Comment Plaato a aidé son sous-traitant de fabrication à accélérer la DFM grâce à l’impression 3D
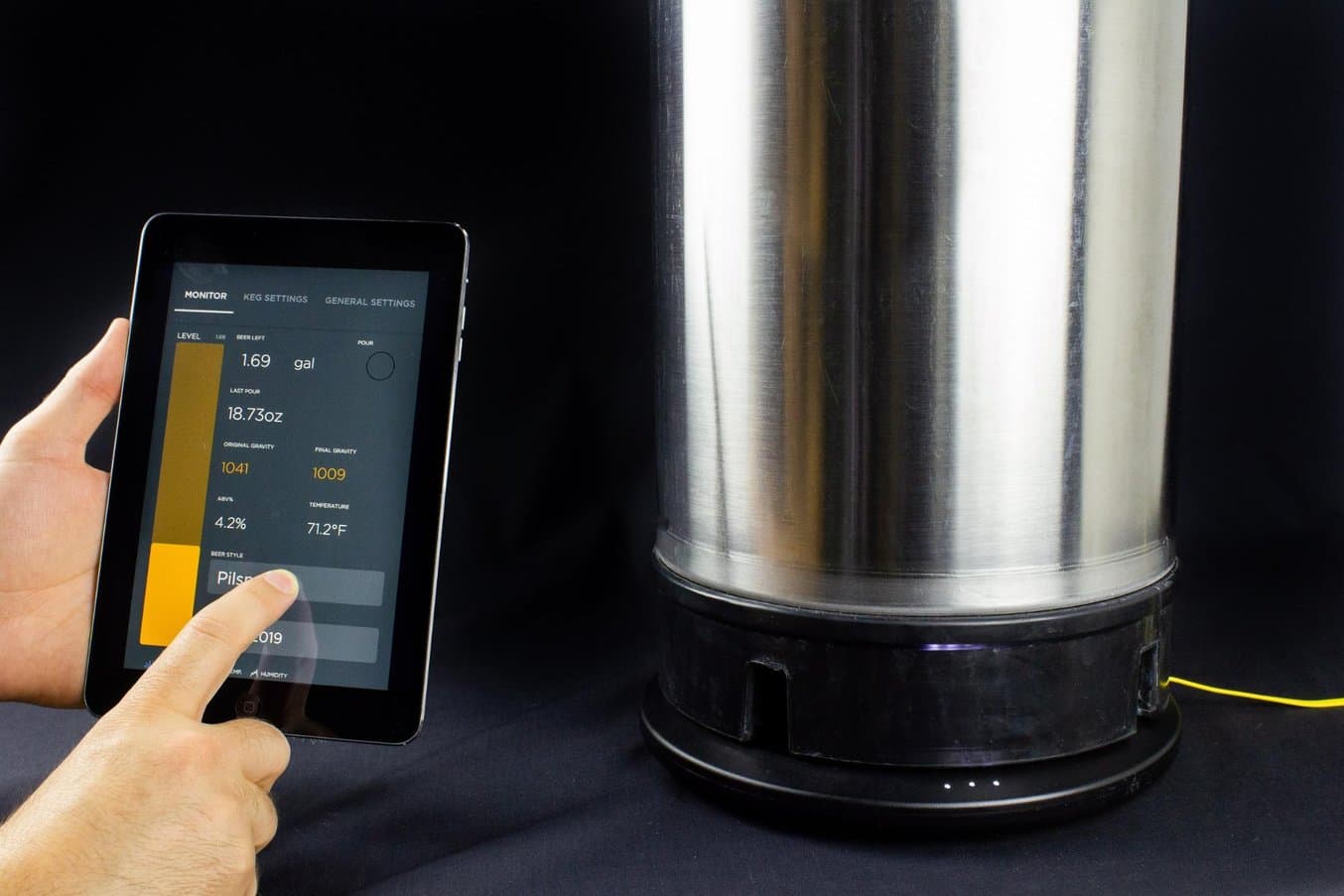
Le nom de Plaato doit dire quelque chose aux lecteurs de notre blog. En effet, l’année passée, nous avons raconté leur histoire sur le développement d’un barboteur intelligent qui mesure la quantité de CO2 relâchée pendant la fermentation des bières artisanales.
Depuis, Michael Kononsky et son équipe ont poursuivi leur mission : donner aux brasseurs le moyen d’exploiter leurs données. Ils ont donc lancé un nouveau produit, le Plaato Keg, une balance intelligente pour surveiller les fûts de bière.
Même si le barboteur nécessitait des pièces translucides complexes, le développement de leur dernier produit a donné lieu à une foule de nouvelles difficultés à résoudre. « Nous avions besoin d’un dispositif étanche qui puisse supporter le poids d’un fût, qui peut peser de 20 à 60 kilos quand il est plein », déclare Kononsky.
Continuez à lire pour découvrir comment l’équipe de Plaato a créé plus de 100 prototypes pour des testeurs bêta aux quatre coins du monde et comment elle a imprimé en 3D de nouvelles itérations dans ses propres bureaux et chez son sous-traitant de fabrication pour finaliser la conception en vue de la fabrication (DFM) de leur nouveau produit, qui a déjà reçu deux prestigieux Red Dot Awards.
Comment permettre aux brasseurs d’exploiter leurs données ?
« En discutant avec un de nos revendeurs, on s’amusait à se lancer des idées et on s’est dit : "Bon, et si on pouvait savoir combien de bière on consomme et combien il en reste dans l’inventaire ?" Parce que beaucoup de gens ont plusieurs fûts différents et un réfrigérateur à fûts. Tout ce matériel se trouve dans leur cave, donc ils ne savent pas quelle quantité de bière il leur reste ou de quand date le fût. Nous avons donc réalisé quelques prototypes et nos clients ont adoré le concept. Ils nous ont dit qu’ils voulaient encourager ce produit », déclare Kononsky.
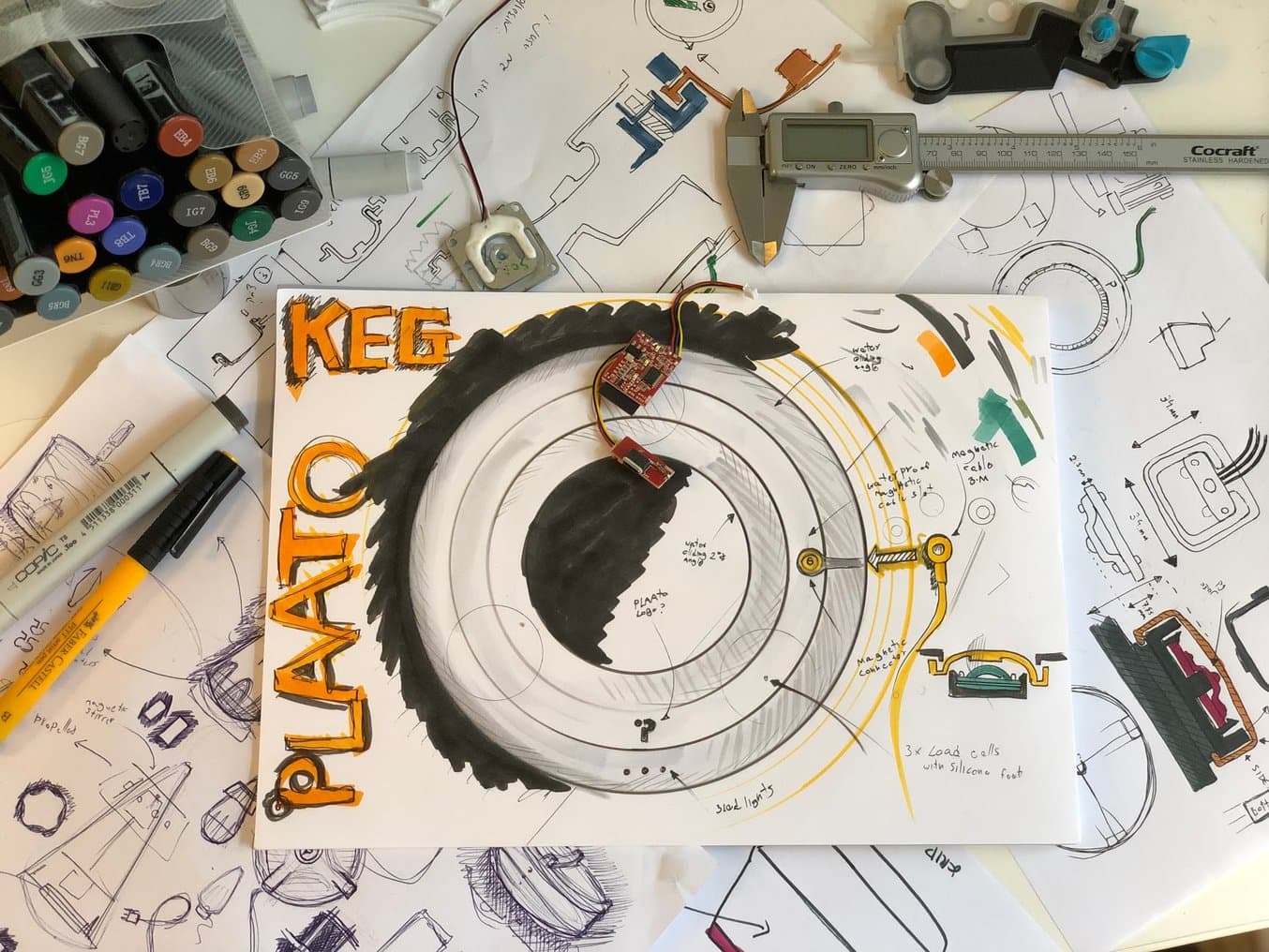
Esquisses de conception du Plaato Keg, comprenant le connecteur et les cellules de pesage.
Les solutions actuellement disponibles sur le marché sont toutes basées sur des débitmètres qui ont tendance à s’encrasser et dont l’installation et le raccordement doivent être effectués par l’utilisateur. Kononsky et son équipe ont pensé qu’ils pouvaient mesurer le volume de bière de manière plus propre et plus facile en convertissant le poids et la gravité spécifique.
« Nous voulions juste mesurer la quantité de bière sans la toucher et sans rien raccorder au circuit du liquide. Il fallait quelque chose d’ultra-simple à placer sous le fût. On pose bêtement le fût sur la plateforme et on peut consulter les données dans le cloud. Rien qu’en Norvège, notre tout petit pays, nous estimons qu’il y a environ 14 000 réfrigérateurs à fûts et que l’utilisateur moyen possède sept à huit fûts », explique Kononsky.
Développer et tester un produit assez robuste pour les fûts
« Nous avons impliqué la communauté dans le développement, nous avons interrogé 300 utilisateurs existants de notre barboteur qui étaient intéressés par un dispositif pour fût. Nous leur avons demandé : "Quel genre de fûts utilisez-vous ? Quels problèmes posent-ils ? Comment utilisez-vous ces fûts ? Se trouvent-ils dans un environnement humide ? Quel genre de raccords et de câbles peuvent trouver place dans votre réfrigérateur à fûts ?" Nous avons reçu des photos et des dimensions pour des milliers de fûts différents, donc nous avons vraiment dû optimiser le produit pour qu’il corresponde à tout ça », dit Kononsky.
Kononsky et son équipe ont commencé par découper au laser des plaques d’acrylique et à les fixer les unes aux autres, mais ils ont trouvé qu’il était trop compliqué de reproduire la forme des fûts et que le processus prenait bien trop de temps. Ensuite, ils ont eu recours à une imprimante 3D FDM équipée d’une buse spéciale de 1 mm de diamètre pour pouvoir produire rapidement une grande quantité de prototypes et accélérer la validation commerciale. Un fois qu’ils ont dû passer à des prototypes plus sophistiqués et plus détaillés, ils se sont tournés vers l’impression 3D par stéréolithographie.
L’équipe de Plaato a utilisé plusieurs techniques pour créer ses prototypes en fonction de l’avancée du développement : des plaques d’acrylique découpées au laser (translucides) et l’impression 3D FDM (texture noire et rugueuse) au début, puis l’impression 3D SLA pour les prototypes détaillés (cadre blanc et boîtier poli peint en noir).
« Nous devions réaliser un produit peu épais, étanche et capable de résister aux impacts, et ça n’a pas été sans peine. Mais Rigid Resin a complètement changé la donne. On pouvait visser tous les capteurs dessus, on pouvait réaliser tout le profilage du plastique et on pouvait la rendre étanche. Elle nous a donné le niveau de détail dont nous avions besoin, un argument que nous avons fait valoir auprès de nos fabricants », déclare Kononsky.
Rigid Resin a complètement changé la donne.
Michael Kononsky, co-fondateur de Plaato
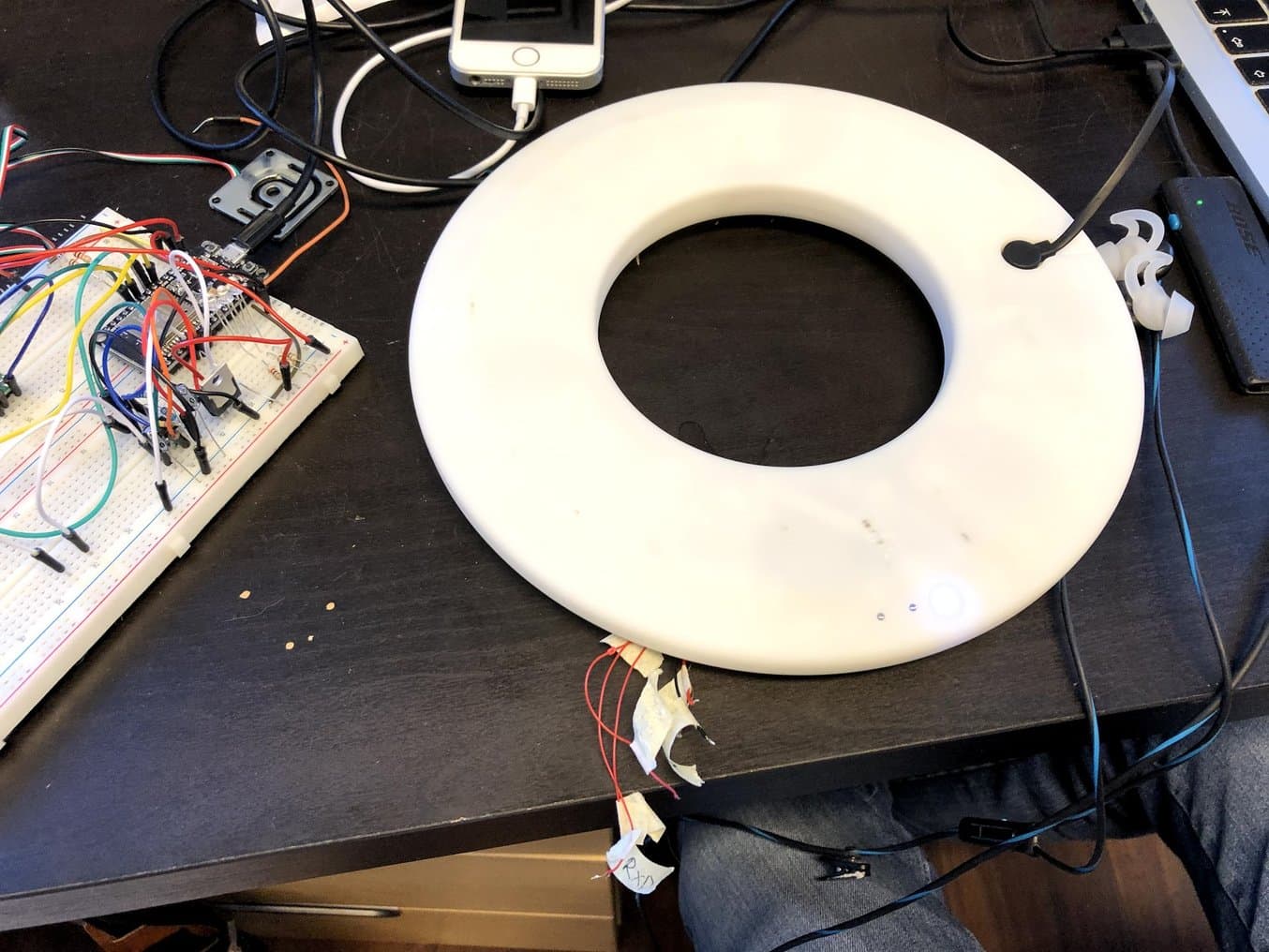
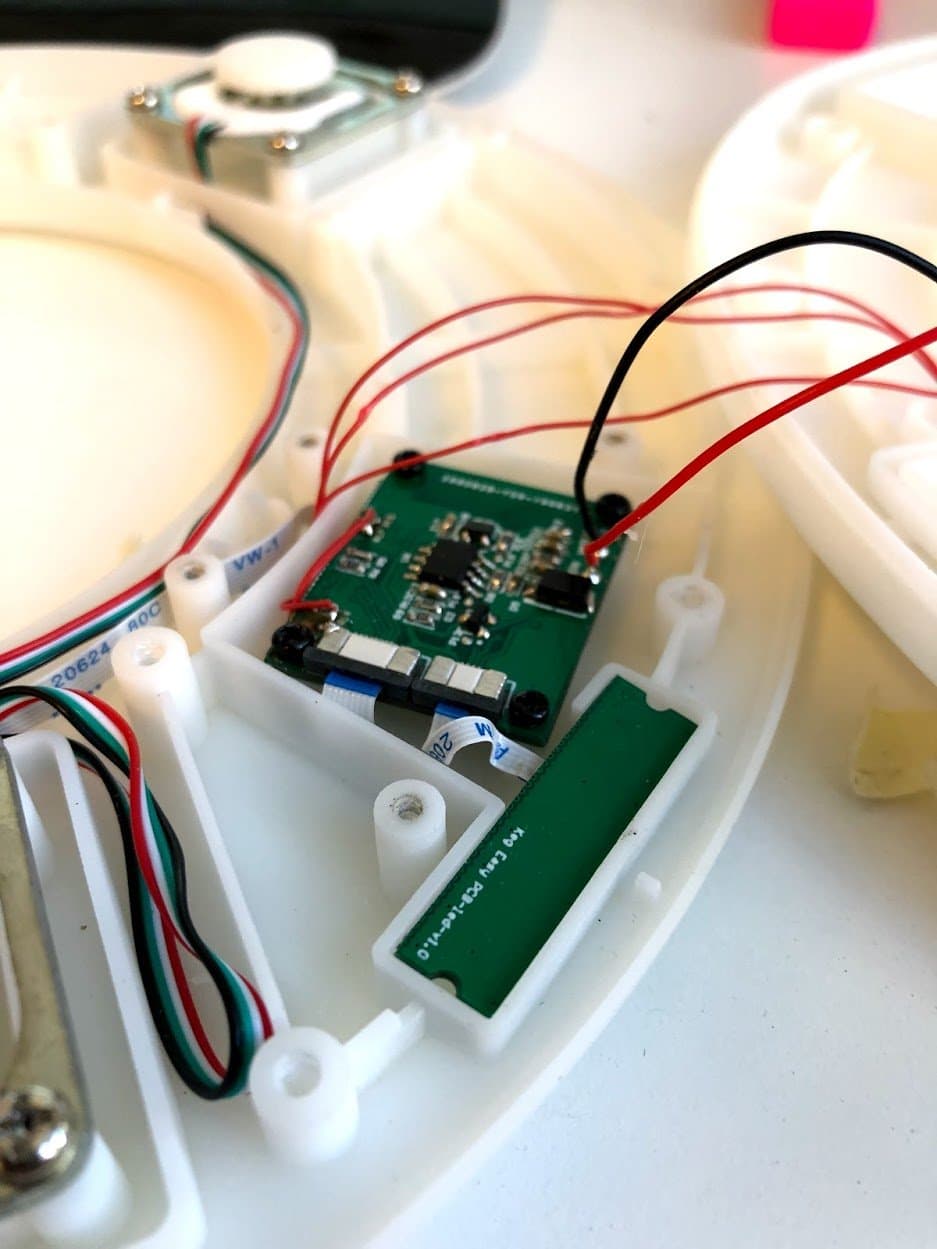
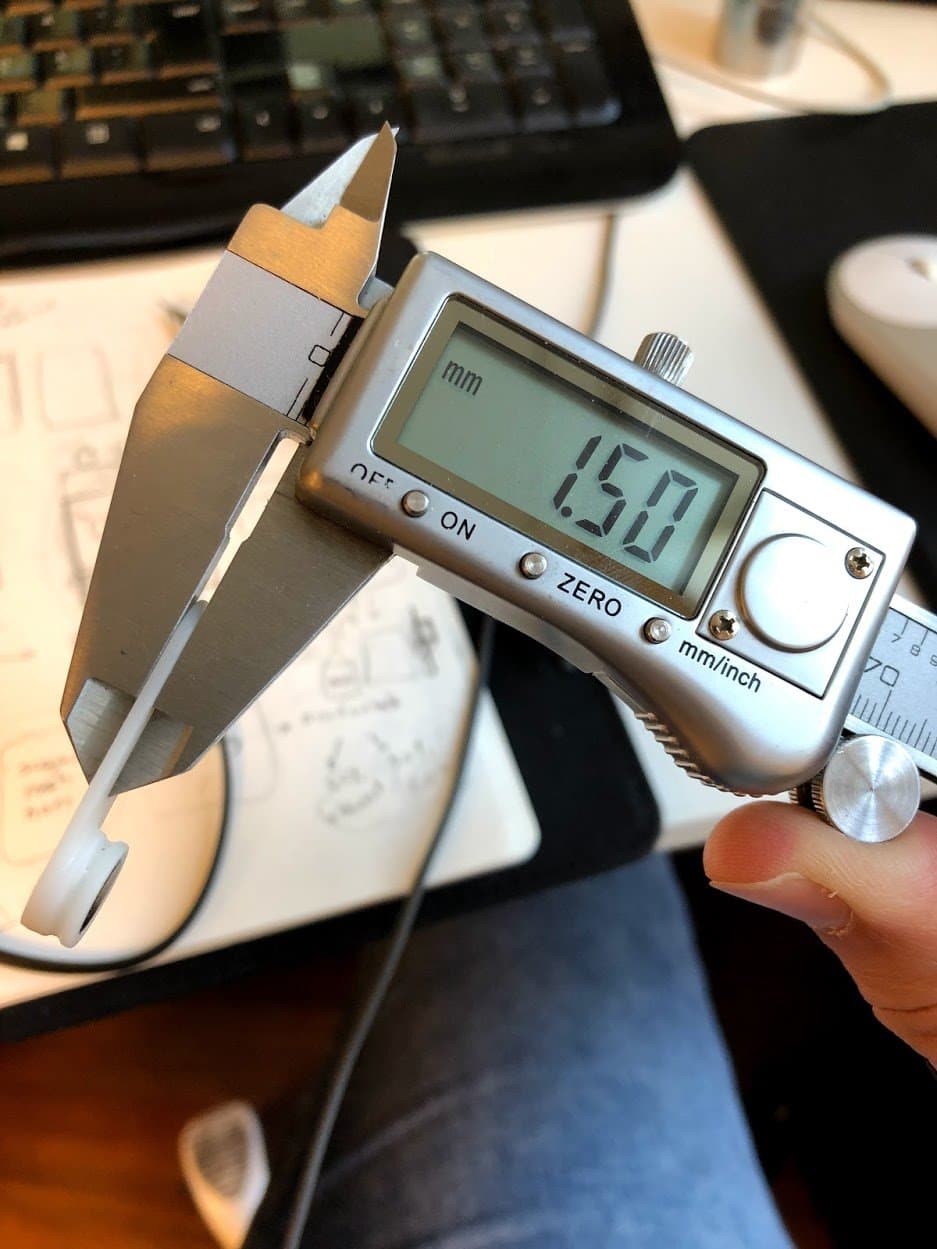
Les ingénieurs ont utilisé Rigid Resin pour créer des prototypes détaillés à parois fines qui présentaient toutes les caractéristiques du modèle final moulé par injection.
Les circuits imprimés, les capteurs et autres modules électroniques sont logés dans des compartiments vissés sur le boîtier. Mais ils ne sont pas étanches à l’eau, donc l’équipe a dû créer des joints sur mesure et les coques qui les enveloppent les empêchent à la fois de bouger et d’être endommagés. Ces compartiments devaient avoir un bon ajustement et de bonnes tolérances pour résister à la compression et rester étanches.
« Nous avons utilisé Elastic Resin pour un prototypage rapide. Nous avons juste joué sur l’épaisseur. C’est très intéressant d’avoir un ensemble de 20 joints différents en une seule impression : un de 1,1 millimètre, un de 1,2, un de 1,4 et ainsi de suite. Il me suffit de tous les essayer et c’est réglé. Ça m’évite de dépenser beaucoup d’argent », explique Kononsky.
En tout, l’équipe de Plaato a créé entre 35 et 40 prototypes sur son imprimante 3D SLA Formlabs. Ils ont fractionné les modèles en plusieurs pièces plus petites de manière à pouvoir toutes les imprimer en même temps sur une seule plateforme en neuf heures.
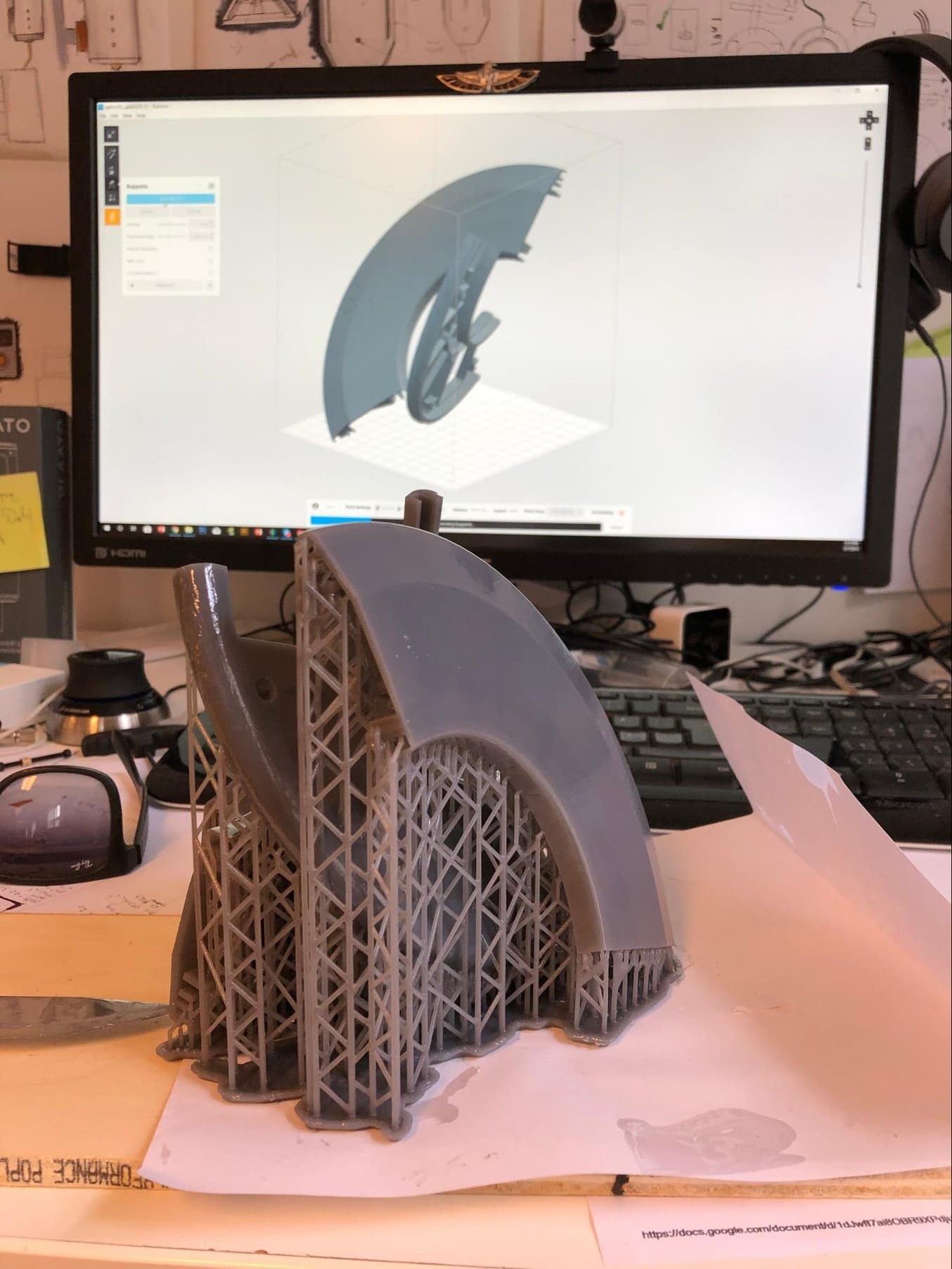
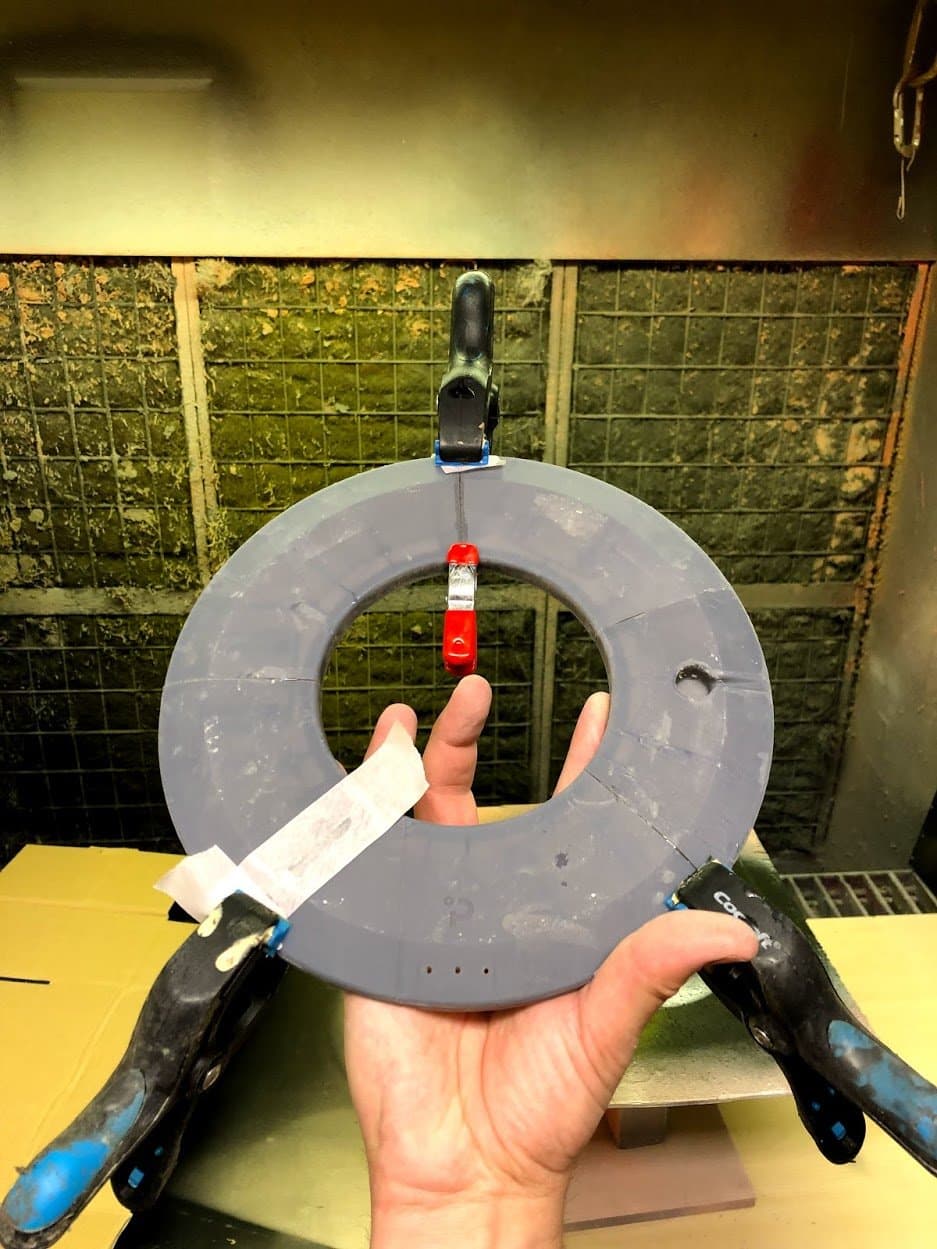
L’équipe de Plaato a fractionné les modèles en plusieurs pièces plus petites pour pouvoir toutes les imprimer en même temps sur une seule plateforme.
« Ce qu’il y a de génial avec cette imprimante, c’est que je peux la laisser faire le boulot pendant la nuit, donc la dernière chose que je fais avant de rentrer chez moi, c’est lancer une impression. Quand je reviens le lendemain matin, l’impression est terminée. Je lave les pièces, je les post-polymérise, je passe environ une heure à les assembler complètement, modules électroniques compris et avant le déjeuner, j’ai ma nouvelle version du prototype », détaille Kononsky.
L’équipe a aussi impliqué la communauté dans les étapes du prototypage. Des premiers prototypes PMV (produit minimum viable) à ceux ressemblant au produit final, Plaato a envoyé environ 100 prototypes à des clients aux États-Unis, en Amérique du Sud, en Asie, en Australie, en Europe et au Moyen-Orient. Cela a fourni à l’équipe de précieux retours d’expérience qu’ils ont pu répercuter dans les itérations suivantes, par exemple les idées d’un système d’avertissement en cas de fuite dans le fût et d’un capteur de température qui émet une alerte si le thermostat prend feu, ce qui arrive parfois aux réfrigérateurs à fûts faits maison.
Les prototypes imprimés en 3D ont aussi permis à Plaato de vérifier que leur modèle serait suffisamment robuste pour résister aux environnements de stockage des fûts.
« Nous l’avons laissé tomber comme pour un crash test d’une hauteur de 10 centimètres, puis 20, 30, 40. On l’a même fait chuter d’un mètre de haut et il a survécu. Nous savions que si ça fonctionnait avec de la résine, ça fonctionnerait à coup sûr pour un moulage par injection, parce qu’on avait choisi du polycarbonate à haute résistance, la même matière dont sont faits les boucliers anti-émeute de la police. Nous avons même réussi à imprimer en 3D un produit qui peut rester immergé dans un mètre d’eau pendant 48 heures et rester parfaitement intact. Cela nous a fait gagner beaucoup de temps de développement et nous a évité beaucoup d’alternatives bien plus chères auxquelles nous aurions eu recours si nous avions pratiqué un développement à l’ancienne », déclare Kononsky.
Conception en vue de la fabrication par impression 3D d’itérations à domicile et en Chine
Kononsky et son équipe se sont légèrement facilité la tâche pour ce nouveau produit parce qu’ils ont opté pour le même sous-traitant de fabrication que pour le barboteur. En utilisant l’impression 3D SLA dans ses bureaux et sur le site du sous-traitant de fabrication, Plaato a pu accélérer le processus de validation et augmenter rapidement le volume de fabrication.
« J’aime que le processus de conception soit terminé à 90–95 % avant de commencer à sous-traiter la fabrication. Je veux laisser une marge de manœuvre au sous-traitant car il connaît ses machines et il sait quelles sont leurs capacités. Nous faisons confiance au professionnalisme de notre partenaire, donc je n’ai pas voulu lui imposer de minuscules détails techniques qui auraient pu compliquer inutilement le projet », explique Kononsky.
« Notre partenaire de fabrication s’est procuré une Form 2 lui aussi, donc la communication en a été facilitée. Comme ils avaient la même imprimante que nous, je pouvais leur envoyer les fichiers que j’avais séparés moi-même pour l’impression. Ensuite je recevais leur fichier revu, je l’imprimais, je le testais et je le validais. C’était une manière de travailler très intéressante, ce fut un plaisir de développer ce produit ensemble.
De nombreuses entreprises et leur sous-traitant de fabrication situé de l’autre côté du globe se renvoient les pièces encore et encore, mais cela ralentit de manière insoutenable le réglage des détails finaux.
« Quand j’étais consultant, c’est ce que nous faisions, mais il fallait quatre jours pour que la pièce fasse un aller-retour [en courrier accéléré]. Ces jours sont précieux, donc si vous voulez éviter ce temps perdu, vous utilisez des captures d’écran et des PowerPoints, mais on rencontre vite des problèmes de communication. Le fabricant peut aussi fraiser les pièces entières, mais ce n’est pas facile et le résultat ne répond pas toujours aux attentes. [L’impression 3D] facilite grandement les choses, il vous suffit de créer le fichier exactement tel que vous le voulez. Sans ce fichier d’impression 3D, certains rayons et niveaux de compression sont particulièrement difficiles à communiquer », déclare Kononsky.
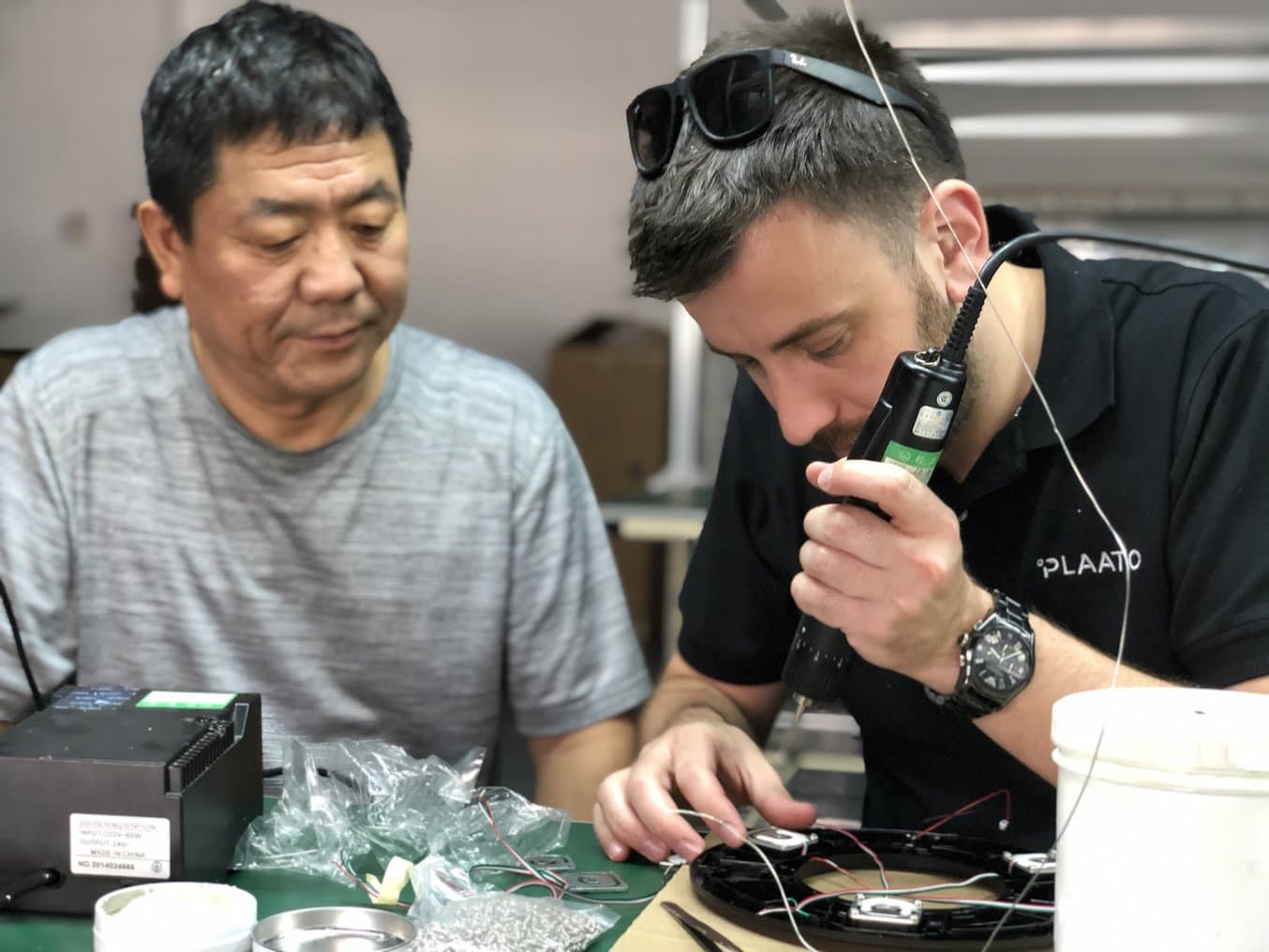
Grâce à l’imprimante 3D présente chez son sous-traitant de fabrication, Plaato a aussi pu imprimer des gabarits et des fixations pour la ligne d’assemblage.
Le fait de disposer d’une imprimante 3D chez le sous-traitant de fabrication a aussi accéléré l’outillage de la ligne de production.
« Nous avons aussi imprimé une grande partie des gabarits pour la ligne d’assemblage, comme des éléments permettant de positionner les composants, de les maintenir en place, de contrôler leur placement, etc. Nous avons imprimé tout cet outillage sur l’imprimante que nous avions emmenée avec nous du bureau de notre fabricant à l’usine quand mon collègue et moi nous sommes rendus sur le site de la ligne de production », explique Kononsky.
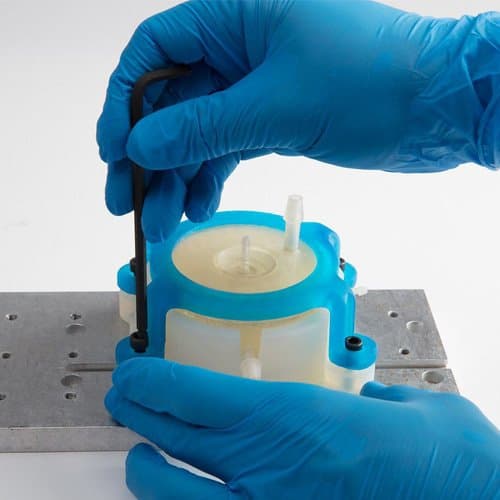
Conception de gabarits et de fixations par impression 3D
Téléchargez notre livre blanc Conception de gabarits et de fixations par impression 3D pour en connaitre les principes de base, les meilleures pratiques et des conseils pour la validation des fixations imprimées.
D’un lancement réussi à de nouvelles applications
En tant que petite entreprise peu encline à tenter un énorme pari financier avant d’entrer sur le marché, Plaato s’est à nouveau tournée vers le financement participatif et a levé plus de 150 000 $ grâce à une campagne sur Kickstarter.
Les précommandes des soutiens ont déjà été honorées et heureusement pour le secteur brassicole amateur, la pandémie de COVID-19 n’a fait qu’encourager davantage de gens à brasser leur propre bière et Plaato a rapidement écoulé le premier lot de son nouveau produit.
En récompense de sa conception novatrice, le Plaato Keg a également reçu des Red Dot Awards dans deux catégories : produit intelligent et design industriel.
Certains utilisateurs ont aussi trouvé des usages créatifs du produit. « Nous avons découvert que beaucoup de clients qui avaient acheté notre fût étaient des bars et toutes sortes de prestataires de services qui placent des fûts et des distributeurs de boisson dans des bureaux. Nous comptons parmi nos clients une entreprise qui possède 150 points de vente de café glacé. Un de ses membres nous a dit : "Eh oui, je gère tout l’inventaire d’ici. Je ne passe pas ma journée au volant à faire la tournée des clients, ni à attendre qu’ils m’appellent quand ils sont à court de café ou de bière à la pression. Je vois tout d’ici, je peux prévoir et organiser ma journée à l’avance." Voilà une très bonne chose car ce genre de service n’existait pas auparavant. Grâce à notre pèse-fût, les prestataires peuvent offrir un meilleur service à leurs clients », conclut Kononsky.
Explorez la dernière imprimante 3D SLA de Formlabs : la Form 3 et notre bibliothèque toujours croissante de résines techniques pour résoudre les difficultés complexes rencontrées dans le développement de produits. Vous êtes curieux de découvrir la qualité des impressions par vous-même ?