Produzione agile: come JetBoatPilot risponde alle esigenze del mercato con la stampa 3D SLS
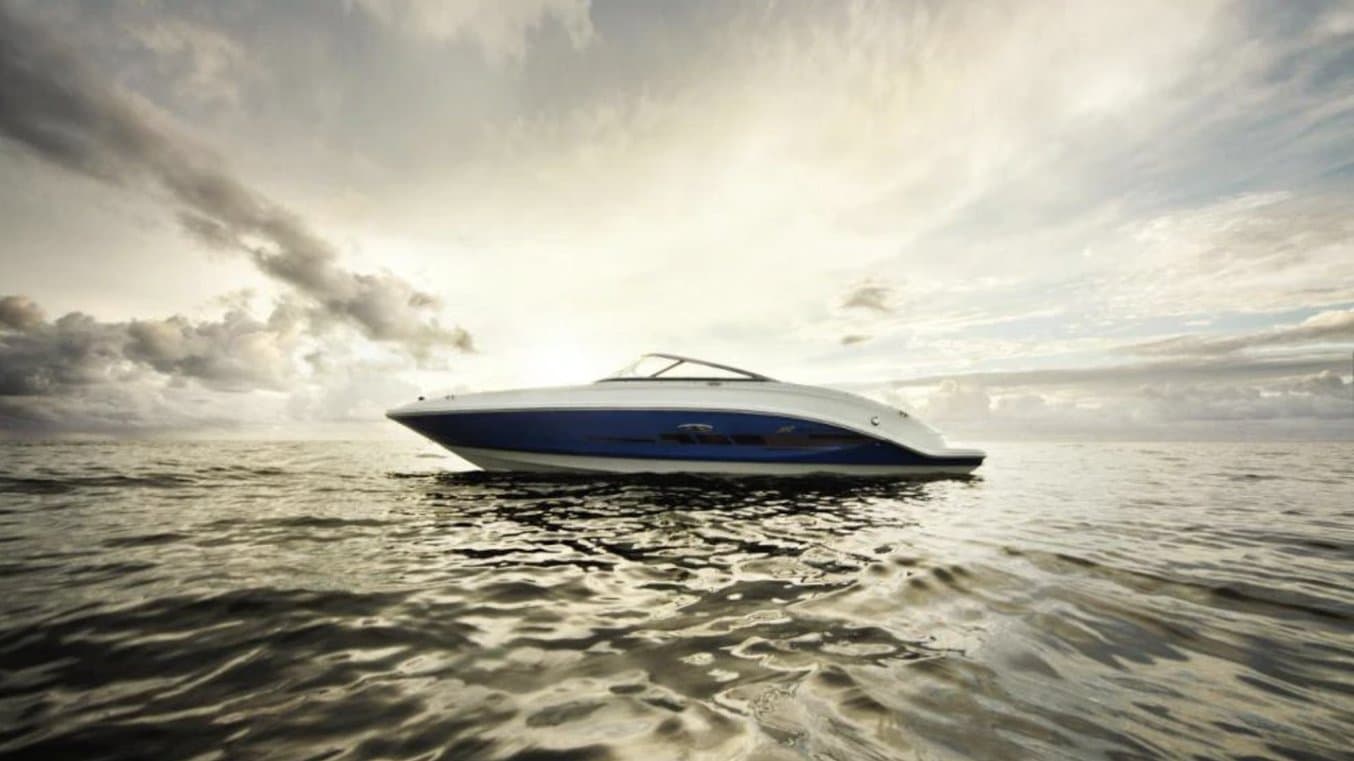
JetBoatPilot, azienda produttrice di parti e accessori per la navigazione, è diventata leader nel settore grazie alla creazione di prodotti aftermarket che migliorano le prestazioni e la manovrabilità a bassa velocità delle barche a idrogetto. Queste ultime, a differenza di quelle tradizionali con motore entrobordo, si comportano in modo molto diverso in fase di ormeggio e nelle zone con divieto di produrre moto ondoso o risucchi. Molti di coloro che hanno poca dimestichezza con queste manovre cercano di migliorare il controllo dell'imbarcazione a bassa velocità mediante l'aggiunta di bulloni per lo sterzo.
I prodotti JetBoatPilot aiutano i proprietari di barche a idrogetto a sentirsi più sicuri migliorando le caratteristiche di guida a bassa velocità dell'imbarcazione. L'utilizzo di stampanti 3D sia per la prototipazione che per le parti per uso finale consente a JetBoatPilot di creare una linea di produzione agile e di rispondere rapidamente sia alle esigenze del cliente che all'approvvigionamento del prodotto.
In qualità di produttore di parti aftermarket, le parti di JetBoatPilot sono solitamente a volumi ridotti e devono evolversi in risposta agli aggiornamenti dei prodotti da parte dei produttori originali. Questo modello aziendale richiede un'agilità di produzione che consenta di iterare e produrre rapidamente parti ad alte prestazioni anche senza attrezzature costose, per evitare costi eccessivi.
Per raggiungere questo obiettivo, JetBoatPilot utilizza le stampanti 3D stereolitografiche (SLA) Form 3 e quelle a sinterizzazione laser selettiva (SLS) Fuse 1 per prototipare e produrre parti aftermarket. Il Lateral Thruster 2.0, prodotto concepito di recente e dalle prestazioni eccezionali, è stato progettato e realizzato con la Fuse 1. Grazie alla Fuse 1 e alla Nylon 12 Powder, JetBoatPilot ha potuto ridurre i costi di sei volte rispetto ai metodi di produzione precedenti.
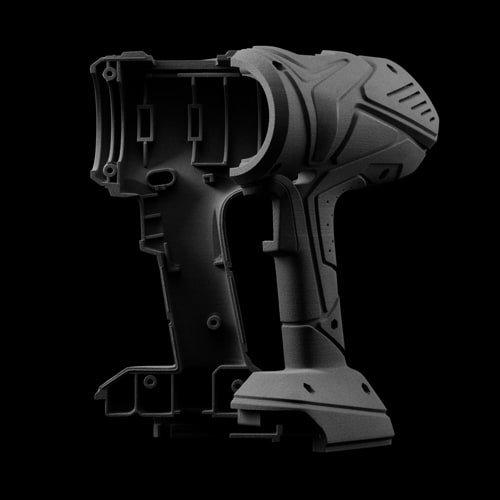
Introduzione alla stampa 3D tramite sinterizzazione laser selettiva (SLS)
Stai cercando una stampante 3D per creare parti robuste e funzionali? Scarica il nostro whitepaper per scoprire come funziona la stampa SLS e perché è un processo di stampa 3D molto diffuso per la prototipazione funzionale e la produzione per l’utilizzo finale.
Nata da una necessità
Nel 2010, il fondatore di JetBoatPilot, Will Owens, lavorava come venditore di barche Yamaha a Panama City, in Florida. Durante la bassa stagione, ha cominciato a creare brevi video per i proprietari di barche Yamaha, per lo più tutorial per ottimizzare le prestazioni delle imbarcazioni. I video hanno dato vita a una comunità online in cui i proprietari di barche parlavano delle loro esperienze e condividevano le medesime frustrazioni. Owens si è reso conto che i clienti provenienti da tutto il paese si lamentavano delle stesse cose.
"Ascoltavo le conversazioni e sentivo sempre la stessa cosa: 'La mia barca va alla grande ad alta velocità, ma è pessima a bassa velocità", spiega Owens. JetBoatPilot è nata grazie a Owens che progettava parti per rendere le barche a idrogetto dei clienti più reattive e affidabili.
"Tutti i prodotti di successo nascono da una necessità, cioè da un problema che va risolto", prosegue Owens.
Individuazione del problema e successo iniziale
La propulsione a getto, presente soprattutto nelle barche sportive, nelle moto d'acqua e negli acquascooter, è molto efficace per la guida ad alta velocità. Tuttavia, a basse velocità e in assenza di propulsione, il conducente ha pochissimo controllo. Al momento dell'ormeggio o quando si naviga al minimo vicino a un'altra imbarcazione, tale mancanza di controllo porta a una manovrabilità meno prevedibile e a costi di riparazione potenzialmente elevati.
"Aumentare il controllo in prossimità del molo o durante le manovre a bassa velocità vicino ad altre barche è una cosa fondamentale. Dare al guidatore di una barca da 80 000 $ la piena certezza di poter avere un'eccellente esperienza di navigazione con la propria famiglia rappresenta per noi un aspetto importante", afferma Owens.
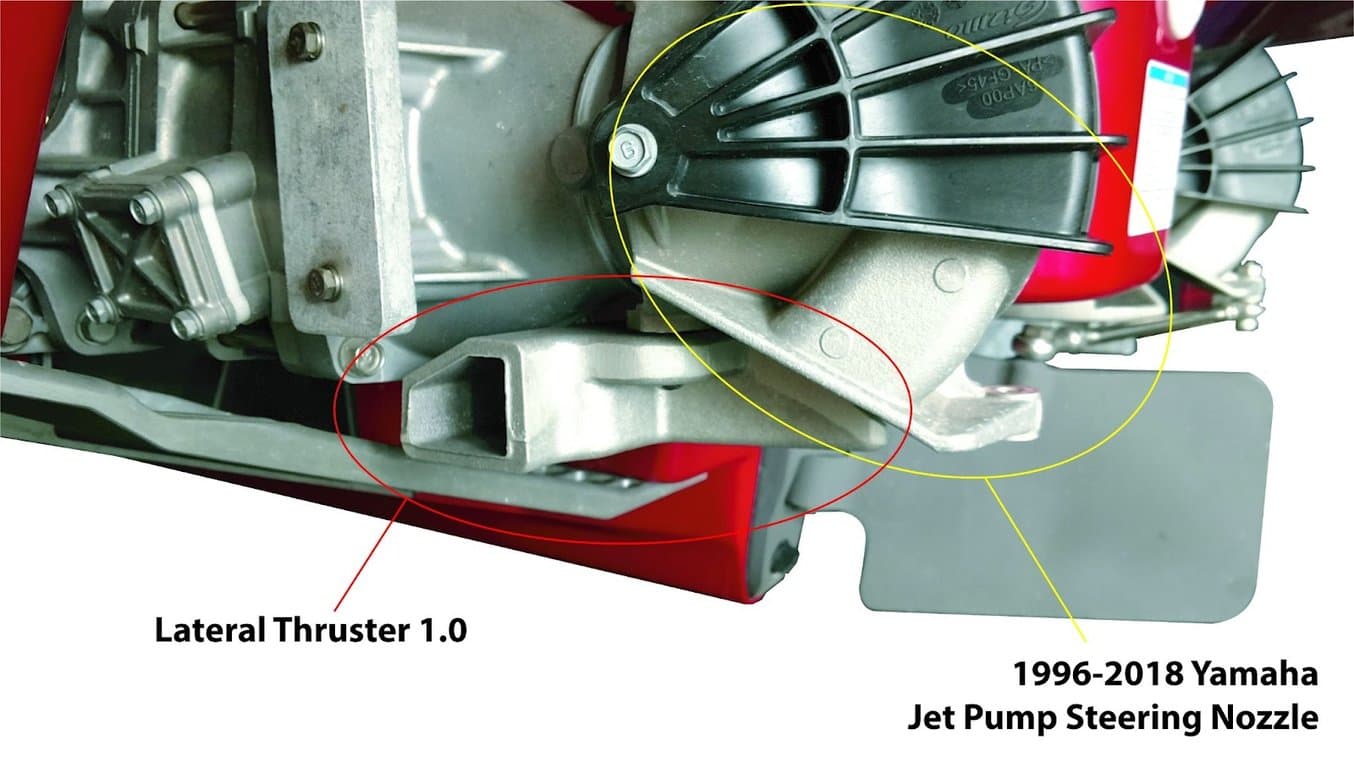
La prima versione del Lateral Thruster, ricavato dall'alluminio
Nel 2018, JetBoatPilot ha presentato dei prodotti per il controllo dello sterzo specificamente per migliorare il controllo della retromarcia, e ha spedito la prima iterazione del Lateral Thruster ai clienti di tutto il mondo. Il primo Lateral Thruster, ottenuto dalla colata in sabbia dell'alluminio e imbullonato utilizzando i punti di montaggio dei componenti già esistenti, si installava sotto la pompa a getto di una barca a idrogetto Yamaha e deviava una parte del flusso inverso verso una direzione più laterale rispetto a quella del sistema di sterzo originale. In questo modo, aumentava significativamente il controllo offerto dall'ugello dello sterzo. Il riscontro dei clienti è stato straordinario e il prodotto è diventato rapidamente uno dei più venduti di JetBoatPilot.
Il primo ostacolo
Tuttavia, appena un anno dopo, Yamaha introdusse un nuovo design dell'ugello dello sterzo che rese obsoleto il nuovo "Lateral Thruster" di JetBoatPilot.
"La prima versione ci ha fruttato solo un anno di vendite nel nuovo mercato. Abbiamo pensato che fosse tutto finito, che ormai fosse passato il nostro momento", racconta Owens.
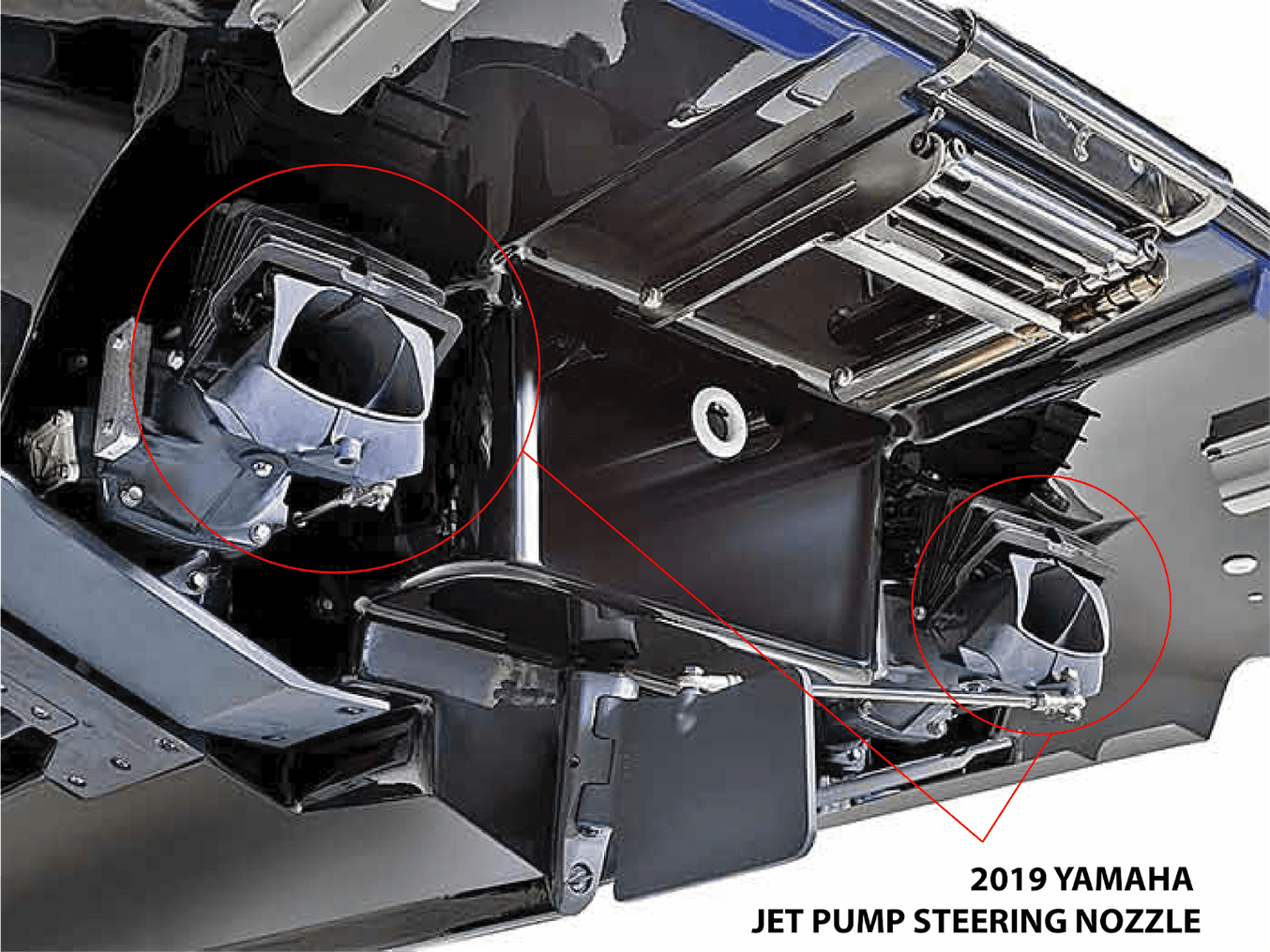
Eppure, quasi subito dopo l'uscita del nuovo ugello Yamaha, gli acquirenti del vecchio Lateral Thruster, che erano passati al modello più recente, inviavano e-mail e telefonavano a Owens, dicendogli di non avere lo stesso controllo sulla nuova barca rispetto a quella precedente su cui era montato il Lateral Thruster, e chiedevano che ne venisse realizzata una nuova versione.
Il passaggio alla stampa 3D
Il team di JetBoatPilot ha cominciato a progettare e poi ha optato per la stampa 3D in virtù della velocità e della versatilità dei materiali. "Siamo passati immediatamente alla stampa 3D, perché permette di costruire il prototipo molto rapidamente. Sapevo che avrei potuto testare subito l'aderenza. Ho una Form 3 in ufficio. Abbiamo realizzato i primi prototipi con la tecnologia SLA e siamo riusciti a ottenere un buon risultato", spiega Owens.
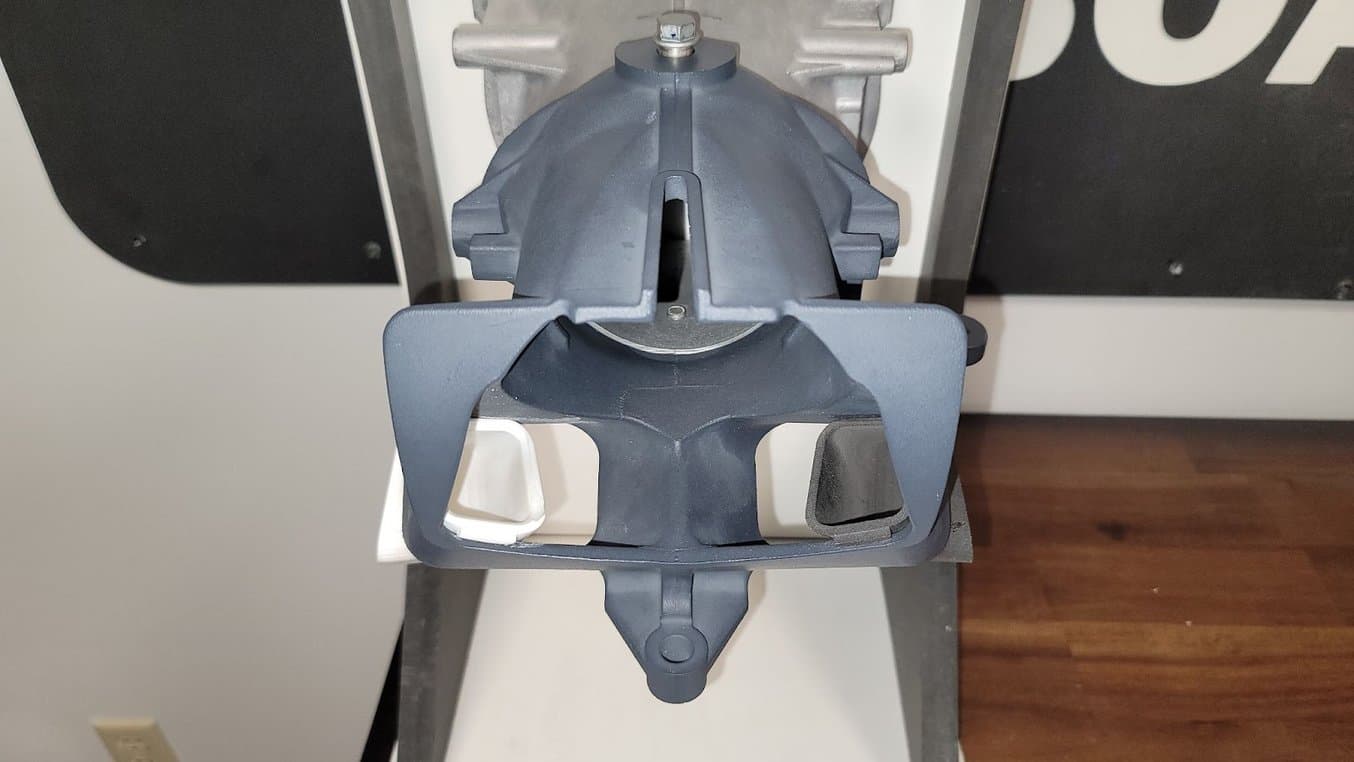
Prototipo del Thruster 2.0 realizzato con la Rigid 10K Resin (parte bianca sul lato sinistro).
Impiegando la Tough 1500 Resin e la Rigid 10K Resin per replicare la rigidità delle parti lavorate, il team di Owens ha testato il design del Lateral Thruster nella nuova versione dei motori Yamaha e ha scoperto con soddisfazione un altro vantaggio della stampa 3D. Laddove le parti in alluminio del propulsore dovevano corrispondere esattamente a quelle del motore a causa della loro rigidità, la leggera flessibilità propria della stampa con le resine SLA ha fatto sì che anche i motori con piccole differenze di tolleranza potessero sfruttare la stessa parte del Thruster.
Il passaggio alla SLS
Dopo i test di aderenza e le iterazioni, era giunto il momento di mettere il Lateral Thruster in acqua. Owens voleva utilizzare un materiale che fosse più simile alle parti lavorate della prima versione del Thruster. "Sentivamo la necessità di passare alla Fuse 1, perché volevamo qualcosa che fosse conforme agli standard e alla qualità dell'utente."
Il team dedicato alla Fuse 1 di Formlabs ha stampato una parte di prova e, dopo aver constatato che il Lateral Thruster funzionava perfettamente in acqua, il team di JetBoatPilot ha deciso di incrementare le proprie capacità di stampa 3D.
"L'abbiamo collaudato, e quell'aggeggio ha funzionato davvero bene. Con la Fuse 1 posso effettivamente inserire la parte negli ugelli che hanno una geometria leggermente più stretta. Posso fletterla e piegarla e va nella posizione corretta. Si incastra subito nel punto giusto, ed è ancora abbastanza resistente per svolgere la sua funzione. E così abbiamo acquisito un po' di coraggio", continua Owens.
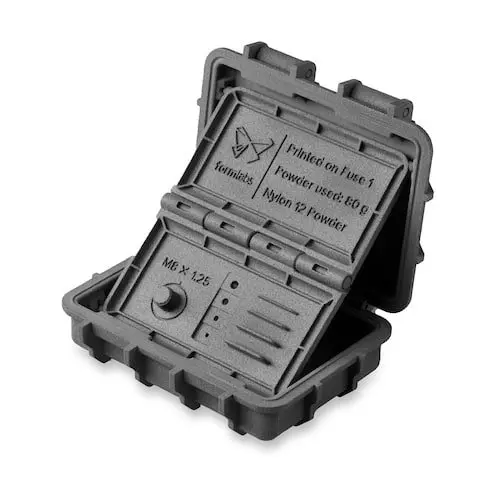
Richiedi un campione gratuito
Guarda e tocca con mano la precisione della stampa SLS di Formlabs. Saremo lieti di inviare presso la tua azienda un campione gratuito.
JetBoatPilot ha acquistato una Fuse 1 e ha proseguito con le iterazioni, eseguendo sia test interni che inviando i prototipi ai clienti per ottenere un riscontro.
"Siamo usciti, abbiamo portato la barca in retromarcia a 4000 giri al minuto e l'abbiamo lasciata andare, no? Non ne abbiamo mai rotta una. Quindi penso che l'aspetto migliore di tutta la faccenda sia che tutte le parti che abbiamo stampato hanno funzionato bene", sostiene Owens.
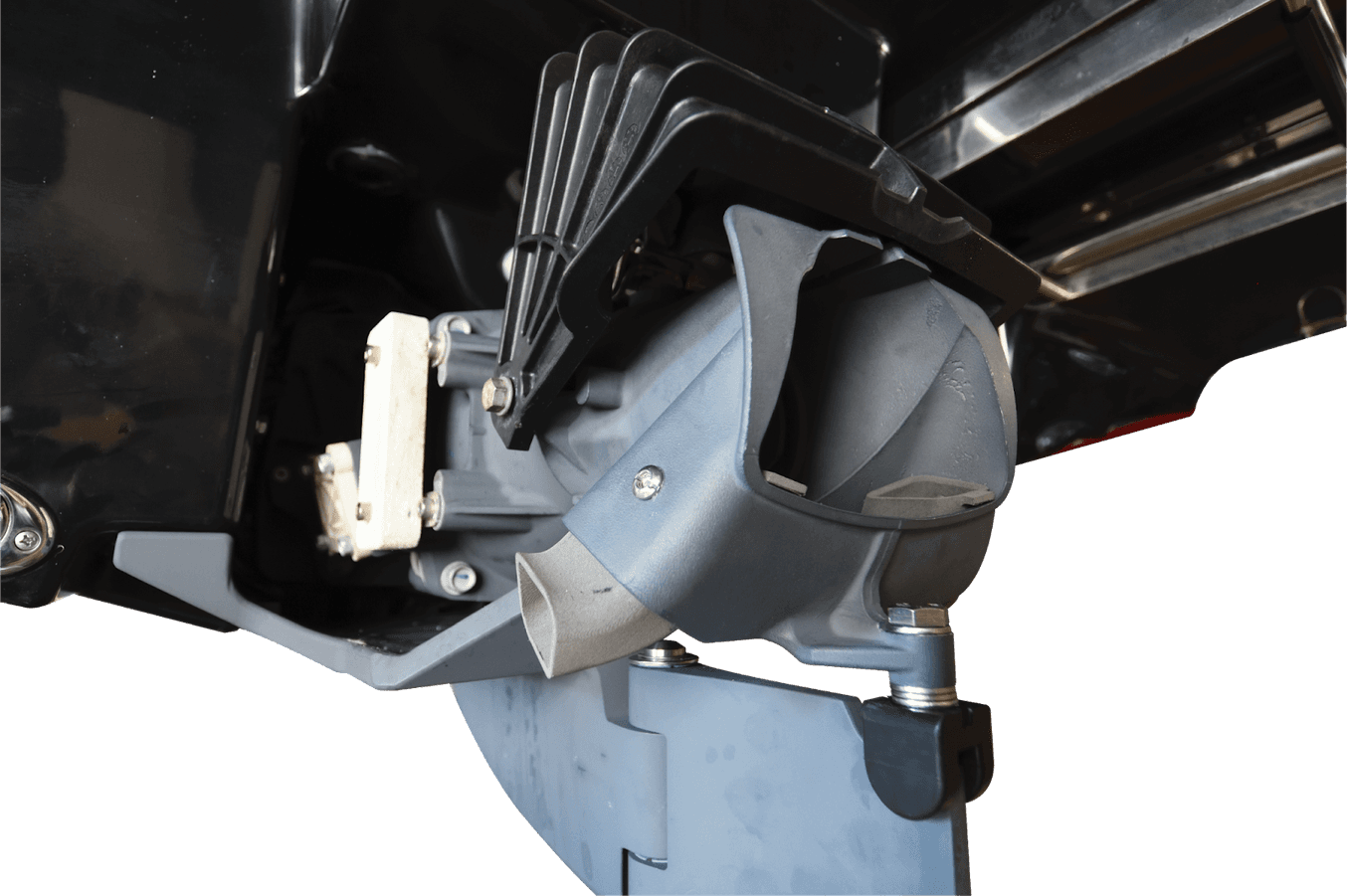
Una parte per uso finale del Thruster 2.0 stampata in 3D con la Fuse 1 (parte grigio chiaro).
Risparmio sui costi con la produzione in-house
Il risparmio di tempo nel processo di iterazione è stato evidente fin da subito. Invece di esternalizzare i processi a un'officina, è stato creato tutto internamente, e JetBoatPilot è stata in grado di progettare, stampare, testare e iterare le parti nel giro di una settimana, anziché di un mese.
L'efficienza del workflow è stata certamente utile, ma il vero vantaggio è stato il costo della merce. Il Lateral Thruster 2.0 Kit, che include due parti realizzate con la Nylon 12 Powder, un paio di viti, una chiave e un adesivo, costa a JetBoatPilot 11 $ in materiali.
Lo stesso kit per il Lateral Thruster 1.0 costa sei volte tanto in materie prime. L'esternalizzazione a un'officina per i due pezzi di alluminio non solo stava rallentando il processo, ma era anche incredibilmente dispendiosa, e il costo si riversava sul cliente.
"Probabilmente il prezzo al dettaglio della versione in alluminio sarebbe stato di 400 $, o addirittura di 600 $, se avessi voluto esagerare. Ma a quel prezzo non ne avrei venduti così tanti. Adesso invece lo vendo a 199 $ e il cliente ne è entusiasta. E guadagno venti volte il costo delle materie prime", dice Owens.
L'algoritmo di nidificazione riduce i costi dell'intera linea di prodotti
La Fuse 1 ha anche un altro vantaggio. L'algoritmo di posizionamento 3D permette a Owens di collocare 34 pezzi, o 17 kit completi, in una camera di stampa, e di inserire nello spazio intermedio anche le parti di un altro prodotto, chiamato cavalletto. Aumentando la densità di stampa, il costo dei materiali si abbassa ulteriormente.
"Abbiamo realizzato i cavalletti in polietilene ad alto peso molecolare (HMW), e ci apprestiamo a passare allo stampaggio a iniezione, ma li abbiamo stampati in 3D durante lo sviluppo delle attrezzature per lo stampaggio a iniezione. Pertanto li abbiamo montati all'interno della cavità tra le parti del Lateral Thruster. Riusciamo a ricavare 34 cavalletti da ciascun lotto di 34 Lateral Thruster."
Produzione agile
Portare la produzione in-house con la Fuse 1 ha permesso a JetBoatPilot di creare un sistema di produzione più reattivo e dinamico. È possibile avvalersi dell'elevato impegno della comunità nautica e ottenere un feedback rapido e onesto da parte dei clienti. Di conseguenza, se un cliente fornisce un feedback che porta a modificare il design, o se Yamaha lancia sul mercato una nuova versione del motore, JetBoatPilot può contare su un workflow agile che si evolve per soddisfare la domanda.
"Proprio perché ascolto chi usa i miei prodotti e sono io a progettarli e a programmarli, posso intervenire e modificare il design molto rapidamente. E poi, grazie alla Fuse 1, non ho uno strumento da buttare nella spazzatura. Siamo in grado di cambiare velocemente", dice Owens.
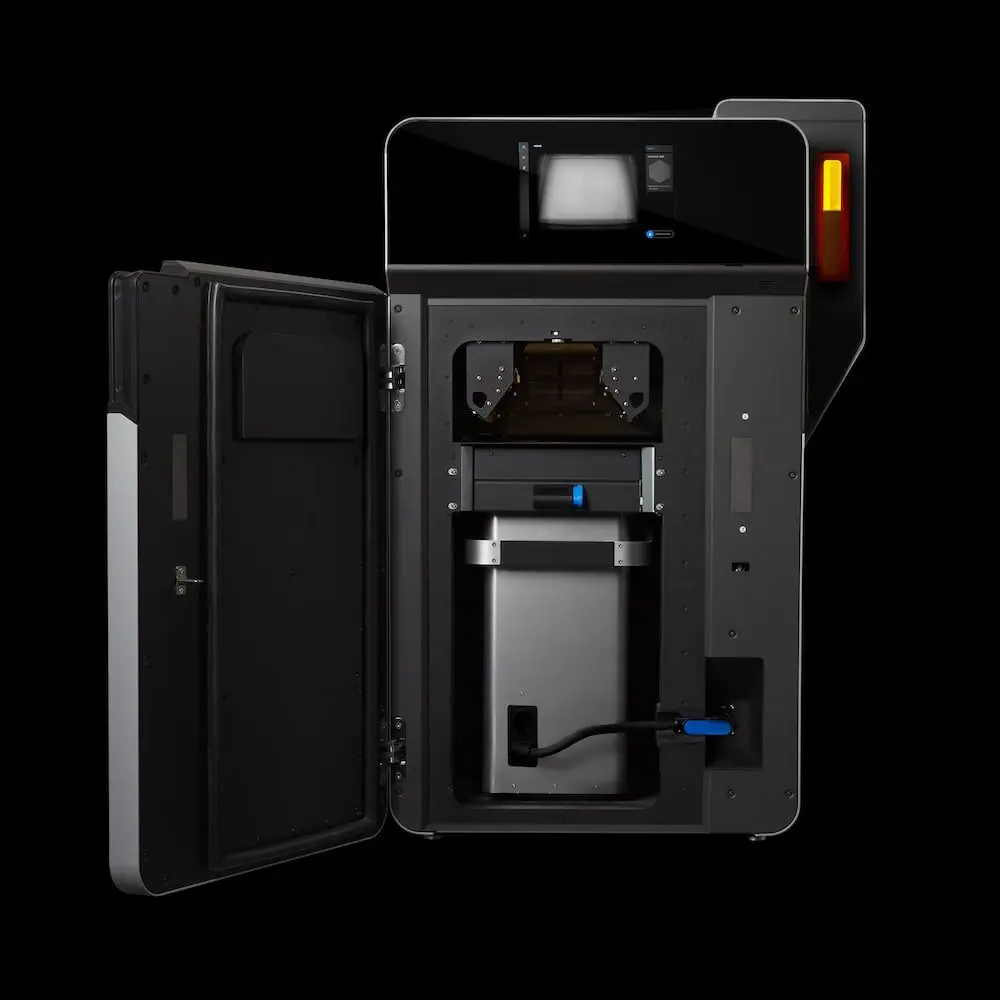
Dimostrazione di prodotto della Fuse 1
Guarda la nostra dimostrazione di prodotto per un’introduzione alla Fuse 1 e alla stampa 3D SLS svolta dagli esperti di Formlabs.