Kriwat GmbH est un fournisseur de services médicaux spécialisé en orthopédie et dont le siège se trouve à Kiel, en Allemagne. Depuis ses débuts, l'entreprise se caractérise par son souci unique de combiner les meilleures performances sportives et la recherche médicale de pointe.
Michael Kriwat a créé l'entreprise en 1987. Il était alors l'un des premiers experts en Allemagne dans le domaine de l'analyse de la marche sur tapis roulant pour les athlètes amateurs et professionnels. Depuis, l'entreprise s'est étendue sur six sites à Kiel, Hambourg et Preetz, et compte aujourd'hui une équipe de 75 personnes. Elle a également étendu ses services à la fourniture de soins personnalisés aux patients dans le domaine des bandages, des semelles, des orthèses et des chaussures orthopédiques.
Le secteur des soins orthopédiques est confronté à une grave pénurie de main-d'œuvre qualifiée : peu de jeunes professionnels veulent se lancer dans ce processus laborieux qu'est la création d'orthèses. Ils sont encore moins à vouloir assumer la responsabilité de la gestion de ces petites et moyennes entreprises, qui sont souvent familiales.
Découvrez comment Lais Kriwat, le fils de Michael, a mis au point un flux de travail numérique pour la production de semelles grâce à l'impression 3D à frittage sélectif par laser (SLS) afin de moderniser l'entreprise et de relever ces défis. L'entreprise est ainsi sur la bonne voie pour produire 10 000 paires de semelles cette année grâce à l'impression 3D.
Transformer un métier manuel grâce à l'impression 3D
Le processus traditionnel de production de semelles orthopédiques est extrêmement complexe et gourmand en main d'oeuvre, tant pour le client que pour le fournisseur. Tout d'abord, le client place son pied dans un moule en mousse pour créer une empreinte. Un liquide polymère est versé dans cette empreinte pour recréer la forme du pied, qui est ensuite utilisée pour produire une semelle orthopédique adaptée.
Ce travail nécessite des compétences spécialisées et des qualités pratiques dans un environnement rempli de poussière et de vapeurs chimiques. « C'est quelque chose qui m'a beaucoup gêné pendant ma formation. Beaucoup de choses devaient être produites à l'aide de produits chimiques. Il fallait beaucoup poncer, ce qui impliquait un contact permanent avec les produits chimiques et la poussière. C'est la raison pour laquelle je me suis fixé comme objectif de faire les choses différemment afin de ne pas être autant en contact avec les produits chimiques », a déclaré Lais Kriwat.
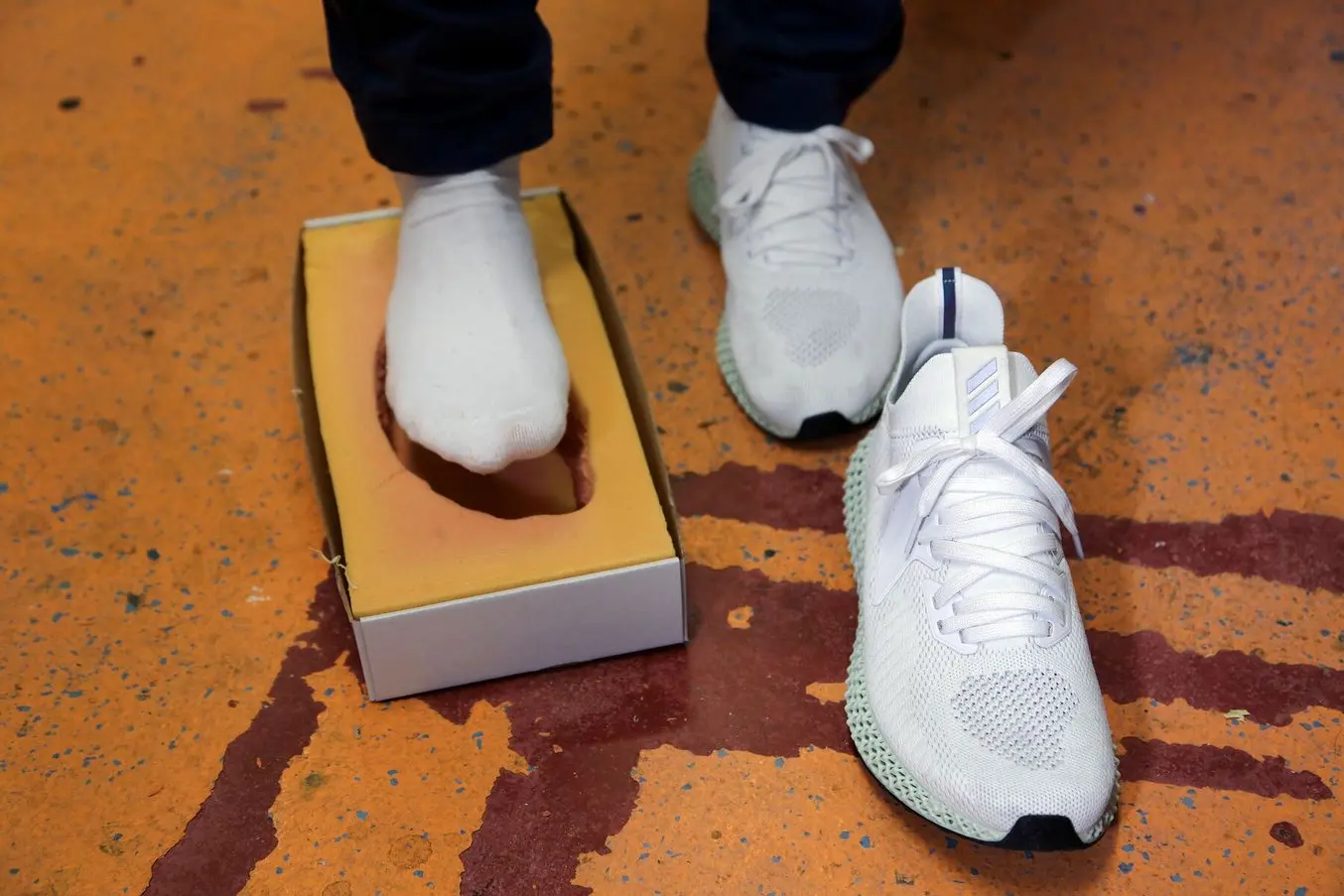
En général, les empreintes des pieds des clients sont prises à l'aide d'un moule en mousse.
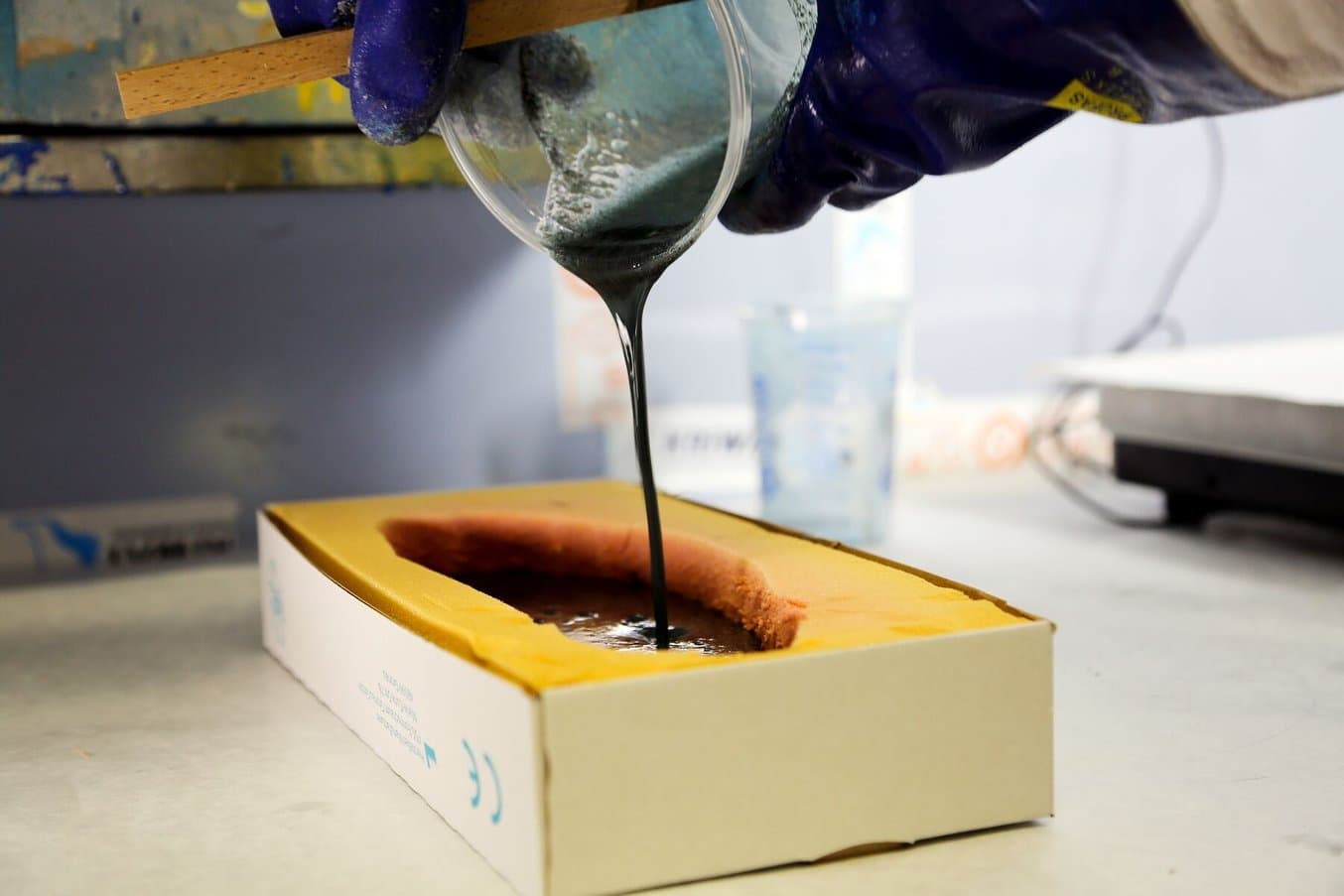
Le moule est ensuite rempli de produits chimiques pour recréer la forme du pied.
Étant donné qu'il est entré dans le secteur il y a peu, Lais a pu faire l'expérience directe des défis posés par le flux de travail traditionnel et a réalisé qu'il était temps d'apporter des changements.
« Le plus grand défi de notre secteur aujourd'hui est clairement le manque de personnel. Il est difficile de trouver des personnes qui souhaitent encore exercer notre profession et qui sont intéressées par l'artisanat en tant que travail. Nous devons rendre le travail intéressant, et c'est là que les nouvelles technologies sont très importantes », a déclaré Lais Kriwat.
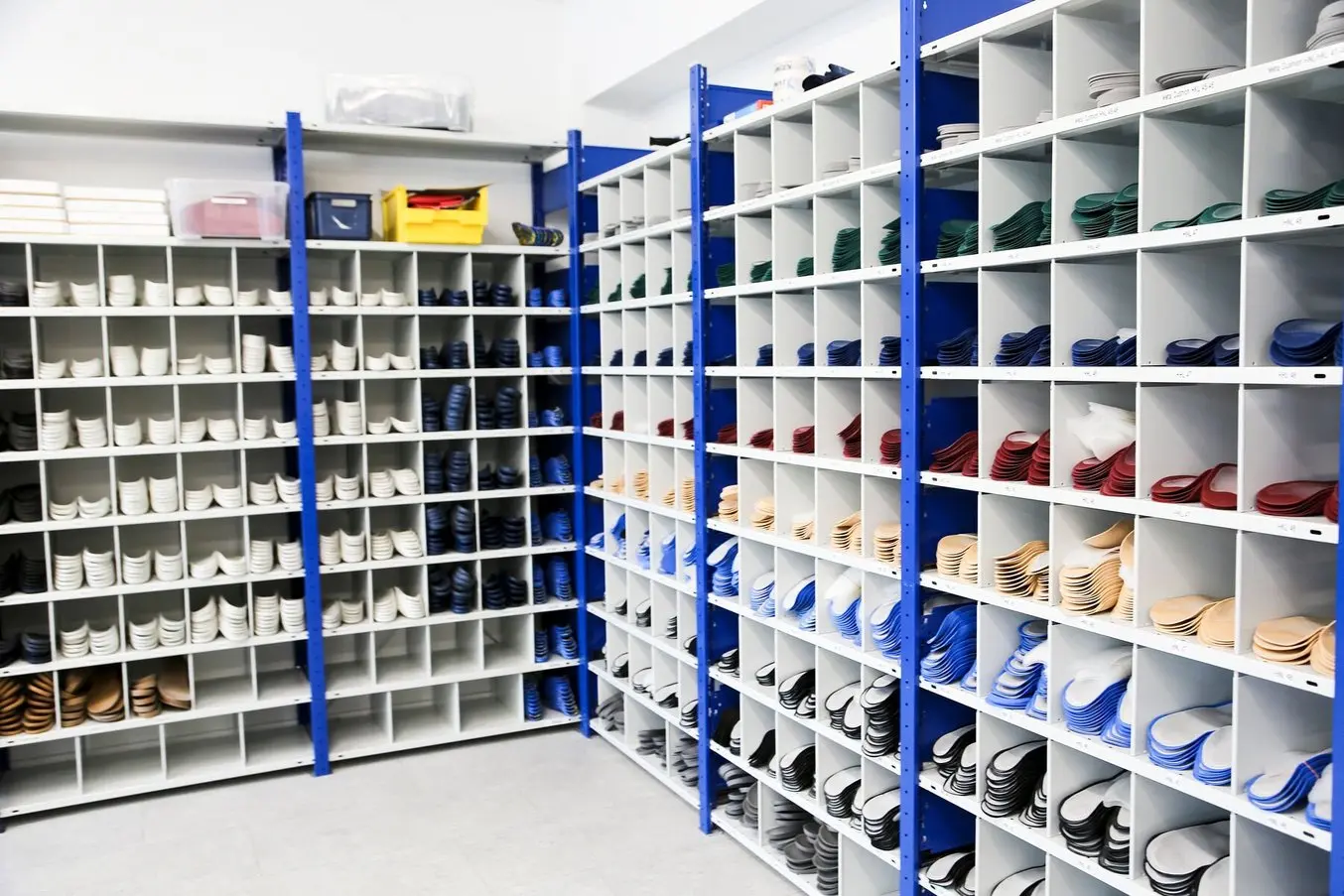
Kriwat GmbH produit des milliers de semelles chaque année.
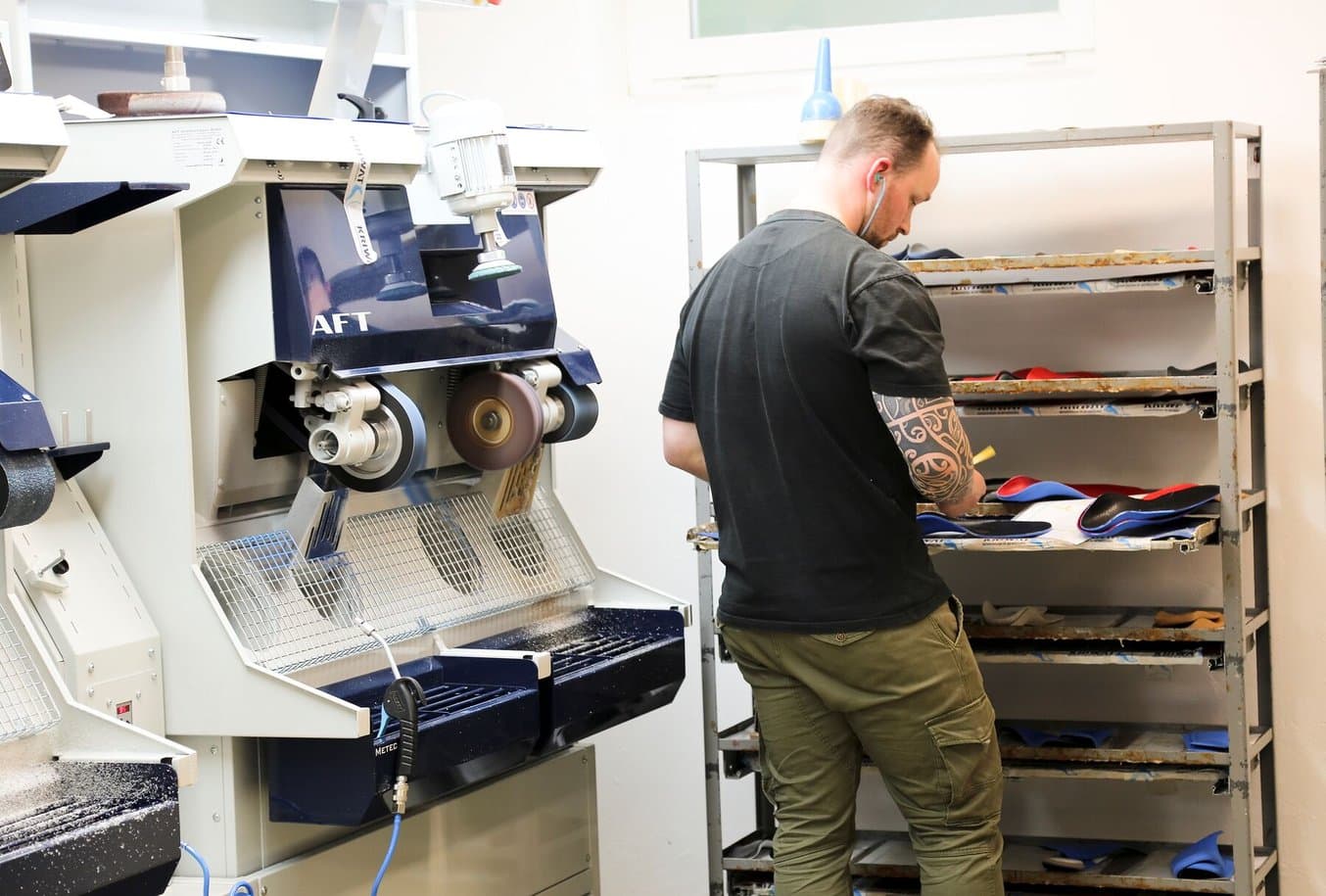
Le processus traditionnel de production de semelles orthopédiques est extrêmement gourmand en main-d'œuvre.
Lais a commencé à se familiariser avec l'impression 3D en 2017, en imprimant des projets de loisirs et des prototypes sur une petite imprimante 3D à dépôt de fil fondu (FDM). Au fur et à mesure qu'il se familiarise avec la conception et l'impression 3D, il commence à explorer les moyens de les mettre en œuvre dans l'entreprise familiale. Après avoir découvert la technologie de la stéréolithographie (SLA), l'entreprise familiale a investi dans une imprimante Form 3BL pour les modèles à l'échelle humaine, ce qui a ouvert de toutes nouvelles possibilités pour la production d'orthèses. Lais a commencé à maîtriser de nouvelles applications étape par étape, et a finalement tourné son attention vers ce qui constitue le gros de leur activité : les semelles intérieures.
« Au début, il s'agissait d'un projet dont je ne connaissais pas vraiment les prochaines étapes. C'est pourquoi j'ai commencé à chercher de très bons partenaires, et je suis tombé sur Formlabs. Je dois dire que cela a été un véritable coup de chance pour moi, car j'ai pu concrétiser l'idée que j'avais en tête. J'ai pu envoyer des conceptions, et ils les ont imprimées pour que je puisse voir si cette technologie 3D était vraiment adaptée. Je n'avais aucune expérience dans ce domaine et Formlabs m'a énormément aidé », déclare Lais Kriwat.
Étape par étape, Lais a numérisé le flux de production des semelles et validé les produits finis en les testant à la fois en interne et auprès des clients. Grâce au nouveau flux de travail numérique, les empreintes manuelles de pieds sont remplacées par la numérisation 3D, la longue liste d'étapes manuelles est réduite par la conception numérique et l'impression 3D, et les pièces imprimées en 3D sont combinées au flux de travail traditionnel pour créer le produit final.
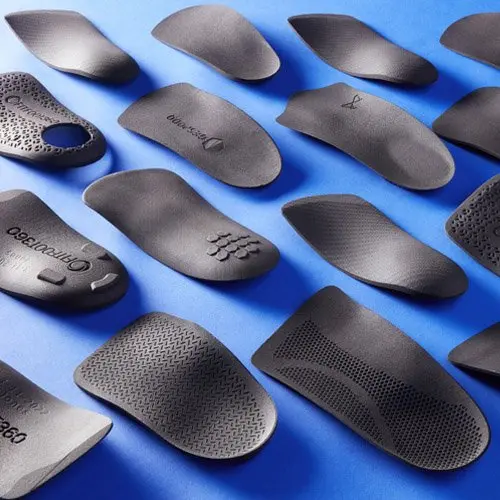
Impression 3D de semelles rigides
Découvrez comment produire des semelles intérieures solides et ductiles dépassant les 4 millions de cycles de pliage grâce à l'écosystème SLS compact et abordable de Formlabs. Ce guide complet vous aidera à vous lancer dans la production d'enveloppes de semelles sur la Fuse 1+ 30W.
Quels sont les avantages de l'impression 3D pour la production de semelles ?
L'équipe de Kriwat utilise deux imprimantes 3D SLS Fuse 1+ 30W et Nylon 11 Powder pour produire des noyaux de semelles individuels et même des semelles entières. Naturellement, avant de passer à la production numérique, il était extrêmement important pour Lais de montrer que le nouveau processus de production d'une semelle orthopédique présentait réellement des avantages décisifs tant pour l'entreprise que pour les clients. Examinons les principaux avantages qu'il a mis en évidence.
Gains de temps
Avec le nouveau flux de travail, il est possible de réaliser un scan 3D, de créer un modèle numérique à partir de celui-ci le même jour, de le grouper avec d'autres semelles et de toutes les imprimer avec la Fuse 1+ 30W pendant la nuit. L'équipe de M. Kriwat peut alors post-traiter les pièces, suivre le processus traditionnel de production et terminer les semelles le lendemain.
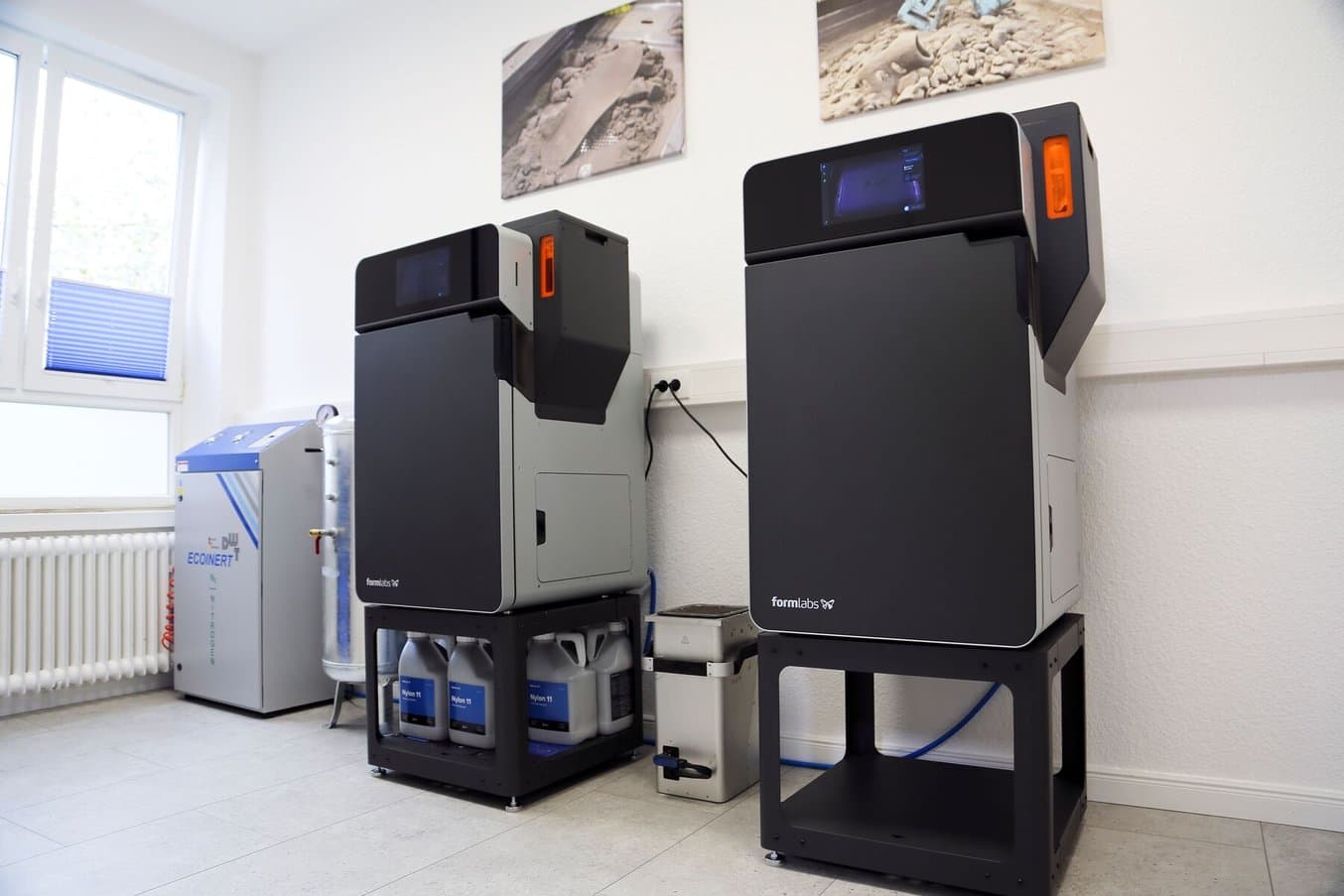
Kriwat GmbH dispose désormais de deux imprimantes 3D SLS Fuse 1+ 30W.
« Nous avons désormais la possibilité de créer une orthèse parfaitement adaptée à un patient en l'espace de 24 heures. C'est quelque chose qui nous offre bien sûr un grand avantage parce que nous pouvons fournir des soins rapidement, mais en fin de compte, le plus important est le patient, à qui nous pouvons fournir les meilleurs soins dans le délai le plus court possible. »
Lais Kriwat, maître technicien en chaussures orthopédiques, direction de Kriwat GmbH
Réduction des coûts
Par rapport à la fabrication manuelle traditionnelle, le nouveau flux de travail numérique offre des avantages conséquents en termes de coûts des matériaux et, surtout, de coûts de personnel. Avec le flux de travail, de nombreuses étapes sont désormais numériques et ne nécessitent pas de matériaux ou de main-d'œuvre importante. Pour les volumes requis par Kriwat, l'achat d'un scanner 3D et d'un logiciel de conception est moins coûteux que les grandes quantités de mousse et de produits chimiques liquides.
En outre, les employés peuvent prendre en charge plus de patients par jour car le flux de travail est plus rapide, ce qui réduit les coûts de main-d'œuvre. Lais estime que les coûts de production ont baissé d'environ 15 à 17 % grâce à l'impression 3D.
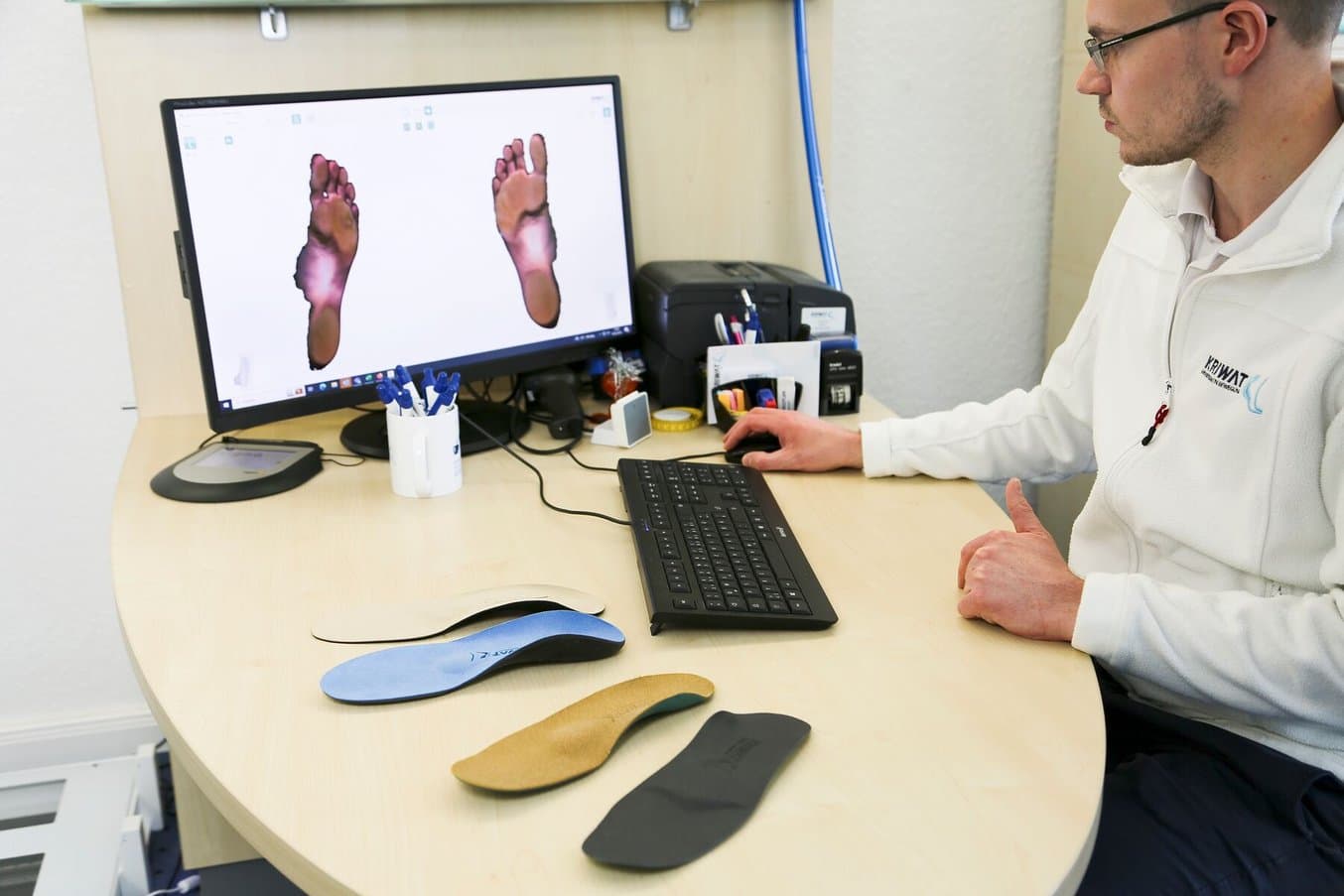
La numérisation 3D permet de prendre une empreinte plus précise et plus complète du pied, tout en facilitant l'envoi des données sous forme numérique.
Bien que l'équipe de Kriwat ait immédiatement compris que l'installation d'imprimantes 3D en interne était la clé pour réduire les coûts et améliorer leur flux de travail, la plupart des solutions d'impression 3D SLS étaient hors de leur gamme de prix et leur prix dépassait largement les six chiffres. L'imprimante SLS Fuse 1+ 30W était la seule machine qui offrait la solution industrielle qu'ils recherchaient à un prix accessible aux petites et moyennes entreprises.
« Avec Formlabs, le grand avantage est évidemment l’aspect financier. En tant qu'entreprise de taille moyenne, je peux me permettre cet investissement, mais d'autres fabricants sont bien trop chers pour nous ainsi que pour d'autres entreprises dans notre secteur. »
Lais Kriwat, maître technicien en chaussures orthopédiques, direction de Kriwat GmbH
Processus de travail simplifié
L'impression 3D SLS avec la série Fuse offre de nombreux avantages qui simplifient le flux de travail pour la production de semelles. Comme les pièces imprimées ne nécessitent pas de supports, de nombreuses semelles peuvent être imprimées ensemble en une seule fois, ce qui optimise le flux de travail et réduit les coûts. Les pièces finies présentent une surface légèrement rugueuse, idéale pour le collage d'additifs et d'enveloppes pour les différents types de produits finis. Les pièces en nylon peuvent également être usinées et rectifiées pour obtenir une finition parfaite du produit final.
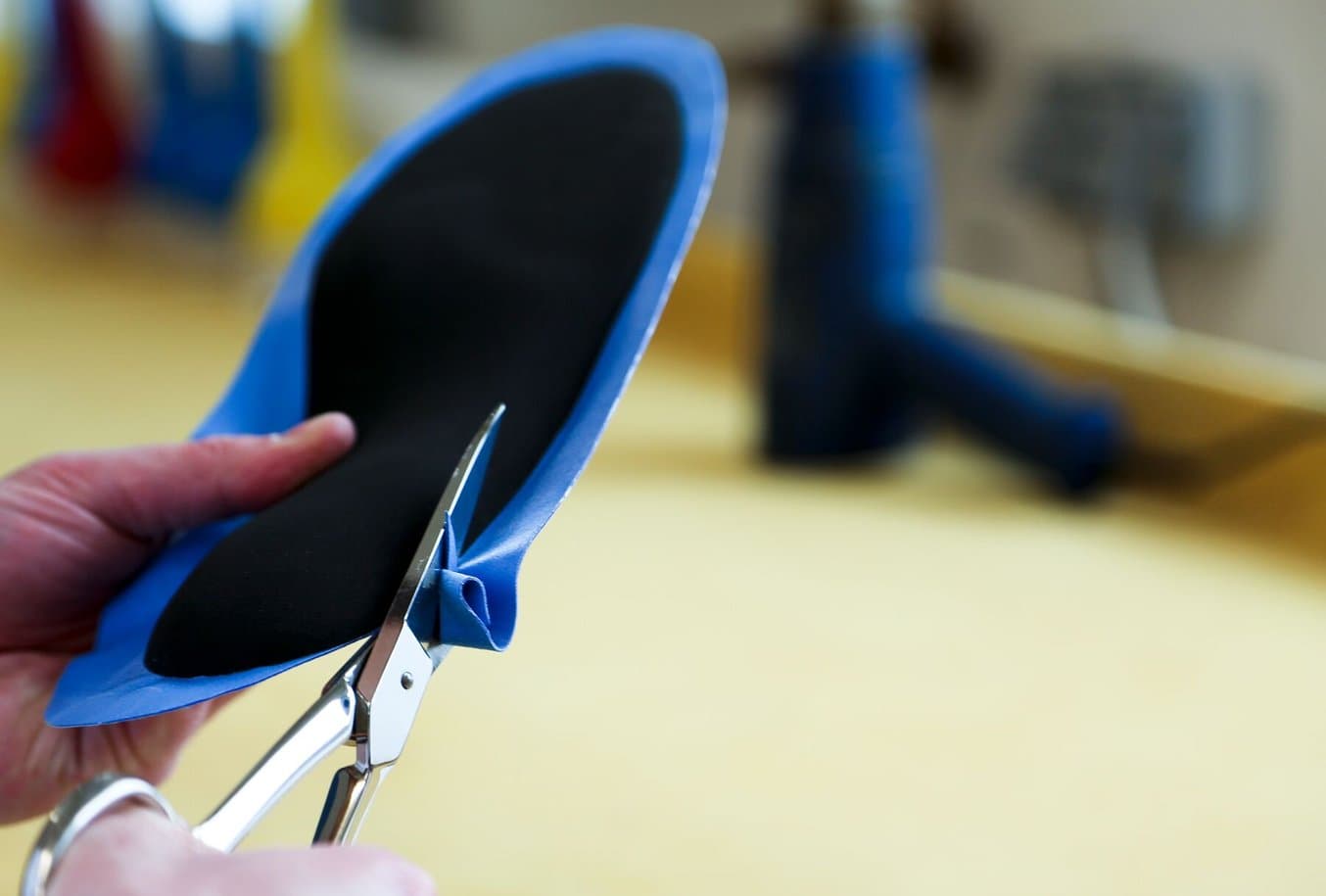
Les semelles et les noyaux de semelles imprimés en 3D sont combinés avec des enveloppes et d'autres matériaux pour créer le produit final.
Dashboard est un outil en ligne qui permet aux opérateurs de gérer plusieurs imprimantes 3D, de suivre les impressions et l'utilisation des matériaux, et de recevoir des notifications sur l'état des impressions, ce que Lais a trouvé essentiel pour la planification. Après avoir travaillé avec une longue liste de logiciels de découpe d'imprimantes 3D au cours de sa carrière, il a également trouvé que PreForm, le logiciel de préparation d'impression pour les imprimantes Formlabs, était simple et facile à utiliser.
« PreForm est le logiciel idéal pour lancer une impression rapidement. Pour nous, il est également important de montrer à nos employés à quel point imprimer en 3D peut être facile. PreForm est parfait parce que l'utiliser est un jeu d'enfant : il est facile à expliquer et on peut très rapidement envoyer la tâche à l'imprimante », a déclaré Lais Kriwat.
Amélioration de la logistique
La numérisation simplifie également la gestion de la logistique. Kriwat GmbH dispose désormais de scanners 3D dans ses bureaux de Hambourg, ce qui facilite grandement l'envoi des données numériques au siège de Kiel, où l'équipe peut alors concevoir les différents produits. Auparavant, ils devaient transporter les empreintes jusqu'à leur siège où les semelles sont produites, ce qui prenait beaucoup plus de temps et était beaucoup plus coûteux, car ils devaient régulièrement parcourir de longues distances.
Durabilité
Outre la réduction des transports, l'impression 3D rend le flux de travail plus durable à bien des égards. Avec le flux de travail numérique, il faut beaucoup moins de matières premières pour produire le produit final, car il ne faut plus créer de réplique de pied. Kriwat GmbH n'a plus besoin de réfléchir au meilleur moyen d'éliminer les milliers de modèles de pieds, les mousses inutilisées et les déchets chimiques. Grâce au système efficace de la série Fuse, la poudre non frittée peut être recyclée pour l'impression suivante, créant ainsi un flux de travail circulaire qui peut réduire ou même éliminer complètement les déchets.
« Le développement durable est le sujet le plus important pour ma génération. Mon objectif était de ne devoir jeter qu'un minimum de matériau. Par exemple, nous avons ici une poubelle enpour les déchets en plastique, et mon objectif était qu'elle ne soit pas ramassée toutes les semaines, mais toutes les quatre semaines. Je voulais également réduire l'utilisation de produits chimiques et en jeter moins. La technologie SLS de Formlabs est parfaitement adaptée, car nous n'imprimons que ce dont nous avons vraiment besoin », a déclaré Lais Kriwat.
L'avenir de l'innovation en matière de semelles
Pour sa première année, l'objectif de Kriwat est de numériser environ 50 % de sa production de semelles intérieures et d'imprimer environ 10 000 paires de noyaux de semelles et de semelles complètes. Mais leurs deux imprimantes 3D SLS Fuse 1+ 30W offrent également de nombreuses possibilités pour l'avenir.
« Lors de la première étape de la numérisation, notre objectif était de numériser le processus traditionnel. Nous pouvons ainsi introduire les formes de nos semelles dans l'ordinateur et les imprimer en 3D. Par la suite, nous pourrons imprimer en 3D des produits entièrement nouveaux », a déclaré Lais Kriwat.
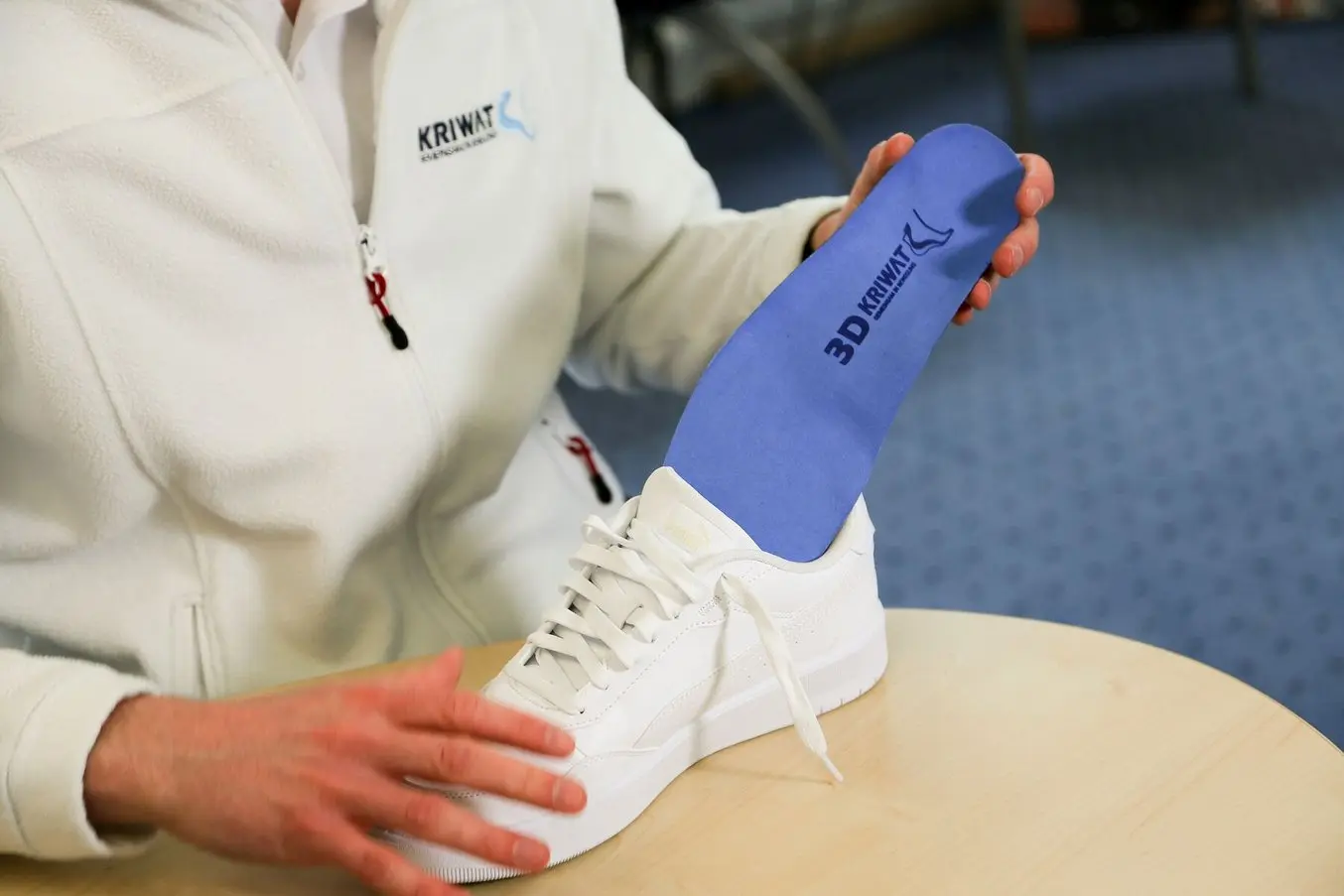
Après avoir numérisé la ligne de produits actuelle, l'objectif de Kriwat est de proposer de nouveaux produits innovants grâce à l'impression 3D.
Les possibilités offertes par la liberté de conception de l'impression 3D SLS comprennent la redistribution de la pression pendant la marche, des produits individuels haut de gamme, certains supports impossibles à produire avec des méthodes traditionnelles, et des produits de qualité qui offrent au pied un soutien optimal pour des sports tels que la course et le football.
« Je suis très enthousiaste à l'idée que nous allons amener sur le marché de nouvelles innovations auxquelles on ne pouvait que rêver il y a 15 ans. La technologie 3D offre aujourd'hui énormément de nouvelles possibilités. Des choses impensables aujourd'hui deviendront bientôt réalité. »
Lais Kriwat, maître technicien en chaussures orthopédiques, direction de Kriwat GmbH
Pour en savoir plus sur l'impression 3D de semelles, visitez notre page d'application ou contactez nos experts médicaux si vous avez des questions sur le flux de travail ou les solutions d'impression 3D de Formlabs.