En intégrant l'informatique et l'ingénierie, la robotique s'avère très prometteuse pour le secteur des soins de santé. Qu'il s'agisse de désinfecter les chambres des patients ou de servir d'assistants de laboratoire, les robots peuvent remplir toutes sortes de fonctions. Certaines procédures médicales à haut risque, comme les opérations chirurgicales, exigent une précision maximale. En Amérique du Nord, les erreurs médicales sont à l'origine de plus de 400 000 décès chaque année, ce qui en fait la troisième cause de décès non naturels après le cancer et les maladies cardiaques. Comment la robotique peut-elle aider ?
Chez Haply Robotics, une entreprise montréalaise fondée en 2018, les robots aident les chirurgiens à affiner les procédures chirurgicales. Haply Robotics fabrique des consoles de simulation nouvelle génération pour permettre à plus de deux millions de chirurgiens dans le monde de perfectionner près de 260 procédures chirurgicales, grâce à des technologies de pointe en matière de réalité virtuelle et augmentée. Surnommée la « PlayStation des chirurgiens », la console à retour de force inverse Haply permet aux chirurgiens de simuler des opérations avant de les réaliser, afin de réduire les risques pour les patients et la durée des interventions.
Haply Robotics a adopté l'impression 3D en interne pour réaliser le prototypage rapide, et utilise des imprimantes 3D FDM, SLA et SLS pour ses projets. Dans cet article, vous découvrirez comment l'équipe de Haply Robotics a utilisé diverses technologies d'impression 3D et pourquoi elle a acheté une Fuse 1.
Au commencement : le développement de respirateurs pour COVID-19
Felix Desourdy, responsable de l'ingénierie mécanique chez Haply Robotics, a rencontré Colin Gallacher et Steve Ding, cofondateurs de Haply Robotics, en 2018. « Nous nous sommes rencontrés au Conseil national de la recherche du Canada, où nous travaillions dans une équipe chargée du développement haptique pour la simulation chirurgicale. Nous étions tous très enthousiastes à l'idée de pouvoir concevoir quelque chose et d'en créer rapidement plusieurs prototypes pour obtenir exactement le résultat voulu. »
En 2020, l'un de ses projets avec le gouvernement canadien ayant été suspendu, l'équipe a décidé de mettre à profit ses compétences en conception et en robotique en participant au Défi Respirateur Code Vie. Ce concours a fait appel aux fabricants de dispositifs pour concevoir un respirateur peu coûteux, simple, facile à utiliser et à fabriquer, qui pourrait servir aux patients souffrant de COVID-19.
Plus de 2600 inscriptions ont été reçues, représentant plus de 1000 équipes de 94 pays. Le modèle de Haply a remporté le concours en raison de la simplicité de sa conception et de son fonctionnement, de son faible coût de production et de sa prise en main facile.
« Le Défi Respirateur Code Vie nous a demandé beaucoup d'efforts, mais c'est l'une des expériences les plus enrichissantes que nous ayons vécues en tant qu'équipe. Nous avons été motivés par la problématique des disparités entre les pays développés et les pays en développement en matière d’accès aux technologies médicales essentielles, comme les respirateurs – un enjeu qui a été mis en évidence par l'épidémie de COVID-19. Nous sommes incroyablement reconnaissants envers le comité organisateur, et plus particulièrement envers le Pr Reza Farivar, la Fondation de l’Hôpital général de Montréal, l’IR-CUSM et la Faculté d'ingénierie de McGill pour avoir mis sur pied une initiative aussi pertinente », a déclaré Colin Gallacher, cofondateur de Haply Robotics.
Haply a eu recours à l'impression 3D pour développer le respirateur, et a utilisé la Form 3 et Tough Resin pour fabriquer les composants internes de la machine. L'impression 3D en interne a permis à l'équipe de créer des pièces finales pour l'intérieur du respirateur, ce qui a permis d'élaborer rapidement une conception capable de remporter le concours et de rendre ces dispositifs plus accessibles pendant la pandémie.
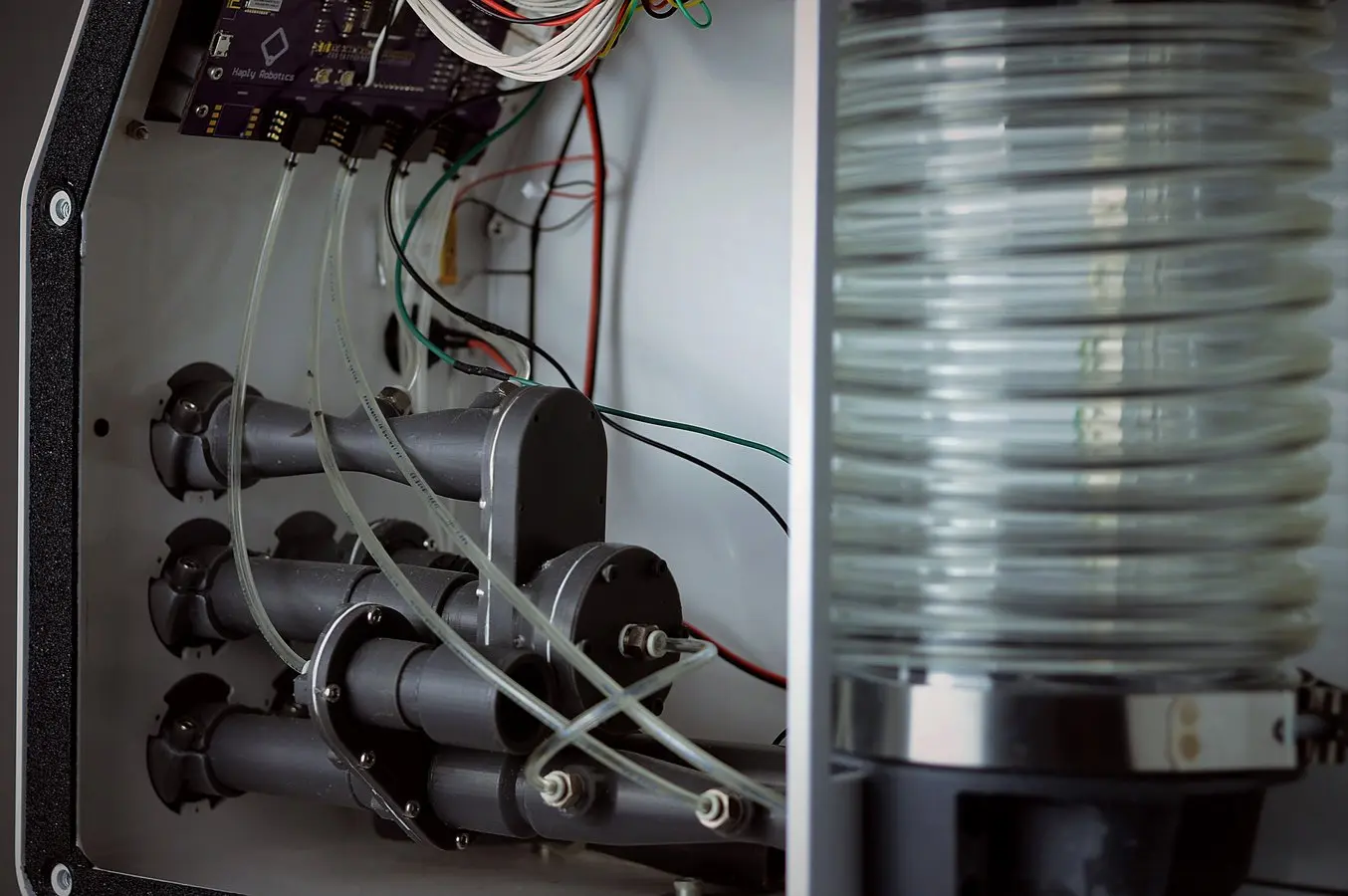
Les composants internes du respirateur Haply imprimés en 3D.
« Tough Resin convenait parfaitement pour ce projet, car elle peut être scellée. Nous pouvions forer et insérer des raccords dans la résine sans qu'il y ait de fuite. Elle est très similaire à l'ABS », a déclaré M. Desourdy.
Prototypage rapide de la conception parfaite
Forte de son expérience acquise pendant le développement du respirateur, l'équipe a continué à travailler sur son projet principal : le développement haptique pour la simulation chirurgicale.
Le prototypage rapide est la raison principale pour laquelle Haply a investi dans l'impression 3D en interne. Grâce aux imprimantes de bureau, l'équipe peut imprimer plusieurs versions de pièces complexes jusqu'à trouver la forme parfaite. Pour M. Desourdy, il est essentiel d'itérer pour pouvoir obtenir une forme et une ergonomie optimales. Il déclare en effet que « la technologie a révolutionné les méthodes de conception : nous pouvons créer tous les prototypes que nous souhaitons jusqu'à trouver la forme parfaite. Tout ce que nous fabriquons a la taille idéale pour être imprimé en 3D. »
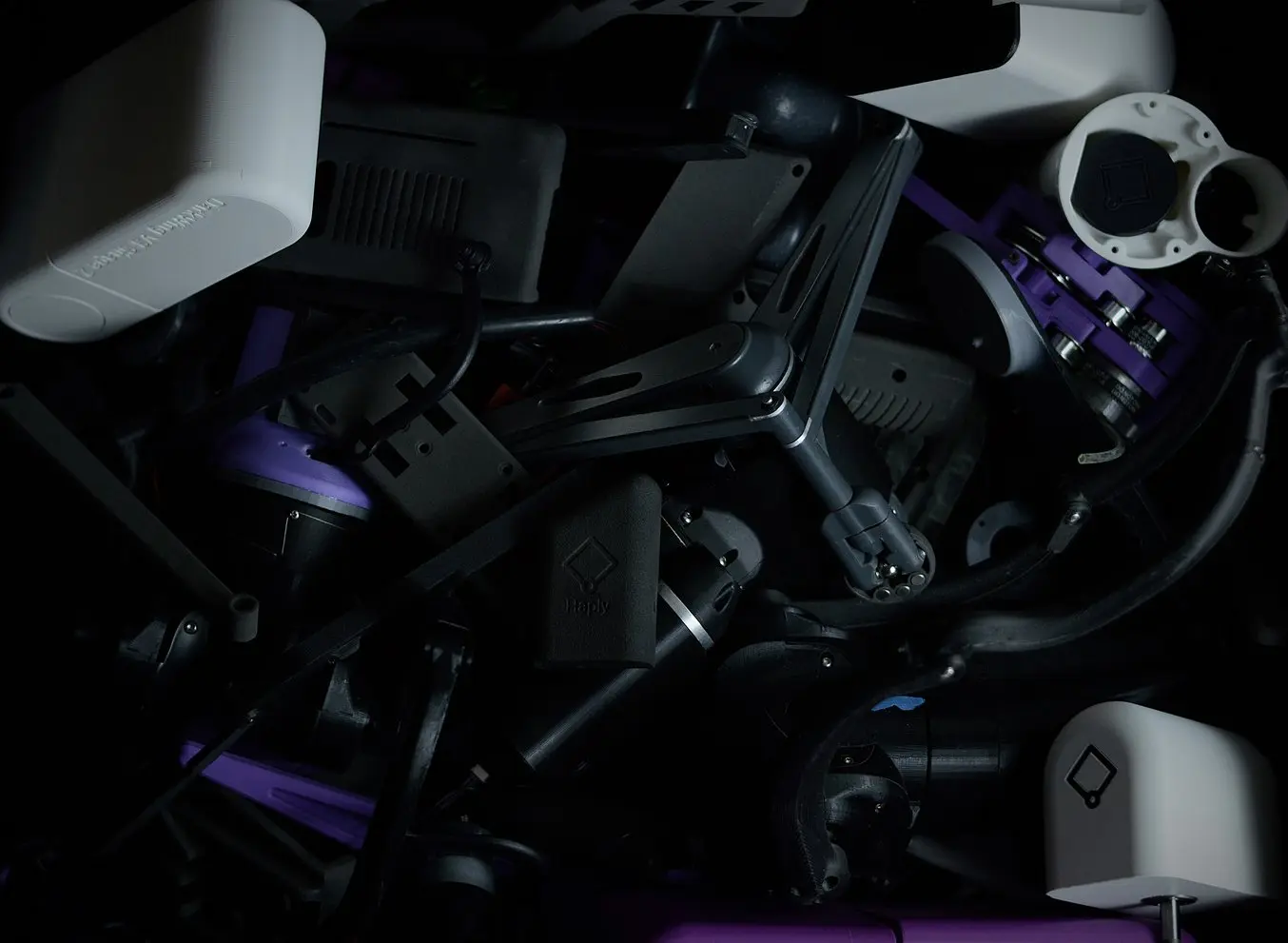
Haply a réalisé des dizaines d'itérations pour sa console de simulation à retour de force inverse.
L'équipe a d'abord investi dans des imprimantes FDM, en raison de leur faible coût et de leur rapidité d'impression. Au début, ces machines répondaient aux objectifs de l'équipe en matière de prototypage rapide. Mais au fil du temps, l'équipe a voulu fabriquer des prototypes plus esthétiques et plus fonctionnels qui nécessitaient une impression de meilleure qualité. Elle a fini par acheter une Form 2, puis une Form 3 pour une impression haute résolution.
« Nous avons besoin de pièces d'une grande précision, notamment pour le simulateur chirurgical. Nous devons être capable d'itérer, encore et encore », a déclaré M. Desourdy. « Nous avons réalisé beaucoup d'itérations pour rendre notre dispositif plus rigide. Nous avons d'abord cherché à trouver une forme adaptée, sans modifier le matériau. Notre façon de faire est celle-ci : nous itérons pour optimiser la forme de la pièce, et quand cette étape est terminée, il suffit de changer le matériau pour obtenir quelque chose de plus rigide. C'est l'adaptation de la forme qui nous prend le plus de temps et d'efforts. »
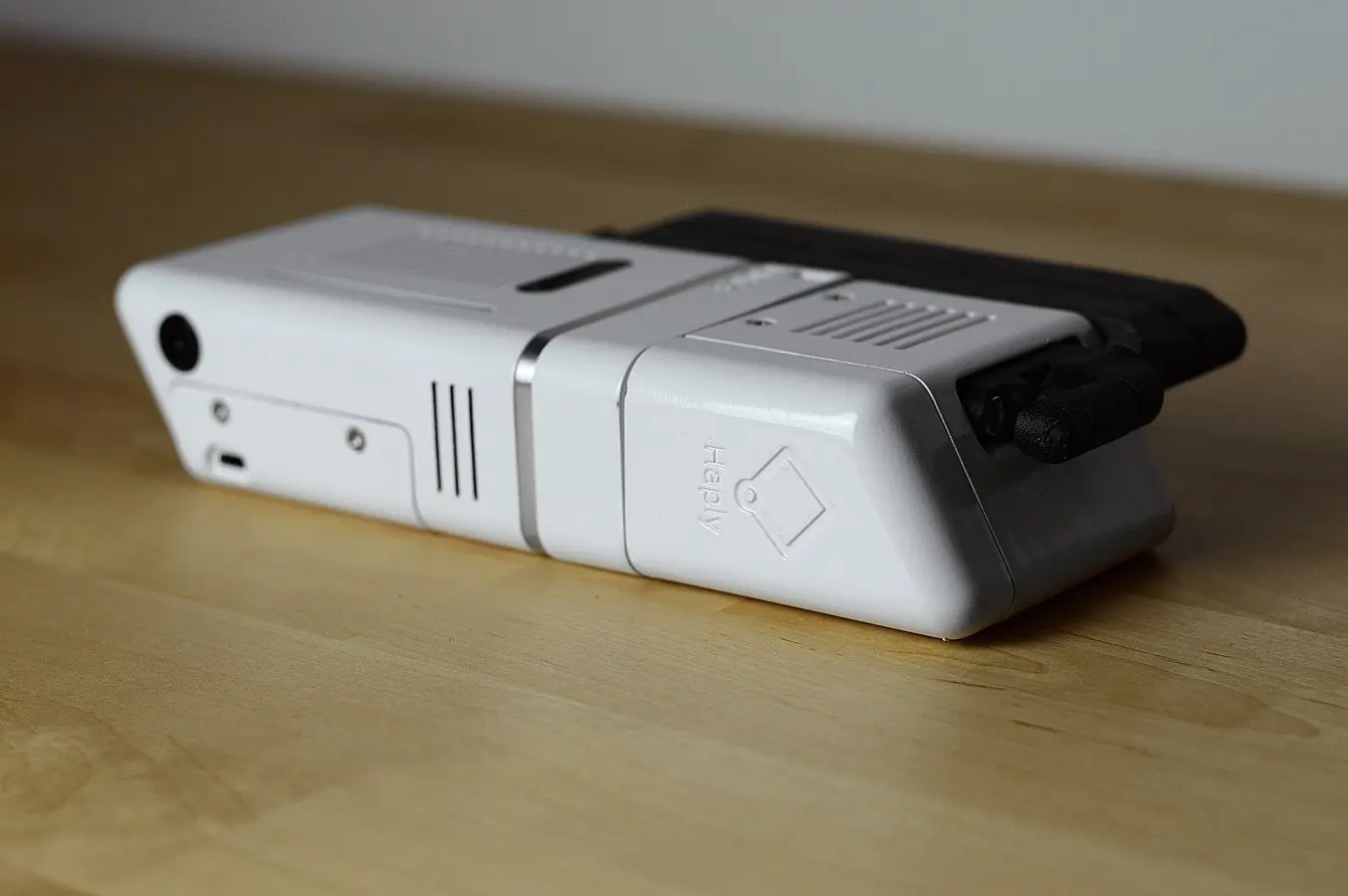
Le bras robotique fermé.
Prototypage de pièces finales avec la Fuse 1
Tandis que l'équipe de Haply Robotics continuait à fabriquer des prototypes pour son bras robotique, elle a décidé d'adopter l'impression 3D SLS en interne avec la Fuse 1. En effet, les pièces en nylon imprimées sur la Fuse 1 sont plus similaires au produit final développé par l'équipe. Auparavant, ils sous-traitaient la production de pièces en nylon, ce qui posait de nombreux problèmes. « Avec la Fuse 1, le prototypage a changé du tout au tout. Nous pouvons fabriquer une pièce en deux jours au lieu de cinq, et les pièces en nylon sont plus similaires au produit final. Ayant l'imprimante dans nos locaux, nous pouvons mieux nous rendre compte de la tolérance de la machine et des matériaux. Le processus gagne en précision, ce qui est un net avantage », a déclaré M. Desourdy.
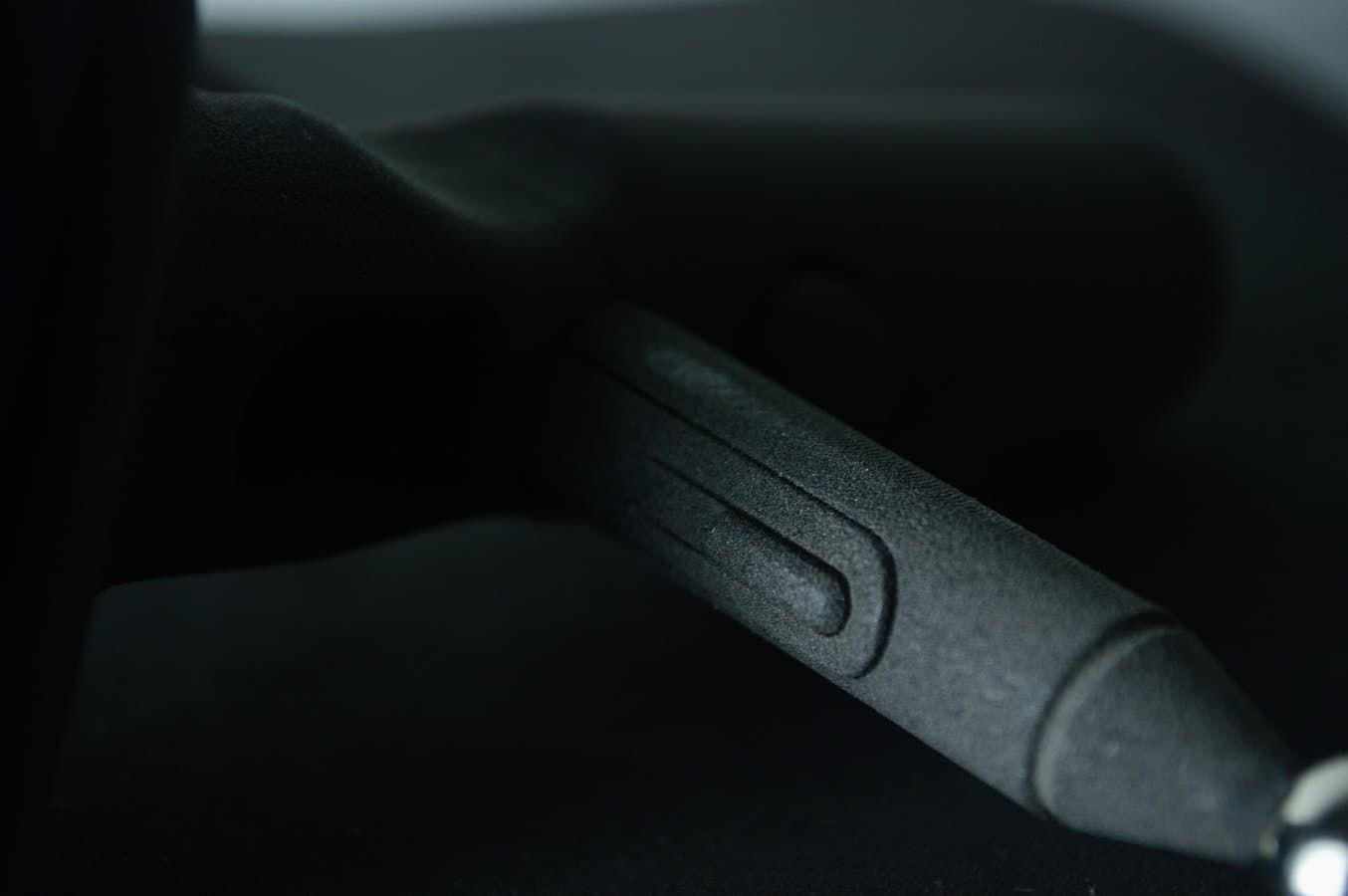
L'équipe a pu imprimer un bouton fonctionnel à l'aide de la Fuse 1.
M. Desourdy ajoute que passer par un sous-traitant l'empêche d'avoir le contrôle désiré sur le résultat final. « Lorsque vous envoyez votre conception au sous-traitant, l'orientation ou la spécification n'est pas forcément optimale, et vous ne connaissez pas l'imprimante dont disposera l'agence ni la façon dont ils l'entretiennent. Vous ne pouvez donc pas savoir quel résultat vous obtiendrez », a-t-il déclaré. « Je pense vraiment que le fait de pouvoir itérer si rapidement nous donne une belle longueur d'avance. »
Un autre point important à prendre en considération pour les petites entreprises en pleine croissance comme Haply Robotics est l'espace disponible dans les locaux, souvent assez restreint. La plupart des imprimantes 3D SLS traditionnelles prennent beaucoup de place, et il est souvent difficile de trouver l'espace nécessaire à leur installation. La Fuse 1 offre une taille relativement compacte, et son rendement est élevé. « Ce qui est bien avec la Fuse 1, c'est qu'elle n'est pas très grande. Elle prend plus de place qu'une imprimante 3D de bureau ordinaire, mais honnêtement, si vous la comparez à n'importe quelle machine industrielle utilisée pour ce type de production, elle est très petite », a déclaré M. Desourdy. Selon lui, l'équipe a envisagé d'investir dans une imprimante SLS HP, mais la grande taille de la machine ne lui convenait pas. Il a ajouté : « Quand vous commencez à passer en revue des machines de qualité industrielle, vous vous rendez compte que la Fuse 1 est petite par rapport à ce qui existe sur le marché. »
Jessica Henry, responsable de produit chez Haply, a déclaré qu'imprimer en 3D avec la Fuse 1 optimise et automatise leur processus de travail. Selon Mme Henry, la capture des détails, même infimes, est essentielle pour l'impression 3D. « Il suffit qu'un seul petit détail soit modifié pour que le bras robotique fonctionne de façon plus fluide. Nous pouvons apporter de nouveaux changements à chaque impression », a déclaré Mme Henry. Grâce à la Fuse 1, l'équipe peut imprimer plusieurs pièces par cycle d'impression, ce qui permet d'augmenter le nombre de bras robotisés produits en même temps. Pour atteindre le même niveau de production, l'équipe devrait acheter plusieurs machines FDM, et les pièces produites ne seraient pas aussi performantes.
Enfin, un autre avantage majeur de la Fuse 1 par rapport aux imprimantes FDM et SLA est que les pièces n'ont pas besoin de structures de support.
M. Desourdy dit l'avoir remarqué immédiatement : « Si je conçois quelque chose pour une imprimante FDM, je sais qu'il me faut intégrer une surface plane qui soutiendra les supports, et qui sera donc moins belle. Il en va de même pour les imprimantes résine ; l'un des côtés de la pièce devra soutenir les supports. La Fuse 1 a changé ma façon de concevoir les pièces, car elle n'a pas besoin de supports. Quelle que soit l'orientation, le niveau de détail est le même. » Ce changement a même un impact sur le processus de conception. M. Desourdy déclare : « Je m'inquiète moins du processus d'impression 3D, et peux ainsi mieux me concentrer sur la conception. »
Pour rendre ses prototypes encore plus réalistes, l'équipe cherche des solutions pour teindre ou peindre les pièces post-traitées.
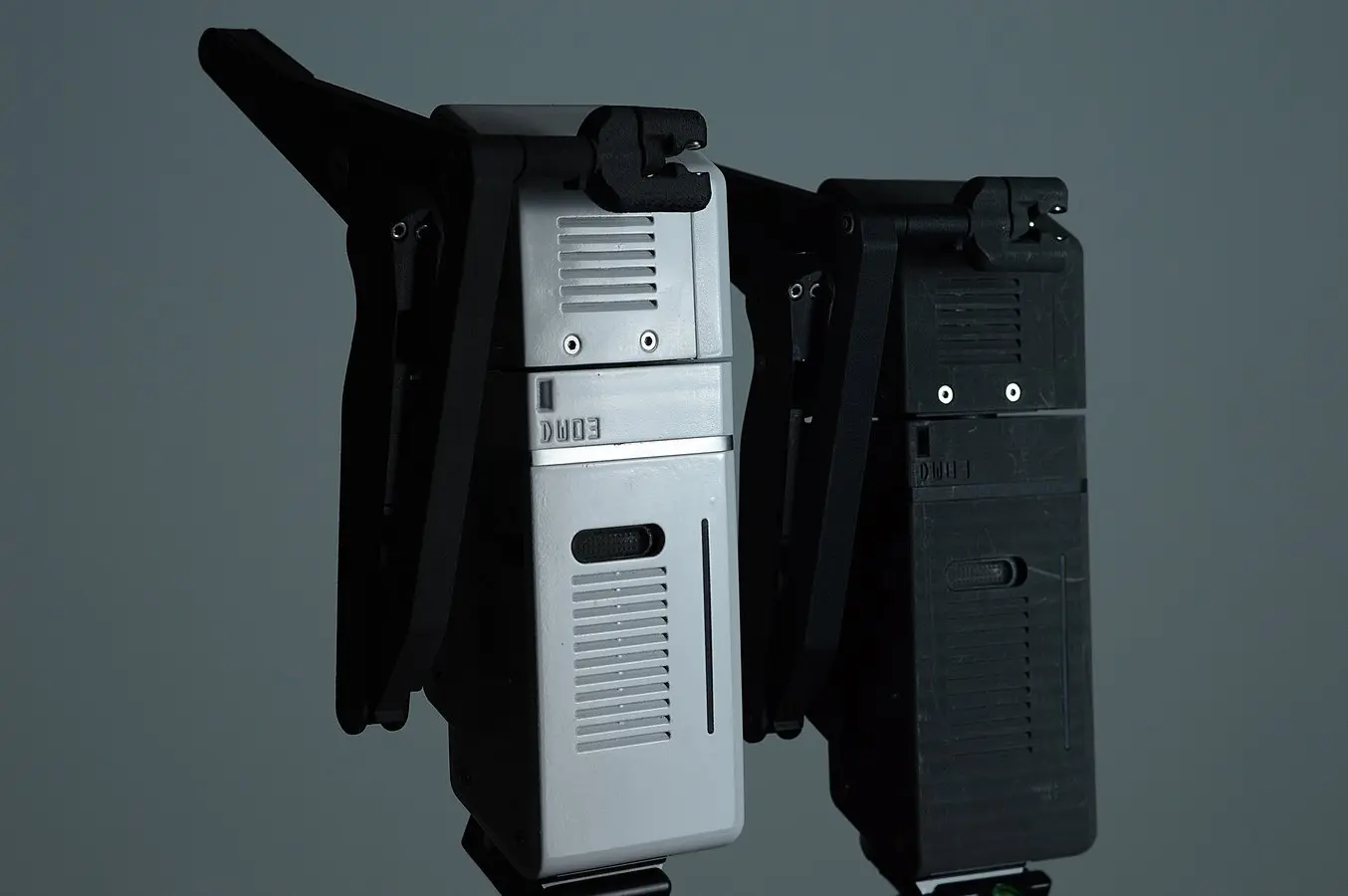
Le boîtier du bras robotique, imprimé en nylon et peint.
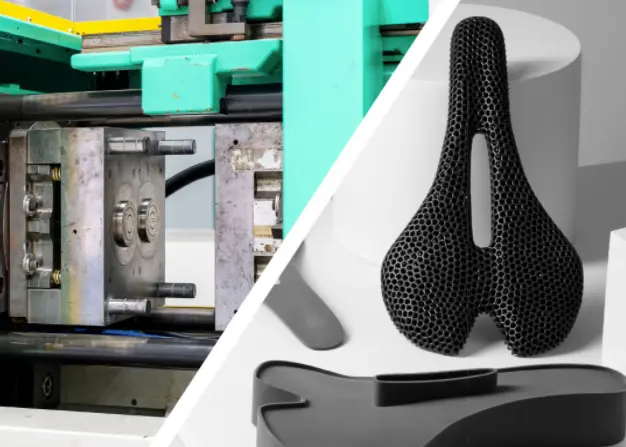
SLS 3D Printing vs. Injection Molding: When to Replace Molded Parts With 3D Printing?
This white paper showcases the cost-dynamics for real-life use cases, and presents guidelines for using SLS 3D printing, injection molding, or both.
En savoir plus sur la Fuse 1
Bien que la Fuse 1 soit actuellement utilisée pour le prototypage, Haply Robotics a l'intention de l'utiliser également pour fabriquer des pièces finales. « D'après mon expérience, la fabrication de petites séries ne devrait pas poser de problème particulier. Ça va être super intéressant. Certaines des pièces produites seront des prototypes, d'autres seront des pièces finales », a déclaré M. Desourdy. Mme Henry ajoute que « si l'on peut toujours ajouter ou modifier des pièces sur la machine, le produit ne sera jamais dépassé. »
La Fuse 1 est actuellement utilisée par plusieurs fabricants du secteur des soins de santé, notamment des entreprises de dispositifs médicaux. Des entreprises telles que Partial Hand Solutions et Tension Square ont également décidé d'intégrer l'impression 3D SLS en interne et utilisent la Fuse 1 pour créer des prothèses spécifiques aux patients, ainsi que des dispositifs pour traiter les pneumothorax.
« J’ai toujours voulu une imprimante SLS, mais la plupart sont hors de prix. La Fuse 1 est idéale pour une petite entreprise comme Partial Hand Solutions. »