Comment Ford a développé le nouvel Explorer à l'aide des imprimantes 3D SLA et SLS de Formlabs
L’industrie automobile est en pleine transformation, car la demande des consommateurs et les exigences réglementaires la poussent à se départir des combustibles fossiles et à passer aux véhicules électriques. Ford est à l’avant-garde de ce mouvement, comme c’était le cas lorsqu’elle a produit le modèle T et introduit la chaîne de montage il y a plus de 100 ans.
Ford Motor Company est le sixième constructeur automobile mondial : elle produit plus de 4 millions de véhicules par an et emploie plus de 175 000 personnes dans le monde. Au cœur des opérations européennes de Ford se trouve Ford Cologne, fondée en 1930 et surtout connue pour l'assemblage de la Ford Fiesta.
À côté de l'usine se trouve le centre de développement de Cologne-Merkenich, où toutes les voitures particulières destinées au marché européen sont conçues de A à Z. Il s'agit notamment de modèles à succès comme la Fiesta, la Focus, la Kuga et maintenant l'Explorer, la première voiture électrique destinée au marché européen, qui a récemment été produite en série dans l'usine de montage de Cologne. L'équipe soutient également le développement de véhicules commerciaux, et collabore pour ce faire avec le Dunton Technical Centre de Ford au Royaume-Uni.
Mais comment Ford parvient-elle à faire face à une concurrence si acharnée et à des cycles de développement toujours plus courts ? Lisez la suite pour en savoir plus sur le centre de développement de Cologne-Merkenich, qui joue un rôle central dans la création de prototypes rapides pour le développement de produits.
Les outils pour produire des prototypes automobiles à grande échelle
« Le prototypage est très important dans le processus de développement. Il donne aux ingénieurs la possibilité de vérifier la conception. Si vous devez modifier votre outil de moulage par injection ou votre outil de production, cela vous revient très cher. Le processus est chronophage, et peut même dans certains cas causer l'arrêt de la production. Heureusement, le prototypage et l'exploitation de toutes les technologies disponibles permettent d'éviter cela », a déclaré Sandro Piroddi, superviseur du Rapid Technology Center de Ford.
La production de prototypes de véhicules à l'échelle réelle nécessite une large gamme d'outils. Le Rapid Technology Center est une vaste installation équipée des méthodes de fabrication les plus récentes : il dispose de ses propres machines de moulage par injection, d'outils de formage et d'une large gamme d'outils de fabrication soustractive, par exemple des fraiseuses capables d'usiner même les plus grandes pièces de châssis.
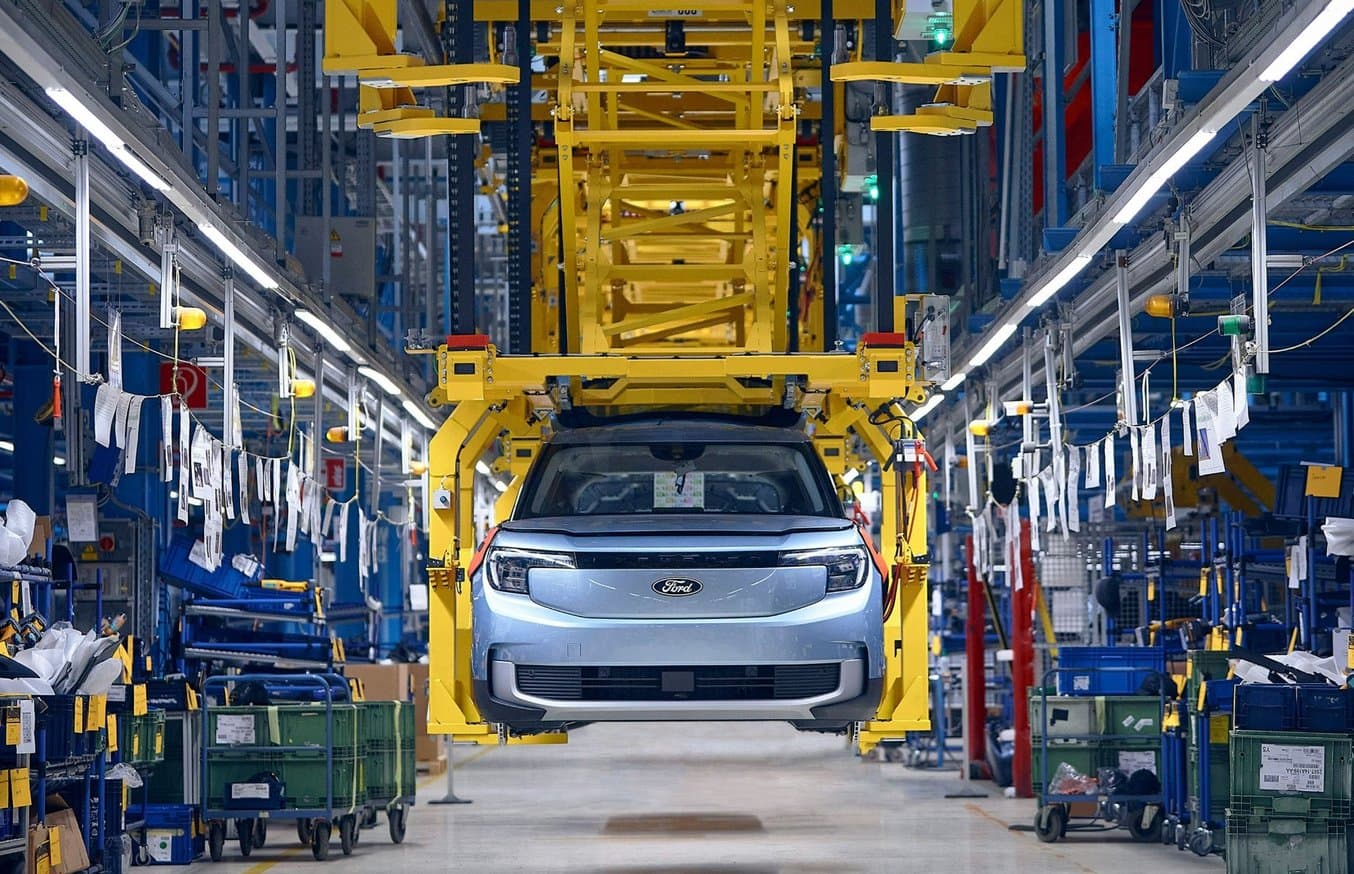
L'Explorer tout électrique est produit en série depuis peu dans l'usine de montage de Cologne.
Bien entendu, la liste ne serait pas exhaustive sans la fabrication additive. Le centre de développement de Cologne-Merkenich a été le premier atelier en Europe à utiliser une imprimante 3D stéréolithographique (SLA) en 1994 et a depuis élargi son parc avec des imprimantes 3D FDM (dépôt de fil fondu), SLA et SLS (frittage sélectif par laser), ainsi qu'à l'impression 3D métallique.
Si les premiers modèles conceptuels sont encore développés en argile, il devient de plus en plus important, à mesure que le développement du produit progresse et que les différents composants se rapprochent de la forme finale, de pouvoir tester aussi bien la forme que la fonction avec des matériaux et des procédés aussi proches que possible de la production.
« La fabrication additive est très importante dans le processus de développement. Elle vous permet de produire des pièces très rapidement, de manière très efficace, et de réduire les coûts. Vous avez également la possibilité de réagir à court terme. Vu l'évolution vers l'électrification, les délais de développement sont de plus en plus courts, ce qui signifie que le temps dont vous disposez pour développer des composants et vérifier des pièces de véhicules est de plus en plus réduit. Il est donc très important de disposer de cette technologie dans le processus de développement. Cela vous rend beaucoup plus compétitif par rapport à vos concurrents. »
Sandro Piroddi, superviseur du Rapid Technology Center, Ford
En raison de calendriers de développement de plus en plus serrés, le Rapid Technology Center est constamment à la recherche d'avancées dans le domaine de la fabrication additive qui lui permettraient d'accélérer la production des composants.
Développer des prototypes de conception avec l'impression 3D SLA
Les imprimantes 3D SLA sont principalement utilisées dans l'atelier pour les prototypes de conception qui nécessitent une bonne qualité de surface et doivent être produits rapidement pour des itérations rapides. La première imprimante Formlabs du centre de Cologne-Merkenich était une Form 2, mais la société a rapidement ajouté à son parc plusieurs unités de bureau et une imprimante 3D SLA grand format Form 3L. Plus récemment, elle a été l'une des premières entreprises à pouvoir tester la Form 4, la dernière imprimante 3D MSLA de Formlabs.
« La Form 4 est très rapide ; je pense que je n'ai jamais vu une vitesse d'impression comparable. Il s'agit d'une très bonne amélioration par rapport aux modèles précédents. Elle est plus facile à utiliser, et il est donc beaucoup plus facile pour les opérateurs de notre atelier d'apprendre à travailler avec la machine et d'obtenir des pièces de bonne qualité », a déclaré Bruno Alves, expert en fabrication additive et spécialiste de l'outillage chez Ford.
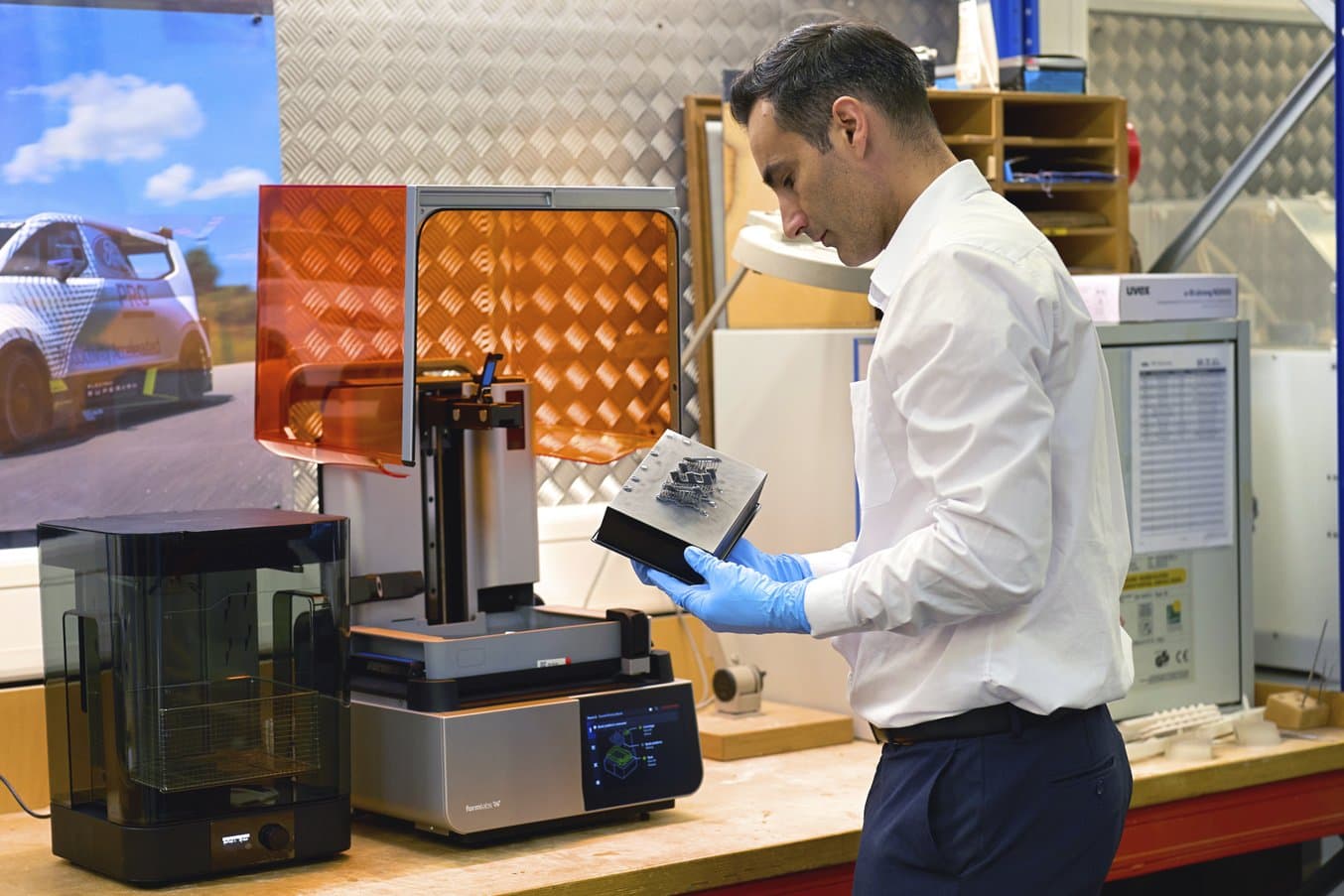
Le centre de Cologne-Merkenich a été l'un des bêta-testeurs de la nouvelle Form 4. La vitesse fulgurante de la nouvelle imprimante permettra à l'atelier de livrer de nouveaux prototypes en quelques heures seulement.
« La Form 4 change la donne. Sa vitesse va révolutionner notre façon de travailler. Nous pouvons produire plus de pièces, et notre rendement est bien plus élevé. Nous sommes beaucoup plus flexibles pour les commandes de dernière minute. Désormais, nous pouvons les honorer sans problème grâce à la Form 4. »
Sandro Piroddi, superviseur du Rapid Technology Center, Ford
« Il y a quelques années, cela nous demandait des journées entières ; aujourd'hui, nous imprimons des pièces en quelques minutes. Les ingénieurs n'ont donc pas peur de faire de nouvelles conceptions et de nouvelles itérations, parce qu'ils savent maintenant qu'ils obtiendront les pièces très rapidement », a ajouté M. Alves.
La rapidité d'impression permet désormais à l'équipe RTC de répondre à un plus grand nombre de demandes en moins de 24 heures ; même celles provenant du Royaume-Uni, où les pièces sont rapidement expédiées pendant la nuit.
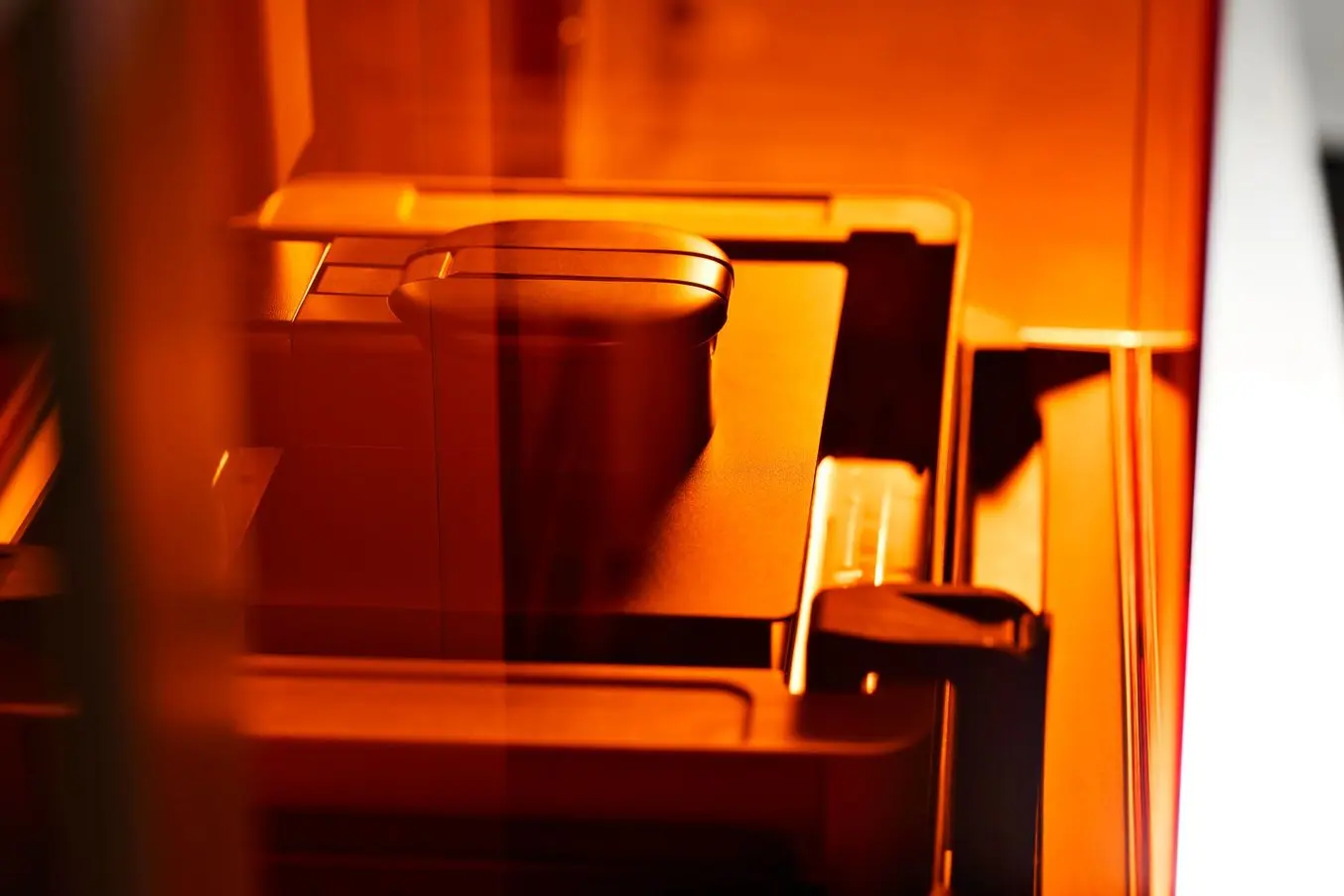
Démonstration produit : Form 4
Découvrez comment la Form 4 établit de nouvelles normes de productivité et d’innovation grâce à une rapidité, une précision et une fiabilité inégalées.
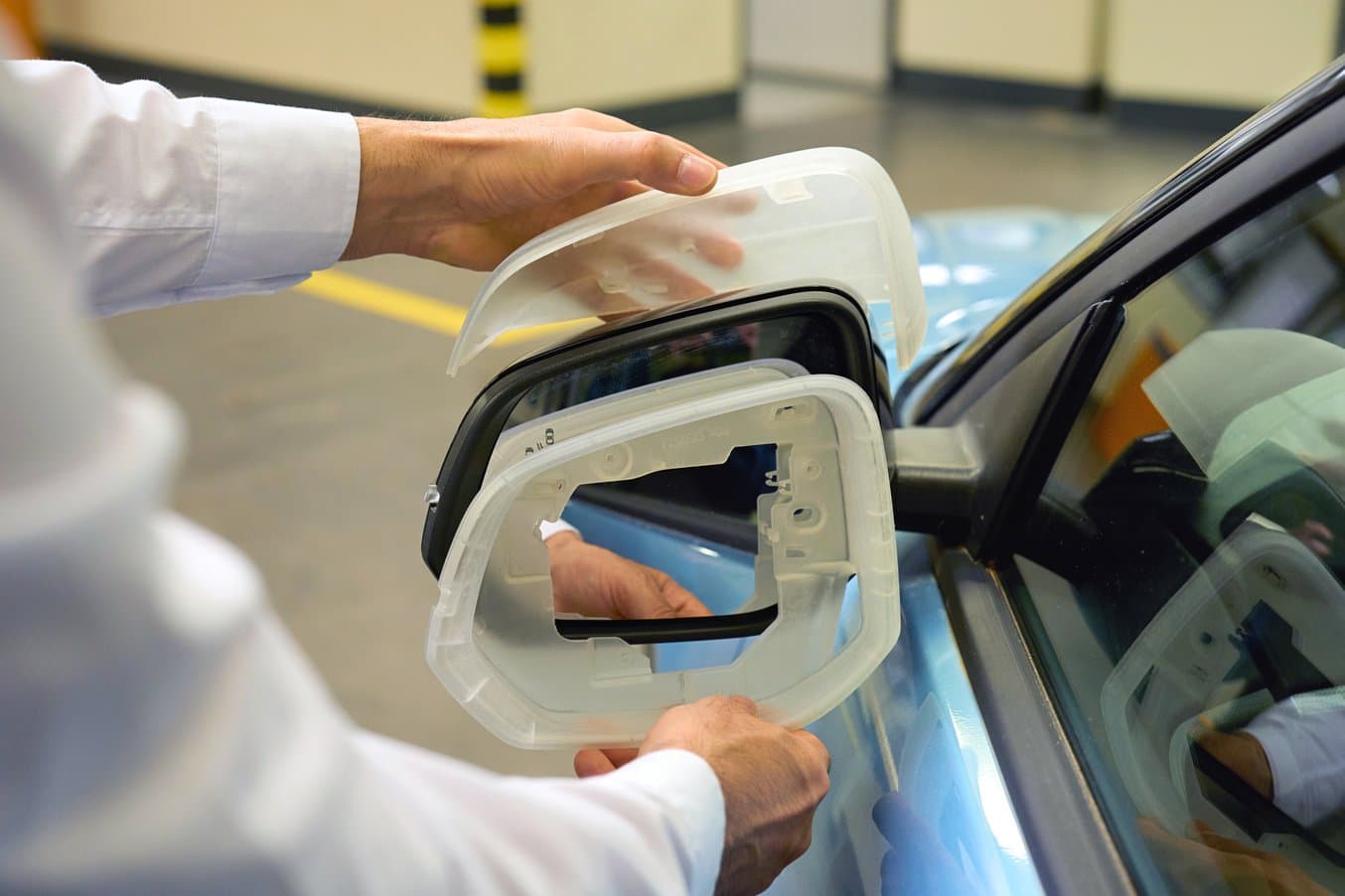
L'équipe a utilisé l'impression 3D SLA pour prototyper de nombreuses pièces du nouvel Explorer, comme l'assemblage des rétroviseurs.
Pour le nouvel Explorer, l'équipe a eu recours à l'impression 3D SLA pour valider la conception de nombreuses pièces extérieures et intérieures.
« La Form 3L nous permet d'imprimer des pièces de grande taille, par exemple des pièces extérieures de la carrosserie du véhicule. Nous avons imprimé cette coque de rétroviseur pour valider une conception. L'impression 3D est parfaite pour cela, car elle est rapide et nous permet d'obtenir une très bonne qualité par rapport aux pièces produites en masse », explique M. Alves.
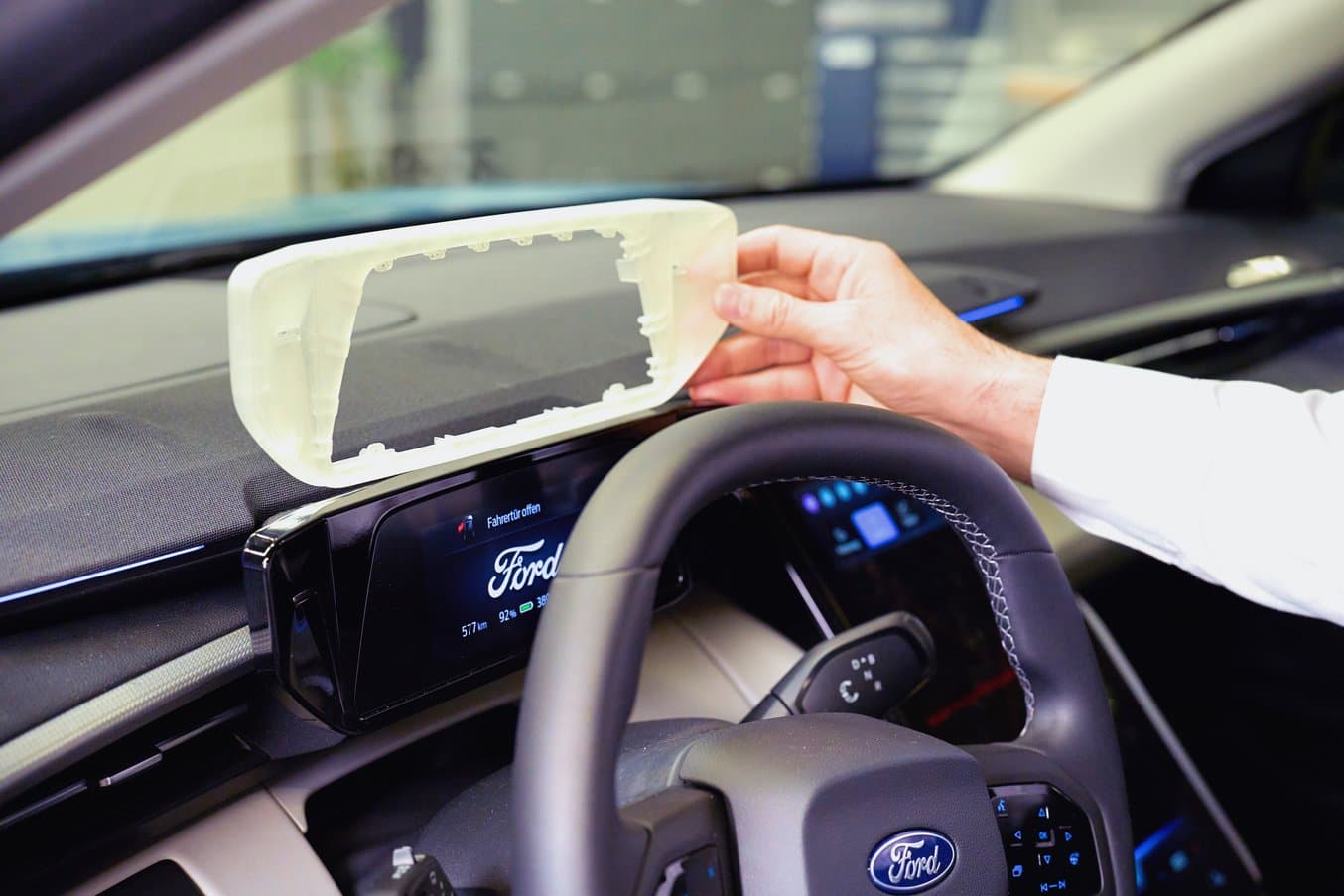
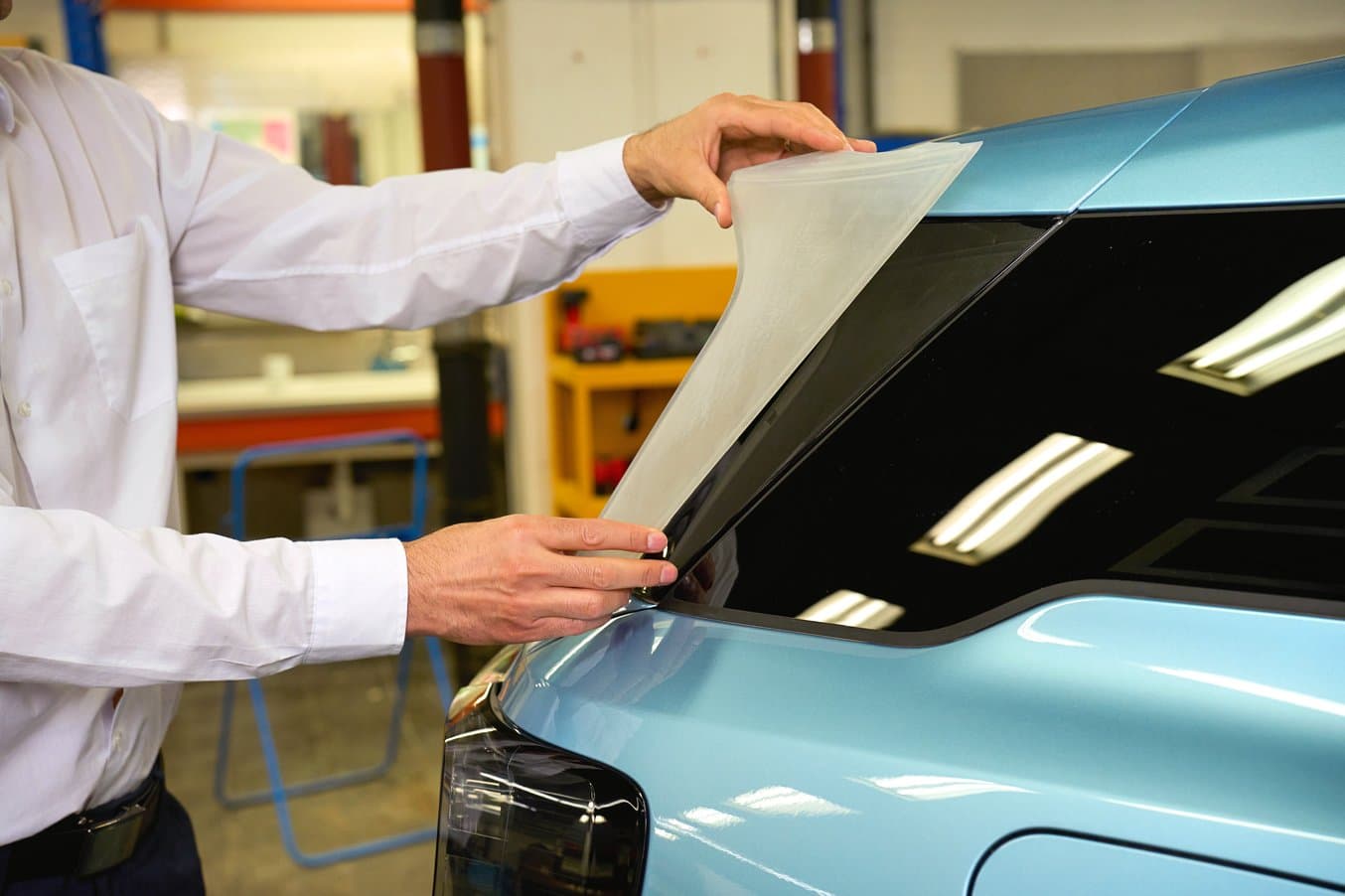
Le grand volume d'impression de la Form 3L permet à l'équipe de produire des prototypes de grande taille en une seule pièce.
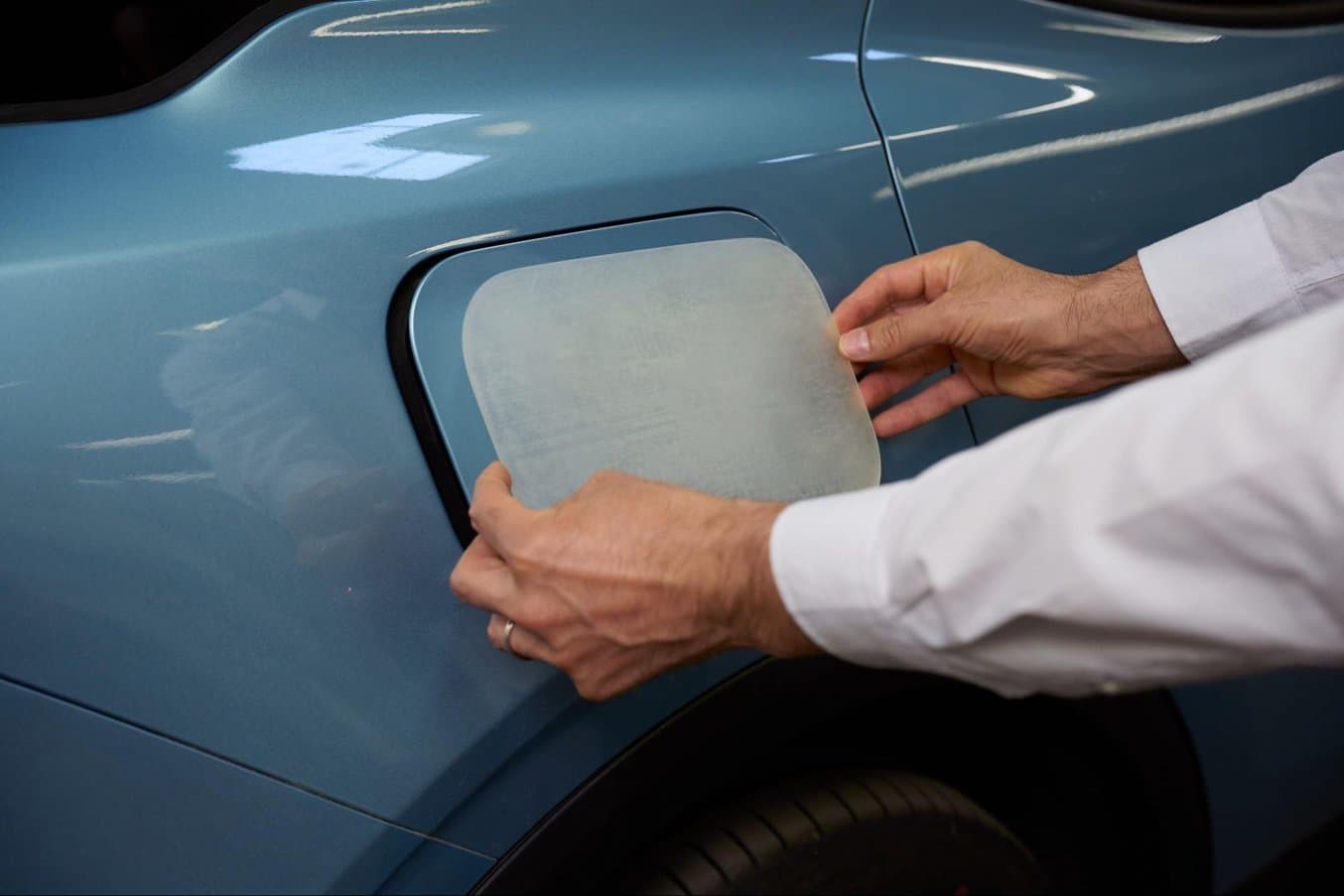
Ces pièces ont été imprimées en Clear Resin et sablées avec la Fuse Blast.
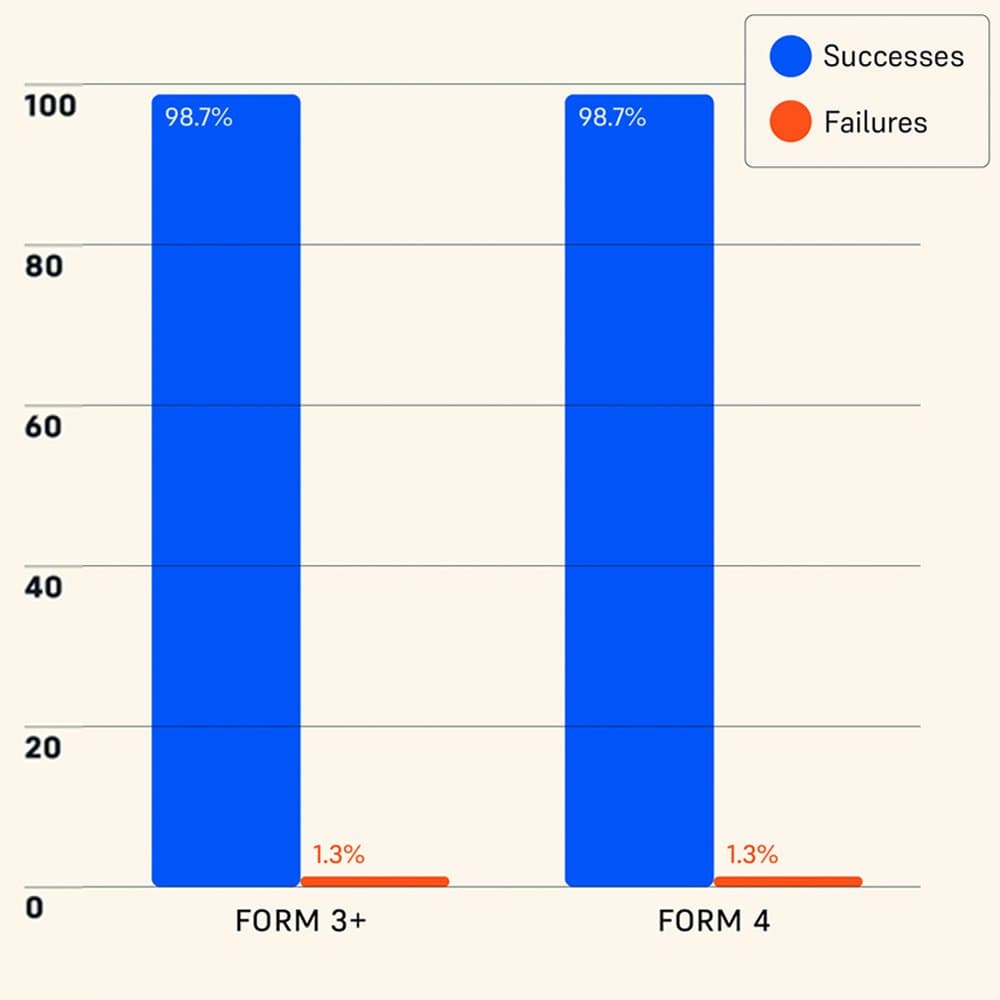
Fiabilité de la Form 4 et d’autres imprimantes 3D résine testée de manière indépendante
Une importante société indépendante de test de produits a mesuré un taux de réussite d’impression de 98,7 % pour la Form 4 de Formlabs. Lisez une description complète de la méthodologie d’essai et consultez les résultats dans notre livre blanc.
Tester des pièces mécaniques avec l'impression 3D SLS
L'atelier dispose également d'un grand nombre d'imprimantes 3D SLS utilisées pour tester des pièces mécaniques.
« Nous essayons toujours de tester et de valider des matériaux semblables à ceux utilisés dans la production de masse. La Fuse 1+ 30W imprime avec du PA-12[ ]nylon, qui ressemble beaucoup aux pièces moulées par injection produites en masse », a déclaré M. Alves.
Bien que l'équipe dispose également d'imprimantes 3D SLS grand format en interne capables d'imprimer de grands panneaux de carrosserie, elle préfère utiliser la Fuse 1+ 30W pour toutes les pièces qui peuvent entrer dans son volume d'impression.
« La Fuse 1+ est beaucoup plus rapide que ses concurrentes. L'utilisation de la machine est également très simple pour nos collaborateurs. En fin de compte, ce qui compte vraiment pour nous, c'est qu'il est très facile de livrer les pièces plus rapidement. »
Bruno Alves, expert en fabrication additive et spécialiste de l'outillage, Ford
L'équipe a également été l'un des bêta-testeurs de la solution automatisée de nettoyage et de polissage Fuse Blast, qui vient compléter le flux de travail SLS et simplifie le post-traitement.
« La Fuse Blast accélère considérablement notre processus car l'opérateur n'a plus besoin de nettoyer les pièces manuellement. Il suffit de les placer dans la boîte et de démarrer la machine. Auparavant, ils le faisaient manuellement et cela prenait beaucoup de temps. Pendant ce temps, les opérateurs peuvent faire d'autres choses et nous accélérons le processus », a déclaré M. Alves.
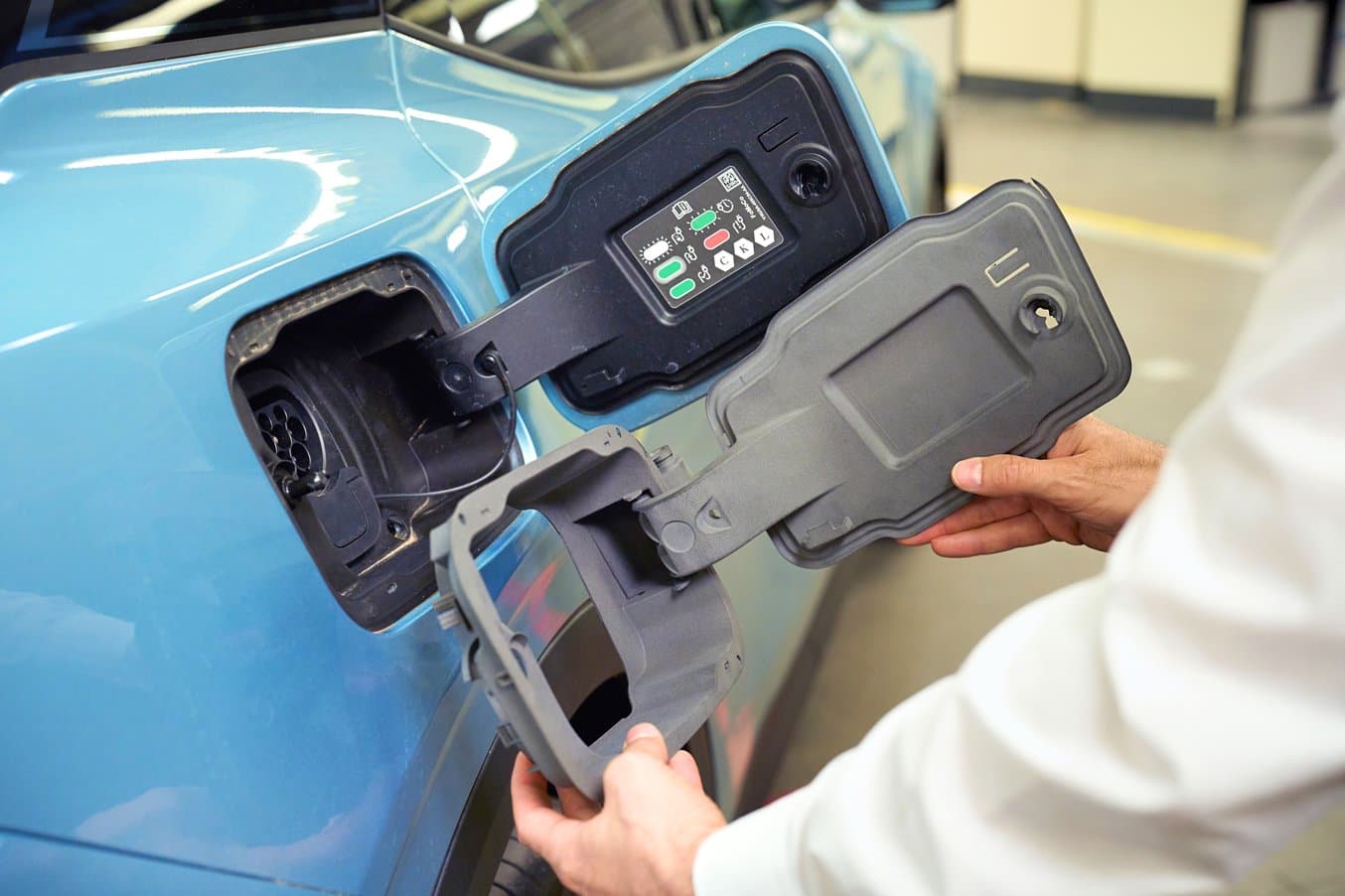
Le port de charge est un assemblage complexe qu'il aurait été impossible de prototyper avec une autre méthode.
La nature autoportante de l'impression 3D SLS facilite la production de modèles complexes. Pour le nouvel Explorer, l'équipe a utilisé la Fuse 1+ 30W afin de produire diverses pièces et assemblages mécaniques.
« Pour ce couvercle de chargement, le SLS était indispensable, car nous avions besoin d'une pièce fonctionnelle qui nous permet de tester les mécanismes. Il s'agit d'une conception très complexe que nous ne pourrions pas produire autrement. L'usinage de ce genre de pièce est impossible. Le moulage par injection ne peut pas non plus être utilisé pour seulement quelques échantillons. Le meilleur moyen est donc d'imprimer avec un matériau que nous pouvons tester physiquement », a déclaré M. Alves.
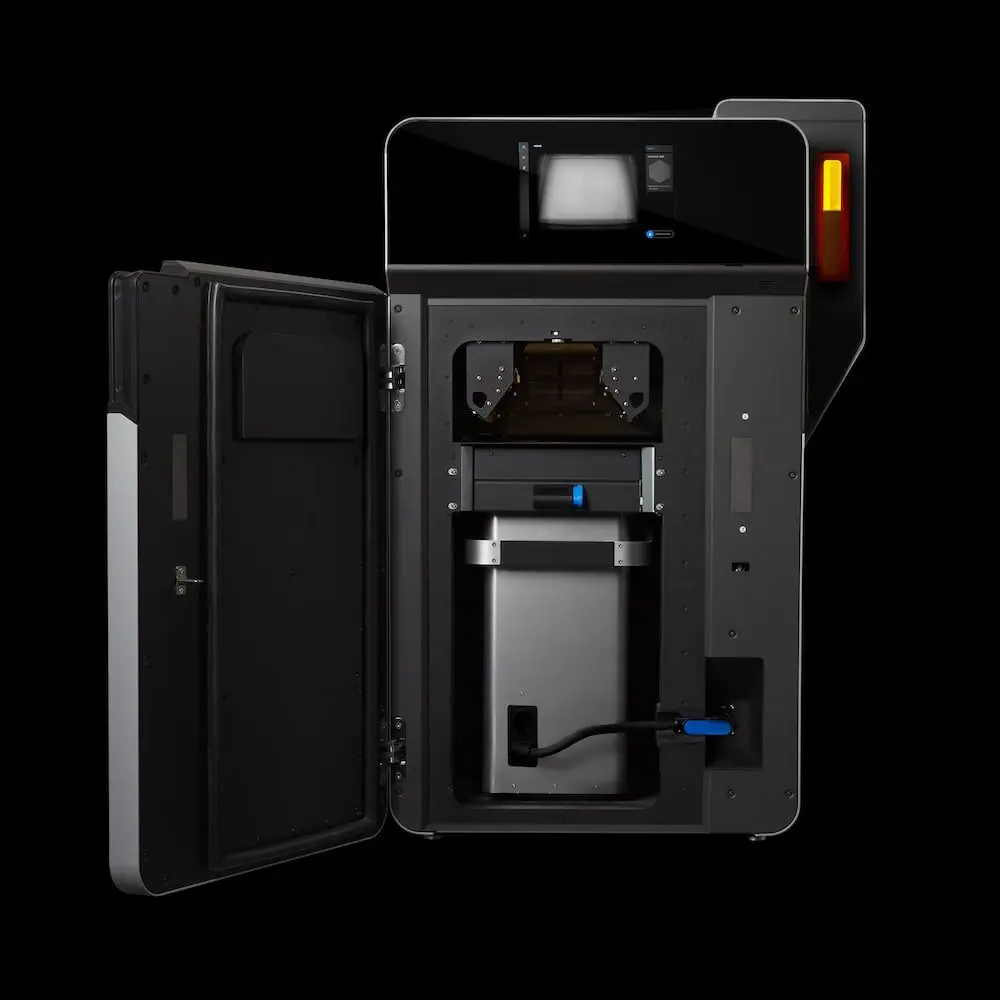
Produire rapidement des pièces SLS haute performance avec la nouvelle Fuse 1+ 30W
Regardez une démonstration détaillée de la Fuse 1 et de l’impression 3D SLS, réalisée par les experts Formlabs.
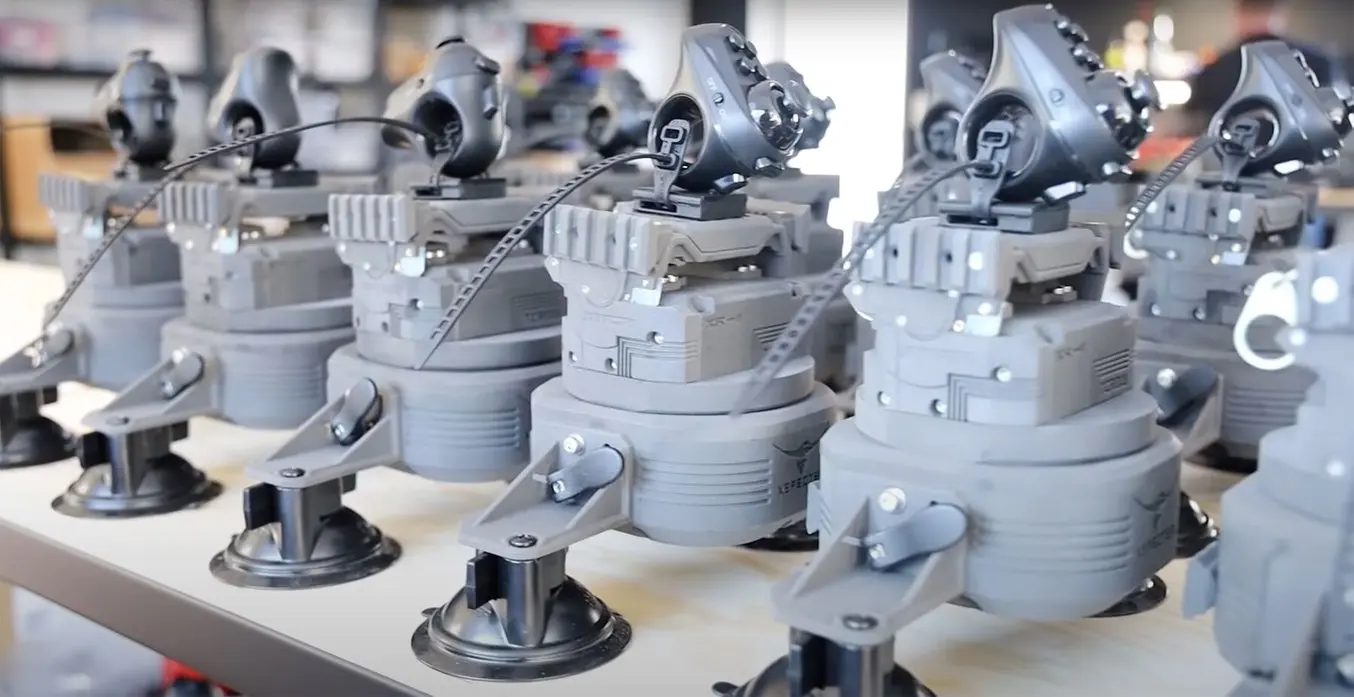
Le SLS pour la production finale
L'impression 3D pour la production finale n'est pas seulement accessible : elle est aussi plus abordable, plus agile et plus évolutive que jamais grâce à l'écosystème SLS Fuse. Explorez notre page dédiée à la production SLS pour comparer les différentes méthodes de fabrication, consulter les tarifs des poudres en vrac et découvrir comment 15 fabricants exploitent actuellement les imprimantes de la série Fuse.
Moulage par injection en interne avec des inserts de moules imprimés en 3D
Le fait de disposer de diverses technologies en interne permet également au Rapid Technology Center de créer des flux de travail hybrides, par exemple en combinant des processus de fabrication traditionnels avec de l'outillage rapide imprimé en 3D.
En fonction de l'application envisagée, l'équipe peut sélectionner le processus de production et le matériau les plus appropriés, afin d'optimiser le coût, la vitesse et l'efficacité globale du flux de travail. Pour les crash-tests, par exemple, les composants doivent être fabriqués dans le même matériau et selon le même procédé que ceux utilisés pour la production de masse. Pour les composants en plastique, il s'agit généralement du moulage par injection, un processus qui nécessite un outillage métallique coûteux et fastidieux.
« Nous voyons un grand potentiel dans l'utilisation d'inserts imprimés en 3D pour le moulage par injection, car nous pouvons itérer la conception très rapidement. Nous imprimons les cavités, que nous remplaçons ensuite dans l'outil pour injecter les pièces », explique M. Alves.
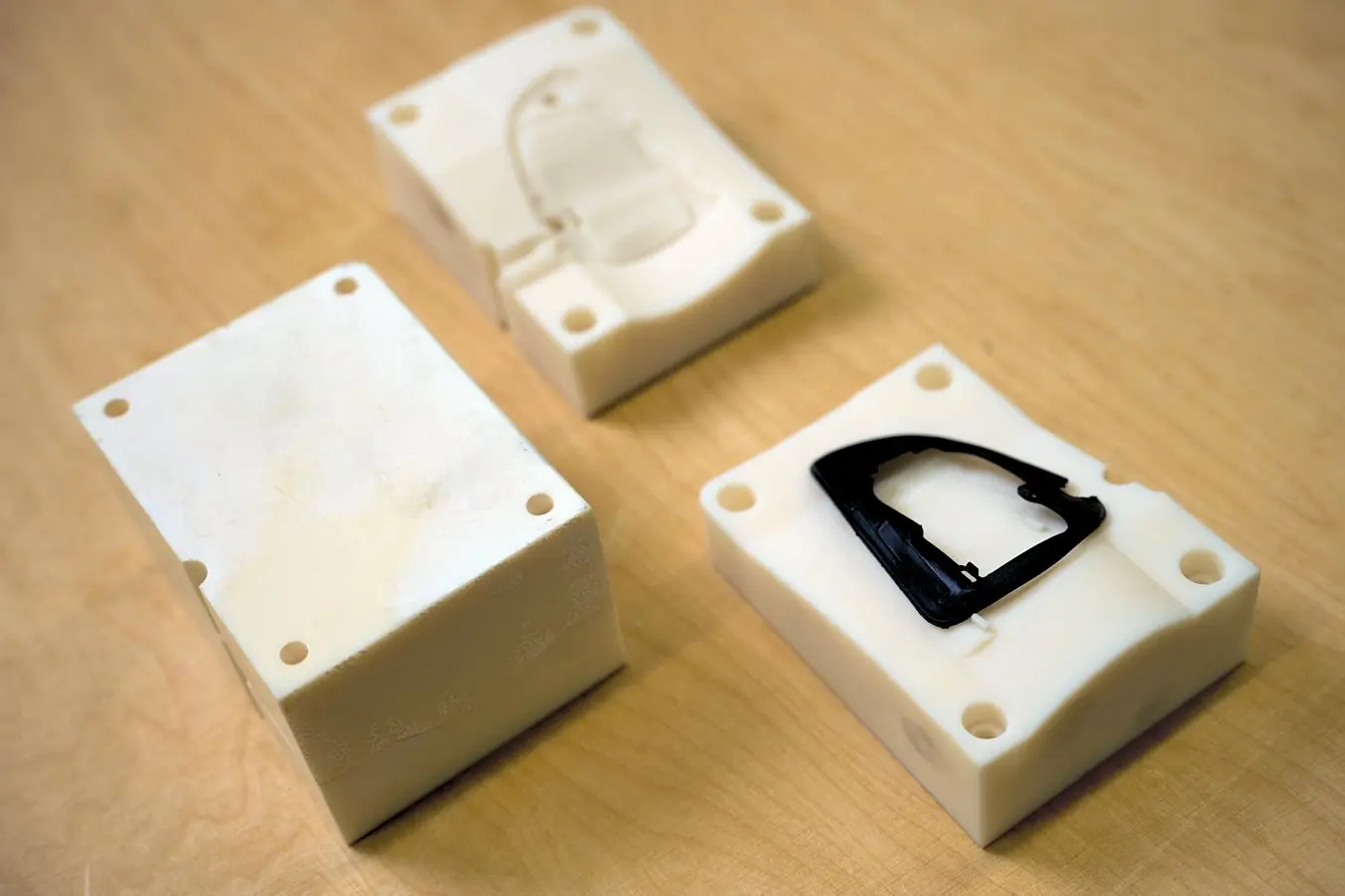
Les membres de l'équipe ont produit les inserts de moulage par injection en Rigid 10K Resin avec des imprimantes SLA.
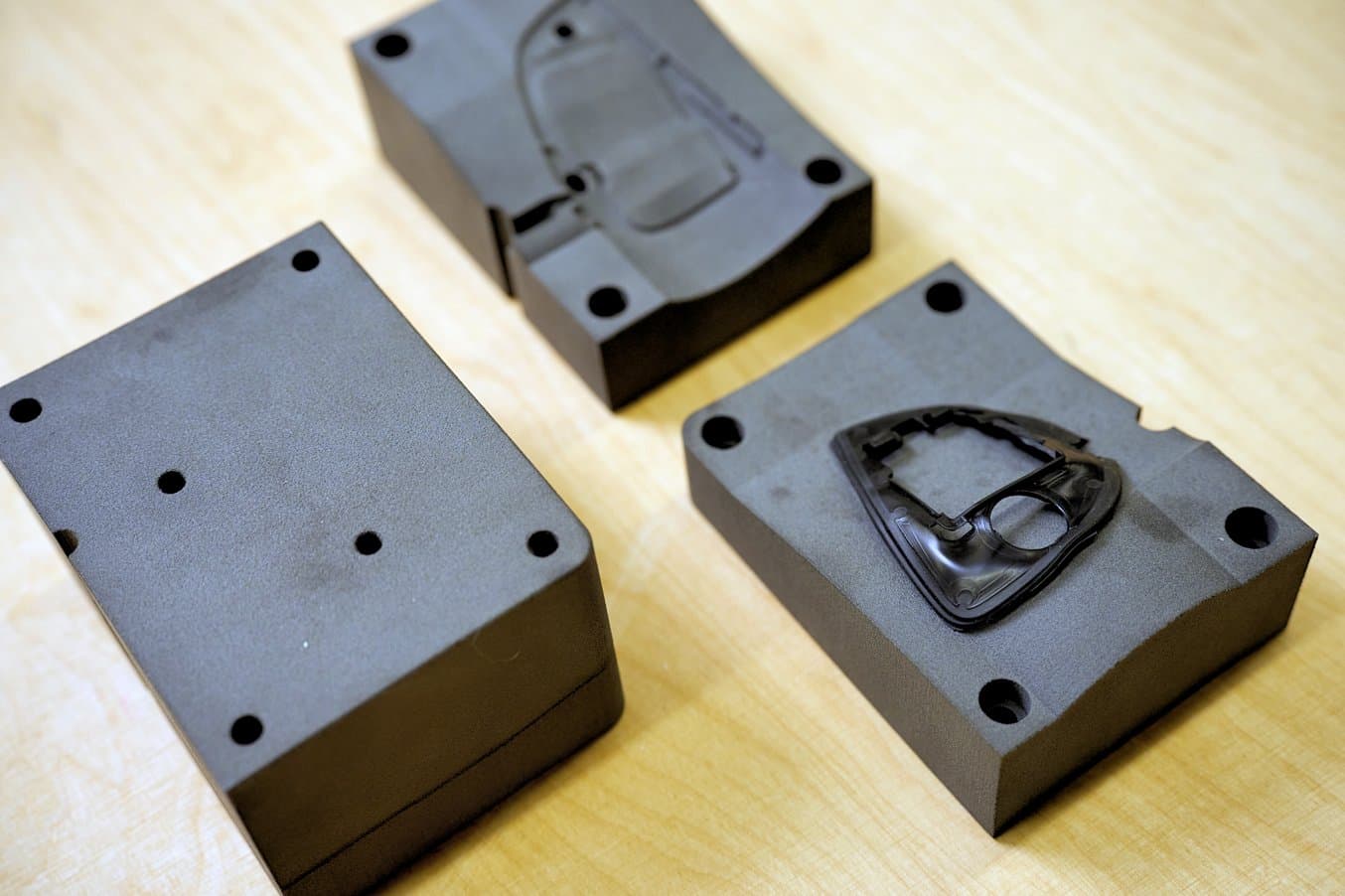
Ils utilisent de la Nylon 12 Powder sur des imprimantes SLS pour la même application.
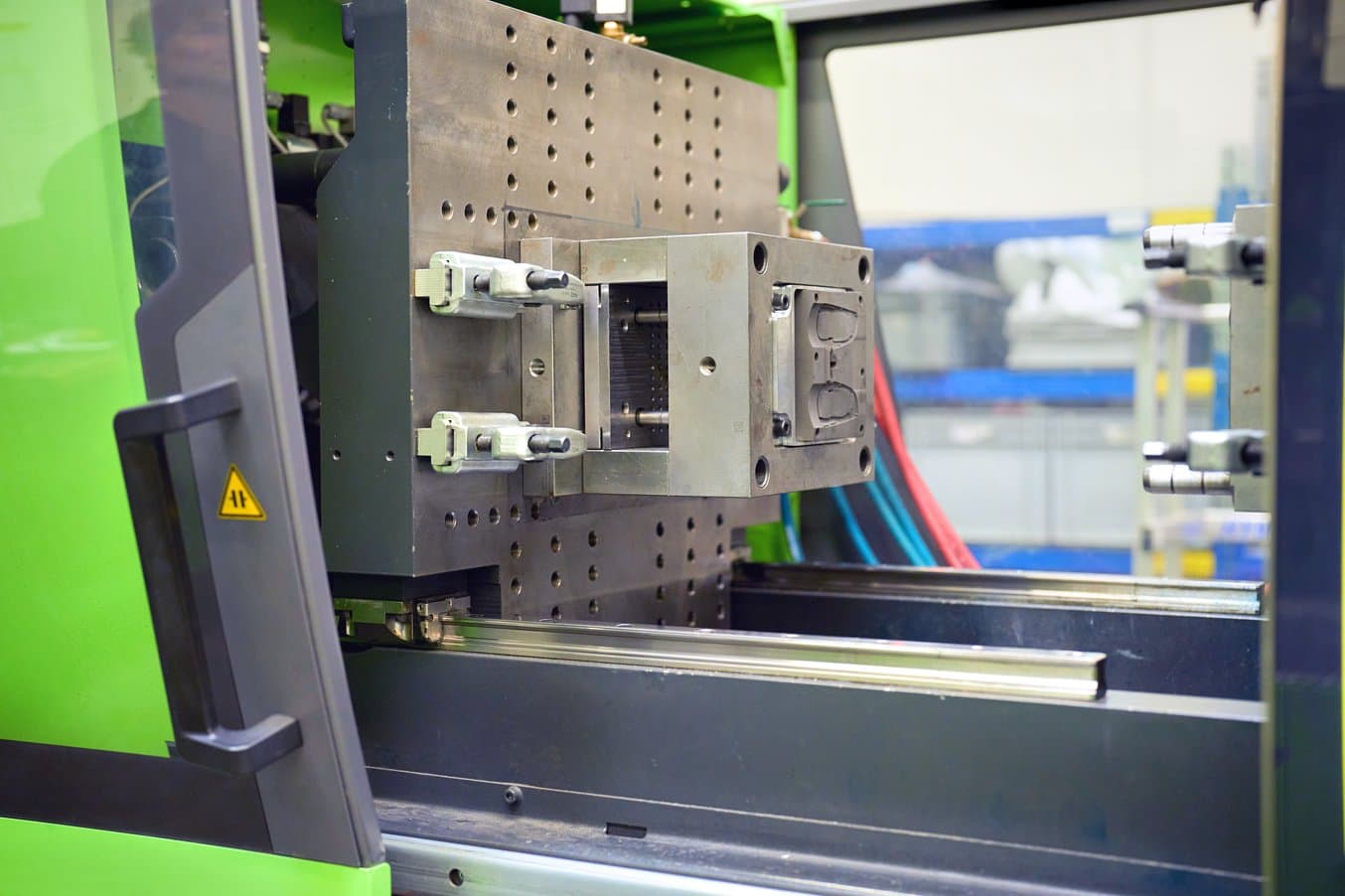
L'impression 3D permet à l'équipe de produire très rapidement des inserts de moules pour différentes conceptions et itérations rapides avec la machine de moulage par injection industrielle de l'entreprise.
Pour le nouvel Explorer, l'équipe a produit des composants en caoutchouc pour l'assemblage de la poignée de porte en utilisant des inserts de moule imprimés en 3D dans leur machine de moulage par injection.
« Il s'agissait d'un processus complexe, car nous utilisons plusieurs inserts et il y a également plusieurs conceptions différentes qui pourraient avoir plusieurs itérations chacune. Généralement, le moulage par injection externe prend deux ou trois mois. En interne, grâce à la fabrication additive, nous pouvons accélérer le processus jusqu'à deux ou trois semaines maximum. Pour ce projet, si nous avions dû utiliser des outils externes, cela aurait pris beaucoup plus de temps et nous n'aurions pas pu livrer les pièces à temps », a déclaré M. Alves.
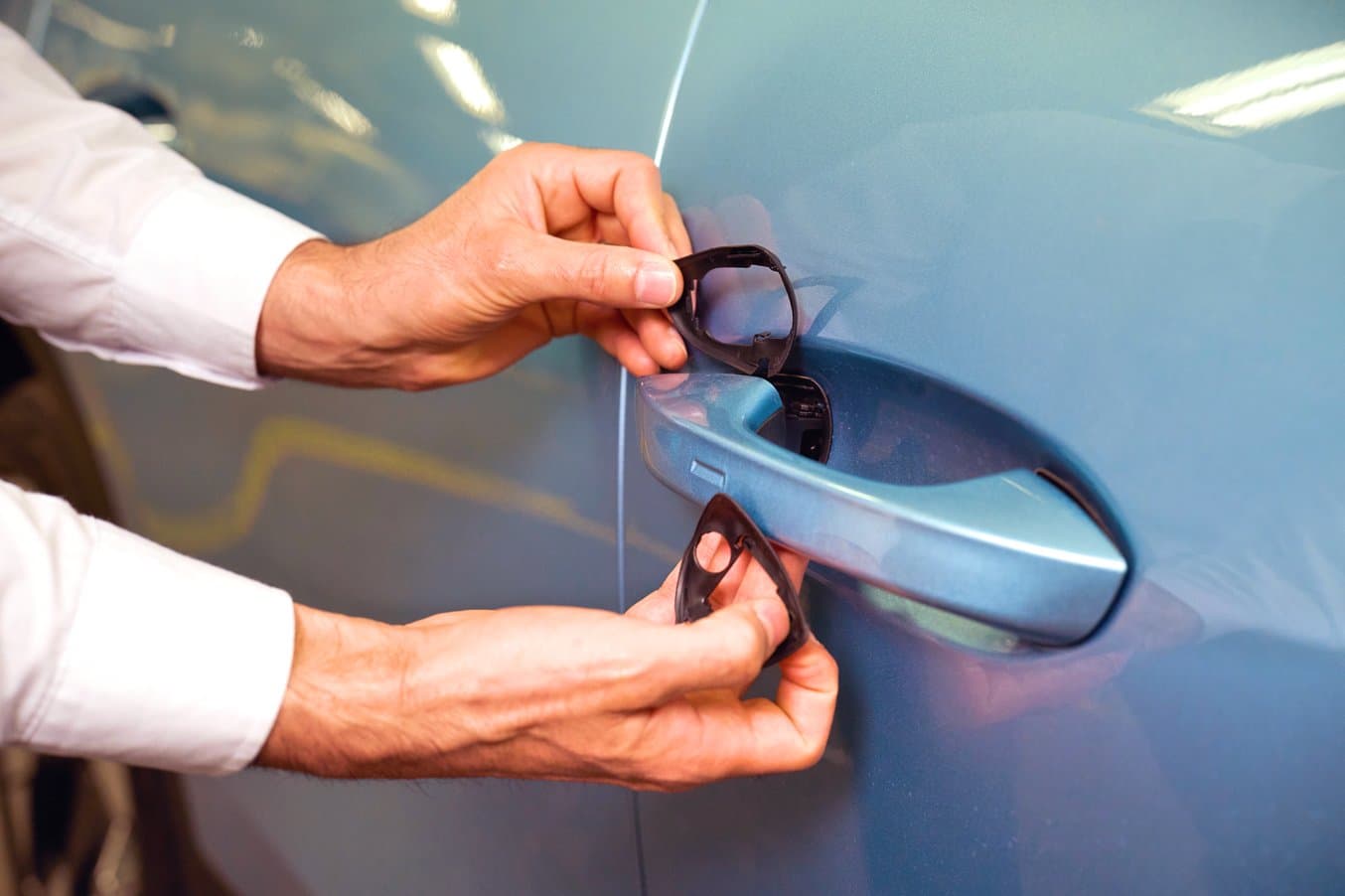
Chaque poignée de porte comprend deux de ces éléments en caoutchouc pour l'amortissement et l'isolation. Pour les SUV à quatre portes, cela signifie huit composants uniques pour chaque itération de conception.
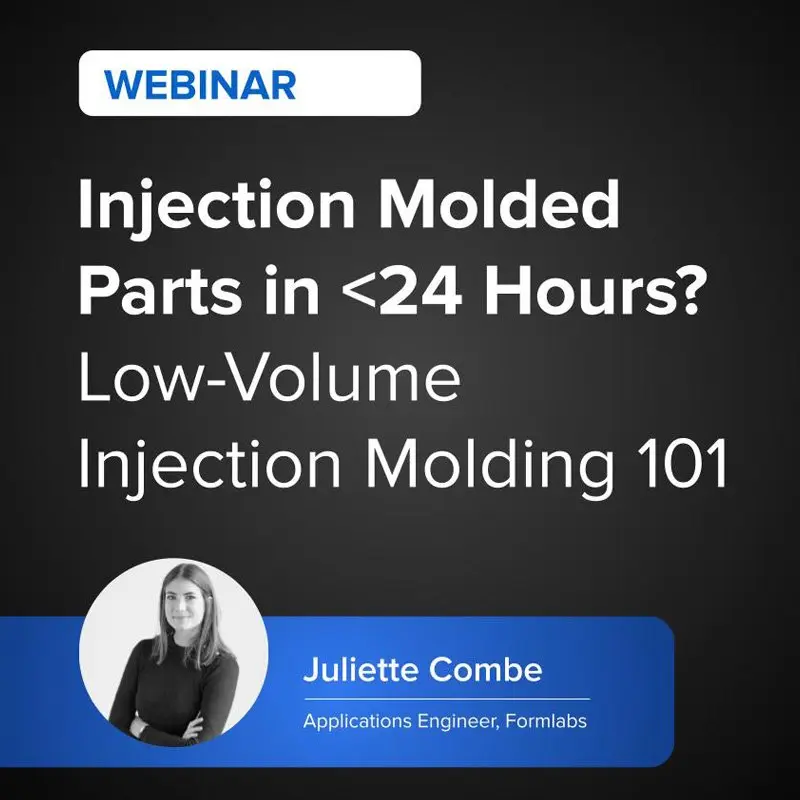
Des pièces moulées par injection en moins de 24 heures ? Le b.a.-ba du moulage par injection en petite série
Dans ce webinaire, nous vous montrerons comment des moules imprimés en 3D par stéréolithographie (SLA) peuvent être utilisés dans le processus de moulage par injection afin de réduire les coûts et les délais de fabrication et de lancer des produits plus qualitatifs sur le marché.
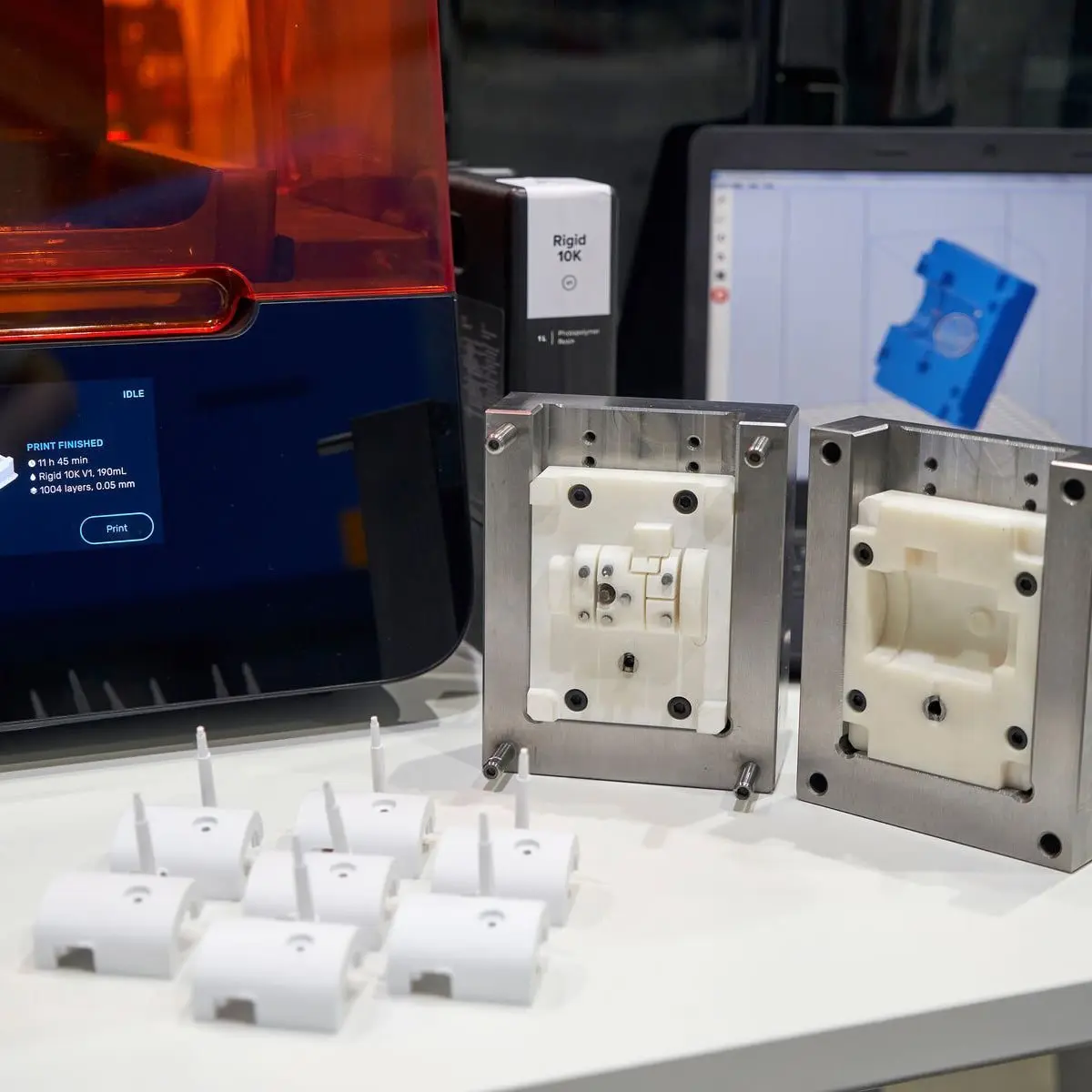
Le moulage par injection rapide de petites séries avec des moules imprimés en 3D
Téléchargez ce livre blanc pour savoir comment utiliser des moules imprimés en 3D pour le processus de moulage par injection, et ainsi réduire les coûts et les délais de production. Vous y trouverez des études de cas réels, réalisées chez Braskem, Holimaker et Novus Applications.
Progresser à pas de géant vers l'électrification
La volonté de Ford de convertir toute sa gamme de produits à l'électricité d'ici 2030 impose un calendrier ambitieux au centre de développement de Cologne-Merkenich. Pour suivre la cadence, l'entreprise devra continuer à trouver des technologies de pointe et à essayer de nouveaux flux de travail innovants. Pour rester compétitive, l'entreprise doit repousser les limites et intégrer de nouveaux matériaux, processus et machines, comme l'outillage interne et l'impression 3D.
« Nos concurrents accélèrent leur processus de développement. Nous ne pouvons pas nous laisser dépasser. La solution consiste donc à tester de nouveaux matériaux, de nouveaux procédés et de nouvelles machines qui arrivent sur le marché. Si nous n'avions pas accès à la fabrication additive, nous ne pourrions pas rivaliser avec la concurrence et nous ne serions pas assez rapides. L'impression 3D nous permet de développer le meilleur produit pour nos clients en moins de temps », a déclaré M. Alves.