Di recente, Formlabs ha pubblicato un whitepaper sullo stampaggio a iniezione con stampi realizzati in 3D per la produzione rapida su scala ridotta e ha organizzato un webinar gratuito all’interno del quale diversi esperti di stampaggio a iniezione hanno discusso il modo in cui la stampa 3D permette di produrre stampi su richiesta per la creazione di centinaia di parti, passando dall’idea iniziale alla produzione nel giro di pochi giorni.
Il webinar ha avuto un grande successo e abbiamo ricevuto quasi 100 domande dai partecipanti. In questo articolo risponderemo alle domande più frequenti riguardanti lo stampaggio a iniezione con stampi realizzati in 3D.
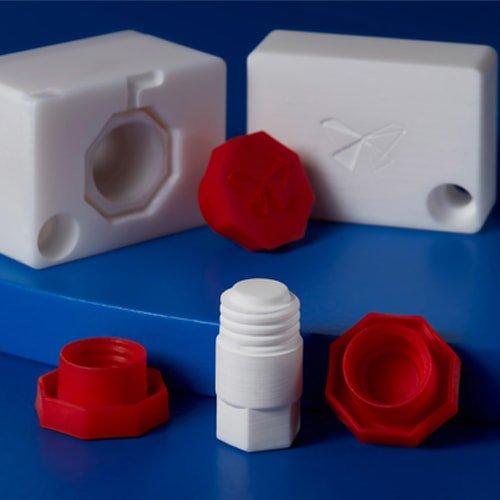
Stampaggio a iniezione rapido su scala ridotta con stampi realizzati in 3D
Scarica il nostro whitepaper per ottenere linee guida su come utilizzare stampi realizzati in 3D per i processi di stampaggio a iniezione, in modo tale da poter ridurre costi e tempi di realizzazione. Inoltre potrai esaminare i casi studio reali di Braskem, Holimaker e Novus Applications.
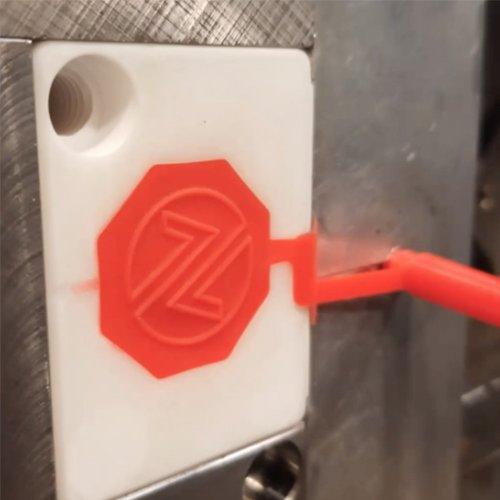
Produzione rapida di piccoli lotti di stampi per stampaggio a iniezione
Guarda questo dibattito nel quale gli esperti di stampaggio a iniezione spiegheranno come la stampa 3D permette di produrre stampi su richiesta per la creazione di centinaia di parti, passando dall’idea iniziale alla produzione nel giro di pochi giorni.
Attrezzatura
D: Potete consigliare un apparecchio per lo stampaggio a iniezione?
Il tipo di pressa per iniezione non ha un impatto significativo sul processo, a patto che sia possibile impostare alcuni parametri fondamentali, come la pressione, la temperatura e la pressione per il serraggio. Tra le aziende di cui parliamo all’interno del whitepaper, Braskem utilizza la pressa interamente elettrica Cincinnati Milacron 110 Ton Roboshot, mentre Novus Applications usa la pressa elettrica Sumitomo da 50 tonnellate. Gli apparecchi per stampaggio automatizzati come quelli della linea Babyplast sono valide alternative per la produzione in serie di piccole parti.
Se non hai dimestichezza con lo stampaggio a iniezione e vuoi sperimentarlo con investimenti e manutenzione limitati, un’opzione può essere quella di usare una macchina da stampaggio desktop manuale dal prezzo accessibile, come la Holipress o la Galomb Model-B100.
Alcuni dei nostri clienti hanno anche consigliato sistemi prodotti da Minijector, Morgan, APSX o Micromolder.
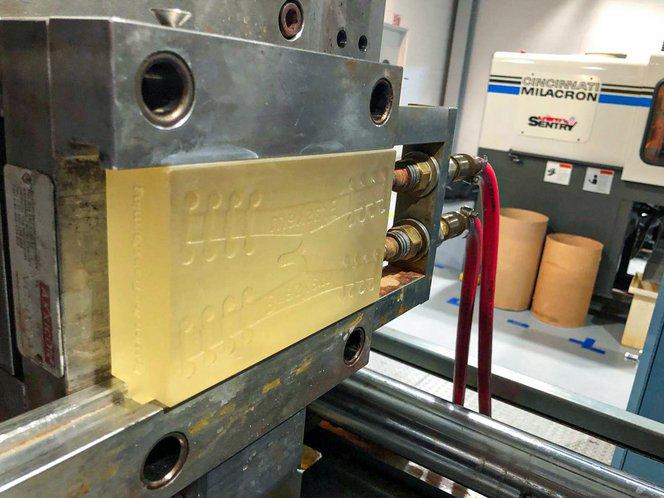
Gli stampi a iniezione prodotti in 3D sono adatti sia agli apparecchi industriali per lo stampaggio a iniezione, sia per dispositivi desktop di dimensioni ridotte.
D: Quali materiali per l’iniezione sono compatibili con i materiali Formlabs?
I nostri clienti hanno utilizzato gli stampi realizzati in 3D con materiali Formlabs per l'iniezione di un'ampia gamma di termoplastiche tra cui polipropilene, polietilene, elastomero termoplastico, poliuretano termoplastico, poliossimetilene, acrilonitrile-butadiene-stirene e poliammide. Con un materiale a bassa viscosità è possibile ridurre la pressione e allungare la vita utile dello stampo. Il polipropilene e gli elastomeri termoplastici sono semplici da processare a un alto numero di cicli. Al contrario, plastiche più tecniche come il poliammide consentiranno un numero minore di cicli. L’uso di un agente distaccante aiuta a separare la parte dallo stampo, soprattutto nel caso di materiali flessibili come il poliuretano termoplastico o gli elastomeri termoplastici.
Panoramica del procedimento
D: Quel è la vita utile di uno stampo realizzato in 3D e che cosa rende uno stampo inutilizzabile? Che cosa si intende per piccoli lotti?
La vita utile di uno stampo realizzato in 3D varia in base al design, al materiale usato per l’iniezione e alle condizioni di stampaggio. Non dovremmo aspettarci che uno stampo polimerico realizzato in 3D assicuri le stesse prestazioni di uno realizzato in metallo tramite lavorazione meccanica. Gli stampi di grandi dimensioni sono i più difficili da realizzare: il tempo di raffreddamento è maggiore, perché il trasferimento termico è più lento nelle plastiche. Gli stampi realizzati con High Temp Resin o Rigid 10K Resin possono danneggiarsi o rompersi se sottoposti a pressione. Solitamente, gli stampi diventano inutilizzabili quando iniziano ad apparire fratture da sollecitazione. A volte può verificarsi la delaminazione degli angoli e dei particolari, che si staccano insieme alla parte.
La maggior parte dei nostri utenti producono centinaia di parti con ciascuno stampo, utilizzando materiali a bassa viscosità come il polipropilene. Le plastiche più tecniche come il poliammide consentiranno un numero minore di cicli. Tuttavia, gli stampi possono essere stampati più volte e possono essere sostituiti con facilità a seconda del sistema utilizzato. Non abbiamo effettuato alcuno studio riguardante l’impatto del tempo di ciclo sulla rottura degli stampi.
D: In quale misura tecnologie come la sinterizzazione laser selettiva o la modellazione a deposizione fusa sono comparabili alla stereolitografia per la stampa 3D di stampi per iniezione?
La tecnologia di stampa stereolitografica (SLA) è la scelta ideale per lo stampaggio a iniezione. È caratterizzata da una finitura superficiale liscia e da un’elevata precisione, che lo stampo conferirà alla parte finale. Questa qualità facilita la rimozione dallo stampo stesso se comparata con stampi realizzati mediante modellazione a deposizione fusa o sinterizzazione laser selettiva. Le stampe 3D realizzate mediante stereolitografia sono legate chimicamente in modo tale da risultare dense e isotropiche, e producono stampi funzionali in una qualità altrimenti non ottenibile con la modellazione a deposizione fusa.
D: Qual è la differenza in termini di costo tra questo processo e gli stampi in metallo tradizionali?
Gli stampi per iniezione stampati in 3D comportano una spesa di 25-200 $ in termini di materiali, in base alle dimensioni. Gli stampi in metallo tradizionali hanno costi molto variabili, a partire da 200 $, fino a più di 10 000 $, a seconda delle dimensioni e della complessità, nonché della disponibilità di macchinari per la lavorazione CNC in-house da parte della tua azienda o della necessità di esternalizzare la produzione dello stampo.
In generale, la convenienza derivante dall’uso degli stampi per iniezione in metallo aumenta all’aumentare dei volumi, in quanto il costo dello stampo viene suddiviso tra un numero maggiore di parti.
Il risparmio provocato dall’uso di stampi per iniezione realizzati in 3D può essere considerevole. Durante la produzione di 6000 estensori per mascherine, Braskem ha ridotto i costi del 97% rispetto all’esternalizzazione di uno stampo in metallo.
D: In quali casi ha senso usare lo stampaggio a iniezione e non la stampa 3D per la produzione di volumi ridotti?
La stampa 3D permette di produrre prototipi e parti funzionali in modo rapido, a costo ridotto e in un’ampia varietà di materiali. In generale, consigliamo di usare la stampa 3D per prototipi e parti durante le fasi inziali dello sviluppo di prodotto, quando è probabile che il design subisca modifiche, nonché per la produzione di volumi ridotti. A seconda dell’applicazione, la stampa 3D può anche essere adatta alla produzione di parti per uso finale. Inoltre la stampa 3D può essere impiegata per la creazione di design complessi che sarebbero impossibili da realizzare con lo stampaggio a iniezione.
Se non trovi un materiale per la stampa 3D adatto alle tue esigenze o se preferisci usare termoplastiche tradizionali, lo stampaggio a iniezione con stampi realizzati in 3D potrebbe essere la scelta migliore. Quando hai bisogno di centinaia di prototipi identici spesso è più rapido stampare un solo stampo e procedere con l’iniezione, piuttosto che stampare in 3D centinaia di parti (a seconda della geometria della parte e della tecnologia di stampa). Siccome i materiali per la stampa 3D sono più costosi, anche la convenienza dello stampaggio a iniezione aumenta all’aumentare dei volumi.
D: Si verificano problemi di cristallinità delle parti con l’utilizzo di stampi realizzati in 3D?
Non abbiamo notato alcun problema di cristallizzazione delle parti con l’utilizzo di stampi realizzati in 3D, né abbiamo ricevuto feedback a riguardo.
Processo di design
La complessità del processo di stampaggio a iniezione deriva in gran parte dalla complessità della parte e della struttura dello stampo. Alcune caratteristiche di design aiutano a migliorare la precisione dimensionale e ad estendere la vita utile degli stampi. Il nostro whitepaper fornisce linee guida di progettazione dettagliate che vanno tenute in considerazione quando si usano stampi realizzati in 3D invece di stampi in metallo.
D: Qual è l’angolo di sformo consigliato? Qual è la profondità consigliata per gli sfiati? Lo sfiato di grandi dimensioni serve al movimento dell’aria o del polimero?
Se possibile, consigliamo angoli di sformo tra i due e i cinque gradi.
Gli sfiati d’aria permettono all’aria di fuoriuscire ed aiutano a evitare che rimanga intrappolata nello stampo. Consigliamo una profondità di 0,05 mm.
D: Come si può evitare di sprecare materiale di stampa? Potete spiegare in maniera più chiara cosa si intende per “svuotare uno stampo di grandi dimensioni”? Ha un significato correlato al mantenimento di uno spessore delle pareti uniforme?
“Svuotare uno stampo di grandi dimensioni” significa adattare la parte posteriore dello stampo per ridurre il consumo di materiale. La riduzione della sezione trasversale nelle aree che non supportano la cavità permette di ridurre il costo dei materiali e il rischio di errori di stampa o deformazioni. È necessario mantenere uno spessore delle pareti uniforme nelle aree che supportano la cavità.
D: Come si possono risolvere problemi di allineamento e linee di separazione quando si usano stampi in due metà?
Consigliamo di progettare un lato piatto, mentre l'altro riprodurrà il design desiderato. In questo modo si ridurranno le possibilità di disallineamento dei blocchi e il rischio di rughe. Se questo non fosse possibile, consigliamo di sottoporre lo stampo ottenuto a post-elaborazione: la fresatura o la levigazione manuali possono aiutare a far aderire le due parti dello stampo e a evitare la fuoriuscita di materiale in eccesso.
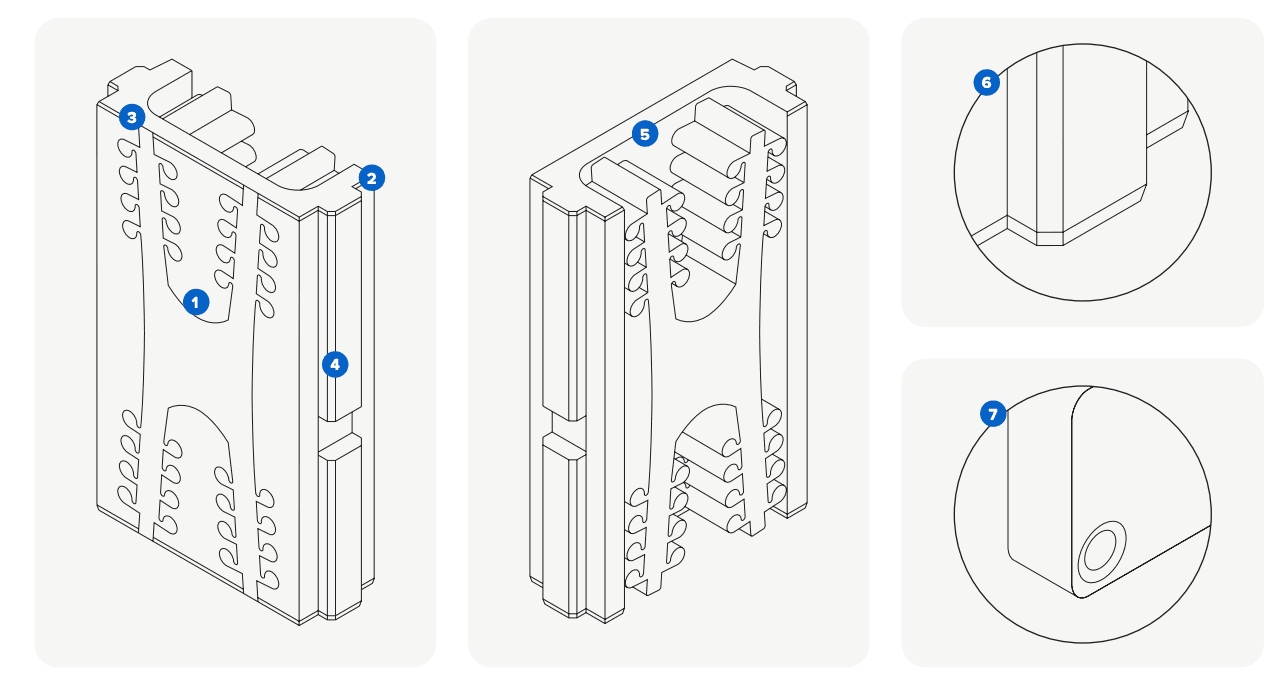
Oltre alle regole generali per la progettazione degli stampi per iniezione, ci sono diversi modi di estendere la vita utile degli stampi e garantirne la precisione dimensionale. Scarica il nostro whitepaper per linee guida dettagliate.
D: Quanto piccoli possono essere i dettagli?
Consigliamo di seguire le linee guida per la progettazione della produzione additiva. Puoi scaricare la guida di progettazione per la Form 3 di Formlabs. Consigliamo inoltre di evitare le sezioni trasversali sottili: uno spessore superficiale inferiore a 1-2 mm può deformarsi con il calore. Potrebbe essere difficile ottenere un buon livello di definizione per i dettagli negativi di dimensioni inferiori a 0,5 mm, mentre i dettagli sporgenti di dimensioni inferiori a 0,1 mm potrebbero essere soggetti a rotture.
D: Gli stampi realizzati in 3D permettono i movimenti laterali?
Sì. A questo proposito, consulta il caso di studio relativo a Novus Applications nel whitepaper.
Processo di stampa
D: Avete raccomandazioni riguardo al restringimento che si verifica a seguito della realizzazione degli stampi?
Stampa uno stampo preliminare per comprendere le variazioni dimensionali. Consigliamo di aggiungere materiale in eccesso al modello CAD dello stampo in modo da compensare le variazioni dimensionali. Sottoponi lo stampo a post-elaborazione per effettuare aggiustamenti manuali. La fresatura o la levigazione manuali permetteranno di ottenere le dimensioni ottimali, di far aderire perfettamente le due metà dello stampo e di evitare la fuoriuscita di materiale in eccesso.
D: Come si possono trattare le linee degli strati sulle stampe con cavità?
Consigliamo di stampare usando il minimo spessore dello strato possibile. La tecnologia di stampa stereolitografica è un'ottima scelta per lo stampaggio in quanto le parti realizzate sono caratterizzate da una finitura superficiale liscia e da un’elevata precisione.
D: È possibile aggiungere una finitura superficiale, una trama o un motivo a rilievo sugli strumenti per lo stampaggio a iniezione realizzati in 3D? Si tratta di un procedimento da svolgere durante la post-elaborazione o è possibile stampare queste caratteristiche direttamente sulla superficie?
La stereolitografia è una soluzione ideale per aggiungere una trama alle parti. Grazie all’elevata risoluzione, è in grado di riprodurre dettagli complessi e di piccole dimensioni. In genere, le superfici stampate senza strutture di supporto non richiedono alcun intervento di post-elaborazione.
D: Ci sono altri materiali consigliati per lo stampaggio a iniezione, oltre alla High Temp Resin e alla Rigid 10K Resin?
Alcuni clienti, tra i quali Holimaker, usano la Grey Pro Resin. La conduttività termica e la stabilità dimensionale della Grey Pro Resin sono inferiori a quelle della High Temp Resin e della Rigid 10K Resin, ma questo materiale è più morbido e ha un maggiore allungamento a rottura, e questo gli consente di sopportare un elevato numero di cicli prima di rompersi.
D: Qual è il processo di polimerizzazione per la High Temp Resin e per la Rigid 10K Resin per questa applicazione?
Consigliamo di effettuare la polimerizzazione post-stampa delle parti in High Temp Resin con supporti per 120 minuti a 80 °C e di effettuare la polimerizzazione post-stampa termica per tre ore a 160 °C. Consulta la pagina di assistenza qui.
Consigliamo di effettuare la polimerizzazione post-stampa delle parti in Rigid 10K Resin con supporti nella Form Cure per 60 minuti a 70 °C e poi di riscaldarle a 125 °C per 90 minuti per ottenere una maggiore temperatura di distorsione termica. Consulta la pagina di assistenza qui.
D: Quali sono le dimensioni massime degli stampi che si possono realizzare con questo procedimento? Il procedimento è adatto alla Form 3L?
Gli stampi realizzati in High Temp Resin e Rigid 10K Resin possono essere stampati sulla Form 3L, con un volume di stampa massimo di 33,5 x 20 x 30 cm. Tuttavia, gli stampi di grandi dimensioni saranno difficili da stampare e l’iniezione potrebbe rivelarsi complicata.
Condizioni di stampaggio
D: Gli stampi per iniezione realizzati in 3D sono compatibili soltanto con i processi a bassa temperatura e a bassa pressione? Quali sono la pressione e la temperatura di iniezione raccomandate?
La riduzione della pressione e della temperatura aiuterà a ridurre il rischio di rottura dello stampo e ad allungare la sua vita utile. Tuttavia, il design dello stampo influenzerà molto l’impatto della pressione sulla cavità.
Nei casi di studio inclusi nel nostro whitepaper, Braskem ha realizzato l’iniezione delle parti a 230 °C e a una pressione di 5000 PSI, mentre nel caso di Novus Applications la pressione al momento della rottura è stata di 11 500 PSI a 210 °C.
La High Temp Resin ha una temperatura di distorsione termica di 238 °C a 0,45 MPa. La Rigid 10K Resin ha una temperatura di distorsione termica di 218 °C a 0,45 MPa e un modulo di elasticità di 10 000 MPa.
D: Consigliate di utilizzare cornici in alluminio con inserti stampati in 3D? È possibile utilizzare stampi realizzati in 3D e senza le cornici in alluminio?
Sì, gli stampi per iniezione realizzati in 3D possono essere usati senza cornici in alluminio, ma si consiglia di posizionare lo stampo ottenuto in una cornice metallica o di stampare l'inserto e realizzare la parte esterna dello stampo tramite lavorazione meccanica per creare un sostegno contro la pressione verso il basso e il calore dell'ugello di iniezione.
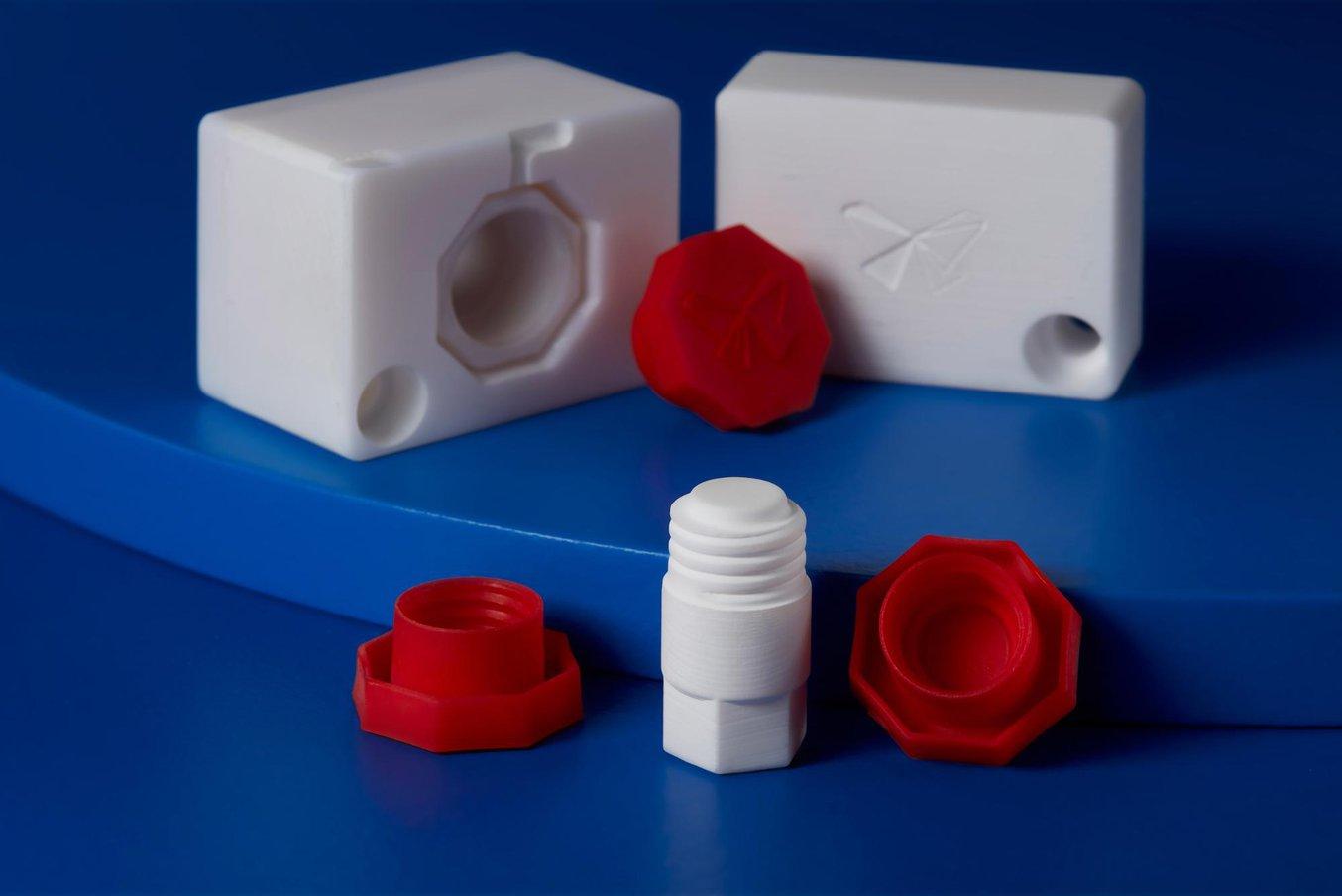
Gli stampi per iniezione realizzati in 3D permettono i movimenti laterali.
Raffreddamento
D: I tempi di raffreddamento sono superiori per gli stampi realizzati in 3D rispetto agli stampi metallici?
Sì, i tempi di raffreddamento sono superiori per gli stampi per iniezione realizzati in 3D in quanto il trasferimento termico è più lento per le parti in plastica. Il posizionamento dello stampo all’interno di una cornice metallica ne assorbe parzialmente il calore e aiuta a ridurre i tempi di raffreddamento. In alternativa, è possibile stampare in 3D più stampi e alternarne l’uso per i diversi cicli in modo da ridurre il tempo di ciclo.
D: Come si procede al raffreddamento delle parti? È necessario aggiungere canali di raffreddamento?
È possibile accelerare il raffreddamento usando lotti intercambiabili, in modo da effettuare nuovi cicli mentre le altre serie si raffreddano, riducendo così il tempo di ciclo e compensando la bassa conduttività termica degli stampi in plastica. Gli stampi usati nei nostri casi di studio non avevano alcun canale di raffreddamento, ma questa potrebbe essere una soluzione, insieme all’applicazione di aria compressa.
Rimozione dello stampo
D: Come si estraggono le parti? È necessario usare un agente distaccante per gli stampi realizzati in 3D? Ne consigliate uno in particolare?
Nei casi di studio inclusi nel nostro whitepaper non sono stati usati perni di estrazione. Ciascuna parte è stata rimossa manualmente. Il processo di estrazione delle parti è facilitato dall’inclusione di angoli di sformo elevati e dalla stampa con uno spessore dello strato ridotto, che garantisce una finitura superficiale liscia. A seconda del materiale usato per l’iniezione, l’adesione della parte allo stampo più causare il deterioramento dello stampo in fase di estrazione, in particolare per materiali flessibili quali i poliuretani e gli elastomeri termoplastici.
L’utilizzo di un agente distaccante è una buona soluzione per facilitare la separazione della parte dallo stampo. Gli agenti distaccanti con silicone sono compatibili con la Grey Pro Resin, la High Temp Resin e la Rigid 10K Resin di Formlabs. Novus Applications si serve dei prodotti di Slide, mentre Braskem adotta il distaccante con silicone sicuro per gli alimenti MR303 di Sprayon.
Processi correlati
D: È possibile galvanizzare gli stampi realizzati in 3D per allungarne la vita utile?
Le parti stampate in 3D tramite stereolitografia possono essere galvanizzate. Guarda il webinar su questo argomento per scoprire di più su questo procedimento. Al momento non siamo in grado di dare indicazioni sull’efficacia o meno della galvanizzazione per allungare la vita utile degli stampi.
D: È possibile usare le parti stampate in 3D con prodotti Formlabs per altri processi di stampaggio?
Sì. Ingegneri e produttori hanno adottato la stampa 3D per varie tecniche di produzione degli stampi, in molti settori diversi. Visita il nostro sito dedicato alle risorse per scoprire di più sull’utilizzo di tecniche che includono stampi e modelli stampati in 3D, ad esempio termoformatura, stampaggio in silicone, fusione in sabbia, fusione a cera persa e processi di laminazione.
Hai altre domande su come usare la stampa 3D per lo stampaggio a iniezione? Scarica il whitepaper e guarda il webinar per linee guida dettagliate e casi di studio reali, oppure contatta il nostro team vendite direttamente.