Global Automotive Supplier Brose Turns to SLS 3D Printing to Produce End-Use Car Parts
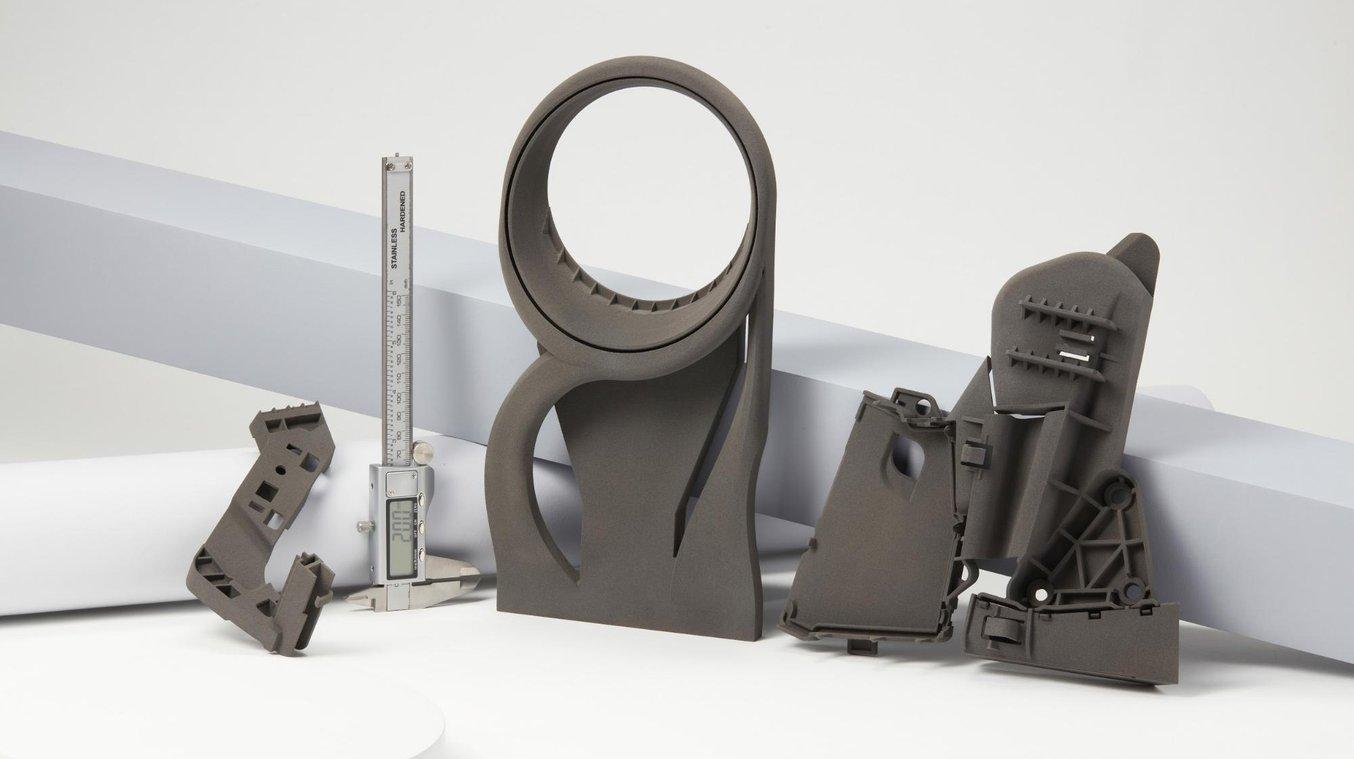
If you have ever sat in a car, it’s safe to say that you’ve most likely interacted with one of Brose’s products. With 25,000 employees in 24 countries, the company is one of the largest family-owned Tier 1 automotive suppliers, working with 80 automotive brands, over 40 suppliers, and 50 e-bike manufacturers.
Every other new vehicle worldwide is equipped with at least one Brose product, including various mechatronic components and systems, such as seat structures, door components, and various electric motors and drives.
As one of Germany’s most innovative companies, Brose is in an excellent position to integrate additive manufacturing (AM) into their products and manufacturing workflow. They use various AM technologies for prototyping, tools, and fixtures, and their next objective is to go into serial production. The latest addition to their printing fleet, the Fuse 1, the first benchtop industrial selective laser sintering (SLS) 3D printer from Formlabs, is one of the tools that will support them on this path.
Read on to learn from Christian Kleylein, technologist for AM Polymer Series Manufacturing at Brose, about his experience with the new device and how they plan to use 3D printing for serial manufacturing.
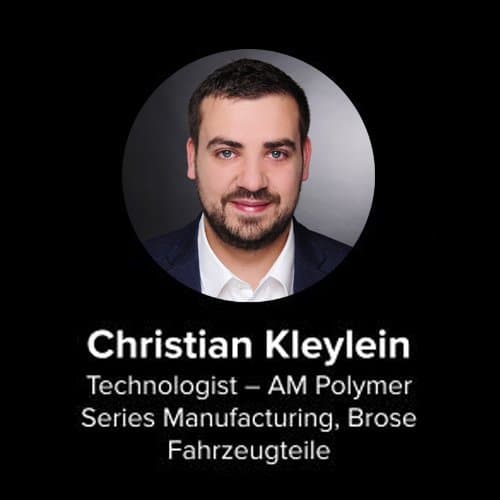
3D Printing at Scale With Two Automotive Giants
Watch our webinar with Christian Kleylein, Technologist at Brose and Bruno Alves, Additive Manufacturing Expert at Ford to see how 3D printing is powering innovation across the automotive industry.
Using the Fuse 1 in an Industrial Environment
Additive manufacturing is one of the newer core competencies of Brose. Their AM center in Germany is a one-stop-shop for prototyping, process development, material development, and validation, that provides parts globally.
They started more than ten years ago with their first fused deposition modeling (FDM) 3D printer, but have rapidly expanded their capabilities since then to almost all AM processes on the market, from stereolithography (SLA) to jetting processes, selective laser sintering, and a large machine park of metal 3D printers.
Brose’s printing fleet is equipped with various SLS printing systems, from small desktop machines to the largest traditional industrial printers. They have vast experience with the technology, and were one of the first companies to get their hands on the Fuse 1 in Europe.
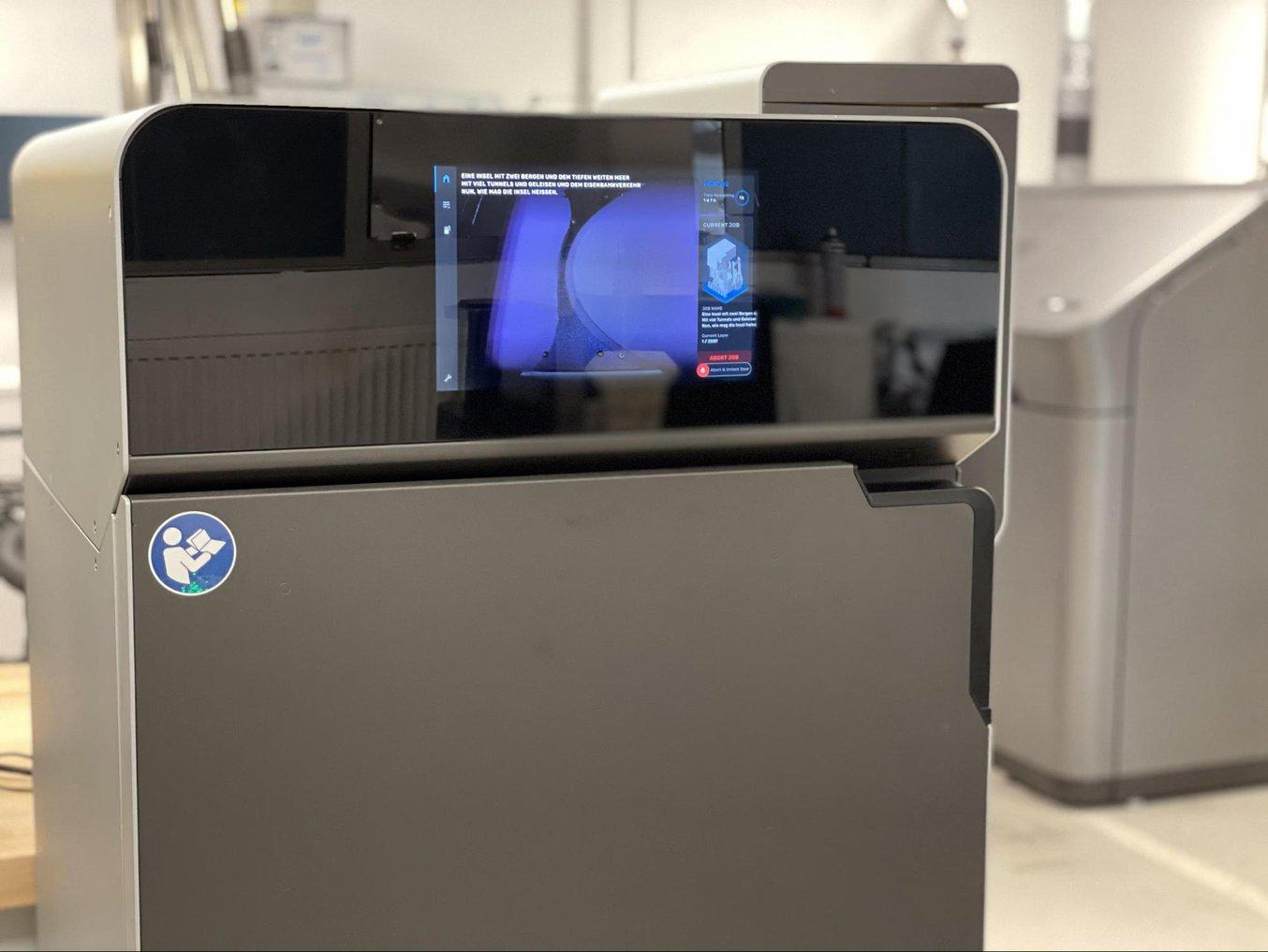
Brose’s AM center is equipped with almost all the 3D printing processes on the market, including their newest addition, the Fuse 1.
While it might take a week to get a bigger machine set up and running, Kleylein found the process for setting up the Fuse 1 straightforward.
“The setup is very easy. If you have an enclosed room with air conditioning, you're basically set to go. It doesn't have a lot of space requirements so that's very good. There's no real calibration needed; all you need to do is make sure it stands level. You plug it in and you start the set-up process and print on the delivery day,” said Kleylein.
“The learning curve is easy. Your first print probably is going to be successful. And then you can start tweaking and getting to know the machine.”
Christian Kleylein
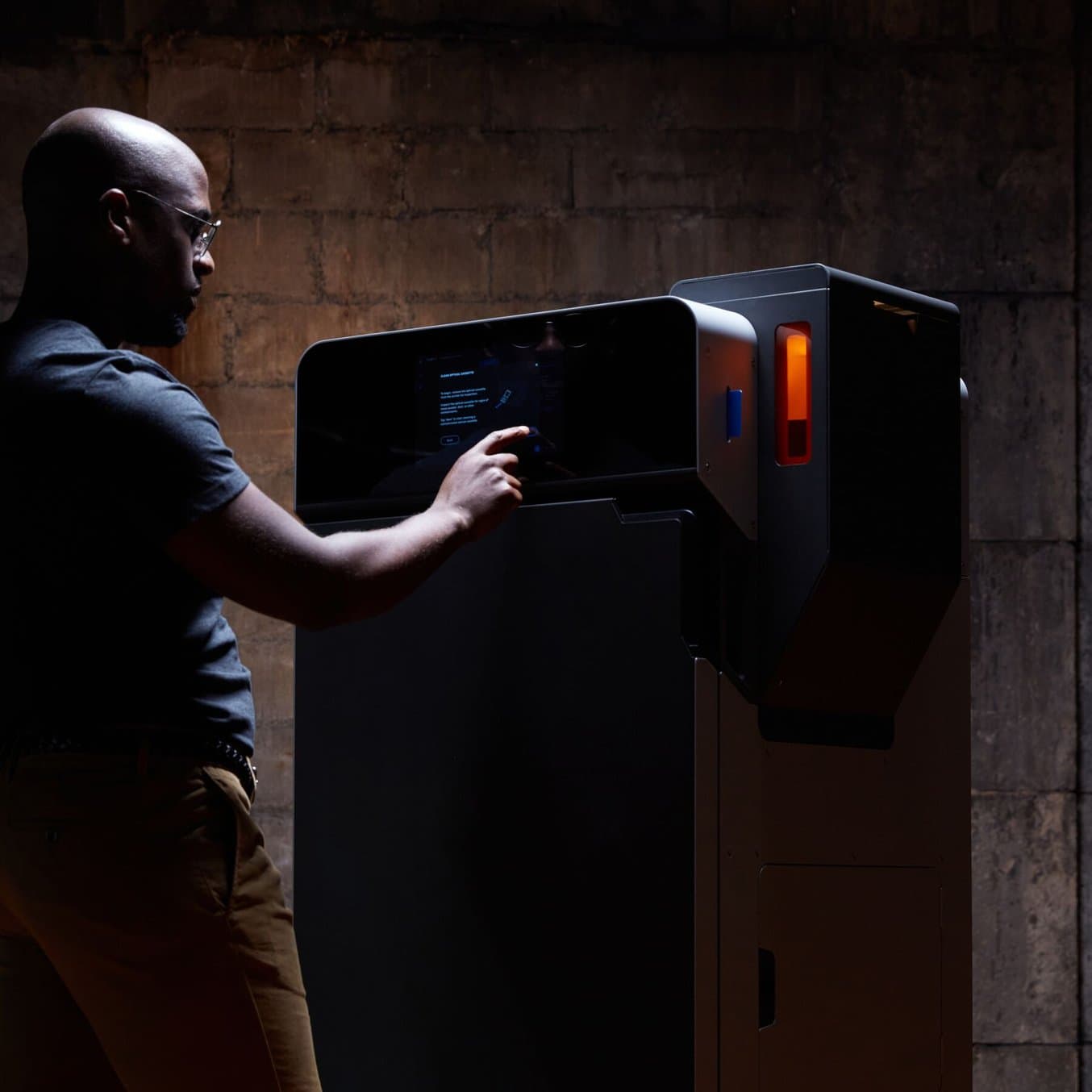
Outsourcing vs. In-House: When Does it Make Sense to Bring SLS 3D Printing In-House?
In this white paper, we evaluate the value proposition of bringing SLS 3D printers in-house, in comparison with outsourcing SLS parts from a service bureau.
“We've tested the Fuse very intensively. We've been printing a lot of the parts with the minimum thickness, and also very thin and very long [designs]. From testing the parts, we saw that even when the dimensions of the parts were off, they veered off always in the same ways. So once you optimize the process, you're going to get very dimensionally accurate parts at the end,” said Kleylein.
The team has run many prints on the Fuse 1 to test its limits, from short overnight builds of around 12 hours to fully packed build chambers with more than 1000 small parts that took four days.
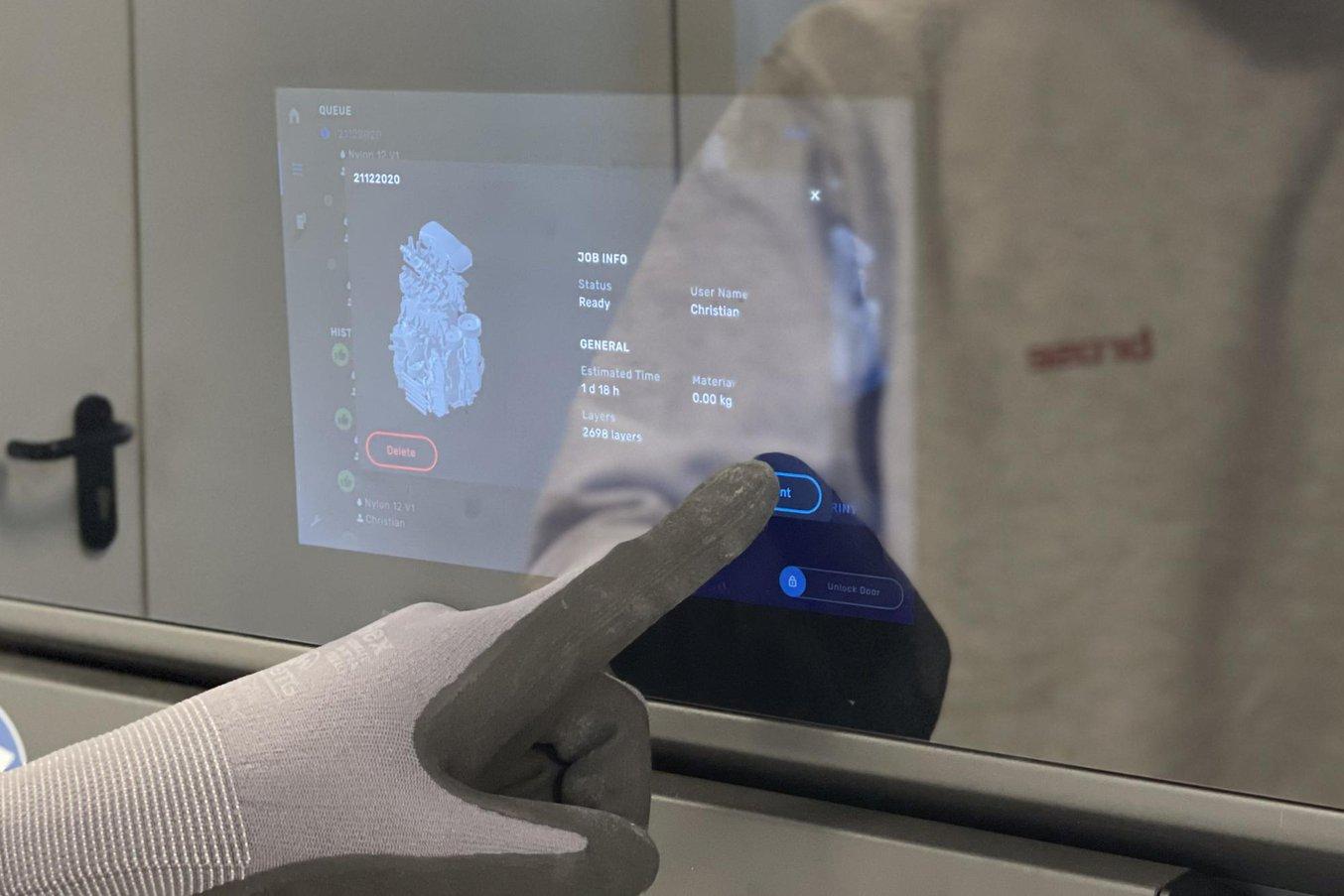
Selective laser sintering does not require support structures because unsintered powder surrounds the parts during printing. Multiple parts can be tightly arranged during printing to maximize the available build space.
“The surface finish is very nice, very smooth, you see very few layers, so you can use the parts once they come out of the printer and they've been blasted to get the last bit of powder off. You can do a lot of very fine details. So, for example, if you print gears, you get really nice round parts,” said Kleylein.
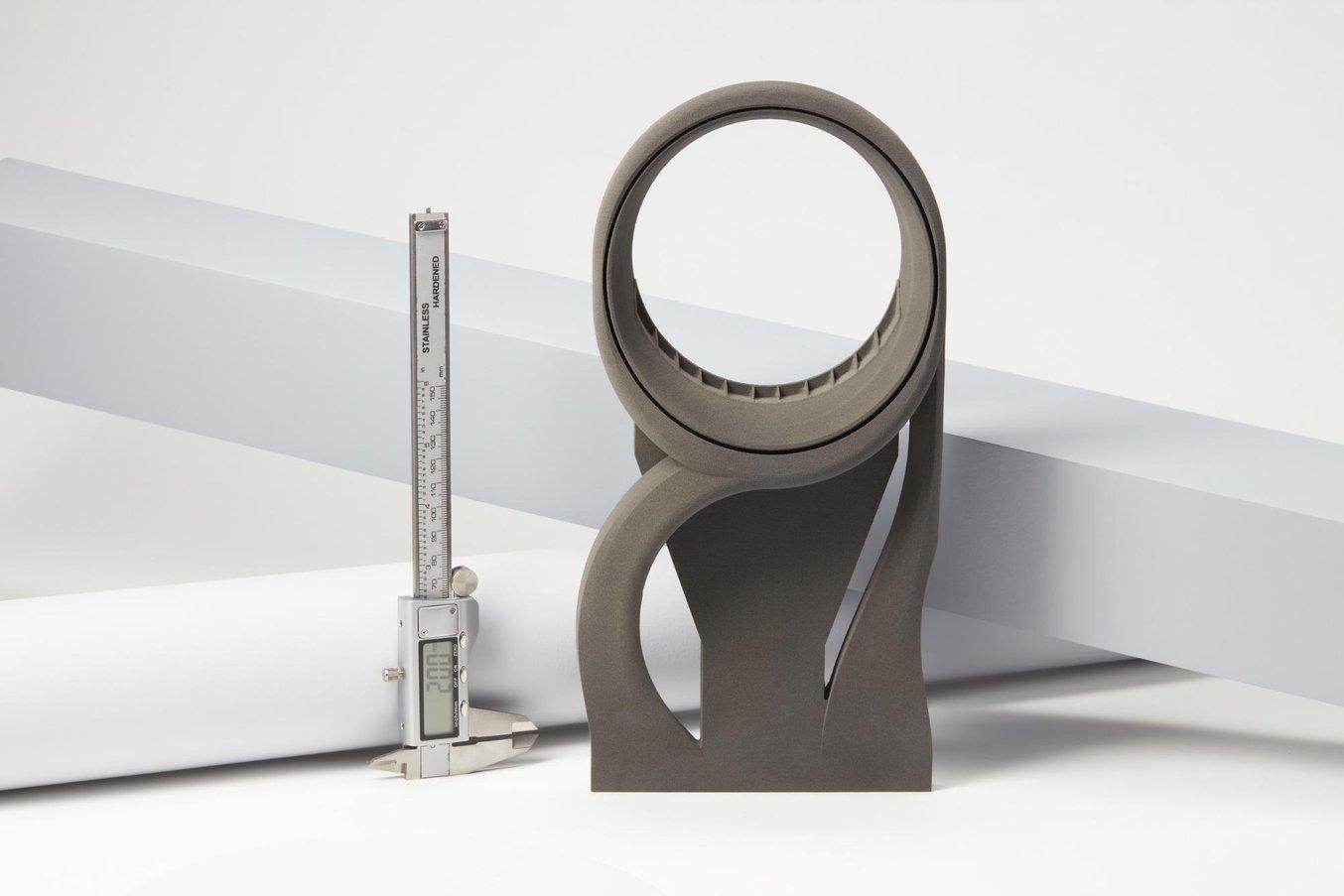
An end of line testing equipment for Brose machines during assembly.
With the Fuse 1, Formlabs aims to bridge the gap between traditional industrial SLS printers and low-cost smaller format printers by offering high quality, compact footprint, and a complete, simplified workflow at a fraction of the cost of traditional industrial SLS systems.
“It's more comparable to industrial printers than to one of the desktop machines. Because you have your fiber laser, Formlabs has developed its own optical scanner system, and the laser beam is deflected in the right way,” said Kleylein.
“It's a machine. It doesn't feel like a toy, it feels like a proper work tool. If you open the door, it looks industrial, and it all works. In the testing [team], they're very happy. You can use it in an industrial environment very easily.”
Christian Kleylein
One might think that larger printers are more suitable for automotive parts, but Kleylein found that the Fuse 1’s build volume is sufficient for most of their designs.
“80% of the parts that we print are about the size of a fist, that's the maximum. So we can print all those parts with the Fuse 1. There are a few parts in-between, and the rest is really big,” said Kleylein.
“The print speed is good, it’ll probably go faster after optimization. But for a starting point, you have a good print speed, and you have the right build space for defined applications,” said Kleylein.
The Fuse 1 also comes with Fuse Sift, a post-processing station that combines part extraction, powder recovery, storage, and mixing in a single free-standing device.
“In the past, with certain machines, the post-processing equipment was an add-on. That's something people have designed themselves, even the mixing. [Fuse Sift] is a nice integrated system. You have all those fans to extract the dust, restrictive personal safety equipment can be kept to a minimum. It sifts the powder, so everything that's too large to go through the sift, you just collect for recycling. The powder is mixed here and you're free to actually do your own refresh rate. If you need certain properties, you can print 100% fresh powder or you print 100% old powder. You put it on the mixer, and it also makes your powder well-dispersed,” said Kleylein.
Kleylein found that producing SLS parts on the Fuse 1 is generally hands-off, only requiring limited time and effort to prepare the new build, maintain the printer, and post-process the parts.
“You can put it in a small workshop, so that way you have a person that only uses a quarter of their time to actually run the workshop. The free software is good, and the printing process is comparable to the larger printers, so it's quick to prepare,” said Kleylein.
“It's easy, very well thought-through. You can restart the printer within 30 minutes.”
Christian Kleylein
“It's one of those machines that is very capable of print farming. It's very plannable; we can keep it running continuously. 24/7 printing is a big advantage. We don't have idle time here, the only idle time is if our build job is not full enough and it stops on the weekend,” said Kleylein.
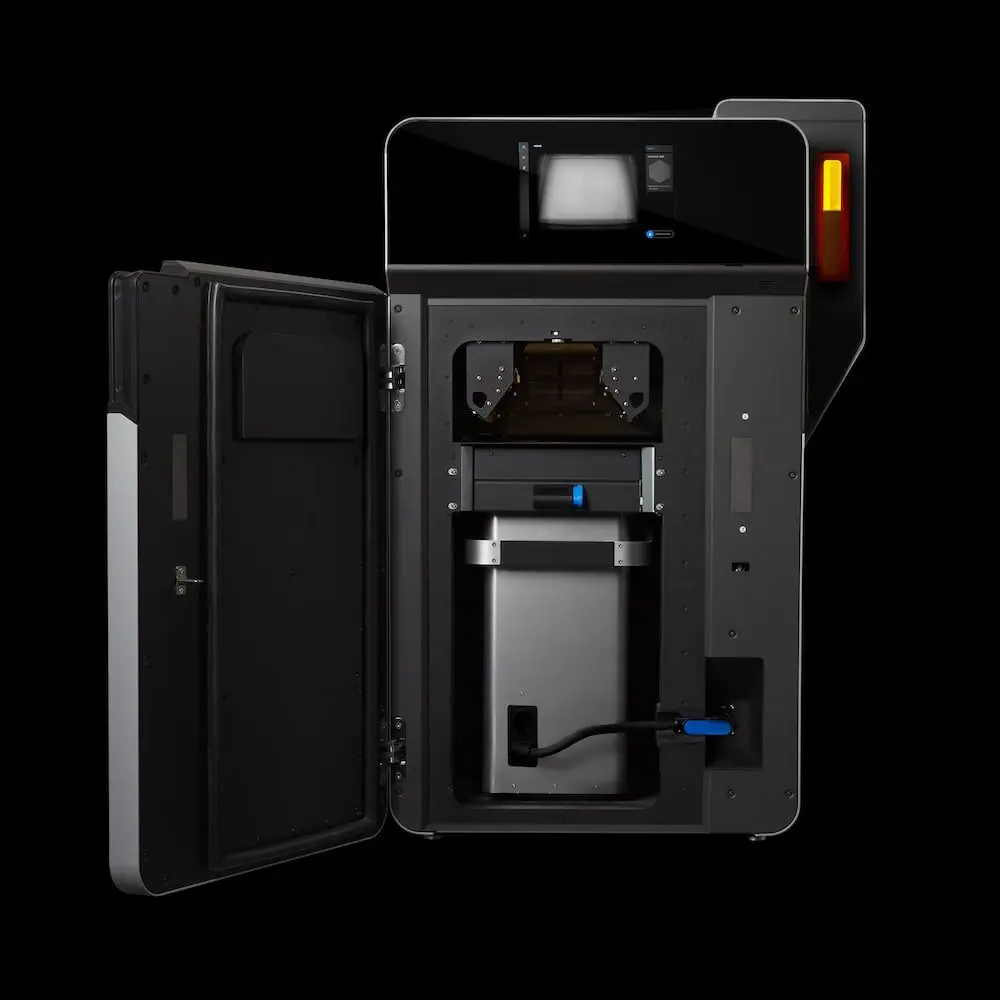
Fuse 1 Product Demo
Watch our product demo for a walkthrough of the Fuse 1 and SLS 3D printing with Formlabs experts.
SLS for End-Use Applications: Spare Parts and Parts for End-of-Life Products
At first, Brose is planning to use the Fuse 1 for functional prototyping to benefit from the fast turnaround and the material, Nylon 12, which offers similar properties to their current production materials. But Kleylein’s team is already validating parts and building cases for the first end-use applications, with the prime candidates being spare parts and parts for end-of-life products.
After a car model gets retired, automotive suppliers still have an obligation to provide spare parts. Traditionally, this means trying to estimate how many spare parts they’ll need, injection molding all of them, and then putting them into storage.
“That's a big waste of resources, a big waste of space, and a big waste of money. If we 3D print them, we don't need to store the injection molds and the parts for the next 15 years. There's a lot of demand for spare parts and end-of-life parts, because products always run out, and we do have a lot of plastic injection-molded parts. If we can stack them nicely and bring the build up to a very high density, it gets cost-efficient,” said Kleylein.
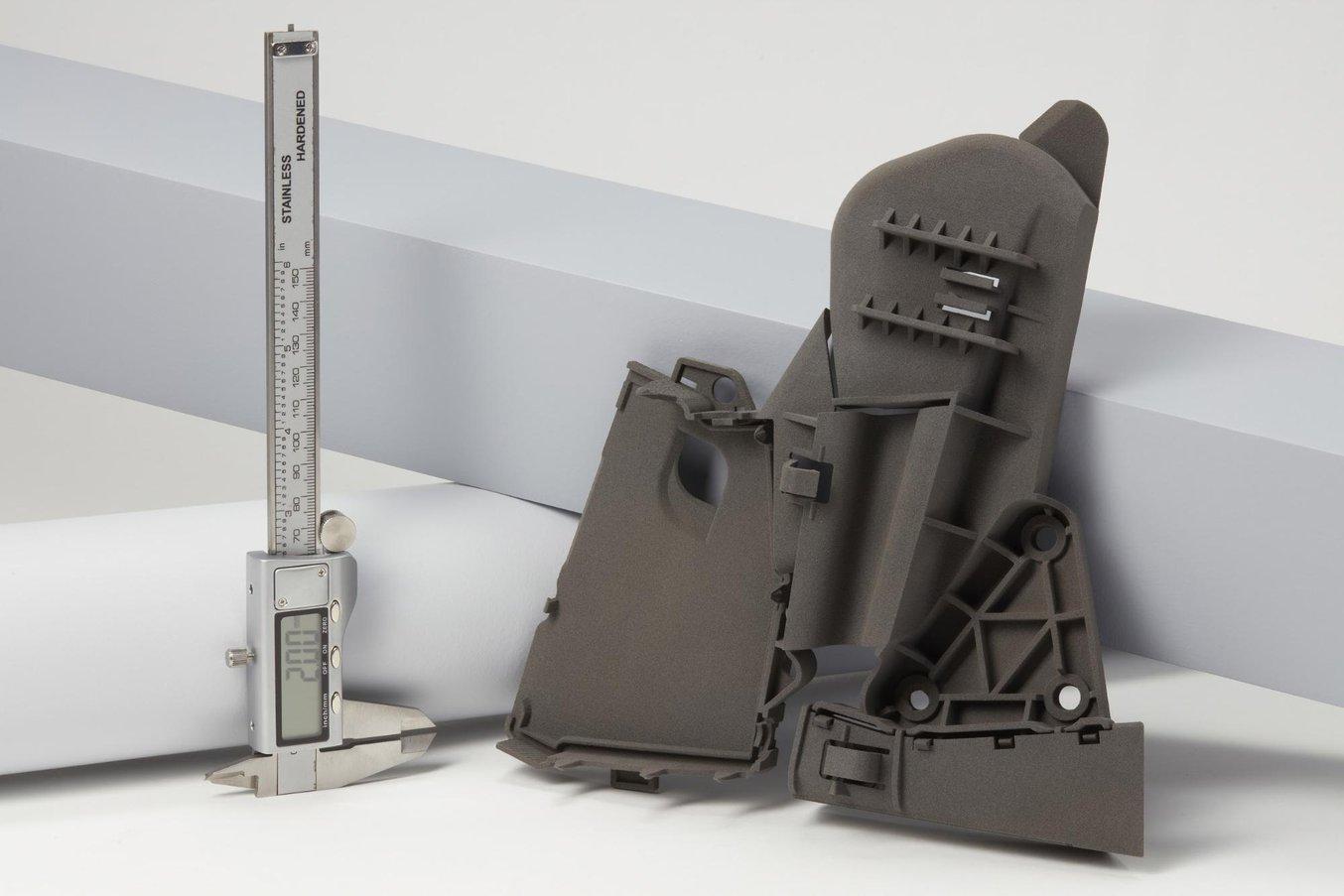
A 3D printed door handle module spare part that is traditionally injection molded.
“In automotive, it is important that you deliver the highest possible quality at the best price possible. At the moment, anything under 10,000 parts per year could be printed in SLS.”
Christian Kleylein
SLS is an ideal technology for production from many aspects:
-
It can create high-quality parts with properties similar to injection molded parts.
-
It can be implemented in a production setting.
-
It’s one of the least wasteful and the cleanest AM process, which is becoming increasingly important for manufacturing.
“You can use technical polymers, so you can build up technical parts, and you don't have to use supports. Post-processing is very clean as well, you take most of the powder off your part before you blast it,” said Kleylein.
“Some of Brose’s customers are very open to it, they do like the idea because we're trying to print with virtually no waste. We can reuse the powder and don't have to throw it away. You don't have any other chemicals either that you need to recycle. By the end of next year, all our SLS machines are expected to run on zero waste,” said Kleylein.
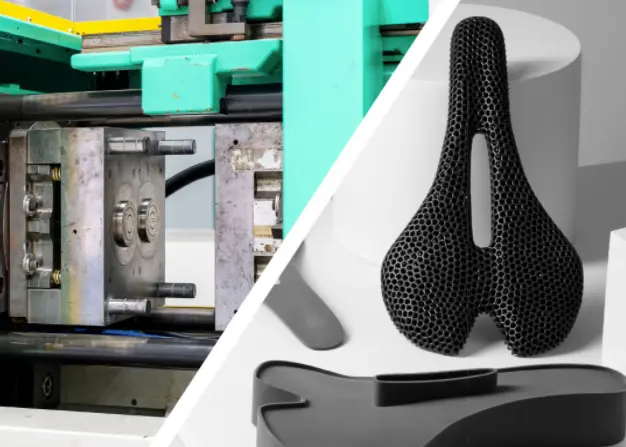
SLS 3D Printing vs. Injection Molding: When to Replace Molded Parts With 3D Printing?
This white paper showcases the cost-dynamics for real-life use cases, and presents guidelines for using SLS 3D printing, injection molding, or both.
The Future of SLS in Serial Production
Of course, the ultimate goal is to use SLS to manufacture serial production parts for the next generation of automotive products, which Christian believes will arrive in the near future.
“Prototyping and spare parts—you can do them now. At the moment, looking at the technical developments, I see [serial] production in four to five years.”
Christian Kleylein
To get there, two key changes need to happen: consideration of AM during product development starting from the design phase, and further decreases in material and machine cost.
“The biggest obstacle is to get the product designer to actually know what they can do with 3D printing and make that decision to 3D print the part. You're never going to be cost-effective with components that are designed for injection molding. You need to design for the process,” said Kleylein.
“It just comes down to how many pieces you plan to print and the efficiency of traditional manufacturing systems. Once the value proposition is right, we’ll produce a part with the most efficient production system available. We're not going to force 3D printing on a product, but if it's the best possible way to produce the part, we're going to print it,” said Kleylein.
By lowering the barrier to entry for SLS 3D printing, the Fuse 1 will play a key role in empowering this shift to production. Brose already has plans to continue rapidly expanding its 3D printing capabilities. Their second plastic AM workshop is under construction in the US, and they'll receive their first Fuse 1 as well soon.
“There are still a lot of big challenges ahead, but if I'm looking at the Fuse 1, we have a very capable product, at a very competitive price.”
Christian Kleylein