Introduction à la fonderie de métaux et aux moyens de combiner l'impression 3D avec les procédés de fonderie.
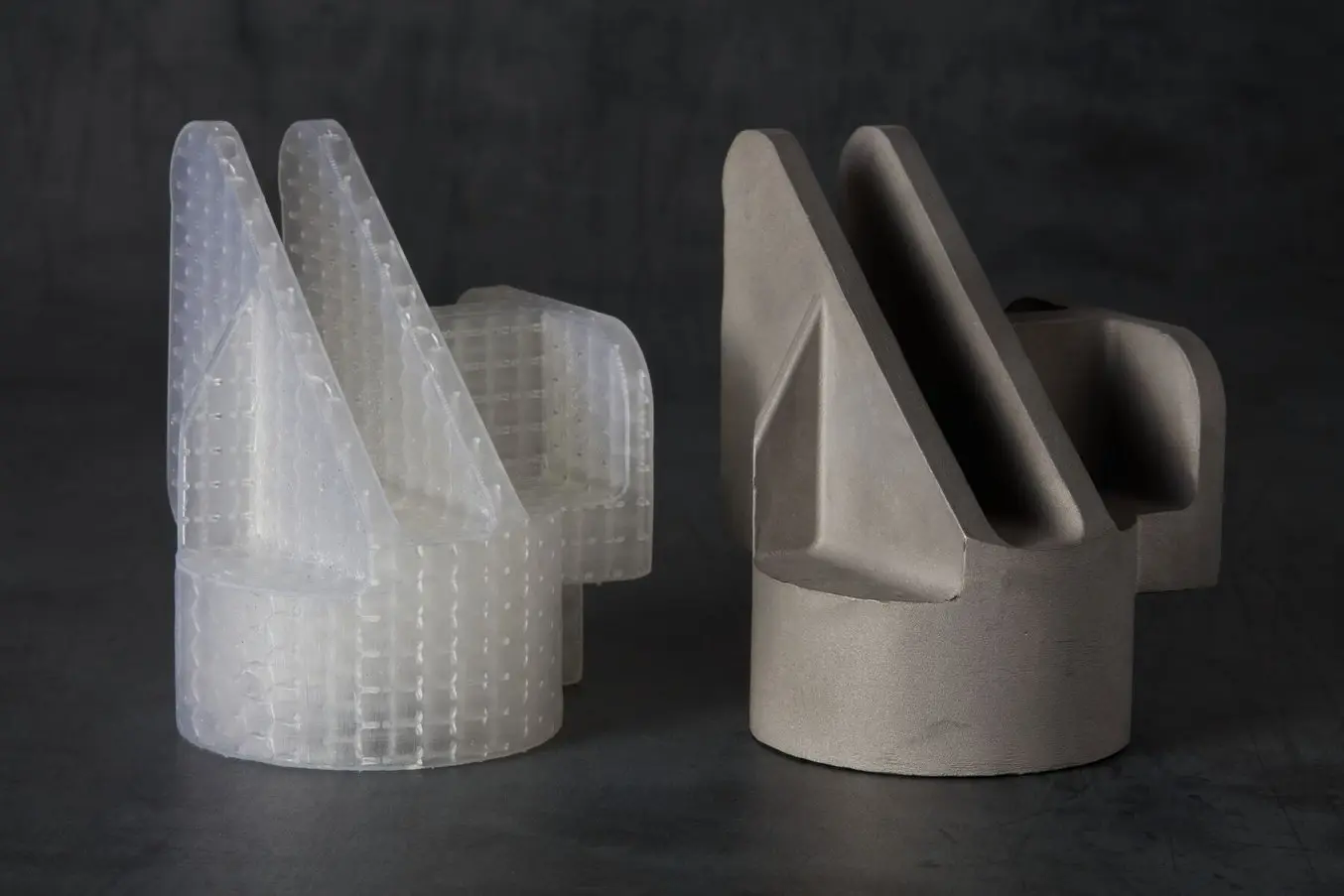
Modèle de moulage à la cire perdue, imprimé en 3D avec Clear Cast Resin, et la pièce métallique coulée.
La fonderie de métaux est un processus séculaire au cours duquel le métal fondu refroidit et se solidifie dans un moule pour former des pièces métalliques. Bien que très ancienne, la fonderie de métaux reste l'un des procédés les plus populaires auprès des entreprises qui cherchent à produire des pièces métalliques.
Cet article explique ce qu'est la fonderie de métaux, son fonctionnement, et vous présente les processus de fonderie les plus courants ainsi que les avantages que les fabricants peuvent obtenir en combinant des outils numériques modernes tels que l'impression 3D avec des procédures de fonderie traditionnelles.
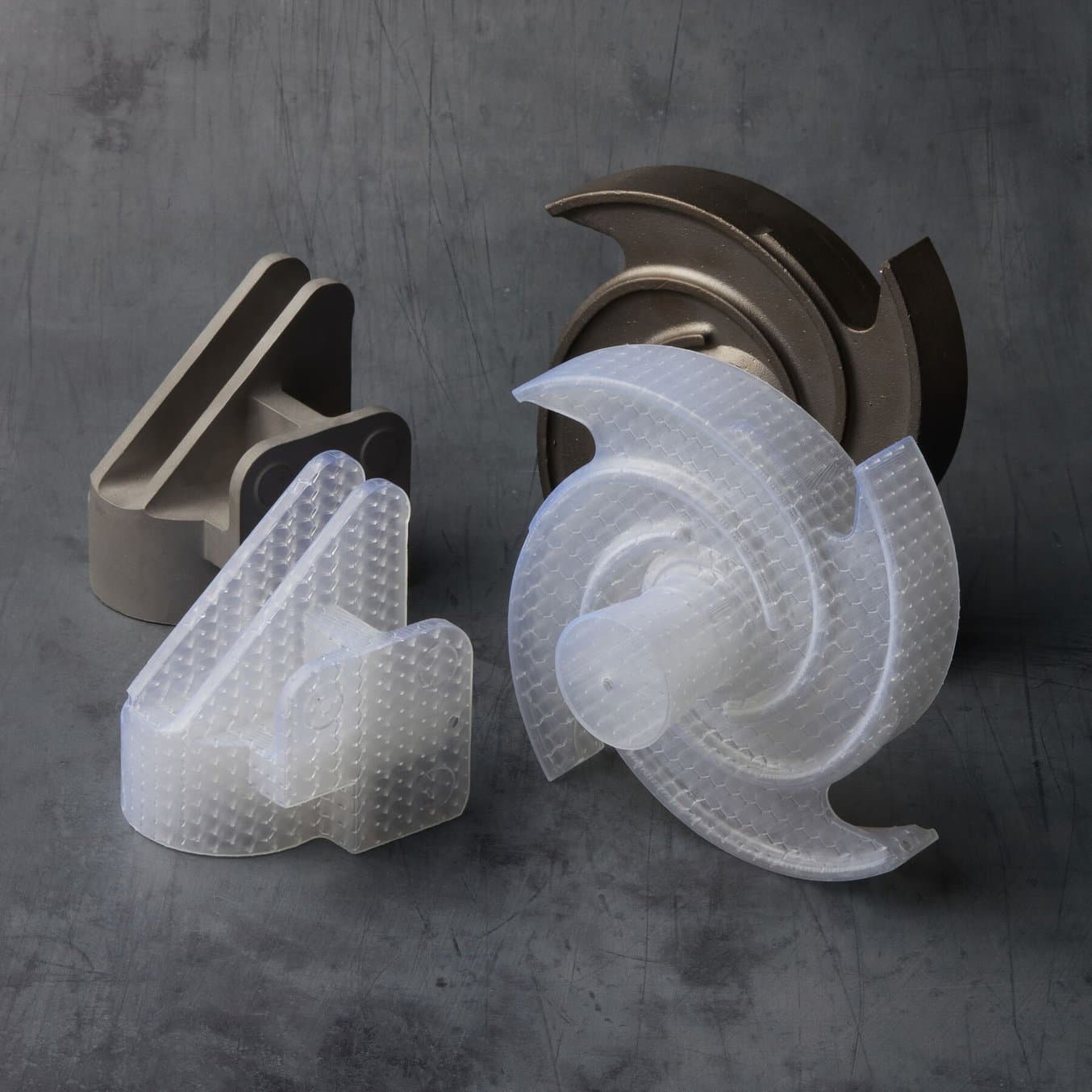
Un moulage précis et rentable : tirer parti de l'impression 3D pour mouler des pièces métalliques
Dans ce webinaire, nous présentons les méthodes qui ont permis à plusieurs fonderies établies de mouler des pièces métalliques à l'aide de modèles imprimés en 3D sur les imprimantes 3D de Formlabs. Découvrez comment les fonderies réduisent les coûts, les délais et améliorent la qualité de leurs pièces métalliques en intégrant Clear Cast Resin de Formlabs et le module de treillis de Materialise Magics aux méthodes de moulage traditionnelles.
Aperçu du processus de fonderie des métaux
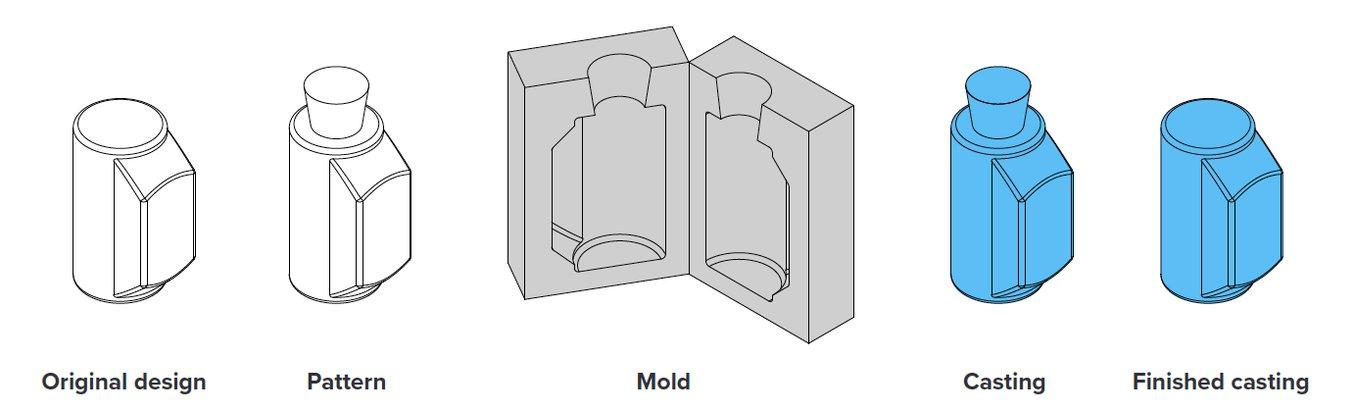
La fonderie de métaux étape par étape, de la conception originale à la coulée finale.
Depuis l'avènement de la fonderie de métaux, les méthodes ont évolué et varié. Ses techniques de base, cependant, sont restées les mêmes. Voici un processus général, étape par étape, pour la fonderie de métaux :
Étape 1 : Création de modèles
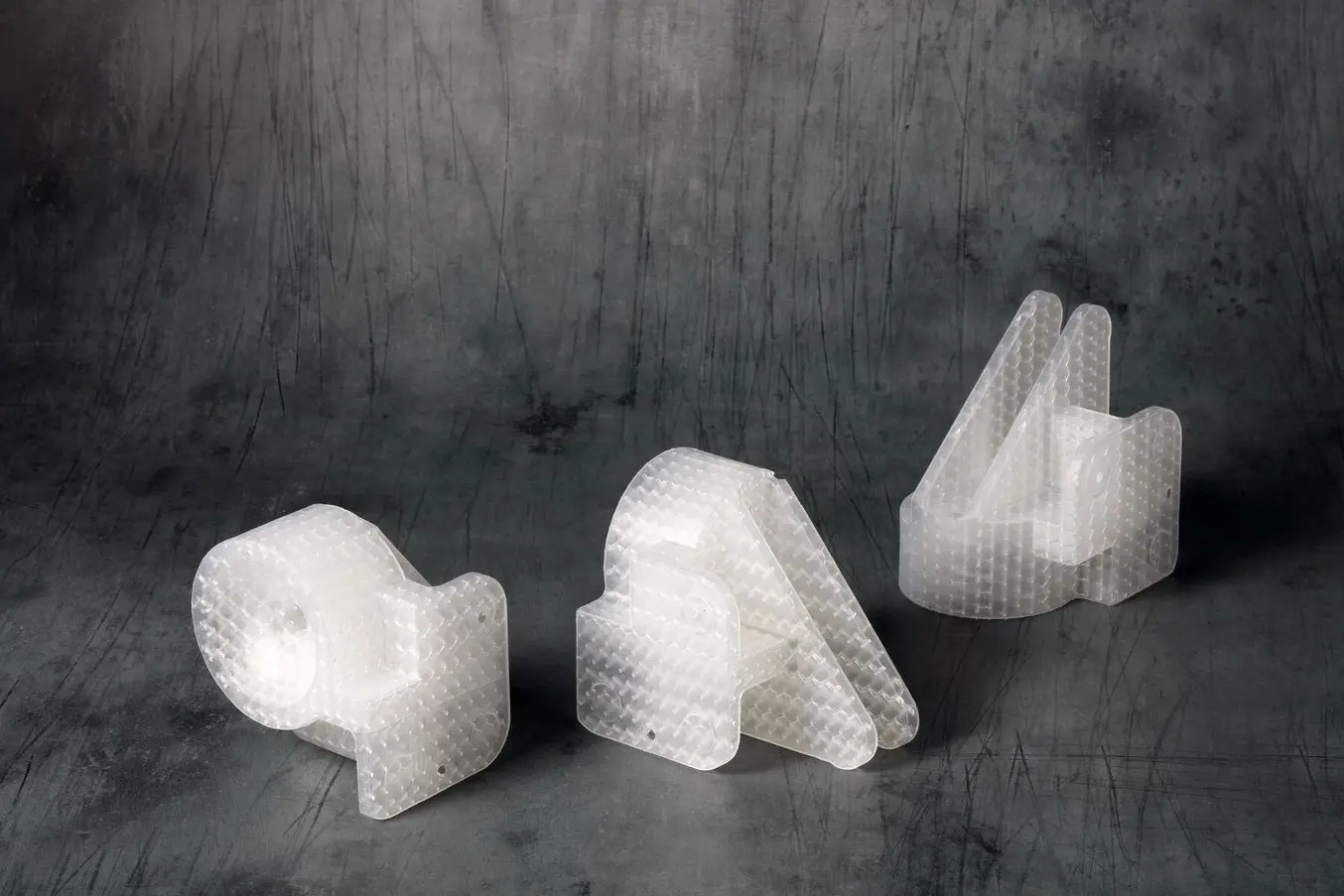
Modèles industriels de moulage à la cire perdue imprimés en 3D avec Clear Cast Resin.
Avant d'entamer le processus de fonderie de métaux, un fabricant doit d'abord élaborer une représentation du modèle souhaité. Ce modèle est essentiel pour concevoir le moule utilisé pour la fonderie. Il est généralement fabriqué en bois, en mousse, en plastique ou en cire, et permet au moule de produire avec précision la pièce métallique finie. Aujourd'hui, l'impression 3D est également une méthode couramment utilisée pour produire des modèles, ce qui permet aux concepteurs de créer des modèles précis directement à partir de logiciels CAO.
Un modèle n'est pas une réplique exacte de la pièce souhaitée. Il comporte des éléments supplémentaires qui rendent le processus de fonderie possible, notamment des entrées qui permettent au métal en fusion de s'écouler à un rythme régulier et des évents pour que le gaz s'échappe. En outre, les modèles sont également plus grands que les pièces qu'ils représentent, afin de tenir compte du rétrécissement qui se produit pendant le refroidissement.
Lorsque la pièce fondue est creuse, le fabricant crée également un noyau de sable ou de métal pour façonner la forme interne. Ce noyau est retiré une fois la pièce fondue.
Étape 2 : Fabrication de moules
L'étape suivante consiste à créer un moule de fonderie, qui peut être réutilisable (non consommable) ou non réutilisable (consommable). Les moules non réutilisables sont généralement fabriqués à partir de sable, de plâtre, de cire ou par impression 3D, et comme leur nom l'indique, ils sont détruits lors du processus de moulage. Les moules réutilisables sont fabriqués en métal ou à partir d'autres matériaux durables, et peuvent être réutilisés pour de multiples cycles de fonte.
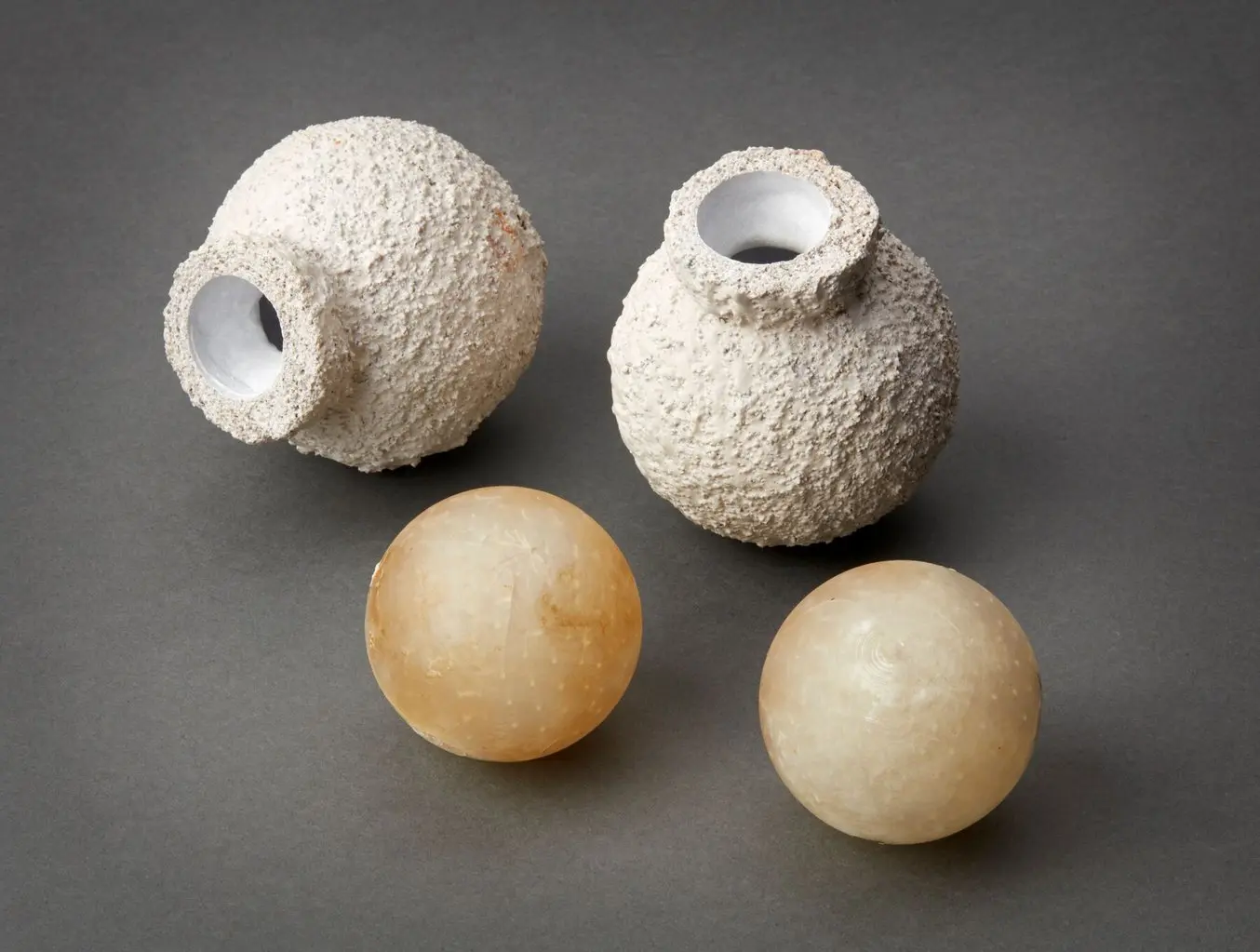
Coques en céramique après brûlage et modèles imprimés en 3D avec Clear Resin.
Étape 3 : Fusion et coulée du métal fondu
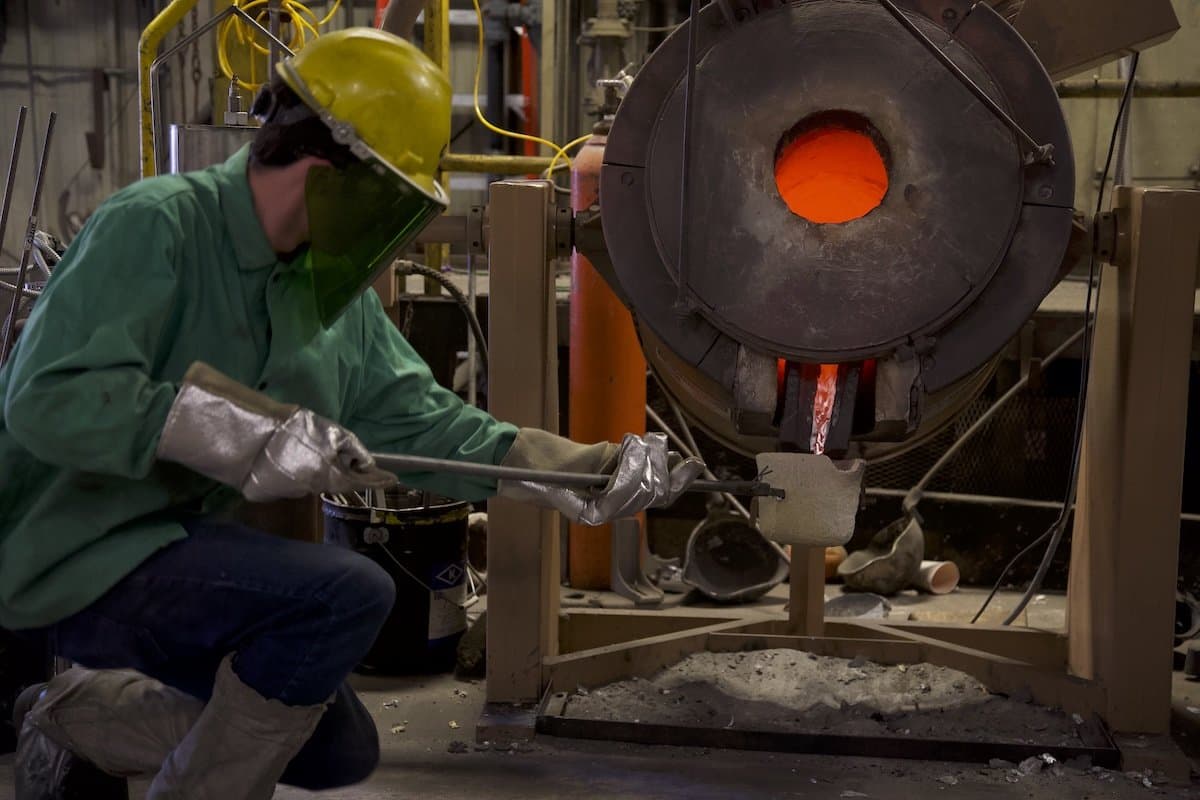
L'aluminium en fusion est coulé dans une coque creuse.
Au cours de cette étape, le métal est chauffé dans un four jusqu'à ce qu'il fonde. En fonction de l'application, les fabricants peuvent utiliser toutes sortes de métaux différents, les métaux les plus couramment utilisés étant le fer, l'aluminium, l'alliage d'aluminium, l'acier, le cuivre et le zinc, ainsi que des métaux précieux comme l'or et l'argent. Une fois le métal fondu, le fabricant le verse dans la cavité du moule et le laisse refroidir et se solidifier.
Étape 4 : Retrait et nettoyage du moule
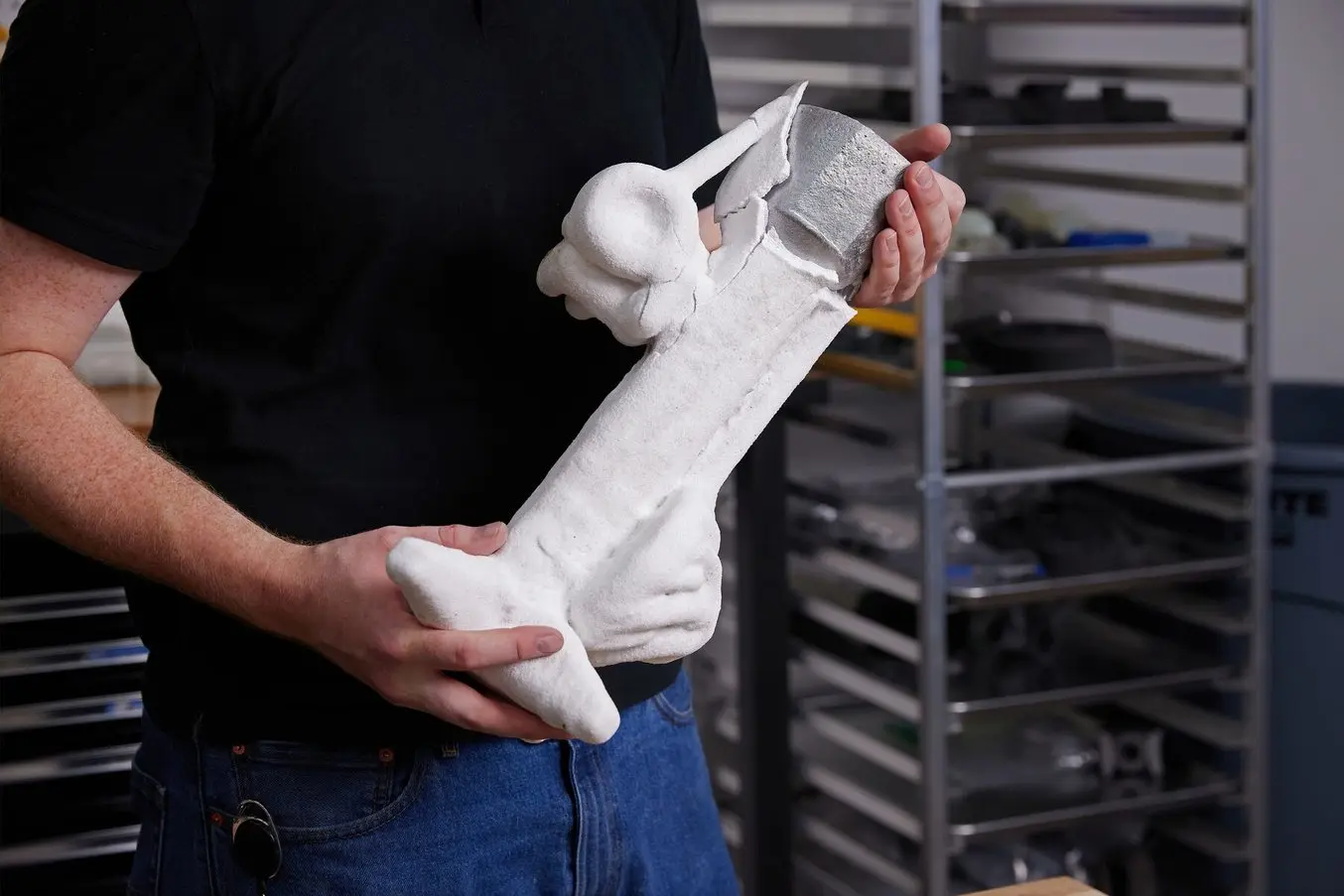
Post-production d'une pièce fondue.
Une fois que le métal a refroidi et s'est solidifié, les pièces sont retirées du moule. Selon le type de moule, cela peut se faire en secouant le moule, en lavant le matériau réfractaire ou en utilisant des broches d'éjection. Ensuite, les matériaux excédentaires tels que les évents, les entrées et les conduits d'acheminement sont retirés des pièces. Enfin, les pièces sont limées, râpées, usinées ou sablées pour obtenir une surface lisse et donner à la pièce sa forme finale.
Types de procédés de fonderie de métaux
Bien que toutes les techniques de fonderie partagent le même processus de base, il existe différentes méthodes mieux adaptées à certaines applications. Parmi les méthodes les plus courantes, citons le coulage sous pression, le moulage à la cire perdue et le moulage en sable.
Coulage sous pression
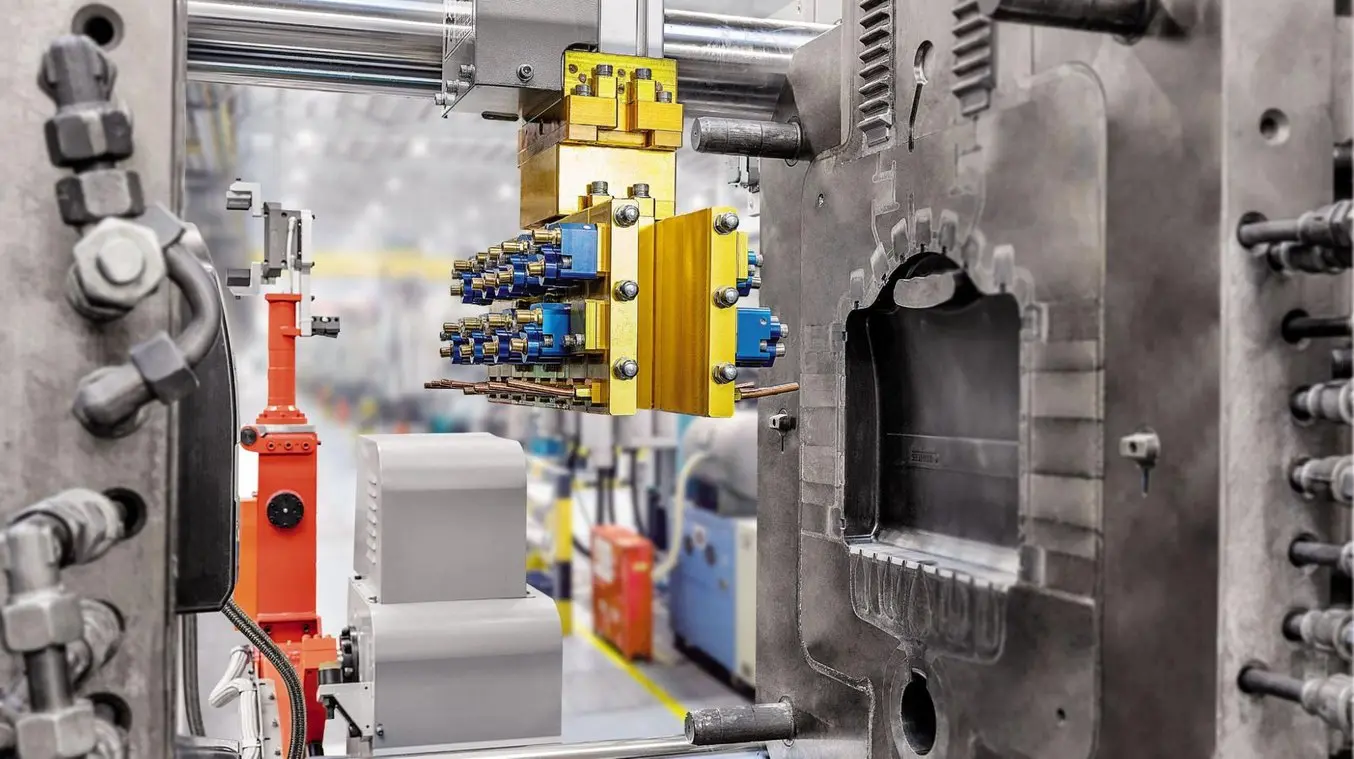
Le coulage sous pression utilise un moule en acier et une pression élevée. (Source: buhlergroup.com)
Le coulage sous pression est un procédé de fonderie dans lequel un fabricant pousse le métal en fusion dans la cavité d'un moule en acier à une pression élevée pour produire rapidement des pièces métalliques. Dans le cas du coulage sous pression, le fabricant assemble deux moitiés d'une matrice ou d'un moule réutilisable et utilise une buse pour injecter du métal fondu sous pression dans la matrice. Lorsque le métal se refroidit, la matrice s'ouvre et des broches d'éjection poussent la pièce vers l'extérieur du moule.
Les deux procédés de coulage sous pression les plus courants sont le coulage à chambre chaude et le coulage à chambre froide. Bien que les spécificités de ces processus varient, il possèdent plusieurs caractéristiques communes.
Coulage sous pression à chambre chaude
Le coulage sous pression à chambre chaude est le plus courant des deux principaux procédés de coulage sous pression. Les machines de coulage sous pression à chambre chaude possèdent un four intégré pour chauffer le métal à l'intérieur de la machine. Une fois que le métal a atteint un état de fusion, la machine abaisse une chambre cylindrique dans le métal en fusion. La forme en col de cygne du système d'injection de métal permet à la chambre de se remplir rapidement, puis de pousser le matériau dans le moule à l'aide de la pression de l'air ou d'un piston.
Le fait d'immerger le mécanisme d'injection pour le remplir permet une injection rapide et optimisée du moule dans ce processus de fonderie. Cependant, comme la chambre est soumise à la chaleur directe du métal fondu, les systèmes de coulage sous pression à chambre chaude sont soumis à la corrosion, ce qui en fait une option moins viable pour les métaux à point de fusion élevé. Il convient plutôt aux matériaux ayant un faible point de fusion et une grande fluidité, comme le plomb, le magnésium, le zinc et le cuivre.
Coulage sous pression à chambre froide
En revanche, le procédé de coulage sous pression à chambre froide fonctionne plus lentement pour éviter la corrosion. Avec cette méthode, un ouvrier de fonderie verse le métal en fusion dans le système d'injection. Un piston pousse ensuite le métal dans le moule.
Ce procédé limite la corrosion, qui est plus fréquente dans le coulage sous pression à chambre chaude. C'est une option idéale pour les métaux à point de fusion élevé, comme l'aluminium et les alliages d'aluminium.
Avantages du coulage sous pression
Le processus de coulage sous pression est rapide et produit des pièces très détaillées. Il convient parfaitement à la production de grands volumes de pièces complexes et peut également produire des pièces solides avec des finitions de surface lisses. La capacité du coulage sous pression à produire un volume élevé de pièces en fait un processus crucial dans les industries automobile et aérospatiale.
Inconvénients du moulage sous pression
L'outillage et l'équipement de moulage sous pression étant coûteux, ce procédé n'est pas rentable pour les petites séries de production. En outre, la malléabilité des métaux utilisés dans le processus peut avoir un impact sur la complexité du produit.
Moulage à la cire perdue
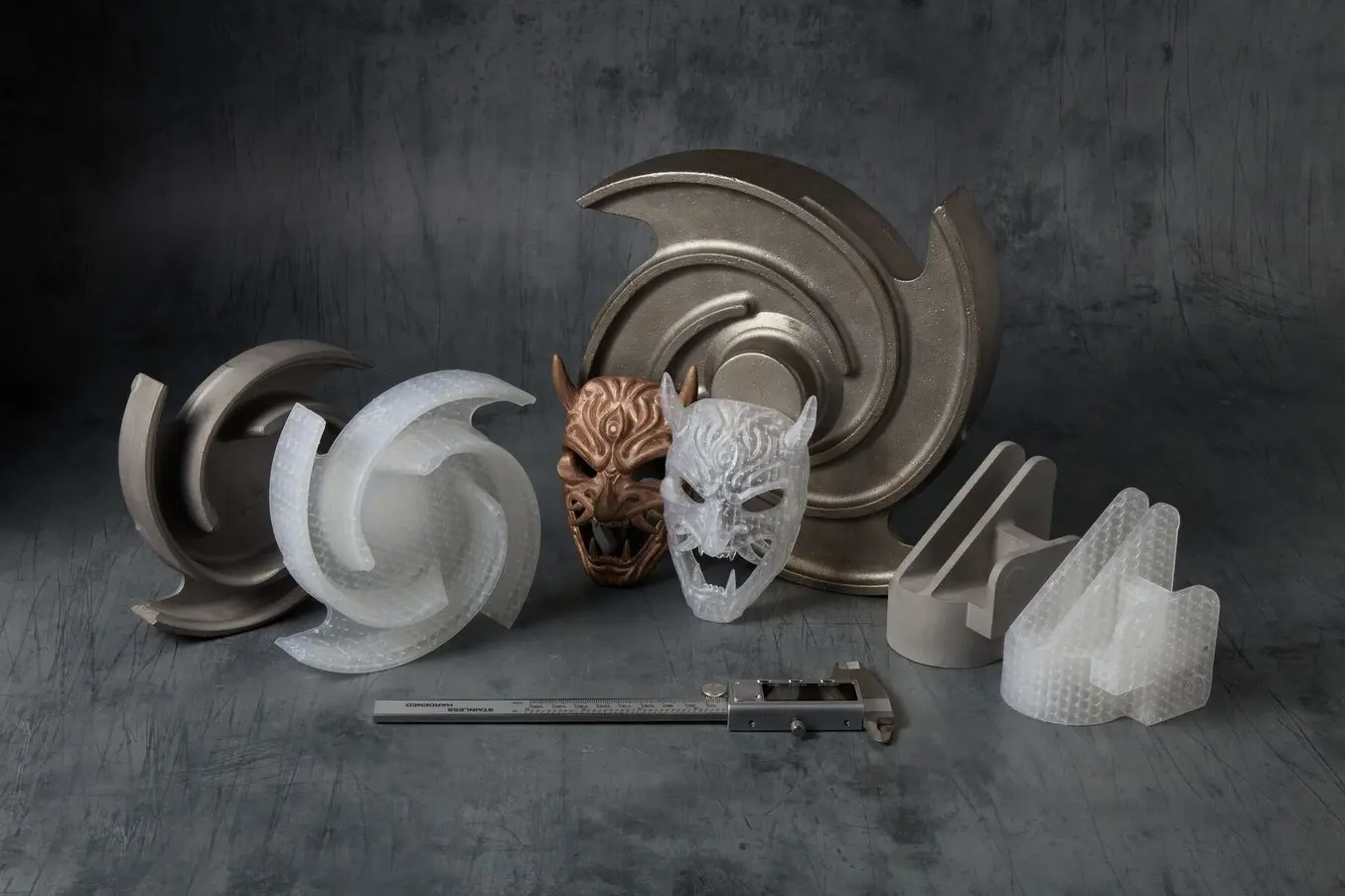
Pièces fondues à partir de modèles imprimés en 3D avec Clear Cast Resin sur une imprimante 3D résine de Formlabs.
Le moulage à la cire perdue, également connu sous le nom de moulage à modèle perdu, est un procédé qui utilise de la cire, de la barbotine et des moules pour produire des pièces complexes. C'est l'une des plus anciennes techniques de fonderie de métaux, mais elle est toujours appréciée pour sa capacité à créer des pièces métalliques précises aux formes complexes.
Ce procédé est encore largement utilisé pour produire des bijoux, des produits dentaires et des œuvres d'art. Dans le secteur industriel, le moulage à la cire perdue est un moyen courant de créer des pièces métalliques de précision en ingénierie et en fabrication industrielle.
Les modèles de moulage à la cire perdue sont généralement fabriqués à partir de cire ou de polymères imprimés en 3D. Les modèles sont assemblés en une structure arborescente et plongés dans une barbotine de silice, ou placés dans un moufle et entourés par le matériau réfractaire liquide. Après que le matériau réfractaire a séché, le moufle est placé à l’envers dans un four, ce qui fait fondre le modèle, créant une cavité négative ayant la forme du modèle original. Le métal est fondu puis versé, en utilisant la gravité ou un vide d’air pour faire entrer le métal dans la cavité. Les pièces moulées sont limées, meulées, usinées ou sablées pour obtenir la géométrie et la finition de surface finales.
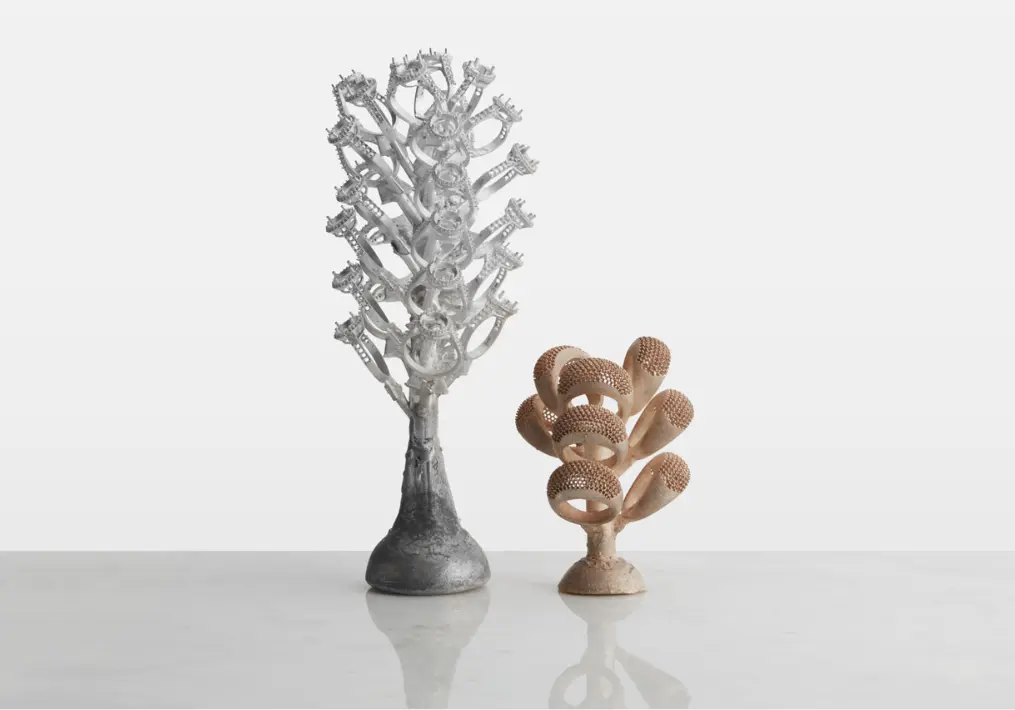
Arbres de coulée avec anneaux fondus.
Clear Cast Resin, Castable Wax Resin, Castable Wax 40 Resin, et True Cast Resin peuvent toutes être utilisées pour imprimer en 3D des pièces pour le moulage à modèle perdu. La sélection des matériaux dépend des caractéristiques de chaque pièce. Castable Wax Resin convient aux bijoux de poids léger à moyen, True Cast Resin aux bijoux de poids moyen et aux composants d’ingénierie usqu’à 5 mm d’épaisseur, et Clear Cast Resin aux pièces de plus de 3 mm d’épaisseur.
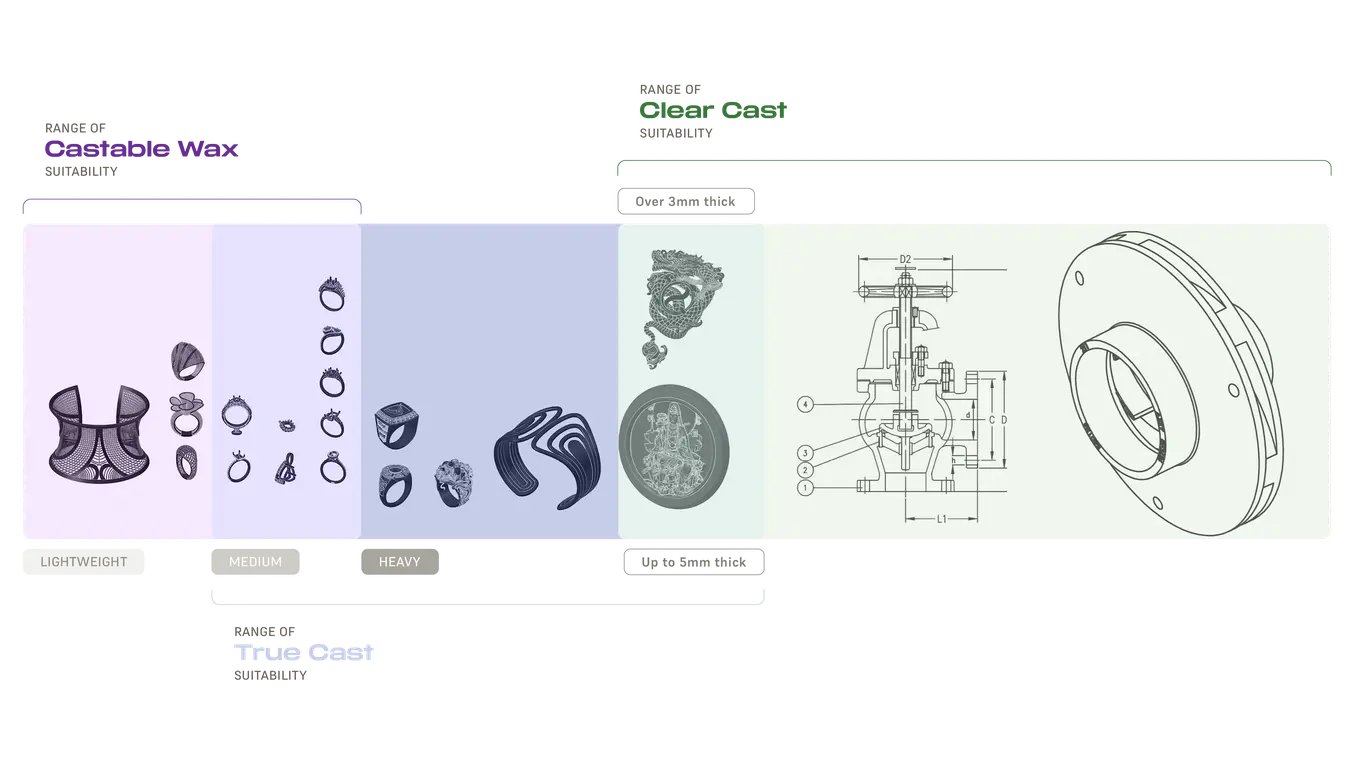
Avantages du moulage à la cire perdue
Le moulage à la cire perdue est un procédé polyvalent. Il permet aux fabricants de produire des pièces précises et reproductibles à partir de presque tous les métaux disponibles pour le moulage, et des formes complexes qui seraient difficiles ou impossibles à réaliser avec d'autres méthodes de moulage. Les pièces moulées présentent également une excellente qualité de surface et de faibles tolérances. De plus, elles ne nécessitent qu'un minimum de finition de surface ou d'usinage.
Ces caractéristiques font du moulage à la cire perdue la solution idéale pour fabriquer des pièces complexes destinées à des applications automobiles, aérospatiales et industrielles, des outils médicaux, des implants dentaires, ainsi que des pièces d'art et de joaillerie.
Inconvénients du moulage à la cire perdue
Le moulage à la cire perdue est un processus complexe et exigeant en main-d'œuvre. La fabrication d'un moule nécessite un équipement spécialisé, des matériaux réfractaires et des liants coûteux, ainsi que de nombreuses opérations manuelles. Il peut être difficile de mouler des pièces qui nécessitent des noyaux, et le procédé est mieux adapté aux petites pièces.
Moulage en sable
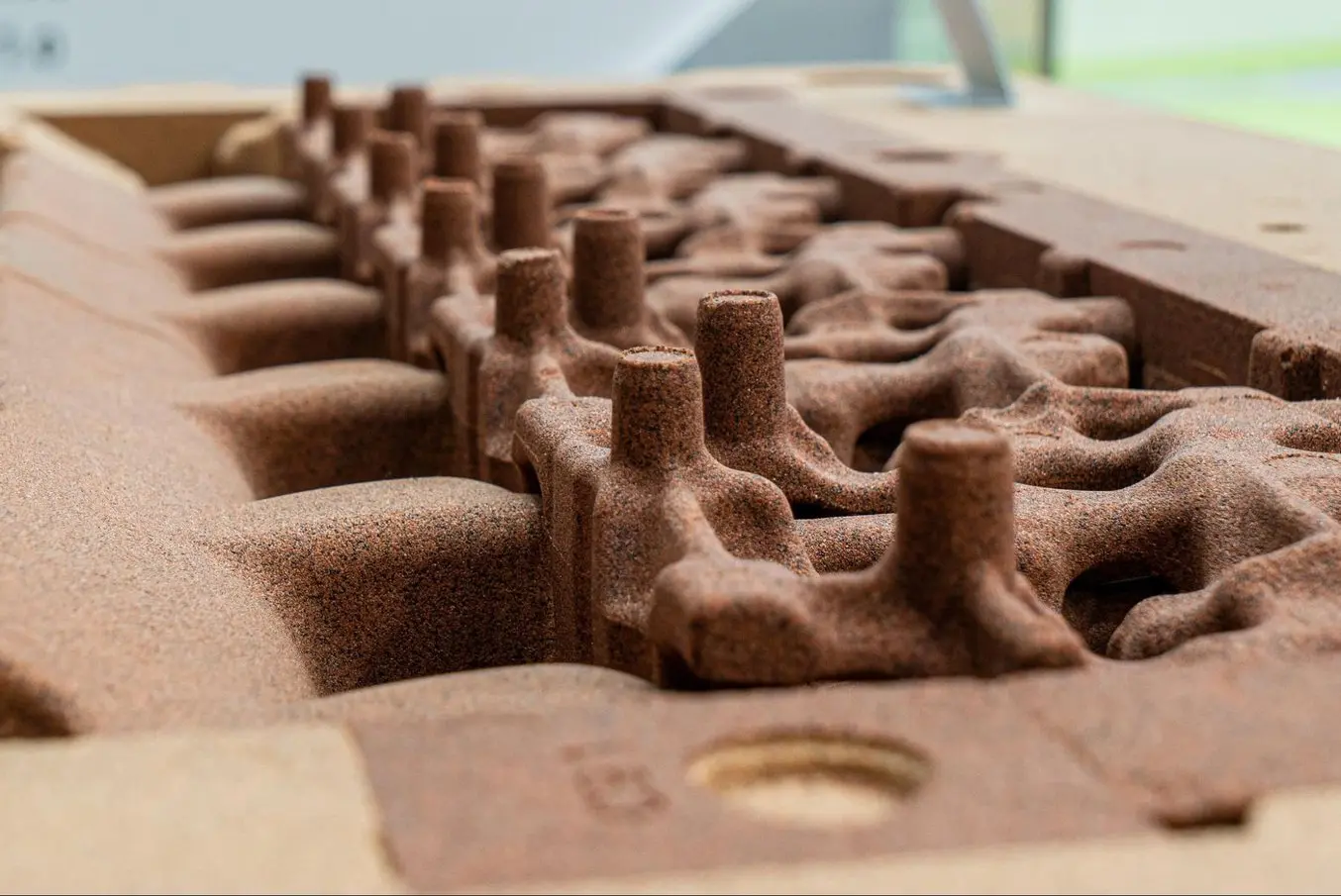
La moitié d'un moule de moulage en sable.
Le moulage en sable est une méthode de fonderie qui a été utilisée pour la première fois il y a 3000 ans et qui reste la méthode de fonderie la plus utilisée à ce jour. Ce procédé permet aux fabricants de couler du métal sans recourir à l'usinage.
Dans le processus de moulage en sable, le fabricant crée d'abord un modèle de fonderie, le plus souvent en bois ou en plastique. Le modèle est plus grand que la pièce finale, afin de tenir compte du rétrécissement. Les pièces ne présentant des caractéristiques que sur une seule face ne nécessitent qu'un moule à face ouverte. Pour les pièces comportant plusieurs surfaces détaillées, le fabricant sépare le modèle de fonderie en deux pour former un moule à cavité fermée. La moitié supérieure s'appelle une chape et la partie inférieure une traînée.
Une fois que le fabricant a créé le modèle, il tasse fermement le sable autour du modèle. Ensuite, il ajoute des carottes de coulée et des entrées pour s'assurer que le métal fondu s'écoule en douceur dans la cavité du moule. Le fabricant retire le modèle puis serre les deux moitiés du moule l'une contre l'autre. Une fois que le métal est en fusion, il est versé dans le moule et on le laisse refroidir. Le moule est alors retiré par vibrations ou en utilisant de l'eau à haute pression. Enfin, le fabricant affine la pièce en retirant les carottes et les entrées, puis en polissant la pièce en métal coulé.
Avantages du moulage en sable
Le moulage en sable est un processus adaptable qui n'a pas besoin de machines. De ce fait, il permet de créer des pièces complexes de pratiquement n'importe quelle taille. Le sable est abondant et bon marché, ce qui réduit les frais d'installation et permet d'apporter des modifications. C'est le seul moyen pratique ou économique de produire des pièces de très grande taille. Les délais du moulage en sable sont également courts, ce qui en fait un procédé viable pour les petites séries de production.
La polyvalence du moulage en sable rend le processus attractif pour un large éventail d'industries. Il permet de produire des équipements médicaux, des pièces automobiles, des équipements électroniques, des réservoirs de gaz, des blocs moteurs, etc.
Inconvénients du moulage en sable
Le moulage en sable crée des métaux très poreux et texturés. Le rétrécissement et la rugosité de la surface diminuent également la précision dimensionnelle des pièces. Il en résulte un produit final peu résistant qui nécessite un post-traitement fastidieux pour obtenir une finition de meilleure qualité.
Choisir le bon procédé de moulage des métaux
Afin de choisir le bon procédé de moulage industriel des métaux, plusieurs facteurs doivent être pris en compte. Nous avons créé ce tableau comparatif pour vous aider à comparer le moulage sous pression, le moulage à la cire perdue et le moulage en sable en termes de types de métaux, de volume de production, de coûts, de temps de production, de complexité des pièces et de secteurs d'activité pour lesquels ils sont généralement utilisés.
Coulage sous pression | Moulage à la cire perdue | Moulage en sable | |
---|---|---|---|
Métaux compatibles | Aluminium, cuivre, plomb, magnésium, zinc | La plupart des métaux | La plupart des métaux |
Volume de production | Volumes élevés | Volumes faibles ou élevés | Pièces uniques ou volumes moyens |
Coûts unitaires | Bas | Modérés à élevés | Modérés |
Coûts d'outillage | Élevé | Modérés | Bas |
Durée de cycle | Rapide | Long | Modérés |
Secteurs | Automobile, aérospatiale, produits de consommation, meubles, outils électriques | Automobile, aérospatiale, bijouterie, médecine, dentisterie, art | Automobile, aérospatiale, équipement industriel, électronique, produits de consommation |
Combiner la fonderie et l'impression 3D
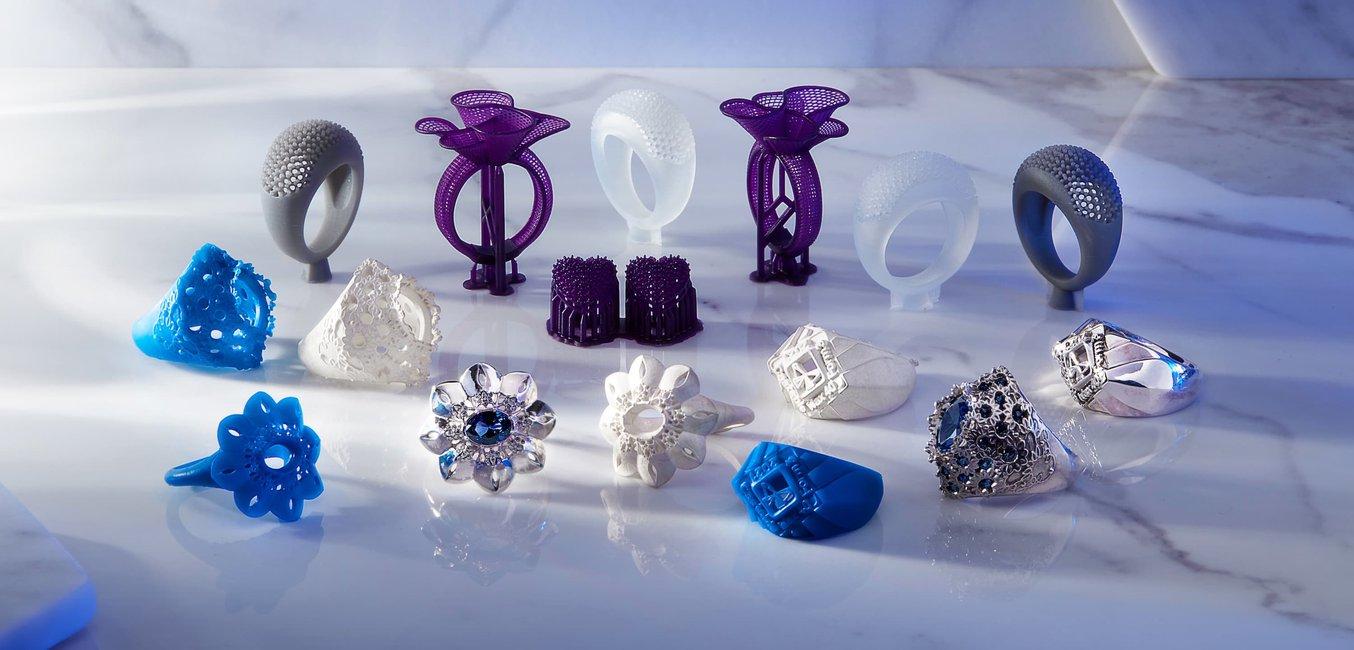
Modèles de bagues imprimés en 3D et pièce en métal coulé.
Ingénieurs, concepteurs, bijoutiers et amateurs peuvent tirer parti de la rapidité et de la flexibilité de l'impression 3D en combinant des procédés de fonderie de métaux (moulage à la cire perdue direct ou indirect, moulage à l'étain, moulage en sable, etc.) avec des modèles imprimés en 3D, ou en coulant du métal dans des moules imprimés en 3D. Les pièces métalliques coulées à l'aide d'outillage rapide imprimé en 3D peuvent être produites beaucoup plus rapidement qu'en utilisant les méthodes de fonderie traditionnelles, et à un coût nettement plus bas que celui de l'impression 3D de métaux.
Les imprimantes 3D stéréolithographiques (SLA) offrent une grande précision et une large gamme de matériaux qui conviennent très bien aux processus de fonderie, et permettent de produire des pièces métalliques à moindre coût, avec une plus grande liberté de conception et des délais plus courts que les méthodes traditionnelles.
Moulage à la cire perdue indirect
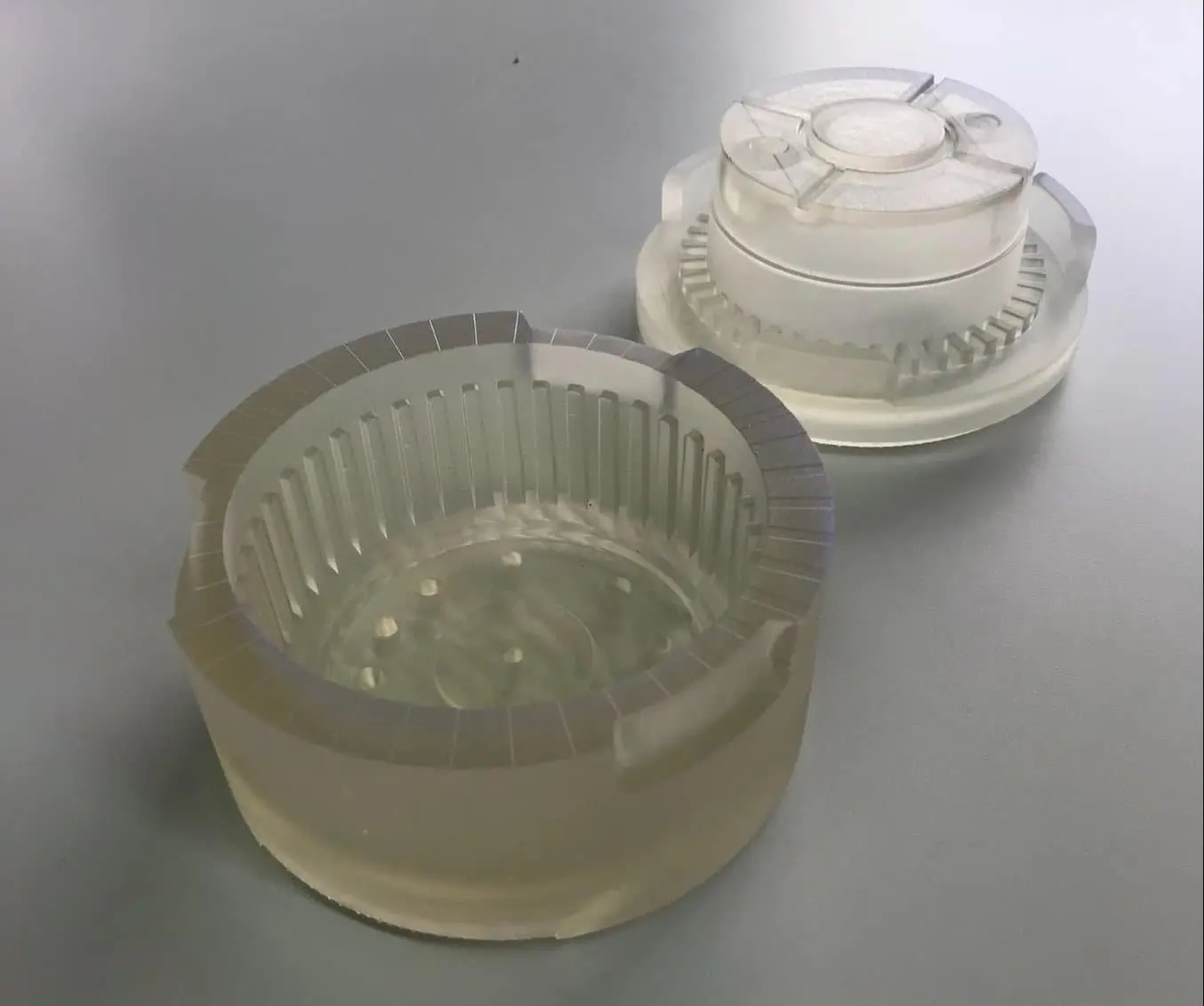
Moule à injection de cire imprimé en 3D avec Clear Resin.
Le processus de fabrication de modèles à partir de moules ou d'outils est appelé moulage à la cire perdue indirect car, en plus des moules de coulée finaux, il requiert la création de moules pour obtenir les modèles.
Les moules rigides pour la cire (souvent appelés outils) sont généralement fabriqués par usinage d'aluminium ou d'acier. La fabrication de moules métalliques usinés coûte des milliers de dollars et nécessite plusieurs semaines d'usinage et de polissage avant de pouvoir procéder aux premiers essais et évaluer les modèles-maitres servant au coulage.
Grâce à l'impression 3D, les fabricants peuvent également imprimer directement le moule de leur modèle en utilisant des matériaux capables de résister à des températures élevées tels que High Temp Resin ou Rigid 10K Resin. Pour obtenir une finition de surface optimale des pièces moulées, il faut traiter les surfaces internes du moule en les ponçant et en les polissant pour qu'elles soient lisses, ou par projection de billes pour obtenir un aspect mat uniforme. Pour vous assurer que les pièces coulées finales auront les bonnes dimensions, il faut compenser le retrait en augmentant les dimensions du moule imprimé. Le rétrécissement exact de la cire et le processus de coulage sont spécifiés dans les caractéristiques techniques du fournisseur.
Les moules imprimés en 3D permettent de réduire les délais entre le concept et les premiers essais à quelques jours seulement, car les fabricants peuvent imprimer directement l'outillage nécessaire pour faire fonctionner et évaluer les pièces.
Les pièces moulées doivent respecter des règles de conception pour pouvoir être moulées (p. ex. aucune contre-dépouille, indications d'angle de dépouille, etc.), mais vous pouvez réaliser des modèle bien plus complexes en utilisant des éléments d'assemblage pour former une structure unique à partir de plusieurs composants.
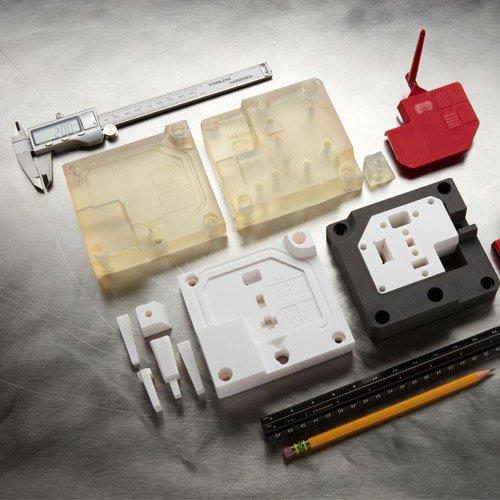
Fabrication de moules par impression 3D : techniques de prototypage et de production
Téléchargez notre livre blanc pour découvrir six procédés de fabrication de moules qui sont possibles avec une imprimante 3D SLA en interne, notamment le moulage par injection, le formage sous vide, le moulage en silicone, etc.
Moulage à la cire perdue direct
Le moulage à la cire perdue direct permet de passer directement de la création du modèle à son enrobage avec le matériau réfractaire. Ce procédé convient pour la fabrication de pièces à géométries trop complexes pour être moulées, ou de pièces présentant des contre-dépouilles importantes et des détails fins de texture de surface, pour lesquelles les coûts d'outillage sont très élevés.
Traditionnellement, les modèles de moulage à la cire perdue direct sont sculptés à la main ou usinés si la pièce est une pièce unique ou s'il n'est prévu d'en produire que quelques-unes. Mais grâce à l'impression 3D, les fabricants peuvent directement imprimer les modèles en 3D, ce qui permet de gagner en temps et en créativité par rapport à d'autres procédés.
Grâce à l’impression 3D, les ingénieurs, les concepteurs et les joailliers peuvent directement imprimer des modèles pour réussir à obtenir des cycles de production plus courts et un choix de géométries plus vaste que ce que permettent les contraintes DFM (conception en vue de la fabrication) des processus de moulage. Formlabs a développé une gamme de matériaux d'impression 3D coulables adaptés au moulage à la cire perdue direct, en particulier au moulage à la cire perdue industriel et au moulage de joaillerie.
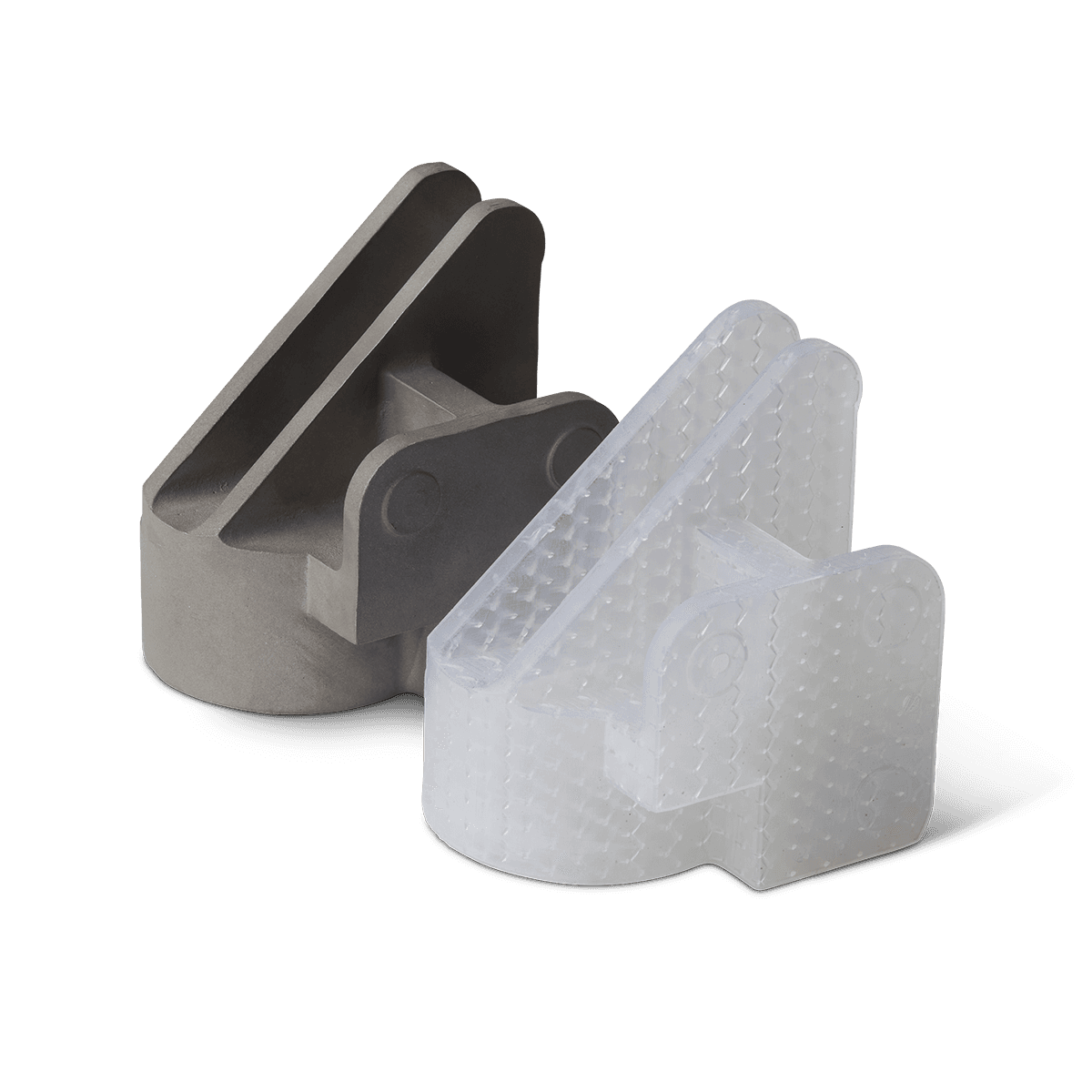
Moulage à la cire perdue industriel avec des modèles imprimés en 3D à l'aide de Clear Cast Resin de Formlabs
Dans ce livre blanc, nous présentons les méthodes qui ont permis à plusieurs fonderies établies de mouler des pièces métalliques à l'aide de modèles imprimés en 3D avec les imprimantes 3D SLA de Formlabs.
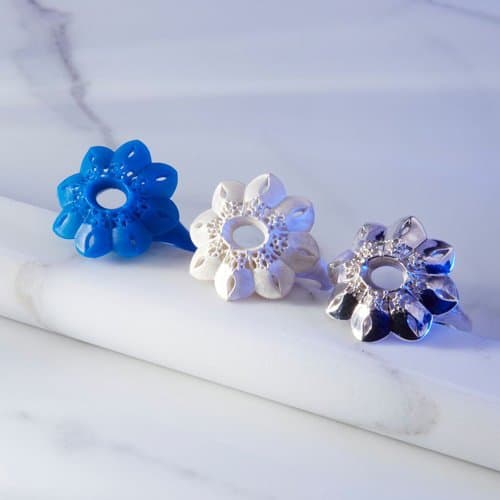
Introduction au moulage pour les bijoux imprimés en 3D
La façon dont les joailliers travaillent est en train de changer, et les résines photopolymères moulables n'y sont pas étrangères. Dans ce guide, vous découvrirez comment mouler de superbes pièces de joaillerie imprimées en 3D sur des imprimantes Formlabs.
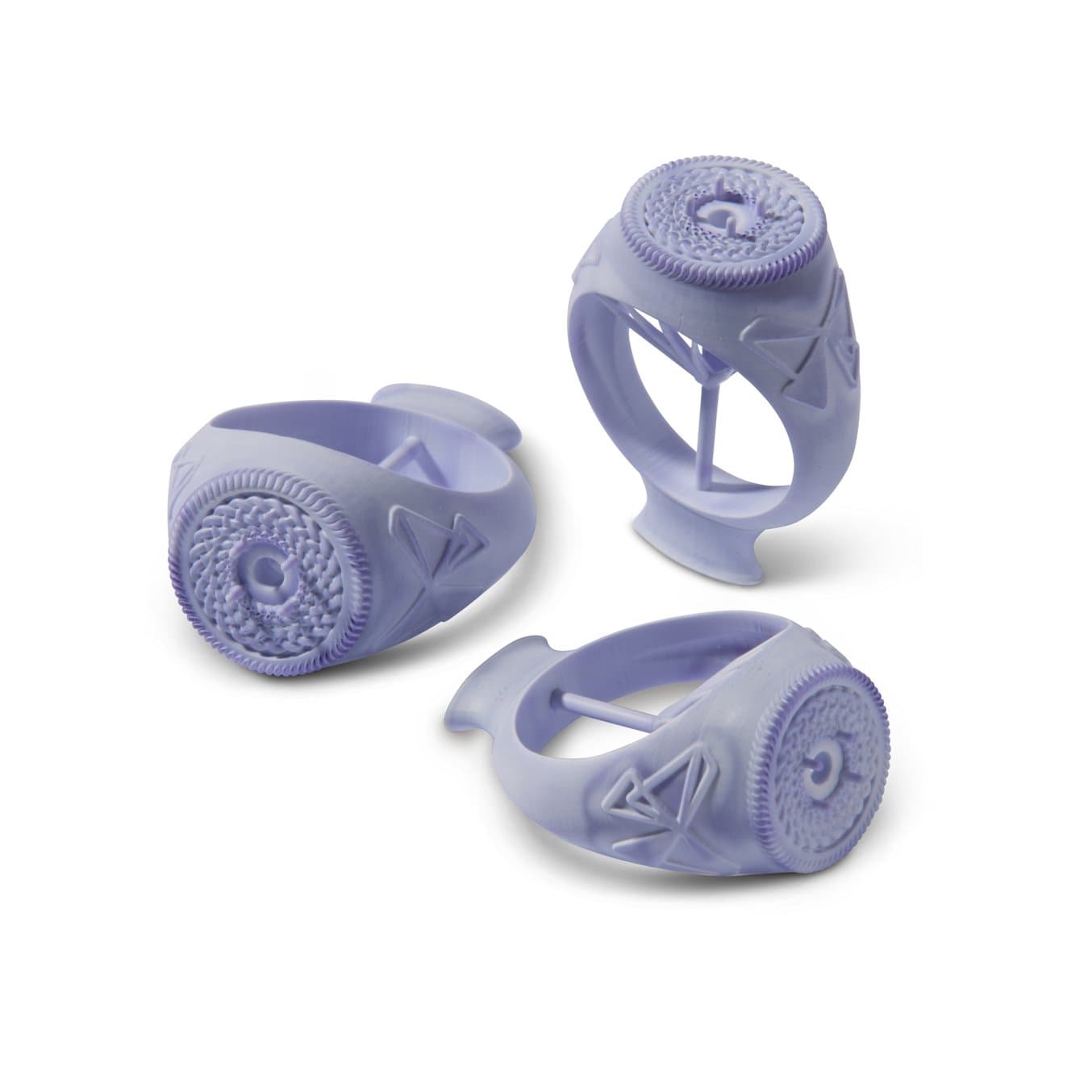
Commander un échantillon gratuit
Examinez et constatez par vous-même la qualité Formlabs. Nous enverrons un échantillon gratuit à votre bureau.
Moulage en sable
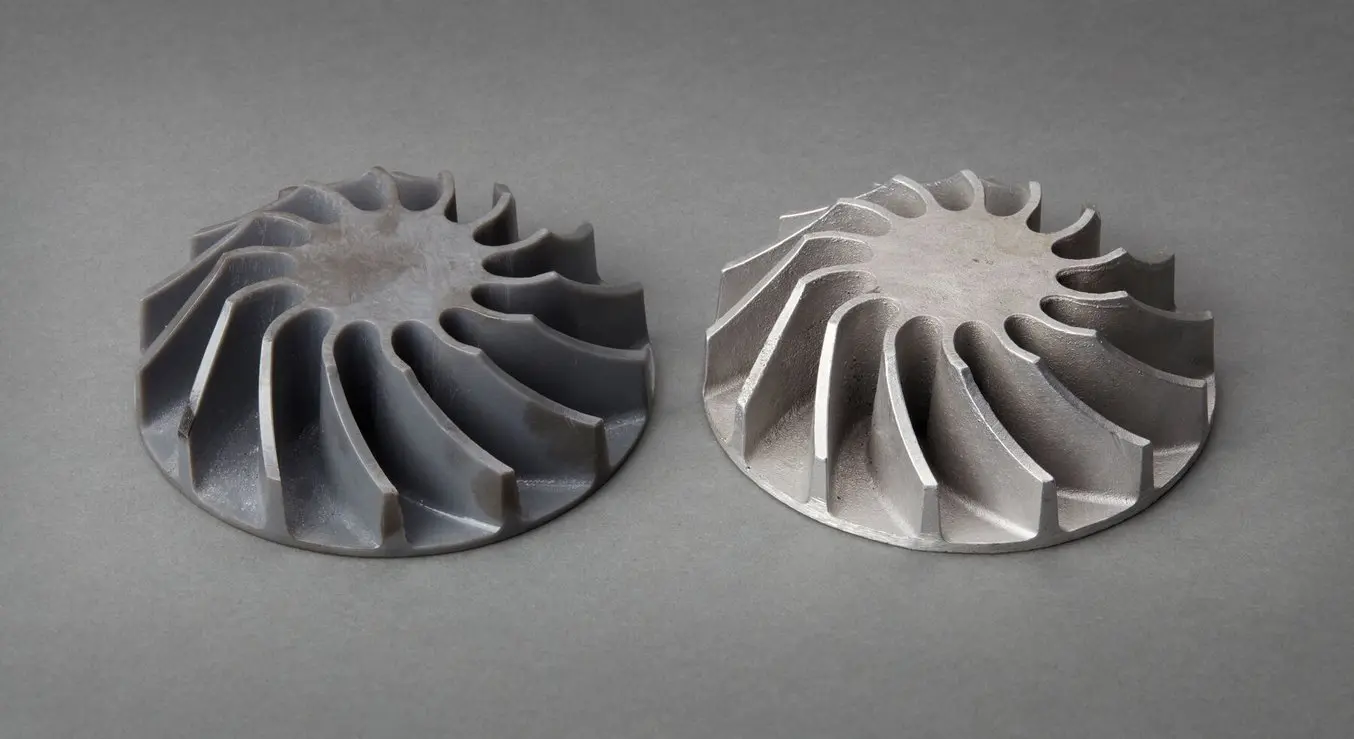
Modèle imprimé en Grey Resin et pièce finie coulée en aluminium à partir d'un moule à sable ouvert.
Comme pour le moulage à la cire perdue, l'impression 3D peut être utilisée pour créer des modèles destinés au moulage en sable.
Contrairement à certains matériaux traditionnels comme le bois, l'impression 3D permet aux fabricants de créer des formes complexes et de passer directement de la conception numérique au moulage.
Moulage de l'étain
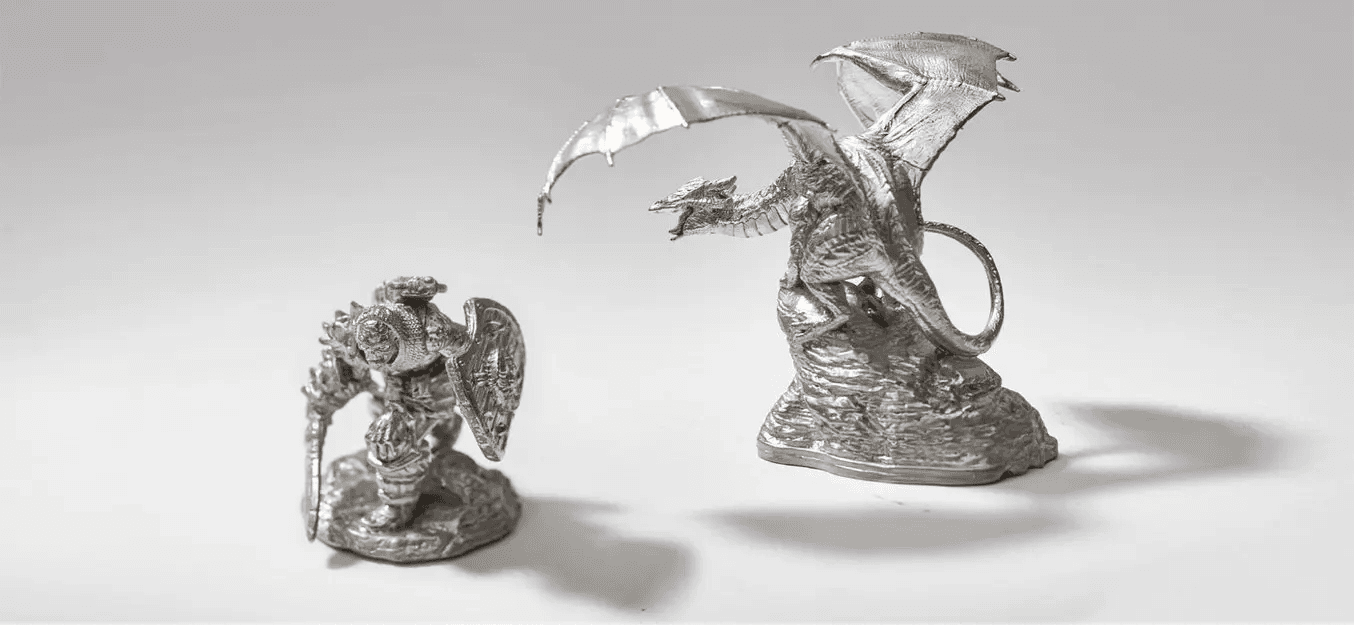
Miniatures en métal réalisées en combinant le moulage de l'étain et l'impression 3D.
L'étain est un alliage métallique malléable à faible point de fusion qui peut être utilisé pour fabriquer des objets entièrement métalliques destinés à des applications décoratives telles que des miniatures métalliques détaillées, des bijoux, des modèles réduits et des répliques d'antiquités.
Grâce à l'évolution récente des matériaux d'impression 3D résistants à la température, comme High Temp Resin pour les imprimantes 3D SLA de Formlabs, il est désormais possible d'imprimer en 3D des moules pour le moulage direct de l'étain.
Il existe deux options pour la conception des moules : un moule sacrificiel ou un moule de séparation. Le moule sacrificiel comporte une coque conçue pour être brisée au cours du processus. Les moules de séparation fonctionnent avec des moitiés séparées, ce qui permet de réutiliser le moule.
Comparé à l'impression directe en métal, le moulage de l'étain dans des moules imprimés en 3D offre des détails et une finition de surface bien meilleurs pour une fraction du coût. Comparée au moulage à la cire perdue, l'impression directe du moule en 3D demande moins de temps et d'effort, et permet de préserver le plus de détails possible.
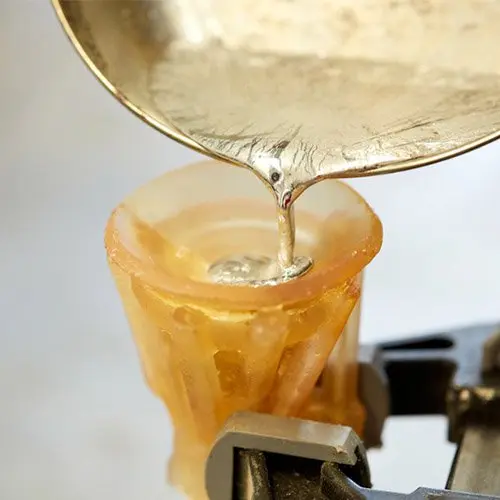
Métal, céramique et silicone : utilisation de moules imprimés en 3D dans des processus de travail hybrides avancés
Regardez notre webinaire pour découvrir comment la fabrication de moules à l'aide de matrices imprimées en 3D et de moules réutilisables ou sacrificiels peut vous permettre de produire des pièces en porcelaine, en métaux précieux et non précieux, en silicone et en matériaux flexibles biocompatibles, etc.
Quand combiner l'impression 3D et la fonderie de métaux ?
La fonderie de métaux combinée à l'impression 3D offre une excellente solution aux entreprises qui veulent plus de liberté de conception ou qui souhaitent réduire les coûts et les délais.
Certains types de pièces métalliques complexes, comme les pièces de grande dimension à sections transversales et les pièces à noyaux multiples, sont difficiles à créer avec les méthodes traditionnelles de fonderie de métaux. L'impression 3D permet aux fabricants de produire ces conceptions complexes. Par exemple, les fonderies ou les joailliers peuvent créer des motifs complexes et personnalisés qui seraient impossibles à obtenir sans un modèle imprimé en 3D.
L'impression 3D permet également de créer des pièces sans dépendre de plusieurs machines ou de plusieurs prestataires de services. Les entreprises n'ont besoin que d'un fichier numérique, d'une imprimante 3D et de matériaux d'impression. Cela permet de réduire les coûts et les déchets, car tous les matériaux utilisés sont intégrés dans le produit final.
Enfin, la combinaison de l'impression 3D et de la fonderie de métaux peut réduire les coûts et les délais. Plus besoin d'attendre des semaines la livraison d'outils coûteux avant de couler un produit final : une imprimante 3D peut créer un modèle ou un moule en quelques heures.
Diversified Metalsmiths, Inc. a intégré des technologies modernes dans ses opérations de fonderie de métaux afin de réduire les coûts, d'améliorer les délais de production et d'augmenter la flexibilité. Grâce aux imprimantes 3D stéréolithographiques (SLA) de la série Form et à Clear Cast Resin, Diversified a pu imprimer des modèles en interne rapidement et à un prix abordable, sans modifier son flux de travail de moulage ni faire appel à des sous-traitants.
« Notre principale raison d'acheter la Form 3L était le coût du modèle... Même en incluant l'amortissement de l'imprimante et de l'équipement associé, nous atteindrons au moins le seuil de rentabilité sur notre commande actuelle et réaliserons une économie de plus de 200 $ par pièce sur les commandes futures. Nos procédures sont pratiquement inchangées, à la fois avant et après le moulage, entre les modèles en PMMA et les modèles SLA en Clear Cast Resin. »
John Farr, vice-président de la technologie, Diversified Metalsmiths
Imprimante 3D pour la fonderie de métaux
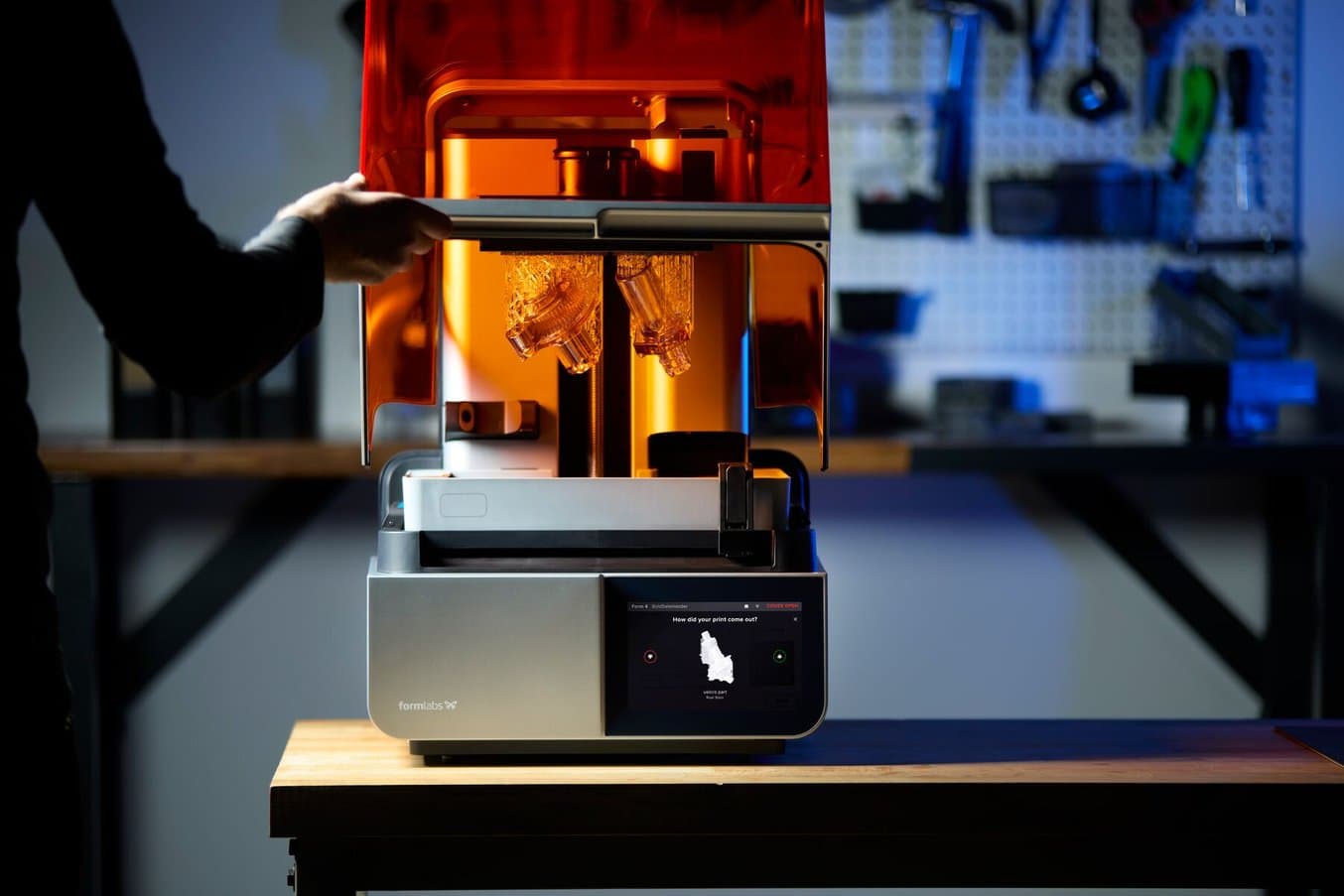
La fonderie de métaux combinée à l'impression 3D permet aux entreprises de créer rapidement et efficacement des pièces métalliques. Avec une imprimante 3D SLA Formlabs, vous pouvez accélérer le processus de fonderie de métaux tout en réduisant les coûts.
En savoir plus sur les imprimantes 3D résine de Formlabs ou contacter nos experts en impression 3D si vous avez des questions.