Comment Unilever et Serioplast développent de nouveaux designs de bouteilles grâce à des moules imprimés en 3D
Unilever, l'une des plus grandes entreprises mondiales de biens de consommation à rotation rapide (FMCG), développe en permanence de nouveaux produits d'usage quotidien, qu'il s'agisse de soins personnels, de soins à domicile, de nutrition ou d'autres choses encore. Il est fort probable que vous ayez un ou plusieurs de leurs produits chez vous en ce moment, étant donné que l'entreprise possède entre autres Dove, Domestos, Cif, Knorr, Axe (Lynx), Ben & Jerry's, ainsi que des dizaines d'autres marques mondiales et locales.
Les produits de grande consommation constituent un marché sur lequel s’exerce une forte pression concurrentielle, obligeant ainsi les entreprises à perpétuellement innover et à ajuster leurs stratégies. L'emballage est un domaine d'innovation important : le design d'une bouteille peut parfois influencer la perception du client autant que son contenu. Les marques comme Unilever doivent prendre en considération l’utilisation des matériaux, l’attrait esthétique, la sécurité et la durabilité d’un vaste catalogue d’emballages et de produits qu’ils contiennent. Mais pour une « simple » bouteille en plastique, le passage de la conception sur l'écran de l'ordinateur au remplissage sur la chaîne de fabrication prend traditionnellement de nombreux mois.
« Une entreprise de biens de consommation comme Unilever doit être sur le marché le plus tôt possible ou avant ses concurrents. Il faut offrir aux consommateurs les meilleurs produits au meilleur prix le plus rapidement possible. L'impression 3D nous aide à accélérer ce processus. »
Stefano Cademartiri, responsable CAO et prototypage, Unilever
Stefano Cademartiri, responsable CAO et prototypage chez Unilever, et Flavio Migliarelli, responsable de la conception R&D chez Serioplast Global Services, vous expliquent comment ils ont testé la viabilité des moules imprimés en 3D pour le moulage par étirage-soufflage de petites séries afin d'accélérer le prototypage et les essais pilotes, réduisant ainsi les délais de six semaines et les coûts jusqu'à 90 %.
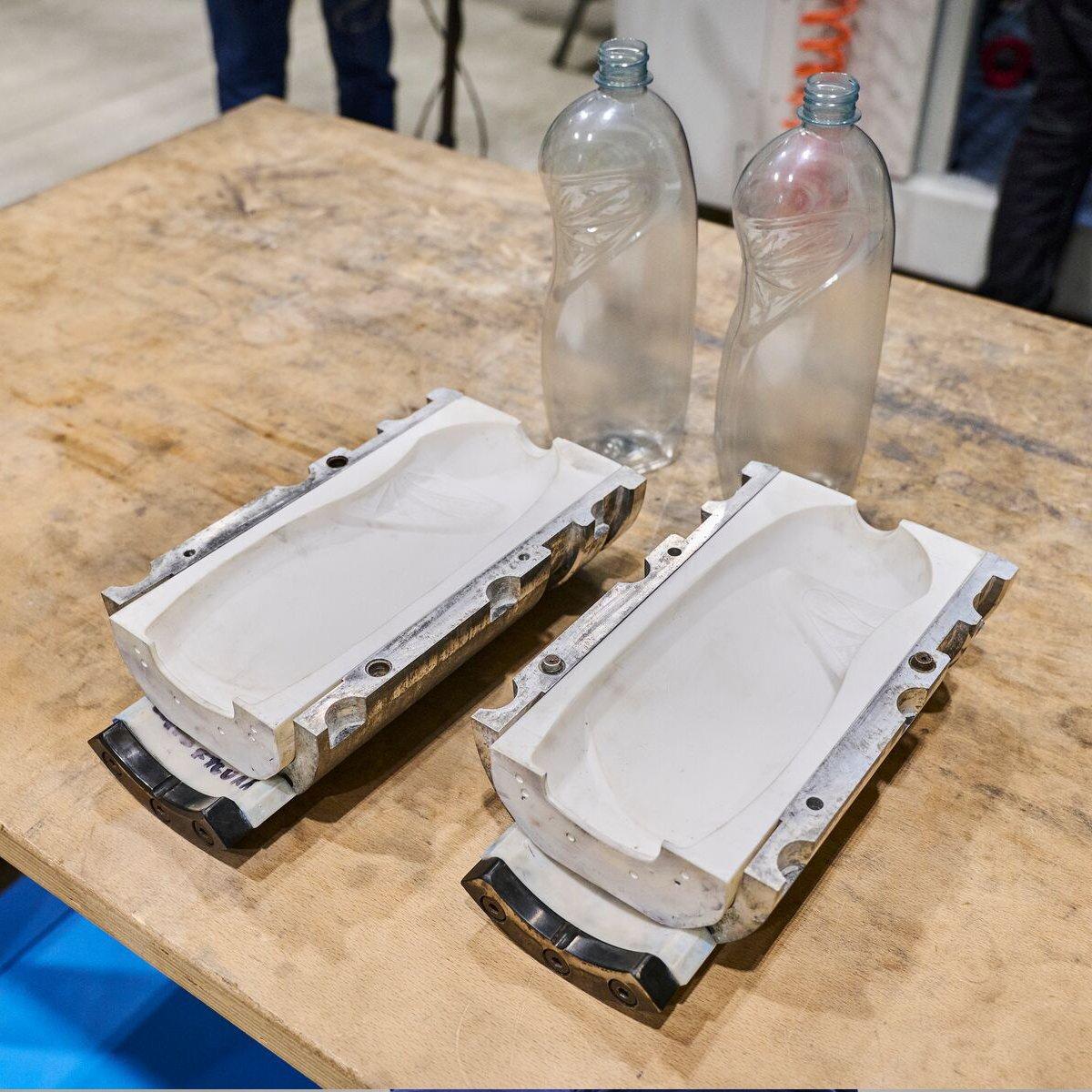
Moulage par étirage-soufflage rapide de petites séries avec des moules imprimés en 3D
Ce livre blanc fournit des méthodes et des lignes directrices pour l'utilisation de moules imprimés en 3D SLA dans le processus de moulage par étirage-soufflage afin de réduire les coûts et les délais pendant la préproduction. Des considérations de conception au flux de travail en passant par les conditions de moulage, nous vous présentons une étude de faisabilité menée par les experts du secteur Unilever et Serioplast.

Calculez votre retour sur investissement
Formlabs collabore avec des centaines de revendeurs pour proposer ses produits dans le monde entier.
Le processus traditionnel de développement et d'essai de nouveaux modèles de bouteilles
Les produits en plastique tels que les contenants destinés aux aliments et aux boissons, les emballages cosmétiques et les emballages médicaux sont généralement obtenus par moulage par soufflage. Ce groupe de méthodes de production de masse rapide a été mis au point il y a longtemps pour produire des pièces de haute qualité présentant des parois minces. Le moulage par soufflage a des temps de cycle très courts, généralement entre une et deux minutes, et est extrêmement rentable pour la production de grands volumes. Il est généralement utilisé pour produire des millions de pièces identiques à un coût par pièce faible.
Le moulage par soufflage permet de former des pièces creuses en plastique en gonflant un tube de plastique chauffé (appelé préforme) à l'intérieur d'un moule, jusqu'à ce qu'il obtienne la forme souhaitée. Il existe trois types de procédés de moulage par soufflage : le moulage par extrusion-soufflage, le moulage par injection-soufflage et le moulage par étirage-soufflage. L'étirage-soufflage est une technique largement utilisée dans la production de récipients PET transparents de haute qualité, tels que les bouteilles d'eau.
Serioplast est un producteur mondial d’emballages en plastique rigide pour l’industrie des produits de grande consommation, et l’un des principaux partenaires d’Unilever dans le domaine du développement et de la fabrication d’emballages destinés au marché des produits d’entretien et de soins personnels. « Nous produisons quatre milliards de bouteilles par an en PET, PEHD et PP », a déclaré M. Migliarelli.
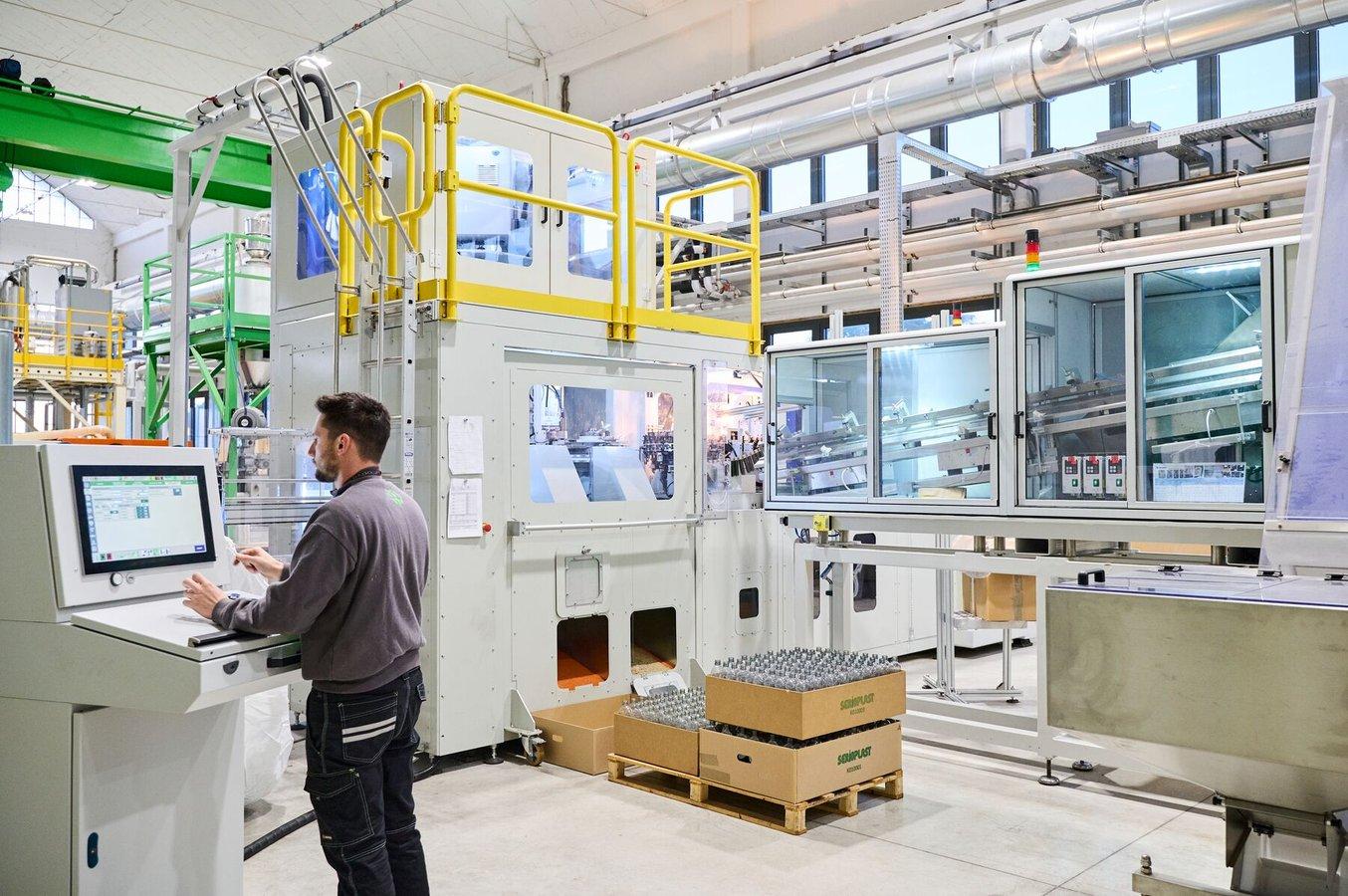
Machine de moulage Seriomac UNIX 4 Cavités de Serioplast dans son installation de R&D en Italie. En collaboration avec Unilever, l'entreprise a mis au point un nouveau flux de travail qui utilise des moules imprimés en 3D dans une installation de production industrielle à grande échelle.
Auparavant, Serioplast fabriquait des prototypes soit sous forme de modèles imprimés en 3D, soit par moulage par soufflage. En général, les maquettes imprimées en 3D n'offraient pas la bonne sensation ou la bonne transparence et n'étaient pas suffisamment fiables pour être envoyées aux consommateurs. Toutefois, le moulage par étirage-soufflage d'échantillons de qualité industrielle nécessite un outillage métallique coûteux, ce qui ajoute six à neuf semaines de délai à une phase d'essai pilote typique en raison de la complexité du processus et de l'externalisation de la production du moule.
« Nous devons attendre six à douze semaines avant de pouvoir présenter un véritable échantillon aux clients. Nous perdons donc de nombreuses semaines à essayer un nouveau design de bouteille. C'est parfois exigeant et frustrant, parce qu'il faut peut-être tout recommencer », explique M. Migliarelli.
Les moules d'étirage-soufflage sont traditionnellement fabriqués en métal par usinage CNC, ce qui nécessite un équipement spécialisé, un logiciel de FAO et une main-d'œuvre qualifiée. La production d'outillage métallique est généralement confiée à des prestataires de services qui proposent des délais de quatre à huit semaines et des coûts allant de 2000 à plus de 100 000 € en fonction de la complexité de la pièce et du nombre de pièces par moule. Même en interne, l'usinage des moules métalliques prend généralement six semaines, car il comprend plusieurs étapes : la commande des matériaux, la FAO et le réglage des appareils, le polissage manuel et l'attente de la disponibilité de la machine.
Par conséquent, le moulage par soufflage de petites séries pour le prototypage et les essais pilotes n'était jusqu'ici pas rentable. Des entreprises comme Unilever devaient planifier des délais très longs pour décider de la conception à partir de prototypes fabriqués dans d’autres matériaux. Cela entraînait souvent l’obsolescence de certains outils de production et des dépenses inutiles.
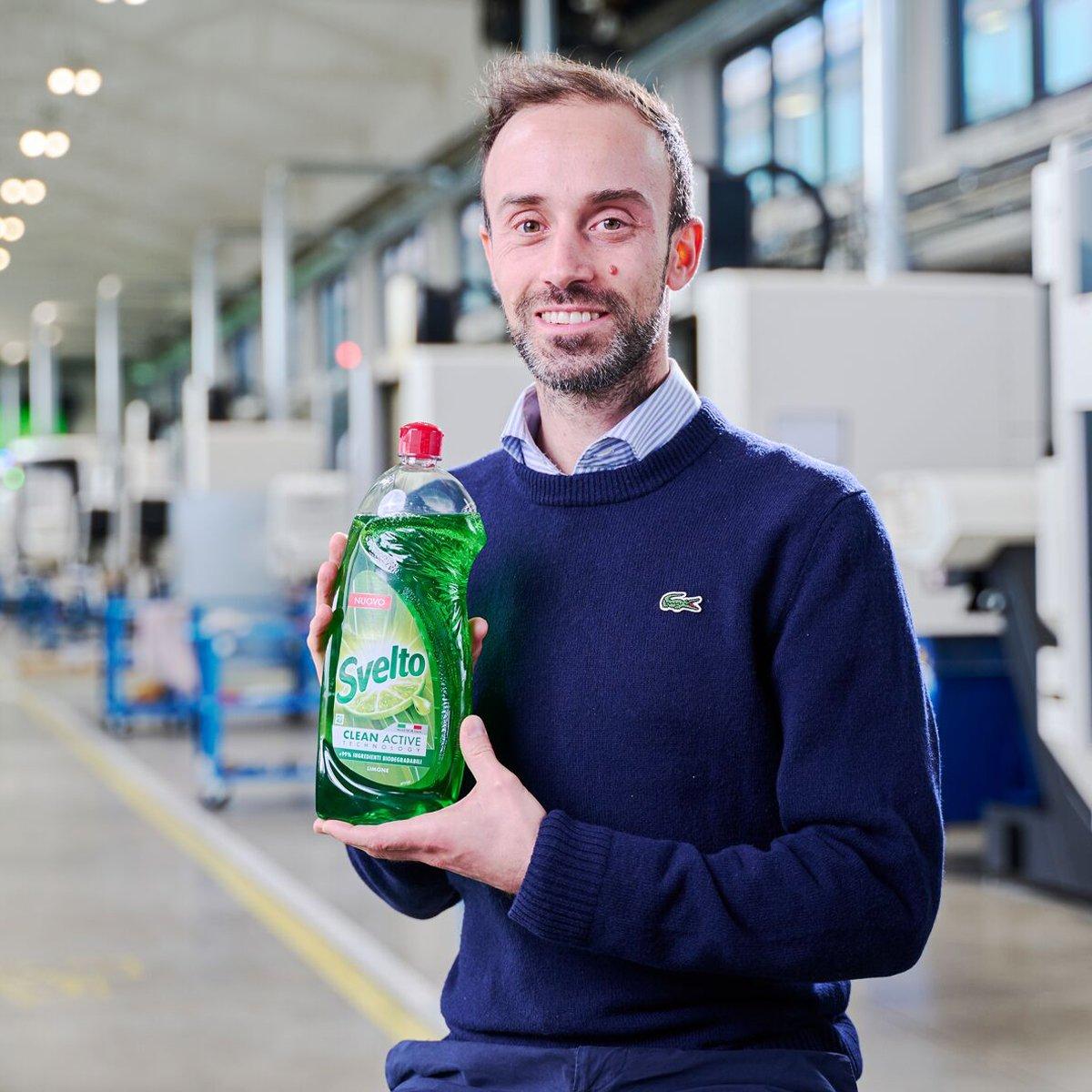
Réduisez les coûts et les délais pour les tests d'emballages moulés par soufflage
Dans ce webinaire, l'expert en moulage par soufflage Flavio Migliarelli vous présentera le processus de travail étape par étape et vous expliquera les principaux avantages et domaines d'application des moules imprimés en 3D pour le moulage par étirage-soufflage.
Mouler par soufflage de vraies bouteilles 70 % plus vite et 90 % moins cher
L’impression 3D de bureau est une solution puissante pour fabriquer des outils rapidement et à moindres coûts. Elle nécessite un équipement très limité, ce qui évite l'usinage et libère le temps des opérateurs qualifiés pour d'autres tâches à forte valeur ajoutée. Grâce à l'impression 3D en interne, les fabricants et les concepteurs de produits peuvent introduire de l'outillage rapide dans le processus de développement des produits afin de valider les étapes de conception et de fabrication avant de passer à la production en série. Les moules imprimés en 3D sont déjà utilisés dans des processus tels que le moulage par injection ou le thermoformage afin d'itérer rapidement, d'accélérer le développement et de mettre de meilleurs produits sur le marché.
L'impression 3D stéréolithographique (SLA) est un excellent choix pour le moulage. Les pièces présentent une finition de surface lisse et une précision élevée, qui sont transférées de l'outil à la pièce finale et facilitent le démoulage. La Form 3L est une imprimante 3D SLA grand formatqui permet de fabriquer des pièces et des moules à grande échelle, tout en étant suffisamment compacte pour tenir sur un bureau.
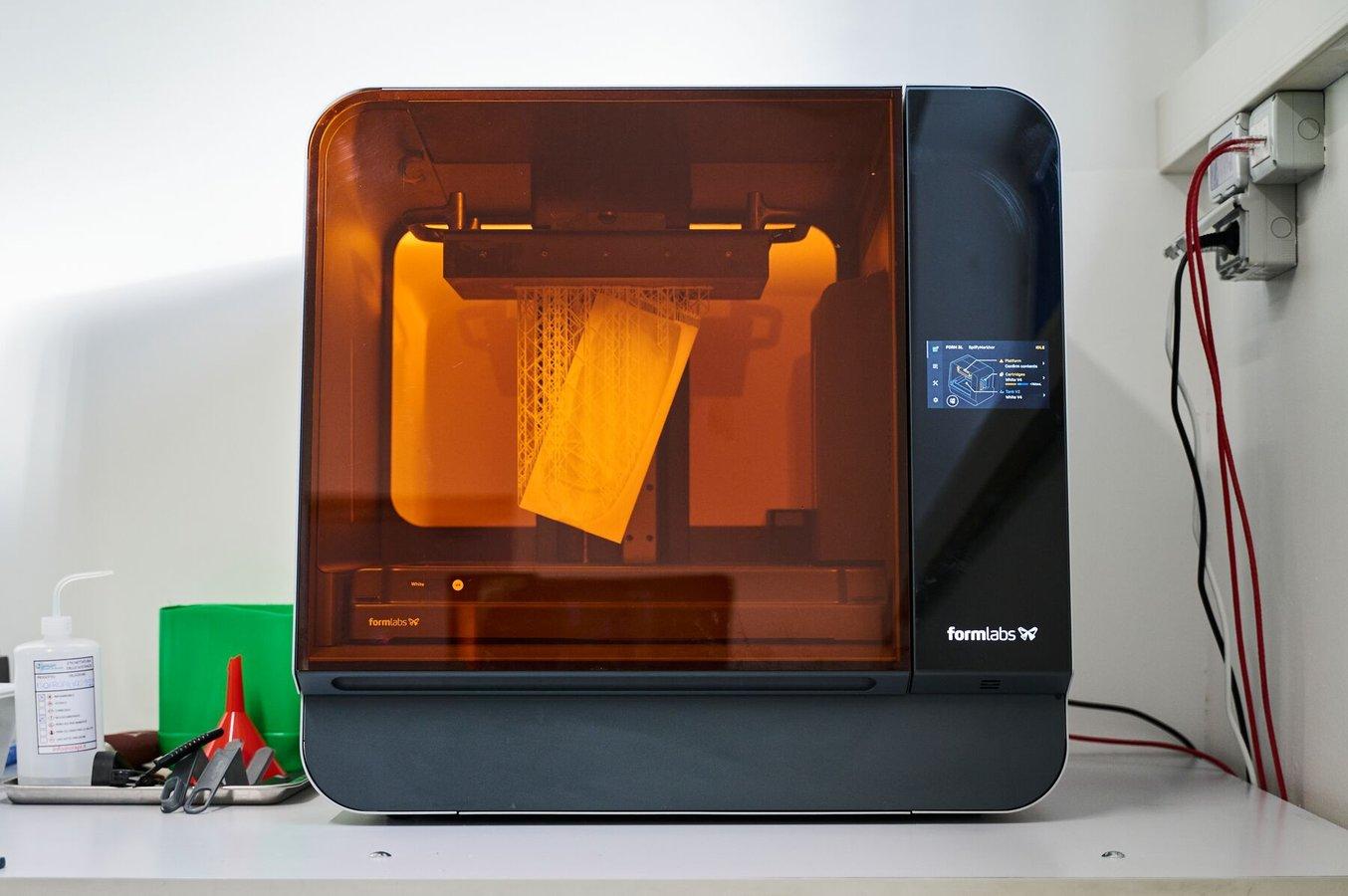
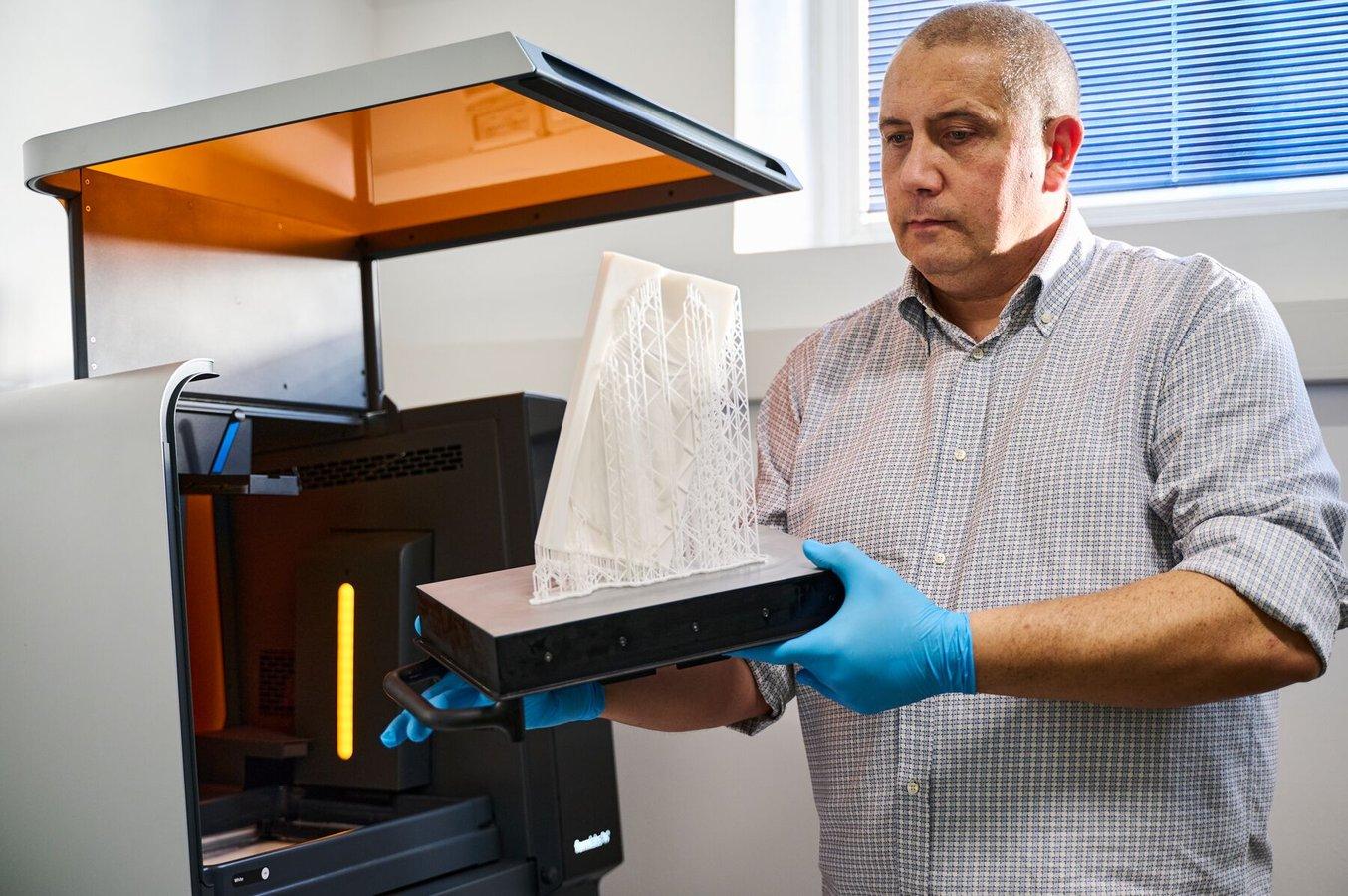
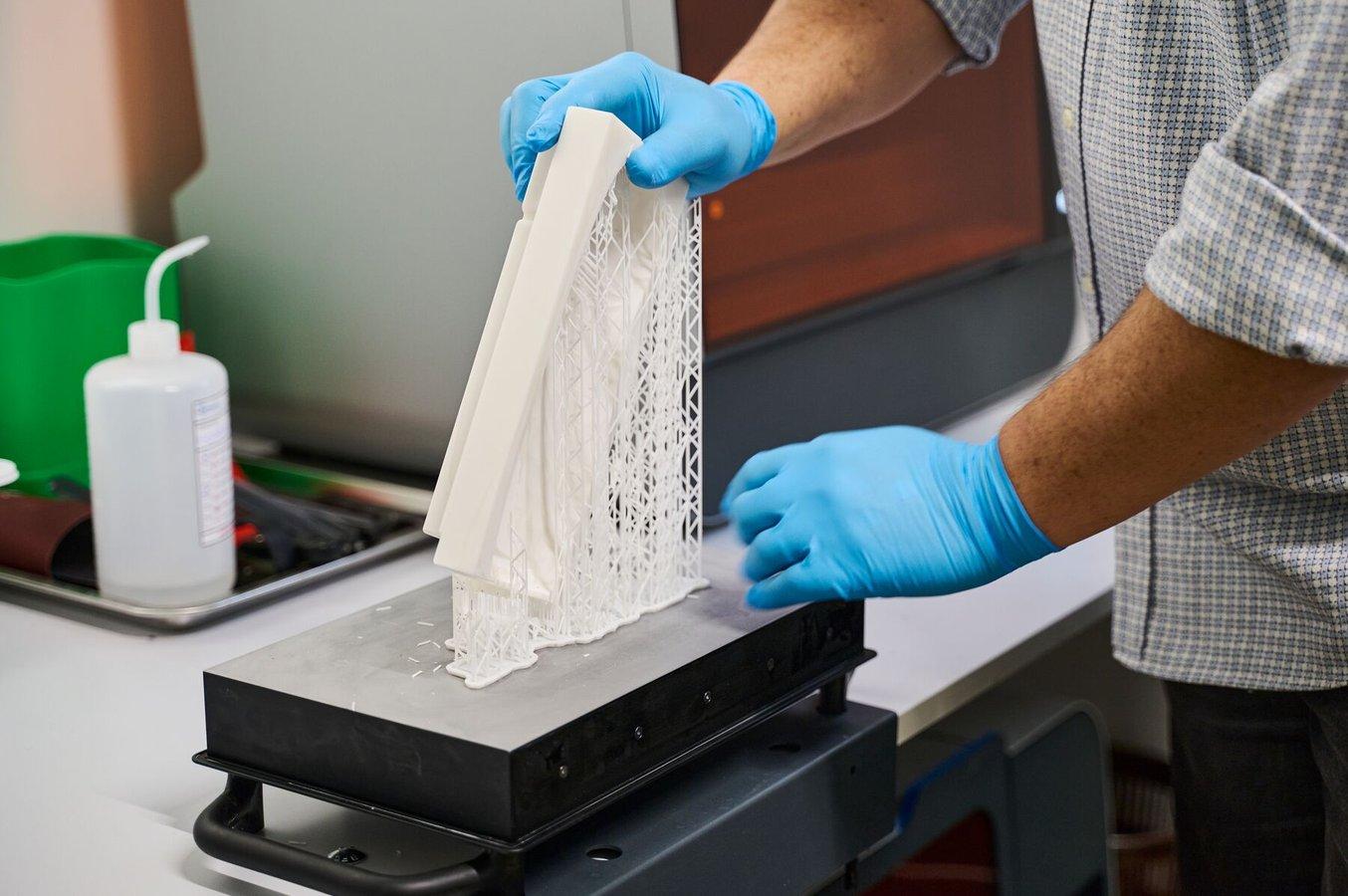
Le moule est imprimé en 3D sur la Form 3L avec Rigid 10K Resin.
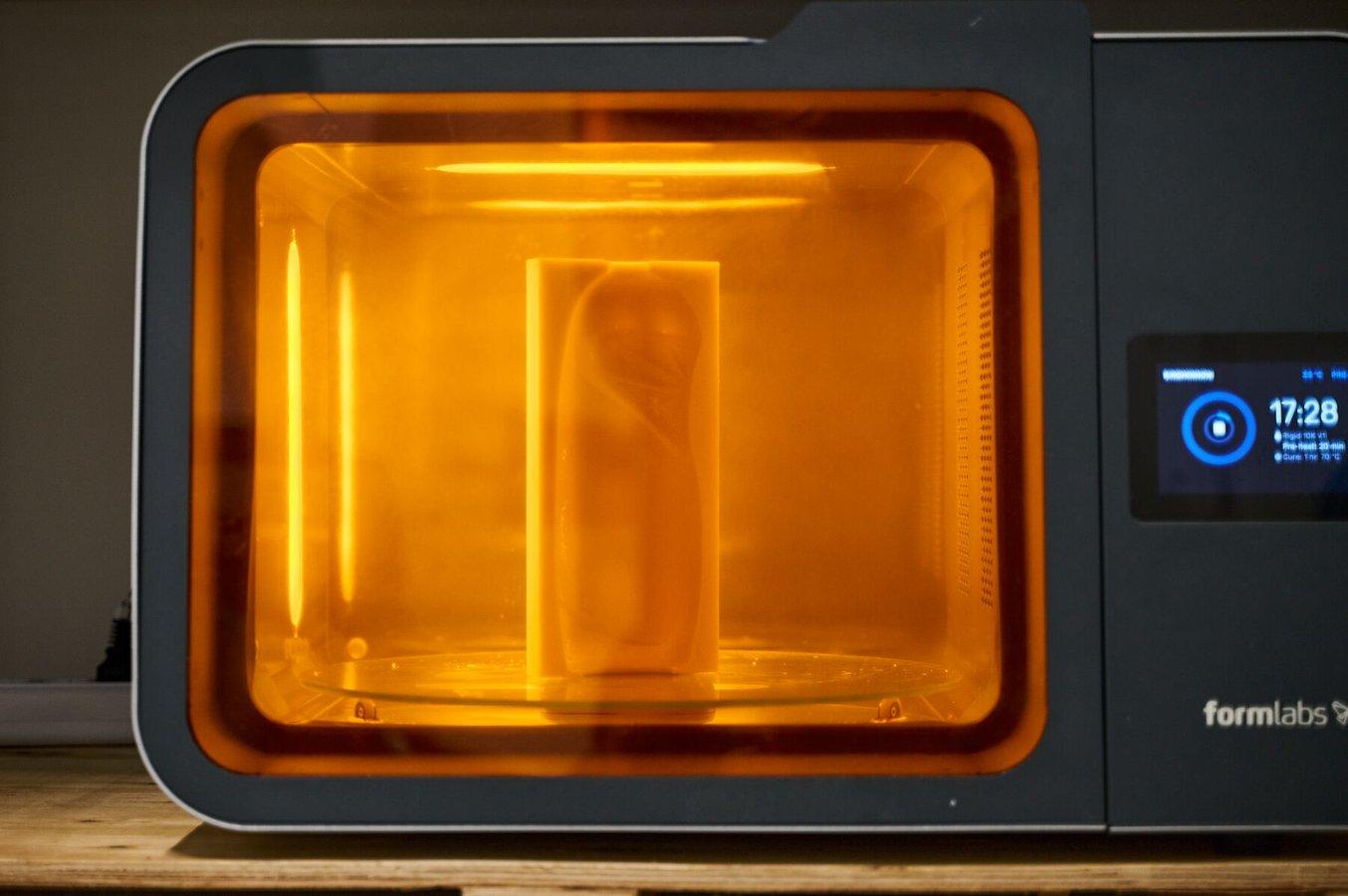
Après le lavage, les supports sont retirés et le moule est post-polymérisé.
Le choix des matériaux est crucial pour la production des moules. Unilever and Serioplast avaient besoin d'un matériau capable de résister à la pression interne et à la température du processus de moulage par étirage-soufflage, tout en assurant une bonne précision dimensionnelle et une bonne stabilité.
« Avec l'aide des ingénieurs de Formlabs, nous avons identifié le matériau qui pourrait nous donner la possibilité d'avoir quelques bouteilles dans les matériaux réels pour effectuer nos tests », a déclaré M. Cademartiri.
Rigid 10K Resin st le matériau recommandé par Formlabs pour le moulage par étirage-soufflage, car elle allie solidité, rigidité et résistance thermique. Il s'agit d'un matériau de qualité industrielle à charge élevée en verre, avec une TFC de 218 °C à 0,45 MPa et un module de traction de 10 000 MPa. L'outillage imprimé avec Rigid 10K Resin offre une bonne stabilité dimensionnelle et convient à des centaines de cycles de moulage par soufflage avec une grande répétabilité.
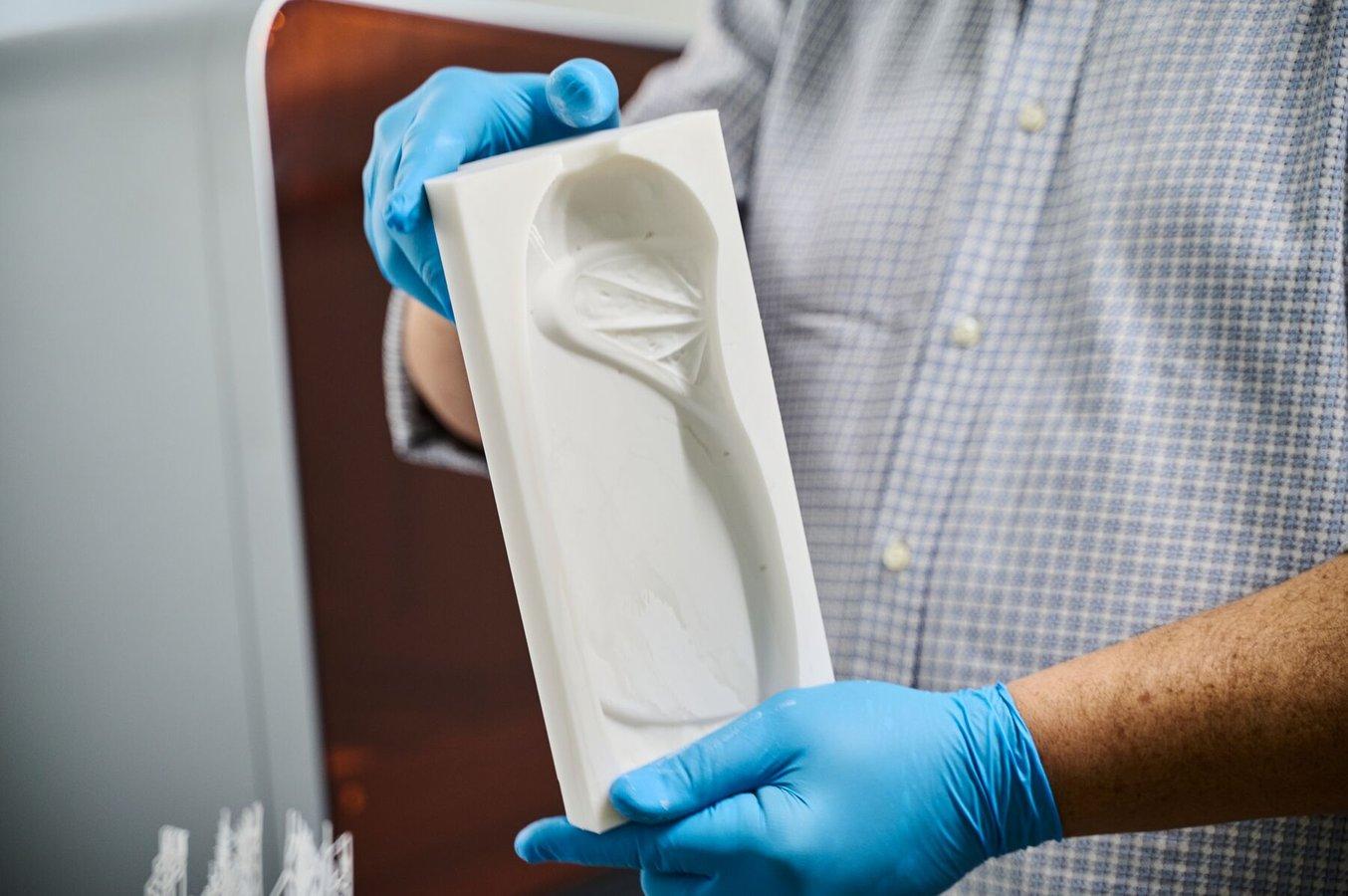
En utilisant Rigid 10K Resin, Serioplast a fabriqué des moules précis avec une finition de surface lisse, capables d'intégrer des caractéristiques fines, y compris des trous aussi petits que 0,5 mm. Ils ont ensuite traité l'outil à l'aide d'une machine à polir ou d'un ponçage manuel afin de respecter les dimensions critiques. Des surfaces texturées ont été incorporées dans la CAO de la cavité du moule.
« Le moule présente des détails ajustés avec précision, en particulier pour une bouteille avec des logos ou des motifs de citron qui exige un haut degré de précision. La machine Formlabs et Rigid 10K Resin permettent d'obtenir de très bons détails qui peuvent ensuite être transférés sur la bouteille réelle », a déclaré M. Cademartiri.
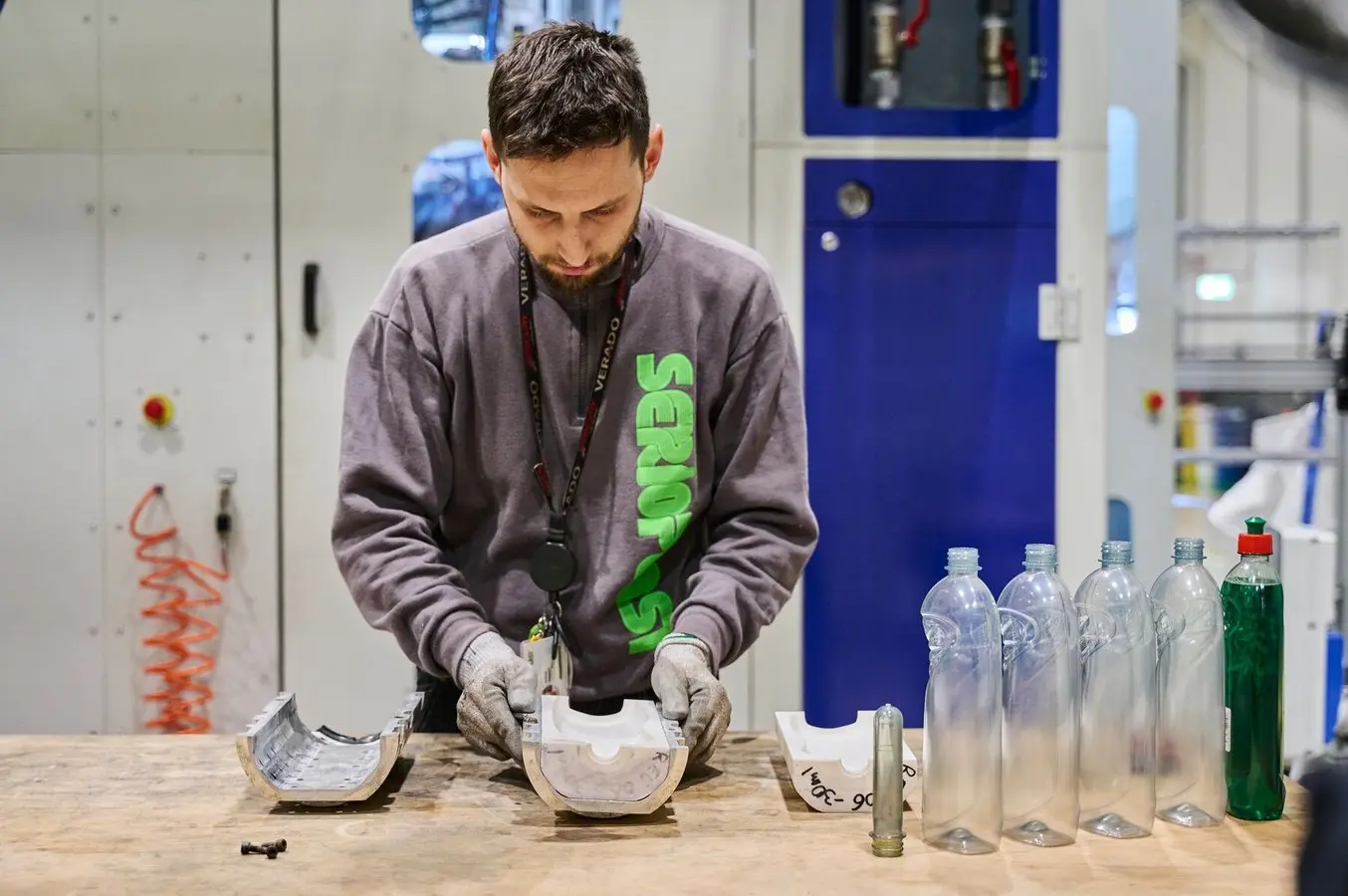
Le moule imprimé en 3D avec Rigid 10K Resin est poli manuellement puis assemblé dans un cadre métallique.
Avec l'impression 3D SLA, un moule peut être fabriqué en deux jours. Les moules imprimés en 3D réduisent le délai de lancement des essais pilotes de six à deux semaines, tout en permettant d'obtenir des pièces de préproduction réalistes dont la qualité est très proche de celle de la production et qui sont moulées avec les mêmes matériaux et les mêmes machines que les unités de production finales. En outre, les moules imprimés en 3D permettent aux opérateurs de tester plusieurs modèles simultanément.
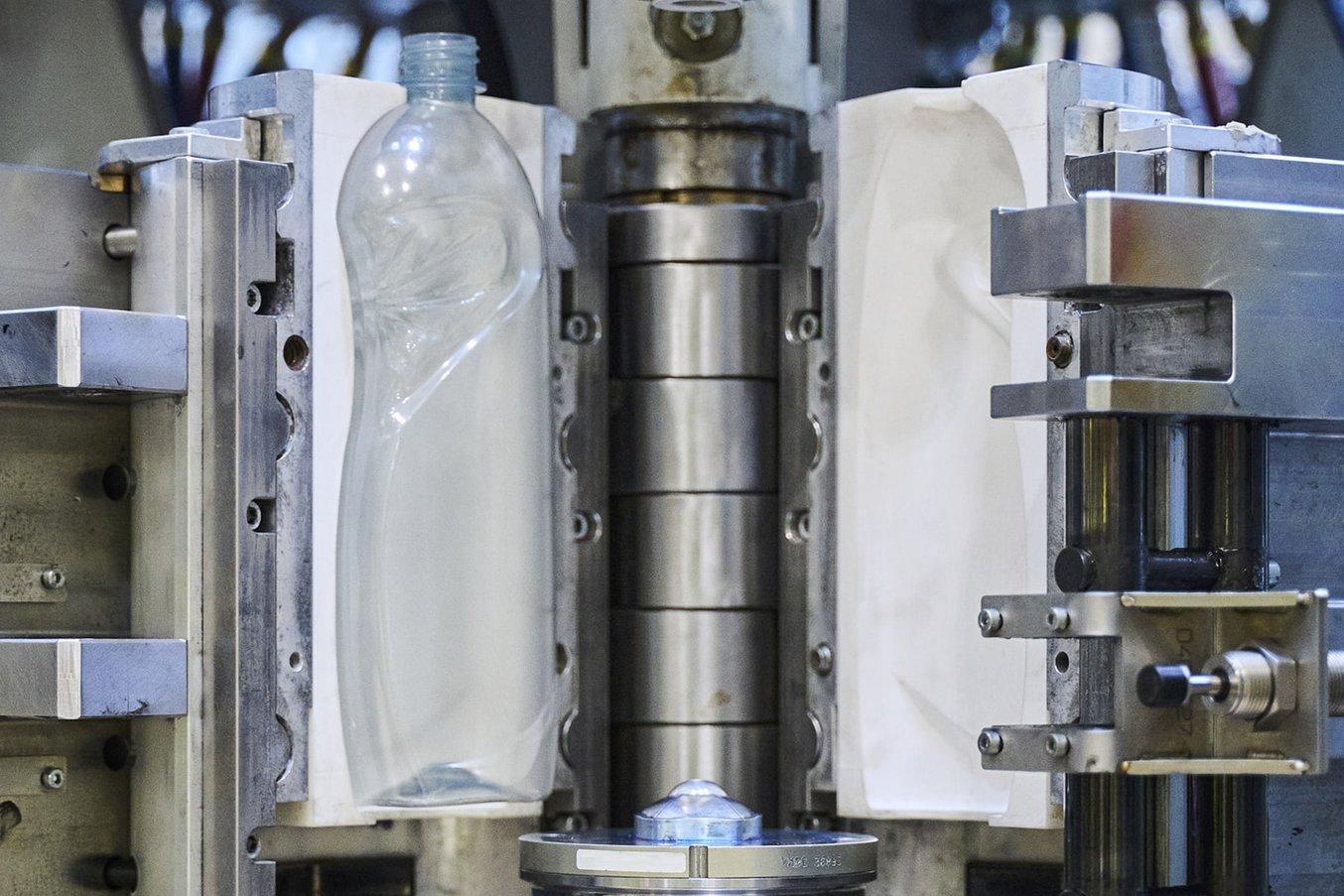
Moule imprimé en 3D avec Rigid 10K Resin pour la bouteille Unilever Slice 750 mL installé sur le porte-moule de la machine. Comme l'équipe peut utiliser la même fenêtre de processus qu'avec des moules pilotes standard, le processus final peut être vérifié de manière fiable.
« Avec le moule imprimé en 3D, nous devons simplement placer le moule dans un porte-moule qui est ensuite inséré dans la machine de moulage par soufflage. Nous gagnons ainsi beaucoup de temps sur la conception des moules et sommes en mesure de gérer notre calendrier d'impression 3D très facilement », a déclaré M. Migliarelli.
Production de 200 unités | Moule en métal usiné | Moule imprimé en 3D |
---|---|---|
Équipement | Machine CNC en interne ou sous-traitance | Form 3L Rigid 10K Resin |
Délai d'exécution des tests pilotes | 6 – 8 semaines | 2 semaines |
Coût de l'outillage | 2500 – 10 000 € | 500 – 1000 € |
« Avec le moule imprimé en 3D, nous pouvons économiser jusqu'à 70 % de temps et 90 % de coûts par rapport au moule standard. Auparavant, [les clients] devaient attendre jusqu'à 12 semaines pour un seul design, alors que maintenant nous pouvons en faire cinq.
Flavio Migliarelli, responsable de la conception R&D, Serioplast Global Services
Il est pratiquement impossible d'effectuer des tests aussi poussés avec les méthodes traditionnelles. L'entreprise devrait faire fabriquer à grands frais un moule métallique spécifique pour chaque design, et les coûts d'outillage ne seraient jamais rentables, faute d'économies d'échelle.
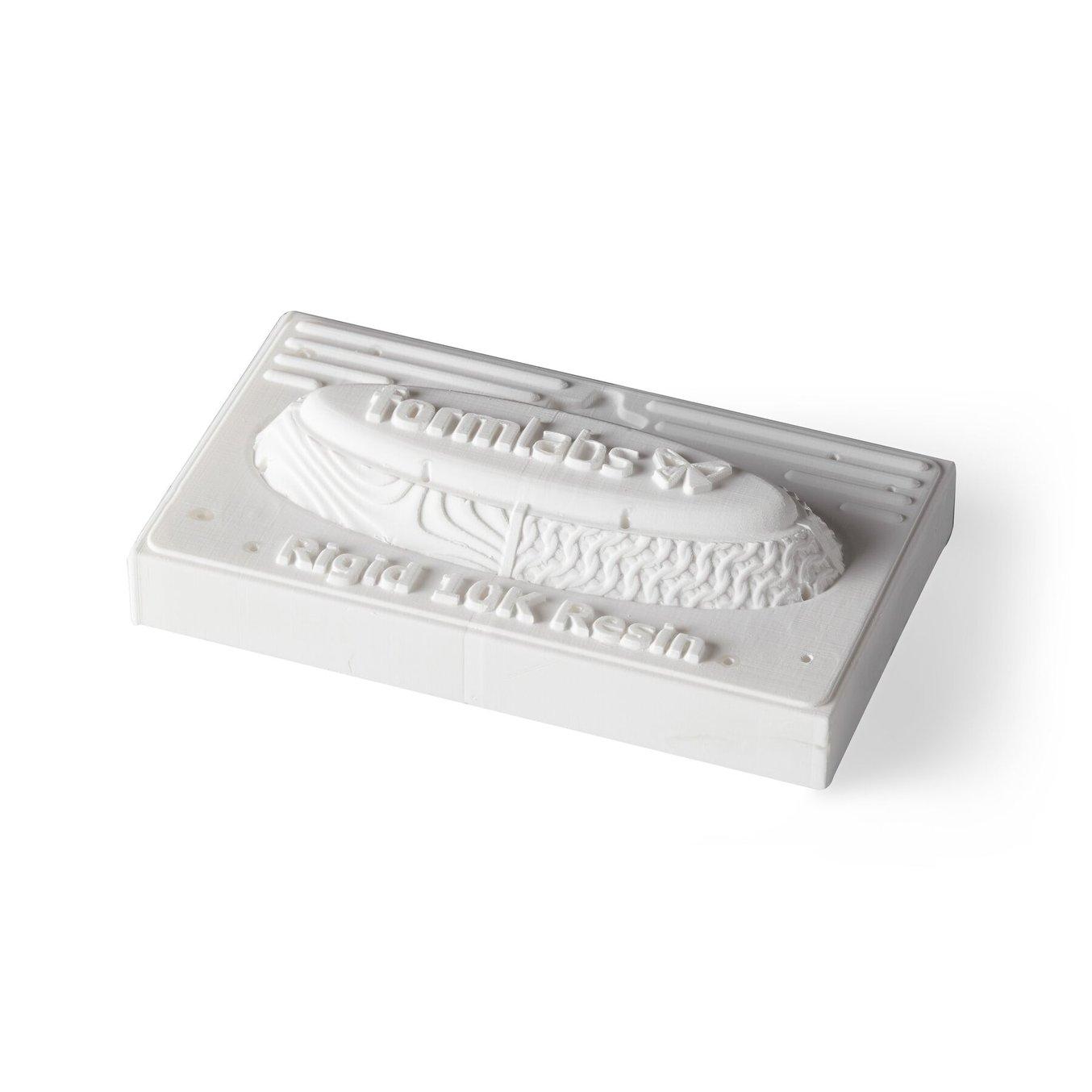
Commander un échantillon gratuit
Examinez et constatez par vous-même la qualité Formlabs. Nous enverrons un échantillon gratuit à votre bureau.
Des tests clients à l'ajustement de la chaîne de production
Les outils imprimés en 3D sont principalement utilisés pour produire des échantillons destinés à être testés par les consommateurs. Ils reproduisent la sensation, l'esthétique et les fonctions du produit final, et sont perçus comme le vrai produit aux yeux du consommateur.
« On peut fabriquer une vraie bouteille avant de produire le moule final. On peut ainsi savoir immédiatement si l'on est sur la bonne voie en matière de développement ou si quelque chose doit être modifié pour éviter des erreurs qui pourraient nous coûter cher. »
Stefano Cademartiri, responsable CAO et prototypage, Unilever
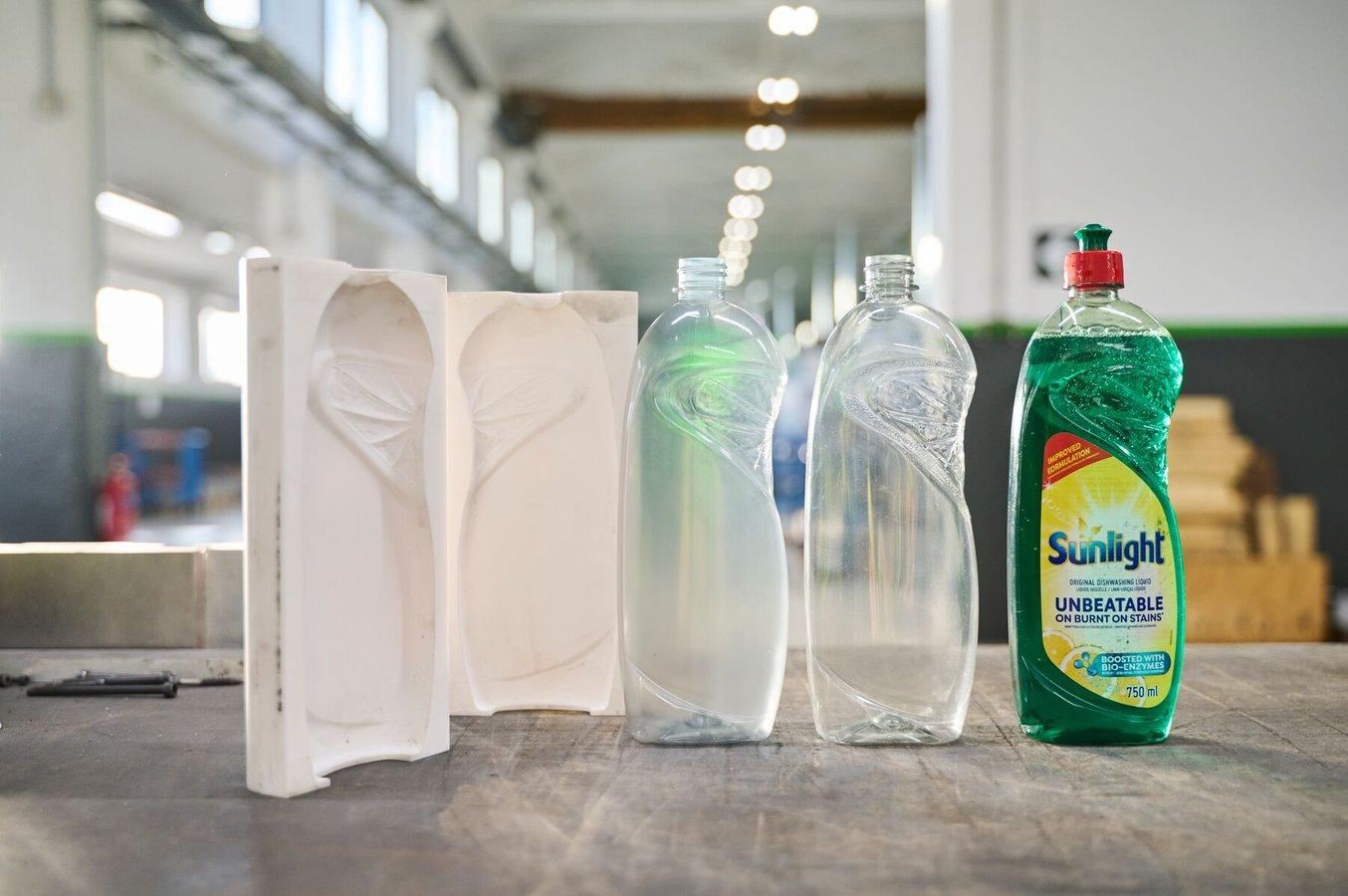
Les bouteilles produites à l'aide d'un outil imprimé en 3D sont pratiquement impossibles à distinguer du produit final fabriqué à l'aide de processus d'outillage métallique traditionnels. De gauche à droite : le moule en deux parties imprimé en 3D avec Rigid 10K Resin, une bouteille produite avec le moule en Rigid 10K Resin, une bouteille produite avec un moule en métal et un prototype étiqueté d'une bouteille pour des tests consommateurs.
Une autre utilisation de l'outil de moulage modulaire est la validation du processus d'étirage-soufflage et de la préforme en PET qui est traitée. Les fenêtres du processus, le taux d'étirage et la répartition du matériau pouvant être obtenue sont étudiés à cet effet. Serioplast produit les préformes en interne par moulage par injection. Si certaines préformes sont fabriquées sur mesure pour une bouteille spécifique, elles fonctionnent généralement avec des articles standardisés que les utilisateurs ne peuvent pas modifier. L’équipe de Serioplast souhaitait en apprendre davantage sur les capacités de la préforme standard. Ces informations leur permettent de déterminer si une préforme donnée est adaptée au moulage par soufflage d'une bouteille spécifique avant d'entrer en production.
« Nous utilisons la même fenêtre de processus que pour un moule pilote standard. C'est une excellente chose, car nous pouvons tester les fenêtres du processus final et voir ce qu'il advient de la bouteille. Il s'agit d'une pression d'environ 30 bars. Le moule est excellent et très fiable pour cela. De plus, la préforme est chauffée à 100 °C sans que la cavité du moule imprimée en 3D ne présente la moindre trace d'usure. Nous pourrions très facilement produire jusqu'à 100 ou 200 bouteilles par jour. Avec plus de temps, nous pourrions tout aussi bien aller jusqu'à 1000 », a déclaré M. Migliarelli.
La troisième application pour les moules fabriqués rapidement est le contrôle de certains aspects de la chaîne de production dès le début de la production. Étant donné que les bouteilles fabriquées à l'aide de moules imprimés en 3D sont très proches des produits finaux, elles se prêtent également aux premières validations de la ligne de remplissage. Par exemple le mouvement de la ligne, le fonctionnement des roues en étoile pour les machines d'embouteillage, le capsulage ou le mouvement de l'encaisseuse robotisée. L'essai pilote de la chaîne de fabrication permet aux usines d'anticiper les pièces de rechange, de préparer la chaîne pour la production de masse et d'accélérer la mise sur le marché.
Lancer plus rapidement de meilleurs produits sur le marché
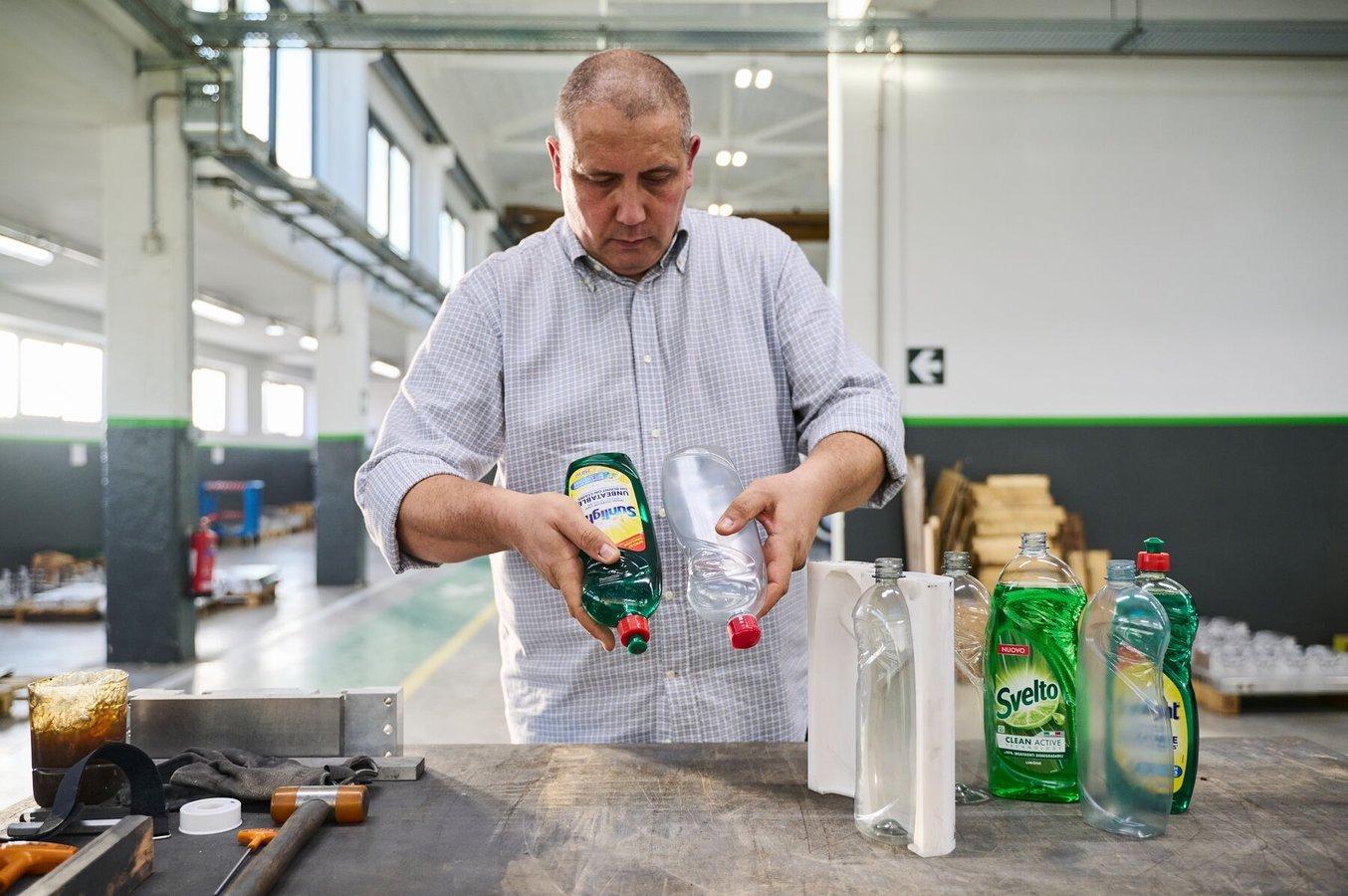
Cademartiri et Serioplast ont déjà testé une quinzaine de modèles de bouteilles avec le nouveau procédé.
Grâce aux imprimantes SLA de Formlabs et à Rigid 10K Resin, Unilever et Serioplast ont pu réduire les délais de 70 % et les coûts d'outillage de 90 % pour produire des séries pilotes de 200 unités en seulement deux semaines.
« Nous avons trouvé en Formlabs un partenaire formidable qui ne se contente pas de nous vendre la machine, mais qui nous aide aussi à explorer les propriétés des matériaux. Ce partenariat m'a permis de me lancer dans l'utilisation des moules imprimés en 3D », a déclaré M. Cademartiri.
Le nouveau flux de travail permettra à Unilever de mettre plus rapidement de meilleurs produits sur le marché et de réduire considérablement les risques et les coûts liés au développement des emballages.
M. Cademartiri résume ainsi son expérience : « Le mieux avec notre imprimante 3D, c’est qu'elle transforme nos rêves en réalité. On voit quelque chose à l'écran et, peu de temps après, on le tient dans la main. Un vrai produit, avec une vraie bouteille, un vrai bouchon et une vraie étiquette. »
Vous avez des questions sur l'utilisation d'une imprimante SLA pour le moulage par soufflage ou d'autres applications d'ingénierie et de fabrication ? Téléchargez notre livre blanc pour obtenir le flux de travail détaillé, contactez nos spécialistes en solutions ou commandez un échantillon gratuit de pièce imprimée en Rigid 10K Resin.