L'impression 3D SLA et SLS permet de contrôler l'utilisation de l'eau en période de sécheresse

Les effets du changement climatique se font sentir dans le monde entier, et l'impression 3D aide les sociétés à évoluer pour relever le défi. Alors que les réglementations relatives à la consommation d'eau et d'électricité sont mises à jour en réponse aux sécheresses prolongées, aux incendies de forêt plus fréquents et à l'augmentation du smog, les particuliers, les entreprises et les municipalités s'efforcent de communiquer des données exactes et d'améliorer leur consommation d'eau. Comme le dit l'adage, si vous ne pouvez pas mesurer quelque chose, vous ne pouvez pas le changer. C'est là qu'interviennent les compteurs suivants.
Next Meters est un fabricant de compteurs d'eau connectés dont la mission est d'éduquer et de récompenser les personnes qui économisent l'eau. Ils créent des débitmètres à semi-conducteurs qui mesurent la consommation d'eau des clients résidentiels, commerciaux ou municipaux. Leur défi consiste à créer des équipements qui peuvent se fixer sur la grande variété de compteurs actuellement utilisés. En utilisant plusieurs imprimantes Form 2, Form 3+, Form 3L, et Fuse 1, Next Meters a été en mesure de créer rapidement des prototypes, d'améliorer les conceptions de moulage et de produire des pièces finales pour son équipement.
Nous nous sommes entretenus avec David Clyde, CMO de Next Meters, sur le marché des compteurs d'eau et sur les raisons pour lesquelles l'impression 3D est le complément idéal de leur procédé de fabrication traditionnel.
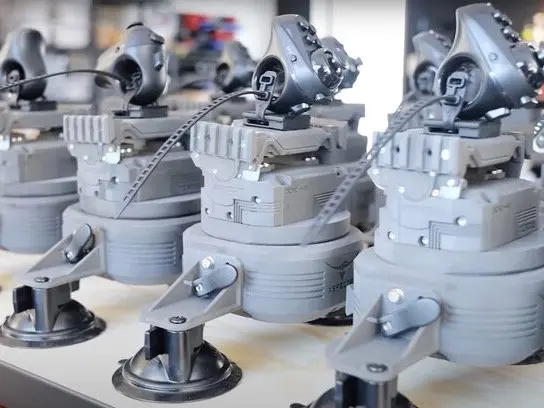
Test de résistance de pièces imprimées en 3D pour les applications finales
Ce livre blanc présente le matériel d'impression 3D et les solutions matérielles de Formlabs pour produire des pièces d'utilisation finale. Il documente les études de cas de divers utilisateurs et inclut les résultats de tests de résistance pour prouver l'adéquation des matériaux d'impression 3D aux applications finales.
Récompenser ceux qui économisent l'eau
Historiquement, les compteurs d'eau sont mécaniques et s'appuient sur le débit de l'eau pour faire tourner des engrenages à l'intérieur d'un tube et calculer la consommation à partir de ce débit. Cela pose plusieurs problèmes : les immeubles à plusieurs logements n'ont généralement qu'un seul compteur municipal, et la consommation est répartie de manière égale entre toutes les unités. Cela pénalise ceux qui économisent et récompense ceux qui gaspillent. En outre, les compteurs mécaniques sont moins précis et se dégradent avec le temps, ce qui crée des écarts importants entre la consommation enregistrée et la consommation réelle.
Next Meters conçoit et fabrique des compteurs d'eau extrêmement précis et entièrement connectés, tels que des débitmètres à ultrasons, des capteurs de détection de fuites et des vannes d'arrêt à distance. Cet équipement permet de détecter les moindres pertes d'eau dues à des problèmes tels que des tuyaux fissurés ou des joints non étanches. En particulier dans les systèmes de distribution d'eau des grandes villes ou des immeubles d'habitation, ces petites fuites peuvent conduire sur le long terme à des pertes massives, ce qui coûte de l'argent aux habitants et entraîne le gaspillage de précieuses ressources en eau.

Un spécialiste de Next Meters examine un système qui sera bientôt ajusté avec un dispositif de compteur d'eau imprimé sur l'imprimante SLS Fuse 1.
« Beaucoup de choses stimulent la demande pour nos produits. Il y a de nouveaux mandats d'État : la Californie fait avancer la législation dans ce domaine. La sécheresse qui sévit depuis de nombreuses années fait des ravages dans de nombreuses régions. Les États placent des lois qui exigent le suivi à des fins de conservation, et les gens veulent généralement être mieux informés sur leur utilisation des services publics. »
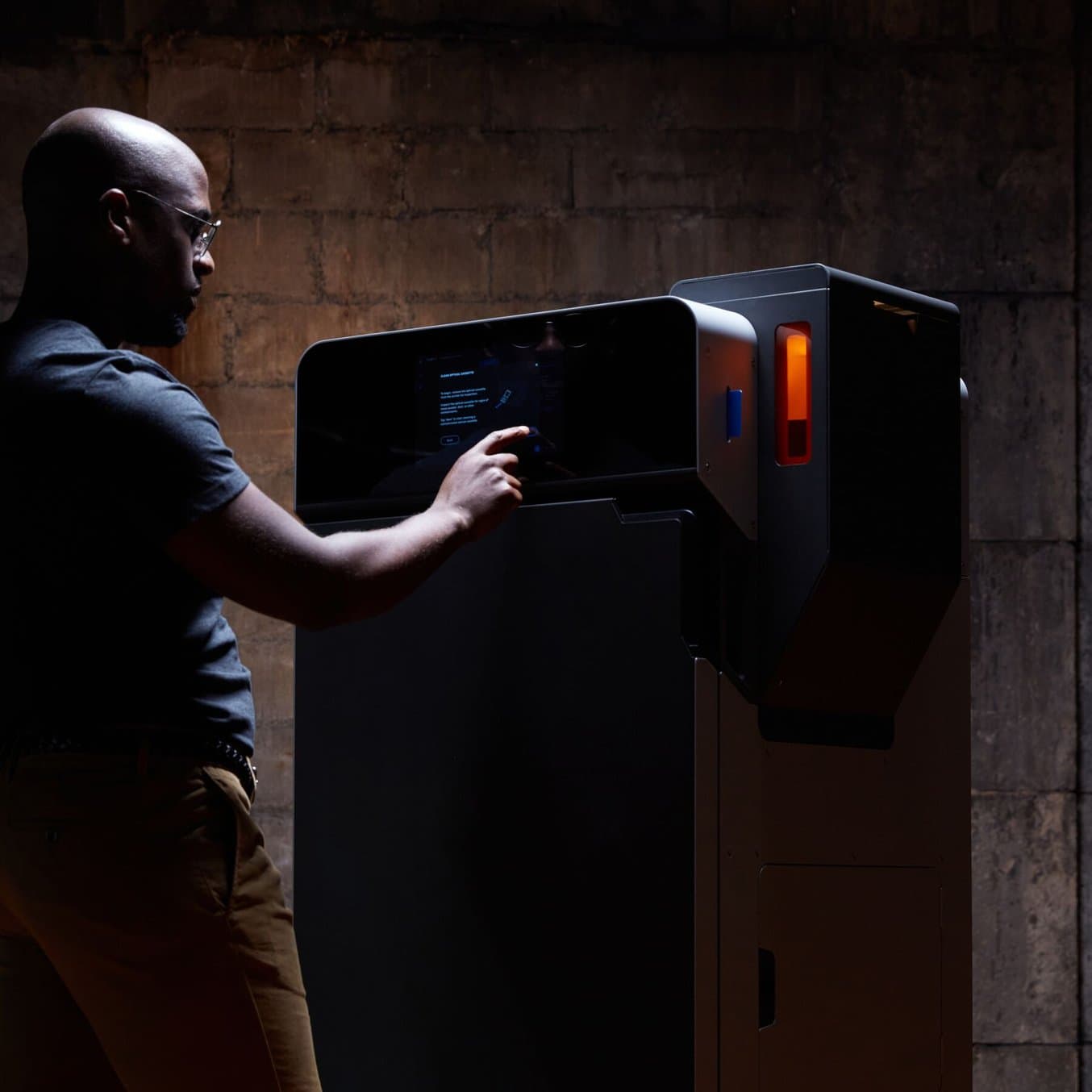
Externalisation ou internalisation : quand est-il judicieux d'adopter l'impression 3D SLS en interne ?
Dans ce livre blanc, nous passons en revue les avantages de l'adoption en interne des imprimantes 3D à frittage sélectif par laser (SLS) par rapport à la sous-traitance des pièces SLS auprès de fournisseurs de services.
Une dimension unique ne convient pas à tous : les compteurs des 50 dernières années doivent être personnalisés
Le récent pic de la demande exacerbe le défi auquel Next Meters est déjà confrontée : elle doit fournir un équipement de mesure du débit qui peut être supporté par une grande variété de types de compteurs d'eau, chacun ayant une date d'installation et un fabricant différents. Pour réussir à fournir une solution, qu'elle soit publique ou privée, l'équipe de M. Clyde doit identifier le compteur d'eau auquel elle a affaire, puis déterminer lequel de ses propres produits conviendra, ou créer et fabriquer un nouveau compteur. Au fur et à mesure que l'entreprise passait d'un marché exclusivement résidentiel à un marché municipal, le nombre de compteurs qu'elle devait faire correspondre augmentait, ce qui compliquait encore la tâche.
« En entrant sur le marché municipal, nous constatons que de nombreuses villes mélangent plusieurs marques ainsi que l'âge des compteurs. Même dans une petite ville de 3000 foyers, on pouvait voir six ou sept types de compteurs différents. Chaque type de compteur a une forme et des dimensions différentes qui nécessitent un bracket unique pour l'adapter à nos appareils IoT », explique M. Clyde.
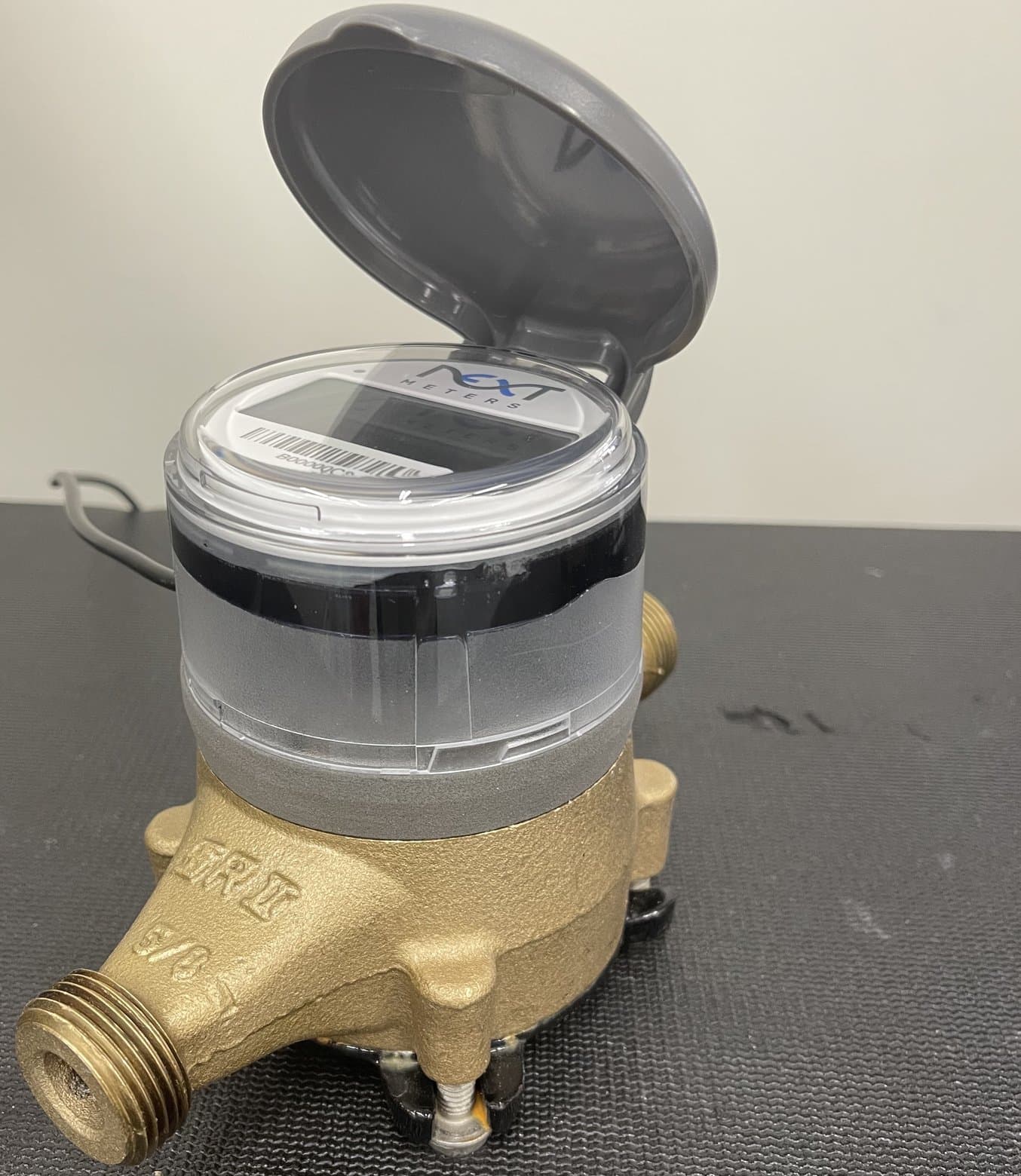
Un compteur d'eau (boîtier transparent) ajusté à un robinet de système d'eau unique (plaqué or) via une fixation SLS Fuse 1 personnalisée (pièce centrale grise).
Une sculpture lente, des outils coûteux
Pour créer leurs produits, les ingénieurs de Next Meters ont toujours démarré par des modèles en argile pour concevoir l'aspect général de leurs appareils. Une fois que la conception leur semblait correcte, ils passaient à la modélisation 3D en CAO, puis envoyaient le tout à une entreprise de moulage pour obtenir un prototype du moule.
« Nos ingénieurs en mécanique étaient littéralement des sculpteurs. Nous sculptons, nous entrons le modèle dans notre logiciel CAO, nous l'envoyons à une société d'approvisionnement, nous nous procurons l'outillage nécessaire, puis nous itérons, tout cela avant même d'avoir testé nos prototypes. Cela prenait du temps et c'était coûteux », a déclaré M. Clyde.
Une solution consistait à prendre les outils existants et à les modifier pour les adapter à un nouveau produit présentant de très légères différences, mais l'équipe de Next Meter s'est heurtée à un obstacle sur ce point également. Chaque fois qu'ils modifiaient un outil, celui-ci s'affaiblissait et, après avoir été modifié plusieurs fois, il fallait le mettre au rebut, alors que le coût de fabrication variait de 5000 à 50 000 dollars et que le remplacement pouvait prendre plusieurs mois.
Non seulement les outils se comptaient par centaines, mais leur fabrication nécessitait une main-d'œuvre abondante et coûteuse. Les historiques de livraison de solutions complètes ont été repoussés et la société a dû faire face à des coûts considérables. Next Meters s'est tourné vers l'impression 3D pour accélérer son processus d'itération, en commençant par une imprimante Form 2, puis en ajoutant une Form 3, une Form 3+ et une Form 3L. Ils utilisent les imprimantes SLA de Formlabs pour concevoir une preuve de concept pour les moules, et itèrent rapidement, faisant passer leur processus de conception de plusieurs mois à quelques jours.
La commande numérique contrôlée par ordinateur prendrait, dans le meilleur des cas, cinq à six semaines. Il nous a parfois fallu un an pour passer de la conception d'une preuve de concept au premier prototype. Un an et plusieurs centaines de milliers de dollars. L'impression 3D nous permet de faire ces choix de conception rapidement et de n'envoyer l'outil fini qu'après avoir validé chaque pièce.
David Clyde
Le moulage par injection pour les grandes séries, le SLS pour les petites séries
Environ 80 % des systèmes d'utilité publique sur le terrain appartiennent à quelques grands acteurs. L'équipement de ces derniers peut être moulé par injection de manière efficace. Mais qu'en est-il des 20 % de clients restants, représentés par plus d'une douzaine de petits fabricants supplémentaires ? Next Meters doit encore fournir une solution globale à ses clients. Si une ville doit mettre à jour son système de compteurs et extraire des données d'utilisation pour se conformer à de nouvelles réglementations, il faut que tout soit couvert, et pas seulement ce qui est pratique, sinon l'ensemble des données est inutile.
« Il n'est pas logique qu'une ville ne puisse lire que 80 % des compteurs. Nous devons nous occuper des cas isolés, afin d'offrir aux clients une solution globale et non partielle », explique M. Clyde.
En s'attaquant aux derniers 20 % du marché, Next Meters s'est heurté à un autre problème. Bien que les imprimantes SLA aient accéléré la conception des moules et le processus d'itération, le coût du moulage par injection reste prohibitif en raison des faibles quantités de production nécessaires pour chaque pièce. Bien que Next Meters ait utilisé la gamme de résines Formlabs disponibles sur son parc d'imprimantes SLA, les résines imprimées en 3D ne pouvaient pas être utilisées pour des pièces de production ayant une durée de vie moyenne de 15 ans. Next Meters avait besoin d'une solution rentable pour produire des pièces de production en petites quantités.
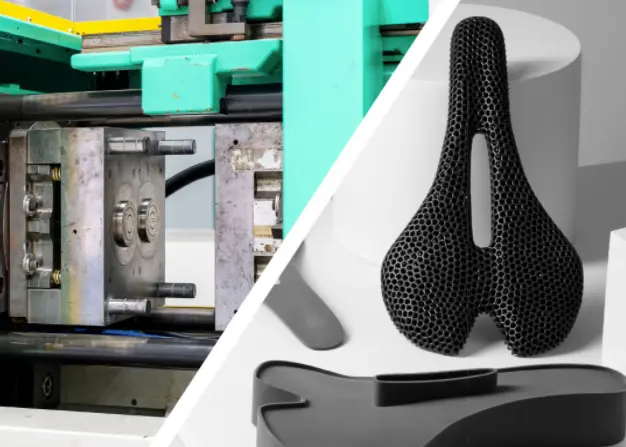
Impression 3D SLS vs. moulage par injection : quand remplacer les pièces moulées par l'impression 3D ?
Ce livre blanc présente la dynamique des coûts pour des cas d'utilisation réels, et vous montre comment utiliser l'impression 3D SLS, le moulage par injection, ou les deux ensemble.
Fin 2021, l'équipe de M. Clyde a acheté une imprimante 3D à frittage sélectif par laser (SLS) Fuse 1, une unité de post-traitement Fuse Sift, et ont ajouté Nylon 12 Powder puis plus tard Nylon 11 Powder à leur gamme de matériaux. Ils utilisent Nylon 12 Powder pour le prototypage des bracket qui maintiennent le compteur, et Nylon 11 Powder pour les pièces sur le terrain.
« Il existe des dizaines de modèles de compteurs dont les quantités sont si faibles que nous ne pourrions jamais amortir les coûts d'outillage. Pour ces compteurs spécifiques, nous imprimons donc les pièces sur la Fuse 1 selon la demande. Nous pouvons désormais fournir des équipements aussi bien pour les compteurs courants que pour les 20 % restants, et nous pouvons le faire beaucoup plus rapidement et à moindre coût grâce à l'imprimante SLS », explique M. Clyde.
Turbulences à venir : l'impression 3D sans supports résout les problèmes de débit
La Fuse 1 offre un autre avantage : son lit d'impressionest autoporté. Pour les pièces dans le compteur d'eau à ultrasons lui-même, le frottement est le grand ennemi : l'eau doit circuler dans le compteur sans entrave afin de permettre une lecture précise. Pour les pièces compliquées, Next Meters utilise la Fuse 1 afin que la pièce puisse être produite avec des caractéristiques internes sans supports.
L'outillage d'un moule pour une pièce aussi compliquée prendrait des mois et le paramétrage de la fabrication des centaines de milliers de dollars, mais grâce à ses capacités de SLS en interne, Next Meters est en mesure de produire un dispositif fonctionnel en quelques jours seulement.
« Pour les impressions plus complexes, nous les imprimons sur la Fuse 1, nous les récupérons avec la Fuse Sift, puis nous les sablons. Il est possible d'obtenir de meilleurs détails lorsqu'il n'est pas nécessaire de tenir compte des supports, et les pièces peuvent glisser et interagir correctement en tant qu'assemblages fonctionnels. Dans l'exemple d'un compteur d'eau, avec un tube de débit de sept pouces, nous ne pouvons pas nettoyer les supports de ce compteur. Les chocs provoqués par les supports affecteraient le débit de l'eau, créant des turbulences et faussant la lecture », explique M. Clyde.
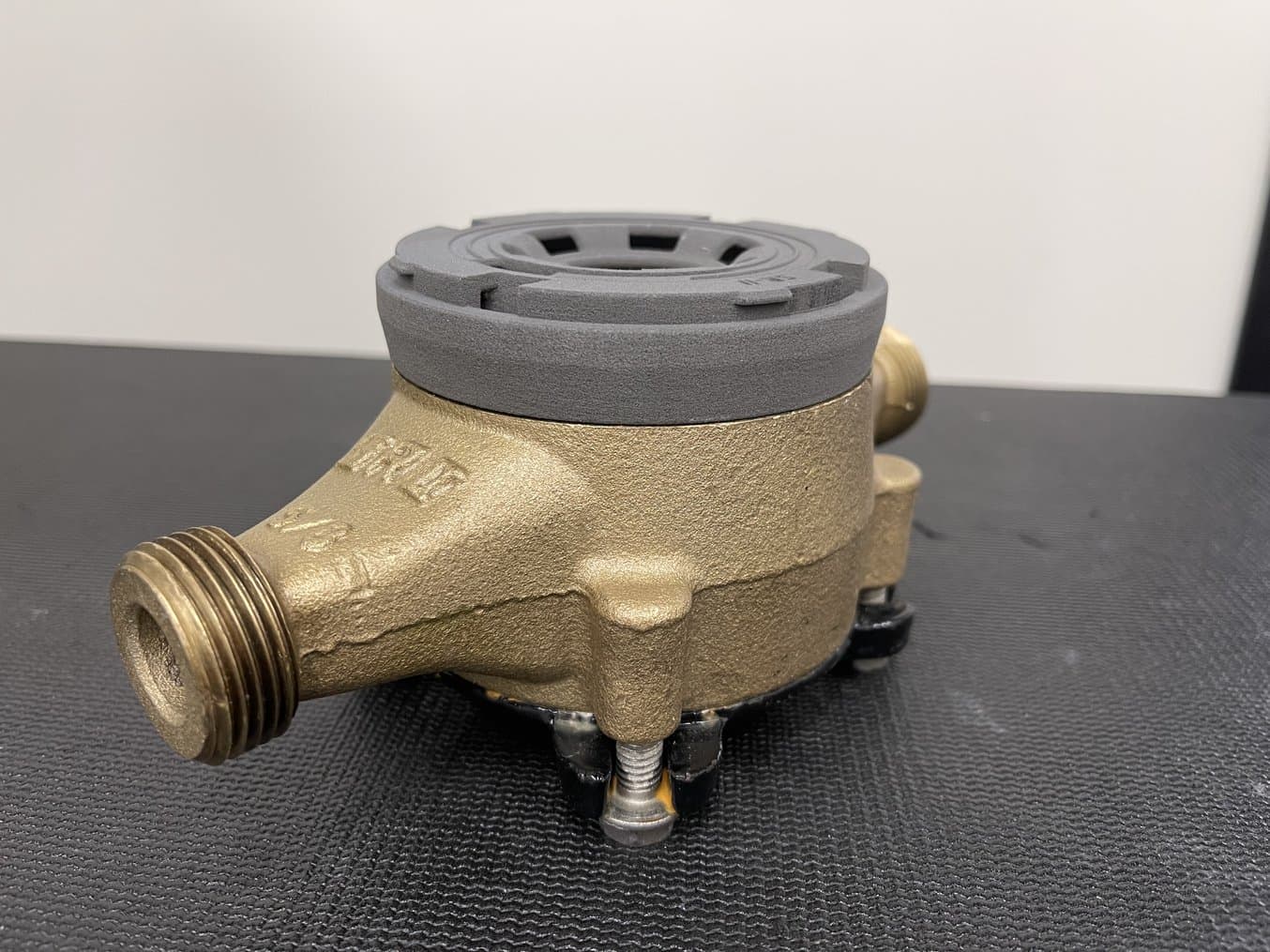
Le composant imprimé sur la Fuse 1 des compteurs d'eau personnalisés de Next Meters.
Des essais sous contrainte pour reproduire les conditions sur le terrain
Pour s'assurer que ses pièces finales sont capables de résister aux exigences imposées sur le terrain, Next Meters dispose de sa propre équipe d'essai interne. Le bracket qu'ils impriment en Nylon 11 Powder pour fixer leur technologie au compteur d'eau existant ne doit pas être soumis à des tests réglementaires externes. Next Meters mène donc son propre processus d'impression pour s'assurer que ses pièces sont performantes sur le terrain.
À l'aide d'une chambre climatique ultramoderne, ils ont fait passer les brackets de 70 °C à 0 °C, puis à nouveau à 0 °C, plusieurs fois par jour pendant plus de trois mois, simulant ainsi un séjour de 15 ans dans un environnement extérieur. Le succès des tests leur a permis de démarrer la production de ces pièces finales avec leur imprimante Fuse 1 et de passer à l'utilisation de deux matériaux.
« Il y a environ 250 brackets imprimés avec la Fuse 1 actuellement sur le terrain, faits pour s'adapter à trois compteurs différents et imprimés en Nylon 11 Powder. Nous les prototypons en Nylon 12 [Powder] parce qu'elle a le meilleur taux de renouvellement, puis nous nettoyons l'appareil et passons à Nylon 11 Powder pour les pièces à déployer sur le terrain. »
David Clyde
L'impression 3D permet l'expansion et l'enseignement
Comme la Fuse 1 a rendu rentable la fabrication de pièces sur demande et réduit les coûts de développement et de prototypage, l'équipe de Next Meters peut développer son activité et toucher davantage de communautés. La croissance de la société est en partie due à ses programmes internes de formation et d'évolution de carrière. Alors que de plus en plus de sociétés tirent parti de la fabrication avancée, la main-d'œuvre doit acquérir les compétences nécessaires pour mettre en œuvre la technologie, et Next Meters a trouvé une solution en interne. Chaque employé a l'avantage d'utiliser les imprimantes 3D sur demande, et beaucoup ont profité de cette opportunité pour en savoir plus sur la conception de produits et la fabrication avancée.
« Nous avons eu plusieurs employés en dehors de notre département d'ingénierie qui ont appris eux-mêmes des compétences en ingénierie mécanique et qui se sont déplacés pour faire progresser la société grâce à ces nouvelles compétences. C'est un plaisir de voir la créativité de notre personnel et de soutenir ceux qui ont envie de découvrir et d'évoluer professionnellement », déclare M. Clyde.
En outre, M. Clyde est partenaire d'un club local d'impression 3D afin de fournir un accès et un enseignement aux élèves des écoles intermédiaires. Chaque mois, les étudiants viennent au laboratoire de prototypage de Next Meters et ont la possibilité d'imprimer leurs propres conceptions sur les imprimantes FDM, SLA et SLS. M. Clyde y voit l'occasion d'aider à l'adoption de la technologie et d'améliorer le secteur dans son ensemble en enseignant à la future main-d'œuvre.
« C'est amusant de les voir réfléchir à ce processus. L'impression 3D va de toute façon se développer en production industrielle : les enfants l'adoptent déjà et ils conçoivent des pièces spécialement adaptées, contrairement aux ingénieurs mécaniques traditionnels, qui doivent changer leur façon de concevoir. C'est pourquoi nous menons nos activités en soutenant ces groupes de jeunes, ce jeune groupe d'ingénieurs qui, en grandissant, changera l'avenir de la production industrielle », déclare M. Clyde.
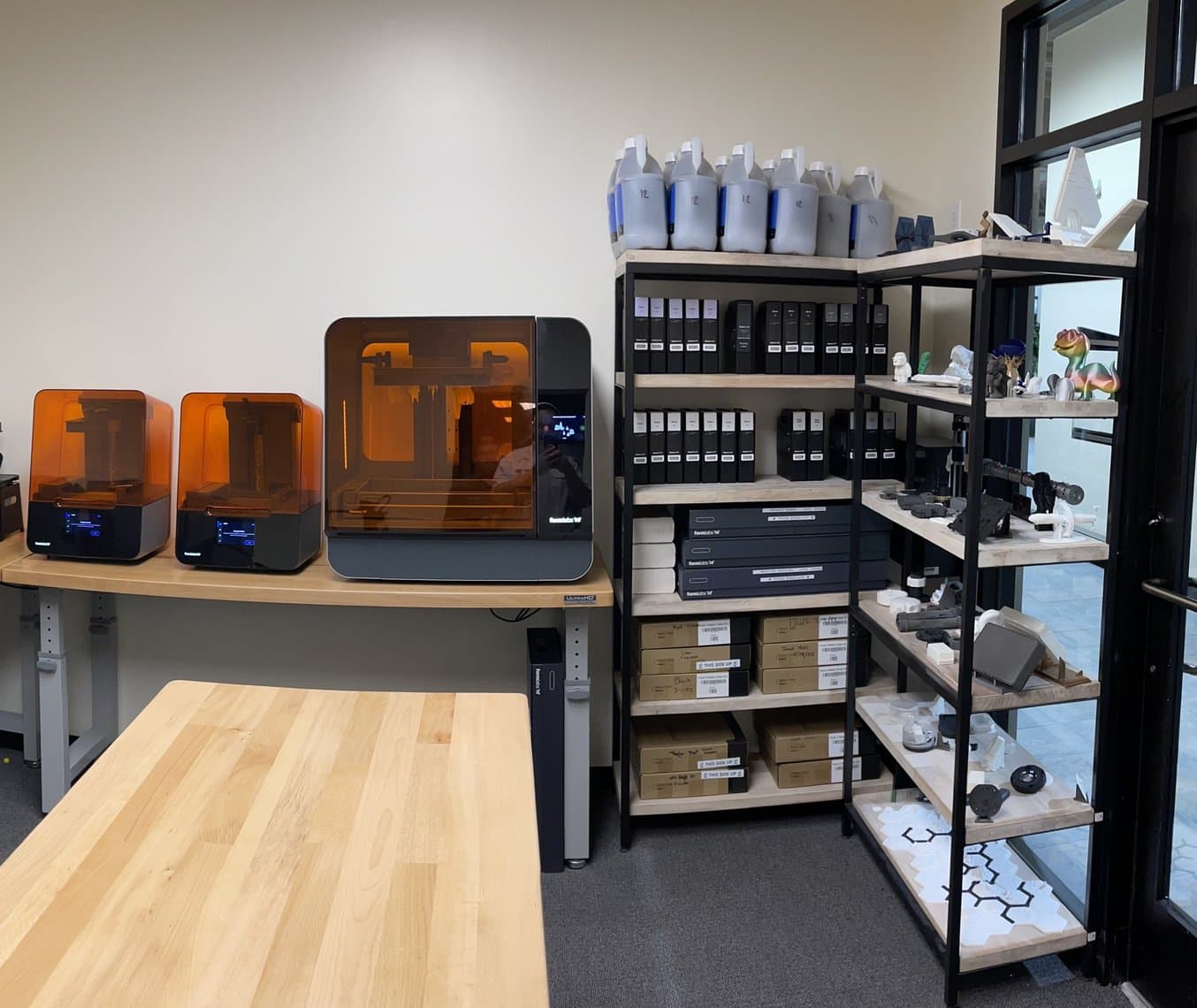
La Form 3L permet aux employés et aux membres étudiants du club d'impression 3D d'imprimer des prototypes et des modèles de grande taille.
Améliorer l'accès
En s'appuyant sur leurs nouveaux flux de travail complémentaires de moulage par injection et d'impression 3D, Next Meters peut maintenant faire face à toutes les situations et continuer à permettre aux communautés de suivre avec précision leur consommation d'eau et de récompenser ceux qui conservent cette ressource naturelle de plus en plus précieuse. L'impression 3D a accéléré les délais de prototypage et de développement, réduit les coûts de la phase d'outillage et permis la production de pièces finales, tout en fournissant des outils d'enseignement et de formation à leurs employés et à leur communauté.
« L'investissement que nous avons réalisé dans notre laboratoire d'impression 3D nous a non seulement fourni une méthode de fabrication plus rapide et plus rentable, mais il nous a également permis de maintenir nos normes de qualité élevées en ramenant une plus grande partie du processus d'impression à l'intérieur de l'entreprise, sous notre contrôle. Nous avons hâte de continuer à développer nos capacités d'impression 3D, et nous sommes enthousiastes de voir ce qu'elle nous réserve. »
David Clyde