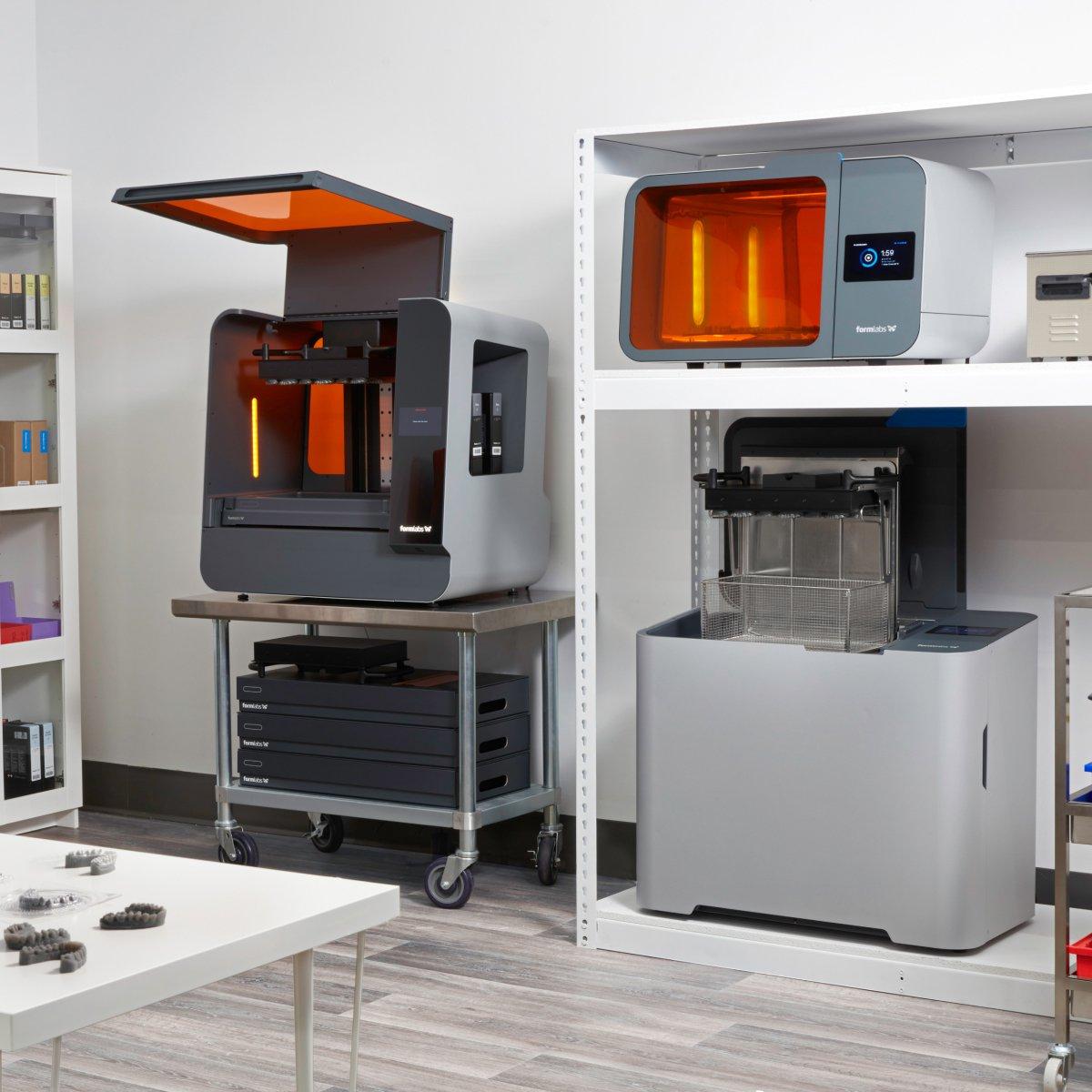
Prima del rilascio della Form Wash L e della Form Cure L, le opzioni per la post-elaborazione di parti di produzione di grandi dimensioni realizzate con la stereolitografia (SLA) erano limitate. La Form 3L e Form 3BL di Formlabs erano già usate da un gran numero di clienti, ma era ancora necessaria una soluzione per la post-elaborazione. Vi era una certa urgenza di progettare e produrre apparecchi abbinati per il lavaggio e la polimerizzazione.
Il team ingegneristico di Formlabs aveva bisogno di una soluzione di prototipazione flessibile e di alta qualità, oltre che della capacità di produrre parti per utilizzo finale robuste per design ancora in evoluzione. La risposta era davvero a portata di mano: la stampante SLS Fuse 1 e la Nylon 12 Powder.
Continua a leggere per scoprire come Formlabs ha usato la stampante Fuse 1 per la prototipazione e la produzione di parti delle unità di post-elaborazione Form Wash L e della Form Cure L.
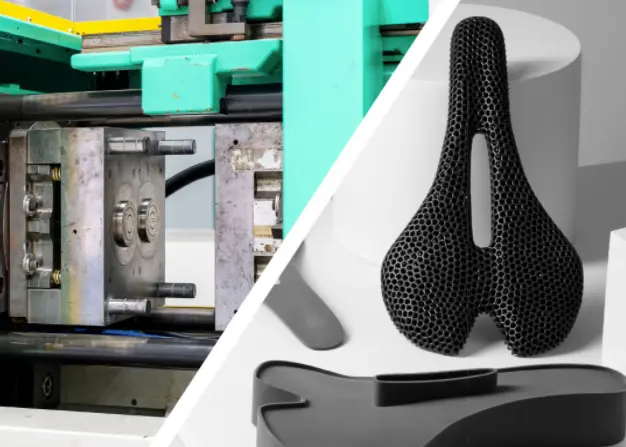
Stampa 3D SLS e stampaggio a iniezione: quando sostituire le parti stampate a iniezione con la stampa 3D?
Questo whitepaper illustra le dinamiche economiche in casi d'uso reali e raccoglie linee guida per l'utilizzo della stampa 3D SLS, dello stampaggio a iniezione o di entrambi.
Un workflow SLA completo per parti di grande formato
Abbiamo iniziato a spedire la Form 3L, la nostra stampante SLA di grande formato di punta, a settembre 2020. Per anni avevamo detto alla nostra clientela che l'unica soluzione per realizzare parti di grandi dimensioni era suddividere il file CAD a metà, stamparlo pezzo per pezzo e poi incollare il tutto. Col lancio della Form 3L, era finalmente possibile realizzarle in un'unica stampa senza dover rinunciare a precisione, finitura superficiale o gamma di proprietà dei materiali offerte dalle stampanti 3D SLA standard di Formlabs.
La Form 3L ha avuto un impatto immediato su ogni settore: i laboratori ortodontici potevano stampare fino a 120 arcate complete al giorno, le aziende di sviluppo del prodotto, come la Black Diamond, riuscivano a stampare prototipi di caschi a grandezza naturale, e gli ospedali erano in grado di stampare un modello anatomico di gabbia toracica di una persona adulta per gli studi preoperatori.
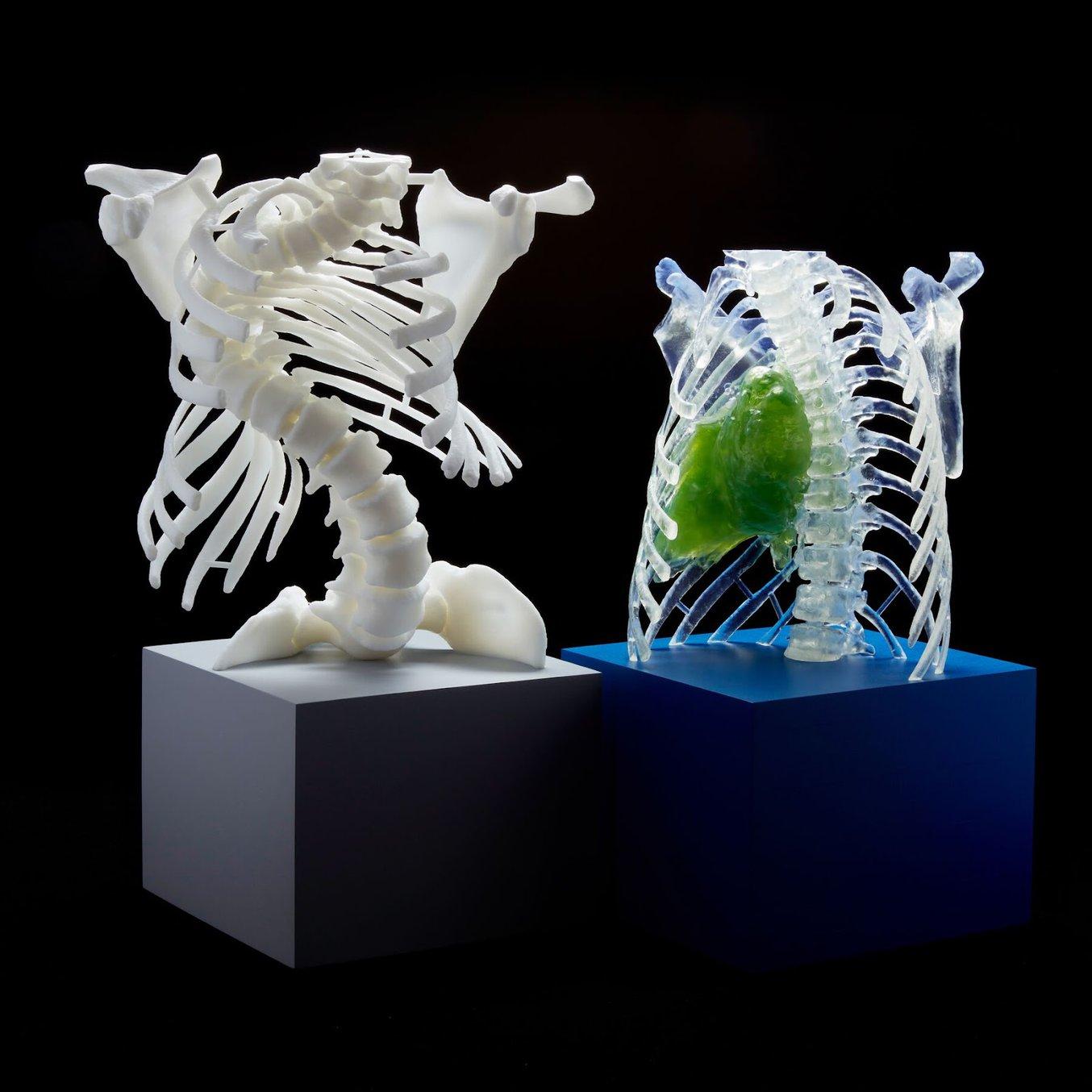
Tuttavia, tutti questi clienti risentivano di un workflow incompleto: il ritardo nella realizzazione di apparecchi abbinati per la post-elaborazione di parti di grande formato li ha portati ad acquistare opzioni da terze parti o a creare soluzioni fai da te, con risultati incostanti.
Prototipazione della Form Wash L e della Form Cure L con la Fuse 1
Il principio di base dei nuovi prodotti era chiaro: creare versioni più grandi dei sistemi Form Wash e Form Cure già esistenti. Ma esternalizzare la realizzazione di alcune parti era diventato difficile a causa dei problemi della catena di fornitura globale, aggravati dalla pandemia di COVID-19, che hanno causato il ritardo nella consegna di molti materiali necessari per la prototipazione.
"Abbiamo dovuto affrontare delle sfide. I tempi stretti rendevano molto complicata la preparazione dei materiali per le versioni di sviluppo. C'erano problemi legati alla catena di fornitura e dovevamo stare al passo con un calendario di consegne piuttosto intenso", afferma Megan Liu, Supply Chain Engineer di Formlabs.
Per fortuna, il team aveva una soluzione di qualità industriale a portata di mano sia per la prototipazione che per la produzione. Il sistema SLS Fuse 1 ha permesso al team addetto alla Form Wash L e alla Form Cure L di eseguire rapidamente molteplici iterazioni di ciascuna parte del design per entrambi gli apparecchi, anche quando certi processi di fabbricazione tradizionali non erano accessibili per questioni di costo o di tempi di realizzazione. Sei di quelle parti sono ancora stampate con la Fuse 1 e sono integrate nella versione di produzione dei prodotti finali.
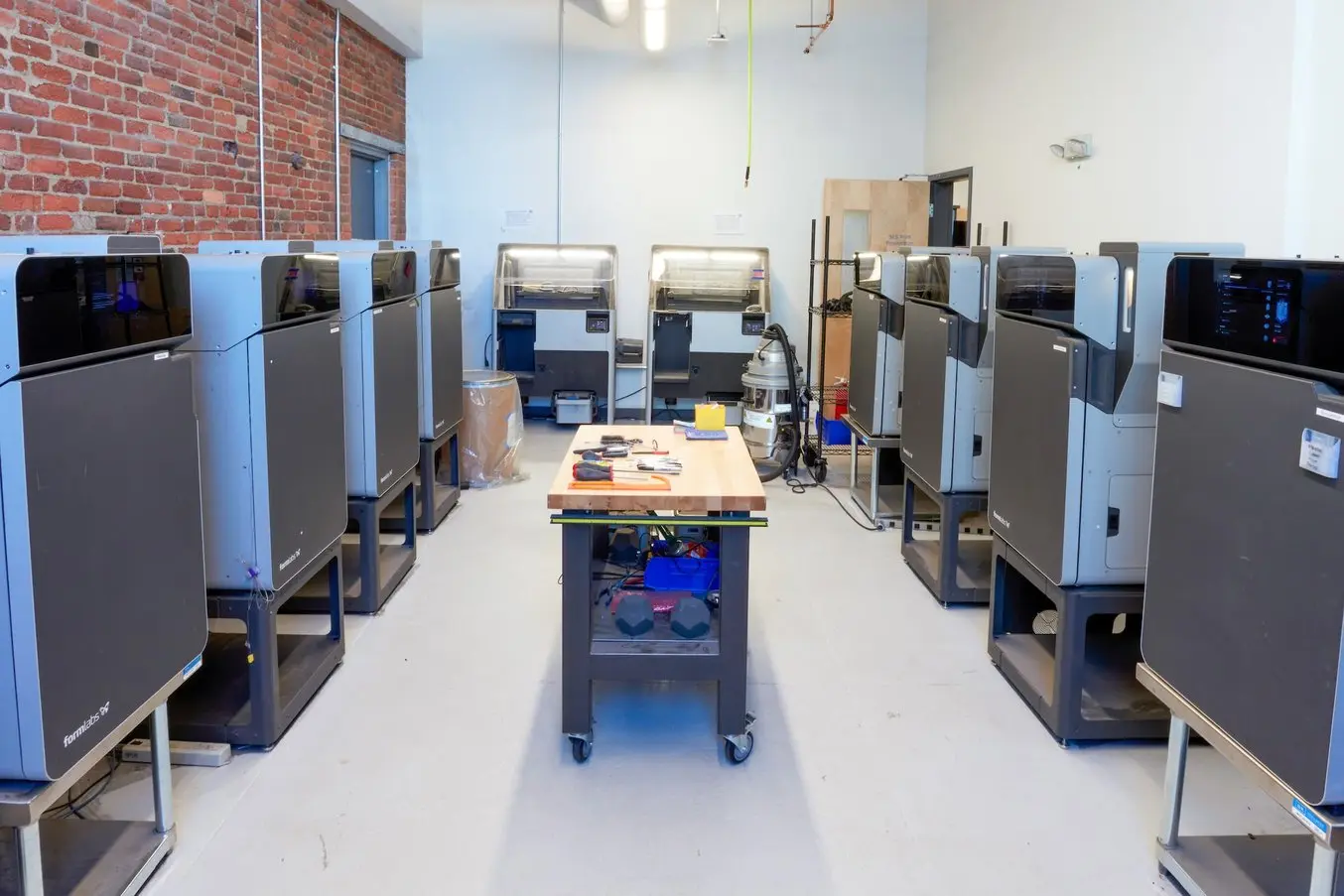
Produzione di parti della Form Cure L con la Fuse 1
Le Form Cure L spedite alla clientela includono tre parti stampate con la Fuse 1: l'ingranaggio della piattaforma rotante, il supporto dei magneti dello sportello e lo spaziatore di interblocco. Le Form Wash L hanno due diversi attacchi della pompa stampati con la Nylon 12 Powder sulla Fuse 1 e il primo ciclo di unità di produzione comprendeva anche un piccolo coperchio protettivo per il magnete. Non è la prima volta che i nostri team di approvvigionamento globale usano stampanti Fuse 1 per produrre parti per utilizzo finale per i prodotti Formlabs: alcune parti delle unità di produzione della Fuse 1 stessa sono state stampate presso il centro di fabbricazione Formlabs su Fuse 1 già disponibili.
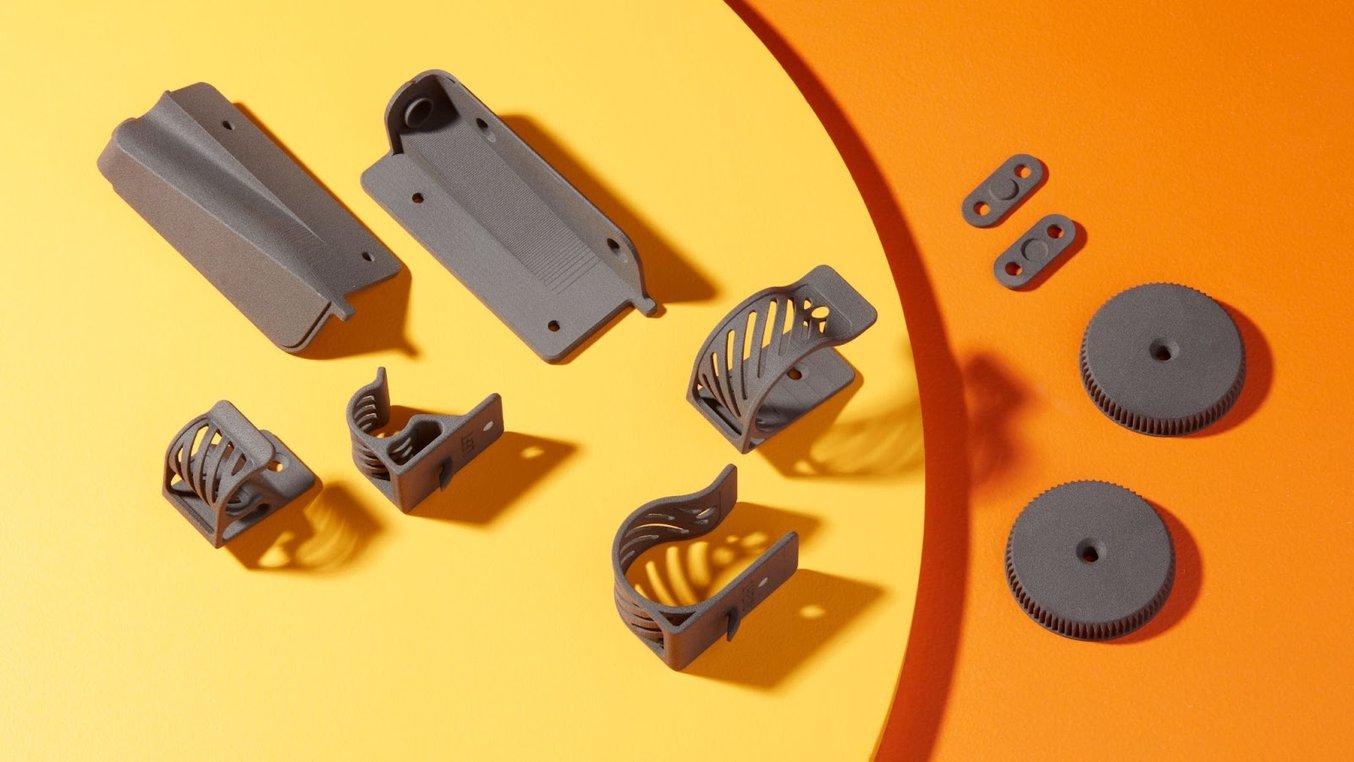
Per progettare l'ingranaggio della piattaforma rotante della Form Cure L, il team ha realizzato molteplici iterazioni per assicurarsi che il foro smussato al centro fosse in grado di stringere saldamente la piattaforma rotante e di generare una forza sufficiente per far ruotare la piattaforma. Dopo svariati design e prototipi, il team ha deciso di realizzare la parte finale tramite stampa 3D, a causa del nucleo centrale: per realizzarlo tramite stampaggio a iniezione, sarebbe stato necessario uno stampo a due componenti. Al contrario, la stampa SLS ha permesso di realizzare il design in un unico pezzo.
"Se la dimensione del foro dell'ingranaggio non era corretta, la cambiavamo immediatamente. Riuscivamo ad adattare la parte molto velocemente, sistemando ciò che non andava bene e provando nuove soluzioni. Il passaggio da un'iterazione all'altra era molto più semplice, perché sapevamo che non era necessario cambiare strumenti o fornitori per ottenere una nuova iterazione", spiega Liu.
Per gli spaziatori di interblocco della Form Cure L, il team ha realizzato il prototipo con la stampante SLA Form 3 e stampato la parte finale con la Fuse 1. È stato necessario usare la plastica perché i sensori di interblocco funzionano al meglio quando non è presente metallo tra il magnete e il sensore stesso. Questa parte sigilla l'esterno a livello estetico, consente l'uso di una quantità minima di plastica davanti al sensore effettivo e stabilisce la distanza del sensore fungendo da quattro distanziatori isolanti. Il team è stato in grado di ridurre tempi e costi spostando ogni fase in-house, dal prototipo di fase finale al test di produzione, azzerando così i tempi di creazione delle attrezzature.
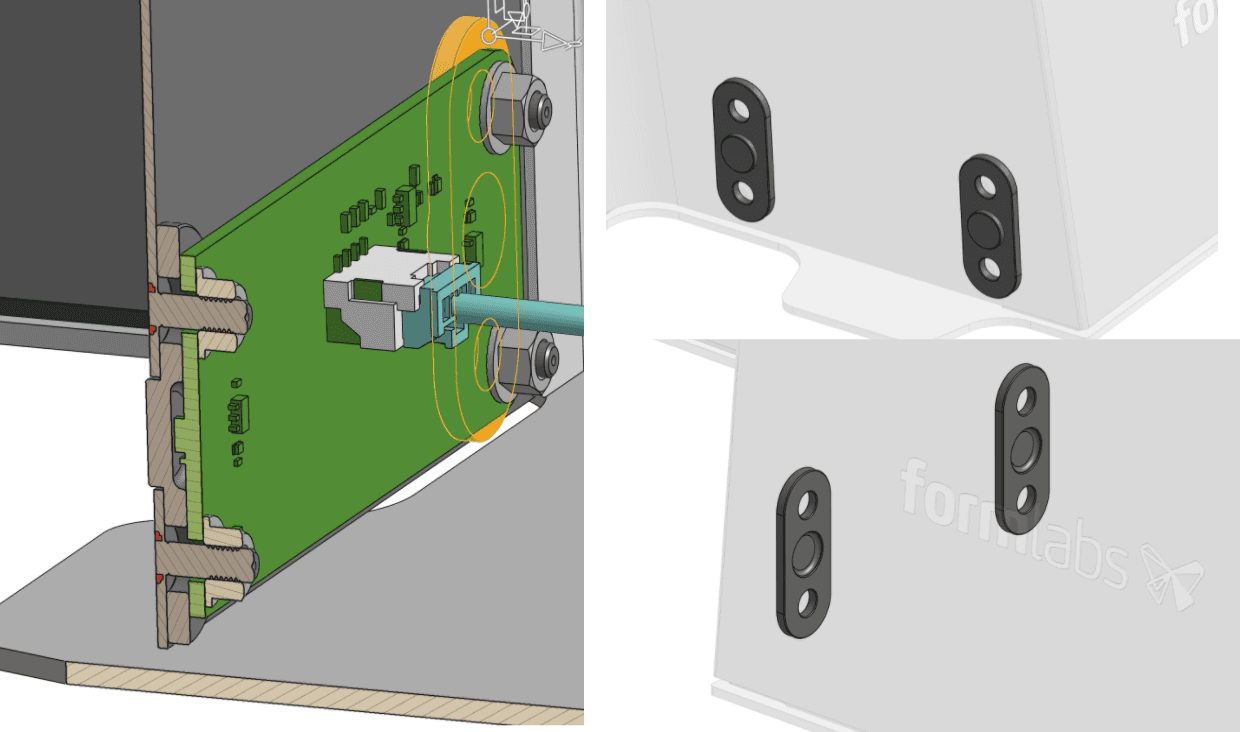
Parti di spaziatore di interblocco della Form Cure L, renderizzate in CAD.
Le ultime parti della Form Cure L realizzate con la Fuse 1 sono due supporti dei magneti dello sportello, responsabili della sospensione dei magneti che chiudono lo sportello della Form Cure L con uno scatto. Queste parti dovevano essere in plastica non solo per ragioni legate all'interferenza magnetica, ma anche all'aspetto tattile: una parte in metallo graffierebbe il rivestimento in polvere e produrrebbe fastidiosi rumori di attrito alla chiusura dello sportello. Poiché questa parte doveva rispondere a criteri sia oggettivi (l'effettiva chiusura dello sportello) che soggettivi (la sensazione provocata dalla chiusura dello sportello), è stato difficile stabilire un design prima che ogni altro elemento venisse finalizzato. Se il team avesse dovuto esternalizzare lo stampaggio a iniezione della parte, le tempistiche di produzione si sarebbero allungate di settimane. La stampa in-house ha permesso invece di stare al passo con le scadenze serrate.
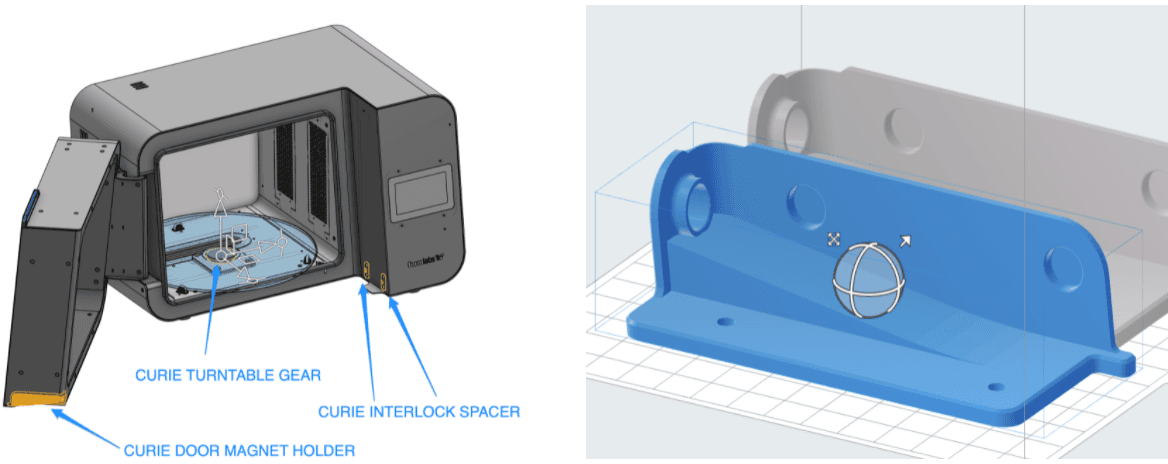
A sinistra, le tre parti della Form Cure L stampate con la Fuse 1. A destra, un ingrandimento del supporto dei magneti dello sportello.
Produzione di parti della Form Wash L con la Fuse 1
La Form Wash L è dotata di due attacchi per bloccare la pompa del solvente a batteria nel vano di stoccaggio. Sono progettati su misura per inserirsi attorno alla pompa e studiati per garantire l'efficienza dei materiali. Il loro design unico, caratterizzato da dettagli a spirale, non sarebbe stato possibile realizzare in modo tradizionale. Durante il processo iterativo, il team ha potuto apportare modifiche senza dover creare di nuovo le attrezzature. Poiché la parte è stata completamente riprogettata nel corso del ciclo di sviluppo, il team ha avuto molto più margine di manovra in termini di budget.
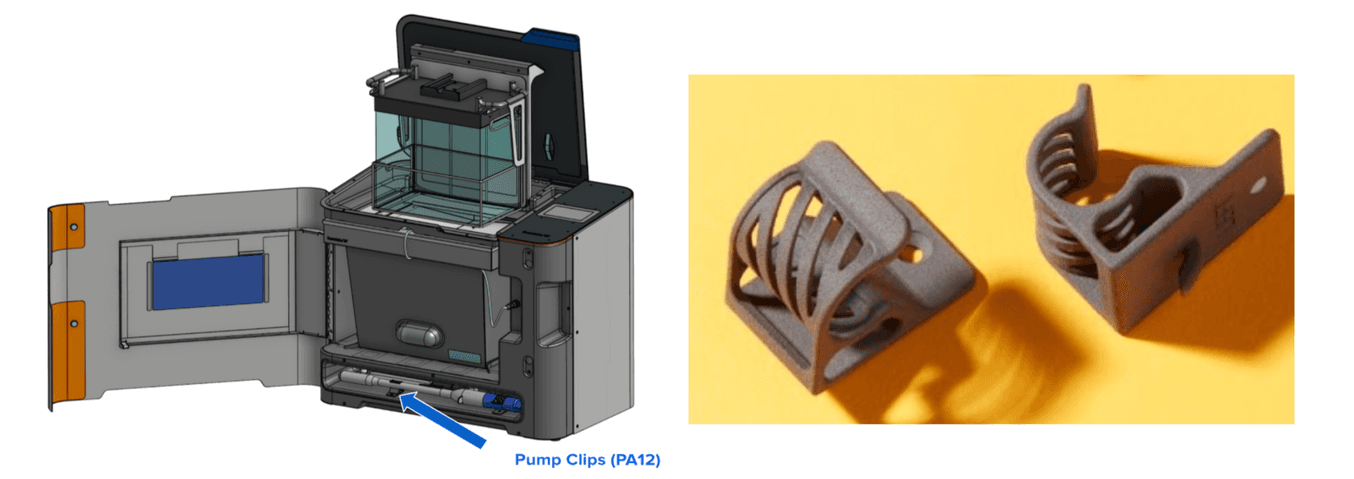
Nella Form Wash L, un magnete tiene il sistema di monitoraggio del solvente in posizione all'interno del recipiente di lavaggio. Per proteggere il magnete dalla ruggine o dai graffi, il team ingegneristico ha progettato un piccolo coperchio dedicato. La scelta di stampare le prime centinaia di unità di produzione della Form Wash L era provvisoria: al momento la parte è realizzata tramite stampaggio a iniezione. Nonostante i tempi di realizzazione fossero lunghi, aveva senso stamparle con la Fuse 1: grazie al suo algoritmo di posizionamento migliorato, questa parte di piccole dimensioni poteva essere inserita facilmente all'interno di altre più grandi.
Tempistiche più strette e catene di fornitura interrotte
Il calendario di produzione della Form Wash L e della Form Cure L ha coinciso con la pandemia di COVID-19, ma anche con problemi legati alla catena di fornitura che hanno compromesso la capacità del team di procurarsi i materiali e comunicare con i fornitori a contratto.
Liu e il resto del suo team hanno instaurato nel corso degli anni relazioni con diversi fornitori e solitamente riescono a trovare le parti necessarie in un modo nell'altro. Ma con i porti sovraccaricati, le fabbriche cinesi chiuse e le compagnie di trasporto alle prese con scioperi sindacali e personale ridotto a causa del COVID-19, qualunque opzione per l'approvvigionamento dei materiali di prototipazione era un vicolo cieco.
"La presenza delle stampanti in-house ci consente una grande flessibilità, anche quando siamo in attesa di campioni che alla fine produrremo con metodi tradizionali. L'uso di parti stampate in 3D era una misura temporanea per ottimizzare i tempi."
Megan Liu, approvvigionamento globale di Formlabs
A causa di questi ritardi, il team addetto alla Form Wash L e alla Form Cure L ha assistito a una drastica abbreviazione delle tempistiche: invece delle consuete 600 unità ogni sei settimane, doveva produrre 200 unità a settimana per rispettare la scadenza. Il parco stampanti di Formlabs dell'impianto di produzione di materiali in Ohio non era abbastanza grande, così il team ingegneristico di Formlabs ha spostato le operazioni di stampa nella sede di Somerville.
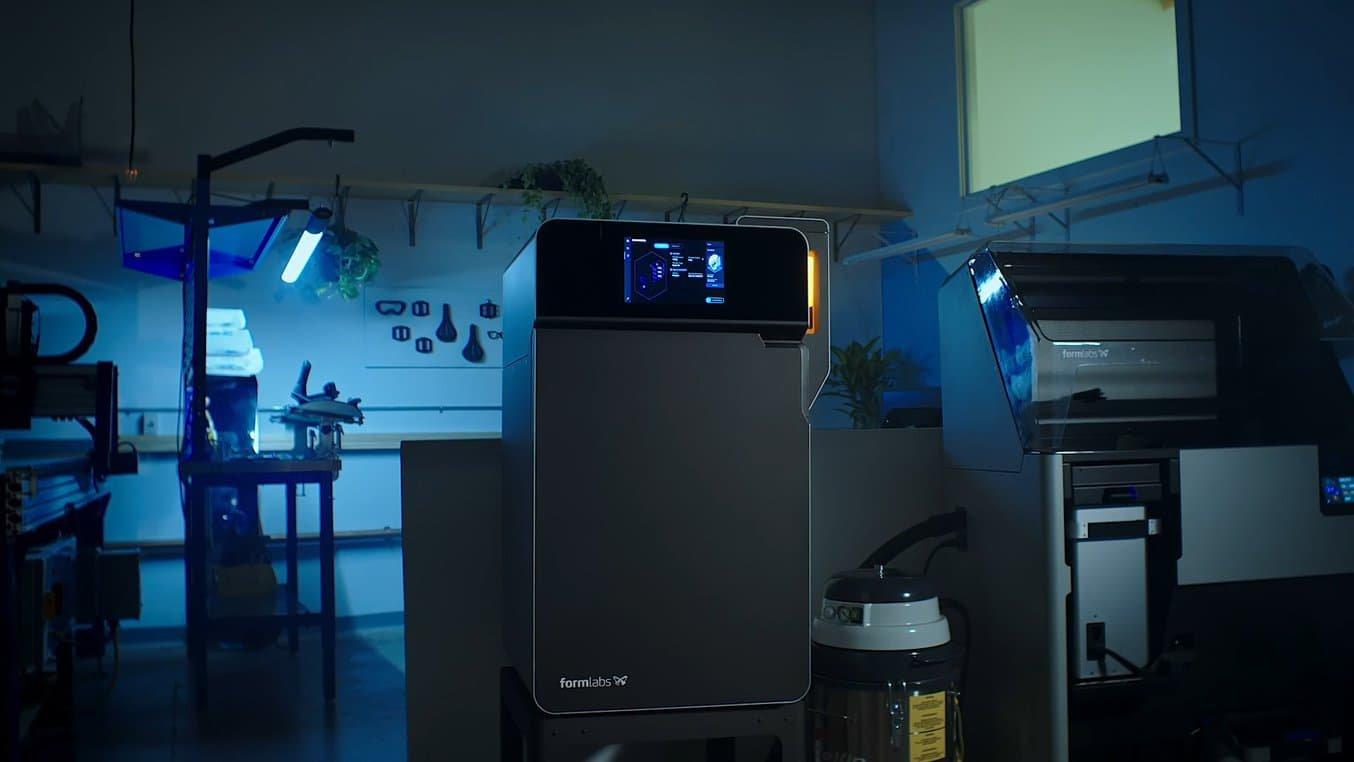
"Con le stampanti a portata di mano, siamo immediatamente riusciti a raddoppiare la capacità. Se avessimo esternalizzato e il fornitore avesse smesso di lavorare, non avremmo potuto semplicemente reindirizzare lo strumento a un altro fornitore; ma grazie alle stampanti, siamo immediatamente riusciti a decentralizzare la produzione e a incrementare la capacità per rispettare le scadenze", afferma Liu.
Quando e perché passare allo stampaggio a iniezione
Una volta che il team ha prodotto con successo quelle 600 unità, ha avuto modo di valutare le opzioni per una produzione completa con tempistiche e domanda consolidate. Sebbene abbia ancora senso produrre alcune parti con la Fuse 1, come i due attacchi della pompa, gli spaziatori di interblocco e l'ingranaggio della piattaforma rotante, per altre parti, come il coperchio protettivo del magnete, si è passati a un workflow con stampaggio a iniezione.
Di seguito analizziamo due esempi per dimostrare come si prende una decisione simile e quando ha senso passare dal workflow con stampa 3D SLS diretta a quello con stampaggio a iniezione tradizionale.
Parte 1: coperchio protettivo del magnete del sensore di saturazione (Form Wash L)
Lo stampo per il coperchio protettivo del magnete del sensore di saturazione sarebbe costato 3700 € e completarlo avrebbe richiesto più di un mese dall'inizio del programma di produzione, il che avrebbe ritardato le fasi iterative finali e i primi cicli di produzione della Form Wash L.
Il costo per parte (manodopera inclusa) della stampa con la Fuse 1 era di soli 2,20 €, un'alternativa più economica per quantità minori a 2000 unità. Il team di approvvigionamento globale ha stabilito che la stampa 3D SLS era un'ottima opzione di produzione momentanea, ma una volta realizzato lo stampo, ha capito che sarebbe stato più economico procedere con lo stampaggio a iniezione.
SLS | Stampaggio per parte | Costo attrezzature stampaggio | |
---|---|---|---|
Coperchio protettivo del magnete del sensore di saturazione | 2,20 € | 0,11 € | 3700 € |
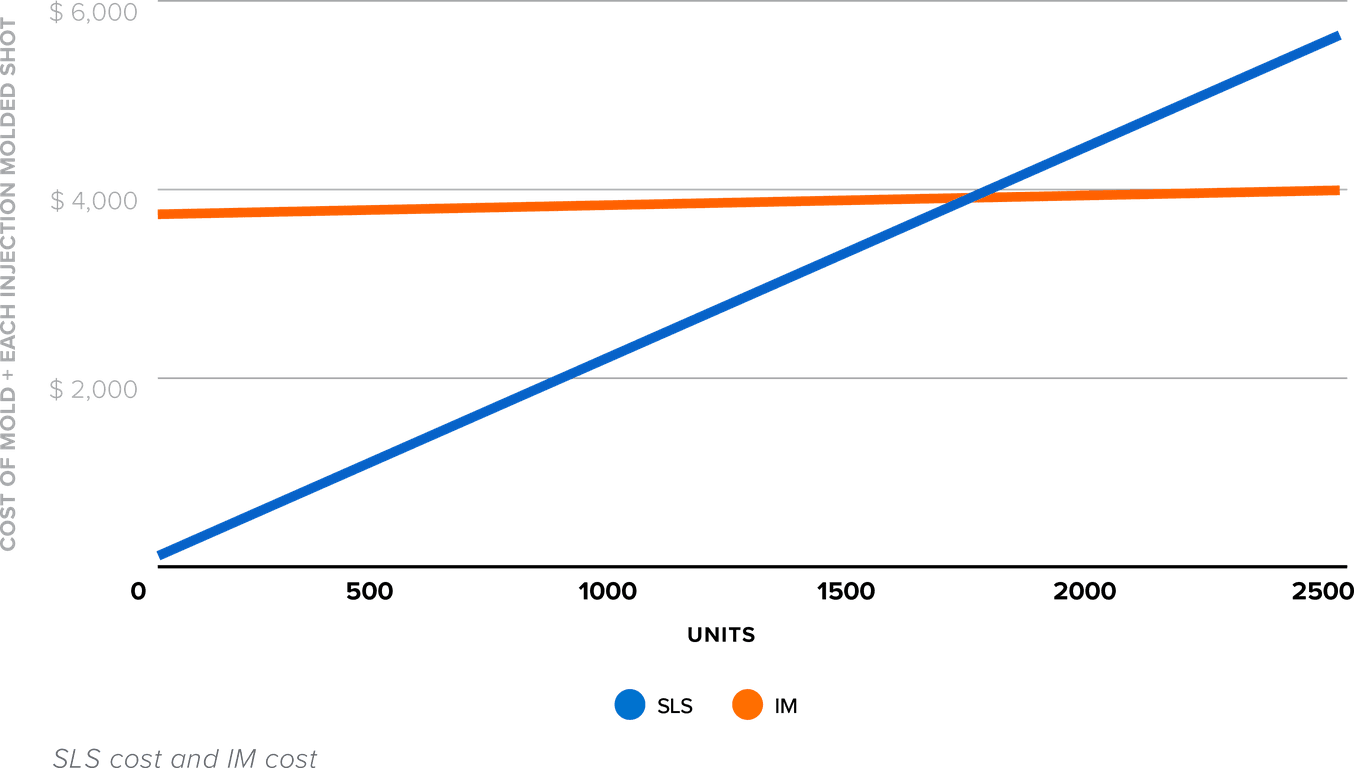
Parte 2: ingranaggio della piattaforma rotante
Questa parte presenta al centro un foro smussato che consente il fissaggio saldo dell'inserto della piattaforma rotante e la generazione di una forza sufficiente a far girare la piattaforma della Form Cure L.
Per realizzare il nucleo di questo design, sarebbe stato necessario uno stampo a iniezione in due componenti, che è decisamente più costoso. Il costo stimato dal produttore a contratto per lo stampaggio a iniezione era di 10 000 €.
SLS | Stampaggio per parte | Costo attrezzature stampaggio | |
---|---|---|---|
Ingranaggio della piattaforma rotante | 3,50 € | 2,20 € | 10 000 € |
La stampa 3D SLS dell'ingranaggio della piattaforma rotante ha permesso al team di progettazione di unire il design in un'unica parte. Il costo per parte era di soli 3,50 €, quindi il punto di pareggio con lo stampaggio a iniezione corrispondeva a circa 8000 unità. Il team ha deciso di stampare la parte con la Fuse 1, risparmiando migliaia di euro e riducendo il costo del prodotto finale. Lo sviluppo di questo livello di produzione darà al team di approvvigionamento globale tempo in abbondanza per pianificare, ordinare stampi e passare allo stampaggio a iniezione quando risulta più economico. La stampa 3D SLS di queste parti ha al momento permesso al team di velocizzare i tempi di avvio e concentrarsi su altre parti del prodotto.
Si può sostituire lo stampaggio a iniezione con la stampa 3D?
La flotta di stampanti Fuse 1 è una parte complementare della catena di fornitura. Sebbene abbia effettivamente sostituito i tradizionali metodi di produzione per alcune parti, la creazione di attrezzature convenzionale, la fusione, lo stampaggio e la lavorazione meccanica sono ancora elementi necessari del ciclo di vita di un prodotto. Potersi affidare a stampanti 3D di qualità industriale offre un maggior controllo ai produttori e li protegge da variabili esterne come il ritardo nella consegna di materiali grezzi o i lungi tempi di creazione delle attrezzature.
Le stampanti SLS Fuse 1 hanno permesso a Formlabs di consegnare due prodotti in tempi brevi, superando al contempo gli ostacoli posti dalla pandemia di COVID-19 e dai disservizi della catena di fornitura. Le unità di produzione della Form Wash L e della Form Cure L hanno, ciascuna, molteplici parti stampate con la stessa tecnologia Formlabs, a dimostrazione del fatto che la Fuse 1 è una soluzione completa di produzione e di sviluppo del prodotto. Nel whitepaper Stampa 3D SLS e stampaggio a iniezione: quando sostituire le parti stampate a iniezione con la stampa 3D?, abbiamo approfondito ogni possibile applicazione per le parti per utilizzo finale con la stampante SLS Fuse 1, dalle parti sostitutive alle protesi personalizzate, fino ad arrivare alle parti di motore per il mercato post-vendita.