Impression de pièces pour la Form Wash L et la Form Cure L avec la Fuse 1
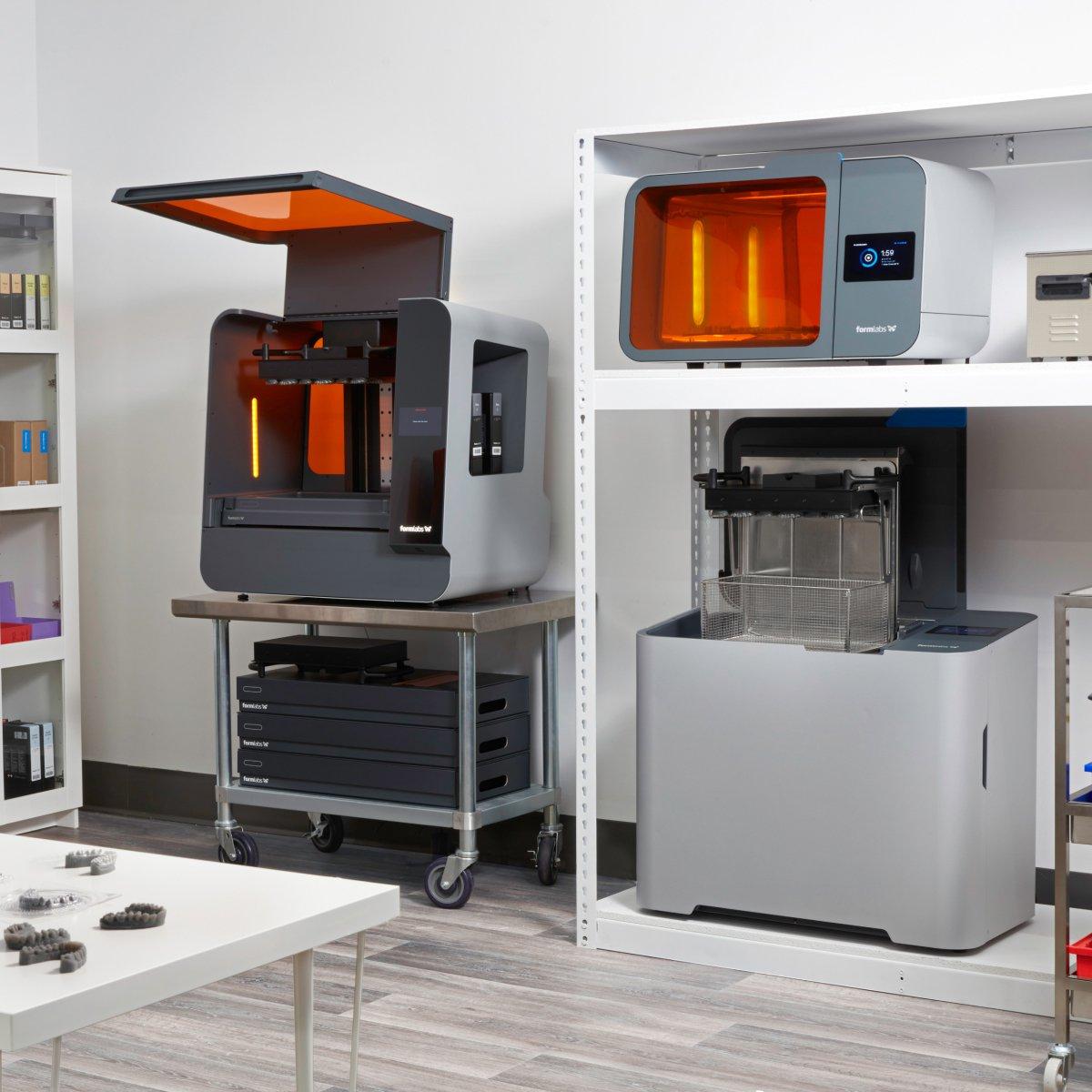
Avant le lancement de la Form Wash L et de la Form Cure L, les options de post-traitement pour les grands volumes de pièces stéréolithographiques (SLA) étaient limitées. Nos clients avaient commencé à imprimer avec les imprimantes SLA grand format Form 3L et Form 3BL de Formlabs, mais avaient encore besoin d'une solution de post-traitement adaptée. Il fallait donc concevoir et fabriquer des machines de lavage et de post-polymérisation complémentaires.
L'équipe d'ingénieurs de Formlabs avait besoin d'une solution de prototypage agile et de haute qualité, et devait pouvoir produire des pièces finales robustes pour des conceptions encore en développement. La réponse se trouvait juste sous leur nez : l'imprimante SLS Fuse 1 de Formlabs et Nylon 12 Powder.
Découvrez comment Formlabs a utilisé l'imprimante Fuse 1 pour prototyper et fabriquer des pièces d'utilisation finale qui font aujourd'hui partie des unités de post-traitement Form Wash L et Form Cure L livrées aux clients.
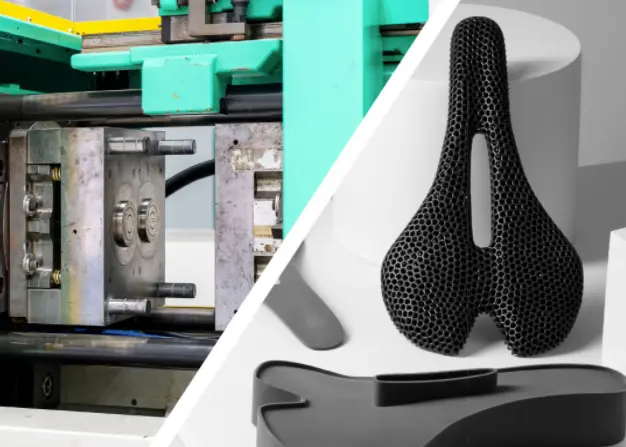
Impression 3D SLS ou moulage par injection : quand remplacer les pièces moulées par l'impression 3D ?
Ce livre blanc présente la dynamique des coûts pour des cas d'utilisation réels, et vous montre comment utiliser l'impression 3D SLS, le moulage par injection, ou les deux ensemble.
Un flux de travail complet pour l'impression SLA de grandes pièces
En septembre 2020, Formlabs avait commencé à livrer la Form 3L, notre imprimante SLA grand format phare. Pendant des années, nous avons répété à nos clients que la seule solution pour imprimer de grandes pièces était de couper leur fichier CAO en deux, de l'imprimer pièce par pièce, puis de coller le tout. La Form 3L a enfin permis d'imprimer de grandes pièces sans sacrifier la précision, la finition de surface ou les propriétés de matériaux qu'ils pouvaient obtenir avec les imprimantes 3D SLA standard de Formlabs.
La Form 3L a eu un impact immédiat sur les clients de tous les secteurs : les laboratoires d'orthodontie ont pu imprimer jusqu'à 120 arcades complètes par jour, les entreprises de développement de produits comme Black Diamond ont pu imprimer des prototypes de casques grandeur nature et les hôpitaux ont pu imprimer un modèle anatomique de cage thoracique adulte pour une étude préopératoire.
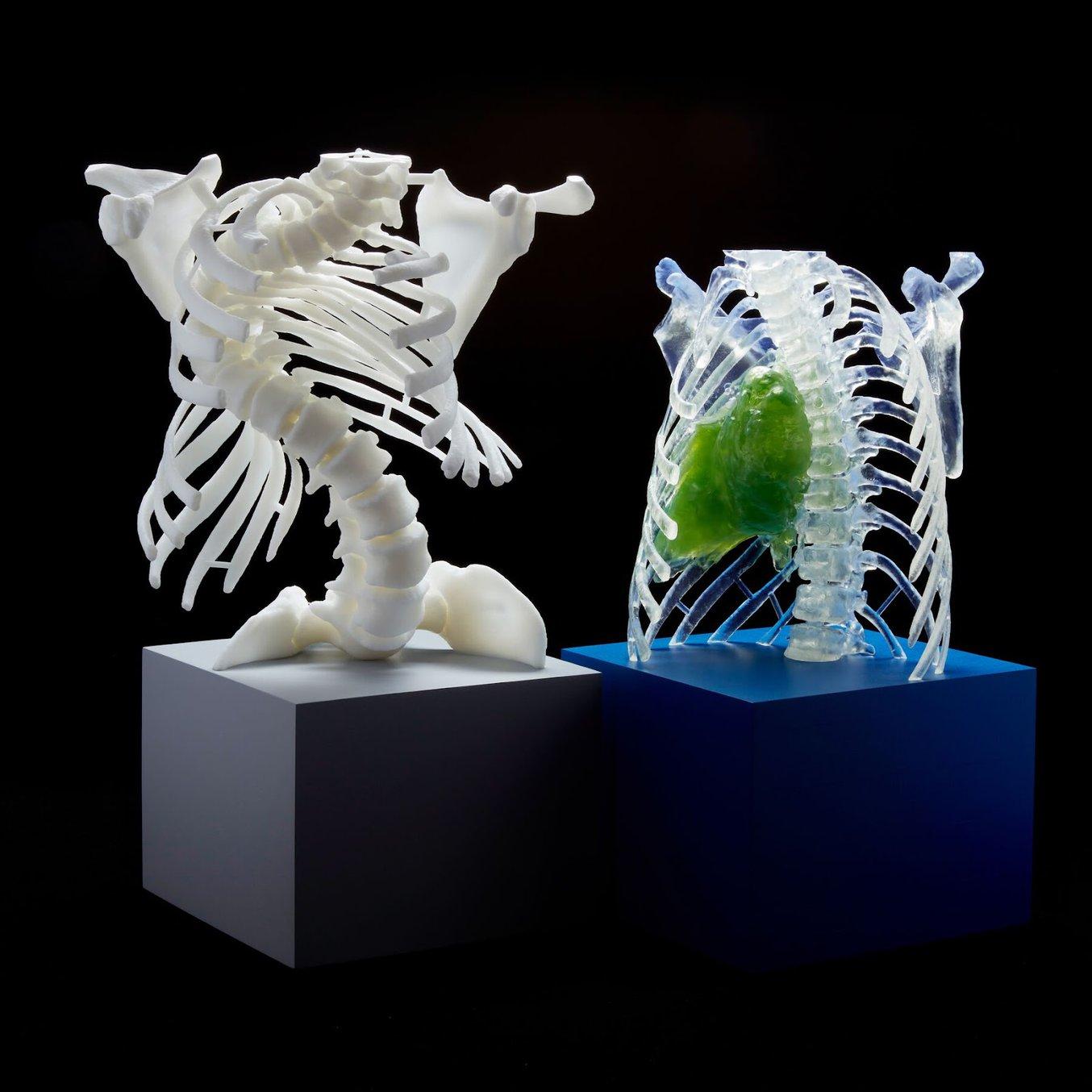
Cependant, chacun de ces clients devait faire face aux problèmes que représente un flux de travail incomplet : n'ayant pas de machine de post-traitement grand format à disposition, ils devaient acheter des produits tiers ou bricoler des solutions qui donnaient des résultats incohérents.
Prototypage de la Form Wash L et de la Form Cure L avec la Fuse 1
Le but des nouveaux produits était clair : il s'agissait simplement de créer des versions agrandies des systèmes Form Wash et Form Cure. Mais l'approvisionnement de certaines pièces est devenu problématique, car les problèmes globaux de chaîne d'approvisionnement se sont combinés à la pandémie de COVID-19 et ont retardé la livraison de nombreux matériaux dont l'équipe avait besoin pour le prototype.
« Nous avons rencontré pas mal de difficultés. Nous avions un calendrier serré et il était très difficile de préparer les matériaux nécessaires pour la phase de développement. Il y avait des problèmes de chaîne d'approvisionnement et nous devions respecter un calendrier de livraison plutôt strict », explique Megan Liu, ingénieur de chaîne d'approvisionnement chez Formlabs.
Heureusement, l'équipe disposait dans le même bâtiment d'une solution de qualité industrielle, tant pour le prototypage que pour la production. Le système SLS Fuse 1 a permis à l'équipe de Wash L/Cure L de réaliser rapidement de multiples itérations de chaque partie des deux machines, même lorsque certains processus de fabrication traditionnels étaient inaccessibles en raison de leur coût ou des délais. Six de ces pièces continuent d'être imprimées sur la Fuse 1 et font partie intégrante des produits finis.
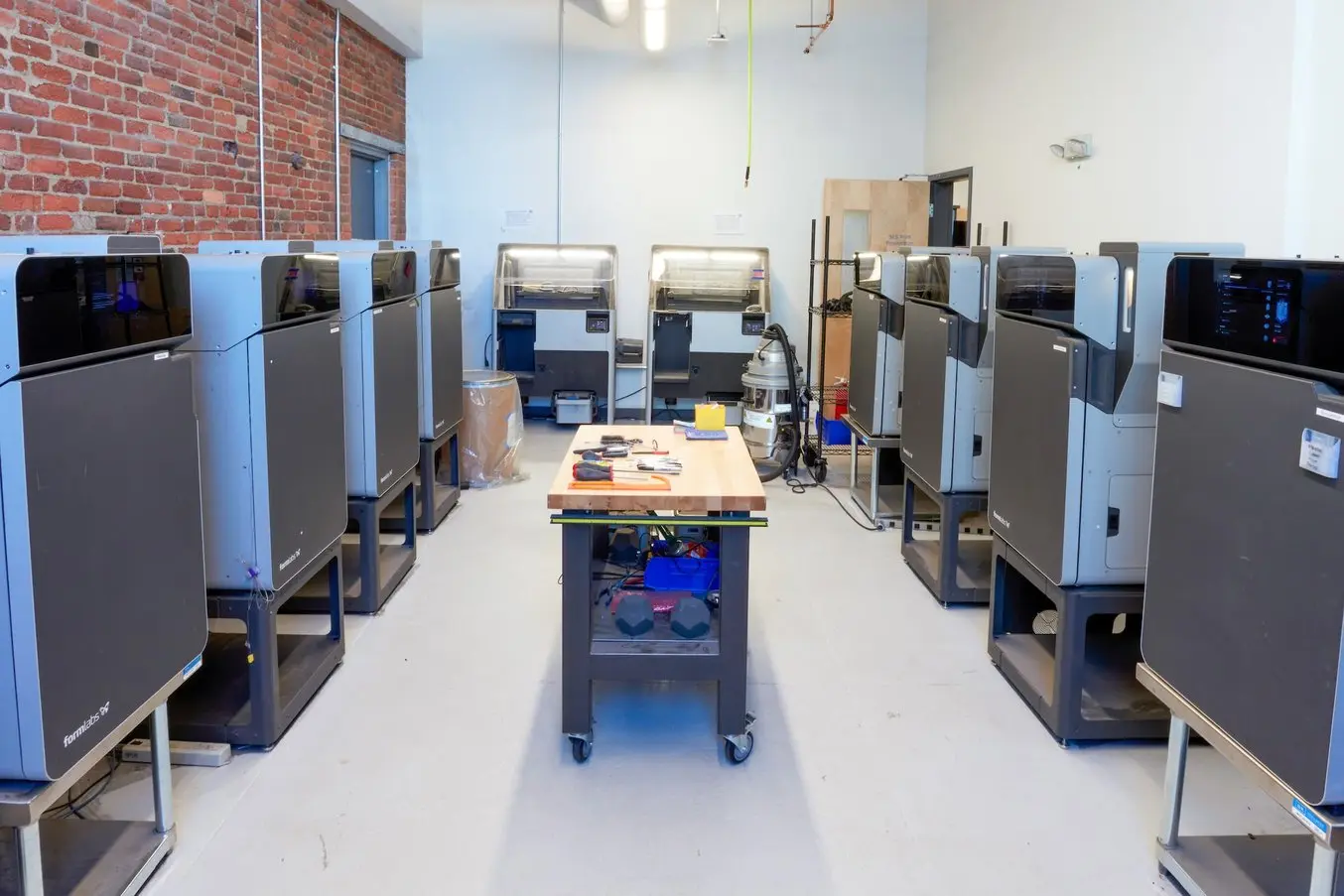
Fabrication de pièces de la Form Cure L avec la Fuse 1
Les unités Form Cure L expédiées aux clients comportent trois pièces imprimées sur la Fuse 1 : l'engrenage du plateau tournant, le support de l'aimant de la porte et l'entretoise de verrouillage. Les unités Form Wash L ont deux attaches de pompe différentes imprimées avec Nylon 12 Powder sur la Fuse 1, et la première série d'unités de production avait également un petit couvercle aimanté. Ce n'est pas la première fois que nos équipes d'approvisionnement mondial utilisent des imprimantes Fuse 1 pour fabriquer des pièces destinées aux produits Formlabs : il existe des pièces faisant partie des unités de production de la Fuse 1 qui ont été imprimées au centre de fabrication de Formlabs sur des unités Fuse 1 existantes.
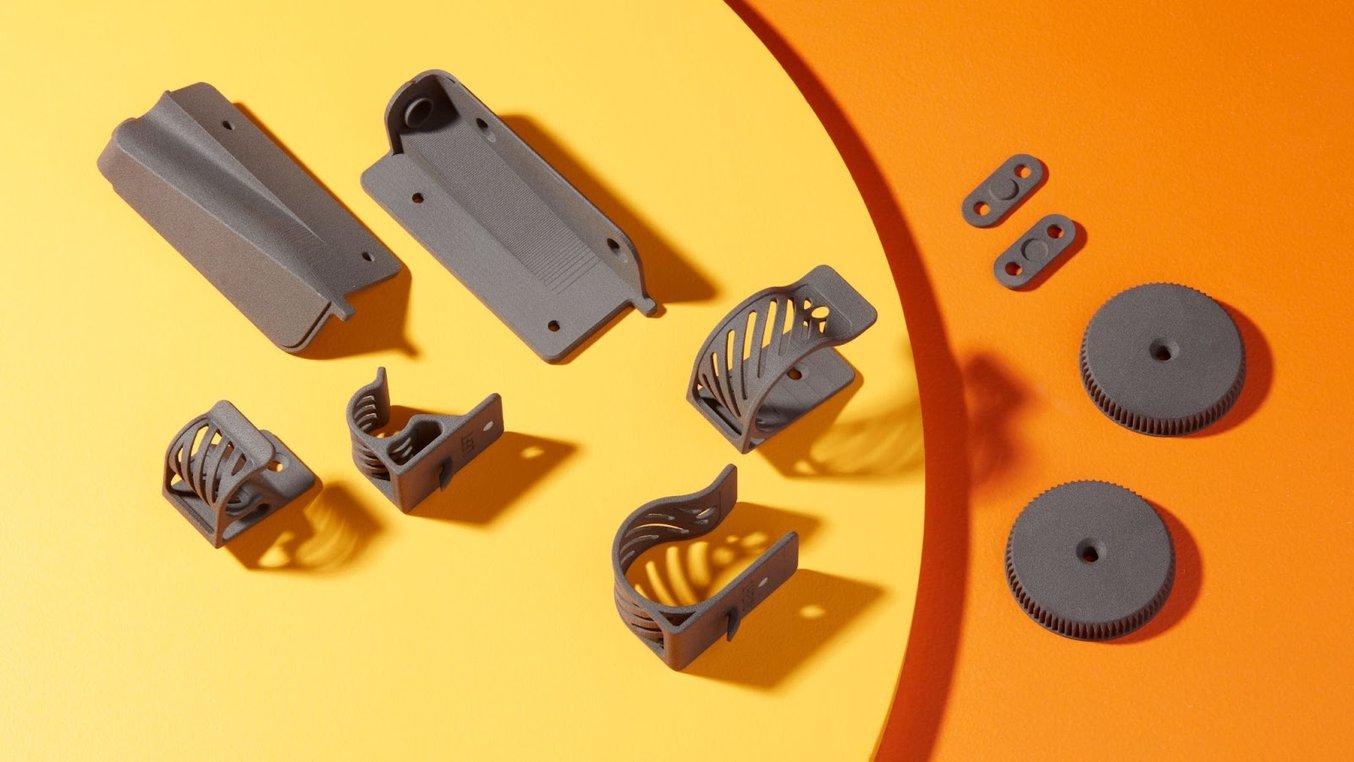
Pour concevoir l'engrenage du plateau tournant de la Form Cure L, l'équipe a dû itérer plusieurs fois pour s'assurer que le trou chanfreiné au centre pouvait saisir fermement le plateau tournant et générer une force suffisante pour le faire tourner. Après plusieurs conceptions et prototypes, ils ont choisi d'imprimer en 3D la pièce finale plutôt que de la mouler par injection en raison du noyau au centre. Un moule à injection aurait nécessité deux pièces pour réaliser ce noyau, mais l'impression SLS a permis aux concepteurs de fabriquer leur conception d'une seule pièce.
« Si la taille du trou de l'engrenage n'était pas conforme, nous pouvions la modifier immédiatement. Nous avons pu nous adapter très rapidement, arrêter ce qui ne fonctionnait pas et essayer quelque chose de nouveau. Le processus de changement entre les itérations était beaucoup plus facile, car nous savions que nous n'aurions pas à changer d'outil ou de fournisseur pour une nouvelle itération », explique Mme Liu.
Pour les entretoises de verrouillage de la Form Cure L, l'équipe a réalisé un prototype avec l'imprimante SLA Form 3, puis a imprimé la pièce finale sur la Fuse 1. L'équipe devait utiliser du plastique, car les capteurs de verrouillage fonctionnent mieux lorsqu'il n'y a pas de métal entre l'aimant et le capteur. Cette pièce assure l'étanchéité de la machine, permet de laisser un minimum de plastique devant le capteur et définit la distance du capteur en agissant comme quatre balises isolantes. L'équipe a pu réduire les délais et les coûts en passant de la phase finale du prototypage aux essais de production directement en interne, sans devoir commander d'outillage.
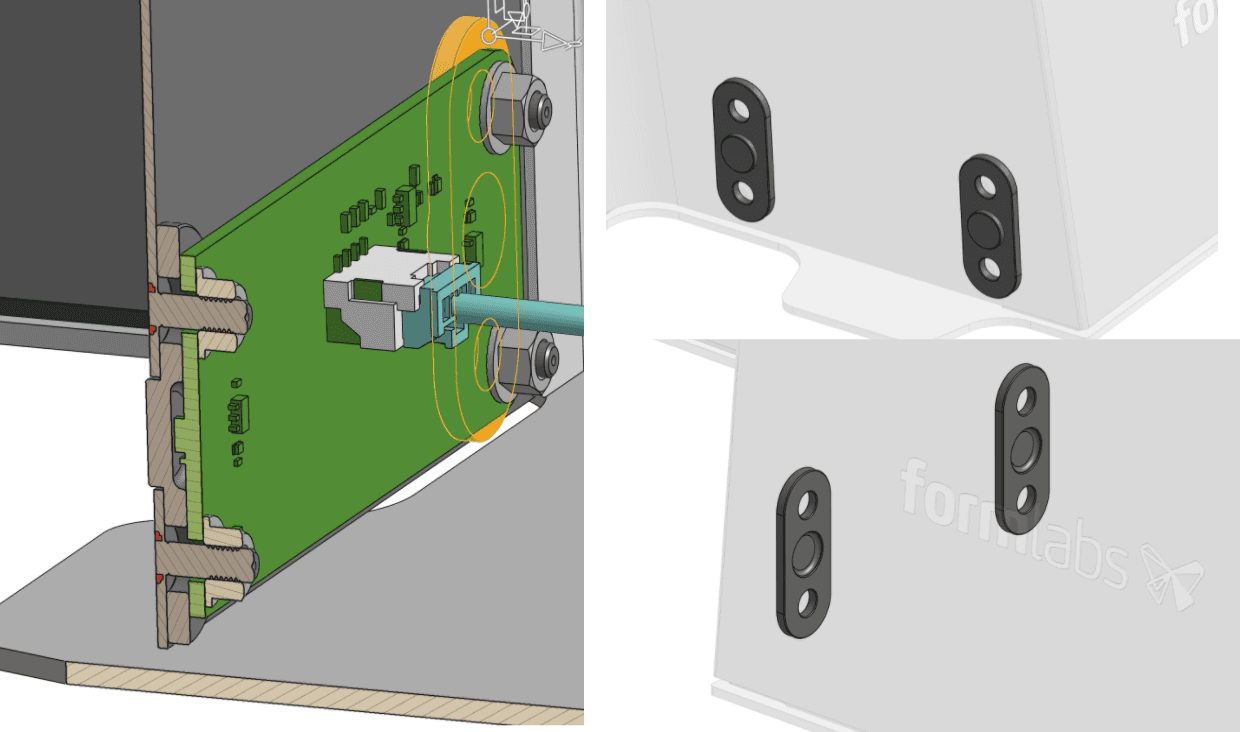
Les pièces de l'entretoise de verrouillage de la Form Cure L, rendues en CAO.
Les dernières pièces de la Form Cure L fabriquées sur la Fuse 1 sont deux supports d'aimants de porte qui maintiennent la porte de la Form Cure L fermée et la font « claquer ». Les pièces devaient être en plastique en raison d'interférence avec les aimants ainsi que pour des raisons tactiles : une pièce en métal aurait rayé la peinture et provoqué des bruits de raclage désagréables lors de la fermeture de la porte. Cette pièce devant répondre à des critères à la fois objectifs (la porte se ferme-t-elle ?) et subjectifs (quelle est la sensation de fermeture de la porte ?), il était difficile de définir un design avant que tous les autres composants ne soient finalisés. Si l'équipe avait dû confier la pièce à un mouleur par injection, le calendrier de production aurait été allongé de plusieurs semaines. L'impression en interne leur a permis de respecter leur calendrier serré.
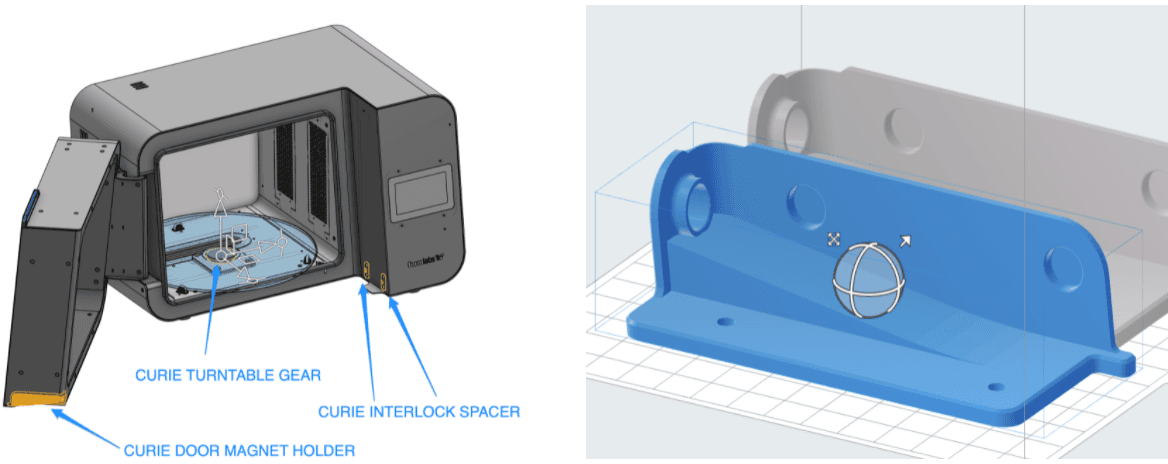
La Form Cure L comporte trois pièces imprimées sur la Fuse 1 (à gauche). Gros plan du support de l'aimant de porte (à droite).
Fabriquer la Form Wash L avec la Fuse 1
Les deux attaches de pompe maintiennent la pompe à solvant alimentée par batterie dans le compartiment de rangement de la Wash L. Ils ont dû être dimensionnés sur mesure pour s'adapter à la pompe, et ont été conçus spécifiquement pour plus d'efficacité. Leur design unique avec des côtés en spirale les empêcherait d'être fabriquées avec des méthodes traditionnelles. Tout au long du processus itératif, l'équipe a pu apporter des modifications à la conception sans avoir à refaire l'outillage. Comment la pièce était constamment repensée tout au long du cycle de développement, l'équipe disposait d'une marge de manœuvre beaucoup plus importante.
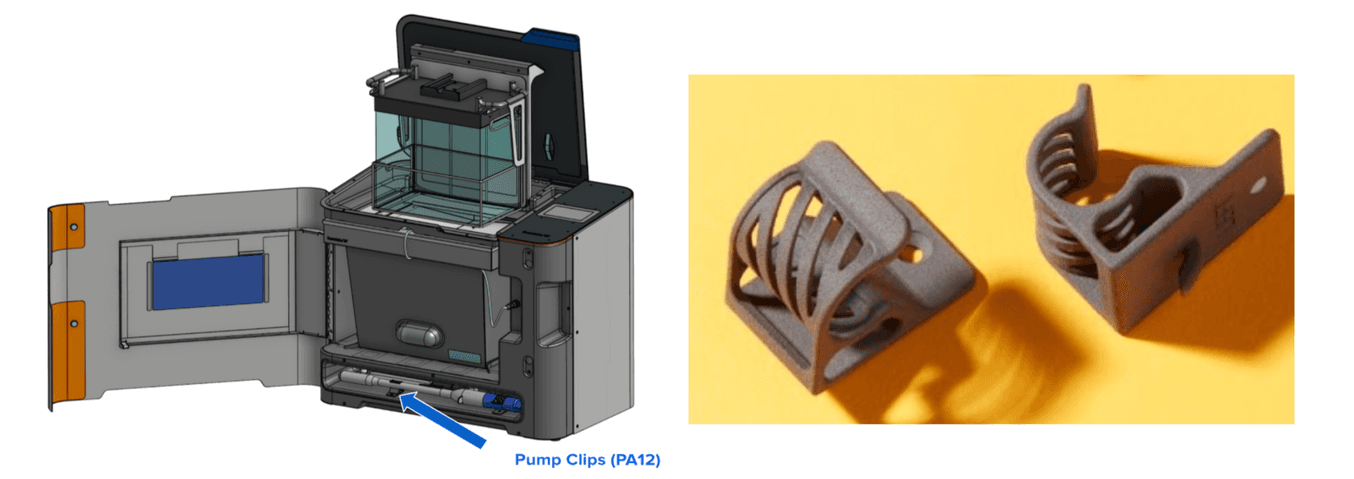
Dans la Form Wash L, un aimant maintient le moniteur de solvant en place à l'intérieur du seau de lavage. Pour protéger cet aimant de la rouille ou des rayures, l'équipe d'ingénieurs a conçu un petit couvercle pour aimant. L'impression de ces pièces pour les quelques centaines d'unités de production de la Wash L était une solution provisoire, et la pièce est actuellement fabriquée par moulage par injection. Bien que les délais d'exécution soient élevés, il était logique d'imprimer ces pièces sur la Fuse 1, car la petite pièce pouvait facilement être imbriquée dans d'autres grâce à l'algorithme d'agencement amélioré de la Fuse 1.
Délais raccourcis et problèmes de chaînes d'approvisionnement
Le calendrier de production de la Form Wash L et de la Form Cure L a coïncidé avec la pandémie de COVID-19, ainsi qu'avec des problèmes de chaîne d'approvisionnement qui ont affecté la capacité de l'équipe à se procurer des matériaux et à communiquer avec les sous-traitants.
Mme Liu et le reste de l'équipe d'ingénierie de la chaîne d'approvisionnement chez Formlabs ont développé des relations avec divers fournisseurs au fil des ans, et peuvent généralement espérer trouver les pièces dont ils ont besoin auprès d'un fournisseur ou d'un autre. En raison des retards de livraisons, de la fermeture d'usines en Chine, des grèves syndicales et des employés affectés par la COVID-19, il n'était plus possible de prototyper les matériaux en externe.
« Avoir les imprimantes en interne nous permet d'être très flexibles, même lorsque nous attendons l'arrivée d'échantillons que nous allons finalement fabriquer avec des méthodes traditionnelles : nous avons provisoirement utilisé les pièces imprimées en 3D pour rentabiliser notre temps. »
Megan Liu, Formlabs Global Sourcing
En raison de ces retards de matériaux, l'équipe Form Wash L et Form Cure L a vu son calendrier de travail habituel considérablement réduit. Au lieu de six semaines pour produire 600 unités, l'équipe disposait de la moitié de ce délai : elle devait produire 200 unités par semaine pour respecter ses échéances. Le parc d'imprimantes de Formlabs, située dans son usine de production de matériaux dans l'Ohio, n'avait pas la capacité nécessaire. L'équipe d'ingénieurs de Formlabs les a donc imprimées au siège social de Somerville.
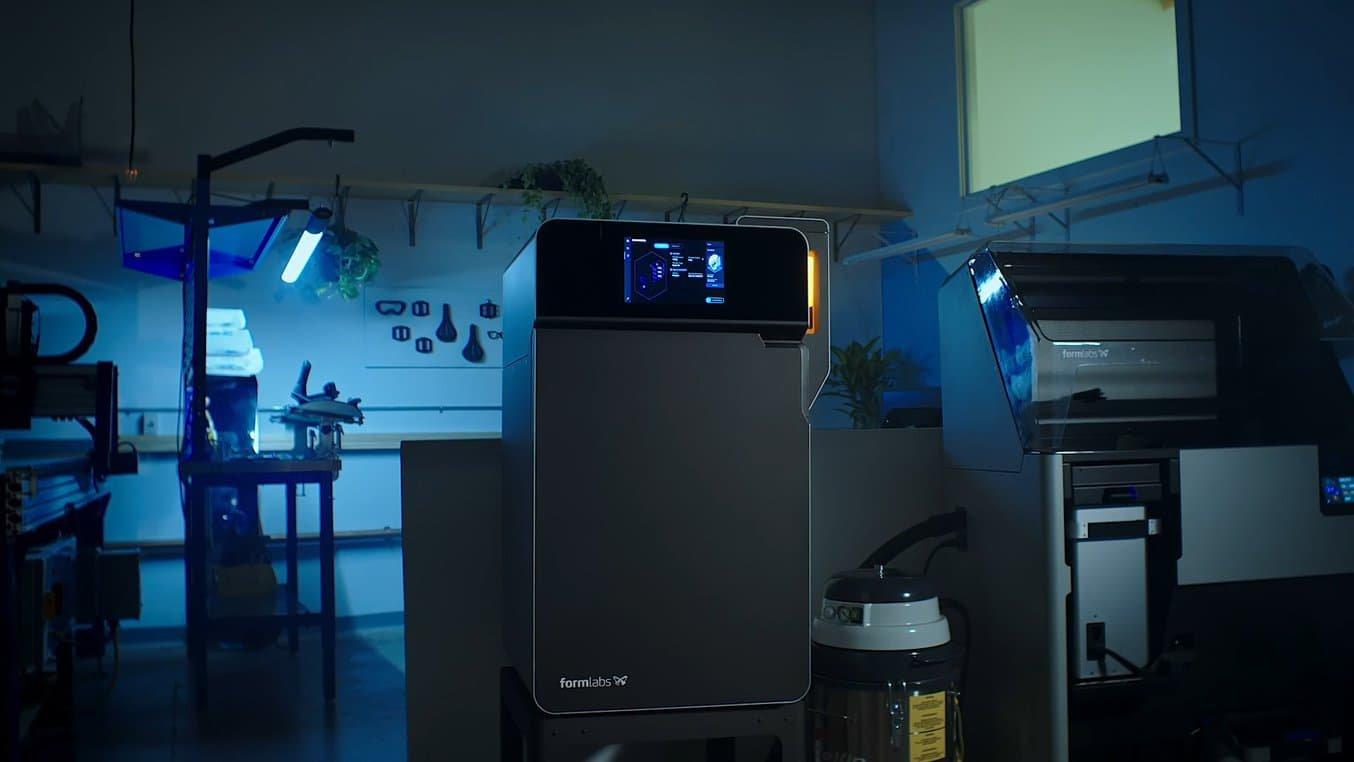
« Nous avons pu immédiatement doubler notre capacité en ayant ces imprimantes sous la main. Si nous avions fait appel à la sous-traitance et que le fournisseur avait fermé ses portes, il n'aurait pas été possible de transporter cet outil vers un nouveau fournisseur, mais grâce à nos imprimantes, nous avons pu décentraliser la fabrication et augmenter immédiatement notre capacité pour respecter le calendrier », explique Mme Liu.
Passage au moulage par injection : Quand et pourquoi ?
Une fois que l'équipe a réussi à produire ces 600 unités, elle a pu songer à passer à la production complète en s'accordant sur des délais et en établissant une estimation de la demande. Bien que certaines pièces telles que les deux attaches de la pompe, les entretoises de verrouillage et l'engrenage du plateau tournant aient intérêt à toujours être produites sur la Fuse 1, d'autres pièces, comme le couvercle de l'aimant, ont été moulées par injection.
Nous examinerons deux pièces (l'engrenage du plateau tournant et le couvercle de l'aimant) pour montrer comment cette décision a été prise et quand il est judicieux de passer de l'impression 3D SLS directe au moulage par injection traditionnel.
Pièce 1 : couvercle magnétique du capteur de saturation (Form Wash L)
Le couvercle magnétique du capteur de saturation aurait coûté 3700 $, et sa réalisation aurait pris plus d'un mois, ce qui aurait pu retarder tout le calendrier de production et les étapes d'itérations finales de la Form Wash L.
Le coût par pièce de l'impression du couvercle magnétique pour la Fuse 1, main d'œuvre comprise, n'était que de 2,20 $, ce qui était plus avantageux à condition que moins de 2000 pièces soient produites. L'équipe de Global Sourcing a décidé que l'impression 3D SLS était une excellente option de fabrication provisoire, mais une fois le moule réalisé, elle a réalisé qu'il serait plus économique de passer au moulage par injection.
SLS | Coût du moulage par injection, par pièce | IM tooling cost | |
---|---|---|---|
Couvercle magnétique du capteur de saturation | $2.20 | $0.11 | $3700 |
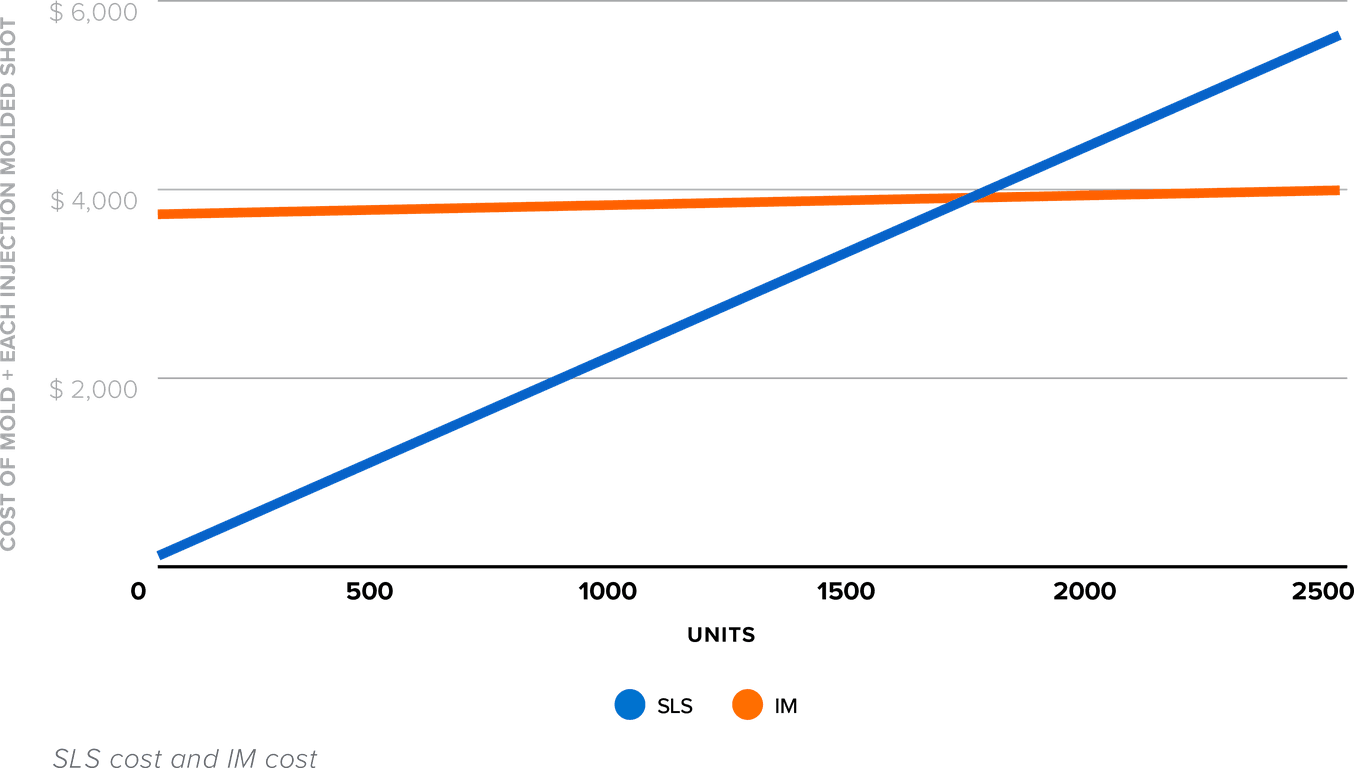
Pièce 2 : engrenage de plateau tournant
Cette pièce est dotée d'un trou chanfreiné au centre afin de saisir fermement la cheville du plateau tournant et de générer une force suffisante pour faire tourner la plateforme de la Form Cure L.
Il faudrait un moule en deux partie pour mouler cette pièce par injection, or un moule en deux parties est plus coûteux. Le coût estimé par le fabricant contractuel de moulage par injection était de 10 000 $.
SLS | Coût du moulage par injection, par pièce | Coût de l'outillage du moulage par injection | |
---|---|---|---|
Engrenage du plateau tournant | 3,50 $ | 2,20 $ | 3700 $ |
L'impression 3D SLS de l'engrenage du plateau tournant a permis aux concepteurs de ne modeler qu'une seule pièce. Par ailleurs, le coût par pièce n'était que de 3,50 $, ce qui signifie que le seuil de rentabilité pour le moulage par injection se situait à des quantités proches de 8000 unités. L'équipe a décidé d'imprimer la pièce avec la Fuse 1, ce qui lui a permis d'économiser des milliers de dollars et de réduire le coût du produit final. Jusqu'à ce niveau de production, l'équipe a ainsi disposé de plus de temps pour planifier et commander des moules, avant de passer au moulage par injection lorsqu'il est devenu plus économique. L'impression 3D SLS de ces pièces leur a ainsi permis d'accélérer le lancement et de se concentrer sur d'autres parties du produit.
Peut-on remplacer le moulage par injection par l'impression 3D ?
Le parc d'imprimantes Fuse 1 est un élément complémentaire de la chaîne d'approvisionnement. Bien qu'il ait remplacé les méthodes de production traditionnelles pour certaines pièces, l'outillage, le coulage, le moulage et l'usinage restent des éléments nécessaires du cycle de vie d'un produit. Le fait de pouvoir s'appuyer sur des imprimantes 3D de qualité industrielle permet au fabricant de mieux contrôler le processus et le protège des variables externes telles que les retards dans l'approvisionnement en matières premières ou les longs délais d'approvisionnement en outillage.
Les imprimantes SLS Fuse 1 ont permis aux ingénieurs de Formlabs de livrer deux produits dans un délai serré et de surmonter les obstacles posés par la pandémie de COVID-19 ainsi que les problèmes de chaîne d'approvisionnement. Les unités de production Form Wash L et Form Cure L comportent chacune plusieurs pièces imprimées avec les produits Formlabs, ce qui prouve que la Fuse 1 est une solution de développement et de fabrication de produits complète. Dans le livre blanc sur l'impression 3D SLS et le moulage par injection, nous avons examiné toutes les applications possibles pour fabriquer des pièces d'utilisation finale avec l'imprimante SLS Fuse 1, des pièces de rechange aux prothèses personnalisées en passant par les pièces détachées de moteurs.