La production de prothèses fait un grand pas en avant avec le NOVA Foot imprimé en 3D
« Souvent, les idées naissent parce que l'on découvre le potentiel des technologies avec lesquelles on travaille quotidiennement. Si nous n'avions pas accès aux imprimantes 3D, le NOVA Foot n'aurait même pas vu le jour. Avoir accès à la Fuse 1+ 30W m'a amené à penser que je pouvais créer quelque chose de vraiment fonctionnel et accessible à tous, qui pourrait révolutionner le quotidien des personnes amputées. »
Marco Garano, PDG, C.P.T.
Le NOVA Foot est un pied prothétique personnalisé à haut rendement énergétique, disponible en six tailles. Développé par Marco Garano, PDG de C.P.T. (Custom Precision Technology), le NOVA Foot a été prototypé, testé et est maintenant produit avec les imprimantes 3D de Formlabs. Sans l'accès à l'impression 3D, cette prothèse n'existerait pas, car toute autre méthode de production serait d'un coût prohibitif et inefficace. Le NOVA Foot est vendu par Protosystem, une spin-off du C.P.T., ouverte dans le but de créer des produits fonctionnels et accessibles dans le domaine orthopédique.
« Grâce à l'impression 3D, qui nous a permis de diminuer considérablement les coûts de production, le NOVA Foot est accessible à tous les amputés du pied en Italie, et est entièrement couvert par le NHS. »
Valentina Garano, responsable des ventes et du marketing, Protosystem
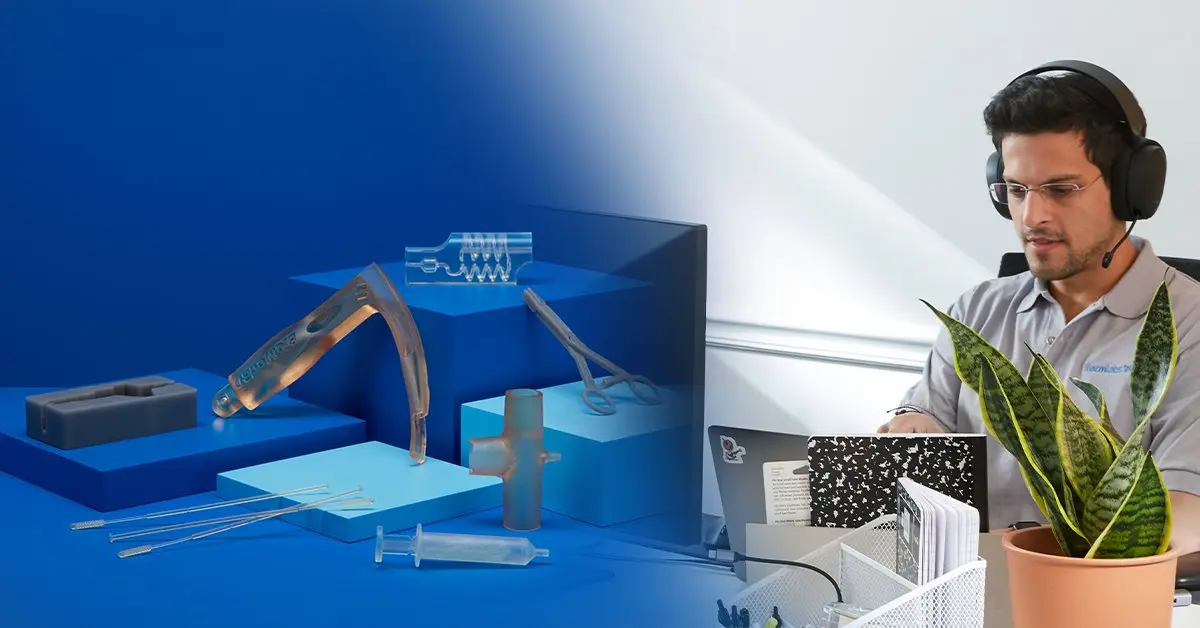
Discutez avec notre équipe commerciale médicale
Que vous deviez fabriquer des outils chirurgicaux adaptés aux patients ou un prototype de dispositif médical cardiaque, nous sommes là pour vous aider. L'équipe de Formlabs Medical est composée de spécialistes dévoués qui savent exactement comment vous soutenir et répondre aux besoins de votre entreprise.
Le NOVA Foot : personnalisable pour un meilleur confort
La plupart des pieds prothétiques nécessitent une adaptation importante de la part du patient. Avec le Nova Foot, l'objectif était plutôt d'adapter la prothèse au patient et de lui garantir confort et stabilité lors de son utilisation quotidienne.
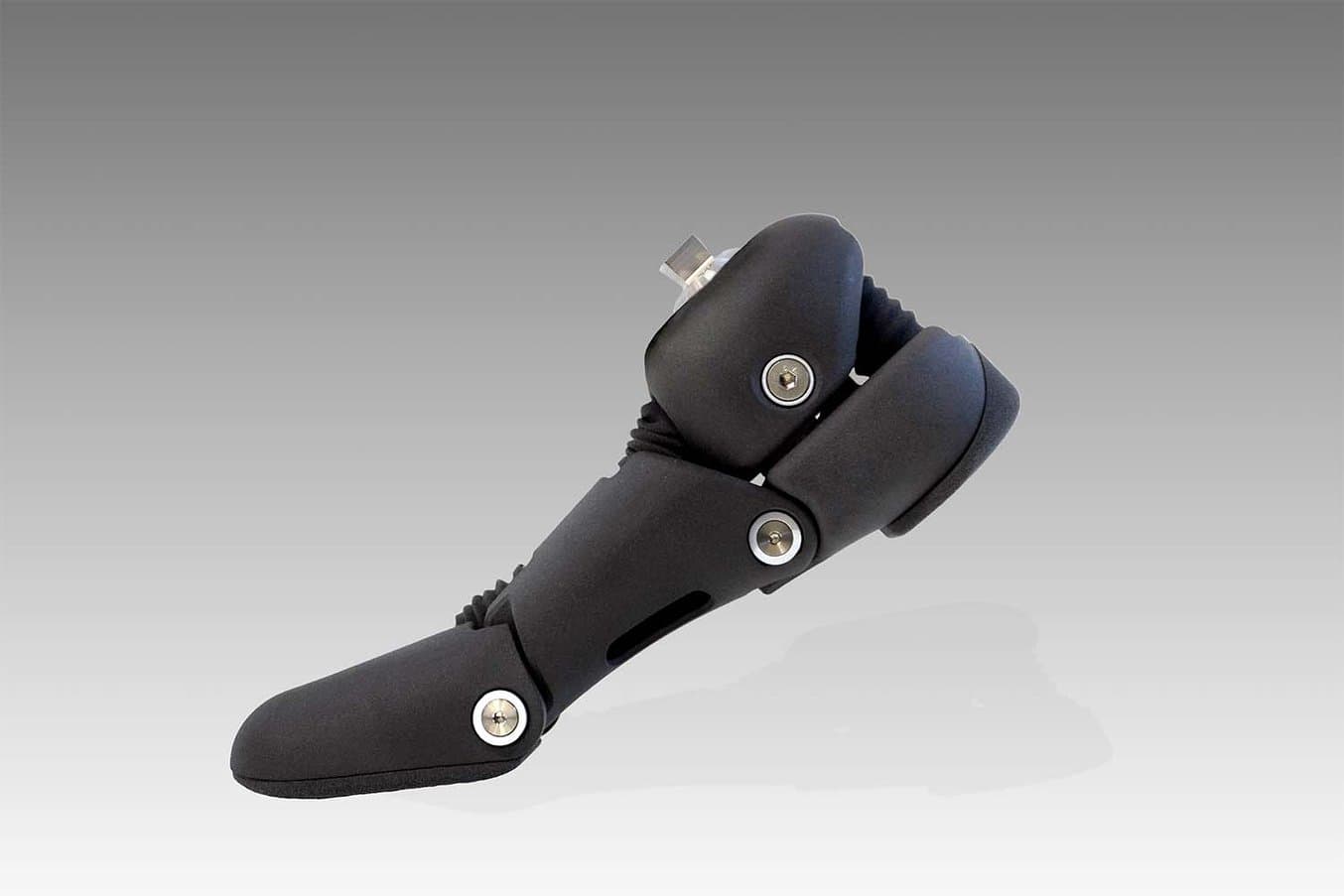
Le NOVA Foot est imprimé en 3D sur la Fuse 1+ 30W de Formlabs avec des composants supplémentaires imprimés sur la Form 3B+.
Le NOVA Foot se compose de plusieurs sections pour l'avant-pied, le milieu du pied, le talon et la cheville. Chaque segment du pied peut être personnalisé en fonction des besoins du patient. Ces sections hautement personnalisables sont imprimées sur l'imprimante à frittage sélectif par laser (SLS) Fuse 1+ 30W. Des semelles supplémentaires au niveau des orteils et du talon, également imprimées sur la Fuse 1+ 30W, sont totalement imperméables et offrent maintien et stabilité dans les environnements humides, comme sous la douche.
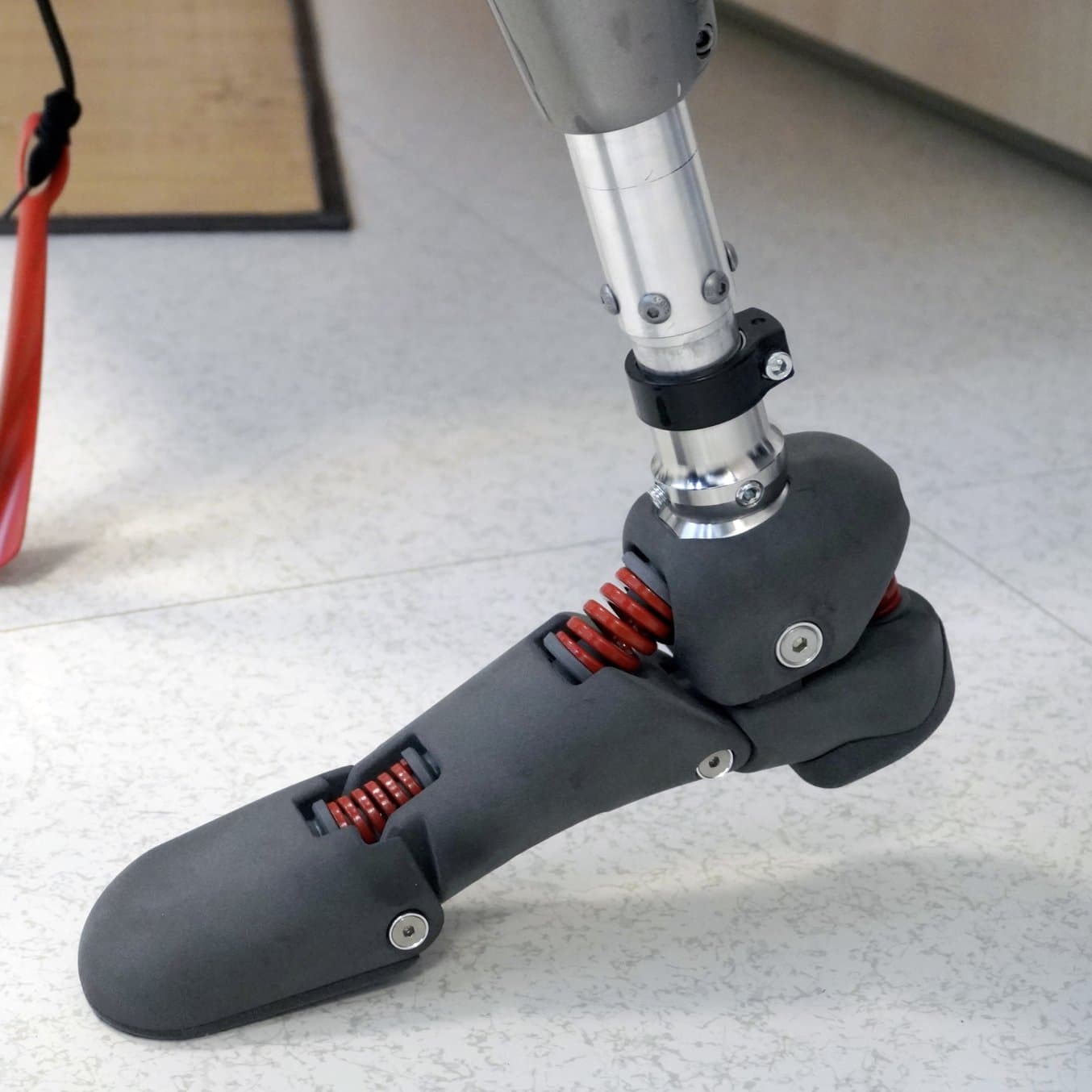
Les ressorts du NOVA Foot, ici en rouge, peuvent être remplacés par des ressorts plus souples ou plus rigides afin d'adapter la réactivité du NOVA Foot.
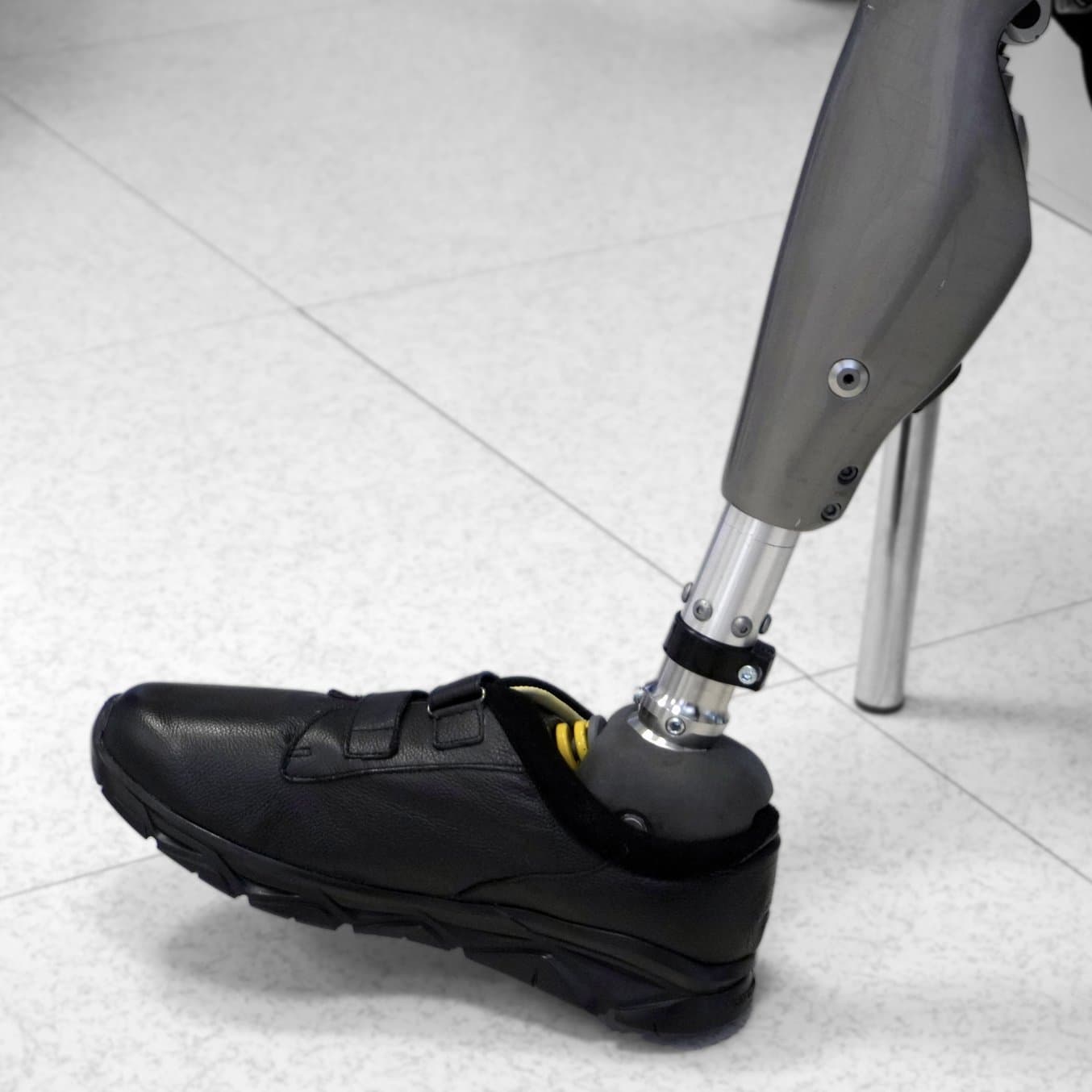
Le NOVA Foot peut être utilisé dans la chaussure ou à nu.
Trois ressorts assurent la mobilité des composants imprimés en 3D du pied. La flexion du pied peut être personnalisée avec des ressorts plus souples ou plus rigides. Les trois ressorts pouvant être remplacés à tout moment, le NOVA Foot est idéal pour les patients moins actifs qui préfèrent une prothèse offrant des mouvements fluides et un grand confort, mais aussi pour les patients plus actifs qui ont besoin d'une prothèse réactive qui restitue l'énergie lors d'activités sportives de courte durée. Le remplacement des trois ressorts favorise également le processus de rééducation immédiatement après une amputation de la jambe.
Si un patient souhaite par exemple plus de confort lors de la phase d'attaque du talon et plus de pression lors de la phase d'attaque des orteils, il est possible d'intégrer un ressort plus souple dans le talon et deux ressorts plus rigides dans l'avant-pied afin d'adapter individuellement la réaction de la semelle NOVA Foot.
Pourquoi fabriquer avec l'impression 3D ?
« Grâce à l'impression 3D, nous sommes en mesure de produire les pièces en interne dans un délai très court. Cela nous permet de passer très rapidement de l'idée au prototype et du prototype à la production. L'impression 3D nous permet également de créer des géométries complexes qui ne seraient pas possibles avec les technologies de production traditionnelles. »
Marco Garano, PDG, C.P.T.
La production du NOVA Foot ne serait pas possible avec une autre méthode de production. Le haut niveau de personnalisation d'un si grand nombre d'éléments serait d'un coût prohibitif s'il était produit par une autre méthode de production, notamment le moulage par injection ou l'usinage. Marco Garano ajoute : « Comme nous fabriquons les pièces avec la Fuse 1+ 30W, nous sommes en mesure de réaliser des géométries très complexes, creuses à l'intérieur, avec des renforts à certains endroits, qui ont été déterminés à l'aide de la méthode des éléments finis. Les pièces sont donc légères, mais en même temps tenaces et fonctionnelles. Un autre exemple est la semelle d'assistance Formlabs au niveau du talon, qui utilise du TPU, créant une cavité interne pour réduire la densité à cet endroit précis. »
« Nous avons choisi l'impression 3D pour produire les pièces du NOVA Foot parce que nous avons un contrôle total du processus de production. De plus, si nous devons modifier les pièces pour les personnaliser en fonction des besoins des patients, nous pouvons le faire sans avoir à supporter les coûts de modification des moules. »
Valentina Garano, responsable des ventes et du marketing, Protosystem
Le coût des moules d'injection pour la fabrication de tous les composants du NOVA Foot peut être estimé entre 50 000 et 60 000 € par taille de pied, pour un minimum de six tailles. Le coût des moules pour les six tailles s'élèverait à 300 000 € au minimum, ce qui est prohibitif.
L'impression 3D en interne offre également une protection de la chaîne d'approvisionnement, une diminution des risques et des temps d'exécution rapides pour le prototypage et la production. En outre, les taux de renouvellement de la poudre avec le SLS minimisent les déchets. Actuellement, l'impression d'un seul NOVA Foot avec la Fuse 1+ 30W prend environ cinq heures, et jusqu'à quatre prothèses peuvent être imprimées en même temps.
« Selon nous, les avantages de l'écosystème Formlabs (SLS et SLA) résident dans la possibilité d'estimer immédiatement les coûts, dans la simplicité du flux de travail, du remplissage du matériau au post-traitement, et dans l'analyse très précise du temps d'impression dans PreForm. »
Marco Garano, PDG, C.P.T.
Protosystem utilise à la fois une imprimante 3D SLS Fuse 1+ 30W et une imprimante 3D stéréolithographique (SLA) Form 3B+ pour le prototypage et la production, ainsi que le logiciel de préparation PreForm de Formlabs PreForm permet à Marco Garano de connaître en temps réel la durée estimée et la consommation du matériau, pour un contrôle total de la production.
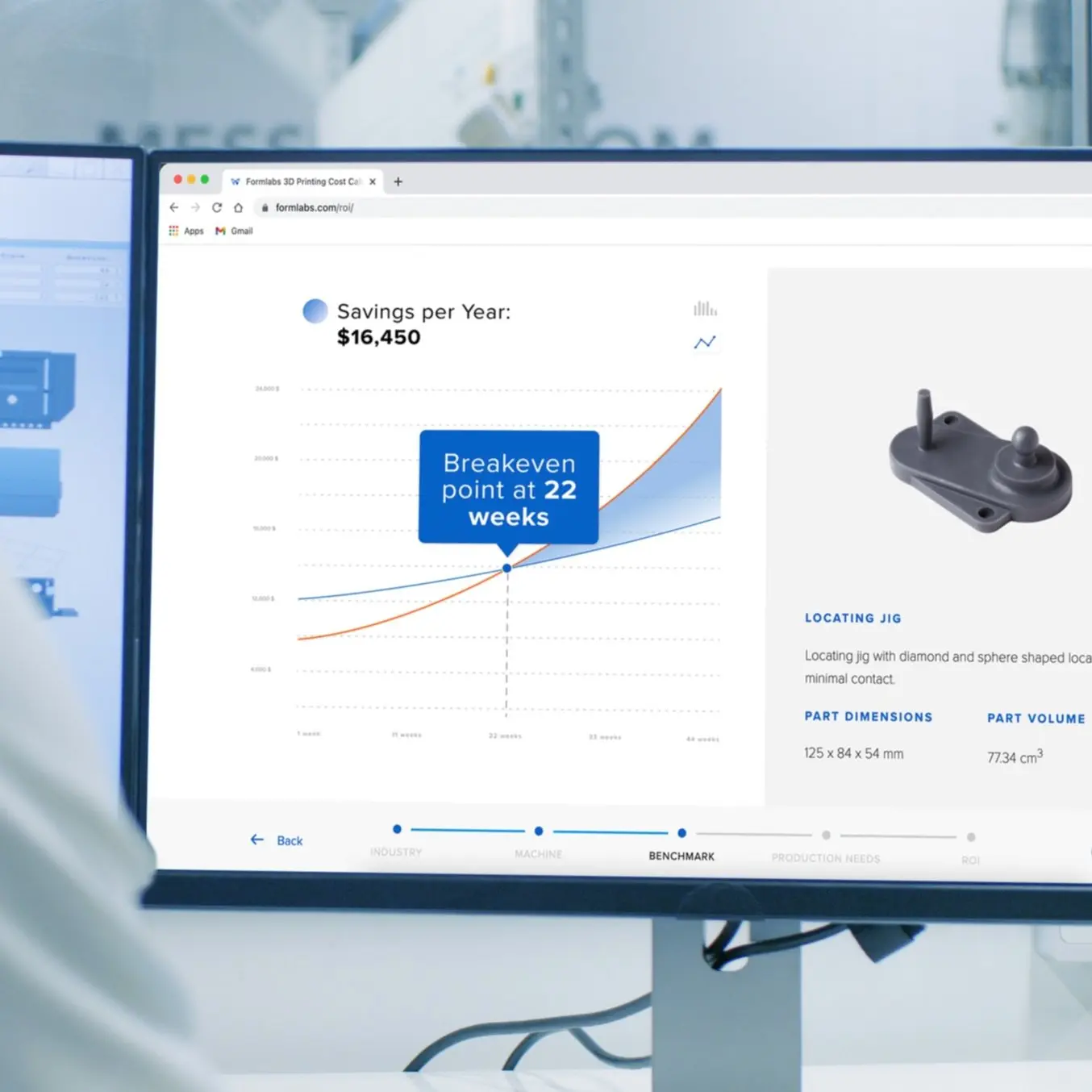
Calculez vos gains de temps et d’argent
Essayez notre outil de retour sur investissement interactif pour découvrir quel gain de temps et d’argent peut vous apporter l’impression 3D sur les imprimantes 3D Formlabs.
« Un avantage offert par Formlabs est la quantité de matériaux disponibles pour créer et essayer différentes pièces. »
Valentina Garano, responsable des ventes et du marketing, Protosystem
L'accès au vaste catalogue de Formlabs, qui comprend plus de 40 matériaux haute performance, a été un avantage clé pour répondre aux exigences strictes de ce projet. Le NOVA Foot exigeait des propriétés matérielles très spécifiques : il devait être durable, léger, imperméable, esthétique, abordable et capable de résister à une utilisation répétée dans des conditions difficiles. Marco Garano a travaillé avec des matériaux SLS, en démarrant avec Nylon 11 Powder pour le prototypage, puis est passé à Nylon 12 Powder pour la production.
Nylon 12 Powder est utilisé pour le gros du pied car il est léger tout en étant résistant à la compression et aux chocs, et présente une grande stabilité environnementale. Marco Garano précise : « Nous avons choisi de fabriquer les pièces en Nylon 12 Powder principalement parce que les tolérances d'impression sont meilleures avec ce matériau, que les matériaux en contact les uns avec les autres ne nécessitent pas d'ajustement manuel et que le coût des pièces finales est légèrement inférieur à celui de Nylon 11 Powder. »
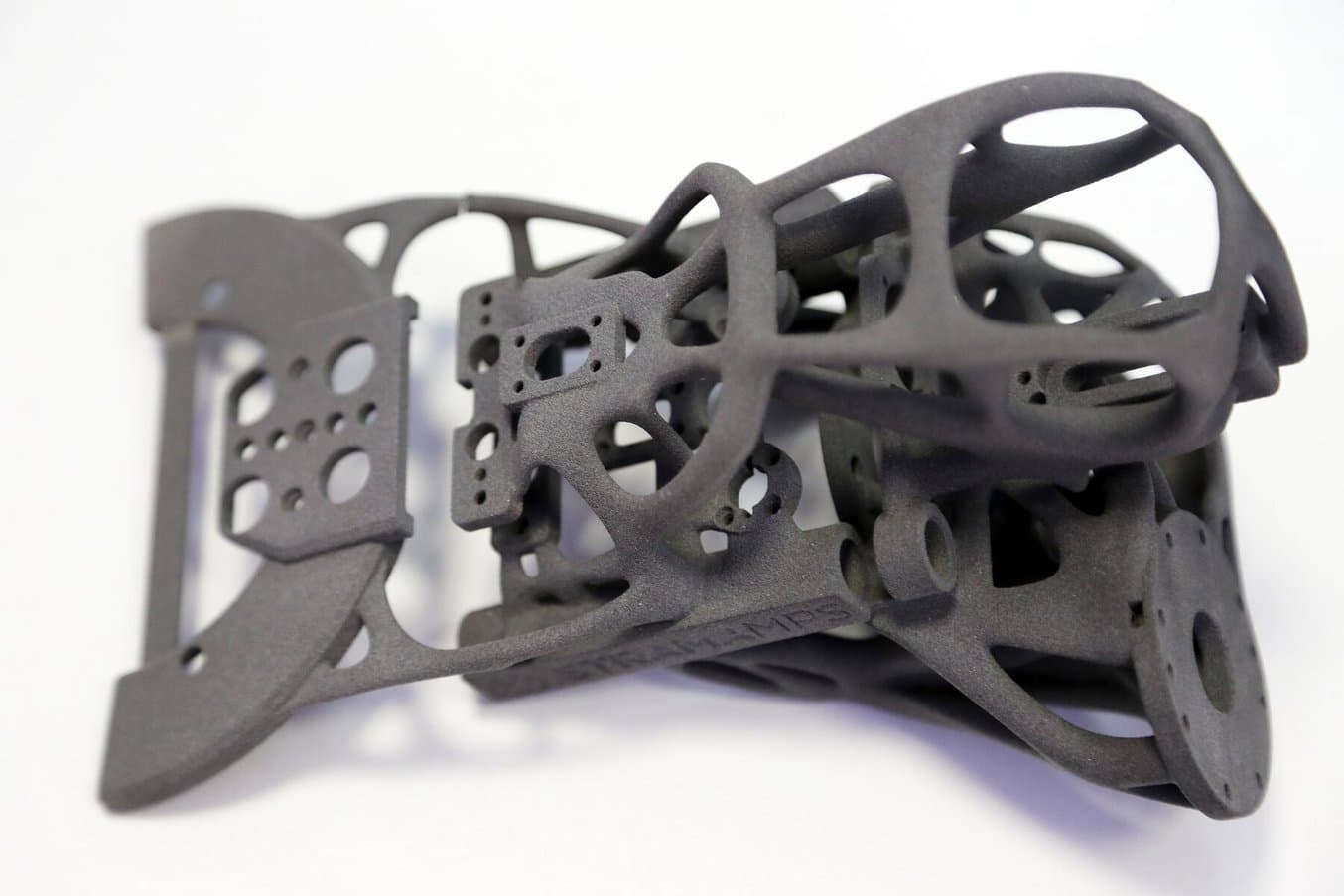
Guide de conception pour les imprimantes de la série Fuse
Dans ce guide de conception, vous découvrirez certains points importants à prendre en compte pour concevoir des pièces que vous souhaitez fabriquer avec l'imprimante SLS Fuse 1, et comment vous pouvez tirer parti de ces pratiques pour créer des pièces réussies.
TPU 90A Powder est utilisée pour le rembourrage du talon et de l'avant-pied, ainsi que pour les couvre-ressorts qui nécessitent une certaine ductilité. Le rembourrage au talon dispose d'une structure interne en treillis qui assure le confort lors de l'utilisation quotidienne du pied. Les structures en treillis ne peuvent pas être produites avec des méthodes de fabrication autres que l'impression 3D.
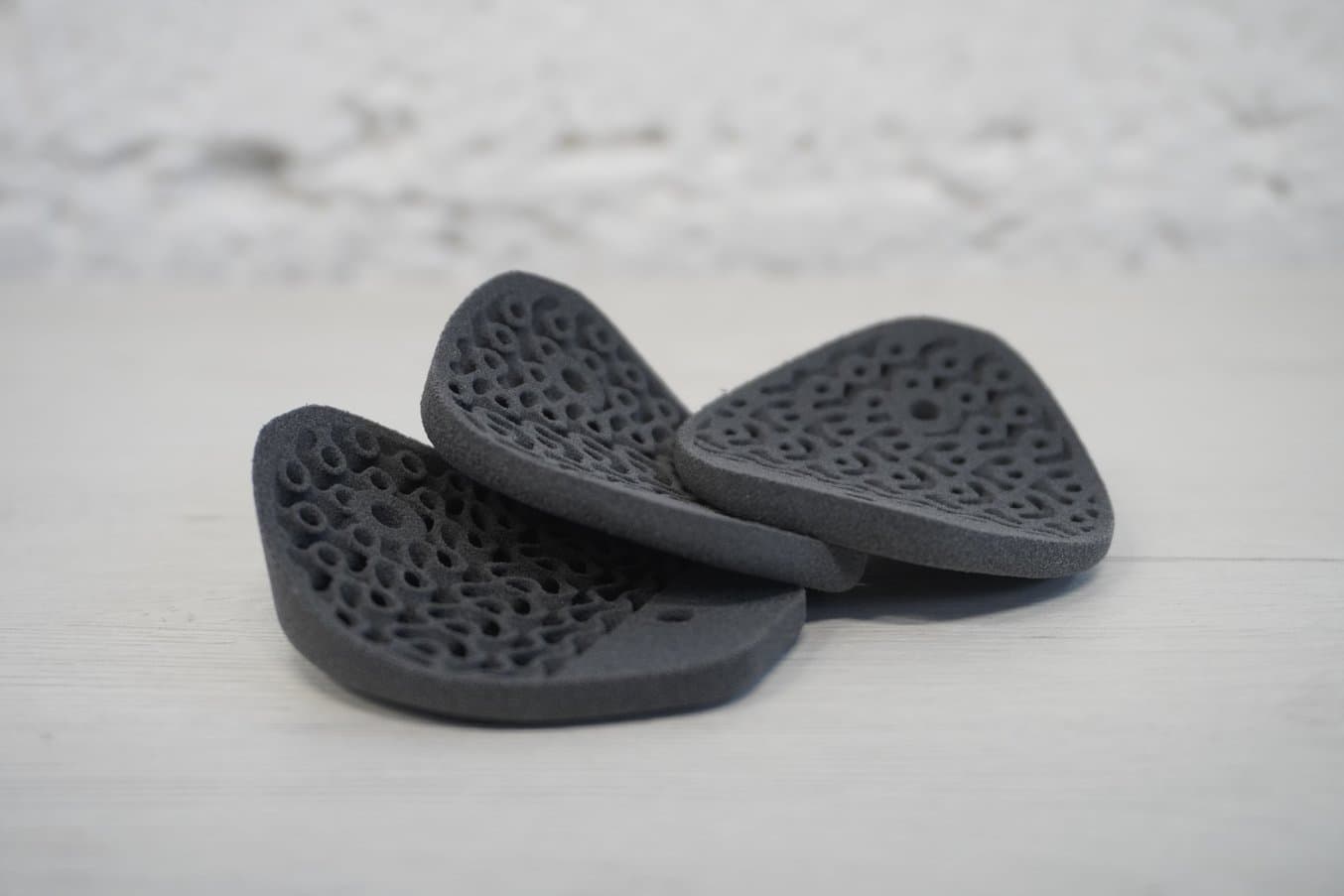
La structure en treillis des coussinets au talon amortit les chocs. Ces structures internes seraient impossibles à créer avec une méthode de fabrication autre que l'impression 3D.
Les coussinets ne se contentent pas d'absorber les chocs, ils donnent également de l'adhérence lors de la marche. Marco Garano explique : « Deux semelles nous ont permis d'éviter de créer un revêtement comme dans les prothèses traditionnelles en fibre de carbone, ce qui a considérablement réduit le poids final de la prothèse. »
Les prothèses en carbone traditionnelles sont recouvertes d'une housse qui assure leur adhérence, protège le pied de l'humidité et remplit la chaussure. La conception du NOVA Foot permet de remplir les chaussures sans avoir besoin d'une housse. En outre, les matériaux utilisés pour fabriquer NOVA Foot n'ont pas besoin d'être protégés de l'eau, et les coussinets en TPU 90A Powder assurent l'adhérence.
En moyenne, une prothèse en fibre de carbone pour adulte pèse de 400 à 600 grammes, auxquels s'ajoutent ~200 grammes de housse esthétique. En revanche, le NOVA Foot pèse 550 grammes et ne nécessite pas de housse esthétique, ce qui le rend plus léger qu'une prothèse en fibre de carbone.
Outre les pièces imprimées en 3D par SLS, des pièces SLA sont utilisées pour maintenir les ressorts. Ces porte-ressorts doivent avoir une surface très lisse parce qu'ils glissent, et doivent être très précis parce qu'ils doivent s'emboîter dans les pièces en Nylon 12 Powder avec un minimum de jeu. Les porte-ressorts sont imprimés en Tough 2000 Resin, un matériau similaire à l'ABS pour des matériaux solides et robustes qui contiennent une utilisation prolongée.
« La liaison entre les supports de ressort en Tough 2000 Resin et les pièces de base en Nylon 12 Powder met en valeur la grande précision des imprimantes Formlabs. »
Valentina Garano, responsable des ventes et du marketing, Protosystem
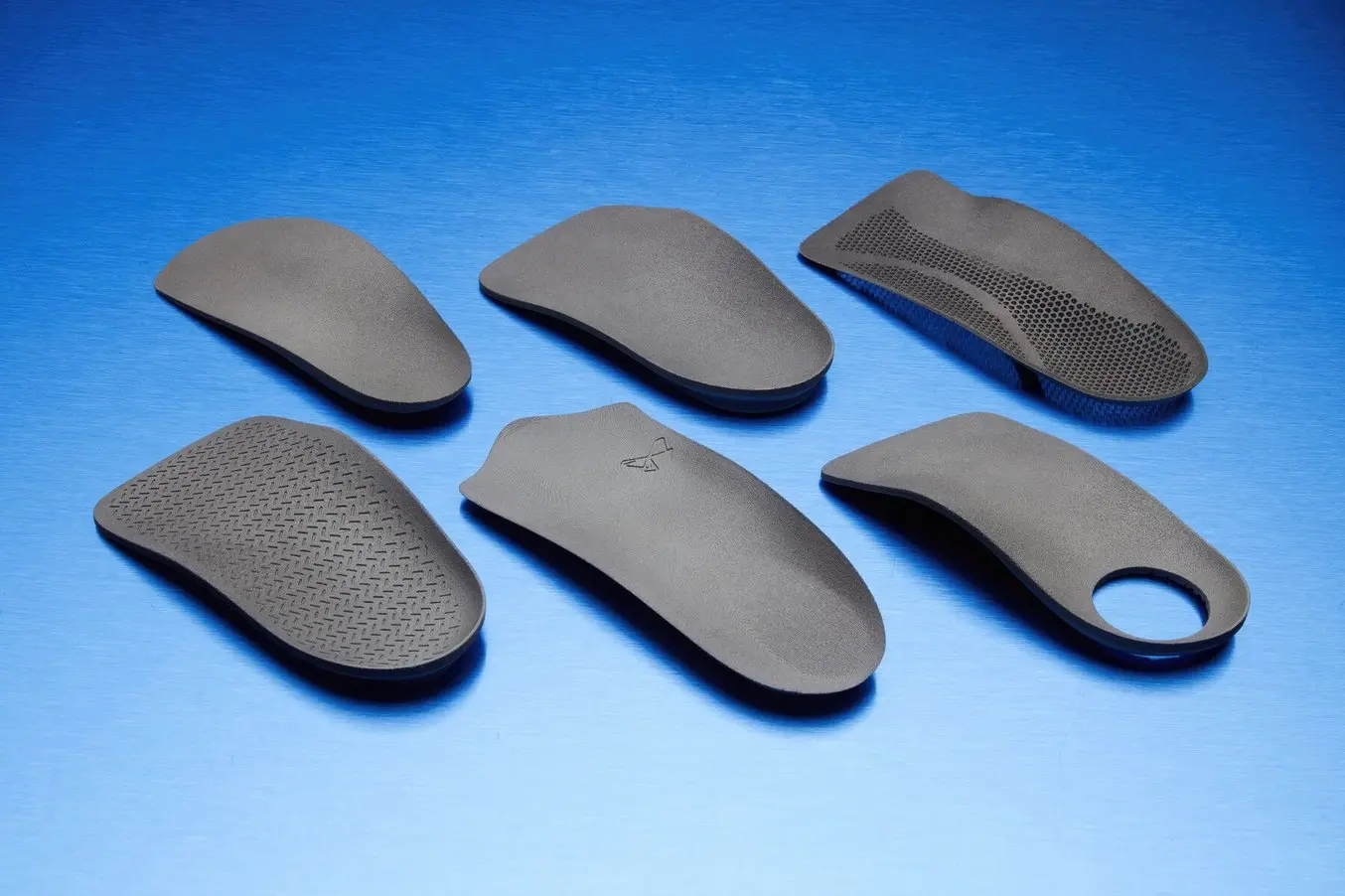
Orthèses personnalisées grâce à l'impression 3D
Vous pouvez désormais produire en interne des produits orthopédiques personnalisées facilement et à un prix abordable grâce à un flux de travail numérique simple et propre qui permet non seulement de réduire les coûts et les besoins en main-d'œuvre, mais aussi d'améliorer les délais d'exécution et le confort de vos clients.
Essai du NOVA Foot
Les premiers tests sont réalisés à l'aide de l'analyse par éléments finis (FEA) dans SolidWorks. Ensuite, une fois la conception testée, elle est imprimée pour être testée physiquement. À l'aide de machines, le mouvement mécanique de différentes activités est simulé et le pied est soumis à un test de résistance. Le produit fini doit être capable de supporter des mouvements répétitifs et le poids du corps. Le prototypage utilisant la même méthode de production que la fabrication, les résultats de ces essais affichent exactement les performances du NOVA Foot.
Les ressorts du NOVA Foot doivent être remplacés chaque année par l'utilisateur afin de garantir leur bon fonctionnement. Cependant, comme les pièces en Nylon 12 Powder ne sont soumises qu'à des compressions, elles devraient durer plus de trois ans.
Après des essais internes, Protosystem travaille avec des spécialistes et des centres orthopédiques pour des essais en conditions réelles. Avant sa mise sur le marché, le NOVA Foot a été testé par des patients volontaires dans un centre sportif pour personnes amputées ainsi que dans la vie quotidienne. Protosystem a constaté que les utilisateurs sont surpris par la fluidité du NOVA Foot lorsqu'ils montent ou descendent une rampe. Les patients ont également indiqué que le NOVA Foot leur renvoie beaucoup d'énergie pendant la marche, en les supportant à chaque pas.
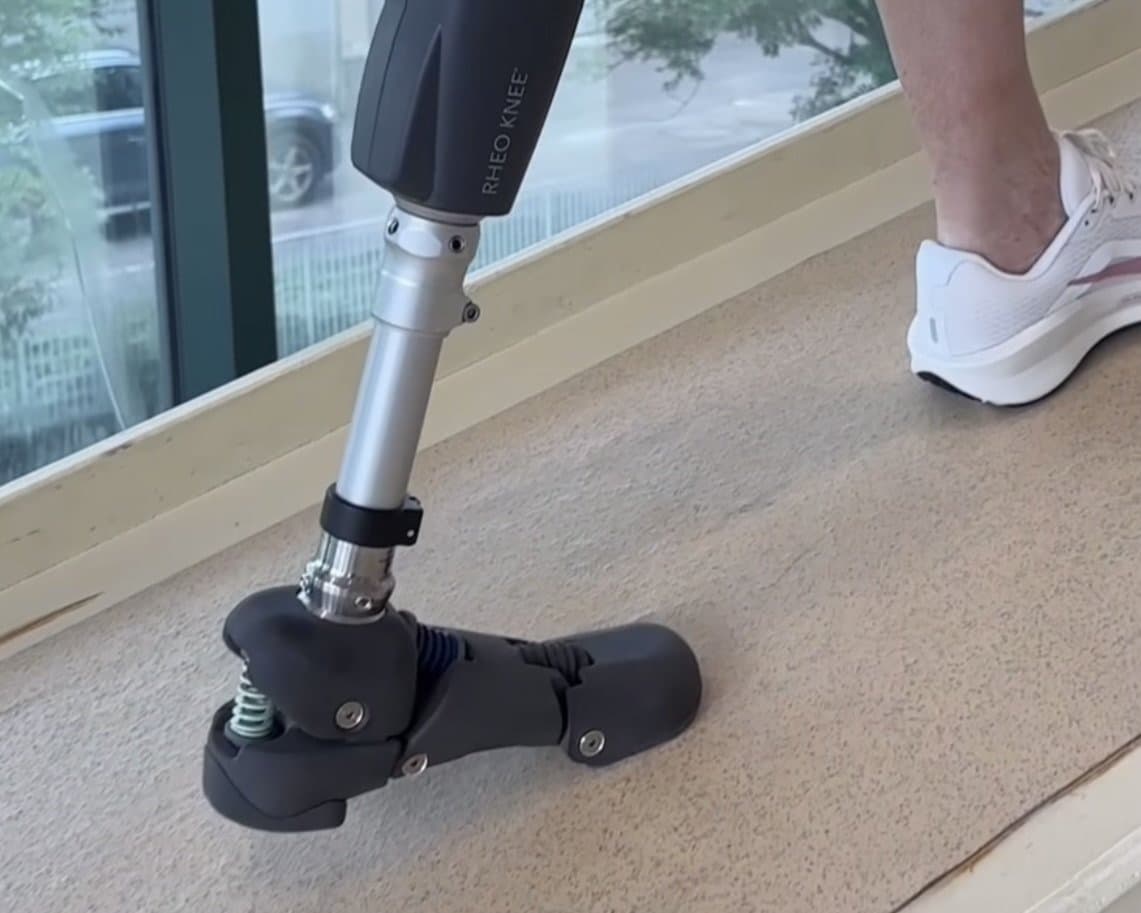
Le NOVA Foot a été testé aussi bien pendant le sport que dans la vie quotidienne, et les testeurs ont remarqué la fluidité avec laquelle ils pouvaient monter les rampes.
Grâce à l'impression 3D, au fur et à mesure que les patients utilisent NOVA Foot et font part de leurs retours, les modifications et les personnalisations peuvent continuer à être apportées sans interruption de la production. Un patient amputé avait par exemple besoin d'un maintien supplémentaire lors de la phase d'appui du talon et d'un meilleur amortissement des chocs. Marco Garano a pu personnaliser le modèle en quelques heures, en modifiant la partie supérieure du pied et l'attache du pied afin d'améliorer le support et d'offrir plus d'absorption des chocs. Une fois les modifications apportées, il faut cinq heures pour imprimer le pied, ce qui permet de le personnaliser en une journée.
Après une année de recherche et plusieurs itérations de prototypes, le NOVA Foot a été lancé sur le marché en mars 2025 et a suscité beaucoup d'enthousiasme chez les patients qui ont essayé la prothèse jusqu'à présent grâce à ses caractéristiques uniques.