Migliaia di metri sotto al mare: alloggiamenti stampati in 3D per l'esplorazione delle profondità oceaniche
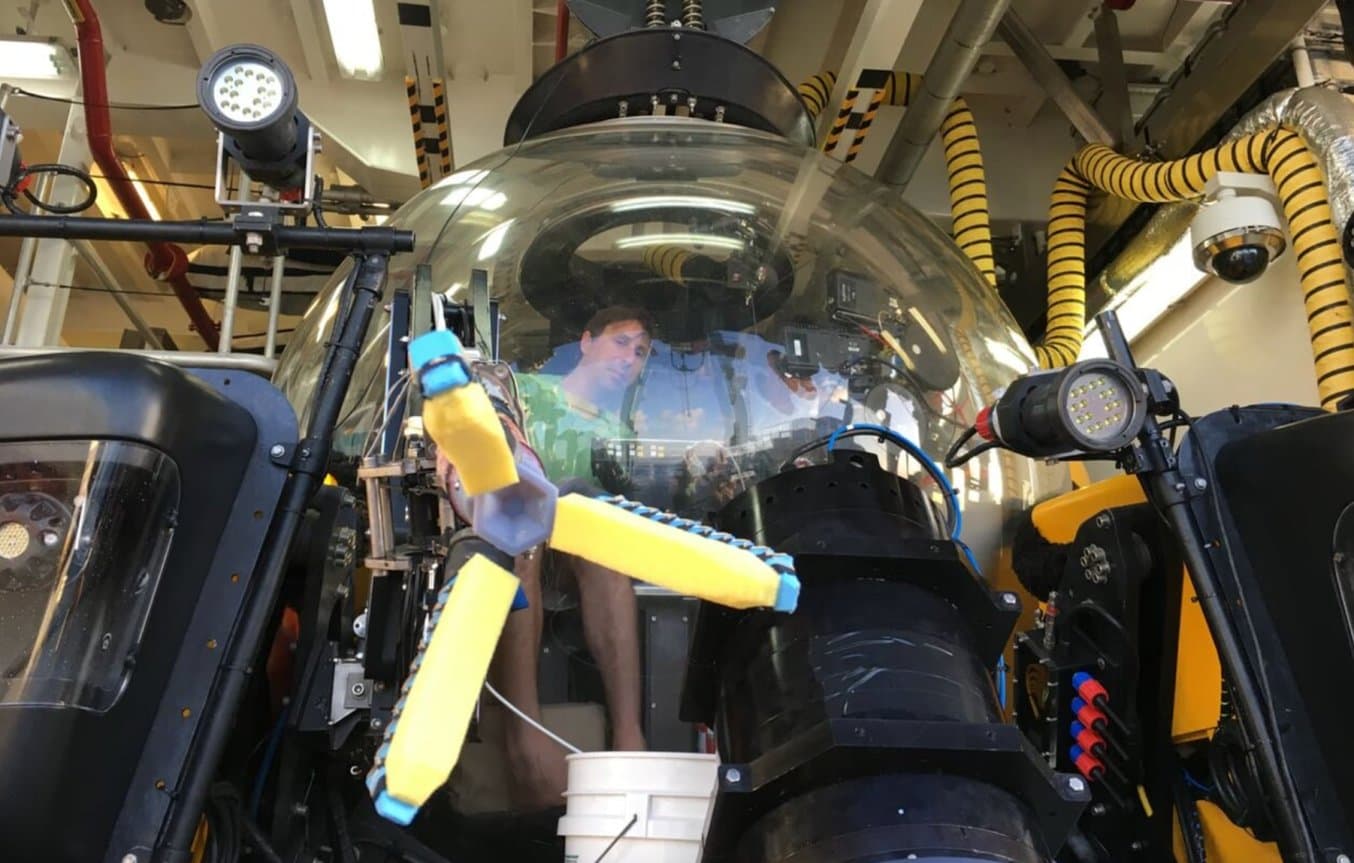
Brennan Phillips, ricercatore di robotica marina presso l'Università del Rhode Island Immagine per gentile concessione di David Gruber.
I viaggi spaziali hanno generato grande entusiasmo a livello internazionale, ma la vera ultima frontiera potrebbe essere più vicina di quanto si pensi. Nonostante gli oceani occupino oltre il 70% della superficie terrestre, la National Oceanic and Atmospheric Administration (NOAA) stima che meno del 20% sia stato completamente esplorato.1 Ma rispetto alle esplorazioni spaziali, quelle oceaniche non hanno ricevuto la stessa considerazione in termini di finanziamenti e riconoscimento. Malgrado le difficoltà, alcuni ricercatori continuano a portare avanti le loro ricerche, e hanno deciso di servirsi della stampa 3D per indagare ancora più a fondo.
Presso l'Undersea Robotics and Imaging Laboratory (URIL), parte del Bay Campus dell'Università del Rhode Island (URI), il professor Brennan Phillips e i suoi studenti costruiscono strumenti destinati alle esplorazioni oceaniche. Utilizzando le stampanti stereolitografiche (SLA) Form 3+ e Form 3L, il laboratorio stampa in 3D alloggiamenti impermeabili per videocamere e numerosi altri strumenti di ricerca per le loro attività.
Parti impermeabili sotto pressione
La mappatura degli oceani richiede la creazione di strumenti che non siano soltanto impermeabili, ma che rimangano tali anche alle profondità più estreme, dove la pressione è colossale. Phillips e i suoi studenti hanno quindi iniziato a progettare un alloggiamento per videocamera stampato in 3D che mantenesse il dispositivo al suo interno completamente asciutto, anche quando sottoposto alla pressione dell'acqua, e al contempo fosse facilmente smontabile, per poter recuperare i dati dopo l'utilizzo. Dopo decine di iterazioni, il team ha optato per questo design cilindrico costituito da due componenti stampati in Clear Resin sulla Form 3+. La struttura interna dell'alloggiamento contiene il circuito stampato e presenta un riempimento in resina epossidica in grado di mantenere l'obiettivo della videocamera sospeso nell'aria. Tutto ciò che si trova al di sotto dell'obiettivo è resina epossidica, iniettata attraverso fori incorporati nel design dell'alloggiamento.
"La sfida era realizzare la videocamera adatta alle profondità oceaniche più piccola ed economica possibile. Così ne abbiamo stampate a decine, con forme diverse. Grazie alla flessibilità della stampa 3D non ci siamo posti limiti in relazione alla forma. Possiamo creare design rapidamente, realizzare i componenti elettronici, inserirli, ottimizzare le dimensioni e infine versare la resina epossidica", spiega Phillips.
La stampa 3D ha permesso al laboratorio di eseguire iterazioni minuziose senza preoccupazioni del budget, con l'ulteriore vantaggio di una maggiore flessibilità di design rispetto alla lavorazione meccanica.
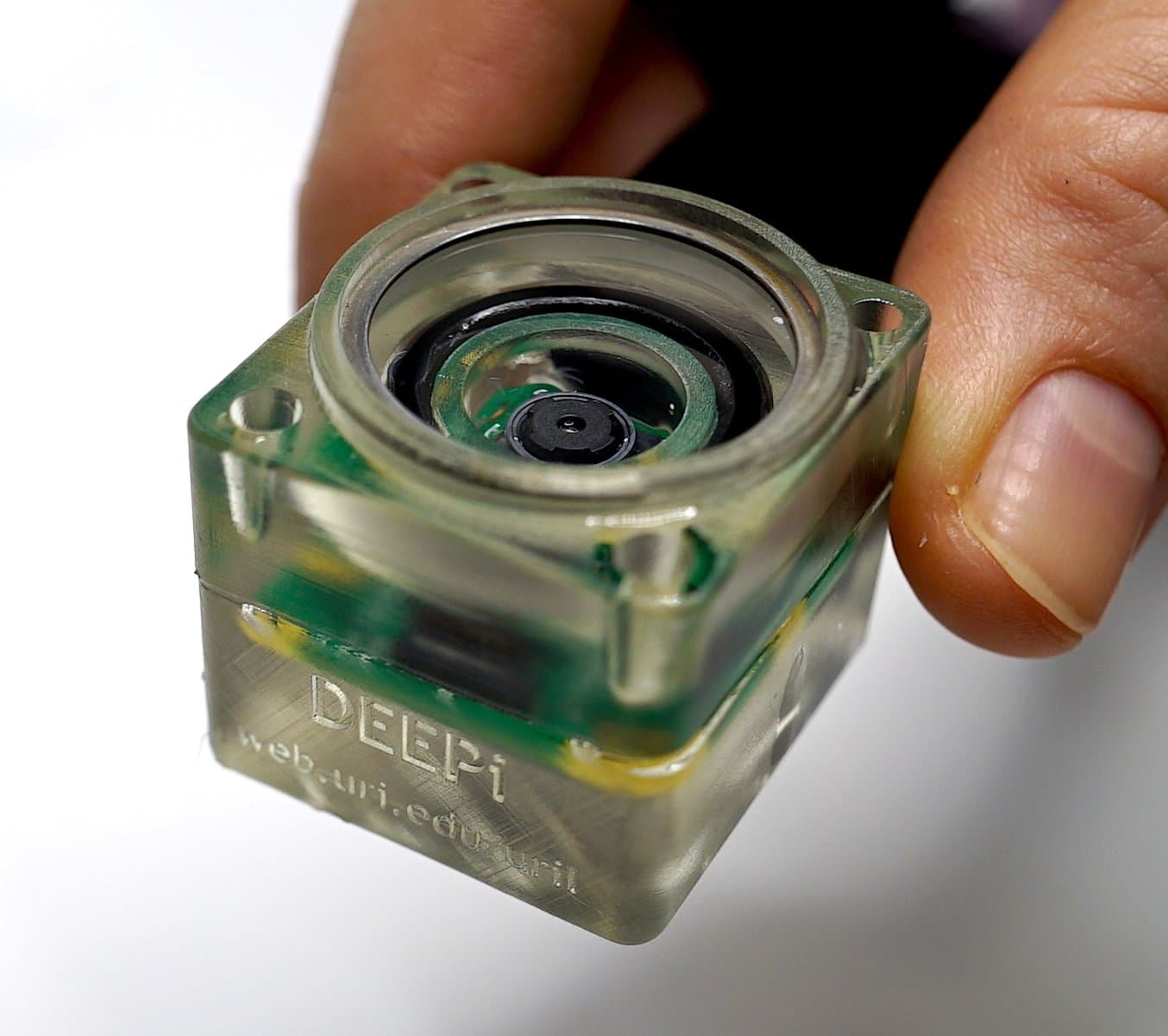
Il design della videocamera DEEPi include uno stampo ibrido realizzato in 3D, una guarnizione O-ring, un riempimento in resina epossidica per i componenti del circuito stampato e una finestra esterna in vetro trasparente (brevetto USA n. 16/920,577) (Immagine per gentile concessione di Brennan Phillips).
Una volta approvato il design a due componenti con riempimento in resina epossidica, Phillips e gli studenti hanno inserito le parti in una camera a pressione per simulare le condizioni reali delle profondità oceaniche. "È stato un vero e proprio esperimento. Ho iniziato ad aumentare sempre di più la pressione fino a raggiungere quella che si incontra a migliaia di metri di profondità. Un risultato che non ci saremmo mai aspettati", afferma Phillips.
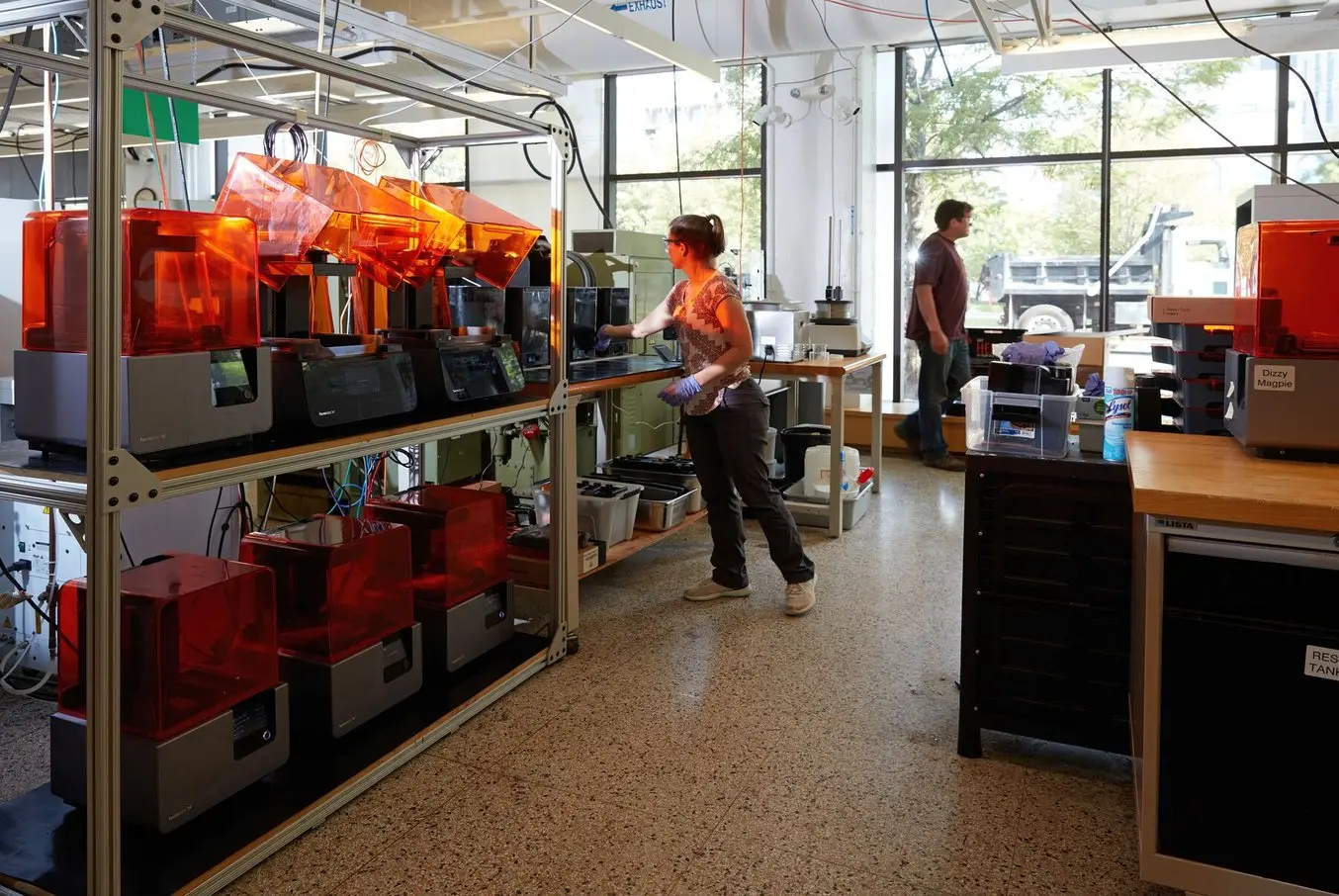
Prezzo speciale per gli istituti formativi
Gli istituti formativi accreditati possono richiedere un prezzo speciale, che include uno sconto del 10% su stampanti, hardware e accessori selezionati, oltre all'accesso gratuito alla Open Material Mode. Contatta Formlabs o un rivenditore autorizzato per verificare l'idoneità.
Perché la stampa SLA è perfetta per la robotica marina
Durante la scelta della stampante 3D, le priorità per il laboratorio di Phillips erano la precisione e le proprietà dei materiali. Le parti stampate in 3D tramite SLA, grazie alla loro natura isotropica, non sono porose e quindi non sono soggette a fuoriuscite di acqua, a differenza di quelle stampate tramite modellazione a deposizione fusa (FDM). La finitura superficiale liscia delle parti SLA garantisce inoltre che i componenti degli assemblaggi funzionali, come le due parti che formano il nostro alloggiamento cilindrico, aderiscano perfettamente tra loro senza spazi vuoti dovuti a irregolarità superficiali. La precisione e l'alta risoluzione contribuiscono alla tenuta stagna, con tolleranze e dimensioni dei dettagli incredibilmente ridotte che consentono agli utenti di stampare filettature direttamente nel materiale. Il laboratorio di Phillips applica questa procedura sia all'alloggiamento a due componenti sia alle viti, che fungono da ulteriori elementi di fissaggio.
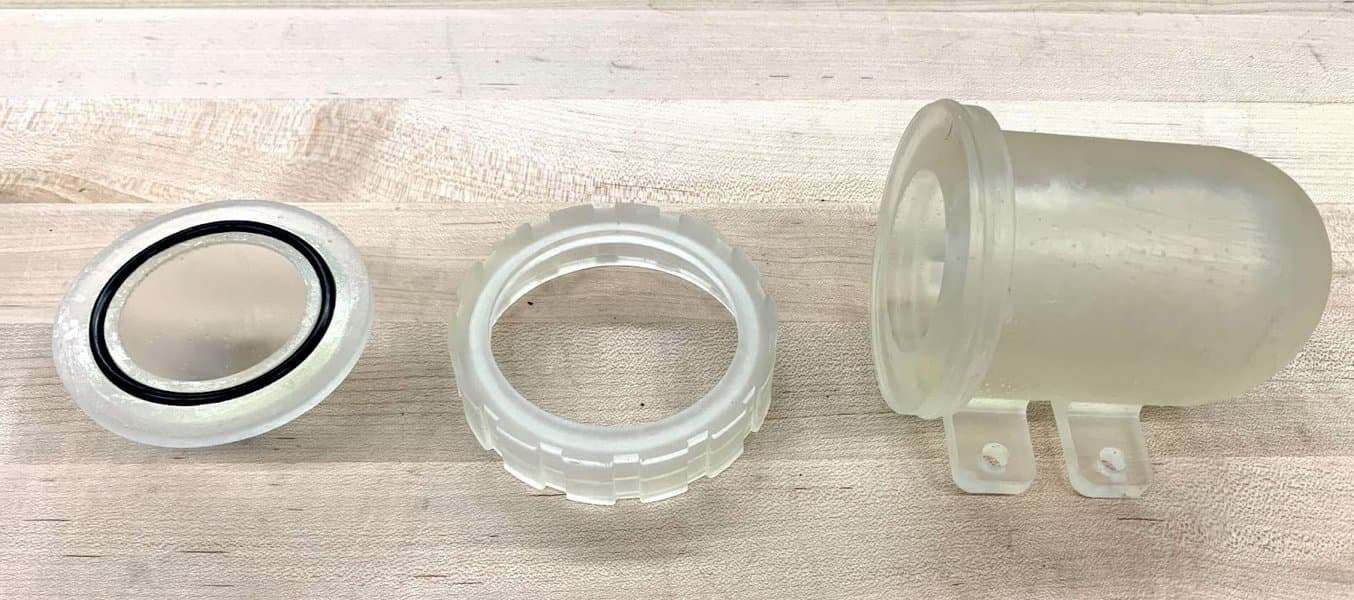
Un assemblaggio completo dell'alloggiamento stampato in 3D che, con la sua resistenza alla pressione, è in grado di proteggere i componenti elettronici dall'acqua marina a profondità di oltre 1000 metri. Le guarnizioni O-ring vengono stampate direttamente all'interno delle parti e l'alloggiamento viene sigillato con una ghiera avvitata manualmente. Foto e design per gentile concessione di Breanna Motsenbocker
"La completa densità di riempimento delle parti SLA è fondamentale. Le parti prodotte tramite modellazione a deposizione fusa offrono un certo grado di impermeabilità ma non possono resistere alla pressione oltre un paio di metri. Un altro fattore imprescindibile è la risoluzione, che deve essere perfetta affinché l'O-ring tra i due componenti crei una guarnizione sigillante. Queste parti sono pronte per l'uso appena uscite dalla stampante e al massimo effettuiamo un lieve intervento di levigatura. Ma ci assicuriamo di orientare le parti in modo che le superfici critiche siano lisce e così otteniamo una tenuta perfetta", prosegue Phillips. "Infine, le proprietà dei materiali SLA sono decisamente superiori, non c'è confronto. Sia il carico di rottura che i moduli sono migliori rispetto a qualsiasi altro materiale."
La precisione delle stampanti e la varietà dei materiali di Formlabs sono state determinanti per la principale creazione dal laboratorio, ovvero gli alloggiamenti impermeabili, che sono stati un successo non solo sulla terraferma, ma anche in mare aperto. A gennaio 2020, Phillips e i suoi studenti hanno pubblicato il processo di stampa 3D utilizzato con la Form 2, alla quale avevano aggiunto uno stabilizzatore. Così facendo sono riusciti a ottenere alloggiamenti quasi del tutto simili alle controparti stampate a terra, aprendo la strada alla stampa e all'utilizzo questi dispositivi direttamente sulle navi, ovunque ce ne sia bisogno. Questa pubblicazione scientifica, che condivide la missione del laboratorio di rendere la conoscenza delle profondità oceaniche alla portata di tutti, fornisce la prova che questi importanti strumenti possono essere prodotti in loco e in modo economico.
Adozione della Form 3L
Quando Formlabs ha annunciato l'introduzione della Form 3L, Phillips e il laboratorio sono stati tra i primi a sceglierla. "Siamo stati tra i primi ad adottare la Form 3L", afferma Phillips. Il suo grande formato ha permesso di sperimentare design subacquei più grandi e di migliorare altre funzioni del laboratorio grazie a strumenti di ricerca innovativi.
Per poter utilizzare questi alloggiamenti e altri dispositivi subacquei di monitoraggio, il team deve utilizzare e gestire migliaia di metri di cavi sottili in fibra ottica. Per evitare la formazione di nodi, hanno quindi utilizzato ruote di bicicletta riconvertite per trasferire la fibra ottica a bordo dell'imbarcazione. Grazie alla stampante SLA di grande formato, tuttavia, il team ha potuto eseguire la prototipazione dei design per ridurre le dimensioni e migliorare le prestazioni del processo.
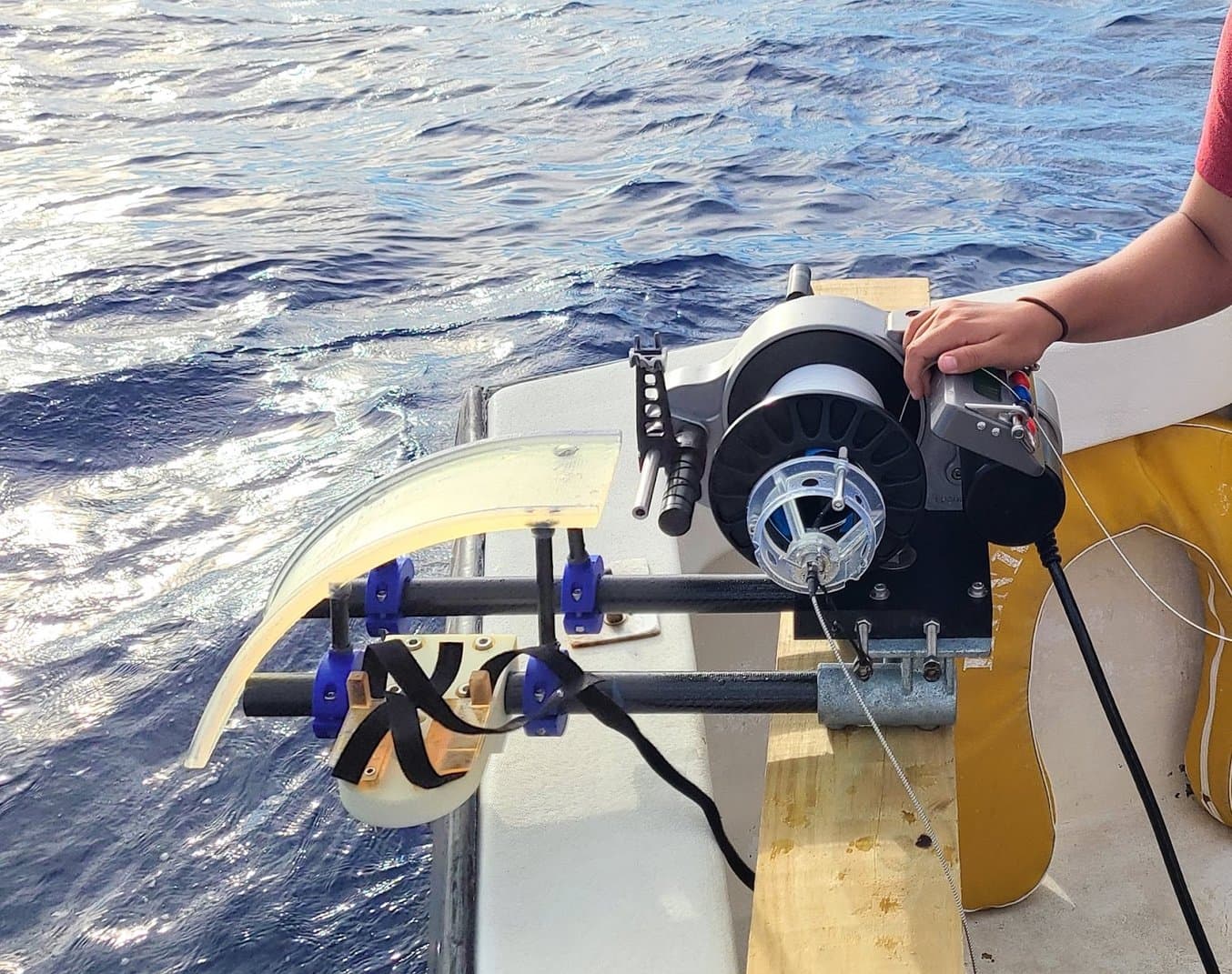
Uno "scivolo" stampato in 3D è utile per trasferire in modo agevole i cavi in fibra ottica a bordo dell'imbarcazione, senza rischi di rottura o formazione di nodi. (Immagine per gentile concessione di Brennan Phillips)
"Per questo filo da pesca non volevamo usare una puleggia rotante o una ruota, ma uno scivolo. Così abbiamo stampato tre o quattro iterazioni. È grande, funzionale e liscio, una qualità ideale per i cavi più sottili", spiega Phillips. Lo scivolo stampato in Clear Resin sulla Form 3L riduce il tempo necessario per riporre con cura il filo da pesca per un uso successivo. Inoltre, a differenza dell'attrezzatura precedente, non richiede un riposizionamento frequente.
Innovazioni in fibra ottica
Il filo da pesca, pur essendo difficile da riavvolgere, non è un materiale estremamente delicato. I cavi in fibra ottica, invece, richiedono un trattamento diverso dal filo da pesca tradizionale e, in caso di rottura, sono molto più costosi da sostituire. Il laboratorio di Phillips, in collaborazione con Nautilus Defense LL, azienda con sede a Pawtucket, Rhode Island, ha inventato un nuovo tipo di filo da pesca in fibra ottica, chiamato FOFL (in attesa di brevetto). "La fibra ottica ci permette di avere un collegamento Ethernet, video in tempo reale e molto altro, cosa che non sarebbe stata possibile su grandi distanze con cavi di rame. Abbiamo creato qualcosa di completamente nuovo: un filo da pesca in fibra ottica", dice Phillips.
Ma il filo da pesca in fibra ottica non poteva essere utilizzato da solo. Aveva bisogno di un punto terminale meccanico, che potesse essere tirato su senza danneggiare la parte centrale della fibra ottica. Poiché i cavi in fibra ottica non possono essere annodati o maneggiati allo stesso modo di altri cavi più resistenti, il laboratorio ha dovuto inventare un fissaggio per l'estremità del cavo.
Utilizzando una parte stampata in 3D con tolleranze ridotte realizzata sulle stampanti SLA ad alta risoluzione di Formlabs, è possibile separare la guaina intrecciata esterna portante del cavo dalla parte centrale più fragile in fibra ottica. Grazie a resina epossidica iniettata, la guaina aderisce al fissaggio stampato in 3D e la fibra ottica vi passa attraverso all'interno di un condotto di biforcazione metallico, che si può collegare a un computer per ricevere le informazioni trasmesse dalla fibra ottica.
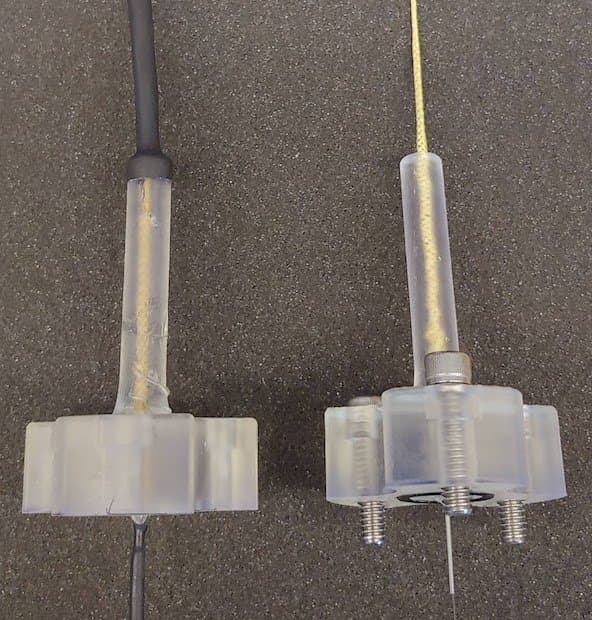
Le parti stampate tramite SLA vengono utilizzate come punti terminali meccanici per il "filo da pesca in fibra ottica", o FOFL (in attesa di brevetto), e servono a separare la guaina intrecciata esterna portante dalla parte centrale più delicata in fibra ottica. Immagine per gentile concessione di Brennan Phillips
"Questo tipo di fissaggio è estremamente resistente e può sostenere almeno 45 kg. Abbiamo anche depositato un brevetto, che abbiamo reso disponibile per la libera divulgazione", spiega Phillips. "Senza la stampa 3D, in un normale processo di produzione, questi componenti arriverebbero a costare dai 3000 ai 4000 $ ciascuno. E considerate che noi abbiamo eseguito diverse iterazioni. Penso che nessuno abbia percorso questa strada, perché è troppo costosa. Ma grazie alla combinazione di metodi di prototipazione rapida, come quelli resi possibili dalle stampanti Formlabs, e del nuovo cavo in fibra ottica, nuove idee come questa potranno vedere la luce", prosegue Phillips.
Guarnizioni stampate in 3D in modo più economico
Prima della stampa 3D, la realizzazione di questi strumenti era costosa, perciò i team di ricerca esitavano ad apportare le modifiche di design necessarie, e neanche i programmi di studio disponevano di sufficienti finanziamenti per svilupparli. L'Undersea Robotics and Imaging Laboratory fa parte di un movimento globale che ha l'obiettivo di ampliare l'accesso alla scienza delle profondità oceaniche, rendendola più democratica ed economica, così da incrementare la consapevolezza collettiva relativa agli oceani. "Ho iniziato a stampare in 3D tappi terminali con guarnizioni O-ring integrate, e ha funzionato. Lo stesso processo eseguito con la lavorazione meccanica costerebbe centinaia o migliaia di dollari e i disegni dovrebbero essere incredibilmente precisi. Grazie a queste stampanti posso realizzare tre o quattro parti e ottenere subito la giusta aderenza, il tutto spendendo circa 50 $ per i materiali", dice Phillips.
Il team del laboratorio non si è limitato a stampare solo parti per utilizzo finale, ma ha anche creato un workflow efficiente per produrre gli stampi con la Clear Resin. Il risultato finale è una soluzione ottimizzata per separare rapidamente i cavi subacquei utilizzando stampi realizzati in 3D.
Un'ampia gamma di casi d'uso
Le stampanti Formlabs del laboratorio di Phillips vengono utilizzate per la prototipazione, la creazione di prodotti per utilizzo finale, la produzione rapida di attrezzature, dime e fissaggi, nonché dispositivi medici.Anche in un piccolo laboratorio di ricerca come quello di Phillips e dei suoi studenti, la gamma di applicazioni e di opportunità viene costantemente ampliata grazie a un forte spirito innovativo.
Durante la pandemia di COVID-19, Phillips e i suoi studenti si sono resi conto di poter fornire un aiuto concreto per affrontare la crisi nell'area del Rhode Island. Dopo aver eseguito test e ricerche approfondite, hanno pubblicato i risultati relativi al rilascio di particolati chimici della Surgical Guide Resin di Formlabs, utilizzata nelle parti stampate in 3D per respiratori. Oltre a raggiungere il traguardo della pubblicazione scientifica, hanno anche inviato i risultati ottenuti all'Agenzia per gli alimenti e i medicinali degli Stati Uniti (FDA) e all'Emergency Use Authorization (EUA) per l'approvazione.
"Durante la pandemia c'è stata una grande mobilitazione e anche per noi era molto importante contribuire e aiutare come potevamo. Grazie alla qualità di queste stampanti e alla possibilità di utilizzare la Surgical Guide Resin, abbiamo potuto farlo a un livello ancora più alto", spiega Phillips.
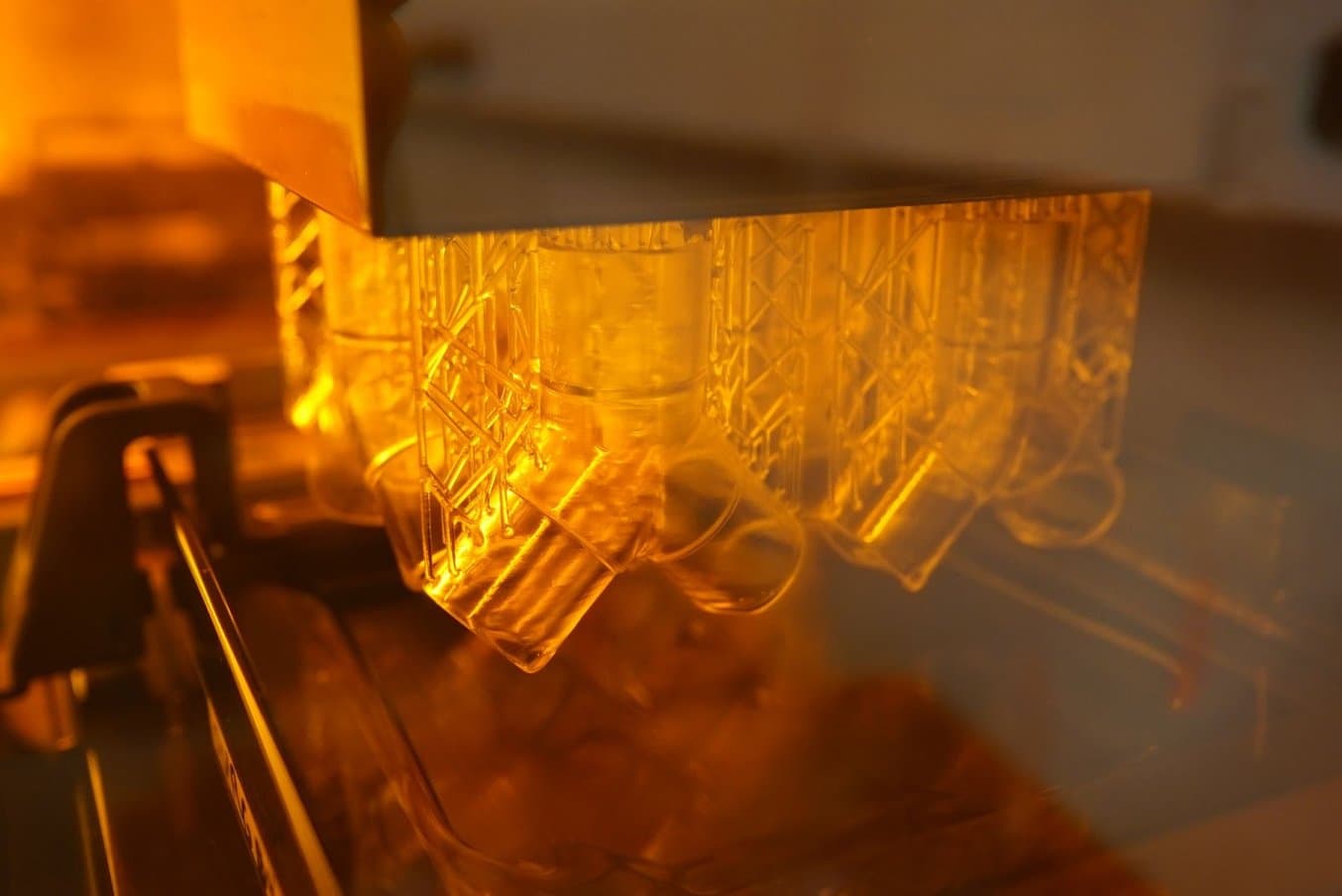
I separatori a Y per respiratori, progettati in collaborazione con i team di ricerca della Brown University e del Rhode Island Hospital, sono stati stampati in 3D in Surgical Guide Resin durante le prime fasi della pandemia di COVID-19. Immagine per gentile concessione di Brennan Phillips
Profondità oceaniche alla portata di tutti
I minori costi per la produzione di queste parti non sono soltanto vantaggiosi per il budget del laboratorio, ma consentono anche agli studenti di accedere a questi apparecchi e di utilizzarli per testare nuove idee (con tutti gli errori e fallimenti del caso). Gli studenti universitari che progettano parti per la prima volta possono quindi usare la stampa 3D e apprendere i segreti di questa tecnologia senza paura di sbagliare e sprecare risorse costose.
Ogni anno, gli studenti del secondo anno della URI hanno anche l'opportunità di progettare e stampare in 3D alloggiamenti resistenti alla pressione, contribuendo così alla ricerca e al contempo imparando nuove competenze in ambito di stampa 3D e CAD. "Prima di queste stampanti 3D, gli studenti non avrebbero potuto progettare o realizzare alloggiamenti subacquei fino alla laurea o finché non avessero iniziato a lavorare nel settore. La formazione era davvero impegnativa per via dei costi e dell'accesso estremamente selettivo. Ma queste stampanti hanno aperto una nuova strada. È persino capitato che uno studente di scuola superiore realizzasse un alloggiamento resistente alla pressione", afferma Phillips.
Queste opportunità non si limitano esclusivamente agli studenti universitari americani. Infatti, Phillips fa parte di una comunità internazionale che si propone di migliorare l'accesso agli strumenti per la ricerca delle profondità oceaniche nei paesi costieri svantaggiati di tutto il mondo. "Ci stiamo impegnando per ampliare le capacità di quei paesi che vorrebbero condurre le proprie esplorazioni oceaniche. Il denaro, così come la formazione, rappresenta una limitazione, ma questi metodi hanno davvero il potenziale di aprire nuove strade, rendendo più democratica l'esplorazione delle profondità oceaniche", spiega Phillips.
1 https://oceanservice.noaa.gov/facts/exploration.html
2 Brennan T. Phillips, Josh Allder, Grady Bolan, R. Sean Nagle, Allison Redington, Tess Hellebrekers, John Borden, Nikolai Pawlenko, Stephen Licht,
Additive manufacturing aboard a moving vessel at sea using passively stabilized stereolithography (SLA) 3D printing, Additive Manufacturing, Volume 31, 2020, 100969, ISSN 2214-8604, https://doi.org/10.1016/j.addma.2019.100969.