A tutta velocità: Rome Snowboards accelera lo sviluppo di prodotto con la stampa 3D SLS
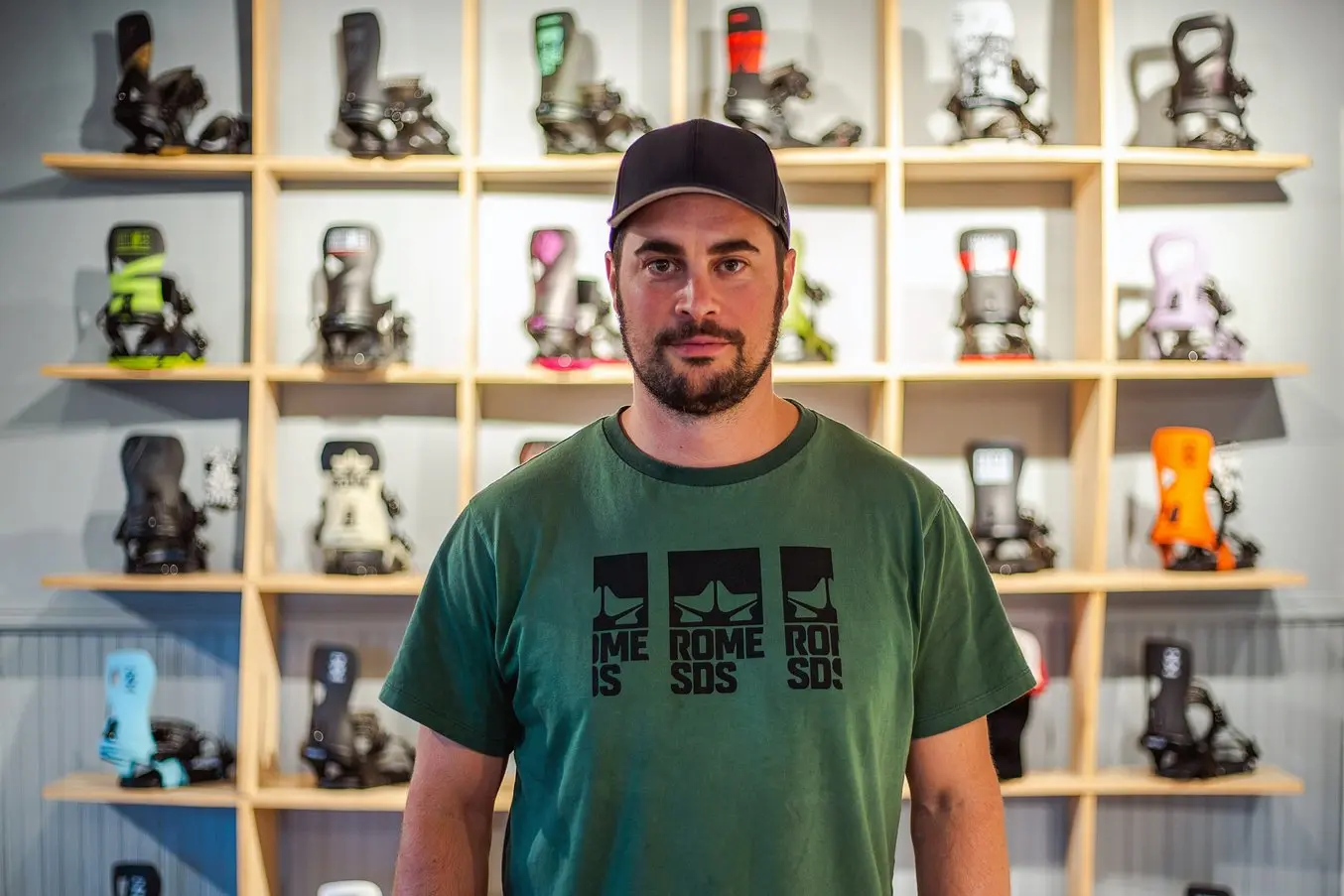
Justin Frappier, designer di prodotto di Rome Snowboards, ha portato in-house la stampa 3D SLS e ora è in grado di progettare, creare prototipi ed eseguire iterazioni ogni giorno.
Cerchiamo sempre di creare qualcosa di nuovo. Abbiamo iniziato ad avere un ritorno d'investimento già nei primi cinque mesi: è bastato accelerare la prototipazione.
Justin Frappier, designer di prodotto di Rome Snowboards
Fin dalla sua invenzione negli anni '60, lo snowboard è sempre stato visto come uno sport da ribelli. L'abbigliamento largo e le incredibili evoluzioni negli snowpark lo hanno reso il "fratellino punk" dei tradizionali sport invernali, mentre le analogie con il surf e lo skateboard contribuiscono a riunire lo stesso pubblico giovane e impertinente in un'unica controcultura.
Lo snowboard è nato dal desiderio di fare le cose in modo diverso e la sua attrezzatura altamente tecnica riflette questo spirito. Le aziende produttrici sono sempre alla ricerca di nuove soluzioni per migliorare l'esperienza sulla neve grazie ad attrezzature affidabili, facili da usare e in grado di resistere a un'intera stagione. La stampa 3D in-house è la soluzione per accelerare il processo iterativo e mantenere un flusso costante di nuovi design innovativi.
Il motto di Rome Snowboards, piccola azienda di dieci persone di Waterbury, in Vermont, è "All Ways Down", traducibile con "fino in fondo". Questo principio si applica alla loro filosofia aziendale e al loro processo di sviluppo. Infatti, il designer di prodotto Justin Frappier è costantemente alla ricerca di nuovi processi e metodi per creare attacchi e scarponi. L'obiettivo essenziale di Rome è quello di creare attrezzature che garantiscano un'esperienza più confortevole e duratura, in grado di resistere alla torsione e agli impatti generati durante le evoluzioni e le discese. Grazie all'adozione in-house di una stampante 3D a sinterizzazione laser selettiva (SLS) Fuse 1, Rome è riuscita a innovare più velocemente e a testare i suoi prototipi direttamente in montagna, dando vita a un processo iterativo più rigoroso. "Cerchiamo sempre di creare qualcosa di nuovo. Abbiamo iniziato ad avere un ritorno d'investimento già nei primi cinque mesi: è bastato accelerare la prototipazione", ha dichiarato Frappier.
Rome crea già alcuni dei prodotti più apprezzati del settore, con ottime recensioni da riviste come White Lines, che ha inserito gli attacchi Vice nel suo elenco dei migliori prodotti per snowboard del 2021-2022. "Sono attacchi estremamente versatili che uniscono la tecnologia tradizionale con alcune funzionalità innovative. Con la sua ultima versione dei loro famosi Vice, Rome ha fatto centro".
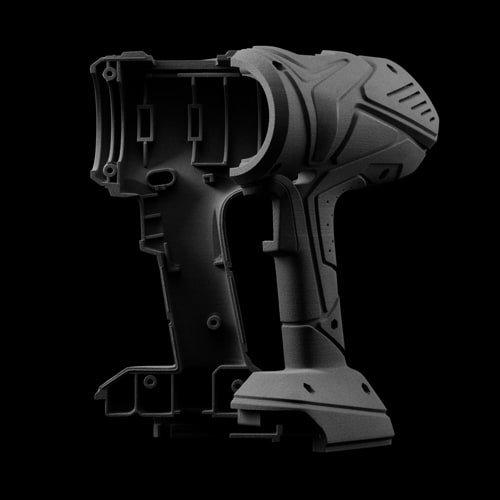
Introduzione alla stampa 3D tramite sinterizzazione laser selettiva (SLS)
Stai cercando una stampante 3D per creare parti robuste e funzionali? Scarica il nostro whitepaper per scoprire come funziona la stampa SLS e perché è un processo di stampa 3D molto diffuso per la prototipazione funzionale e la produzione per l’utilizzo finale.
Il percorso verso la stampa SLS
Prima della Fuse 1, Frappier e il suo collega nel team di progettazione realizzavano i design manualmente, lavorando con materiali come l'argilla, il mastice Bondo e parti esternalizzate che dovevano essere assemblate e post-elaborate per ottenere prototipi estetici finali. Pur conoscendo le potenzialità della stampa 3D, Frappier ha iniziato a interessarsi a questa tecnologia solo dopo aver visto un attacco da snowboard stampato in 3D in un video promozionale della Fuse 1. "Era circa da otto anni che desideravo adottare la stampa 3D in azienda. Abbiamo valutato pro e contro e prezzi di varie apparecchiature, e alla fine la Fuse 1 ci è sembrata la soluzione ideale, perché oltre alla stampante era inclusa anche la Fuse Sift. Ogni aspetto era curato nel dettaglio" afferma Frappier.
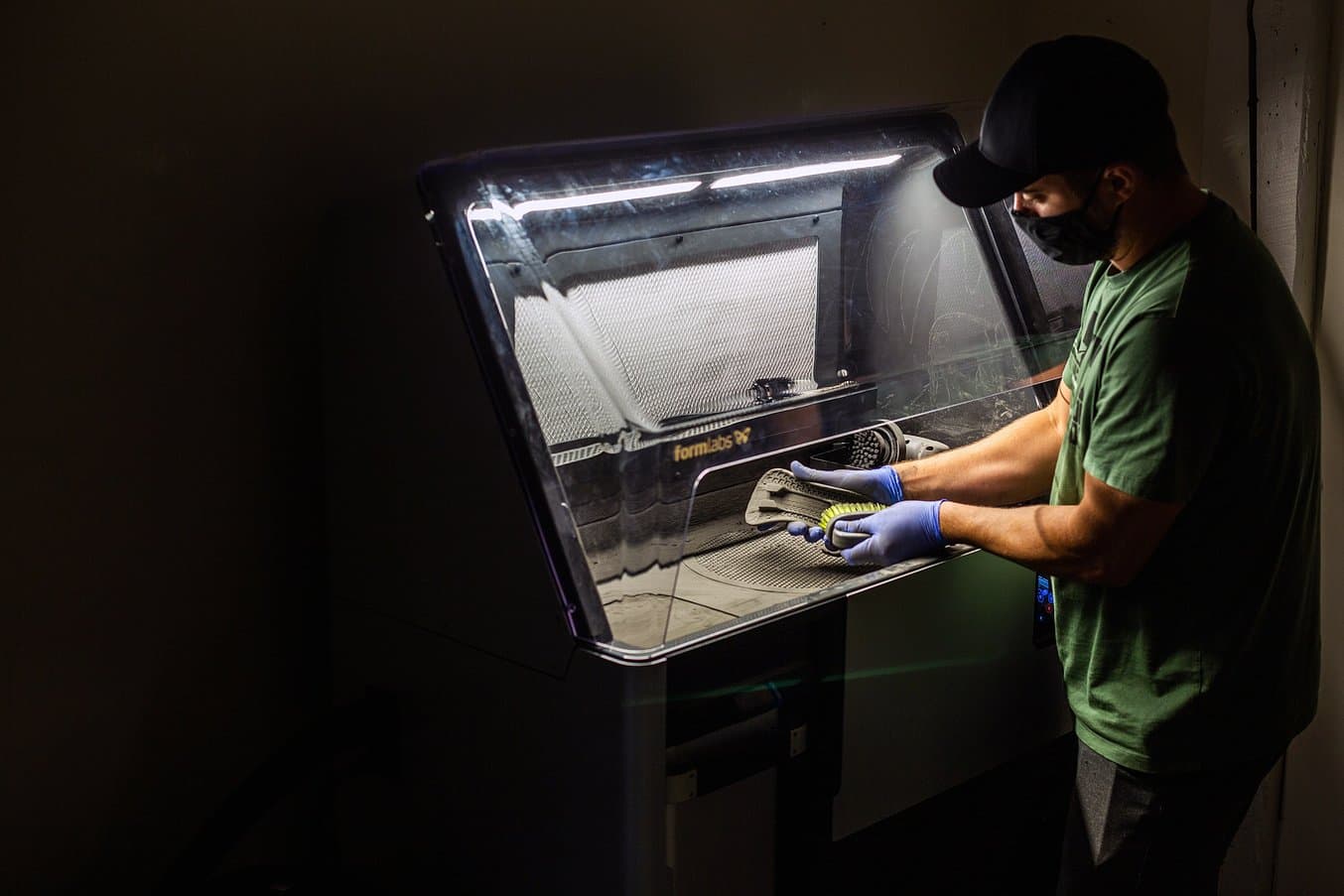
La Fuse Sift semplifica la post-elaborazione e il processo di riciclo della polvere. In questo modo, Frappier ha più tempo da dedicare all'attività di progettazione.
Oltre a intagliare l'argilla, capitava anche che il team ordinasse parti stampate in 3D poco oltre il confine, a Montreal, in Canada. La spesa non era esorbitante, ma i tempi di realizzazione e consegna non consentivano loro di progettare rapidamente. "Eravamo in lista d'attesa con altre aziende, quindi la nostra velocità di sviluppo dipendeva da quando avremmo ricevuto le parti", ha commentato Frappier.
Per una piccola azienda come Rome, conosciuta per i suoi attacchi altamente personalizzabili, i ritardi nello sviluppo rappresentavano uno svantaggio rispetto a produttori più grandi. I loro punti di forza sono la capacità di eseguire iterazioni, ottenere rapidamente le approvazioni interne e creare prodotti unici e innovativi come le loro tecnologie brevettate AuxTech, PivotMount e AsymWrap.
"I vantaggi di una soluzione in-house sono diventati chiari dopo appena sei mesi dall'acquisto della Fuse 1. Abbiamo lavorato sulle fibbie per circa sei mesi. Le stampavamo, le assemblavamo, ne verificavamo la prestazioni, i problemi e le interferenze. Avere la possibilità di stampare una parte, esaminarla la mattina seguente, assemblarla, apportare modifiche e ripetere tutto il giorno dopo è stato davvero utile", ha affermato Frappier.
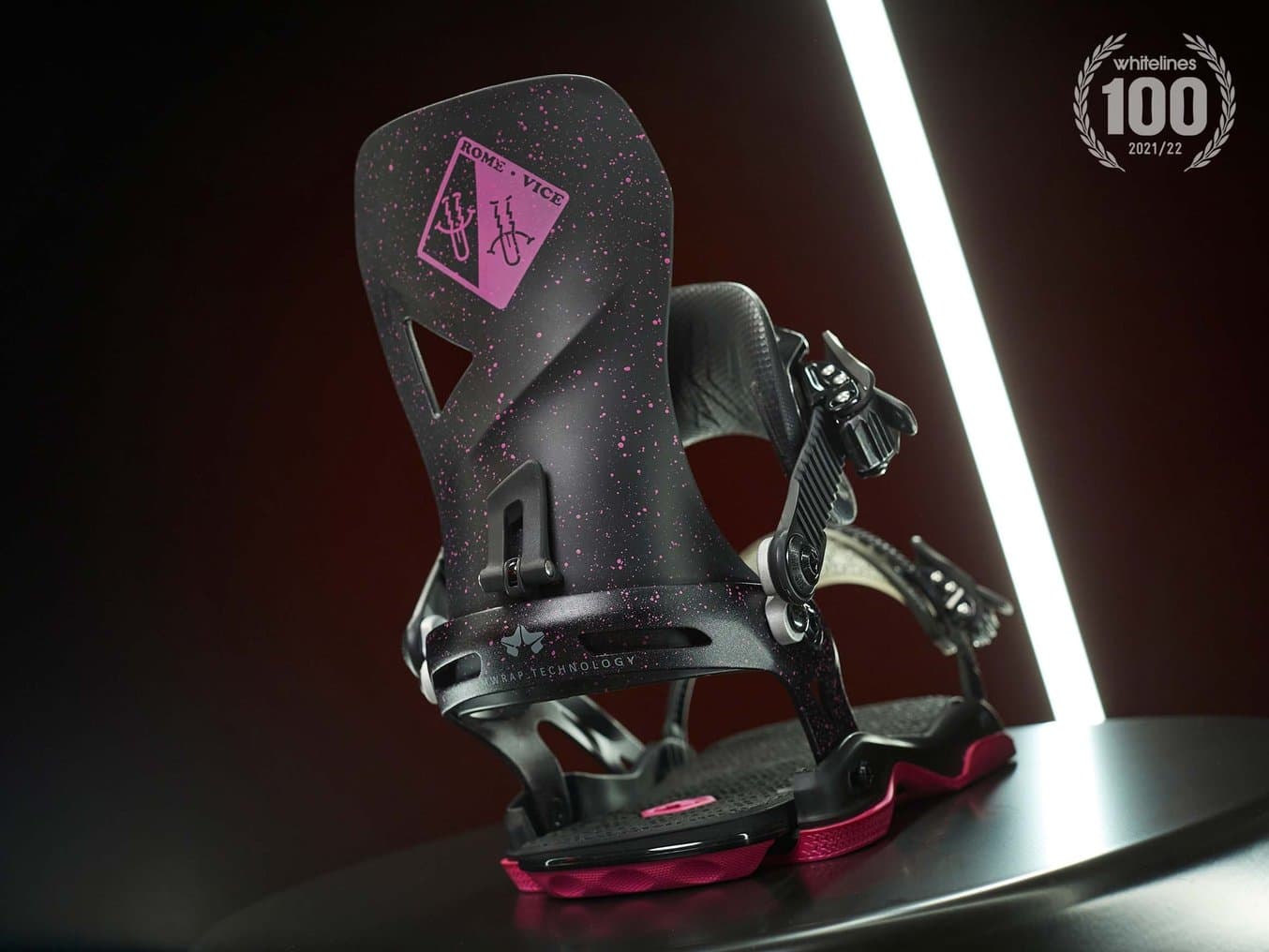
Il pluripremiato attacco Vice, raffigurato nella recensione di White Lines. Foto per gentile concessione di White Lines.
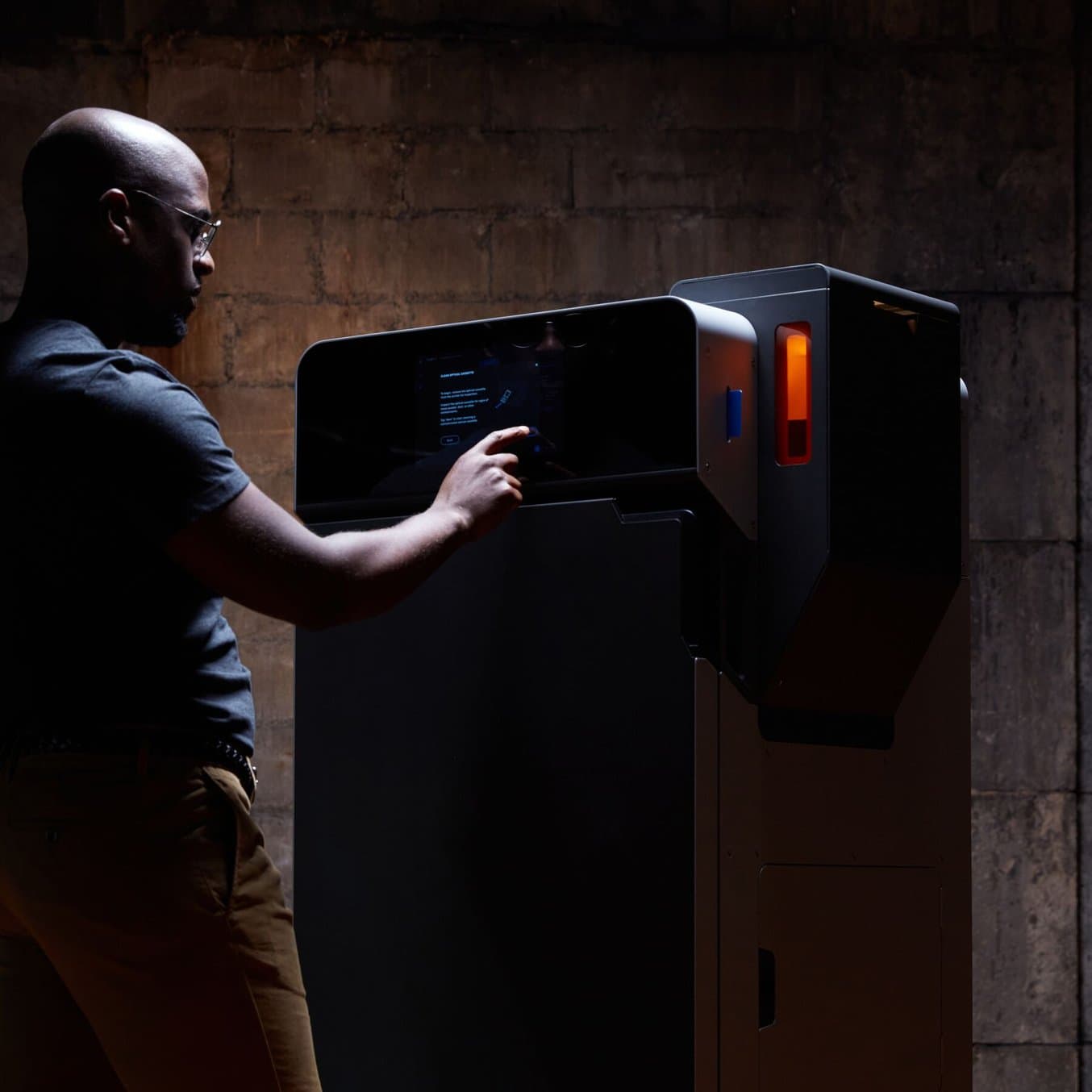
Esternalizzazione o produzione interna: quando conviene portare la stampa 3D SLS in-house?
In questo whitepaper valuteremo la proposta di valore dell'adozione di stampanti 3D SLS in-house e la confronteremo con l'esternalizzazione delle parti SLS a un fornitore di servizi.
Soluzioni diverse per persone diverse
I prodotti Rome sono dotati di numerosi componenti che consentono di adattarli in base al peso, alla corporatura e allo stile della persona che li usa, nonché alle diverse condizioni ambientali. Per contro, un simile livello tecnologico richiede un design complesso e tolleranze ridotte, in modo che l'assemblaggio sia perfetto. La recensione di White Lines riportava: "L'highback è realizzato in nylon al 100% per un alto livello di flessione che riduce notevolmente la rigidità. Qualsiasi snowboarder che utilizza i Vice si sentirà immediatamente a suo agio".
La facilità di utilizzo è data dalla cura e dal tempo che il team di Rome dedica a ogni fase del processo. Frappier afferma: "Cerchiamo sempre di assicurarci che le nostre parti siano perfette e affidabili. Anche se ci sono più parti, l'assemblaggio è perfetto e ogni cliente ha sempre un'esperienza positiva, perché l'attacco è stato progettato in modo meticoloso. La stampa 3D è grandiosa: ci permette di affinare ogni parte e garantire che tutte funzionino alla perfezione una volta assemblate".
Ingombro ridotto, grandi risultati
Per ottenere lo stesso risultato, molte aziende devono fare affidamento su grandi team di designer che collaborano tra loro. In Rome lavorano solo due designer, il che consente all'azienda una grande agilità e un flusso di lavoro continuo. La Fuse 1, che permette di stampare tutto il giorno quando il team lo richiede, è un ottimo argomento di convincimento quando si tratta di proporre potenziali sponsorizzazioni ad atleti ed atlete. Dimensioni e prezzo accessibili la rendono una soluzione facilmente integrabile, anche per le aziende che non dispongono di grandi spazi o di un personale numeroso.
Rispetto ad altre aziende produttrici di attacchi, noi siamo molto piccoli. Nella nostra sede di Waterbury lavorano da otto a dieci persone e il fatto di avere accesso a una soluzione di stampa 3D completa è davvero fantastico. Molti pensano che siamo una grande azienda. Questo è uno dei tanti vantaggi della Fuse 1, senza contare che possono permettersela anche le piccole aziende.
Justin Frappier, designer di prodotto di Rome Snowboards
Come sostiene Frappier, ogni volta che atleti e distributori di attrezzature visitano la sede di Waterbury, le reazioni di fronte alla Fuse 1 sono sempre molto positive. "La stampante lascia a bocca aperta chiunque venga a trovarci. Siamo in grado di mostrare ad atleti e rappresentanti dei distributori di attrezzature il passaggio rapido dalla progettazione alla parte finale, con la possibilità di toccare con mano la parte. Dopo di che possiamo ottenere un feedback prima di mandare la parte in produzione", ha affermato Frappier.
Prototipazione funzionale sempre più rapida
La linea di prodotti Rome del 2022 non verrà prodotta in massa tramite la stampa 3D, ma ciò non ha impedito al team di eseguire alcuni test di validazione finale molto realistici. Questi test hanno avuto luogo durante la stagione invernale successiva all'acquisto della stampante. Il team di progettazione ha così potuto verificare le massime prestazioni dei prototipi e garantire che le fibbie e gli assemblaggi resistessero alle condizioni d'uso, evitando così di mandare in produzione parti che non fossero perfette.
"Non ci piace perdere tempo e non vogliamo rischiare di sprecare le attrezzature lavorando troppo di fretta. Da questo punto di vista la stampa 3D ci ha reso più efficienti", ha affermato.
Frappier e i suoi colleghi hanno portato attacchi completamente stampati (a eccezione di alcune viti metalliche) sulle montagne del Vermont, aumentando la rapidità ad ogni discesa. La possibilità di testare la flessione e la resistenza degli attacchi direttamente in montagna permette a Frappier di risparmiare settimane rispetto alle tempistiche di sviluppo tradizionali. Questo spirito innovativo è ciò che ha permesso al marchio di avere successo. Esternalizzare le parti implica settimane di attesa, e nulla spegne la creatività quanto una lunga attesa.
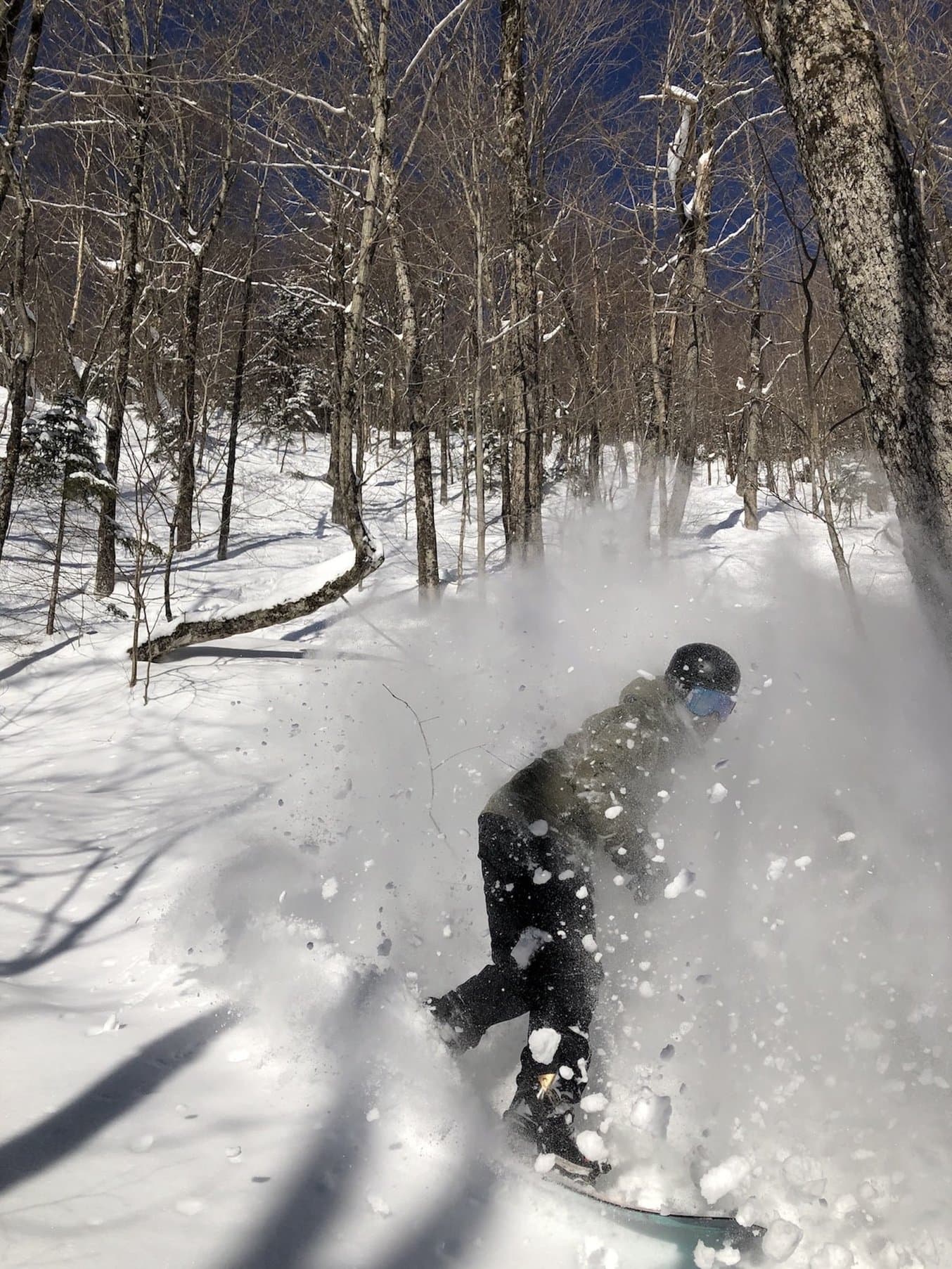
Il principale argomento di vendita era la possibilità di provare sul campo le parti stampate. Con altre parti, ciò non è mai stato possibile. La prima volta avevamo la tavola di base e i componenti del telaio. A ogni discesa aumentavamo sempre di più la velocità e la tenuta era perfetta. Ora possiamo stampare, testare e ristampare ogni giorno.
Justin Frappier, designer di prodotto di Rome Snowboards
Dare al team di progettazione il controllo completo dell'intero processo creativo, iterativo e di test ha permesso a Rome Snowboards di continuare ad ampliare le possibilità delle attrezzature da snowboard.
"Realizziamo prodotti competitivi in ogni categoria. Cerchiamo sempre di creare qualcosa di nuovo e continuiamo a migliorare. Abbiamo iniziato ad avere un ritorno d'investimento già nei primi cinque mesi: è bastato accelerare la prototipazione", ha dichiarato Frappier.
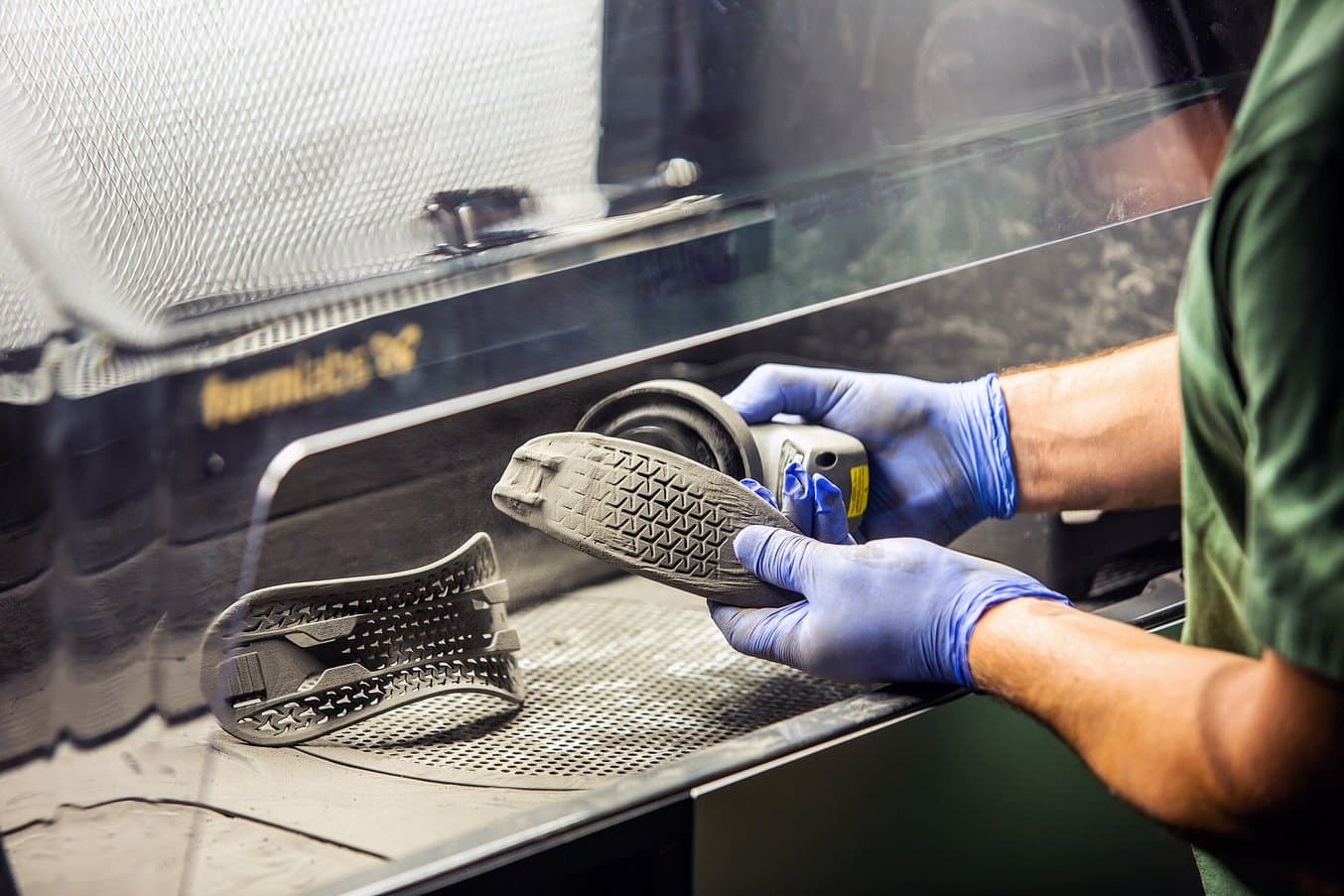
La rimozione e il riciclo della polvere non sinterizzata è semplice grazie al workflow integrato e intuitivo della Fuse Sift.
Le stampanti serie Fuse consentono ai team di progettazione di testare i prodotti dal punto di vista funzionale e di eseguire iterazioni senza i tempi di inattività tipici dell'esternalizzazione. La Fuse 1 ha permesso di accelerare notevolmente il processo di sviluppo di Rome Snowboards, così Frappier è riuscito a provare sul campo i suoi attacchi stampati in 3D. Per scoprire se la Fuse 1 può fare al caso tuo, ordina un campione oppure leggi il caso di studio in cui mettiamo a confronto le parti stampate SLS in-house con quelle esternalizzate a un fornitore di servizi.