Galvanoplastie de pièces imprimées en 3D pour des antennes haute performance
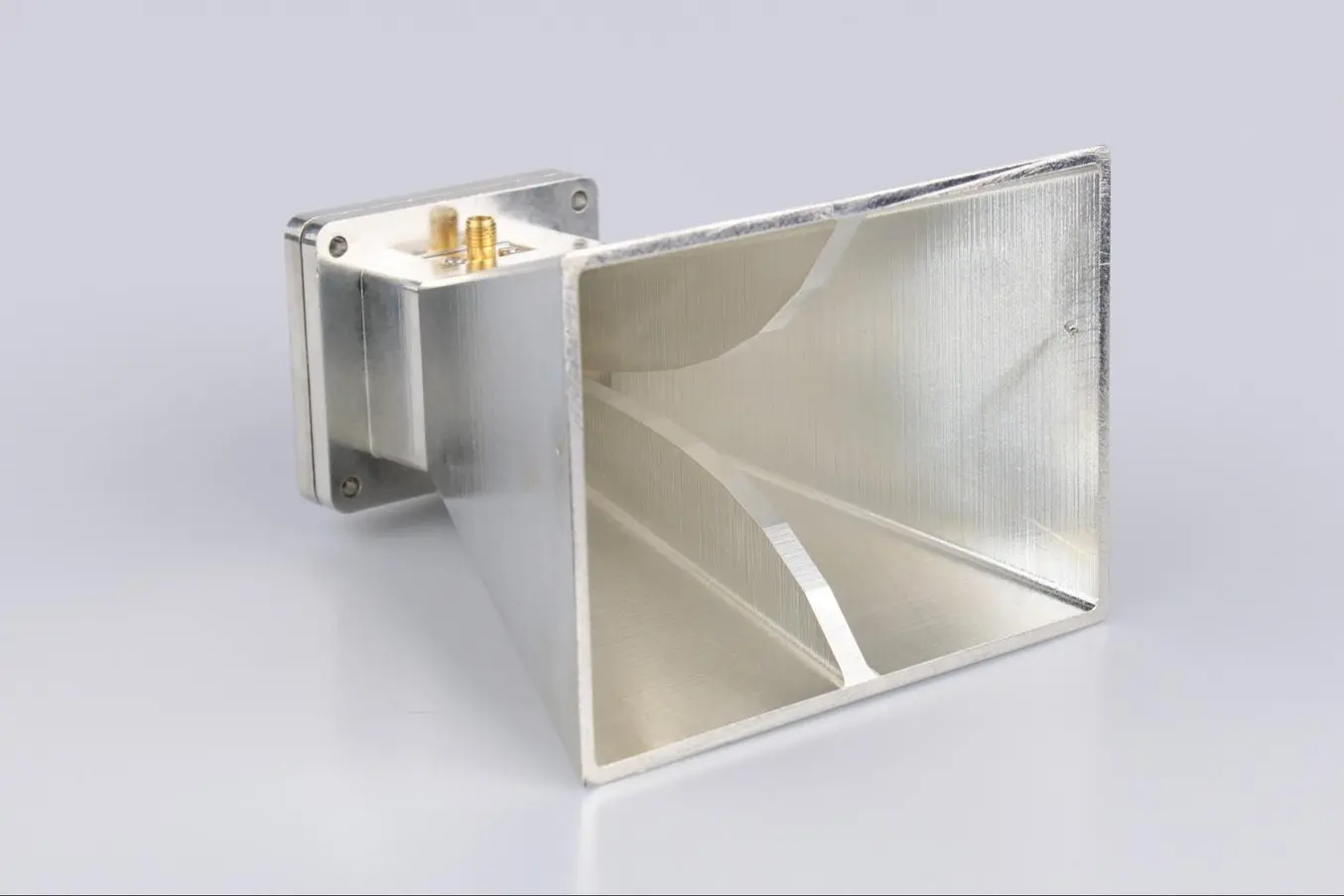
Basée à Brest, en France, l’entreprise Elliptika s’est spécialisée dans la conception et le développement de produits et de solutions RF et microondes. Elle conçoit des filtres et des antennes de pointe et sur mesure, utilisées pour la recherche et le développement dans les secteurs de l’automobile, de la défense, de la médecine et de l’éducation, par des sociétés comme Thales.
Pour que ses antennes satisfassent aux conditions exigeantes au niveau du gain ou de la compacité, tout en gardant de bas coûts et en fournissant les modèles rapidement, l’entreprise a dû dépasser les limitations imposées par les techniques de fabrication traditionnelles.
Cet article explique comment Gwendal Cochet et Alexandre Manchec, concepteurs radio fréquence chez Elliptika utilisent l’impression 3D et la galvanoplastie pour fabriquer des antennes très performantes et réduire coûts et délais de production de plus de 90 %.
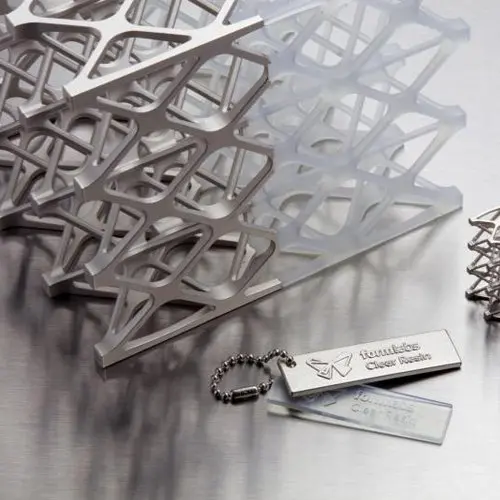
Au plus près de l’impression 3D métallique avec une imprimante à 3500 $
Dans ce webinaire, découvrez comment la galvanoplastie élargit la palette de matériaux de l’impression 3D SLA pour obtenir des pièces finales à haute rigidité et résistantes à l’usure. Si l’impression par SLA permet de créer des pièces sur mesure complexes, la galvanoplastie peut transformer ces pièces SLA pour leur conférer des propriétés quasi-métalliques, y compris un module élevé, une conductivité électrique ou une finition esthétique.
Regarder le webinaire dès maintenantComment appliquer la galvanoplastie à des impressions 3D
Les antennes doivent conduire l’électricité pour propager les ondes radio. Les pièces imprimées en 3D en plastique ne conduisent pas l’électricité mais elles offrent une liberté de conception pratiquement infinie et un choix de matériaux présentant de bonnes propriétés mécaniques et thermiques. En combinant ces avantages à la galvanoplastie qui donne la conductivité souhaitée, on obtient des solutions d’antennes sur mesure très intéressantes.
L’équipe d’Elliptika a travaillé avec différents procédés de fabrication additive et a trouvé que c’est l’impression 3D par stéréolithographie qui se combine le mieux à la galvanoplastie.
« La surface des composants RF doit être lisse pour éviter des pertes dues aux rugosités en surface. Par exemple, si nous utilisons une imprimante à dépôt de filament fondu (FDM) avec des épaisseurs de couche importantes, il y aura des problèmes. En plus de l’augmentation des pertes, la rugosité des pièces va poser problème pendant la galvanoplastie : la métallisation n’adhérera pas. Avec les pièces SLA, nous n’avons pas ce type de problèmes », explique M. Cochet.
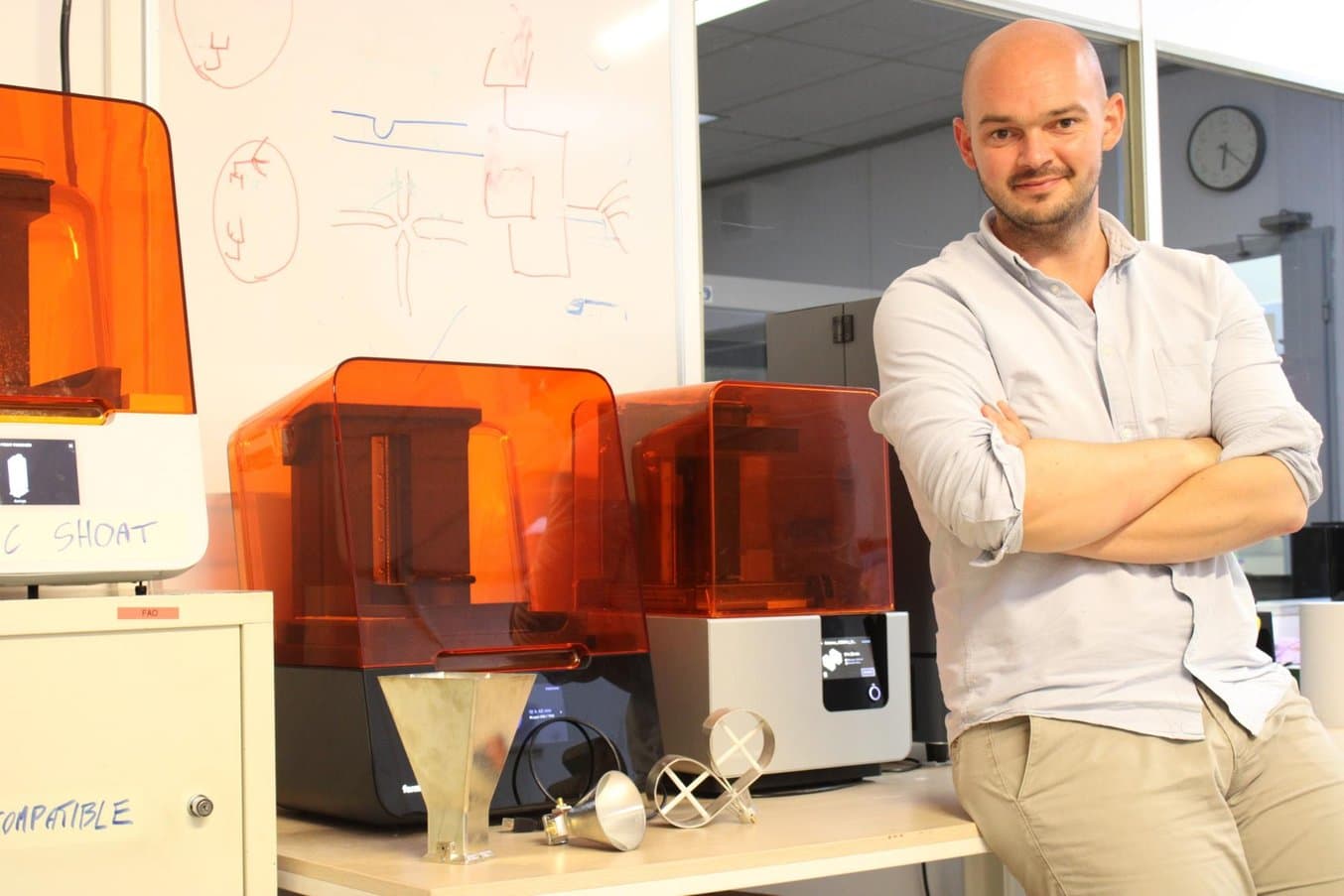
L’équipe a commencé avec une imprimante SLA Form 2, puis a acquis le modèle suivant, la Form 3, et plus récemment, elle a ajouté sept Form 3B à son parc pour réaliser des projets d’aide liés à la pandémie de COVID-19. Elle utilise principalement White Resin pour fabriquer les pièces pour la galvanoplastie, mais se sert également de Tough Resin et de High Temp Resin pour des pièces mécaniques.
Le procédé de galvanoplastie fonctionne comme suit :
« Après impression 3D de la pièce, nous devons supprimer les supports, nettoyer la surface et la polymériser. Ensuite, la pièce est soumise à un procédé chimique qui dépose une fine couche de cuivre à sa surface (environ 3 µm). Finalement, la pièce peut recevoir un traitement de finition de surface, comme le dépôt d’une couche plus épaisse d’étain », explique M. Cochet.
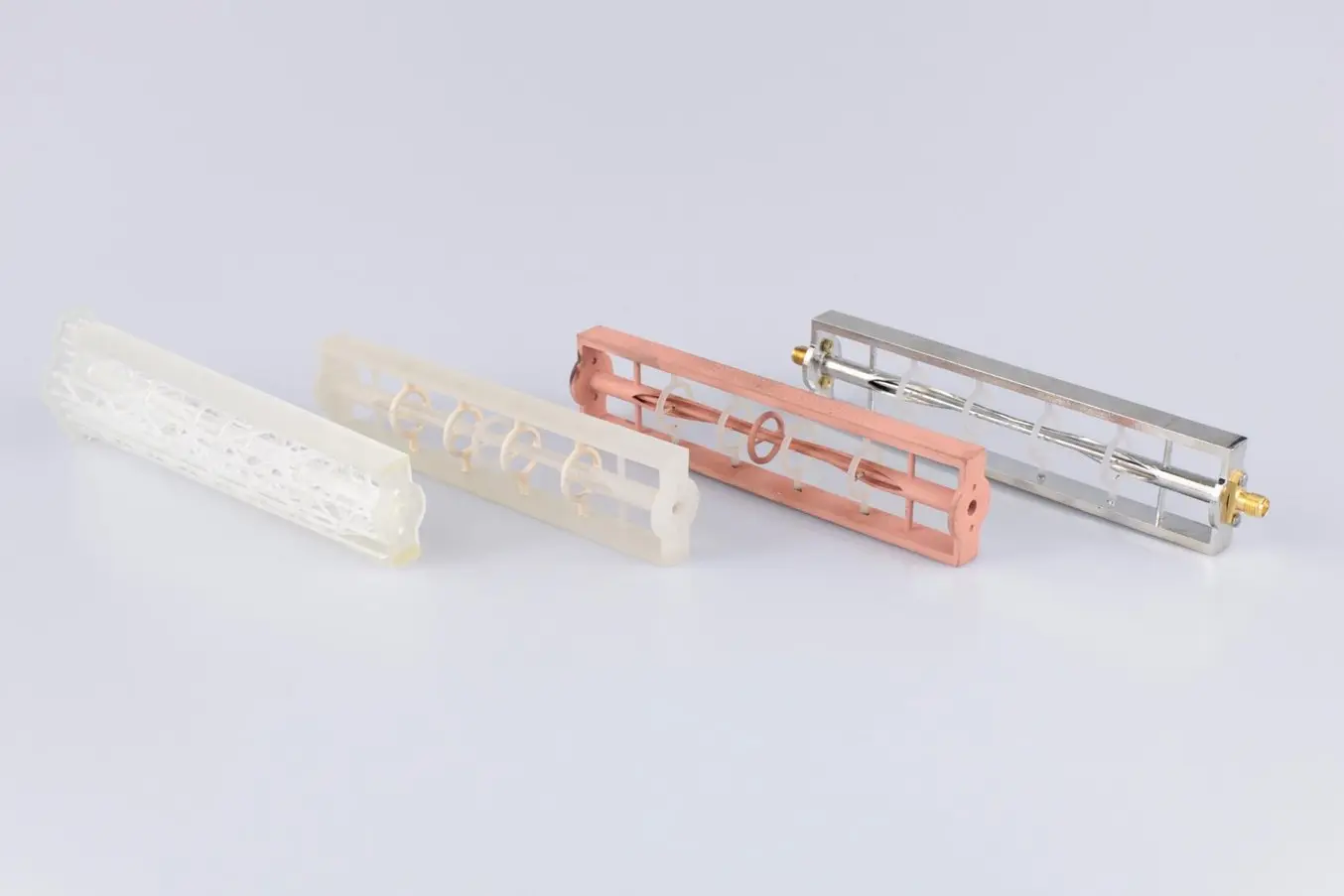
Les différentes étapes du processus de galvanoplastie, de gauche à droite : pièce en plastique imprimée en 3D, pièce post-polymérisée après élimination des supports, pièce après dépôt du cuivre et pièce finale, après dépôt d’étain.
Réduire coûts et délais de production de plus de 90 %
Comme la plupart des antennes sont utilisées en recherche et développement, Elliptika n’a habituellement à fabriquer que de petits lots, d’une à 20 unités.
« L’impression 3D est très intéressante pour nous parce que nous pouvons produire des antenne complexes à un coût très compétitif. Nous ne souhaitons pas travailler avec d’autres procédés comme l’usinage et le moulage par injection », explique Alexandre.
Avec ces procédés de production traditionnels, la fabrication d’une antenne peut prendre jusqu’à trois mois. Ce délai couvre la réalisation de l’outillage requis et les échanges avec le prestataire, nécessaires pour préciser les détails du modèle.
« Grâce à l’impression 3D en interne, nous obtenons nos pièces de travail en deux jours. Une journée pour l’impression, une journée pour la galvanoplastie et elles sont prêtes à fonctionner. C’est donc vraiment, vraiment plus court. Le prix représente également une véritable différence. La fabrication d’une antenne par un sous-traitant coûte environ 3000 €. Son impression coûte peut-être 20 €. Ce que nous coûte la fabrication de cette antenne [en tenant compte du coût d’une imprimante 3D] est complètement couvert en une seule commande », ajoute M. Cochet.
Fabrication d’une antenne | Coût | Délai de réalisation |
---|---|---|
Impression 3D SLA | €20 | 2 jours |
Sous-traitance | €3000 | Jusqu’à 3 mois |
La rapidité de développement et la possibilité de fabriquer sur mesure ouvrent de nouvelles opportunités de marchés
L’impression 3D et la galvanoplastie ont également ouvert de nouvelles opportunités de marché pour l’entreprise.
« Avant d’utiliser l’impression 3D, nous ne réalisions que l’antenne et le filtre sur circuit imprimé. Maintenant, nous fabriquons aussi les pièces volumiques. C’était faisable, mais pas pour une petite entreprise comme nous. Il nous faut être très rapides pour développer de nouvelles antennes pour nos clients et, avant l’impression 3D, c’était simplement trop long et trop coûteux pour y arriver », explique M. Cochet.
« La personnalisation des produits est très simple pour nous et nos clients reçoivent donc très rapidement et de façon rentable un prototype avec des spécifications très précises. Parfois, les spécifications de poids ou de volume sont très importantes. Nous fabriquons parfois des antennes logées dans des espaces très restreints que nous ne pourrions pas réaliser par usinage. Lorsque vous fabriquer une antenne par usinage, vous devez généralement concevoir plusieurs pièces à assembler ensuite, ce qui finalement est plus volumineux qu’une seule pièce imprimable en 3D », explique M. Cochet.
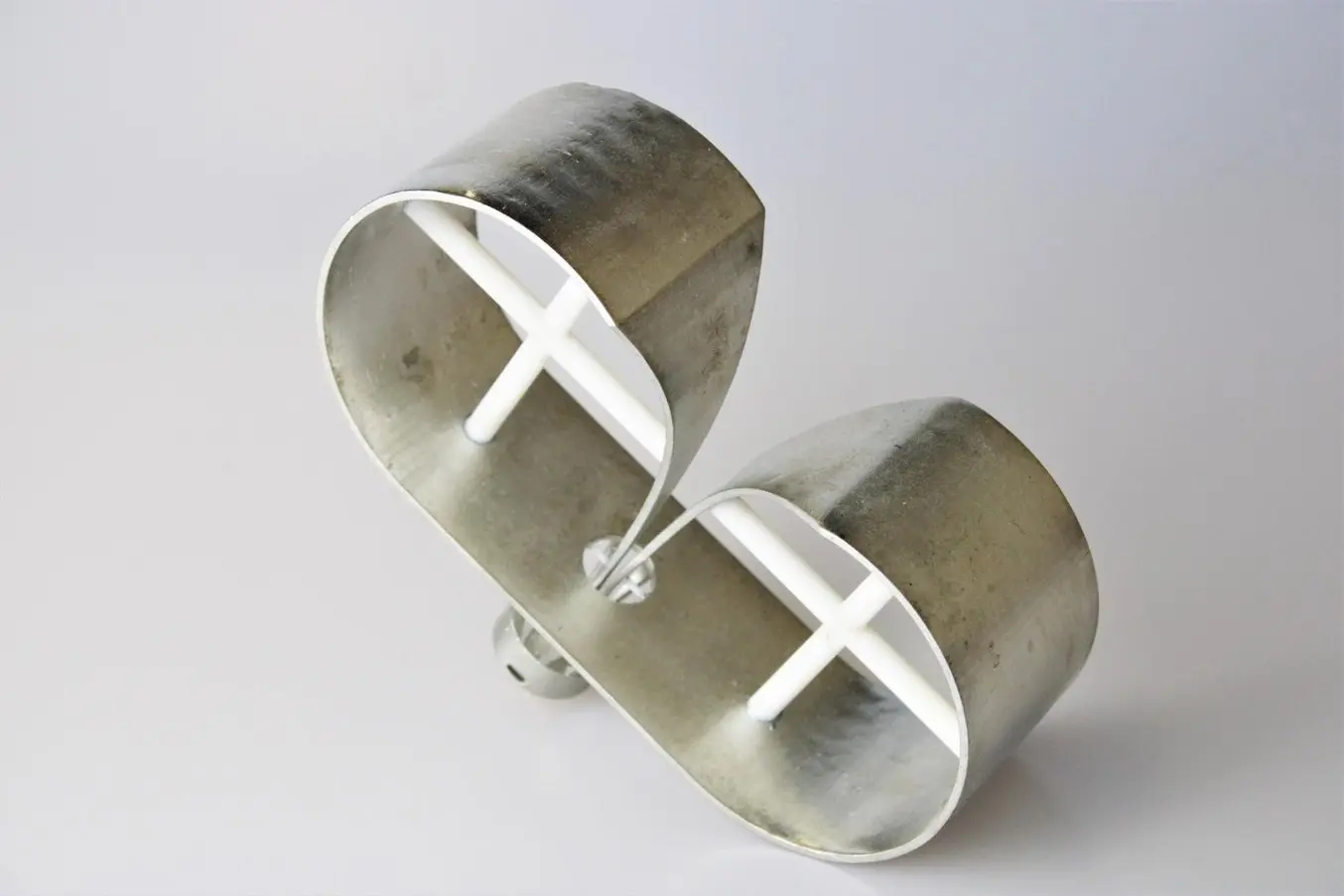
Une antenne cornet imprimée en 3D avec galvanoplastie sélective conçue par Julien Haumant, ingénieur R&D chez Elliptika.
« Par exemple, l’une de nos antennes est très complexe parce qu’elle présente des formes incurvées. Grâce à l’impression 3D, cet appareil peut être fabriqué en une seule pièce et ne pèse que 75 grammes. Un appareil avec les mêmes propriétés fabriqué par usinage comporterait de nombreuses pièces, serait très lourd et 10 à 20 fois plus grand », ajoute M. Cochet.
En savoir plus sur les applications de la galvanoplastie
La galvanoplastie sur des pièces imprimées en 3D a de nombreuses applications. Volkswagen et Autodesk utilisent ce procédé pour produire un jeu d’enjoliveurs incroyables pour un concept de véhicule futuriste, des chercheurs en Suisse ont réalisé des installations de séparateurs de faisceau et bien d’autres entreprises appliquent la galvanoplastie à des pièces imprimées en 3D pour fabriquer des pièces complexes ayant la résistance des métaux et à un coût abordable.
Regardez notre webinaire gratuit où Sean Wise, président et fondateur de RePliForm, explique comment lui et son équipe ont exploité la galvanoplastie pour élargir leur gamme d’applications d’impression 3D. Il traitera aussi de la galvanoplastie et de ses applications spécifiques à l’impression 3D, ainsi que des processus divers qui permettent d’obtenir une pièce finie après galvanoplastie d’une impression 3D.