
Nonostante la fusione dei metalli sia ancora un settore da 50 miliardi di dollari e che solo negli Stati Uniti dà lavoro a 160 000 persone, le fonderie sul territorio statunitense hanno dimezzato il volume di produzione rispetto a dieci anni fa. Questo calo può essere attribuito a diversi fattori, tra cui la delocalizzazione in aree in cui la produzione è più conveniente, le prestazioni migliorate dei materiali alternativi al metallo e il ricorso a manodopera meno specializzata a ogni fase del processo. Come fanno quindi le aziende che producono per i settori dell'industria pesante, come quello aerospaziale, automobilistico o energetico, a ottenere parti in metallo in modo rapido ed economico?
Le fonderie che ancora realizzano parti per questi settori stanno vivendo una fase di grande prosperità, perché hanno adottato nuovi metodi di produzione e sperimentato tecnologie emergenti. Abbiamo parlato con John Farr di Diversified Metalsmiths, Inc. per scoprire come questa azienda ha incorporato tecnologie moderne nel suo workflow di fusione dei metalli per ridurre i costi, migliorare i tempi di produzione e aumentare l'agilità.
Utilizzando le stampanti 3D stereolitografiche (SLA) della serie Form e la nuova Clear Cast Resin, Diversified ha potuto stampare modelli in-house in modo rapido ed economico, senza necessità di modificare il workflow di fusione o ricorrere all'esternalizzazione.
"Il motivo principale per cui abbiamo acquistato la Form 3L è il costo dei modelli. Anche ammortizzando la spesa per la stampante e l'attrezzatura associata, come minimo arriveremo a pareggiare i costi dell'ordine in corso, mentre sui prossimi prevediamo di risparmiare oltre 200 dollari per parte. Non ci sono grandi differenze tra i modelli in PMMA e quelli in Clear Cast Resin in termini di processo di produzione, né prima né dopo la fusione."
John Farr, vicepresidente del dipartimento di tecnologia, Diversified Metalsmiths
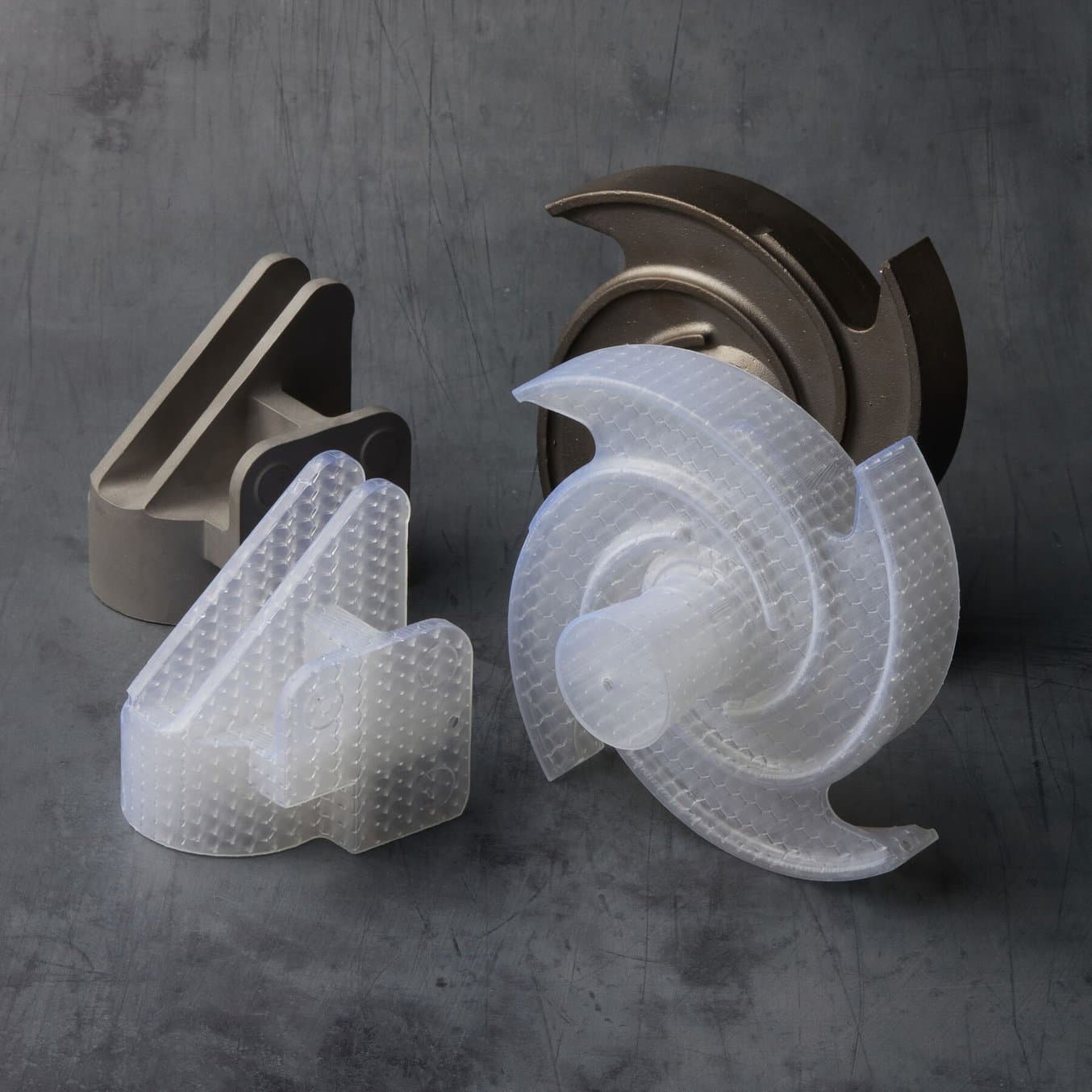
Fusione di parti in metallo precisa e conveniente grazie alla stampa 3D
Questo whitepaper presenta i metodi che hanno permesso a diverse fonderie leader di eseguire la fusione di parti in metallo utilizzando modelli 3D realizzati con stampanti Formlabs. Scopri come le fonderie riescono a risparmiare, ridurre i tempi di produzione e migliorare la qualità delle parti in metallo grazie all'integrazione nei processi di fusione tradizionali della Clear Cast Resin di Formlabs e del modulo di reticolazione di Materialise Magics.
Base clienti diversificata
Diversified è un'azienda che opera in modo più simile a un'officina che come uno stabilimento con alti volumi di produzione, e non è l'unica. Molte delle piccole fonderie degli Stati Uniti hanno una produttività simile e una clientela stabile che si affida a loro per la produzione rapida di parti altamente accurate. "La nostra clientela non va a richiedere preventivi ad altre aziende, perché sa che da noi può ottenere esattamente ciò che chiede", afferma Farr.
Diversified è il partner perfetto per i progetti che richiedono volumi medio-bassi di parti in metallo con tolleranze ridotte e tempi di consegna brevi. Circa il 70% degli ordini riguarda applicazioni per il controllo dei fluidi, ad esempio giranti, alloggiamenti per pompe, valvole, tubi di scarico, griglie e componenti per fluidi industriali. Il rimanente 30% spazia invece dai componenti per la produzione di droni a quelli per il settore automobilistico, passando per i dispositivi medici e persino le belle arti.
Sebbene il volume possa leggermente variare, ogni mese Diversified realizza fusioni per circa tre tonnellate di metallo. Per ogni lavoro viene scelto il forno di cottura più adatto: quello da 180 kg per le parti di dimensioni ridotte, quello da 500 kg per le parti più grandi.
Uno degli articoli più commissionati a Diversified è un girante in titanio, che raggiunge un volume annuale di 100 parti. Poiché i costi del titanio sono aumentati, l'azienda ha dovuto cercare soluzioni alternative per risparmiare in altre fasi del workflow. Una di queste soluzioni è la stampa 3D SLA.
Unione di tradizione e modernità
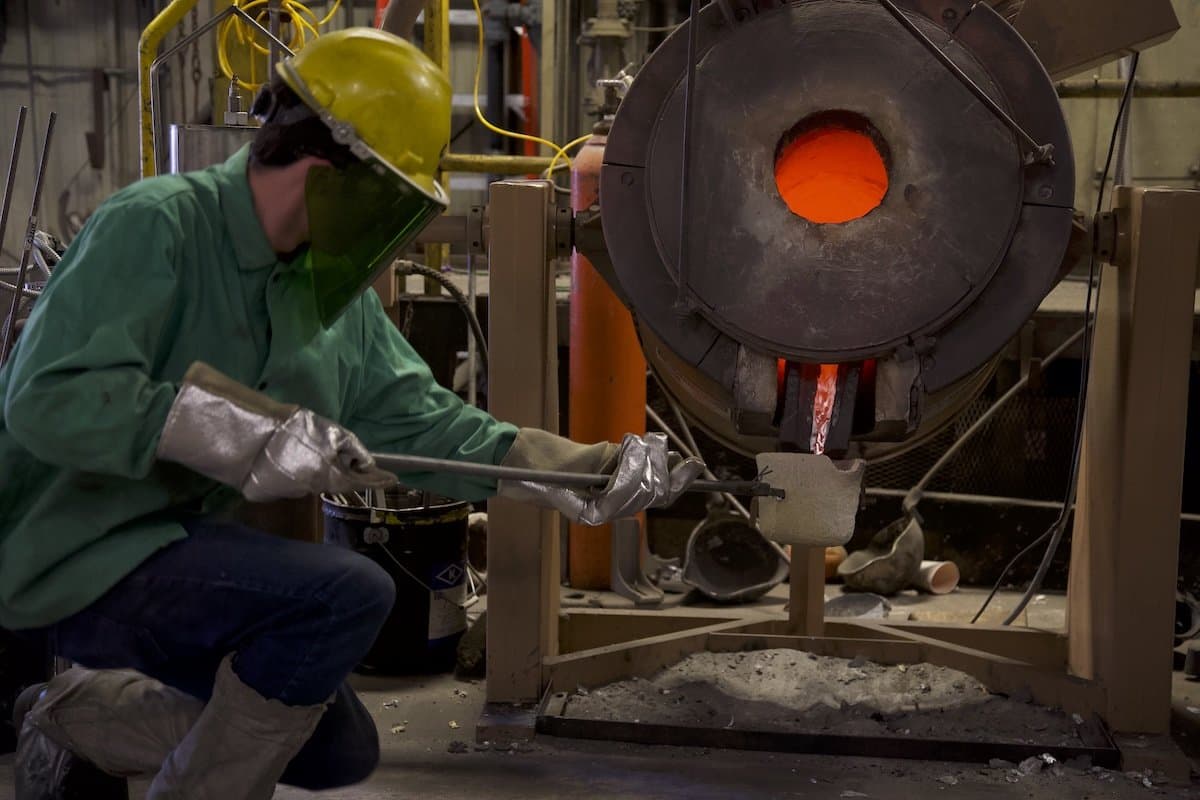
Il settore della fusione a cera persa industriale sfrutta ancora oggi processi tradizionali per molte fasi del workflow, ad esempio per versare l'alluminio fuso nello stampo cavo, mostrato sopra.
Sebbene la fusione dei metalli sia per alcuni versi un settore molto tradizionalista, con un workflow rimasto sostanzialmente invariato per migliaia di anni, le fonderie sono state pioniere della produzione moderna. Farr e il team di Diversified, infatti, sono stati tra i primi ad adottare la tecnologia di stampa 3D. "In un modo o nell'altro, abbiamo a che fare con i modelli per la fusione stampati in 3D all'incirca dalla metà degli anni '90", spiega Farr.
Diversified ha iniziato a usare le stampanti 3D a cera per creare i modelli quando la realizzazione di quelli tradizionali in cera (iniezione di cera liquida in uno strumento metallico cavo) era diventata troppo onerosa in termini di tempo e costi. Un progetto in particolare prevedeva l'uso di quattro strumenti distinti, tra cui strumenti per iniettare nuclei di cera solubile, elementi di raffreddamento in cera solubile e non solubile e le parti interamente assemblate. Tutti questi dovevano essere realizzati su misura, iniettati con la cera, assemblati e (spesso) rilavorati per eliminare eventuali imperfezioni. "Le ore-persona richieste per la realizzazione di un singolo modello in cera per la fusione erano proibitive. Il processo occupava gran parte della giornata; dal punto di vista della manodopera, era chiaro che avrebbe avuto vita breve", afferma Farr.
Il team di Diversified ha introdotto le stampanti a cera di 3D Systems e le stampanti 3D ThermoJet, che ha integrato nel workflow come alternativa diretta al processo di iniezione tradizionale. Alcuni anni dopo, un cliente ha fatto conoscere all'azienda un nuovo prodotto: i polimeri di PMMA stampati in 3D su una stampante binder jetting di VoxelJet, che offriva una combustione pulita e una maggiore stabilità dimensionale rispetto alle stampanti a cera.
Con l'aumento generale dei costi nel settore, anche l'esternalizzazione ad aziende di stampa 3D di polimeri era diventata troppo cara. Ogni modello costava a Diversified circa 300 dollari e anche l'eventuale investimento per portare le apparecchiature di stampa in-house avrebbe facilmente superato le sei cifre.
"L'aumento dei prezzi ci ha spinto a cercare nuove soluzioni. Abbiamo quindi considerato le tecnologie FDM e SLA, decidendo poi di acquistare cinque stampanti FDM, che permettevano di creare strutture di supporto solubili. Al tempo erano perfette per le nostre esigenze", spiega Farr.
Tuttavia, quando il team di Farr ha ricevuto un ordine di 100 giranti da completare in un anno, ha dovuto ancora un volta cercare una nuova soluzione. È stato in quell'occasione che si è rivolto a Formlabs per la stampante 3D SLA di grande formato Form 3L.
Fusione dei metalli con l'ecosistema Formlabs
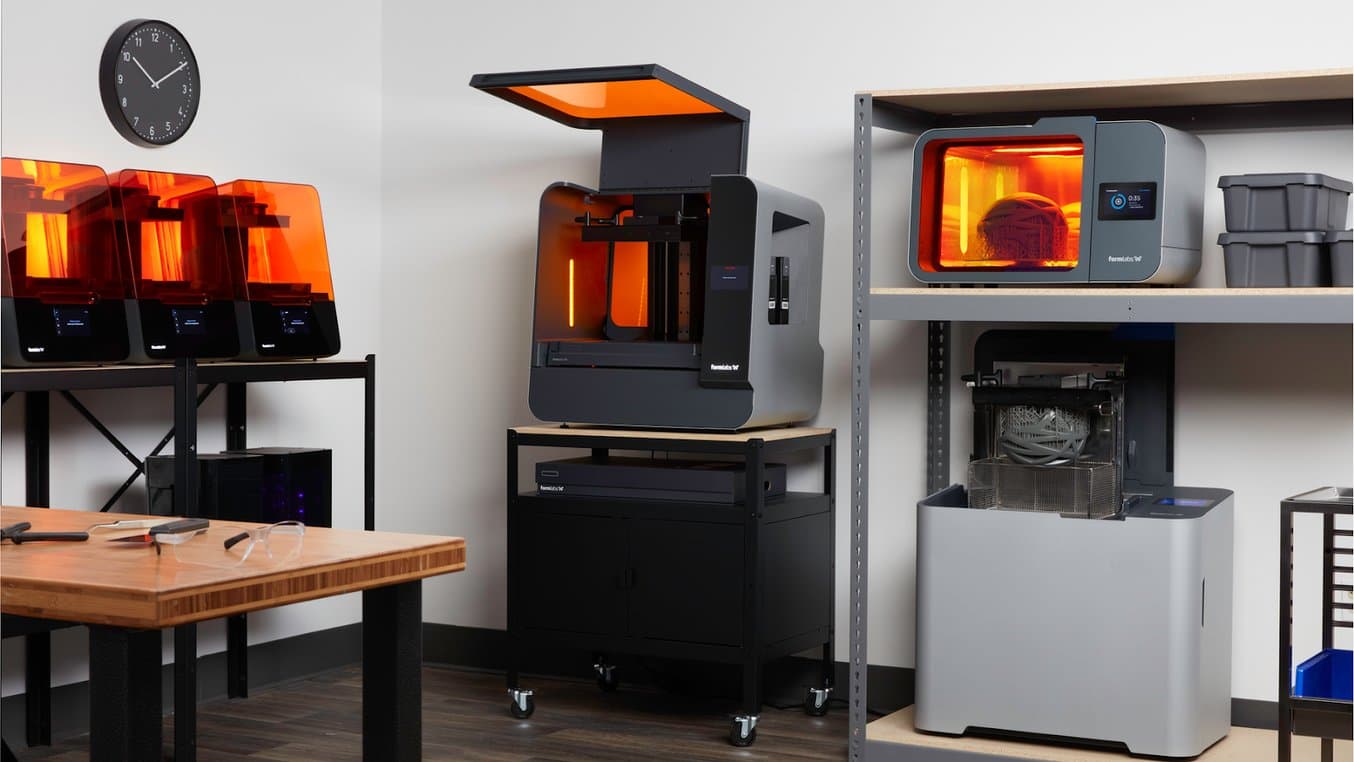
La Form 3L, insieme alle soluzioni di post-elaborazione Form Wash L e Form Cure L, offre un formato più grande rispetto a molti apparecchi desktop per l'hobbistica, oltre a un workflow accessibile e una qualità di stampa estremamente elevata.
Il nuovo ecosistema di stampa 3D adottato da Diversified doveva rispettare alcuni requisiti fondamentali: offrire una combustione pulita del materiale, essere affidabile e facile da usare e avere le dimensioni adatte al progetto dei giranti. "L'intero ecosistema e il sistema dei supporti erano perfetti per noi. Ogni aspetto, dall'aderenza e la finitura delle parti stampate fino al software, superava di gran lunga le altre soluzioni disponibili in quella fascia di prezzo", afferma Farr. Dopo aver ottenuto un prototipo stampato dal team di Formlabs, Farr ha potuto riscontrare che la Form 3L e la Clear Cast Resin si integravano perfettamente nel workflow, senza alcuna necessità di modificare le temperature di combustione, la formulazione dell'impasto o il design della parte. I modelli realizzati sulle stampanti Formlabs consentivano anche di migliorare leggermente il processo, grazie alla possibilità di aggiungere punti di iniezione direttamente nelle parti.
"Le parti realizzate con la Clear Cast Resin si sono rivelate perfette per il workflow. Uno dei vantaggi è la possibilità di stampare i punti di iniezione direttamente nelle parti, cosa che non avremmo potuto fare con il PMMA."
John Farr, vicepresidente del dipartimento di tecnologia, Diversified Metalsmiths
A livello di workflow, la transizione è stata semplice. L'ultima cosa che rimaneva da verificare era il procedimento di combustione. Anche in questo caso, la Clear Cast Resin si è dimostrata un'alternativa efficace, ed estremamente conveniente, ai modelli in PMMA esternalizzati. "Le modalità di combustione sono simili a quelle del PMMA, trattiamo la resina allo stesso modo", spiega Farr.
Per un singolo modello di girante stampato in 3D sulla Form 3L con la Clear Cast Resin, Diversified spende circa 80 dollari per materiali e manodopera, contro i 300 richiesti dall'esternalizzazione. Il team è quindi riuscito a recuperare rapidamente l'investimento, ma allo stesso tempo ha anche ampliato lo spettro di casi d'uso e applicazioni. Con appena tre stampe alla settimana, sono bastati meno di nove mesi per ripagare la spesa per la stampante.
Modello in PMMA esternalizzato | Modello in Clear Cast Resin in-house | |
---|---|---|
Costo | 300 € | 80 € |
Tempo di realizzazione | 2 settimane | 24 ore |
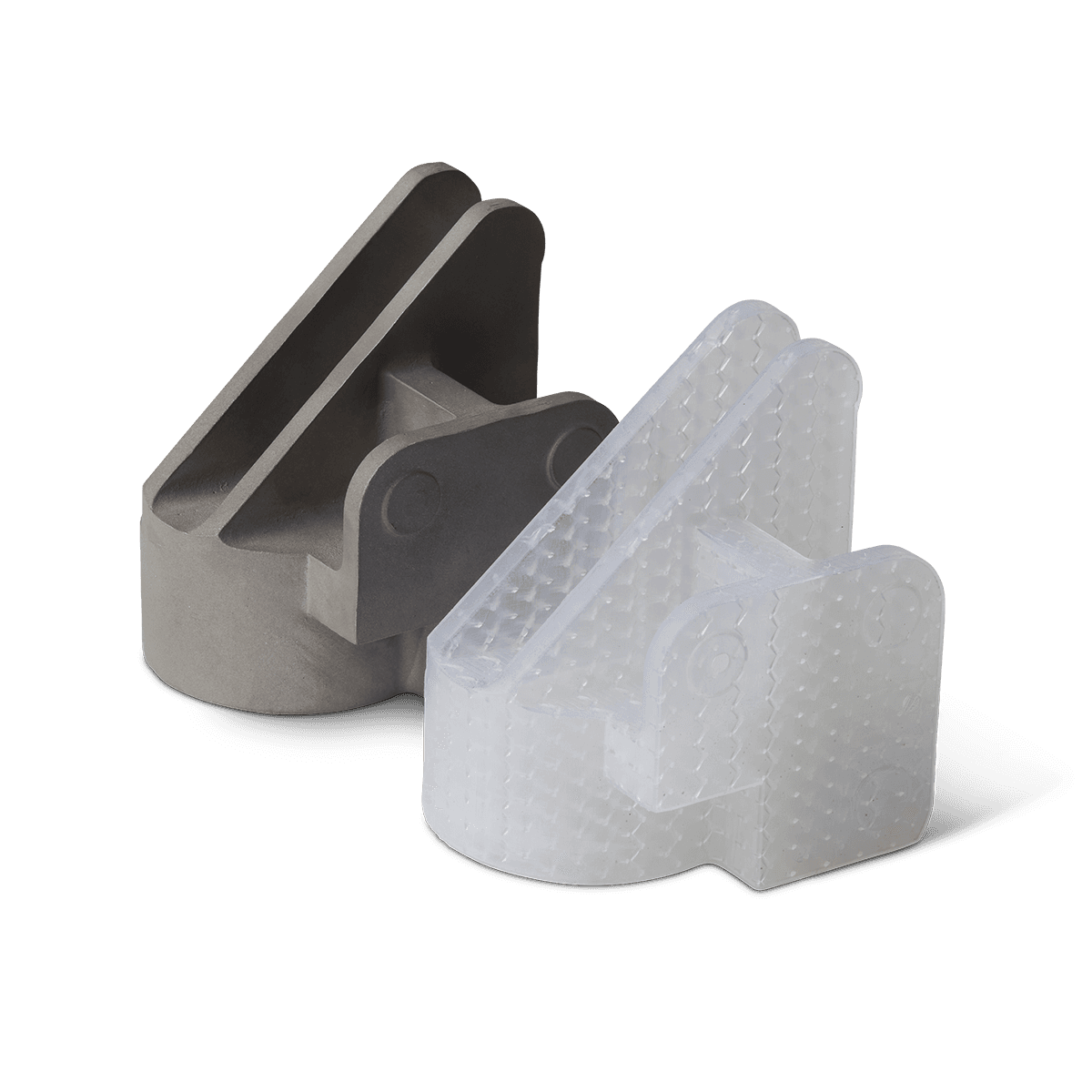
Fusione a cera persa industriale con modelli stampati in 3D usando la Clear Cast Resin di Formlabs
Questo whitepaper presenta i metodi che hanno permesso a diverse fonderie leader di eseguire la fusione di parti in metallo utilizzando modelli stampati in 3D su stampanti stereolitografiche (SLA) di Formlabs.
Scelta degli strumenti ideali in base al volume
I modelli per la fusione a cera persa sono elementi usa e getta; quando i volumi di ordini aumentano, non sempre risulta conveniente stampare in 3D ogni singolo modello di un ciclo di produzione. Tuttavia, esiste un certo volume di produzione a cui la Form 3L e la Clear Cast Resin si dimostrano la soluzione ideale. "Se riceviamo un ordine di mille parti, normalmente optiamo per la creazione di attrezzature specifiche. In questi casi, il prezzo potrebbero raggiungere i 30 000 dollari, una cifra che può essere giustificata soltanto con la produzione di un gran numero di parti", afferma Farr.
Disporre in-house di una stampante e un materiale come la Form 3L e la Clear Cast Resin consente di ridurre i tempi di manodopera complessivi e di ottenere geometrie complesse e dimensioni corrette al primo tentativo.
"I modelli in sabbia non hanno lo stesso livello di accuratezza di quelli per la fusione a cera persa stampati in 3D. Questi ultimi hanno una geometria quasi perfetta e consentono di risparmiare tempo e manodopera sia prima della stampa che in fase di post-elaborazione, perché non devono essere levigati. Con la stampa 3D risparmio tempo: mi basta premere un tasto, dopodiché sono libero di dedicarmi ad altre attività. Inoltre, la parti ottenute non richiedono lavorazione meccanica o manuale, il che mi permette di recuperare facilmente il costo dei modelli stampati in 3D", afferma Farr.
Inizia a stampare con la Clear Cast Resin
La stampa 3D viene utilizzata nei workflow di fusione a cera persa da decenni. Nonostante non sia adatta a tutti i casi d'uso, i progressi nel campo della scienza dei materiali e nell'accuratezza di stampa l'hanno resa uno strumento più efficace per alcuni tipi di lavoro.
Le stampanti 3D SLA della serie Form e la Clear Cast Resin offrono un'impostazione semplice, nonché un'accuratezza leader del settore e una combustione pulita. Grazie alla riduzione della manodopera nelle operazioni pre-stampa e della necessità di sottoporre le parti a levigazione o lavorazione meccanica dopo la stampa, i modelli stampati in 3D permettono di tagliare il costo complessivo per unità e introdurre nuove possibilità di produzione, il tutto senza modifiche del workflow.
Ordina la Clear Cast Resin e inizia subito a stampare. Per scoprire come iniziare a produrre parti in metallo con stampi per fusione a cera persa realizzati in 3D, scarica il nostro whitepaper.