Impression 3D rapide et rentable d’outils de fabrication pour l’horlogerie
Sinn Spezialuhren, fabricant de montres mécaniques aux nombreuses fonctionnalités, avait au départ acheté une imprimante 3D stéréolithographique (SLA) Form 3 pour créer des prototypes. Consultez cet article pour en savoir plus sur la façon dont l’équipe de développement de produits a utilisé l’impression 3D pour créer des prototypes de haute précision.
Cependant, l’équipe de développement a rapidement compris que l’entreprise pouvait aussi utiliser l’impression 3D pour produire des outils de fabrication, tels que des supports, des fixations et des équipements de test.
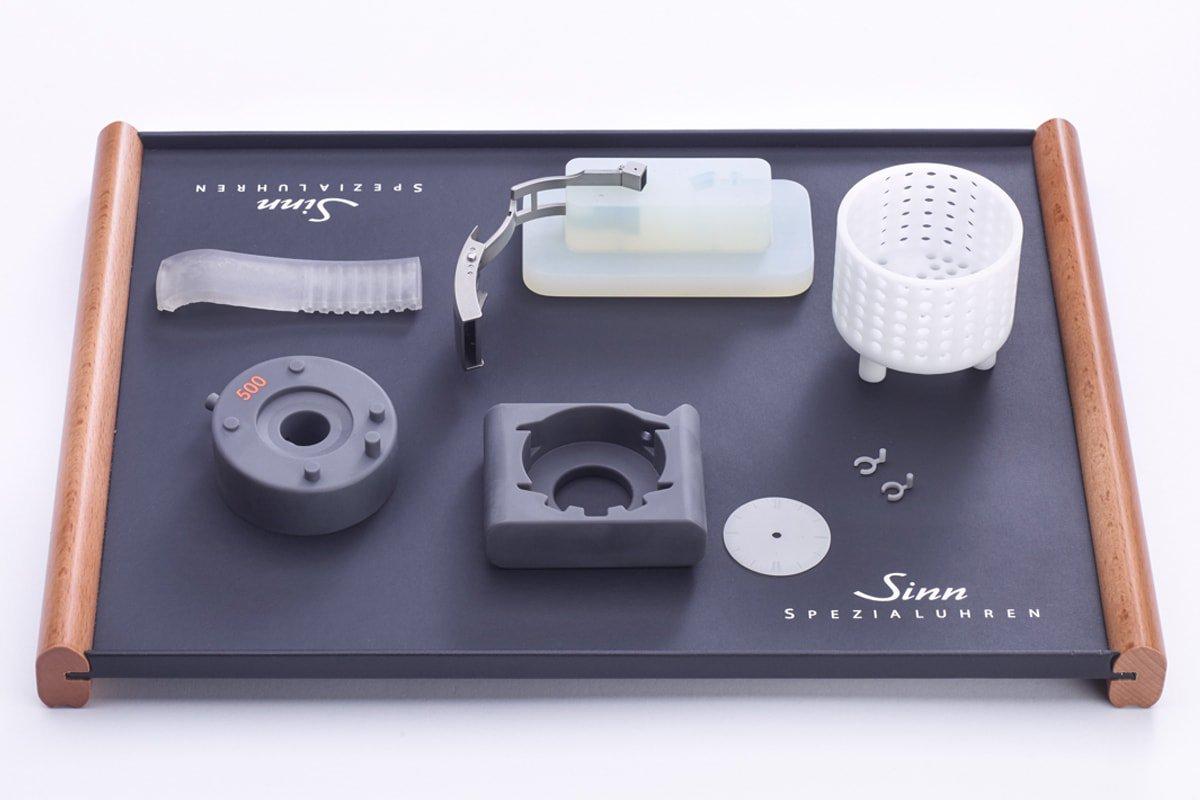
Prototypes de pièces de montre, fixations et équipements de test imprimés en 3D avec la Form 3.
Des outils sur mesure aux pièces produites en série
Dès que la société a reçu sa première imprimante 3D en interne, les employés ont tout de suite manifesté leur intérêt pour l’utilisation de cette technologie dans des applications autres que le prototypage, comme la fabrication d’équipements sur mesure. Nils Hunder, responsable de la conception des montres et du développement des prototypes et de l’impression 3D chez Sinn Spezialuhren, déclare : « Nous avons remarqué que l’imprimante nous était vraiment très utile dans ce domaine. »
« Nous pouvons fabriquer des supports et des fixations dans la nuit, très rapidement et à un faible coût. »
Nils Hunder, Responsable de l’ingénierie, du développement de produits et du prototypage
Avant d’utiliser l’impression 3D, la société faisait principalement appel à des fournisseurs de services externes pour fabriquer ses outils sur mesure. Les coûts de sous-traitance étaient élevés et les délais de production très longs, en moyenne une à deux semaines pour les supports et les fixations. De plus, les employés de Sinn Spezialuhren ne pouvaient jamais être sûrs que les outils répondraient vraiment à leurs besoins, ou pire, que les dépenses engagées ne s’avéreraient pas inutiles.
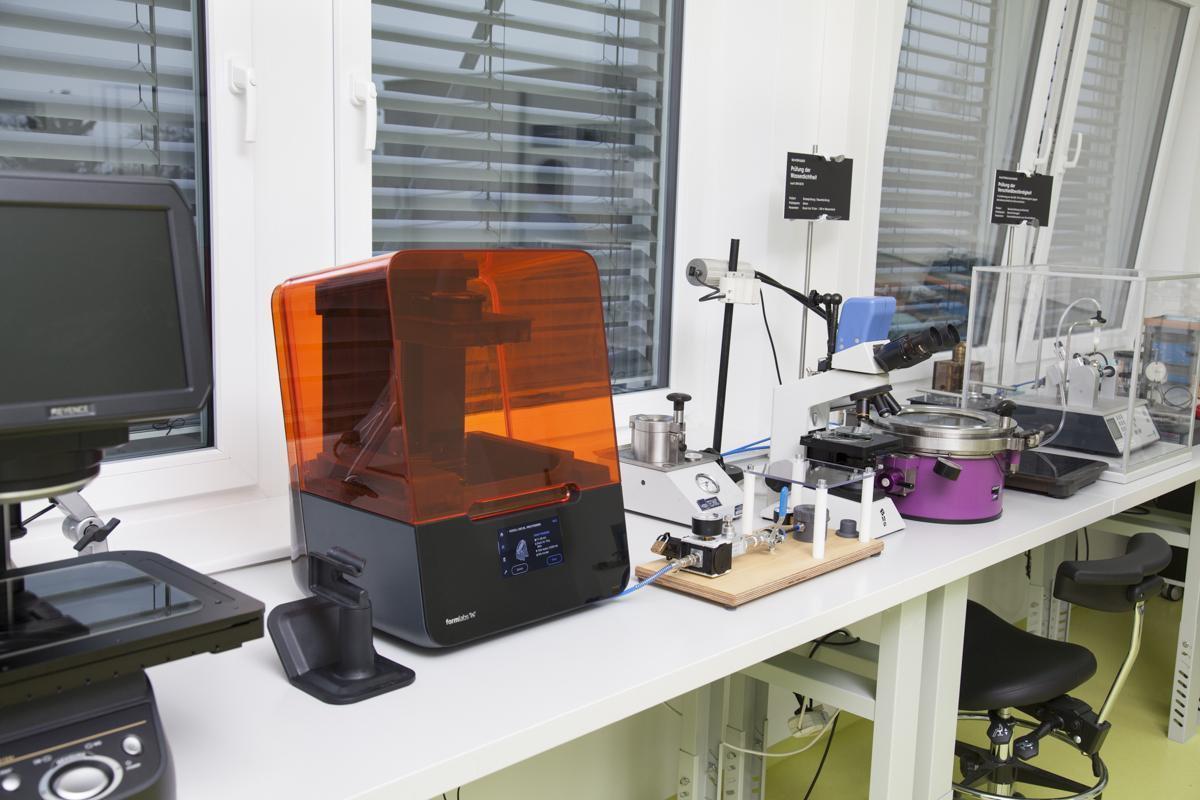
La Form 3 dans le laboratoire de Sinn Spezialuhren.
Désormais, la Form 3 est de plus en plus utilisée pour la fabrication d’équipements. Les seuls coûts sont ceux des matériaux et du temps requis pour le post-traitement. Les pièces peuvent être imprimées dans la nuit, et des ajustements peuvent être faits rapidement si les pièces imprimées ou les conceptions ne correspondent pas aux attentes.
Nils Hunder utilise principalement Tough 1500 Resin et Tough 2000 Resin, car ces matériaux permettent de fabriquer des pièces solides avec une déformation minimale. La Form 3 a notamment été utilisée pour imprimer des pièces en série pour 500 bouchons de couronnes pour des montres à quartz, qui n’étaient pas disponibles en production de masse. Ces bouchons de couronnes sont insérés entre le boîtier et la couronne, pour éviter que la batterie soit activée lorsque les montres sont stockées. Le fournisseur habituel de Sinn Spezialuhren n’avait pas la capacité de produire ces bouchons de couronnes en raison de la pandémie, et les coûts de production auraient de toute façon été trop élevés, car la quantité de commande minimale était de 10 000 pièces. Heureusement, la Form 3 a permis d’imprimer 50 bouchons de couronnes en une seule impression. Grâce à la légère flexibilité de Tough 1500 Resin, les pièces imprimées ne rayent pas les montres et sont réutilisables.
Dans une autre application, des boîtiers de montre en acier de Damas sont gravés en interne à des fins de test, et l’acide utilisé doit être mélangé afin d’homogénéiser la température. L’équipe de Sinn utilise des paniers imprimés en 3D en Rigid 4000 Resin, en raison de la grande résistance de ce matériau aux produits chimiques et aux acides.
Un autre champ d’application est la technologie de déshumidification Ar, qui a été développée par Sinn Spezialuhren pour les montres de plongée. Ces montres contiennent un gaz protecteur et nécessitent un support supplémentaire afin d’ajouter le gaz dans le boîtier de la montre. En utilisant la technique de production classique par fraisage, les deux pièces du support pour cette phase de production coûtent environ 200 €, pour un délai de production d’une à deux semaines. Avec un coût du matériau de 30 €, le coût total par pièce imprimée à l’aide de la Form 3, y compris le post-traitement, est de moins de la moitié. Le délai de production est également drastiquement réduit, les ingénieurs pouvant imprimer les pièces dans la nuit.
De plus, l’équipe peut graver des étiquettes personnalisées sur les supports, pour savoir au premier coup d’œil à quel modèle de montre un support correspond, ce qui facilite le travail au quotidien. Avec des outils de fabrication conventionnels, le marquage sur mesure des équipements entraînerait un coût supplémentaire.
Développement en interne d’un système de test certifié par l’association allemande pour le contrôle technique (TÜV)
La montre de plongée UX, l’un des modèles de la gamme Sinn, est remplie d’une huile limpide. Le volume du liquide varie avec la température, la montre est donc pourvue d’une base de membrane qui s’étend lorsqu’elle est chauffée ou qui se rétracte lorsque la température diminue. Cette base de membrane a offert l’élément le plus impressionnant pour M. Hunder et son équipe durant le développement d’un système de test.
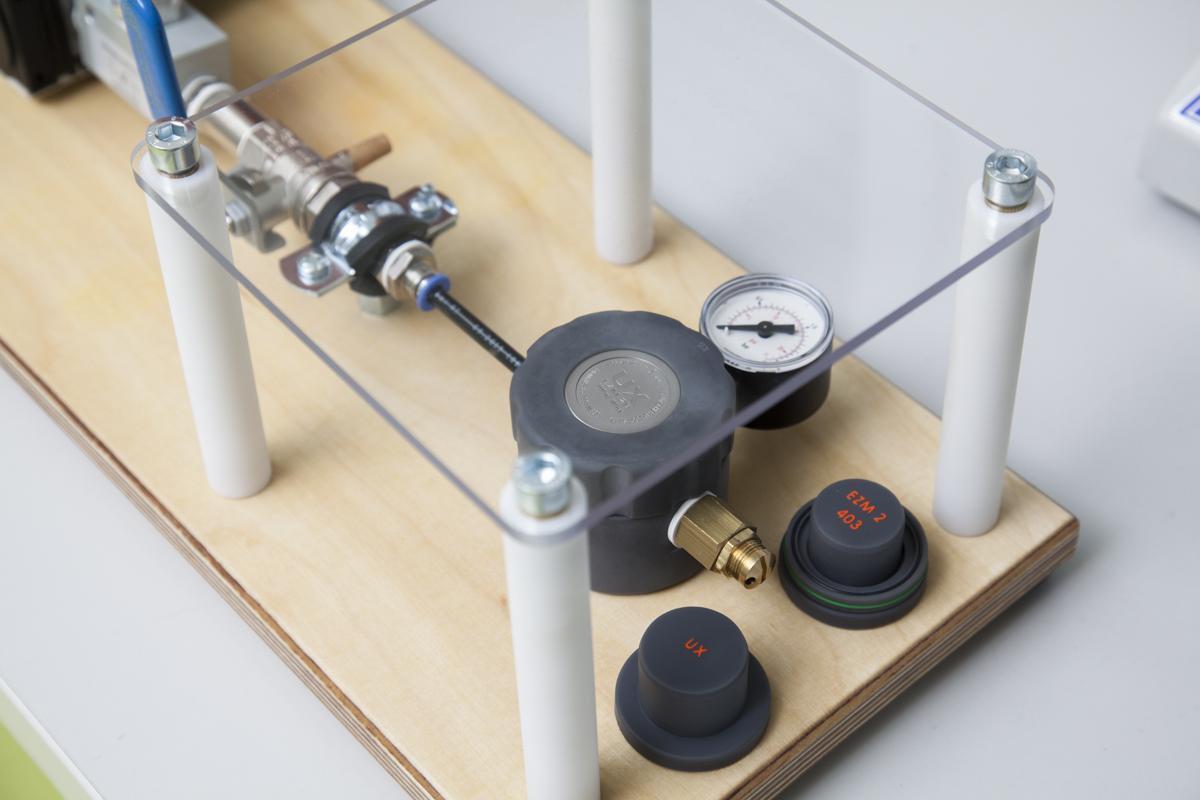
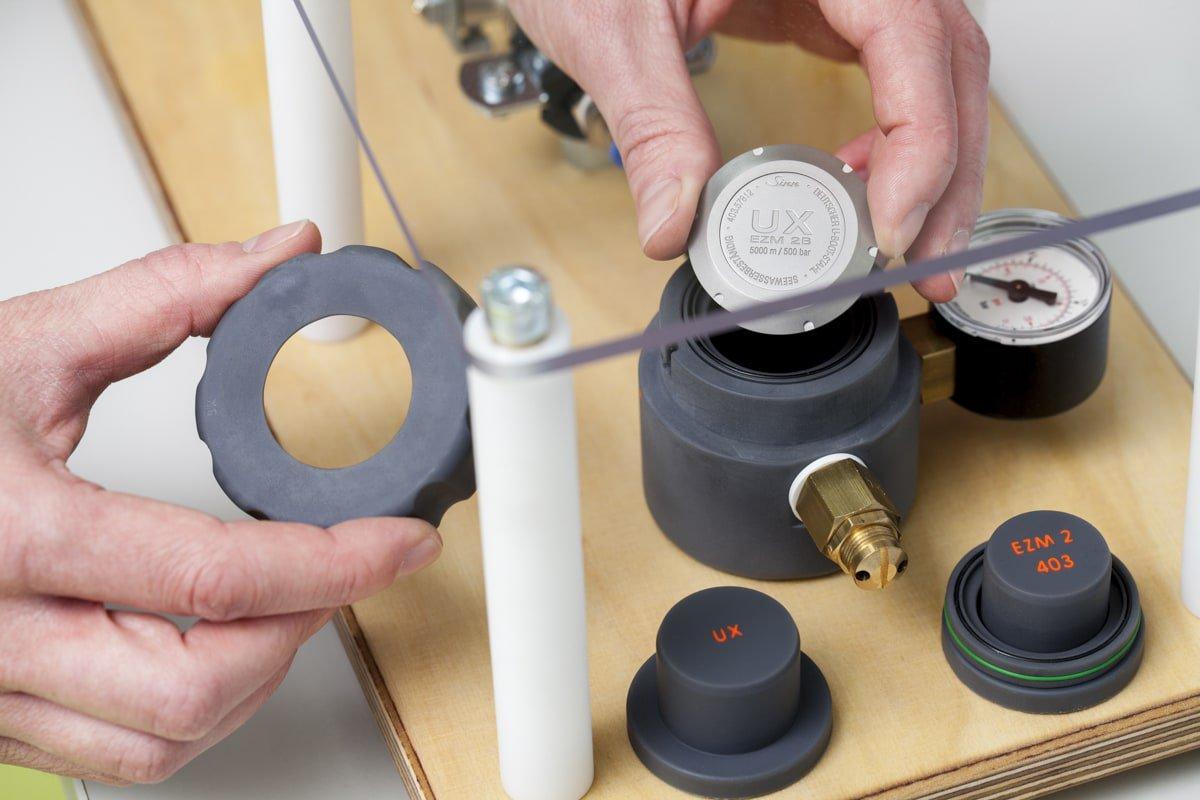
Système de test de la membrane de la montre UX avec un boîtier imprimé en 3D.
Le but du système de test est de vérifier le mouvement de la base de membrane, pour voir si elle se déploie de manière parfaitement rectiligne ou légèrement inclinée, afin de l’aligner en conséquence. Auparavant, pour tester cet alignement, il fallait entièrement construire une montre, puis la chauffer. Ce processus était chronophage, car tous les composants étaient salis par le liquide et devaient donc être nettoyés ensuite.
Pour alléger cette tâche fastidieuse, un système de test utilisant la pression de l’air pour simuler le comportement du liquide a été développé.
Vidéo : Le système de test de la membrane, imprimé en 3D, en action.
Tough 2000 Resin a été utilisée pour imprimer le générateur de pressurisation avec plusieurs anneaux d’insertion pouvant accueillir différents boîtiers, ainsi que le système de verrouillage, qui se ferme par une monture à baïonnette. La monture à baïonnette était la partie la plus délicate, car elle est très difficile à fabriquer dans un système de production classique. En outre, les supports du couvercle en verre acrylique ont été fabriqués en Rigid 4000 Resin.
Le banc d’essai imprimé en 3D était à l’origine prévu uniquement pour tester la faisabilité générale des tests et l’utilisation de la monture à baïonnette. Les tests ont été si concluants que les méthodes de production conventionnelles ne sont plus nécessaires. Le banc d’essai imprimé en 3D a été également été contrôlé et approuvé par l’association allemande pour le contrôle technique (Technische Überwachungsvereine, TÜV).
« Une fois que vous savez que vous pouvez imprimer la pièce dont vous avez besoin, vous pouvez vous concentrer uniquement sur la fonctionnalité. C’est un avantage considérable. »
Nils Hunder, Responsable de l’ingénierie, du développement de produits et du prototypage
L’équipe de M. Hunder avait initialement demandé à son fournisseur habituel chargé de la production en série des boîtiers de montres de fabriquer le système de test. Cependant, le fournisseur aurait utilisé la même fraiseuse que pour fabriquer les boîtiers de montres, ce qui aurait retardé la production des montres. Finalement, Sinn Spezialuhren a envoyé le système de test conçu en interne à son fournisseur, la société devenant ainsi elle-même un fournisseur — une toute nouvelle expérience pour l’équipe.