Veteran and Paramedic Develops 3D Printed Device that Prevents Collapsed Lung Complications
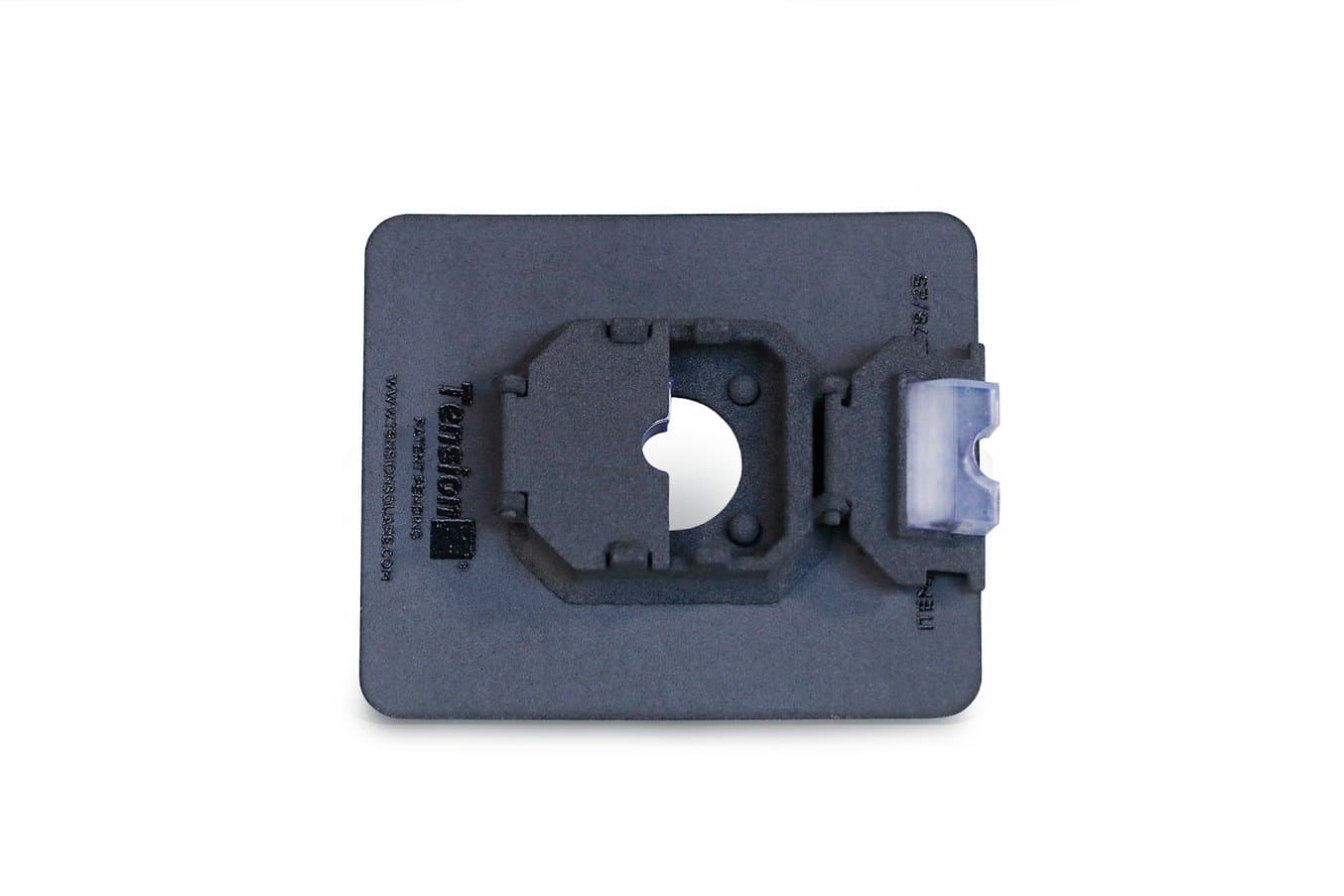
A pneumothorax (noo-moe-THOR-aks), or collapsed lung, occurs when air leaks into the space between the lung and chest wall. The air pushes on the exterior of the lung and causes either complete lung collapse or a collapse of only a portion of the lung.1 Often, a blunt or penetrating chest injury such as those in armed combat leads to collapsed lungs and associated symptoms including sudden chest pain, shortness of breath, and in some cases, death. Published literature has found that over 15% of all wartime injuries take place in the chest, and the most common life-threatening complications from both blunt and penetrating thoracic injury are hemothorax, pneumothorax, or a combination of both. 2 The standard prehospital treatment for a traumatic pneumothorax is needle thoracostomy to allow re-expansion of the lung. As these injuries often take place in the field and far from a hospital, “the therapeutic goal in the war scenario is to restore normal physiology and thereby to restore cardiac and pulmonary function and evacuate the patient after stabilization.” Unfortunately, inserting a catheter and having it stay in place without disruption can be difficult tasks in such environments and is known to be the third leading cause of death in combat situations.
Mychael Overstreet, a military veteran, and paramedic, has been exposed to such cases regularly while on duty in the US and abroad. While trying to insert catheters, Overstreet, like many medical professionals and veterans before him, found that kinking and dislodging of needle decompression catheters was common and led to pneumothorax complications that proved fatal. With these experiences in mind, Oversteet founded Tension Square, a device which holds a needle decompression secure in place, while preventing damaging kinking, folding, or dislodgement. After years of R&D, he is now printing the final end-use device on his Fuse 1 SLS 3D printer.
According to Overstreet, “I’ve gone to medical trade shows where people come up to me and ask how I built the Tension Square, because they’ve been trying to solve this problem for a long time. But until recently, the technology wasn’t there. We happened to be working on this at the right time, and had access to the right 3D printers.”
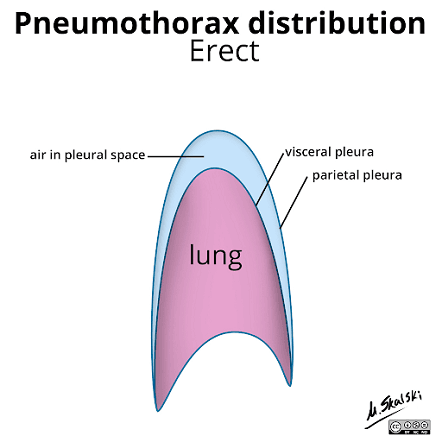
Figure 1: diagram showing the expected distribution of air within the pleural space https://radiopaedia.org/cases/pneumothorax-distribution-diagram

Figure 2: Traumatic Pneumothorax, Case courtesy of Dr David Cuete, Radiopaedia.org, rID: 24619, https://radiopaedia.org/cases/24619
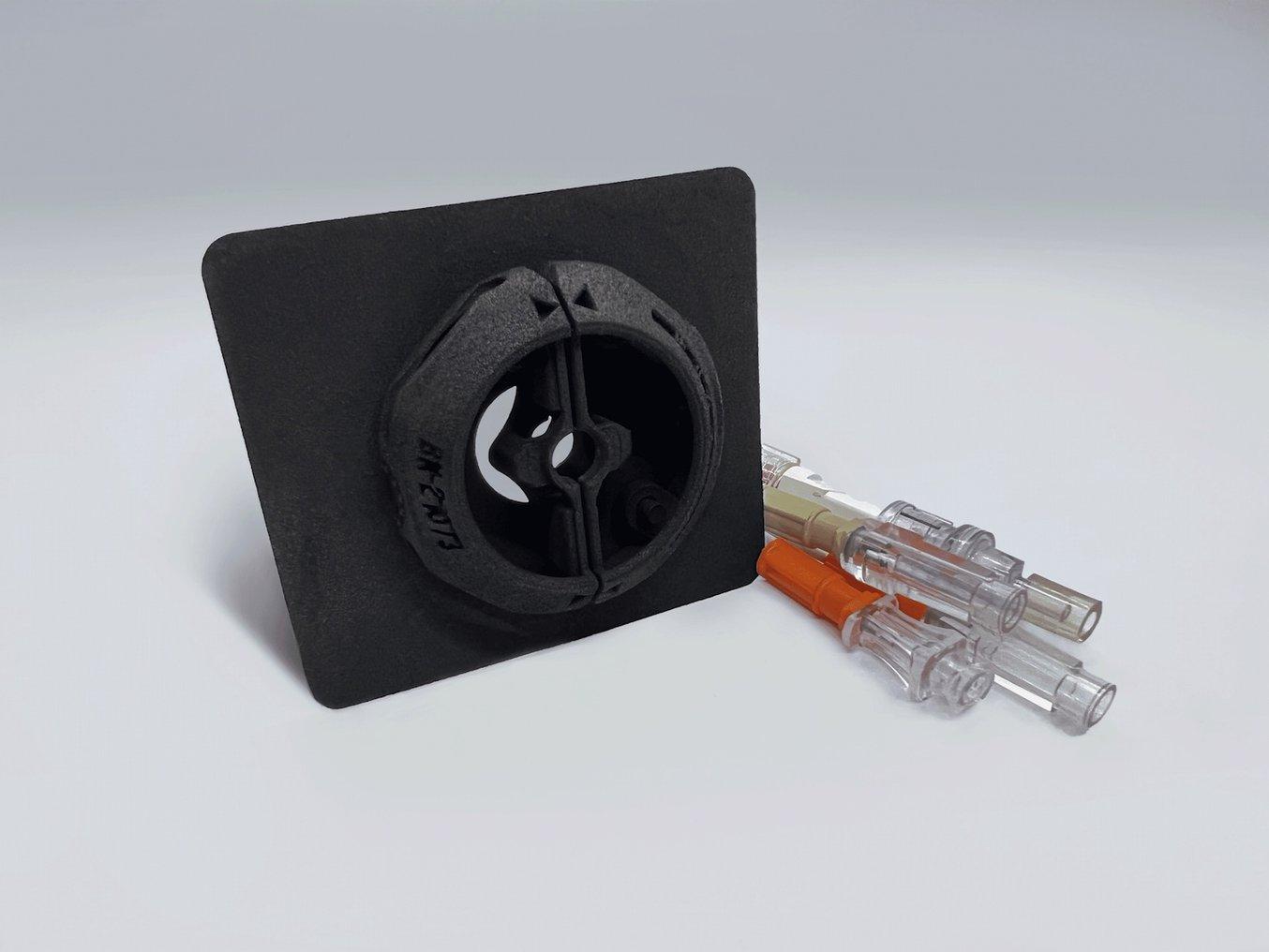
Fuse 1 For End Use Parts
Watch our webinar with Myke Overstreet for more details about Tension Square and using the Fuse 1 for end use applications.
Prototyping a New Medical Device
Before a planned commercial launch in September 2021, Overstreet had been developing Tension Square for approximately three years, originally investing in prototyping with a combination of the Form 3 and outsourcing multi-jet fusion prints. However, his design was running into problems, especially around printing functioning hinges. Furthermore, Overstreet needed a material that met a slew of different requirements: long lasting, accurate, lightweight, skin safe, and durable.
When the Fuse 1 started shipping in early 2021, Overstreet, who did not have engineering experience, was curious, saying “as soon as I got the Fuse 1, I took the stickers off, followed the instructions on the screen, and started printing immediately. It was easy.” He quickly realized that nylon would work better than other materials. After a few prints, the design was coming together quickly, saying that “the Fuse 1 was so important for finalizing the design. The ability to print parts in place that move, like the hinges, that changed everything for us. I would not have been able to design that for myself.” With the Fuse 1 on his workbench, Overstreet was able to finalize his design and rapidly move towards production of his medical device. According to him, “we tried multiple resins on the Form 3, but even the Tough 1500 Resin wasn’t meeting our needs. The Nylon 12 material, and the support I could get from the Formlabs team, are really the top two reasons I bought the Fuse 1.”
Having already spent years developing the Tension Square, Overstreet moved to quickly finish his design, saying “since this Fuse 1 design came about, we’ve been moving forward at 200% speed. Things are moving faster now, the post-processing, the printing, everything compared to when we tried to make these on the SLA machines. The design we are going into production with is version V. We almost went through the entire alphabet with prototypes.”
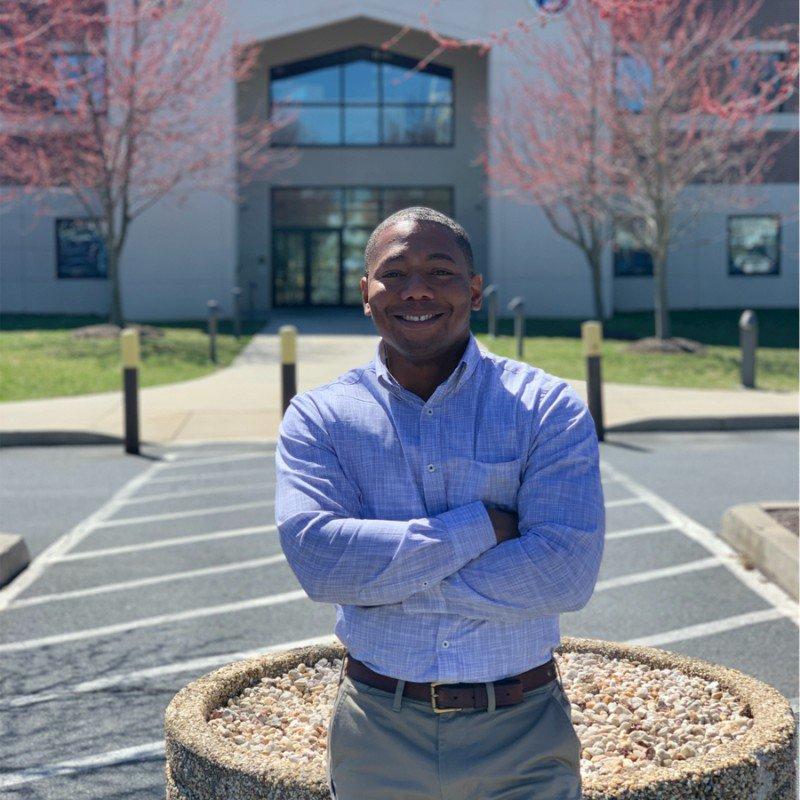
Tension Square, LLC
Mychael Overstreet, a military veteran, and paramedic, created a revolutionary needle decompression catheter stabilizing & securement device that eliminates kinking & dislodgment.
End-Use Production With In-House 3D Printing
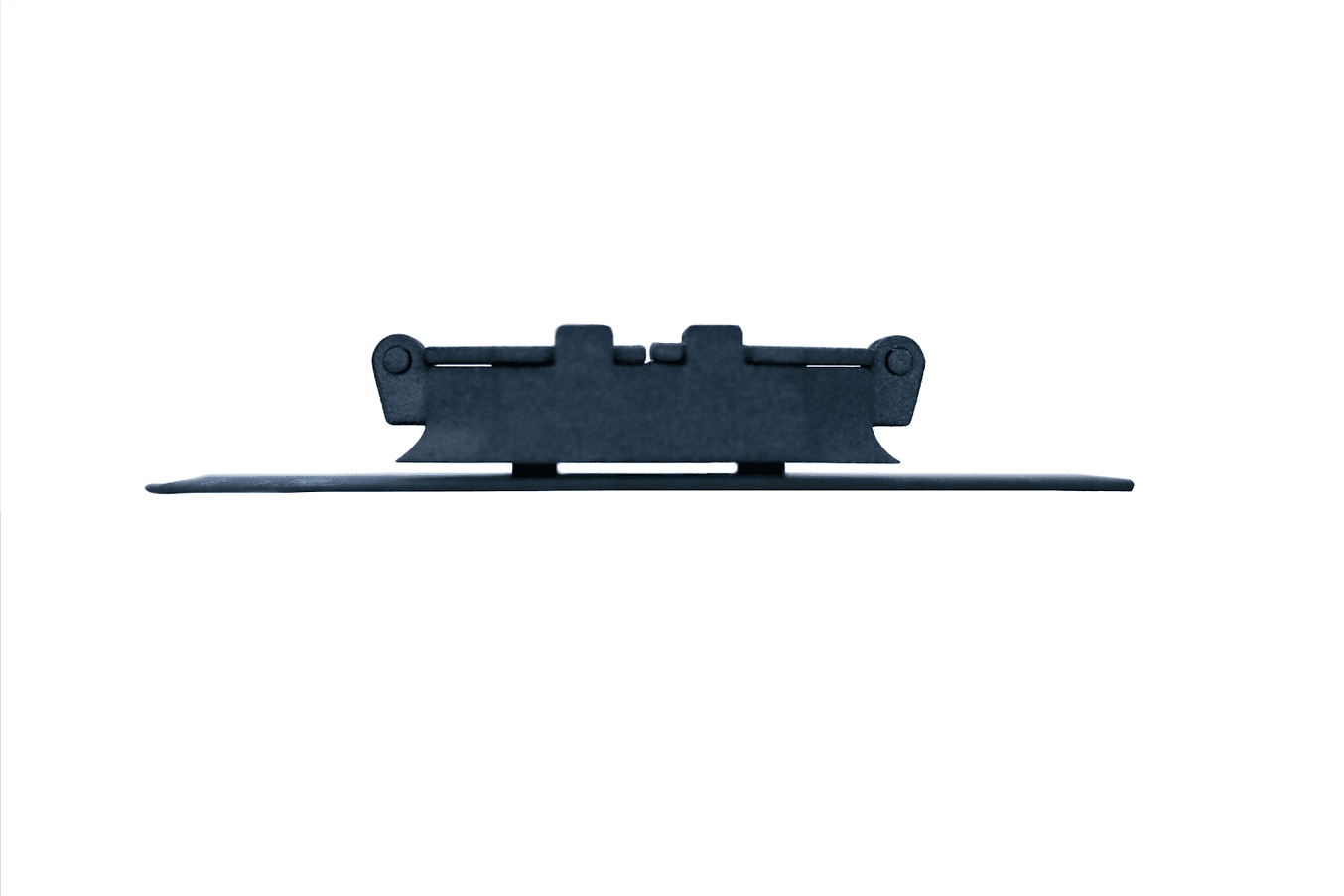
Overstreet needed a material that was long-lasting, accurate, lightweight, and durable.
For Overstreet, not only is he launching a new medical device, but also his first small business. Despite the ups and downs, he is excited about the next phase of the company, and getting his device into the hands of medical professionals. He noted that “the first few years, it was a lot of learning, it was difficult, but now we’re here. I’m an airman, a firefighter, a paramedic, but not an engineer.”
After dozens of prototypes, users feedback, and field testing, the team is ready to move into small-batch production. Overstreet said, “our goal is to use the Fuse 1 for production. I don’t like middlemen, we want to cut them out of the process and stop outsourcing. And after all the prototyping we printed in-house, we know we can do production, too.”
Overstreet is printing two parts on the Fuse 1: the base and the housings. The Fuse 1, when properly packed, is able to deliver 125 base-units for the Tension Square per print cycle. For the housings, Overstreet felt comfortable with 90 parts in a single print, which takes approximately 25 hours. This means batches can be started in the morning, and will be finished at the start of the next working day.
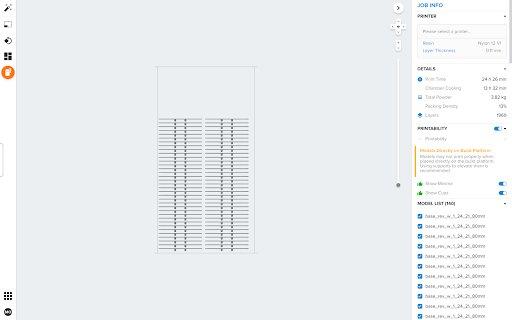
Figure 1 & 2: Parts are packed in PreForm for optimal printing on the Fuse 1
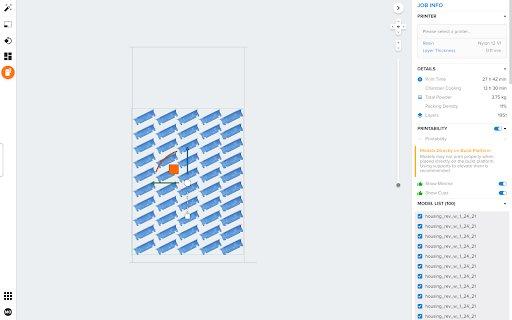
While Overstreet moved away from the Form 3 for creating the base and housings, he is still printing clear pads with Elastic 50A Resin. These pads fit inside the device, acting as a cushion and extra retention mechanism, when the device is deployed. So while the Form 3 did not end up delivering the entire design, Overstreet was still able to find other components to create with it. Being able to affordably print and create new medical devices in-house, using both SLA and SLS 3D printing, was simply not possible just a couple of years ago. Overstreet anticipates profitably scaling to millions of parts per year using a fleet of Fuse 1 printers in his US-based manufacturing facility.
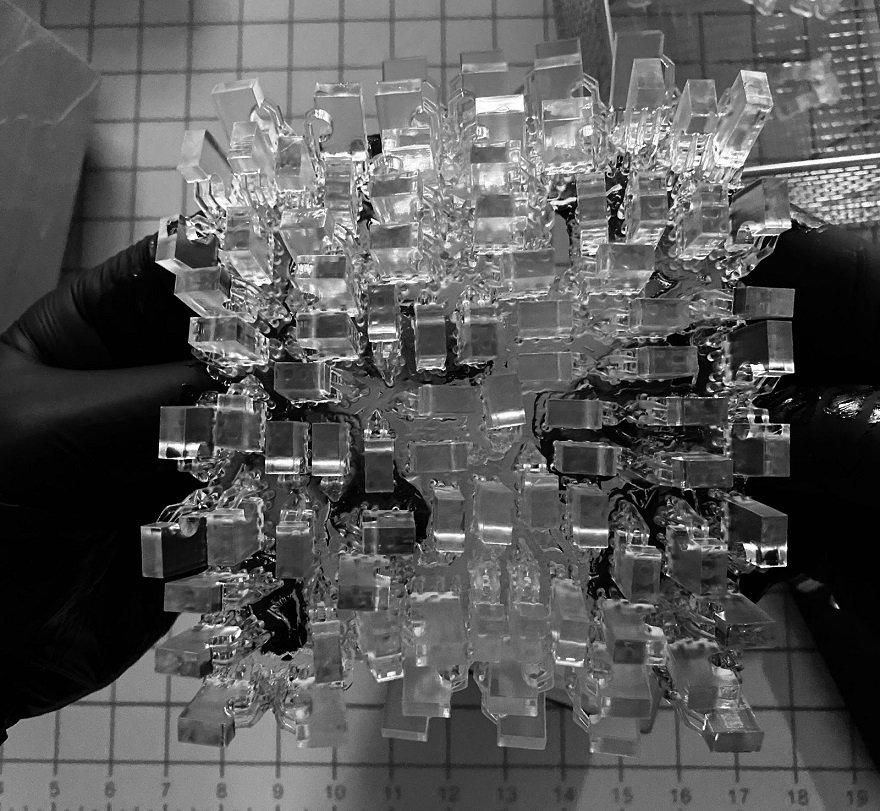
Clear pads for the device, printed in batches with Elastic 50A Resin on the Form 3.
Nylon parts also have an additional benefit in post-processing: they could survive a rigorous batch-sanitation process. “The resin materials could not survive batch-sanitation, there’s a lot of heat and moisture that would impact them. The nylon is perfect”, Overstreet told us. Once the parts are printed, Overstreet post-processes the parts himself before putting them through batch-sanitation, saying “I actually enjoy removing the powder and sandblasting the parts. I put on music and it’s a surprisingly relaxing experience.”
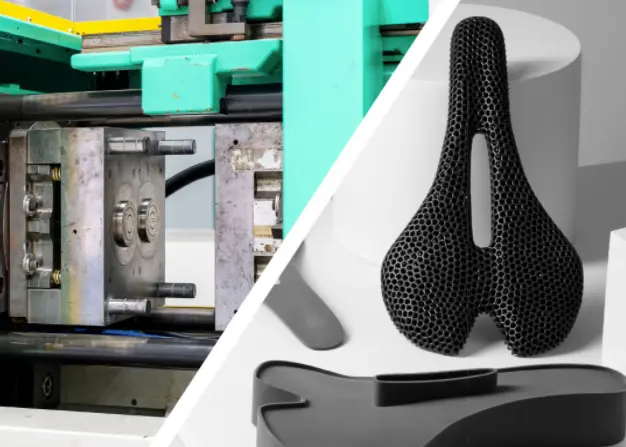
SLS 3D Printing vs. Injection Molding: When to Replace Molded Parts With 3D Printing?
This white paper showcases the cost-dynamics for real-life use cases, and presents guidelines for using SLS 3D printing, injection molding, or both.
One Printer, Many Applications
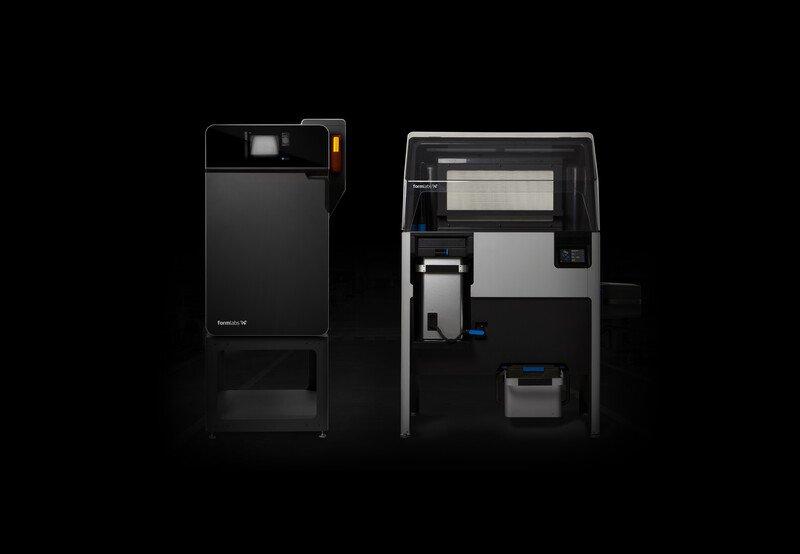
For now, Overstreet is looking to ramp production and begin taking more orders for the Tension Square. But he’s already thinking about what’s next, saying “there are expensive securing devices used right now during other invasive and painful procedures, that cost anywhere from $80 -$100 each, and I have a lot of ideas around those processes. We’re definitely excited for Nylon 11 for those applications.”
Every medical facility should have access to the latest tools to improve care and provide the best patient experience. Looking to learn more about if the Fuse 1 printer is right for your medical application? Contact us to talk to a 3D printing expert.
- https://www.mayoclinic.org/diseases-conditions/pneumothorax/symptoms-causes/syc-20350367
- https://www.ncbi.nlm.nih.gov/pmc/articles/PMC4919804/