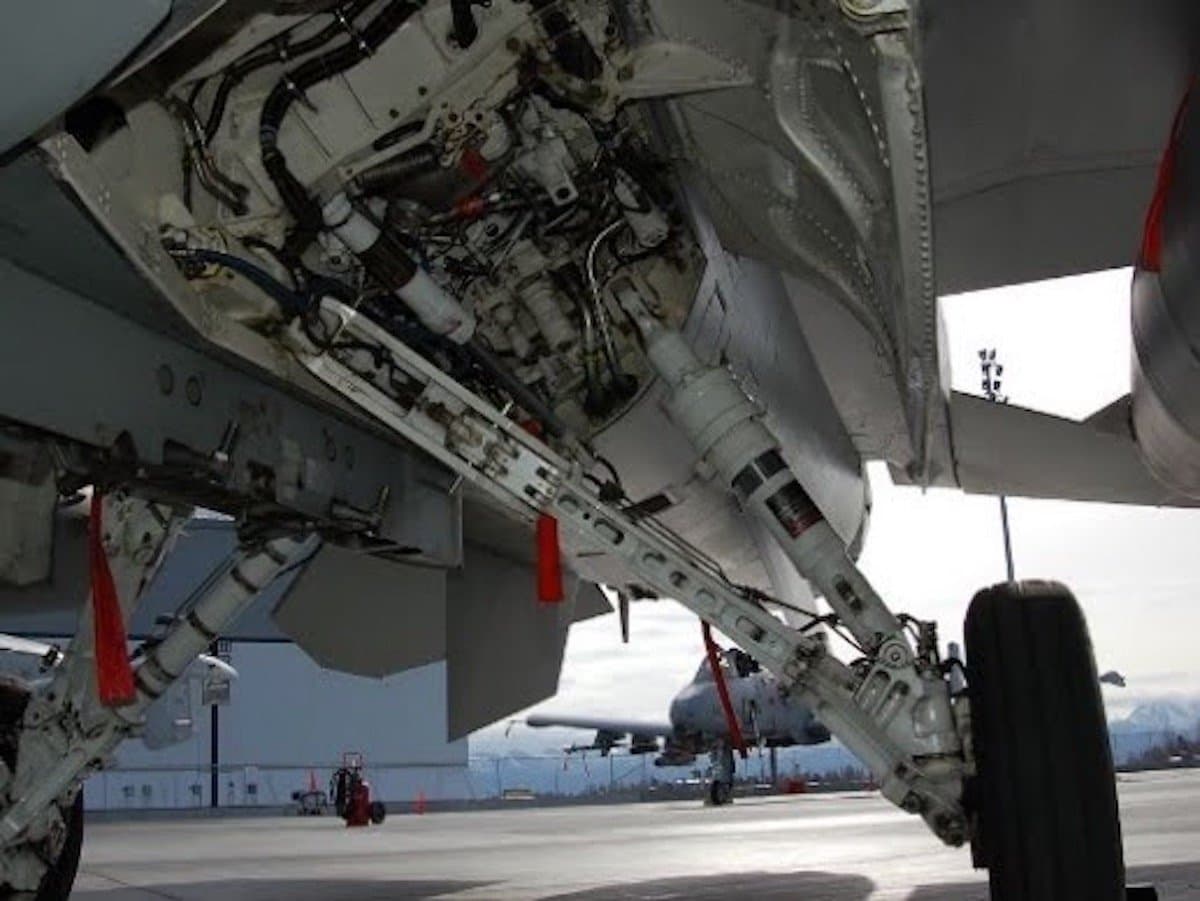
Per ogni ora di volo di un jet gestito dal Dipartimento della difesa degli Stati Uniti, vengono completate circa 12 ore di manutenzione. Sebbene manutenzione, riparazione e revisione siano fondamentali per garantire che ogni velivolo operi in sicurezza e al massimo delle prestazioni, spesso queste attività si prolungano a causa degli interventi manuali e dei processi tradizionali impiegati.
Il Dipartimento della difesa è alla costante ricerca di modi per migliorare queste operazioni e rendere il workflow più efficiente. Figure Engineering, grazie al nuovo ecosistema aperto di Formlabs, ha sviluppato una soluzione innovativa e conveniente per raggiungere questo obiettivo.
Figure Engineering sfrutta la velocità della stampante 3D stereolitografica (SLA) Form 4 per sviluppare un nuovo materiale specifico per la mascheratura e la produzione delle attrezzature utilizzate nel processo di galvanizzazione. L'editor delle impostazioni di stampa e la Open Material Mode hanno permesso a Jonathon McDaniels, cofondatore di Figure Engineering, di mettere a punto insieme al suo team il processo di sviluppo del materiale e trovare una nuova soluzione per un problema dal valore di milioni di dollari.
Ricerca di una soluzione avanzata
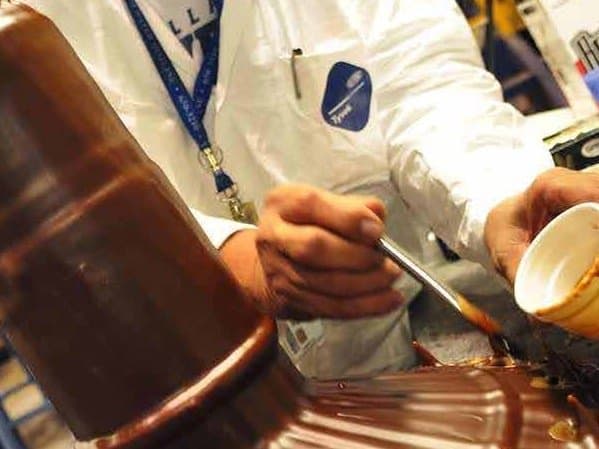
La verniciatura manuale con smalti per mascherare le parti destinate alla galvanizzazione può presentare dei rischi se i materiali impiegati sono tossici. Quando il personale raggiunge i limiti di esposizione, è necessario fermare l'intero progetto, aumentando potenzialmente i tempi di inattività dei velivoli.
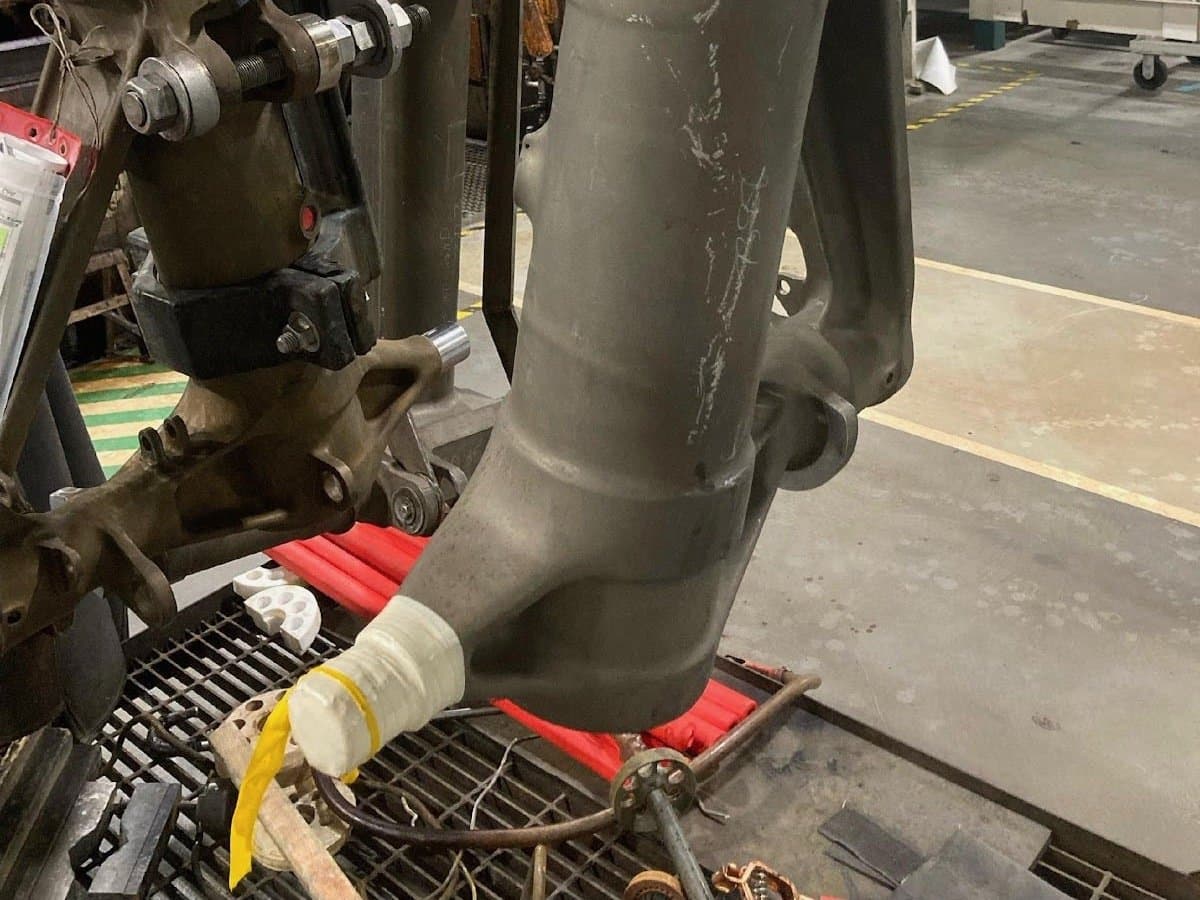
L'applicazione manuale del nastro adesivo per mascherare specifiche aree nel processo di galvanizzazione è dispendiosa in termini di tempo e manodopera e deve essere ripetuta per ogni parte, comportando costi di manodopera eccessivi.
Figure Engineering sviluppa soluzioni avanzate per la produzione e la manutenzione, principalmente come società appaltatrice per diverse divisioni del Dipartimento della difesa, ma anche per aziende private. Nel caso dei velivoli gestiti da aeronautica, marina ed esercito degli Stati Uniti, oltre che da compagnie aeree commerciali, Figure Engineering è stata chiamata a intervenire in aree spesso trascurate nel processo di manutenzione: sabbiatura, verniciatura, placcatura e rivestimento.
Queste operazioni vengono considerate spesso come sporche, ripetitive e pericolose, perché sono meno visibili e note rispetto a processi come la sostituzione dei motori o l'innovazione delle alette di estremità. Tuttavia, sono altrettanto importanti per le prestazioni complessive del velivolo. Se eseguiti con workflow inefficienti, questi processi possono prolungare i tempi di manutenzione, influire negativamente sulla rapidità di intervento, aumentare i costi operativi e, a causa dell'uso di sostanze chimiche tossiche, mettere a rischio la sicurezza del personale impegnato nelle operazioni di manutenzione, riparazione e revisione.
Figure Engineering è specializzata nella ricerca di soluzioni innovative per rendere questi processi più sicuri ed efficienti e da anni collabora con le officine di deposito dell'aeronautica militare statunitense. "Le soluzioni migliori nascono da una stretta collaborazione con la persona che controlla il processo, che conosce perfettamente i problemi che deve affrontare. Ad esempio, nel caso della galvanizzazione, è emerso che la manutenzione del velivolo non veniva completata abbastanza rapidamente e che si generavano molti scarti", ha affermato McDaniels.
Problemi legati al workflow di galvanizzazione dei velivoli
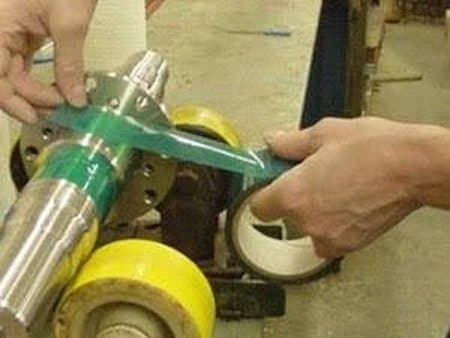
Applicazione manuale del nastro adesivo.
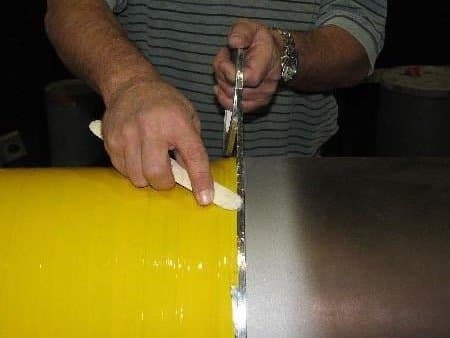
Taglio manuale del nastro adesivo.

Immersione delle parti mascherate nel bagno galvanico.
Uno dei più lunghi e difficili processi di manutenzione, riparazione e revisione degli aerei è la galvanizzazione di grandi componenti per i carrelli di atterraggio. Il workflow prevede bagni in sostanze chimiche aggressive ed estremamente abrasive, nonché ore di lavoro manuale per mascherare le aree non destinate al trattamento tramite l'applicazione manuale di una lacca rimovibile o di nastro adesivo.
"Il lavoro manuale necessario per far sì che il rivestimento venga applicato solo sulle aree desiderate è lungo, ripetitivo e costoso. I centri di riparazione cercavano un modo per ridurre il tempo impiegato nelle attività manuali, sviluppando maschere che potessero essere fissate con morsetti o bulloni," ha affermato McDaniels.
Tuttavia, quando Figure Engineering ha iniziato a progettare ed eseguire la prototipazione delle mascherature per la galvanizzazione, si è verificata tutta una serie di problemi complessi. "I nostri primi studi suggerivano che nulla avrebbe potuto resistere all'intensità del processo di galvanizzazione. Il materiale doveva essere estremamente tenace e resistente alle sostanze chimiche, ma anche resistente agli urti per sopportare frequenti cadute e martellate", ha aggiunto McDaniels.
Oltre al materiale, anche la scelta del giusto hardware per la stampa è stata una sfida. "All'inizio, abbiamo preso in considerazione tutte le opzioni. Avevamo bisogno di una stampante facile da utilizzare, affidabile, e di un marchio riconosciuto, in modo da ottenere un ampio supporto dai vari depositi", ha continuato McDaniels.
Dopo aver testato diverse parti realizzate con stampanti 3D a modellazione a deposizione fusa (FDM) e sinterizzazione laser selettiva (SLS), il team si è reso conto di avere bisogno di parti completamente dense e non porose. Le sostanze chimiche utilizzate nel processo di galvanizzazione erano in grado di penetrare nelle parti realizzate con la stampa 3D FDM e SLS e, quando venivano rimosse dal bagno, continuavano a rilasciare tali sostanze dalle superfici. La stampa in resina si è rivelata essere la soluzione ideale e, sebbene Figure Engineering abbia provato diverse stampanti 3D, una si è distinta rispetto alle altre.
"È apparso subito evidente che Formlabs era l'azienda con cui volevo lavorare. Grazie al costo conveniente per prodotti di qualità eccezionale, all'elevata affidabilità delle stampanti e alla sua notorietà sul mercato, era la migliore scelta possibile."
Jonathon McDaniels, cofondatore di Figure Engineering
McDaniels ha iniziato con la Form 3+, modificando le impostazioni di stampa ed eseguendo iterazioni con una formulazione personalizzata creata con la Open Material Mode. Con l'introduzione della Form 4, il processo di iterazione è stato potenziato, accelerando lo sviluppo di una resina personalizzata.
"Con l'introduzione della Form 4, molti dei problemi che avevamo sono stati risolti rapidamente. Questa stampante ha rivoluzionato la nostra capacità di stampare materiali estremamente difficili. Ci stiamo spingendo oltre i limiti del possibile nella produzione additiva con polimeri per far sì che questi materiali resistano al processo di placcatura", ha affermato McDaniels.
Sviluppo di materiali unici con l'ecosistema aperto di Formlabs
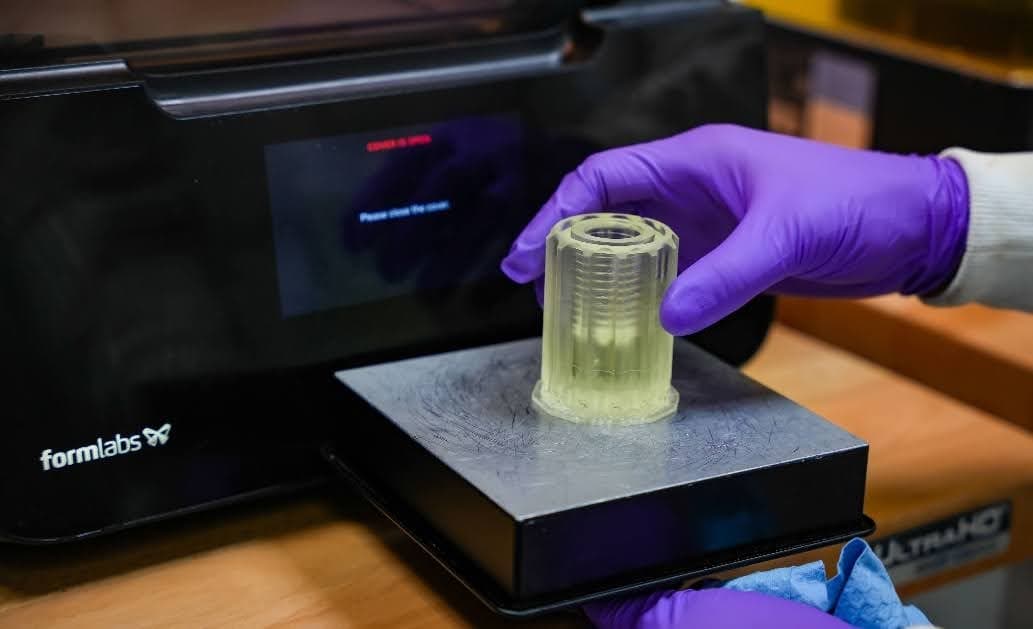
La Form 4 ha dato a Figure Engineering l'impulso di cui aveva bisogno: triplicare il numero di iterazioni quotidiane ha permesso di ottenere un feedback più rapido e provare un maggior numero di parametri di stampa in un lasso di tempo più breve, così da trovare le impostazioni perfette.
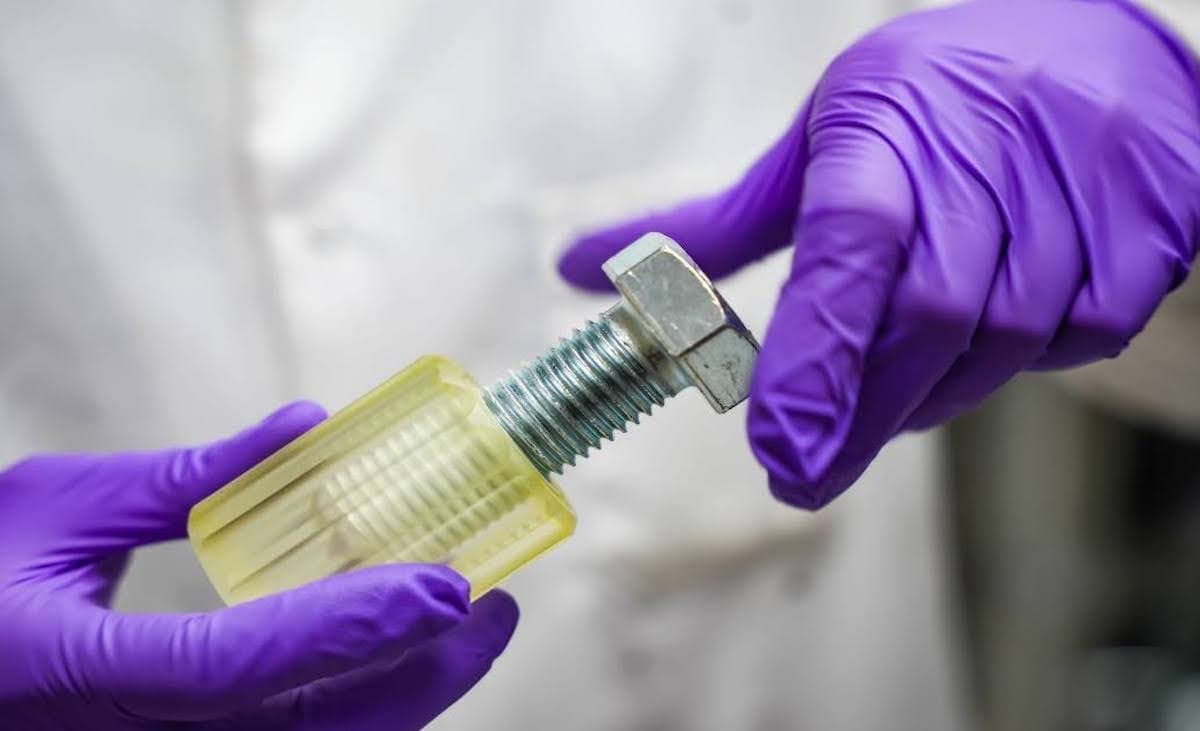
Il materiale personalizzato sviluppato da Figure Engineering consente di creare strumenti di mascheratura estremamente resistenti alle sostanze chimiche, resistenti e riutilizzabili, come questo strumento che su cui può essere avvitato direttamente un grosso bullone che richiede la galvanizzazione.
La velocità di stampa della Form 4 ha consentito al team di Figure Engineering di raddoppiare il numero di test rispetto al passato, ma è stato l'accesso alle impostazioni della stampante a rendere possibile lo sviluppo di un nuovo materiale, completamente funzionale e tecnicamente avanzato.
"Non avremmo raggiunto questo risultato senza la Open Material Mode e senza la possibilità di modificare le impostazioni di stampa", ha sostenuto McDaniels. Lo sviluppo di nuovi materiali e la regolazione delle impostazioni di stampa richiedono la comprensione dell'impatto di ciascuna impostazione sul risultato finale. La formazione di McDaniels in ingegneria chimica si è rivelata utile durante la collaborazione con il team di Formlabs per mettere a punto alcuni processi. "Modificare le impostazioni di stampa è stato piuttosto intuitivo. Abbiamo ricevuto indicazioni su aspetti come il funzionamento della stampante, il modo in cui la resina riempie e sostiene il primo strato e altri aspetti di questo tipo. Puoi inserire i valori adatti alle tue esigenze e stampare parti che rispettano i requisiti del progetto. Una volta acquisita familiarità, questo passaggio diventa semplice", ha spiegato McDaniels.
Riduzione della manodopera e dei costi
Lo sviluppo di una resina per la galvanizzazione di parti di mascheratura richiedeva proprietà specifiche, che non erano disponibili in nessun sistema esistente. Formlabs ha messo a disposizione di Figure Engineering una piattaforma completa per la ricerca, che comprendeva una stampante 3D veloce e affidabile, l'accesso alle impostazioni di stampa e al software e un team pronto a supportare e collaborare con McDaniels e il suo team.
La formulazione personalizzata sviluppata da Figure Engineering è già stata presentata a un deposito dell'aeronautica militare statunitense che si occupa di manutenzione, riparazione e revisione. Una volta progettate e stampate le parti, la loro implementazione nel processo di mascheratura riduce drasticamente il tempo necessario per preparare i componenti dei velivoli alla galvanizzazione. "Il nostro obiettivo è far sì che il personale dedichi meno tempo a questo processo e che si allontani il più possibile dai bagni con sostanze chimiche", ha spiegato McDaniels.
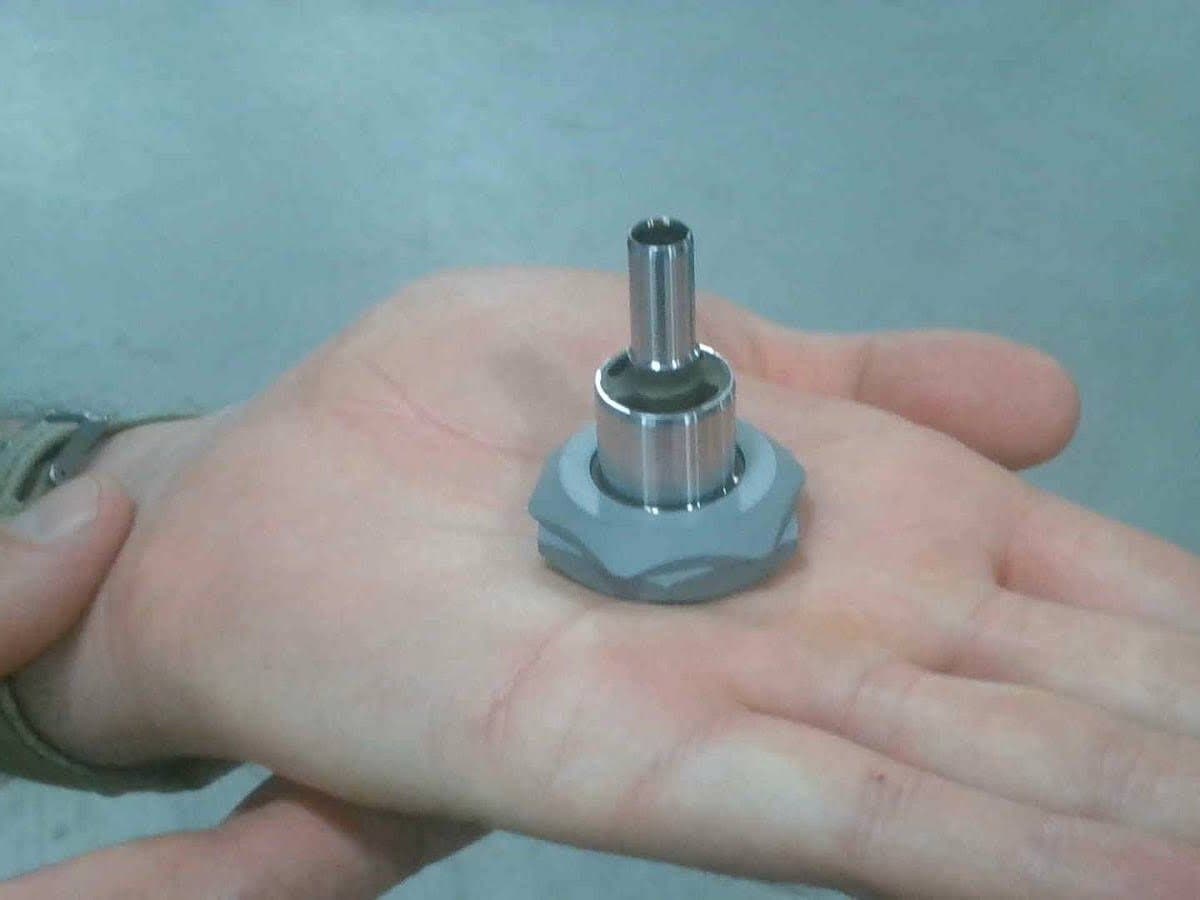
Una sola maschera creata a mano per questo bullone in metallo è costata circa 250 $, mentre stampandola con le filettature della vite in Resist™ è costata solo 5 $.
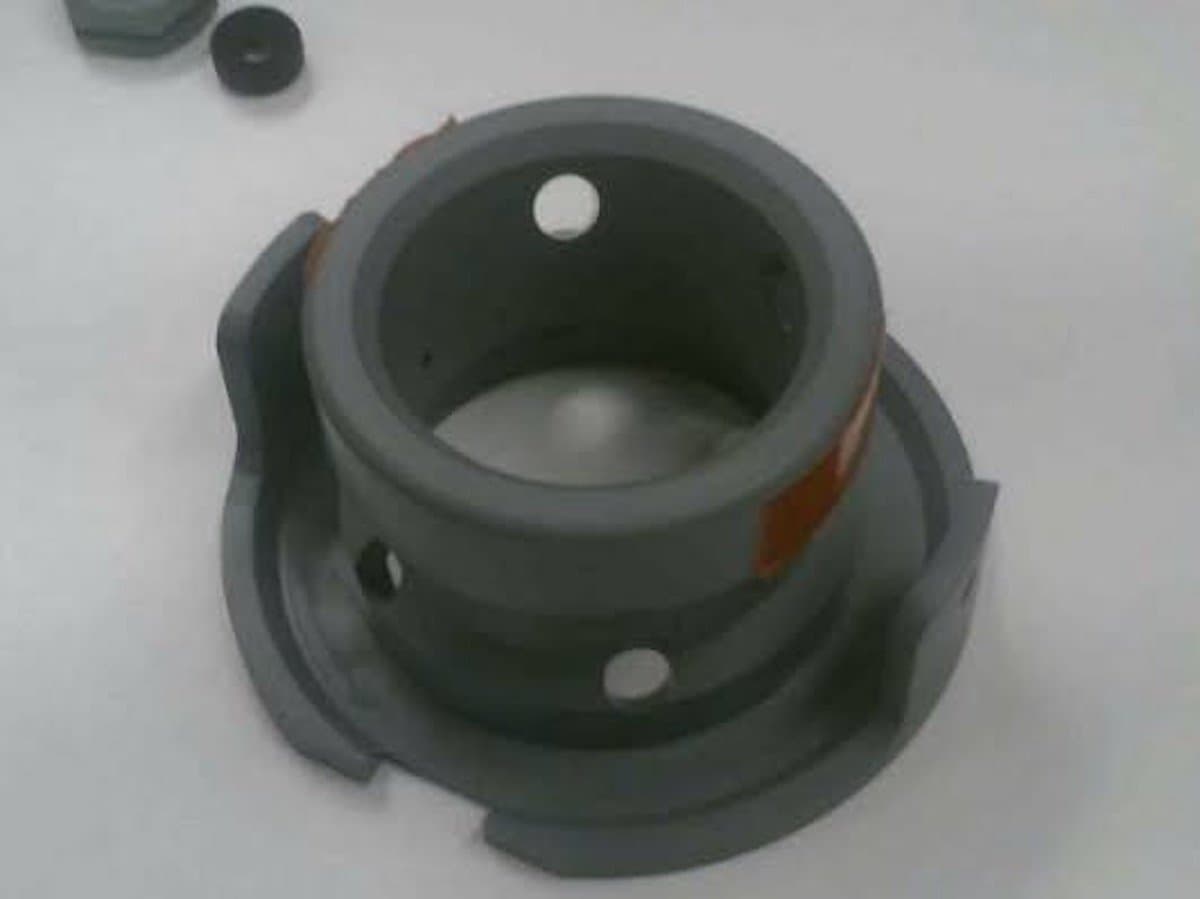
Questa parte di grandi dimensioni ha un costo di circa 550 $ tra materiali e manodopera durante l'applicazione, mentre il tradizionale processo di mascheratura manuale ha un costo compreso tra i 2000 e i 4000 $.
Ogni parte stampata in 3D può essere riutilizzata fino a 20 volte nel processo di galvanizzazione, a differenza degli smalti e dei nastri, che sono monouso e costano alle officine di placcatura milioni di dollari all'anno. Sebbene le fasi di progettazione, stampa e post-elaborazione della stampa 3D possano richiedere tempo, il design può essere condiviso tra diversi dipartimenti, depositi o persino reparti delle forze armate, permettendo a qualsiasi velivolo che necessiti di un componente da galvanizzare di usare lo stesso design e stamparlo su richiesta. Inoltre, le maschere stampate in 3D possono essere prodotte in lotti e conservate fino a quando non sono necessarie. La mascheratura rappresenta uno dei principali colli di bottiglia nel processo di galvanizzazione, richiedendo spesso tempi lunghi, ma l'adozione di maschere stampate in 3D risolve questo problema.
Possibilità infinite
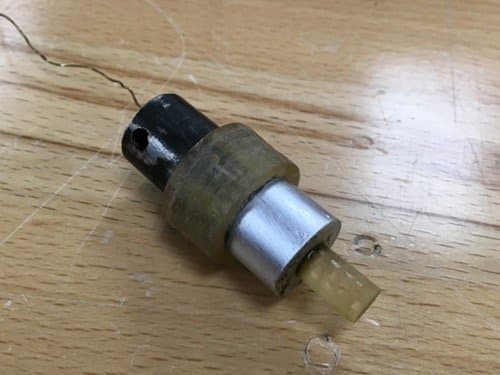
Fase 1: fattibilità
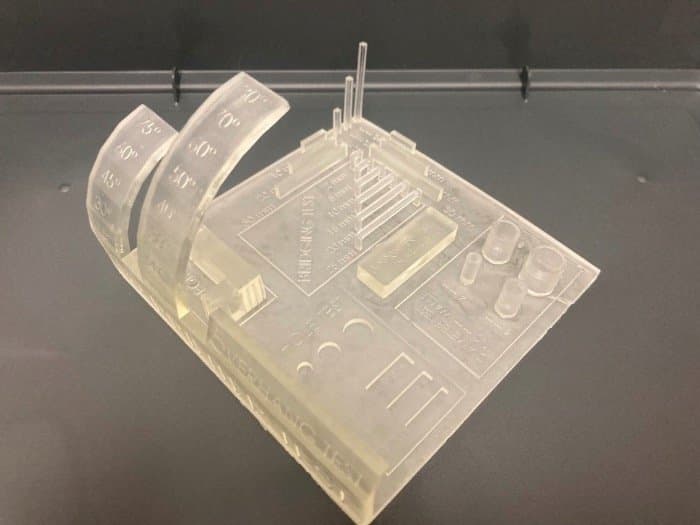
Fase 2: sviluppo
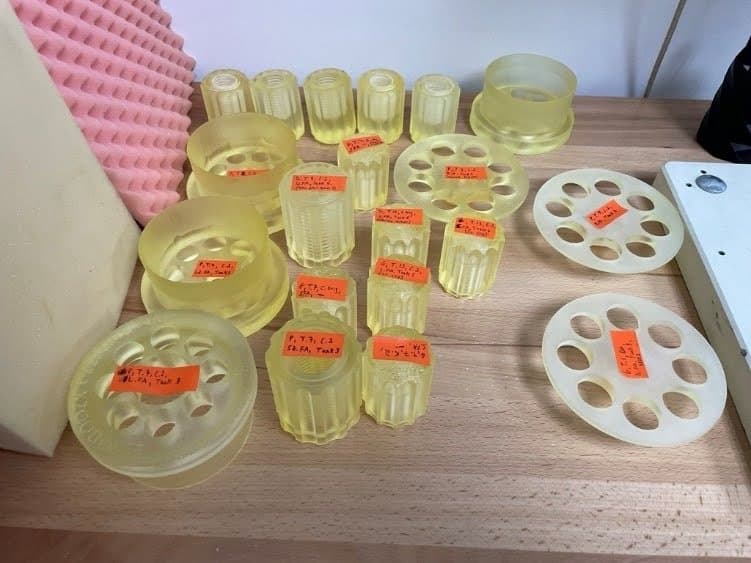
Fase 3: dimostrazione del primo articolo
La collaborazione tra Figure Engineering e Formlabs ha dimostrato che unendo le forze è possibile risolvere rapidamente problemi grandi e complessi. L'esperienza di Figure Engineering nel campo dell'ingegneria chimica e la profonda comprensione del problema sono state decisive, ma per trovare la soluzione ottimale non era sufficiente un semplice apparecchio: era necessario l'accesso e il supporto di una potente piattaforma di stampa 3D.
Grazie all'ecosistema aperto di Formlabs e alla Open Material Mode, McDaniels e il suo team sono riusciti a sviluppare un nuovo materiale e un workflow innovativo per il Dipartimento della difesa, con un potenziale risparmio di milioni di dollari in materiali e manodopera, oltre a migliorare la sicurezza del personale di manutenzione, riparazione e revisione nei depositi di tutto il Paese. "Non avremmo potuto eseguire il nostro lavoro senza la Open Material Mode", ha affermato McDaniels. "Ha cambiato il nostro approccio ai nuovi progetti futuri. Questo non sarà l'ultimo materiale per la stampa 3D che produrremo. Attualmente stiamo lavorando con altri dipartimenti della difesa, ma anche con linee aeree sia private che commerciali. La Open Material Mode ci ha aperto le porte a tutte queste opportunità."
Scopri di più sull'ecosistema aperto di Formlabs o richiedi un campione gratuito per toccare con mano la qualità offerta dalla Form 4.