L'avenir des accessoires et des effets de maquillage : impression 3D de grands accessoires et de moules avec la Form 3L pour la saison 2 de « Raised by Wolves »
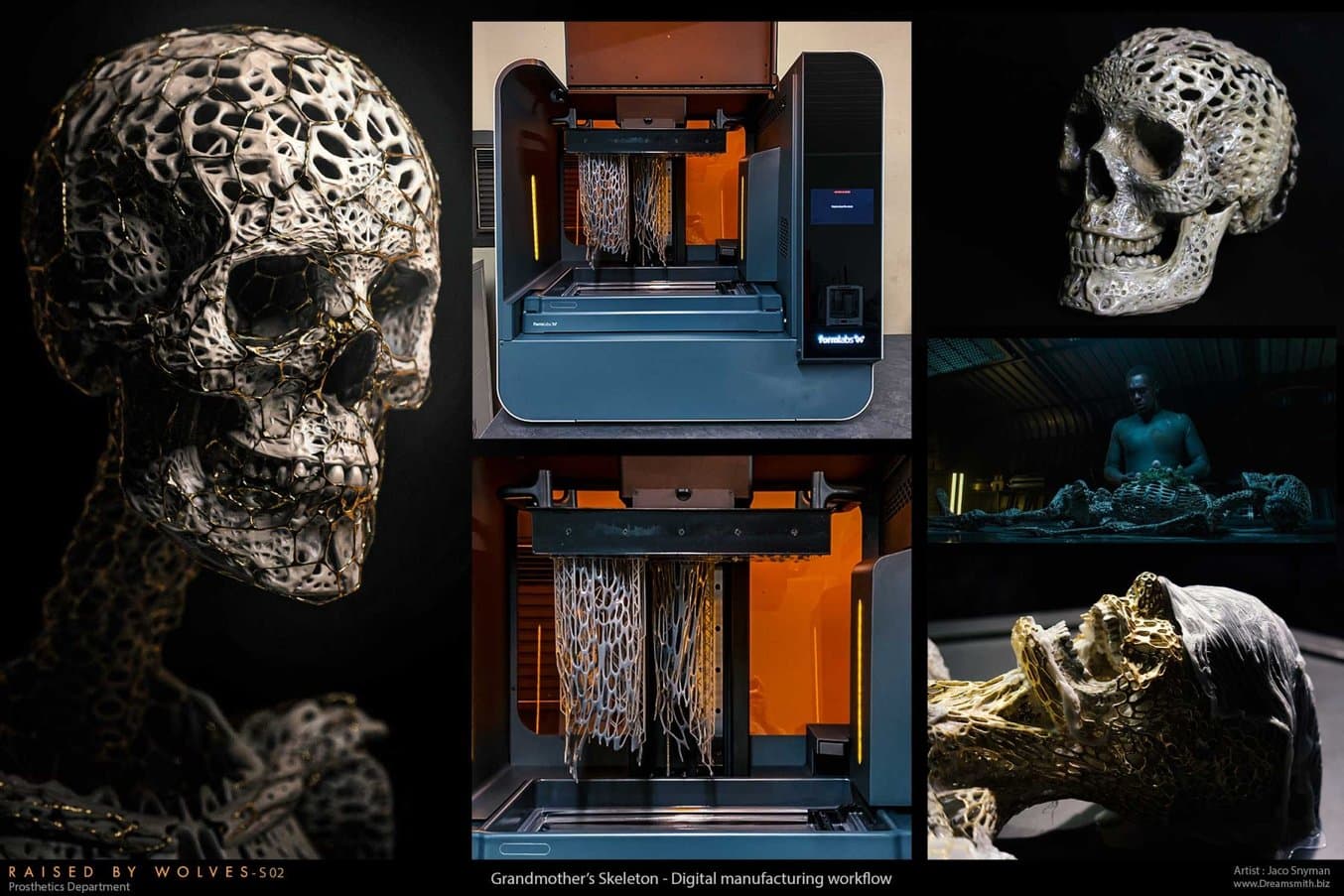
En 2020, nous avons interviewé Jaco Snyman, fondateur de l'entreprise primée spécialisée dans les effets de maquillage et la fabrication d'accessoires Dreamsmith Studio, et concepteur principal des prothèses de la série de science-fiction « Raised by Wolves .». À l'époque, Snyman nous avait parlé de son flux de travail pour produire les moules imprimés en 3D et les modèles finauxutilisés dans la première saison de la série.
La série de HBO Max, créée par Aaron Guzikowski et produite par Ridley Scott, nous raconte l'histoire de deux androïdes, Père et Mère, qui ont reçu pour mission d'élever des enfants humains. La deuxième saison de la série est arrivée en février 2022 et fait apparaître à l'écran encore plus d'accessoires et de prothèses imprimés en 3D, cette fois à l'aide d'un parc d'imprimantes stéréolithographiques (SLA) grand format Form 3L.
Bande-annonce de la saison 2 de « Raised by Wolves »
Cet article a été rédigé par Snyman et son équipe, qui nous expliquent comment Dreamsmith a utilisé la Form 3L pour imprimer de grands moules et modèles afin de donner vie à des extraterrestres, des androïdes bien plus dans le monde apocalyptique de « Raised by Wolves. »
Révolutionner les accessoires et les effets de maquillage : cinq études de cas tirées de la saison 2 de « Raised by Wolves »
L'impression 3D apporte une vague de changements dans le monde de l'industrie cinématographique, où tout va très vite et où les délais sont très serrés. Elle offre tous les avantages d'un flux de travail numérique, permet de fabriquer des pièces de manière fiable et précise, et également de libérer de la main-d'œuvre, qui peut ainsi se consacrer à des tâches plus créatives. Tout cela semblait absolument révolutionnaire, et nous étions impatients d'intégrer l'impression 3D dans notre flux de travail. Malheureusement, comme pour toutes les technologies émergentes, certaines questions restaient en suspens.
Pour que l'impression 3D réponde à nos besoins, elle devait remplir trois critères spécifiques. Tout d'abord, nous voulions que le niveau de détail corresponde à celui obtenu avec des techniques traditionnelles. Elle devait également pouvoir reproduire ces détails à une échelle suffisamment importante : nous souhaitions que le volume d'impression soit assez grand pour imprimer une tête humaine complète, par exemple. Et enfin, elle devait être fiable, précise et facile à utiliser. Nos délais serrés et nos contraintes budgétaires exigeaient aussi qu'il y ait le moins de défaillances possible.
Il s'est avéré extrêmement difficile de trouver une imprimante qui réponde à tous ces critères et dont le prix ne soit pas prohibitif. Les imprimantes bas de gamme disponibles sur le marché se sont avérées peu fiables, et les options les plus fiables ne permettaient pas d'obtenir un haut niveau de détail à l'échelle souhaitée. Après quelques années d'essais et d'erreurs, nous nous sommes résignés au fait que, du moins pour l'instant, l'impression 3D ne serait qu'un outil de plus et non la révolution complète que nous espérions. Puis, la Form 3L est arrivée.
La Form 3L cochait toutes les cases. Elle offre un grand volume d'impression de 33,5 x 20,0 x 30 cm avec une résolution de 25 microns, et est compatible avec le logiciel PreForm, qui rend l'ensemble extrêmement fiable et facile à utiliser. Toutes ces raison et son impressionnante variété de résines font de la Form 3L un outil incroyablement puissant qui a complètement révolutionné notre flux de travail en deux ans à peine.
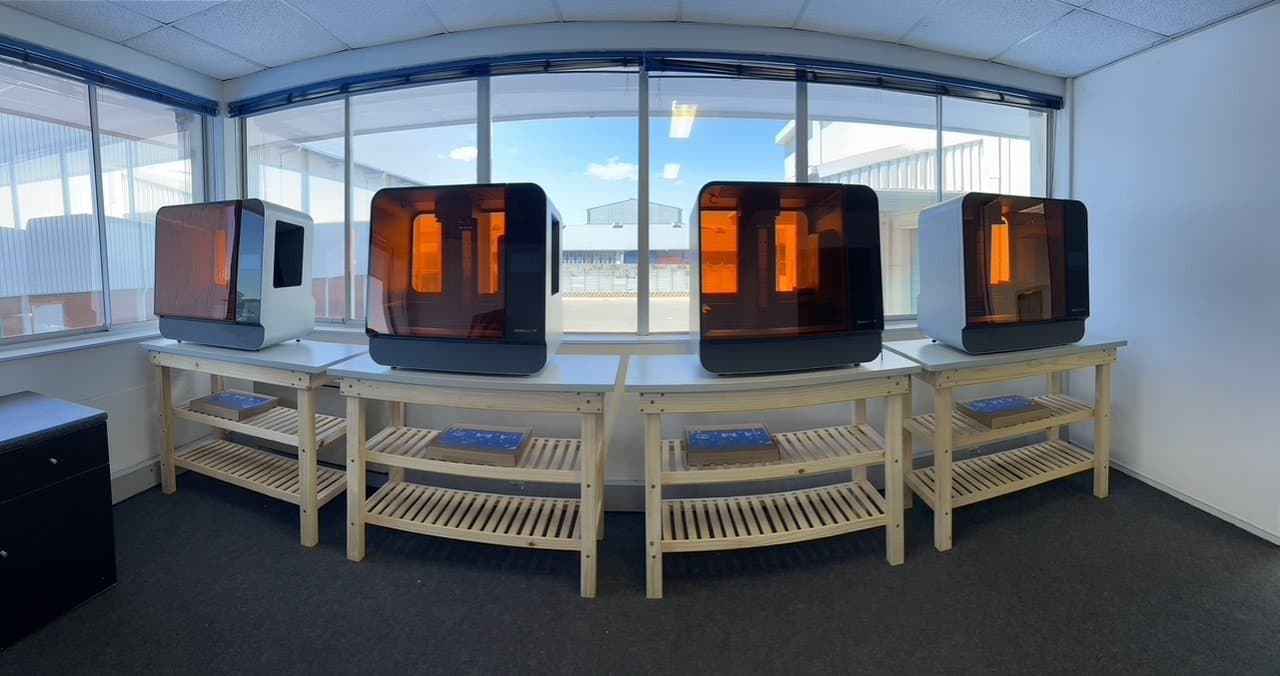
Imprimantes 3D Form 3L dans l'espace de travail de Dreamsmith à Cape Town, en Afrique du Sud.
Il est difficile de rendre compte à quel point la Form 3L a changé la donne sans nous pencher sur la manière dont elle nous a permis de mieux résoudre nos problèmes de création. Dans les exemples suivants, nous allons analyser notre flux de travail et tenterons de vous expliquer pourquoi nous pensons que cette imprimante est si révolutionnaire pour notre secteur.
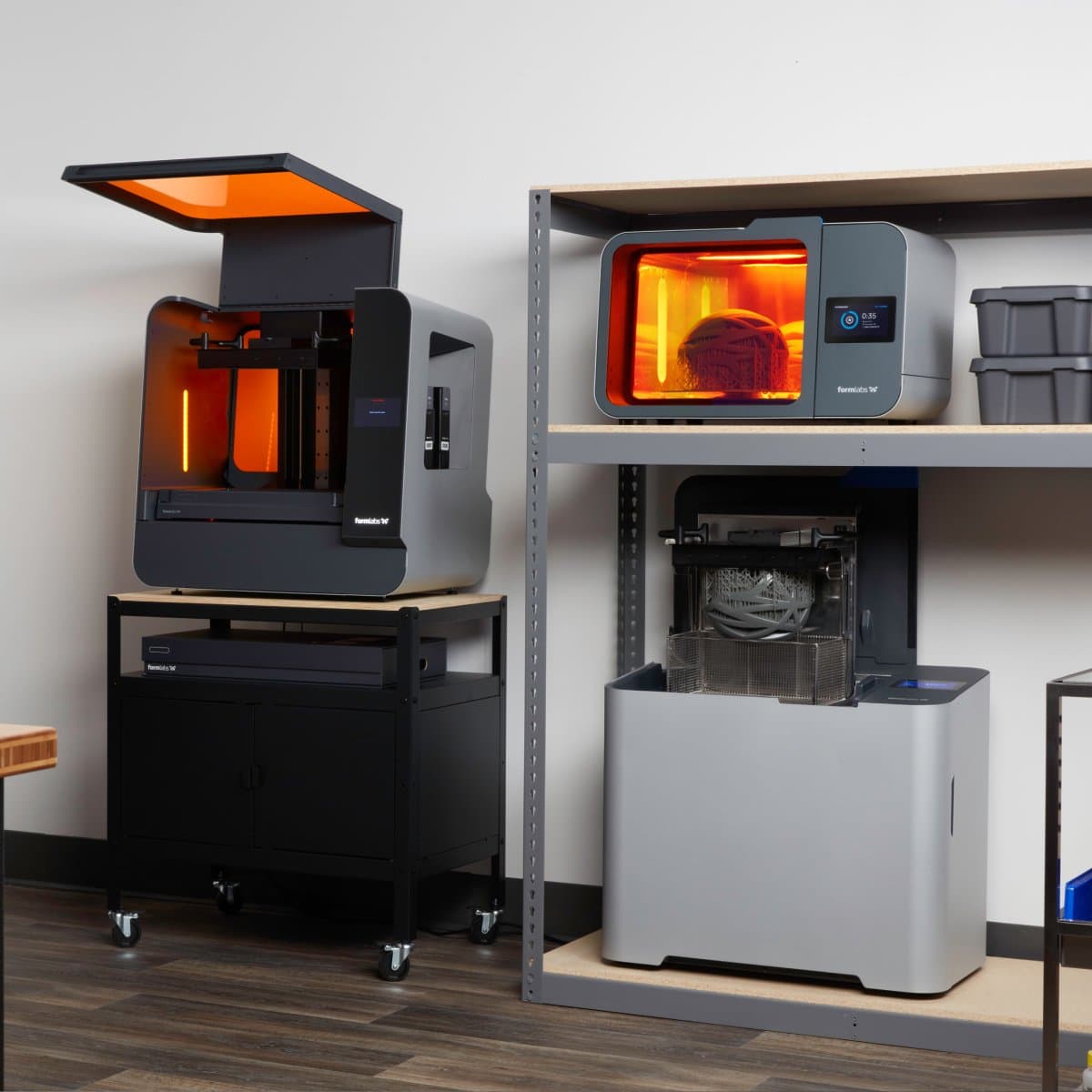
Démonstration en direct de l'imprimante 3D grand format Form 3L
Vous souhaitez en savoir plus sur l’écosystème Form 3L et Form 3BL, ainsi que sur les nouvelles solutions de post-traitement grand format ? Dans cette démonstration, Thibault Leroy vous expliquera en détails le flux de travail complet de la Form 3L, y compris le post-traitement.
#1 : Remplacer le moulage sur nature - reproduction du visage d'une actrice
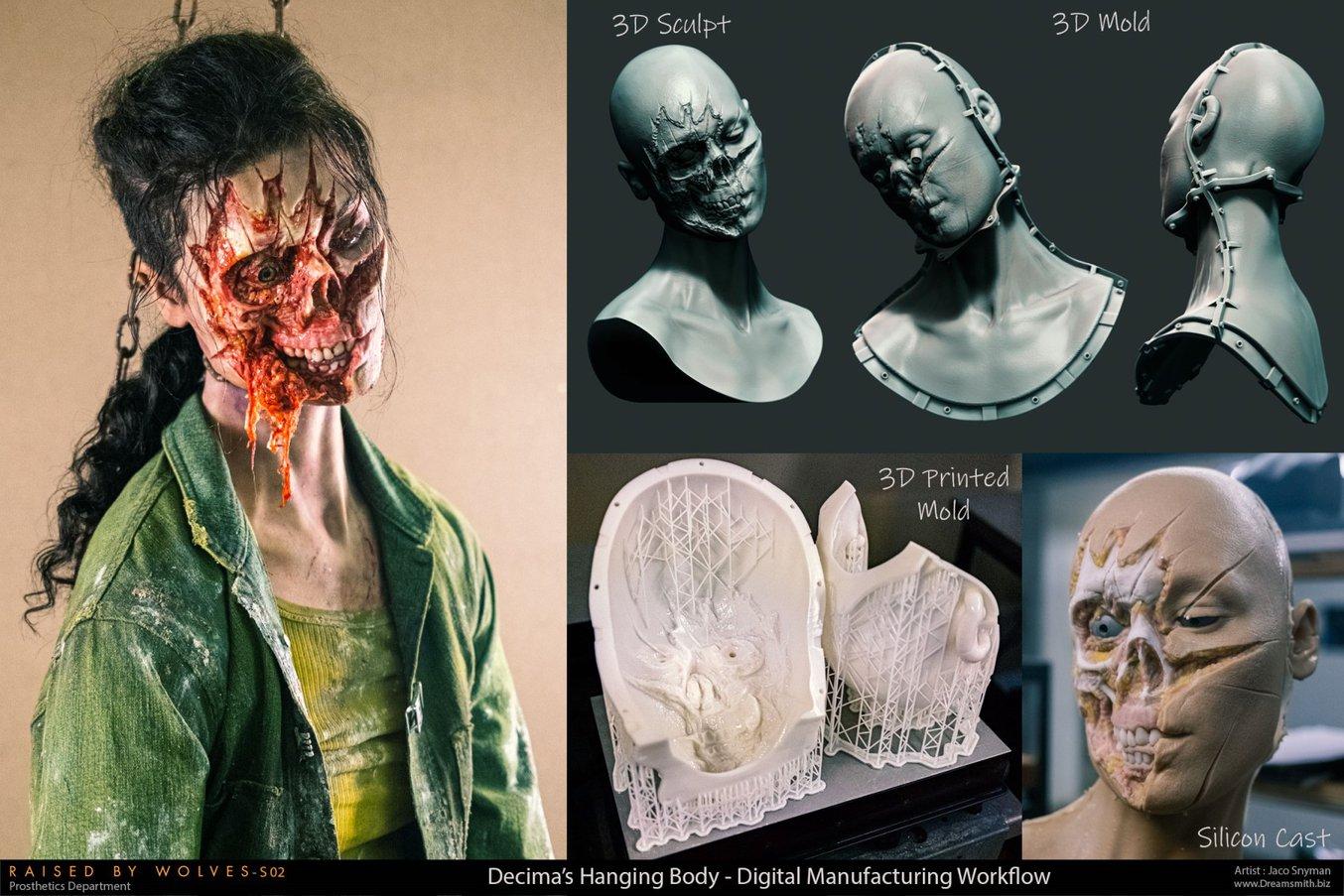
Reproduction hyperréaliste en silicone du visage d'une actrice, avec des moules conçus numériquement et imprimés en 3D sur la Form 3L avec Rigid 10K Resin.
Dans cet exemple, nous avons été chargés de créer une reproduction hyperréaliste en silicone du corps d'une actrice. Le point délicat est que la tête devait pendre de son cou, avec la moitié du visage en moins.
Auparavant, nous faisions un moulage en silicone de l'actrice, c'est-à-dire que nous couvrions physiquement son visage avec du silicone et des bandes de plâtre pour créer un moule à usage unique de son visage. À partir de ce moulage sur nature, nous fabriquions un moule en argile sur lequel nous sculptions à la main les détails requis pour la scène. Dans le cas présent, cela impliquait d'allonger son cou et d'enlever des parties de son visage.
Cette sculpture en argile était ensuite remodelée avec de la résine époxy et de la fibre de verre. À partir de ce moule final, nous créions ensuite la reproduction finale de la tête en silicone. Ce processus prenait trois semaines et devait être supervisé par au moins trois artistes et techniciens expérimentés. De plus, la reproduction de la tête n'était encore que du silicone brut : il fallait encore la peindre et implanter minutieusement chaque cheveu pour atteindre le niveau d'hyperréalisme requis. Au total, ce processus prenait environ un mois.
« La Form 3L peut imprimer le moule entier de la tête avec suffisamment de détails pour qu'il soit impossible de le distinguer d'un moule réalisé avec des techniques traditionnelles. Cela nous a permis de passer à un flux de travail numérique et de nous baser sur un scan 3D très précis de l'actrice. Nous n'avons plus dû recourir au moulage sur nature, ce qui a rendu les choses beaucoup plus agréables pour l'actrice. »
Jaco Snyman, fondateur de Dreamsmith Studio
Nous avons ensuite utilisé ZBrush pour ajouter numériquement les détails requis. Ce processus non invasif, reproductible et très fluide nous permet d'apporter facilement des changements créatifs importants au fur et à mesure que nous recevons des informations du réalisateur.
Nous avons ensuite conçu le moule numérique. Grâce au volume d'impression de la Form 3L, nous avons pu imprimer de plus grandes pièces pour obtenir un produit final avec moins de lignes de chevauchement. Le moule a ensuite été imprimé en un jour, et après un peu de nettoyage, il était prêt à être traité le jour suivant.
Processus étape par étape
L'ensemble de ce flux de travail peut être réalisé par une seule personne en une fraction du temps nécessaire auparavant, permettant ainsi à la main-d'œuvre de se concentrer sur une étape cruciale pour le produit : la finition. Ce flux de travail plus efficace nous évite de précipiter les étapes finales, ce qui était presque toujours le cas auparavant en raison de la lourdeur du flux de travail traditionnel.
Ce seul exemple permet de mieux comprendre comment l'impression 3D peut devenir un véritable atout. Nous travaillons plus rapidement, sommes plus productifs et économisons sur les matériaux et la main-d'œuvre. La Form 3L a rendu notre travail plus rapide, plus efficace et moins cher.
#2 : Créer des formes complexes - masque en silicone
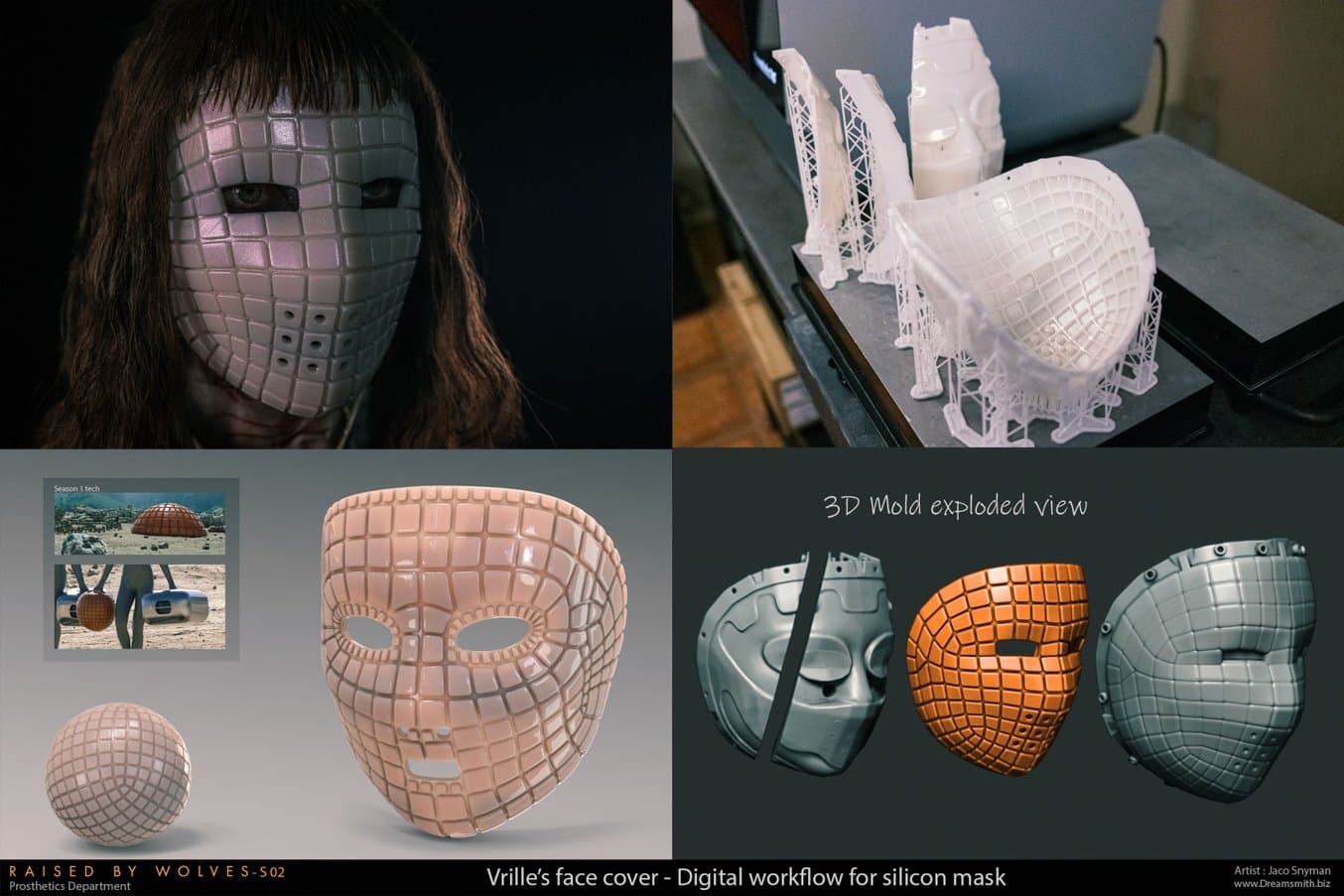
Conception et impression 3D d'un masque en silicone complexe et très détaillé.
Certains éléments peuvent grandement bénéficier de la conception assistée par ordinateur (CAO). Il arrive qu'un objet soit impossible à réaliser à la main ou qu'il soit peu pratique et trop long à réaliser. Auparavant, nous devions sous-traiter ces pièces à un atelier d'usinage ou tout simplement confier le travail à quelqu'un d'autre. Nous savions que l'impression 3D pourrait résoudre ces problèmes un jour, mais nous attendions que la technologie évolue pour pouvoir acheter une imprimante qui soit abordable et de qualité.
La Form 3L a récompensé notre attente. Nous sommes désormais beaucoup moins limités par les techniques de fabrication traditionnelles et pouvons réaliser beaucoup plus de choses en interne sans avoir recours à une sous-traitance coûteuse. Notre imagination est maintenant notre seule limite, ce qui est une excellente chose !
L'objet mentionné ci-dessus aurait été très difficile à réaliser sans l'impression 3D. Le masque de Vrille présentait deux problèmes uniques qu'il nous fallait résoudre.
Tout d'abord, il devait inclure à la fois des détails organiques et géométriques : la couche extérieure devait être composée de formes géométriques épousant la forme organique et asymétrique du visage de l'actrice.
Deuxièmement, il y avait un problème de matériau : le masque final devait être fabriqué en silicone, ce qui nécessitait un moule, car nous ne sommes pas en mesure d'imprimer directement en silicone.
Processus étape par étape
Ce projet montre comment il est possible de combiner différentes technologies de pointe. Nous avions besoin d'un scan 3D de l'actrice, d'un logiciel pour créer l'image numérique et concevoir le moule numérique, et d'une imprimante 3D suffisamment grande et précise pour imprimer le moule.
En regardant les images ci-dessus, vous pouvez voir que nous avons pu faire tenir l'ensemble du moule sur une seule plateforme de fabrication, réduisant ainsi considérablement la durée d'impression. Les améliorations apportées aux matériaux d'impression ont également joué un rôle énorme. Le moule final imprimé avec Rigid 10K Resin de Formlabs était extrêmement précis, ce qui a permis d'obtenir un masque final presque parfait que vous pouvez voir ci-dessus.
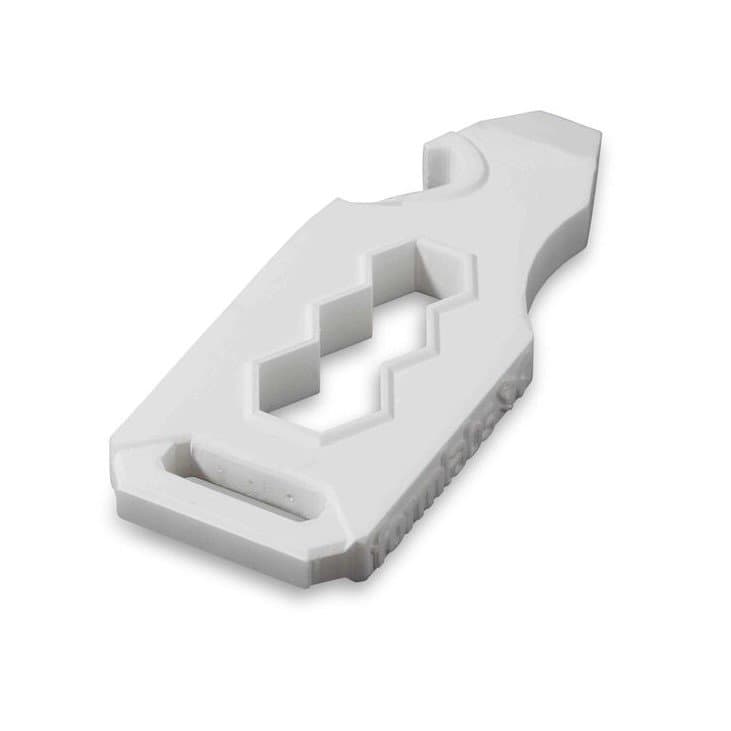
Commander un échantillon imprimé en 3D avec Rigid 10K Resin
Examinez et constatez par vous-même la qualité Formlabs. Nous enverrons un échantillon gratuit à votre bureau.
#3 : Imprimer des formes impossibles - squelette biomécanique
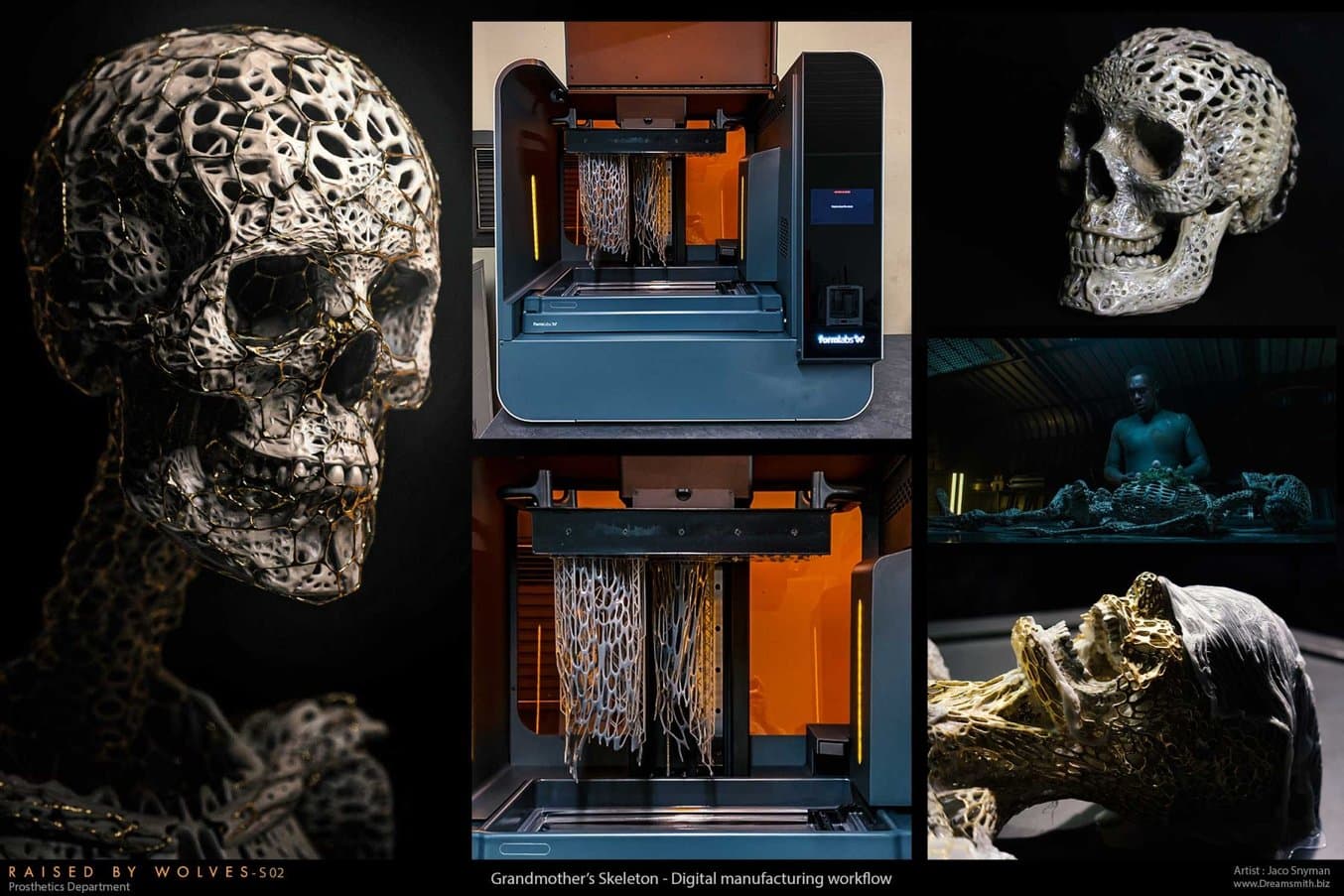
Un squelette biomécanique de grande taille, imprimé en 3D sur la Form 3L.
Si certaines conceptions sont plus faciles à fabriquer avec l'impression 3D, d'autres seraient tout bonnement impossibles à réaliser sans elle.
Le dessin ci-dessus représente par exemple un squelette biomécanique grandeur nature. Il s'agit d'un accessoire aux détails complexes qu'il aurait été extrêmement difficile de sculpter dans l'argile et pratiquement impossible de mouler avec des techniques traditionnelles.
Le squelette de Grand-Mère est un exemple parfait de conception qu'il aurait été impossible de réaliser sans l'impression 3D. Ces formes impossibles et ces engrenages imbriqués peuvent être imprimés depuis un certain temps déjà, mais ce que nous voulions, c'était imprimer de grandes pièces avec un haut niveau de détail. Il nous fallait un squelette grandeur nature ! Le volume d'impression de la Form 3L nous a permis d'imprimer en haute résolution le squelette entier divisé en plusieurs pièces.
Processus étape par étape
Cet accessoire aurait été pratiquement et financièrement impossible à fabriquer sans la Form 3L.
#4 : Impression rapide de grandes pièces - reproduction de la tête d'une actrice
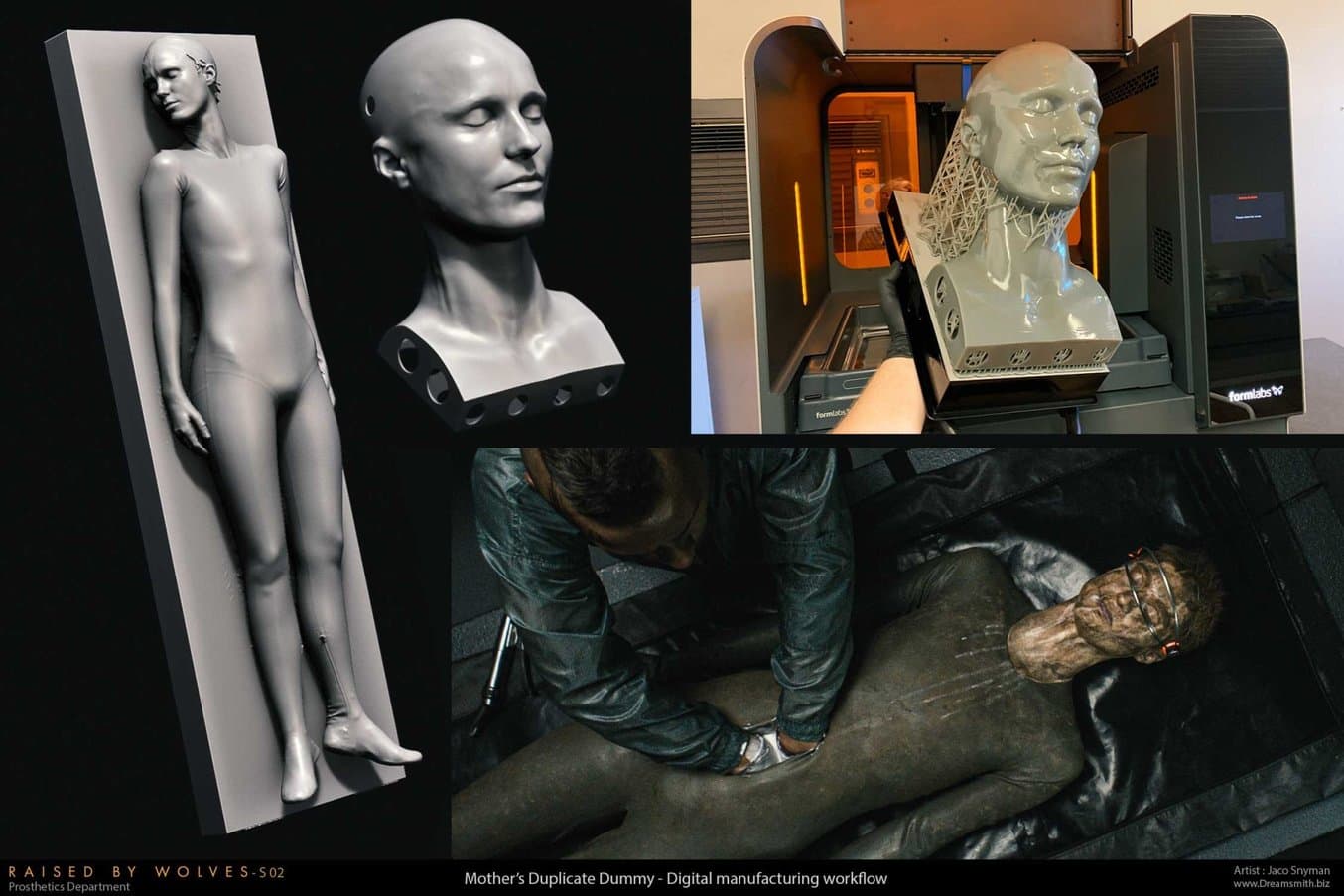
La tête de l'actrice Amanda Collin, imprimée en 12 heures avec Draft Resin sur la Form 3L.
La taille du volume d'impression est extrêmement importante. L'une des conditions préalables au choix de l'imprimante était qu'elle devait être capable d'imprimer une tête humaine entière. En divisant un objet en plus petites pièces, vous rendez le processus de finition plus long. Chaque joint ou ligne de chevauchement doit être soigneusement travaillé et retexturé pour créer un accessoire final impeccable.
Le mannequin de Mère, visible ci-dessus, en est un parfait exemple. Nous avons pu imprimer sa tête d'une pièce avec la Form 3L, ce qui nous a permis d'obtenir une reproduction en résine parfaite du visage de l'actrice, que nous avons ensuite peinte avec soin.
Auparavant, ce processus aurait pris énormément de temps et nécessité un moulage sur nature, des moules en époxy faits à la main et un moulage final en silicone. À titre de comparaison, avant d'avoir accès à la Form 3L, nous avons dû créer une autre reproduction qui a pris un mois à toute notre équipe. Cette fois-ci, nous avons pu imprimer le visage de Mère, usiner le corps en une semaine et avoir l'accessoire final peint et prêt pour le tournage en moins de deux semaines.
Processus étape par étape
Il est important de noter que cet accessoire n'aurait pas tenu dans un gros plan ; il a été fabriqué spécialement pour le plan final que vous voyez ci-dessus. Cela nous a permis d'utiliser la pièce en résine dès sa sortie de l'imprimante ; elle était tout juste assez détaillée pour cette distance. Nous avons ainsi pu économiser énormément de temps, de matériaux et d'argent.
Créer ce mannequin avec les techniques traditionnelles de moulage et de coulage aurait pris le même temps, quels que soient les détails finaux du produit fini. La Form 3L nous a permis d'obtenir le niveau de détail que nous souhaitions : nous avons pu fabriquer un accessoire qui répondrait exactement aux besoins de la scène. Cela nous permet de faire plus en moins de temps et à un prix plus avantageux, ce qui est un atout considérable dans le monde de l'industrie cinématographique, où les budgets sont souvent serrés.
#N°5 : Flux de travail hybrides - le maquillage de Paul
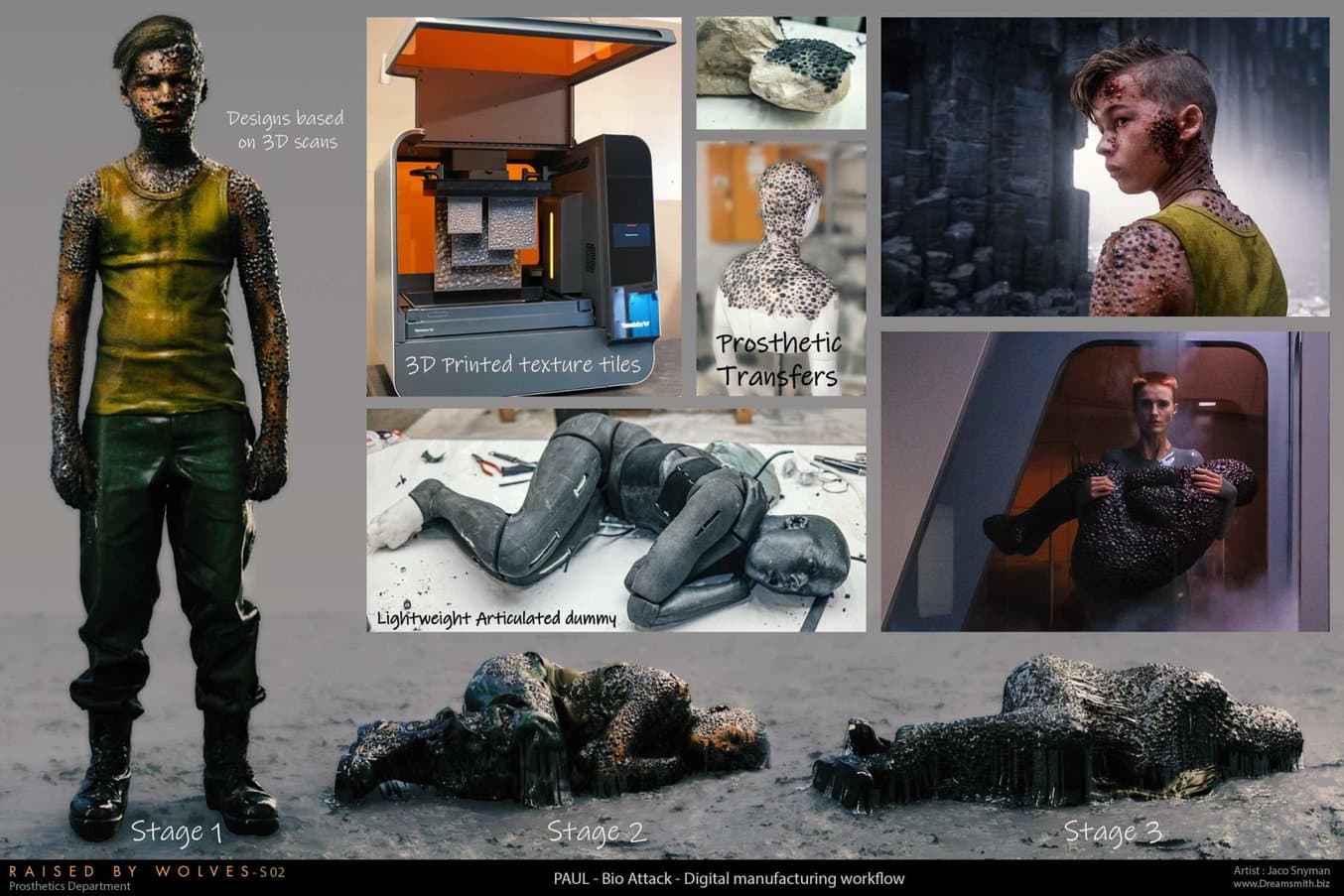
Combinaison de carreaux de texture imprimés en 3D et de techniques traditionnelles de fabrication de mannequins.
L'impression 3D ne doit pas forcément remplacer complètement les techniques conventionnelles. Avoir la Form 3L à notre disposition nous a permis de créer de nouveaux flux de travail hybrides qui utilisent les avantages des deux approches.
Le cocon de Paul illustre bien la manière dont nous avons combiné les techniques de fabrication traditionnelles et l'impression 3D pour créer quelque chose qu'il aurait été très difficile de fabriquer avec seulement l'une ou l'autre de ces techniques.
Jaco Snyman, fondateur de Dreamsmith Studio
Pour le cocon, nous avions besoin d'une peau écailleuse et malléable qui puisse épouser les mouvements du mannequin articulé à l'intérieur. Cela nécessiterait normalement un moule très grand et coûteux, mais comme les écailles sont organiques et peuvent être assemblées comme un puzzle, il était logique de lier la peau à la main sur le mannequin pour ne pas devoir fabriquer un moule coûteux.
Nous avions cependant besoin d'une grande quantité d'écailles pour reconstituer le puzzle du cocon. Pour cette étape du processus, l'impression 3D nous a paru être la solution parfaite, en raison de sa capacité à reproduire avec précision et rapidité des détails complexes. Nous avons imprimé des moules de différentes tailles que nous avons pu utiliser pour mouler des écailles en silicone. Nous avons ensuite utilisé ces carreaux en silicone pour fabriquer le cocon.
Processus étape par étape
Le fait de disposer de la Form 3L et de plusieurs résines différentes rend possible ce type de flux de travail hybride et constitue un outil extrêmement puissant pour résoudre les problèmes quotidiens de l'industrie cinématographique.
Dans les coulisses de la saison 2 de Raised By Wolves : les leçons de Dreamsmith
La saison 2 de Raised By Wolves a été extrêmement instructive pour nous : c'était la première fois que nous nous appuyions autant sur des flux d'impression 3D. Bon nombre des exemples ci-dessus n'ont été envisagés qu'en théorie avant que nous puissions les essayer dans les délais impartis
Il s'agit généralement d'un secteur où les erreurs et les conséquences imprévues sont nombreuses et, bien que nous ayons rencontré les deux, notre expérience avec la Form 3L a été excellente, et notre confiance dans le produit a augmenté avec chaque projet réussi.
La fiabilité de la plateforme nous a prouvé que nous pouvions aller de l'avant et appliquer ce que nous avons appris à des projets plus importants et plus exigeants. Nous avons depuis ajouté quatre Form 3L à notre parc et, grâce à cette capacité accrue, nous avons pu atteindre un niveau de productivité que nous aurions jugé impossible auparavant.
Ce flux de travail entièrement numérique nous permet de travailler à distance. Nous pouvons numériser en 3D, concevoir, sculpter et mouler des prothèses complètes de personnages et les envoyer partout dans le monde sans que notre équipe ait à se déplacer physiquement ou que le client doive attendre l'arrivée de colis fragiles. Si vous souhaitez en savoir plus sur ce service, n'hésitez pas à nous contacter à l'adresse [email protected].
Nous avons beaucoup bénéficié de cette expérience acquise pendant la saison 2 de Raised By Wolves et nous sommes très enthousiastes à l'idée de partager certains des nouveaux projets sur lesquels nous avons travaillé depuis. Quand on voit le rôle que joue l'impression 3D chez nous aujourd'hui, on peut vraiment dire que la Form 3L a révolutionné notre façon de travailler.
Suivez Dreamsmith sur Instagram (@dreamsmith_) pour être au courant de leurs dernières productions.
Nous remercions tout particulièrement Jaco Snyman et Mathew Howard-Tripp pour la rédaction de cet article, ainsi que notre partenaire sud-africain BuildVolume.
Un regard vers l'avenir : un processus de conception entièrement numérique pour les prothèses de maquillage
Après avoir adopté la Form 3L et essayé de nombreux matériaux de la gamme de résines Formlabs, Snyman et son équipe ont découvert comment fabriquer des moules de prothèses pour leur projet secret qui sortira en 2023.
Ils sont passés à un processus entièrement numérique pour fabriquer des prothèses de maquillage. Ils réalisent d'abord un scan 3D de l'acteur, sculptent numériquement les prothèses, puis utilisent une technique hybride de moulage au silicone avec une fine couche de silicone prise en sandwich entre une coquille de moule imprimée en 3D et une base imprimée en 3D.
Selon eux, cette méthode révolutionne complètement leur façon de travailler, car ils peuvent désormais produire des prothèses de maquillage en six fois moins de temps à un prix abordable. Parmi les autres avantages, citons également la possibilité de scanner les visages des acteurs depuis n'importe quel endroit du globe, ce qui permet de mieux respecter les calendriers de tournage chargés.
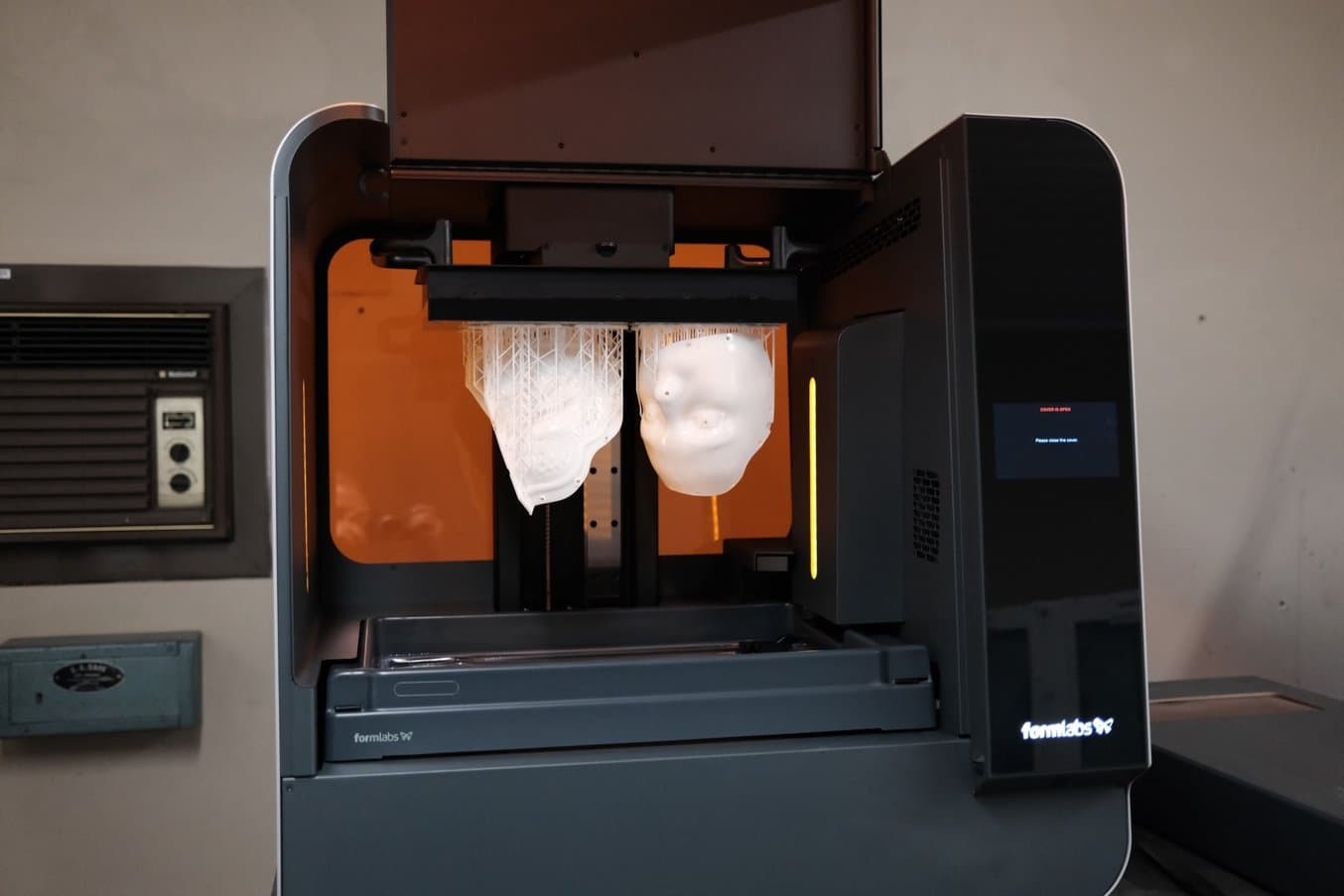
Expérimentation avec Rigid 10K Resin et l'imprimante 3D Form 3L pour réaliser des moules de prothèses.
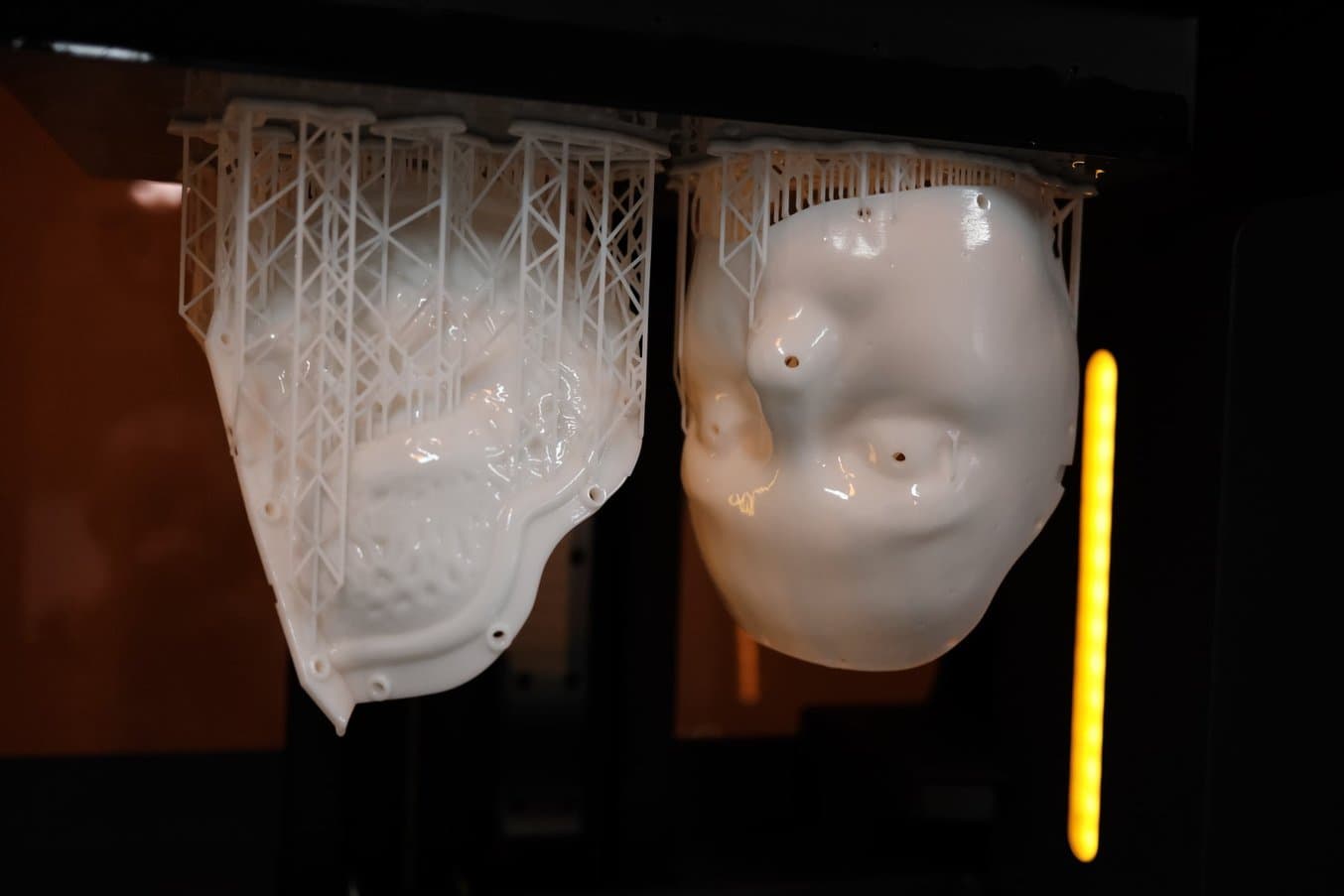
Snyman et son équipe travaillent sans relâche pour tirer parti de toutes les possibilités qu'offre l'impression 3D SLA dans l'industrie du divertissement. L'équipe de Dreamsmith est impatiente de continuer à utiliser l'impression 3D dans son flux de travail pour de futurs projets. Restez connecter pour en savoir plus sur leurs prochaines créations avec la Form 3L.