Comment IGESTEK développe des pièces composites avec l'impression 3D et l'outillage rapide
Située dans la région de Bilbao en Espagne, IGESTEK est une entreprise de premier plan qui développe des solutions légères pour l'industrie automobile en utilisant des matières plastiques et des matériaux composites.
La société développe et intègre différentes techniques de traitement hybride pour fabriquer des composants composites, qui peuvent ensuite être utilisés par des fournisseurs automobiles de niveau 1 et des fabricants d'équipements d'origine (FEO) pour produire des pièces destinées à des voitures et à des motos haut de gamme.
L'équipe d'IGESTEK utilise l'impression 3D tout au long du processus de développement de produits, de la phase de conception pour vérifier les géométries jusqu'à la phase de conception pour créer des prototypes fonctionnels. Ils utilisent également l'impression 3D pour fabriquer des outils rapides, tels que des inserts pour les moules d'injection plastique ou des outils de thermoformage pour les composites.
Lisez la suite pour savoir comment IGESTEK améliore sa vitesse de développement, réduit les coûts et trouve des solutions agiles aux problèmes rencontrés.
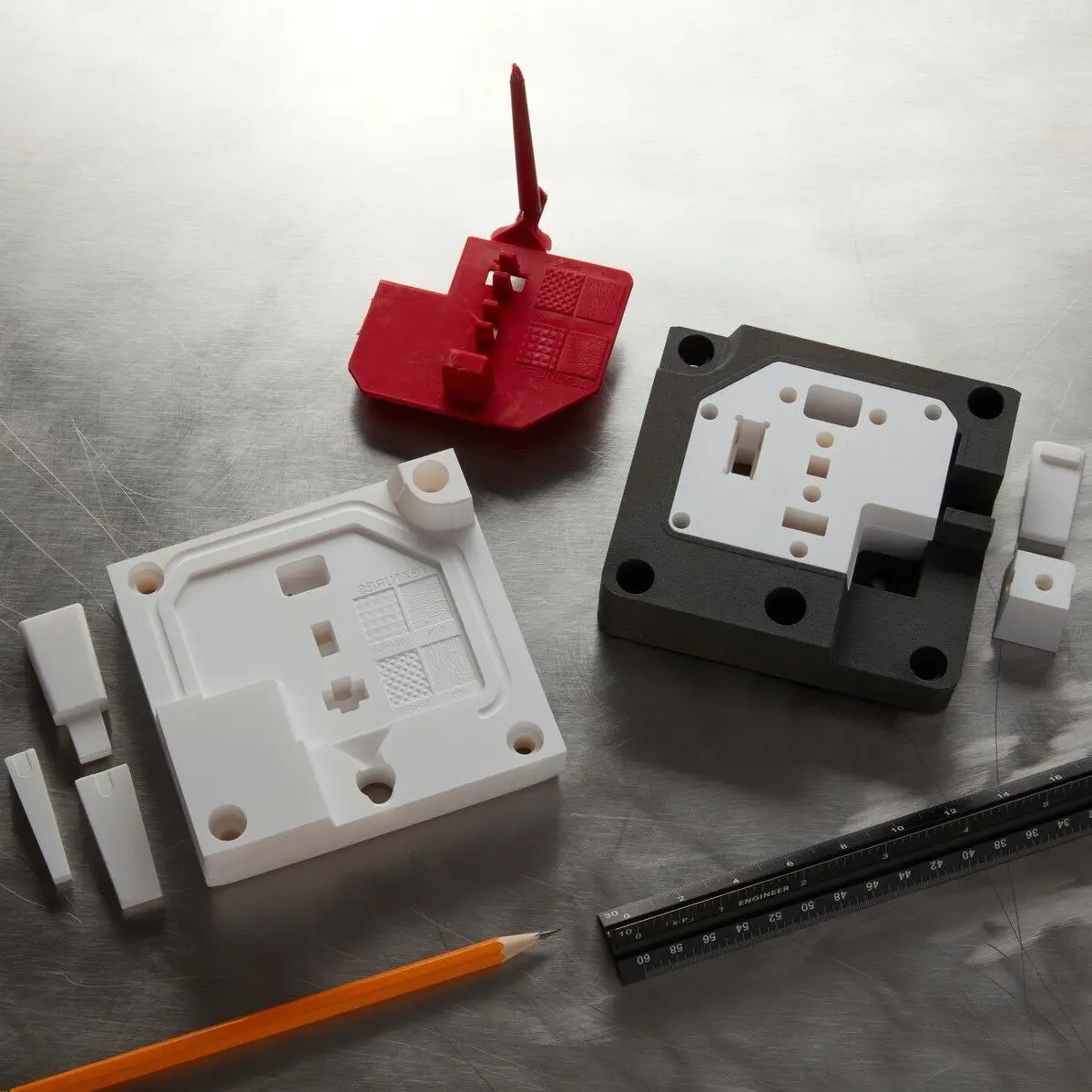
Guide de l'outillage rapide
Dans ce livre blanc, apprenez comment combiner l'outillage rapide imprimé en 3D avec des procédés de fabrication traditionnels tels que le moulage par injection, le formage sous vide ou la fonderie.
Itérer un composant automobile de conception générative avec la Form 3L
L'un des derniers projets innovants d'IGESTEK est un support d'amortisseur de suspension (montage supérieur). Ces composants font partie du système de suspension d'une voiture et visent à réduire les vibrations produites par le roulement du véhicule afin d'améliorer le confort des passagers.
Le support d'amortisseur a été développé à l'aide du logiciel de conception générative Fusion 360 d'Autodesk, qui a fourni de nombreuses solutions en se basant sur une série limitée d'exigences.
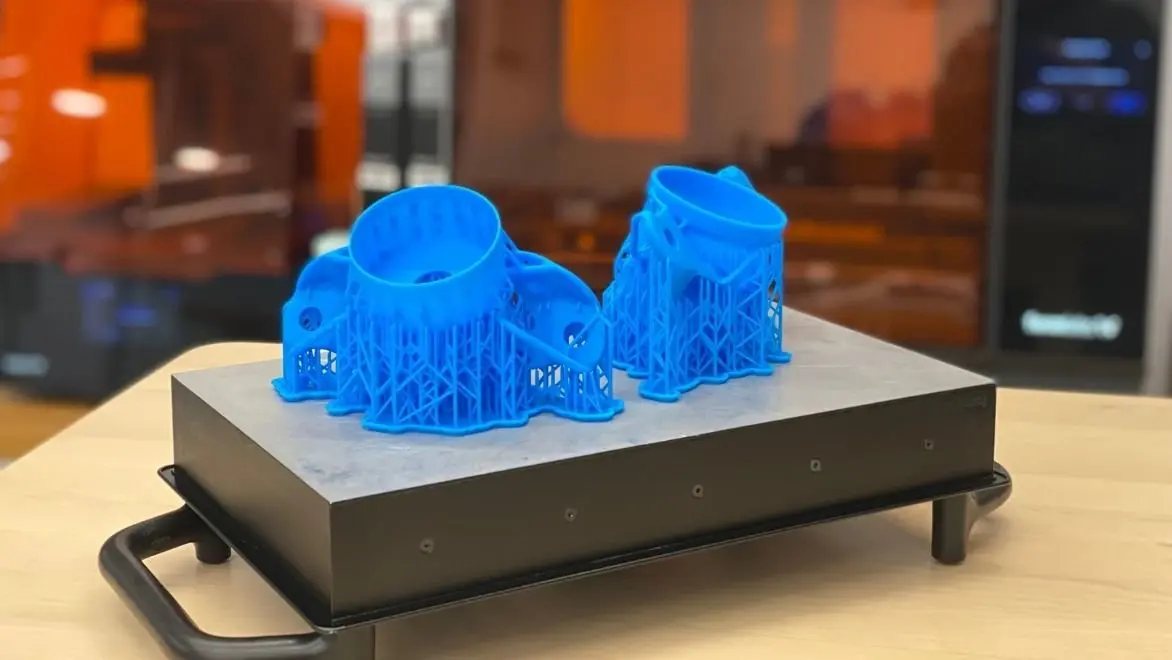
Le grand volume de fabrication de la Form 3L a permis à IGESTEK d'imprimer en même temps plusieurs versions du composant.
L'équipe a ensuite imprimé en 3D les modèles les plus prometteurs sur son imprimante 3D stéréolithographique (SLA) grand format Form 3L en interne pour valider la géométrie, tirant parti de son grand volume de fabrication pour imprimer en même temps jusqu'à trois versions différentes du composant. L'impression 3D SLA a permis de rendre les géométries complexes obtenues par conception générative et de valider les processus d'assemblage et de cinématique avec des prototypes fonctionnels, sans devoir investir dans un outillage coûteux.
Le résultat final du processus de R&D a été une architecture multi-matériaux, qui combine l'impression 3D de métaux présentant des géométries génératives et des matériaux composites plus légers pour offrir les meilleures performances possibles. L'ensemble est 40 % plus léger que les solutions actuellement disponibles sur le marché.
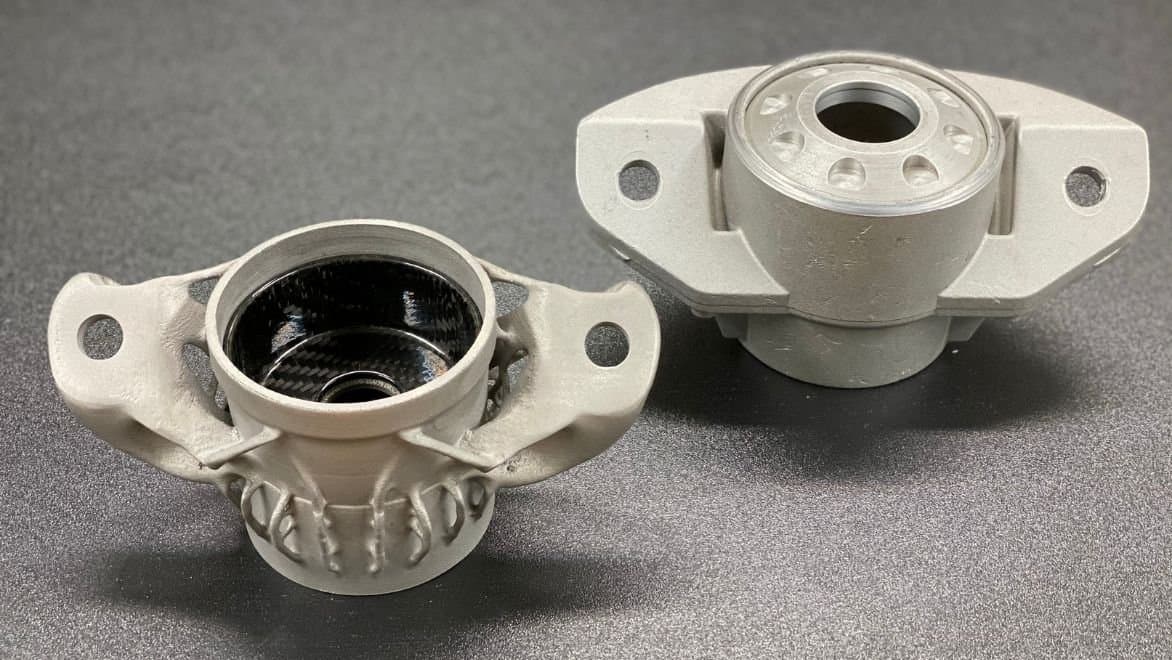
Le résultat final, fabriqué en utilisant l'impression 3D de métaux et des matériaux composites.
Utilisation de divers matériaux d'impression 3D SLA pour créer un outil de thermoformage
L'équipe d'IGESTEK utilise également l'impression 3D pour d'autres applications que le prototypage. Elle produit par exemple de l'outillage rapide destiné à la fabrication de pièces composites, comme le thermoformage de préimprégnés de carbone.
« Les résines Formlabs, telles que Rigid 10K Resin et High Temp Resin, sont très pratiques en ingénierie. Nous travaillons généralement avec des technologies de thermoformage par compression de composites. Pour fonctionner avec une presse, l'outil doit être rigide et résistant à la chaleur, car elle utilise une pression et une température élevées, généralement de 180 ou 200 degrés, [pour former les pièces composites] », explique Nerea Romero, responsable de l'innovation chez IGESTEK.
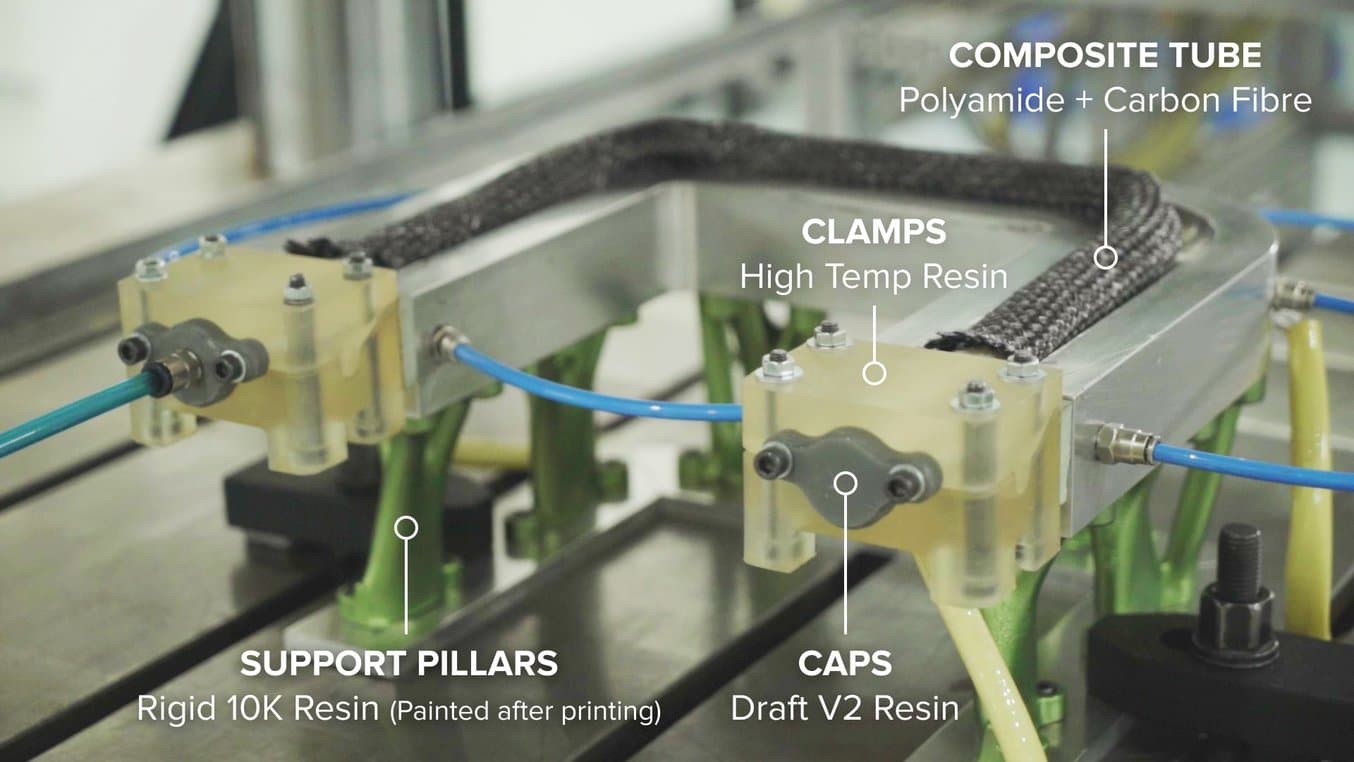
Cette plateforme de thermoformage pour tubes composites a été fabriquée avec diverses pièces imprimées en 3D.
L'équipe a récemment développé un outil pour fabriquer des tubes composites. Ils ont utilisé Rigid 10K Resin pour produire les piliers de support de la plateforme qui nécessitaient une grande rigidité, High Temp Resin pour produire les pinces qui devaient résister à des températures élevées et à la pression de l'air, et Draft Resin pour produire rapidement les embouts de l'outil.
« [Si nous n'avions pas eu accès à l'impression 3D], nous aurions dû le produire avec du métal, ce qui demande bien évidemment plus de temps et d'argent. L'impression 3D nous permet de trouver rapidement ce que nous recherchons. Si quelque chose ne fonctionne pas, nous pouvons simplement imprimer un autre prototype et l'améliorer », a déclaré M. Romero.
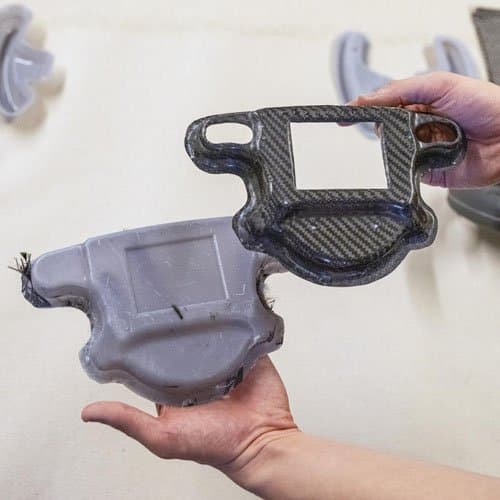
La fabrication de pièces en fibre de carbone avec des moules imprimés en 3D
Téléchargez ce livre blanc pour obtenir des instructions de conception de moules ainsi que des guides étape par étape concernant les méthodes de pré-imprégnation et de laminage manuel pour créer des pièces en fibre de carbone.
Le moulage par injection avec des inserts de moules imprimés en 3D
L'équipe d'IGESTEK utilise également l'impression 3D pour fabriquer des inserts de moules d'injection plastique. Auparavant, ils usinaient les inserts en aluminium et en acier ; en interne pour les pièces simples, et en externe pour les moules plus complexes. Mais cela entraînait des coûts élevés et de longs délais, en particulier pour les prototypes uniques ou produits en petite série.
Récemment, l'équipe a imprimé en 3D un insert de moule d'injection pour fabriquer un des composants du revêtement extérieur d'une voiture, réduisant ainsi les coûts et les délais de plus de 65 %.
Insert de moule d'injection | Imprimés en 3D | Métallique usiné |
---|---|---|
Coût | 300 € | 1000 € |
Délai de réalisation | ~ 10 heures | 30 heures |
Le moule comporte deux cavités : l'une est constituée d'un insert métallique et l'autre d'un insert personnalisé imprimé en 3D qui contient le négatif de la conception. C'est parfait pour le prototypage, car l'équipe peut facilement changer les inserts imprimés en 3D et tester rapidement différentes versions.
« Pour la phase de prototypage, il faut juste assembler quelques composants avec d'autres composants pour tester la symétrie de l'ensemble. 20 ou 50 composants suffisent pour prouver que ce que vous faites fonctionne », a déclaré M. Romero.
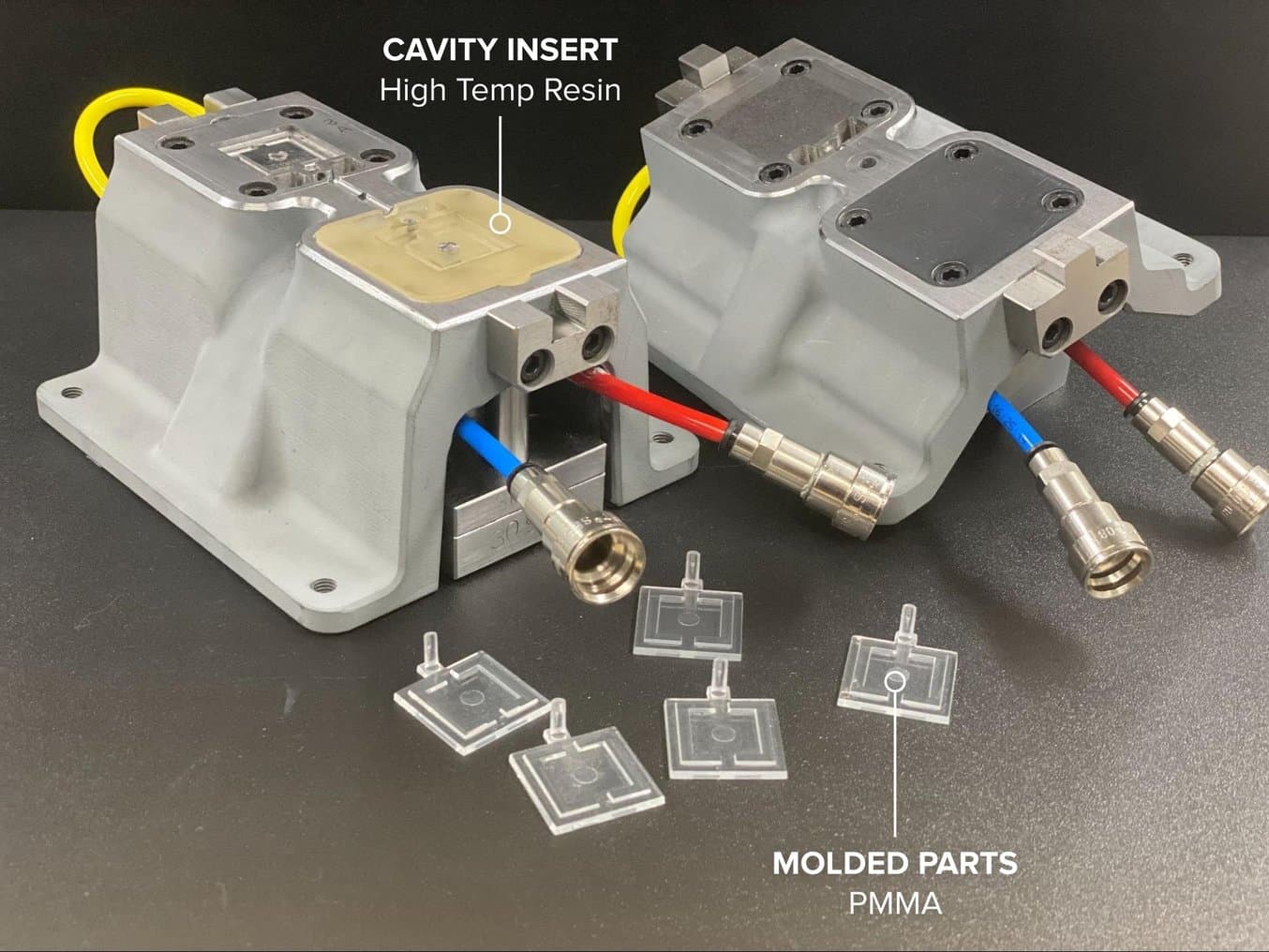
Installation de moulage par injection pour un composant automobile en PMMA, avec un insert de moule imprimé en High Temp Resin.
Le nombre de pièces moulées que l'on peut obtenir avec un insert imprimé en 3D dépend principalement de trois facteurs : le matériau de moulage, le système d'injection et les paramètres du processus de moulage.
« Cela dépend beaucoup du type de matériau que vous utilisez pour le moulage par injection ou pour le composite. Pour le moulage par injection par exemple, le plastique renforcé de fibres est beaucoup plus agressif que les matériaux conventionnels. [L'insert] s'usera donc plus vite. Vous pouvez peut-être fabriquer 20 composants, mais si vous en voulez plus, il vous suffit d'échanger les inserts pour continuer à produire », a déclaré M. Romero.
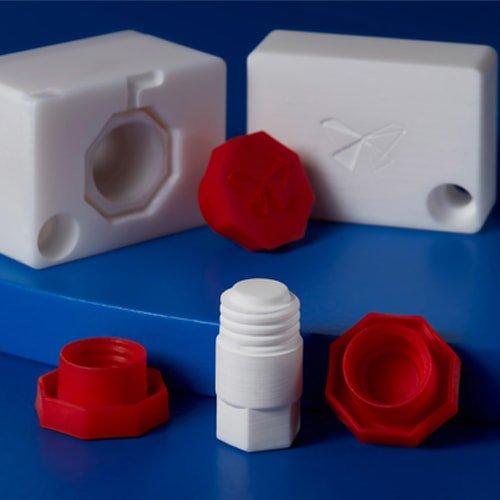
Le moulage par injection rapide en petites séries avec des moules imprimés en 3D
Téléchargez ce livre blanc pour savoir comment utiliser des moules imprimés en 3D pour le processus de moulage par injection, et ainsi réduire les coûts et les délais de production. Vous y trouverez des études de cas réels, réalisées chez Braskem, Holimaker et Novus Applications.
Passer au prochain grand projet
Tout en continuant à innover, l'équipe d'IGESTEK réfléchit déjà à la façon dont elle utilisera l'impression 3D dans ses prochains projets pour repousser les limites de ce qui est possible.
Pour ses prochains projets, elle souhaite notamment fabriquer de l'outillage de thermoformage à grande échelle, tirer parti du volume de fabrication de la Form 3L, et expérimenter d'autres matériaux tels que Flexible 80A Resin et Elastic 50A Resin pour donner de nouvelles propriétés à l'outillage.