Secondo il Bureau of Labor Statistics, metà delle aziende statunitensi fallisce entro i primi cinque anni. Alla luce di statistiche così sfavorevoli, come può una nuova azienda garantire la propria stabilità e longevità?
Per Brandon Talkmitt, fondatore e proprietario di BTI Gauges, la risposta a questa domanda è la stampa 3D con la stampante a sinterizzazione laser selettiva (SLS) Fuse 1. Talkmitt non ha solo conquistato una nicchia di mercato, ma è stato in grado di trasformare un'attività secondaria in un'azienda di successo che è riuscita a superare la pandemia di COVID-19, i problemi legati alle catene di fornitura globali e la crescita dei prezzi delle materie prime.
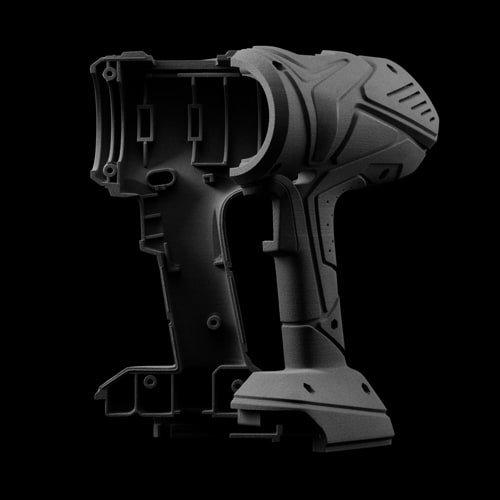
Introduzione alla stampa 3D tramite sinterizzazione laser selettiva (SLS)
Stai cercando una stampante 3D per creare parti robuste e funzionali? Scarica il nostro whitepaper per scoprire come funziona la stampa 3D SLS e perché è un processo molto diffuso per la prototipazione funzionale e la produzione per utilizzo finale.
Una lacuna nel mercato
Come molte altre aziende di successo, BTI Gauges è nata per colmare una lacuna del mercato. Talkmitt desiderava personalizzare il display telemetrico della sua auto ad alte prestazioni. Nelle auto più comuni, i display del cruscotto mostrano solo parametri standard, come la velocità e i giri al minuto. Tuttavia, nelle auto ad alte prestazioni, chi guida ha bisogno di molti più dati per poter viaggiare a velocità superiori a 240 km/h. A velocità e potenza così elevate, aspetti come la pressione del liquido refrigerante sono di vitale importanza per la sicurezza. Per ottenere tutte queste informazioni, i conducenti aggiungono una serie di indicatori che mostrano parametri come il rapporto aria/carburante, la spinta del turbocompressore, la pressione del liquido refrigerante e altro ancora.
"Data la potenza di queste auto, i guasti sono molto comuni e le riparazioni molto costose", ha affermato Talkmitt. Per evitare che si verifichino problemi, durante la guida occorre sempre tenere sotto controllo i display per far sì che il motore non si surriscaldi o vada in sovrappressione. Più sono i parametri da monitorare, più sono gli indicatori che ingombrano il cruscotto dell'auto.
Talkmitt ha cercato invano uno strumento che contenesse più parametri sulle prestazioni: avere troppi display sul parabrezza sarebbe stata una potenziale fonte di distrazione. Per questa ragione, così come è successo per molte altre aziende, ha semplicemente creato ciò che non riusciva a trovare sul mercato. "Cercavo qualcosa che ancora non esisteva, per cui ho progettato un unico strumento rotondo dotato di touchscreen che mostrava tutte le informazioni di cui avevo bisogno", ci ha raccontato Talkmitt. Il primo passaggio è stato la prototipazione degli involucri esterni dello strumento con una stampante 3D a modellazione a deposizione fusa (FDM). Successivamente, ha testato personalmente gli involucri, sottoponendoli a temperature elevate all'interno di auto e forni e modificando il design per adattarlo a diversi modelli di automobili.
Splendido aspetto, prestazioni eccezionali
Da subito il prodotto ha suscitato l'interesse di clienti che guidavano auto da corsa giapponesi anni '90, Lamborghini, Dodge Viper e altri veicoli ad alte prestazioni. Per le persone che tengono molto allo stile, riempire il cruscotto di strumenti antiestetici può essere fonte di fastidio. Un unico schermo touchscreen dall'aspetto sarebbe stato efficiente ed esteticamente gradevole.
A questo punto, Talkmitt ha dovuto affrontare un altro problema. La finitura superficiale delle parti realizzate con la stampa FDM non eguagliava l'eleganza ricercata del quadro strumenti. "Le linee degli strati non piacevano a tutti", ha dichiarato Talkmitt. "Abbiamo dovuto levigarle e poi riempirle con stucco per automobili. È stato un processo molto difficile".
Talkmitt ha iniziato a valutare altre soluzioni di stampa 3D, tra cui costose stampanti 3D a fusione su letto di polvere di plastica, stampanti 3D a resina e una soluzione SLS compatta ed economica. Alcune arrivavano a costare mezzo milione di dollari, altre utilizzavano materiali difficili da reperire, per cui sembrava non ci fossero alternative disponibili. Questo fin quando non ha sentito parlare della Fuse 1. "Quando ho ricevuto il campione ho pensato che avrei tanto voluto che le mie parti avessero quell'aspetto. Ho effettuato dei test e capito che tipo di calore era in grado di tollerare. Infine, ho eseguito un processo di finitura e verniciatura ed è andato tutto bene", ha affermato Talkmitt.
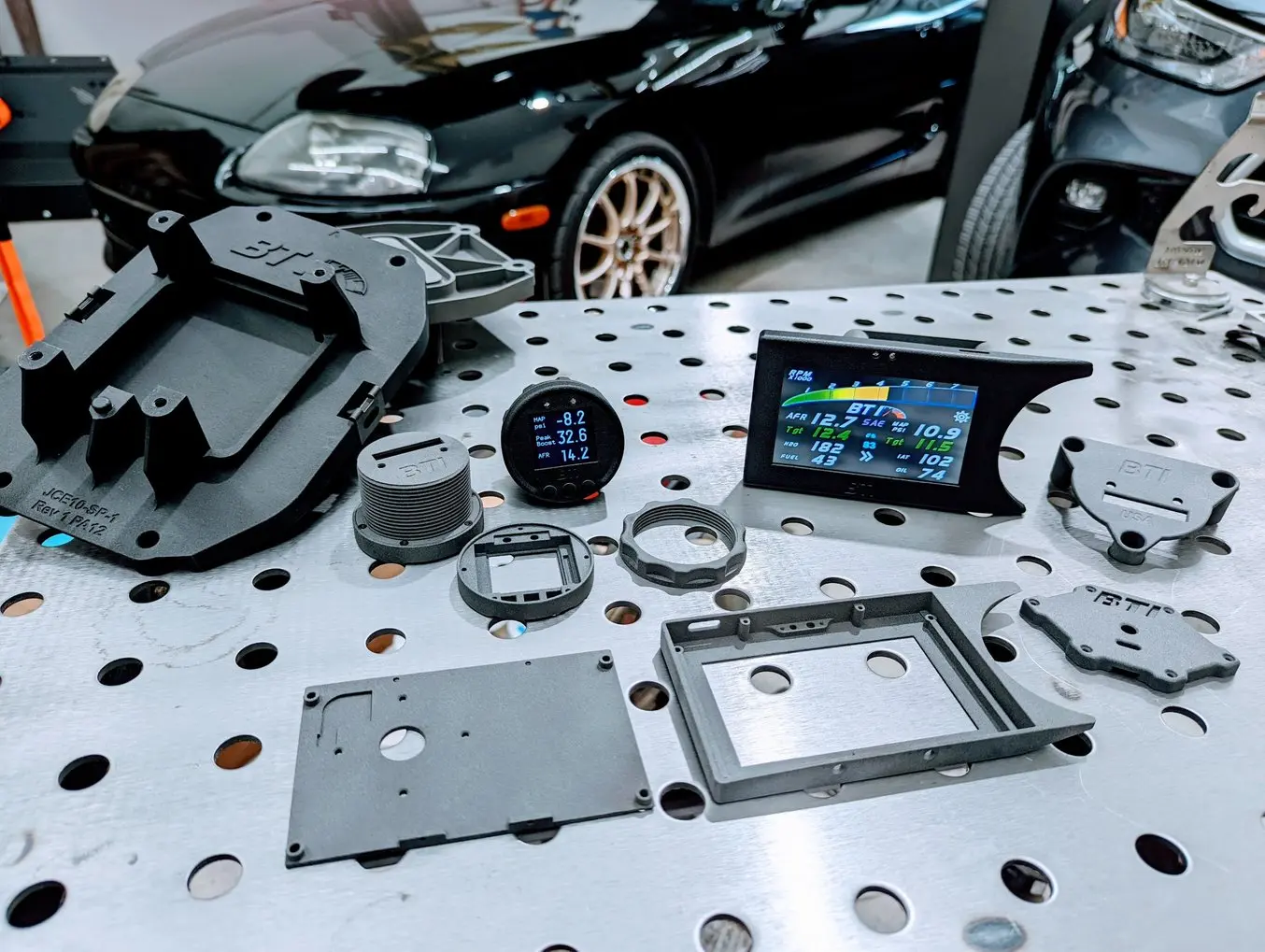
Precisione millimetrica
Per aumentare la produzione con la Fuse 1, Talkmitt non puntava solo sull'estetica: voleva che le parti fossero sempre precise anche a volumi elevati. Finalmente aveva una stampante in grado di ottenere tolleranze strette e ripetibili. Talkmitt ha potuto ottimizzare la precisione dei file, sapendo che la Fuse 1 sarebbe stata in grado di stampare fedelmente i dettagli che aveva progettato.
"Ho progettato un foro di 40 mm x 40 mm e ora con la Fuse 1 posso stampare un perno delle stesse dimensioni che si incastra perfettamente. Realizziamo filettature e altri dettagli che devono essere precisi. In un ambiente come quello di un'auto, è facile che le parti si deformino. Ma da quando utilizziamo la Fuse 1, non è mai più successo."
Brandon Talkmitt
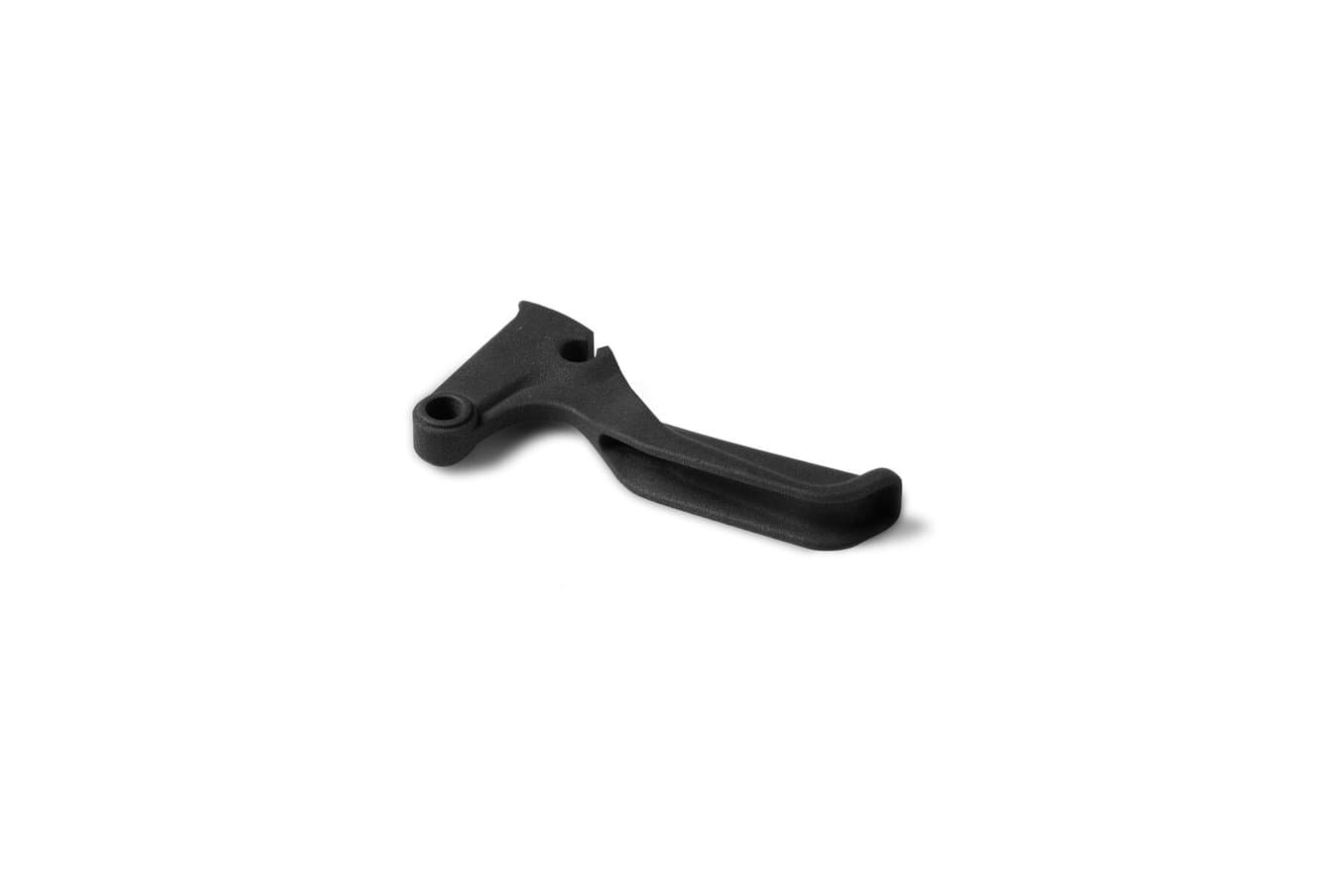
Richiedi un campione gratuito
Guarda e tocca con mano la qualità di Formlabs. Saremo lieti di inviare presso la tua azienda una parte SLS stampata con la Fuse 1+ 30W come campione gratuito.
Produzione antifragile
Parti come queste possono essere fabbricate in diversi modi, perciò qual è il vantaggio di avere una stampante SLS in-house? BTI Gauges ha raggiunto la cosiddetta "antifragilità", principio teorizzato dal saggista Nassim Nicholas Taleb. Le entità antifragili non solo riescono a resistere a stress e shock, ma anche a fortificarsi, migliorarsi e diventare più efficienti grazie a questi eventi. A causa dei problemi legati alla catena di fornitura degli ultimi due anni, in diverse occasioni BTI Gauges ha dovuto affrontare la carenza di display touchscreen e di altri componenti necessari per le nove linee di produzione dell'azienda. Queste problematiche, se affrontate da un produttore "fragile", avrebbero interrotto produzione, distribuzione e generazione di profitto. Al contrario, Talkmitt è riuscito a procurarsi nuovi tipi di display, scelta che ha inciso sul tipo di processore, sul circuito stampato e sulla forma stessa dello strumento.
Grazie alla stampa 3D in-house con la Fuse 1, Talkmitt ha potuto cambiare immediatamente il design, senza dover spendere migliaia di dollari per acquistare nuove attrezzature o accumulare prodotti che sarebbero presto diventati obsoleti. "Mi sarei ritrovato con moltissima plastica, ma grazie alla Fuse 1 sono riuscito a cambiare il design rapidamente. Mi sono bastati 30 minuti. Senza questa stampante, sarei sicuramente fermo in questo momento", ha raccontato Talkmitt.
Talkmitt non si è affidato a fornitori esterni e ha mantenuto il più possibile un'integrazione verticale. Per proteggersi da eventuali problemi futuri con la catena di fornitura, ha sviluppato un inventario digitale di parti di ricambio. L'aver affrontato pressioni economiche fuori dal suo controllo ha rafforzato il suo modello aziendale e lo ha preservato da shock futuri: ecco cosa vuol dire "antifragile".
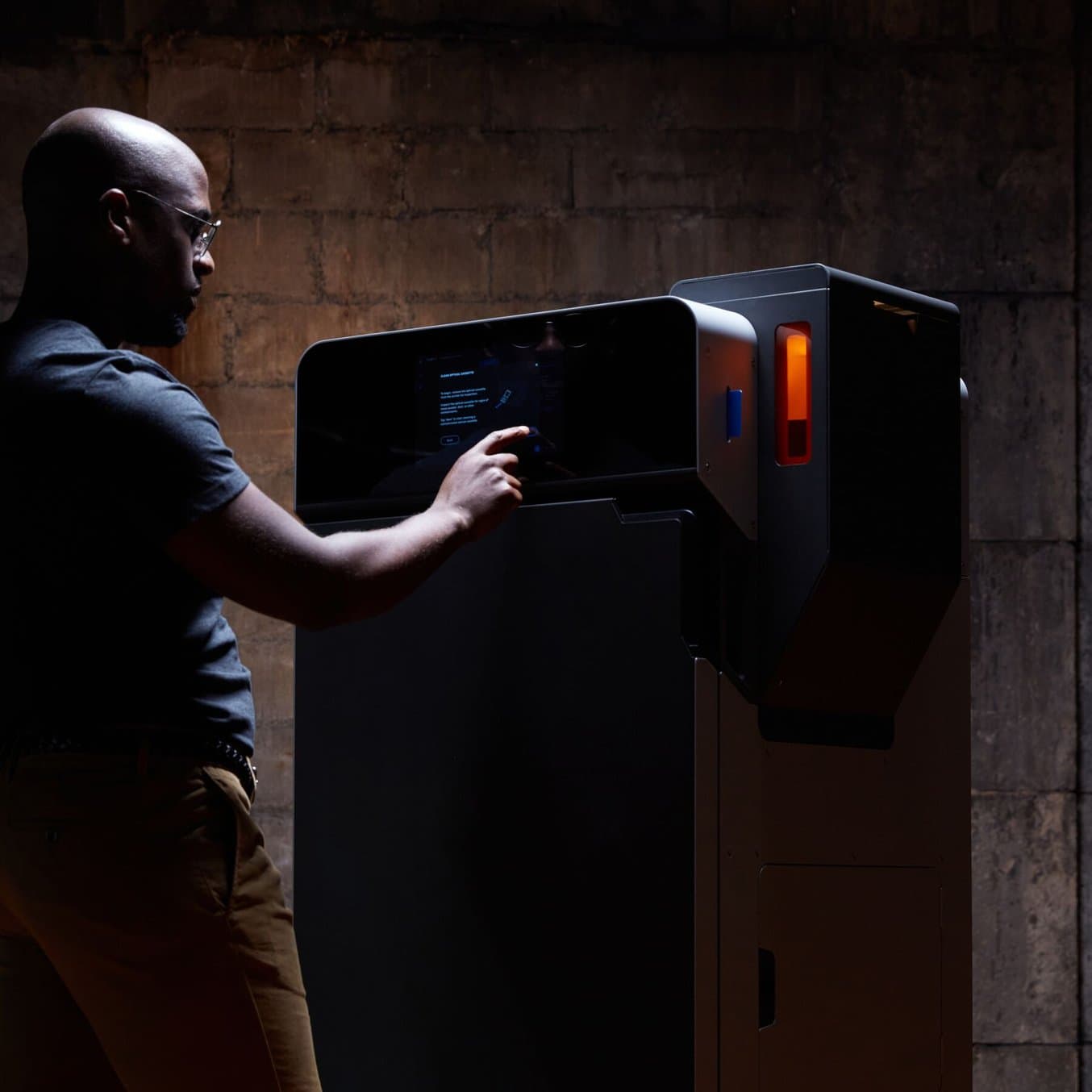
Esternalizzazione o produzione interna: quando conviene portare la stampa 3D SLS in-house?
In questo whitepaper valuteremo la proposta di valore dell'adozione di stampanti 3D SLS in-house e la confronteremo con l'esternalizzazione delle parti SLS a un fornitore di servizi.
Alta produttività
Per mantenere la produzione sempre economica e sostenibile, Talkmitt fa affidamento sull'efficienza di tutto il sistema della serie Fuse. Grazie all'algoritmo avanzato di posizionamento di PreForm, riesce a inserire le parti una nell'altra per aumentare la densità di stampa complessiva e farla coincidere il più possibile con il tasso di rigenerazione del 30% della Nylon 12 Powder. "Uno dei nostri prodotti è uno strumento di 4,3 mm che ha bisogno di due pezzi, uno anteriore e uno posteriore. Tra di essi c'è uno spazio molto ampio, per cui prendo un altro pezzo da 3,5 mm e lo inserisco all'interno. Riusciamo a riempire strategicamente il volume di stampa, raggiungendo regolarmente una densità di stampa del 25%", ha affermato Talkmitt.
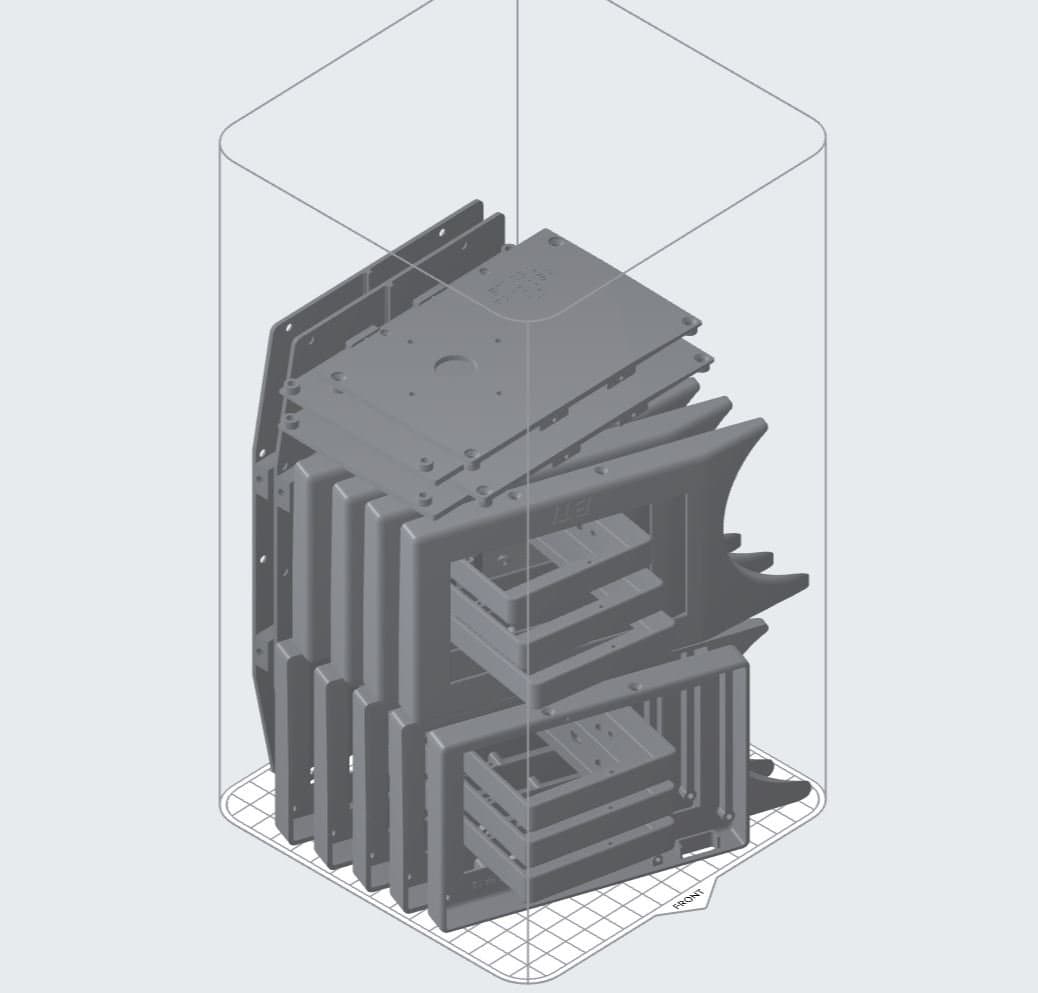
Immagine di PreForm della camera di stampa della Fuse 1 che mostra il posizionamento delle parti: quelle più piccole sono inserite in quelle più grandi (sinistra); parte stampata con la Fuse 1 nella fase di post-elaborazione (destra).
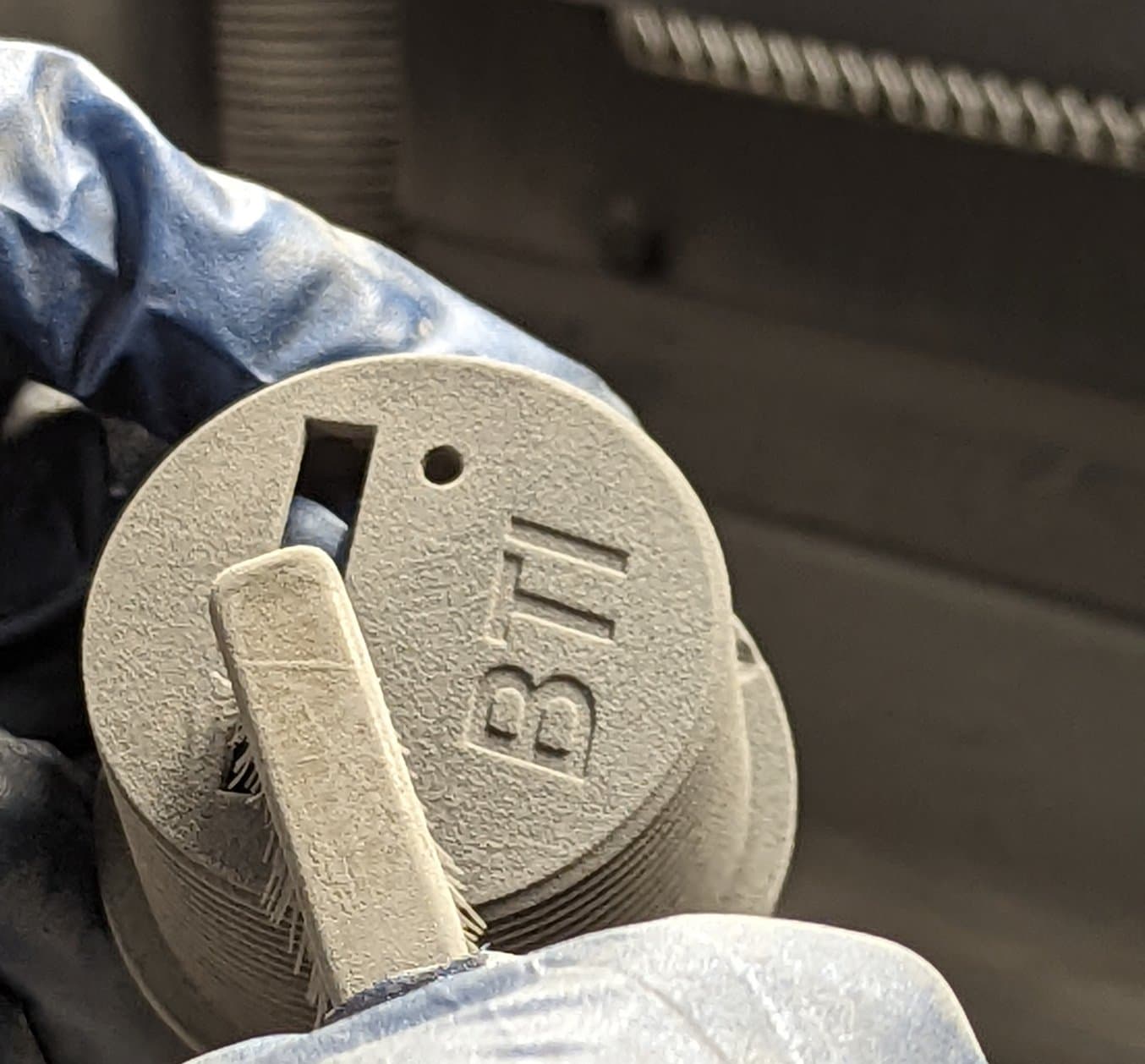
Grazie a una densità di stampa così alta, Talkmitt riesce a ottenere un workflow di stampa senza sprechi, nel quale ogni singolo granello di polvere viene utilizzato nei cicli successivi. Per un piccolo produttore, questa efficienza si traduce in un minor costo per parte e in tempistiche più rapide per il raggiungimento di un ritorno d'investimento positivo.
L'elevato rendimento della Fuse 1 ha permesso a Talkmitt di passare dalle tre stampanti FDM che lavoravano ininterrottamente alle camere di stampa della Fuse 1 riempite completamente una volta a settimana. Il workflow semplificato della Fuse Sift consente a Talkmitt di dedicare meno tempo alla post-elaborazione e più tempo alla progettazione di nuove parti e alla crescita della notorietà del brand. "Lungo la parte posteriore del laboratorio abbiamo la Fuse 1, la Fuse Sift e la sabbiatrice, mentre le fasi di verniciatura, assemblaggio e imballaggio si svolgono nello stabilimento di produzione. La dimensione e l'ingombro ridotto della Fuse 1 sono perfetti per il processo", ha detto Talkmitt.
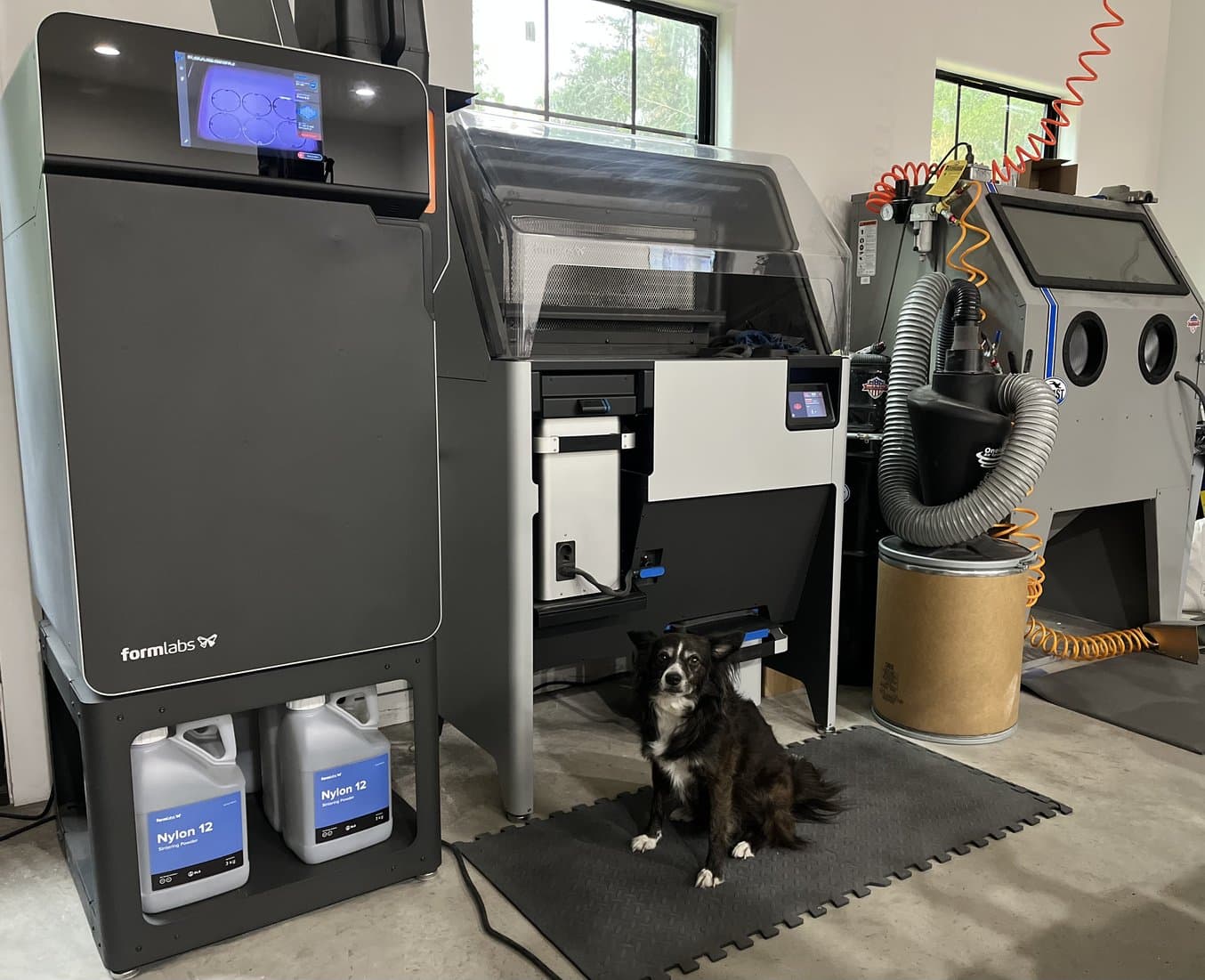
La Fuse 1 e la Fuse Sift hanno un ingombro ridotto e un workflow ottimizzato che si adatta facilmente alle aree di lavoro esistenti.
Il futuro dell'azienda
Per una nuova impresa, è difficile entrare in un settore in cui le auto vengono vendute regolarmente a centinaia di migliaia di dollari. Farlo nel bel mezzo di una crisi globale, di un blocco internazionale della catena di fornitura e di turbolenze economiche è quasi impossibile.
Implementando la produzione in-house con una stampante di alta qualità come la Fuse 1, Talkmitt è riuscito a controllare e garantire la propria capacità produttiva, superando le aziende che ancora dipendono dai metodi di produzione tradizionali o da fornitori esterni. "La consiglio a tutti. La Fuse 1 ha rivoluzionato la nostra azienda", ha concluso Talkmitt.