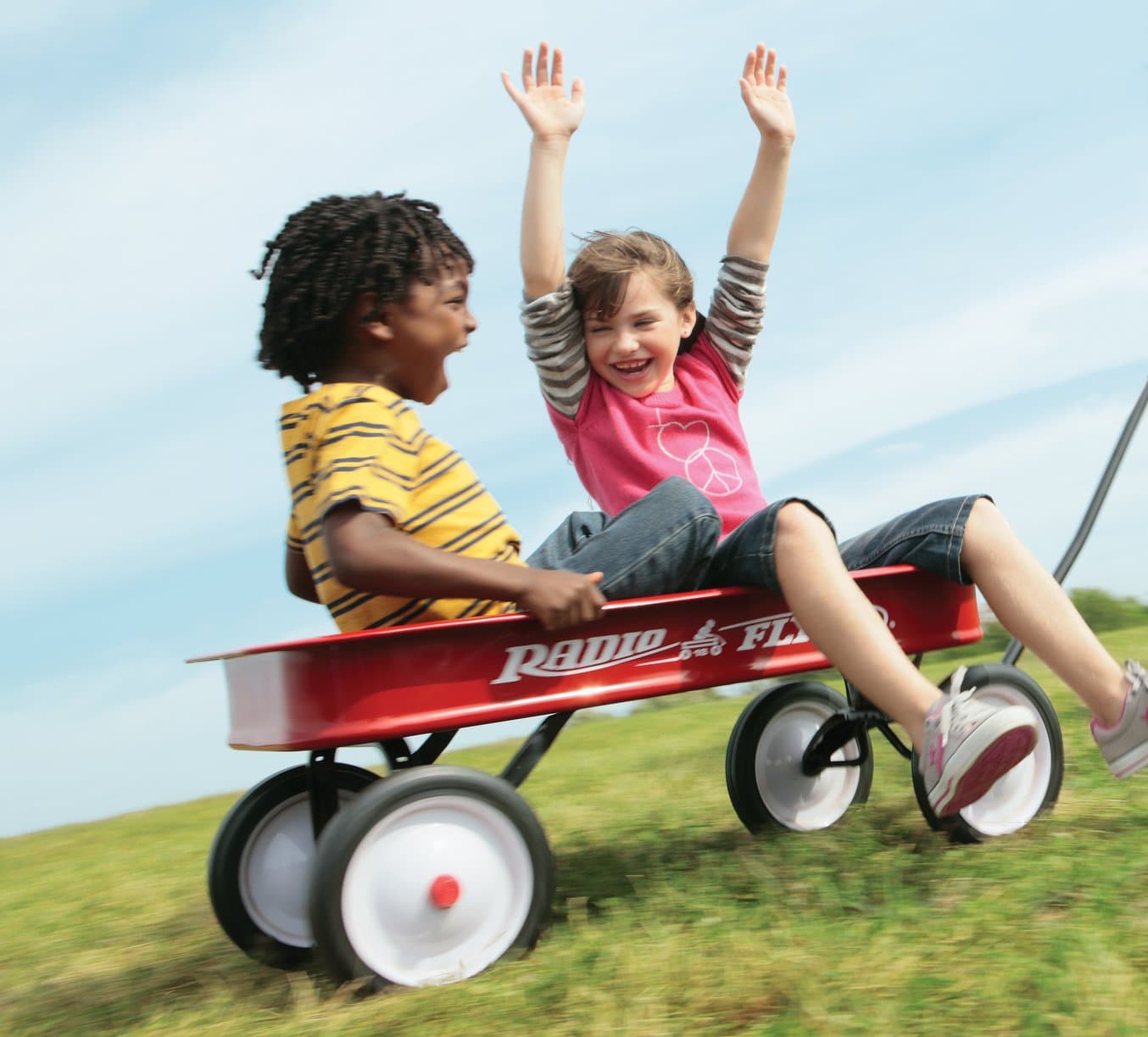
Sebbene il prodotto più famoso di Radio Flyer, lo storico carrettino Original Little Red Wagon®, potrebbe trasmettere un senso di tradizionalismo che guarda agli Stati Uniti di metà '900, l'azienda di Chicago non è affatto rimasta ancorata al passato. Restare leader del settore per oltre un secolo richiede idee innovative e un interesse costante per le nuove tecnologie. La stampa 3D rappresenta uno dei principali strumenti con cui l'azienda continua a produrre i suoi cavalcabili conosciuti in tutto il mondo, tra cui carrettini, monopattini, tricicli, go-kart, biciclette elettriche e molti altri.
Il team di sviluppo del prodotto di Radio Flyer si dedica alla stampa 3D tutto il giorno, tutti i giorni. L'officina di prototipazione dell'azienda utilizza sia le stampanti 3D a sinterizzazione laser selettiva (SLS) della serie Fuse sia quelle stereolitografiche (SLA) di grande formato di Formlabs, con le quali aiuta il team a rispettare le scadenze e realizzare prodotti in grado di portare sorrisi e creare ricordi che durano tutta la vita.
Abbiamo parlato con Agostino LoBello, ingegnere specializzato nel design di prodotto presso Radio Flyer, che offre supporto nella valutazione e integrazione di nuove tecnologie per l'officina. La nuova stampante 3D a resina di grande formato Form 4L ha ridotto i tempi di produzione di parti ad alta fedeltà da mostrare ai rivenditori per l'approvazione e ha aumentato il rendimento giornaliero di prototipi in scala reale. La Form 4L, combinata con la produzione ininterrotta di prototipi funzionali sulle stampanti della serie Fuse, consente all'officina di produrre centinaia di parti ogni mese.
"Non appena abbiamo introdotto la Form 4L, la prima cosa che abbiamo stampato in 3D è stato un sedile per il nostro quadriciclo Stingray, che abbiamo poi mostrato durante un incontro con i fornitori. La velocità di stampa e l'accuratezza dimensionale hanno fatto un grande differenza in officina. Oggi riusciamo a stampare senza problemi una scatola delle dimensioni dell'intero volume di stampa. Quando provavamo a farlo con la Form 3L, la struttura e il coperchio della scatola non si allineavano. Prima della Form 4L, avremmo optato per la lavorazione meccanica con una fresatrice o l'avremmo assemblata a partire dalla stampa SLS."
Agostino LoBello, ingegnere specializzato nel design di prodotto presso Radio Flyer
Resistenza e funzionalità della serie Fuse per i test con le famiglie
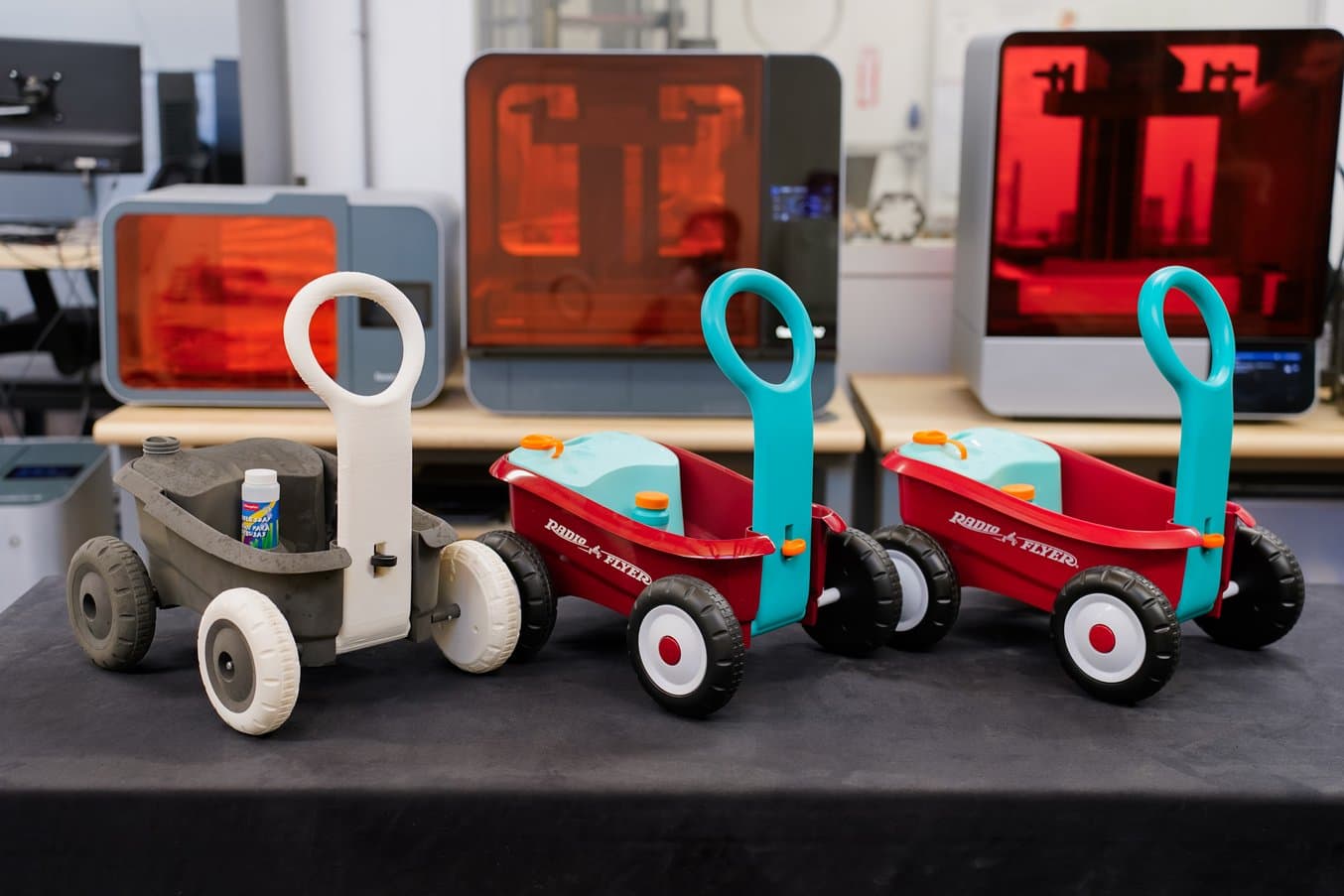
A sinistra, prototipo originale stampato tramite sinterizzazione laser selettiva; al centro, prototipo da roadshow stampato in 3D tramite stereolitografia e verniciato; a destra, il Bubble Buddy Walker Wagon® finale.
L'affetto che si prova verso un giocattolo può portare a usarlo per anni, passando di generazione in generazione. Radio Flyer si impegna a creare prodotti della massima qualità e sicurezza in grado di durare nel tempo.
Il segreto della loro longevità risiede nell'intensivo processo di prototipazione a cui viene sottoposto ogni componente. Dall'introduzione della prima Fuse 1 nel 2022 e della Fuse 1+ 30W nel 2023, l'officina di prototipazione di Radio Flyer è stata in grado di produrre rapidamente molte parti in Nylon 12 Powder per i team di ingegneria e progettazione, tra cui prototipi funzionali di sedili, cuscinetti a sfera, manopole per manubri e altro ancora.
"È l'unica stampante di cui ci fidiamo per la produzione di un nuovo carrettino o triciclo. La usiamo per realizzare capsule funzionali per le rotelle, assemblaggi di ruote, freni e molto altro. Le parti stampate con la serie Fuse rispondono alla nostra esigenza di parti funzionali per utilizzo finale che possano essere testate dalle famiglie con la massima tranquillità."
Agostino LoBello, ingegnere specializzato nel design di prodotto presso Radio Flyer
Le famiglie sono tra i clienti più esigenti, e quando si tratta di garantire la sicurezza dei bambini, la resistenza è la priorità assoluta. Realizzare le parti sugli apparecchi della serie Fuse consente di superare le prime fasi di prototipazione più rapidamente e condurre diversi cicli di test senza necessità di stampare nuove parti.
Accuratezza dimensionale affidabile
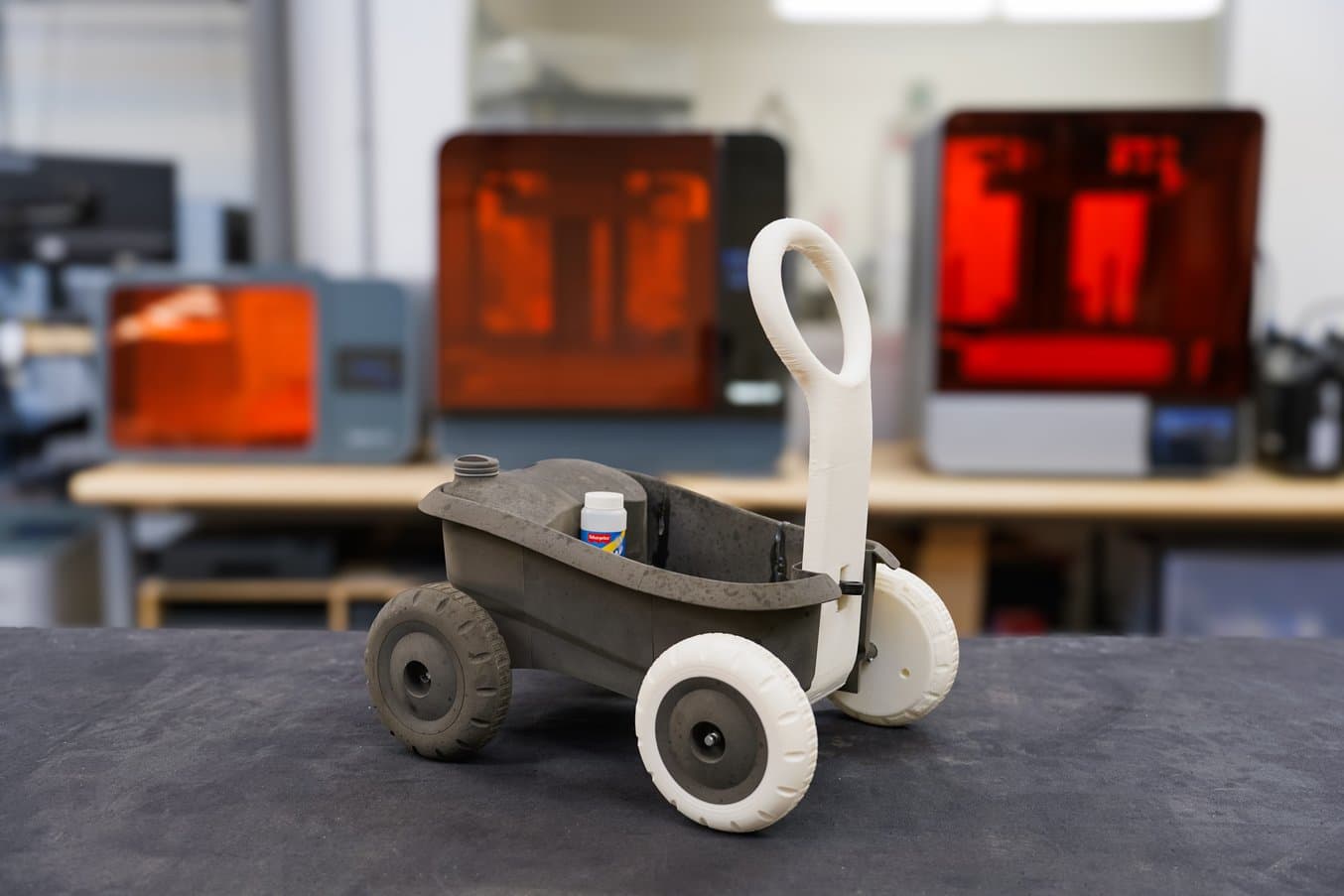
Il prototipo del carrettino Bubble Buddy Walker Wagon® è stato realizzato in Nylon 12 Powder sulla stampante 3D SLS Fuse 1+ 30W di Radio Flyer. Nell'immagine, è mostrato come assemblaggio in più parti.
Pur essendo di dimensioni adatte ai bambini, i prodotti di Radio Flyer sono comunque più grandi del volume di stampa di una normale stampante 3D, incluse quelle della serie Fuse. Per poter entrare nel volume di stampa, i prototipi vengono quindi divisi in più parti e successivamente assemblati. Il letto di stampa autoportante delle stampanti 3D SLS consente di nidificare le parti in un'unica camera di stampa. In questo modo, nel caso dei progetti che prevedono l'assemblaggio dopo la stampa, è possibile ottenere tutte le parti in una sola volta senza che quelle di grandi dimensioni rallentino il processo di iterazione.
"Quando dobbiamo separare le parti di grandi dimensioni per poterle inserire nella camera di stampa, devono sempre combaciare tra loro una volta stampate. Questo è un ulteriore vantaggio che offre la serie Fuse: anche se stampiamo in momenti diversi, l'apparecchio mantiene la stessa accuratezza dimensionale. Le parti stampate si combinano sempre alla perfezione", afferma LoBello.
Le stampanti della serie Fuse hanno fornito parti sempre accurate, il che ha portato i team di progettazione e ingegneria a fidarsi sempre di più di questa tecnologia. In passato avevano utilizzato una stampante 3D FDM, ma grazie alla Fuse hanno potuto ottenere un livello di fedeltà superiore e imparare di più dalle parti senza tener conto dei supporti o delle geometrie anisotropiche prima di passare alla creazione delle attrezzature.
"Il team studia le parti stampate con gli apparecchi Fuse allo stesso modo di quelle realizzate tramite stampaggio a iniezione. Confidiamo sempre nel fatto che otterremo le parti funzionali per utilizzo finale richieste, così come da progetto inviato alla stampante."
Agostino LoBello, ingegnere specializzato nel design di prodotto presso Radio Flyer
Velocità e rendimento con la stampa 3D SLS
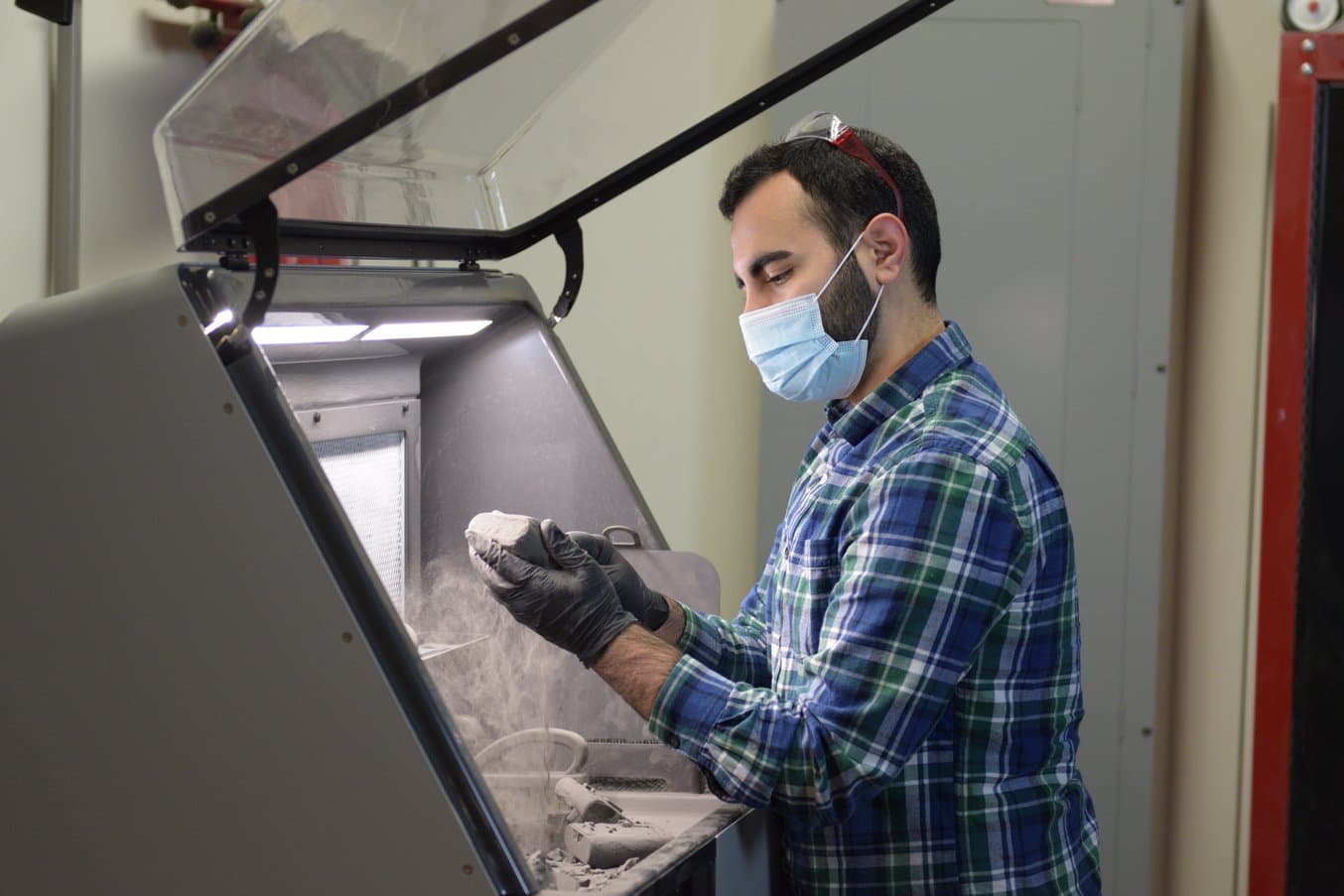
Durante l'estate, il periodo di attività più intenso dell'anno, le due stampanti della serie Fuse di Radio Flyer funzionano senza sosta, spesso superando i 20 kg di Nylon 12 Powder consumata al mese.
Ogni categoria di prodotto dell'azienda, come carrettini, biciclette elettriche o monopattini, include diversi articoli e componenti, di conseguenza vengono costantemente avviati nuovi progetti di sviluppo. Le parti SLS vengono utilizzate a ciascuna fase del processo, dai primi Proof-of-Concept ai modelli finali che vengono inviati a potenziali acquirenti e partner. Lo stampaggio a iniezione non avrebbe senso prima di un completo consolidamento degli ordini e delle quantità di parti da produrre. Per arrivare a quel punto in modo rapido e conveniente, Radio Flyer continua a sfruttare il costo per parte e il rendimento elevato offerti dalle stampanti della serie Fuse.
"Le stampanti della serie Fuse sono sempre in funzione ed eseguono una stampa al giorno, o anche due se i tempi lo consentono. Durante l'estate, che è il periodo di attività più intenso, eseguiamo più iterazioni di diversi concept ogni giorno, arrivando a consumare dai 20 ai 30 kg di polvere al mese", spiega LoBello.
L'introduzione delle capacità SLS ha cambiato alcune parti del workflow di Radio Flyer che prevedevano la FDM o l'esternalizzazione. La stampa SLS consente di spingersi più in là nel ciclo di sviluppo del prodotto prima di passare alla creazione delle attrezzature, in quanto le parti stampate con la serie Fuse replicano le prestazioni dei componenti stampati a iniezione. "La stampa SLS ha velocizzato il workflow. Non dobbiamo più ricorrere così tanto all'esternalizzazione, e a livello di ingegneria e sviluppo di prodotto sono necessari meno cicli di ottimizzazione e definizione dei parametri prima di inviare i design all'officina", afferma LoBello.
Miglioramenti introdotti dalla Form 4L
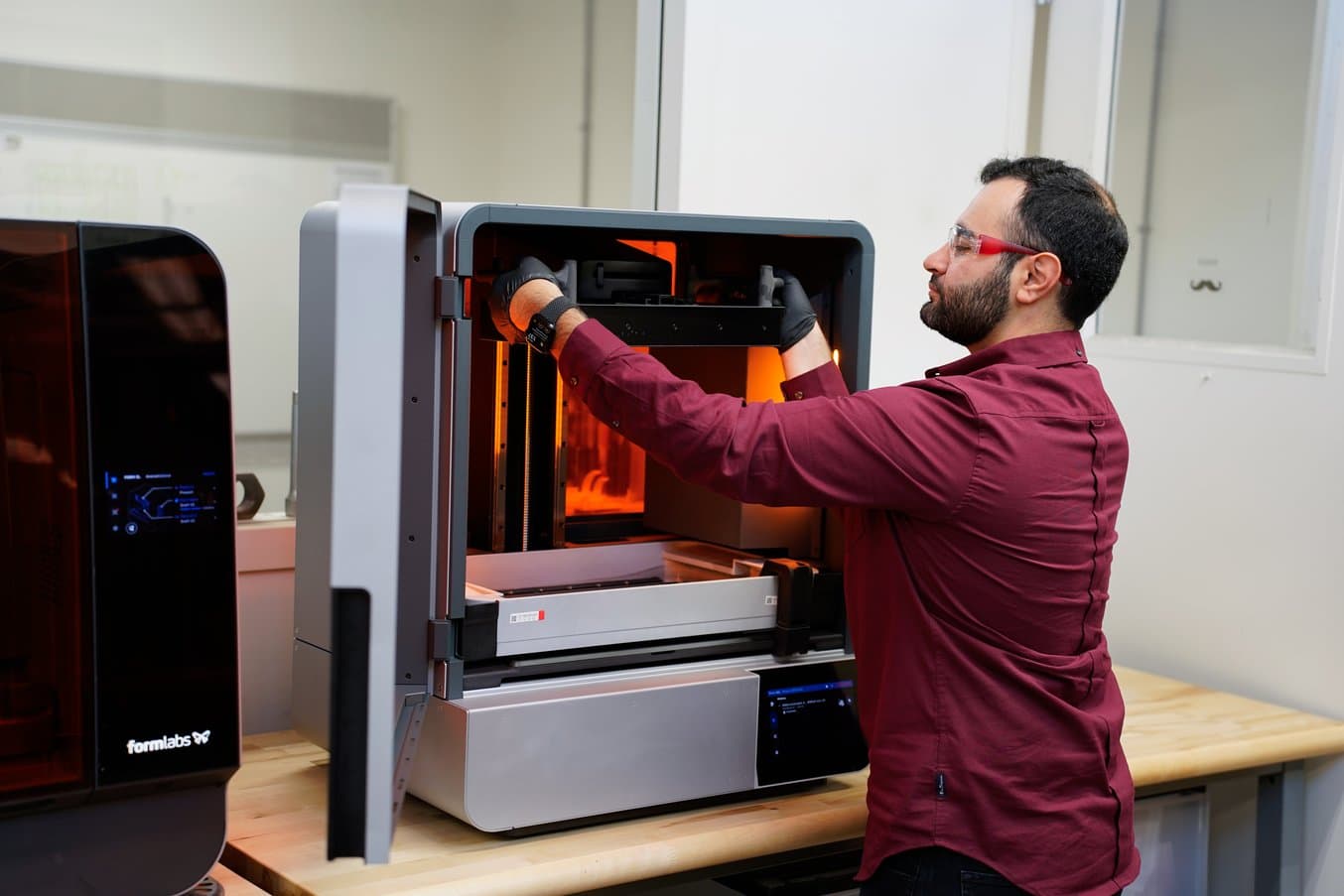
La Form 4L ha aiutato Radio Flyer a stampare rapidamente parti di grandi dimensioni e permesso ai team di progettazione e ingegneria di rispettare scadenze importanti con tranquillità, perché ha dato loro la certezza di poter realizzare tutte le iterazioni e i test richiesti delle loro idee.
Oggi, il workflow di sviluppo di Radio Flyer si basa sulla stampa 3D SLS. La sua precedente stampante 3D SLA di grande formato, la Form 3L, non riceveva molte richieste dal team, ma le cose hanno iniziato a cambiare con l'arrivo della Form 4L.
"Spesso ci servono tempi di produzione rapidi per le revisioni dei design. Le opzioni di grande formato precedenti non ci permettevano di ottenere le parti in breve tempo, ed è stato proprio sotto questo aspetto che la Form 4L ha dimostrato una netta superiorità. Grazie alla sua velocità, il nostro personale tecnico può eseguire più stampe al giorno", afferma LoBello.
I tempi di stampa più rapidi e il maggior numero di cicli di stampa al giorno hanno portato alla realizzazione di idee più definite e complete, oltre che a una comprensione più approfondita di come ciascun prodotto sia in grado di soddisfare un'esigenza specifica. "Dedichiamo molto tempo alla progettazione dei nostri prodotti e allo studio di tutti i loro possibili utilizzi. Ci chiediamo: 'Chi utilizzerà questo articolo? Cosa vi aggiungerebbe?'" spiega LoBello. La stampa 3D rapida e avanzata fornisce tutte le risposte a queste domande.
"Ora abbiamo la possibilità di creare i prototipi delle nostre idee in breve tempo, perché possiamo generare più versioni e testarle rapidamente con la Form 4L. In questo modo riusciamo a sviluppare i concept più a fondo e più velocemente. Inoltre, possiamo integrare nuove funzionalità nei prodotti, cosa che prima non avremmo potuto fare."
Agostino LoBello, ingegnere specializzato nel design di prodotto presso Radio Flyer
Accuratezza e affidabilità migliorate
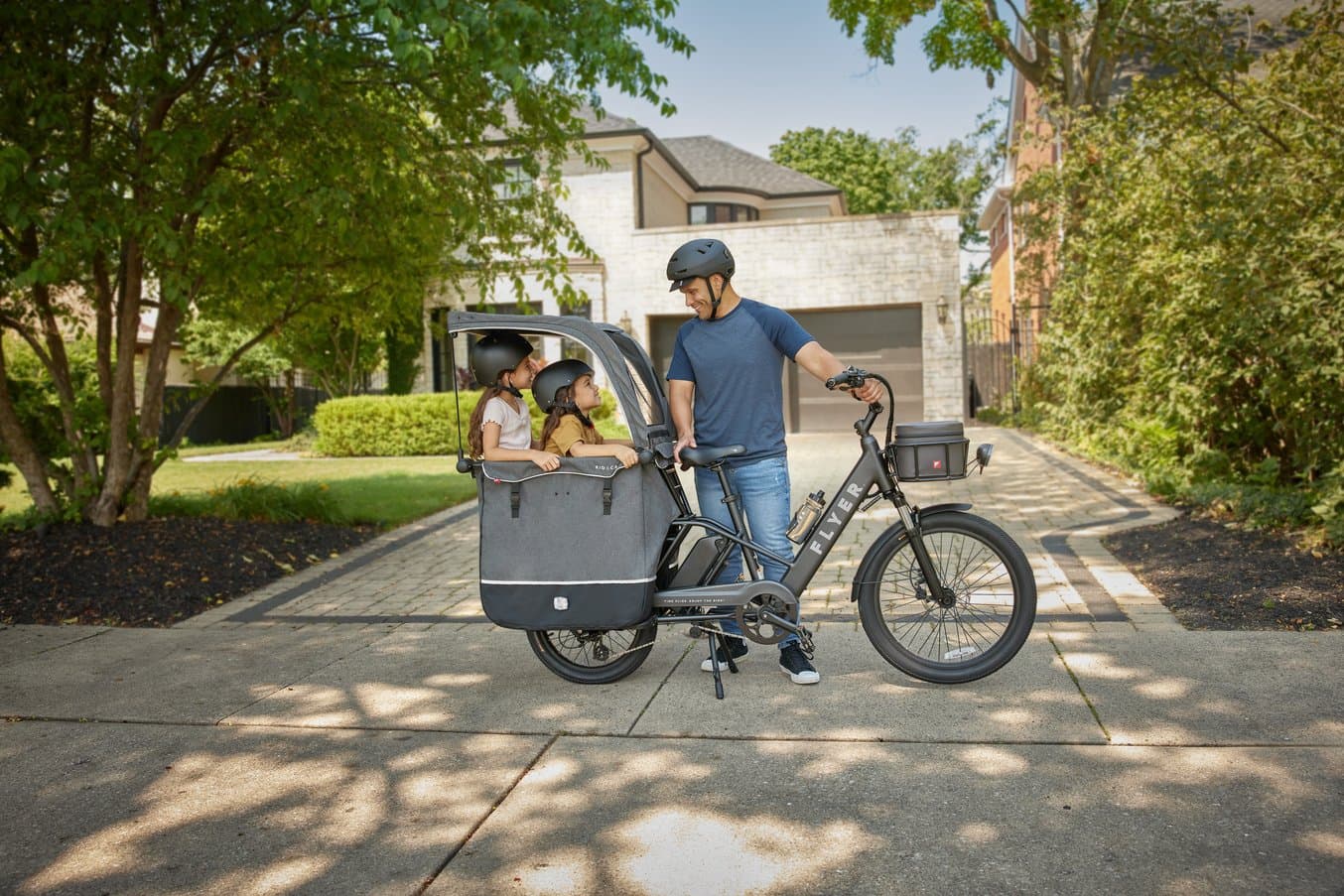
Prima che Radio Flyer portasse la Form 4L in-house, i nuovi prototipi di biciclette elettriche e relativi accessori venivano spesso inviati alle stampanti della serie Fuse. Ora, l'affidabilità comprovata e l'accuratezza dimensionale della Form 4L danno ai team la sicurezza che le parti risulteranno accurate e facili da sottoporre a post-elaborazione per ottenere i prototipi finali.
Prima dell'introduzione della Form 4L, il team dell'officina di prototipazione non riceveva molte richieste per la stampante SLA di grande formato a causa della mancanza di accuratezza dimensionale segnalata dai team di design di prodotto. "Quando assembliamo un prototipo, i diversi componenti devono fissarsi tra loro alla perfezione, altrimenti si genera confusione e non riusciamo a imparare quanto vorremmo dalle revisioni dei design", afferma LoBello.
Per decidere di richiedere una parte in-house anziché esternalizzare a un'officina specializzata in lavorazione meccanica CNC o a un costoso fornitore di servizi di stampa 3D industriale, il team di prodotto deve avere la piena certezza di ottenere il risultato richiesto e di poter risolvere eventuali problemi in breve tempo. "Questo è il grande vantaggio rispetto alla Form 3L. La Form 4L ci dà molta più sicurezza sul fatto che le parti funzioneranno per lo scopo previsto", spiega LoBello.
Ora che ha a disposizione la Form 4L, il team ha iniziato a ricevere sempre più richieste per parti SLA. In occasione dei roadshow, dove il team di sviluppo di prodotto e il team vendite incontrano acquirenti e hanno la possibilità di mostrare i nuovi prodotti e idee, sono necessarie parti con finiture superficiali pressoché identiche a quelle ottenute tramite stampaggio a iniezione.
"Le parti devono essere precise, perché le utilizziamo per mostrare ai futuri rivenditori cosa acquisteranno. Un occhio non allenato dovrebbe scambiarle per un prodotto finale; le parti realizzate con la Form 4L ci aiutano a dare questa impressione", afferma LoBello.
Test aggiuntivi per prodotti eleganti e intramontabili
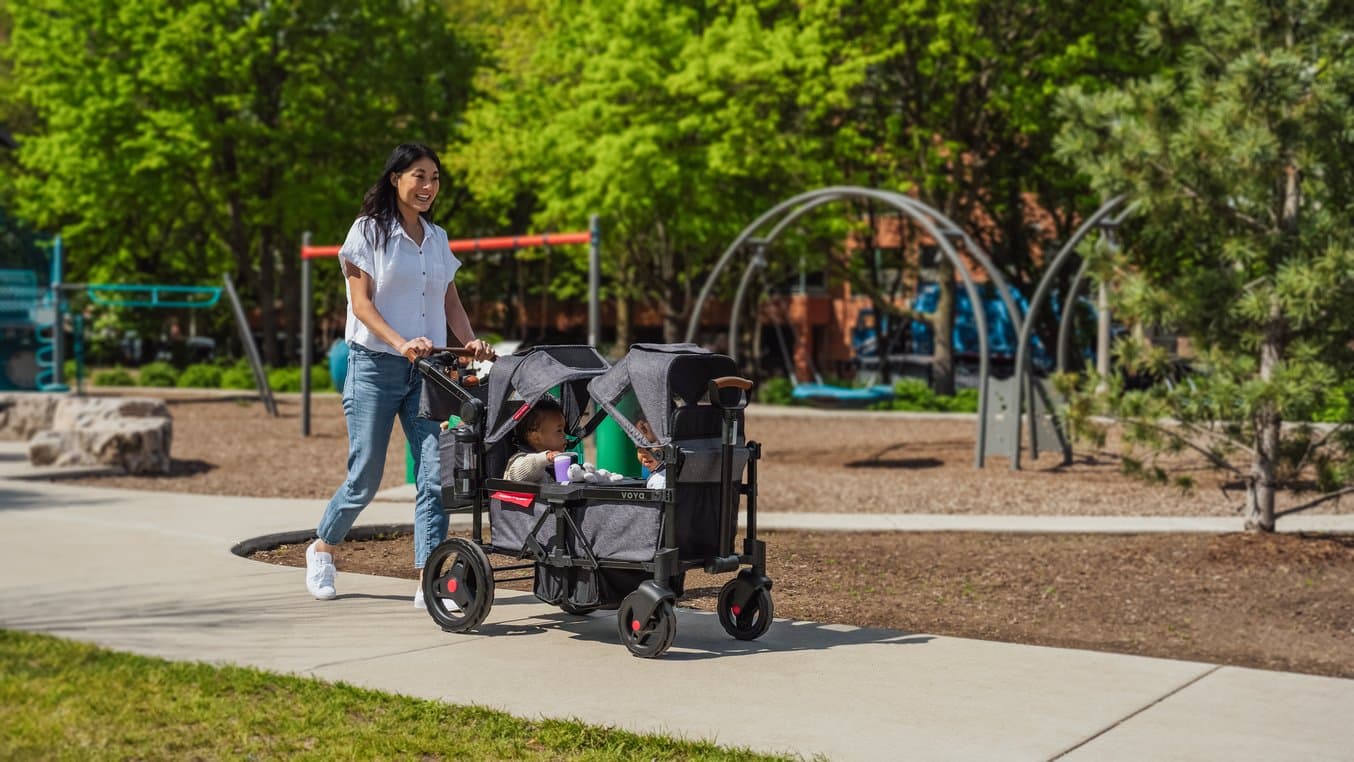
La prototipazione rapida e affidabile con le stampanti 3D SLA e SLS ha aiutato Radio Flyer a dare vita a nuove evoluzioni dei suoi storici giocattoli e prodotti per la famiglia, offrendo strumenti con cui creare ricordi duraturi.
Punto di riferimento per le famiglie americane da oltre un secolo, Radio Flyer ha creato linee di prodotti innovativi e di alta qualità che vengono apprezzati da generazioni. Per coniugare design dall'estetica eccellente a funzionalità e sicurezza è necessario eseguire lunghi processi di iterazione e implementare il feedback reale delle famiglie che hanno testato il prodotto. La stampa 3D consente a Radio Flyer di fare tutto ciò.
Portando in-house stampanti 3D di qualità industriale come la serie Fuse e la Form 4L, i team di progettazione di Radio Flyer possono sperimentare nuove idee, apportare piccole modifiche e creare prototipi paragonabili alle parti finite.
Con l'introduzione della Form 4L, l'officina di prototipazione può realizzare progetti che prima non sarebbero stati possibili, come produrre in meno di un giorno modelli ad alta fedeltà quasi indistinguibili da parti realizzate tramite stampaggio a iniezione. La velocità, l'accuratezza e l'affidabilità della Form 4L supportano Radio Flyer in ciò che sa fare meglio: approcciare la tradizione attraverso la lente della tecnologia moderna per creare giocattoli in cui questi due aspetti si combinano alla perfezione.
Visita le nostre pagine per ulteriori informazioni sulla Form 4L o sulla serie Fuse.