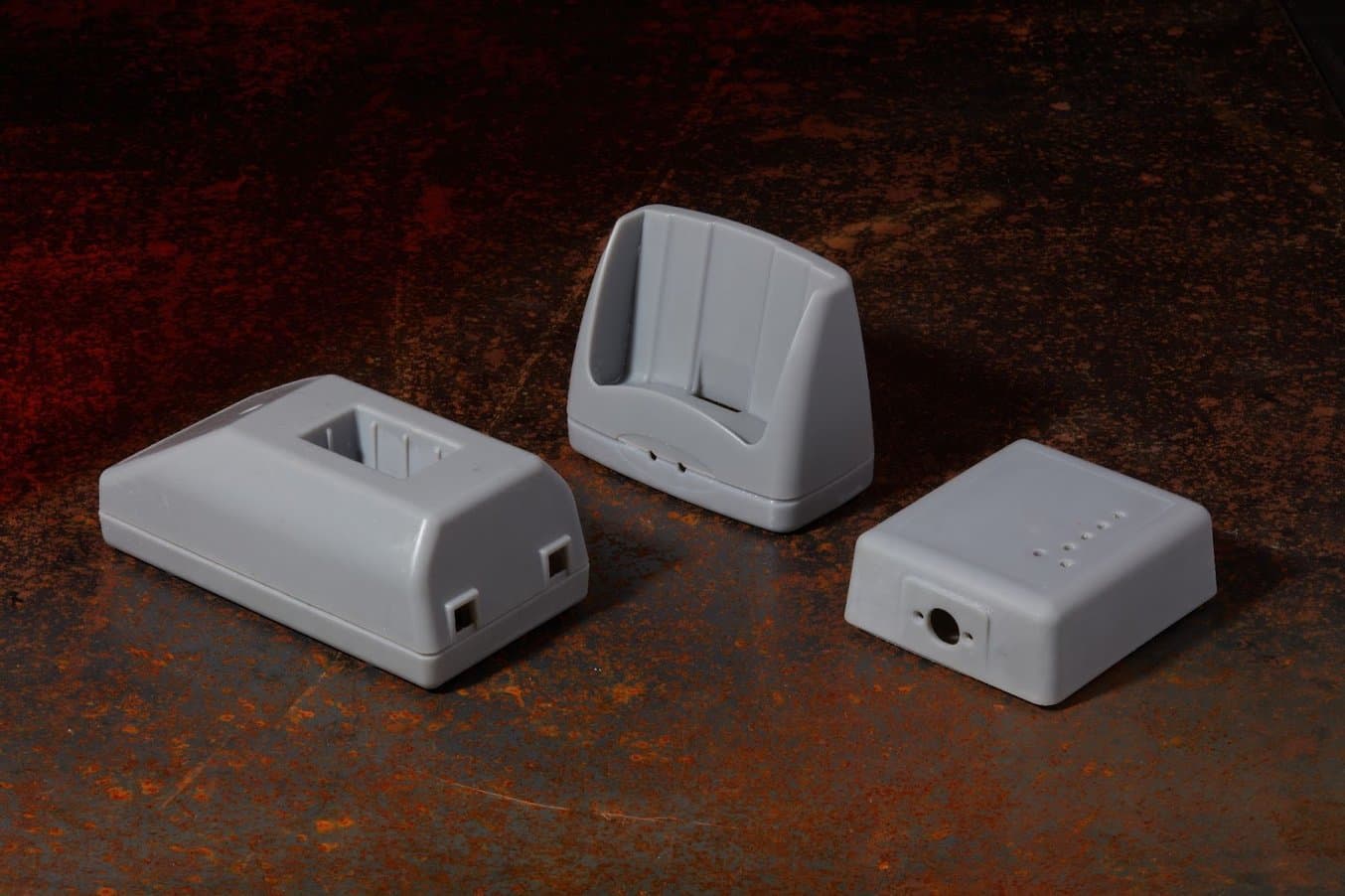
Avance Design, azienda di sviluppo prodotti e consulenza ingegneristica di Indianapolis, negli Stati Uniti, utilizza la stampa 3D da oltre vent'anni, ma ogni volta che viene sviluppato un nuovo materiale per la stampa 3D, vede aprirsi nuove opportunità e applicazioni.
Oltre alla fusione, allo stampaggio, alla lavorazione meccanica e alla stampa FDM, Avance utilizza tre stampanti SLA Form 3+ e due Form 3 per sviluppare prodotti per la medicina, la robotica, l'architettura e l'elettronica. Da quando utilizza la nuova Flame Retardant Resin di Formlabs, Avance ha accorciato il proprio ciclo di sviluppo e ridotto i costi e la manodopera associati alla produzione di parti con certificazione UL 94.
Tony Parker, direttore di Avance, ci ha parlato di produzione con volumi ridotti, di personalizzazione di massa e di una produzione di successo per un cliente resa possibile dalla Flame Retardant Resin.
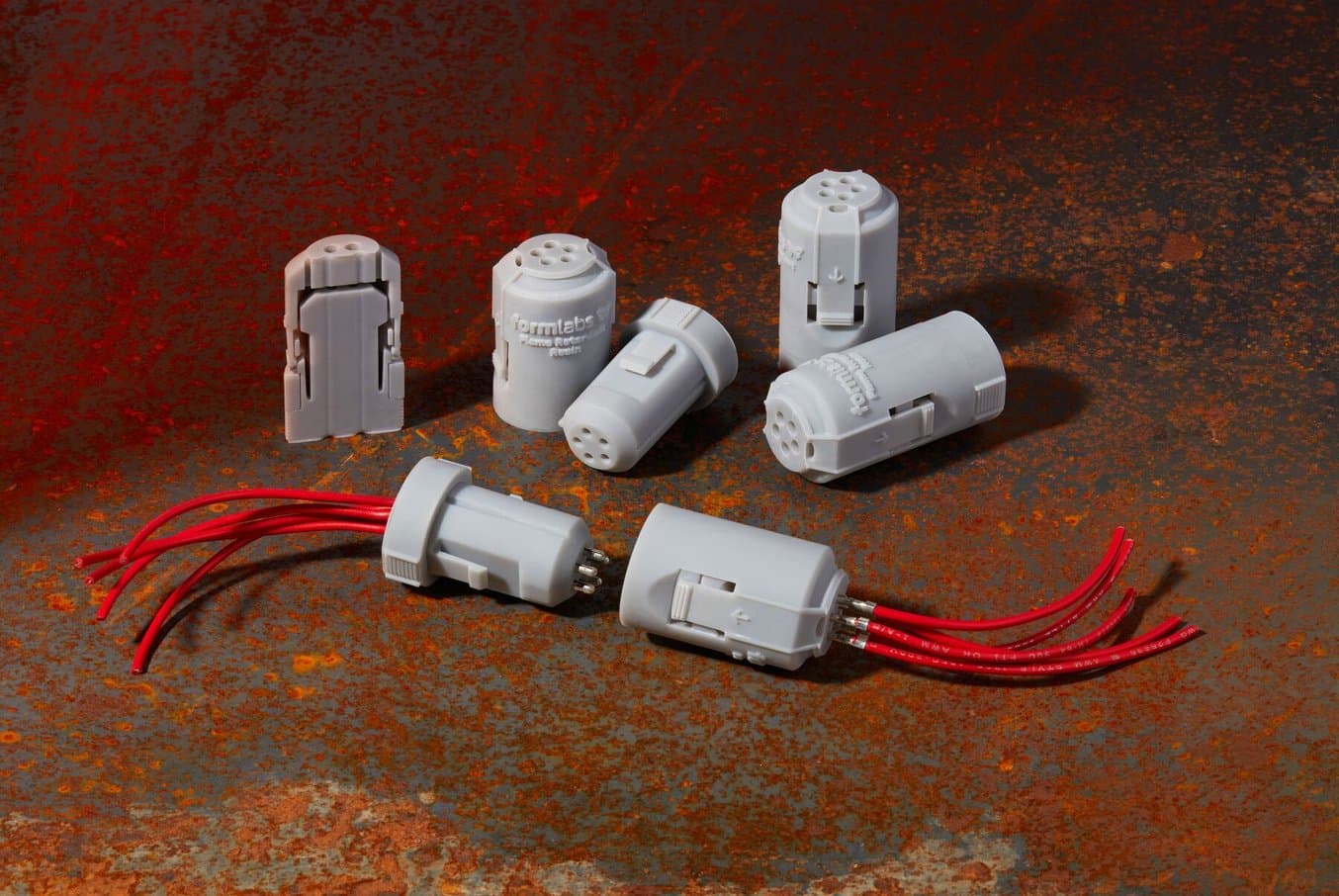
Come la Flame Retardant Resin apre le porte a nuove applicazioni per Avance Design
Scopri come utilizzare la Flame Retardant Resin per stampare facilmente in 3D parti ignifughe, rigide e resistenti a calore e scorrimento, in grado di offrire prestazioni eccezionali a lungo termine in ambienti chiusi e industriali con alte temperature o fonti di ignizione.
Cicli di produzione con stampa diretta, da tre a una settimana di durata
Uno dei clienti di Avance Design è Energy Access, azienda produttrice di soluzioni personalizzate per la ricarica delle batterie di apparecchi elettronici nei settori medico, della difesa, dell'industria pesante, della sicurezza e della robotica. Energy Access coinvolge il team di Avance nella fase di design di soluzioni di ricarica che si adattino alle batterie su misura e dalla forma unica. "Il mio compito è quello di progettare un alloggiamento che consenta di riporre e posizionare in modo sicuro la batteria per una soluzione di ricarica e di progettare uno scomparto che consenta di realizzare la connessione", afferma Parker.
Per Avance, progettare e sviluppare prodotti in grado di integrarsi con apparecchi specifici e di forma unica è la parte più semplice. Le difficoltà sorgono quando si cerca di far coincidere le proprietà dei materiali della parte personalizzata stampata in 3D con i componenti realizzati in serie e stampati a iniezione dei prodotti finali.
Energy Access ha imposto come standard aziendale che ogni parte abbia la certificazione UL 94 per prevenire eventuali rischi ambientali, pertanto Avance deve essere in grado di proporre parti che si integrino perfettamente con i prodotti esistenti dell'azienda. "Vorremmo ottenere le stesse proprietà dei materiali, perché così si completerà la metodologia di assemblaggio finale e sarà più facile integrare queste caratteristiche meccaniche nel prodotto finale", spiega Parker.
In passato, per ottenere tali proprietà del materiale (resistenza, levigatezza e resistenza alla fiamma UL 94), Avance ha dovuto ricorrere a un processo di fusione del poliuretano. Parker avrebbe dovuto realizzare un modello attraverso la lavorazione meccanica o la stampa 3D, poi costruirvi intorno uno stampo in silicone, quindi trovare un poliuretano con classificazione UL disponibile in commercio, versarlo nello stampo in silicone, e infine estrarre la parte in poliuretano ottenuta e sottoporla a post-elaborazione. "Per ogni parte ci sarebbero voluti giorni e se avessimo ricevuto un ordine di 20 parti ci sarebbero volute circa tre settimane", dice Parker.
Ora, con la Flame Retardant Resin di Formlabs, Parker può ridurre i passaggi e passare dal progetto CAD alla parte finita molto più rapidamente. "La possibilità di stampare in 3D la parte con la Flame Retardant Resin accorcia i tempi fino a una settimana per tutte e 20 le parti", spiega Parker.
Confronto tra i metodi di produzione di un alloggiamento ignifugo
Passaggi | Tempo di realizzazione di 20 parti | Costo per parte | |
---|---|---|---|
Flame Retardant Resin per la SLA | Stampa, lavaggio, polimerizzazione, rimozione dei supporti, verniciatura | 4-5 giorni | 19,80 $ (6,50 $ per i materiali, 13,30 $ per la manodopera*) |
Filamento FDM | Stampa, scioglimento dei supporti, pulizia, levigatura, riempimento, applicazione del primer, verniciatura | 5-6 giorni | 42 $ (7 $ per i materiali, 35 $ per la manodopera*) |
Fusione del poliuretano | Stampa, lavaggio, polimerizzazione, rimozione dei supporti, colata del silicone negli stampi, colata del poliuretano, pulizia, verniciatura | 21 giorni | 85 $ (25 $ per modello, stampo e uretano, 60 $ per la manodopera*) |
Stampo a iniezione tradizionale | Esternalizzazione di attrezzature e stampaggio | 20-30 giorni | 250 $ (5000 $ per le attrezzature, 0,50 $ per parte successiva) |
*Labor costs are calculated at $80/hour.
Finitura superficiale e lavorabilità
Questo flusso di lavoro ridotto ha inciso sul processo di sviluppo di Parker, ma è opportuno fare anche altre considerazioni. Anche la stampa 3D FDM offre da anni materiali con certificazione UL. Le parti devono avere anche una finitura superficiale superiore, senza le linee degli strati tipiche delle parti stampate con le stampanti FDM. "Sono rimasto molto colpito dalla finitura superficiale che otteniamo con la Flame Retardant Resin. Le parti sembrano quasi rivestite da un primer e vengono levigate come se avessero già un primer applicato. Sono molto facili da rifinire e preparare per la verniciatura, e questo è un ulteriore vantaggio per noi", afferma Parker.
Il team di Avance deve anche garantire che queste parti siano in grado di funzionare in un assemblaggio più grande, per cui devono poter accogliere inserti filettati. "Gli inserti a pressione hanno parametri specifici, ma noi abbiamo rispettato le raccomandazioni sulle dimensioni del foro desiderato e poi abbiamo usato una piccola pressa per riempire un inserto di base, e la parte è venuta bene. Non c'è stato alcun problema e le parti stampate hanno tollerato molto bene gli inserti", dice Parker.
Questa facilità di integrazione è determinante per i processi di assemblaggio successivi. Parker ha la certezza che le parti stampate di Formlabs superino i test UL, abbiano le stesse caratteristiche di levigatezza e resistenza dell'intero caricabatterie e integrino in modo coerente i sistemi di fissaggio filettati. Nonostante siano stampate in 3D, le parti in Flame Retardant Resin possono integrarsi senza problemi nelle metodologie di assemblaggio dei suoi clienti. "Nel caso di Energy Access, l'azienda ha espresso il proprio entusiasmo perché non era rimasta colpita dalle soluzioni FDM o di fusione per i materiali ignifughi. L'idea di poter sviluppare, apportare modifiche e mantenere lo stesso materiale in tutto il processo di design e produzione è piaciuta", spiega Parker.
La possibilità di ottenere una parte stampata in 3D che assomiglia in tutto e per tutto a una termoplastica, con finitura eccellente, dettagli precisi e proprietà meccaniche simili a quelle delle parti stampate a iniezione è un vantaggio enorme, anche in termini di tempo. Con la Flame Retardant Resin possiamo passare dal design in CAD alla parte finale senza tutto il lavoro addizionale necessario per altri metodi.
Tony Parker, direttore di Avance Design
Produzione con più materiali
Avance Design si occupa di molti progetti diversi che esulano dall'ambito dei materiali con certificazione UL. Ogni progetto inizia con una discussione e l'analisi delle caratteristiche più importanti per il cliente, e in genere Parker è in grado di individuare la resina Formlabs più adatta. "Abbiamo sempre a disposizione circa 20-30 cartucce di resina", spiega. In un progetto recente, un cliente ha richiesto un materiale flessibile per dispositivi destinati a simulazioni per la formazione medica. Parker ha progettato parti in Flexible 80A Resin da utilizzare nel dispositivo. Le parti sono state un successo e Avance ne ha stampate più di 1000 con le stampanti Form 3+, a dimostrazione del caso d'uso della produzione di volumi ridotti.
Il settore dell'architettura offre altre possibilità, in quanto la produzione di volumi ridotti di elementi come i componenti delle porte deve armonizzarsi con lo stile e gli arredi dell'ambiente. I clienti si rivolgono ad Avance per articoli come alloggiamenti per componenti elettronici progettati su misura che si adattano allo stile e agli arredi di un edificio. Per soddisfare i requisiti di resistenza e forma di un'applicazione per utilizzo finale, evitando al contempo i costi di stampaggio o lavorazione meccanica, Parker utilizza la Form 3+ e la Form 3 per le applicazioni per utilizzo finale con volumi ridotti.
La prospettiva di nuove opportunità
Un nuovo materiale si aggiunge alla sua gamma e Parker si dice entusiasta delle opportunità che si aprono per le applicazioni con la Flame Retardant Resin. "Le persone si sono abituate alle tecnologie di fusione o di stampa FDM, ma quando vedranno che è disponibile questa resina, si apriranno delle porte. È un modo più rapido e meno costoso per ottenere una parte", afferma Parker.
Secondo Parker, il complicato processo di fusione ha dissuaso alcuni clienti di Avance dall'utilizzare la stampa 3D in campo medico, ingegneristico o della robotica. "Sono sicuro che alcuni clienti hanno pensato che non valesse la pena ricorrere alla fusione. Ma ora che c'è un modo per farlo direttamente con la stampa 3D per i settori in cui esiste questo requisito, non vedo l'ora di scoprirne le potenzialità", afferma Parker.
Per vedere se la Flame Retardant Resin può fare al caso tuo, visita la pagina del prodotto o contatta il nostro team vendite per parlare della tua applicazione specifica.