Maximiser le volume d'impression avec des modèles à éléments rétractables et pliables
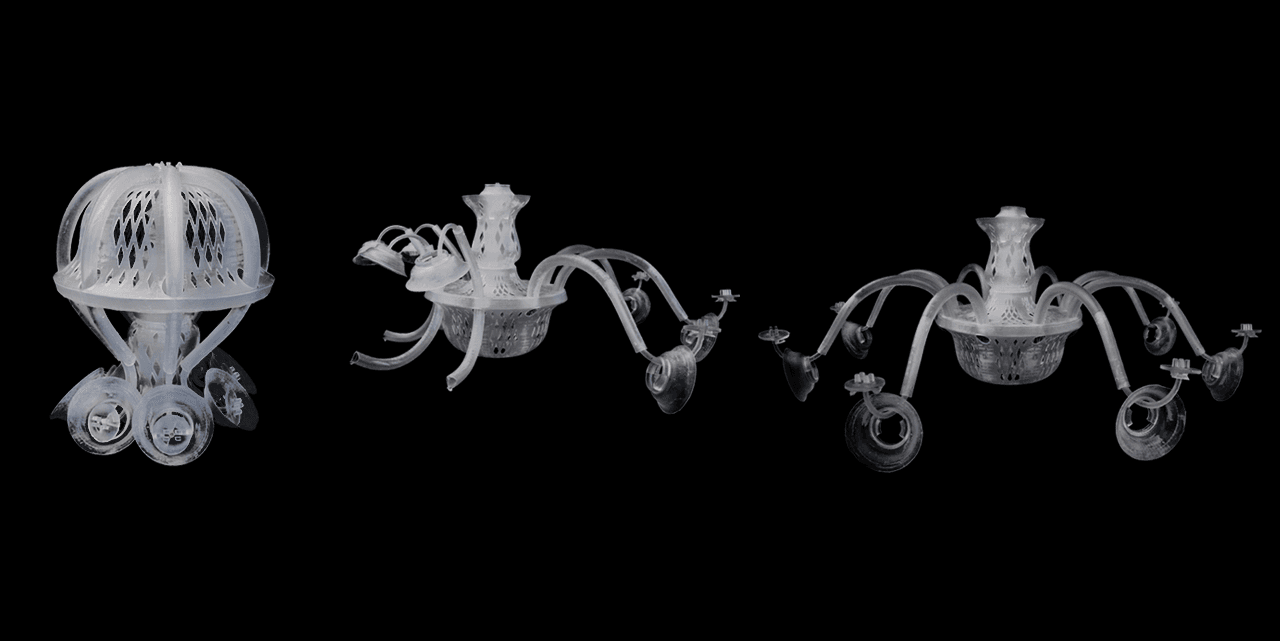
Il existe plusieurs façons d'imprimer des pièces plus grandes que le volume d'impression de votre imprimante 3D de bureau. Découpez les pièces en plusieurs sous-ensembles plus petits qui seront ensuite collés, ou ajoutez des ajoutez des filetages et des logements d'écrou pour renforcer la liaison mécanique dans le cas de pièces fonctionnelles.
Pour les concepteurs CAO expérimentés (ou aventureux), il est possible d'intégrer au modèle 3D des éléments tels que des articulations, des parties déployables ou mobiles, qui permettront de fabriquer des pièces de grande taille en une seule impression et sans assemblage. Ces éléments complexes, surplombs et cavités peuvent permettre l'utilisation intégrale du volume d'impression d'une imprimante 3D.
Parmi ces éléments à envisager dès la conception pour gagner de la place, on peut citer :
- Éléments pliables : Ces éléments relient différentes parties d'un assemblage qui, après impression, peuvent être dépliés, comme le seraient une table pliante ou des chaises escamotables.
- Éléments extensibles ou rétractables : Ils existent déjà dans des objets courants, comme les parapluies ou les casques audio, et permettent d'en modifier la taille ou de les ajuster précisément.
Dans ce guide, l'équipe de concepteurs et d'éclairagistes artistiques du Studio Waldemeyer vous présentent des modèles de lustres étonnants, montrant comment utiliser certains éléments pour concevoir et optimiser des modèles complexes qui peuvent être dépliés et déployés après impression 3D par stéréolithographie (SLA).
Note : Cet article est destiné plus particulièrement aux concepteurs CAO confirmés ayant une expérience en impression 3D.
Découvrez comment le Studio Waldemeyer a conçu ce lustre exceptionnel.
Tester les limites de l'impression 3D SLA
Le Studio Waldemeyer a travaillé sur ce projet de lustre pour tester les limites extrêmes du volume d'impression de l'imprimante 3D SLA Form 2.
Pendant la phase de conception, il leur a fallu considérer la charge que devaient supporter les points de connexion, en fonction de l'usage prévu de la pièce.
Pour l'impression de ces lustres, le Studio Waldemeyer a utilisé les résines standards Black Resin et Clear Resin et une résine technique, Rigid Resin. Ces matériaux présentent en effet une rigidité et une solidité suffisantes des éléments de faible épaisseur et peuvent supporter le poids des ampoules LED.
Les concepteurs se sont également efforcés de minimiser au mieux les structures de support nécessaires à l'impression 3D. Cela a fait gagner de l'espace d'impression et réduit le traitement après impression que requiert l'enlèvement de ces structures.
Pendant la phase expérimentale, les concepteurs ont d'abord cherché une surface qui soit adaptée au modèle de lustre, à la fois esthétique et ne nécessitant pas de supports à l'impression.

Après avoir essayé des formes de Voronoi et des hexagones, la forme en diamant s'est avérée la meilleure solution, esthétique, fonctionnelle et nécessitant le moins de supports d'impression.

Le logiciel PreForm de préparation à l'impression de Formlabs fait apparaître en rouge les surfaces dont les supports sont insuffisants. L'équipe s'est rendue compte que certaines zones en rouge pouvaient malgré tout être imprimées, tant que ce n'était pas des zones isolées, appelées « îlots », et tant que les parois des structures qui s'autoportaient avaient au moins 1 mm d'épaisseur.
En savoir plus sur l'optimisation du positionnement du modèle et du placement des supports..

Instructions de conception
Articulations pour éléments pliables

De la résine liquide non polymérisée, prisonnière de cavités, peut empêcher le bon fonctionnement des articulations après cuisson de la pièce. Les concepteurs ont constaté qu'un jeu de 0,5 mm était nécessaire pour que la résine se vide complètement des joints d'articulations.
Lustre conçu par le Studio Waldemeyer
Il comporte un corps principal avec huit bras qui se déplient grâce à des articulations, et trois éléments extensibles. L'ensemble du modèle tient dans le volume d'impression de la Form 2 (145 x 145 x 175 mm) pour occuper ensuite 447 x 447 x 447 mm lorsqu'il est complètement déplié.
Éléments extensibles

Ces éléments extensibles doivent être conçus avec des tolérances suffisantes pour permettre leur nettoyage, ainsi que leur bon fonctionnement.
Des tolérances entre 0,7 et 1,4 mm sont indiquées pour le bras extensible (en violet sur le schéma ci-dessus) pour respecter les marges autour des bras. L'espace autour du bras extensible (indiqué avec 0,7 mm de jeu) doit être plus faible que le diamètre le plus grand de l'élément extensible (indiqué avec 0,8 mm de jeu) pour que l'ajustement avec serrage permettent aux éléments de se verrouiller à l'extension.
La cavité interne présente un jeu plus important de 1,4 mm, pour permettre au bras de s'étendre et à la résine sans cuisson d'être facilement évacuée après impression.

Lustre avec bras extensibles imprimé en 3D
Le plus grand modèle imprimé par le Studio Waldemeyer est un lustre avec huit bras extensibles et trois autres éléments extensibles, reliés à un corps principal. Le modèle déplié occupe un volume de 529 x 529 x 374 mm.
Mécanisme de verrouillage

La coque (en bleu) et la douille elle-même (en rouge) sont imprimées séparément pour gagner de la place. Après impression, il suffit de les assembler par simple rotation. Ce modèle est conçu avec des marges de 0,5 mm pour obtenir l'ajustement avec serrage.
Résultats et enseignements
L'équipe de conception du Studio Waldemeyer n'avait aucune expérience préalable de la stéréolithographie ni de la Form 2. Elle a passé environ trois mois sur le premier modèle, les itérations successives et la réalisation des deux variantes présentées.
Ces deux modèles montrent comment utiliser le volume de l'imprimante 3D de bureau pour imprimer des pièces de plus grande taille, avec un peu de créativité et d'expertise CAO. Le premier modèle présente un volume englobant 24 fois plus grand que le volume d'impression de la Form 2 et le second est encore plus impressionnant, avec un volume que ses bras extensibles étendent à 28 fois celui de l'imprimante.
Nous remercions le Studio Moritz Waldemeyer (@moritzwaldewayer) pour nous avoir fait part de leur expérience sur la conception de leurs lustres exceptionnels. Tweetez @formlabs ou taguez-nous dans vos posts sur Instagram (@formlabs) pour partager vos résultats.