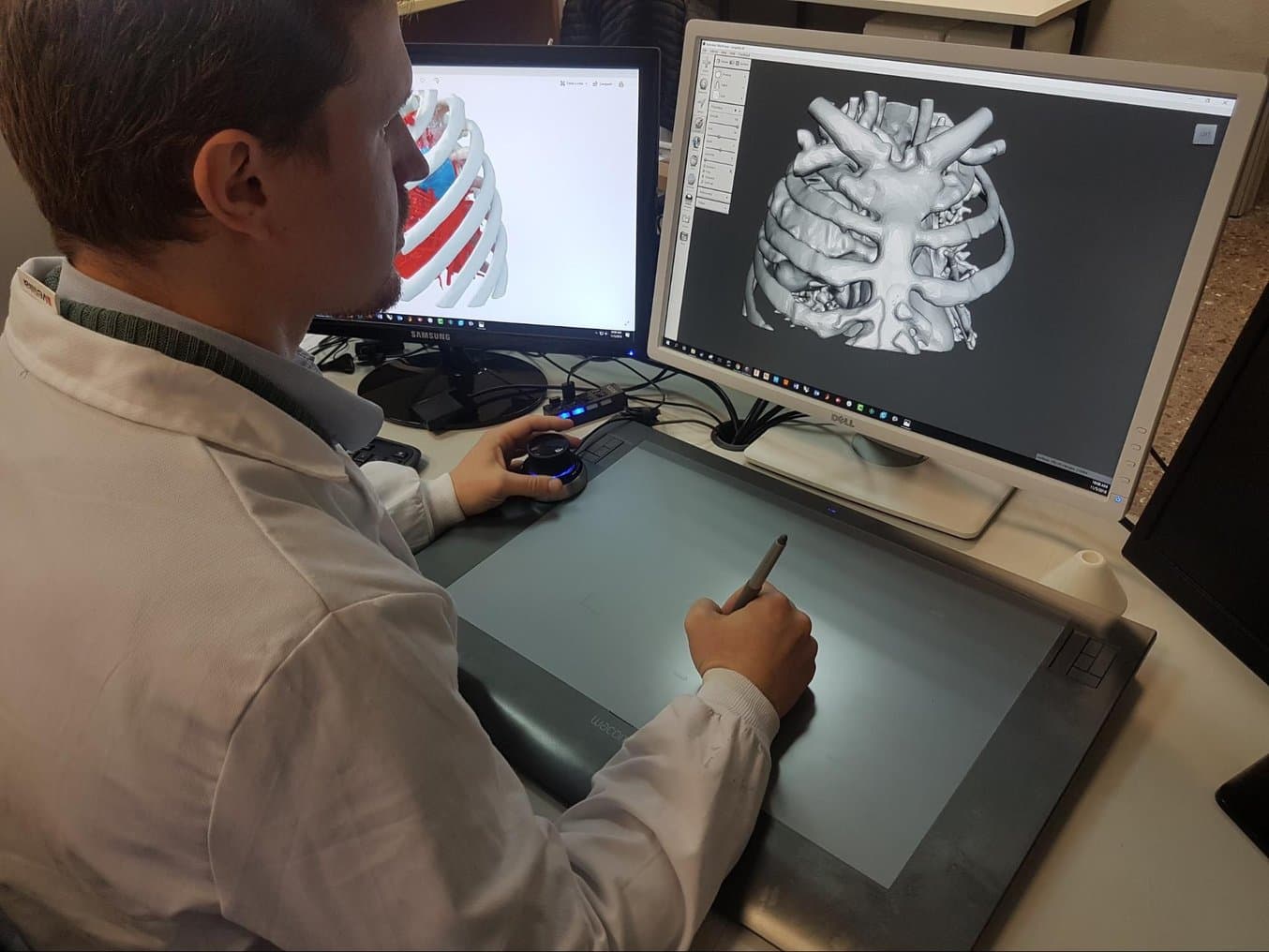
Les modèles anatomiques sont basés sur des scans CT ou IRM d'un patient. Les données des scans doivent être segmentées dans un logiciel afin d'isoler les zones reproduites par le modèle imprimé en 3D.
Collaborer avec d'autres chercheurs
M. De Rossi a pu constater que le fait de collaborer avec d'autres chercheurs, de partager ses connaissances et d'offrir l'accès aux outils de fabrication numérique en échange de ressources était bénéfique à la fois pour son doctorat et pour le laboratoire d'impression 3D.
« Il faut trouver un moyen de gagner de l'argent pour maintenir le projet à flots. Vous pouvez collaborer avec d'autres chercheurs pour trouver le moyen d'acheter de l'équipement et du matériel. Les universités sont de très grandes institutions et leurs budgets sont très stricts. Si vous trouvez un projet qui est assorti d'un budget pour acheter de l'équipement, vous pouvez vous coordonner avec les responsables, leur proposer de partager vos connaissances et de les aider [pour recevoir en échange l'imprimante à la fin du projet] », a déclaré M. De Rossi.
Partager vos ressources avec la communauté
« Certains responsables reçoivent un gros budget de départ pour leur projet de recherche, mais ils dépensent tout pour une imprimante qui prend vite la poussière. Ils l'utilisent une ou deux fois, et c'est tout. Si vous menez un projet d'envergure et que vous ne créez un laboratoire que pour parvenir à vos fins, le coût n'en sera pas rentable. Cette idée de tout garder pour vous parce que vous voulez tout contrôler est préjudiciable à long terme ; non seulement pour votre propre projet, mais aussi pour la communauté en général », a déclaré M. De Rossi.
« Beaucoup de ressources pourraient être partagées : nous sommes à l'ère de l'économie collaborative. Vous souhaitez qu'un investissement soit utilisé par le plus grand nombre de personnes possible. Collaborer vous permet d'investir dans de meilleurs équipements, du personnel mieux formé, de meilleures infrastructures. C'est l'un des avantages de l'université », a déclaré M. De Rossi.
M. De Rossi a constaté que, souvent, les gens passaient au laboratoire pour présenter fièrement un petit projet qu'ils avaient réalisé eux-mêmes, mais qu'ils se retrouvaient toujours bloqués dans le développement de ce projet parce qu'ils n'avaient pas accès à un équipement de prototypage. S'ils devaient investir le temps et l'argent nécessaires à l'achat d'une imprimante et à l'apprentissage de toutes les compétences nécessaires, ils abandonneraient probablement leur projet. Mais avec un accès aux machines et l'aide d'autres personnes expérimentées, la plupart des projets peuvent continuer et ont une chance de se concrétiser.
« C'est probablement la raison pour laquelle les Fab Labs connaissent un grand succès, car ce sont des endroits où énormément de ressources sont mises à disposition et dont tout le monde peut profiter. Chaque visiteur n'en utilisera probablement qu'une partie et n'apportera qu'une petite pierre à l'édifice, mais contribuera tout de même à soutenir un grand projet », a déclaré M. De Rossi.
Maintenir les ressources humaines
« Vous devez veiller à ce que des personnes soient présentes au laboratoire. Sinon, vous aurez l'espace, les machines, les matériaux, mais vous n'aurez personne qui sache comment les utiliser. Vous devez avoir une stratégie à long terme pour toujours avoir des personnes travaillant au laboratoire », a déclaré M. De Rossi.
Certaines universités engagent des techniciens pour faire fonctionner les équipements et entretenir le laboratoire, mais ce n'est qu'une partie du travail. Comme M. De Rossi l'a constaté, il vaut mieux que quelqu'un soit également présent pour aider les autres à utiliser les outils et leur apprendre comment les imprimantes fonctionnent. Il peut s'agir d'un professeur, d'un doctorant ou d'une personne passionnée qui aime tout simplement transmettre ses connaissances.
« C'est une bonne idée d'avoir des doctorants pour remplir ce rôle. Car il leur permet de faire des recherches, d'expliquer et d'enseigner. Les gens viennent au laboratoire parce qu'ils veulent apprendre. Si vous leur offrez la possibilité d'utiliser les machines, les matériaux et de s'impliquer dans le projet, ils vous donneront leur temps en échange », a déclaré M. De Rossi.
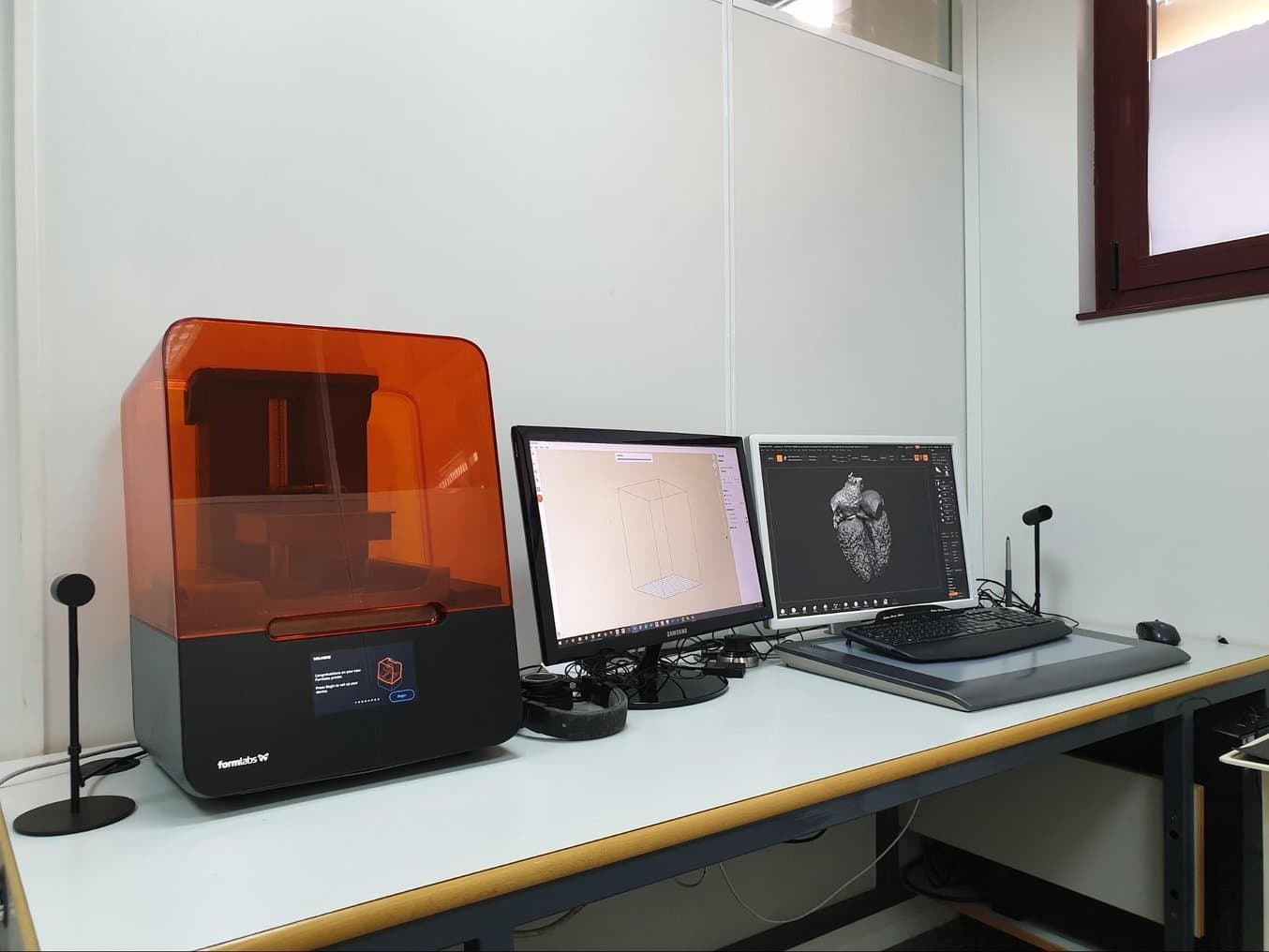
Le laboratoire est composé de trois salles indépendantes spécialisées. Une salle de conception propre accueille les imprimantes 3D de bureau ; ci-dessus, une station de travail avec une imprimante SLA Form 3.
Des projets de rétroconception aux modèles anatomiques
Le laboratoire de l'Université polytechnique de Valence se compose actuellement de trois salles indépendantes spécialisées. Une salle est équipée de différents outils de fabrication numérique : une découpeuse laser, de petites machines à commande numérique, une imprimante 3D à projection de liant, etc. Une partie est réservée à la peinture et à d'autres activités pouvant s'avérer salissantes. La salle suivante contient des outils traditionnels, tels que des scies, des perceuses et d'autres outils à main.
Enfin, une salle de conception propre accueille les imprimantes 3D de bureau, dont des imprimantes 3D stéréolithographiques (SLA) Form 2 et Form 3, plusieurs imprimantes à dépôt de fil fondu (FDM) et une station de conception. Au fur et à mesure que la panoplie d'outils du laboratoire s'est développée, de plus en plus de collègues de l'université ont souhaité mettre le laboratoire à contribution pour leurs projets.
« Si ce que vous construisez fonctionne, les gens viendront. Nous travaillons constamment pour les chercheurs, pour les étudiants, et pour l'industrie », a déclaré M. De Rossi.
L'une des applications les plus courantes est la rétroconception de composants spécifiques, par exemple pour l'analyse aérospatiale de composants de réacteurs.
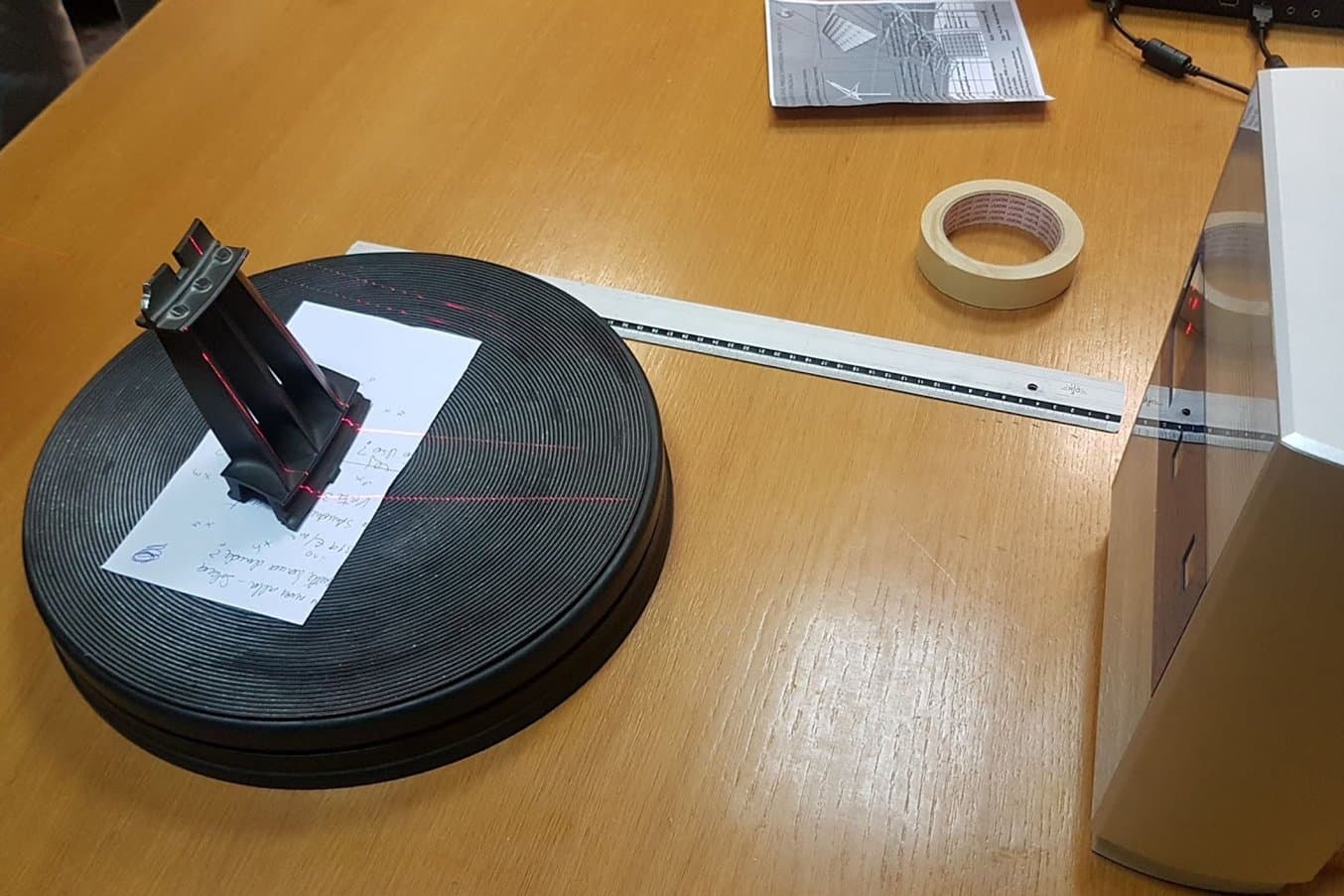
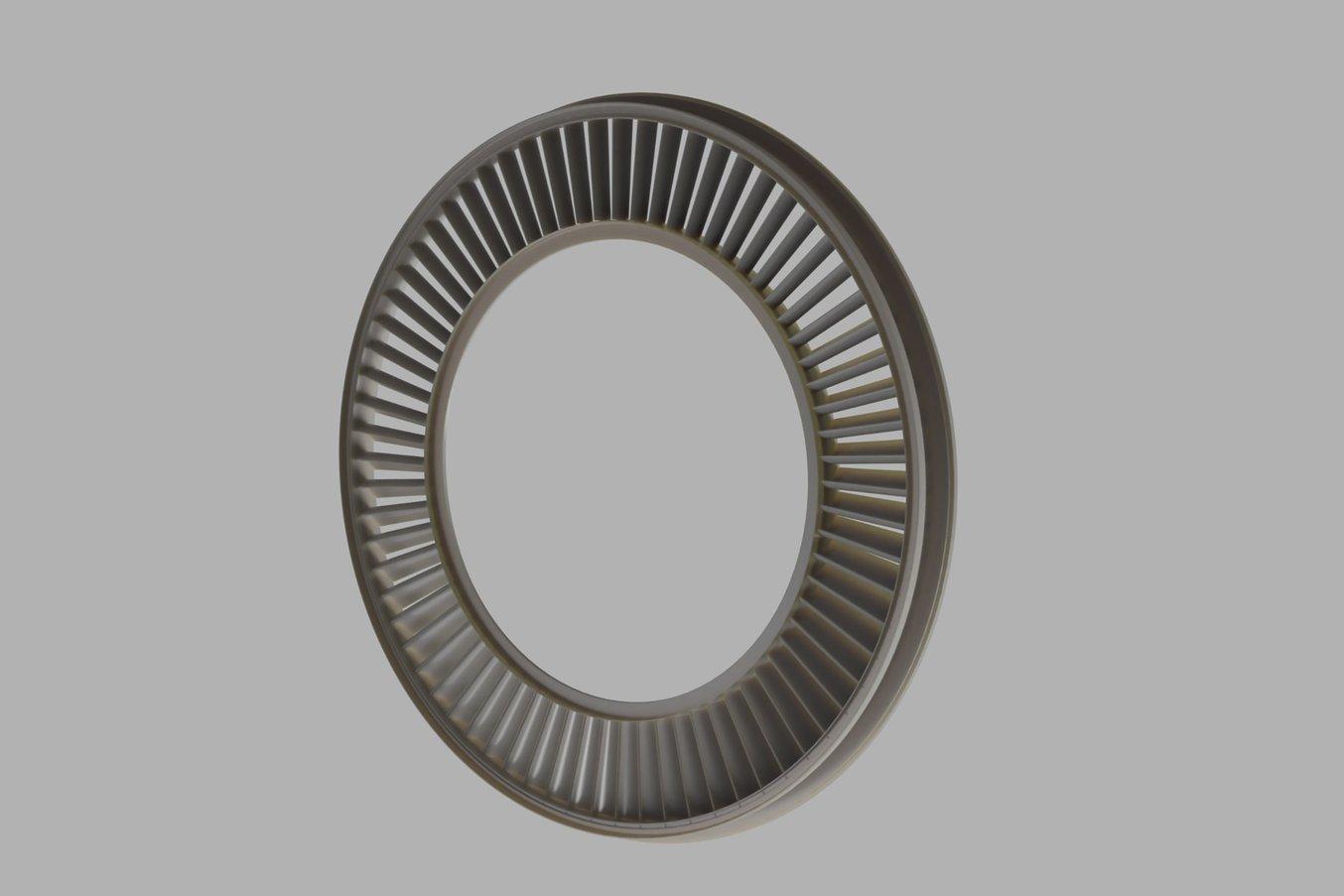
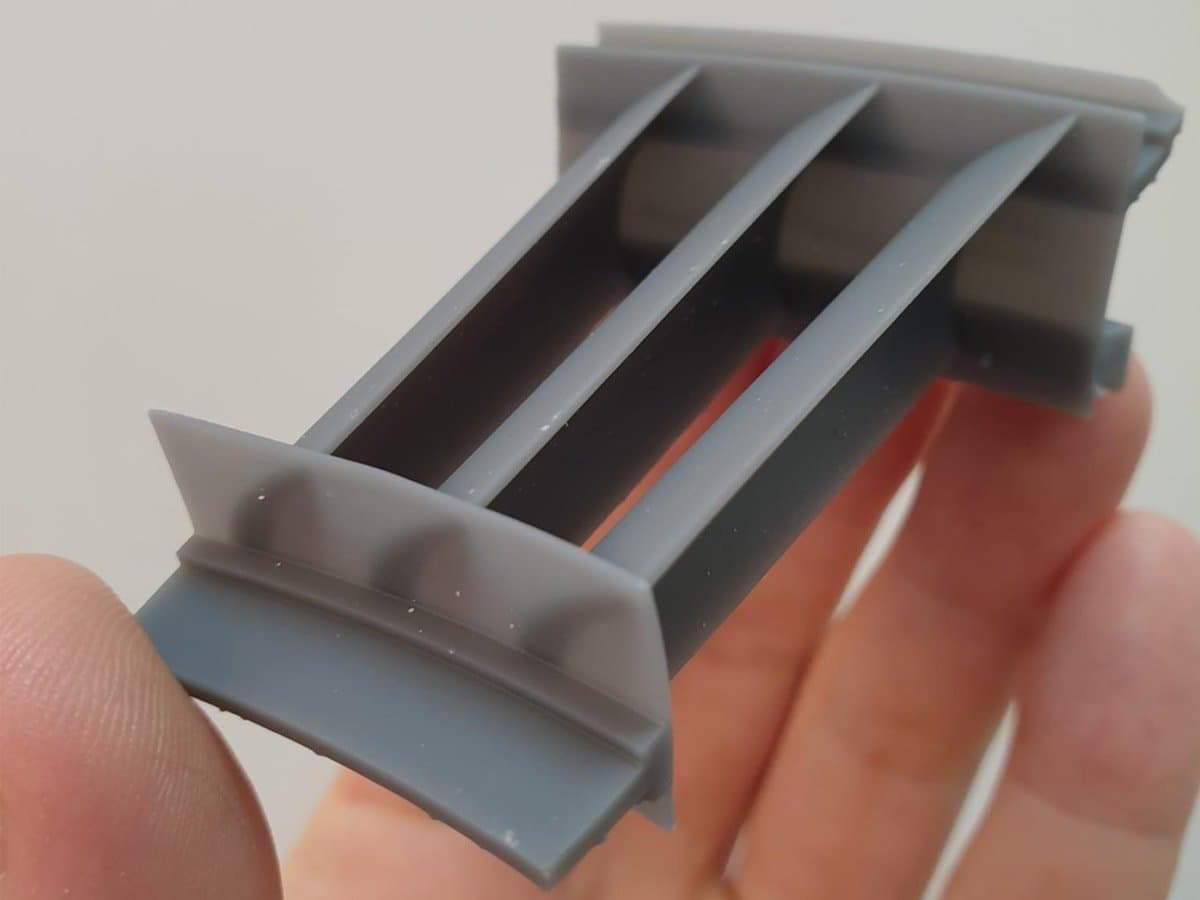
Scan 3D d'une pièce de compresseur appartenant à une turbine d'avion (en haut à gauche) et reconstruction 3D de l'anneau complet du compresseur (en haut à droite). La pièce a été imprimée en 3D sur la Form 3 et utilisée dans un test en tunnel aérien (en bas).
« Nous prenons une petite section d'aile ou de turbine de réacteur. Ensuite, nous la scannons en 3D, nous en faisons un modèle par rétroconception, et nous l'imprimons en 3D avec une imprimante 3D SLA. Comme ce genre de pièces présentent une très petite surface et des détails très fins, il est important qu'elles soient parfaitement reproduites. Au final, nous l'avons mise dans une soufflerie pour nous assurer de son fonctionnement. Il y a beaucoup d'objets très complexes qu'il serait difficile de concevoir à nouveau », a déclaré M. De Rossi.
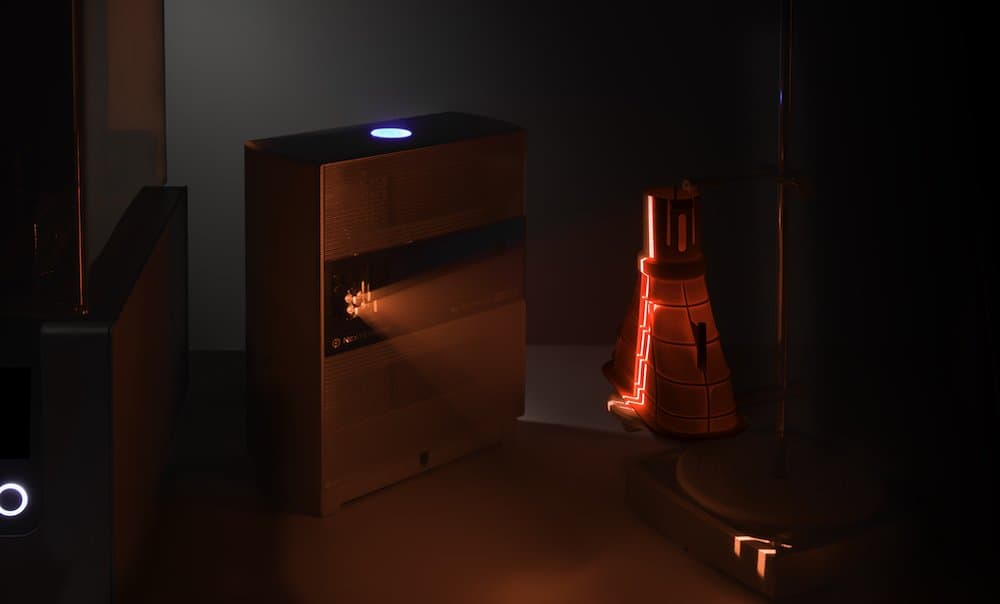
Numérisation 3D pour la rétro-ingénierie, la restauration et la métrologie
Ce livre blanc vous explique en détail comment utiliser la numérisation 3D pour améliorer la conception et la production de pièces, et comment, associés à l’impression 3D, les processus de numérisation 3D peuvent être appliqués efficacement en réplication, en restauration, en rétro-ingénierie et en métrologie.
Télécharger le livre blanc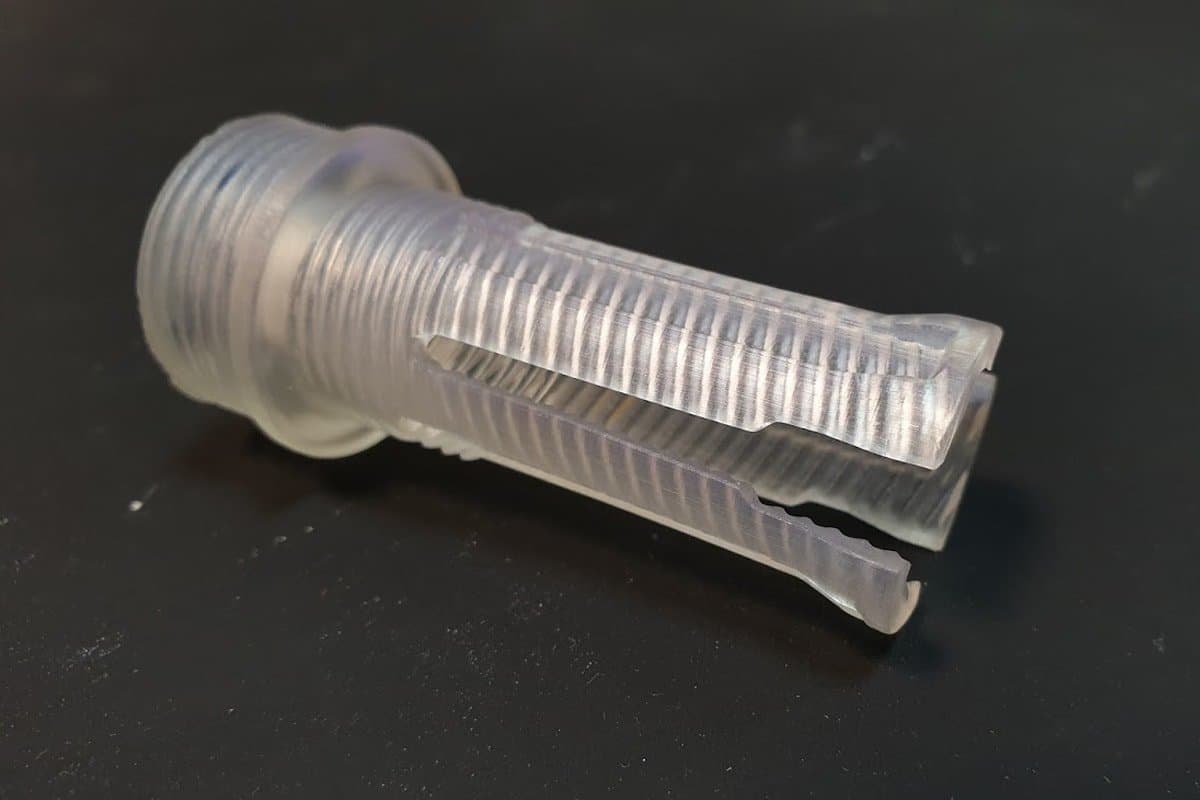
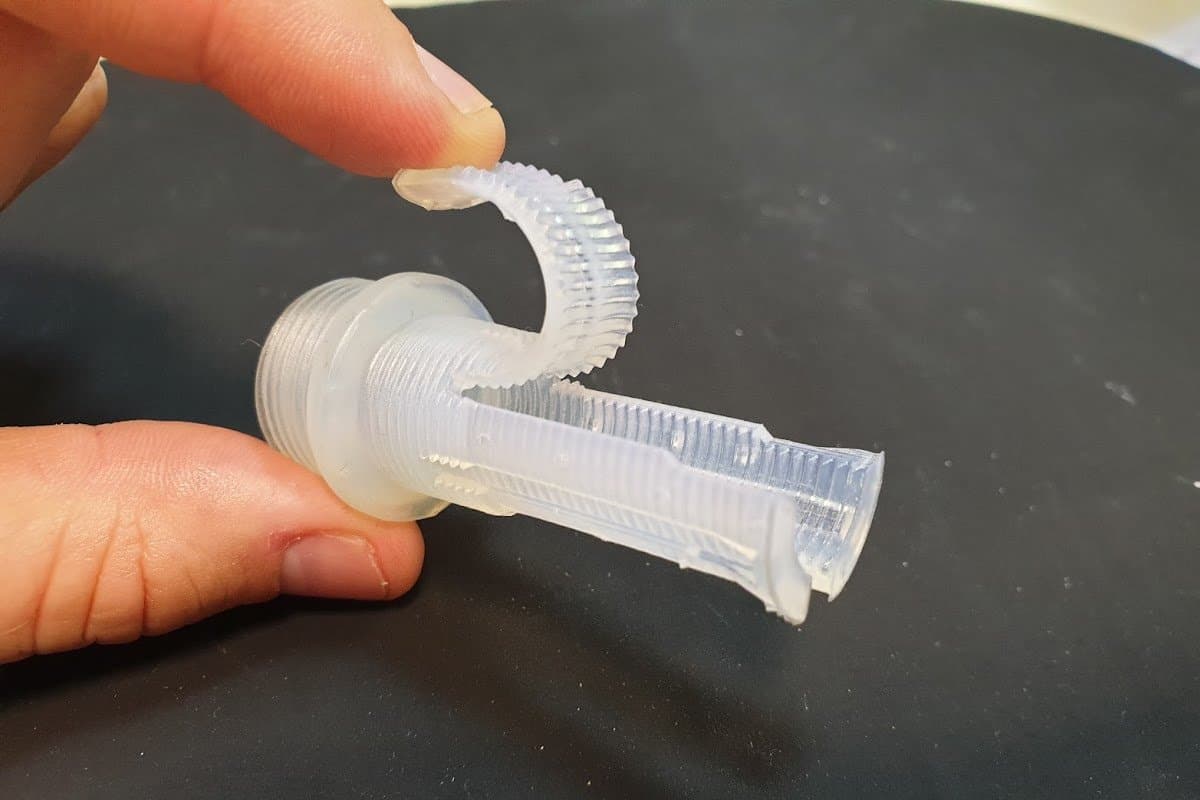
Cette pièce de rechange pour une machine à rayons X a été imprimée en 3D avec Durable Resin pour résister à l'utilisation prévue.
« Une fois, nous avons rétroconçu une pièce d'appareil à rayons X. Les appareils à rayons X sont très coûteux, et les hôpitaux peuvent les utiliser pendant une décennie ou même plus. Quand ils arrivent à la fin de leur durée de vie, ils doivent continuer à fonctionner, même si de nombreux composants sont indisponibles. Dans notre cas, une seule petite pièce était défaillante. À cause de cette petite pièce en plastique, nous allions devoir arrêter d'utiliser une machine valant plus de 100 000 dollars. Ils m'ont apporté la pièce, nous l'avons scannée en 3D et nous l'avons rétroconçue à l'aide de plusieurs logiciels. Nous l'avons imprimée avec Durable Resin sur une imprimante Formlabs. Le résultat était parfait. La machine fonctionne depuis plus d'un an sans aucun problème », a déclaré M. De Rossi.
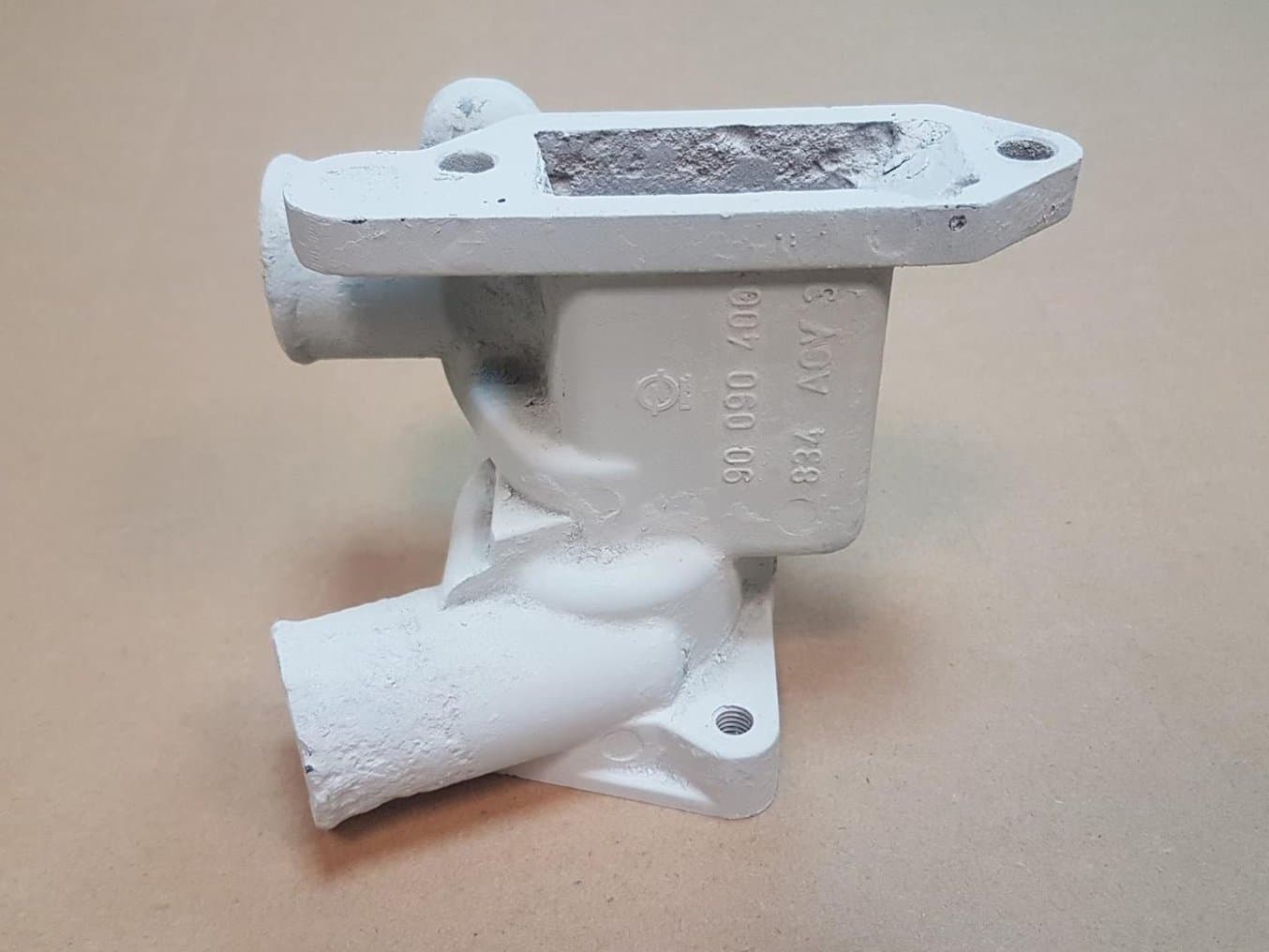
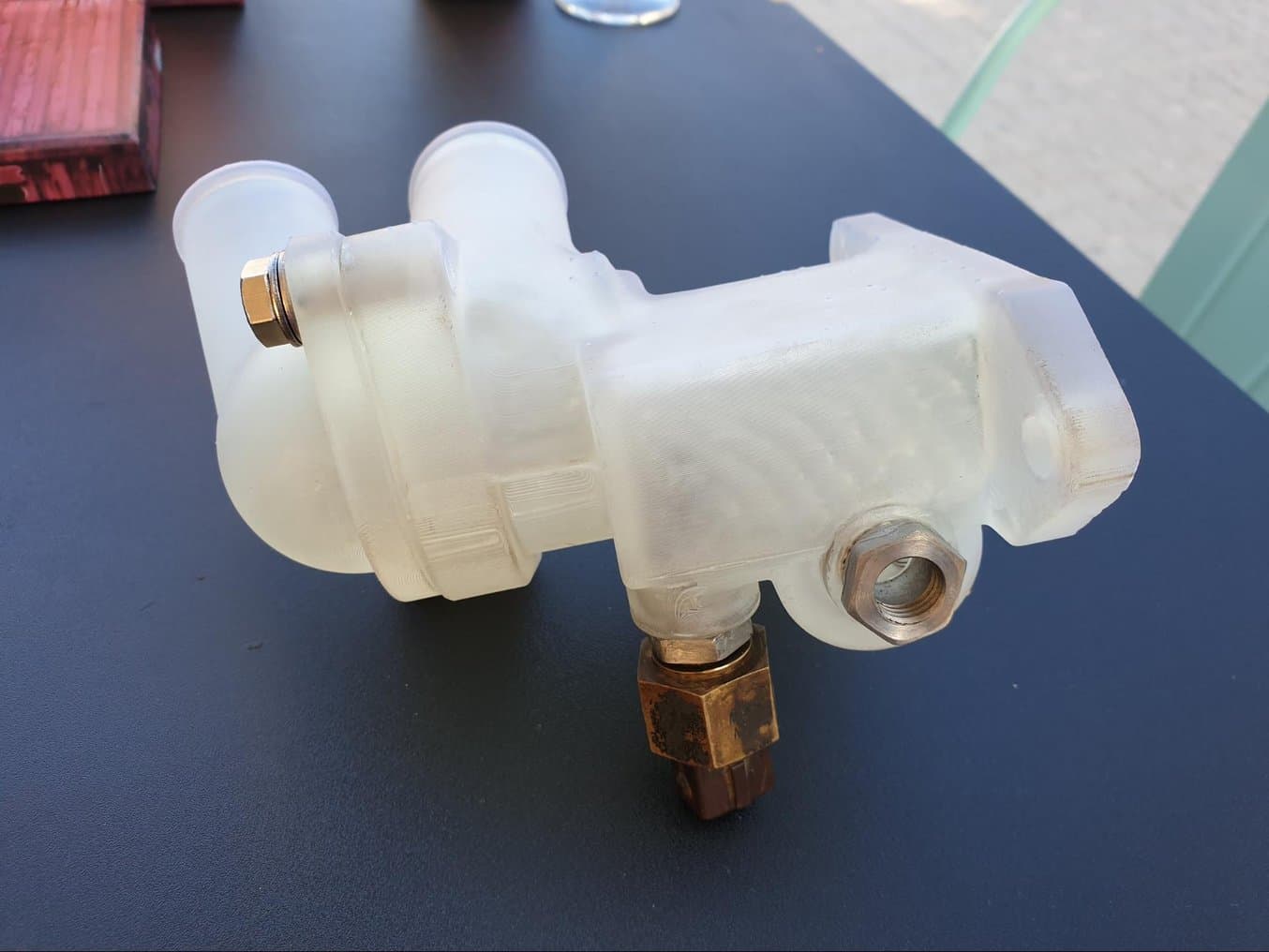
L'un des projets consistait à rétroconcevoir un thermostat corrodé pour une voiture ancienne. La pièce défaillante a été peinte en blanc pour être scannée, rétroconçue en CAO, imprimée en 3D avec High Temp Resin pour la résistance thermique, puis assemblée avec des pièces filetées et des composants métalliques par un spécialiste du fraisage traditionnel.
Fidèle au sujet de son doctorat, M. De Rossi a également réalisé de nombreux projets dans le domaine médical.
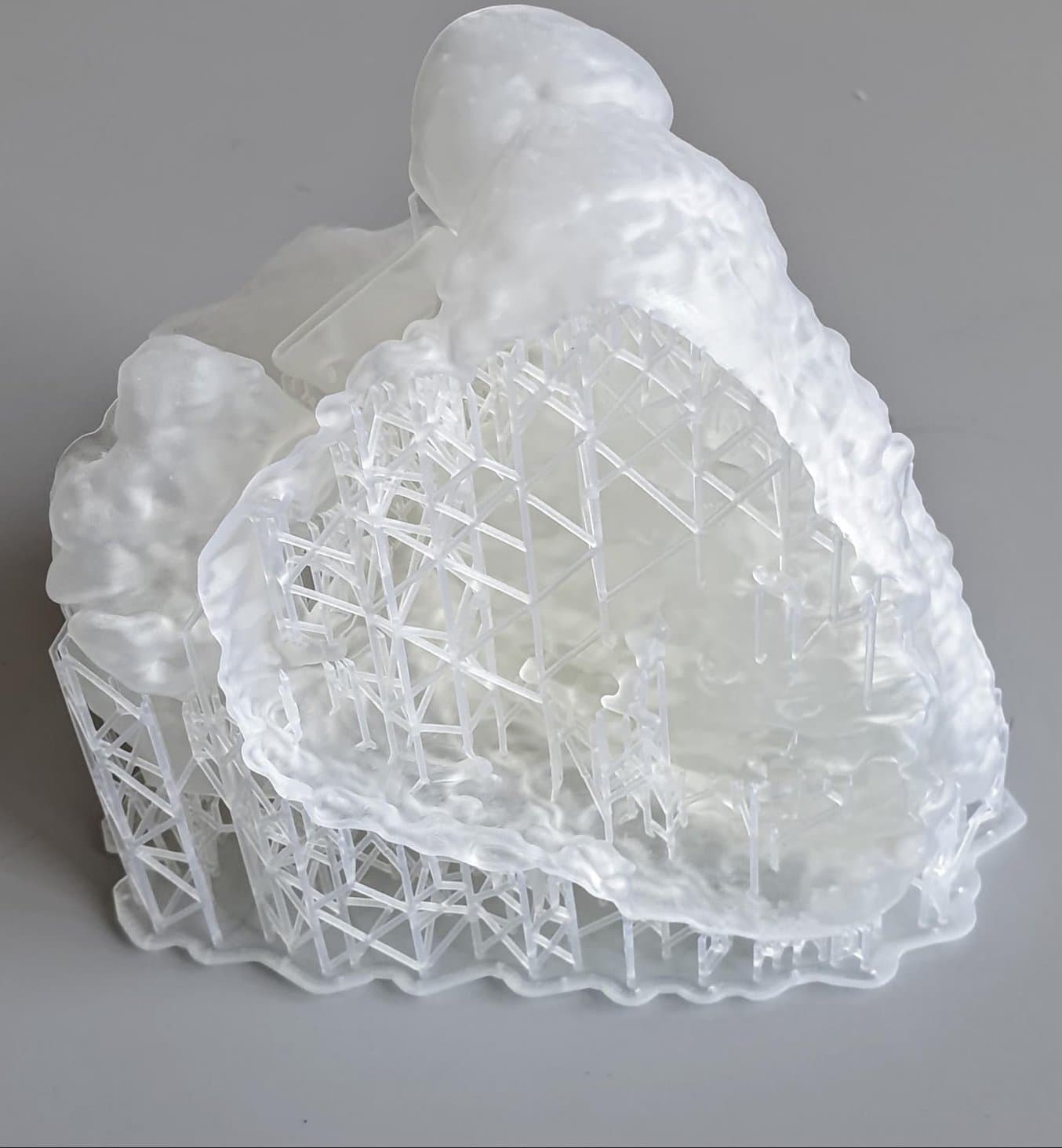
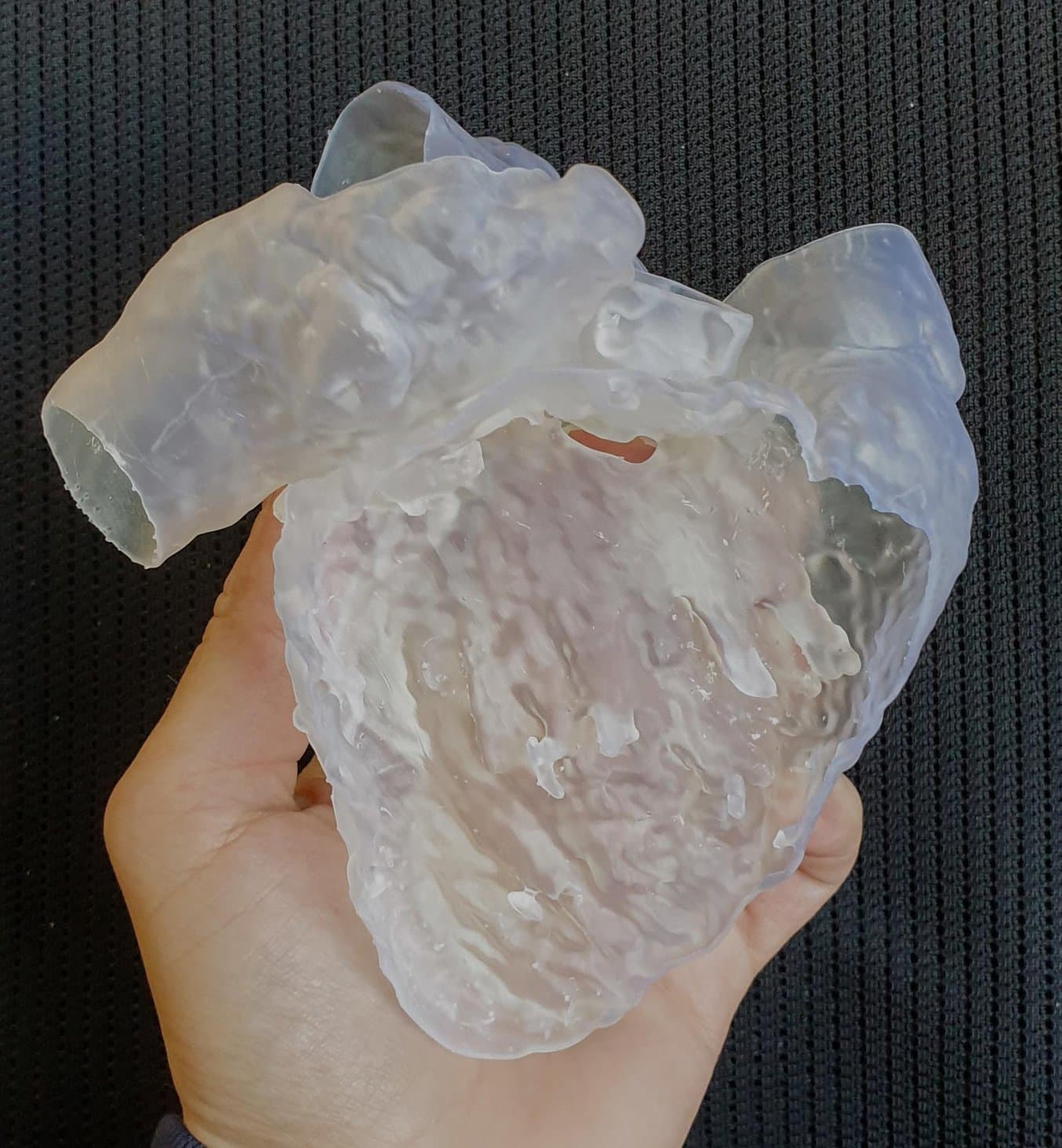
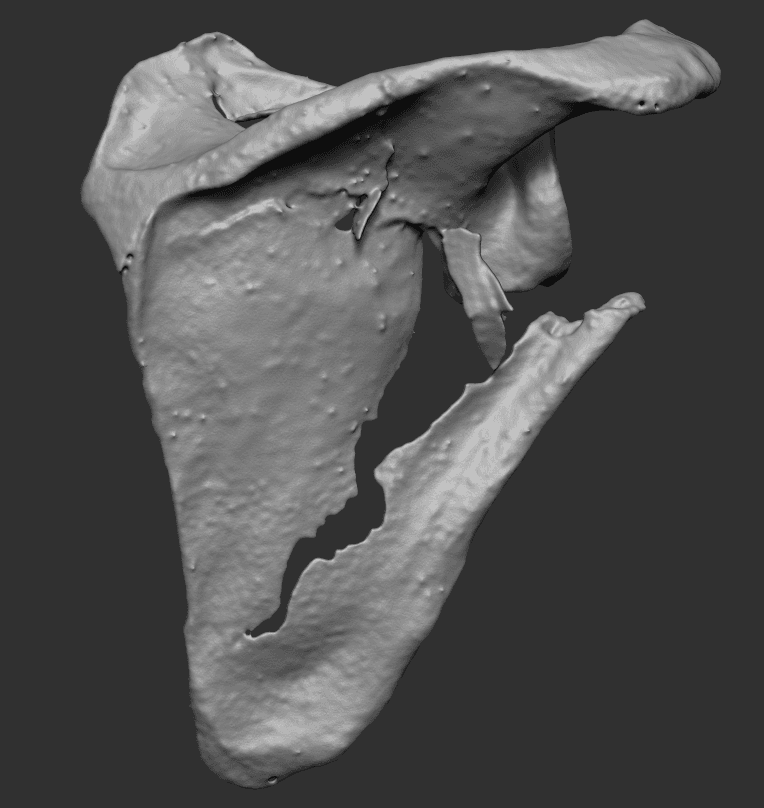
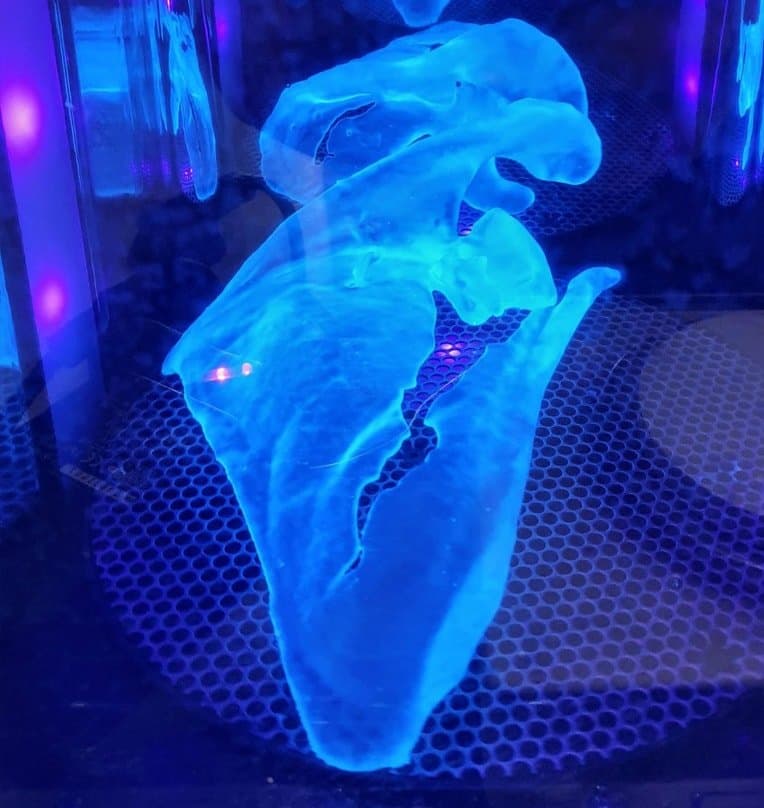
Modèle de cœur imprimé en 3D pour la préparation d'une opération, avec supports (en haut à gauche) et sans supports (en haut à droite). Modèle numérique 3D d'une scapula fracturée (en bas à gauche) et modèle imprimé en 3D en cours de post-polymérisation dans une Form Cure (en bas à droite).
« Mes tâches les plus délicates et les plus difficiles concernent les modèles de cardiologie pédiatrique. C'est un travail extrêmement complexe. Nous devons modéliser en 3D des cœurs minuscules pour aider les chirurgiens à vraiment les comprendre et à les visualiser. Certains utilisent des imprimantes 3D à projection de liant qui coûtent un quart de million de dollars. Mais nous utilisons les imprimantes 3D Formlabs, et les chirurgiens avec qui nous collaborons sont plus que satisfaits. C'est tout simplement incroyable », a déclaré M. De Rossi.
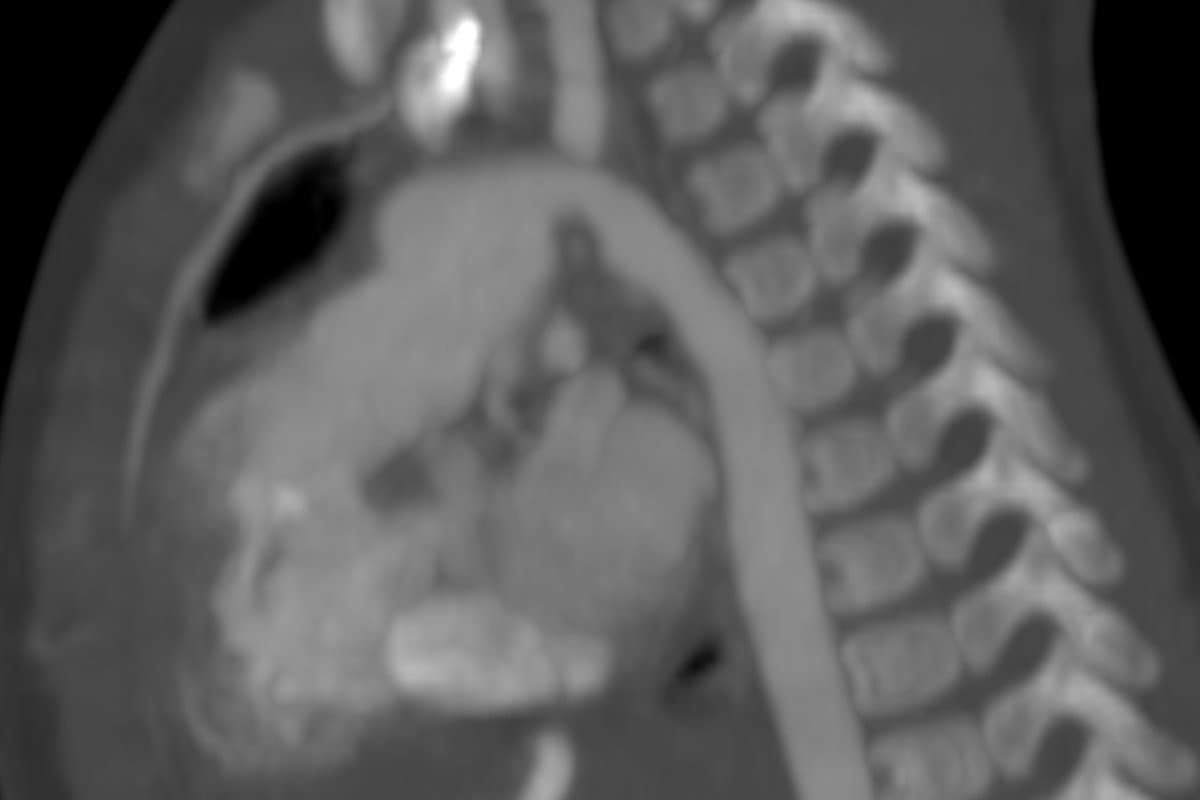
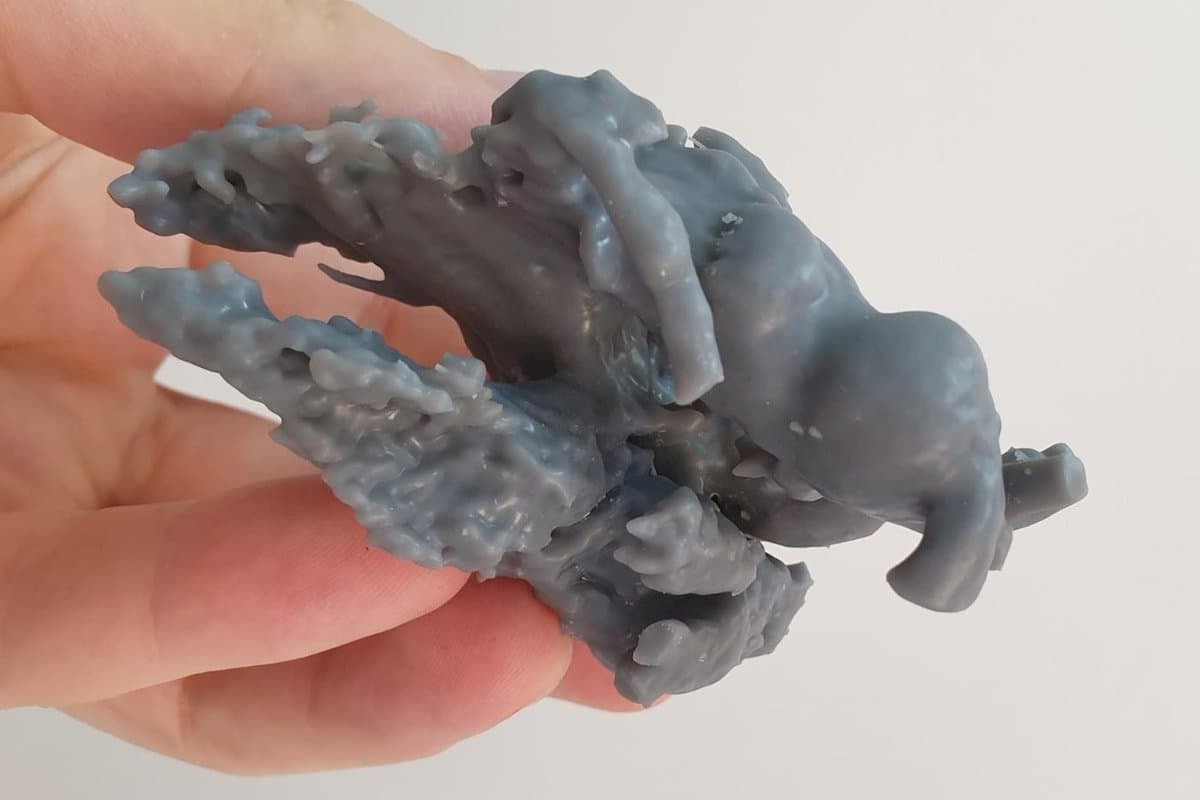
Vue traditionnelle d'un scan CT (à gauche) et d'un modèle de cavités cardiaques imprimé en 3D pour la planification d'une opération cardiaque pédiatrique (à droite).
M. De Rossi considère que le large choix de matériaux est l'un des principaux avantages de l'impression 3D SLA.
« Puisque vous pouvez imprimer presque toutes les formes, tout ce dont vous avez besoin, c'est de matériaux différents. C'est un gros avantage d'avoir une machine capable d'utiliser autant de matériaux différents. Surtout si vous ne savez pas sur quoi vous devrez travailler le lendemain matin. Ce sera peut-être un artiste qui voudra mouler une pièce, ou un ingénieur qui aura besoin d'une coque solide et résistante. Si vous disposez d'une machine capable d'utiliser d'autres matériaux, même ceux que vous n'utilisez pas pour le moment, c'est une garantie de la pérennité de votre investissement », a déclaré M. De Rossi.
C'est un gros avantage d'avoir une machine capable d'utiliser autant de matériaux différents.
Marco De Rossi
Intégrer la fabrication numérique dans le programme d'études
Après avoir obtenu son doctorat, M. De Rossi espère devenir professeur à l'université, créer son propre groupe de recherche et faire en sorte que de nouveaux doctorants poursuivent le travail qu'il a mené en laboratoire.
« Il vous faut quelqu'un de passionné qui veut vraiment apprendre. Je pense que ce rôle est fondamental dans un laboratoire d'impression 3D. Vous devez impérativement trouver quelqu'un qui s'impliquera pendant quelques années et qui transmettra ensuite son savoir à la génération suivante », a déclaré M. De Rossi.
« L'une des choses que j'aime à l'université, c'est que l'objectif n'est pas de former les étudiants à être les meilleurs dans une chose très spécifique, mais à être suffisamment bons dans de nombreux domaines pour pouvoir appréhender tous les projets qui se présentent à eux. Vous devez donner aux étudiants suffisamment d'outils pour les aider à devenir les meilleurs dans ce qu'ils font », a déclaré M. De Rossi.
« Vous devez avoir une méthode pour enseigner les compétences nécessaires à la fabrication numérique. Aujourd'hui, certaines universités disposent d'un laboratoire 3D ou proposent un cours. Mais je pense que cela ne fait pas encore partie intégrante [du programme d'études]. Il faut que tous les aspects d'une profession tournent autour de la fabrication numérique. C'est l'avenir. C'est le présent. Et si vous n'enseignez pas cela, alors vous êtes déjà presque obsolète », a déclaré M. De Rossi.