Production juste-à-temps de pièces en plastique avec la Form 3
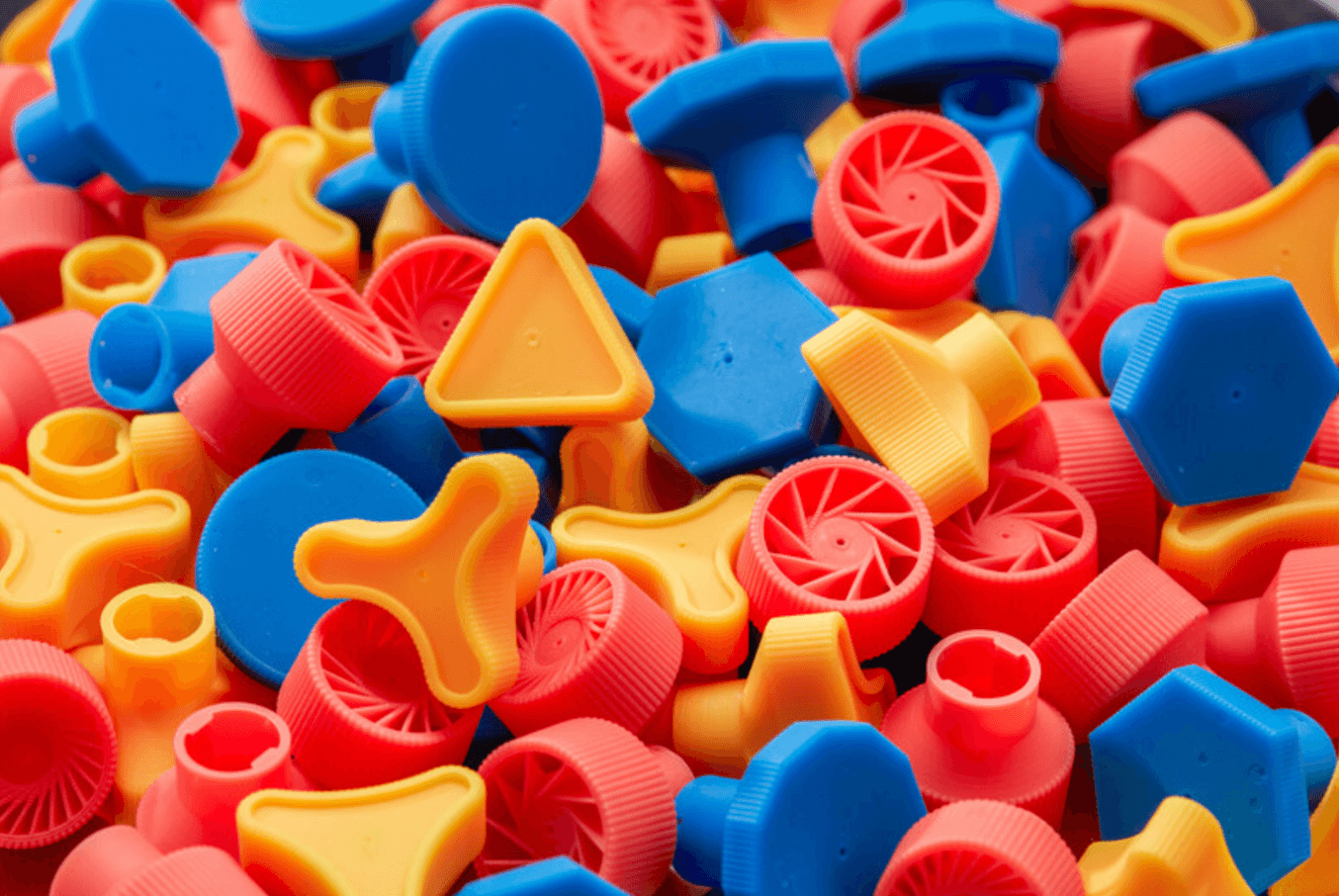
The Digital Factory est une conférence sur les processus de pointe en production industrielle, présentant comment les entreprises utilisent les innovations technologiques récentes pour établir de nouvelles normes d'efficacité et développer de nouvelles pratiques. Ces initiatives high-tech se produisent souvent de façon inaperçue dans les grandes entreprises, au sein des équipes R&D ou de groupes de projets spéciaux. The Digital Factory constitue un moment privilégié pour les professionnels et les responsables, en leur permettant de se rencontrer, de dévoiler et échanger des idées et de voir les projets Industrie 4.0 qui ont réussi dans d'autres domaines.
À l'occasion de la conférence 2019 à Boston, pour montrer aux participants comment ces innovations et ces bonnes pratiques peuvent se combiner, nous avons monté une démonstration interactive sur un processus d'assemblage moderne, associant des technologies développées par Amazon Web Services, Tulip, Vention, RightHand Robotics et, bien sûr, Formlabs.
Les participants étaient invités à configurer et fabriquer un modèle spécial d'un appareil radio uni-station, The Public Radio, élaborée par Spencer Wright et Zach Dunham. Le présent article explique en détail comment nous avons utilisé les propriétés des résines pour l'impression 3D par stéréolithographie (SLA), ainsi que l'évolutivité de l'imprimante Form 3, pour la production de pièces en plastique et leur assemblage juste-à-temps, à l'aide également de postes de travail équipés sur commande de Vention, et de capteurs et de logiciels de Tulip et AWS. Nous décrivons également des éléments DFM (Design for manufacturing) du processus de fabrication de pièces par impression SLA, les étapes de leur conception et leur intérêt pour optimiser le volume de production et réduire le temps de post-traitement.
Le processus de la Pop-up Factory
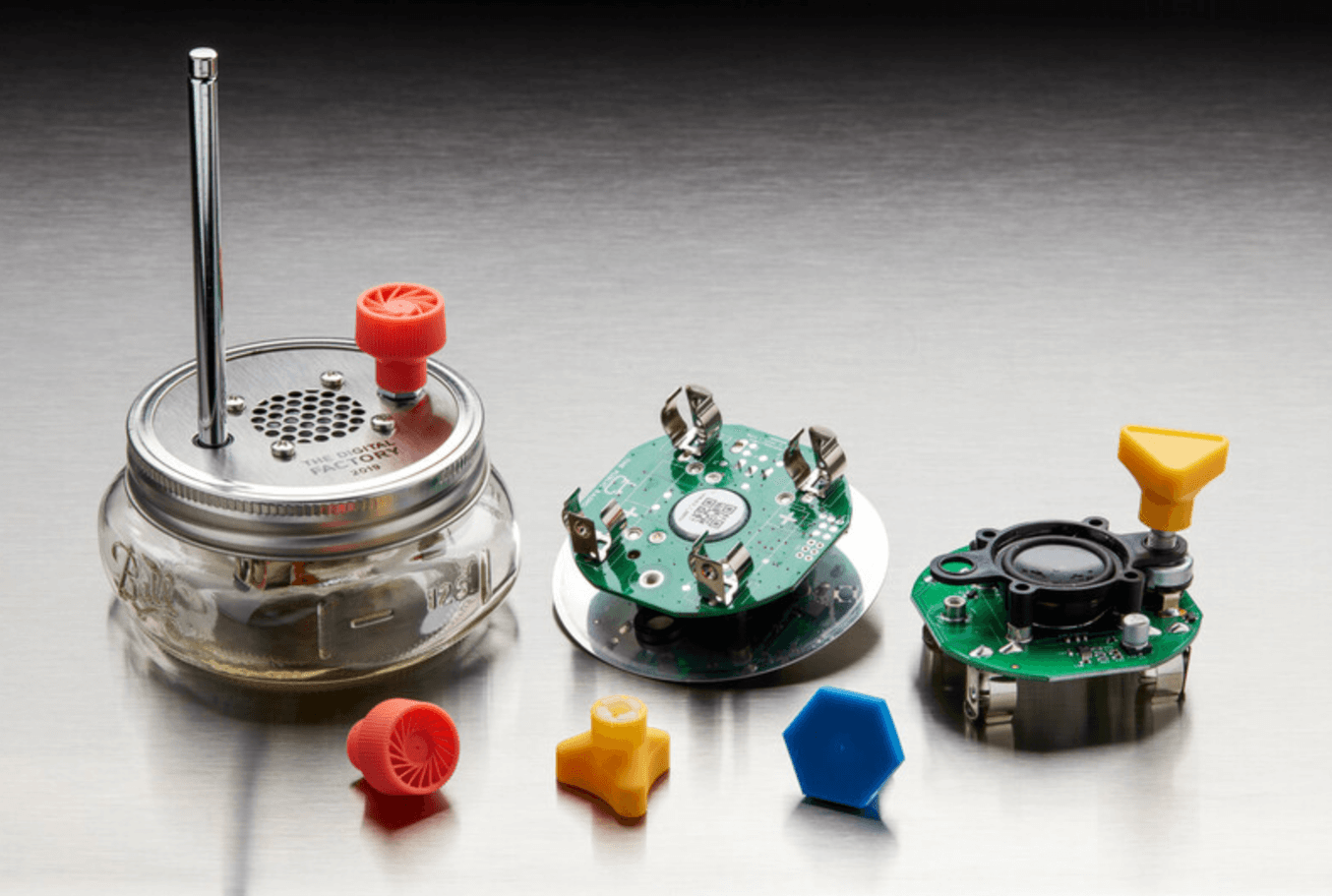
Le processus commence au stand Tulip, où vous choisissez une station radio et le style de bouton que vous souhaitez. Une étiquette est imprimée avec un code QR personnel, qui est alors scanné au niveau des postes de travail Tulip.
Chaque poste de travail dispose d'un stock de composants d'assemblage de boutons imprimés en 3D, de batteries, d'antennes et de sous-ensembles radio, ainsi que d'outils classiques de fabrication, comme un gabarit de programmation, réalisé à l'aide de pièces imprimées en 3D et d'une découpe laser. Le poste de travail affiche les instructions de réalisation de chaque étape. Des capteurs enregistrent vos actions pour assurer que rien ne manque et les variations de stock sont surveillées en temps réel.
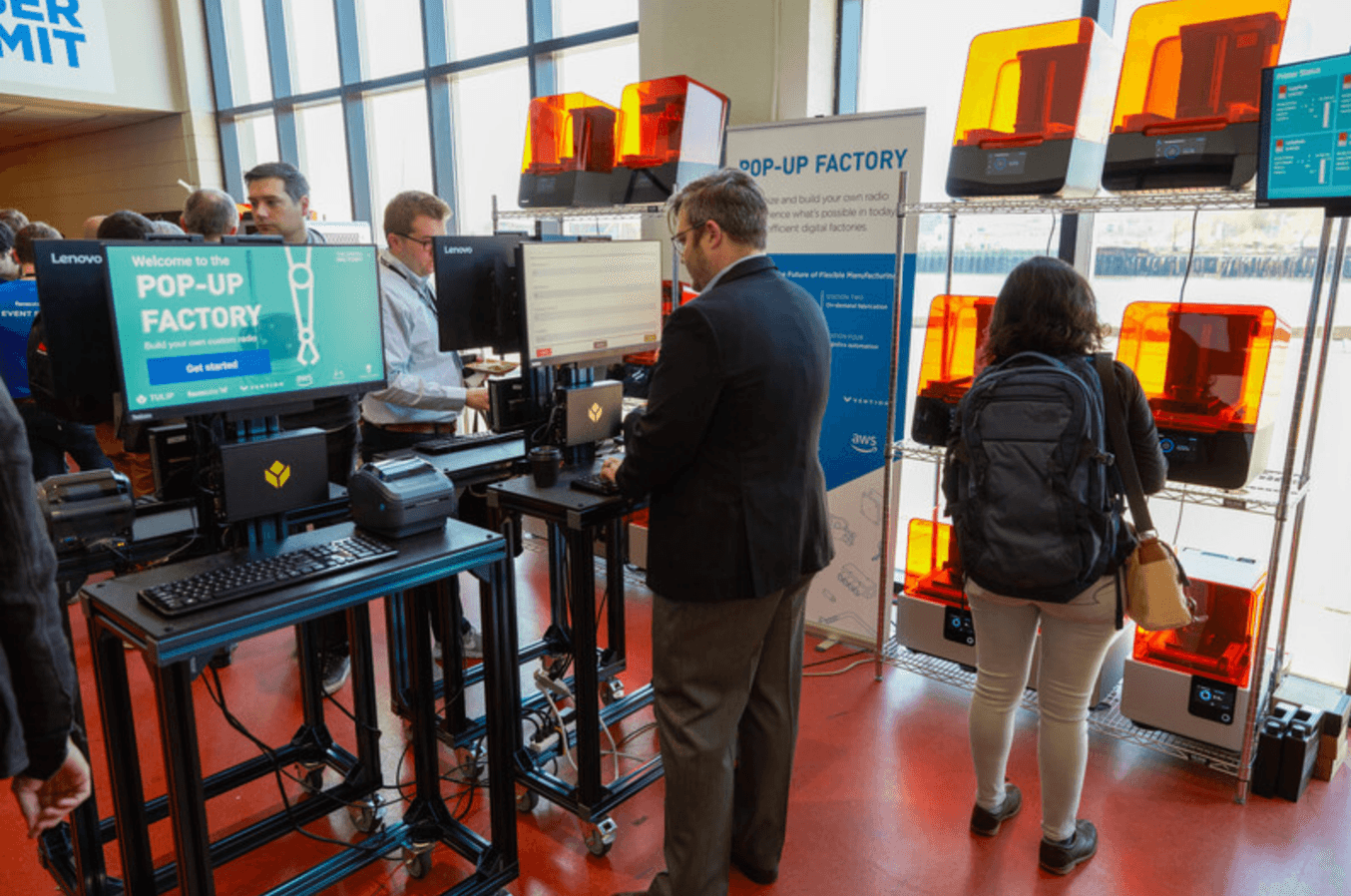
Les participants configurent leurs radios aux stands Tulip et effectuent leur commande. Pendant ce temps, des imprimantes Form 2 et Form 3 tournent pour produire les composants des boutons.
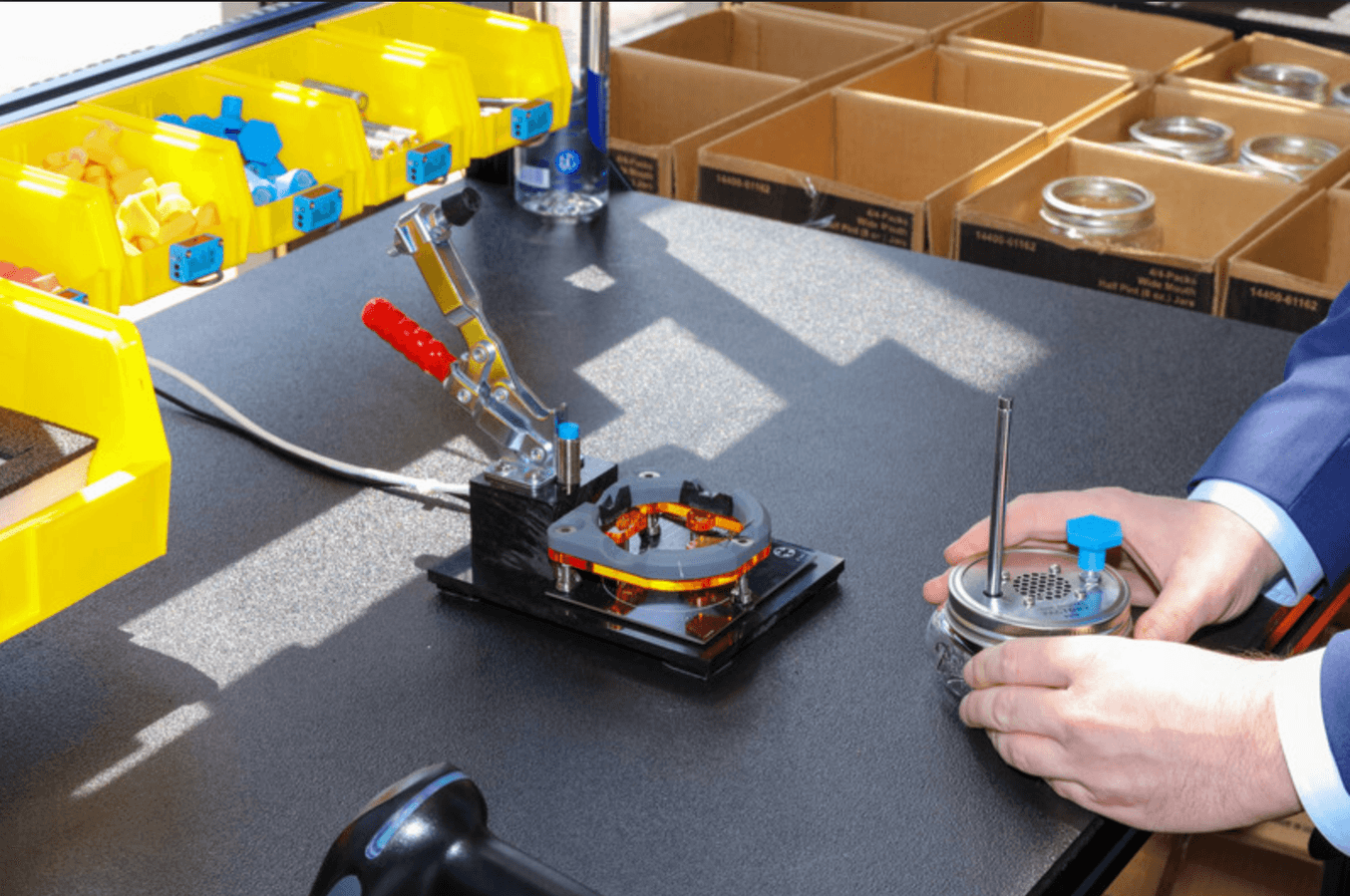
Des participants assemblent et programment leur radio aux postes de travail Vention, équipés du matériel Tulip. Un grand écran affiche les instructions pas-à-pas et des capteurs suivent les stocks, la durée de cycle et d'autres données de fabrication pertinentes.
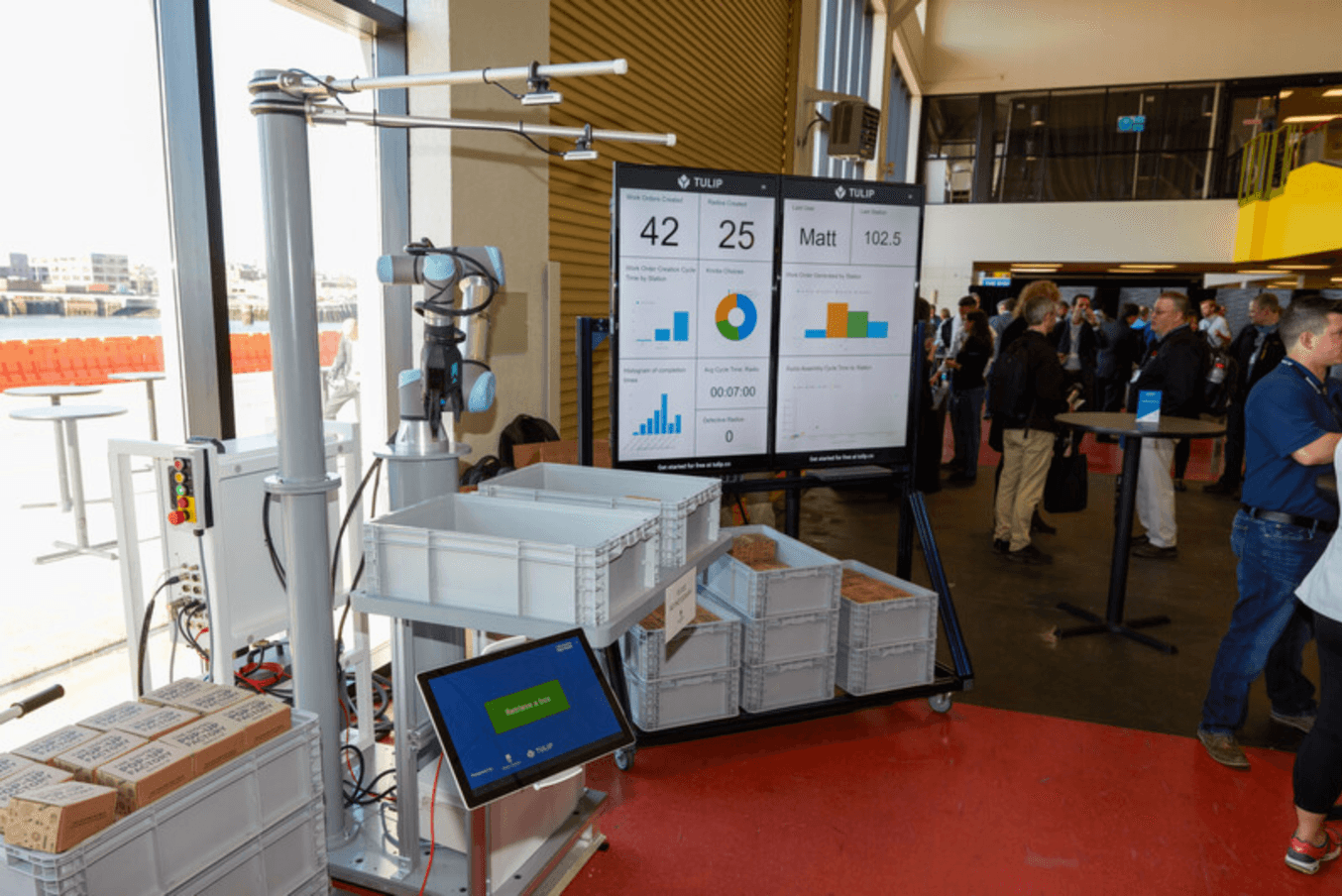
Une pince robotique de RightHand Robotics au-dessus d'une boite en carton.
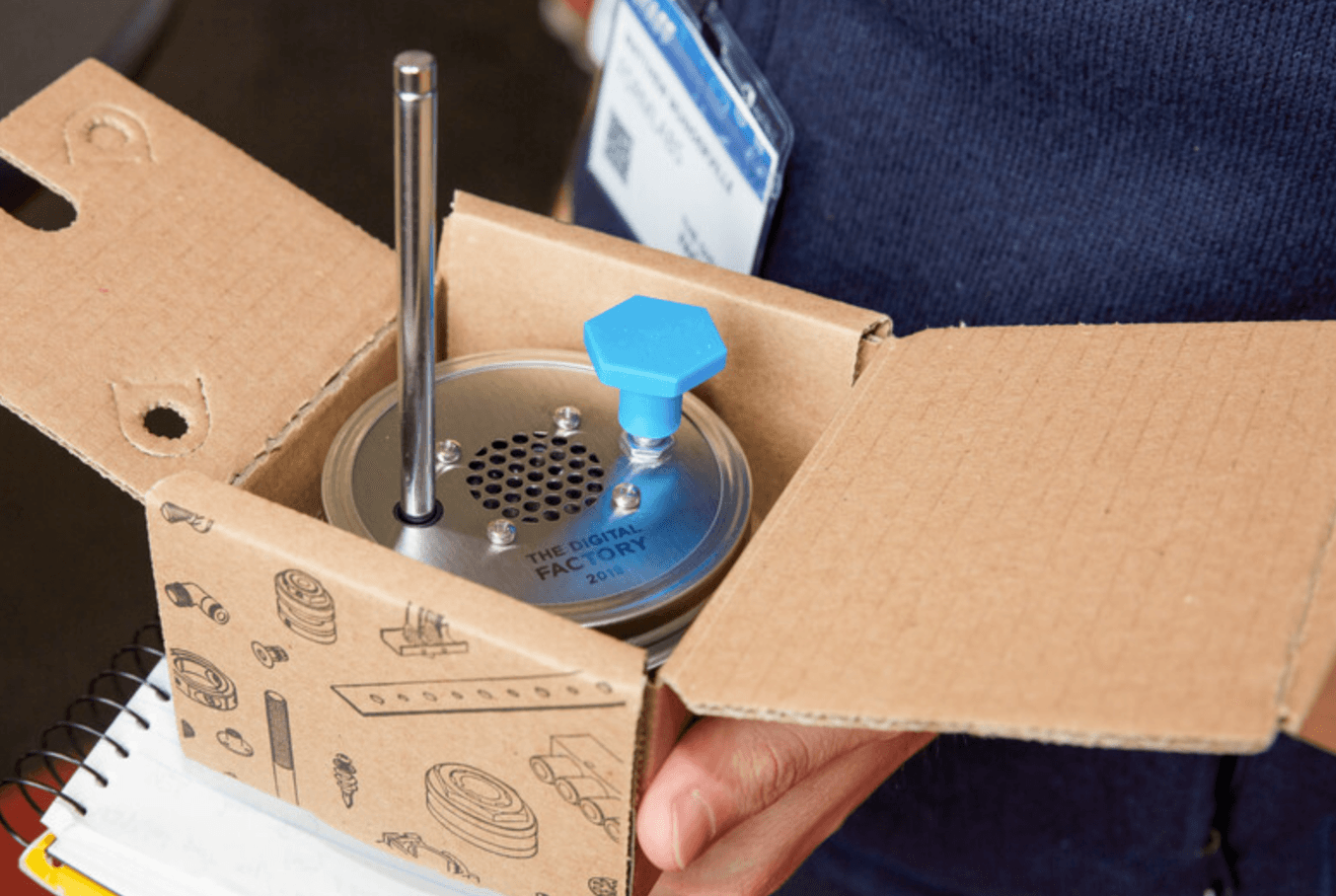
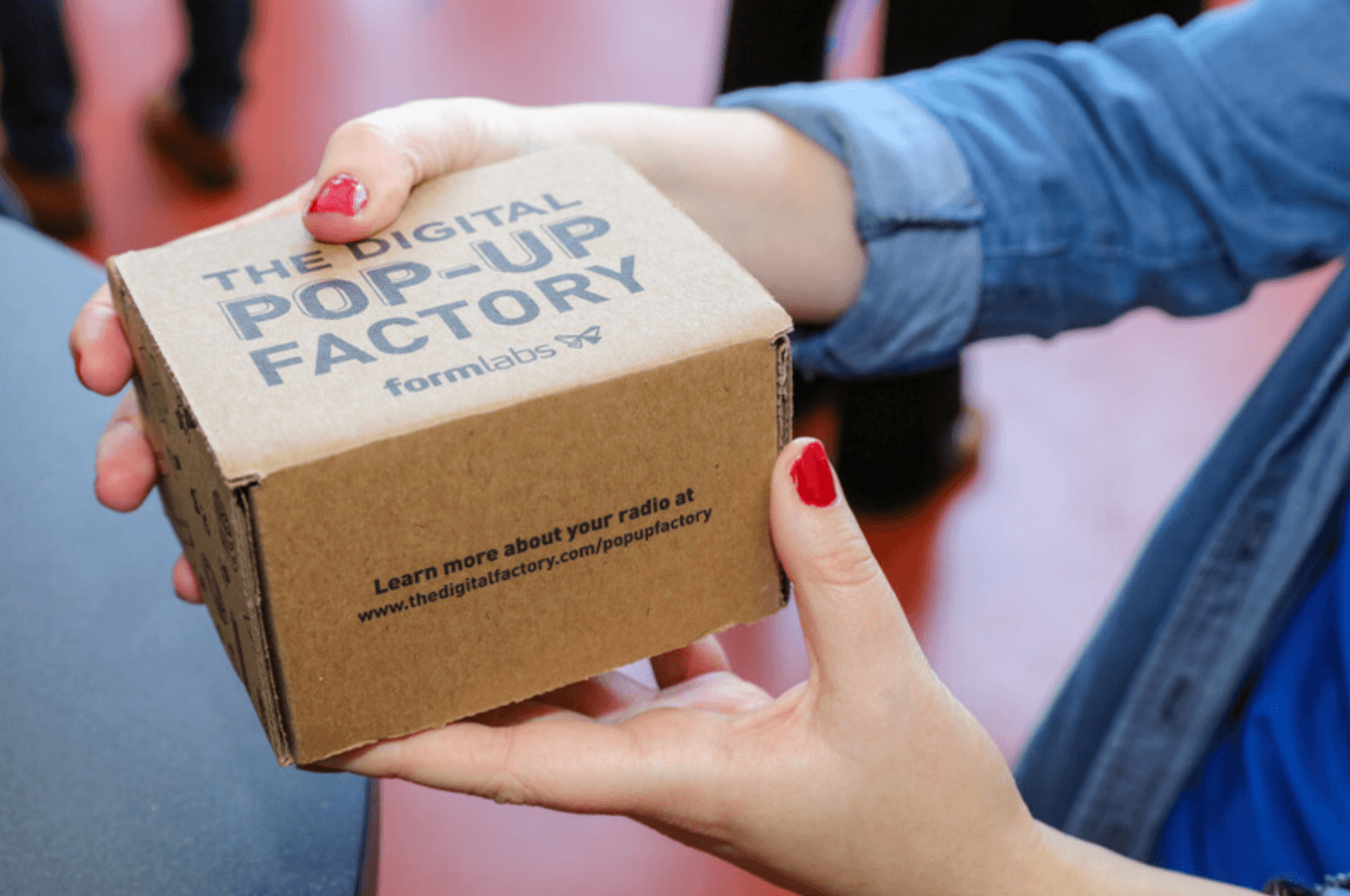
Un poste de radio The Public Radio, fabriqué à The Digital Factory, dans sa boite.
Conception pour la fabrication additive et l'assemblage
Les boutons imprimés en 3D devaient satisfaire certains critères esthétiques et fonctionnels :
-
Nous voulions que les postes The Public Radio soient de couleurs vives et qu'il y ait plusieurs options.
-
Nous voulions démontrer la flexibilité de fabrication sur demande de pièces imprimées en proposant 12 formes complètement différentes. Si vous fabriquiez votre poste radio le matin avec un bouton rouge, son design serait différent de celui fabriqué l'après-midi.
-
Il fallait un bouton qui se fixe bien à l'axe en D de la commande du poste radio.
-
Il fallait que l'assemblage du bouton puisse se faire avec une pression manuelle standard pour ne pas ralentir le processus d'assemblage ou nécessiter un outil supplémentaire.
Pour que tous ces critères soient satisfaits, nous avons utilisé deux résines : notre Color Kit, pour nous permettre de proposer un grand choix de couleurs, et Durable Resin, un matériau technique très résistant aux chocs et présentant un bon allongement.
L'allongement était nécessaire pour que les cannelures internes de la pièce s'agrippent bien à l'axe en D de la commande, mais qu'elles s'effacent pendant l'installation sans requérir une pression plus forte.
L'insert en Durable Resin devait aussi retenir l'extérieur en Color Kit pour l'empêcher de tourner librement.
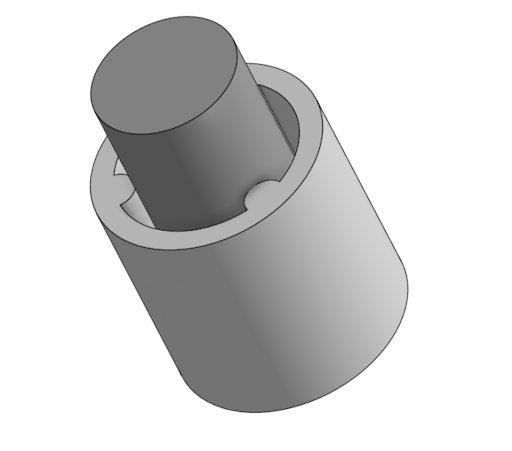
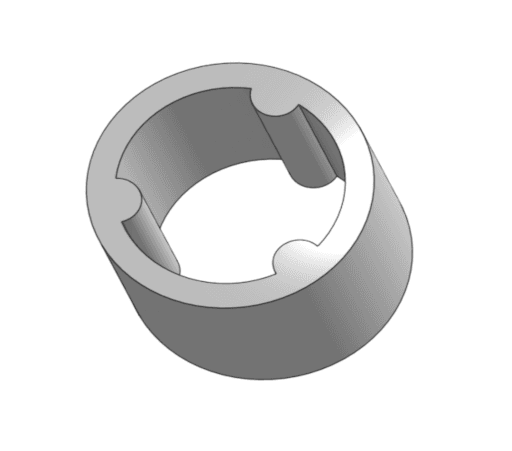
Exemple de forme de cannelures internes d'écrasement typiquement utilisées pour des pièces en plastique.
Passer en production
Après validation fonctionnelle des pièces, nous avons réalisé quelques petits ajustements pour leur production. Toutes les pièces de l'assemblage du bouton devaient être imprimables sans supports, être faciles à retirer de la plateforme de fabrication et être arrangées ensemble sur la plateforme de façon à minimiser le nombre d'impressions. Le bouton ayant globalement la forme d'un tube fermé, nous avons rajouté de minuscules évents pour éviter le phénomène d'aspiration.
Pour la même raison et pour faciliter également le retrait des pièces, l'insert en Durable Resin a été entaillé à la base.
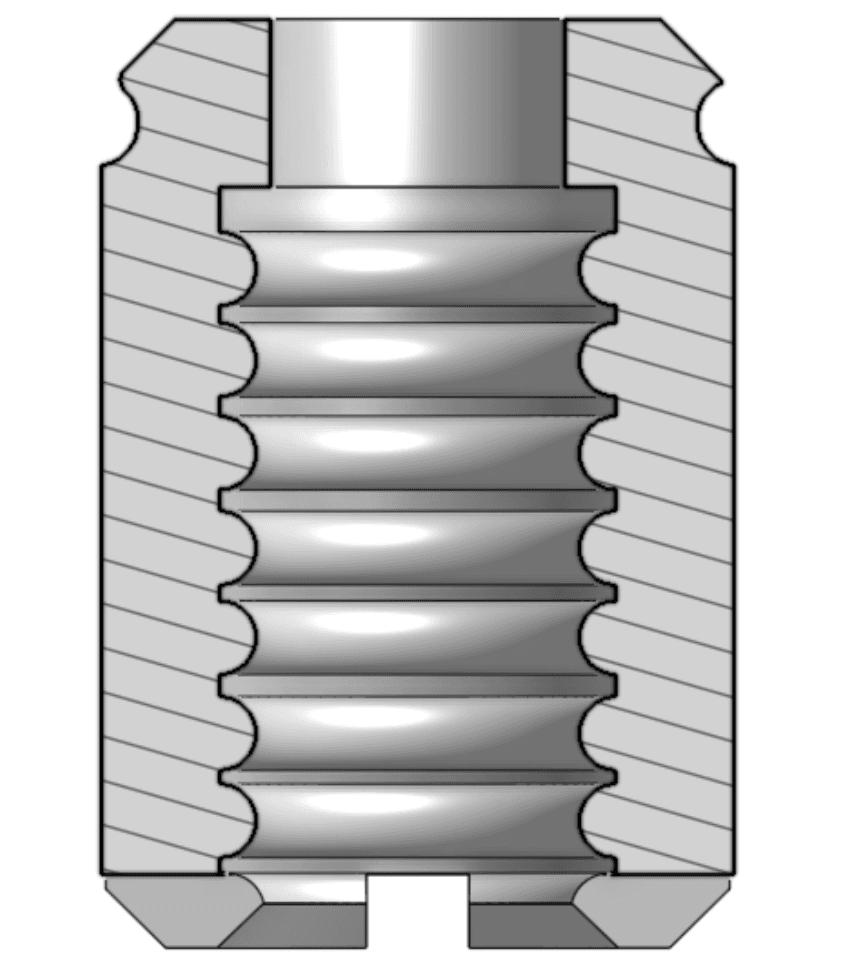
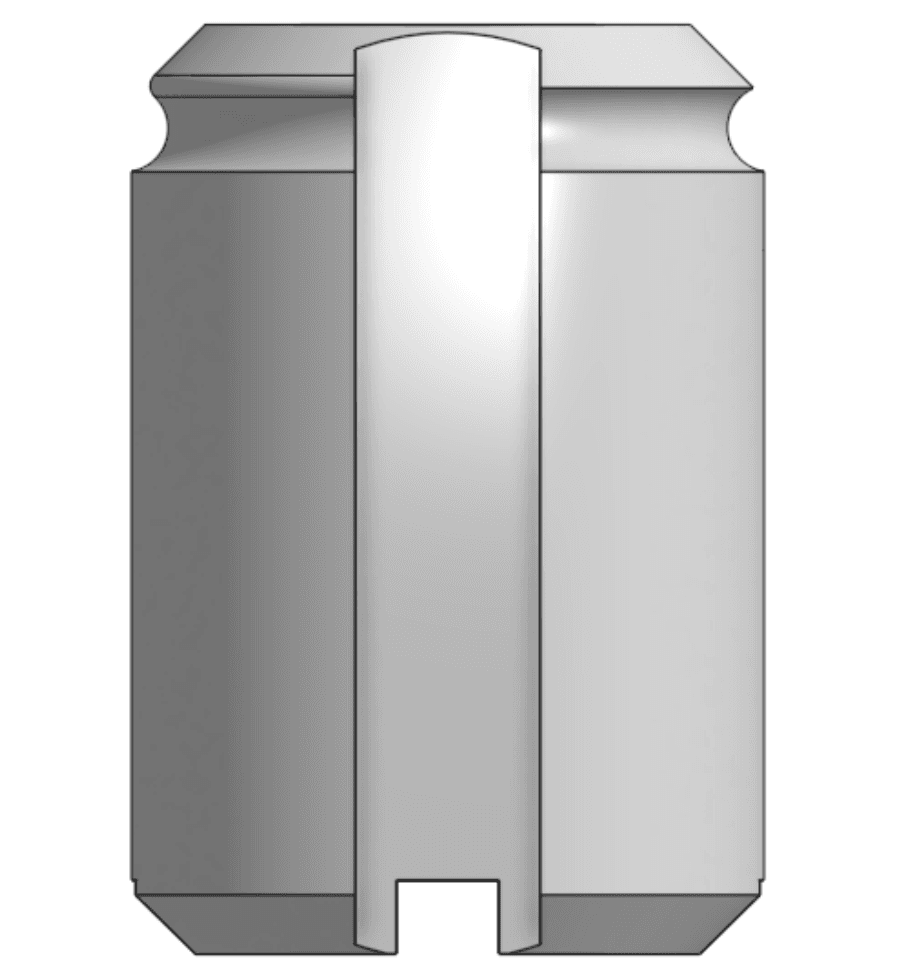
Les éléments DFM et DFA de l'insert en Durable Resin : entaille et chanfrein de la base pour aider le retrait de la pièce, anneau supérieur pour assemblage par encliquetage, et des rainures pour fixer le bouton et empêcher sa rotation.
Les inserts en Durable Resin ont pu être disposés suffisamment densément sur la plateforme pour obtenir 81 pièces par impression. Quant aux pièces en Color Kit, il a été possible d'en imprimer 30 à 40 ensemble, du fait de leur encombrement plus important en moyenne.
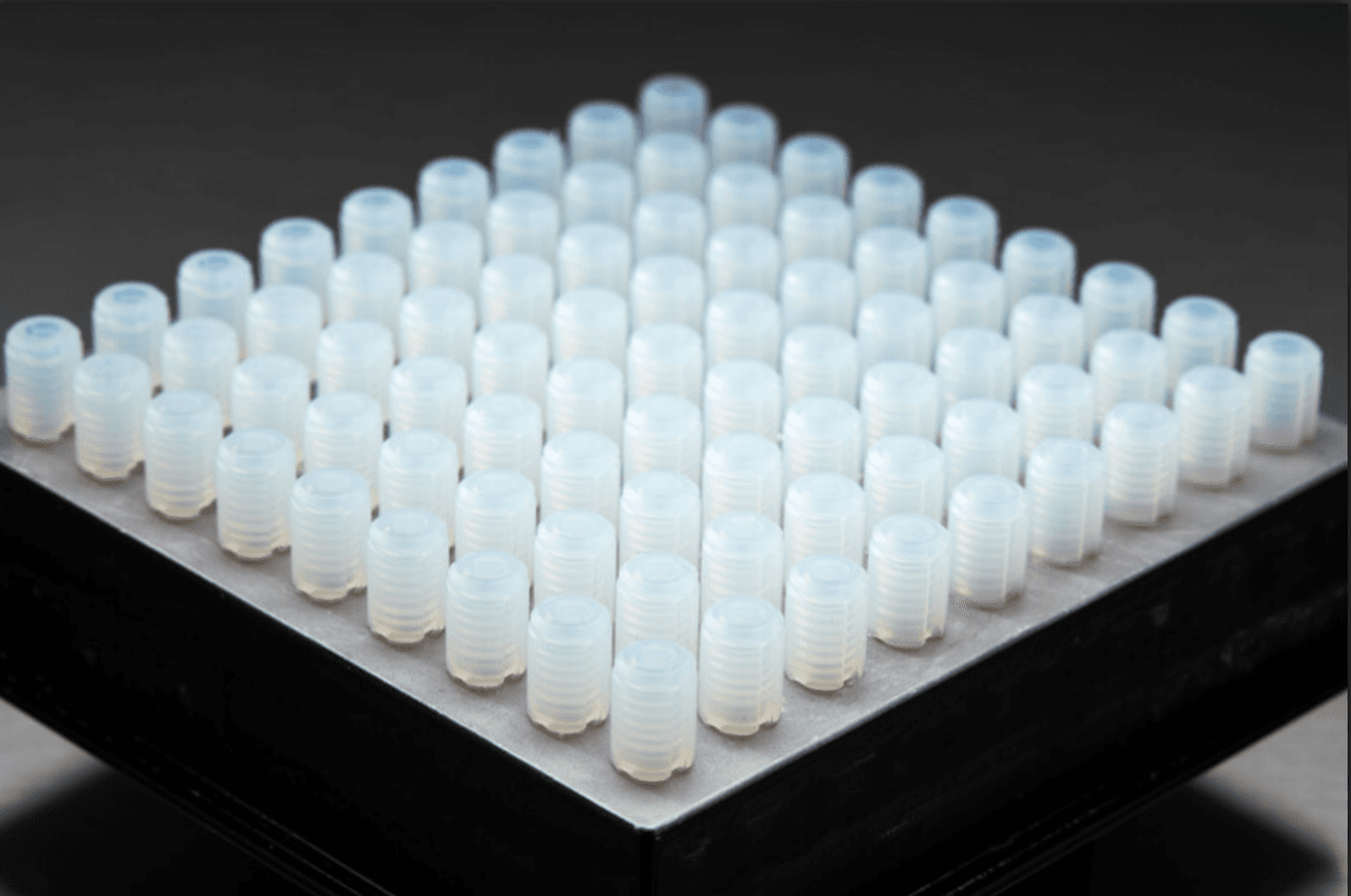
Arrangement des inserts en Durable Resin sur la plateforme de fabrication.
600 kits radio étant prêts pour l'assemblage, nous souhaitions disposer d'un stock d'au moins 400 boutons de chaque couleur possible. En plus des 400 boutons de chaque couleur, rouge, bleu et jaune, nous avions aussi besoin d'un insert en Durable Resin par bouton, ce qui donnait un total de 2 400 pièces à imprimer pour les deux jours de démonstration.
Il fallait donc 55 impressions pour réaliser les 2400 pièces nécessaires aux 1200 boutons assemblés. Nous avons réparti cette charge de travail entre les imprimantes en interne et celles en démonstration sur site, de façon à commencer avec des ensembles de boutons en stock et sur les postes de travail dès la première matinée de la conférence.
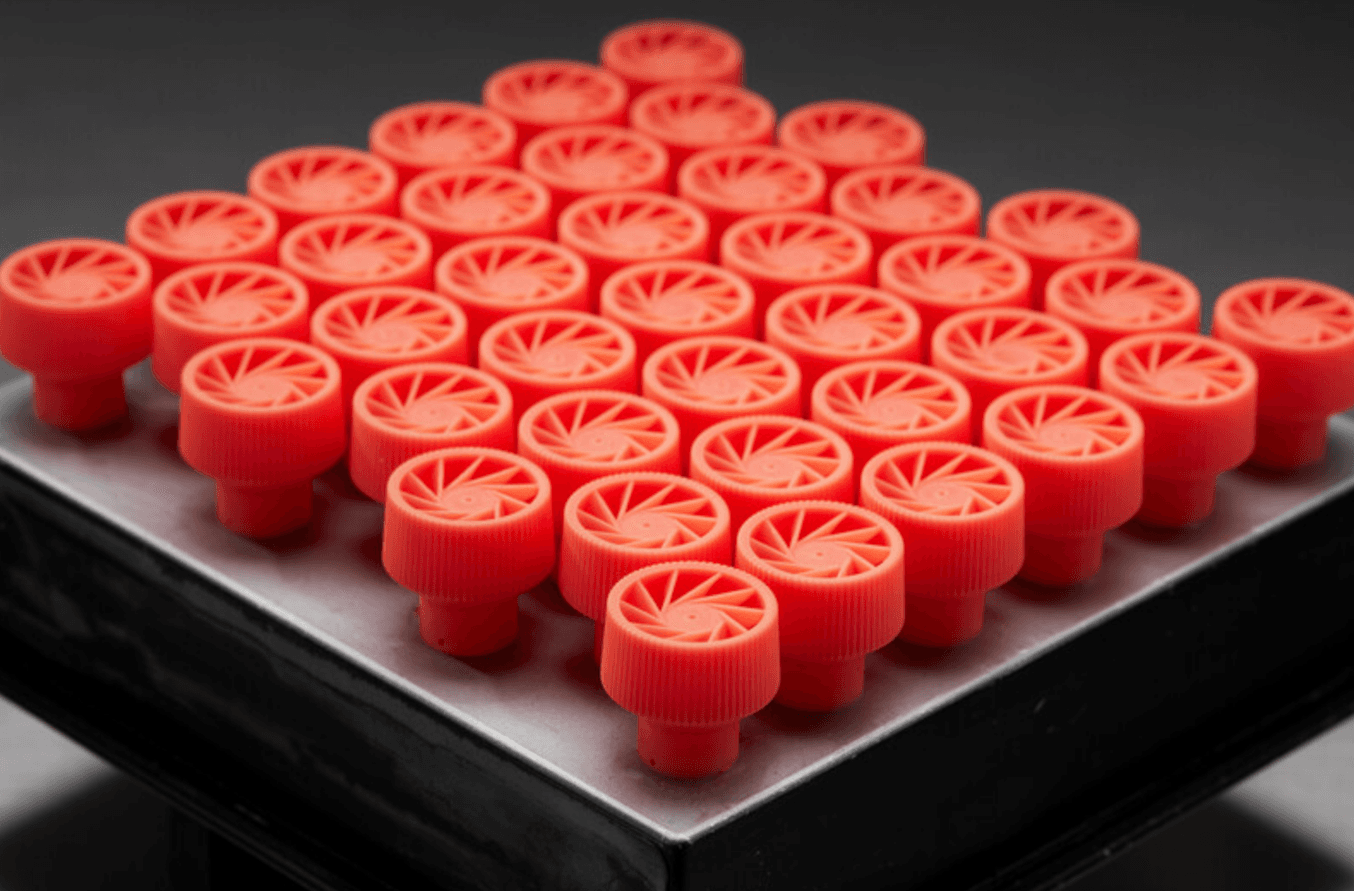
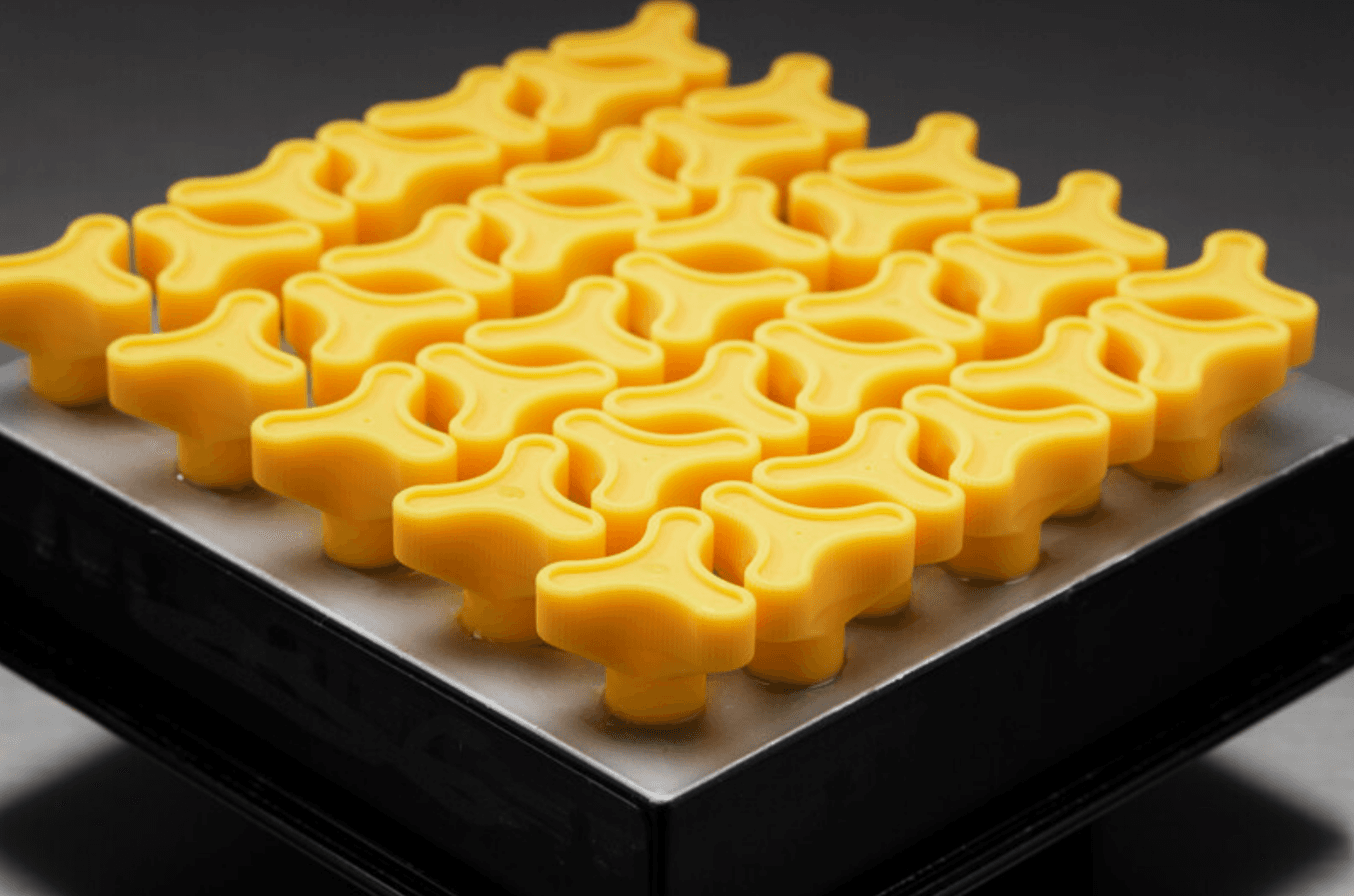
Mise en place des processus de travail à partir des caractéristiques de la demande
Les informations relatives à la demande du produit, comme la préférence de couleur, étant enregistrées en temps réel et les outils de fabrication des pièces étant sur site, il était possible d'intégrer étroitement l'offre et la demande afin de réduire les dépassements de stock et les pertes. La difficulté à prédire la demande de couleurs est bien connue et de nombreuses entreprises consacrent beaucoup de ressources à élaborer des outils et des méthodes pour améliorer la précision de leurs prévisions.
Pendant les deux jours qu'a duré la Pop-Up Factory, la couleur Sonic Red était de loin la préférée, environ deux fois plus que les couleur Blue ou Mellow Yellow. À l'occasion d'autres événements ponctuels comme celui-ci, nous pourrions modifier la programmation de la production pour en tenir compte. Afin de mieux comprendre le comportement du client, nous pourrions aussi essayer une autre méthode, par exemple, garder la même forme de bouton pour les trois couleurs.
De nos jours, les fabricants sont soumis à une pression extrêmement forte tant au niveau de leur flexibilité que de leur efficacité. La Pop-Up Factory a démontré que des technologies de fabrication à l'aide de capteurs et de logiciels se combinent parfaitement à des procédés flexibles de fabrication telle que l'impression 3D.
Pour en savoir plus sur la façon dont les fabricants exploitent aujourd'hui l'impression 3D pour innover, consultez nos études de cas relatives à l'utilisation des imprimantes 3D et les résines Formlabs par Google, New Balance et Ashley Furniture pour repenser leur processus de fabrication.
En savoir plus sur l'impression 3D en production industrielle