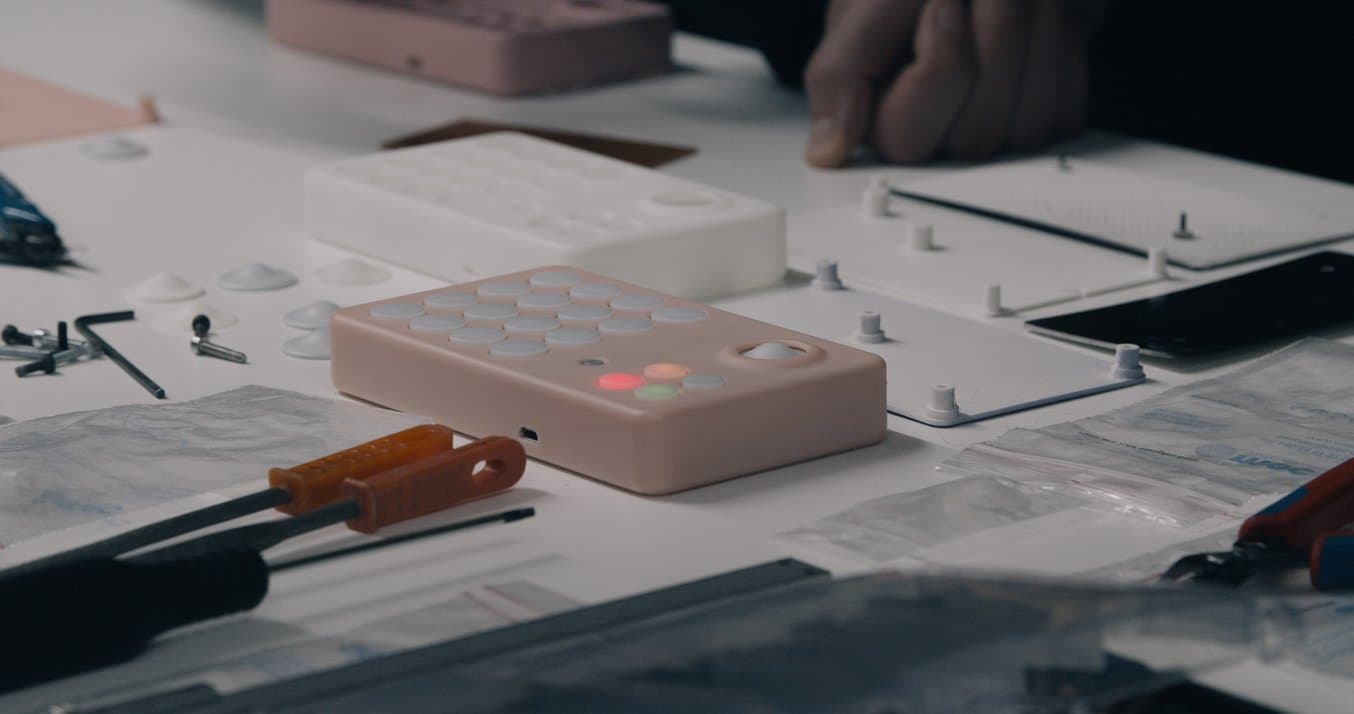
Produttore, direttore creativo e regista di professione, Michael Beim mirava a ispirare gli altri e a far sì che potessero esprimere le loro passioni e condividere il loro punto di vista con il mondo.
Nel 2012 fonda l'etichetta discografica birdkids, che presto imbocca un'altra strada dedicandosi all'hardware e affermandosi nella produzione di nicchia di sintetizzatori modulari di alta qualità. I primi prodotti sono acclamati dalla critica e ad oggi la piccola azienda vanta una clientela che include alcuni dei più grandi nomi della musica elettronica, del cinema e della TV.
L'ultimo progetto del team, °Grid, un controller aptico portatile e wireless, è un'evoluzione naturale della linea di prodotti dell'azienda, che punta a favorire l'uso agevole delle applicazioni creative in movimento. Passare da prodotti artigianali a dispositivi compatti che possono essere fabbricati in volumi maggiori da partner esterni, però, ha posto nuove sfide per il team durante il processo di sviluppo del prodotto.
Continua a leggere per scoprire come Beim e il suo team di cinque persone hanno sviluppato °Grid usando la stampa 3D con un ampio ventaglio di materiali, incluso il Color Kit, per creare il prototipo della gamma di colori del nuovo prodotto.
Testare decine di iterazioni con materiali diversi
Con °Grid, Beim e il suo team volevano creare un dispositivo estremamente mobile e compatto che gli utenti potessero maneggiare con facilità. Inizialmente hanno cominciato a creare prototipi con delle stampanti 3D FDM, ma ben presto sono incappati in alcune limitazioni, soprattutto in quanto a qualità e disponibilità di materiali specifici.
"Volevamo dei prototipi non solo per noi, ma che potessero anche essere mostrati ad altri e distribuiti a tester alfa e beta, produttori, artisti e musicisti fin dalle prime fasi di lavorazione. Dovevano avere l'impressione di usare il prodotto effettivo, quasi definitivo. La finitura superficiale liscia e la stabilità dei materiali in resina con cui stavamo creando i prototipi erano sicuramente dei vantaggi in più" ricorda Beim.
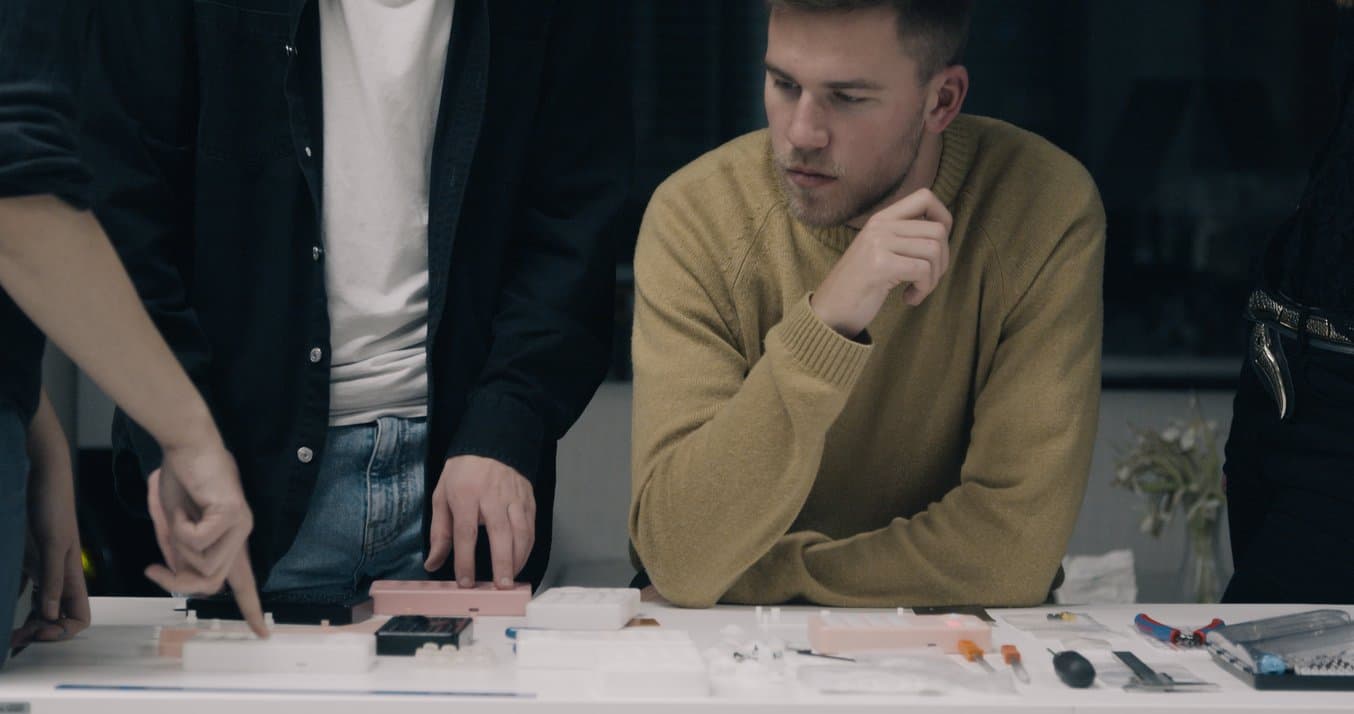
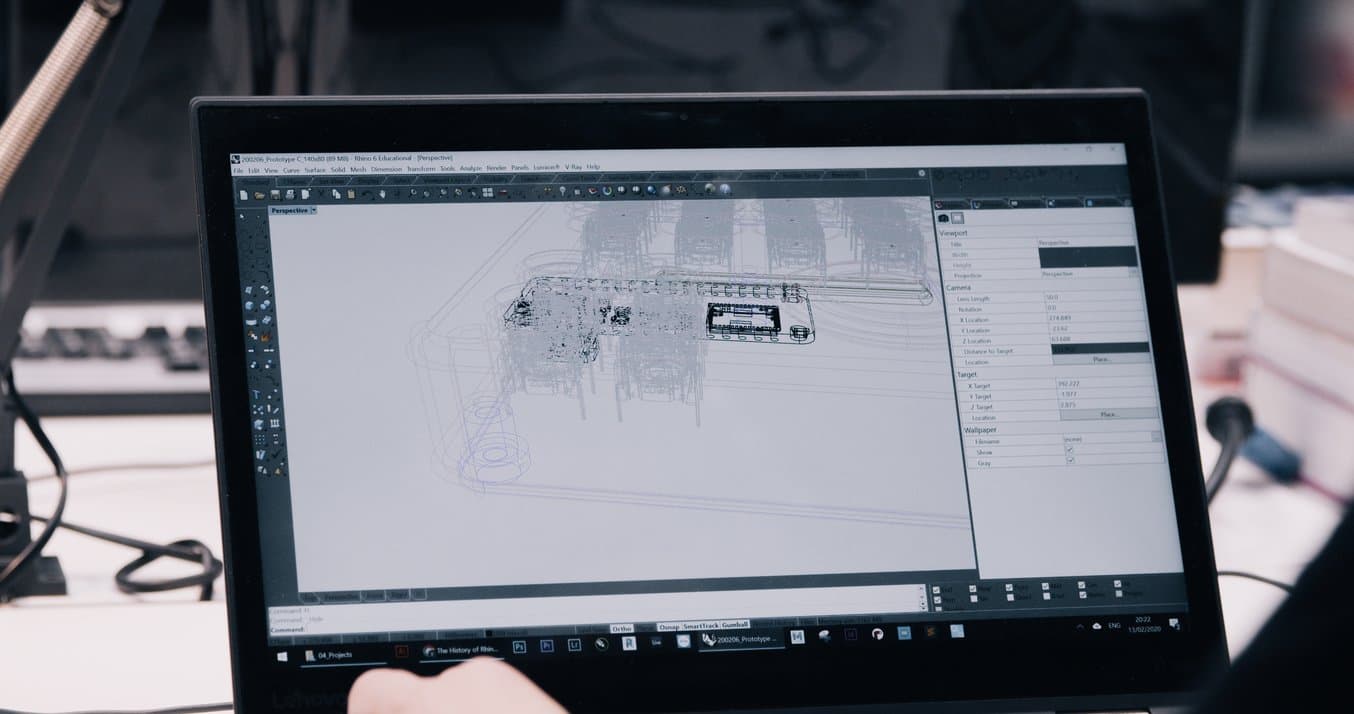
Il team di birdkids ha testato dalle 30 alle 50 diverse iterazioni della scocca esterna, rifinendone l'aspetto e gli elementi funzionali all'interno man mano che il circuito stampato, i sensori e altre componenti elettroniche si evolvevano.
La prima volta che hanno provato a stampare un prototipo con la stampante 3D SLA di Formlabs di un amico sono rimasti affascinati dall'altissima qualità delle parti. "Ci siamo detti: 'Sono quasi identiche al prodotto finale che vogliamo ottenere'. Ci siamo resi conto che utilizzare una stampante 3D e le resine di Formlabs avrebbe portato grandissimi benefici al momento del lancio sul mercato" spiega Beim.
Il team di birdkids ha quindi creato tra le 30 e le 50 iterazioni diverse della scocca esterna, rifinendone l'aspetto e gli elementi funzionali all'interno man mano che il circuito stampato, i sensori e altre componenti elettroniche si evolvevano. Hanno testato i prototipi internamente e ciascuna revisione principale è inoltre passata per le mani dei tester.
"La Rigid Resin è il primo materiale di riferimento che ci ha lasciato a bocca aperta. La qualità lattiginosa e la finitura superficiale liscia erano proprio quello che faceva al caso nostro: già le prime stampe superavano di gran lunga le nostre aspettative" racconta Beim.
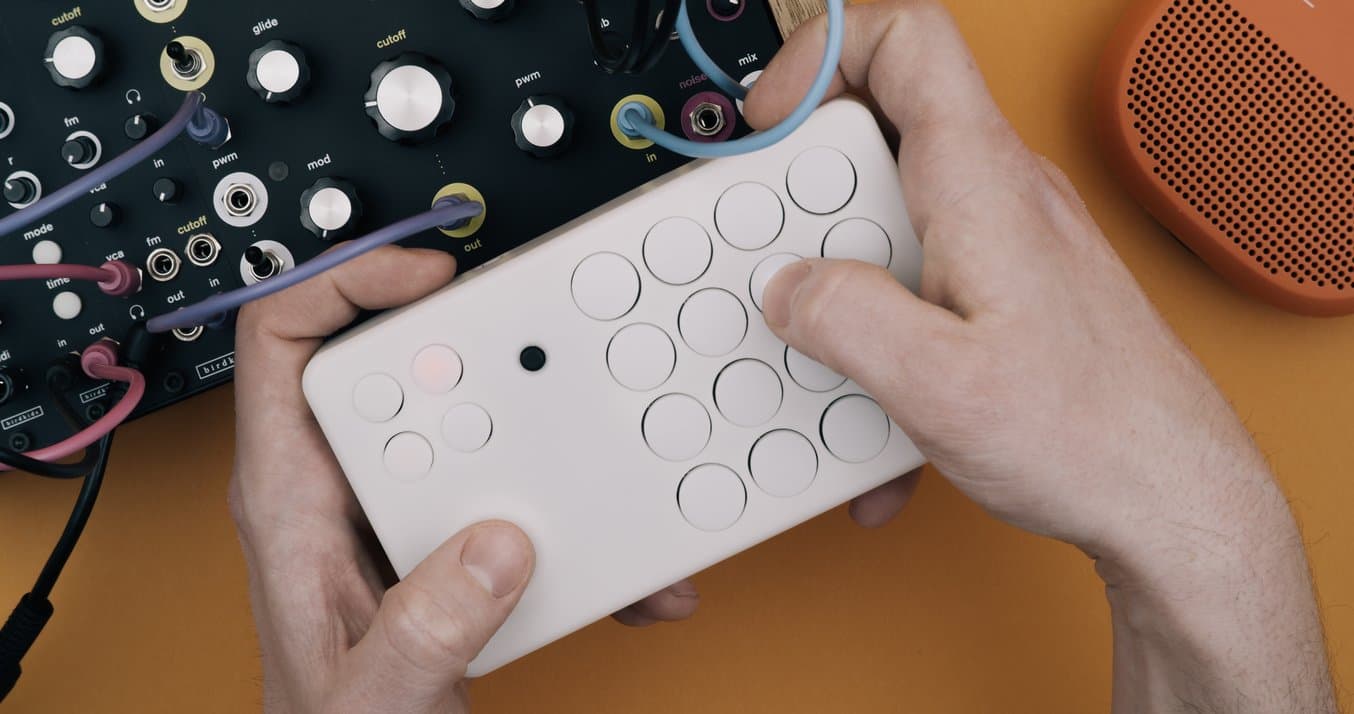
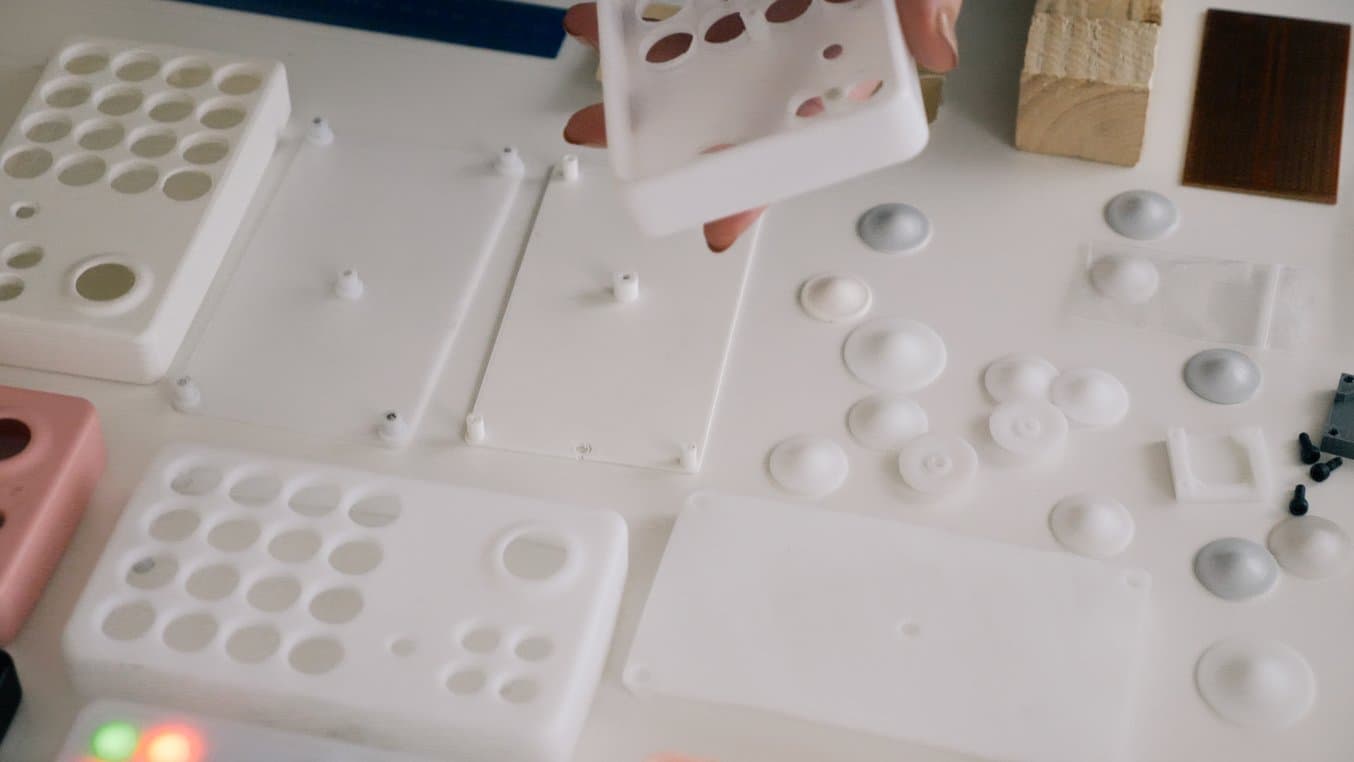
Grazie alla qualità "lattiginosa" e alla finitura superficiale liscia, la Rigid Resin era uno dei materiali preferiti dal team. Rinforzata con vetro per assicurare un'elevata rigidità e un'alta resistenza alle deformazioni nel tempo, la Rigid Resin è una scelta eccellente per la stampa di pareti e finiture sottili.
Il team ha usato anche la Draft Resin, la più veloce resina SLA di Formlabs per iterazioni rapide. "Grazie alla Draft Resin siamo riusciti a testare posizioni complesse nella scocca esterna, svolgere test di resistenza alle sollecitazioni, effettuare alcune calibrazioni meccaniche e regolare lo spessore delle pareti, dove non conta molto l'aspetto, quanto piuttosto la sensazione che dà quando si sta utilizza il prodotto" ricorda Beim.
Beim ha affermato che senza la possibilità di utilizzare in-house una stampante 3D di Formlabs sarebbero dipesi in larga misura da servizi esterni per ottenere una finitura della scocca esterna della qualità desiderata. Stima di aver impiegato meno di un giorno per completare ciascun prototipo invece di cinque giorni lavorativi e di aver speso un quarto del prezzo che avrebbero pagato per l'esternalizzazione.
"Con una stampante 3D a base di resina siamo riusciti a ottenere dei risultati in meno di 24 ore. Il che è sorprendente, perché crei il modello, lo testi, premi il tasto di stampa e dopo un paio d'ore hai un prodotto che funziona" spiega Beim.
Prototipazione della gamma di colori con il Color Kit
Dopo aver risolto il design dell'involucro esterno, Beim e il suo team sono passati a sperimentare la gamma di colori per il dispositivo. Le stampe 3D SLA possono essere facilmente colorate con vernice spray, ma erano curiosi di vedere se era possibile utilizzare una soluzione che sembrasse più integrata nel materiale stesso. Ed è qui che è entrato in gioco il Color Kit di Formlabs, la prima soluzione integrata per la miscelazione di colori per la stampa 3D stereolitografica.
"È stato incredibile scoprire che c'è effettivamente la possibilità di approssimare opzioni di colore con il Color Kit. Nonostante le proprietà del materiale siano leggermente diverse [da quelle della Rigid Resin], è esattamente ciò di cui avevamo bisogno per poter posizionare le componenti meccaniche ed elettroniche all'interno dell'involucro esterno" racconta Beim.
Il team ha cercato di miscelare i colori che avevano in mente, ma anche di seguire i suggerimenti del libretto di istruzioni come punto di partenza.
"Nel caso del colore pesca, il punto di partenza era davvero vicino a quello che volevamo ottenere. Abbiamo pensato che forse potevamo enfatizzare alcune qualità, ad esempio un aspetto più neutro color carne, il colore giallo, o aumentare la saturazione. Siamo riusciti ad avvicinarci al risultato sperato semplicemente sperimentando con un po' più di [pigmento] rosso o aggiungendo del bianco alla miscela" ricorda Beim.
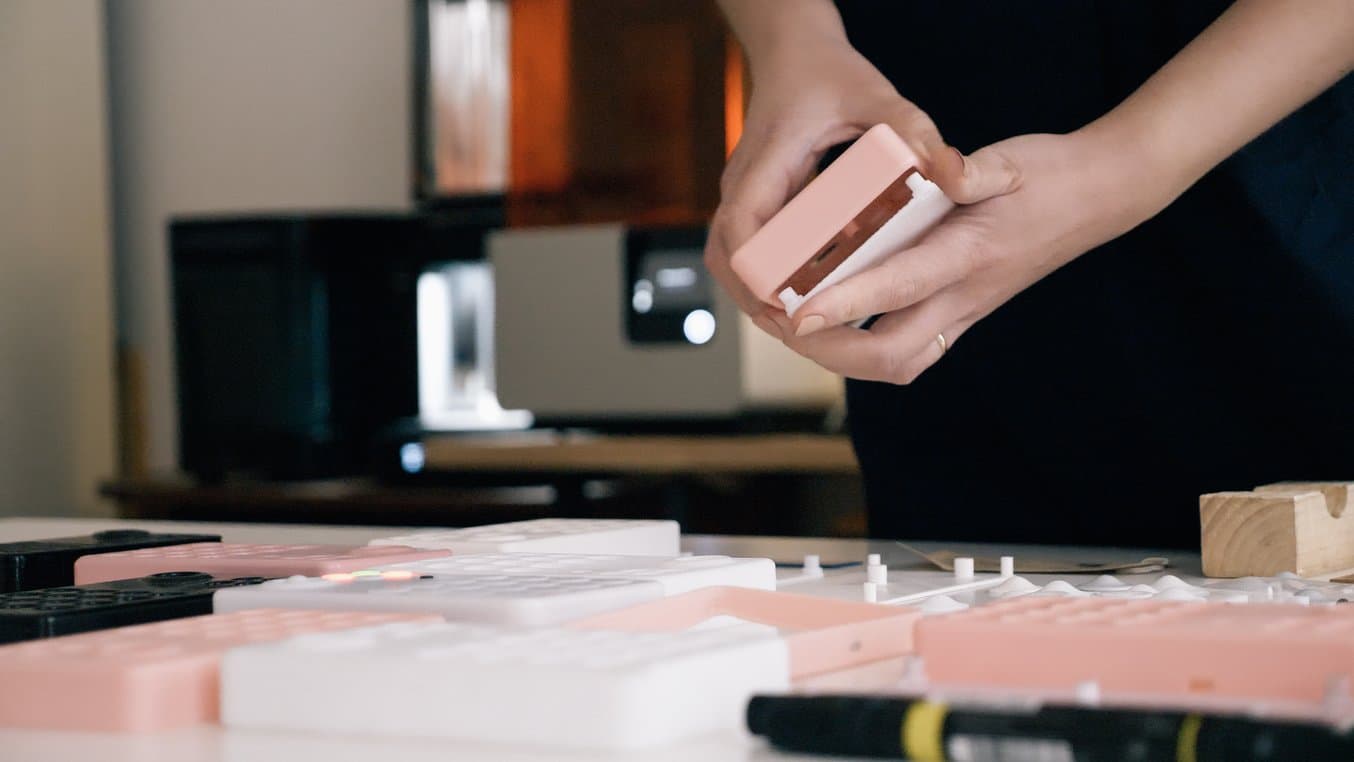
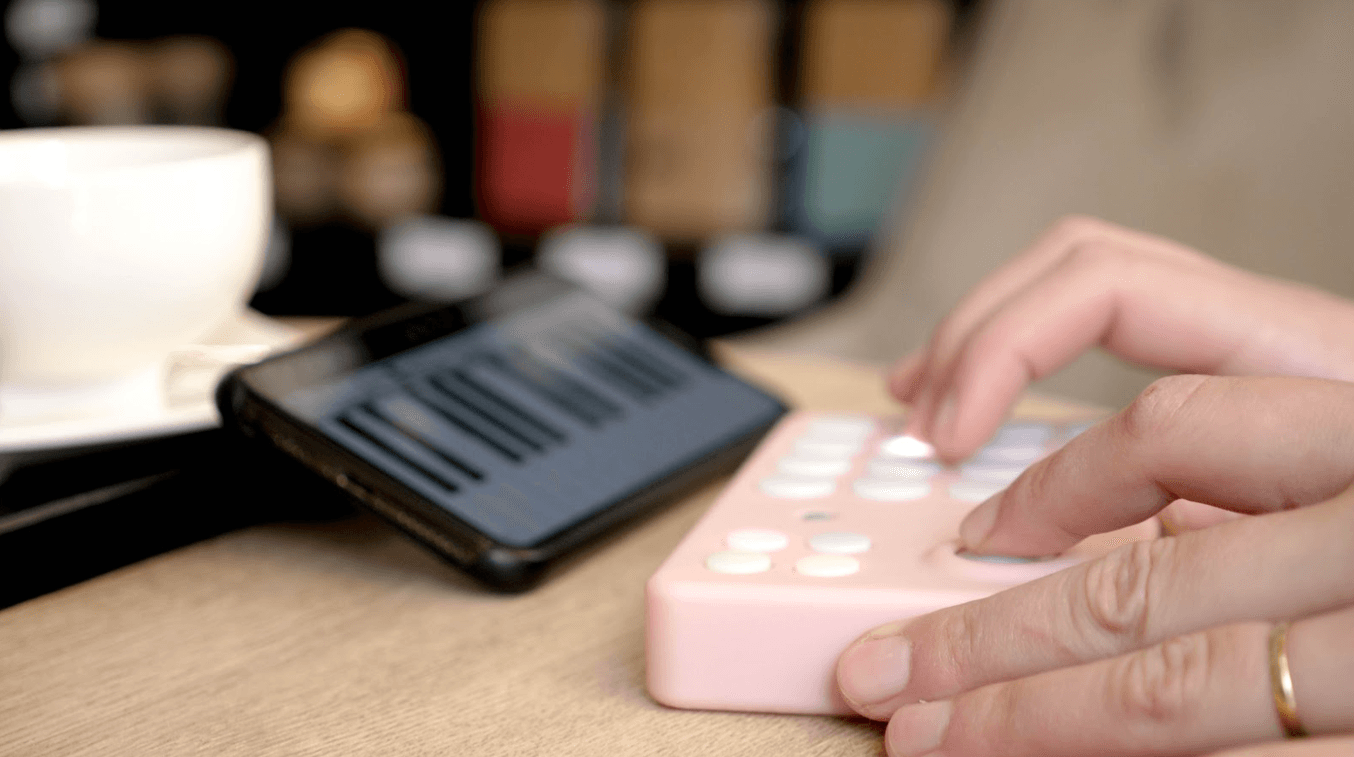
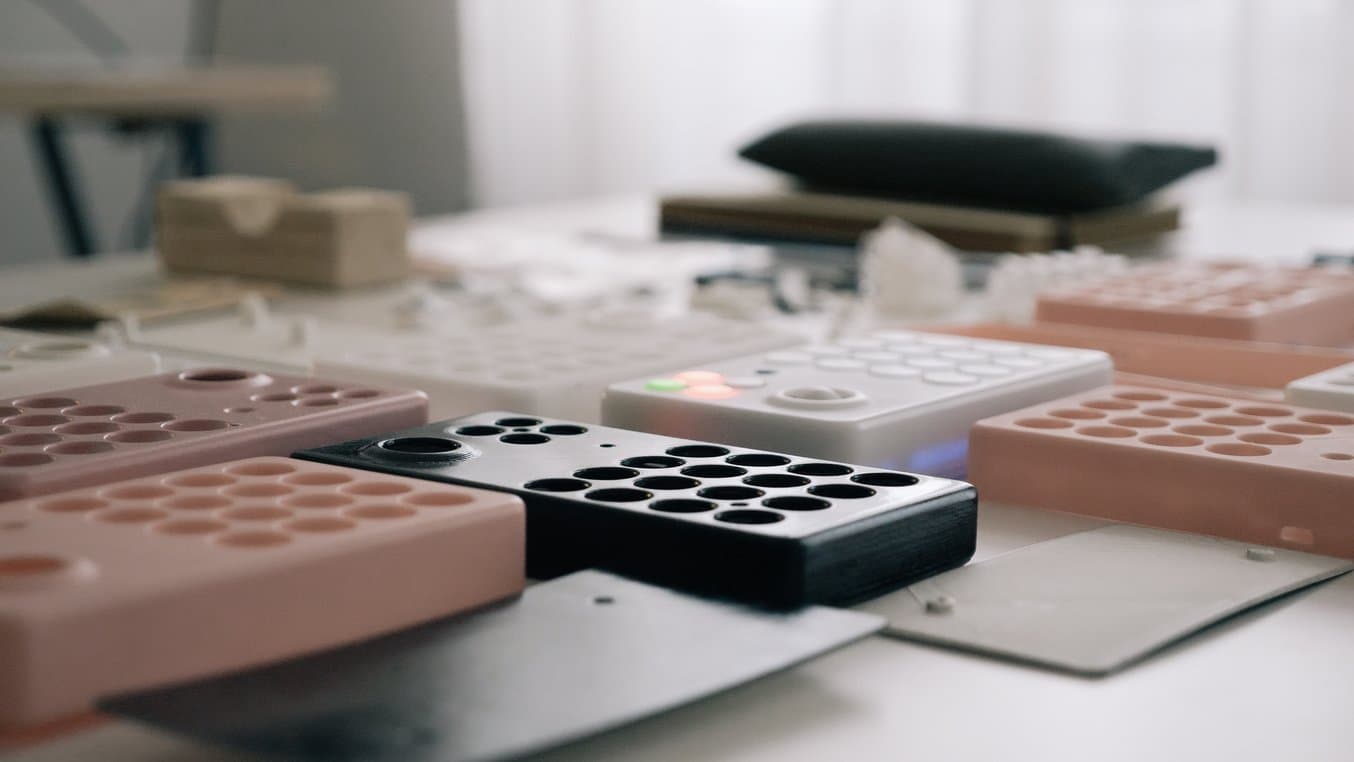
Beim e il suo team hanno utilizzato il Color Kit, la prima soluzione integrata per la miscelazione di colori per la stampa 3D SLA, per creare prototipi di diversi colori, come la varietà "pesca".
"Forse il risultato non sarà perfetto come quando si lavora con una gamma di colori Pantone, ma ci si può avvicinare molto. E non dimentichiamoci che le parti effettivamente stampate sono di una bellezza incredibile e in pratica hanno le stesse proprietà della parte finale" spiega Beim. "Sembra quasi ceramica, come se avessi tra le mani un pezzo di ceramica, del tutto liscio e colorato a meraviglia. Perciò non esiterei a darlo a un tester alfa e beta e dormirei sonni tranquilli, consapevole di avergli dato qualcosa di davvero molto simile a quello che vogliamo raggiungere."
Il team ha riscontrato una maggiore facilità d'uso degli strumenti rispetto a quanto pensato all'inizio. "È fantastico sulla carta ed è fantastico sul sito Internet, ma quando ti rendi davvero conto di quanto sia facile gestire la stampante, Form Wash e Form Cure, e anche colorare e miscelare la resina... All'inizio sembra un'operazione scientifica complessa, ma in realtà è estremamente semplice, ed è proprio facile raggiungere ottimi risultati" commenta Beim.
Passare alla produzione
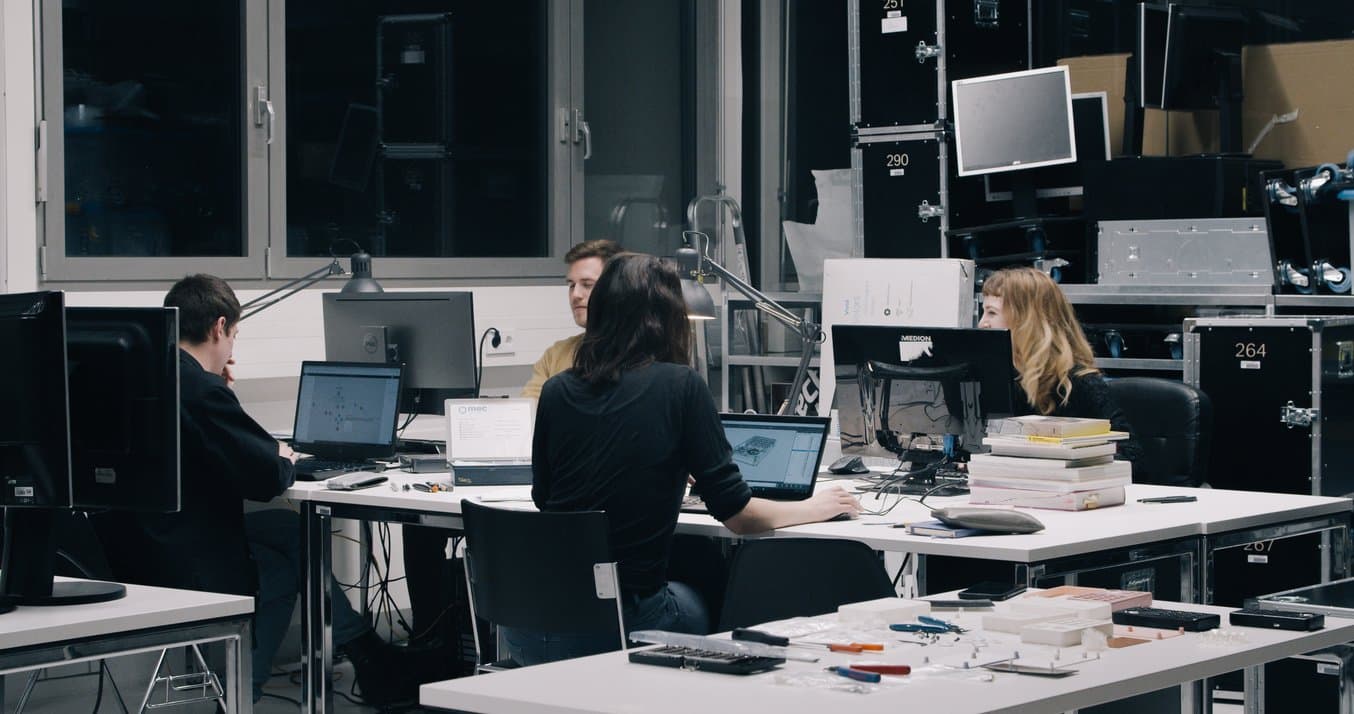
Con sede a Vienna, in Austria, il team di birdkids è composto da cinque persone. Due ingegneri, uno sviluppatore di software e due cofondatori che sono anche responsabili della progettazione.
Con °Grid ormai pronto per essere presentato al pubblico, birdkids ha lanciato una campagna di crowdfunding per suscitare interesse e raccogliere fondi per finanziare il passaggio alla fase di produzione. Durante la primavera e l'estate, il team continuerà a sviluppare il software e a ottenere i certificati richiesti per vendere il dispositivo in tutto il mondo.
Sebbene la forma e la funzionalità finale siano ormai ben definite, il team continuerà inevitabilmente a creare prototipi fino a quando non saranno prese le ultime decisioni riguardo all'esternalizzazione e non saranno fissate le componenti finali. L'obiettivo di Beim è trovare partner che possano produrre °Grid con il minor impatto ambientale possibile, dall'utilizzo di plastica biodegradabile per la scocca esterna a quello di un imballaggio riciclabile.
Durante la sperimentazione dei diversi design e materiali, Beim e il suo team si sono affidati spesso al team di Assistenza Formlabs per ottimizzare il loro flusso di lavoro per la prototipazione. "L'intero team del servizio clienti è sempre in prima linea per aiutarci nel minor tempo possibile, qualunque sia la nostra richiesta" afferma Beim. "Avere delle persone disposte a sostenerti quando cerchi di migliorarti in ciò che fai credo sia qualcosa di ancora più importante dei vantaggi tecnici del prodotto."