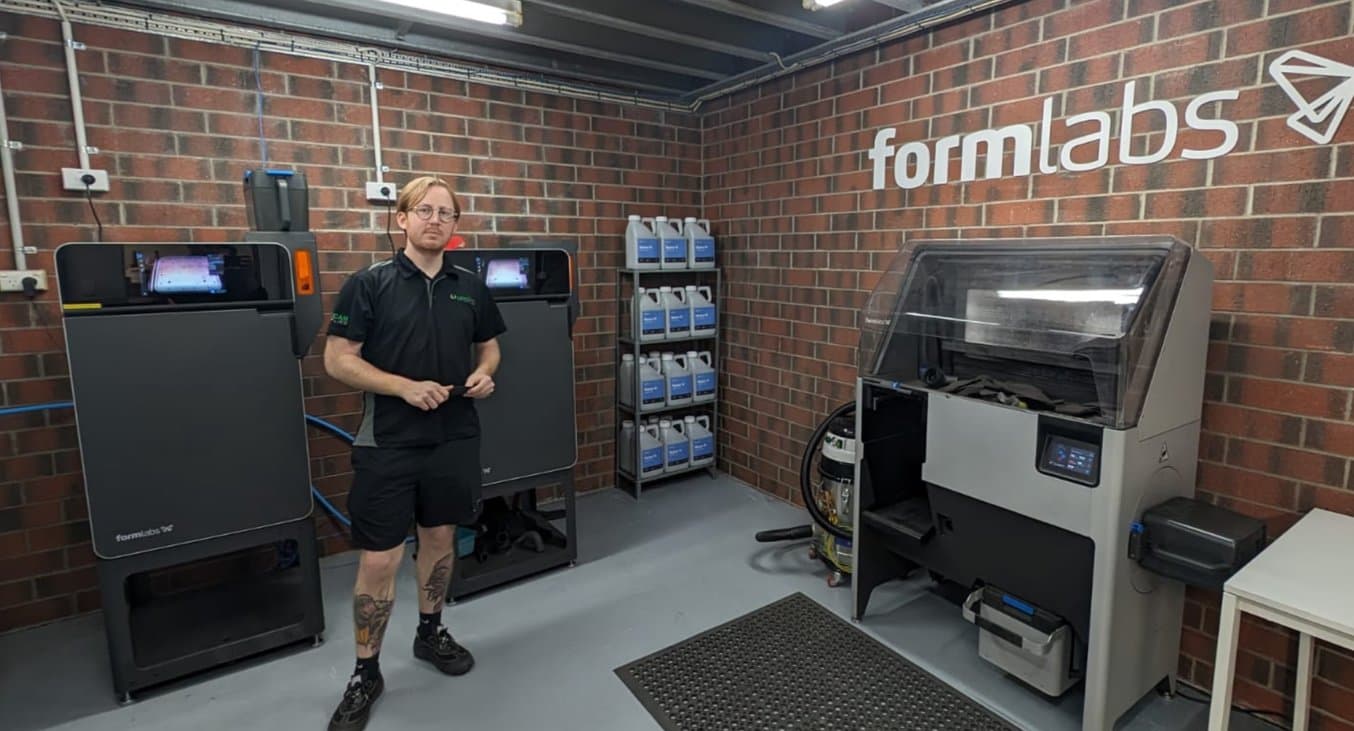
GMZ Medical est un groupe australien de fabrication de semelles intérieures composé d'entreprises spécialisées dans divers domaines, depuis la fourniture d'équipements et le développement de logiciels de conception jusqu'à la production en interne. Cette diversification permet à GMZ Medical d'avoir une connaissance approfondie de tous les aspects de la production de semelles, ainsi qu'une expérience des différents flux de travail et matériaux. Le groupe s'appuie sur la technologie de Formlabs : non seulement son laboratoire de fabrication de semelles, CADCAM Orthotics, utilise deux imprimantes 3D à frittage sélectif par laser (SLS) Fuse 1+ 30W, mais sa division de chaîne d'approvisionnement, PodCAM Supplies, recommande l'écosystème Fuse aux fabricants de semelles et au personnel de santé.
Konrad Job, podologue chez GMZ Medical, explique que cette combinaison d'activités, qui comprend également la solution logicielle Laser CAMOrthotics, permet à l'entreprise de tester tous les aspects de la production de semelles, ce qui lui permet de définir la configuration et le flux de travail optimaux.
« Notre objectif est de créer un modèle qui puisse être suivi par d'autres entreprises. Nous voulons montrer que notre logiciel peut être utilisé efficacement dans notre cycle de production, ce qui nous permettra de créer une entreprise prospère. Nous testons minutieusement l'ensemble du processus avant de le recommander à d'autres personnes ».
Konrad Job, podologue, CADCAM Orthotics
Le modèle de CADCAM Orthotics pour le flux de production des semelles imprimées en 3D utilise l'écosystème Fuse de Formlabs. Nous nous sommes entretenus avec M. Job pour en savoir plus sur les avantages de l'adoption de flux de travail numériques et pour comprendre comment ce modèle peut résoudre les principaux problèmes rencontrés par les fabricants de semelles et les professionnels de la santé.
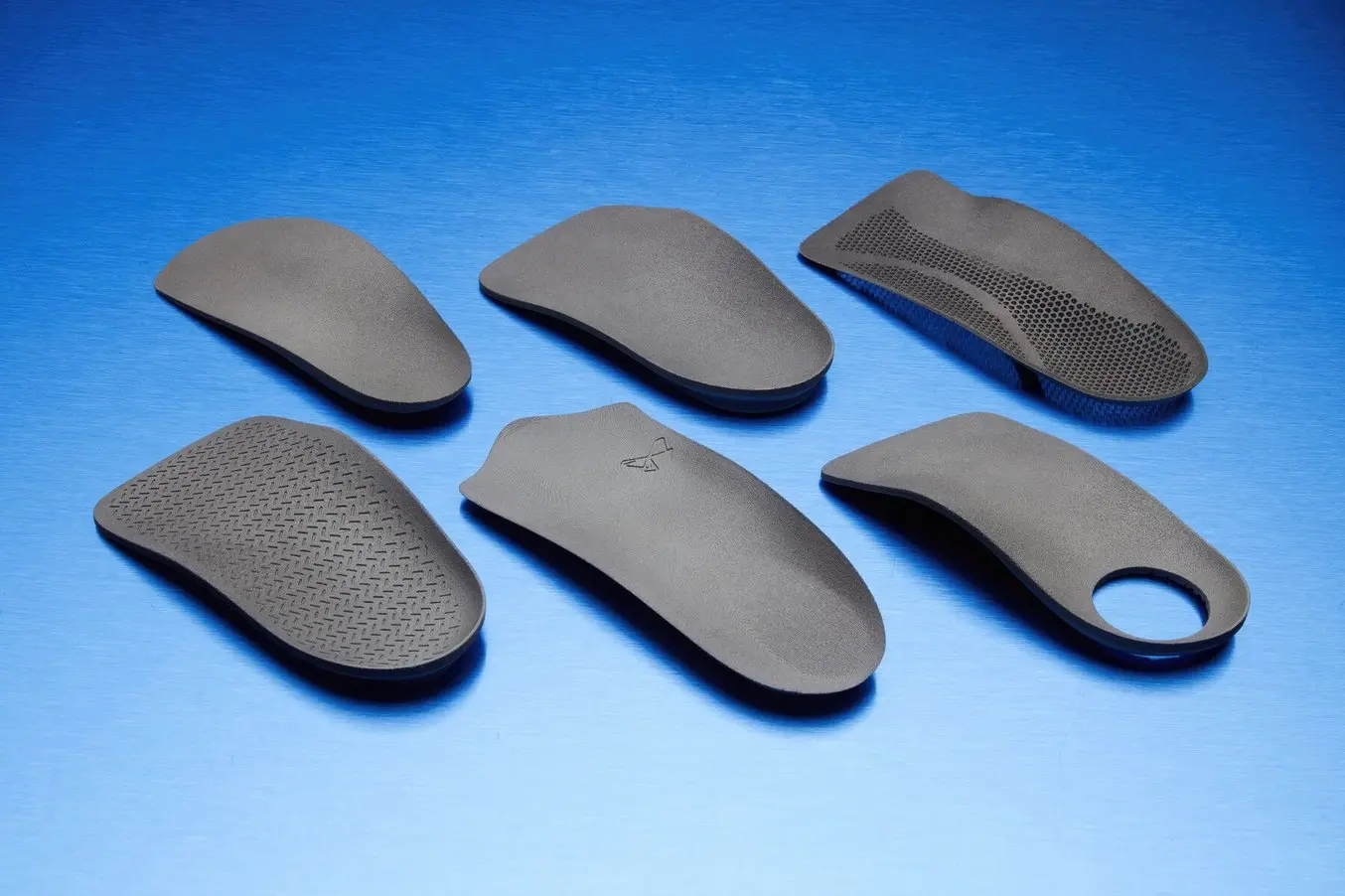
Révolutionnez votre production de semelles avec la Fuse 1+ 30W de Formlabs
Augmentez votre production de semelles tout en économisant du temps et de l'argent. Dans ce webinaire, nous expliquons pourquoi la Fuse 1+ 30W de Formlabs est la solution idéale pour commencer à passer à la fabrication numérique ou à augmenter votre production de manière abordable et efficace.
Impression 3D : un flux de travail simple dans un environnement propre
CADCAM Orthotics est la division de fabrication de GMZ Medical. La production de semelles a commencé en 1997 avec le traitement mécanique des semelles en éthylène-acétate de vinyle (EVA) et, quelques années plus tard, avec le moulage sous vide de produits en polypropylène.
Le processus de formage sous vide des produits en polypropylène a commencé par la réception d'un scan 3D. Ensuite, CADCAM Orthotics a dû concevoir un modèle positif dans le logiciel de CAO, l'usiner dans un panneau de fibres de densité moyenne (MDF) et utiliser plusieurs couches de formage sous vide sur le positif MDF pour produire l'assise plantaire avec les spécifications correctes.
« Le principal problème était le nombre d'étapes et la formation nécessaire pour que tous les membres du personnel puissent les exécuter correctement à plusieurs reprises. Au fil du temps, nous avons fini par n'avoir qu'une seule personne réellement compétente dans le processus de production », a déclaré M. Job.
Ce n'est pas seulement la formation qui a posé problème, mais aussi le MDF, qui a créé un environnement de travail sale et désagréable. « Le travail avec le MDF n'était pas agréable, car il générait beaucoup de poussière et il fallait porter des masques. Nous avons essayé la mousse haute densité, mais elle a légèrement fondu. Lorsque nous sommes passés de l'usinage mécanique des plaques de pied à l'impression 3D, aucun membre du personnel ne s'est plaint », a ajouté M. Job.

Les semelles en EVA doivent être produites par usinage CNC, ce qui est compatible avec les dessins créés avec LaserCAM Orthotics.
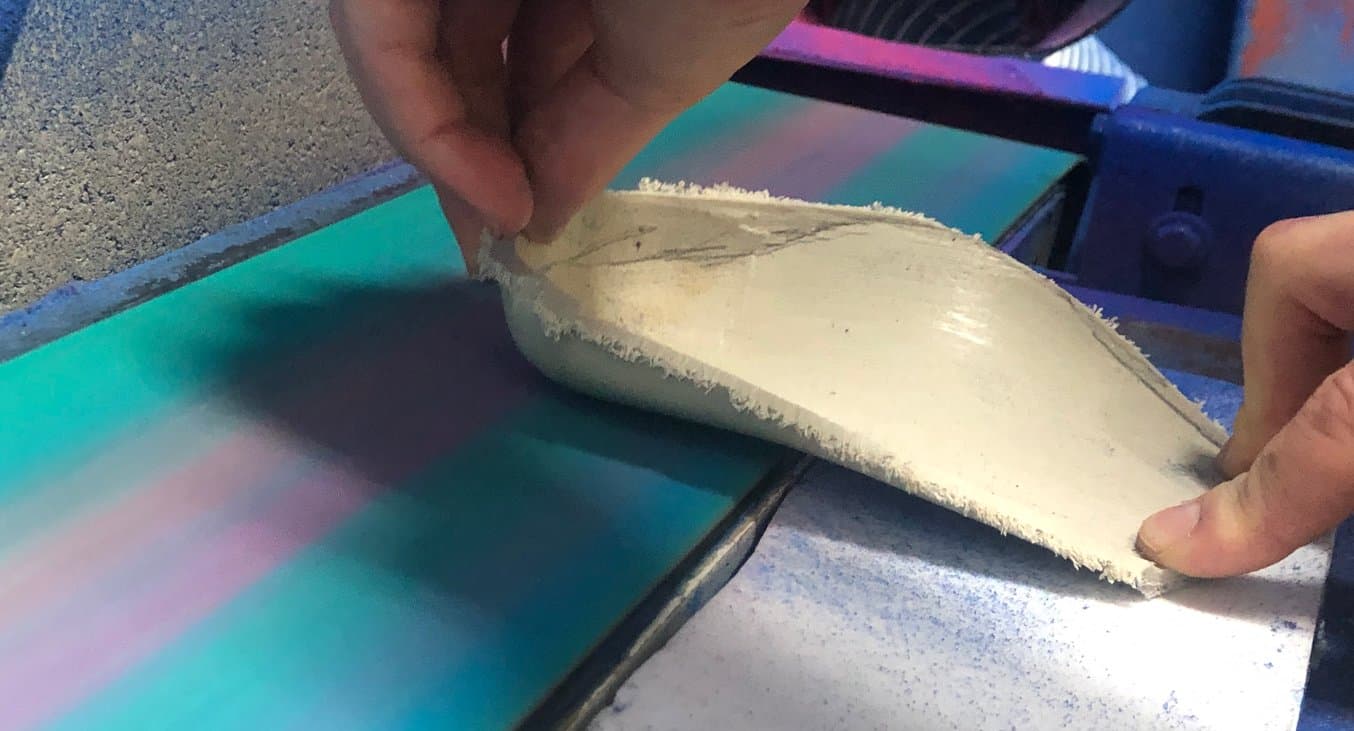
Formage sous vide de plusieurs couches pour créer des semelles avec la bonne rigidité.
Le troisième problème que pose le formage sous vide concerne l'état de surface. « Il suffit d'une empreinte digitale ou d'un cheveu tombé accidentellement pour abîmer la finition de la semelle. En outre, lors du meulage des autres couches formées sous vide, il faut faire très attention à ne pas les rayer », explique M. Job.
Dans un premier temps, CADCAM Orthotics a remplacé la production de polypropylène en externalisant l'impression 3D pendant deux ans. Comme le dit M. Job : « L'expérience a été positive, nous avons reçu beaucoup de soutien, mais nous n'avons pas eu le contrôle que nous souhaitions sur les temps de production et les détails, ainsi que sur la quantité de poudre recyclée. Nous voulions nous assurer que les pièces moulées répondaient à nos normes. »
Pour mieux maîtriser le processus, CADCAM Orthotics a décidé d'intégrer l'impression 3D en interne en 2022.
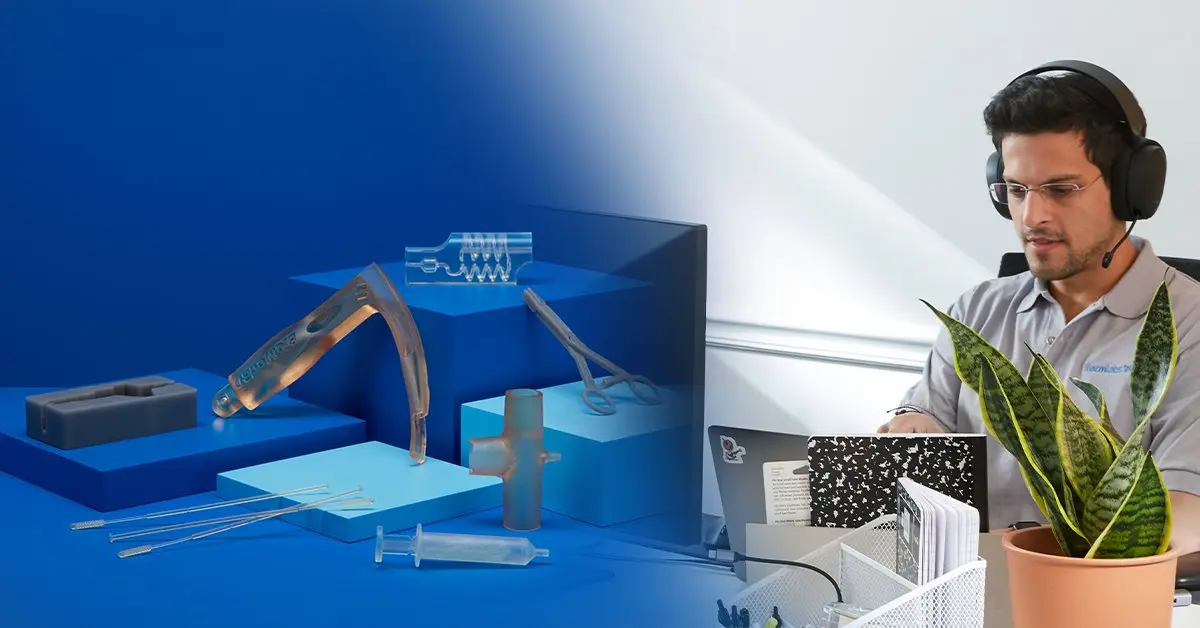
Discutez avec notre équipe commerciale médicale
Que vous deviez fabriquer des outils chirurgicaux adaptés aux patients ou un prototype de dispositif médical cardiaque, nous sommes là pour vous aider. L'équipe de Formlabs Medical est composée de spécialistes dévoués qui savent exactement comment vous soutenir et répondre aux besoins de votre entreprise.
Production en interne avec l'écosystème Fuse
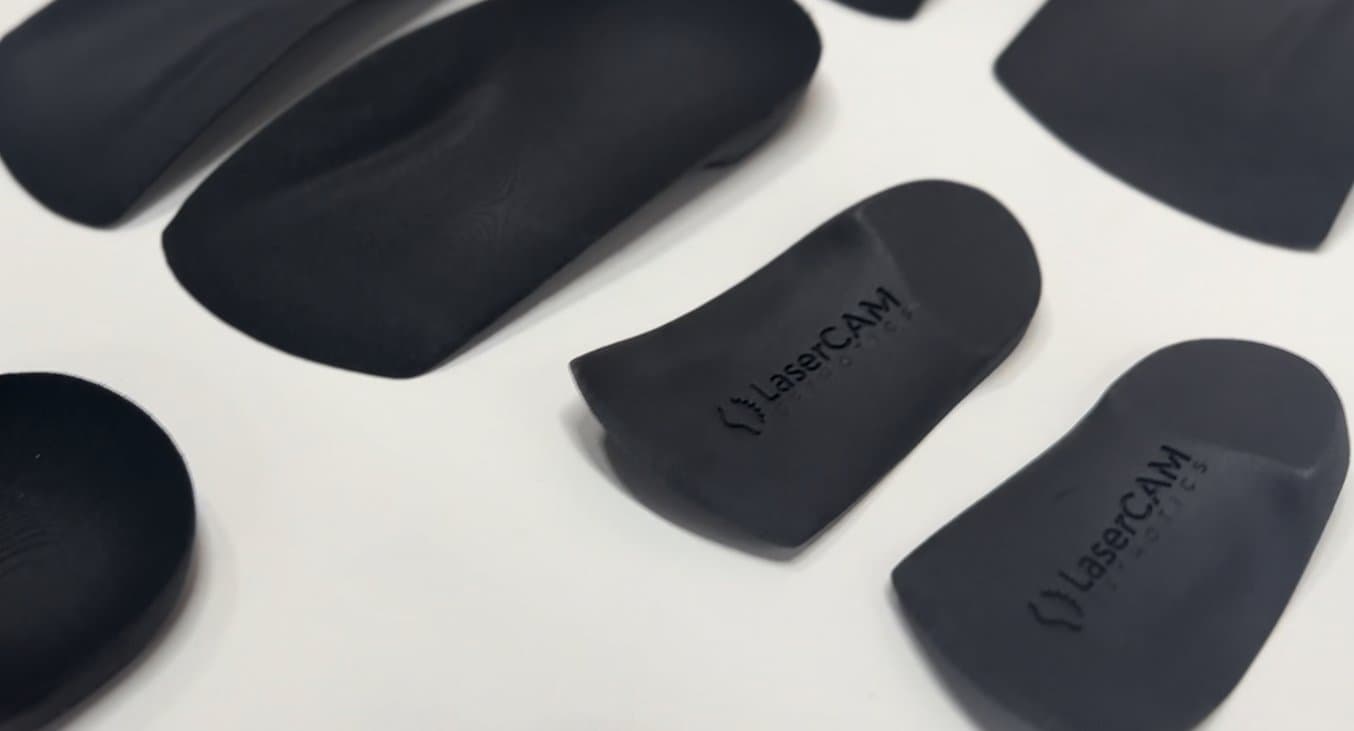
Les semelles LaserCAM imprimées en interne avec la Fuse 1+ 30W en Nylon 11 Powder sont 40 % moins chères que l'externalisation de l'impression 3D.
En fin de compte, l'externalisation est un excellent moyen de valider le processus d'impression 3D avant de passer à la production en interne. Cette dernière permet de maîtriser l'ensemble du processus de production et d'accélérer les délais ; pour CADCAM Orthotics, cela s'est traduit par la production des pièces en interne en quatre jours ouvrables, contre dix en cas de sous-traitance. En outre, le passage à l'impression 3D a permis de réaliser d'importantes économies sur la production.
Méthode de production | Coût par paire | Heures de travail pour la production | Délai de production |
---|---|---|---|
Thermoformage traditionnel | 77,20 $ | 1,5 | 10 jours ouvrables |
Impression externalisée | 92,63 $ | 0,7 | 10 jours ouvrables |
Impression en interne | 54,29 $ | 0,8 | 4 jours ouvrables |
L'impression 3D en interne permet de mieux contrôler les cycles de production. Pour CADCAM Orthotics, cela signifie imprimer tous les jours, pour au moins cinq séries de production par semaine, et parfois même une le week-end, pour un total d'environ 30 à 50 paires de semelles rigides par semaine. L'impression 3D SLS inclut un temps de refroidissement des pièces, que CADCAM Orthotics prend en compte lors de l'impression, du déchargement et du démarrage d'un nouveau cycle au cours de la journée de travail. Cela permet de post-traiter les pièces le jour même et de s'assurer que les nouvelles pièces sont prêtes pour le lendemain.
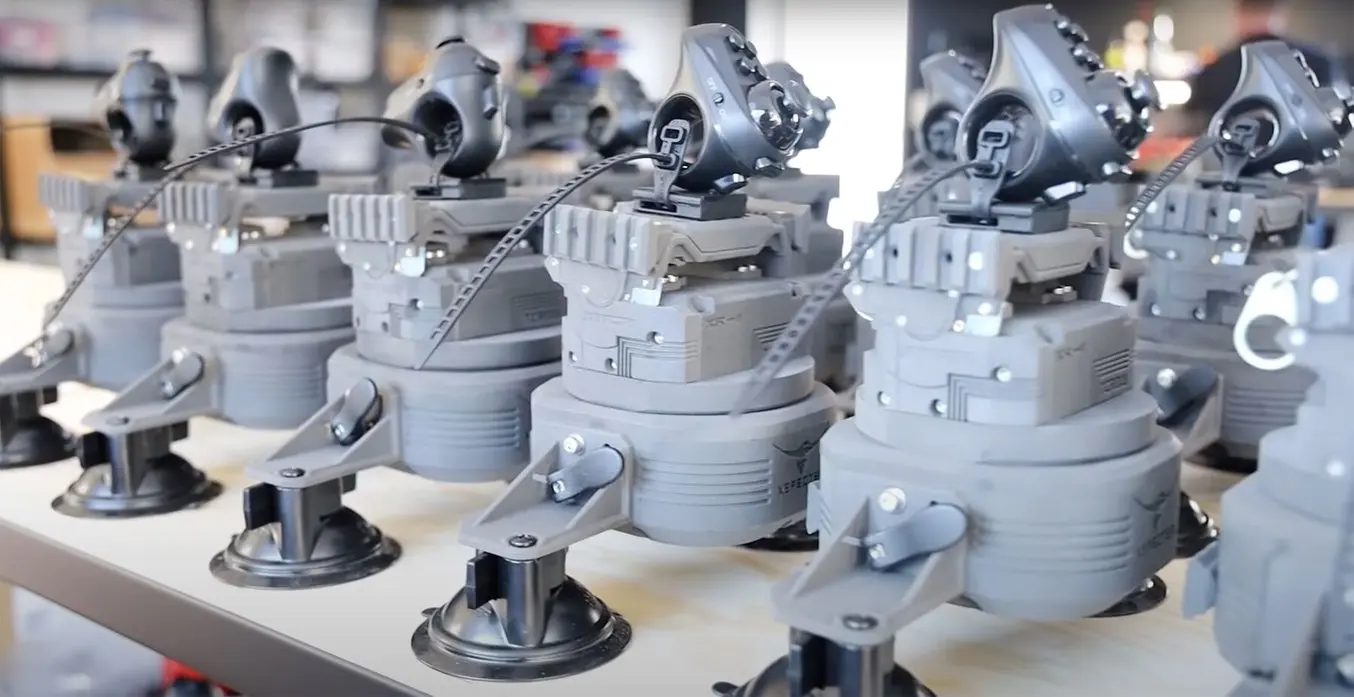
Le SLS pour la production finale
L'impression 3D pour la production finale n'est pas seulement accessible : elle est aussi plus abordable, plus agile et plus évolutive que jamais grâce à l'écosystème SLS Fuse. Explorez notre page dédiée à la production SLS pour comparer les différentes méthodes de fabrication, consulter les tarifs des poudres en vrac et découvrir comment 15 fabricants exploitent actuellement les imprimantes de la série Fuse.
Un flux de travail simple et efficace
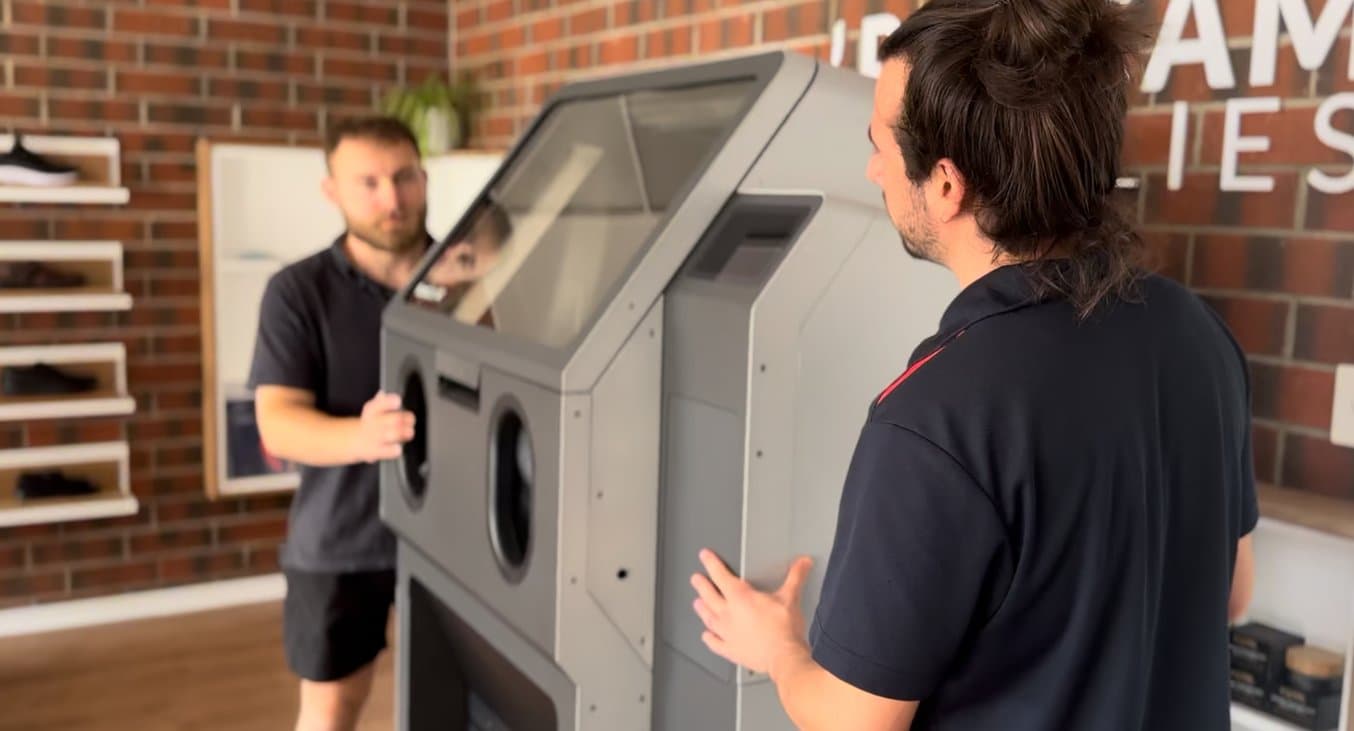
CADCAM Orthotics a récemment ajouté une Fuse Blast à son flux de travail, ce qui permet de nettoyer les semelles intérieures en 78 % de temps en moins.
M. Job a remarqué qu'avec les flux de travail traditionnels, il n'y avait qu'une seule personne spécialisée. « Mais aujourd'hui, avec l'impression 3D, nous avons au moins cinq personnes capables de le faire. La formation est donc essentielle. » La simplicité du flux de travail de l'impression 3D avec l'écosystème Fuse augmente non seulement la productivité du personnel, mais rend également le processus plus simple et plus propre que les méthodes traditionnelles.
« Le flux de travail m'enthousiasme car c'est la première fois que nous disposons de pièces que nous pouvons simplement retirer d' une machine et recouvrir, ce qui est très agréable. Personnellement, je préfère passer mon temps à concevoir les pièces plutôt qu'à les rectifier. »
Konrad Job, podologue, CADCAM Orthotics
En éliminant les opérations de meulage et de finition physiquement exigeantes requises par les flux de travail traditionnels, l'écosystème Fuse libère M. Job et d'autres employés de CADCAM Orthotics pour des tâches à plus forte valeur ajoutée, notamment la conception.
Pour le nettoyage et le polissage, CADCAMOrthotics utilise la Fuse Blast, une solution entièrement automatisée qui permet d'obtenir des produits propres au toucher en 78 % de temps en moins. En outre, le processus de nettoyage se déroule dans un environnement clos, ce qui permet de maintenir les zones de travail et le personnel plus propres et de créer un environnement plus agréable.
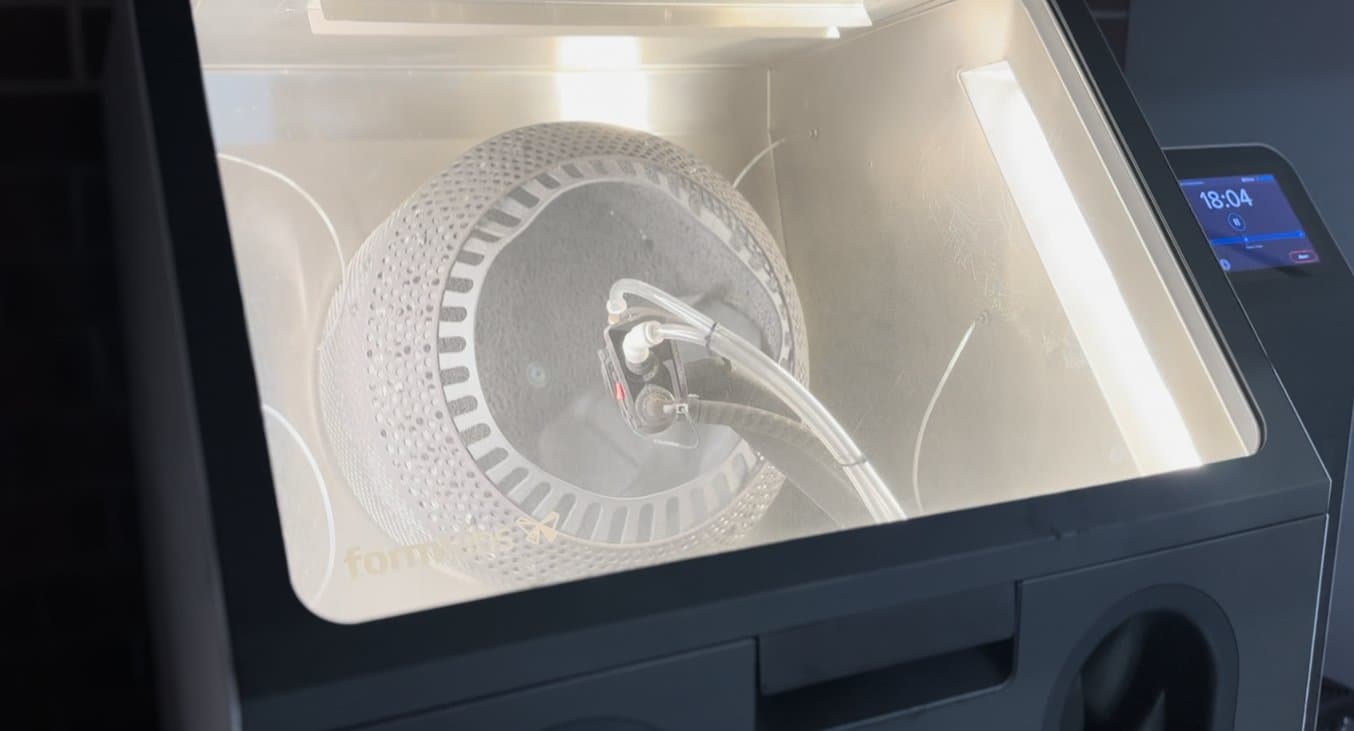
La Fuse Blast peut nettoyer automatiquement une chambre d'impression entière contenant des semelles, ce qui permet de gagner du temps.
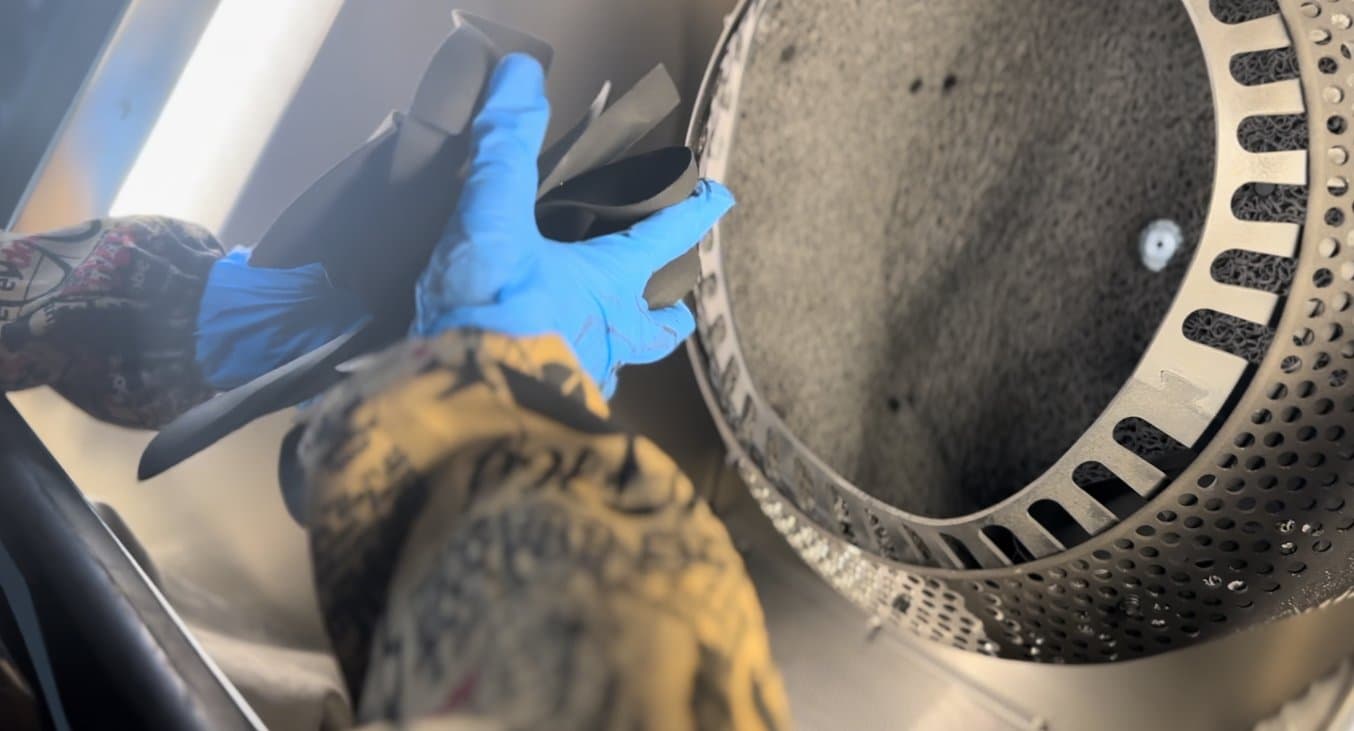
Les pièces sortent de la Fuse Blast propres et prêtes à être recouvertes.
« Avec la Fuse Blast, nous disposons d'une boucle de production totalement parfaite, sans post-traitement manuel. Nous le modélisons, nous le chargeons dans l'imprimante et nous le recouvrons, c'est donc très, très facile ».
Konrad Job, podologue, CADCAM Orthotics
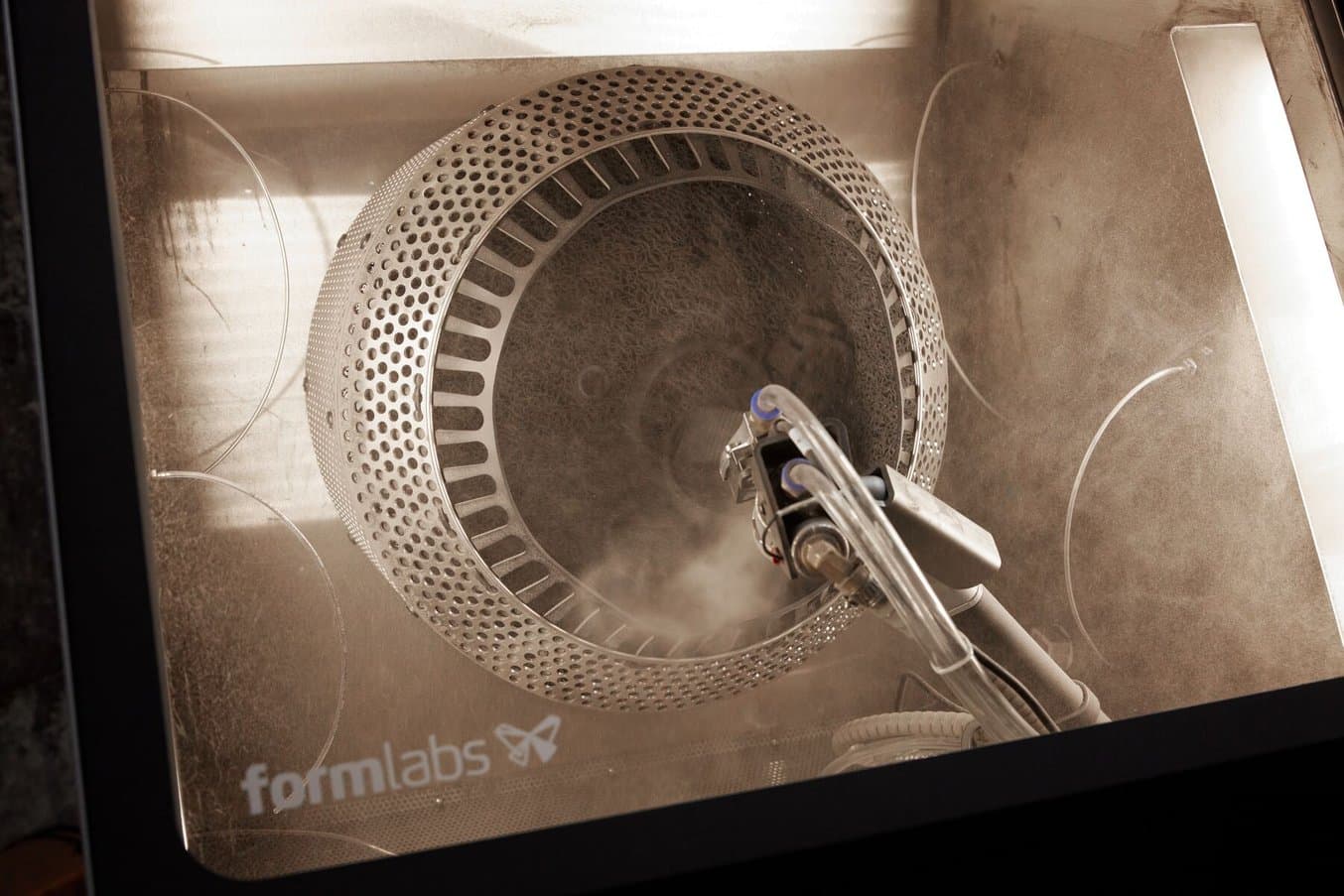
Post-traitement des pièces SLS en 10 minutes : la Fuse Blast pour les semelles intérieures
La Fuse Blast réduit considérablement le temps de post-traitement. Dans ce webinaire, Shiden Yohannes montre comment il est possible d'éliminer la poussière d'une chambre d'impression entière contenant plus de 40 semelles en seulement dix minutes, ce qui permet de réduire de 78 % le temps de post-traitement de 45 minutes.
Plus de redondance pour une plus grande sécurité
« Nous avons intégré la technologie CNC et vendons des systèmes CNC, nous sommes donc très conscients de l'importance de la redondance dans la production. Par conséquent, lorsque nous évaluons les machines SLS, nous devons être en mesure d'en acheter deux ».
Les imprimantes 3D peuvent également connaître des temps d'arrêt, dus à des erreurs d'utilisation ou à des besoins de maintenance générale. Si vous n'avez qu'une seule imprimante, cela entraînera une interruption totale de la production. Cependant, avec deux imprimantes, la continuité peut être assurée. La redondance permet également une certaine flexibilité en cas de travaux urgents ou de commandes importantes.
« Le prix de la Fuse 1+ 30W nous a permis d'en acheter deux, et le système était évolutif. C'était notre premier critère : la possibilité d'acheter plus d'unités pour assurer la redondance ».
Konrad Job, podologue, CADCAM Orthotics
Outre la redondance, le fait de disposer de deux imprimantes permet une plus grande flexibilité dans l'augmentation de la production. Après avoir augmenté la production sur une deuxième imprimante, d'autres unités peuvent être ajoutées, tout en utilisant le même flux de travail et sans avoir à refuser des commandes en attendant que d'autres machines soient installées.
Les avantages d'un faible encombrement
« En vue de la commercialisation de notre logiciel, il était vraiment important de disposer d'une imprimante SLS suffisamment compacte pour être utilisée dans une clinique.
Konrad Job, podologue, CADCAM Orthotics
LaserCAM Orthotics est la solution logicielle de GMZ Medical pour la conception des semelles, que CADCAM Orthotics utilise pour la conception interne avant la production. La production en interne permet à CADCAM de tester les systèmes et les flux de travail avant de les recommander aux cliniques via PodCAM Supplies.
PodCAM Supplies fournit des produits aux cliniques de santé, il est donc nécessaire que LaserCAM Orthotics soit facile à utiliser, mais aussi que les imprimantes recommandées par PodCAMSupplies prennent en compte les besoins d'une clinique, y compris l'encombrement de la machine et les solutions de post-traitement, le prix de vente et la simplicité du flux de travail.
« Nous ne pouvions pas installer un mastodonte d'un demi-million de dollars dans une petite pièce et la transformer en salle d'impression, mais nous avons pu le faire avec la Fuse. La promotion de l'imprimante de la série Fuse et la sensibilisation du personnel de santé à la possibilité de l'utiliser en clinique ont apporté d'importants avantages commerciaux ».
Konrad Job, podologue, CADCAM Orthotics
Bien que l'écosystème Fuse soit peu encombrant, CADCAM Orthotics peut produire jusqu'à 12 paires de semelles en une seule impression. M. Job a déclaré : « En distribuant des logiciels de CAO, les imprimantes Fuse se sont révélées extrêmement compétitives par rapport aux machines SLS et MJF de grand format pour nos clients qui souhaitent imprimer dans leurs propres cliniques et dans des laboratoires spécialisés plus petits.
Un catalogue de matériaux polyvalent sur une seule imprimante
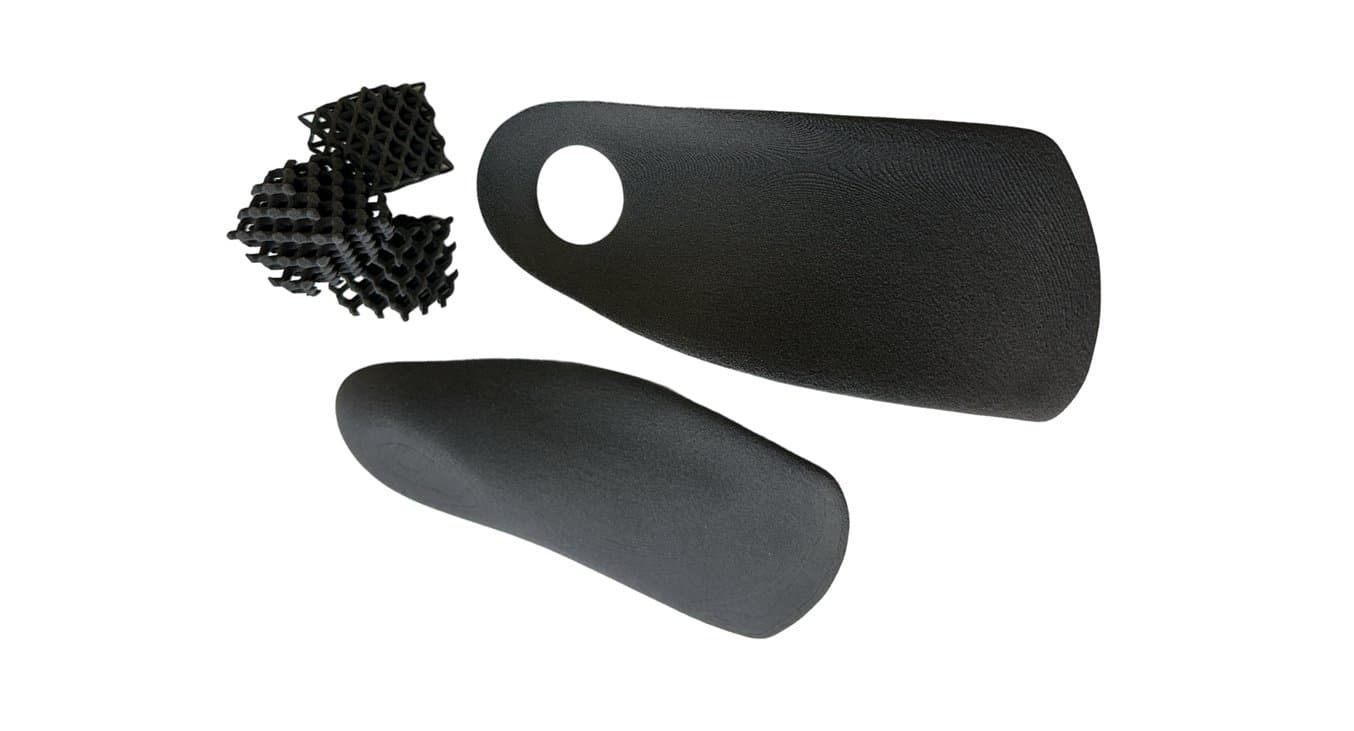
Modèles de LaserCAM Orthotics imprimés en 3D sur la Fuse 1+ 30W présentant les propriétés de Nylon 11 Powder.
Lorsqu'elle a décidé de passer à l'impression 3D, l'équipe de CADCAM Orthotics a cherché des options pour le polypropylène, la norme du secteur à l'époque, qui a ensuite été remplacée par le nylon. En ce qui concerne les matériaux d'impression 3D pour les semelles en nylon, M. Job nous dit : « Il était important d'avoir des pièces suffisamment résistantes à la traction et à la flexion, afin qu'elles ne se brisent ou ne se déforment pas ».
Nylon 11 Powder est un matériau idéal pour imprimer des semelles rigides, y compris des semelles partielles, avec une rigidité, une ductilité élevée et une stabilité à long terme sur la Fuse 1+ 30W. En outre, les pièces imprimées avec Nylon 11 Powder sont écologiquement stables, absorbent très peu d'humidité et résistent à la lumière, à la chaleur et aux produits chimiques, tout en étant certifiées biocompatibles pour un contact prolongé avec la peau.
Tableau de comparaison des matériaux | Nylon 11 Powder |
---|---|
Résistance à la rupture par traction | 49 MPa |
Allongement à la rupture (X/Y) | 40 % |
Résistance à la flexion | 55 MPa |
Module de flexion | 1,4 GPa |
Commandez un échantillon gratuit pour évaluer la performance et la qualité des semelles en Nylon 11 Powder.
La variété des matériaux a également influencé la décision d'adopter le Fuse 1+ 30W. M. Job explique : « Au départ, nous voulions imprimer en Nylon 11 Powder pour remplacer notre polyéthylène, et ce produit s'est avéré efficace. Mais qu'en est-il si nous voulons imprimer différents types de produits en utilisant Nylon 12 Powder, du polypropylène ou du TPU ? Sans parler des autres matériaux que Formlabs pourrait développer au cours des dix prochaines années ».
La Fuse 1 30W est capable d'imprimer six poudres, y compris des matériaux biocompatibles, et les experts en matériaux de Formlabs travaillent sans relâche à la mise au point de nouveaux matériaux à la pointe de l'industrie.
Le catalogue croissant de matériaux est un avantage pour l'écosystème Fuse. M. Job déclare : « Grâce à l'augmentation de la production avec la Fuse 1+ 30W, nous serons en mesure d'offrir une plus large gamme de matériaux avec plus de redondance que nos concurrents. Cela nous donnera un avantage concurrentiel indéniable ».
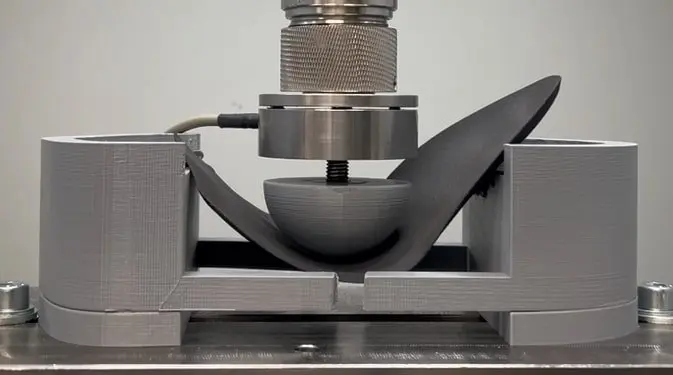
Analyse des performances mécaniques de semelles rigides imprimées en 3D et fabriquées de manière traditionnelle
Cette étude compare les propriétés mécaniques et les méthodes de fabrication utilisés pour produire des semelles orthopédiques personnalisées : la Fuse 1+ 30W de Formlabs et Nylon 11 Powder, HP 3D High Reusability PA 11, et un polypropylène fabriqué de façon traditionnelle.
Logiciel de conception orthodontique LaserCAM
Il existe de nombreuses solutions logicielles pour la conception de semelles, ce qui rend ce secteur très compétitif. M. Job reconnaît que chaque solution logicielle a ses propres caractéristiques et avantages. LaserCAM se concentre donc « sur la conception de dispositifs médicaux qui utilisent directement des données normatives pour générer des modèles d'orthèses ».
L'entreprise s'efforce également de maintenir un système ouvert, permettant aux personnes de travailler avec la technologie qu'elles préfèrent. M. Job précise : « Nous ne verrouillons pas nos types de fichiers pour qu'ils ne fonctionnent qu'avec une seule imprimante ou un seul type de scanner 3D. Nous essayons d'introduire n'importe quel scan dans notre système et de produire un fichier STL qui peut être utilisé avec n'importe quelle machine CNC que nous utilisions autrefois, ou avec n'importe quelle imprimante 3D que nous utilisons aujourd'hui. Je pense que cela nous a aidés parce que nous n'avons pas le même niveau de partialité, nous pouvons donc recommander directement ce que nous pensons être le meilleur matériel pour fonctionner avec le logiciel. »
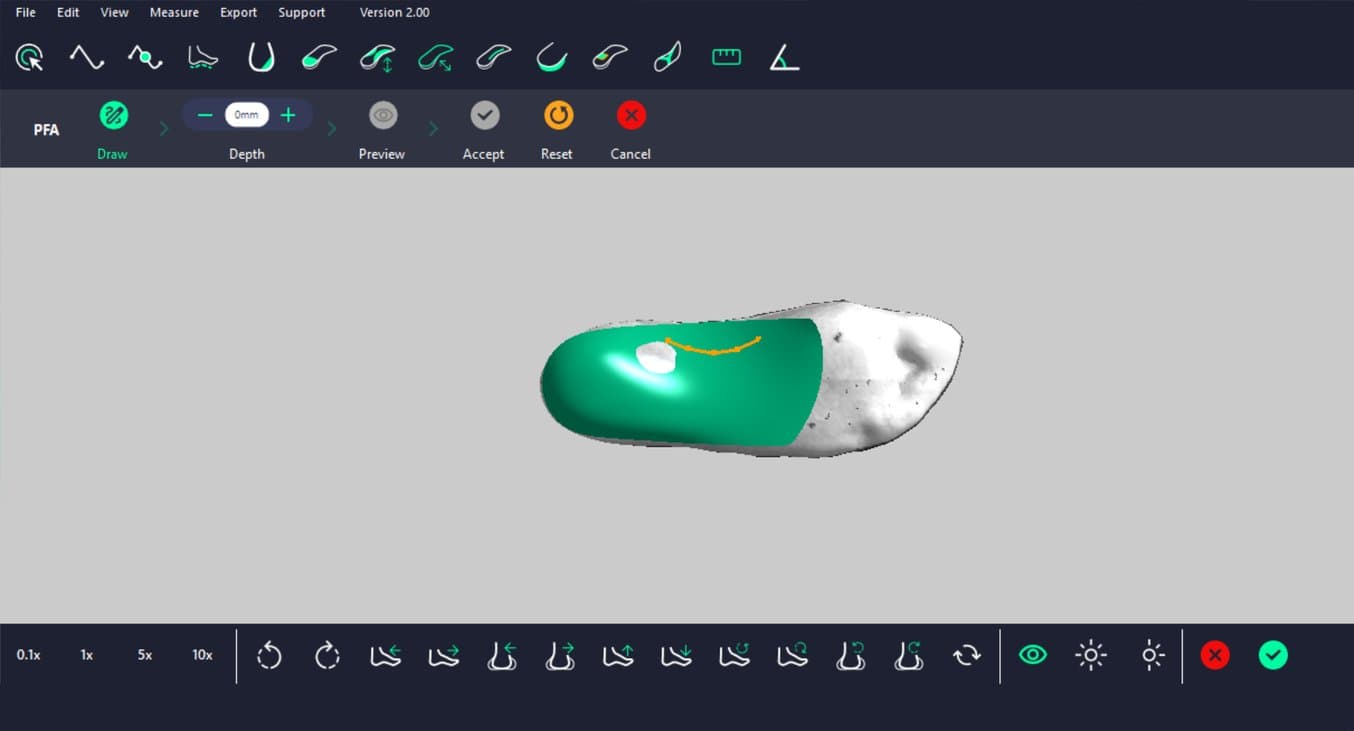
Après avoir conçu une semelle dans LaserCAM, les utilisateurs peuvent la fabriquer eux-mêmes ou l'envoyer à CADCAM Orthotics pour qu'elle soit produite.
Cette flexibilité permet à PodCAM Supplies de travailler avec les prestataires de soins de santé et les fabricants de semelles pour sélectionner les systèmes optimaux pour leur activité, tout en utilisant le logiciel de conception de semelles LaserCAM Orthotics.
La volonté d'innover
Dans l'ensemble, les avantages de l'impression 3D – économies, efficacité et espace de travail plus propre – favorisent l'innovation. M. Job ajoute : « Avoir une imprimante 3D sur un lieu de travail est amusant pour le personnel, car elle permet d'innover, de développer différents produits et prototypes que nous aurions autrement eu beaucoup de mal à fabriquer avec le CNC ».
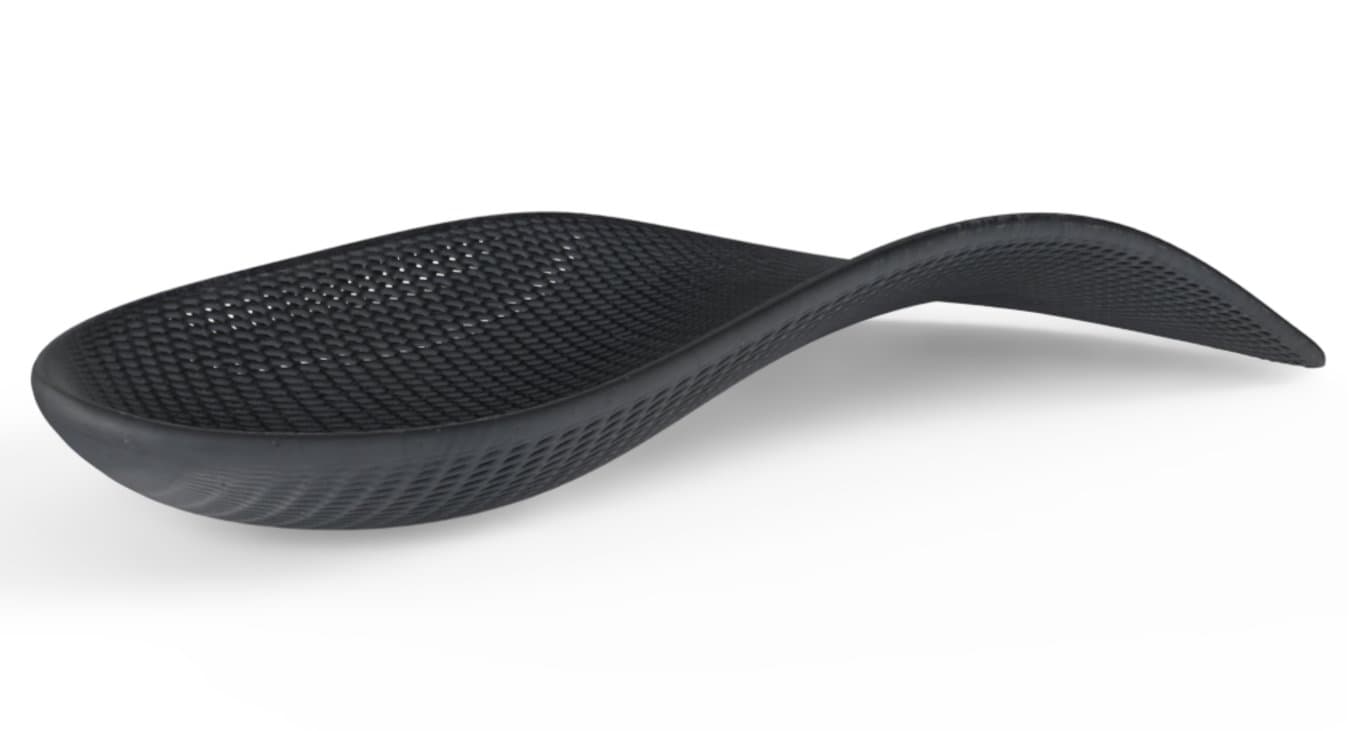
Une semelle en treillis montre la polyvalence rendue possible par LaserCAM et l'impression 3D.
Avec des flux de travail plus faciles, des espaces de travail plus propres et les propriétés mécaniques des poudres SLS, l'écosystème Fuse et le logiciel LaserCAM permettent à M. Job de repousser les limites du possible en matière de semelles orthopédiques.
Pour découvrir comment l'écosystème Fuse peut stimuler la fabrication et l'innovation, contactez nos experts en impression 3D ou demandez un échantillon de semelle imprimée avec la Fuse 1+ 30W pour évaluer sa qualité par vous-même.