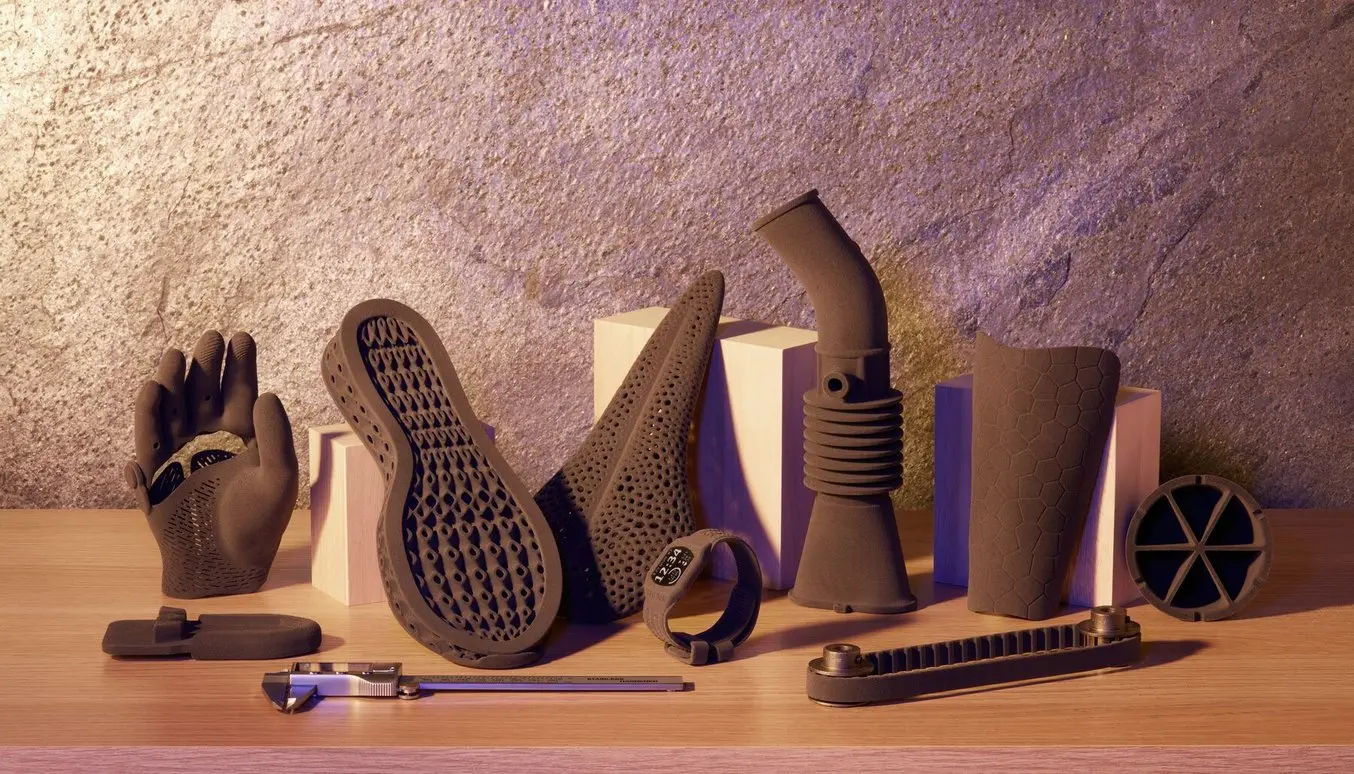
Formlabs è orgogliosa di presentare la TPU 90A Powder, il primo materiale morbido per le stampanti SLS della serie Fuse. Il poliuretano termoplastico (TPU) apre nuove possibilità di applicazione, poiché combina l'elevato allungamento a rottura e la straordinaria resistenza alla lacerazione dei materiali in gomma con la libertà di design della stampa 3D SLS.
La TPU 90A Powder è un elastomero flessibile, ideale per la stampa 3D di parti come:
- Dispositivi indossabili sicuri per il contatto con la pelle
- Suole, tutori, plantari e protesi
- Dispositivi di protezione per lo sport
- Sigillanti, guarnizioni, mascherine, cinghie, tappi e tubi
- Imbottiture, smorzatori, ammortizzatori e impugnature
Aggiungendo la TPU 90A Powder al proprio catalogo di materiali SLS, è possibile combinare l'efficienza, la convenienza e la facilità di utilizzo delle stampanti della serie Fuse con la capacità inedita di fabbricare in-house parti SLS morbide. Con il tasso di rigenerazione del 20%, il più basso di tutte le nostre polveri SLS finora, si riduce il costo per parte ed è possibile creare in-house e senza attrezzature costose prototipi in gomma, prodotti per utilizzo finale e supporti di produzione.
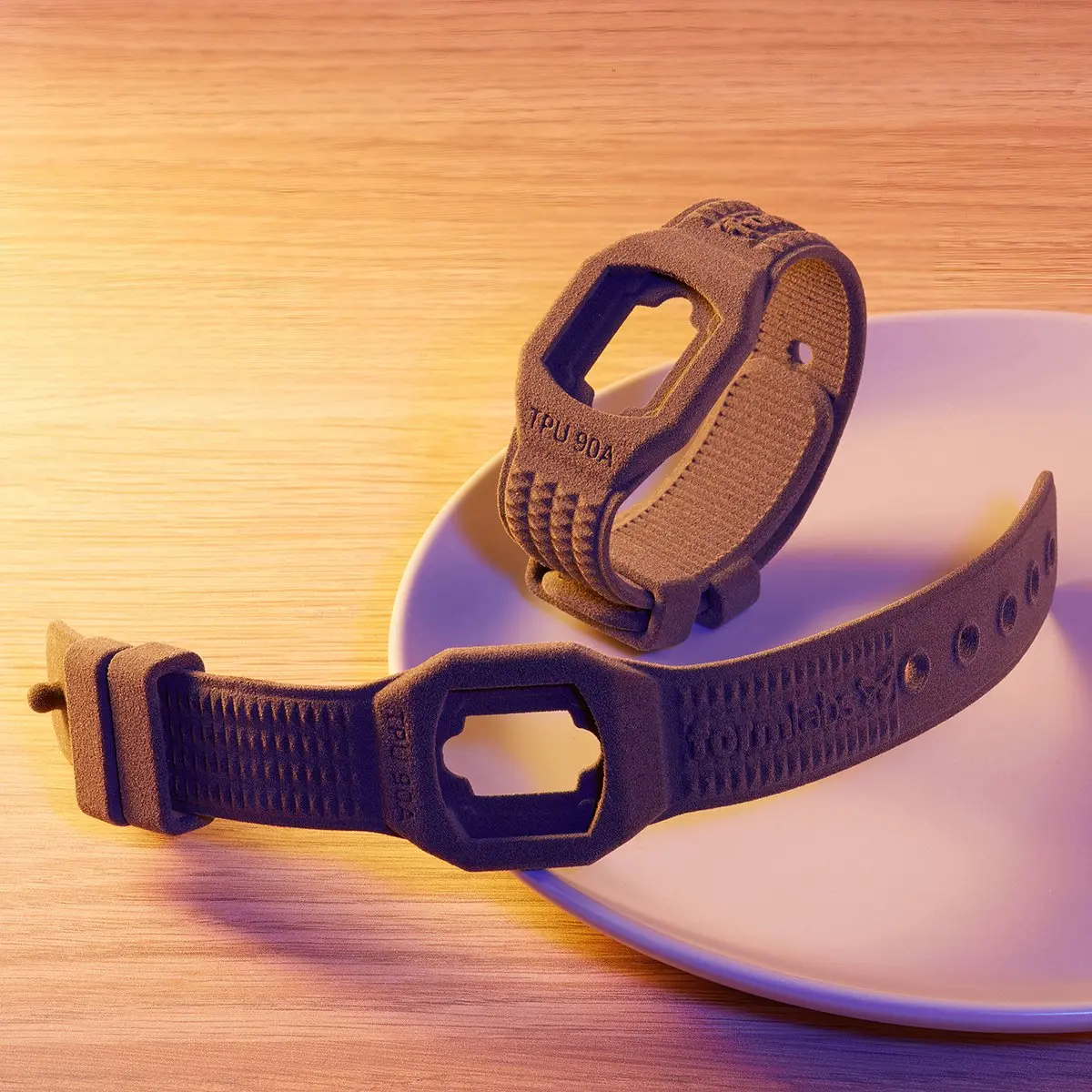
TPU 90A Powder: la polvere SLS flessibile di Formlabs
Guarda il nostro webinar per scoprire come la TPU 90A Powder può aiutarti a produrre in-house parti morbide in gomma con le stampanti 3D della serie Fuse.
Perché scegliere il TPU per la serie Fuse?
Attualmente esistono molti modi per realizzare parti in elastomero, tra cui i tradizionali flussi di lavoro di stampaggio e le stampanti 3D a fusione su letto di polvere. Questi flussi di lavoro sono penalizzati dalle limitazioni geometriche dello stampaggio o dai costi e la complessità d'uso della maggior parte delle soluzioni di stampa 3D industriali di grandi dimensioni. La TPU 90A Powder per la serie Fuse di Formlabs è la soluzione ideale per creare in-house parti geometricamente avanzate e flessibili.
Le stampanti Fuse di Formlabs sono i primi sistemi di stampa 3D a fusione su letto di polvere in grado di offrire una tecnologia SLS di livello industriale a un prezzo economico e con un ingombro ridotto. Ora che il flusso di lavoro è stato collaudato da migliaia di clienti Fuse, l'espansione del catalogo di polveri è la priorità assoluta di Formlabs. Poter contare su una soluzione SLS accessibile è un vantaggio per aziende di qualsiasi dimensione: le piccole imprese possono prendere slancio e ottenere il controllo sui propri mezzi di produzione, mentre le grandi imprese possono diversificare e decentralizzare i metodi di produzione, stabilizzando le catene di fornitura. L'introduzione di materiali nuovi per la serie Fuse ma noti nel settore è il modo più efficace per favorire l'innovazione e stimolare nuovi flussi di lavoro in tutte le discipline.
Proprietà | Nylon 11 CF Powder | Nylon 12 GF Powder | Nylon 12 Powder | Nylon 11 Powder | TPU 90A Powder |
---|---|---|---|---|---|
Rigidità | ★★★★ | ★★★★ | ★★★ | ★★ | ★ |
Duttilità | ★★★ | ★ | ★★ | ★★★★ | ★★★★★ |
Stabilità termica | ★★★★ | ★★★★ | ★★★ | ★ | ★ |
Tasso di rigenerazione | 30% (N2) | 30-50% (aria) | 30% (aria) | 30% (N2) 50% (aria) | 20% (aria) |
La TPU 90A Powder offre la rigidità più bassa e la duttilità più elevata della nostra famiglia di polveri SLS.
Cosa è in grado di fare la TPU 90A Powder?
Il TPU, o poliuretano termoplastico, è una delle termoplastiche elastomeriche più usate in ambito ingegneristico, produttivo e di progettazione. Questo materiale resistente in gomma si trova ovunque: dagli articoli sportivi ai dispositivi medici, fino alle suole delle scarpe.
Esistono flussi di lavoro collaudati per la produzione tradizionale di parti in TPU, che sono tuttora ideali per la produzione di massa di prodotti in gomma. I vantaggi di stampare con la TPU 90A Powder sulla serie Fuse risiedono nella facilità di utilizzo del sistema per la prototipazione rapida, nei supporti di produzione su richiesta e nelle possibilità di personalizzazione.
Prototipazione rapida
La serie Fuse consente alle aziende che in passato ricorrevano all'esternalizzazione di portare la capacità di prototipazione in-house, riducendo i tempi di realizzazione e abbattendo i costi.
La creazione di un prototipo di casco sportivo, ad esempio, richiede la capacità di fabbricare una calotta rigida e un'imbottitura morbida interna. Alcune aziende innovative sono al lavoro per progettare nuove strutture reticolari e tecnologie antiurto per l'imbottitura, e il TPU è un materiale perfetto.
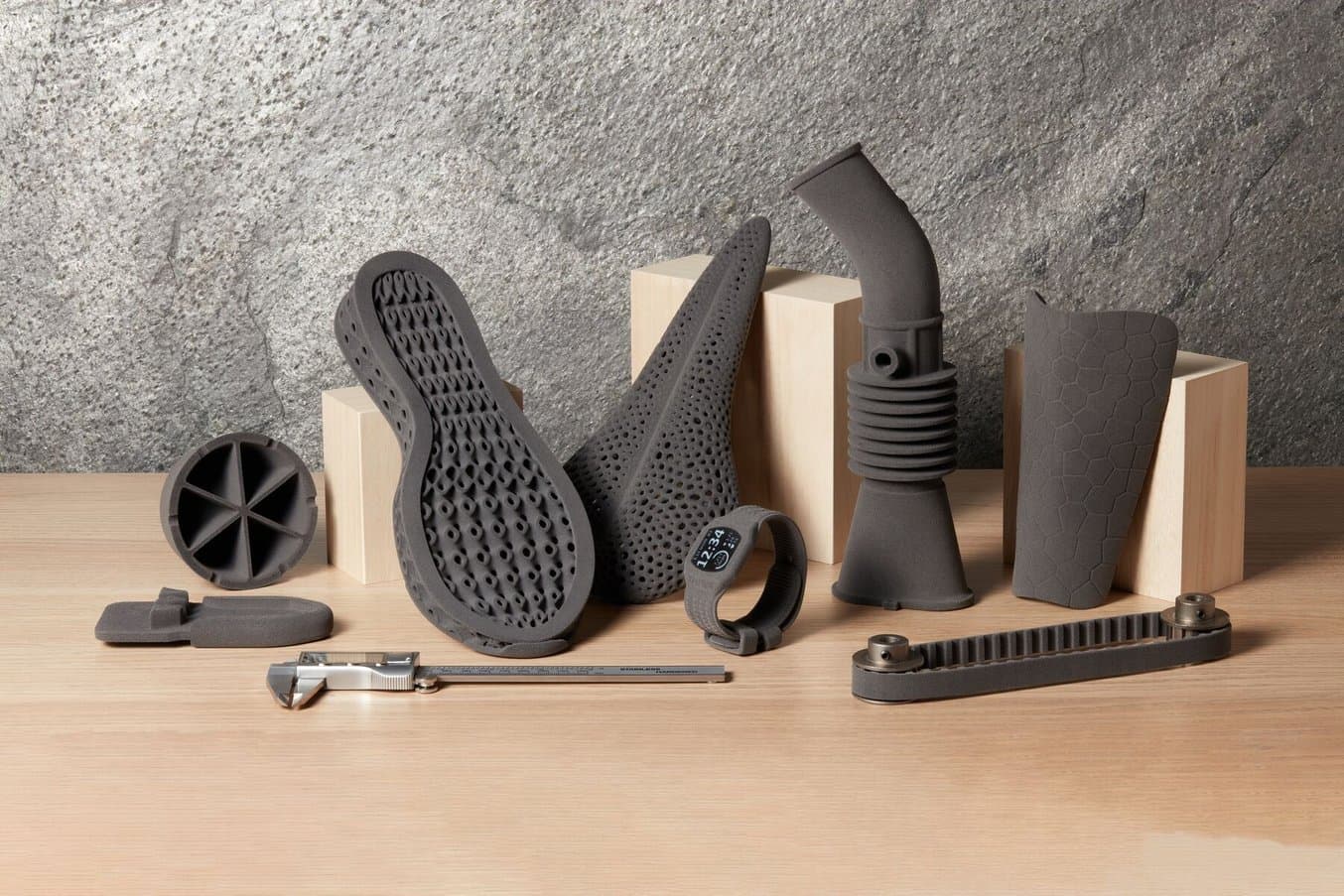
La TPU 90A Powder è il materiale ideale per la realizzazione di prototipi funzionali per parti che richiedono flessibilità, come dispositivi indossabili sicuri per il contatto con la pelle, attrezzature sportive ad alte prestazioni o solette per scarpe.
Tuttavia, la sperimentazione di nuovi design e geometrie rende i metodi tradizionali di creazione di attrezzature eccessivamente costosi, mentre l'esternalizzazione può richiedere settimane. Poter utilizzare un unico flusso di lavoro e un unico tipo di tecnologia sia per la calotta rigida esterna che per l'imbottitura interna permette di eseguire iterazioni a un ritmo molto più elevato. I caschi dovranno essere sottoposti a test fisici approfonditi, per cui saranno necessarie dieci imbottiture per un singolo collaudo. Si tratta di volumi troppo elevati per realizzare a mano in modo meticoloso una superficie ammortizzante, ma troppo bassi perché lo stampaggio tradizionale del TPU sia conveniente. La soluzione è la stampa 3D in-house. Le stampanti 3D della serie Fuse possono facilmente stampare più strutture reticolari in gomma con la TPU 90A Powder, con leggere variazioni per testare diverse versioni. Modificando il design della parte, ad esempio cambiando lo spessore delle pareti, è possibile produrre parti con diversi livelli di durezza per applicazioni diverse o come iterazioni dopo i test.
Il flusso di lavoro della serie Fuse consente di accedere a più materiali che includono una vasta gamma di proprietà meccaniche, di mantenere la produzione in-house e di poter progettare molti componenti diversi con un'unica tecnologia. La TPU 90A Powder introduce un nuovo tipo di componente per la stampa 3D, con la stessa piattaforma affidabile.
Radio Flyer crea prototipi in TPU per bici elettriche e giocattolo
Punto di riferimento per le famiglie americane da oltre un secolo, Radio Flyer è il produttore dello storico Little Red Wagon®, un carrettino giocattolo diventato talmente riconoscibile da meritare l'ingresso nella National Toy Hall of Fame. L'azienda è il più grande fabbricante al mondo di veicoli giocattolo come carrettini, monopattini, tricicli, go-kart, nonché biciclette elettriche e molti altri prodotti innovativi che le hanno permesso di guadagnarsi un posto nella cultura popolare, ma soprattutto nei sogni di ogni bambino e bambina.
La stampa 3D è un elemento molto importante del processo di sviluppo di Radio Flyer e Agostino Lobello, tecnico di progettazione dell'azienda, ha scoperto che la TPU 90A Powder permette di creare prototipi perfettamente funzionanti. "La finitura superficiale a elevata aderenza è di gran lunga superiore a quella che si può ottenere con i TPE/TPU per la stampa in 3D coi quali ho lavorato in passato. È molto simile a quella del TPE/TPU stampato a iniezione, il che è fantastico per le applicazioni di prototipazione. Questo processo è efficace sia dal punto dei vista dei costi che dei tempi perché, al momento, l'unica alternativa sarebbe quella di usare un prototipo e iniettarvi all'interno vero e proprio TPE o un altro uretano", ha dichiarato Lobello.
I prodotti di Radio Flyer vengono sottoposti a test approfonditi per garantire che siano sicuri, pratici e piacevoli da usare per chiunque. Poter testare i prototipi in condizioni reali è fondamentale, pertanto il team di progettazione ha bisogno di eseguire iterazioni rapide di parti resistenti e robuste. "Le parti sono piuttosto resistenti. Non ci sarebbero problemi a installarle su prototipi realistici destinati a test di ergonomia e usabilità. Non vediamo l'ora di usare questo materiale per raggi, manopole, paraurti e imbottiture di sellini, ma anche per creare prototipi di molle in TPE con una specifica flessibilità", ha commentato Lobello.
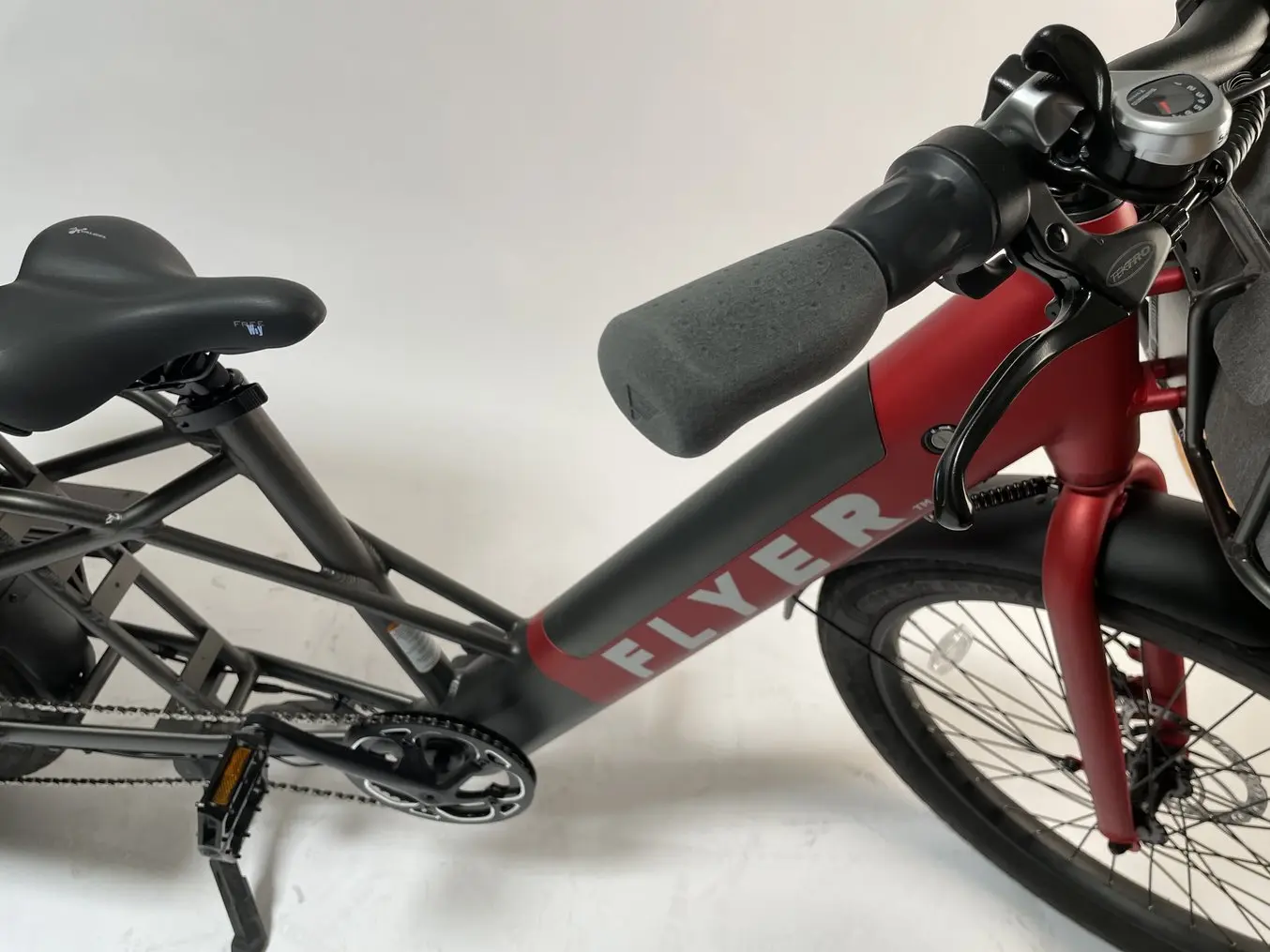
Usare la TPU 90A Powder sulle stampanti della serie Fuse permette a Radio Flyer di creare prototipi funzionali di parti, come il manubrio a impugnatura morbida della bici elettrica da trasporto Flyer™ L885.
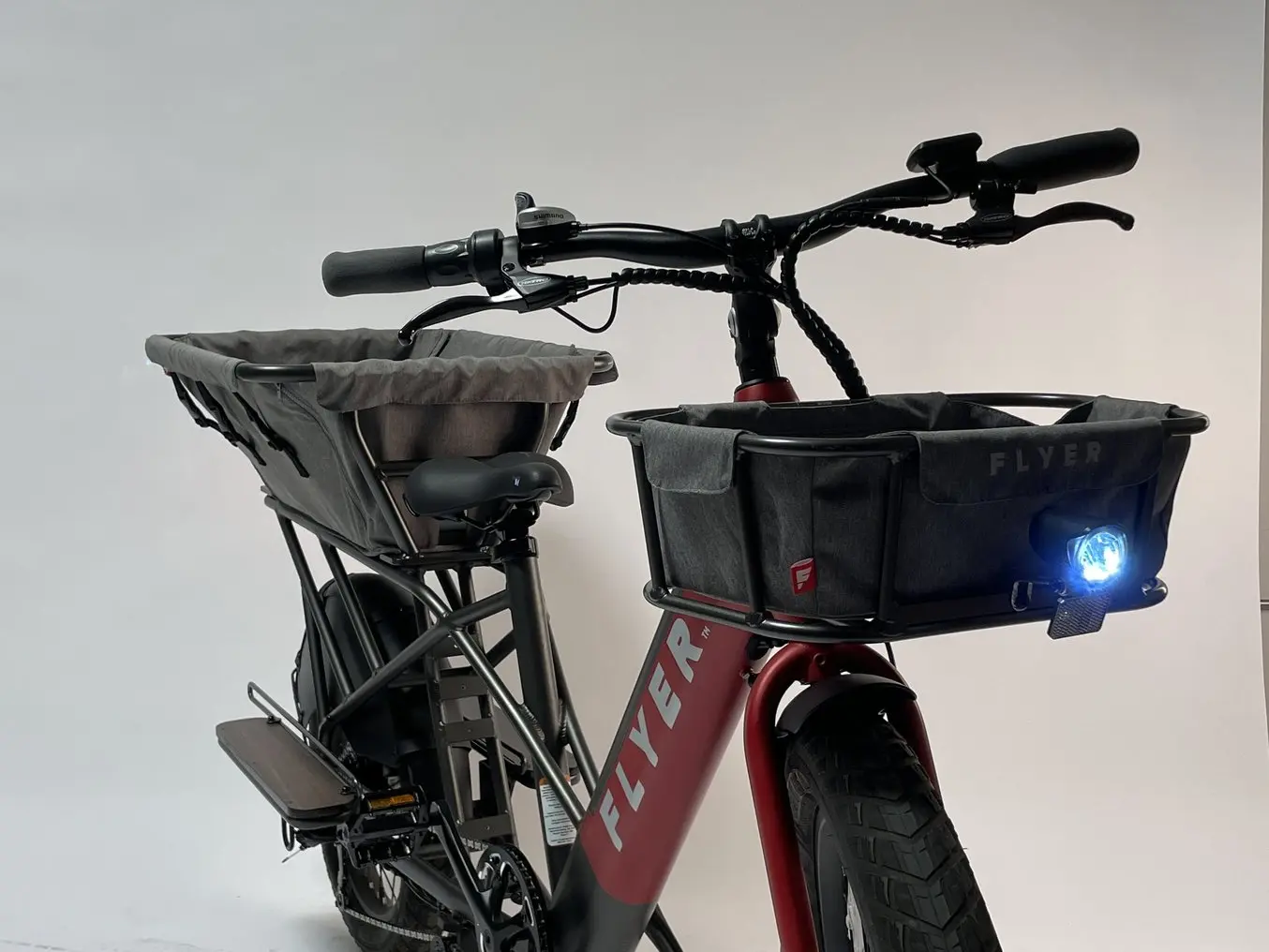
Supporti di produzione
Per chi non lavora nel settore della fabbricazione può essere difficile distinguere tra i vari tipi di supporti di produzione. Ad ogni modo, il concetto di fondo rimane lo stesso, a prescindere dal fatto che si tratti di una dima, una staffa, un involucro o uno dei tanti altri modi in cui gli apparecchi vengono tenuti insieme: quando sono necessari, lo sono davvero. La TPU 90A Powder è la risposta a un problema che molti produttori si trovano ad affrontare, ovvero come evitare che una tecnologia di produzione da milioni di dollari si usuri troppo.
I supporti di produzione morbidi possono aiutare a prolungare la durata di apparecchiature pesanti, attutendo gli urti o fornendo un'impugnatura dalla forma perfetta. Quando un sigillo o una guarnizione si rompe dopo anni di utilizzo continuo, è possibile stampare istantaneamente la parte di ricambio e rimettere in funzione la linea di produzione in poche ore, invece di aspettare giorni o settimane per riceverne una nuova.
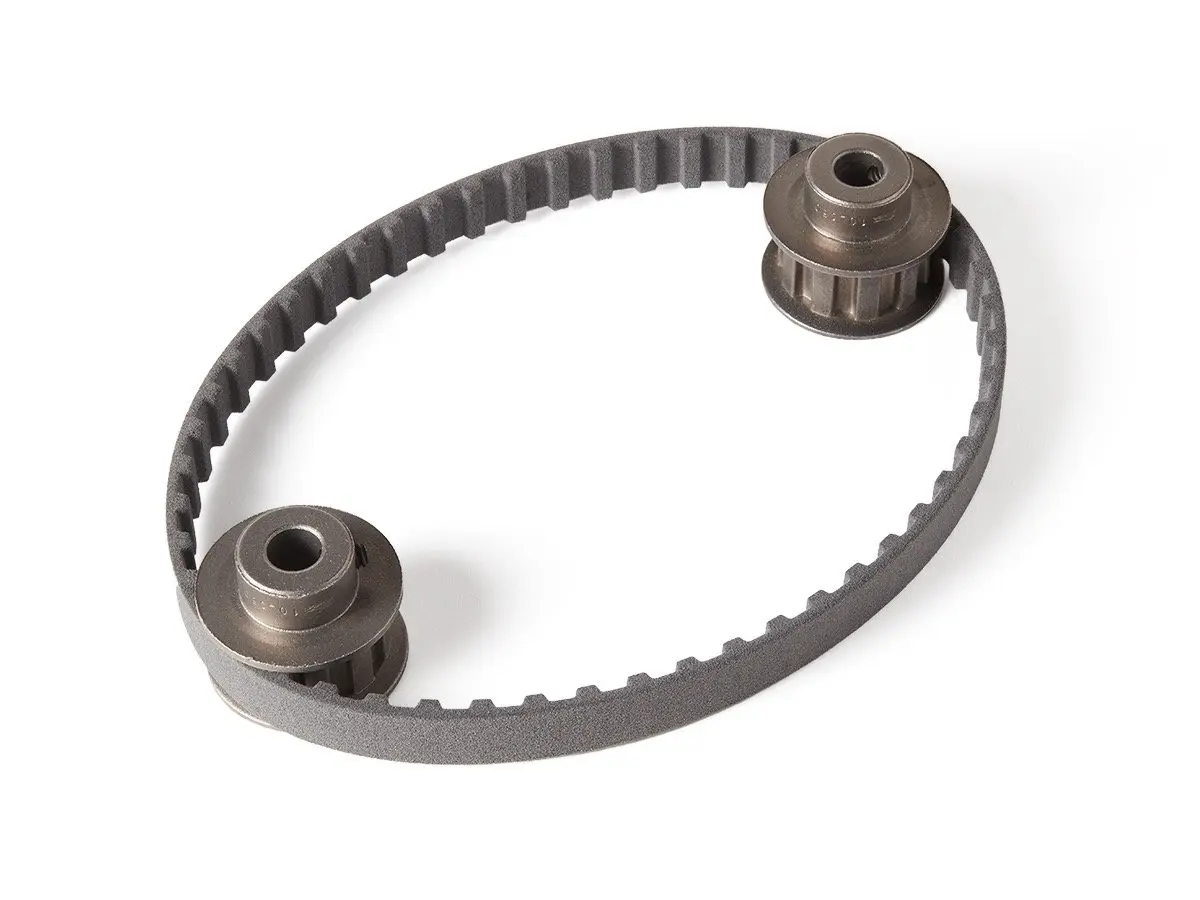
Avere a disposizione un materiale come il TPU significa che è possibile progettare e stampare in giornata parti di ricambio e supporti di produzione flessibili, in modo che la produzione non subisca mai interruzioni.
Arricchire il catalogo di materiali è un'ulteriore sicurezza per i produttori, poiché garantisce loro una protezione contro la rottura imprevista di parti o apparecchi. Poter contare su maggiori proprietà meccaniche in-house consente di ridurre l'impatto dei ritardi della catena di fornitura e dei costi elevati delle riparazioni effettuate dal produttore originale delle apparecchiature. Grazie alle parti in gomma stampate in 3D, ora è possibile riparare o sostituire su richiesta un intero sottoinsieme di componenti delle attrezzature. Evitando l'interruzione di una linea di produzione o di un processo, si possono risparmiare migliaia di dollari al giorno.
La TPU 90A Powder può essere utilizzata per gli smorzatori di vibrazioni nei test automobilistici e aerospaziali, ma anche per le dime destinate ai processi industriali, come la termoformatura di parti dalla forma unica. Nelle fabbriche automobilistiche, i grandi sistemi robotici operano su binari che devono piegarsi e ruotare. Ammortizzatori personalizzati e alloggiamenti morbidi possono evitare l'attrito e allungare la vita utile di questi apparecchi.
Prodotti personalizzati indossabili realizzati con volumi ridotti
Nei settori dello sport, della moda e delle tecnologie indossabili, i marchi che puntano a conquistare maggiori quote di mercato devono necessariamente offrire opzioni di personalizzazione. In passato, fino a quando la stampa 3D non è diventata accessibile, i costi associati alla creazione di attrezzature rendevano quasi impossibile la produzione di volumi ridotti o di pezzi unici. Tuttavia, prima dell'introduzione della TPU 90A Powder, la maggior parte dei materiali per la stampa 3D risultavano troppo rigidi per gli articoli sportivi o i dispositivi indossabili. Dalle suole per scarpe personalizzabili sulla base della pianta e della distribuzione del peso di una persona, ai caschi da football progettati per attutire gli urti, fino al cinturino per orologio adattato alla forma del polso, le possibilità sono infinite.
La sicurezza per la pelle della TPU 90A Powder in combinazione con il flusso di lavoro Fuse rendono finalmente possibile la personalizzazione della stampa diretta dei dispositivi indossabili. Sebbene alcuni marchi di lusso di orologi, accessori e calzature offrano dettagli personalizzati come monogrammi o grafiche, la personalizzazione della forma vera e propria di un articolo ha sempre avuto costi proibitivi. Grazie alla serie Fuse e alla TPU 90A Powder, la personalizzazione nel settore dei dispositivi indossabili è diventata una realtà.
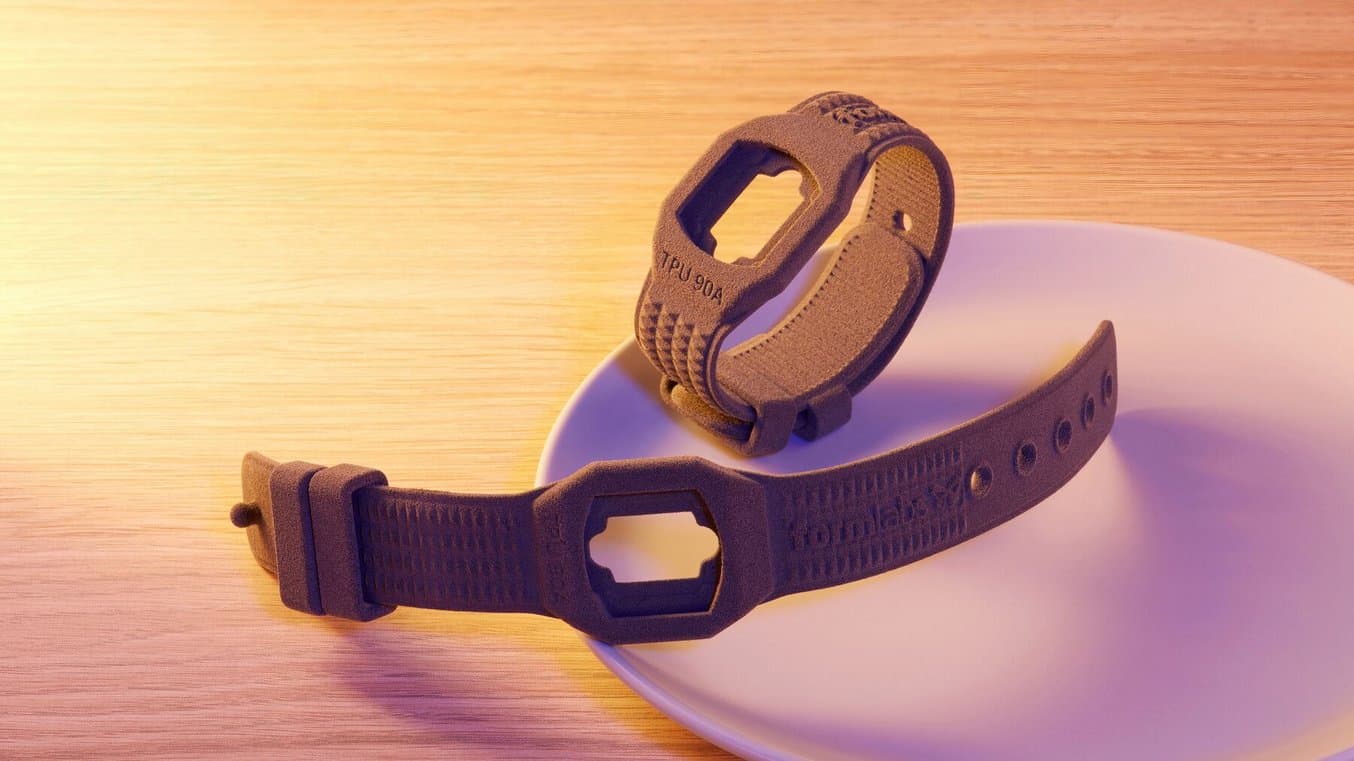
Il flusso di lavoro della serie Fuse con la TPU 90A Powder permette la produzione personalizzata in-house a un prezzo accessibile e con una configurazione semplificata.
Dispositivi medici
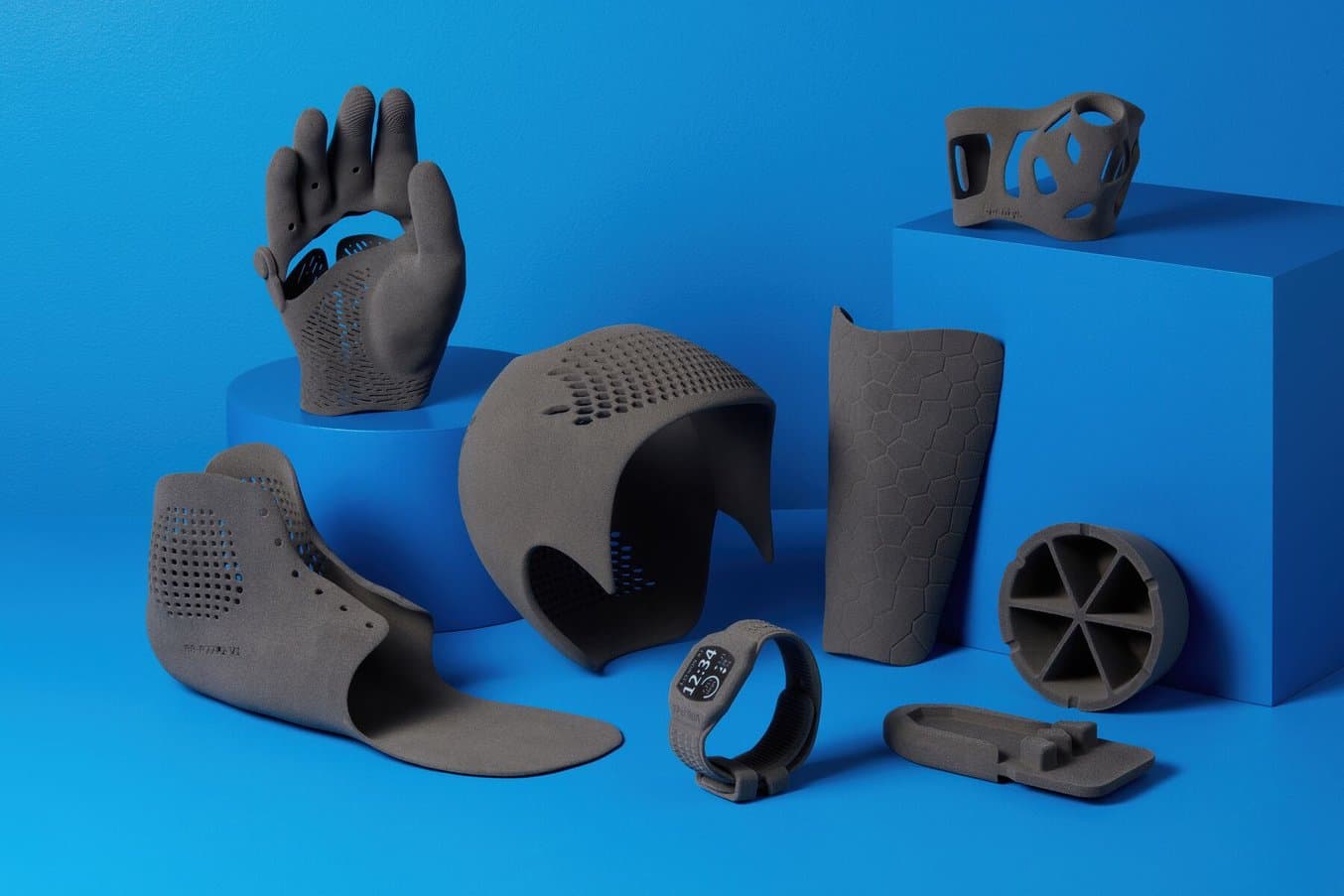
La TPU 90A Powder consente di creare diverse parti mediche ad alte prestazioni. Nell'immagine: un dispositivo protesico (OT Supply GmbH), un tutore per pollice (Spentys), un rivestimento ortopedico per caviglia e piede (Spentys), un cinturino per orologio e altro ancora.
Presso Formlabs Medical, crediamo che ogni struttura sanitaria dovrebbe avere accesso agli strumenti più recenti per migliorare le cure e fornire la migliore esperienza possibile ai pazienti. La TPU 90A Powder è la fase successiva della nostra visione, poiché arricchisce la nostra linea di polveri SLS leader del settore e fornisce un valore aggiuntivo alle nostre stampanti 3D della serie Fuse.
Grazie alla sua eccezionale durata e resistenza, la TPU 90A Powder è ideale per protesi, plantari, apparecchi su misura e dispositivi medici. Questo materiale crea nuove opportunità per i professionisti del settore medico, poiché combina l'elevato allungamento a rottura e la straordinaria resistenza alla lacerazione dei materiali in gomma con la libertà di design della stampa 3D SLS.
La TPU 90A Powder è un elastomero flessibile, ideale per la stampa 3D di parti mediche come:
-
Prototipi di dispositivi medici e dispositivi medici e componenti per utilizzo finale
-
Solette plantari e rivestimenti protesici
-
Dispositivi indossabili, guarnizioni, componenti antiurto e tubi
-
Tutori, caschetti di rimodellamento cranico
-
Solette correttive e per calzature sportive
Come altri materiali SLS, la TPU 90A Powder offre ai professionisti del settore medico il metodo più economico per la produzione in-house. Dalle suole per scarpe personalizzabili sulla base della pianta e della distribuzione del peso di una persona, ai caschi da football progettati per attutire gli urti, fino al cinturino per orologio adattato alla forma del polso, le possibilità sono infinite.
La TPU 90A Powder ha ottenuto la certificazione per il contatto cutaneo a breve termine e può essere considerata sicura per questo tipo di applicazione. Tuttavia, poiché non è stata sottoposta a ulteriori test per altre applicazioni biocompatibili, è responsabilità del produttore verificare l'idoneità delle parti stampate per l'uso previsto.
Come integrare la TPU 90A Powder nella produzione in-house
La TPU 90A Powder può essere integrata facilmente nel flusso di lavoro della serie Fuse e della Fuse Sift. Il materiale viene stampato in un ambiente aerato e non richiede un'atmosfera inerte. Inoltre, le parti in TPU non utilizzano la Surface Armor, ovvero il guscio di materiale semi-sinterizzato che circonda le parti in polvere più rigide, per cui il processo di eliminazione della polvere è abbastanza semplice. Sebbene la TPU 90A Powder non sia provvista di Surface Armor, è comunque consigliata la sabbiatura per rimuovere tutta la polvere in eccesso dalle parti, in modo da ottenere un materiale più pulito e facile con cui lavorare.
La conversione di una stampante Fuse alla TPU 90A Powder è assolutamente possibile, anche se si consiglia di utilizzare una Fuse Sift e una camera di stampa dedicate.
Nuove possibilità con la TPU 90A Powder
Indipendentemente dal fatto che la tua sia una piccola impresa che sta cercando di immettere sul mercato il suo primo prodotto o una grande impresa che vuole tutelarsi dalla crisi della catena di fornitura degli ultimi anni, portare la stampa 3D ad alte prestazioni in-house riduce i costi e migliora la stabilità. Un materiale come la TPU 90A Powder aumenta la portata di questi vantaggi permettendo nuove applicazioni e persino modelli aziendali completamente nuovi. Le parti morbide che dovevano essere prodotte in massa per garantire l'affidabilità possono ora essere stampate in 3D in modo coerente con un apparecchio accessibile.
I materiali sono determinanti per sbloccare nuovi modi di progettare e produrre o ridefinire quelli esistenti. Le parti in TPU si trovano ovunque e la combinazione di queste prestazioni comprovate con il flusso di lavoro avanzato delle stampanti SLS della serie Fuse aprirà la strada all'innovazione in ogni settore.