Utilizzare la stampa 3D SLS per realizzare controller personalizzati ad alte prestazioni
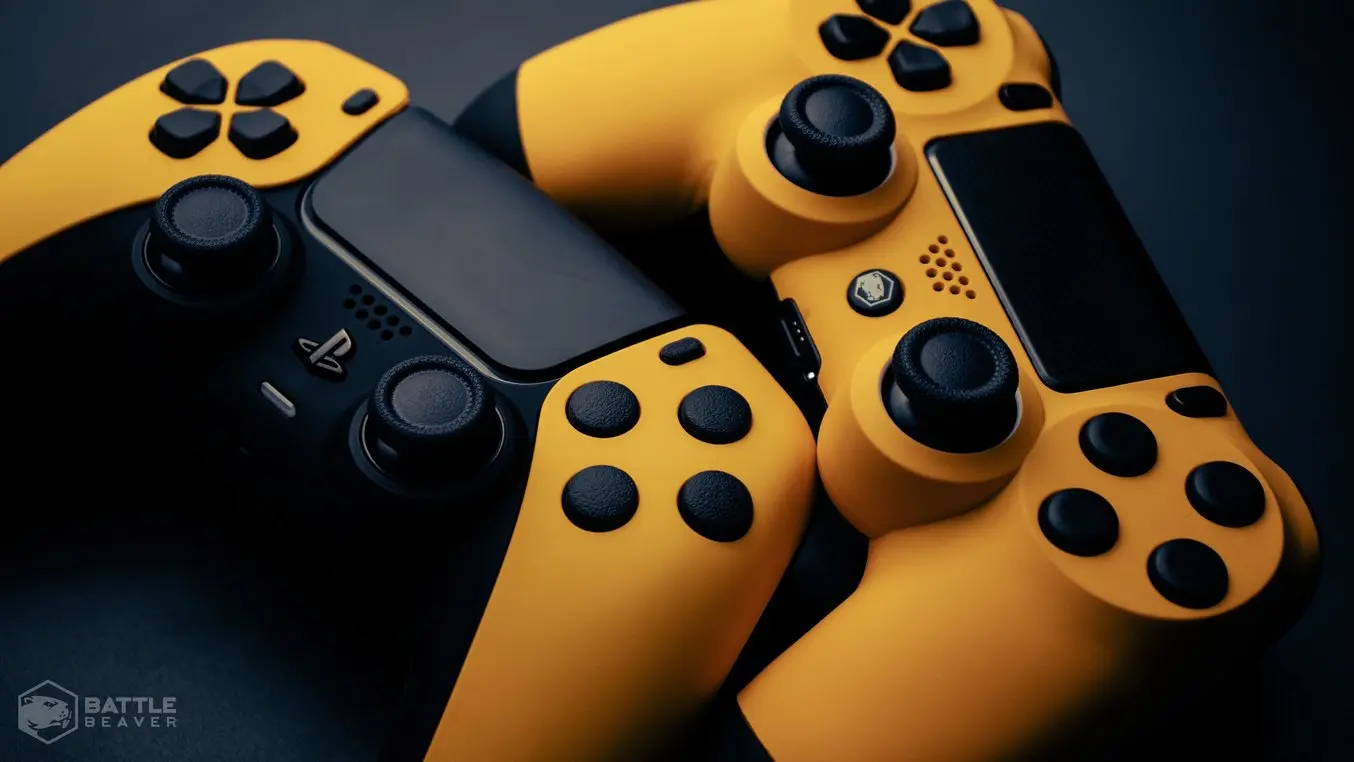
Un controller con pulsanti stampati con la Fuse 1 (a sinistra) e un altro con tasti realizzati tramite stampaggio a iniezione (a destra).
Battle Beaver Customs ha l'obiettivo di fornire un'esperienza di gioco di alto livello con controller personalizzati. Grazie alle modifiche, i controller sono più reattivi e competitivi, e i giocatori possono aumentare il loro potenziale e raggiungere prestazioni eccellenti in un'ampia varietà di giochi.
Battle Beaver Customs mette a disposizione dei suoi ingegneri stampanti 3D in-house, tra cui apparecchi a modellazione a deposizione fusa, la stampante SLA Form 2 e la stampante SLS Fuse 1. Di recente il team ha usato la Fuse 1 per evitare l'esternalizzazione di parti interne dei controller, portando la produzione di parti per uso finale in-house. Questo ha ridotto di diverse settimane i tempi di produzione e ha evitato a Battle Beaver Customs qualsiasi complicazione legata alla catena di fornitura.
In questo articolo scopriremo da Micheal Crunelle, responsabile di ricerca e design, come fornisce con continuità controller per i videogiochi tra i migliori sul mercato.
Arrivare sul mercato prima della concorrenza
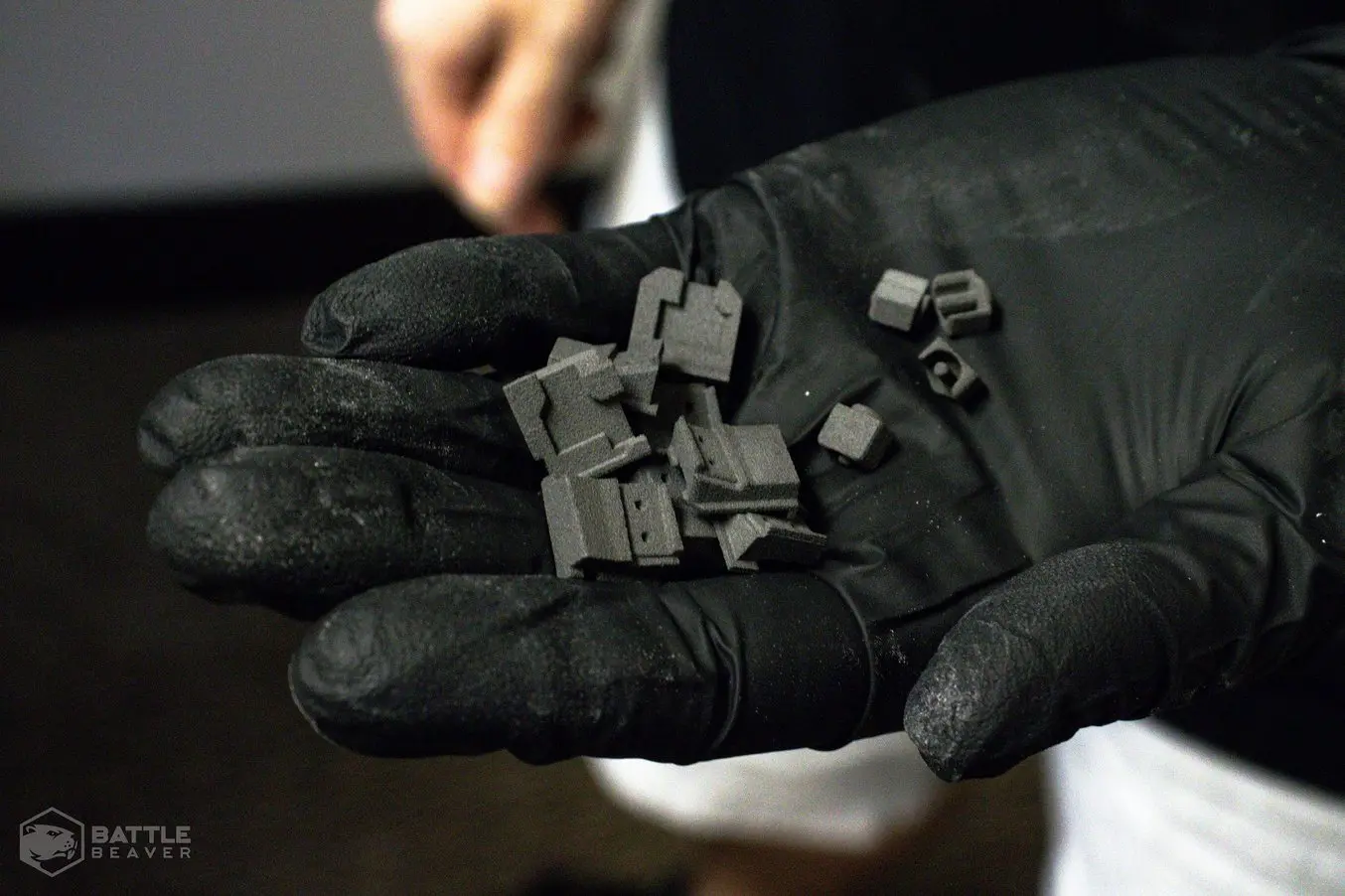
Parti interne dei controller ad altre prestazioni di Battle Beaver Customs.
Nel corso di un sola generazione di console, i controller per videogiochi sono riprogettati più volte. Questo può essere un problema per i produttori di controller personalizzati come Battle Beaver Customs, perché il design dei vecchi attacchi e dei pulsanti può non essere più adatto ai nuovi modelli.
Laprototipazione rapida con la Fuse 1 consente a Battle Beaver Customs di cambiare velocemente il design di attacchi e tasti. Nella costruzione di prodotti personalizzati per il consumatore, i tempi di esecuzione possono fare la differenza per le aziende che vogliono essere un passo avanti rispetto alla concorrenza. Secondo Crunelle "la Fuse 1 è stata fantastica, perché ci ha consentito di apportare modifiche velocemente dal concept alla parte per uso finale. La concorrenza non riesce a stare al passo."
Per una recente riprogettazione interna del controller della Playstation 5, Crunelle ha lavorato giorno e notte per creare nuovi attacchi e afferma: "Sony ha riprogettato l'interno del controller circa quattro volte durante il ciclo di vita della Playstation 4, e il controller della Playstation 5 è già alla seconda versione. Questo significa che dobbiamo cambiare il modo in cui progettiamo la piattaforma interna. Per il controller della Playstation 5 siamo stati in grado di progettare e stampare nuove piattaforme nel giro di 48 ore in modo che le modifiche funzionassero. Di solito questo richiede uno o due mesi, ma ora non è più un problema."
Sostituzione dello stampaggio a iniezione (esternalizzato) con la stampa SLS in-house a un prezzo accessibile
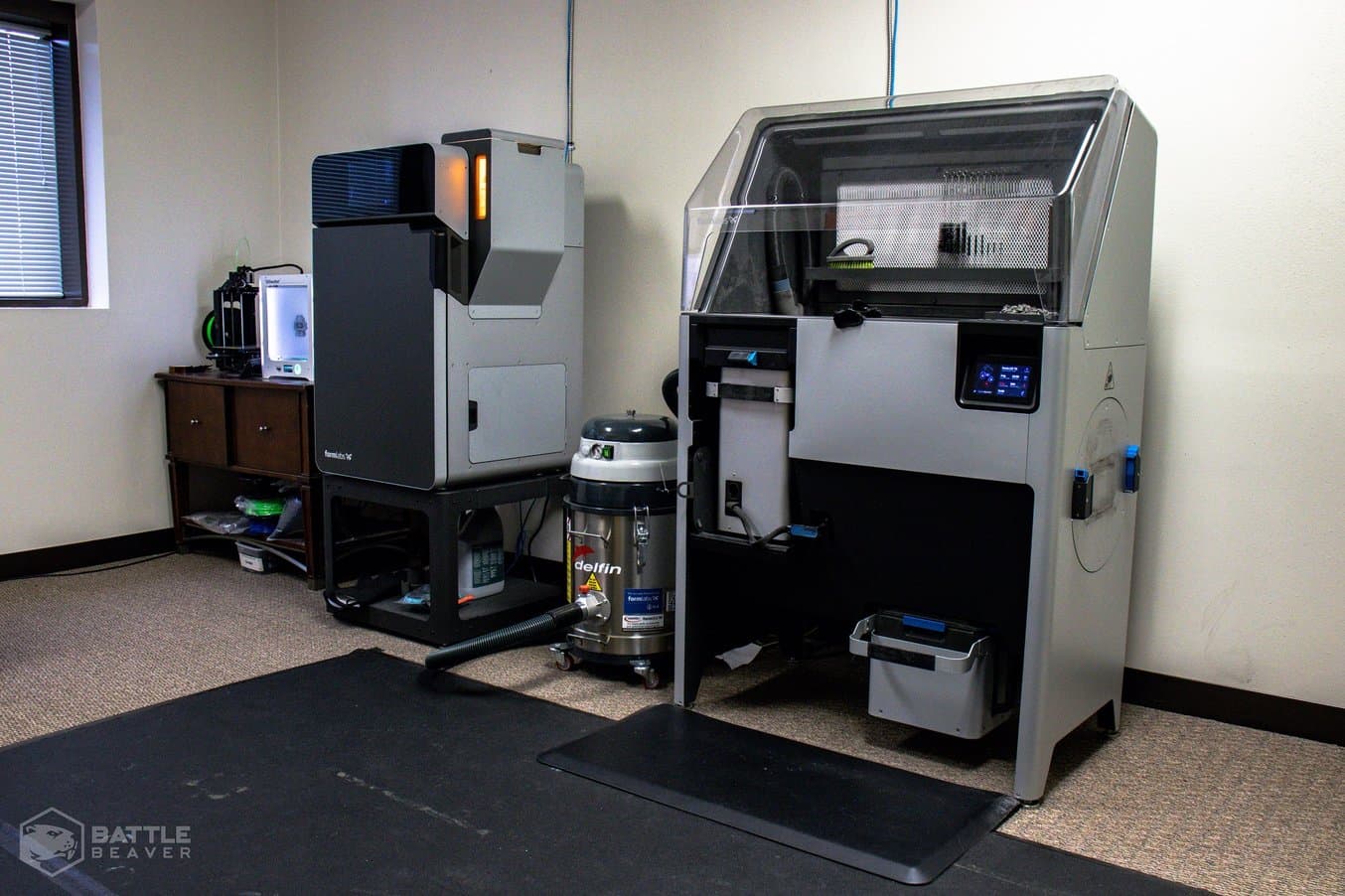
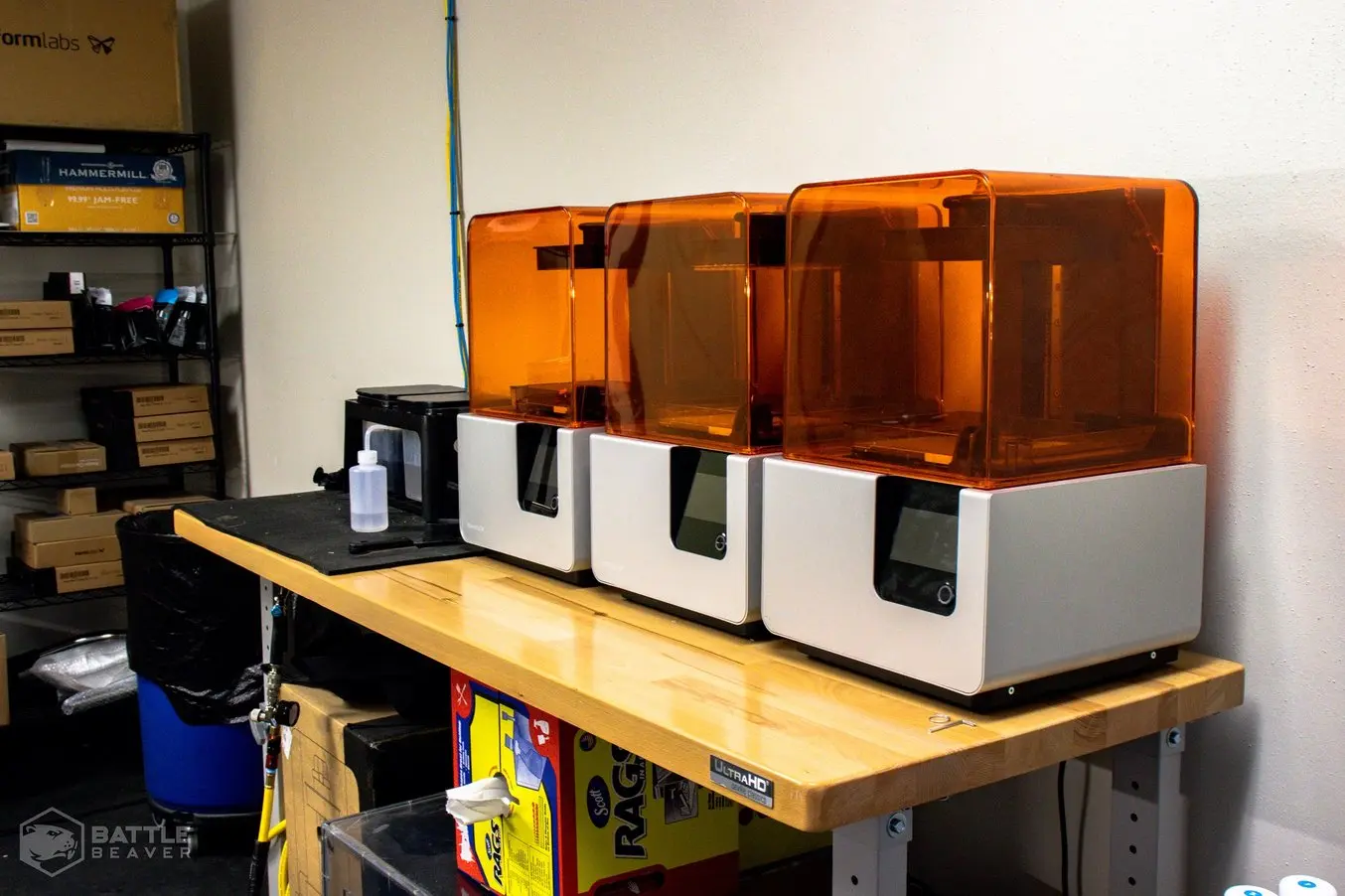
Il team ha spostato gran parte della produzione sulla Fuse 1, ma continua a mantenere una flotta di stampanti SLA Form 2 per la prototipazione e per alcune parti per uso finale.
All'inizio Crunelle ha comprato una Form 1+ su eBay, e successivamente ha ampliato la sua flotta, con tre stampanti Form 2.
Crunelle afferma che l'azienda usa ancora le stampanti Form 2 per realizzare le parti sostitutive per la croce direzionale SmartPad e alcune parti esterne che richiedono superfici lisce. Ma grazie alle sue proprietà, il nylon ha assunto un ruolo cruciale per le modifiche interne dei controller, e Crunelle sostiene che "in confronto alla resina normale, è stato più semplice per noi usare resine epossidiche e colle con la polvere di nylon. Anche avere una maggiore capacità termica è stato un fattore importante. Si può avvicinare alla parte la punta di un saldatore, e comunque non si scioglie."
Con la Fuse 1, Battle Beaver Customs ha trasferito in-house la produzione di tutti gli attacchi e le parti interne. In precedenza le parti venivano prodotte tramite stampaggio a iniezione e spedite dalla Cina agli Stati Uniti. Con la camera di stampa della Fuse 1, che può contenere dalle 500 alle 800 parti, il team sta realizzando una produzione in lotti su richiesta, e la Fuse 1 sostituisce completamente le forniture esterne.
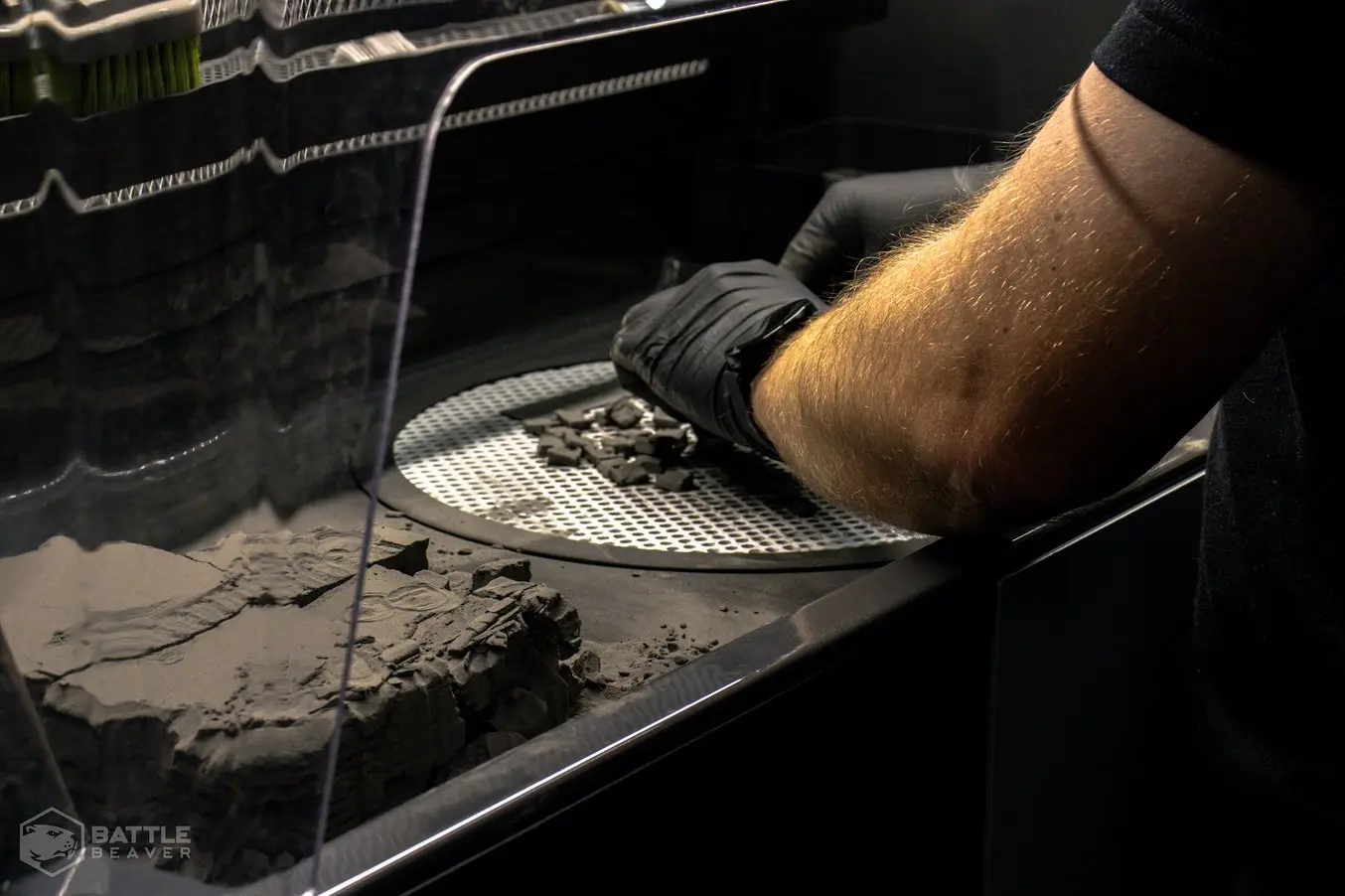
Prima dell'utilizzo le parti vengono inserite nella Fuse Sift e poi sabbiate.
Con la stampa 3D in-house, il team ha ridotto di settimane i tempi di produzione e ha potuto fare a meno della catena di fornitura, con tutte le complicazioni e i lunghi tempi di consegna che comportava. Ridurre il tempo di commercializzazione per le nuove parti interne da sei mesi a pochi giorni ha inoltre il vantaggio di ridurre il rischio associato alla creazione di nuovi prodotti, e potenzialmente permetterà di aumentare l'innovazione e le varianti dei prodotti in futuro.
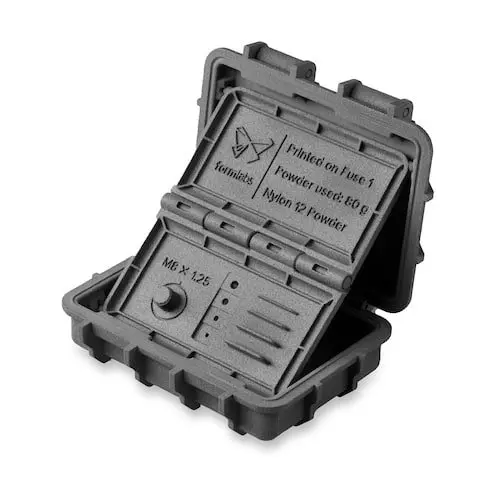
Richiedi un campione gratuito
Guarda e tocca con mano la precisione della stampa SLS di Formlabs. Saremo lieti di inviare presso la tua azienda un campione gratuito.
Produzione di parti già esistenti su richiesta
Inoltre, poiché il numero di controller prodotti dall'azienda è aumentato, la stampa 3D in-house consente la produzione in piccoli lotti di parti fuori commercio. Se un cliente richiede la vecchia versione di un controller che è stato modificato, Crunelle può caricare il file STL corrispondente, stampare le parti e consegnare il controller. Ora è possibile supportare un'ampia gamma di prodotti grazie ai costi ridotti per la manutenzione delle parti già esistenti. Secondo Crunelle "avendo la libertà di stampare diverse strutture con la Fuse 1, possiamo fare le modifiche che ci servono, e non dobbiamo preoccuparci di pagare per l'attrezzatura." In passato Battle Beaver Customs era in grado di fornire soltanto un numero limitato di vecchi modelli di controller, a causa dei costi e dei tempi di produzione.
Infine, un vantaggio inaspettato della stampa 3D SLS in-house è il fatto che la sua versatilità consente di realizzare progetti inaspettati. Dato che i lotti di Battle Beaver Customs sono costituiti da oltre 500 parti, la sabbiatura può richiedere molto tempo. Crunelle ha usato la Fuse 1 per costruire una postazione personalizzata e ha acquistato un motore che si inserisce nella sabbiatrice. Le parti possono ruotare da sole per venti minuti, riducendo il tempo necessario e i problemi durante la fase di post-elaborazione.
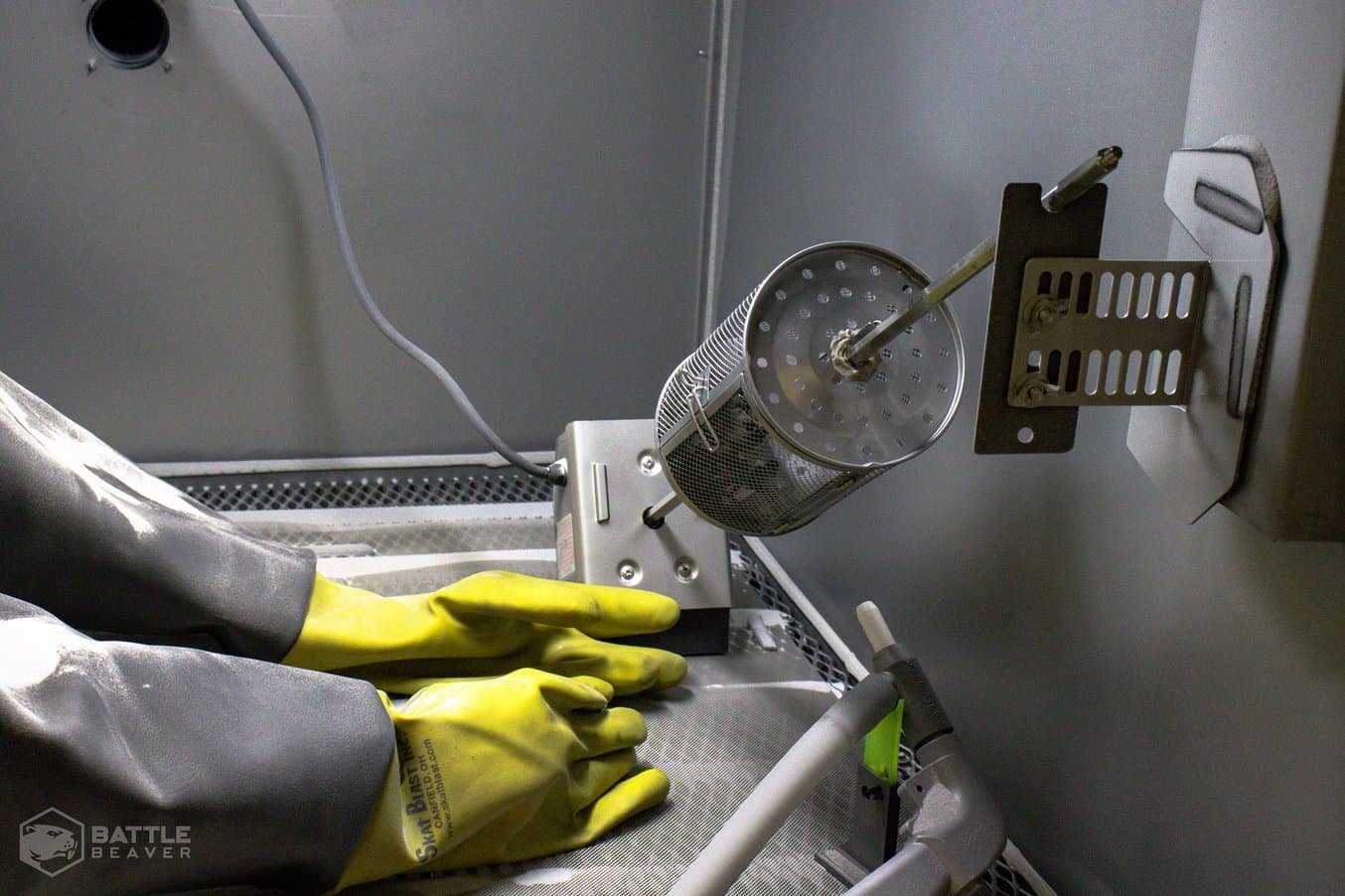
Il team ha costruito una griglia per automatizzare il processo di sabbiatura.
Crunelle è stato uno dei primi a servirsi della Fuse 1. Dodici mesi dopo, con la stampante completamente integrata nel workflow, dice: "Dopo aver stampato per quasi un anno, è diventata uno strumento irrinunciabile per noi".
Per saperne di più su Battle Beaver Customs, seguila su Twitter.