Sinn Spezialuhren, un produttore di orologi meccanici con una vasta gamma di funzionalità, aveva originariamente acquistato una stampante 3D stereolitografica (SLA) Form 3 per la prototipazione. Per scoprire di più su come il loro team di sviluppo del prodotto ha utilizzato la stampa 3D per creare prototipi di alta precisione per orologi, leggi la loro storia.
Il team di sviluppo dell'azienda ha però capito molto velocemente che avrebbe potuto sfruttare la stampa 3D per la fabbricazione di strumenti di produzione come attacchi, fissaggi e attrezzatura per i test.
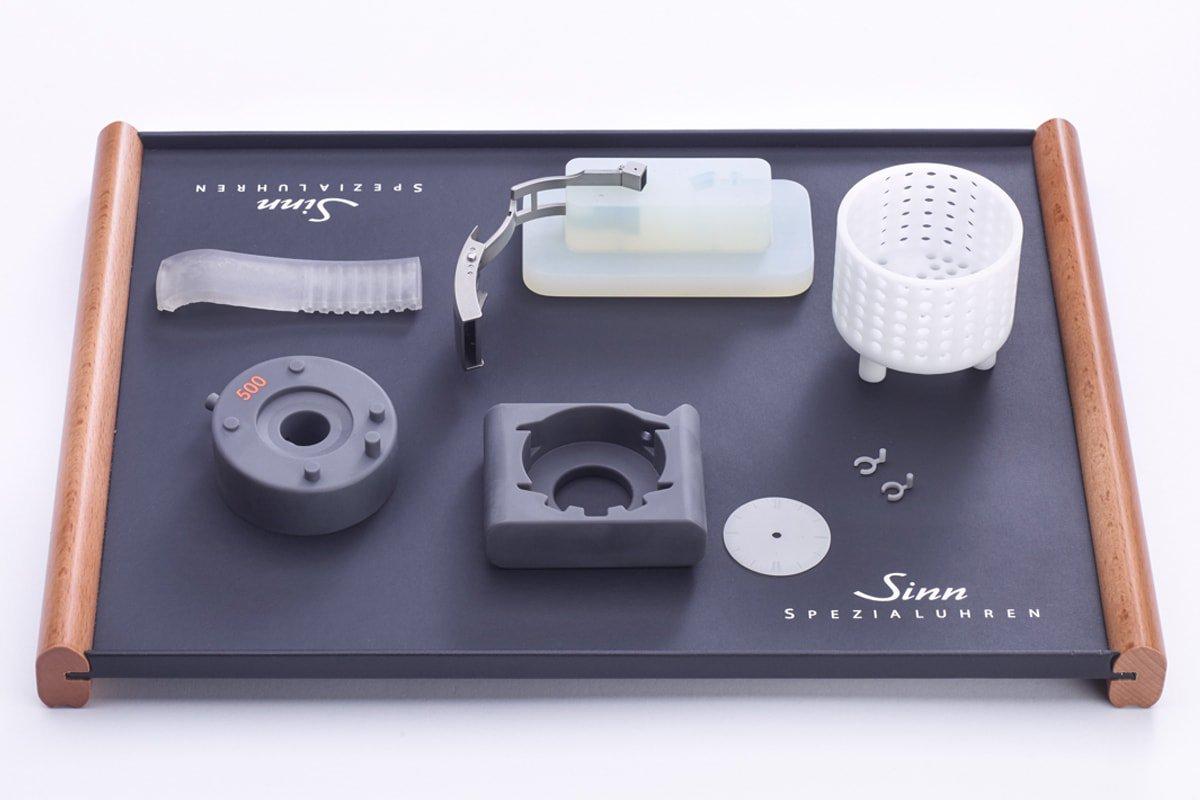
Prototipi di parti di orologi, fissaggi e attrezzatura per test stampati in 3D usando la Form 3.
Dagli strumenti personalizzati alla produzione in serie di parti
Non appena l'azienda ha ricevuto la sua prima stampante 3D per l’utilizzo in-house, tutti si sono dimostrati interessati a un possibile uso di questa tecnologia per applicazioni che andavano oltre la prototipazione, come ad esempio la produzione di attrezzature personalizzate. Nils Hunder, responsabile del design degli orologi e dello sviluppo di prototipi e stampa 3D presso Sinn Spezialuhren, ci ha raccontato: “La stampante ci sta aiutando molto in questo campo”.
“Possiamo creare attacchi e fissaggi durante la notte in modo rapido ed economico”.
Nils Hunder, direttore del dipartimento di ingegneria, sviluppo del prodotto e prototipazione
Prima di iniziare a usare la stampa 3D, l’azienda affidava la produzione di strumenti personalizzati a fornitori di servizi esterni. Ciò si traduceva in elevati costi di esternalizzazione e tempi di consegna più lunghi, in media 1-2 settimane per montaggi e attrezzature, e anche in questo modo era difficile avere la certezza che i risultati sarebbero stati quelli sperati o che il denaro era stato speso bene.
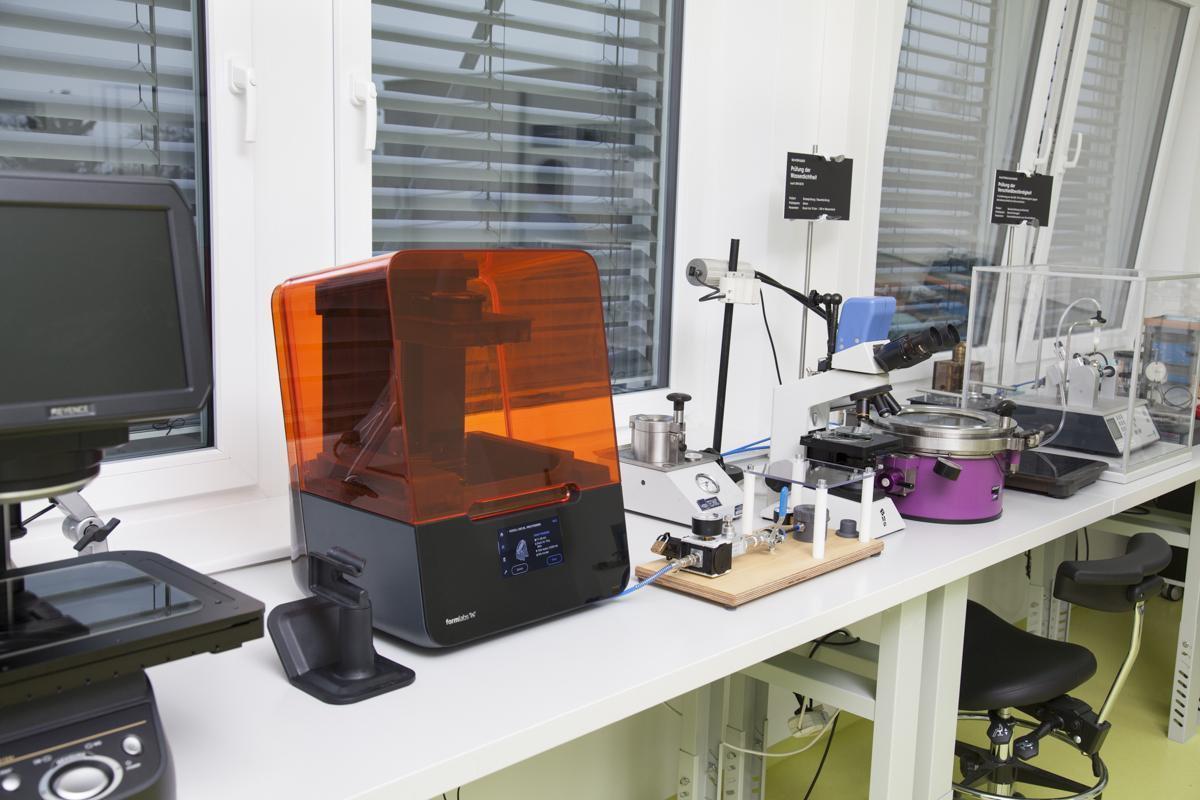
La Form 3 nel laboratorio di Sinn Spezialuhren.
Ora la Form 3 viene utilizzata sempre di più nella produzione di attrezzature. Gli unici costi sostenuti sono quelli per il materiale e il tempo necessario per la post-elaborazione. Le parti possono essere stampate durante la notte e se le parti o i design stampati non soddisfano i requisiti, è possibile apportare rapidamente le modifiche necessarie.
Nils Hunder usa principalmente la Tough 1500 Resin e la Tough 2000 Resin perché sono adatte a produrre parti resistenti con una distorsione minima. In un’occasione la Form 3 è stata utilizzata per stampare delle parti in serie: 500 tappi a corona per orologi al quarzo, che non erano disponibili come prodotti di massa. Quando gli orologi sono conservati in magazzino, questi tappi a corona vengono inseriti tra la cassa e la corona per evitare che la batteria si attivi durante lo stoccaggio. Il fornitore abituale di Sinn Spezialuhren non aveva disponibilità di tappi a corona a causa della pandemia di coronavirus e i costi di produzione sarebbero stati troppo alti con un ordine minimo di 10 000 pezzi. Fortunatamente la Form 3 è in grado di stampare 50 di questi tappi a corona in una sola volta. Grazie alla leggera flessibilità della Tough 1500 Resin, le parti stampate non graffiano gli orologi e sono riutilizzabili.
In un'altra applicazione, le casse di orologi in acciaio Damasco vengono incise in-house a scopo di test e l'acido utilizzato nel processo deve essere mescolato per una migliore distribuzione della temperatura. Il team di Sinn utilizza cestelli stampati in 3D con la Rigid 4000 Resin per la sua elevata resistenza a sostanze chimiche e acidi.
Un ulteriore campo di applicazione è la tecnologia di deumidificazione sviluppata da Sinn Spezialuhren per gli orologi subacquei. Questi orologi vengono riempiti di un gas protettivo e la cassa richiede un supporto che consenta di far penetrare il gas direttamente nella cassa. Utilizzando la tecnica di produzione convenzionale della fresatura, le due parti della montatura per questa fase di produzione sarebbero costate circa 200 € e la produzione avrebbe richiesto 1-2 settimane di tempo. Con un costo di 30 € per i materiali, il costo totale per parte stampata utilizzando la Form 3, inclusa la post-elaborazione, ammonta a meno della metà. Anche i tempi di produzione sono stati drasticamente ridotti, poiché gli ingegneri possono stampare le parti durante la notte.
Inoltre, il team può incidere gli attacchi con etichette personalizzate in modo che sia evidente a quale modello di orologio appartengono, e questo semplifica molto il lavoro quotidiano. Con strumenti di produzione convenzionali anche questo passaggio avrebbe comportato dei costi aggiuntivi.
Sviluppo in-house di un sistema di test certificato dall’ente di supervisione tecnica tedesco (TÜV)
L'orologio subacqueo UX, uno dei modelli della gamma di orologi Sinn, è riempito con un olio trasparente che cambia volume con i cambi di temperatura, quindi l'orologio ha una base a membrana che si estende quando viene riscaldata o si ritrae nella cassa quando la temperatura si abbassa. Questa base a membrana è stata una vera sorpresa per il team di Hunder durante lo sviluppo di un sistema di test.
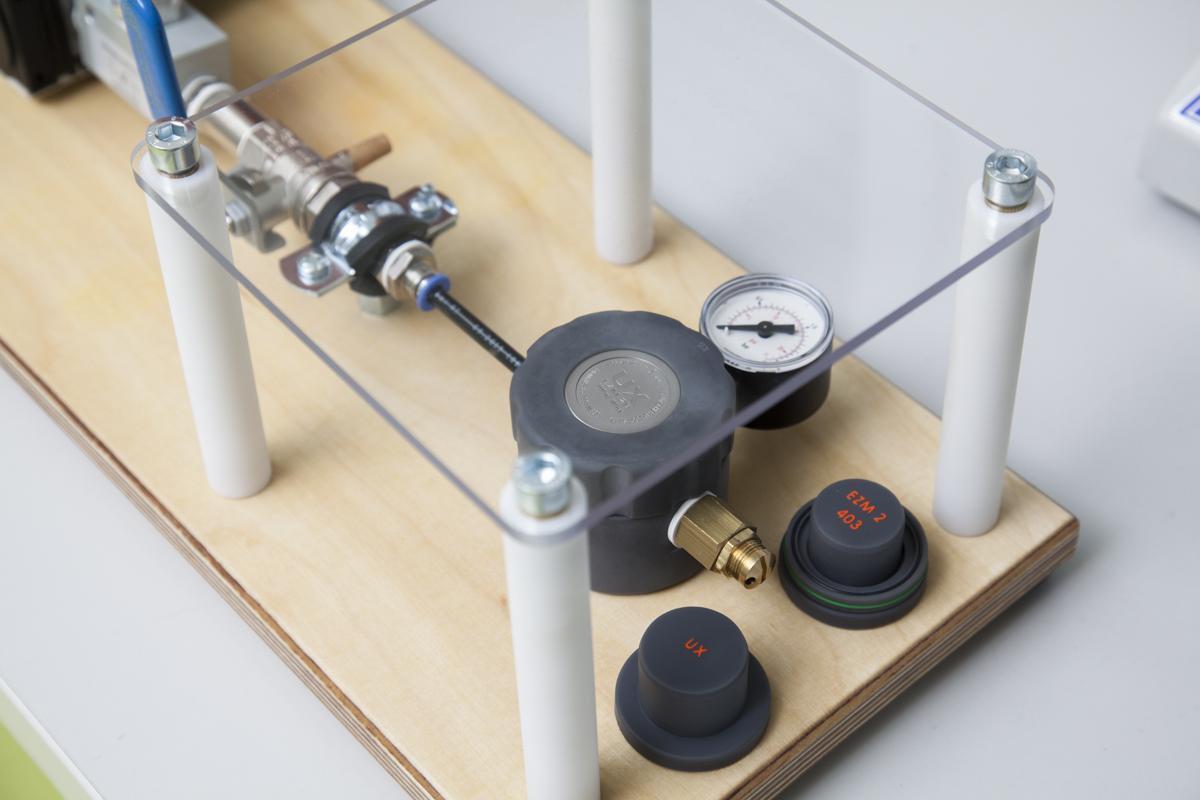
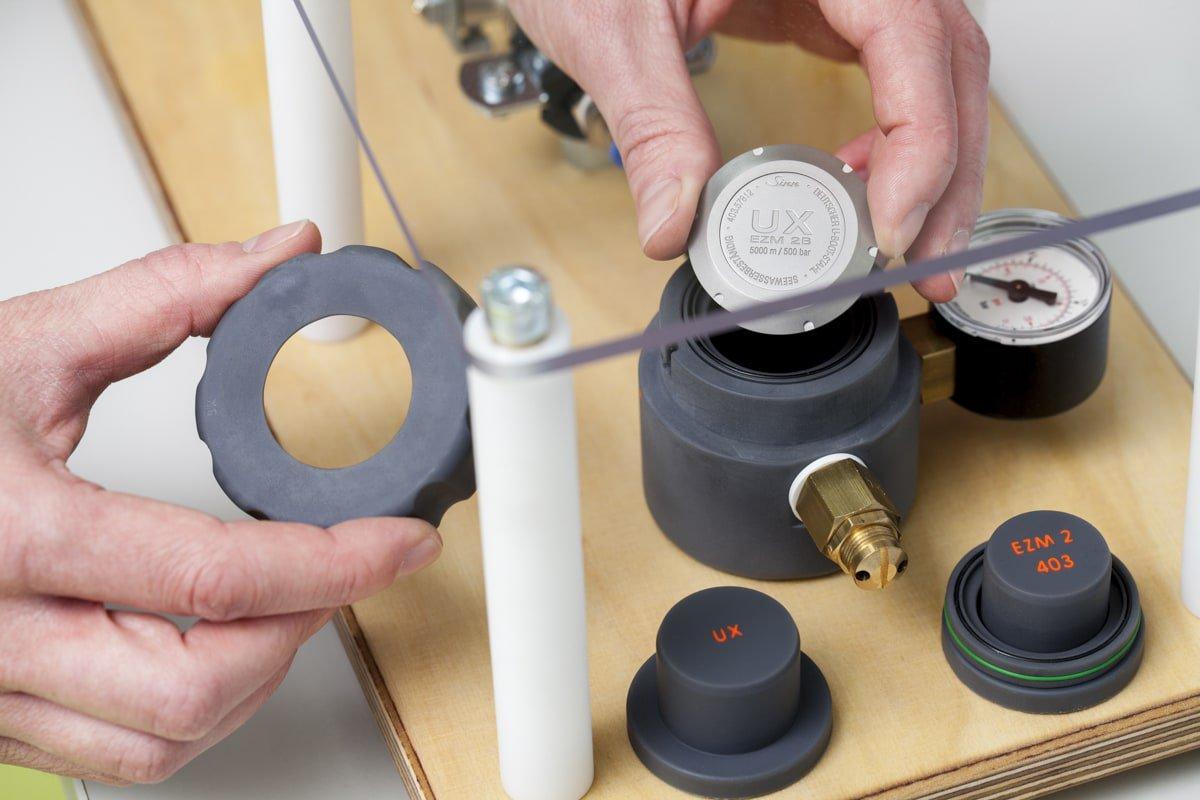
Sistema di test del fondo a membrana per il modello di orologio UX, con attacco stampato in 3D.
Lo scopo del sistema di test è quello di controllare l'oscillazione della base della membrana, che può essere piana o leggermente inclinata, in modo da poterla riallineare se necessario. In precedenza, era necessario assemblare e riscaldare un intero orologio al solo scopo di effettuare i test. Si trattava di un processo molto lungo, perché tutte le parti entravano a contatto con il liquido e dovevano poi essere ripulite.
Per semplificare questo processo così laborioso è stato sviluppato un sistema di test che utilizza la pressione dell'aria per simulare il comportamento del liquido.
Guarda il video: il sistema di test della base della membrana stampato in 3D in azione.
La Tough 2000 Resin è stata utilizzata per stampare il contenitore a pressione, con diversi anelli di inserimento in cui si adattano diverse casse, e la chiusura con attacco a baionetta. Questo attacco a baionetta è stato la sfida più grande perché è molto difficile da produrre con i metodi convenzionali. Inoltre, i supporti per il cristallo del quadrante in acrilico sono stati realizzati con la Rigid 4000 Resin.
Il banco da test stampato in 3D all’inizio era stato pensato solo per testare il funzionamento delle strumentazioni di prova e l’utilizzo dell’attacco a baionetta, ma alla fine ha funzionato così bene da eliminare la necessità della produzione convenzionale. Il banco da test stampato in 3D è stato anche ispezionato e approvato dall’ente di supervisione tecnica tedesco (TÜV).
“Una volta stabilito che la parte di cui hai bisogno può essere stampata, puoi concentrarti esclusivamente sulla funzionalità, il che è un enorme vantaggio”.
Nils Hunder, direttore del dipartimento di ingegneria, sviluppo del prodotto e prototipazione
Inizialmente il team di Hunder aveva richiesto la creazione del sistema per test al fornitore che si occupa della produzione in serie delle casse degli orologi, ma poi hanno scoperto che il fornitore avrebbe utilizzato la stessa fresatrice che utilizza per fabbricare le casse degli orologi, il che avrebbe comportato un ritardo nella produzione degli orologi stessi. Alla fine Sinn Spezialuhren ha inviato al fornitore il sistema di test progettato in-house e l’azienda è diventata a sua volta un fornitore: un'esperienza completamente nuova per il team.