Progettazione della sedia a rotelle del futuro con la stampa 3D
“Ho perfino rinunciato ad andare al supermercato, che dista solo due isolati.”
Quando Satoshi Sugie, fondatore di WHILL, sentì questa frase, si rese conto che le persone meritavano di meglio. Oggi è a capo di un’azienda che produce sedie a rotelle e la loro missione è quella di offrire soluzioni di mobilità divertenti e innovative.
Costruire la nuova generazione di sedie a rotelle non è stato facile. Gli ingegneri di WHILL hanno usato stampanti Formlabs e un processo di design generativo per superare i propri limiti e creare un prodotto davvero unico.
Continua a leggere per scoprire da Yasuhiro Hirata com’è stata sviluppata la sedia a rotelle WHILL.
La stampa 3D per accelerare lo sviluppo
Le startup devono affrontare una serie di problemi, primo fra tutti le pressioni legate ai tempi e ai costi. Questo vale soprattutto per le startup che producono hardware (ne sappiamo qualcosa!), che si trovano spesso a dover risolvere problemi mai affrontati prima. Il vero banco di prova di qualunque startup è il superamento di ostacoli improvvisi, che possono essere economicamente costosi e far perdere tempo prezioso. Dato che la produzione di parti in volume ridotto con i metodi di produzione tradizionali può essere difficoltosa, le parti complesse di cui WHILL aveva bisogno per la sua sedia a rotelle creavano non pochi problemi al team. Per sopravvivere, l’azienda ha dovuto trovare un modo per ridurre il costo di ogni sedia a rotelle.
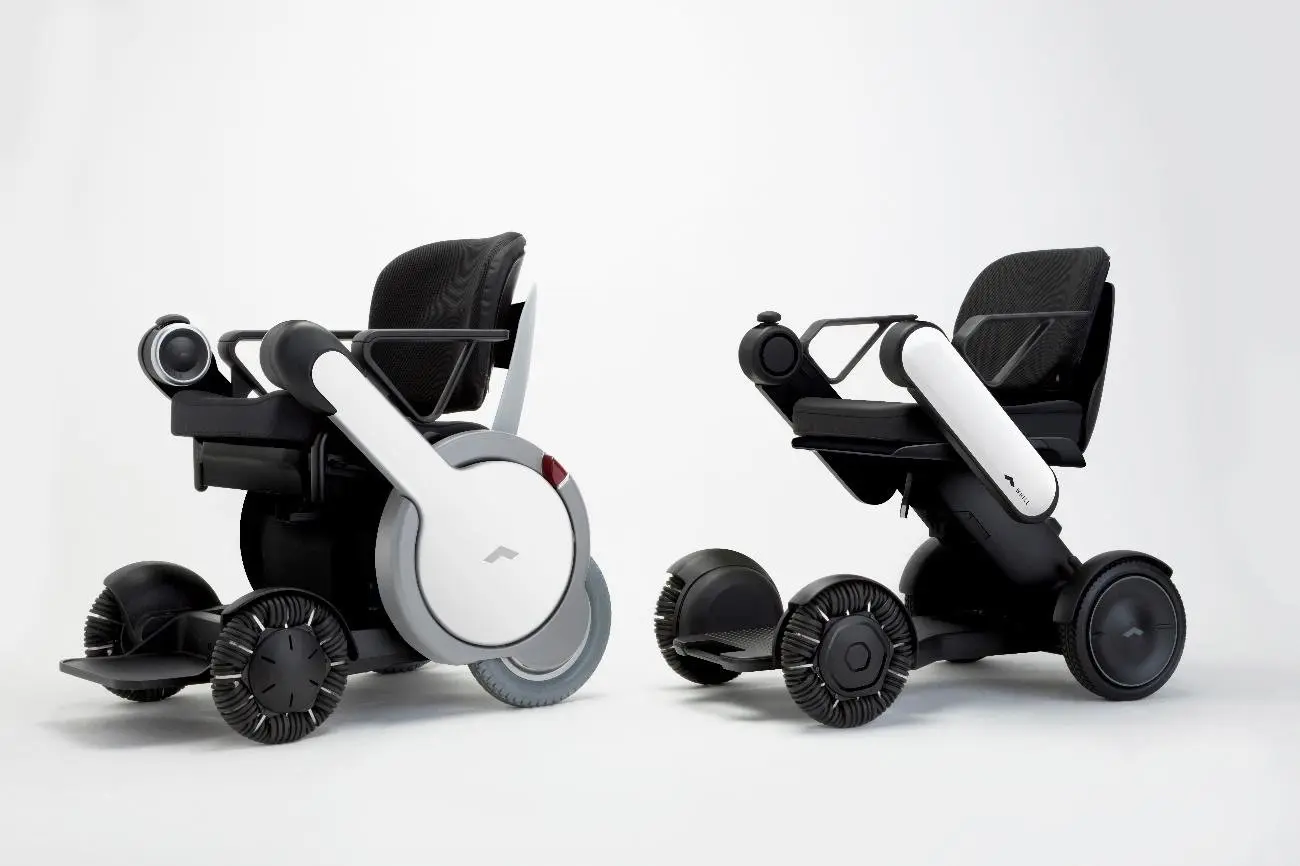
L’azienda ha capito che bisognava creare velocemente dei prototipi per molte delle parti complesse della sedia a rotelle e per questo si è rivolta a un fornitore esterno in grado di stamparli in 3D. Ma WHILL si è presto resa conto che i costi e le tempistiche associate all’esternalizzazione della stampa 3D non sarebbero stati sostenibili a lungo termine. Hirata sapeva che WHILL non avrebbe potuto completare il progetto senza dei prototipi fisici, quindi, l’azienda ha deciso di portare la stampa 3D in-house.
"Se non sai quale sia la forma migliore, creane una e testala"
Hirata non era soddisfatto di alcune vecchie stampanti a fabbricazione a fusione di filamento (FFF) che aveva usato in precedenza. Ma era al corrente del successo di Formlabs e ha deciso di investire in uno dei nostri apparecchi. WHILL ha introdotto la prima stampante Formlabs nel 2016. Da allora è stata usata per vari progetti e con il suo aiuto il team ha ottenuto esattamente ciò di cui aveva bisogno: prototipi di alta qualità in tempi rapidi. I prototipi delle parti che entrano in contatto diretto con gli utenti sono i più importanti. Per questi prototipi, le stampe devono risultare realistiche alla vista e al tatto e non possono essere di qualità scadente. La stampante SLA Formlabs ha fornito a Hirata esattamente quello di cui aveva bisogno per i prototipi per uso finale: parti di alta qualità ricche di dettagli, ma a prezzi contenuti.
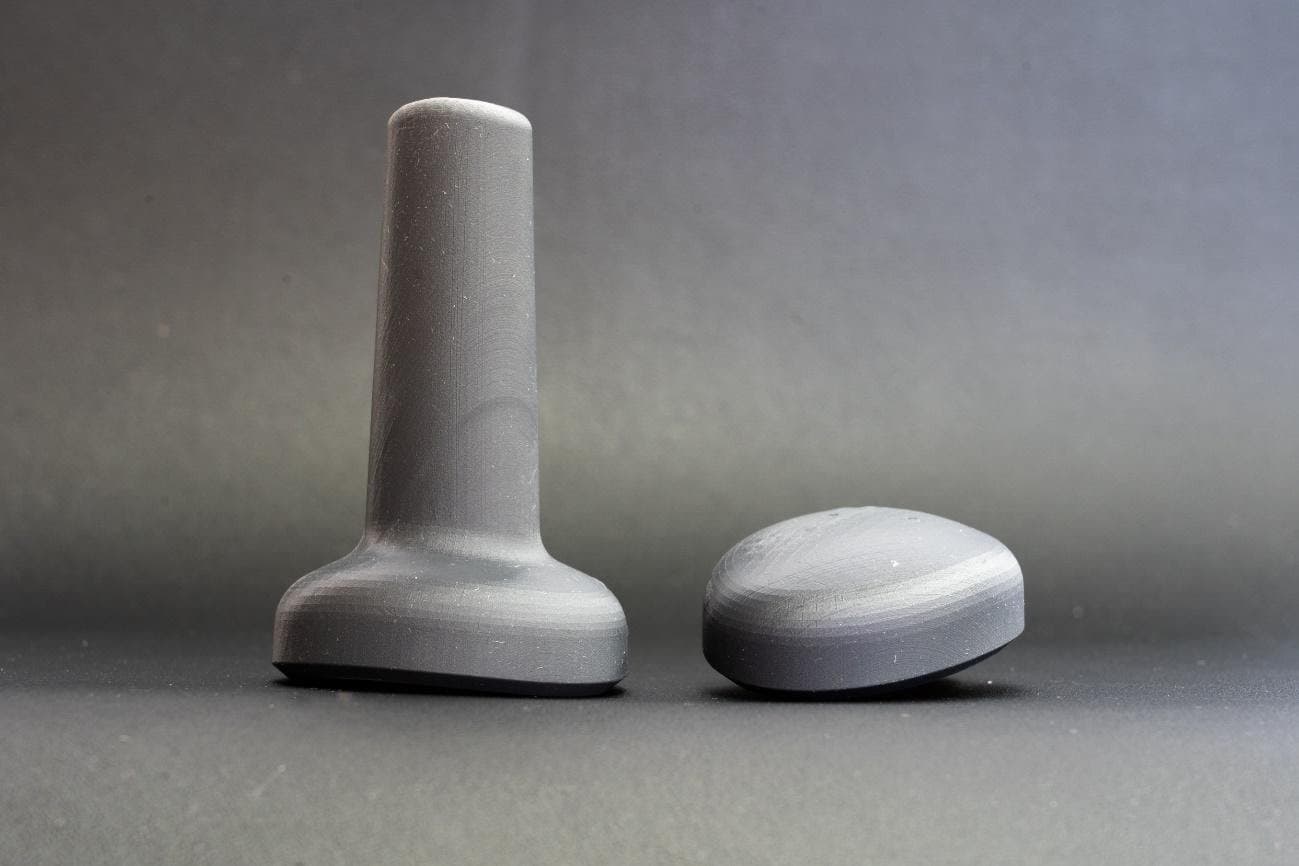
L’introduzione di una stampante 3D ad alta definizione all’interno del team di sviluppo di WHILL è stata fondamentale per arrivare al prodotto finale. Quando si effettuano delle valutazioni che includono le sensazioni tattili, le verifiche non hanno senso se la qualità delle parti non è simile a quella che si ottiene tramite la produzione in serie per uso finale. WHILL ha trovato nelle parti Formlabs dei sostituti quasi perfetti che consentono test sia interni che con gli utenti sui prototipi delle sedie a rotelle.
"Ci impegniamo a creare più prototipi possibili delle parti che gli utenti toccano, come i regolatori, e a testarli. Se esternalizzassimo la produzione di prototipi, come avveniva in passato, il numero di parti prodotte e le opportunità di studio risulterebbero limitate da vincoli di tempo e budget. L’uso della Flexible Resin con la Form 2 offre una sensazione tattile simile a quella dei prodotti di massa veri e propri. In questo modo possiamo modellare e sottoporre a verifiche prototipi ad alta precisione senza preoccuparci troppo dei numeri."
Yasuhiro Hirata
Il team ha usato varie resine su un singolo progetto, dimostrando la versatilità di una singola stampante Formlabs. La Flexible Resin era ideale per le parti che richiedono sensazioni tattili, la Clear Resin è stata usata per le parti semitrasparenti intorno al display della sedia a rotelle, mentre la Tough Resin per le parti che dovevano essere sottoposte ad ulteriori test di resistenza. Avere un apparecchio capace di stampare con successo più parti in materiali diversi in base all’uso specifico è un enorme risparmio di tempo e costi per una startup di hardware.
“La Form 2 non solo è precisa, ma si guasta raramente. Questo ci ha permesso di creare ogni giorno prototipi in più varianti e di portare a termine diverse verifiche per contribuire al miglioramento della qualità.” (Hirata)
Yasuhiro Hirata
Realizzare prototipi non significa solo perfezionare una singola parte. Testando diversi design, si possono ottimizzare e combinare più parti per consolidare l’assemblaggio. WHILL è riuscita a ridurre i costi di produzione finale della sua sedia a rotelle diminuendo il numero totale delle parti che compongono il prodotto. Si è trattato di un importante passo avanti per il team, reso possibile dalla stampa 3D in-house e da un processo di design generativo delle parti complesse.
Design generativo
Il design generativo è un processo che usa algoritmi per creare centinaia o, a volte, migliaia di design ottimizzati, tenendo conto di specifiche quali obiettivi del progetto, funzioni, condizioni dello spazio, materiali, metodi di produzione e vincoli di costo.
Il team di WHILL voleva creare un’unica parte compatta per il centro della sedia a rotelle. Usando il design generativo il team è riuscito ad analizzare più design in una volta. Il problema dei design complessi fuoriserie sono i costi elevati e l’impossibilità di realizzarli con i workflow tradizionali.
"Se tralasci il costo, usare un materiale leggero come la fibra di carbonio può essere un’opzione, ma non è un’opzione realistica. Mentre pensavamo a come ridurre il peso usando un materiale dai costi accettabili, ci è venuto in mente di provare il design generativo. Avevamo bisogno di creare prototipi dalle forme complesse in meno tempo e potevamo farlo solo grazie alle stampanti 3D e alle resine Formlabs."
Yasuhiro Hirata
La nuova parte complessa è stata prima stampata in-house usando la Castable Wax Resin di Formlabs. Il team ha usato Autodesk Fusion 360 per creare la parte centrale della sedia a rotelle, poi ha prototipato in-house la parte progettata con il metodo generativo, lasciando tutti a bocca aperta. Il risultato finale: WHILL è riuscita ad alleggerire il telaio della sedia a rotelle di più del 40%.
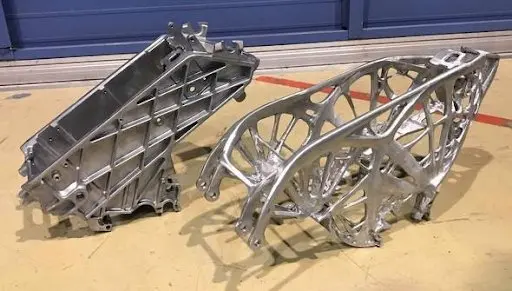
Realizzare prototipi in-house con Formlabs
WHILL è una delle molte aziende che sono riuscite a creare prodotti incredibili grazie alla prototipazione rapida in-house. Scarica il nostro e-book gratuito sulla prototipazione rapida per conoscere altre sei aziende che hanno rivoluzionato la loro attività con l’acquisto di una stampante Formlabs.