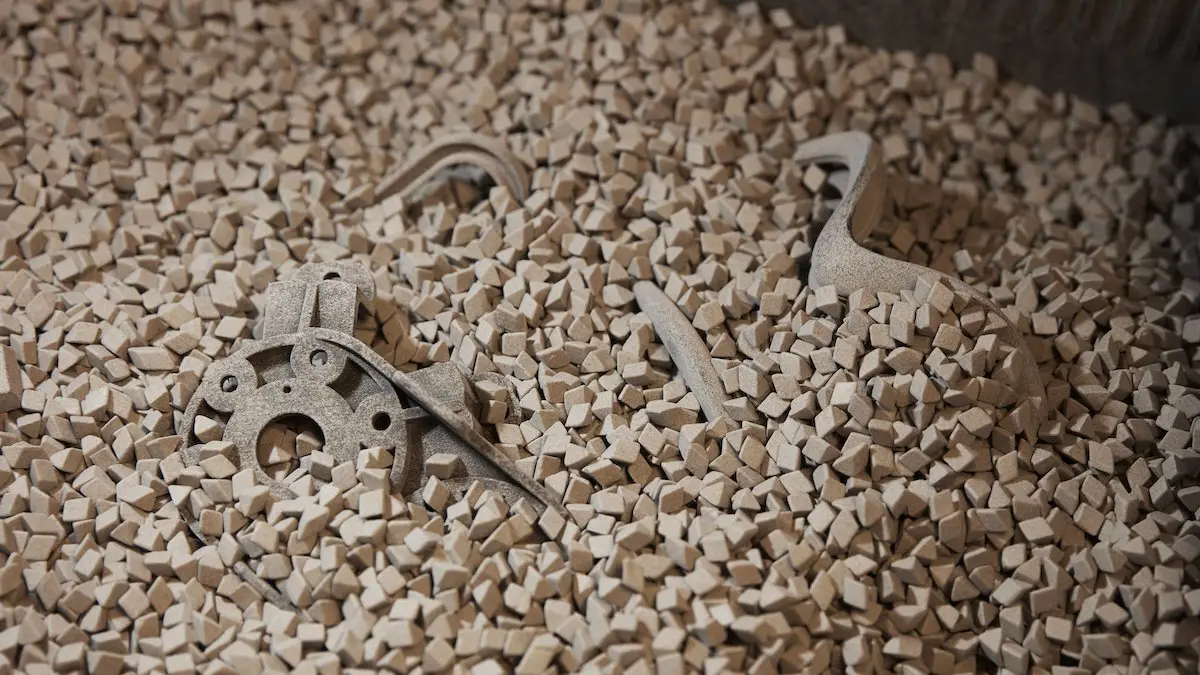
La burattatura, anche nota come vibrofinitura, è un metodo consolidato per migliorare la durezza e la levigatezza superficiale di diversi materiali. Tradizionalmente utilizzata sulle parti in metallo per rimuovere le sbavature dopo la lavorazione meccanica o la pressatura, questa tecnica viene ora considerata da molte aziende come un passaggio di post-elaborazione fondamentale anche per le parti stampate in 3D.
La burattatura si rivela particolarmente utile quando si utilizza la stampa 3D a sinterizzazione laser selettiva (SLS), che a volte conferisce alle parti una superficie leggermente granulosa. Questa tecnica contribuisce a renderle pronte per l'utilizzo finale o a semplificare il loro inserimento all'interno di assemblaggi funzionali.
Leggi questa guida per avere una panoramica introduttiva sulla burattatura di parti realizzate con la stampa 3D SLS e guarda il nostro webinar per vedere i risultati completi dei test eseguiti e del confronto tra buratti, nonché per scoprire di più sul workflow.
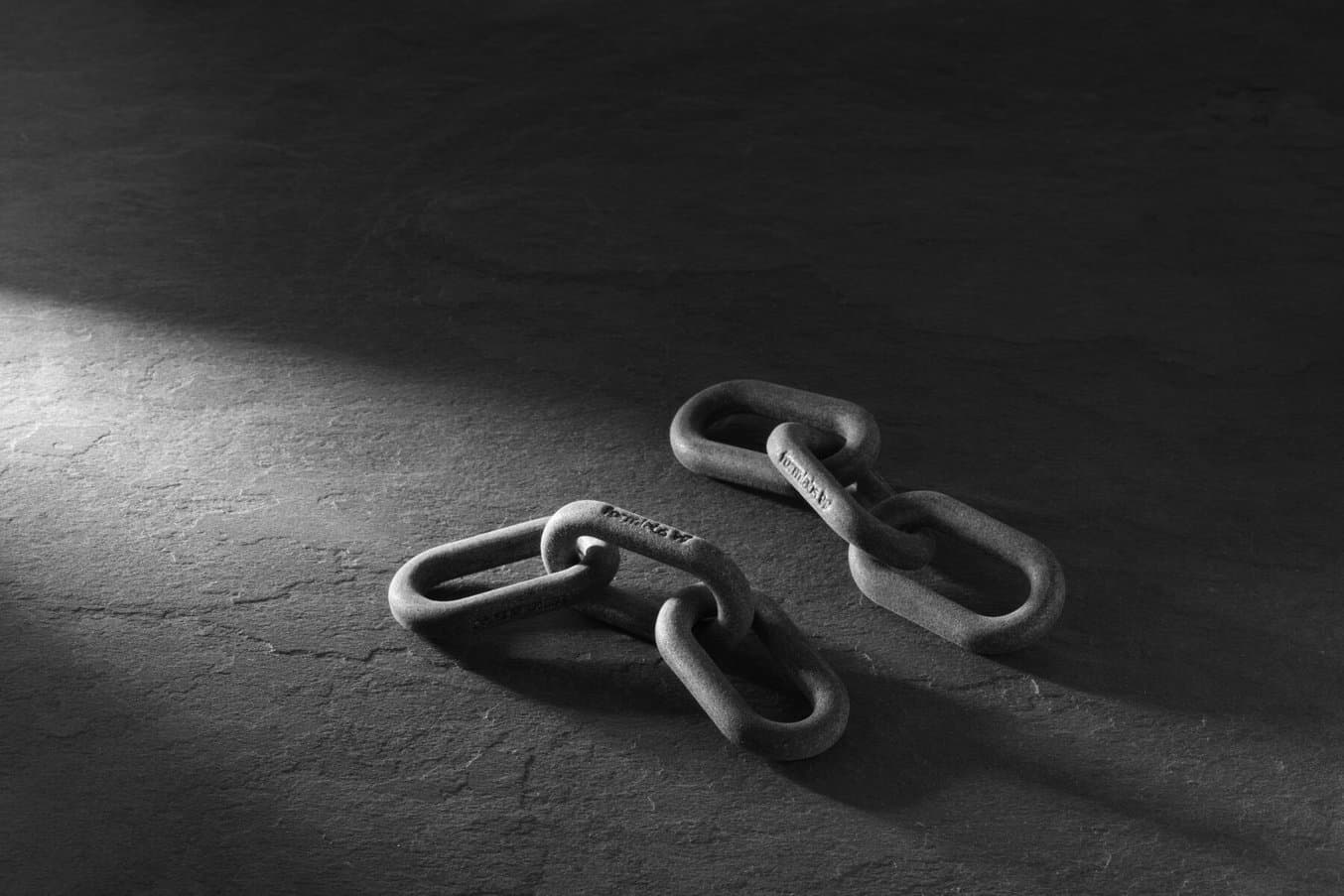
Burattatura per parti realizzate con la stampa 3D SLS
In questo rapporto spiegheremo come scegliere l'apparecchio e i materiali giusti per il tuo workflow e illustreremo le buone pratiche e i metodi per ottenere risultati eccellenti.
Processo e vantaggi della burattatura
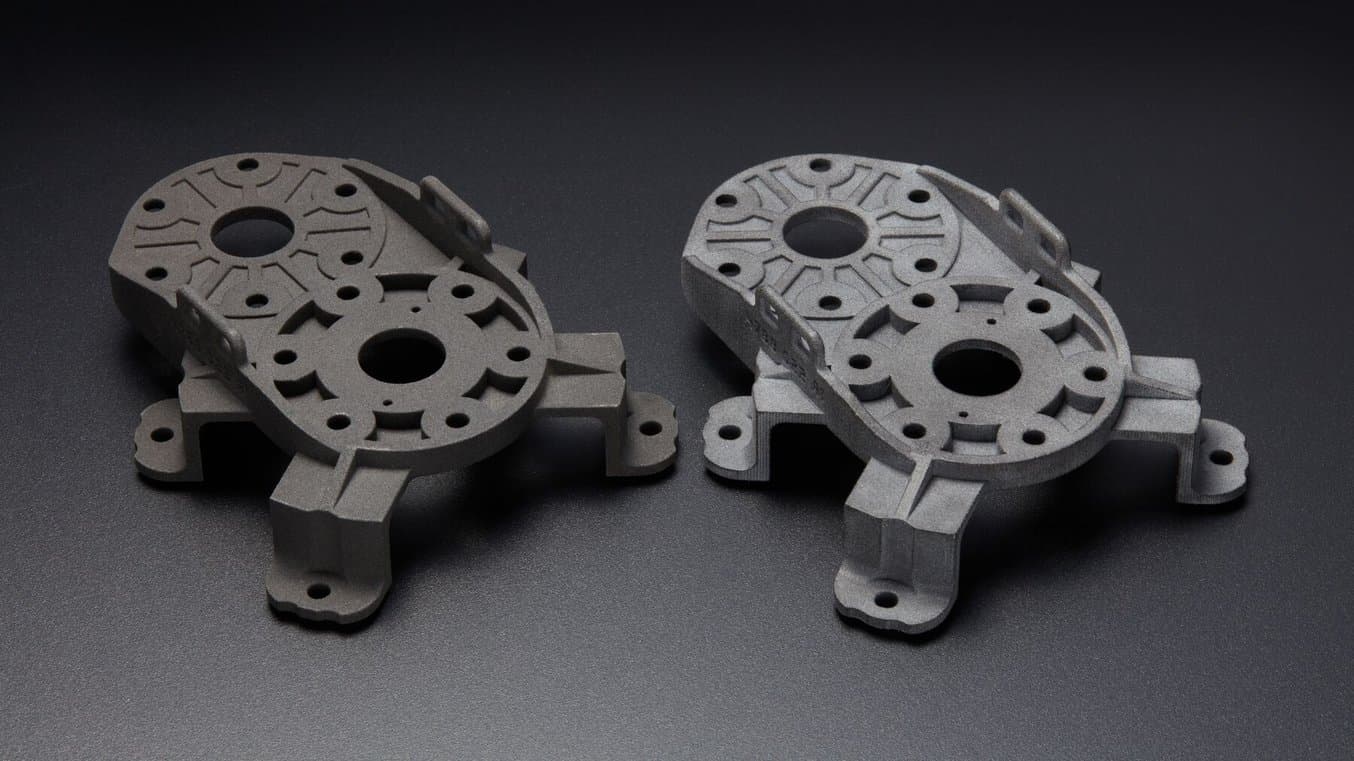
La nostra parte di prova, prima e dopo la burattatura. La parte burattata è di colore grigio chiaro e ha un aspetto opaco.
La burattatura consiste nell'agitare le parti per utilizzo finale insieme a pellet di diversi materiali (solitamente metallo, ceramica, plastica o materiale organico come gusci di noce) per generare attrito, che leviga la superficie delle parti e ne migliora la durezza. I buratti vibranti sono ampiamente utilizzati, date le loro dimensioni accessibili, il prezzo contenuto e la gamma di vantaggi che offrono senza aggiungere ulteriore manodopera al ciclo di produzione.
La burattatura offre due vantaggi fondamentali al workflow di stampa 3D: migliore funzionalità e migliore estetica. Questo processo riduce la ruvidità superficiale dei componenti mobili, che di conseguenza funzionano con un coefficiente di attrito inferiore. Si tratta quindi di una tecnica di post-elaborazione ideale per applicazioni come cerniere stampate, componenti di azionamento, ganci funzionali e qualsiasi altra parte che si muove o è integrata in un assemblaggio mobile. Una migliore finitura superficiale ottimizza anche la porosità, rendendo le parti burattate più resistenti all'assorbimento dei fluidi.
I vantaggi estetici della burattatura sono in primo luogo una finitura superficiale migliore e un aspetto più definito, ma anche la possibilità di avere un substrato più omogeneo su cui applicare ulteriori rivestimenti, come vernice acrilica o Cerakote.
La burattatura è un metodo semplice per migliorare drasticamente la durezza e la levigatezza della superficie di qualsiasi parte stampata in 3D da utilizzare come parte per utilizzo finale, in un assemblaggio funzionale o che debba avere un'elevata visibilità in un prototipo Proof-of-Concept.
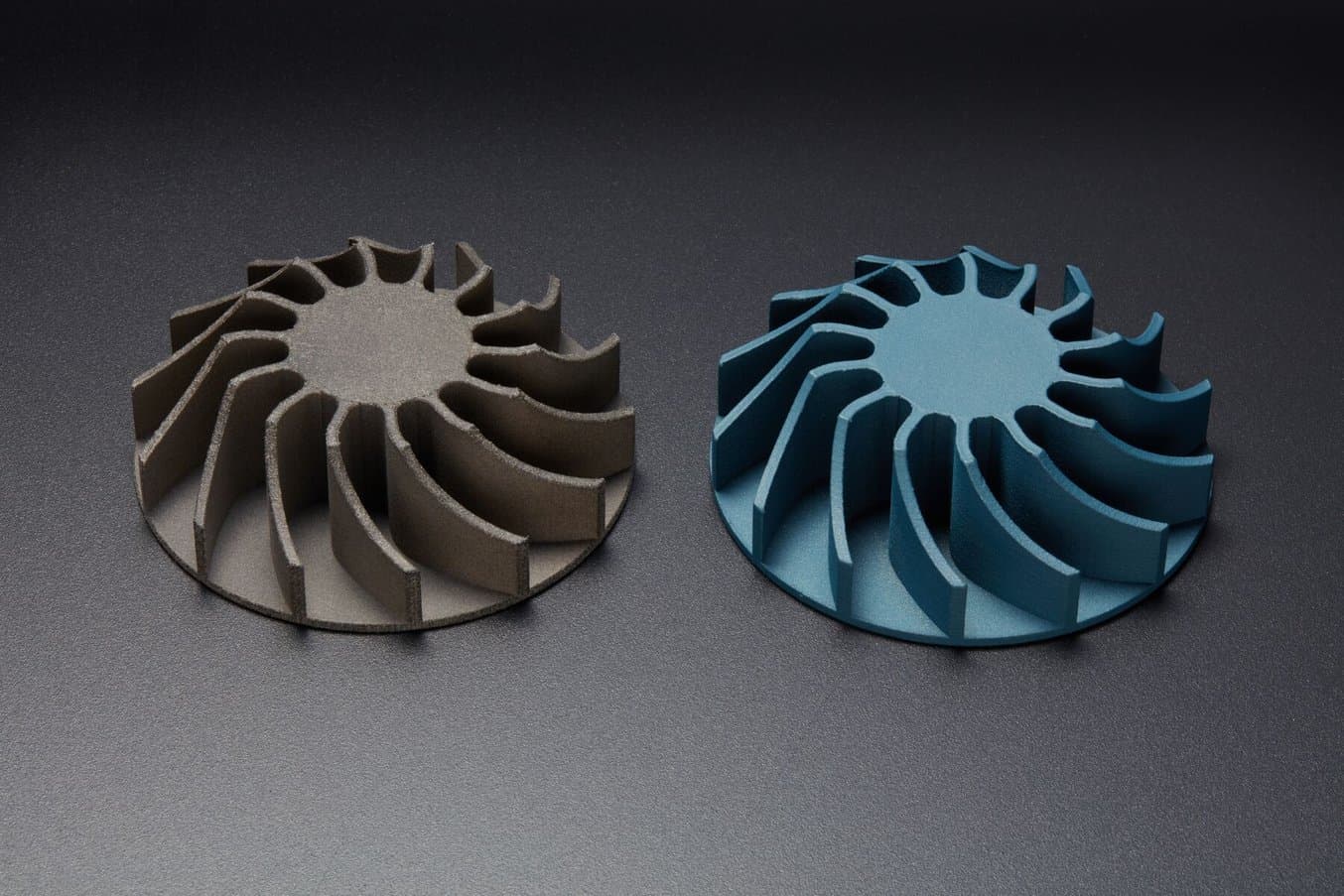
La burattatura crea un substrato più omogeneo su cui applicare ulteriori rivestimenti, come la vernice acrilica o il rivestimento in ceramica Cerakote.
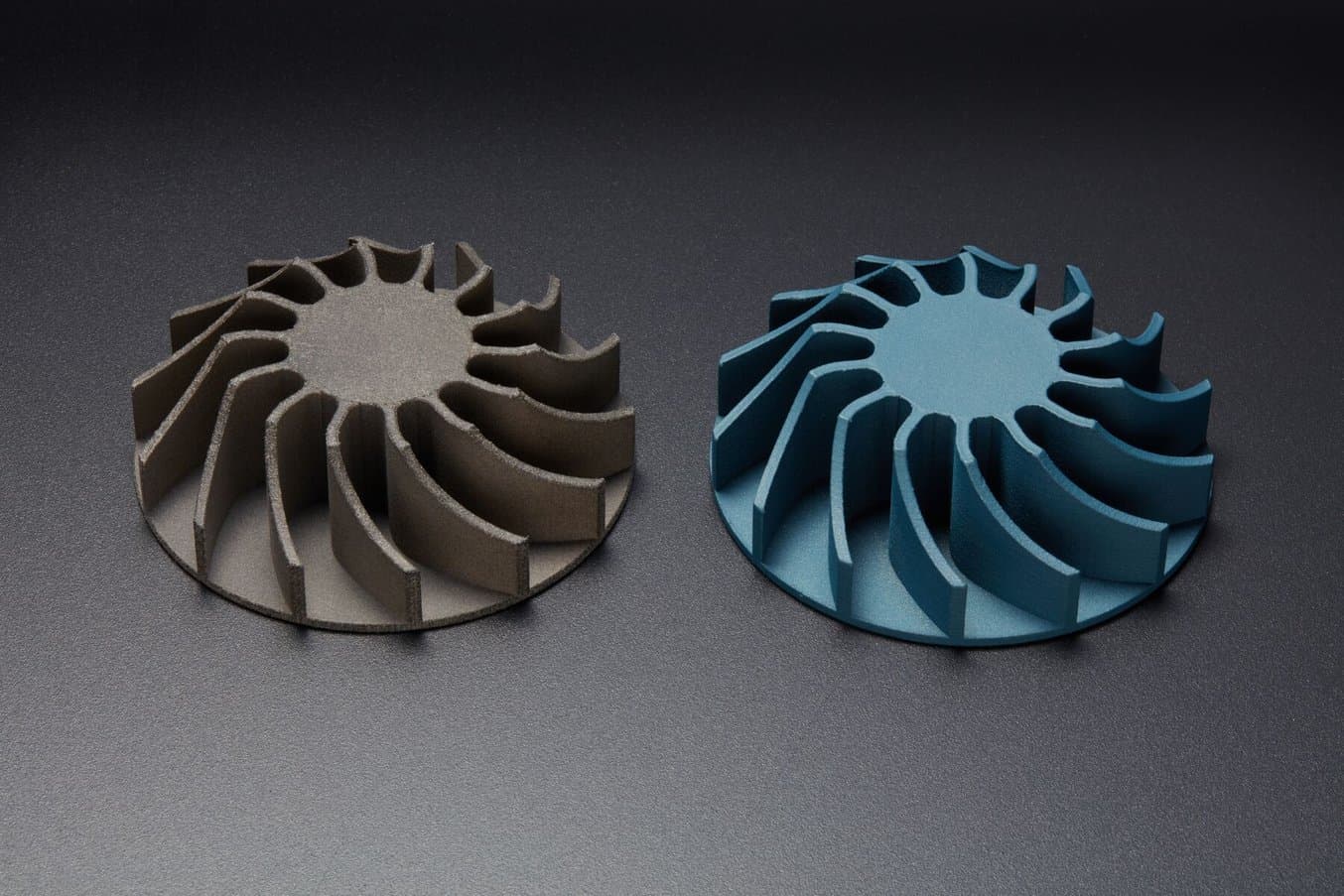
Tecniche di post-elaborazione avanzate per la stampa 3D
Guarda questo webinar per scoprire più di 10 tecniche di post-elaborazione avanzate per la stampa 3D, tra cui rivestimento con Cerakote, galvanizzazione, levigazione a vapore e molte altre.
Come scegliere un buratto vibrante per parti stampate in 3D
Gli apparecchi per la burattatura di parti stampate in 3D possono essere suddivisi in due categorie principali: industriali e di consumo. Gli apparecchi industriali hanno una capacità maggiore e requisiti di alimentazione più elevati e di solito costano almeno 5000 €. I buratti industriali sono adatti a volumi di diversi livelli di produzione, come la personalizzazione di massa o la produzione di soluzioni provvisorie.
Possono gestire facilmente più lotti di parti, anche di dimensioni medio-grandi, il che li rende ideali per i fornitori di servizi o la produzione su larga scala. Molti apparecchi industriali, come il buratto Rösler, sono progettati per integrarsi in un flusso di lavoro automatizzato, caricando e scaricando le parti mediante un nastro trasportatore o un sistema robotico. I cicli di burattatura degli apparecchi più grandi possono durare anche solo quattro o sei ore, riducendo in modo significativo la ruvidità superficiale.
Molti buratti vibranti più piccoli riescono a raggiungere lo stesso risultato finale di quelli industriali, ma hanno una capacità inferiore e possono richiedere cicli di burattatura più lunghi. Per ottenere quasi la stessa riduzione della ruvidità superficiale, gli apparecchi più piccoli devono burattare le parti per circa 72 ore, a fronte delle sei ore necessarie per i buratti industriali.
Tuttavia, il prezzo accessibile e l'ingombro ridotto consentono alle aziende più piccole di usufruire dei loro vantaggi senza la spesa necessaria per l'acquisto di un apparecchio di livello industriale. I buratti vibranti di piccole dimensioni sono sufficienti per chi utilizza stampanti 3D con volumi inferiori a 100 parti a settimana.
Sebbene non siano stati inclusi nel protocollo di test di questo studio, una terza opzione sono i buratti centrifughi. Il flusso di lavoro varia leggermente rispetto ai buratti vibranti tradizionali, in quanto sfruttano la rotazione ad alta velocità per levigare le parti, invece di agitarle. Nei buratti centrifughi, i componenti e i materiali sono sigillati in un contenitore e poi fatti girare ad alta velocità. Le forze G che ne derivano permettono di levigare le parti molto rapidamente. I buratti centrifughi sono una valida opzione per ridurre il tempo di ciclo complessivo, anche se si tratta di un processo più aggressivo che può danneggiare i particolari delicati di alcune parti.
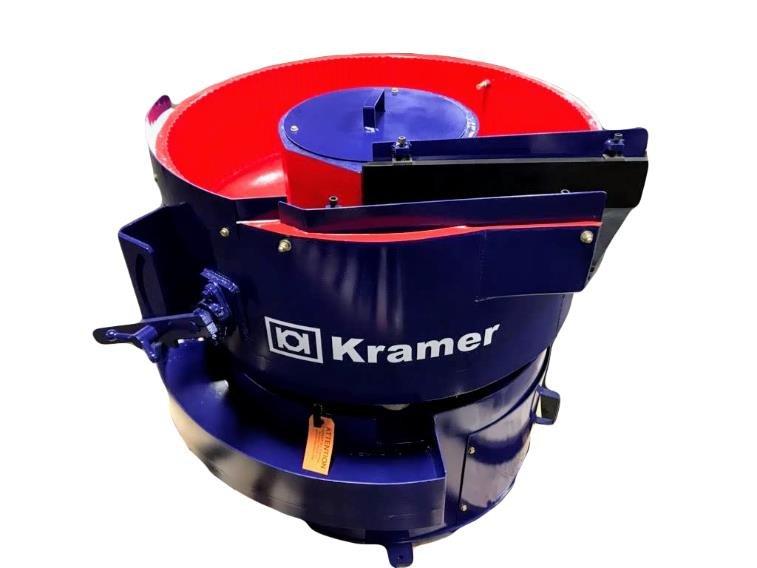
Industriale, produzione di volumi elevati
Esempio: Rösler
Costo: >5000 €
Ideale per:
-
Alto rendimento
-
Parti di grandi dimensioni
-
Più parti di grandi dimensioni
-
Flusso di lavoro automatizzato
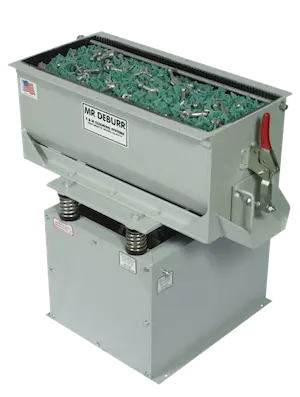
Produzione di volumi medi
Esempio: CM Topline
Costo: 1000-5000 €
Ideale per:
-
Parti di grandi dimensioni
-
Volumi di stampa raggruppati di parti più piccole
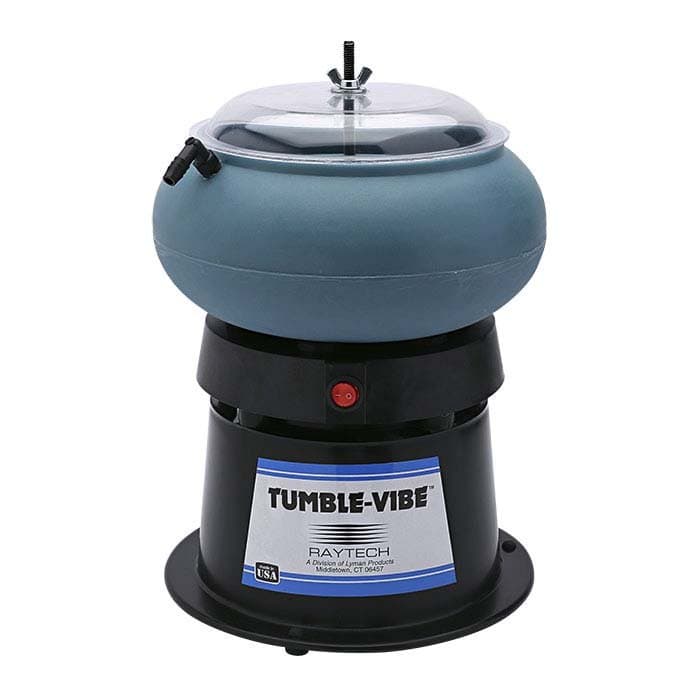
Livello base, volumi ridotti
Esempio: Tumble Vibe di Raytech
Costo: <1000 €
Ideale per:
-
Singole parti di dimensioni medie
-
Stampe a pieno volume di parti più piccole
Come scegliere materiali e detergenti per la burattatura
Nei workflow di burattatura possono essere utilizzati diversi tipi di pellet di materiale; la scelta di quello giusto avrà un grande impatto sul risultato finale. Tra i vari materiali troviamo acciaio inossidabile, porcellana, silice, compositi di poliestere o gusci di noce. Gli effetti della burattatura con queste sostanze vanno dalla levigatura aggressiva con eliminazione della ruvidità superficiale alla leggera lucidatura a scopo estetico.
Forme dei materiali
Quando si scelgono i materiali da utilizzare in un buratto vibrante, insieme al tipo di materiale occorre tenere conto delle dimensioni e della forma dei singoli pellet. Esistono pellet di dimensioni grandi e piccole e di forma appuntita o arrotondata. I pellet più grandi sono utilizzati per una smerigliatura più grossolana, ad esempio per rimuovere sbavature o ruggine da parti in metallo; quelli più piccoli sono utilizzati per ottenere pezzi più precisi, garantiscono una lucidatura o una brunitura maggiore e possono essere utilizzati per una gamma più ampia di materiali. I pellet affilati (triangoli, cunei e punte di freccia) sono ideali per la finitura di parti complesse con angoli, fessure e canali, anche se possono verificarsi più facilmente scheggiature o sfaldamenti. Al contrario, i pellet arrotondati sono ideali per una lucidatura e una brunitura più leggere e molto raramente producono scheggiature o sfaldamenti. Sebbene rallentino il processo di levigatura completa delle superfici, sono molto più delicati e possono essere utilizzati per le parti più fragili.
Detergenti
In alcuni workflow basati sulla vibrazione, chiamati "finitura a umido", ai pellet vengono aggiunti acqua o detergenti chimici. Il liquido aiuta a temperare il calore generato dall'elevato attrito e favorisce la rimozione di contaminanti o ossidi dalla superficie della parte. Le parti risulteranno più pulite e lucide rispetto a quelle ottenute con un flusso di lavoro di burattatura a secco. Tuttavia, i detergenti sono costosi e producono rifiuti chimici che devono essere smaltiti e trattati correttamente. Nel flusso di lavoro a umido si possono utilizzare materiali come metallo, ceramica o plastica, ma non quelli organici come i gusci di noce o i tutoli di mais.
Tabella di confronto: materiali per burattatura
Materiale tipico | Costo | Vantaggi | Svantaggi | Aggressività | |
---|---|---|---|---|---|
Metallo | Carbonio indurito Acciaio inossidabile | €€€ | Tempi di esecuzione brevi Durata prolungata Resistenza all'usura superiore Brunitura e lucidatura ad alta intensità | Potrebbe danneggiare le parti | Alto |
Ceramica | Porcellana Ossido di alluminio Carburo di silicio Silice | €€ | Brunitura e lucidatura ad alta intensità Materiali più comuni | Potrebbe danneggiare le parti I frammenti di ceramica possono staccarsi e incastrarsi nei canali o nei particolari negativi | Alto |
Plastica | Poliestere Urea Formaldeide | € | Ideale per la finitura sicura di parti filettate o fragili Crea superfici e bordi morbidi e definiti Sono disponibili diverse densità per personalizzazione in base all'applicazione | Tempi di esecuzione maggiori | Media |
Organica | Gusci di noce Tutoli di mais | € | Possono essere utilizzati come fase di burattatura secondaria Possono assorbire oli e umidità | Tempi di esecuzione maggiori Può essere necessario utilizzarli in un processo in due fasi | Eliminazione di sbavature da leggera a media |

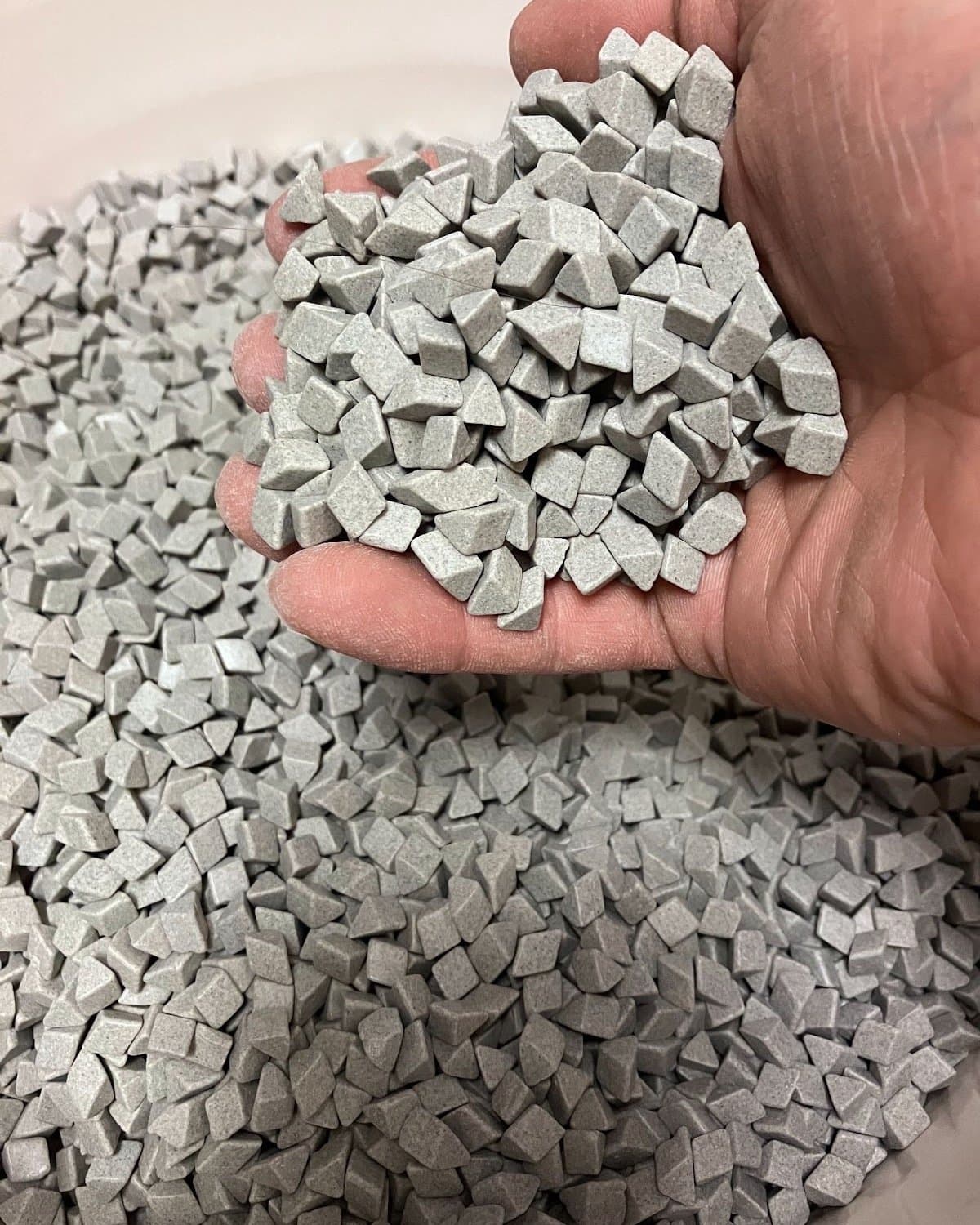
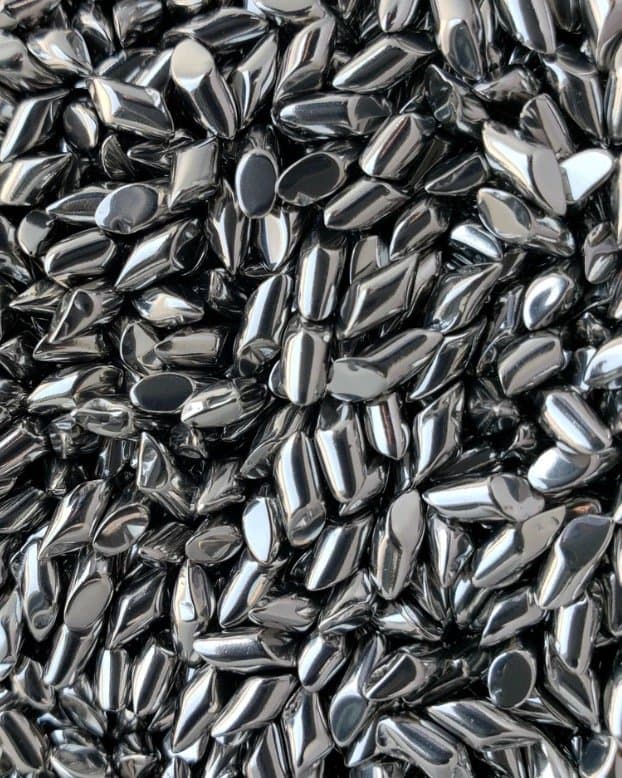
Materiali da sinistra a destra: gusci di noce, ceramica e acciaio.
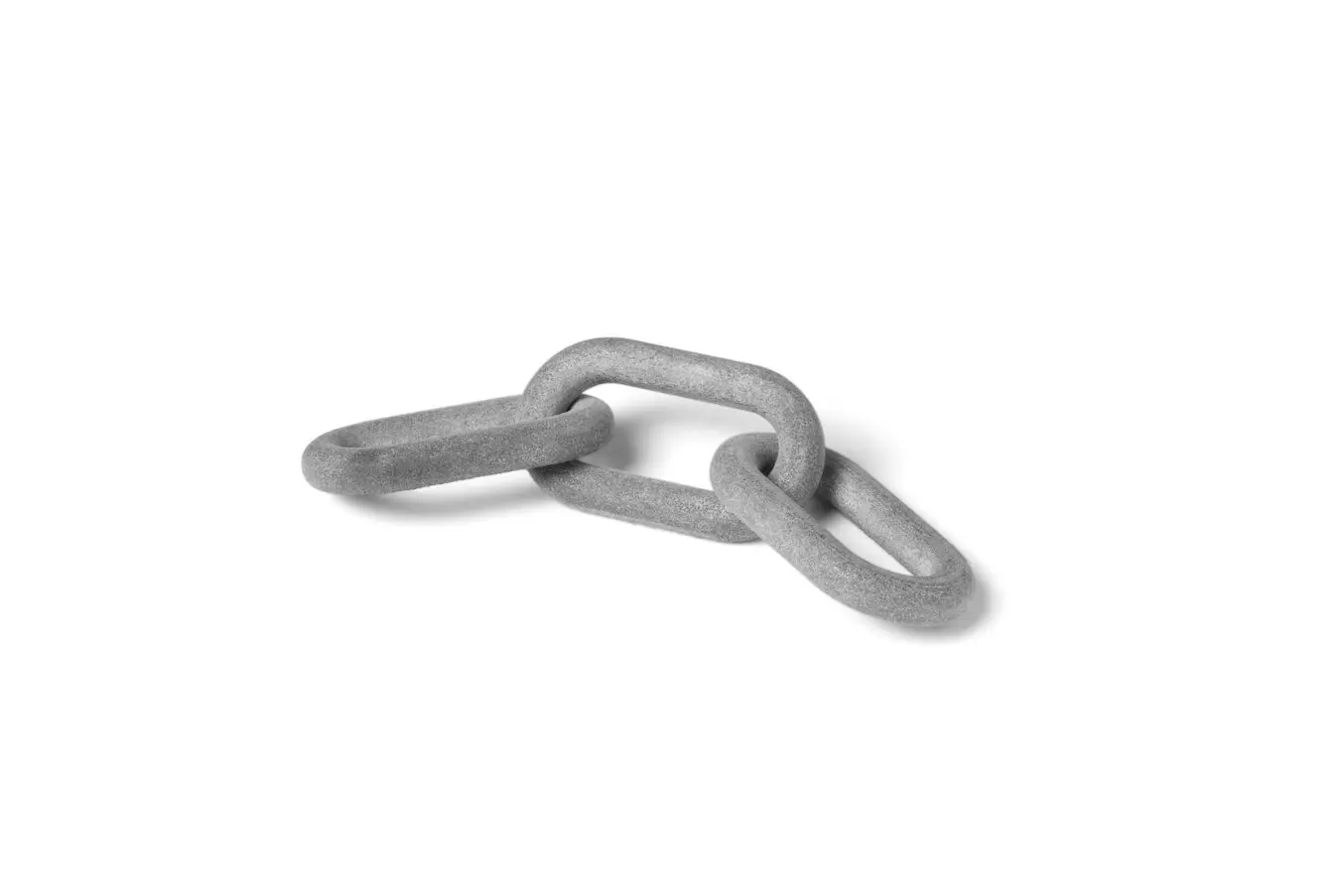
Richiedi un campione gratuito realizzato con la Nylon 11 CF Powder e sottoposto a burattatura
Questa catena a incastro realizzata tramite SLS è stata stampata interamente in posizione e sarebbe quasi impossibile da rifinire manualmente. La parte è stata sottoposta a burattatura durante la notte in un buratto vibrante DB-300 con triangoli di ceramica tagliati ad angolo. La superficie finita è ideale per la verniciatura, il rivestimento e la galvanizzazione.
Applicazioni delle parti SLS burattate
Molte applicazioni di stampa 3D richiedono una finitura superficiale liscia e un coefficiente di attrito ridotto. Aggiungere la burattatura al proprio workflow migliora sia la funzionalità che l'aspetto delle parti usate nei settori e nei contesti più disparati.
Burattatura di prodotti per utilizzo finale
Man mano che la tecnologia di stampa 3D rende la personalizzazione di massa sempre più una realtà, le applicazioni di stampa 3D ad alta produttività diventano sempre più comuni. L'ecosistema della serie Fuse consente la produzione di volumi medi e alti di prodotti per utilizzo finale che si comportano come parti stampate a iniezione, pur sfruttando la libertà di progettazione della tecnologia SLS.
La burattatura è un metodo a basso costo per ottenere una finitura superficiale paragonabile a quella dello stampaggio a iniezione, evitando ore di manodopera o di post-elaborazione manuale. Raggruppare le parti in un buratto più grande consente di ridurre i punti di contatto e di ottenere risultati ottimali. La burattatura prepara anche le parti a un ulteriore rivestimento, che può migliorare ulteriormente la funzionalità, la finitura e il colore delle parti realizzate con la stampa 3D SLS.
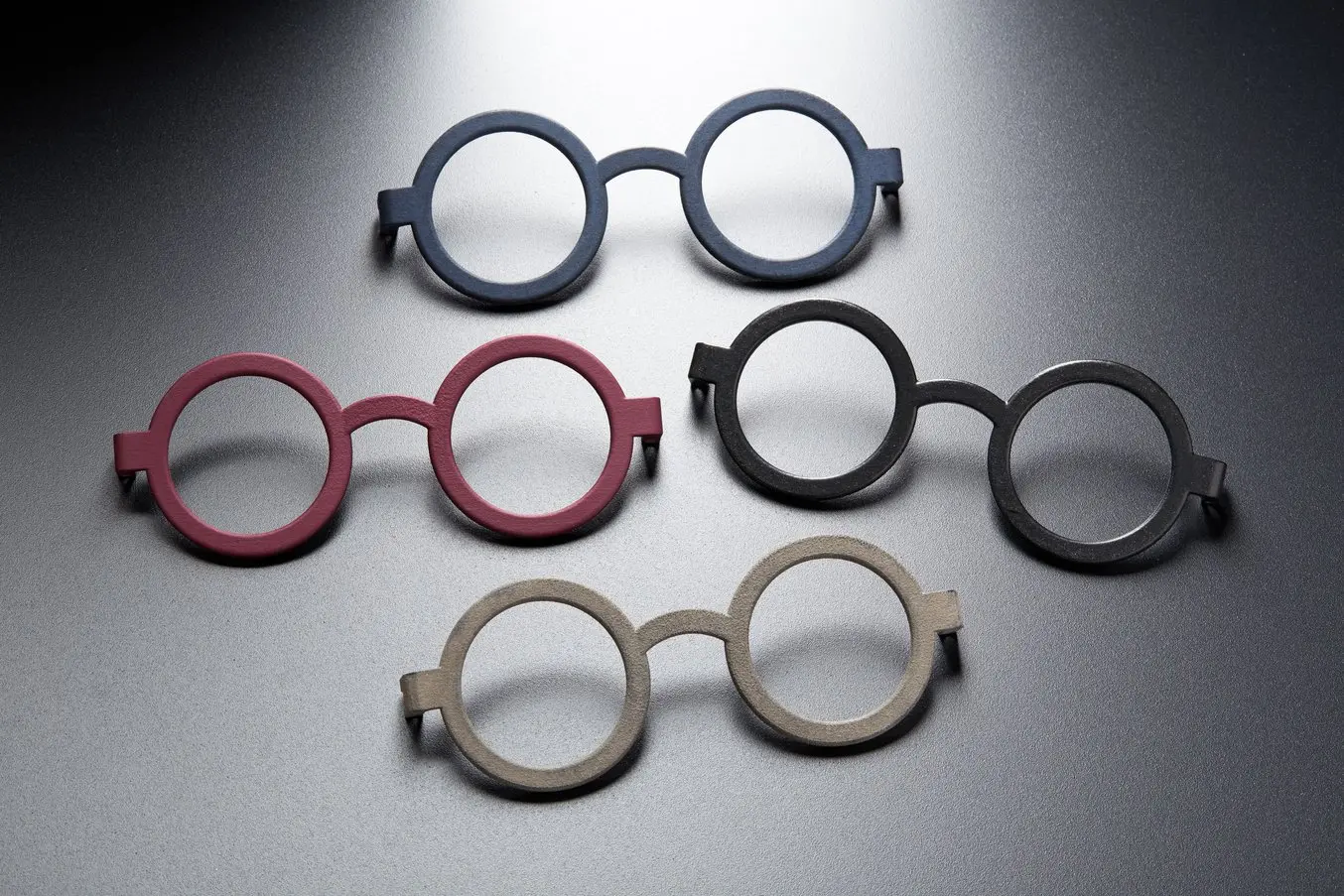
La burattatura è particolarmente indicata per migliorare la finitura superficiale e preparare le parti a una post-elaborazione successiva, come la tintura, la verniciatura o il rivestimento.
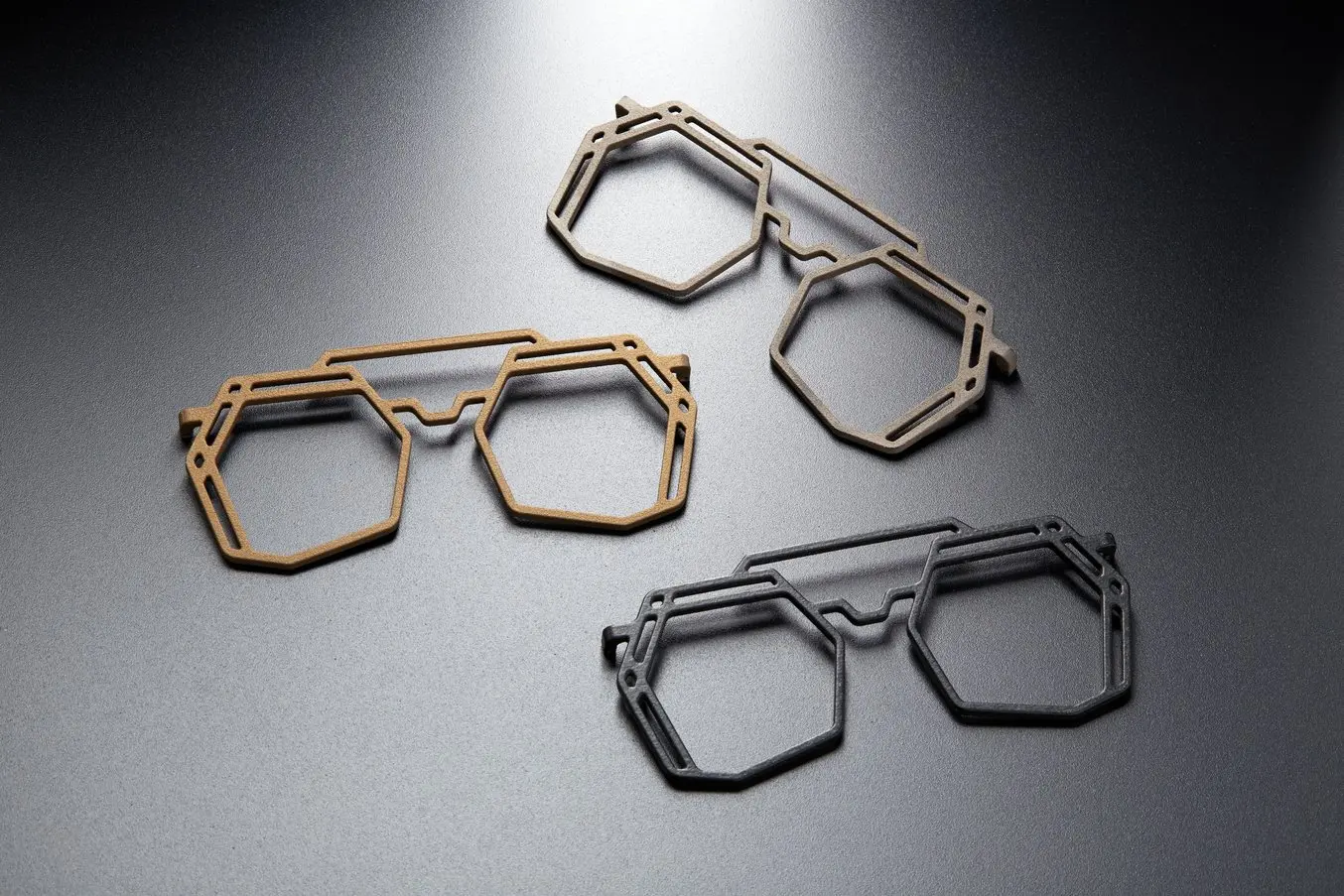
Le montature di occhiali per utilizzo finale sono un'applicazione in cui la burattatura esprime tutto il suo potenziale.
Burattatura per il settore medico
La stampa 3D applicata al settore medico favorisce l'innovazione in quasi tutte le specializzazioni, dalle protesi e ortesi personalizzabili alla produzione a basso volume di nuovi dispositivi medici. La ruvidità superficiale delle parti realizzate con la stampa 3D SLS può rappresentare un punto dolente per i clienti in ambito ortesico e protesico. La burattatura può contribuire a migliorare l'aspetto di tutori, ortesi e protesi.
Il tutore per polso raffigurato qui sotto è stato stampato con la Fuse 1+ 30W in Nylon 12 Powder e personalizzato per adattarsi all'esatta forma dell'avambraccio del paziente. Sebbene il file sia progettato per calzare comodamente e la parte finita abbia una tolleranza di 0,1 mm, avere una superficie più levigata permetterebbe al paziente di sentirsi più a suo agio. La burattatura migliorerebbe il livello di comfort e la porosità della superficie del dispositivo, aumentandone la resistenza all'umidità ambientale e rendendolo più funzionale.
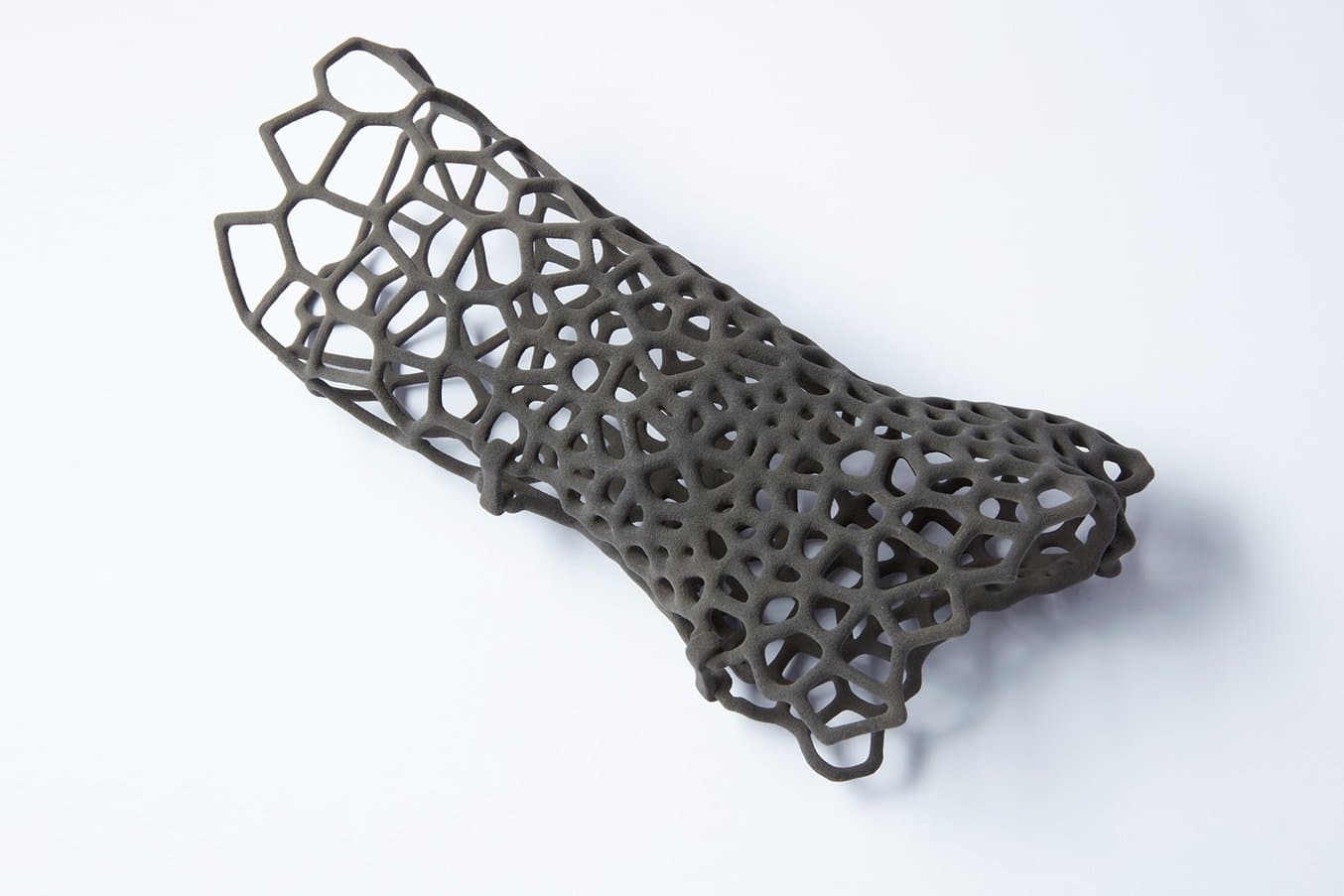
La burattatura migliora la vestibilità e la ruvidità superficiale delle parti realizzate con la stampa 3D SLS, come nel caso di questo tutore per braccio. Per i tutori, che sono molto visibili e spesso toccano direttamente la pelle dei pazienti, una finitura superficiale liscia, più simile a quella dello stampaggio a iniezione, può fare una grande differenza.
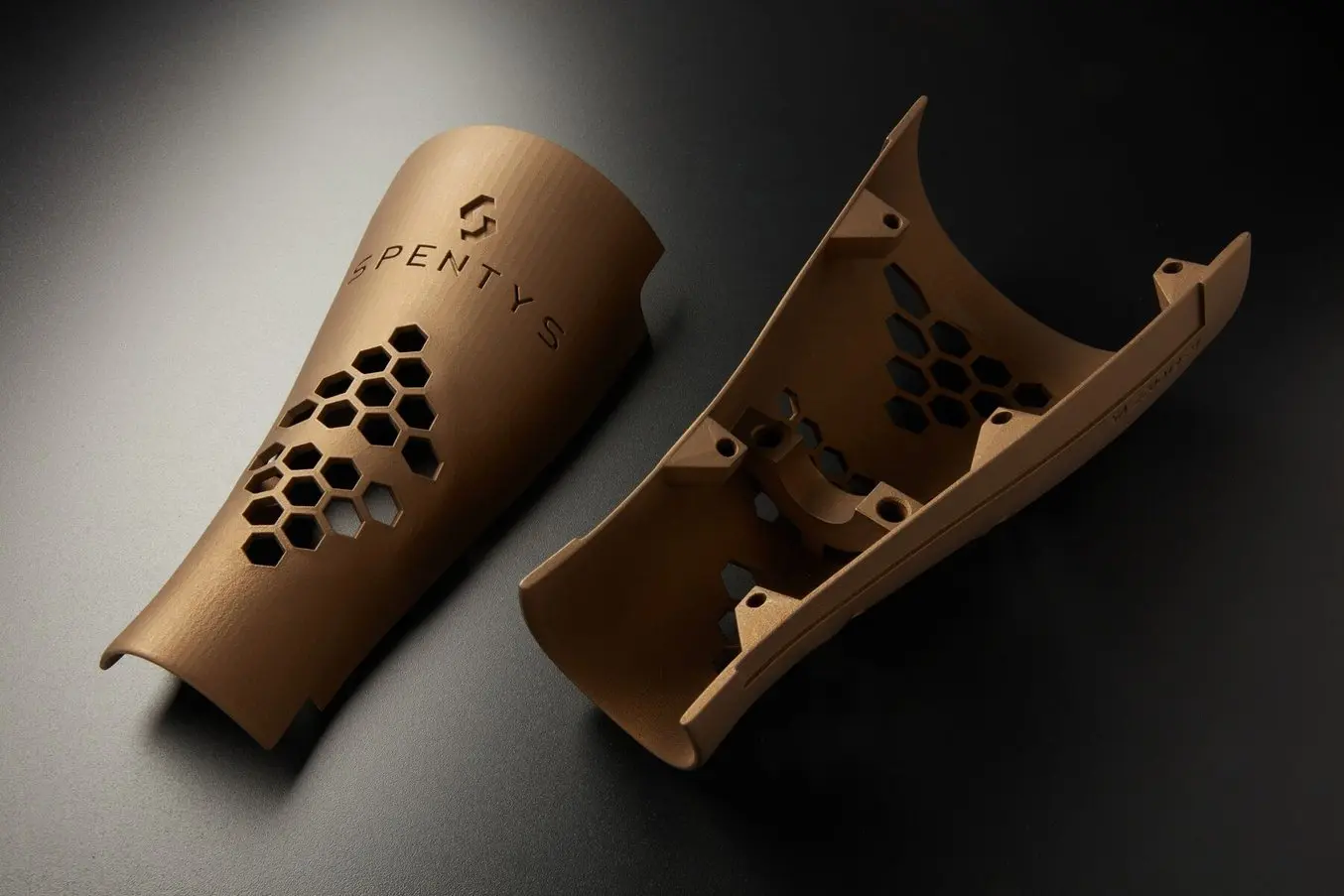
La burattatura aiuta anche a preparare la superficie al rivestimento: queste coperture estetiche Spentys (a destra) sono state burattate per otto ore con ceramica e poi trattate con Cerakote. Le coperture sono destinate a protesi per gli arti inferiori con l'obiettivo di fornire un rivestimento personalizzabile, in modo che l'utente possa scegliere coperture diverse a seconda dello stato d'animo e dell'abbigliamento.
Burattatura per supporti di produzione
I supporti di produzione sono spesso utilizzati in applicazioni a elevato attrito e come parte di assemblaggi negli stabilimenti di produzione. La burattatura può migliorare il coefficiente di attrito e aumentare la durezza della superficie, con una conseguente maggiore durata e un utilizzo più prolungato.
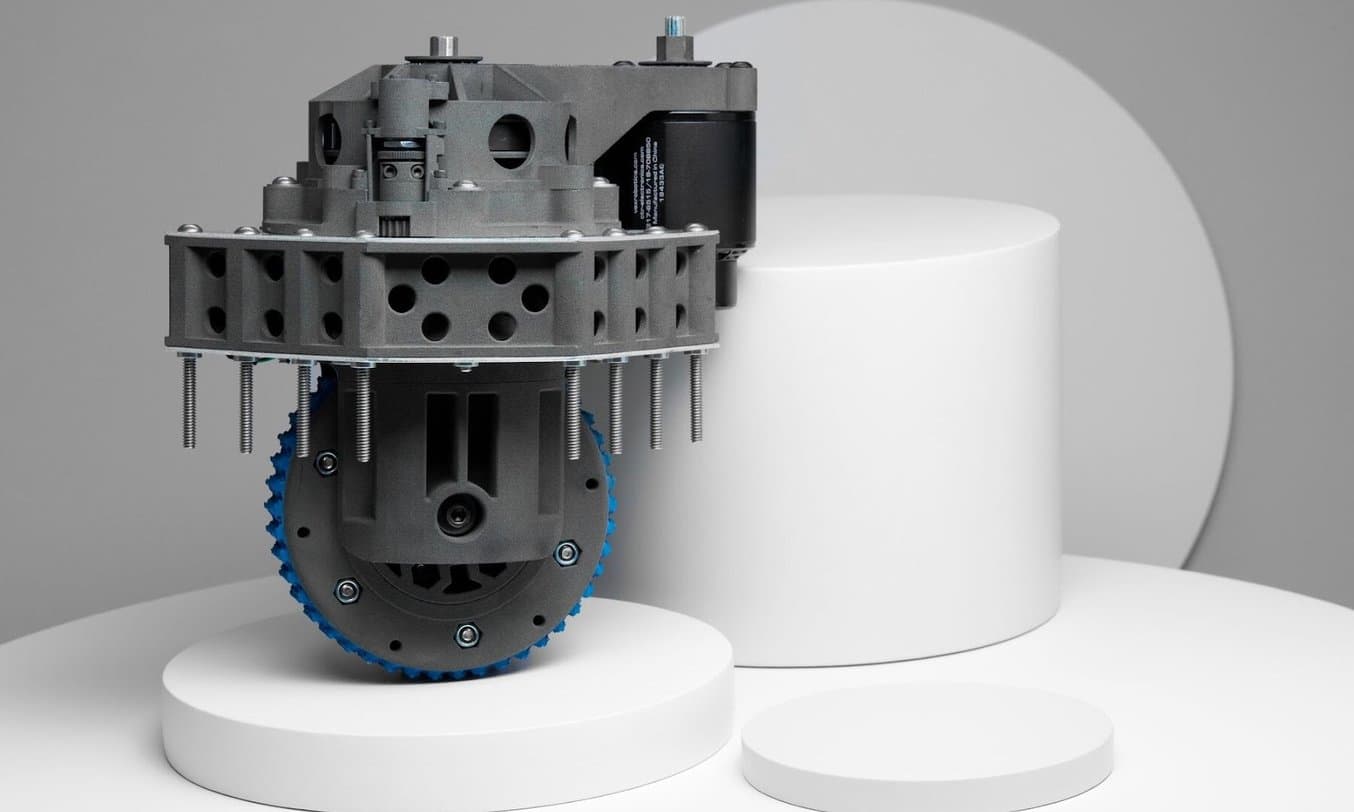
La burattatura incrementa la durata di assemblaggi complessi e supporti di produzione.
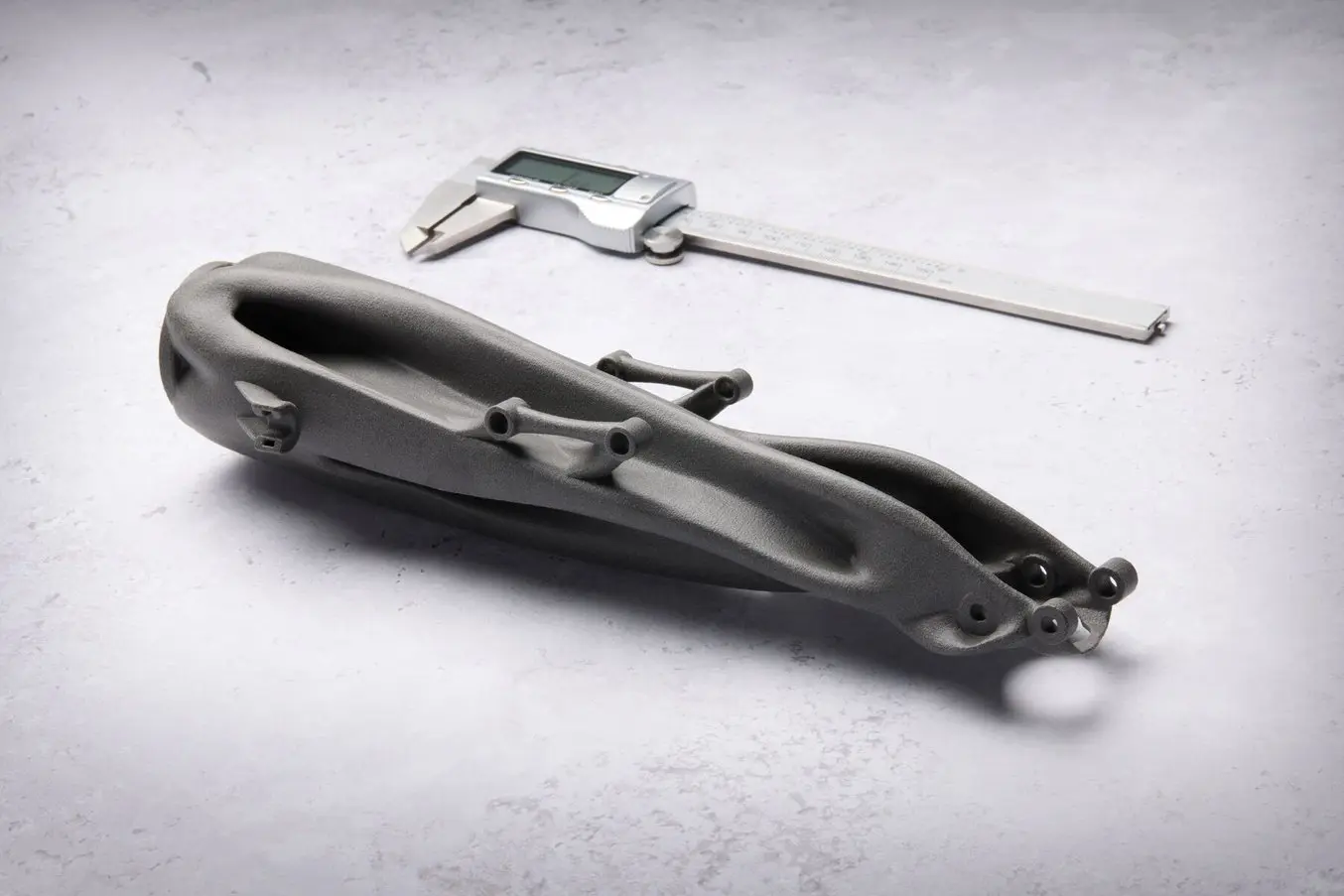
Gli strumenti per estremità di braccio robotico, come questo braccio robotico pick-and-place, possono trarre vantaggio dalla burattatura, che ne garantisce l'integrazione facile e senza attrito in macchinari e flussi di lavoro esistenti.
Test e risultati
Formlabs ha condotto test in-house approfonditi sulla burattatura utilizzando parti realizzate con la stampa 3D SLS, al fine di consigliare i flussi di lavoro più idonei per ottenere risultati ottimali.
Processo
Abbiamo stampato in 3D diverse parti sulla base di un design standard che presenta superfici piane e curve, nonché superfici interne ed esterne. Le parti sono state realizzate con la stampante 3D SLS Fuse 1+ 30W, mentre la polvere è stata rimossa nella Fuse Sift secondo le linee guida standard per la post-elaborazione. Le parti sono state stampate con la Nylon 12 Powder e con la Nylon 11 Powder.
A parte il numero di identificazione, tutte le parti erano identiche. L'accuratezza dimensionale di tutte le parti è stata misurata utilizzando calibri, mentre la ruvidità superficiale è stata misurata con un microscopio a scansione laser di Keyence.
Abbiamo scelto di eseguire il test principalmente in un buratto vibrante CB300, comunemente chiamato Mr. Deburr.L'apparecchio ha una capacità di burattatura di circa 0,084 metri cubi e funziona con un motore da 0,75 cavalli. Il Mr. Deburr costa 3500 $ ed è una buona scelta per le applicazioni ad alto rendimento. La capacità dell'apparecchio consente di burattare contemporaneamente più lotti di parti realizzate con la stampa 3D SLS, oppure una quantità inferiore di parti molto grandi. Il materiale utilizzato era costituito da pellet di ceramica a forma di triangolo tagliato ad angolo, con una dimensione dei lati di circa 0,63 cm. Per facilitare il processo, è stato usato un composto generico per la finitura. Il composto liquido scelto è stato "Kramco 1010", fornito da Kramer Industries. Si tratta di un liquido che funziona bene con la ceramica ed è ottimo per la rimozione di sbavature e il taglio leggero.
I componenti sono stati sottoposti a burattatura per due, quattro, sei e otto ore prima di essere rimossi e misurati nuovamente per determinare se e in che misura si fossero verificati cambiamenti nelle dimensioni e riduzione della ruvidità superficiale. La ruvidità superficiale è stata nuovamente misurata con un VR-5000 di Keyence. La rugosità è stata misurata in termini di Sa, ovvero la media aritmetica di una superficie. Il profilometro di Keyence rileva l'altezza media di una superficie e poi confronta la differenza di altezza di ciascun punto rispetto alla media. Le misure di precisione dimensionale sono state effettuate con calibri a corsoio a nonio con una precisione di ±0,02 mm. Questo ci permette di determinare la quantità di materiale rimosso dalle superfici durante il processo di burattatura. Il risultato può essere diverso se si utilizza un materiale, un detergente o un apparecchio diverso; inoltre esiste un'ampia gamma di materiali, forme e dimensioni differenti che possono incidere sui risultati. A seguito di un confronto con le principali aziende del settore, abbiamo scelto di utilizzare la ceramica per i nostri test.
Nota sugli apparecchi più piccoli
Per verificare l'efficacia di buratti base più piccoli, abbiamo effettuato i test anche su un modello più economico, che però non ha prodotto gli stessi risultati del Mr. Deburr, probabilmente poiché agitava i materiali in maniera meno aggressiva. Tuttavia, il buratto più piccolo è riuscito ugualmente a lucidare le parti, con una riduzione di circa il 70% della ruvidità superficiale in 48-72 ore. Questi risultati non sono stati inclusi nelle nostre tabelle per evidenziare l'efficacia degli apparecchi più grandi e la loro efficienza per volumi di queste dimensioni.
Risultati con il Mr. Deburr
Sia le parti realizzate in Nylon 11 Powder che quelle in Nylon 12 Powder hanno ottenuto una riduzione della ruvidità superficiale superiore all'80% dopo otto ore di burattatura, mentre alcune parti hanno raggiunto lo stesso risultato in meno di quattro-sei ore.
Un dato fondamentale: le parti in Nylon 11 Powder e in Nylon 12 Powder avevano ruvidità superficiali diverse sia all'inizio che alla fine del processo, ma le loro variazioni proporzionali sono state abbastanza simili. Durante le nostre prove, è emerso che le parti in Nylon 11 Powder hanno una ruvidità superficiale iniziale media di circa 35 µm, mentre quelle in Nylon 12 Powder hanno una ruvidità superficiale iniziale di circa 26 µm. Le parti in Nylon 12 Powder si sono ridotte di 4 µm, mentre quelle in Nylon 11 Powder si sono ridotte di 5,5 µm. In termini di materiale rimosso complessivamente, la Nylon 11 Powder (0,12 mm) ha riportato un'usura leggermente inferiore rispetto alla Nylon 12 Powder (0,15 mm) durante le otto ore di burattatura. Si tratta all'incirca della stessa ruvidità superficiale delle tubazioni commerciali in acciaio.
Osservando entrambi i grafici che confrontano la riduzione della ruvidità superficiale con il tempo di burattatura, è evidente che sia il tasso di levigatezza che la quantità di materiale rimosso all'ora diminuiscono. Per entrambi i materiali, non sembra che la ruvidità superficiale si stabilizzi e ipotizziamo che, se prolungassimo la burattatura, i valori di Sa continuerebbero a diminuire, ma a velocità sempre più ridotte.
Visivamente abbiamo notato diversi cambiamenti al prolungarsi dei tempi di burattatura: gli angoli e i bordi più duri si sono leggermente arrotondati, le estrusioni più sottili e le goffrature più dettagliate si sono leggermente consumate e il materiale ha cominciato a depositarsi in fori e fessure in prossimità della soglia delle 72 ore.
Risultati della burattatura di parti in Nylon 12 Powder
Tempo di esecuzione (ore) | Perdita di materiale superficiale (mm) | Ruvidità superficiale (Sa) | Riduzione della ruvidità superficiale (%) |
---|---|---|---|
0 | N/A | 25,687 | 0% |
2 | -0,108 | 10,393 | 59,54% |
4 | -0,126 | 6,314 | 75,42% |
6 | -0,139 | 6,168 | 75,99% |
8 | -0,150 | 4,513 | 82,43% |
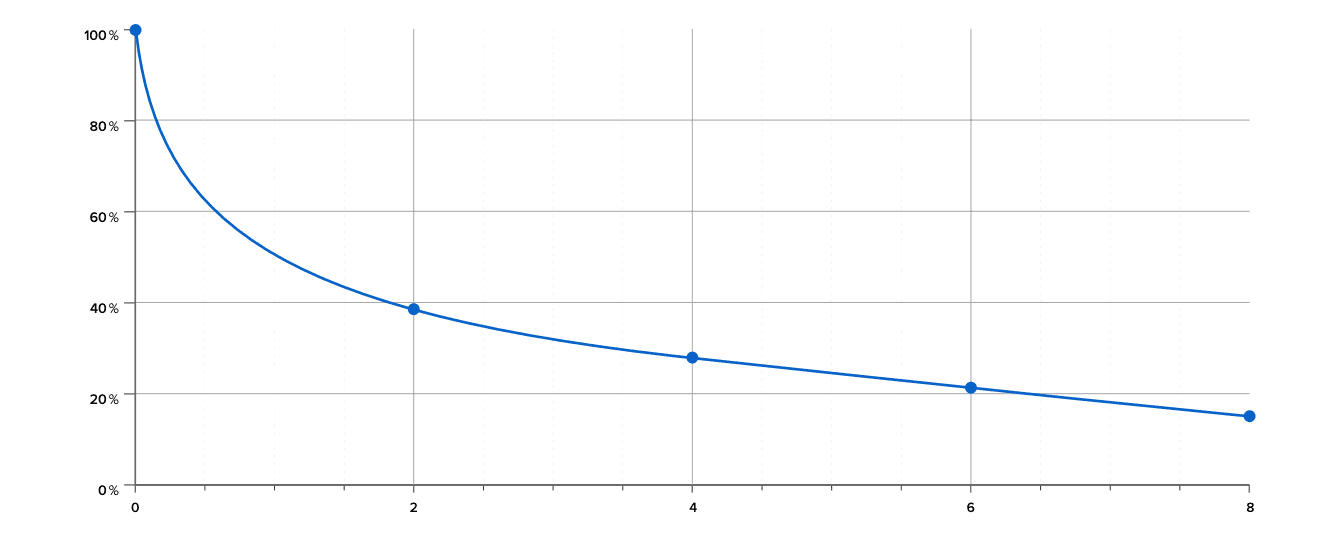
Risultati della burattatura di parti in Nylon 11 Powder
Tempo di esecuzione (ore) | Perdita di materiale superficiale (mm) | Ruvidità superficiale (Sa) | Riduzione della ruvidità superficiale (%) |
---|---|---|---|
0 | N/A | 35,081 | 0% |
2 | -0,046 | 11,916 | 66,03% |
4 | -0,081 | 10,056 | 71,43% |
6 | -0,106 | 8,367 | 76,15% |
8 | -0,120 | 6,712 | 80,87% |
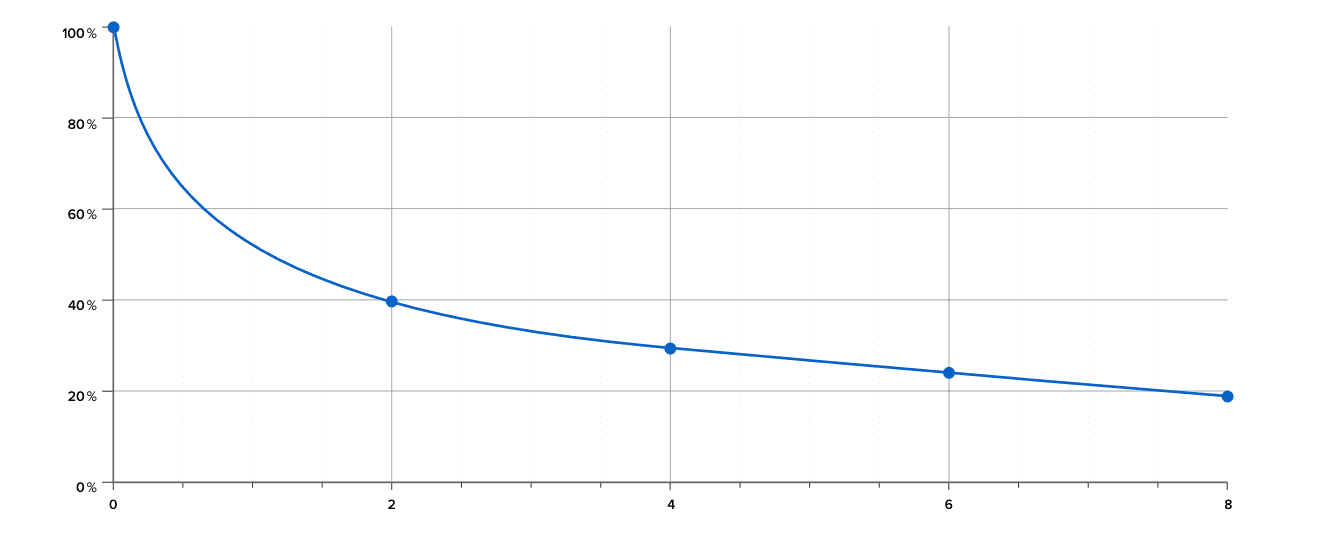
Consigli
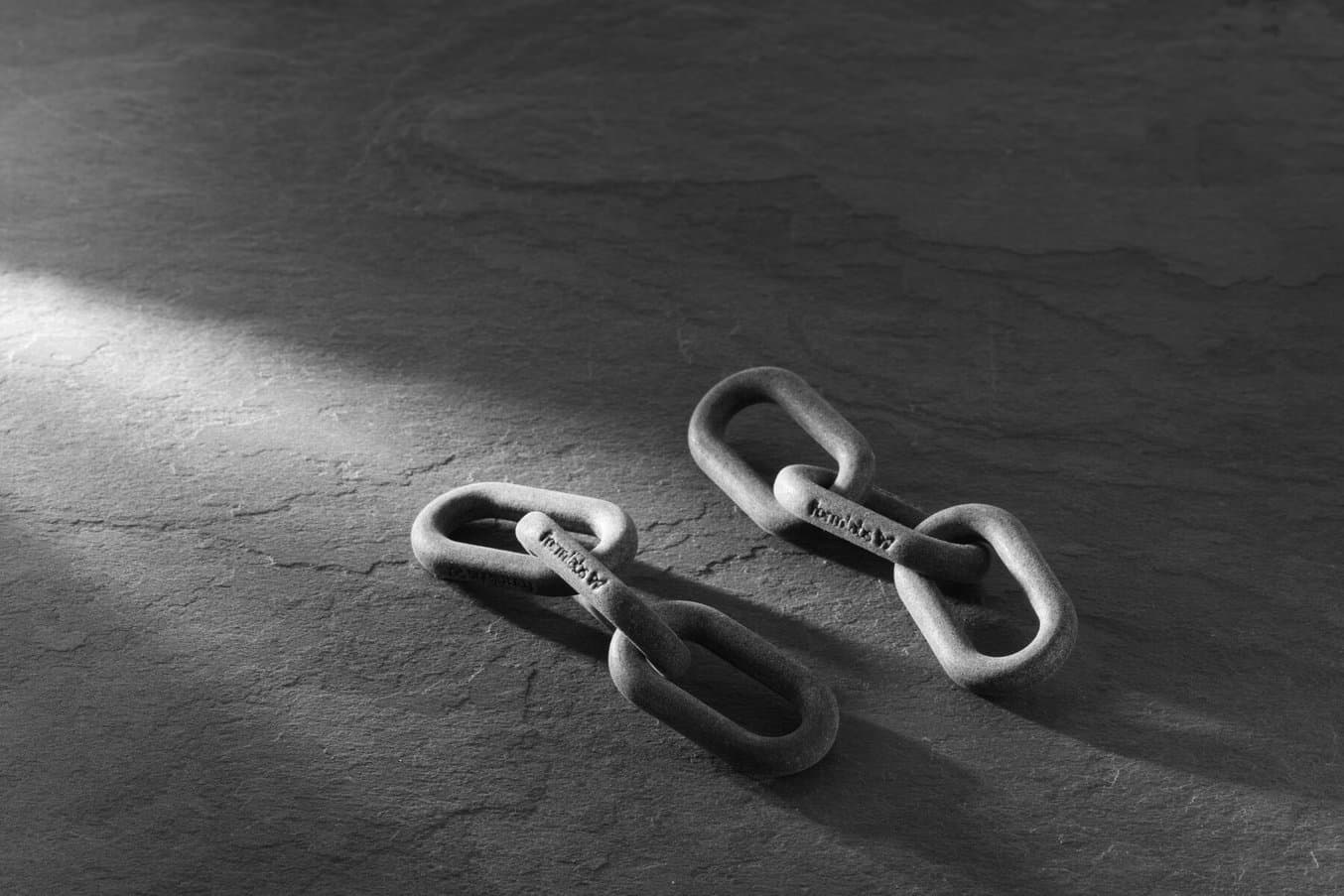
La burattatura è un metodo eccellente per migliorare la finitura superficiale delle parti stampate in 3D. Le attrezzature sono convenienti e il flusso di lavoro è personalizzabile in base alle proprie esigenze. Quando si aggiunge la burattatura al flusso di lavoro, bisogna tenere presente che apparecchi e materiali diversi producono risultati diversi.
Prima di scegliere il buratto da acquistare per un flusso di lavoro della stampa 3D, bisogna prima considerare il volume di parti stampate in 3D: volumi di produzione medio-alti richiederanno un buratto industriale più grande, mentre per prototipi, supporti di produzione e applicazioni per la creazione rapida di attrezzature sarà sufficiente un buratto più piccolo ed economico. In queste applicazioni, i tempi maggiori richiesti dal buratto più piccolo non dovrebbero influire negativamente sul flusso di lavoro.
La scelta del materiale è il passo successivo e dipende molto dalla parte. Per le parti realizzate con la stampa 3D SLS vanno bene ceramica, plastica o materiali organici, mentre il metallo potrebbe essere troppo abrasivo. Nel caso di parti con molte fessure o canali interni, la ceramica potrebbe sfaldarsi e incastrarsi nelle parti. Sebbene la rimozione sia semplice utilizzando piccoli strumenti manuali, la scelta migliore potrebbe essere quella di ricorrere a materiali organici o plastici. Per le parti con particolari molto piccoli, goffrature delicate o estrusioni sottili, è preferibile utilizzare un materiale meno abrasivo. Allo stesso modo, la scelta di materiali arrotondati anziché appuntiti contribuirà a proteggere le parti più delicate.
Inizia a usare la stampa 3D e la burattatura
La burattatura è un metodo accessibile per rendere le parti realizzate con la stampa 3D SLS più simili, per aspetto e funzionalità, a quelle stampate a iniezione. Aggiungere questo processo al flusso di lavoro della stampa 3D non è necessariamente complicato o costoso: esistono molti buratti a prezzi contenuti e accessibili in termini di ingombro e requisiti di alimentazione. Per applicazioni come la prototipazione rapida, i supporti di produzione o le parti per utilizzo finale, la burattatura amplia la gamma di possibilità della stampa 3D. Abbinata alla libertà geometrica della stampa 3D SLS e alle capacità di personalizzazione di un flusso di lavoro di produzione a volumi ridotti, la burattatura offre vantaggi in tutti i settori.
Per sapere di più su come ottimizzare il flusso di lavoro SLS e di burattatura o per ricevere i consigli degli esperti sugli apparecchi e i materiali più adatti alle tue esigenze specifiche, contatta il team vendite di Formlabs. In alternativa, scopri le opzioni di post-elaborazione delle parti SLS sul nostro sito Internet.