Guide de l'impression 3D de fibre de carbone : comparaison des imprimantes et des matériaux
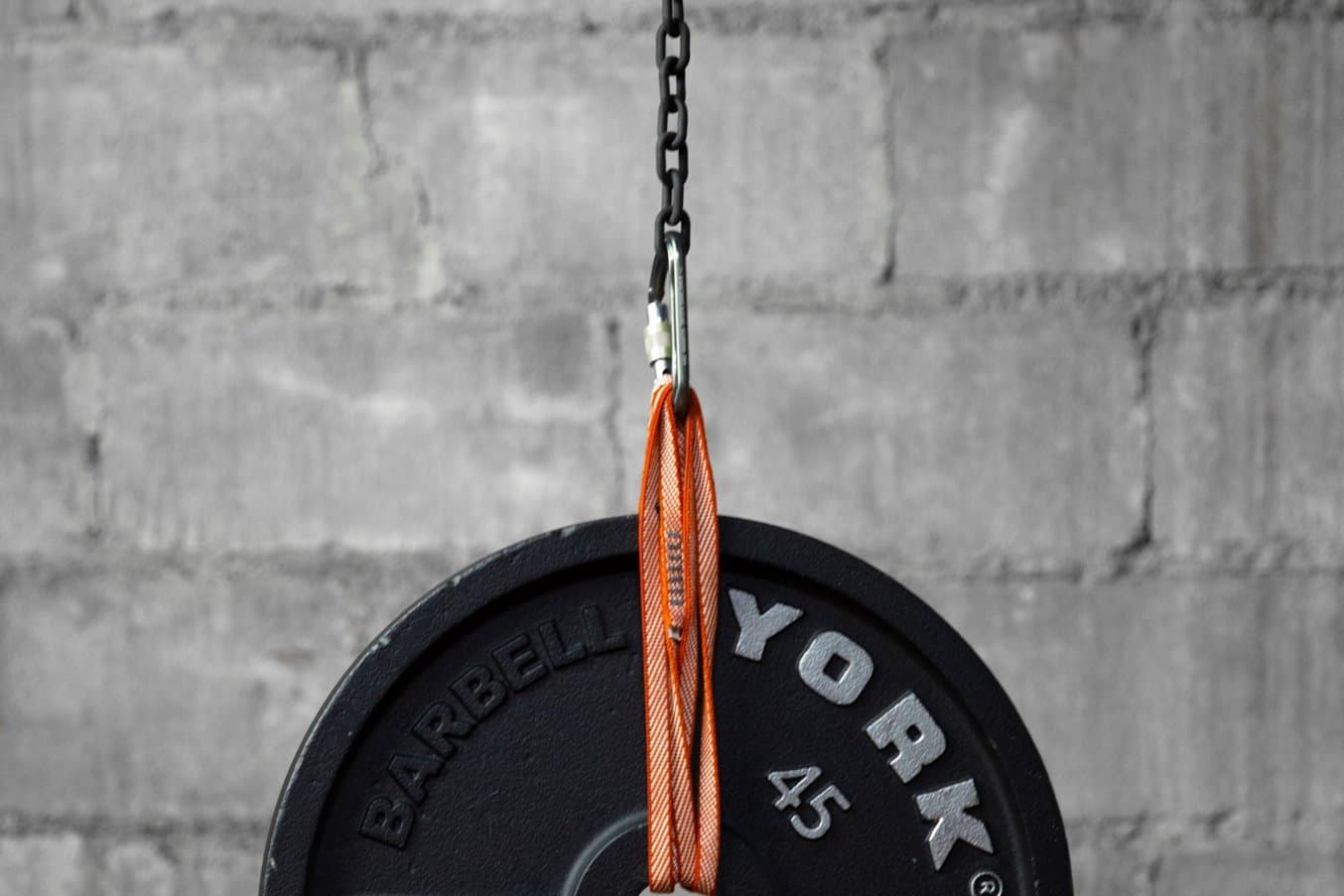
Vélos, voitures de course, drones ou raquettes de tennis : tous ces produits nécessitent une résistance et une durabilité élevées sans pour autant peser trop lourd. Les matériaux composites en fibre de carbone offrent cette combinaison de propriétés : c'est pourquoi on les trouve partout, du châssis des Formule 1 au cadre des vélos de route légers.
Comme de nombreuses imprimantes 3D professionnelles utilisent aussi couramment des matériaux à base de polymères, y compris divers composites, beaucoup de gens se posent la question « peut-on imprimer en 3D de la fibre de carbone ? ».
En effet, l'impression 3D peut être utilisée de deux manières pour créer des pièces en fibre de carbone : en soutenant les méthodes de fabrication traditionnelles grâce aux moules imprimés en 3D, ou en imprimant directement en 3D des composites en fibre de carbone. Dans cet article, nous allons vous présenter les moyens de fabrication traditionnels ainsi que les nouveaux flux de travail pour imprimer des moules et l'impression 3D directe de pièces composites en fibre de carbone.
Combiner l'impression 3D avec les méthodes traditionnelles de fabrication pour les pièces en fibre de carbone
La fibre de carbone est un matériau composite généralement produit en entrelaçant de longs filaments de fibre de carbone, puis en y ajoutant un polymère. Ces brins peuvent être entrelacés de manière à aligner la force le long d'un certain vecteur, ou de manière à ce que le produit final présente une force multilatérale dans toutes les directions. Le matériau obtenu est ensuite transformé en produit final par l'un des trois procédés suivants : la stratification en voie humide, la stratification de préimprégnés ou le moulage par transfert de résine (RTM).
Stratification en voie humide
Avec la stratification en voie humide, les feuilles de fibre de carbone sont découpées et pressées dans un moule, puis peintes avec une résine liquide qui, en durcissant et en se solidifiant, lie les feuilles et leur donne la forme finale souhaitée. Cette méthode nécessite le moins d'équipement et est également la plus facile à maîtriser pour un débutant. Comme la plupart des opérations peuvent être effectuées à la main, il s'agit de l'une des méthodes les moins coûteuses, mais la contrepartie est que les pièces obtenues reproduisent moins bien la matrice du moule que les pièces produites par d'autres méthodes.
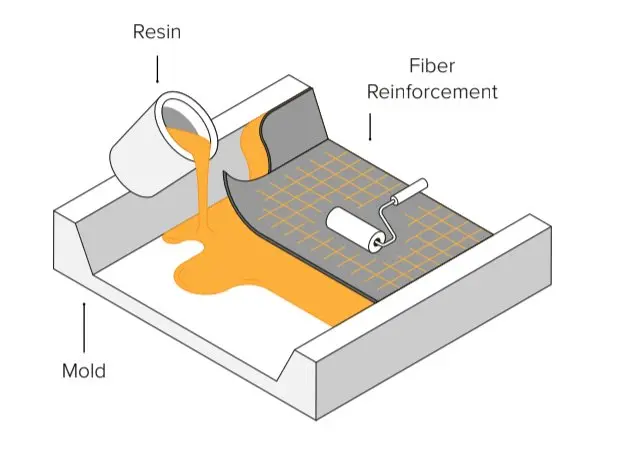
Stratification de préimprégnés
Avec cette méthode, la fibre de carbone est déjà imprégnée de résine, puis insérée dans un moule qui utilise la pression et la chaleur pour lui donner sa forme finale. Cette méthode est la plus coûteuse car elle nécessite un équipement spécialisé pour stocker et manipuler les feuilles préimprégnées, ainsi qu'une machine à mouler chauffée et pressurisée. Cette méthode est la plus reproductible et la plus uniforme : elle est donc la plus appropriée pour la production en série de pièces en fibre de carbone.
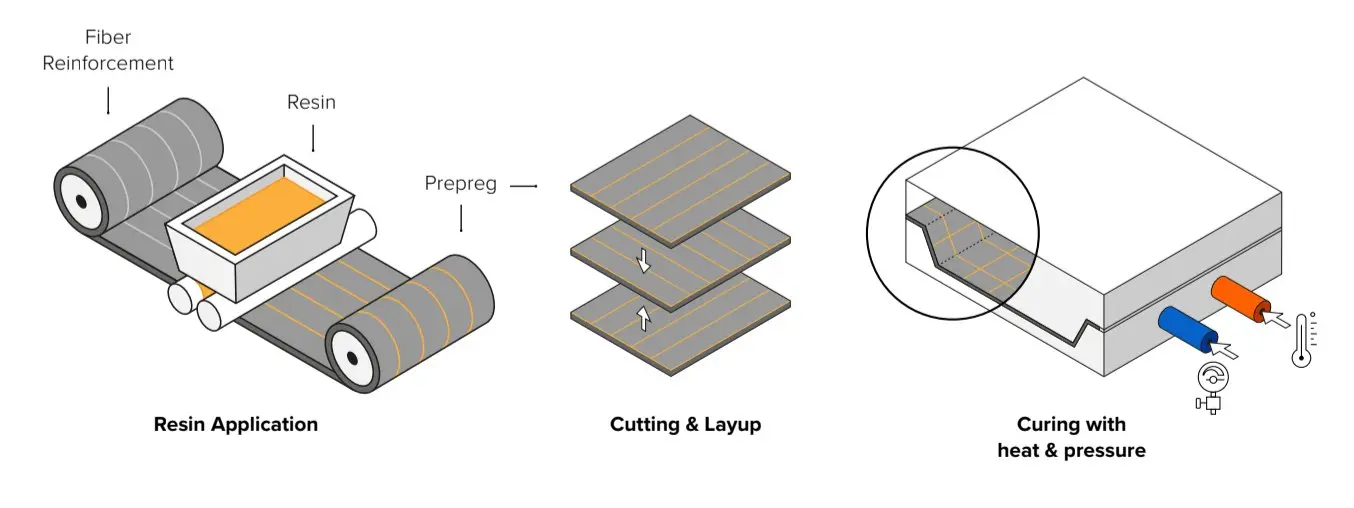
Moulage par transfert de résine (RTM, Resin Transfer Molding)
Avec le moulage par transfert de résine, la fibre sèche est insérée dans un moule en deux parties. Le moule est refermé avant l'injection à haute pression de la résine dans la cavité. Cette technique est généralement automatisée et utilisée pour la fabrication à grande échelle.
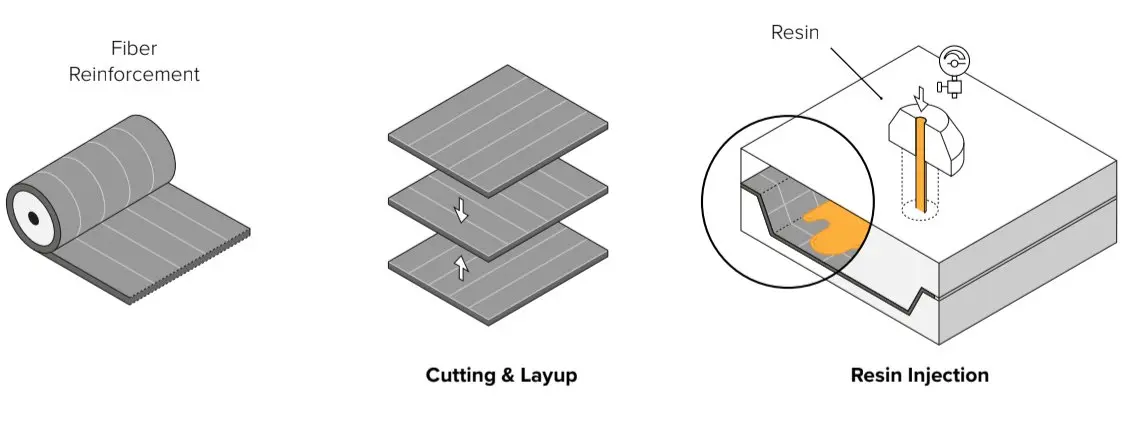
La fabrication de pièces en fibre de carbone avec des moules imprimés en 3D
Pour chacune des trois méthodes précédentes, l'impression 3D peut être utilisée pour réduire les coûts et les délais. Ces trois méthodes de fabrication traditionnelles nécessitent l'utilisation d'un ou plusieurs moules qui sont généralement créés par des procédés soustractifs chronophages, tels que l'usinage du bois, de la mousse, du métal, du plastique ou de la cire. L'impression 3D offre un autre moyen de fabriquer des moules. Les moules imprimés en 3D sont personnalisables, plus efficaces et plus rentables pour la production de petites séries personnalisées.
Pour les applications nécessitant des prototypes fonctionnels comme par exemple dans les industries automobile et aérospatiale, le processus itératif peut nécessiter des centaines de moules différents. La réalisation de ces itérations à l'aide des méthodes de fabrication traditionnelles peut être longue et coûteuse. L'impression 3D constitue donc un moyen efficace de produire de petits volumes. Bien que les moules imprimés en 3D ne soient pas aussi adaptés à la production de grandes séries que les moules en métal, ils peuvent être créés à peu de frais en interne, ce qui accélère le développement et la validation des produits ainsi que la production de petites séries.
Les moules pour la production de pièces en fibre de carbone peuvent être réalisés à l'aide de diverses techniques, mais la finition de surface lisse et la vaste gamme de matériaux des imprimantes 3D stéréolithographiques (SLA) les rendent parfaites pour la production de moules en interne. Les pièces SLA ne présentent pratiquement aucune ligne de couche ni aucune porosité, de sorte que les feuilles de fibre de carbone peuvent être pressées fermement dans le moule sans créer une surface texturée.
Panoz, un fabricant de voitures de course, a dû fabriquer un conduit d’évacuation d’air pour le cockpit d’une voiture de course personnalisée afin d’évacuer l’air de l’habitacle et de faire baisser la température intérieure. En collaboration avec DeltaWing Manufacturing, ils eu recours à une imprimante 3D SLA Formlabs pour imprimer le modèle avec High Temp Resin. Ils ont ensuite coulé un moule sur ce modèle imprimé en utilisant de l'époxy haute température. Grâce à l'impression 3D, DeltaWing a pu éviter de sous-traiter un moule métallique coûteux pour réaliser cette pièce en fibre de carbone personnalisée, ce qui a permis de réduire à la fois le coût global et les délais de livraison.
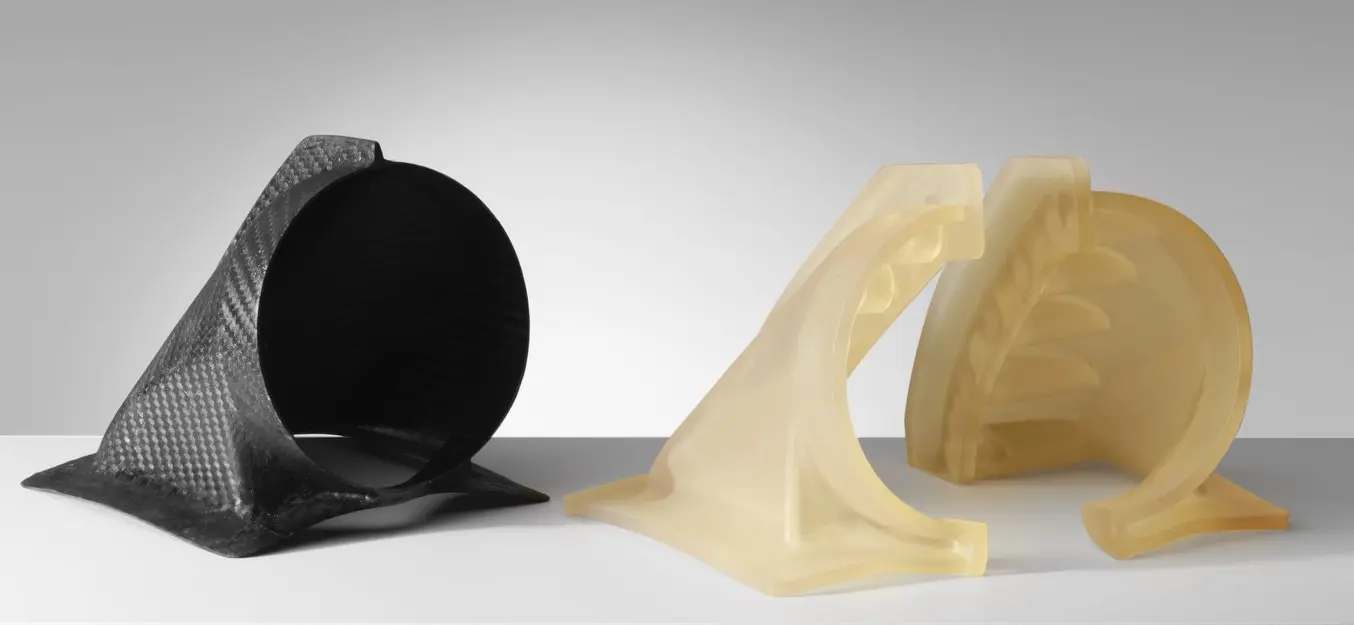
Un conduit d’aération d’aile en fibre de carbone à côté du moule en deux parties imprimé avec High Temp Resin, produit par DeltaWing Manufacturing.
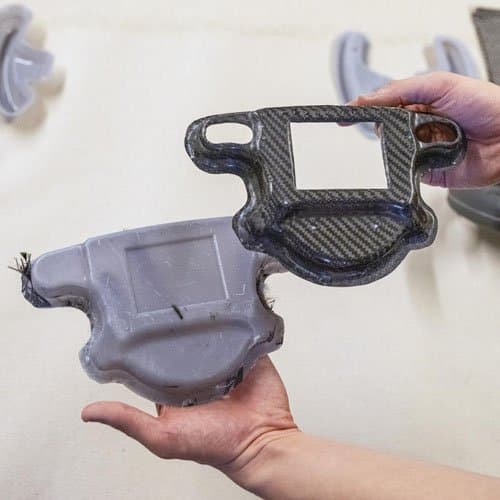
La fabrication de pièces en fibre de carbone avec des moules imprimés en 3D
Téléchargez ce livre blanc pour obtenir des instructions de conception de moules ainsi que des guides étape par étape concernant les méthodes de pré-imprégnation et de laminage manuel pour créer des pièces en fibre de carbone.
Impression 3D directe de fibre de carbone
Vous recherchez la meilleure imprimante 3D à fibre de carbone ? Il existe une forte demande pour des flux de travail combinant la résistance, la durabilité et la robustesse des pièces traditionnelles en fibre de carbone avec l'agilité, les possibilités géométriques et la répétabilité de l'impression 3D. Il n'est donc pas surprenant que de nombreuses entreprises proposent l'impression 3D de fibre de carbone, les deux procédés actuellement disponibles étant l'impression avec des fibres coupées ou continues.
Impression 3D de fibres de carbone coupées
Les fibres coupées font référence à un matériau plastique composite d'impression 3D imprégné de petits morceaux de fibres de carbone. Ces fibres coupées confèrent une résistance supplémentaire au composite, qui peut être un filament de fibre de carbone pour l'impression par dépôt de fil fondu (FDM) ou une poudre de nylon pour l'impression 3D à frittage sélectif par laser (SLS).
Par rapport aux autres types de matériaux d'impression 3D à base de polymères, les principaux avantages des matériaux d'impression 3D renforcés de fibres de carbone coupées sont qu'ils sont solides, légers, résistants à la chaleur et moins susceptibles de se déformer. Par rapport aux pièces en fibre de carbone moulées de manière traditionnelle, la fibre coupée offre une meilleure flexibilité géométrique dans la conception de la pièce en particulier pour l'impression 3D SLS, ce qui permet de réduire la main-d'œuvre importante requise par le moulage traditionnel et d'offrir aux utilisateurs de nouvelles possibilités innovantes pour incorporer ce matériau dans leur flux de travail.
L'imprimante 3D SLS Fuse 1+ 30W de Formlabs permet d'imprimer des pièces en fibre de carbone grâce à Nylon 11 CF Powder, le matériau le plus résistant dans la gamme de matériaux SLS de Formlabs. La Fuse 1+ 30W est l'option haute performance la plus abordable pour l'impression SLS de fibres de carbone coupées. Bien que les machines SLS industrielles traditionnelles offrent également certains matériaux en fibre de carbone, leur coût de départ élevé annule la plupart de leurs avantages par rapport aux méthodes RTM ou de stratification de préimprégné.
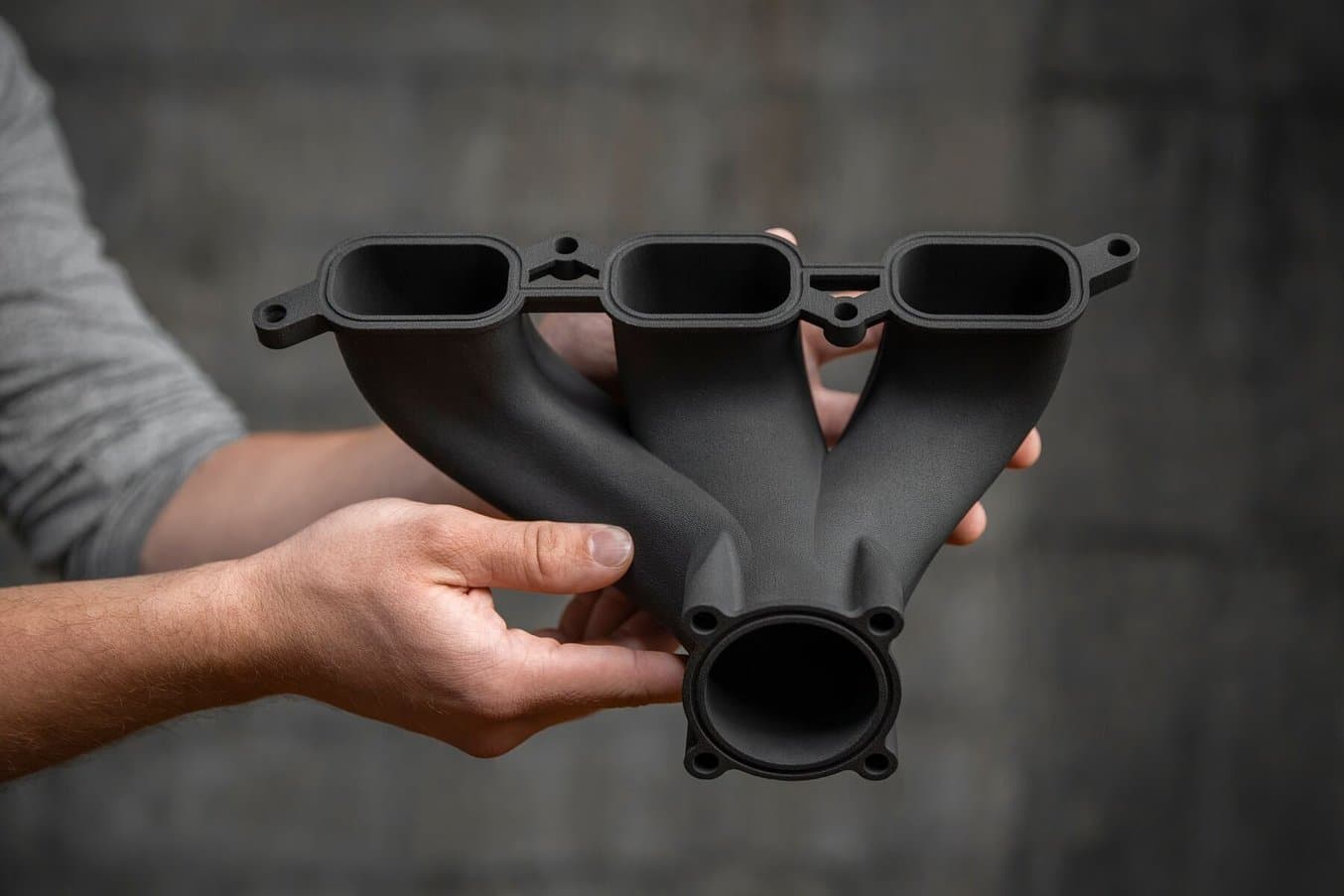
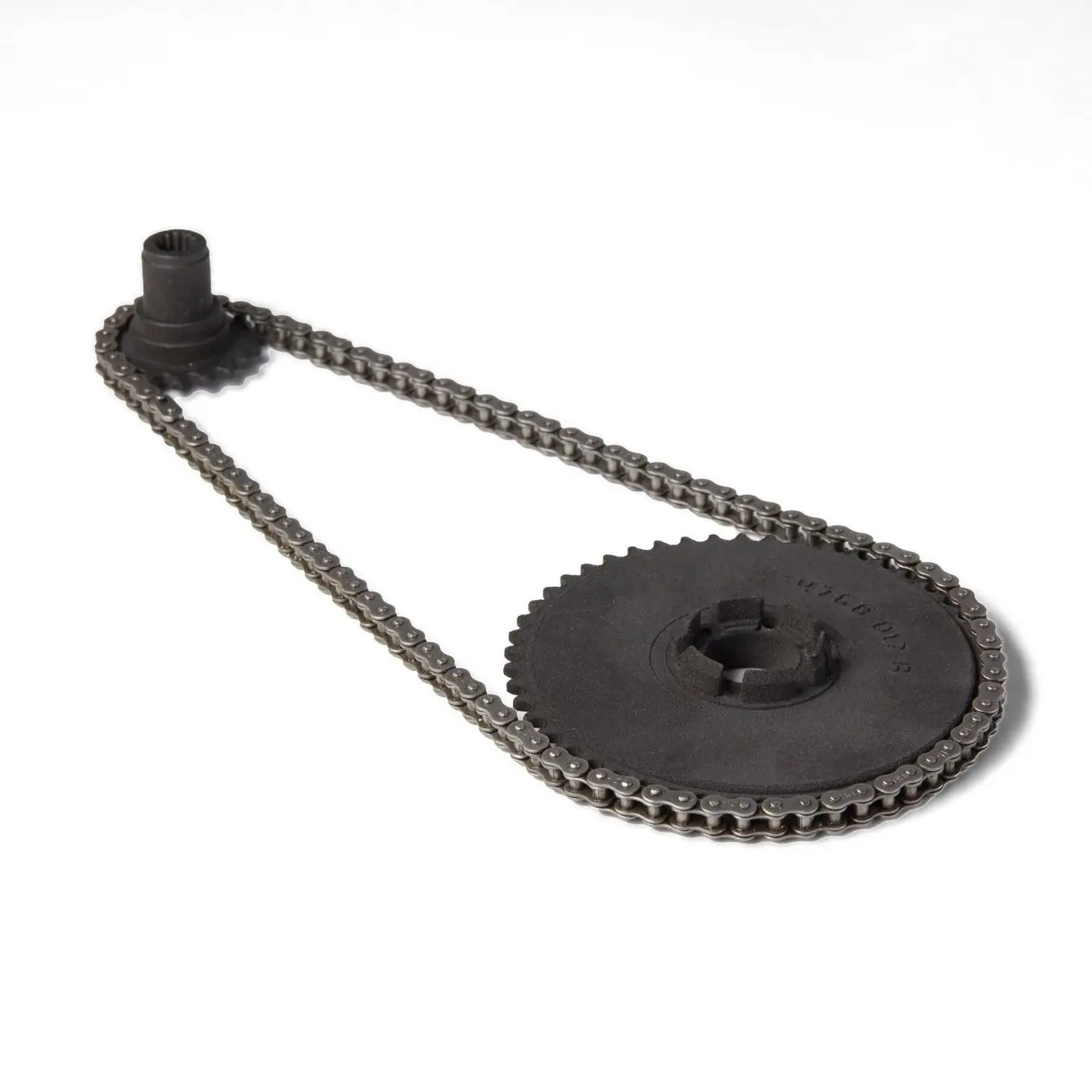
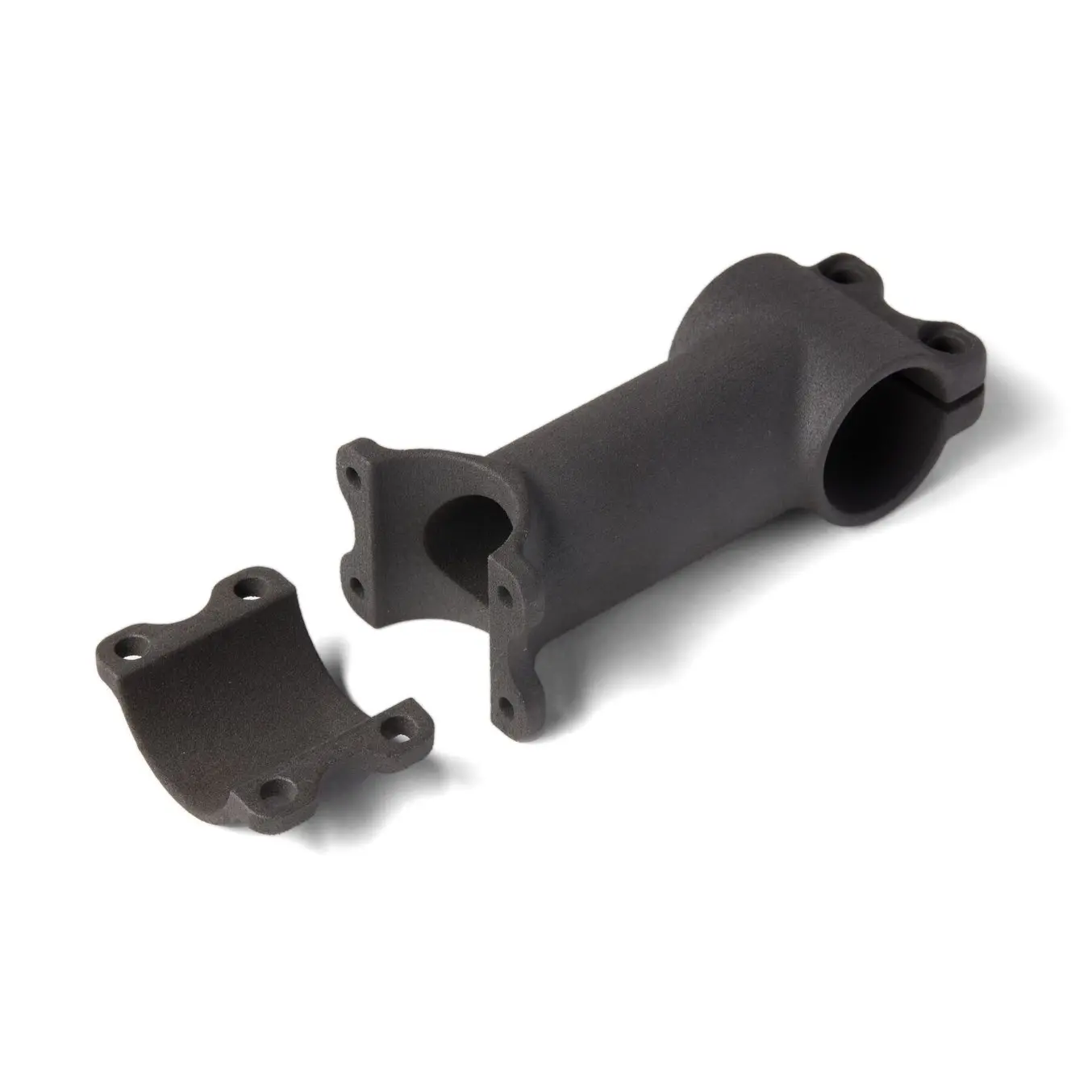
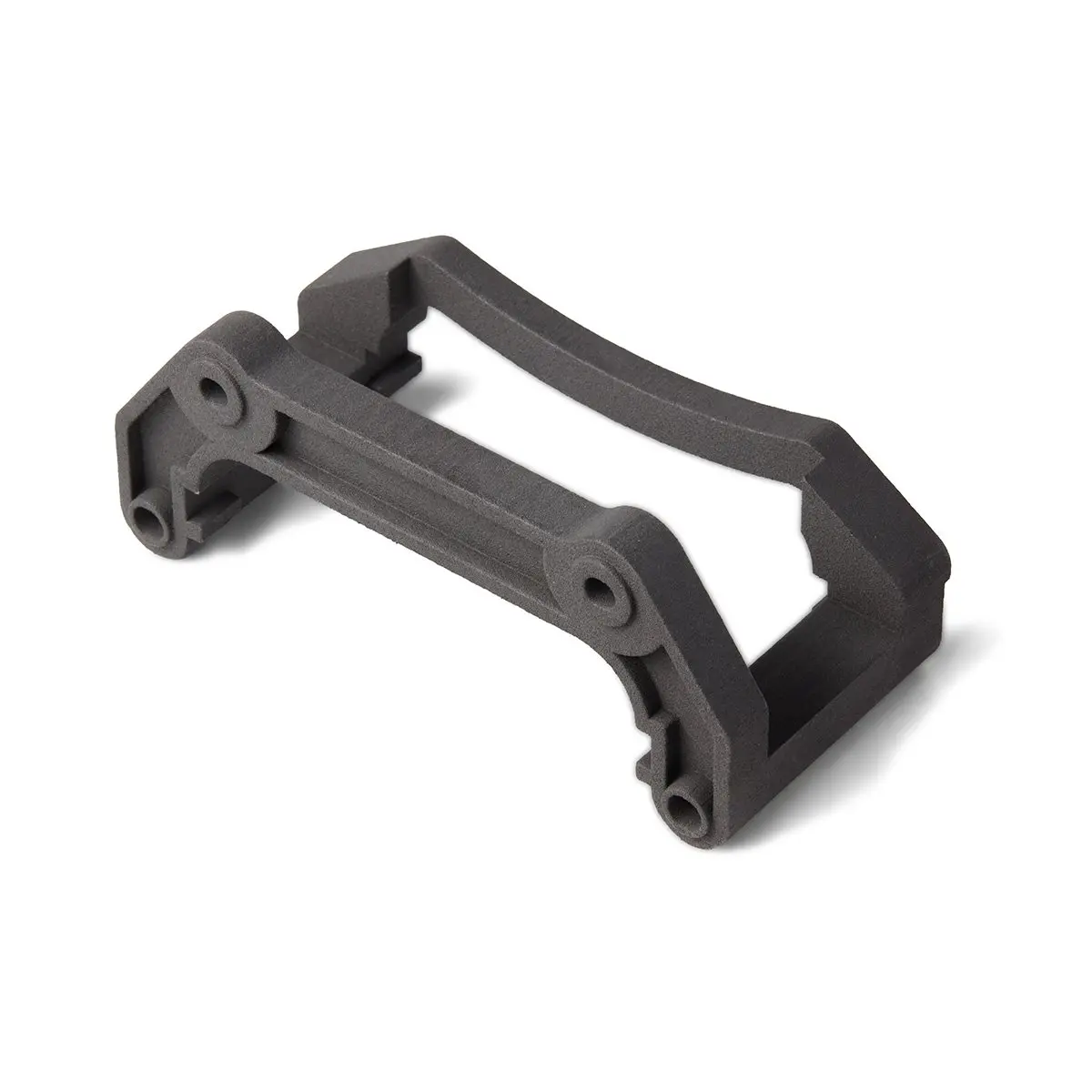
Nylon 11 CF Powder de Formlabs est solide, légère et résistante à la chaleur, ce qui la rend idéale pour les applications automobiles, aérospatiales et de production industrielle.
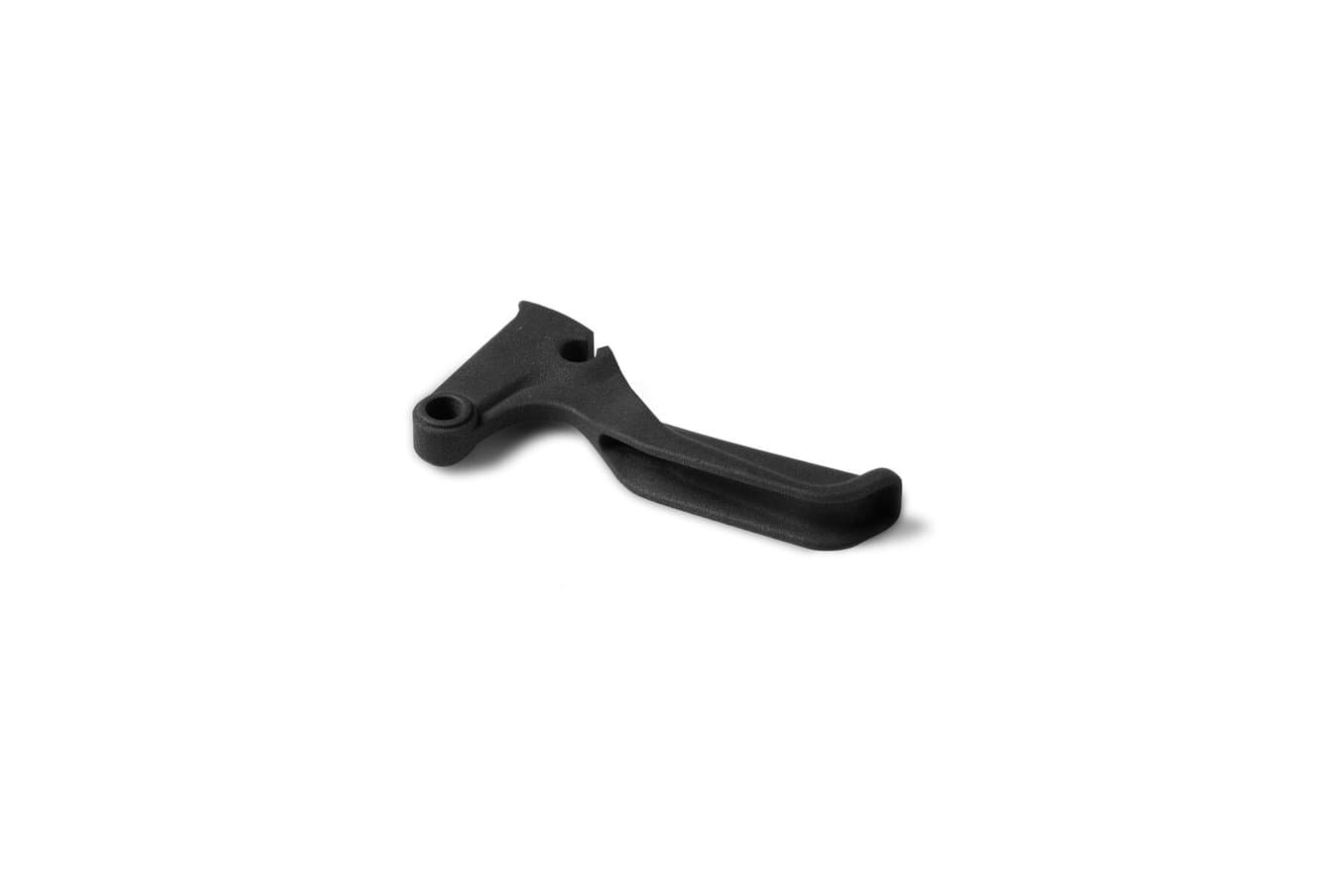
Commander un échantillon gratuit
Examinez et constatez par vous-même la qualité Formlabs. Nous enverrons un échantillon gratuit à votre bureau.
De nombreuses imprimantes 3D FDM peuvent fonctionner avec des filaments en fibre de carbone, mais l'impression avec ces matériaux est plus compliqué qu'avec des filaments ABS ou PLA standard : le filament abrasif use les buses en laiton, ce qui entraîne des colmatages fréquents et davantage de maintenance. Des imprimantes 3D FDM spécialement conçues pour les filaments de fibre de carbone coupés sont également disponibles, mais leur prix est élevé.
La principale limite des pièces en fibre coupée imprimées par SLS et FDM est qu'elles doivent être considérées comme des pièces résistantes et non comme de véritables alternatives aux pièces traditionnelles en fibre de carbone avec des fibres entrelacées et continues. Elles peuvent offrir une résistance bien plus élevée en fonction de la direction dans laquelle elles sont orientées lors de l'impression 3D : direction X pour les pièces SLS et plan XY pour les pièces FDM. Les méthodes traditionnelles de création de pièces en fibre de carbone permettent d'obtenir une résistance multidirectionnelle grâce à la planification et au placement minutieux de différentes feuilles de fibre de carbone dans la configuration du pré-moule.
Impression 3D de fibres de carbone continues
L'impression 3D de fibres de carbone continues est disponible sur certaines imprimantes 3D FDM spécialisées, et les pièces produites peuvent avoir une résistance similaire à celle des pièces traditionnelles en fibre de carbone, mais comme avec les imprimantes FDM pour fibres coupées, uniquement sur le plan XY. Avec ces imprimantes, des brins continus de fibre de carbone sont mélangés au thermoplastique, et les brins peuvent être appliqués de manière stratégique pour renforcer de manière sélective certains plans ou axes de pression. Cette méthode peut utiliser soit une double buse d'extrusion pour déposer une combinaison de fils de fibre de carbone et de polymère, soit deux buses combinées, auquel cas une buse dépose le fil de fibre de carbone tandis que l'autre chauffe et extrude le filament.
L'impression 3D de fibres de carbone continues offre une alternative comparable aux pièces en fibre de carbone moulées traditionnelles, bien que la liberté de conception soit limitée. Ces pièces sont incroyablement résistantes, mais cette résistance n'existe que dans le plan XY, et les impressions doivent être orientées pour que cette résistance corresponde à la direction de la force appliquée. Pour les conceptions adaptées, cette méthode peut être utilisée pour remplacer les pièces en aluminium et pour créer des aides à la fabrication ou des pièces d'utilisation finale robustes.
Comparaison : fabrication traditionnelle de fibres de carbone et flux de travail pour l'impression 3D de fibres de carbone
Stratification en voie humide | Stratification de préimprégnés | Moulage par transfert de résine | Impression 3D FDM de fibres coupées | Impression 3D SLS de fibres coupées | Impression 3D FDM de fibres continues | |
---|---|---|---|---|---|---|
Fabricant et modèle | Divers | Divers | Divers | Markforged Onyx, Markforged X3 | Fuse 1+ 30W de Formlabs | Markforged Mark Two, Desktop Metal Fiber, Markforged X7 |
Précision | ★★★☆☆ | ★★★★★ | ★★★★★ | ★★★☆☆ | ★★★★★ | ★★★☆☆ |
Finition de surface | ★★★☆☆ | ★★★★★ | ★★★★★ | ★★★☆☆ | ★★★★☆ | ★★★☆☆ |
Liberté de conception | ★★★☆☆ | ★★★☆☆ | ★★★☆☆ | ★★★★☆ | ★★★★★ | ★★★★☆ |
Léger | ★★★★★ | ★★★★★ | ★★★★★ | ★★★★☆ | ★★★★☆ | ★★★★☆ |
Résistance | ★★★★★ | ★★★★★ | ★★★★★ | ★★★☆☆ | ★★★☆☆ | ★★★★★ |
Résistance en fonction de la direction | XYZ | XYZ | XYZ | XY | X(Y) | XY |
Volume de production | ★☆☆☆☆ | ★★★☆☆ | ★★★★★ | ★★★☆☆ | ★★★★☆ | ★★★☆☆ |
Coût de l'équipement (spécifique) | Variable, à partir de <100 € | Variable, démarrant à <3000 € | Variable, généralement 100 000 € et plus | Les solutions de bureau commencent à 5000 €, les solutions industrielles à environ 40 000 €. | Solution industrielle complète à partir de 37 243 €. | Les solutions de bureau commencent à 20 000 €, les solutions industrielles à environ 70 000 €. |
Coût par pièce | $$$$ | €€€ | €€ | €€€ | €€ | $$$$ |
Idéal pour | Produits personnalisés haute performance, flux de travail d'entrée de gamme | Production de petits ou moyens volumes | Production de gros volumes | Itérations rapides, pièces solides imprimées en 3D | Itérations rapides, géométries complexes, production en petites séries de pièces solides imprimées en 3D | Itérations rapides, pièces imprimées en 3D aussi solide que les composites traditionnels à base de fibres de carbone (dans le sens XY) |
Avantages | Haute résistance Faible coût d'équipement | Haute résistance | Haute résistance Précision et répétabilité Possibilités d'automatisation | Peu coûteux Aucun outil n'est nécessaire | Précision et répétabilité Liberté de conception Aucun outil n'est nécessaire | Haute résistance Aucun outil n'est nécessaire |
Inconvénients | Requiert beaucoup de main d'oeuvre Difficile de maintenir une qualité élevée | Requiert beaucoup de main d'oeuvre | Outillage et machines coûteux | Résistance anisotrope Résistance moindre Difficile à imprimer | Résistance anisotrope Résistance inférieure | Résistance anisotrope |
Les pièces en fibre de carbone imprimées en 3D sont-elles solides ?
Les propriétés mécaniques des composites en fibre de carbone imprimés en 3D dépassent celles de presque tous les autres plastiques imprimés en 3D en termes de solidité et de résistance à la température. Voyons comment l'impression 3D de fibres coupées se compare à l'impression 3D de fibres continues et de matériaux courants.
Processus de fabrication | SLS - Fibres coupées | FDM - Fibres coupées | FDM - Fibres continues | FDM - Fibres continues | Moulage par injection | Moulage ou usinage |
---|---|---|---|---|---|---|
Matériau | Nylon 11 CF Powder de Formlabs | Filament de nylon renforcé de fibres de carbone | Filament de nylon 6 + Fibre de carbone | Filament PEEK + fibre de carbone | ABS | Aluminum |
Module de traction (GPa) | 1,6 - 5,3 | 2,4 | 60 - 100 | 145 | 2,3 | 70 |
Résistance à la rupture par traction (MPa) | 38 - 69 | 40 | 800 - 1000 | 2400 | 39 | 310 |
Module de flexion (GPa) | 4,2 | 3,0 | 51 - 71 | 124 | 2,4 | 70 |
Résistance à la flexion (MPa) | 110 | 71 | 540 - 800 | 1300 | 74 | 310 |
Allongement à la rupture | 5 - 15 % | 25 % | 1,5 % | N/A | 6 - 15 % | N/A |
Résistance au choc Izod (J/m) | 74 | 330 | 960 | N/A | 200 | N/A |
Température de fléchissement sous charge à 0,45 MPa (°C) | 188 | 145 | 105 | N/A | 70 - 107 | N/A |
Applications des pièces en fibre de carbone imprimées en 3D
La solidité, la légèreté, ainsi que la résistance aux chocs, à la chaleur et aux produits chimiques des pièces en fibre de carbone imprimées en 3D les rendent idéales pour toute une série d'applications pour lesquelles l'impression 3D n'était même pas envisagée auparavant. Les pièces en plastique et en composite de fibre de carbone imprimées en 3D peuvent désormais résister à la chaleur générée par les composants de moteurs automobiles ou aérospatiaux, être utilisées pour remplacer les pièces en aluminium usiné et les aides à la fabrication, et permettre la production d'équipements durables et résistants.
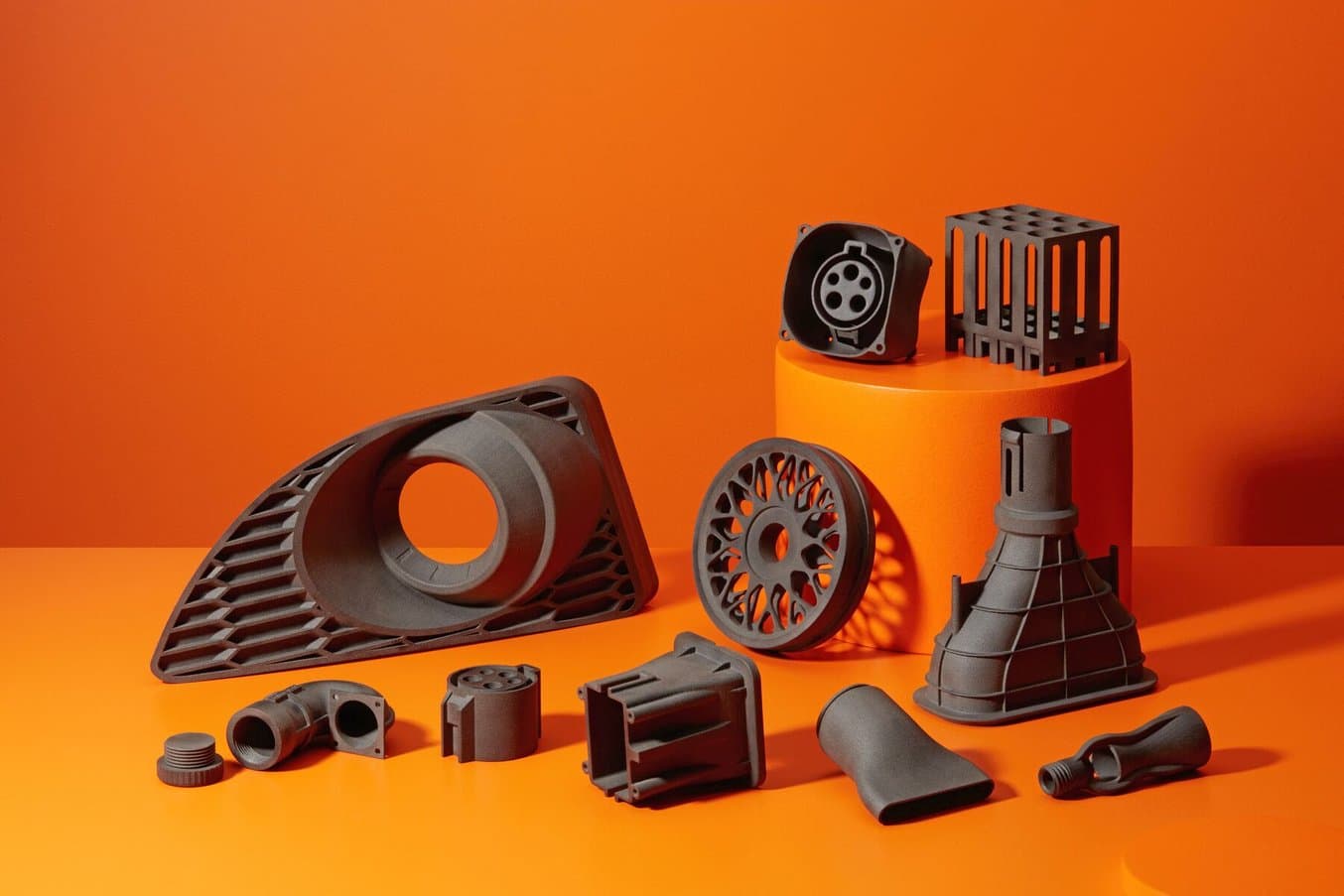
Les pièces en fibre de carbone imprimées en 3D sont idéales pour le prototypage rapide, la production d'aides à la fabrication résistantes à l'usure et durables telles que des gabarits et des fixations, et la production en petites séries de pièces finales solides et complexes.
L'impression 3D a ouvert de nouvelles possibilités en matière de conception et de fabrication, et les composites en fibre de carbone imprimés en 3D vont encore plus loin, permettant aux utilisateurs des secteurs de l'automobile, de l'aérospatiale, de la défense et de la fabrication industrielle de produire rapidement et efficacement des pièces très solides, résistantes à la température, et facilement modifiables. En évitant d'utiliser des processus traditionnels d'usinage ou de moulage, ces utilisateurs peuvent plus facilement créer des pièces personnalisées, des pièces de rechange et des prototypes fonctionnels. Bien qu'elles ne puissent pas remplacer totalement les pièces créées de manière traditionnelle, les pièces en fibre de carbone imprimées en 3D sont toujours plus solides que la plupart des autres plastiques, ce qui les rend très utiles dans de nombreuses applications.
Le bon procédé pour produire des pièces en fibre de carbone par moulage ou directement par impression 3D dépend fortement de l'application visée et de facteurs tels que la conception de la pièce, le volume de production, etc. L'impression 3D SLS avec des fibres coupées offre un équilibre parfait pour ceux qui cherchent à fabriquer des pièces solides, mais pas nécessairement aussi résistantes que les pièces en fibre de carbone moulées traditionnelles.
La Fuse 1+ 30W de Formlabs et Nylon 11 CF Powder permet aux entreprises ne disposant pas d'un budget important et soumises à des délais serrés d'itérer rapidement et de produire des pièces finales présentant une résistance et des propriétés mécaniques plus avancées que celles des plastiques traditionnels. Ces entreprises peuvent également faire passer des tests fonctionnels à leurs pièces puis modifier facilement la conception avec un logiciel CAO, ce qui leur permet d'améliorer les performances de leur produit et de le commercialiser plus rapidement.
Commandez un échantillon gratuit pour constater la qualité et la résistance d'une pièce en fibre coupée imprimée en 3D par SLS, ou contactez l'un de nos spécialistes pour trouver la solution adaptée à votre application.